Расчет и выбор посадок для редуктора




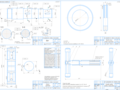
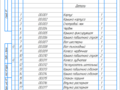
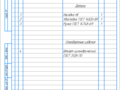
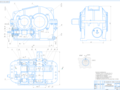
- Добавлен: 24.01.2023
- Размер: 1 MB
- Закачек: 2
Описание
Расчет и выбор посадок для редуктора
Состав проекта
![]() |
![]() ![]() ![]() |
![]() |
![]() |
![]() ![]() ![]() ![]() |
![]() |
![]() |
![]() ![]() ![]() ![]() |
![]() ![]() ![]() ![]() |
![]() ![]() ![]() ![]() |
![]() |
![]() ![]() ![]() |
![]() ![]() ![]() |
Дополнительная информация
Пояснительная_записка.docx
Качество продукции является движущей силой с помощью которой государство решает важнейшие экономические и политические задачи как внутри страны так и за ее пределами. От качества машин и оборудования зависят темпы технологического прогресса.
Важнейшим показателем качества деталей является точность изготовления их геометрических параметров. Полученные при обработке размер форма и взаимное расположение элементарных поверхностей определяют фактические зазоры и натяги в сопряжениях деталей а следовательно работоспособность и технико-экономическую эффективность изделий.
Точность и ее контроль являются одним из важнейших показателем качества и служат исходной предпосылкой организации взаимозаменяемого производства.
Взаимозаменяемость – основной принцип конструирования изготовления контроля эксплуатации машин.
Стандартизация – процесс установления и применение правил с целью упорядочения деятельности в данной области на пользу и при участии всех заинтересованных сторон для достижения всеобщей оптимальной экономии и соблюдением функциональных условий и требований безопасности.
Описание конструкции и назначение узла
Редукторы и мотор-редукторы служат для понижения частоты вращения выходного вала. В мотор-редукторах предусмотрены различные способы крепления фланцевого электродвигателя к корпусу редуктора.
Двигатель со встроенным червячным редуктором называют червячным мтор-редуктором.
Благодаря своей конструкции мотор-редукторы с червячной передачей характеризуются плавностью и бесшумностью работы. К достоинствам червячного мотор-редуктора также можно отнести компактность — червячный мотор-редуктор будет значительно меньшего размера по сравнению с аналогичным мотор-редуктором с зубчатой передачей с одним и тем же передаточным числом редуктора. Характерной особенностью червячного мотор-редуктора является свойство самоторможения.
Для сборки предусмотрено отверстие в цельном корпусе редуктора к которому через переходный стакан-крышку прикреплен фланцевый электродвигатель. Вал электродвигателя соединен с входным валом редуктора упругой компенсирующей муфтой. Червяк нарезан на входном валу на котором с натягом посажены роликовые радиально-упорные конические подшипники по схеме враспор. "Осевую игру" подшипников регулируют набором металлических прокладок под крышкой и под стаканом-крышкой опор входного вала. На выходной вал установлены с натягом червячное колесо и роликовые радиально-упорные конические подшипники по схеме враспор. Собранный выходной вал вставлен в корпус через отверстия и закрыт большими боковыми крышками. Для регулировки подшипников и червячного зацепления имеется набор металлических прокладок под малыми крышками опор вала червячного колеса.
Расчет и выбор посадки с зазором
Рассчитать и выбрать из числа предпочтительных посадок системы отверстия посадку для подшипника скольжения по следующим исходным данным:
номинальный диаметр сопряжения d = 130 мм;
частота вращения вала n = 1000 мин-1;
нагрузка на опору R = 9 кН;
марка смазочного масла: Турбинное-46;
шероховатость поверхности втулки RzD = 32 мкм;
шероховатость поверхности вала Rzd = 16 мкм;
материал втулки – сталь 30; вала – чугун.
Для выбранной посадки построить схемы полей допусков определить наибольшие и наименьшие предельные размеры отверстия и вала наибольший и наименьший зазор. Выполнить эскизы деталей и эскиз сборочного чертежа соединения.
Рассчитываем угловую скорость вращения вала радс по формуле
Определяем среднее удельное давление P Нм2 по формуле
Устанавливаем допустимую минимальную толщину масляного слоя h м по формуле
=2(32×10-6+16×10-6+3×10-6)= 156 × 10-6 м.
Определяем динамическую вязкость масла Па×с по формуле
где m – табличная динамическая вязкость масла при температуре
t = 50 °С для масла турбинного-46 m = 004 Па×с; tп – температура нагрева подшипника в масле принимаем tп = 65 °С.
Определяем функциональный комплекс по формуле
По графику по величине функционального комплекса Ah = 007 и отношению c2 = 091. Поскольку c103 определяем функциональный комплекс для c1=03 .
Рассчитываем минимальный допустимый зазор мкм по формуле
= = 195274×10-6 м = 195 мкм.
Определяем температурное изменение зазора м по формуле
=130×10-3(126×10-6–110×10-6)(65 – 20) = 936 × 10-6 м
где a1 a2 – температурные коэффициенты линейного расширения материалов втулки и вала соответственно определяем для стали 30 a1 = 126 × 10-6 град -1; для чугуна a2 = 110 × 10-6 град -1.
Рассчитываем минимальный действующий зазор мкм по формуле
= 195274×10-6936 × 10-6 = 185914×10-6 м = 186 мкм.
Рассчитываем максимальный допустимый зазор мкм по формуле
= = 34667× 10-6 м = 346 мкм.
Вычисляем максимальный действующий зазор мкм по формуле
=34667×10-6936×10-6 2(32×10-6 + 16×10-6)=32771×10-6 м = 328 мкм.
Выбираем по таблицам стандарта ГОСТ 25347 предельные зазоры Smin табл и Smax табл соблюдая условия:
Smin табл ³ Smin и Smax табл Smax.
Получаем Smin табл = 200 мкм и Smax табл = 303 мкм для посадки 130 мм.
Определяем предельные размеры втулки и вала:
наибольший предельный размер отверстия во втулке мм по формуле
= 130 + 0054 = 130054 мм;
наименьший предельный размер отверстия во втулке мм по формуле
наибольший предельный размер вала мм по формуле
= 130 – 02 = 1298 мм;
наименьший предельный размер вала мм по формуле
= 130 – 0263 = 129773 мм.
Строим схему расположения полей допусков выбранной посадки (Рисунок 2.1).
Рисунок 2.1. Схема расположения полей допусков посадки 130 мм
Выполняем эскизы втулки вала и сборочного чертежа соединения (Рисунок 2.2).
Рисунок 2.21. Эскизы: а – вала; б – втулки; в – сборочного чертежа соединения:
Расчет и выбор посадки с натягом
Рассчитать и выбрать из системы отверстия посадку с натягом желательно предпочтительного применения по следующим исходным данным:
диаметр сопряжения d = 20 мм;
наружный диаметр втулки d2 = 50 мм;
передаваемый крутящий момент Мкр = 500 Нм;
материал втулки и вала – сталь 40;
диаметр осевого отверстия d1 = 0;
осевое усилие Р = 0;
шероховатость поверхности втулки RzD = 6.3 мкм; вала Rzd = 32 мкм.
Для выбранной посадки определить предельные размеры отверстия и вала наибольший и наименьший натяги построить схему полей допусков. Выполнить эскизы вала и втулки эскиз сборочного чертежа соединения.
Определяем величину удельного контактного эксплуатационного давления рэ между сопрягаемыми поверхностями вала и втулки принимая коэффициент запаса прочности n = 1.5 – 2.0:
Определяем характер деформирования отверстия и вала по графику деформаций и величинам pэ т d d2. Предел текучести для стали 40 т=333108 Па.
Для pэ т = = 019 и d d2 = = 04 получаем что вал и втулка испытывают упругие деформации.
По графику деформаций определяем наибольшее допустимое значение pнб т на границе допустимой зоны деформирования pнб т = 049.
Рассчитываем соответствующее значение удельного контактного давления pнб = 049 т = 049 333108 = 163108 Па.
Определяем коэффициент неравномерности распределения удельного давления c по отношению l d = 0.060 0.020 = 3 получаем c = 092.
Рассчитываем наибольшее для этого коэффициента значение удельного давления:
pнб.доп = pнб c (3.2)
pнб.доп = 163108 092 = 15 108 Па.
Определяем коэффициенты формы отверстия:
где и – коэффициенты Пуассона для материала втулки и вала соответственно = = 03.
Рассчитываем величину максимального допустимого натяга:
Nmaxдоп = pнб.доп(3.5)
Nmaxдоп =1.5108 = 3610-6 м = 36 мкм
где и – модуль упругости материалов втулки и вала соответственно = = 21011 Па.
Определяем величину минимального допустимого натяга:
Nminдоп = 66348106 = 15910-6 м = 159 мкм.
Рассчитываем поправку на смятие микронеровностей сопрягаемых поверхностей:
= 2(056310-6 + 053210-6) = 9510-6 м = 95 мкм
где K1 и K2 – коэффициент учитывающий поправку на смятие микронеровностей поверхности втулки и вала соответственно K1 = K2 = 05.
Определяем предельные расчетные натяги:
Nmaxр = Nmaxдоп + ш(3.8)
Nmaxр = 3610-6 + 9510-6 = 45510-6 м = 455 мкм
Nminр = Nminдоп + ш(3.9)
Nminр = 15910-6 + 9510-6 = 25410-6 м = 254 мкм.
Выбираем стандартную посадку выполняя условия Nmaxр ≥ Nmaxтабл и Nminр Nminтабл где Nmaxтабл и Nminтабл – максимальный и минимальный табличные натяги соответственно.
Выбираем посадку наиболее близкую к указанным условиям:
Табличные натяги равны:
максимальный Nmaxтабл = es – EI
минимальный Nminтабл = ei – ES
Nmaxтабл = 0.041 – 0.021 = 0.020 мм.
Строим схему расположения полей допусков выбранной посадки (Рисунок 3.1).
Рисунок 3.1. Схема расположения полей допусков посадки 20 мм
Рисунок 3.2. Эскизы: а – вала; б – втулки; в – сборочного чертежа
Расчет и выбор посадок подшипника качения
Целью решения задачи является ознакомление с методикой назначения посадок контрдеталей с подшипниками качения.
Рассчитать и выбрать из числа стандартных посадок посадки для внутреннего и наружного колец подшипника качения по следующим исходным данным:
шарикоподшипник № 206;
радиальная реакция опоры R = 7 кН;
Осевое усилие А= 0 Н;
условия работы: вращается вал корпус неподвижен; корпус неразъемный стальной;
dотв.d = 0.5; DDкорп = 0.75 (dотв – диаметр отверстия полого вала мм; Dкорп – диаметр отверстия тонкостенного корпуса мм);
нагрузка с сильными толчками и вибрациями. Перегрузка до 300%.
Построить схемы полей допусков выбранных посадок с соответствующими отклонениями. Определить усилие запрессовки подшипника. Сделать эскиз сборочного чертежа с указанием посадок.
Определяем геометрические параметры подшипника качения № 206:
внутренний диаметр d = 30 мм;
наружный диаметр D = 62 мм;
радиус закругления r = 15 мм.
Рассчитываем интенсивность нагружения Нм по формуле
где Kп – динамический коэффициент посадки при перегрузке до 150 % умеренных точках и вибрации Kп = 18; F – коэффициент учитывающий степень ослабления посадочного натяга при полом вале и тонкостенном корпусе для dотвd=0.5 и Dd= 6230 = 2067 F = 16; FA – коэффициент учитывающий неравномерность распределения радиальной нагрузки для радиального однорядного шарикоподшипника FA = 1.
Выбор квалитета для посадок колец подшипников проводится в зависимости от класса точности самого подшипника. Выбранный квалитет представлен в таблице 4.1:
Рекомендуемые квалитеты для сопрягаемых деталей
По величине интенсивности нагружения выбираем поле допуска вала m5. Посадка вала во внутреннее кольцо подшипника 30 мм.
Для местно нагруженного наружного кольца подшипника с учетом того что корпус является неразъемным и перегрузка до 300 % выбираем поле допуска для корпуса Js6 и получаем посадку 62 мм.
Определяем отклонения для колец подшипника для вала и корпуса и строим схемы полей допусков.
Посадка вал – внутреннее кольцо подшипника:
наибольший табличный натяг:
наименьший табличный натяг:
Nmin = ei – ES = 0.009 – 0 = 0009 м = 9 мкм следовательно появляется зазор в сопряжении.
Посадка внешнее кольцо подшипника – корпус:
наибольший табличный зазор:
наименьший табличный зазор:
Smin = EI – es = – 00095 – 0 = –00095 м = – 95 мкм.
Схемы полей допусков показаны на рисунке 4.1
Рисунок 4.1. Схемы расположения полей допусков:
а – посадки 30 мм; б – посадки 62 мм
Определяем минимальный допустимый натяг в сопряжении вал – внутренне кольцо подшипника:
= = 0.018 мм = 18 мкм
где K – конструктивный фактор ; d0 – приведенный диаметр внутреннего кольца для подшипника № 206 = 30 + (62–30)4=38мм K= 1 [1 – (30 38)2] = 2.654.
Условие Nmin ³ Uminдоп не выполняется поскольку в полученной посадке Nmin = 8 мкм. Введем поправку на шероховатость:
где и – шероховатость отверстия и вала соответственно 063 = 125.
Условие Nmin ³ Uminдоп выполняется.
Определяем максимально допустимый натяг:
где [s] – предел прочности шарикоподшипниковой стали [s] = 400 Нмм2.
Условие Nmax Umaxдоп выполняется т.к. 26 мкм 110 мкм.
Проверяем наличие посадочного рабочего зазора:
Gр = 0.017 – 0.012 = 0.005 м
где Gн – начальный радиальный зазор в подшипнике
Dd – поправка на приведенный диаметр внутреннего кольца ; Uэф – эффективный натяг = 085 (0.026 + 0.009) 2 = 0.015 мм
Dd = 0015 × 30 38 = 0.012 мм.
Поскольку Gр > 0 то условие выполняется в сопряжении имеется посадочный рабочий зазор.
Определяем усилие запрессовки подшипника на вал:
где – коэффициент трения при запрессовке принимаем = 012; Е – модуль упругости стали Е = 2 × 1011 Па.
Определяем температуру нагрева подшипника в масле для установки его на вал:
где Sсб – сборочный зазор равный Sсб = 0003 мм; a – температурный коэффициент линейного расширения подшипниковой стали a = 12 × 10-6 °С-1.
Расчет рабочих и контрольных калибров
Предельные калибры для контроля гладких цилиндрических деталей выполняются в виде пробок и скоб. Для контроля каждого размера необходимо иметь два предельных калибра – проходной (ПР) и непроходной (НЕ). На изготовление таких калибров как и на изготовление деталей задается величина допуска. Валы и отверстия с допусками точнее IT6 проверять калибрами не рекомендуется.
Построение полей допусков калибров-пробок и калибров-скоб а также расчет их размеров производится для одного сопряжения по указанию преподавателя.
Порядок построения полей допусков сопряжения деталей с посадкой 130 мм.
По таблицам допусков на гладкие цилиндрические соединения ГОСТ 25347-82 определяем величины отклонений:
отверстия 130 H7: ES = + 0054 мм; ЕI = 0 мм;
вала 130 с8: es = – 02 мм; ei = – 0263 мм. Строим поля допусков этих деталей.
Рисунок 5.1. Схема расположения полей допусков посадки 130 мм
Размечаем нулевые линии для построения полей допусков калибров:
Нулевая линия поля допуска проходной стороны калибра-пробки 130000мм. Нулевая линия поля допуска проходной стороны 130054;
Нулевая линия поля допуска проходной стороны калибра-кольцо 129800мм. Нулевая линия поля допуска проходной стороны 129737 мм;
По таблицам допусков на калибры (ГОСТ 24853-81) выбираем отклонения:
- отклонение середины поля допуска на изготовление проходного калибра для отверстия относительно Dm
- допустимый выход размера изношенного проходного калибра для отверстий за границу поля допуска Y мм Y = 4 мкм = 0004 мм;
- допуск на изготовление калибра для отверстий Н мм Н = 6 мкм = 0006мм.
- отклонение середины поля допуска на изготовление проходного калибра для контроля валов Z1 мм Z1 = 8 мкм = 0008 мм;
- допустимый выход размера изношенного проходного калибра для валов за границу поля допуска Y1 мм Y1 = 6 мкм = 0006 мм;
- допуск на изготовление калибров для контроля валов Н1 мм Н1 = 6 мкм = 0006 мм;
- допуск контрольного изношенного калибра для валов Нр мм Нр = 4 мкм = 0004 мм;
Поля допусков калибров строятся от соответствующих нулевых линий. Участок износа штрихуется вертикальными линиями.
Рисунок 5.2. Схема расположения поля допуска отверстия и полей допусков
Рисунок 5.3. Схема расположения поля допуска вала и полей допусков
Рассчитываем предельные размеры калибров:
- наибольший размер проходной новой калибр-пробки Р-ПРmаx мм:
Р-ПРmаx= Dmin + Z + H2(5.1)
- наименьший размер проходной новой калибр-пробки Р-ПРmin мм:
Р-ПРmin= Dmin + Z - H2(5.2)
- наибольший размер непроходной калибр-пробки Р-НЕmax мм:
Р-НЕmax = Dmax + H2(5.3)
- наименьший размер непроходной калибр-пробки Р-НЕmin мм:
Р-НЕmin = Dmax – H2(5.4)
- размер изношенной проходной калибр-пробки Р-ПРизн мм:
Р-ПРизн = Dmin – Y(5.5)
Р-ПРизн = 130 – 0004 = 129996 мм.
наибольший размер проходной новой калибра-кольца Р- ПРmax мм:
Р-ПРmax= dmax – Z1 + H2(5.6)
- наименьший размер проходной новой калибра-кольца Р- ПРmin мм:
Р-ПРmin= dmax – Z1 – H2(5.7)
- наибольший размер изношенной проходной калибра-кольца Р- ПРизн мм:
Р-ПРизн = dmax +Y1(5.8)
Р-ПРизн = 129800 + 0006 = 129806 мм;
- наибольший размер непроходной калибра-кольца Р- НЕmax мм:
Р-НЕmax= dmin + H12(5.9)
- наименьший размер непроходной калибра-кольца Р- НЕmin мм:
Р-НЕmin= dmin - H12(5.10)
Определяем предельные размеры контрольных калибров:
К-ПРmax = dmax - Z1 + HP2(5.11)
К-ПРmin= dmax - Z1- HP2(5.12)
К-НЕmax =dmin + HP2(5.13)
К-НЕmin = dmin - HP2(5.14)
K-ИЗНmax = dmax +Y1 + HP2(5.15)
K-ИЗНmin = dmax + Y1 - HP2(5.16)
K-ИЗНmin = 129800 + 0006 – 00042 = 129804 мм.
Предельные размеры калибров представлены в таблице 5.1.
Предельные размеры калибров мм
Проходная сторона новая
Проходная сторона изношенная
Определяем исполнительные размеры калибров для простановки их на чертежах:
Р-ПРисп = (Р-ПРmax) +Н = 130009+0006 мм
Р-ПРисп = (Р-ПРmin) -H = 129789-0.006 мм
Р-НЕисп=( Р-НЕmin) -H =129734-0.006 мм.
1. Выбор степеней точности и расчет бокового зазора зубчатой передачи
Назначить степень точности зубчатого колеса по трем видам норм: кинематической точности плавности работы контакта зубьев; рассчитать гарантированный минимальный боковой зазор:
- число зубьев ведущего колеса Z1 = 40;
- число зубьев ведомого колеса Z2 = 36;
- окружная скорость колес Vокр = 13 мс;
- модуль зубчатой передачи m = 5 мм;
- ширина колеса В = 120 мм;
- рабочая температура колеса и корпуса: tкол = 75°C tкорп = 55°C;
- материал корпуса и колес: сталь 40Х;
- вид передачи: силовой редуктор.
По величине скорости Vокр мс выбираем степени точности зубчатой передачи и затем корректируем по виду передачи .
Выбираем степень точности (по нормам плавности) 7. Для скоростных передач норма контакта принимается на одну степень ниже 8 по нормам кинематической точности 7.
Определяем межосевое расстояние aw мм по формуле
где aw – межосевое расстояние мм;
Z1 – число зубьев ведущего колеса Z1 = 40;
Z2 – число зубьев ведомого колеса Z2 = 36;
m – модуль зубчатой передачи мм m = 5 мм;
Определяем температурную компенсацию зазора jn1 мм и оптимальную толщину слоя смазки jn2 мкм по формуле
jn1 = a[α1 (tкол - 20C) – α2 (tкорп - 20C)] 2sin α (6.2)
где jn1 - часть бокового зазора на температурную компенсацию мм;
α1 и α2 – температурный коэффициент линейного расширения материала ведущего и ведомого колеса соответственно град-1 α1 = 11810-6 град-1 α2 =11810-6 град-1 ;
tкол – температура колес С tкол = 75 С;
tкорп – температура корпуса С tкорп = 55 С;
α - угол зацепления ведущего колеса α = 20;
jn1 = 190[11810-6 (75 - 20) – 11810-6(55 - 20)]2 sin 20 = 0082 мм
jn2 = 30·5 = 150 мкм.
Определяем минимальный боковой зазор передачи jnmin мкм по формуле
jnmin = jn1 + jn2 (6.4)
jnmin = 82 + 150 = 232 мкм.
По [2] выбираем вид сопряжения.
Таким образом степень точности передачи 5 – 6 – 5 В ГОСТ 1643-81.
2. Выбор измерительных средств для контроля комплексов
Стандарт на допуски зубчатых колес и передач (ГОСТ 1643-81) предусматривает для каждой нормы точности ряд показателей . Однако на основании многолетнего опыта работы каждый вид машиностроения разрабатывает свои рекомендации по выбору комплексов контролируемых параметров. Для химического и пищевого машиностроения эти рекомендации приведены в работе по которой и следует подбирать комплексы для контроля зубчатых колес. Измерительные средства для контроля каждого комплекса выбираются с учётом степени точности и основных характеристик колес по справочным данным .
Выбрать для контролируемых параметров средства их измерений.
По таблице определяем контролируемые параметры:
) нормы кинематической точности при степени точности 5:
- наибольшая кинематическая погрешность колеса Fi' определяемая по формуле:
- колебания длины общей нормали FW ;
- рекомендуемая погрешность шага Fр ;
- накопленная погрешность k шагов Fрk ;
) нормы плавности при степени точности 6:
- отклонение шага зацепления
- погрешность профиля ;
) норма контакта зубьев при степени точности 5:
- погрешность направления зуба F ;
) нормы бокового зазора при виде сопряжения А:
- наименьшее дополнительное смещение исходного контура Ане;
- допуск на смещение исходного контура Тн ;
Значения данных параметров определяем исходя из величины диаметров делительной окружности колеса и шестерни d1 d2 мм которые определяются по формулам
Значения контролируемых параметров для шестерни и колеса представлены в таблице 6.1.
Для шестерни Z1 = 36
погрешность Fi' = 33 мкм
Рекомендуемая погрешность шага
Рекомендуемая погрешность шага
Накопленная погрешность k шагов Fpk = 22 мкм
Отклонение шага зацепления
Погрешность направления зуба
Наименьшее дополнительное смещение исходного контура
Допуск на смещение исходного контура Тн =90 мкм
Допуск на смещение исходного контура Тн =90 мкм
Средства измерения зубчатых колес указаны в таблице 6.2.
Обозначение контролируемого параметра
Наименование измерительного прибора
БВ-5058 для контроля кинематической погрешности
БВ – 5056 для автоматического контроля накопленной погрешности k – шагов шага по колесу
БВ – 5061 цехового типа для контроля
БВ – 5070 универсальный
Универсальный эвольвентомер с участком для контроля винтовой линии (с ходомером) БВ - 5062
Нормалимер НЦ 23500-23800
Расчет допусков на элементы резьбового соединения
1. Для резьбового соединения M10 – 7H7g6g определить допуски предельные отклонения размеры и зазоры. Начертить схемы полей допусков для основных диаметров резьбы.
Определяем основные размеры гайки и болта М10 с крупным шагом по ГОСТ 8724-2002 и 24705-2004 Р = 15 мм:
наружный диметр резьбы d = D = 10 мм;
средний диаметр резьбы d2 = D2 = 9026 мм;
внутренний диаметр резьбы d1 = D1 = 9.376 мм.
Поля допусков для наружной резьбы заданы: по среднему диаметру d2 –7g и по наружному диаметру d – 6g по внутреннему диаметру d1 допуск не устанавливается. Для внутренней резьбы: по среднему диаметру D2 и по внутреннему диаметру D1 – 7H по наружному диаметру D допуск не устанавливается.
Определяем предельные отклонения для диаметров наружной и внутренней резьбы рассчитываем допуски и записываем их в виде таблицы 7.1.
Предельные отклонения мкм
Определяем предельные размеры и предельные зазоры в посадке:
Для наружной резьбы:
dmax = 10 – 0032 = 9968 мм
d2 max = d2 + es (7.3)
d2 max = 9026 – 0032 = 8.994 мм
d2 min = d2 + ei(7.4)
d1 max = d1 + es (7.5)
d1 max = 9.376 – 0032 = 9.344 мм
d1 min не нормируется.
Для внутренней резьбы:
D2 max = D2 + ES (7.6)
D2 max = 9026 + 0236 = 9.262 мм
D1 max = D2 + ES (7.7)
D1 max = 9.376 + 0375 = 9.751 мм
Предельные зазоры резьбовой посадки:
для наружного диаметра:
Smin = Dmin – dmax (7.8)
для среднего диаметра:
Smin = D2 min – d2 max(7.9)
Smin = 9.026 – 8.994 = 0032 мм = 32 мкм
Smax = D2 max – d2 min(7.10)
для внутреннего диаметра:
Smin = D1 min – d1 max(7.11)
Smin = 9.376 – 9.344 = 0032 мм = 32 мкм.
Схемы полей допусков резьбового соединения M10 – 7H7g6g изображены на рисунке 7.1
Рисунок 7.1. Схема полей допусков резьбового соединения M10 – 7H7g6g
2. Для резьбового соединения M12 – 6H6g определить допуски предельные отклонения размеры и зазоры. Начертить схемы полей допусков для основных диаметров резьбы.
Определяем основные размеры гайки и болта М12 с крупным шагом по ГОСТ 8724-2002 и 24705-2004 Р = 10 мм:
наружный диметр резьбы d = D = 12 мм;
средний диаметр резьбы d2 = D2 = 11350 мм;
внутренний диаметр резьбы d1 = D1 = 11918 мм.
Поля допусков для наружной резьбы заданы: по среднему диаметру d2 и по наружному диаметру d – 6g по внутреннему диаметру d1 допуск не устанавливается. Для внутренней резьбы: по среднему диаметру D2 и по внутреннему диаметру D1 – 6H по наружному диаметру D допуск не устанавливается.
Определяем предельные отклонения для диаметров наружной и внутренней резьбы рассчитываем допуски и записываем их в виде таблицы 7.2.
dmax по формуле (7.1)
dmax = 12 – 0026 = 11974 мм
dmin по формуле (7.2)
d2 max по формуле (7.3)
d2 max = 11350 – 0026 = 11324 мм
d2 min по формуле (7.4)
d1 max по формуле (7.5)
d1 max = 11918 – 0026 = 11892 мм
D2 max по формуле (7.6)
D2 max = 11350 + 0160 = 11550 мм
D1 max по формуле (7.7)
D1 max = 11918 + 0236 = 12154 мм
Smin по формуле (7.8)
Smin по формуле (7.9)
Smin = 11350 – 11324 = 0026 мм = 26 мкм
Smax по формуле (7.10)
Smin по формуле (7.11)
Smin = 11918 – 11892 = 0026 мм = 26 мкм.
Схемы полей допусков резьбового соединения M12 – 6H6g изображены на рисунке 7.2
Рисунок 7.2. Схема полей допусков резьбового соединения M12 – 6H6g
3. Для резьбового соединения M10 – 7H8g определить допуски предельные отклонения размеры и зазоры. Начертить схемы полей допусков для основных диаметров резьбы.
Определяем основные размеры гайки и болта М10 с крупным шагом по ГОСТ 8724-2002 и 24705-2004 Р = 10 мм:
средний диаметр резьбы d2 = D2 = 9188 мм;
внутренний диаметр резьбы d1 = D1 = 9674 мм.
Поля допусков для наружной резьбы заданы: по среднему диаметру d2 и по наружному диаметру d – 8g по внутреннему диаметру d1 допуск не устанавливается. Для внутренней резьбы: по среднему диаметру D2 и по внутреннему диаметру D1 – 7H по наружному диаметру D допуск не устанавливается.
Определяем предельные отклонения для диаметров наружной и внутренней резьбы рассчитываем допуски и записываем их в виде таблицы 7.3.
dmax = 10 – 0026 = 9974 мм
d2 max = 9188 – 0026 = 9162 мм
d1 max = 9674 – 0026 = 9648 мм
D2 max = 9188 + 0190 = 8998 мм
D1 max = 9674 + 0300 = 9374 мм
Smin = 9188 – 9162 = 0026 мм = 26 мкм
Smin = 9674 – 9648 = 0026 мм = 26 мкм.
Схемы полей допусков резьбового соединения M10 – 7H8g изображены на рисунке 7.3
Рисунок 7.3. Схема полей допусков резьбового соединения M10 – 7H8g
Выбор посадок для сборочного соединения и их расчет
В соответствии с заданием на курсовую работу необходимо назначить посадки для десяти сопряжений сборочной единицы. В них обязательно должны войти:
а) сопряжения по размерам подшипника качения;
б) резьбовое сопряжение по трем параметрам;
в) три сопряжения шпоночного соединения.
Результаты выбора посадок представляются в виде таблицы 8.1
Выбранные посадки по ГОСТ 25347-82
Болт – крышка корпуса
Червяк – втулка распорная
Вал – колесо червячное
Вал – колесо зубчатое
Посадки для двух сопряжений подшипника качения выбираются по расчетам. В этих сопряжениях поля допусков самих подшипников обозначаются буквами «L» и «l» в сочетании с номером класса точности подшипника.
Для резьбового сопряжения посадки выбираются в зависимости от назначения и длины свинчивания а для шпоночного (по ширине b) – в зависимости от типа соединения. Для резьбового соединения привести расчет и построить поля допусков по наружному среднему и внутреннему диаметрам. Для других сопряжений выбор посадок производится по методу прецедентов или по методу подобия.
Расчет выбранных посадок оформляем в таблицу 8.2.
Номера сопрягаемых деталей
Номинальный размер с отклонениями
Предельные размеры мм
Продолжение таблицы 8.2
Окончание таблицы 8.2
Выбор средств измерения деталей
Выбор измерительных средств осуществляется с учётом допускаемой погрешности измерений а также предельной погрешности измерительных средств. Значение допускаемой погрешности измерения изм зависит от величины допуска на изготовление изделия IT который в свою очередь связан с номинальным размером и квалитетом. Для размеров от 1 до 500 ГОСТ 8051-81 устанавливает 15 рядов наибольших допускаемых погрешностей измерения в зависимости от величины допуска .
При выборе средств измерения необходимо назначить такое средство измерения предельная погрешность которого (пр) не превышала была бы изм то есть призм. Для выбранного средства измерения по справочным данным следует установить его основные метрологические характеристики: пределы измерения цену деления.
Характеристики измерительных средств оформляются в виде таблице 9.1.
Пределы измерений мм
Комплексный резьбовой калибр-кольцо ГОСТ 22110-80
Комплексный резьбовой калибр-пробка ГОСТ 22110-80
Продолжение таблицы 9.1
Нутромер индикаторный ГОСТ 868-72
Скоба рычажная ГОСТ 11098-75
Окончание таблицы 9.1
Нутромер микрометрический
Микрометр гладкий ГОСТ 6507-78
Расчет размерной цепи вероятностным методом
Вычертить в векторном изображении размерную цепь узла коробки скоростей. Выполнить вероятностный расчет размерной цепи при ограниченной взаимозаменяемости: определить допуски составляющих звеньев и возможный процент брака при сборке.
Исходные данные для расчета представлены в таблице 10.1.
размеры составляющих звеньев мм
Где РВ – равной вероятности Н – нормальный РТ – закон распределения равнобедренного треугольника (закон Симпсона).
Рисунок 10.1. Векторное изображение размерной цепи
Отклонения замыкающего звена АΣ:
верхнее отклонение ES(АΣ) = +08 мм;
нижнее отклонение EI(АΣ) = - 08 мм.
Определяем допуск замыкающего звена мкм по формуле
Определяем номинальный размер замыкающего звена мм по формуле
Для каждого номинального размера составляющих звеньев (кроме замыкающего) определяем значение единицы допуска i мкм. В зависимости от закона распределения определяем значение коэффициента относительного рассеивания для каждого звена . В зависимости от процента брака определяем для каждого звена добавочный множитель t – коэффициент риска.
Результаты расчета средней точности цепи представляем в виде таблицы 10.2
Определяем значение среднего коэффициента точности цепи aср по формуле
По полученному значению аср для звеньев размерной цепи выбираем квалитет – IT13.
Производим расчет вероятностного допуска исходного звена.
По выбранному квалитету с табличным коэффициентом а определяем допуски составляющих звеньев ТАi мкм находим вероятностный допуск замыкающего звена результаты расчетов заносим в таблицу 10.3
Проверяем выполнение условия ;
9722 мкм 1600 мкм. Условие выполнено.
Находим среднее отклонение замыкающего звена мкм по формуле
Т.к = 0 то полученные допуски разбиваем на симметричные отклонения.
Проверяем выполнение обязательного условия
Вычисляем выход годных деталей при сборке узла.
Среднее квадратичное отклонение замыкающего звена мкм вычисляем по формуле
Границы нового допуска X мкм вычисляем по формуле
Пределы интегрирования расчетного вероятностного допуска Z определяем по формуле
Вероятность изготовления годных деталей P вычисляем по формуле
где Ф(Z) – интеграл функции Лапласа значение которого определяем по прил. Ф(Z)=04886.
Процент годных деталей П % определяем по формуле
Процентное содержание бракованных деталей Б % определяем по формуле
В ходе выполнения данной курсовой работы были освоены методики назначения параметров и контролируемых показателей стандартизированных норм точности гладких цилиндрических и нецилиндрических соединений.
Курсовая работа выполнена в соответствии с индивидуальным заданием включающим сборочный чертеж соединения – редуктора комбинированного исходные данные для расчета и назначения посадок подшипников качения посадок для десяти сопряжений. Также в ходе работы расчетным путем определены посадка с зазором и посадка с натягом рассчитаны предельные исполнительные размеры гладкого калибра-пробки и гладких калибра-кольца. Были назначены степени точности и рассчитан боковой зазор зубчатой передачи выбраны средства контроля зубчатой передачи. В графическую часть работы вошли сборочный чертеж редуктора чертеж зубчатого колеса вала калибра-пробки и калибра-кольца.
Перечень стандартов на курсовую работу
ГОСТ 2.307-68 ЕСКД. Нанесение размеров и предельных отклонений.
ГОСТ 2.308-79 ЕСКД. Указание на чертежах допусков формы и расположений.
ГОСТ 2.309-73 ЕСКД. Обозначение шероховатости поверхностей.
ГОСТ 2.403-75 ЕСКД. Правила выполнения чертежей цилиндрический зубчатых колес.
ГОСТ 25346-89 ЕСДП. Основные нормы взаимозаменяемости. Общие положения ряды допусков и основных отклонений.
ГОСТ 25347-89 ЕСДП. Поля допусков и рекомендуемые посадки.
ГОСТ 6636-69 Основные нормы взаимозаменяемости. Нормальные линейные размеры.
ГОСТ 23360-78 Основные нормы взаимозаменяемости. Соединения шпоночные с призматическими шпонками. Размеры шпонок и сечений пазов. Допуски и посадки.
ГОСТ 24071-80 Основные нормы взаимозаменяемости. Соединения шпоночные с сегментными шпонками. Размеры шпонок и сечений пазов. Допуски и посадки.
ГОСТ 1139-80 Основные нормы взаимозаменяемости. Соединения шлицевые прямобочные. Размеры и допуски.
ГОСТ 27284-87 Калибры. Термины и определения.
ГОСТ 27851-81 Калибры гладкие для цилиндрических отверстий и валов. Виды.
ГОСТ 24853-71 Калибры гладкие для размеров до 500 мм. Допуски.
ГОСТ 11708-82 Основные нормы взаимозаменяемости. Резьба. Термины и определения.
ГОСТ 24705-81 Основные нормы взаимозаменяемости. Резьба метрическая. Основные размеры.
ГОСТ 8724-81 Основные нормы взаимозаменяемости. Резьба метрическая. Диаметры и шаги.
ГОСТ 16093-81 Основные нормы взаимозаменяемости. Резьба метрическая. Допуски. Посадки с зазором.
ГОСТ 24834-81 Основные нормы взаимозаменяемости. Резьба метрическая. Переходные посадки.
ГОСТ 4608-81 Основные нормы взаимозаменяемости. Резьба метрическая. Посадки с натягом.
ГОСТ 3478-79 Подшипники качения. Основные размеры.
ГОСТ 3325-85 Подшипники качения. Поля допусков и технические требования к посадочным поверхностям валов и корпусов. Посадки.
ГОСТ 1643-81 Основные нормы взаимозаменяемости. Передачи зубчатые цилиндрические. Допуски.
ГОСТ 25142-82 Шероховатость поверхности. Термины и определения.
ГОСТ 2789-73 Шероховатость поверхности. Параметры и характеристики.
ГОСТ 24643-81 Основные нормы взаимозаменяемости. Допуски формы и расположения поверхностей. Числовые значения.
ГОСТ 14140-81 Основные нормы взаимозаменяемости. Допуски расположения сей отверстий для крепежных деталей.
ГОСТ 16319-80 Цепи размерные. Термины и определения. Методы расчета.
Список используемой литературы
Допуски отверстий валов резьбы калибров [Текст] : справочные материалы к курсовой работе по дисциплине «Метрология стандартизация и сертификация» Воронеж гос. технол. акад.; сост. Н. Л. Клейменова Н. А. Ерофеева.- Воронеж : ВГТА 2008. - 40 с.
Расчет посадок с зазорами и натягами. Допуски и посадки подшипников качения. Выбор средств измерения. Допуски зубчатых передач [Текст] : справочные материалы к курсовой работе по дисциплине «Метрология стандартизация и сертификация» Воронеж гос. технол. акад.; сост. Н. Л. Клейменова Н. А. Ерофеева.- Воронеж : ВГТА 2008. - 36 с.
Руководство для выполнения курсовой работы для дисциплин «Метрология стандартизация и сертификация» «Взаимозаменяемость» [Текст] : учеб. пособие Г.В.Попов Н.Л.Клейменова Л.И.Назина Н.А.Ерофеева; Воронеж гос. технол. акад. – Воронеж: ВГТА. 2010. 68 с.
Анухин В.И. Допуски и посадки. Выбор и расчет указание на чертежах: Учеб.пособие. 2-е изд. перераб. и доп. СПб.: Изд-во СПбГТУ2001.219с.
Спецификация ред.spw

Крышка подшипника глухая
Маслоуказатель шомпольный
Крышка подшипника сквозная
Болт М10х38-7g6g ГОСТ 77805-70
Болт М12х260-6g ГОСТ 15589-70
Болт М10х16-8g ГОСТ 1198-70
Гайка М10-7g6g ГОСТ 15526-70
Гайка М12-6g ГОСТ 5915-70
Манжета ГОСТ 8752-79
Манжета ГОСТ 14896-84
Подшипник №206 ГОСТ 8338-75
Подшипник №305 ГОСТ 8338-75
Подшипник №207 ГОСТ 8338-75
Подшипник №205 ГОСТ 8338-75
Фланец плоский приводной ГОСТ 12820-80
Шайба пружинная 10 ГОСТ 6402-70
Шайба проужинная 12 ГОСТ 6402-70
Шайба уплотнительная 10 ГОСТ 11371-78
Комплекты принадлежностей
Калибр-пробка гладкий непроходной
Калибр-кольцо гладкий непроходной
Калибр-пробка.spw

Хвостовик ГОСТ 14820-89
Штифт цилиндрический
Редуктор 1.cdw

Вращающий момент на тихоходном валу
Частота вращения тихоходного вала
Передаточное число редуктора
Степень точности изготовления передачи
Коэффициент полезного действия
Радиальная консольная сила на тихоходном валу
КР-02068108-МСС-151000-27-2012-00.000
Вал, колесо, калибры.cdw

Остальные технические требования по ГОСТ 2015-84
Нормальный исходный контур
Коэффициент смещения
Допуск на радиальное биение зубчатого венца
Допуск на колебание длины общей нормали
Предельные отклонения шага зацепления
Допуск на погрешность профиля зуба
Допуск на направление зуба
Наименьшее дополнительное смещение исходного контура
Допуск на смещение исходного контура
Наибольшая кинематическая погрешность
Рекомендуемая погрешность шага
Накопленная погрешность k шагов
улучшение НВ 180 205
Острые кромки притупить R=0.3
Неуказанные предельные отклонения
размеров отверстий Н11
Надпись выполнять гравированием шрифтом 10 по ГОСТ 2.304-81
Неуказанные предельные отклонения размеров вала h14
Покрытие рабочих поверхностей - Хим.Фос.прм.
КР-02068108-МСС-151000-01.000
Сталь 40Х ГОСТ 4543-71
Рифление сетчатое Т1
КР-02068108-МСС-151000-27-2012-00
КР-02068108-МСС-151000-27-2012-00.008
Задания.docx
Расчет и выбор посадки с зазором.
номинальный диаметр сопряжения d = 130 мм;
частота вращения вала n = 1000 мин-1;
нагрузка на опору R = 9 кН;
марка смазочного масла: Турбинное-46;
шероховатость поверхности втулки RzD = 32 мкм;
шероховатость поверхности вала Rzd = 16 мкм;
материал втулки – сталь 30; вала – чугун.
Расчет и выбор посадки с натягом.
диаметр сопряжения d = 20 мм;
наружный диаметр втулки d2 = 50 мм;
передаваемый крутящий момент Мкр = 500 Нм;
материал втулки и вала – сталь 40;
диаметр осевого отверстия d1 = 0;
осевое усилие Р = 0;
шероховатость поверхности втулки RzD = 6.3 мкм; вала Rzd = 32 мкм.
Расчет и выбор посадок подшипника качения.
шарикоподшипник № 206;
радиальная реакция опоры R = 7 кН;
Осевое усилие А= 0 Н;
условия работы: вращается вал корпус неподвижен; корпус неразъемный стальной;
dотв.d = 0.5; DDкорп = 0.75 (dотв – диаметр отверстия полого вала мм; Dкорп – диаметр отверстия тонкостенного корпуса мм);
нагрузка с сильными толчками и вибрациями. Перегрузка до 300%.
Расчет рабочих и контрольных калибров:
- Калибр-пробка гладкий непроходной;
Выбор степеней точности и расчет бокового зазора зубчатой передачи
- число зубьев ведущего колеса Z1 = 40;
- число зубьев ведомого колеса Z2 = 36;
- окружная скорость колес Vокр = 13 мс;
- модуль зубчатой передачи m = 5 мм;
- ширина колеса В = 120 мм;
- рабочая температура колеса и корпуса: tкол = 75°C tкорп = 55°C;
- материал корпуса и колес: сталь 40Х;
- вид передачи: силовой редуктор.
Выбор измерительных средств для контроля комплексов зубчатых колес.
Расчет допусков на элементы резьбового соединения.
Выбор посадок для сборочного соединения и их расчет.
Выбор средств измерения деталей.
Расчет размерной цепи вероятностным методом.
размеры составляющих звеньев мм
Содержание.doc
Расчет и выбор посадки с зазором .6
Расчет и выбор посадки с натягом 10
Расчет и выбор посадок подшипника качения 14
Расчет рабочих и контрольных калибров 19
1. Выбор степеней точности и расчет бокового зазора зубчатой передачи ..24
2. Выборизмерительныхсредств дляконтроля комплексовзубчатых колес ..26
Расчет допусков на элементы резьбового соединения 29
Выбор посадок для сборочного соединения и их расчет ..36
Выбор средств измерения деталей ..41
Расчет размерной цепи вероятностным методом .44
Список используемой литературы 52