Разработка фрезерного рабочего оборудования (дорожная фреза) на базе трактора МТЗ-80




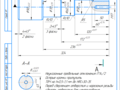
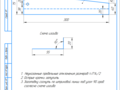
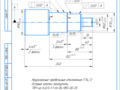
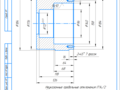
- Добавлен: 24.01.2023
- Размер: 5 MB
- Закачек: 0
Описание
Состав проекта
![]() |
![]() |
![]() |
![]() |
![]() |
![]() |
![]() |
![]() |
![]() ![]() ![]() ![]() |
![]() ![]() ![]() ![]() |
![]() ![]() ![]() ![]() |
![]() ![]() ![]() ![]() |
![]() ![]() ![]() ![]() |
![]() ![]() ![]() ![]() |
![]() ![]() ![]() ![]() |
![]() ![]() ![]() ![]() |
![]() ![]() ![]() ![]() |
![]() ![]() ![]() ![]() |
![]() ![]() ![]() ![]() |
![]() ![]() ![]() ![]() |
![]() ![]() ![]() ![]() |
![]() ![]() ![]() ![]() |
![]() ![]() ![]() ![]() |
![]() |
![]() |
![]() |
![]() |
![]() |
![]() |
![]() |
![]() |
![]() ![]() ![]() |
![]() ![]() ![]() |
![]() ![]() ![]() |
![]() ![]() ![]() |
![]() ![]() ![]() |
![]() ![]() ![]() |
![]() ![]() ![]() |
![]() ![]() ![]() |
![]() ![]() ![]() |
![]() ![]() ![]() |
Дополнительная информация
корпус.cdw

Острые кромки притупить
Рычаг основной.cdw

Острые кромки затупить
Заготовку согнуть по штриховой линии под угол 90 град.
согласно схеме изгиба
-1250-2500 ГОСТ 19903-74
Пластина.cdw

Острые кромки затупить
-1250-2500 ГОСТ 19903-74
Палец.cdw

Неуказанные радиусы скруглений R2
Корпус подшипника.cdw

Острые кромки притупить
Планка 3.cdw

Острые кромки затупить
Заготовку согнуть по штриховой линии согласно схеме изгиба
Лента 50-5 ГОСТ 3560-73
стойка.cdw

Острые кромки притупить
Вал.cdw

Острые кромки притупить
Крышка.cdw

Острые кромки притупить
Вал ротора длинный.cdw

Острые кромки притупить
Перед сверлением отверстия и нарезания резьбы
сделать отверстие для центрирования
Рычаг.cdw

Острые кромки затупить
Уголок неравнобокий
Ст3пс-3 ГОСТ 11474-76
Бок корпуса.cdw

Острые кромки затупить
-1250-2500 ГОСТ 19903-74
Планка 2.cdw

Острые кромки затупить
Лента 40-8 ГОСТ 3560-73
вкладыш.cdw

Неуказанные радиусы R=5 мм
Планка.cdw

Острые кромки затупить
-1250-2500 ГОСТ 19903-74
глава 1.doc
1. Хозяйственная деятельность дорожного комитета Саратовской области
Протяженность дорожной сети области составляет 29377 тыс. км из них 0717 тыс. км – федеральные 9876 тыс. км - региональные 14416 тыс. км – муниципальные 4368 тыс. км – межмуниципальные.
В сеть автомобильных дорог общего пользования входит 761 мостовой переход (38643 тыс. погонных метра) в том числе:
- 63 моста (4135 тыс. погонных метра) на федеральных дорогах;
- 508 мостов (28219 тыс. погонных метра) на региональных дорогах;
- 77 мостов (2057 тыс. погонных метра) на муниципальных дорогах;
- 113 мостов (4232 тыс. погонных метра) на межмуниципальных дорогах.
Протяженность опорной дорожной сети области обеспечивающей основной объем автомобильных грузо и пассажироперевозок составляет 1007 км в том числе: Самара-Пугачев-Энгельс-Волгоград – 3681 км Энгельс – Ершов – Озинки – граница респ. Казахстан – 29525 км Тамбов – Ртищево – Саратов – 22425 км Балашов – Ртищево – 963 км Елшанка – Песчаный Умет – 231 км.
Финансовое обеспечение дорожного хозяйства
Законом области «Об областном бюджете на 2008 год» на финансирование сети автомобильных дорог находящихся в государственной собственности области выделено 2277 млрд рублей в том числе 10 млрд рублей – субсидии из средств федерального бюджета.
Финансирование дорожного хозяйства осуществлялось в соответствии с росписью расходов областного бюджета и выполнено в полном объеме.
Проведение торгов (конкурсов) по размещению заказов на поставки товаров выполнение работ оказание услуг для государственных нужд позволило получить экономию средств областного бюджета в размере 87164 млн рублей что составляет 7 процентов экономической эффективности размещения заказов.
Об итогах выполнения программы дорожных работ
Программа дорожных работ на территориальных дорогах общего пользования за 2008 год выполнена в полном объеме по всем показателям таблица 1.1. и рисунок 1.1
Таблица 1.1. – Итоги выполнения дорожных работ по Саратовской области
Лимит затрат на 2008 год
Факт за январь-декабрь 2008 года
Строительство и реконструкция
Приобретение техники
Погашение кредиторской задолженности
Затраты на строительство и реконструкцию профинансированы в объеме 11516 млн рублей или 506% в общем объеме расходов что позволило провести работы на наиболее грузонапряженных участках опорной сети региональных дорог.
Введены в эксплуатацию 10422 км дорог и 24566 погонных метров мостов:
9 км автомобильной дороги Энгельс-Ершов-Озинки на участке км88-км 96 в Федоровском районе (в рамках Федеральной целевой программы (ФЦП);
52 км подходов к мостам;
929 погонных метра - мостовой переход через р.Большой Узень на автодороге Александров Гай – Новоалександровка (ФЦП);
26 погонных метра - 3 мостовых перехода: в Балтайском районе – 2 моста и в Вольском – 1 мост;
вторая очередь Гусельской эстакады на автомобильной дороге Саратов – Усть – Курдюм (ФЦП).
На переходящих объектах:
продолжено строительство автомобильной дороги Самара-Пугачев-Энгельс-Волгоград на участке обхода г.Пугачева; построено 14 км (без верхнего слоя асфальтобетонного покрытия) (ФЦП);
на строительстве мостового перехода через реку Волгу у с.Пристанное (ФЦП):
В 2008 году выделено 433 млн рублей из них 385 млн рублей - субсидии из федерального бюджета и 48 млн рублей – средства областного бюджета. Все выделенные средства полностью освоены:
осуществлена сборка 23 тыс. тонн пролетных строений в том числе 11тыс. тонн через основное русло;
отсыпано 1995 тыс. куб. метров грунта на подходах;
устроена дорожная одежда на площади 1017 тыс. кв. метров.
По состоянию на 1 января 2008 года на строительстве мостового перехода освоено 90 процентов от стоимости объекта. Остаток сметной стоимости строительства - 1885млн рублей.
Основная часть работ по строительству и реконструкции региональных дорог велась в рамках реализации Федеральной адресной инвестиционной программы «Модернизация транспортной системы России (2002-2010 годы)».
На выполнение программы в 2008 году направлено 1125975млн рублей в том числе 10000 млн рублей из средств федерального бюджета и 125975 млн рублей из средств областного бюджета:
96 млн рублей – реконструкция автомобильной дороги Саратов - Усть-Курдюм из них 3300млн рублей – средства федерального бюджета 396 млн рублей – средства областного бюджета;
Рисунок 1.1. Итоги работы дорожного комитета за 2008 год.
)4330 млн рублей – строительство мостового перехода через р. Волга у с. Пристанное из них 3850 млн рублей – средства федерального бюджета 480 млн рублей – средства областного бюджета;
) 47074 млн рублей – строительство мостового перехода через р.Большой Узень на автодороге Александров Гай – Новоалександровка изних435млн рублей – средства федерального бюджета 3574млнрублей – средства областного бюджета;
)183127 млн рублей – строительство автомобильной дороги Самара – Пугачев – Энгельс – Волгоград на участке обхода г.Пугачева из них 1515 млн рублей – средства федерального бюджета 31627 млн рублей - средства областного бюджета;
)93174 млн рублей – реконструкция автомобильной дороги Энгельс – Ершов – Озинки на участке км 88 – км 96 в Федоровском районе из них 900млн рублей - средства федерального бюджета 3174 млн рублей – средства областного бюджета.
Затраты на ремонт региональных автомобильных дорог общего пользования и мостов профинансированы в объеме 2916 млн рублей что составило 128% в структуре расходов на дорожное хозяйство.
Отремонтировано 5476 км автомобильных дорог в том числе на опорной сети:
- ад Самара-Пугачев-Энгельс-Волгоград - 265 км;
- ад Тамбов-Ртищево-Саратов - 88 км;
- ад Энгельс-Ершов-Озинки – 2 км;
- ад Урбах-Новоузенск-Александров Гай – 6 км;
- ад Балашов-Ртищево – 11 км;
- ап к г.Балаково – 3985 км;
- территориальная сеть – 6375 км.
В разрезе муниципальных образований: в Аркадакском районе – 11км Балаковском– 68км Вольском – 3985км Ивантеевском – 20км Краснокутском – 30км Марксовском– 82км Новобурасском – 2275км Новоузенском – 30км Пугачевском – 20км Ртищевском – 88км Хвалынском – 36 км Энгельсском – 95км Воскресенском – 05 км.
Закончены ремонтом и введены в эксплуатацию 53421 погонных метра мостов (100% от годового плана) в том числе в Марксовском районе – 6774 п.м. Аткарском – 5152 п.м. Краснокутском – 5412 п.м. Вольском – 3877 п.м. Советском – 1189 п.м. Перелюбском – 11346 п.м. Пугачевском – 402 п.м. Федоровском – 186 п.м Базарно-Карабулакском-204 п.м Петровском – 105 п.м.
На автомобильном мосту «Саратов-Энгельс» в 2008 году освоено 30314 млн рублей из них 21063 млн рублей – на ремонт 9251 млн рублей – на содержание. Произведен ремонт опор № 6 11 16. Осуществлено 29% от проектного объема монтажа и антикоррозионной защиты. Установлено 900м перильного ограждения (161%).
Содержание автомобильных дорог
Затраты на содержание региональных автомобильных дорог общего пользования и мостов профинансированы в объеме 6087 млн рублей что составило 267% в структуре расходов на дорожное хозяйство.
На протяжении всего года велись работы по содержанию автомобильных дорог с целью обеспечения требований к эксплуатационному состоянию допустимому по условиям обеспечения безопасности дорожного движения:
- поддерживалось бесперебойное и безопасное движение поавтомобильным дорогам области;
- производились работы входящих в норматив по зимнему и летнему содержанию автомобильных дорог искусственных сооружений на них.
Состояние дорог в Саратовской области
Однако необходимо отметить то обстоятельство что состояние дорог в Саратовской области зависит от категории дороги протяженности и насыпи дорожного покрытия. Места перехода дорог от внутри городского назначения к федеральному определит наличие смещения покрытия дороги т.к. эксплуатируются при движении большегрузных машин при малой скорости движения. В весенний период движение грузовых машин движущихся по федеральной трассе проезд через город запрещен.
На трассах федерального назначения за чертой города основные дефекты разломы и трещины асфальтированных покрытий. Это связано с нарушением технологии строительства просадкой дорожной насыпи и дорожной одежды.
При строительстве плохо производится геологическая развертка места строительства. При просадке дорожной одежды на поверхности асфальта образуются трещины и наплывы в местах разлома. Основная длина трещин порядка 15-20 м по одной стороне движения автотранспорта по выраженным участкам разлома образуются ямы и выбоины что приводит к увеличению в размерах за счет динамических ударов протекторов автомобилей. Количество трещин составляет порядка 4-6 в месте одного разлома дорожного покрытия количество образовавшихся ям 5-7 на поверхности трещин на данном разломе. Наплывы образуются в результате проникновения влаги под поверхность асфальтобетона в весенне-осеннее время. За счет тяжелых автогрузовиков образуется смещение асфальта в сторону движения. Количество наплывов составляет 3-6 в зависимости от загруженности и угла спуска дороги.
По причине малого финансирования строительства происходит экономия строительного материала при проектировании и строительстве. Актуальной проблемой по ремонту дорог является ямочный ремонт. При определенных климатических условиях происходит разрушение и последующее увеличение глубины выбоин и объема ремонтных работ.
В конечном итоге это обстоятельство приводит к увеличению дорожно-транспортных происшествий (ДТП) так происходит рост количества автомобилей рис. 1.2. Анализ ДТП показал рис. 1.3 что постоянно растущее количество автомобилей приводит к повышению количества аварий. В первую очередь это связано с некачественным дорожным покрытием а особенно в зимнее время.
Несмотря на некоторый спад количества ДТП в последние годы травматизм аварий значительно увеличился.
Рисунок 1.2. Количество автомобилей в городе Саратов на 1000 человек
Рисунок 1.3. Количество ДТП и пострадавших в городе Саратове на 100000 человек
В связи с эти необходимо проводить ремонт автомобильных дорог. Но в первую очередь необходимо определить причины возникновения дефектов дороги и как они влияют на ДТП.
2. Причины возникновения ДТП связанные с дорожными условиями
2.1. Восприятие водителями дорожных условий и режимы движения по дорогам
Каждая дорога является сочетанием участков с различными элементами в плане и продольном профиле. Поэтому скорости движения автомобилей на маршруте не остаются постоянными. На длинных прямых горизонтальных участках а тем более на спусках современные автомобили могут развивать скорости существенно превышающие расчетные по строительным нормам и правилам. На длинных подъемах скорости значительно ниже расчетных.
Действовавшие в разное время Технические условия на проектирование автомобильных дорог и строительные нормы и правила всегда предусматривали напряженный режим движения. Поэтому водители автомобилей если они не движутся в составе плотного транспортного потока когда их режим движения вынужден предпочитают спокойное движение со скоростями меньшими чем предусмотрены расчетом и избираемыми ими интуитивно в соответствии со своим опытом и восприятием дорожных условий. Иногда при этом они как бы корректируют решения проектировщиков заезжая на кривых малых радиусов на полосу встречного движения или проезжая их со скоростью соответствующей удобным для них коэффициентам поперечной силы и скоростям изменения продольного и поперечного ускорений.
Водитель оценивает условия движения преимущественно визуально. Дополнительными источниками информации являются также передающиеся на его организм ускорения возникающие при проезде по кривым и неровным участкам дороги.
Факторами влияющими на избираемые водителями режимы движения являются:
- элементы дороги непосредственно влияющие на управление автомобилем (изменения направления дороги дорожные знаки неровности проезжей части примыкания разветвления и перекрестки обеспеченная видимость). Мысленно оценивая их влияние на условия движения увязывая эту оценку с требованиями Правил движения водитель подсознательно изменяет скорость движения;
- обстановка движения — встречные и попутные автомобили мотоциклисты и велосипедисты пешеходы на обочинах погодные условия;
- привлекающие внимание водителя объекты не связанные непосредственно с движением — здания сооружения и деревья на придорожной полосе пролетающие над дорогой самолеты горные вершины на горизонте и др. В процессе движения взгляд водителя скачкообразно перебрасывается с одного объекта на дороге и придорожной полосе на другой как бы выделяя опорные точки вырисовывающие пространственный коридор по которому он ведет автомобиль (рис. 1.4). Ими являются края проезжей части и земляного полотна линии разметки и осевой шов бетонных дорожных покрытий ряды придорожных насаждений нависающие над дорогой скалы дорожные знаки встречные автомобили и др. При выборе объекта в первую очередь взгляд водителя останавливается на предметах более ярких и расположенных на пути следования автомобиля особенно на проезжей части и обочинах дороги.
Рисунок 1.4. Перемещение взгляда водители при проезде кривых в плане на горных дорогах (по опытам В. В. Варлашкина):
а — выпуклая кривая; б - вогнутая кривая; номера точек соответствуют последовательности сосредоточения взгляда водителя диаметры кружков — его относительной продолжительности
Количество объектов которые водитель может различить и зафиксировать в своем сознании ограничено продолжительностью времени необходимого для восприятия отдельных раздражителей его органами чувств. Для каждого из них существует пороговая величина зависящая от эмоционального напряжения человека. В среднем для зрения она равна 110 с для слуха — 120 с для мускульной реакции на толчки и тряску — 15 с. Более частые воздействия сливаясь воспринимаются органами чувств как непрерывные процессы — мелькание в глазах гул вибрация. Обычно водитель в каждый момент времени сосредоточивает свое внимание только на одном конкретном явлении получая о других одновременно происходящих только самое общее представление
При возрастании скорости взгляд водителя охватывает все меньшую ширину дорожной полосы и сосредоточивается на большем удалении автомобиля (рис. 1.5). Сужение зоны сосредоточения внимания водителей повышает опасность наезда на неожиданно появляющихся на дороге с придорожной полосы пешеходов или животных.
При свободном движении одиночных автомобилей характерном для малой интенсивности водители движутся со скоростью при которой плотность объектов близка к оптимальной для их восприятия. При монотонности дорожных условий — малой плотности или однообразии объектов привлекающих внимание например при движении по длинному прямому участку в открытой степной местности или по однородной лесной просеке поступающее к водителю количество информации меньше чем необходимо для поддержания его активности. Наступает «сенсорный голод» по терминологии инженерной психологии. Острота восприятия водителем окружающей обстановки снижается мысли рассеиваются или переключаются на события не имеющие отношения к движению по дороге и отвлекающие водителя. Водитель начинает ощущать повышенную утомляемость своеобразное дремотное состояние граничащее со сном — «дорожный гипноз» характерное заторможенное состояние высшей нервной деятельности. Возникновению его способствует наряду с укачивающими колебаниями автомобиля гипнотизирующее действие на водителя вида набегающей светлой полосы бетонного покрытия и белых линий разметки на асфальтобетоне бликов на капоте автомобиля. Продолжительность реакции водителя увеличивается а надежность работы снижается. Самое незначительное осложнение условий движения может явиться причиной дорожно-транспортного происшествия. Такой характер воздействий особенно типичен для водителей грузовых автомобилей.
Рисунок 1.5. Точки сосредоточения взгляда водителя за период 3 мин при проезде по дороге с разными скоростями (по опытам Е. М. Лобанова):
а — 20 кмч; б — 80 кмч; в — зоны охватываемые взглядом; Цифры на сетке координат характеризуют отклонения точек от взгляда водителя направленного вдоль дороги в градусах
В сознании водителя при движении происходит непрерывная смена картин. В зависимости от дорожной обстановки частоты встреч и обгонов ландшафта местности количество объектов сосредоточения внимания — раздражителей — меняется. Основное внимание сосредоточивается на полотне дороги дополняясь событиями на прилегающей дорожной полосе. Распознавание объектов в поле зрения происходит как бы в два этапа начинаясь с беглого их осмотра. Выполняя предварительную их оценку водитель начинает более детальное распознавание объектов сосредоточиваясь затем на более важных из них пока не опознает их на 70-80%.
Органы чувств водителя дают ему возможность в каждый момент времени воспринять ограниченное количество факторов. Считается что в открытой местности водители фиксируют явления происходящие перед ними в зоне до 600 м на городской улице — от 50 до 100 м.
Если в пределах зоны L охватываемой в какой-то момент времени взглядом водителя находится М объектов которые могут привлечь его внимание то осознать из них водитель может только
v — скорость движения автомобиля.
При возрастании скорости количество осознаваемых объектов уменьшается.
Для каждого водителя существует оптимальная плотность объектов внимания характеризуемая продолжительностью времени которое ему необходимо для их распознавания и оценки значимости. При оптимальной плотности и разнообразии объектов внимание водителей активизируется. При перегрузке информацией внимание рассеивается и водитель не замечает существующих элементов например знаков.
При движении по дороге с различными скоростями число объектов попадающих в поле зрения водителя в единицу времени тем больше чем выше скорость. Водитель непроизвольно реагирует на изменение поступающей информации изменением зоны сосредоточения своего взгляда или избирательным отношением к поступающей информации.
Часть водителей стремится довести количество получаемой информации до оптимального увеличением скорости движения. Однако в однообразной степной местности при отсутствии расположенных рядом с дорогой предметов водителям трудно точно оценить развитую скорость которая нередко достигает опасного значения.
Чрезмерная плотность событий привлекающих внимание водителей— «перегрузка информацией» количество которой превышает пропускную способность анализаторов человека приводит к своеобразному «отказу» — недоучету значения того или иного раздражителя и как следствие к неправильным действиям ведущим к дорожно-транспортному происшествию.
Трудные условия создаются при движении автомобиля в составе насыщенного транспортного потока когда из-за сложности или даже невозможности осуществления обгона все водители должны ехать со сложившейся в потоке скоростью которая может не соответствовать их опыту психологическим особенностям и степени утомления. Следуя в составе «пачки» или колонны автомобилей на минимальном расстоянии от впереди идущего автомобиля в более сложных условиях чем оптимальные для него водитель ориентируясь в большей степени на маневры идущих впереди автомобилей чем на изменение трассы дороги имеет ограниченное время для принятия решений. При этом существует риск совершить ошибку которая приведет к происшествию. Наблюдения показали что следуя по одной и той же дороге при одиночном движении в течение 1 мин водитель в 15 раза чаще бросал взгляд на знаки чем при колонном движении и в 27 раза на кромку проезжей части. Если придорожные ландшафты и проложение трассы в плане однотипны на большом протяжении у водителей вырабатывается определенная последовательность движения с которой они свыкаются а их внимание притупляется. Однообразный ритм движения вызывает автоматизм операций управления автомобилем. Изменение дорожных условий воспринимается водителями как дополнительная трудность.
Детальный анализ обстановки возникновения дорожно-транспортных происшествий показывает что в 70% случаев скорости в месте возникновения происшествий и в 500 м перед ним были практически одинаковы т. е. водители подъезжая к опасному месту не снижали скорости. Происшествия явились результатом того что в меняющихся дорожных условиях водители своевременно не изменили режим движения.
Таким образом признаком опасных мест является не столько значительное осложнение дорожных условий сколько необходимость часто неожиданного для водителя изменения режимов движения транспортных потоков по сравнению с предшествующими участками. Это подтверждается тем что на многих участках горных дорог со сложной и трудной трассой создающей у водителей понимание ее опасности относительное количество происшествий на 1 млн. авт-км меньше чем на дороге с более легкой трассой.
Опасность участков дороги определяется не абсолютной величиной геометрических элементов их трассы или состояния дорожного покрытия а их отличием от характеристик предшествующих участков вызывающим необходимость резкого изменения режима движения.
2.2. Эмоциональная напряженность водителей при движении по дороге
Изменение условий проезда на разных участках дороги или их осложнение в связи с увеличением интенсивности движения и тем более при неправильных действиях других водителей или пешеходов немедленно отражается на нервно-психическом состоянии водителя и степени его эмоциональной напряженности. Это вызывается усложнением ведения автомобиля необходимостью преодоления «психологической инерции» при изменении стереотипа ритма движения выработавшегося на предыдущих участках воздействием неожиданных маневров других автомобилей уменьшением расстояния видимости. Особенно опасен переходный период когда водитель изменяет скорость своего автомобиля приспосабливаясь к условиям движения на новом участке дороги.
Изменение условий движения сопровождается рядом внешних проявлений нервно-психических процессов возникающих в организме водителя— изменением частоты пульса и дыхания частотой перемещения взгляда водителя с одних объектов на другие изменением электропроводности кожи кожно-гальваническая реакция — сокращенно (КГР).
Используемые при исследованиях показатели состояния водителей хорошо отражают изменения нервно-эмоциональной напряженности водителей. В табл. 1.1 приведены средние относительные значения разных показателей при различной степени напряженности выраженные в долях оптимальной напряженности соответствующей максимальной надежности работы водителя.
Таблица 2.1 – Характеристика напряженности водителя
Относительные характеристики напряженности
Запредельная напряженность
Кожно-гальваническая реакция
Организм водителей чутко реагирует на изменение дорожных условий. Чем меньше элемент трассы например радиус кривой в плане тем сильнее возрастает эмоциональная напряженность водителем.
Процент происшествий возрастает с увеличением продолжительности пребывания за рулем во время рабочей смены. По наблюдениям В. В. Чванова и С. С. Петросяна он составляет:
Продолжительность пребывания за рулем ч . 2 2—4 4—8 8—12 12
Процент происшествий. % 82 100 232 245 341
Возрастание эмоциональной нагрузки водителей при проезде трудных для проезда и опасных мест соответствует местам резкого снижения средней скорости транспортных потоков и следовательно уменьшения коэффициента безопасности. При плавном логическом сочетании элементов трассы дороги и постепенной нерезкой смене ландшафта придорожной полосы скорость движения по дороге изменяется в малых пределах а нервно-эмоциональная нагрузка водителей существенно снижается оставаясь оптимальной в отношении внимательности и активности водителей и продолжительности их реакции. Движение безопаснее а управление автомобилем менее утомительно. Характерна связь между нервно-эмоциональной напряженностью водителей и коэффициентом безопасности при смене дорожных условий (табл. 1.2).
Таблица 1.2 – Коэффициент безопасности
Характеристика участка
Коэффициент безопасности
Эмоциональная напряженность
Запредельно напряженная
Таким образом установленные в нормах значения коэффициентов безопасности предусматривают несколько повышенную напряженность водителей при движении.
Дальнейшее совершенствование методов проектирования дорог и их оборудования должно быть направлено на обеспечение безопасности движения не только с позиций механической устойчивости автомобилей как было до сих пор но и на соблюдение требований оптимальной нервно-эмоциональной нагрузки водителей.
2.3. Пути предотвращения происшествии связанных с дорожными условиями
Изменение скоростей транспортных потоков в местах сосредоточения происшествий связанных с дорожными условиями показывает что для их предотвращения необходимы мероприятия обеспечивающие плавное изменение скорости и устранение причин возникновения в этих местах внутренних помех. Может быть проведена аналогия с движением водных потоков в открытых руслах согласно которой следует так рассчитывать и располагать все элементы дороги чтобы по возможности устранить в транспортном потоке возникновение турбулентности (частых обгонов) застое (заторов) и подпора (резкого сосредоточения дистанции между автомобилями в процессе скорости движения).
Этим целям может способствовать ряд мероприятий примеры которых показаны на рис. 1.6.:
Рисунок 1.6. Изменение коэффициента безопасности при проведении мероприятий по регулированию скорости движения:
а — устройство переходно-скоростных полос; б — устройство трясущих полос перед переездом; в — увеличение радиуса кривой; г — увеличение видимости на кривой вырубкой деревьев; д—устройство кольцевой развязки на пересечении; е- постройка путепровода через железную дорогу; ж — устранение неровного или скользкого участка покрытия; з— устройство тротуара в населенном пункте;
— место снижении скорости; 2—срезка видимости; 3—неровное или скользкое покрытие; 4— отремонтированное покрытие; 5— пешеходы на обочинах; 6 — тротуары
- выравнивание эпюры скоростей по протяжению дороги — повышение скоростей путем реконструкции мест где скорости существенно снижаются и ограничение скоростей на опасных участках;
- обеспечение пространства необходимого для маневров автомобилей и уверенного ведения автомобиля по дороге (видимость в плане продольном профиле и на придорожной полосе уширение проезжей части в кривых малого радиуса и в конце спусков устройство обгонных прямых участков при извилистой трассе);
- обозначение трассы дороги для водителей — общего ее направления за пределами непосредственной видимости и разметка на проезжей части полос пути движения.
В зависимости от местных условий для достижения этих целей могут предусматриваться следующие мероприятия:
- перестройка опасных участков дороги — изменение элементов плана продольного и поперечного профилей вызывающих снижение скоростей и создающих помехи для движения (увеличение радиусов кривых расчистка придорожной полосы для увеличения видимости смягчение продольных уклонов уширение проезжей части перестройка узких мостов постройка объездов населенных пунктов);
- разделение транспортного потока на группы следующие по самостоятельным полосам движения с разными скоростями (местное и транзитное движение в населенных пунктах) когда часть потока в определенном месте дороги изменяет скорость движения (переходно-скоростные полосы на подходах к пересечениям дорог) а также в местах где резко проявляется различие в динамических качествах автомобилей разных типов (затяжные подъемы в сильно пересеченной и горной местностях);
- использование мер пассивного регулирования движения — разметка проезжей части устройство пересечений в одном уровне с направляющими островками.
3. Причины образования дефектов на дороге
3.1. Воздействие породно-климатических и температурных факторов на дорогу
Транспортные средства воздействуют на дорогу одновременно с факторами зависящими от природно-климатических условий (температурой влагой солнечной радиацией и др.). Закономерные изменения водно-теплового режима в течение года дополняются ежесуточными погодными воздействиями. В годовом цикле выделяют четыре характерных периода работы дорожной одежды:
- накопление влаги осенью;
- промерзание перераспределение и накопление влаги зимой;
- оттаивание и переувлажнение весной;
- просыхая не летом.
Осенью под воздействием потока воды от затяжных атмосферных осадков проникающих в дорожную конструкцию происходит переувлажнение слоев дорожной одежды и грунта земляного полотна. Во II дорожно-климатической зоне к которой относится территория саратовской области осенняя влажность грунтов нередко достигает 07 WT (WT — влажность на пределе текучести грунта) и наблюдается их разуплотнение. В водонасыщенных слоях дорожной одежды при прохождении автотранспорта возникают гидравлические удары и динамические перемещения воды. При этом в органно-минеральных материалах часто нарушается адгезия (сцепление) на границе раздела фаз между вяжущим и минеральными частицами и происходит разрушение структуры. В слоях укрепленных минеральными вяжущими возможно вымывание водорастворимых компонентов и постепенное их разуплотнение.
Зимой в процессе промерзания земляного полотна наблюдается приток влаги к фронту промерзания. При этом происходит разуплотнение грунта. Аналогично в связанных слоях дорожной одежды возникают растягивающие напряжения за счет замораживания воды в порах. Однако ввиду того что грунт и слои дорожной одежды находятся в замерзшем состоянии их прочностные характеристики достаточно велики.
Весной при оттаивании земляного полотна грунт наиболее увлажнен (по 085 WT) и разуплотнен. Чем больше влажность талого грунта тем меньше его деформационные (модуль упругости Еу) и прочностные характеристики (угол внутреннего трения j сцепление с). Наименьшие значения Еу j и с наблюдаются обычно в апреле-мае. В это время дорожная конструкция обладает наименьшей прочностью. Кроме того суточные колебания температуры вызывают замерзание воды ночью и оттаивание днем что разрушает структуру связанных материалов.
Летом земляное полотно интенсивно просыхает влажность грунта уменьшается (до 05WT). Дорожная одежда имеет хорошую опору однако при высоких температурах возможно размягчение органических вяжущих и колееобразование на покрытии.
3.2. Причины появления дефектов
Из вышесказанного следует что во все времена года под воздействием транспортных нагрузок и погодно-климатических факторов происходят деструктивные процессы приводящие к появлению дефектов на автомобильных дорогах и необходимости выполнения соответствующих ремонтных работ. В зависимости от конструкции прочности и состояния дорожной одежды под действием повторяющихся нагрузок в отдельных слоях и в дорожной одежде в целом могут появляться упруго-вязкие деформации либо одновременно упруго-вязкие и вязко-пластические деформации которые накапливаясь могут достичь предельных значений. Для одежды из монолитных материалов наиболее опасны растягивающие напряжения возникающие в слое при изгибе а для слоев из слабосвязных материалов (зернистых) — напряжения сдвига.
Согласно данным Л.П.Васильева максимальные растягивающие напряжения в асфальтобетонном и подобном ему покрытии возникают на его нижней поверхности по оси действующей нагрузки автомобиля.
Основным видом нарушения сплошности грунтов и слабосвязных материалов дорожной одежды под действием транспортных нагрузок является сдвиг. Чрезмерные напряжения от транспортных нагрузок приводят к возникновению необратимых деформаций. Их развитию способствуют природно-климатические факторы вызывающие увлажнение перегрев или промерзание конструкции.
При высоких положительных температурах и тяжелом интенсивном движении прочностные свойства покрытий из материалов на органических вяжущих существенно ухудшаются появляется опасность возникновения пластических деформаций в виде наплывов волн колеи (рис. 1.7) вмятин сдвигов. При отрицательных температурах такие покрытия приобретают свойства хрупкого тела. При этом значительно повышаются модули упругости и сопротивления сжатию но одновременно снижается их способность деформироваться без нарушения сплошности. Предельные относительные удлинения асфальтобетона уменьшаются от 0006-0002 при 0°С до 00015-00006 при -20°С. При резком изменении в сторону низких температур такие покрытия растрескиваются вследствие недостаточной деформационной компенсации линейному сжатию. Весной в результате повторяющихся нагрузок от транспорта в покрытии лежащем на ослабленном основании возникают многократные прогибы вызывающие усталостное разрушение в виде сетки трещин.
Напряжения в цементобетонных покрытиях возникают от воздействия нагрузки и изменения температуры.
При нагревании или охлаждении покрытие стремится изменить размеры но из-за сопротивления сил трения по основанию это становится затруднительным. В результате появляются температурные напряжения. К ним добавляются напряжения от неравномерного распределения температур по толщине и от транспортных нагрузок. Все это приводит к образованию и развитию трещин в цементобетонном покрытии (рис. 1.8). Основываясь на механике разрушения разработан алгоритм расчета прогноза долговечности бетона по обобщенному критерию трещиностойкости который учитывает зоны концентрации указанных напряжений в вершинах радиальных трещин возникающих на границе зерен клинкера и гидратированной массы зерен мелкого заполнителя и цементного камня зерен крупного заполнителя и цементно-песчаного раствора. Согласно физической модели бетона (рис. 1.9.) все дефекты структуры бетона как исходные так и развившиеся в результате силовых и несиловых воздействий делят на пять основных видов:
Рисунок 1.7. Образование колеи
Рисунок 1.8. Трещины на бетонном покрытии
Рисунок 1.9.Физическая модель бетона:
I - зерна щебня; II - зерна песка; III — зерна клинкера; IV — гидратированная масса цемента; C Cj— адгезионные контакты: 1 —капилляры заполненные водой симметрично; 2 — капилляры защищенные допой несимметрично; 3 — микротрещины; 4 - трещины на контакте с зернами; 5 — полости контактов
— крупные поры с выходящими на их границы субмикротрещинами образовавшимися в результате концентрации напряжений вокруг круглого отверстия;
- эллипсовидные поры с выходящими на их границы микротрещинами;
— трещиновидные дефекты в теле бетона;
— краевые трещиновидные дефекты;
— радиальные и контактные трещины вокруг зерен и включений.
Характеристики наиболее распространенных деформаций и повреждений дорожной одежды приведены в табл. 1.3.
Таблица 1.3 – Характеристика дефектов дороги
Деформаций и разрушения
Наиболее вероятные причины возникновения дефектов
Покрытия на органических вяжущих
Часто наблюдаются на грузопассажирских трассах а также в местах остановок транспорта
Излишняя пластичность из-за избытка вяжущего или недостаточной теплоустойчивости смеси при высоких температурах (низкая температура размягчения вяжущего неправильно подобран минеральный каркас) слабое основание
Наблюдаются на крутых спусках в местах торможения и остановок транспорта
Аналогично п.1 в условиях недостаточного сцепления покрытия с основанием
Выкрашивание и шелушение
Наблюдается на всей поверхности
Недостаточно прочное сцепление (адгезия) вяжущего с каменным материалом
Наблюдается на всех видах покрытий
Недостаточное сопротивление покрытия касательным усилиям от транспортных средств выбивающих и выдергивающих каменные частицы
- температурные поперечные располагаются примерно через одинаковые расстояния (не менее 10 м);
— косые и поперечные трещины с ответвлениями не образующие замкнутых фигур (через 1-4 м);
— сетки трещин с крупными ячейками;
— сетки трещин с мелкими ячейками
Недостаточная деформативная способность покрытия и малая сопротивляемость его напряжениям возникаемая от изменения температуры.
Неоднородность свойств покрытия и основания
Воздействие многократной нагрузки
Недостаточная прочность дорожной конструкции старение вяжущего деструкция бетона
Аналогично п. 4 выщелачивание неорганических вяжущих водой и растворами противогололедных материалов
Покрытия на неорганических вяжущих
— поперечные сквозные;
Превышение допустимого расстояния между швами сжатая или расширения излишне длительные перерывы в бетонировании
— продольные сквозные;
Деформация в продольных швах недостаточное качество уплотнения земляного полотна
Неравномерное распределение температуры по толщине покрытия обусловливающее его коробление недостаточная деформативная способность под действием нагрузки
Усадка бетона при неправильном уходе после укладки покрытия низкая морозостойкость материала
— косые вблизи углов плиты;
Недостаточно полное прилегание бетонной плиты к основанию и повышенные напряжения при проезде транспортных средств
Недостаточная прочность и высокая истираемость материала покрытия.
Дефекты земляного полотна (недостаточное уплотнение размыв)
От распределения указанных дефектов определяемого главным образом составом бетона зависит способность бетонных покрытии воспринимать транспортные и температурные нагрузки. При неблагоприятных условиях микротрещины в структуре бетона развиваются в макротрещины в слое покрытия. Таким образом трещины образуются в разное время в различных местах плит имеют разные очертания и направления неодинаковую глубину.
Анализ хозяйственной деятельности дорожного комитета Саратовской области показал что на ремонт и содержание дорог области расходуется большое количество денежных средств. При этом качество дорожного покрытия оставляет желать лучшего.
Анализ состояния дорог показал что они находятся в удовлетворительном состоянии. На дорогах имеются многочисленные выбоины и трещины наличие которых негативно отражается на движении автотранспорта что приводит к частым ДТП.
Рассмотрев основные причины возникновения дефектов на дорожном полотне было установлено что наибольшая часть из них обусловлена плохим качеством дорожного основания. В результате природно-климатических условий Саратовской области происходит разрушения основания дороги (тела дороги) вследствии размыва и воздействия низких температур.
В итоге необходимо проводить мероприятия по устранению в первую очередь дефектов тела дороги а затем дорожной одежды (полотна).
В связи с этим целью дипломного проекта является разработка сменного фрезерного рабочего оборудования на базе трактора ОМТЗ-82.1.
Для реализации поставленной цели необходимо решить следующие задачи:
Рассмотреть конструкции машин и рабочих органов способных разрабатывать грунт путем фрезерования;
Разработать конструктивно-компановочную схему фрезерного рабочего оборудования на базе трактора ОМТЗ-82.1;
Произвести выбор и обоснование основных параметров фрезерного рабочего оборудования а так же произвести тяговый и мощностной расчеты;
Определить экономическую эффективность от применения нового фрезерного оборудования.
спецификации.doc
СГАУ 22.01.00.000.СБ
СГАУ 22.02.00.000.СБ
Фрезерный рабочий орган
Трактор ОМТЗ-82.1 с фрезерным рабочим органом
СГАУ -22.02.00.000.СБ
СГАУ – 22.02.01.000. СБ
Обойма подшипниковая
Болт М6х20 ГОСТ 7798-92
Шайба 6 ГОСТ 6402-91
Болт М8х20 ГОСТ 7798-92
Шайба 8 ГОСТ 6402-91
Болт М10х31 ГОСТ 7798-92
Шайба 10 ГОСТ 6402-91
Болт М12х40 ГОСТ 7798-92
Шайба 12 ГОСТ 6402-91
Болт М17х40 ГОСТ 7798-92
Шайба 17 ГОСТ 6402-91
Гайка М17 ГОСТ5915-90
Болт М17х60 ГОСТ 7798-92
Болт М10х40 ГОСТ 7798-92
Болт М12х20 ГОСТ 7798-92
Шайба 22 ГОСТ 6402-91
Болт М22х30 ГОСТ 7798-92
Шпонка 10х7х28 ГОСТ23360-78
Болт М24х40 ГОСТ 7798-92
Шайба 24 ГОСТ 6402-91
Шпонка 12х7х28 ГОСТ23360-78
Подшипник радиальный №109
Манжета 45 ГОСТ 22925-75
Гайка М24 ГОСТ5915-90
Шплинт 4х90 ГОСТ 397-98
Гидромотор 210.12 ГОСТ23417-89
глава 5.doc
1. Правовые и организационные основы охраны труда
1.1. Анализ охраны труда на предприятии
Обеспечение здоровых и безопасных условий труда законом возложено на администрацию предприятий учреждений организаций и т.д. Добиваться этого администрация должна путем применения своевременных средств безопасности и обеспечения санитарно-гигиенических условий предотвращающих профессиональные заболевания. Для выполнения этих целей в организации предусмотрена должность специалиста по охране труда выполнение его обязанностей возложено приказом начальника предприятия на заведующего ремонтной мастерской [28].
Руководство и ответственность за правильную организацию инструктирования рабочих и служащих безопасным приемам труда и методам работы на оросительной сети возлагается на начальника сети и главного инженера а на эксплуатационных участках – на их руководителей.
На предприятии периодически проводят следующие виды инструктажей: вводный первичный повторный внеплановый текущий.
Вводный инструктаж обязаны пройти все вновь поступающие на работу рабочие и служащие. Его проводит главный инженер по технике безопасности. Вводный инструктаж обычно заканчивается ознакомлением с основными объектами предприятия. О результатах инструктирования производится запись в журнале вводного инструктажа а работнику выдается контрольный лист.
После прохождения вводного инструктажа по технике безопасности работники направляются на рабочие места имея на руках контрольный лист прохождения инструктажа по технике безопасности. Работники могут быть допущены к выполнению работ только после прохождения инструктажа на рабочем месте. Этот вид инструктажа проводится непосредственно на рабочем месте до начала смены с вновь принятым рабочим – первичным а также при переходе на другую работу с одного вида оборудования на другое. Первичный инструктаж проводит непосредственно руководитель работ.
Повторный инструктаж по технике безопасности проводится для всех рабочих не реже одного раза в три месяца. Цель повторного инструктажа – обеспечить лучшее усвоение рабочими правил безопасности ведения работ проверить их знание техники безопасности путем устного опроса.
Кроме первичного и повторного инструктажа на рабочем месте может проводиться внеплановый инструктаж рабочих безопасным приемам и методам труда. Его проводят работники в обязанности которых входит организация инструктажа на рабочем месте.
Текущий инструктаж проводится с работниками перед производством работ на которые оформляют наряд – допуск.
1.2 Опасные производственные факторы на предприятии. Травматизм и заболевания за 5 лет.
Показатель частоты травматизма Кч представляет собой отношение количества пострадавших n1 к среднесписочному числу работающих и служащих nр за учетный период отнесенное к тысяче работающих таблица 5.1.
Таблица 5.1. – Динамика производственного травматизма на предприятии.
Число несчастных случаев
Число дней нетрудоспособности
Коэффициент частоты Кч
Коэффициент тяжести Кт
Травмы со смертельным исходом Ксм
Кч = n1 nр 1000(5.4)
где n1 – число пострадавших с утратой трудоспособности и со смертельным исходом.
Кч = 3 893 1000 = 336
Показатель тяжести травматизма Кт характеризует среднюю длительность временной нетрудоспособности пострадавших:
где Dн – число человеко-дней нетрудоспособности у всех пострадавших за учетный период;
n2 – число пострадавших с утратой трудоспособности без учета погибших.
Показатель потерь рабочего времени Кн на 1000 работающих за определенный период времени (год) более полно характеризует состояние травматизма в хозяйстве. Он определяется по формуле:
Кп = Dн nр 1000(5.6)
Кп = 63 893 1000 = 7055.
Дополнительной характеристикой тяжести несчастных случаев является также показатель травм со смертельными исходами:
где С – число случаев со смертельными исходами за рассматриваемый промежуток времени.
Если снижен только показатель Кч это не означает что уровень травматизма понизился. Для этого необходимо чтобы снизился коэффициент Кт.
Поэтому применяют общий показатель травматизма:
Руководство предприятия ведет расследование и учет несчастных случаев на производстве. Это делается для установления причин несчастных случаев травмирующих факторов определение виновных разработки и осуществления мероприятий по предупреждению травматизма в дальнейшем.
1.3. Предлагаемые мероприятия по улучшению условий труда
Произвести перерасчет заземления гаража.
Разработать положения по технике безопасности при работе на дождевальных машинах.
Произвести расчет искусственного освещения гаража так как были выведены из строя несколько светильников.
Произвести расчет естественного освещения центральной мастерской.
Разработать мероприятия повышающие пожарную безопасность на предприятии.
Произвести расчет вентиляции в мастерской где производится ремонт топливной аппаратуры.
Произвести закупку ручного инструмента.
Произвести централизованную закупку средств индивидуальной защиты.
Вывесить план эвакуации на предприятии в случае пожара и ответственных за пожарную безопасность.
Вести журнал по технике безопасности.
2. Производственная санитария
2.1. Расчет искусственного освещения гаража
Производственное освещение – важнейший показатель гигиены труда. Освещение является главным фактором качества информации. Рационально устроенное освещение позволяет легко различать цвет и размеры объектов труда снижать утомленность повышает безопасность труда. Освещение может быть естественным и искусственным осуществляемое электрическими лампочками. Искусственное освещение может быть общим местным и комбинированным.
Произведем расчет искусственного освещения помещения гаража площадью 200 м2 высота подвеса светильников – 5 м. Гараж предназначен для стоянки автомобилей соответственно наличие местного освещения не обязательно. Расчет производится по методу удельной мощности [29 30].
Удельной мощностью называется отношение мощности осветительной установки к площади освещаемого помещения.
Мощность одной лампы Рл в этом случае рассчитывается по следующей формуле:
где Ру – удельная мощность осветительной установки Втм2;
Sп – площадь помещения м2;
Принимая число ламп равное десяти nл=10 определим значение удельной мощности Ру осветительной установки для светильника ОДС с лампой 40 Вт при коэффициенте запаса 15 и коэффициенте отражения потока dп=50 % и стен dст=30 % [30]. Необходимая освещенность Е=200 (ЛЮ). Для этих значений удельная мощность осветительной установки Ру=106 Втм2.
Подставляя полученные значения в формулу (5.1) определим мощность одной лампы
Определим расстояние между центрами светильников по формуле:
где hс – высота подвески светильника м.
Так как высота подвески светильников задана и равна hс=5 м тогда
Схема расположения светильников показана на рис. 5.1.
2.2. Расчет естественного освещения гаража
Источником естественного освещения служит лучистая солнечная энергия. Естественное освещение оказывает сильное тонизирующее действие на организм человека и имеет большое гигиеническое значение. Оно бывает боковым – когда свет небосвода проникает через световые проемы в наружных стенах; верхним – через световые фонари в крышах и проемы в местах перепадов высот пролетов зданий; комбинированным – через световые проемы для бокового и верхнего освещения.
Рисунок 5.1. Схема расположения светильников.
Для создания рационального освещения на рабочих поверхностях необходимо нормировать уровень освещенности. За показатель эффективности естественного освещения принят коэффициент естественной освещенности (КЕО) представляющий собой отношение естественной освещенности создаваемой в некоторой точке А внутри помещения светом неба(непосредственным ил после отражений) к одновременному значению наружной горизонтальной освещенности в точке В создаваемой светом полностью открытого небосвода; выражается в процентах.
Определим нормированное значение КЕО для нашего региона по формуле:
где е – значение КЕО по СниП 11-4 –70; при боковом освещении для работ малой точности е = 09
m – коэффициент светового климата (m = 09 – согласно световому климату Саратовской обл).
с – коэффициент солнечности климата с = 065 .1
ен = 09 09 09 = 073 .
где SН – площадь пола м2;
еН – нормативное значение КЕО;
о – световая характеристика окон;
о – общий коэффициент светопропускания оконного проема равный 015 06;
к – коэффициент учитывающий затемнение окон соседними зданиями равный 1-17;
r – коэффициент учитывающий отражение света от внутренних стен равный 1 – 10 (r = 4).
После этого выбираем оконные проемы размером 15 х 21 м в количестве 3 штук.
2.3. Расчет защитного заземления
Искусственными заземлителями могут служить трубы стержни уголковая и полосовая сталь. Верх заземлительного устройства должен быть ниже поверхности на 07 08 м [21].
Сопротивление резанию тока Rрт ОМ в заземлителе зависит от удельного сопротивления грунта и размеров заземлителя и определяется по формуле:
где Р = 100 Омм – удельное сопротивление грунта;
L =25 м – длина заземлителя;
d = 0035 м – ширина заземлителя;
h = 1 м – глубина забивки.
Количество заземлителей определяется по формуле:
где Кс = 15 – коэффициент сезонности;
эз = 062 – коэффициент экранирования заземлителей;
Rн – номинальное сопротивление заземления в грунтах при 100 Оммr500 омм (чернозем) равное 10 Ом;
Для соединения заземлителей принимаем полосовую сталь шириной 30 см и толщиной 35 мм.
Длину полоски определяем по формуле
Lп = 105 а п м(5.15)
где а – расстояние между трубами;
п – количество труб .
Lп = 105 20 21 = 441 см
Сопротивление растеканию тока соединительной полосы Rп Ом определим по формуле:
где В = 03 м – ширина полосы;
h = 08 м – глубина заложения полосы в грунт;
п = 03 – коэффициент экранирования полосы.
Результирующее сопротивление R Ом определяем по формуле
3. Техника безопасности
Безопасность труда – состояние условий труда при которых не исключено воздействие на рабочих опасных производственных факторов.
Правила для машиниста работающего на дорожной фрезе:
Машинист должен работать на машине в крепкой одежде и перчатках чтобы не зацепиться за движущиеся части машины рваными частями одежды или перчаток.
Заправлять машину горючим разрешается только при выключенном двигателе.
При снятии заливной пробки с радиатора горячего двигателя следует соблюдать осторожность; во избежание ожогов рук пробку снимают прикрыв ее плотной тряпкой. Доливать жидкость в радиатор следует при работающем на малых оборотах или остановленном двигателе. Если двигатель перегрет заливать жидкость в радиатор не разрешается.
Запускать двигатель машины без подключенного воздухоочистителя запрещается так как это приводит к повышенному износу двигателя.
Не следует запускать двигатель машины и давать ему работать в закрытых гаражах или сараях не снабженных системой вентиляции или вытяжкой во избежание отравления людей продуктами сгорания топлива.
Перед запуском двигателя следует установить в нейтральное (выключенное) положение все механизмы привода в том числе механизмы управления гидросистемами.
Машинист не должен оставлять без присмотра машину если ее двигатель работает.
Машинист никогда не должен включать любой из механизмов если его невозможно немедленно выключить так как в противном случае может создаться аварийная обстановка для машины или ее рабочего оборудования.
При движении вниз под уклон передачи трансмиссии базовой машины оставляют включенными.
Машинист должен вести машину на скорости достаточной для обеспечения безопасности движения.
При движении в темное время суток по дорогам в общем потоке транспорта обязательно включают осветительные приборы положенные по правилам движения.
Машинист не должен сходить с машины до ее полной остановки.
4. Пожарная безопасность
Пожарная безопасность (ГОСТ 12.1.033-81) – состояние объекта при котором с установленной вероятностью исключается возможность возникновения и развития пожара и воздействия на людей опасных факторов пожара а так же обеспечивается защита материальных ценностей.
Пожарная безопасность ремонтных мастерских обеспечивается соблюдением установленных правил пожарной безопасности. Контроль за выполнением этих правил осуществляется заведующим ремонтной мастерской.
Помещение должно удовлетворять СНиП и санитарным нормам проектирования предприятий.
В ремонтных мастерских должны быть средства тушения пожара доска боевого пожарного расчета и инструкция о мерах пожарной безопасности. Участки цеха склады сгруппированы по признакам пожарной безопасности. В ремонтных мастерских не допускается проведение технических обслуживаний техники с баками наполненными топливом.
Основную пожарную и взрывную опасность представляют цехи сварочных работ так как в них могут находиться ацетиленовые генераторы из которых возможна утечка газа.
Ацетиленовые генераторы устанавливают в отдельных одноэтажных помещениях без потолков с легкой несгораемой кровлей. Объем помещений для ацетиленовых генераторов производительностью 10 м3ч не менее 60 м3. Освещение аппаратной – только естественное через окно.
Для обеспечения пожарной безопасности заправочной станции необходимо ее территорию окапать с обволакиванием чтобы на случай пожара или аварии нефтепродукты не растекались. Всю территорию огораживают и озеленяют цистерны устанавливают на фундаментные опоры подсоединяют их к защитному заземлению от статического электричества. Так же заземлены все фильтры электродвигатели трубопроводы насосы бензоколонки.
Выводы: для обеспечения безопасности труда на предприятии были произведены анализ условий труда разработаны мероприятия связанные с безопасностью труда вопросы по производственной санитарии и гигиены труда вопросы по пожарной безопасности а так же произведены расчеты заземления.
содержание.doc
1. Хозяйственная деятельность дорожного комитета
Саратовской области 7
2. Причины возникновения ДТП связанные с дорожными условиями 15
2.1. Восприятие водителями дорожных условий и режимы движения
2.2. Эмоциональная напряженность водителей при движении по дороге 21
2.3. Пути предотвращения происшествии связанных с
дорожными условиями . ..23
3. Причины образования дефектов на дороге ..26
3.1. Воздействие породно-климатических и температурных
факторов на дорогу . 26
3.2. Причины появления дефектов .27
СПОСОБЫ РЕМОНТА ДОРОГ И ПРИМЕНЯЕМЫЕ МАШИНЫ .34
1. Технология ремонта и содержания дорог используемые машины ..34
2. Существующие конструкции дорожных фрез . 51
3. Предлагаемая конструкция дорожной фрезы . .57
КОНСТРУКТОРСКАЯ РАЗРАБОТКА . 61
1. Выбор и расчет основных параметров дорожной фрезы 61
2. Тяговый расчет дорожной фрезы .. 63
3. Мощностной расчет дорожной фрезы на базе трактора ОМТЗ-82.1 65
4. Расчет производительности машины 67
5. Статический расчет дорожной фрезы на базе трактора ОМТЗ-82.1 . 67
6. Расчет привода рабочего органа дорожной фрезы ..69
6.1. Расчет гидропривода фрезы . ..69
6.2. Расчет гидроуправления подъема рабочего оборудования 80
6.3. Расчет редуктора привода фрезерного рабочего органа 81
7. Расчет элементов конструкции фрезерного рабочего
оборудования на прочность ..91
8. Расчет технологического процесса изготовления пальца к
репления гидроцилиндра .96
ЭКОНОМИЧЕСКОЕ ОБОСНОВАНИЕ ПРОЕКТА . . 102
1. Расчет стоимости изготовления дорожной фрезы 102
2. Технико-экономические показатели дорожной фрезы 105
БЕЗОПАСНОСТЬ ЖИЗНЕДЕЯТЕЛЬНОСТИ 115
1. Правовые и организационные основы охраны труда .. .115
1.1. Анализ охраны труда на предприятии 115
1.2. Опасные производственные факторы на предприятии. Травматизм
и заболевания за 5 лет . ..116
1.3. Предлагаемые мероприятия по улучшению условий труда .. 118
2. Производственная санитария .. 118
2.1. Расчет искусственного освещения гаража .118
2.2. Расчет естественного освещения гаража . 120
2.3. Расчет защитного заземления 121
3. Техника безопасности .. 123
4. Пожарная безопасность .. .124
литература.doc
Бабков В.Ф. Дорожные условия и безопасность движения: учебник для вузов В.Ф. Бабков. – М.: Транспорт 1993. – 271с.
Технология устройства и ремонта асфальтобетонных покрытий: Учебн. пос. Ищенко И.С Калашникова Т.Н. Семенов Д.А. - М.: Аир-Арт 2001. - 176 с.
Справочник дорожного мастера под. ред.С.Г. Цупикова. – М.: Инфа-Инженерия 2005. – 928с.
Технология и организация строительства автомобильных дорог Под. ред. Н. В. Горелышева. - М.: Транспорт 1992. -550с.
Строительство автомобильных дорог. Т1 Под ред. В. К. Некрасова. -М.: Транспорт 1980. -415с.
Евгеньев И.П Казарновский В. Д. Земляное полотно автомобильных дорог на слабых грунтах. М.: Транспорт 1976.-270 с.
Баловнев В. И. Хмара Л. А. Интенсификация земляных работ в дорожном строительстве. М.: Транспорт 1983. - 181 с.
Львович Ю. М. Мотылев Ю. Л. Укрепление откосов земляного полотна автомобильных дорог. М.: Транспорт 1983. -181с.
Алоян P.M. Цупиков С. Г. Технология и организация строительства автомобильных дорог. Часть 1. Возведение земляного полотна. Иваново: ИГАСА 2003. - 350 с.
Бородачев И.П. Справочник конструктора дорожных машин. М.: Машиностроение. – 1973. - 505с.
Репко А.В. Клещенков В.Ф. Устройство для фрезерования дорожных покрытий и нарезки швов. Патент РФ. № 2055104 Кл. Е01 С 32082 Приоритет от 27.02.1996. Бюл. №6.
Ермилов А.Б. Бараташвили М.П. Устройство для фрезерования дорожных покрытий. АС СССР №1399389 Кл. Е01 С 2309. Опубликовано 30.05.88. Бюл. № 20.
Дубинин В.Ф. Демин Е.Е. Глухарев В.А. Павлов П.И. Гидропривод сельскохозяйственных погрузчиков и транспортных машин. саратовский ЦНТИ Саратов. – 2001. – 168с.
Расчет гидропривода строительных машин. Под ред. Локшина В.Ф. М.: Высшая школа. – 1982. – 226с.
Гузенков П.Г. Детали машин. М.: Высшая школа. 1989. – 350с.
Дунаев П.Ф. Конструирование узлов и деталей машин. Дунаев П.Ф. Леликов О.П. М.: Высшая школа. – 1985. - 160с.
Горбацевич А.Ф. Курсовое проектирование по технологии машиностроения. Минск: Вышэйшая школа. – 1975. – 288с.
Батеенков П.С. Методическое указание по проведению расчетно-практических занятий по теме: «Расчет экономической эффективности внедрения новой техники». Саратов. Саратовская гос. с.-х. академия. 1994. 17с.
Леонтьев И.П. Правовые и организационные вопросы охраны труда в гидромелиоративном производстве. Саратов. Саратовская гос. с.-х. академия. 1994. 99с.
Леонтьев И.П. Производственная санитария и гигиена труда в гидромелиоративном производстве. Саратов. Саратовская гос. с.-х. академия. 1993. 135с.
Шкрабак В.С. Леонтьев И.П. Шкрабак В.В. Пожарная безопасность в гидромелиоративном производстве. Саратов. Саратовская гос. с.-х. академия. 1994. 111с.
выводы.doc
Наиболее лучшая технология строительства и ремонта тела дороги производится с использованием дорожных фрез способных осуществлять перемешивания грунта в теле дороги со связующими материалами тем самым стабилизировать грунт от разрушения. При этом в области насчитывается высокий дефицит данных машин. Основываясь на патентной проработке существующих конструкций фрез была разработана новая конструкция дорожной фрезы.
Для доказательства работоспособности фрезы был представлен расчет ее основных параметров проведен тяговый и мощностной расчеты. Представлен статический расчет и определена производительность процесса фрезерования грунта с использованием нового рабочего оборудования. Представлен расчет привода фрезерного рабочего оборудования и элементов ее конструкции.
Применение гидропривода фрезы позволит повысить производительность труда на 533 % по сравнению с серийной фрезой МДФ-400Е. Это позволит получить годовой экономический эффект в размере 1299904 рубля при сроке окупаемости дополнительных капитальных вложений равный 143 года.
Для обеспечения безопасности труда на предприятии были произведены анализ условий труда разработаны мероприятия связанные с безопасностью труда вопросы по производственной санитарии и гигиены труда вопросы по пожарной безопасности а так же произведены расчеты заземления.
глава 2.doc
1. Технология ремонта и содержания дорог используемые машины
Автомобильная дорога представляет собой инженерное сооружение включающее земляное полотно; слой дорожной одежды; мосты трубы и туннели; обустройство и защитные дорожные сооружения (ограждения знаки озеленение и т.д.).
В зависимости от расчетной интенсивности и скорости движения дороги делятся на 5 категорий табл.2.1.
Таблица 2.1 – Категории дорог
Число полос движения
Ширина проезжей части м
Ширина земляного полотна м
Расчетная скорость движения кмч
Основными конструктивными элементами дороги являются: земляное полотно (от устойчивости которого зависит скор службы дороги) и дорожная одежда (от типа и конструкции которой зависят эксплуатационные характеристики и долговечность дороги).
Дорожная одежда – это многослойная конструкция проезжей части дороги передающая и уменьшающая нагрузки от движущегося по ней автомобильного транспорта на земляное полотно.
Дорожная одежда классифицируется: капитальная облегченная переходная и низшая.
Для каждого типа дорожной одежды должно быть свое покрытие и вид основания которые представлены в табл. 2.2.
Таблица 2.2 – Виды покрытий и оснований дорог
Основные виды покрытий
Основные виды оснований
Цементобетонные монолитные
Каменные материалы и грунты обработанные неорганическими вяжущими жидкостями
Железобетонные или армобетонные сборные
Песчаные песчано-гравийные
Асфальтобетонные из щебня гравия и песка обработанных вяжущими элементами
Все виды жестких и нежестких
Щебеночные и гравийные: из грунтов и местных малопрочных каменных материалов обработанных вяжущими материалами
Из грунтов укрепленных или улучшенных добавками
Песчаные щебень гравий
Основными работами при строительстве земляного полотна дороги являются возведение насыпей и разработка выемок. Кроме это производится строительство зданий и искусственных сооружений но их объем невелик.
Земляное полотно дороги прокладываемое в равнинной или холмистой местности при высоте насыпи от 0 до 15 метров возводится с использованием грунта забираемого из боковых резервов представляющих собой неглубокие выемки идущие вдоль дороги. При этом грунт перемещается поперек трассы дороги и используются бульдозеры автогрейдеры и грейдер-элеваторы.
Насыпь высотой более 15 м может сооружаться из боковых резервов или из ближайших выемок на трассе строящейся дороги. При этом используются скрепера одноковшовые экскаваторы автомобили бульдозеры и автогрейдеры.
Отсыпанный грунт в теле насыпи уплотняется с помощью катков а откосы с помощью трамбующих машин.
Укладка дорожного полотна осуществляется с помощью укладчиков.
Однако существует дорожное покрытие произведенное непосредственно в теле дороги. Это когда осуществляется перемешивание грунта с одновременным внесением вяжущих элементов при этом применяются специальные машины называемое грунтосмесителями или дорожными фрезами.
В связи с разной конструкцией дорог и оснований при ремонте используется различная технология и используемый комплект машин.
При ремонте дорог выделяют два основных вида: текущий и капитальный рис. 2.1. В зависимости от износа и деформации дороги выбирают различную технологию ремонта и типов машин.
Воздействие транспортных средств на проезжую часть вызывает напряжение и деформации в дорожных конструкциях и земляном полотне в результате чего возможны повреждения и разрушения. Этому способствует также неблагоприятное влияние природно-климатических факторов (переувлажнение замораживание и др.). При ремонте земляного полотна восстанавливают его деформированные и разрушенные элементы. При ремонте неукрепленных обочин профилируют и планируют их поверхность с приданием требуемого поперечного уклона (до 50-60%). Для подсыпки обычно используют супесчаный песчаный грунт или аналогичный тому из которого отсыпана насыпь. На укрепленных обочинах заделывают разрушения покрытий и нижних слоев укрепления. Эти работы целесообразно совмещать с ремонтом проезжай части. При размыве боковых канав ливневыми и талыми водами подмыве оснований и выемок их укрепляют сборными бетонными элементами или монолитным бетоном (рис. 2.2) стабилизацией грунта мощением дернованием и другими способами с учетом скорости течения и объема перемещаемой воды вида грунта.
Рисунок 2.1. Технология ремонта и содержания дорог в Саратовской области
Рисунок 2.2. Ремонт боковой канавы монолитным бетонированием
Стабилизация грунта осуществляется дорожными фрезами. Данный процесс прост в использовании и не требует больших капитальных вложений.
Для снижения расхода материалов на укрепление земляного полотна и повышения срока его службы в конструкции вводят прослойки из синтетических материалов тканого или нетканого типов. При сильном увлажнении насыпей грунтовыми водами на границе полосы отвода следует устраивать продольные дренажные прорези. В случае необходимости ремонтируют дренажные системы усиливая щебеночные фильтры и промывая заилившиеся участки с помощью гидромелиорационных машин. В отдельных случаях заменяют отдельные дрены ремонтируют колодцы заменяют фильтровальную обсыпку.
На пучинистых участках частично заменяют грунт инъецируют растворы закрепляющих материалов выполняют очистку дренажных устройств. Эти работы связаны с заменой участков дорожной одежды. Удалив покрытие и слои основания убирают слой пучинистого грунта который заменяют песчаным с послойным уплотнением. Сопряжение мест замены грунта на пучинистых участках с соседними неперестраиваемыми осуществляют в виде клина с крутизной откоса вдоль оси дороги 1:10. Такая мера позволяет предотвратить неравномерное морозное пучение в местах сопряжений. В местах ремонта устраивается более мощная дорожная одежда с использованием традиционных технологий. Для уменьшения толщины слоев дорожной одежды при перестройке земляного полотна создают прослойки из рулонных синтетических текстильных материалов. Полотна таких материалов укладывают с перекрытием на 8-12 см и соединяют с помощью специальной установки оснащенной газовой горелкой.
При ремонте земляное полотно может быть уширено как с одной так и с двух сторон. Двухстороннее уширение выполняется в случае когда не изменяется положение оси дороги. При этом с двух сторон досыпают откосы насыпей и срезают откосы выемок. В случае одностороннего уширения новая часть дорожной одежды располагается на свежеотсыпанном грунте которому надо придать высокую степень уплотнения и обеспечить связь с существующим земляным полотном. Для этого на существующем земляном полотне нарезают выступы (рис. 2.3) или укладывают синтетический рулонный материал таким образом чтобы он пересекал поверхность скольжения и заглублялся в существующее земляное полотно. При этом в целях повышения местной устойчивости прослойки синтетического материала укладывают с выводом на откос и объединением в обоймы.
Рисунок 2.3. Одностороннее уширение насыпи: 1 — ось новой дороги; 2 - ось существующей дороги.
На косогорах земляное полотно уширяется только с одной стороны.
Работы при ремонте земляного полотна выполняются с помощью экскаваторов планировщиков автогрейдеров дорожных фрез и специальных катков.
В процессе ремонта выполняют работы по строительству площадок для остановки и стоянок автомобилей площадок отдыха вне проезжей части. Производится переустройство транспортных развязок на новых пересечениях и примыканиях дорог устраивают съезды и систему водоотвода. Дня улучшения условий эксплуатации на отдельных участках изменяют план и продольный профиль дороги с доведением ее геометрических параметров до нормативных требований производят изменение радиусов вертикальных и горизонтальных кривых смягчение продольных уклонов устройство виражей. Из условий обеспечения снегонезаносимости изменяют высоту насыпей и крутизну откосов. С помощью растительности укрепляют разделительные полосы обочины склоны местности и откосы земляного полотна.
Откосы земляного полотна обычно укрепляют посевом трав причем его сочетают с укладкой синтетических материалов (рис. 2.4) предотвращающих вымывание семян и защищающих откос от эрозии на период формирования травяного покрова. В отдельных случаях на откосах укладывают бетонные сборные решетчатые конструкции ячейки которых заполняют каменным материалом или растительным грунтом с посевом трав.
Рисунок 2.4. Укладка синтетических материалов с одновременным посевом трав.
К основным видам текущего ремонта капитальных асфальто- и цементобетонных покрытий относят устранение повреждении в виде выбоин трещин колей обломов и неровностей кромок. До начала работ необходимо провести обследование состояния покрытия подлежащего ремонту оценить причину разрушения составить дефектную ведомость и смету. При ремонте соблюдают общую технологическую последовательность которая включает подготовку поврежденного места приготовление укладку и разравнивание смеси ее уплотнение (в случае необходимости).
Ямочный ремонт асфальтобетонных покрытий включает выполнение следующих операций:
- ограждение участка производства работ
- очистку покрытия от грязи льда и снега;
- определение зон разрушения покрытия разметку мест ремонта;
- нарезку контуров "карт";
- вырубку и очистку "карт";
- сушку "карты" (при необходимости)
- огрунтовку стенок и дна "карты";
- укладку и разравнивание ремонтного материала;
- уплотнение смеси и отделку мест сопряжения;
- уборку отходов вывоз асфальтобетонного лома; контроль качества ремонтных работ;
- снятие ограждений.
К выполнению ремонтных работ разрешается приступать только после полного обустройства участка временными дорожными знаками и ог раждениями.
Перед разметкой участков ремонта производят при необходимости очистку покрытия от пыли и грязи механическими щетками за 1-2 прохода по одному следу а при наличии льда и снега — скребками вручную. После очистки определяют зоны разрушения покрытия глубину разрушений и контуров будущих "карт". В одну "карту" включают все выбоины одинаковой глубины расположенные рядом (не далее 50 см одна от другой) с захватом окружающей их неповрежденной части покрытия шириной 3-5 см. Минимальная длина стороны "карты" — 20 см. Разметка контуров "карт" выполняется контрастным по отношению к покрытию материалами (краской или мелом) которые легко могут быть удалены с покрытия после завершения работ. Размеченные контуры "карт" должны представлять собой прямые линии параллельные и перпендикулярные к оси дороги. "Карты'' должны иметь форму квадрата или прямоугольника.
По размеченным линиям производится нарезка продольных и поперечных контуров "карт" с использованием нарезчика швов (рис. 2.5). Глубина нарезки контуров "карт" равна толщине поврежденного слоя.
Рисунок 2.5. Нарезчик швов
Перед началом нарезки контуров "карт" нарезчик подготавливается к работе к нему подсоединяются шланги подачи воды для охлаждения дисковой алмазной пилы. В состав работ по нарезке "карты" входит установка нарезчика на размеченную линию заглубление режущего круга нарезка шва подъем режущего круга повороты нарезчика и перемещение на следующую "карту". При необходимости производят замену режущего круга и заправку нарезчика.
Вырубку покрытия производят отбойным молотком на глубину повреждения но не менее толщины конструктивного слоя. Стенки подготовленных "карт" должны быть вертикальными а дно относительно ровным (выступы не должны превышать впадины более чем на 15 мм).
Дно и стенки "карты" а также прилегающую к ней поверхность дорожного покрытия на ширину 1-2 см подгрунтовывают битумом нагретым до температуры 90-100" С или битумной эмульсией. Разогрев битума производится в передвижном битумном котле оборудованном мешалкой. Нанесение битума на дно и стенки "карты" обычно производится кистью вручную подноска разогретого битума осуществляется ведрами по мере необходимости. Для подгрунтовки применяют битумы разжиженные до вязкости 110-140 град пенетрации (в качестве пластификаторов используют мазут гудрон экстракт селективной очистки масел экстракт фенольной очистки масел). Расход битума обычно составляет 04-06 лм2. При температуре воздуха ниже 5°С перед обработкой битумом производится нагрев стенок и дна "карты" терможалом.
После подгрунтовки производят укладку ремонтного материала. Если "карта" расположена у кромки дорожного покрытия то перед укладкой ремонтного материала в качестве опалубки устанавливают вдоль кромки упорный брус который в последующем удаляют после формирования уложенного материала.
Для ремонта асфальтобетонного покрытия используют материалы приготовленные на органических вяжущих.
Укладку складируемой органоминеральной смеси производят в сухую погоду при температуре воздуха от минус 15"С до 30°С. На месте производства работ вскрывают мешки с органоминеральной смесью которую укладывают в подготовленные "карты" с учетом коэффициента запаса на уплотнение 15-16 и равномерно распределяют по всей площади. При глубине "карты" более 50 мм укладка смеси производится в два слоя. При ремонте "карт" большого размера при низких температурах их последовательно разогревают.
Укладку горячей асфальтобетонной смеси производят в сухую погоду при температуре воздуха не ниже 5°С. Теплую асфальтобетонную смесь допускается применять и при пониженных температурах воздуха — до минус 10°С. Асфальтобетонную смесь укладывают в "карту" и распределяют аналогично органоминеральной смеси.
Температура горячих смесей при укладке должна быть не ниже 120°С теплых — не ниже 100°С. После укладки и разравнивания смеси утрамбовывают виброплитой. Уплотнение производят от краев "карты" к ее середине. Число проходов виброплиты по одному следу назначается из расчета одного прохода на 1 см глубины "карты".
Места сопряжения ремонтного материала со старым покрытием выравнивают и заглаживают. Для герметизации мест сопряжения ремонтного материала с дорожным покрытием рекомендуется наносить по контуру "карты" поверх уплотненного слоя ремонтного материала разогретый битум на ширину 8-10 см.
По окончании работ производят визуальный контроль качества ремонта проверяют ровность отремонтированного покрытия трехмерной рейкой ликвидируют следы временной разметки убирают и вывозят асфальтобетонный лом снимают ограждение и дорожные знаки.
Достаточно эффективным методом для предупреждения отраженного трещинообраэования является применение геотекстильных материалов в сочетании с георешетками (рис. 2.6). При устройстве трещинопрерывающих прослоек геотекстильный материал наклеивают на битумную под-грунтовку после чего укладывают выравнивающий слой а затем георешетку под покрытие. Зарубежный опыт применил указанных мер показывает что трещинообразование уменьшается в среднем в 3 раза а затраты на ремонт возрастают в 15-20 раза.
Рисунок 2.6. Варианты усиления конструкции дорожных одежд с армированием в зонах трещин: 1 -трещиноватое старое покрытие; 2 — гетекстильный материал; 34- слои усиления; 5 — георешетки.
Однако необходимо сказать о том что использование трещинопреры-вающих прослоек влечет за собой и некоторые проблемы. Отсутствие специальной техники для выполнения этих работ приводит к увеличению трудозатрат кроме того в нашей стране не существует нормативной базы регламентирующей применение подобных материалов для ремонта дорожных одежд.
Эффективным методом прерывания отраженных трещин является использование мембранной технологии включающей устройство битумопо-лимерной прослойки между старым и новым слоем. Эта эластичная биту-мополимерная мембрана воспринимает деформации нижележащих блоков не передавая значимых растягивающих усилий в слой нового покрытия.
Устройство тонких защитных слоев с использованием мембранных технологий находится на начальной стадии внедрения. Постоянный мониторинг за состоянием таких покрытий позволяет судить о перспективности данного метода. Однако отсутствие развитой производственной базы для получения полимербитумных вяжущих является определенным препятствием для широкого внедрения данного способа ремонта дорог.
При восстановлении дорожных одежд наиболее рентабельными оказываются методы связанные с максимальным использованием материалов старого покрытия и основания. Технологию восстановления (регенерации) применяют обычно в условиях снижения прочности дорожной одежды ниже установленных требований при растрескивании и недопустимом деформировании покрытий. Регенерация дорожных одежд обычно выполняется на дорогах имеющих покрытия на органических вяжущих. Она может выполняться по холодной и горячей технологиям.
Регенерация асфальтобетонных покрытий по горячей технологии осуществляется по технологиям ремикс и ремикс плюс. Для этого используются специальные машины представляющие собой самоходные агрегаты рис. 2.7 имеющие блок горелок для разогрева покрытия. Горелки собраны на панели и расположены на небольшом расстоянии друг за другом. Первая панель 1 блока горелок расположена по бокам бункера 3; вторая — за ним на всю ширину обрабатываемой полосы; третья — перед рыхлителем 7; четвертая — по бокам мешалки 8. Работу блока горелок обеспечивает газовое оборудование. Оно состоит из двух емкостей для хранения газа 2 испарителя и коммуникаций подающих газ от емкости к блокам 1. Обычно общая тепловая нагрузка блока составляет 7..11 Джч.
Рисунок 2.7. Схема работы по методу ремикс. 1 - панели блока горелок; 2 - емкости для хранения газа; 3—приемный бункер; 4 - транспортер; 5 - промежуточный бункер; 6 —обогреваемый транспортер; 7 - рыхлитель; 8 - мешалка; 9 — распределительный шпек; 10 - трамбующий брус с виброплитой; 11 —емкость для битума; 12— топливный бак; 13 — двигатель; 14 — место водителя
В головной части ремиксера находится приемный бункер 3 для новой асфальтобетонной смеси. Новая смесь по транспортеру 4 поступает в промежуточный бункер из которого подается на обогреваемый транспортер 6. В средней части машины находится рыхлитель 7 имеющий несколько рядов зубьев и состоящий из секций которые можно поднимать и опускать автономно что позволяет обходить препятствия на покрытии дороги (люки смотровых колодцев "островки безопасности" и др.). За рыхлителем 7 расположен шнек 9 состоящий из двух частей которые перемещают разрыхленный асфальтобетон к краям ремонтируемой полосы. Каждая часть шнека имеет автономное управление вследствие чего они могут вращаться в одну или разные стороны независимо друг от друга. Позади рыхлителя 7 находится отвал выравнивающий поверхность нижележащего слоя покрытия. На отвале закреплена мешалка 8 в которой осуществляется перемешивание разрыхленного старого асфальтобетона с новой асфальтобетонной смесью при использовании технологии ремикс и перемешивание старого разрыхленного асфальтобетона с добавляемыми компонентами (щебнем или битумом) при использовании технологии ремикс плюс. Уплотнение смеси осуществляется трамбующим брусом с виброплитой 10.
При использовании технологии ремикс плюс за мешалкой 8 устанавливаются дополнительный распрямительный шнек 5 и дополнительный брус 11 выравнивающий скорректированную смесь (рис. 8.3). Для введения в старую смесь битума на ремиксере имеется емкость для битума с дозатором и распределитель 12 распыляющий битум над рыхлителем 7.
Технология ремикс включает технологические операции по введению новой асфальтобетонной смеси или ее отдельных компонентов и перемешивание их со старой смесью а технология ремикс плюс предусматривает кроме того укладку защитного слоя из нового асфальтобетона и одновременное уплотнение слоев.
Ремонт покрытия по технологии ремикс производится в следующем порядке:
— предварительный разогрев покрытия дополнительными асфальто-разогревателями;
— разогрев покрытия ремиксером;
— заполнение приемного бункера ремиксера новой асфальтобетонной смесью;
— рыхление разогретого покрытия;
— подача новой асфальтобетонной смеси по обогреваемому транспортеру в промежуток между мешалкой и распределительным шнеком для образования валика перед трамбующим брусом;
— перемещение разогретой разрыхленной старой смеси шнеком к центру отвала и подача ее в мешалку;
— прием новой смеси в бункер и подача ее по обогреваемому транспортеру в мешалку;
— перемешивание новой и старой смеси в мешалке;
— распределение полученной смеси распределительным шнеком;
— выглаживание и предварительное уплотнение перемешанной смеси трамбующим брусом и вибрационной выглаживающей плитой;
— окончательное уплотнение покрытия пневмокатком и вибрационными катками.
Однако данная технология дорога и требует наличие специальных машин и оборудования. В связи с этим она не нашла широкого распространения в Саратовской области.
Тем более необходимо отметить скудность парка машин осуществляющих содержание и ремонт в Саратовской области. О наличии и готовности техники занятой на зимнем содержании дорог общего пользования Саратовской области по состоянию на 01.02.09г. показаны на рисунке 2.8.
Общие данные по количеству техники обслуживающие в зимнее время 842 единицы к готовности представлено 741 это 88%. КДМ – 94%; автогрейдеры – 87%; прицепные грейдеры – 90%; роторные снегоочистители – 81%; экскаваторы погрузчики – 88%; колесные тракторы со снегоочистителями – 91%; Камаз с отвалом – 85%.
Рисунок 2.8. Количество дорожных машин по Саратовской области по состоянию на 1.01.09г.
Наличие и готовность техники для летнего содержания территориальных дорог.
Косилки – 42%; фрезы – 13%; компрессоры – 38%; тракторы – 80%; кусторезы – 24%.
Информация о приобретенной техники в 2006-2008 году на 9835 километров дороги рис. 2.9.
Несмотря на то что за последний год было приобретено большое количество техники необходимой для ремонта дорожного покрытия все же ее не хватает. При этом количество выделяемых средств из бюджета на ремонтно-восстановительные работы снижается. В результате необходимо повысить производительность машин что позволит выполнить все намеченные работы в срок.
Так же необходимо отметить что предприятия Саратовской области нуждаются в поступлении новой техники рис. 2.10.
Рисунок 2.9. Виды приобретенного оборудования и техники в 2006-2008г.г.
Рисунок 2.10. Потребность предприятий Саратовской области в новой технике.
Как видно из вышеизложенного наибольшая потребность в приобретении новой техники зафиксирована у фрез. При этом данные машины используются при ремонте дорог по технологии которая имеет малую стоимость и высокую надежность так как связана с укреплением тела дороги. Так же данные машины используются при строительстве новых дорог.
2. Существующие конструкции дорожных фрез
Дорожными фрезами называются однороторные передвижные машины осуществляющие измельчение грунта и перемешивание его с вяжущими материалами за несколько проходов по одному следу.
По компоновке в зависимости от вида базового шасси расположения и характера привода рабочего органа наличия и особенностей тяговых машин фрезы подразделяют на пять групп (рис. 2.11).
Рисунок 2.11. Схемы компоновок дорожных фрез:
а - навесные фрезы на базе серийных колесных и гусеничных тракторов (колесных автомобилей) с консольным расположением рабочего органа; б - самоходные фрезы с рабочим органом расположенным на базе машины; в и г — прицепные фрезы соответственно с автономным приводом ротора и с приводом ротора от вала отбора мощности трактора; д - полуприцепные машины на базе одноосных тягачей
Основными показателями дорожной фрезы являются мощность глубина и ширина обработки рабочие скорости.
Известна землеройно-фрезерная машина (рис. 2.12) предназначеная для послойного рыхления мерзлых грунтов и твердых пород.
Рисунок 2.12 Землеройно-фрезерная машина для послойной разработки мерзлого грунта:
— бульдозер; 2 — рама неподвижная; 3 — гидроцилиндр для подъема и опускания рабочего органа; 4—коробка отбора мощности; 5 — карданный вал; 6 — редуктор дифференциальный; 7 — муфта предельного момента; 8 — редуктор бортовой левый; 9 — фреза; 10 — рама подвижная.
Фрезерное рабочее оборудование расположено сзади трактора. На подвижной раме 10 смонтирована фреза 9 два боковых редуктора 8 и дифференциальный редуктор 6 с муфтой предельного момента 7. Поднимается и опускается подвижная рама с фрезой гидроцилиндрами 3 подвешенными на неподвижной раме 2 которая закреплена на опорах прицепной скобы трактора.
При поступательном движении машины фреза вращается разрыхляя грунт на заданную глубину. Привод фреза получает от коробки отбора мощности 4 через карданный вал и дифференциальный редуктор.
Бульдозерное оборудование используют для перемещения разрыхленного грунта.
Недостатком конструкции данной машины является большая материалоемкость сложность в управлении.
Известна фреза (рис. 2.13) представляющая собой горизонтально расположенный вал на котором равномерно укреплены кронштейны с установленными в их пазах ножами. Рeжущая часть их покрыта наплавкой из твердого сплава.
Рисунок 2.13. Фреза для разработки мерзлых грунтов:
— трактор; 2 —привод рабочего органа; 3 — редуктор отбора мощности; 4 — гидроцилиндр подъема и опускания рабочего органа; 5 — тяга; 6 — цепная передача; 7—балка; 8 — рабочий орган; 9 — бортовые редукторы; 10 — рама; 11 — предохранительная муфта; 12 — гидропривод ходоуменьшителя; 13 — противовес.
Грунт разрыхляется вращающимся ротором-фрезой 5 при поступательном движении машины.
Привод ротор-фреза 8 получает от вала отбора мощности трактора 2 через редуктор 3 установленный на заднем мосту трактора 1 бортовые редукторы 9 и цепные передачи 6.
Рама подвески 10 рабочего органа 8 и бортовые редукторы 9 образуют четырехзвенный параллелограмный механизм обеспечивающий подъем и опускание рабочего органа параллельно самому себе.
Фрезерные машины работают попеременно: сначала рыхлят грунт на заданную глубину ротором-фрезой затем с помощью бульдозерного отвала разрыхленный грунт убирают с полосы разработки и производят следующий проход.
Недостатком данной конструкции является низкая надежность.
Известна конструкция фрезерного рабочего оборудования которое состоит (рис. 2.14) из рамы 1 навешиваемой на трактор МТЗ-80 МТЗ-82 поворотного кронштейна 2 шарнирно установленного на раме 1 рабочего органа 3 (дисковой или цилиндрической фрезы) установленного на рабочий вал 4 механизма ограничения заглубления 5 смонтированного на поворотном кронштейне 2 и гидроцилиндра 6 перевода устройства из транспортного положения в рабочее и обратно.
Рисунок 2.14. Схема фрезерного рабочего оборудования: 1 – рама; 2 – кронштейн; 3 – рабочий орган; 4 – вал; 5 – механизм ограничения заглубления; 6 – гидроцилиндр.
Устройство работает следующим образом.
Гидростанция (гидропривод) навешиваемая на вал отбора мощности трактора приводит во вращение гидромоторы расположенные на поворотном кронштейне 2. Гидромоторы передают вращение на рабочий вал 4 посредством цепной передачи. Поворотный кронштейн 2 с вращающимся рабочим органом 3 опускается в рабочее положение. Разрушая покрытие рабочий орган 3 заглубляется на величину заданную механизмом ограничения заглубления. После перевода гидроцилиндра в нейтральное положение трактор начинает поступательное движение. Возникающая при движении вперед сила F2 прижимает поворотный кронштейн 2 с рабочим органом 3 к обрабатываемой поверхности при этом производится нарезка швов или плоское фрезерование. При плоском фрезерозании происходит планировка обрабатываемой поверхности. Для прекращения работы устройства действия совершаются в обратном порядке. Помимо гидропередачи вращения от вала отбора мощности базовой машины может быть применена и механическая передача. В этом случае рама 1 навешивается сзади базовой машины и рабочий вал получает вращение при помощи цепной передачи непосредственно от вала отбора мощности через конический редуктор. Ось выходного вала конического редуктора должна совпадать с осью шарнира вокруг которой совершает вращение поворотный кронштейн для сохранения межосевого расстояния цепной передачи неизменной. Могут быть и другие варианты механической передачи. При использовании механической передачи базовая машина должна быть снабжена реверсивным управлением.
Недостатком данной конструкции является сложность контролирования процесса фрезерования.
Известна конструкция фрезы содержащая рис. 2.15 базовый тягач 1 на колесном ходу 2 с бульдозерным оборудованием 3.
На плите 4 ведущего моста 5 тягача 1 размещен редуктор и шарнирно закреплен многозвенный механизм навески 7.
Редуктор 6 выполнен с механизмами 8 отбора мощности приводов насоса хода и сообщен с приводом 9 фрезерного рабочего органа 10 и гидроцилиндров 11.
Механизм навески 7 состоит из тяг 12 рамы 13 и поперечной балки 14.
Рисунок 2.15. Общий вид фрезерного рабочего оборудования.
К плите 4 ведущего моста 5 крепятся кронштейны 15 посредством шпилек 16 и гаек 17. Тяги 12 соединяются с кронштейнами 15 и балкой 14 посредством пальцев 18 и 19. Рама 13 соединяется с кронштейнами 15 и с приводом 9 при помощи пальцев 20 и 21. Гидроцилиндры 11 установлены на пальцах 19 и 20.
Кронштейны 15 выполнены в виде двух параллельных 22 и перпендикулярной им пластины. Пластины 22 выполнены с попарно соосными отверстиями 23. Многозвенный механизм навески 7 крепится в отверстиях 23 таким образом что по крайней мере одна пара из них смонтирована между плоскостью плиты 4 ведущего моста 5 и поверхностью огибающей гусеницы 2 тягача 1. Редуктор 6 размещается между кронштейнами 15.
Недостатком данной конструкции является низкая надежность трудность в монтаже и эксплуатации рабочего оборудования.
Проанализировав недостатки всех вышеперечисленных технических решений возникает вопрос о создании нового рабочего фрезерного оборудования который имел бы высокую надежность низкую стоимость простоту конструкции удобство монтажа и демонтажа а так же возможностью работы в дорожном строительстве.
3. Предлагаемая конструкция дорожной фрезы
Предлагаемая конструкция дорожной фрезы рис. 2.16 состоит из ротора 1 шарнирно подсоединен через коленчатый рычаг 2 оканчивающийся опорой 3 ротора и корпус трансмиссии 4 к тягачу 5.
Ротор 1 показанный в рабочем положении закрыт «плавающим» корпусом 6 который опирается лыжами 7 на спланированную поверхность грунта. На боковой стенке «плавающего» корпуса 6 установлен следящий золотник 8 со штоком 9 контактирующим с основной частью 10 составного рычага шарнирно прикрепленной в точке А к «плавающему» корпусу. Концевая часть 11 составного рычага может передвигаться по вертикальной стойке основной части 10 составного рычага и фиксироваться на ней. Концевая часть 11 составного рычага контактируется с опорой 3 ротора.
Рисунок 2.16. Схема предлагаемой конструкции дорожной фрезы
Основная линия гидросистемы рис. 2.17 состоит из золотника 12 трубопроводов 13 и 14 силового цилиндра 15 с замком 16. Следящий золотник 8 подсоединен к замку 16 трубопроводами 17 и 18. В гидравлическую систему входят также золотник 19 делитель потока 20 трубопроводы 21—24 гидронасос 25 и бак 26.
Рисунок 2.17. Гидравлическая схема дорожной фрезы
Для быстрого подъема или опускания ротора дорожной фрезы пользуются золотником 12 при этом золотник 19 находится в положении «Нейтрально» и следящий золотник 8 не оказывает влияния на работу силового цилиндра 15.
Работа устройства осуществляется следующим образом.
Когда ротор 1 дорожной фрезы находится в нерабочем положении т. е. приподнят над грунтом устанавливают концевую часть 11 составного рычага по заранее тарированной шкале вертикальной стойки основной части 10 составного рычага в положение соответствующее заданной глубине обработки грунта и закрепляют ее например стопорными болтами. Концевая часть 11 составного рычага не контактирует с опорой 3 ротора 1. Золотник 12 ставят в положение «Нейтрально» а золотник 19 в положение обеспечивающее движение рабочей жидкости по трубопроводу 21 в делитель потока 20 а затем необходимое ее количество по трубопроводу 22 — в следящий золотник 8. Остальная жидкость по трубопроводу 23 через золотник 19 идет на слив в бак 26. На подпружиненный шток 9 действует только вес частей 10 и 11 составного рычага и он пропустит жидкость через трубопровод 17 в правую часть замка 16 и штоковую полость силового цилиндра 15. Ротор начинает опускаться врезается в грунт а «плавающий» корпус лыжами 7 станет на спланированную поверхность грунта. Ротор опускается до тех пор пока опора 3 не войдет в контакт с концевой частью 11 составного рычага а основная часть 10 составного рычага не надавит на подпружиненный шток 9 следящего золотника 8. Следящий золотник 8 займет положение «Нейтрально» прекратится поступление жидкости в силовой цилиндр 15 и опускание ротора 1.
При работе дорожной фрезы когда например задняя часть движителя тягача 5 окажется на возвышении опора 3 ротора 1 отойдет вверх от концевой части 11 составного рычага возвращение ротора 1 в заданное положение произойдет как описано выше.
Если задняя часть движителя тягача окажется во впадине то опора 3 ротора 1 через концевую часть 11 составного рычага основной частью 10 составного рычага опустит подпружиненный шток 9 в положение обеспечивающее движение рабочей жидкости по трубопроводу 18 через левую часть замка 16 в поршневую полость силового цилиндра 15 а из штоковой через правую часть замка 16 трубопровод 17 следящий золотник 8 трубопровод 24 и золотник 19 — на слив в бак.
Начинается подъем ротора 1 который продолжается до тех пор пока подпружиненный шток 9 не станет в положение «Нейтрально» тем самым перекроет обе полости силового цилиндра 15. Подъем ротора 1 дорожной фрезы прекратится а глубина обрабатываемого слоя грунта будет соответствовать заданной.
Зная конструкцию дорожной фрезы необходимо провести расчеты с целью доказательства ее работоспособности.
В данном разделе рассмотрена технология ремонта и содержания дорог а так же используемая техника. На основании проведенного анализа было выявлено что наиболее лучшая технология строительства и ремонта тела дороги производится с использованием дорожных фрез способных осуществлять перемешивания грунта в теле дороги со связующими материалами тем самым стабилизировать грунт от разрушения.
Анализ парка машин показал значительный дефицит дорожных фрез вследствии этого необходимо осуществлять модернизацию имеющихся фрез с целью повышения производительности.
Основываясь на патентной проработке существующих конструкций фрез опираясь на их недостатки была разработана новая конструкция дорожной фрезы.
глава 3.doc
1. Выбор и расчет основных параметров дорожной фрезы
Так как базовой машиной дорожной фрезы является трактор ОМТЗ-82.1 представим его техническую характеристику [10]:
Номинальная мощность кВт59
Колея (расстояние между серединами колес) мм1430
Дорожный просвет с непогруженными грунтозацепами мм820
Габаритные размеры мм:
Максимальная скорость кмч40
Масса трактора кг3300
Основные параметры дорожной фрезы на тракторе ОМТЗ-82.1 будем определять по методике [11].
Диаметр фрезы определяют по следующей формуле
где h – глубина фрезерования м.
Ширина ротора фрезы определяется по следующей формуле
где В – ширина обрабатываемой полосы дороги м;
К – количество полос обработки;
Db – перекрытие полос м.
Рабочая скорость перемещения машины равна uр=05 мс.
Частота вращения ротора определяется по формуле
где uрез – скорость резания 8-14 мс;
D – диаметр ротора м.
Для осуществления измельчения грунта толщина стружки срезаемой каждой лопаткой должна быть в пределах 02-05 см. Меньшее значение толщины стружки относятся к резанию связных грунтов.
Минимальная рабочая поступательная скорость фрезы определяется по формуле
где s – толщина стружки см;
n – частота вращения ротора обмин;
z’ – число лопастей в сечении ротора.
На легких грунтах поступательная скорость фрезы может быть повышена за счет увеличения толщины стружки.
Крутящий момент на валу ротора определим по формуле
где Nдв – мощность двигателя фрезы кВт;
Основным элементом фрезы от надежности которого зависит ее работоспособность является рабочий орган с приводом. Расчет элементов ротора и его трансмиссии производятся на максимальный крутящий момент на оси ротора с учетом динамических перегрузок (до значений воспринимаемых предохранительными элементами)
где к1 – коэффициент динамичности к1=152.
Окружное усилие по которому рассчитывают усилия в лопатках и других элементах ротора определяем по формуле
где D – диаметр ротора м.
Далее произведем тяговый расчет дорожной фрезы.
2. Тяговый расчет дорожной фрезы
Для определения максимального тягового усилия которое необходимо развить базовой машине запишем уравнение тягового баланса
где Fп – сила затрачиваемая на перемещение машины кН;
Fф – сила затрачиваемая на перемещение рабочего органа кН.
Сила затрачиваемая на перемещение базовой машины определяется по формуле
где f – коэффициент сопротивления перемещению;
Gт – вес базовой машины кН.
Сила затрачиваемая на перемещение рабочего органа определяется по формуле
где Fх и Fz – соответственно горизонтальная и вертикальная составляющая силы затрачиваемой на перемещение рабочего органа кН.
Горизонтальная и вертикальная составляющие силы перемещения рабочего органа определяются по формулам
Fx=Fрезcosj+Rsinj(3.11)
Fz=Fрезsinj-Rcosj(3.12)
где Fрез – сила затрачиваемая на резание грунта кН;
j - угол наклона результирующей Fп j=43о;
R – сила трения на рабочем органе кН.
Сила затрачиваемая на резания грунта определяется по формуле
Fрез=Судh(kвb+mks)(1+0256lgup)kaz(3.13)
где Суд – число ударов ударника ДорНИИ;
h – глубина фрезерования м;
kв – удельный коэффициент трудоемкости резания грунта kв=5 Нсм2;
m – число закрытых боковых срезов m=2;
ks – удельный коэффициент среза грунта боковыми сторонами ножа ks=15 Нсм;
uр – рабочая скорость мс;
kа – коэффициент учитывающий влияние угла резания kа=09;
Fрез=50.02(5×19+2.15)(1+0256lg027)09.21=8510 Н или 851 кН
Сила трения на рабочем органе определяется по формуле
где f1 – коэффициент трения грунта по металлу.
Подставив соответствующие значения в формулы (3.11) и (3.12) получим
Fx=851cos43+426sin43=912 кН
Fz=851sin43-426cos43=268 кН
Подставив значения в зависимость (3.10) получим результирующую силу на рабочем органе
Подставив полученные значения в уравнение тягового баланса машины получим тяговое усилие необходимое для работы дорожной фрезы тогда
Проверим работоспособность фрезы по номинальному тяговому усилию тогда должно удовлетворяться условие
где Т – номинальное тяговое усилие трактора кН.
Как видно из данного условия базовая машина в виде трактора ОМТЗ-82.1 вполне проходит по тяговому усилию. В связи с тем что на привод фрезы тратиться около 95 % всех усилий затрачиваемых на перемещение и привод рабочего оборудования необходимо провести мощностной расчет.
3. Мощностной расчет дорожной фрезы на базе трактора ОМТЗ-82.1
Суммарная мощность которую должна развивать базовая машина складывается из суммы мощностей
N=Nр+Nот+Nп+Nпф+Nт(3.16)
где Nр – мощность затрачиваемая на резание грунта кВт;
Nот – мощность затрачиваемая на отбрасывание грунта кВт;
Nп – мощность затрачиваемая на перемещение фрезы кВт;
Nпф - мощность затрачиваемая на подталкивание фрезы кВт;
Nт – мощность затрачиваемая на трение в передачах кВт.
Мощность затрачиваемая на резание грунта определяется по следующей формуле
где g - удельное сопротивление резанию грунта кНм2;
b – ширина лопатки м;
s – толщина стружки м;
h – глубина обработки м;
z – количество ножей на роторе;
n – частота вращения ротора обмин.
Мощность затрачиваемая на отбрасывание разрыхленного грунта определяется по формуле
где k – коэффициент k=075;
В – ширина захвата м;
uп – поступательная скорость фрезы мс;
uокр – окружная скорость фрезы мс.
Мощность затрачиваемая на перемещение фрезы определяется по следующей формуле
где f – коэффициент сопротивления передвижению;
Nп=01×35×981.027=093 кВт
Мощность затрачиваемая на подталкивание фрезы определяется по формуле
Мощность затрачиваемая на преодоление трения в передачах определяется по формуле
Nт=(Nр+Nот)(1-h)(3.21)
где h - КПД передачи.
Nт=(962+046)(1-085)=15 кВт
Подставив получившиеся значения в уравнение мощностного баланса получим мощность двигателя необходимую для работы дорожной фрезы
N=962+046+093+034+15=1285 кВт
Так как мощность двигателя трактора ОМТЗ-82.1 равна 59 кВт то разработанная дорожная фреза на базе данного трактора вполне работоспособна что подтверждают тяговый и мощностной расчеты.
4. Расчет производительности машины
Техническую производительность дорожной фрезы определим по следующей зависимости
где uр – рабочая скорость машины мс;
b – ширина захвата рабочего органа м;
h – глубина рыхления м.
Пт=3600.027×19×02=3694 м3ч.
В связи с тем что дорожная фреза навешивается на трактор сзади то необходимо произвести расчет на устойчивость данной машины.
5. Статический расчет дорожной фрезы на базе трактора ОМТЗ-82.1
Статический расчет произведем в рабочем положении для этого рассмотрим схему сил действующую на дорожную фрезу рис. 3.1.
Рисунок 3.1. Схема сил действующих на дорожную фрезу
Так как дорожная фреза навешивается сзади трактора то в процессе работы может произойти опрокидывание трактора относительно точки О (рис. 3.1). Устойчивость трактора будет определяться коэффициентом устойчивости равным отношению удерживающего и опрокидывающего моментов тогда
где Муд и Мопр – соответственно удерживающий и опрокидывающий моменты Н.м.
Для определения данных моментов составим уравнения моментов относительно точки О тогда опрокидывающий момент будет определяться по формуле
Мопр=Gноl2+Fнl3(3.24)
где Gно – вес навесного оборудования кН;
Fн – горизонтальная составляющая результирующей силы на рабочем органа кН;
l3 – расстояние от силы Fн до точки опрокидывания м.
Мопр=043×16+1293×02=328 кН
Удерживающий момент определим по формуле
где Gт – вес трактора кН;
l1 – расстояние от точки приложения веса трактора до токи где произойдет опрокидывание м.
Тогда коэффициент устойчивости равен
Как видно из данного выражения коэффициент устойчивости равный Куст=14 выше нормативного показателя равного Куст=105 характеризуют хорошую устойчивость трактора.
Далее произведем расчет некоторых элементов конструкции дорожной фрезы на базе трактора ОМТЗ-82.1.
6. Расчет привода рабочего органа дорожной фрезы
6.1. Расчет гидропривода фрезы
Из мощностного расчета было определено что мощность затрачиваемая на привод рабочего органа составляет 1285 кВт окружная скорость фрезы равна 8 мс или 382 обмин. Зная данные величины необходимо подобрать передаточное число редуктора для нормальной работы фрезерного рабочего оборудования. Это необходимо для выбора гидромотора.
Передаточное отношение редуктора
где wг – частота вращения вала гидромотора с-1.
w - частота вращения фрезы с-1.
В качестве предварительного гидромотора осуществляющего привод фрезы выберем аксиально-поршневой гидромотор 210.16. Для него характерны номинальная частота вращения wг=40с-1 [14] тогда
В связи с тем что мощность на приводном валу фрезы составляет Nщ=1285 кВт а номинальная мощность выдаваемая гидромотором рана 130 кВт то с учетом передаточного отношения редуктора данный гидромотор нас вполне устраивает.
Далее произведем расчет основных параметров гидроситемы привода фрезы.
Рабочий крутящий момент на входном валу гидромотора:
где NГМ = – мощность развиваемая гидромотором 210.16
nГМ – частота вращения вала гидромотора nГМ = 1920 обмин.
Крутящий момент на валу фрезы:
где – мощность потребляемая щеточным рабочим органом;
nЗ – частота вращения вала фрезы;
nЗ = nГМ iр = 19204=480 обмин.
Крутящий момент передаваемый шестерней Z33 (на привод фрезерного рабочего органа)
Т33 = ТГМ – ТЗ(3.29)
Т33 = 2607-659 = 1948 Нм.
Коэффициент возможной перегрузки:
где рП – давление в гидросистеме по предохранительному клапану рП=32МПа;
рРАБ – рабочее давление в гидросистеме рРАБ = 16 МПа.
Для обеспечения беспрерывной подачи рабочей жидкости необходимо произвести расчет подачи насоса и гидродвигателя. Расчет проведем согласно предложенной методике [14 15].
При объемном способе регулирования стараются максимально использовать приводную мощность двигателя N которая подбирается с учетом максимальной мощности развиваемой насосом и общего к п. д. гидропривода.
Мощность развиваемая насосом без учета его к. п. д. вычисляется по формуле
N1=p1Q1=p1n1q1=N(3.31)
Соответственно мощность потребляемая гидромотором без учета его к. п. д. равна:
N2=p2Q2=p2n2q2=N(3.32)
где N—мощность приводного двигателя;
р— давление в системе;
Здесь и в дальнейшем индексом 1 обозначаются параметры насоса a индексом 2 — гидромотора.
Q1 и Q2 — соответственно подача и расход жидкости;
n1 и п2—скорости вращения соответственно вала насоса и гидромотора;
q1 и q2 — рабочие объемы соответственно насоса и гидромотора.
В системах с регулируемым насосом изменение расхода достигается изменением рабочего объема насоса.
Из технической характеристики трактора известно что частота вращения вала отбора мощности wв=32 с-1 именно данный вал вращает шестеренный насос НШ-32-3 который был предварительно выбран в качестве предварительного расчета в связи с тем что его номинальное давление также равно 16 МПа а в конструкции еще предусмотрено установка одного гидромотора.
N1=16×32×315=16128 Вт
N2=16×32×281=14387 Вт
Для использования максимальной мощности приводного двигателя N необходимо при изменении Q1 стремиться к пропорциональному изменению p1 с таким расчетом чтобы произведение р1 Q1 сохранялось постоянным.
При изменении рабочего объема q2 и неизменном рабочем объеме q1 скорость вращения вала гидромотора определяется из формулы
Момент на валу гидромотора может быть подсчитан из выражения
Подставляя значение p2q2 из формулы (3.31) в выражение (3.34) получаем:
При назначении максимального момента исходят из максимального давления на которое рассчитана передача по прочности. Для самоходных колесных машин максимальный момент не должен превышать величины при которой буксуют колеса а минимальный момент должен соответствовать минимальному сопротивлению как например три движении по горизонтальному участку пути с твердым покрытием. При этом значения Ммакс и Ммин должны обеспечиваться параметрами насоса и гидромотора.
В реальных машинах наблюдаются потери энергии из-за утечек жидкости и трения. Утечки жидкости через неплотности сопряженных элементов насоса и гидромотора снижают объемный к. п. д. 0 а трение взаимно перемещающихся относительно друг друга деталей снижает механический к. п. д. гидропривода м.
С учетом влияния этих факторов можно написать:
Откуда коэффициент трансформации будет равен
Соответственно этому передаточное отношение между насосом и гидромотором будет зависеть от их объемных к.п.д. т.е.
А полный к.п.д. будет равен:
Расчленим потери давления при течении жидкости в напорной и сливной гидролиниях и обозначим их соответственно через р1n и р2n Тогда суммарные потери в системе составят:
рn + р1n + р2n (3.17)
а величина гидравлического к. п. д. гидролиний будет равна:
При ламинарном течении жидкости потери давления в гидролиниях пропорциональны расходу а при турбулентном — квадрату расхода Таким образом гидравлический к. о. д. в одном и другом случаях может быть записан следующим образом:
где g и g' — коэффициенты пропорциональности.
Перепад давления в насосе можно определить из выражения
Подставляя значение р1 в формулы (3.42) и (3.43) соответственно получим:
где A = 1Ng A'=1Ng'.
Из выражений (3.44) и (3.45) видно что увеличение расхода для расширения диапазона изменении скорости вращения гидромотора в закрытых системах с регулируемым насосом невыгодно из-за значительного возрастании потерь (особенно при турбулентном режиме). При уменьшении расхода и связанного с ним увеличения давления будут расти объемные потери в насосе и гидромоторе.
Течение жидкости через зазоры насосов и гидромоторов носит ламинарный характер и утечки в этом случае пропорциональны давлению Qyp. Но в зоне регулирования при постоянной мощности давление обратно пропорционально расходу рNQ. Подставляя в формулу 01—BQ2 значение QypNQ получим 01—BQ2 где В — коэффициент пропорциональности.
Полный к. п. д. закрытой системы гидропривода с регулируемым насосом и нерегулируемым гидродвигателем при ламинарном течении потока будет иметь следующий вид:
Далее проведем тепловой расчет гидросистемы.
Рабочая жидкость в гидросистеме нагревается вследствие дросселирования ее в различных элементах гидросистемы включая и насос.
Особенно значительный нагрев жидкости происходит при отсутствии разгрузки насоса значительных сопротивлениях на сливной гидролинии низком к. п. д. насоса или гидродвигателя а также при дроссельном регулировании скорости движения рабочих органов.
При отсутствии разгрузки насоса слива всей жидкости через предохранительный гидроклапан количество выделяемого тепла в кДж определяется по формул
Емкость гидробака необходимая для поддержания в нем заданной температуры рабочей жидкости определяется из уравнения теплового баланса
где Q — количество тепла выделяемого в гидроприводе в единицу времени;
dT — приращение температуры за время dt в °С;
T1 —температура рабочей жидкосеи вначале рассматриваемого промежутка времени в 0С;
То — температура окружающего воздуха в 0С;
с — теплоемкость рабочей жидкости;
m — масса рабочей жидкост-и;
с1 — теплоемкость металла;
m1 — расчетная масса гидробака;
F — расчетная площадь поверхности гидробака;
k —коэффициент теплопередачи от гидробака к воздуху.
Расчетная площадь поверхноости гидробака определяется следующим образом: вся смачиваемая поверхность гидробака принимается в расчет с коэффициентом равным 1 остальная поверхность не соприкасающаяся с рабочей жидкостью — с коэффициентом равным 03. Расчетная площадь поверхности гидробака в м2 связана с объемом V масла в гидробаке следующей зависимостью:
Коэффициент теплопередачи от гидробака к воздуху определяется по формуле
где а1 — коэффициент теплопередачи от рабочей жидкости к стенке гидробака;
—толщина стенки гидробака в м;
λ — коэффициент теплопроводности стенки гидробака;
а2 — коэффициент теплопередачи от стенки гидробака к воздуху.
Значения коэффициентов а1 и а2 изменяются б широком диапазоне в зависимости от вида рабочей жидкости характера и скорости движения ее в гидробаке а также от температуры рабочей жидкости стенок гидробака и окружающего его воздуха. Коэффициент X также изменяется в зависимости от температуры стенок гидробака.
Установившаяся температура рабочей жидкости определяется из формулы (3.51) при t
Из формулы (3.52) можно определить требуемый объем рабочей жидкости в гидробаке в л:
При охлаждении рабочей жидкости в гидробаках теплообменниками уравнение теплопередачи при установившейся температуре запишется в виде:
Q – kFТдоп = k1F1T(3.54)
где Тдоп — допустимая температура нагревания рабочей жидкости в гидробаке;
F1 — расчетная площадь поверхности теплообменника в м2;
k1 — коэффициент теплопередачи от рабочей жидкости к воде в теплообменнике.
Точный подсчет коэффициента k1 затруднителен так как величины -входящие в формулу для его определения зависят от ряда причин и изменяются в широких пределах.
Средний температурный напор (средняя разность температур масла и воды) Т в °С определяется по формуле
где Тм - установившаяся температура рабочей жидкости;
То.в — начальная температура охлаждающей воды;
Т1в — конечная температура охлаждающей воды.
Уравнение теплового баланса для гидробаков с теплообменниками при установившейся температура рабочей жидкости имеет вид:
Q – kFТдоп = свρвVв(Т1в–То.в)(3.56)
где св — теплоемкость воды;
рв — плотность воды;
VB — часовой расход воды в теплообменнике.
Из уравнения (3.56) находится часовой расход воды в теплообменнике
Температура нагревания рабочей жидкости в зависимости от количества выделяемого в гидросистеме тепла и часового расхода воды в теплообменнике определяется по формуле
Необходимая площадь поверхности теплообменника находится по формуле
Внутренний диаметр нагнетательного трубопровода
где q – расход жидкости лмин;
u - скорость движения жидкости мс.
Толщина стенок трубопровода определится по формуле
где Рн – давление в системе при испытании МПа;
s - допустимое напряжение растяжения для стальных труб МПа;
d – внутренний диаметр трубы см;
К – коэффициент безопасности.
Принимаем для нагнетательной линии (ГОСТ 8734-88) стальные толстостенные трубы с внутренним диаметром 20 мм наружным 25 мм d=25 мм.
Аналогичный расчет ведем для всасывающей линии: испытательное давление Рн=25 МПа; d=30 мм; s=800 кНсм2; К=4; диаметр трубопровода
Принимаем по ГОСТ 8732-89 стальные тонкостенные трубы с внутренним диаметром 20 мм и наружным 25 мм т. е. d=25 мм.
Гибкие шланги принимаем согласно ГОСТ 8318-87 для низкого давления типа Б с внутренним диаметром 20 ±15 мм и для высокого давления «РВД» с внутренним диаметром d = 20 + 08 мм. Распределители золотниковые секционные с предохранительным клапаном.
6.2. Расчет гидроуправления подъема рабочего оборудования
Усилия по штокам цилиндров найдутся из соотношения моментов. Число цилиндров в механизме — 2.
Коэффициент полезного действия механизма принимаем равным 09. Сумма моментов сил веса относительно точки О:
где Рп – усилие на штоке гидроцилиндра Н;
хп – расстояние от линии действия силы Рп до точки О м.
Рп=350×981×0403=4578 Н или 46 кН
На каждый гидроцилиндр с учетом КПД действует сила определяемая по формуле
где h - КПД гидроцилиндра.
Насос имеет производительность Q равную 281 см3с и развивает давление Р=16 МПа. Тогда площадь поршня гидроцилиндра равна
Диаметр гидроцилиндра равен
Диаметр штока гидроцилиндра определим как
dш=05×0063=000315 м.
Ход штока гидроцилиндра определится по следующей формуле
где b – расстояние от точки крепления штока гидроцилиндра до рабочего органа м;
j - угол подъема рабочего органа град.
По ГОСТ 6540-88 выбираем гидроцилиндр двустороннего действия с односторонним штоком: 63-32-320 [14].
Объем полости поршня равен
V=314×632×324=99701 см3
Время на полный подъем равняется
Тп=99701281×1920=184 с
В результате представленных расчетов была рассчитана вся гидросистема обеспечивающая питание привода фрезерного рабочего оборудования.
Далее необходимо провести расчет редуктора привода фрезерного рабочего оборудования.
6.3. Расчет редуктора привода фрезерного рабочего органа
Для привода фрезерного рабочего оборудования используется гидромотор и одноступенчатый цилиндрический редуктор который передает крутящий момент от гидромотора к валу привода фрезы.
Расчет редуктора будем производить согласно методике предложенной Гузенковым П.Г..
Вначале определим обще передаточное число редуктора.
где w1 – частота вращения вала гидромотора мин-1;
w2 – частота вращения вала фрезы мин-1.
Нагрузка передачи постоянная но во время пуска редуктора она кратковременно превышает в 16 раза по сравнению с номинальной. Срок службы передачи 30000 часов.
Для передачи предусматривается эвольвентное зацепление без смещения. Основные параметры ее согласуем с СТ СЭВ 229-73. Материал для обоих зубчатых колес – сталь 40Х с объемной закалкой и отпуском до твердости НRC48. Для зубчатых колес передачи принимаем 7-ю степень точности по нормам плавности по СТ СЭВ 641-77.
Рассчитаем зубья передачи на контактную прочность и изгиб. Из расчета зубьев на контактную прочность вычислим межосевое расстояние передачи аw по формуле
где Ка – коэффициент равный для прямозубых передач Ка=495;
u – передаточное число;
Т2 – крутящий момент передаваемый колесом Нм;
Кнb - коэффициент значения принимают по графику рис. 12.18.;
yва – коэффициент ширины венца;
sн – допустимая контактная прочность МПа.
Определим значения величин входящих в данную формулу.
Валы передачи установим на подшипниках качения и примем h=098. Мощность передаваемая колесом равна
Крутящий момент передаваемый колесом определим по формуле
Т2=126480=0026 кНм или 26 Нм
Принимаем из графиков значения коэффициентов yва=025 тогда
ybd=05yва(u+1).(3.75)
ybd=05×025(4+1)=0625
Выбрав НRC=48 принимаем Кнb=1 рис. 12.19.
Допускаемое контактное напряжение [sн] определим как
[sн]=sн lim bZRZvKHLSн(3.76)
ZR – коэффициент учитывающий шероховатость сопряженных поверхностей зубьев 095;
Zv – коэффициент учитывающий окружную скорость передачи 1;
КНL – коэффициент долговечности;
Sн – коэффициент безопасности 11.
Базовое число циклов напряжений по графику 12.21 для HRC48=HB460 Nно=70×106. Эквивалентное число циклов напряжений равно
где t – продолжительность работы зубчатой передачи ч
Nне=60×480×30000=864×106
Отношению Nне Nно=864×10670×106=123 на графике рис. 12.20 соответствует коэффициент долговечности KHL=11. Подставим полученные значения в зависимость (3.76) получим
[sн]=(18×48+150)×095×1×1111=963 МПа
Тогда межосевое расстояние передачи равно
В соответствии с СТ СЭВ 229-75 принимаем аw=50 мм. Делительное межосевое расстояние а=аw=50 мм. Модуль зубьев
где zс – сумма зубьев шестерни z1 и колеса z2.
Сумма зубьев шестерни и колеса определяется по формуле
Число зубьев шестерни
Проверим рабочие поверхности зубьев на контактную прочность по максимальному контактному напряжению под действием на зубья кратковременной нагрузки. Для этого определим расчетное контактное напряжение sн вызываемое расчетным моментом Т1 и допускаемое максимальное контактное напряжение [sн]max. Коэффициент Zн равен
где bb – основной угол наклона линии зуба;
atw - угол наклона нормальной силы на зубе.
Коэффициент Zм=275 Н12мм. Коэффициент торцового перекрытия равен
Коэффициент Ze определим по формуле
Далее определим по рис. 12.17 коэффициент Кнa=105 коэффициент Кнb=1 коэффициент Кнv=1. тогда расчетное контактное напряжение
Для стали 40Х с объемной закалкой и отпуском по ГОСТ 4543-71 предел текучести sт=700 МПа. Допускаемое максимальное контактное напряжение для зубьев
[sн]max=28×700=1960 МПа
Так как кратковременная перегрузка передачи больше номинальной в 16 раза то
Значит при кратковременной перегрузке зубья по контактной выносливости вполне прочны.
Определим размеры зубьев. В соответствии с СТ СЭВ 308-76 коэффициент высоты головок зубьев hа=1 и коэффициент радиального зазора с=023.
Высота головок зубьев
Делительный диаметр шестерни равен
Внешний диаметр вершин dae и диаметр впадин dfe по формулам
Делительный диаметр колеса равен
dае2=160+2×25=165 мм
dае2=160-2×31=1538 мм
Ширина зубчатого венца равна
Далее определим диаметры валов.
Расчет валов цилиндрического редуктора
Рассчитаем вал цилиндрической передачи. Вал установлен в двух подшипниковых опорах. На валу закреплена цилиндрическая шестерня. Мощность передаваемая валом Р=1285 кВт; угловая скорость вала w=166 радс (n=480 обмин). Расстояние между подшипниками вала =60 мм. Цилиндрическая шестерня имеет делительный диаметр d=160 мм. Расстояния от подшипников до цилиндрической шестерни равны а=20 мм и b=20 мм.
Материал вала – сталь 43. Для этой стали по ГОСТ 1050-74 принимаем: предел прочности при растяжении sв=610 МПа предел текучести sт=360 МПа. Сначала рассчитаем вал на статическую прочность на совместное действие изгиба и кручения. Растяжение или сжатие вала осевой силой действующей на цилиндрическое колесо не учитываем.
Крутящий момент передаваемый валом равен
Т=1285×103166=774 Нм
Окружная сила цилиндрической шестерни определяется по формуле
Ft1=2×7740160=9675 Н
Радиальная Fr1 и осевая Fа1 силы действующие на цилиндрическое колесо определяем по формулам
Fr1=Ft1tgacosd.(3.100)
Fа1=Ft1tgasind.(3.101)
Fr1=9675×0325×0965=3034 Н
Fа1=9675×0325×0264=830 Н
Реакции опор подшипников вала равны
R’A=9675(60-20)60=6450 Н
R’В=9675-6450=3225 Н
R’’A=Fr1(-a).(3.104)
R’’A=3034(60-20)60=2022 Н
R’’В=3034-2022=1011 Н
R’’’A=R’’’B=Fa1dm2.(3.106)
R’’’A=R’’’B=830×1602×60=1106 Н
Изгибающие моменты от действия силы Ft1 равен
Изгибающие моменты от действия силы Fr1 равен
M’’I=2022×002=404 Нм
M’’II=1011×002=202 Нм
Изгибающие моменты от действия силы Fа1 равен
М’’’I=R’’’Aa.(3.111)
M’’’I=1106×002=221 Нм
От силы R’’’A в сечении II
М’’’IIA=R’’’A(-b).(3.112)
M’’’IIA=1106(006-002)=442 Нм
От силы R’’’В в сечении II
М’’’IIВ=R’’’Вb.(3.113)
M’’’IIВ=1106×002=221 Нм
Полный изгибающий момент: в сечении I
Максимальный изгибающий момент
Рассчитаем вал по третьей теории прочности. Эквивалентный (приведенный) момент но формуле
Допускаемое напряжение на изгиб вала [sи]=85 МПа. Диаметр вала в опасном сечении по формуле
В сечении II диаметр вала по расчету равен d=452 мм но с учетом запаса прочности примем равным 50 мм. Диаметр вала в других сечениях примем конструктивно увеличивая каждый переход ровно на 5 мм.
Аналогично произведем расчет другого вала в ходе которого было установлено что диаметр первого вала равны d1=35 мм.
В нашем случае на разрабатываемом рабочем органе будет действовать как радиальная так и осевая силы. Тогда примем радиально-упорные однорядные подшипники по ГОСТ 831-75 так как нагрузки действующие на них незначительны.
Примем подшипник №310 для которого по ГОСТ 8338-75 статическая грузоподъемность равна Со=40200. Расчеты будем производить пользуясь формулами П.Г. Гузенкова. Эквивалентная динамическая нагрузка подшипника рассчитывается по формуле
P=(xVFr+YFa)KбKт(3.118)
где Fr и Fа – (постоянные по размеру и направлению) радиальная и осевая нагрузки на подшипники соответственно.
X – коэффициент радиальной нагрузки;
Y – коэффициент осевой нагрузки;
V – коэффициент вращения учитывающий какое кольцо вращается. Внутреннее V = 1 наружное V = 12;
Кб – коэффициент безопасности учитывающий характер нагрузки на подшипник. При спокойной нагрузки Кб = 1;
Кт – температурный коэффициент учитывающий рабочую температуру нагревания подшипника. Если t 125C Kт=1 а если t=125-150C Kт=105-13.
Коэффициент Y определим пользуясь таблицей 4.1
Таблица 4.1 - Числовые значения коэффициентов е и Y
Частота вращения кольца подшипника
В нашем случае n=30×166314=158
Так как Fa C0 = 830 40200 = 002 то значение е = 032 а Y = 07
Для определения числового значения X приведем выбор по следующим условиям:
если Fa VFr то X=10 Y=0.
если Fa V·Fr > e то Х =046 Y – смотри в таблице 3.3.
FaV·Fr=8301·3034=027
Следовательно е = 034; Х = 10; Y = 0.
Подставляя все данные в формулу (3.118) найдём значение Р.
Р=(1·1·3034+0×830)·1·1=3034 Н.
Найдём требуемую динамическую грузоподъёмность подшипника.
В результате всех расчётов видно что выбранный нами подшипник удовлетворяет следующему условию.
С = 276 кН [С] = 35 кН.
Подшипник № 312 вполне подходит для эксплуатации. Последующий расчет остальных подшипников так же подтвердил их нормальную работоспособность.
Далее необходимо произвести расчет на прочность некоторых элементов конструкции фрезерного рабочего оборудования.
7. Расчет элементов конструкции фрезерного рабочего оборудования на прочность
Расчет шарнирного соединения.
Рассчитаем шарнирное соединение крепления штока гидроцилиндра с проушиной рабочего органа дорожной фрезы.
Изгибающий момент будет определяться как
где Рт – усилие на пальце кН;
l2 – плечо данного усилия м.
Так как в конструкции предусмотрен один палец тогда он будет воспринимать всю нагрузку действующую на рабочий орган Рт=51 кН. Длина пальца равна l=0136 м тогда
Мизг=51.0136=069 кНм.
Для подбора сечения стержня определяем требуемый момент сопротивления
где М - изгибающий момент кН.м;
[s] - допустимое напряжение МПа.
Так как палец изготовлен из стали 3 то допустимое напряжение равно [s]=350 МПа тогда
Диаметр пальца определим по формуле
Принимаем диаметр пальца равным d=60 мм.
Расчет проушины крепления гидроцилиндра
Произведет расчет проушины крепления оси опорного катка к проушине к которой будет установлен гидроцилиндр. Расчет проушины произведем по методике [17 18]. На проушину действует разрывающее усилие равное усилию на штоке гидроцилиндра Fц=51 кН. Расчет произведем используя рис. 3.2.
Рисунок 3.2. Схема для расчета проушины
Для сечения А-А напряженное состояние будет описываться формулой
sр=Рт(2bs)[sр](3.124)
где Рт – усилие действующее на проушину Н;
sр – максимальное напряжение на разрыв нм2;
b и s – соответственно ширина и толщина проушины м.
Из конструктивных соображений проушина изготовлена из стали Ст.3 с толщиной равной 8 мм тогда выразим из формулы (3.124) ширину проушины получим
b=513×0008×160000=000133 м
sр=Рт[2(b-d)s][sр](3.126)
где d – диаметр оси м.
Тогда ширина проушины равна
Как показали расчеты при толщине проушины равной s=8 мм ширина должна быть равной не менее b=65 мм. Из конструктивных соображений длина проушины будет увеличена до 90 мм.
Далее произведем расчет сварного соединения крепления проушины к раме фрезы.
Расчет сварного соединения крепления проушины
Произведем расчет сварного соединения крепления проушины к раме фрезы рис. 3.3. На данный узел действует максимальный крутящий момент и продольная сила следовательно расчетное напряжение шва определится из уравнения
где М – изгибающий момент Нм;
W – момент сопротивления шва;
Р – продольная сила Н;
Рисунок 3.3. Схема для расчета сварного соединения.
Момент сопротивления шва определяется по формуле
где l и b – соответственно ширина и длина шва м.
Изгибающий момент равен
Задаваясь шириной шва равной 05 см определим его длину используя формулу (3.129) и зная что проушина изготовлена из стали 3 то допустимое напряжение равно [s]=360 МПа тогда
Для обеспечения необходимой жесткости сварного соединения необходимо чтобы длина сварного шва была не менее 4 см. Так как длина проушины конструктивно была увеличена до 9 см то сварной шов выполненный по всей длине проушины обеспечит ее надежное крепление что доказано расчетом.
Расчет резьбового соединения
Проведем расчет болтового соединения крепления штанги показывающей расположение фрезы. Так как резьбовое соединение осуществляет соединение штанги то на него действует сила тяжести самой штанги и конструктивно принимаем равной F=25×981=25 Н.
Определим осевую растягивающую силу действующую на болт после предварительной затяжки и приложения внешней силы F по формуле
Fа=[k(1-c)+c]F(3.132)
где k – коэффициент затяжки болта;
c - коэффициент внешней нагрузки;
Примем коэффициент внешней нагрузки c=05. Коэффициент затяжки болта примем равным k=2 тогда осевая растягивающая сила будет равна
Fа=[2(1-05)+05]25=375 Н
Для стали Ст.3 предел текучести sт=220 МПа а допустимый коэффициент запаса прочности для болтов равен [S]=25 тогда определим допустимое напряжение на растяжение по формуле
где sт – предел текучести МПа;
[S] – коэффициент запаса прочности.
Подставив значения получим
Определим внутренний диаметр резьбы болта по формуле
Принимаем болт с метрической резьбой М6 для увеличения запаса прочности.
Как видно из вышеперечисленного были представлены расчеты элементов конструкции дорожной фрезы необходимых для изготовления данной разработки.
8. Расчет технологического процесса изготовления пальца крепления гидроцилиндра
В ходе ранее проведенных расчетов на прочность было установлено что палец крепящий гидроцилиндр подъема рабочего органа имеет следующие геометрические размеры: диаметр 60 мм при длине пальца 136 мм рис. 3.4.
Рисунок 3.4. Палец для крепления гидроцилиндра подъема рабочего органа
Схема технологического процесса изготовления пальца показана на рисунке 3.5.
Рисунок 3.5. Схема технологического процесса изготовления пальца
Выбранный технологический маршрут изготовления пальца имеет вид:
Произведем расчеты режимов при изготовлении и норм времени для выбранного технологического маршрута по каждой его операции.
Операция 005 – токарная
Оборудование: станок токарно-винторезный 16К20.
Приспособления: штангенциркуль резцы шаблоны.
Содержание операции: проточить наружную поверхность пальца и отрезать его по длине.
Выбор режима резания:
Частота вращения детали:
где: V – скорость резания ммин.
Д – диаметр детали мм.
где: С – постоянный коэффициент зависящий от качества обрабатываемой детали и инструмента;
С = 417 – для стали и стального литья;
t – глубина резания мм. t = 05 мм. cм.
S – подача ммоб S = 025 ммоб. см.
Т – стойкость инструмента мин. Т = 60 мин см.
m – показатель относительной стойкости резца m = 0125 см.
Расчет нормы времени:
Основное время вычисляют по формуле:
где: L – расчетная длина обработки в направлении подачи мм.
i -число проходов i=1
п – частота вращения детали обмин.
L = l + l1 + l2 + l3 мм (3.138)
где: l – длина обрабатываемой поверхности мм. l = 100 мм.
l1 -длина врезания инструмента мм.
При точении l1 = t·ctg φ
φ – главный угол в плане φ=45о следовательно l1 = t·= 05 мм.
l2 –длина прохода и пробега инструмента l2 =3 мм. см.
l3 - длина проходов при взятии пробных стружек мм.
L = 136 + 05 + 3 + 6 = 1455 мм
Вспомогательное время выбираем
Дополнительное время
Подготовительно-заключительное время:
где: пшт = 4 – количество деталей в партии.
Операция 010 – сверлильная
Оборудование: универсально-сверлильный станок 6Р82Г
Содержание операции: закрепить деталь установить сверло просверлит отверстие снять деталь.
-глубина отверстия t = 60 мм.
Расчет нормы времени.
Штучное время на сверление 4 отверстий выбираем:
Операция 015 – контроль
Операция контроль проводится с целью правильности геометрических форм соответствие требованиям чертежа. Замер осуществляется с помощью штангенциркуля.
Основное время: То = 14 мин.
Вспомогательное время: Тв = 04 мин.
Дополнительное время определяется по формуле: Тдоп. = 011 × Топ мин.
Топ = 14 + 04 = 18 мин.
Тдоп = 011 × 18 = 02 мин.
Подготовительно-заключительное время Тпз = 5 мин.
Общее время на изготовление пальца равно Т = 20 мин.
Составление документации необходимой для изготовления пальца была разработана в программном продукте «КОМПАС-Автопроект» и представлена в приложении.
Анализ существующих конструкций фрез показал основные недостатки существующих конструкций которые были устранены в предлагаемой конструкции дорожной фрезы.
С целью доказательства работоспособности данной конструкции был представлен расчет основных параметров нового рабочего оборудования а именно выбор основных параметров тяговый и мощностной расчеты.
Представлен статический расчет и определена производительность процесса фрезерования грунта с использованием нового рабочего оборудования.
Представлен расчет привода фрезерного рабочего оборудования.
Выбраны и обоснованы основные параметры гидравлического насоса гидромоторов и гидроцилиндра. Произведен тепловой расчет гидросистемы.
Для привода фрезерного рабочего органа был выбран и рассчитан редуктор. Произведен расчет зубчатых колес валов подшипников.
Так же сделаны расчеты на прочность отдельных элементов конструкции фрезерного рабочего оборудования.
Выбрана и разработана технология изготовления пальца крепления гидроцилиндра.
глава 4.doc
1. Расчет стоимости изготовления дорожной фрезы
Преимущества новой техники получают из обобщенной экономической оценки в виде показателей эффективности. Новые машины должны обеспечивать увеличение производительности при минимальных затратах труда сокращение срока окупаемости капиталовложений увеличение годового экономического эффекта а так же сокращение и совмещение выполняемых операций сокращение сроков выполнения работ повышение качества работы [19].
По своей конструкции новые машины и механизмы должны отвечать современным достижениям науки и требованиям передовой практики.
Экономическую эффективность внедрения новой техники определяют методом сравнения по следующим показателям:
Производительность машины;
Затраты труда на единицу продукции или работы;
Энергоемкость процесса;
Удельная металлоемкость процесса;
Капитальные вложения и удельные капитальные вложения на единицу продукции или работы;
Себестоимость единицы работы себестоимость машино-смены;
Коэффициент сравнительной экономической эффективности или срок окупаемости дополнительных капитальных вложений по вновь проектируемой машине;
Годовая экономия и годовой экономический эффект по приведенным затратам.
В качестве примера расчета определяется экономическая эффективность применения дорожной фрезы на тракторе ОМТЗ-82.1 (модернизированная) и серийной дорожной фрезы МДФ-400Е.
Расчет стоимости переоборудования проводим по следующей формуле:
где Sзп – затраты на заработную плату руб.;
Sмат – затраты на материалы для переоборудования руб.;
Sпрем – затраты на выплату премии руб.;
%НР – процент накладных расходов
Sосню зп – основная заработная плата руб.
Расчет заработной платы для разработки дорожной фрезы на тракторе ОМТЗ-82.1 проведем в табличной форме табл. 4.1.
Таблица 4.1. – Заработная плата необходимая для изготовления дорожной фрезы на базе трактора ОМТЗ-82.1
Дополнительная заработная плата определяется:
Sдоп=01.Sосн.зп(4.2)
где Sосню зп – основная заработная плата производственных рабочих руб.
Sдоп=01×2601=2601 руб.
Выдачи премий к заработной плате определяются как
Sпрем=04Sосн.зп(4.3)
Sпрем=04×2601=10404 руб.
Начисления по социальному страхованию (Sсоц) берутся в размере 26 % от основной и дополнительной заработной платы производственных рабочих
Sсоц=026(Sосн+Sдоп) (4.4)
где Sосн – основная зарплата производственных рабочих руб.;
Sдоп – дополнительная зарплата руб.
Sсоц=026(2601+2601)=74389 руб.
Суммарная зарплата производственных рабочих определится:
Sзп=Sосн+Sдоп+Sсоцюстрах+Sпрем(4.5)
Sдоп – дополнительная зарплата руб.;
Sсоц.страх – начисления по социальному страхованию руб.;
Sпрем – премии к заработной плате руб.
Тогда суммарная заработанная плата будет составлять
Sзп=2601+2601+74389+10404=464539 руб.
Приведем сравнительную оценку затрат для разработки дорожной фрезы на тракторе ОМТЗ-82.1. Сравнение приведем в табличной форме табл. 4.2.
Таблица 4.2. - Затраты на материал для изготовления дорожной фрезы на тракторе ОМТЗ-82.1
Всего затрат на материал руб.
Лист Ст.3 6х1250х2500
Труба 89х35 ГОСТ 3262-62
Лист Ст.3 8х1250х2500
Труба 108х35 ГОСТ 3262-62
Круг 50 Ст.45 ГОСТ 2590-71
Лист Ст.3 2х1250х2500
Круг 120 Ст.45 ГОСТ 2590-71
Круг 100 Ст.3 ГОСТ 380-75
Рукава высокого давления
Стойка фрезы с наконечником
Таким образом затраты на материалы для разработки дорожной фрезы на тракторе ОМТЗ-82.1 равны Sмат=60257 руб. Процент накладных расходов составит %НР=350-400 принимаем %НР=350. Подставив в формулу (4.1) соответствующие числовые значения получим
В итоге стоимость изготовления рабочего органа в виде фрезы составляет 74006 руб. Далее произведем экономический расчет эффективности ее применения.
2. Технико-экономические показатели дорожной фрезы
Техническую производительность дорожной фрезы определим по следующей зависимости [5]:
где uр – рабочая скорость машины мс;
b – ширина захвата рабочего органа м;
h – глубина рыхления м.
Для серийной фрезы МДФ-400Е
Пт=3600.014×19×01=9576 м3ч
В связи с тем привод серийной дорожной фрезы МДФ-400Е является механическим а на предлагаемом фрезерном рабочем оборудовании для привода используются гидромотор 210.10 то он способен развивать большее усилие. Вследствие этого глубина рыхления и скорость передвижения нового рабочего оборудования больше по сравнению с серийным тогда техническая производительность разработанной дорожной фрезы равна
Пт=3600.02×19×015=2052 м3ч.
Сменная производительность машины
где tсм – число часов работы машины в смену ч;
kт – коэффициент перехода от эксплуатационной к сменной производительности kт=08;
kэ – коэффициент перехода от эксплуатационной производительности к сменной kэ=075.
Сменная производительность
серийной дорожной фрезы Псм=9576.8.08.075=4596 м3см;
модернизированной дорожной фрезы Псм=2052.8.08.075=985 м3см
Годовую производительность машины определяют по формуле:
где Псм – сменная производительность машины м3ч;
N – число смен работы машины в год ч;
Годовая производительность
серийной дорожной фрезы Пгод=4596×150=68940 м3год;
модернизированной дорожной фрезы Пгод=985.150=147750 м3год.
Затраты труда на 1000 м3 определятся как
где n – количество рабочих занятых управлением и обслуживанием машины чел.
Так как дорожную фрезу обслуживает один человека тогда затраты труда соответственно составят:
для серийной машины Т1=1.10009576=1044 чел.-ч.;
для модернизированной машины Т2=1.10002052=487 чел.-ч.
Снижение затрат труда определяют:
где Т1 и Т2 – затраты труда при использовании старой (серийной) и новой машины чел.-ч.
Энергоемкость процесса определяет как
где Nном – номинальная мощность двигателя кВт.
Для серийной машины Q1=559576=0574 кВт.чм3.
Для модернизированной машины Q2=552052=0268 кВт.чм3.
Снижение энергоемкости процесса
где Q1 и Q2 – энергоемкость процесса при использовании старой (эталонной) и новой машины кВт.чга.
Удельная металлоемкость процесса определится как
где Вм – масса машины кг.
Для серийной машины М1=540068940=0078 кгм3.
Для модернизированной машины М2=5500147750=0037 кгм3.
Снижение металлоемкости
где М1 и М2 – удельная металлоемкость процесса при использовании старой (эталонной) и новой машины кгм3.
Капитальные вложения определятся как
где Цм – прейскурантная или оптово-отпускная цена машины руб.;
r - коэффициент учитывающий надбавку на транспортировку и монтаж машин и оборудования r=12.
Для серийной машины К1=1145000.12=1374000 руб.
Для модернизированной машины К2=(1145000+74006).12=1462807 руб.
Удельные капитальные вложения определяются следующим образом
где К – капитальные вложения на приобретение машины и оборудования руб.;
Пгод – годовая производительность машины м3год.
Для серийной машины Куд1=137400068940=199 рубм3.
Для модернизированной машины Куд2=1462807147750=99 рубм3.
Расчет стоимости машино-смены
Sсм=Sед+Sа+Sкр+Sтр+Sгсм+Sосн+Sзп+Sнакл(4.17)
где Sед – единовременные затраты то есть затраты на транспортировку машины монтаж и демонтаж приходящиеся на 1 машино-смену руб.;
Sа – затраты на амортизацию руб.;
Sкр – затраты на капитальный ремонт руб.;
Sтр – затраты на текущий ремонт руб.;
Sгсм – затраты на ГСМ руб.;
Sосн – затраты на ремонт и износ сменной оснастки руб.;
Sзп – затраты на зарплату обслуживающего персонала руб.;
Sнакл – накладные расходы руб.
Единовременные затраты то есть затраты выполняемые до начала эксплуатации машины на объекте
Sед=Sтрансп+Sм+Sдм(4.18)
где Sтрансп – затраты на транспортировку машины до объекта руб.;
Sм – затраты на монтаж машины руб.;
Sдм – затраты на демонтаж машины руб.
Затраты на транспортировку машины до объекта определятся как
где m – число перебазирований машины с объекта на объект в течение года с демонтажом и монтажом m=1-3;
S’трансп – стоимость транспортировки 1 тонны массы машины руб.;
N – число часов работы машины за сезон.
Так как дорожная фреза весит больше 1 тонны и поэтому S’трансп=180 рубт тогда затраты на транспортировку машины будут равны:
- для серийной машины Sтрансп 1=2.180×54150=1296 рубт;
- для модернизированной машины Sтрансп 2=2.180×55150=132 рубт
Затраты на монтаж машины определятся как
где S’м – стоимость монтажа 1 тонны массы машины руб.
Так как стоимость монтажа дорожной фрезы составляет S’м=20-30 рубт тогда затраты на монтаж машины будут равны:
- для серийной машины Sм1=2×30×54150=216 руб;
- для модернизированной машины Sм2=2×30×55150=22 руб
Затраты на демонтаж машины определятся как
Стоимость демонтажа:
- для серийной машины Sдм1=05×216=108 руб.;
- для модернизированной машины Sдм2=05×22=11 руб.
Подставляя полученные данные в формулу (4.18) определим единовременные затраты:
- для серийной машины Sед1=1296+216+108=162 руб.;
- для модернизированной машины Sед2=132+22+11=165 руб.
Затраты на амортизацию определятся по формуле
где а – норма амортизационных отчислений %.
Для дорожных фрез норма амортизационных отчислений составляет а=12 % тогда затраты на амортизацию:
- для серийной машины Sа1=1374000.12100.150=10992 руб.;
- для модернизированной машины Sа2=1462807×12100.150=117025 руб.
Затраты на капитальный ремонт определятся по формуле
где акр – норма отчислений на капитальный ремонт %.
Для дорожных фрез норма отчислений на капитальный ремонт составляет акр=14 % тогда затраты на капитальный ремонт:
- для серийной машины Sкр1=1374000.14100.150=12824 руб.;
- для модернизированной машины Sкр2=1462807×14100.150=136529 руб.
Затраты на текущий ремонт и техническое обслуживание определятся по формуле
где атр – норма отчислений на текущий ремонт и техническое обслуживание %.
Для дорожных фрез норма отчислений на текущий ремонт и техническое обслуживание составляет атр=27 % тогда затраты на текущий ремонт и ТО составят:
- для серийной машины Sтр1=1374000.27100.150=24732 руб.;
- для модернизированной машины Sтр2=1462807×27100.150=263305 руб.
Затраты на горюче-смазочные материалы определим по следующей зависимости
Sгсм=gгсмат+Sсмаз(4.25)
где gгсм – сменный расход дизельного топлива кг;
ат – цена дизельного топлива рубкг;
Sсмаз – затраты на смазывающий материал 25 % от стоимости дизельного топлива.
Сменный расход дизельного топлива
gсм=Nномtсмkдв[gл+(gн-gх)kдм](4.26)
где Nном – номинальная мощность двигателя кВт;
kдв – коэффициент использования двигателя по времени kдв=065;
kдм – коэффициент использования двигателя по мощности kдв=05;
gн – удельный расход топлива на 1 кВтч номинальной мощности двигателя при нормальной загрузке кгкВт ч;
gх – удельный расход топлива на 1 кВтч номинальной мощности двигателя при холостой работе кгкВт ч.
gсм=55.8.065[0095+(0285-0095)05]=543 кгсм
Тогда затраты на ГСМ
Sгсм1=(543×178)125=120906 руб
Затраты на износ и ремонт сменной оснастки определятся как
где Косн – коэффициент перехода затрат на текущий ремонт и технического обслуживание к затратам на износ и ремонт сменной оснастки Косн=005-008.
Sтр – затраты на текущий ремонт и техническое обслуживание руб.
Для серийной машины Sосн1=007×24732=17312 руб.
Для модернизированной машины Sосн2=007×263305=18431 руб.
Затраты на заработную плату обслуживающего персонала машины рассчитывают по формуле:
где Тсм – сменная тарифная ставка соответствующего разряда руб.
Принимая тарифную ставку по 4-му разряду получим
Sзп1=888×8×14=9945 руб.
Накладные расходы включают в себя затраты на содержание административно-технического персонала ремонтных мастерских охрану труда и технику безопасности и прочие затраты связанные с обслуживанием парка машин. Эти затраты рекомендуется принимать в размере 10 % от затрат на амортизацию капитальный и текущий ремонт техническое обслуживание и 25 % от заработной платы рабочих занятых управлением машиной.
Sнакл=01(Sа+Sкр+Sтр)+025Sзп(4.29)
Для серийной машины:
Sнакл1=01(10992+12824+24732)+025×9945=51034 руб.
Для модернизированной машины:
Sнакл2=01(117025+136529+263305)+025×9945=54172 руб.
Подставляя полученные значения в формулу (4.17) определим стоимость машино-смены:
- для серийной машины:
Sсм1=162+10992+12824+24732+120906+17312+9945+51034=686297 руб;
- для модернизированной машины:
Sсм2=165+117025+136529+263305+120906+18431+9945+54172=721963 руб.
Годовая экономия определится по формуле
Эгод=(С1-С2)Пгод(4.30)
где С1 и С2 – себестоимость разработки 1 м3 грунта старой (эталонной) и новой машины руб.;
Пгод – годовая производительность новой машины м3.
Себестоимость разработки 1 м3 грунта:
где Sсм – стоимость машино-смены руб.;
Псм – сменная производительность машины м3.
для серийной машины: С1=6862974596=1493 руб.
для модернизированной машины: С2=721963985=733 руб.
Подставляя значения себестоимости разработки 1 м3 грунта в формулу (4.30) получим
Эгод=(1493-733) 147750=1122900 руб.
Срок окупаемости дополнительных капитальных вложений
где Тодк – срок окупаемости дополнительных капитальных вложений лет ТодкТн=8 лет;
Куд1 и Куд2 – удельные капитальные вложения по новой и сравнительной машинам руб.;
С1 и С2 – себестоимость разработки 1 м3 грунта старой и сравниваемой машины руб.;
Тн – нормативный коэффициент окупаемости капитальных вложений лет.
Годовой экономический эффект от внедрения новой техники
Эприв=[(С1+ЕнКуд1)-(С2+ЕнКуд2)]Пгод(4.33)
где С1 и С2 – себестоимость разработки 1 м3 грунта старой и сравниваемой машины руб.;
Ен – нормативный коэффициент сравнительной экономической эффективности капитальных вложений Ен=012.
Эприв=[(1493+012×199)-(733+012×99)]147750=1299904 руб.
Результаты расчетов технико-экономической эффективности внедрения новой техники сводим в таблицу 4.3.
Таблица 4.3. - Технико-экономические показатели эффективности дорожной фрезы агрегатируемой на тракторе ОМТЗ-82.1
Серийная дорожная фреза
Модернизированная дорожная фреза на тракторе ОМТЗ-82.1
Техническая производительность:
Затраты труда на разработку 1000 м3 грунта чел.-ч.
Снижение затрат труда %
Энергоемкость процесса кВт.чга
Снижение энергоемкости %
Металлоемкость процесса кгга
Снижение металлоемкости %
Капитальные вложения руб.
Удельные капитальные вложения на разработку 1 м3 грунта руб.
Стоимость машино-смены руб.
Себестоимость разработки 1 м3 грунта руб
Годовая экономия руб.
Срок окупаемости дополнительных капитальных вложений лет
Годовой экономический эффект от внедрения новой техники руб.
Вывод: произведенный сравнительный экономический анализ серийной фрезы МДФ-400Е и модернизированного фрезерного оборудования показал что применение гидропривода фрезы позволит повысить производительность труда на 533 %. Это позволит получить годовой экономический эффект в размере 1299904 рубля при сроке окупаемости дополнительных капитальных вложений равный 143 года.
введение.doc
От сложности дорожной сети и ее качества зависит эффективность использования автомобильного транспорта и безопасность дорожного движения.
Рост объемов дорожно-строительных работ требует не только дальнейшего укрепления производственной мощности дорожно-строительных организаций но и полного рационального использования техники существенного улучшения организации и технологии строительства.
Работы по строительству автомобильных дорог можно разделить на подготовительные строительно-монтажные заготовительные включающие работу производственных предприятий и складское хозяйство транспортные. Затраты труда и материальные ресурсы на разработку месторождений нерудных материалов переработку обогащение приготовление полуфабрикатов и изделий составляют около 50% от всех затрат на строительство автомобильной дороги.
Для строительства ремонта и содержания автомобильных дорог и сооружений применяют разнообразные природные и искусственные материалы. Природные строительные материалы добывают в местах их образования обычно в верхних слоях земной коры (например песок гравий). Искусственные строительные материалы изготавливают по специальной технологии из природного сырья или отходов промышленности из смеси разных материалов причем свойства исходных составляющих претерпевают физико-химические изменения в результате чего получается новый материал с новыми свойствами отличающийся от исходного сырья. Так после смешения и уплотнения смеси щебня песка цемента и воды и последующего отвердевания смеси получают цементобетон.
За последние годы были пересмотрены многие строительные нормы и правила государственные стандарты на материалы полуфабрикаты изделия правила производства работ и другие документы. Внедрены новые технологии скоростного строительства автомобильных дорог и новые высокопроизводительные комплекты дорожных машин и оборудования производственных предприятий.
Прогресс в области дорожно-строительных материалов способствовал повышению требований к ним а также применению новых материалов в частности - широкому использованию геотекстиля пластиковых георешеток щебеночно-мастичного асфальта и др.
Для работы с новыми материалами необходимо создание новых машин или модернизировать рабочие органы имеющихся.
В связи с этим целью дипломного проекта является разработка фрезерного рабочего оборудования для перемешивания грунта в теле дороге на базе трактора ОМТЗ-82.1
Рекомендуемые чертежи
- 22.07.2023