Расчет, выбор и обоснование посадок соединений




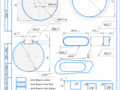
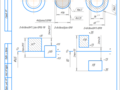
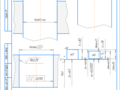
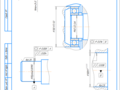
- Добавлен: 24.01.2023
- Размер: 2 MB
- Закачек: 0
Описание
Состав проекта
![]() |
![]() ![]() ![]() |
![]() ![]() ![]() ![]() |
![]() ![]() ![]() ![]() |
![]() ![]() ![]() |
![]() ![]() ![]() ![]() |
![]() ![]() |
![]() ![]() ![]() |
![]() |
![]() ![]() ![]() |
![]() ![]() ![]() ![]() |
Дополнительная информация
Рис. 1.1.dwg

Шлицевое соединение А4.cdw

рис 1.cdw

ПОДШИПНИКИ А4.cdw

рис 2.cdw

Рекомендуемые чертежи
Свободное скачивание на сегодня
Другие проекты
- 29.08.2014