Расчет и выбор посадок редуктора




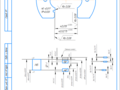
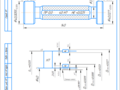
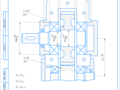
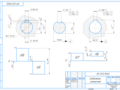
- Добавлен: 24.01.2023
- Размер: 433 KB
- Закачек: 0
Описание
Состав проекта
![]() |
![]() |
![]() ![]() ![]() ![]() |
![]() ![]() ![]() ![]() |
![]() ![]() ![]() ![]() |
![]() ![]() ![]() ![]() |
![]() ![]() ![]() ![]() |
![]() ![]() ![]() |
![]() ![]() ![]() ![]() |
Дополнительная информация
Шпоночное соединение.cdw

Подшипники.cdw

Зубчатое колесо.cdw

Калибр-пробка.cdw

Редукт.cdw

Калибр-скоба.cdw
