Расчет и выбор посадок стандартных соединений




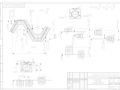

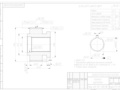

- Добавлен: 25.10.2022
- Размер: 606 KB
- Закачек: 0
Описание
Состав проекта
![]() |
![]() |
![]() ![]() ![]() ![]() |
![]() ![]() ![]() ![]() |
![]() ![]() ![]() ![]() |
![]() ![]() ![]() ![]() |
![]() ![]() ![]() ![]() |
![]() ![]() ![]() |
![]() ![]() |
![]() ![]() |
![]() ![]() |
![]() ![]() |
![]() ![]() |
![]() ![]() |
![]() ![]() |
![]() ![]() |
![]() |
![]() ![]() |
Дополнительная информация
Чертеж4.dwg

Сталь 40Х ГОСТ 1050-88
Неуказанные предельные отклонения размеров:
Острые кромки притупить
Нормальный исходный контур
Коэффициент смещения
Степень точности по ГОСТ 1643-81
Спецификация.dwg

Чертеж2.dwg

Схемы расположения полей допусков
для гладких цилиндрических соединений
и соединений с подшипником качения
Чертеж1.dwg

Чертеж3.dwg

Схемы расположения полей допусков
и шлицевого соединения
МИНИСТЕРСТВО ОБРАЗОВАНИЯ И НАУКИ.doc
Государственное образовательное учреждение высшего профессионального образования
«Курский государственный технический университет»
Кафедра «Метрология и сертификация»
по дисциплине «Метрология стандартизация и сертификация»
на тему «Расчет и выбор посадок стандартных соединений»
Специальность (направление подготовки) 260601 Машины и аппараты пищевой промышленности
Выбор и расчет посадок для гладких цилиндрических соединений
1 Аналитический расчет посадки с натягом 6
2 Выбор и расчет посадки с зазором . .9
3 Выбор и расчет переходной посадки 10
4 Выбор и расчет посадки с натягом 11
Выбор и расчет посадки резьбового соединения 13
Выбор и расчет посадки для шпоночного соединения 15
Выбор посадок для шлицевого соединения 16
Выбор и расчет посадок для соединений с подшипником качения 17
Определение комплекса контрольных параметров зубчатого
колеса по требованиям к точности изготовления . 20
Расчет размерной цепи методом максимум-минимум 23
Выбор средств измерений . 28
Обработка результатов измерений 29
Список использованных источников ..32
Приложение А Условные обозначения 33
Приложение Б Перечень графических материалов 34
Выбор и расчет посадок для гладких цилиндрических соединений
1 Аналитический расчет и выбор посадки с натягом
Рассчитаем и выберем посадку с натягом в соединении в котором:
1.1 По известным значениям внешней нагрузки (Rос) и размерам соединения (d и ) определяем требуемое эксплуатационное удельное давление (Па) на контактных поверхностях соединения из условия обеспечения прочности соединения по формуле 1.107 c.333 [1]:
где Мкр – крутящий момент стремящийся повернуть одну деталь относительно другой Н·м;
f – коэффициент трения при установившемся процессе распрессовки или проворачивания.
1.2 По полученному значению p min определяем необходимую величину наименьшего расчётного натяга Nmin (м) по формуле 1.110 c.334 [1]:
где Е1 и Е2 – модули упругости материалов соответственно охватываемой (вала) и охватывающей (отверстия) деталей в Нм2;
с1 и с2 – коэффициенты Ляме.
Предварительно определив коэффициенты Ляме (c1и c2) по формуле 1.111 c.333 [1]:
где d1- диаметр отверстия в вале (охватываемой детали);
d2 – наружный диаметр втулки (охватывающей детали);
и 2 – коэффициенты Пуассона соответственно для охватываемой и охватывающей деталей.
Для сплошного вала (d1=0) с1=1- 1;для массивного корпуса (d2) с2=1+ 2.
1.3 Определяем с учётом поправок наименьший допустимый натяг по формуле 1.112 c.335 [1]:
[Nmin]= N min+γш (4)
Предварительно определяем γш поправку на снятие микронеровностей деталей при образовании соединения по формуле 1.113 c.335 [1]:
γш=5(Rаd+RаD) =5(125+25)=1875 (мкм)
[Nmin]=985+1875=286 (мкм)
1.4 Определяем наибольшее допустимое удельное давление [pдоп] на поверхности вала и втулки при котором отсутствует пластическая деформация деталей для этого определяем значения p1и p2 по формулам 1.115-1.116 c.336 [1]:
где Т1 и Т2 – предел текучести материалов охватываемой и охватывающей деталей.
В качестве [pдоп] выбираем наименьшее из двух значений:
[pдоп]= 555·107 (Hм²)
1.5 Определяем величину наибольшего расчётного натяга N max по формуле 1.117 c.336 [1]:
1.6 Определяем с учётом поправок величину максимального допустимого натяга по формуле 1.118 c.336 [1]:
[Nmax]= N max ×γуд +γш +γt (8)
где γуд – коэффициент увеличения удельного давления у торцов охватывающей детали принимается 08-09 при ld=0.5-1
γш – поправка учитывающая смятие неровностей контактных поверхностей деталей при образовании соединения.
Поправку γt следует учитывать если при рабочей температуре натяг увеличивается.
[Nmax]=15016×09+1875=15389 (мкм)
1.7 По таблице 1.49 стр.156 [1] выбираем посадку:
Nmax≤[Nmax] и Nmin>[Nmin]
Заданное условие выполняется значит посадка выбрана верно.
1.8 Рассчитаем усилие запрессовки по формуле 1.121 c.336 [1]:
где fп – коэффициент трения при запрессовке fп = (115-12)f.
2 Выбор и расчет посадки с зазором
Выберем посадку с зазором H7h8.
2.1 Определяем предельные отклонения по таблице 1.48 c.79-100 [1]:
для отверстия диаметром 110Н7:
верхнее отклонение: ES=+35 (мкм)=0035 (мм)
нижнее отклонение: EI=0 (мкм)=0 (мм)
для вала диаметром 42h8:
верхнее отклонение: es=0 (мкм)=0 (мм)
нижнее отклонение: ei=-54 (мкм)=-0054 (мм).
2.2 Определяем предельные размеры:
Dmax=D+ES=110+0035=110035 (мм)
Dmin=D+EI=110+0=110 (мм)
dmax=d+es=110+0=110 (мм)
dmin=d+ei=110+(-0054)=109946 (мм)
2.3 Определяем допуски:
TD=Dmax-Dmin=110035-110=0035 (мм)
Td=dmax-dmin=110-109946=0054 (мм)
2.4 Определяем предельный зазор:
Smax=Dmax-dmin=42025-41984=0089 (мм)
Smin=Dmin-dmax=110-110=0 (мм)
2.5 Определяем допуск посадки:
TS=Smax-Smin=0089-0=0089 (мм)
2.6 Изображаем графически расположение полей допуска вала и отверстия на листе формата- 260601.ОПД.Ф.05.61.03.002.
3Выбор и расчет переходной посадки
Была выбрана переходная посадка H7k6.
3.1 Определяем предельные отклонения по таблице 1.28 c.79-100 [1]:
для отверстия диаметром 130H7:
верхнее отклонение: ES=+40 (мкм)=004 (мм)
нижнее отклонение: EI=0 (мкм)=0 (мм)
для вала диаметром 130k6:
верхнее отклонение: es=+28 (мкм)=0028 (мм)
нижнее отклонение: ei=+3 (мкм)=0003 (мм).
3.2 Определяем предельные размеры:
Dmax=D+ES=130+004=13004 (мм)
Dmin=D+EI=130+0=130 (мм)
dmax=d+es=130+0028=130028 (мм)
dmin=d+ei=130+0003=130003 (мм)
3.3 Определяем допуски:
TD=Dmax-Dmin=13004-130=004 (мм)
Td=dmax-dmin=130028-130003=0025 (мм)
3.4 Определяем предельный зазор:
Smax=Dmax-dmin=13004-130003=0037 (мм)
Определяем предельный натяг:
Nmax=dmax-Dmin=130028-130=0028 (мм)
3.5 Определяем допуск посадки:
TS=Smax+Nmax=0037+0028=0065 (мм)
3.6 Изображаем графически расположение полей допуска вала и отверстия на листе формата- 260601.ОПД.Ф.05.61.03.002..
4Выбор и расчет посадки с натягом
Была выбрана посадка с натягом H7t6.
4.1 Определяем предельные отклонения по таблице 1.28 c.79-100 [1]:
для отверстия диаметром 70H7:
верхнее отклонение: ES=+30 (мкм) = +003 (мм)
нижнее отклонение: EI=0 (мкм) = 0 (мм)
для вала диаметром 70t6 :
верхнее отклонение: es=+94 (мкм) =+0094 (мм)
нижнее отклонение: ei=+75 (мкм)=+0075 (мм)
4.2 Определяем предельные размеры:
Dmax=D+ES=70+ 003 = 7003 (мм)
Dmin=D+EI=70+ 0 = 70 (мм)
dmax= d + es = 70 + 0094 = 70094 (мм)
dmin= d + ei=70 + 0075 = 70075 (мм)
4.3 Определяем допуски:
TD = Dmax – Dmin = 7003 – 70 = 003 (мм)
Td = dmax - dmin = 70094 -70075= 0019(мм)
4.4 Определяем предельный натяг:
Nmax = dmax-Dmin= 70094 – 70 = 0094(мм)
Nmin = dmin-Dmax= 70075- 7003 = 0045 (мм)
4.5 Определяем допуск посадки:
TN = Nmax-Nmin = 0094-0045=0049 (мм)
4.6 Изображаем графически расположение полей допуска вала и отверстия на листе формата- 260601.ОПД.Ф.05.61.03.002.
.2 Выбор и расчет посадки для резьбового соединения
1 Определяем внутренний и средний диаметры резьбы по формулам из таблицы 4.24 c.144 [2] учитывая что шаг резьбы Р=175:
D2=d2=d-2+0863=12-2+0863=10863(мм)
D1=d1=d-2+0106=12-2+0106=10106(мм)
2 Определяем предельные отклонения по таблице 4.29 стр.153–165 [2].
d2 (7g): es2=-0034 (мм)
d1 (7g): es1=-0034 (мм)
d (6g): es=-0034 (мм)
D2 (7H): ES2=+0250 (мм)
D1 (7H): ES1=0427 (мм)
D (7H): ES-не нормируется
3 Определяем предельные размеры гайки (внутренние диаметры):
D2max=D2+ES2=10863+0250=11113 (мм)
D2min=D2+EI2=10863+0=10863 (мм)
D1max=D1+ES1=10106+0427=10533 (мм)
D1min=D1+EI1=10106+0=10106 (мм)
Dmin=D+EI=12+0=12 (мм)
4 Определяем предельные размеры для болта (наружный диаметр):
d2max=d2+es2=10863+(-0034)=10829 (мм)
d2min=d2 +ei2=10863+(-0224)=10639 (мм)
d1max=d1+es1=10106+(-0034)=10072 (мм)
d1min-не нормируется
dmax=d+es=12+(-0034)=11966 (мм)
dmin=d+ei=12+(-0299)=11701 (мм)
5 Выполняем схему расположения допусков для резьбового соединения на листе формата- 260601.ОПД.Ф.05.61.03.003.
Выбор и расчет посадки для шпоночного соединения
1 Определяем номинальные размеры шпонки по табл. для d=50 мм:
ширина шпонки b=14 (мм)
высота шпонки: h=9 (мм)
длина шпонки: l=90 (мм)
предельные размеры фаски: Smax= 04 (мм)
глубина паза на валу: t1=55 (мм)
глубина паза на втулке: t2=38 (мм)
2 Вычисляем размеры:
d-t1=50-55=445 (мм)
d+t2=50+38=538 (мм)
3 Выбираем поля допусков принимая что соединение нормальное:
поле допуска на ширину шпонки –
поле допуска на ширину паза на валу –
поле допуска на ширину паза во втулке –
поле допуска на высоту шпонки –
поле допуска на длину шпонки – h14.
4 Определяем предельные отклонения для размеров d-t1 d+t2 по табл. 4.66 c.238 [2]:
5 Изображаем схему расположения полей допусков для шпоночного
соединения на листе формата- 260601.ОПД.Ф.05.61.03.003.
Выбор и расчет посадки для шлицевого соединения
1 Принимаем что шлицевое соединение является прямобочным. Определяем размеры прямобочного шлицевого соединения по таблице табл. 4.71. стр. 250 [2]:
внутренний диаметр: d=42 (мм)
наружный диаметр: D=48 (мм)
ширина зуба: b=80 (мм)
2 Выбираем способ центрирования по внутреннему диаметру (d) т.к. данный вид центрирования применяется в случаях повышенных требований к совпадению геометрических осей т.к. твёрдость втулки не позволяет обрабатывать деталь протяжкой.
3 Выбираем посадки по таблице 4.73 стр. 253 [2]:
4 Определяем поля допусков для нецентрирующего диаметра D по табл. 4.75 стр.253 - 254 [2]:
5 Записываем обозначение шлицевого соединения с учётом найденных посадок:
6 Изображаем схему расположения полей допусков для шлицевого соединения на листе формата- 260601.ОПД.Ф.05.61.03.003.
Расчёт и выбор посадок для соединений с подшипником качения
Определяем основные размеры и параметры подшипника
D=110 мм; d=50 мм; B=27 мм; r=15х45º мм.
Радиальная реакция опоры на подшипник: R = 2000 Н = 2 кН.
1 Определяем интенсивность нагрузки по формуле 4.25 стр. 283 [2]:
где R - радиальная реакция опоры на подшипник Н
b - рабочая ширина посадочного места м
b = B-2r = 27-2×15 = 24 мм = 24×10-3 м
где B - ширина подшипника
Kп - коэффициент посадки зависящий от характера нагрузки.
Принимаем Kп = 18 т.к. наблюдаются сильные удары и вибрации нагрузка достигает до 300%.
F - коэффициент учитывающий степень ослабления посадочного натяга при полом или тонкостенном корпусе. Т.к. вал является сплошным то F = 1 выбираем по таблице 4.80 с.817 [2].
FA – коэффициент неравномерности распределения радиальной нагрузки R между рядами роликов в двухрядных конических роликоподшипниках или между сдвоенными шарикоподшипниками при наличии осевой нагрузки А на опору значение выбираем по таблице 4.80 с.817 [2]. Для радиально-упорных подшипников с одним наружным или внутренним кольцом FA = 1 тогда:
По табл. 4.92 стр. 287 [2] для заданных условий определяем поле допуска на вал – .
2 Проверяем выбор поля допуска по наименьшему натягу используя формулу 4.26 стр. 286 [2]:
R — наибольшая радиальная нагрузка на подшипник кН;
k — коэффициент принимаемый приближенно для подшипников легкой серии — 2.8;средней серии — 2.3; тяжелой — 2; b — рабочая ширина кольца подшипника (за вычетом фасок) м.
Выбираем поле допуска для отверстия стакана подшипника который соприкасается с наружным кольцом: Н7.
3 Определяем верхние и нижние предельные отклонения по табл. 1.29 стр. 79:
Для внешнего диаметра (D=110 мм):
Для внутреннего диаметра (d=50мм):
4 Определяем наибольшие и наименьшие предельные размеры:
Dmax = D+ ES1 = 110+0035=110035 (мм)
Dmin= D+ ei1=110+0=110 (мм)
dmax = d+ EI2 =50+00095=500095 (мм)
dmin = d+ ei2 =50-00095=499905 (мм)
5 Определяем максимальное значение натяга:
Nmax= es2-EI2+ =00095+0012=00215 (мм)
6 Определяем средний натяг по формуле 1.31 стр. 19 [1]:
7 Проверяем допустимость посадки из условий прочности внутреннего кольца подшипника на разрыв:
8 Изображаем схему расположения полей допусков для соединения с подшипником качения на листе формата- 260601.ОПД.Ф.05.61.03.002.
Определение комплекса контрольных параметров для зубчатого колеса по требованиям к точности изготовления
1 Выбираем модуль зубчатого колеса согласно таблицы 5.3 c.836 [2]:
Принимаем степень точности зубчатого колеса 8-В
-показатель характеризующий кинематическую точность зубчатого колеса
В-вид сопряжения характеризующий величину бокового зазора.
Принимаем диаметр делительной окружности
2 Определяем число зубьев по формуле 5.1 c.831 [2]:
3 Определяем высоту головки зуба
4 Определяем высоту ножки зуба
5 Определяем диаметр вершин
6 Определяем диаметр впадин
df=110-2·25=105 (мм).
7 Определяем показатели характеризующие кинематическую точность колеса. Для этого выбираем комплекс III по таблице 2 стр.426[3]:
FVWr – колебание длины общей нормали;
Frr – радиальное биение зубчатого венца.
Определяем допуск на радиальное биение зубчатого венца и колебание длины общей нормали по таблице 5 стр.431[3]:
8 Определяем показатели характеризующие плавность работы по таблице 7 стр.435-436[3] принимаем VII комплекс:
fPbr – отношение шага зацепления
fPtr – отклонение шага.
Предельное отклонение шага и шага зацепления определяем по таблице 10 стр.439[3]:
9 Определяем показатели характеризующие полноту контакта зубьев: суммарное пятно контакта по высоте зуба на менее 40% а по длине зуба не менее 50% согласно таблицы 17 стр.449[3].
10 Определяем величину гарантированного бокового зазора по таблице 17 стр.451[3]:
что соответствует виду сопряжения В и межосевому расстоянию аw=70 (мм).
Предельное отклонение межосевого расстояния fa=±60
Наименьшее дополнительное смещение исходного контура определяем по таблице 19 стр.454[3]:
Допуск на смещение исходного контура определяем по таблице 21 стр.455[3]:
11 Определяем наименьшее отклонение средней длины общей нормали по таблице 23 стр.457[3]:
EWms=EWmI+EWmII=(110+11)=121 (мкм)
12 Определяем допуск на среднюю длину общей нормали по таблице 28 стр.462[3]:
13 Определяем допуск на длину общей нормали по таблице 25 стр.459[3]:
14 Определяем наибольшее отклонение средней длины общей нормали по таблице 23 стр.457[3] :
EWmi=EWmI+EWmII=(121+70)=191(мкм)
Наименьшее отклонение толщины зуба определяем по таблице 29 стр.463[3]:
15 Определяем допуск на толщину зуба из таблицы 30 стр.464[3]:
16 Определяем радиальное биение наружного цилиндра заготовки по таблице 5.26 стр.878[2]:
Fda=06·Fr=06·45=27 (мкм) =0027(мм)
Биение базового торца определяем по таблице 5.27 стр.879[2]:
FT=40·=40·(110100)=44 (мкм) =0044(мм)
17 Определяем длину общей нормали по таблице 5.30 стр.885[2]:
где m — модуль мм; к — коэффициент который при угле зацепления = 20° и определенном числе охватываемых зубьев при измерении зависит от числа зубьев колеса z.
Значение выбираем из таблицы 5.30 стр.884885[2]:
W=1995913 ·2=399182639918 (мм)
Расчёт размерной цепи методом максимум – минимум
А3= A1+ A2- A=49-2=47 (мм)
1 Строим схему размерной цепи. Определяем увеличивающие и уменьшающие размеры:
А1 A2 – увеличивающие размеры
A3 – уменьшающий размер.
2 Определяем номинальный размер замыкающего звена по формуле
АΔ = A1+ A2 - A3=22+27-47=2 (мм)
3 Определяем допуск замыкающего звена по формуле 3.8 стр.566[2]:
TAΔ=AΔmax–AΔmin (14)
4 Определяем верхнее и нижнее предельные отклонения замыкающего звена по формуле 3.13-3.14 стр.567[2]:
ESAΔ= AΔmax– АΔ = 2-2=0 (мм)
EIAΔ=AΔmin– АΔ = 15-2=-05 (мм)
5 Определяем координату середины поля допуска замыкающего звена по формуле 3.10 стр.567[2]:
6 Определяем количество единиц допуска содержащихся в допуске исходного звена AΔ по формуле 3.5 стр.561[2]:
Найденное число единиц допуска арасч=1324 лежит в пределах стандартных значений а расч = 100 (11-й квалитет) и а расч = 160 (12-й квалитет). Отсюда следует что часть звеньев должна изготавливаться по 11-му квалитету а часть — по 12-му. Выберем наиболее предпочтительны 11-ый квалитет.
7 Назначаем предельное отклонение на составляющие звенья исходя из следующих соображений:
) для охватывающих размеров выбираем основное отклонение Н(+) по табл. 1.27 (стр.79 [1]) для охватываемых размеров – h(-) по табл. 1.28 (стр. 80 [1]) для остальных размеров принимаем основное отклонение Js(±).
) выбираем из наибольших размеров и принимаем за А'.
A1 = 22 js 11(+-0065)
Определяем допуски для составляющих звеньев:
8 Определяем допуск звена А' по формуле 3.9 стр.567[2]:
ТА = ТА1+ ТА2 + ТА3'
ТА3' = ТА - ТА1- ТА2
ТА3' = 500 – 130 – 120 = 250 (мкм)
9 Определяем координаты середины поля допуска звена А3' по формуле 3.15 стр.568[2]:
ЕсА = ЕсАi ув - ЕсАi ум (17)
ЕсА = ЕсА3' – (ЕсА1+ЕсА2)
ЕсА3' = -ЕсА + ЕсА1+ЕсА2
ЕсА3' = 250 – 60 = 190 (мкм)
10 Определяем предельные отклонения для размера А3' по ф. 3.16 c. 568[2]:
ЕSАj = ЕсАi + ТАj2 (18)
EIАj = ЕсАi – ТАj2 (19)
ЕSА3' = ЕсА3' + ТА3'2
EIА3' = ЕсА3' – ТА3'2
ESА3' = 190 + 2502 = 315 (мкм)
EIА3' = 190 – 2502 = 65 (мкм)
11 Принимаем стандартное поле допуска для размера А3:
Результаты поэтапных расчетов внесем в таблицу
Номинальный размер мм
Обозначение основного отклонения
Середина поля допуска
12 Проверочный расчет
12.1 Определяем номинальный размер замыкающего звена А:
А = 22 + 27 – 47 = 2 (мм).
12.2 Определяем допуск замыкающего звена:
ТА = 130 + 120 + 160 = 410 (мкм).
12.3 Определяем координату середины поля допуска замыкающего звена:
ЕсА = ЕсАi ув - ЕсАi ум
ЕсА = ЕсА1 + ЕсА2 - ЕсА3
ЕсА = 0 – 60 – 210 = – 270 (мкм).
12.4 Определяем предельные отклонения замыкающего звена:
ЕSА = – 270 + 4102 = – 65 мкм = – 0065 (мм).
EIА = –270 – 4102= -475 мкм = -0475 (мм).
12.5 Определяем предельные размеры замыкающего звена:
А max = А + ЕSА = 2 – 0065 = 1935 (мм)
А min = А + EIА =2 – 0475 = 1525 (мм)
А max (зам.) ≤ А max (исх.)
А min (зам.) ≥ А min (исх.) (21)
Проверка показала что назначенные предельные отклонения составляющих звеньев обеспечивают требуемую точность замыкающего звена.
Выбор средств измерений
Для сопрягаемых поверхностей вала и втулки выберем измерительные средства для контроля размера вала диаметром 55g6 и отверстия втулки диаметром 55H7 по таблице 27 с. 166-172[3].
По таблице 26 с. 165 определяем допускаемую погрешность измерения для измерения вала диаметром 55g6.
Таким образом выбираем следующее измерительное средство:
гладкий микрометр типа МК-75-2 ГОСТ 6507-78 второго класса точности с погрешностью ±0004мм=±4мкм и ценой деления 001мм.
По таблице 26 с. 165 определяем допускаемую погрешность измерения для измерения отверстия втулки диаметром 55H7.
нутромер с измерительной головкой 2ИГ типа 154 ГОСТ 9244-75 с пределом допускаемой погрешности = ±0004мм=±4мкм и ценой деления 001мм.
Обработка результатов измерений
Произведем обработку результатов измерений: 15; 18; 19; 18; 16; 19; 18; 16; 17; 20.
1 Определяем среднее арифметическое:
где n – количество измерений
xi – i-ое значение измерения.
2 Определяем выборочное среднеквадратичное отклонение:
где - среднее арифметическое значение результатов измерений;
Sx – оценка среднеквадратичного отклонения.
3 Принимаем что неисключенная систематическая погрешность:
то неисключенной систематической погрешностью пренебрегаем.
4 Определим доверительные границы случайной погрешности
где tP - коэффициент Стьюдента соответствующий числу степеней свободы и принятой доверительной вероятности Р;
n – число измерений.
5 Запишем окончательный результат
Список использованных источников
Допуски и посадки. Справочник. В 2-х ч. Ч. 1.В.Д. Мягков. – Л.: Машиностроение Ленинградское отделение 1979г. – 543 с.
Допуски и посадки. Справочник. В 2-х ч. Ч. 2.В.Д. Мягков. – Л.: Машиностроение Ленинградское отделение 1979г. – 448 с.
Белкин И.М. Допуски и посадки. – М.: Машиностроение 1992г. – 528 с.
Анурьев В.И. Справочник конструктора-машиностроителя. В 3-х т. Т. 1. – М.: Машиностроение 1978г. – 728 с.
Анурьев В.И. Справочник конструктора-машиностроителя. В 3-х т. Т. 2. – М.: Машиностроение 1978г. – 559 с.
Анурьев В.И. Справочник конструктора-машиностроителя. В 3-х т. Т. 3. – М.: Машиностроение 1978г. – 557 с.
Условные обозначения
Таблица А.1 - Условные обозначения
Номинальный размер отверстия
Номинальный размер вала
Наибольший предельный размер отверстия
Наименьший предельный размер вала
Верхнее отклонение отверстия
Верхнее отклонение вала
Нижнее отклонение отверстия
Нижнее отклонение вала
Допуск для отверстия
Координата середины поля допуска отверстия
Координата середины поля допуска вала
Допуск зазора посадки с зазором
Допуск натяга посадки с натягом
Перечень графических материалов
Таблица Б.1 - Перечень графических материалов
0601.ОПД.Ф.05.61.03.001
0601.ОПД.Ф.05.61.03.002
Схемы расположения полей допусков для гладких цилиндрических соединений и соединений с подшипником качения
0601.ОПД.Ф.05.61.03.003
Схемы расположения полей допусков для резьбового шпоночного и шлицевого соединений
0601.ОПД.Ф.05.61.03.004