Расчёт и выбор посадок для сопряжений сборочного узла Мотор - редуктор


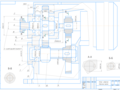
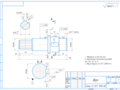
- Добавлен: 24.01.2023
- Размер: 586 KB
- Закачек: 0
Описание
Состав проекта
![]() |
![]() |
![]() ![]() ![]() ![]() |
![]() ![]() ![]() ![]() |
![]() |
![]() |
![]() ![]() ![]() |
![]() ![]() ![]() |
Дополнительная информация
Мотор - редуктор СБ В-1 исправленный.cdw

Вал выходной-исправленный.cdw

Неуказанные отклонения размеров:
Общие допуски по ГОСТ 30893.1-m.
Сталь 45 ГОСТ 1050-80
Метрология Вариант 1 (рис. 2) исправленный.doc
Цель работы: усвоение и закрепление теоретического материала по дисциплине «Метрология стандартизация и сертификация» а также приобретение навыков работы со справочниками и стандартами.
Исходные данные: 1) сборочный узел «Мотор – редуктор»
Расчётно-пояснительная
) Исходные данные (табл. 1; табл. 2):
Зубчатые колёса и передачи
Ради-альная наг-рузка на под-шип-ник кН
Число зубьев зубчатых колёс
Ширина зубчатого колеса мм
На про-ме-жу-точ-ном валу
Размеры вала электродвига-теля мм
Харак-тер шпо-ноч-ного соеди-нения
Замы-каю-щий размер размер-ной цепи мм
Ради-альное биение мкм
Коэф. запаса точно-сти
Функциональ-ный натяг
Точ-ность цент-риро-вания
В данной курсовой работе изучена нормативно-техническая документация; выбор сопряжений и расчёт их параметров.
Рассмотрены следующие понятия: посадка; посадки переходные и с натягом их характеристики. Определение зазора и натяга. Расчётные формулы. Допуски посадки и его расчёт. Графическое изображение посадок. Применение посадок в сопряжённых деталях.
Выбор посадок типовых соединений: шпоночного шлицевого резьбового.
Расчёт размерной цепи методом max-min.
Характеристика основ сертификация.
Основы стандартизации 5
Анализ номинальных размеров 6
Выбор посадок гладких цилиндрических соединений 7
1. Выбор переходной посадки 7
2. Выбор посадки с натягом 9
3. Расчет и выбор подшипников качения 10
4. Выбор посадок распорной втулки на вал и
крышки подшипника в корпус 14
Выбор посадок типовых соединений 16
1. Выбор посадок шпоночного соединения 16
2. Выбор посадок шлицевого соединения 18
3. Расчёт параметров резьбового соединения 20
Расчет размерных цепей 23
Основы сертификации 29
Список использованных источников 31
Конструирование – это процесс создания изделий в виде сборочных и рабочих чертежей. Изделием называется любой предмет или набоp пpедметов пpоизводства подлежащих изготовлению на предприятии.
Виды изделий: а) детали; б) сбоpочные единицы; в) комплексы; г) комплекты.
Деталь – изделие изготовленное из отдельного по наименованию и маpке матеpиала без пpименения сбоpочных опеpаций.
Современная организация производства новая техника инновационные технологические процессы требуют глубоких и разносторонних знаний высокой производственной квалификации. Необходимо знать общие положения единой системы конструкторской документации.
ГОСТ 2.001 – 70 устанавливает общие положения по целевому назначению области распространения классификации и обозначению стандартов входящих в комплекс Единой системы конструкторской документации (ЕСКД).
Единая система конструкторской документации - комплекс государственных стандартов устанавливающих взаимосвязанные правила и положения по порядку разработки оформления и обращения конструкторской документации разрабатываемой и применяемой организациями и предприятиями. Основное назначение стандартов ЕСКД - установление в организациях и на предприятиях единых правил выполнения оформления и обращения конструкторской документации.
Измерения изучаются отдельной наукой — метрологией. Метрология — это наука об измерениях методах и средствах обеспечения их единства а также способах достижения требуемой точности. Измерение — это нахождение значения физической величины опытным путем с помощью специальных технических средств.
Средство с помощью которого выполняют измерение так и называют — средство измерений оно имеет нормированные метрологические свойства Значение величины которое выявили измерением называют результатом измерения.
Основы стандартизации
Номер стандарта – ГОСТ 8752
ГОСТ 8752 – Манжеты резиновые армированные для валов. Технически е условия.введения – 01.01.81
Настоящий стандарт распространяется на резиновые армированные однокромочные манжеты с пружиной для уплотнения валов работающих на минеральных маслах воде дизельном топливе при избыточном давлении до 005 Мпа (05 кгссм2) скорости до 20 мс и температуре от минус 60 до плюс 170°С в зависимости от резины.
Для манжет применяемых в авиационной технике и в изделиях специального назначения стандарт устанавливает только размеры.
Манжеты (сальники) изготавливаются двух типов:
– однокромочные (тип 1);
– двухкромочные (тип 2).
Манжеты (сальники) типа 1 предназначаются для предотвращения вытекания уплотняемой среды.Манжеты (сальники) типа 2 предназначаются для предотвращения вытекания уплотняемой среды и защиты от проникновения пыли.
Поэтому можно услышать и такие названия: "без пыльника" (тип 1) и "с пыльником" (тип 2).
Манжеты (сальники) должны изготавливаться в двух исполнениях:
– с механически обработанной кромкой.
– с формованной кромкой. (наиболее чаще встречаемый вариант сальников).
Обозначение по ГОСТ 8752–81.
Например: 1.2-25х42-1 где
2 – тип манжеты (количество рабочих кромок сальника);
– номинальный диаметр вала (d);
– наружный диаметр манжеты (D);
– группа резины сальника.
Анализ номинальных размеров
Размер полученный в результате обработки детали обязательно отличается от номинального но ведь значение этого размера становится известно лишь в результате измерения а оно в свою очередь также может осуществляться с различной погрешностью. Поэтому мы будем говорить о действительном размере – размере установленном измерением с допустимой погрешностью. Пока лишь отметим что допустимые погрешности измерения а следовательно и выбор измерительных средств необходимо согласовывать с точностью которая требуется для данного размера. Номинальный размер можно определить как размер относительно которого определяются предельные размеры. Разность между наибольшим и наименьшим предельными размерами или алгебраическая разность между верхним и нижним предельными отклонениями характеризует точность с которой должен быть выполнен размер при изготовлении детали и называется допуском.
Анализируемый размер
Номинальный диаметр соединения с натягом
Диаметр внутреннего кольца подшипника 5-7204 на промежуточном валу
Размеры нормируются по ГОСТ 333-79
Диаметр внешнего кольца подшипника 5-7204 на промежуточном валу
Диаметр внутреннего кольца подшипника 5-7308 на выходном валу
Диаметр внешнего кольца подшипника 5-7308 на выходном валу
Размеры шпонки для вала d = 50 мм
Наружный диаметр шлица
Параметры шлицевого соединения нормируются по ГОСТ 1139-80
Внутренний диаметр шлица
Диаметр болта резьбового соединения
Диаметр гайки резьбового соединения
Выбор посадок гладких цилиндрических соединений
Цель: изучить методику расчета допустимых значений минимального и максимального натяга и зазора в посадках и исходя из назначения конструктивных особенностей и условий эксплуатации устройств рассчитать и выбрать стандартные посадки. Рассчитать и выбрать посадки колец подшипников с валом и корпусом назначить отклонения формы и шероховатость посадочных поверхностей.
Разработанная и введенная с 01.01.1977 г. система получила название Единой системы допусков и посадок (ЕСДП) и включает ряд стандартов. Основными из них являются следующие: «Общие положения ряды допусков и основных отклонений» (ГОСТ 25346–89) «Поля допусков и рекомендуемые посадки» (ГОСТ 25347–89). Установление и применение указанных правил норм требований т.е. стандартов называется стандартизацией.
1. Выбор переходной посадки
Переходные посадки подразделяются на три группы: посадки с более вероятными натягами; посадки с равновероятными натягами и зазорами; посадки с более вероятными зазорами. Переходные посадки имеют небольшие предельные зазоры и натяги и поэтому их применяют в тех случаях когда необходимо обеспечить центрирование деталей и сборки-разборки соединения т. е. совпадение осей отверстия и вала; при этом требуется дополнительное закрепление соединяемых деталей. Для создания запаса точности компенсации погрешностей формы и расположения поверхностей сопрягаемых деталей а также износа деталей при повторных сборках наибольший допустимый зазор определим по формуле [6]:
где Fr – допустимое радиальное биение втулки на валу возникающее при одностороннем смещении втулки из-за зазора определяем по ГОСТ 1643-81 [4 с 317];
КT – коэффициент запаса прочности КT = 2–5.
Условия выбора переходной посадки которые обеспечивают её годность и оптимальность: Smax ≤ Smax расч .
Для сопряжения деталей дано: Fr = 90 мкм; kT = 2; d = 20 мм.
Выберем посадку: Smax расч = Fr kT = 90 2 = 45 мкм
ø20 Н7(+00210) js6(+0.0065– 00065) Nma Smax = 275 мкм.
Smax ≤ Smax расч – 275 мкм ≤ 45 мкм. Условия выбора посадки выполняются.
Рис. 2.3. Схема расположения полей допусков переходной посадки
Определим: Smax = 275 мкм Nmax = 65 мкм. Определим средний зазор: Sср = Ес – ес
где серединное отклонение отверстия: Ес = (ES + EI)2 = (21 + 0)2 =105 мкм;
серединное отклонение вала: ес = (es + ei)2 = (65 + (– 65))2 = 0.
Тогда: Sср = х = 105 – 0 =105 мкм – расстояние соответ. нулевому зазору (натягу).
Определим допуски отверстия и вала: TD Td.
TD = ES – EI = 21 – 0 = 21 мкм; Td = es – e Т = TD +Td =34.
Определим среднее квадратичное отклонение (при законе нормального распределения): N = 16 √(TD2 + Td2) = 16 √(212 + 132) = 16 (247) = 41 мкм.
Определим относительное отклонение: Z = х N = 105 41 = 25.
Определим диапазон рассеяния зазоров и натягов: R = 6 = 247 мкм.
Вероятностное количество сопряжений с зазором: РS = 05 + Ф (z).
Определим [2] Ф (z): Ф (25) = 0461.
Таким образом: РS = 05 + 0461 = 0961 или 96 %.
Вероятностное количество сопряжений с натягом: РN = 100 – 96 = 4%.
Следовательно при сборке примерно 96% всех соединений (960 из 1000) будут с зазором и 4% соединений (40 из 1000) – с натягом.
Вывод. Выбранная переходная посадка обеспечивает хорошее центрирование деталей и достаточно легкую сборку-разборку так как для этой посадки более вероятно получение зазора.
2. Выбор посадки с натягом
Посадки с натягом по значению гарантированного натяга подразделяются на три группы: посадки с минимальным гарантированным натягом; посадки с умеренным гарантированным натягом; посадки с большим гарантированным натягом. Посадки с натягом служат для получения неподвижного соединения. Для получения неподвижного соединения нужно чтобы действительный размер охватываемого элемента одной детали (вала) был больше действительного размера охватывающего элемента другой детали (отверстия). Разность действительных размеров вала и отверстия до сборки если размер вала больше размеров отверстия называется натягом. Следует иметь в виду что после сборки размеры вала и отверстия при образовании натяга будут одинаковы так как при сборке поверхности детали деформируются чем и обеспечивается неподвижность соединения. Технологический процесс сборки соединения с натягом осуществляется либо запрессовкой с усилием вала в отверстие (при малых натягах) либо за счет увеличения непосредственно перед сборкой размера отверстия путем нагрева (при больших натягах). Проведём расчёт посадки с натягом для сопряжения деталей: ступицы и венца зубчатого колеса (Z4). Для сохранения требуемого уровня эксплуатационных показателей неподвижного соединения в процессе его длительной эксплуатации необходимо на этапе расчёта и выбора посадки создать гарантированный запас его работоспособности. Следовательно часть функционального допуска посадки ТF N: ТF N = (Nma
NЗ экс = Nmin табл. – Nmin F – запас прочности при эксплуатации.
Условия выбора посадки таковы: Nma Nmin табл. ≥ Nmin F .
Для сопряжения деталей дано: Nma Nmin F = 120 мкм.
Выберем посадку: В общем случае посадки с натягом назначаются с 5-го по 8-й квалитеты. Ближайшей посадкой согласно ГОСТ 25347-82 [6] является посадка:
ø100 Н8(+00540) х8(+0232+0178) – Nma Nmin табл. = 124 мкм.
Тогда получим: – запас прочности при эксплуатации:
– запас прочности при сборке:
NЗ пр = Nmax F – Nmax табл. = 260 – 232 = 28 мкм.
Условия выбора посадки выполнены:
NЗС > NЗЭ – 28 мкм > 4 мкм
Рис. 3.2. Схема расположения полей допусков посадки с натягом
Вывод. Условия выбора посадки выполняются. Выбранная посадка обеспечивает запас прочности как по Nmin так и по Nmax натягом.
3. Расчет и выбор подшипников качения
Подшипники качения являются опорами для вращающихся частей машин и механизмов и делятся на шариковые и роликовые.
Исходя из условий работы по справочнику [4 Т2 с 204-234 табл.126-136]: подберем вид номер номинальные размеры и отклонения подшипника. В данной конструкции используются следующие подшипники.
На промежуточном валу используем подшипник – 5-7204 ГОСТ 333-79 роликоподшипник конический однорядный лёгкой серии.
Его характеристики: диаметр внутреннего кольца d = 20 мм диаметр наружного кольца D = 47 мм ширина колец B = 14 мм радиус фаски r = 15 мм). класс точности подшипника – 5-й режим работы – 1– лёгкий перегрузки до 150 % умеренные толчки и вибрации. Предельные отклонения выберем:
d = 20–0008 мм; D = 47–0009 мм; B = 14–0012 мм.
Примечание. Верхние отклонения d D и В равны нулю. Отклонение ширины колец В выбираются в зависимости от диаметра d.
По значению радиальной нагрузки R = 5 кН рассчитаем интенсивность радиальной нагрузки [1]: : РR = (Rb) · Кп · FA · F
где: b – рабочая ширина посадочной поверхности кольца м;
Кп – динамический коэффициент зависящий от режима работы
подшипника [4 с 283]: Кп = 1 для лёгкого режима работы;
FA – коэффициент неравномерности распределения радиальной нагрузки
в двухрядных или сдвоенных подшипниках при наличии силы осевой А. [4 с 286 табл. 4.91]: FA = 1 для однорядных подшипников.
F – коэффициент учитывающий степень ослабления натяга при
сопряжении кольца подшипника с полым валом или тонкостенным
корпусом [4 с 286 табл. 4.90]: К2 = 1 так как вал сплошной;
Рабочая ширина посадочной поверхности кольца составит:
b = В – 2 · r где: В – ширина кольца; r – радиус фаски.
Тогда: b = (14 – 2 · 15) · 10–3 = 11 · 10–3 м.
Интенсивность радиальной нагрузки для внутреннего кольца будет равной:
РR = (50011) · 1 · 1 · 1 = 454 к·Нм.
По значению РR = 454 к·Нм определим поля допусков валов и корпусов для посадки циркуляционно нагруженных колей подшипников [4 с 287 табл. 4.92]:
вала – ø20 js6(+00065-00065) мм; отверстия – ø47 Н7(+00250) мм.
Для построения схему расположения полей допусков посадочных поверхностей
определим отклонения наружного и внутреннего кольца подшипника по [4 с 273 табл. 4.82] и [4 с 276 табл. 4.83]: L0 = – 9 (внутр. кольцо).
Определим предельные значения зазоров и натягов при установке подшипника на вал и в корпус:
Nmin = ei(js6) – ES(L0) = 65 – 0 = 65 мкм.
L0 js6 – посадка внутреннего кольца подшипника на вал 2.
Определим радиальный зазор: S = Sср – Δ dнб. где Sср – средний нач. рад. зазор в подш.; Δ dнб – наиб диам. деформация беговой. дорожки кольца подш. после соед. с валом. По таблице [4] для d = 20 мм – Sнб = 24 мкм и Sнм =10 мкм.
Sср = (Sнб + Sнм)2 = (24 + 10)2 =17 мкм.
Тогда: Δ dнб = 085 Nmax (d(d + (D – d)4) = 085155(20(20 + (47 – 20)4) = 98 мкм.
Получим: S = Sср – Δ dнб = 17 – 98 = 72 мкм.
На выходном валу используем подшипник – 5-7308 ГОСТ 333-79 роликоподшипник конический однорядный средней серии.
Его характеристики: диаметр внутреннего кольца d = 40 мм диаметр наружного кольца D = 90 мм ширина колец B = 23 мм радиус фаски r = 25 мм). класс точности подшипника – 5-й режим работы – 1– лёгкий перегрузки до 150 % умеренные толчки и вибрации. Предельные отклонения выберем:
d = 40–0010 мм; D = 90–0013 мм; B = 23–0012 мм.
По значению радиальной нагрузки R = 5 кН рассчитаем интенсивность радиальной нагрузки: РR = (Rb) · К1 · К2 · К3
Тогда: b = (23 – 2 · 25) · 10–3 = 18 · 10–3 м.
РR = (50018) · 1 · 1 · 1 = 278 к·Нм.
По значению РR = 278 к·Нм определим поля допусков валов и корпусов для посадки циркуляционно нагруженных колей подшипников [4 с 287 табл. 4.92]:
вала – ø40 js6(+0008-0008) мм; отверстия – ø90 Н7(+00350) мм.
Для построения схему расположения полей допусков посадочных поверхностей определим отклонения наружного и внутреннего кольца подшипника по [4 с 273 табл. 4.82] и [4 с 276 табл. 4.83]:
L0 = – 13 (внутреннее кольцо).
Nma Nmin = ei(js6) – ES(L0) = 8 – 0 = 8 мкм.
L0 js6 – посадка внутреннего кольца подшипника на вал.
Определим радиальный зазор: S = Sср – Δ dнб где Sср – средний нач. рад. зазор в подш.; Δ dнб – наиб диам. деформация беговой. дорожки кольца подш. после соед. с валом. По таблице [4] для d = 40 мм – Sнб = 26 мкм и Sнм = 12 мкм.
Sср = (Sнб + Sнм)2 = (26 + 12)2 = 19 мкм.
Тогда: Δ dнб = 085 Nmax (d(d + (D – d)4) = 08521(40(40 + (90 – 40)4) = 136 мкм.
Получим: S = Sср – Δ dнб = 19 – 136 = 54 мкм.
Рис. 3.3. Схема расположения полей допусков
посадочных поверхностей подшипников вала и корпуса
Определим допуск цилиндричности посадочных мест вала и отверстия. Он не должен превышать а для подшипников 5-го кл. точности 18 допуска на диаметр.
Для подшипника 5-7204 (подшипник 5-ого класса точности): диаметры вала – ø20 js6(+00065-00065) мм; отверстия – ø47 Н7(+00250) мм. Допуск на диаметр вала равен 0013 мм а на диаметр отверстия корпуса 0025 мм. Соответственно допуски цилиндричности составят: для вала – 0002 мм; для отверстия – 0003 мм. Определим шероховатость сопрягаемых поверхностей для вала – Rа = 08 мкм; для отверстия корпуса – Rа = 08 мкм; для опорных заплечиков – Rа = 16 мкм.
Для подшипника 5-7308 (подшипник 5-ого класса точности): диаметры вала – ø40 js6(+0008-0008) мм; отверстия – ø90 Н7(+00350) мм. Допуск на диаметр вала равен 0016 мм а на диаметр отверстия корпуса 0035 мм. Соответственно допуски цилиндричности составят: для вала – 0003 мм; для отверстия – 0004 мм. Определим шероховатость сопрягаемых поверхностей для вала – Rа = 08 мкм; для отверстия корпуса – Rа = 08 мкм; для опорных заплечиков вала и корпуса – Rа = 16 мкм.
На чертеже вала нанесем – посадочный размер подшипника допуски цилиндричности и шероховатости.
4. Выбор посадок распорной втулки на вал
и крышки подшипника в корпус
Для распорной втулки на промежуточном валу выберем переходную посадку чтобы обеспечить правильную работу подшипникового узла. Внутренний диаметр распорной втулки: ø20 Н7(+00210) js6(+0.0065– 00065) Nma Smax = 275 мкм.
Для промежуточного вала используется подшипник 5-7204 ГОСТ 333–79. Допуск отверстия в корпусе определяется при выборе посадки наружного кольца подшипника – ø47Н7. Сопрягаемый размер корпуса как неответственный экономически целесообразно выполнять на 2 3 квалитета грубее например ø479 [5].
Таким образом назначается посадка:
ø47 Н7+00259–0025– 0087 Sm Smax = 156 мкм.
Для выходного вала допуск отверстия в корпусе определяется при выборе посадки наружного кольца подшипника 5-7308 ГОСТ 333–79 – ø90Н7. Сопрягаемый размер корпуса как неответственный экономически целесообразно выполнять на 2 3 квалитета грубее например ø909.
ø90 Н7(+00350)9(–0036– 0123) Sm Smax = 158 мкм.
Рис. 3.4. Схема расположения полей допусков посадки с зазором
Посадка с зазором служит для обеспечения подвижного соединения.
Для обеспечения подвижности соединения нужно чтобы действительный размер охватывающего элемента одной детали (отверстия) был больше действительного размера охватываемого элемента другой детали (вала). Разность действительных размеров отверстия и вала если размер отверстия больше размера вала называется зазором. В данной конструкции по посадке с гарантированным зазором осуществляется соединение корпуса и крышки подшипникового узла.
Вывод. Допуск охватывающей детали нельзя расширять так как он должен обеспечивать работоспособность подшипниковых узлов. Посадка обеспечивает легкую сборку-разборку соединения.
Выбор посадок типовых соединений
1. Выбор посадок для шпоночных соединений
Цель: назначить размеры допуски и посадки для деталей входящих в шпоночные соединения в зависимости от условий эксплуатации и требований к точности центрирования.
Шпоночными называют разъёмные соединения составных частей изделия с применением шпонок. Деталь шпоночного соединения – шпонка – закладывается в пазы вала и ступицы надеваемой на вал детали (шкива зубчатого колеса и т.п.). Шпоночные соединения могут быть неподвижными и подвижными и служат обычно для предотвращения относительного поворота ступицы и вала при передаче вращающего момента. Шпоночные соединения широко применяют во всех отраслях машиностроения.
По форме шпонок соединения подразделяют на призматические сегментные и клиновые. Допуски и посадки шпоночных соединений стандартизированы. На соединение призматических шпонок действует ГОСТ23360–78 на соединения сегментных – ГОСТ 24071–80 и на клиновые ГОСТ 24068–80. [8]
Соединение выходного вала со ступицей зубчатого колеса (Z4) осуществим с помощью шпонки. Номинальные размеры шпоночного соединения выберем в зависимости от диаметра вала [4 с 235 табл. 4.64]:
d = 50 мм; h = 9 мм;
b = 14 мм ; t1 = 55 мм;
Из условий работы и сборки соединения определим [4 с 237 табл. 4.54] вид соединения по ширине шпонки b. Характер шпоночного соединения – нормальный. Так как ступицы съёмная то соединение с её пазом должно быть свободным (ширина паза – 14D10) а с пазом выходного вала – нормальным (ширина паза 14N9).
Назначим поля допусков на диаметры вала и ступицы соединяемых шпонкой. Для соединения выберем переходную посадку которая обеспечивает хорошую точность центрирования. Однако в данном случае с целью обеспечения лёгкой сборки-разборки следует выбрать посадку – ø50H7h6.
Назначим допуски на размеры шпонки [4 с 238 табл. 4.66].
в нашем случае – 14 9 25h14.
Назначим поля допусков на глубину шпоночных пазов на валу и во втулке.
Для длины шпоночных пазов установим поле допусков – Н15.
В нашем случае – t1 = 55+020; d – t1 = 445 0–02; d + t2 = 538 +020.
Рис. 4.1. Соединение с призматической шпонкой
Рис. 4.2. Схема расположения полей допусков на ширину шпоночных пазов
Назначим допуски симметричности Тсим. шпоночного паза относительно оси и параллельности Тпар. плоскости симметрии паза относительно оси по длине паза. Из условий сборки рекомендуются следующие соотношения:
Тсим. ≤ 2 · Тш.; Тпар ≤ 05 · Тш.
где . Тш – допуск на ширину шпоночного паза.
Так как в задании требуется выполнить деталеровочный чертеж только вала то допуски назначим на шпоночный паз вала.
Тсим ≤ 2 · 43 = 86 мкм; Тсим = 80 мкм = 008 мм.
Тпар ≤ 05 · 43 = 21.5 мкм; Тпар = 20 мкм = 002 мм.
Условное обозначение выбранной шпонки:
Шпонка 14 х 9 х 25 ГОСТ 23360–78.
На деталеровочном чертеже вала изобразим сечение вала по шпоночному пазу с указанием всех необходимых размеров и допусков а также требований к отклонениям формы и расположения поверхностей и их шероховатости.
2. Выбор посадок шлицевого соединения
Цель: выбрать номинальные размеры шлицевого соединения и назначить на них допуски и посадки.
Наибольшее распространение имеют соединения шлицевые прямобочные размеры и допуски которых регламентированы ГОСТ 1139-80.
В данном сборочном узле «Мотор-редуктор» шлицевое соединение на конце выходного вала. Это соединение лёгкой серии; точность центрирования – высокая; нагрузка – спокойная.
В данном случае твердость полумуфт высокая (сталь 40Х термообработанная). Применим способ центрирования по внешнему диаметру D .
Для рассматриваемого случая выберем основные параметры сопряжения для лёгкой серии [4 с. 250 табл. 4.71]: D = 30 мм; d = 26 мм; z = 6 мм; b = 6 мм.
Выберем поля допусков для центрирующего наружного диаметра D [9 с. 253 табл. 4.73]. Для размера D: – ø30 Н7n6.
Выберем поля допусков для нецентрирующих поверхностей по [9 с. 253 табл. 4.75]. Нецентрирующие размеры b диаметр d.
Для размеров: диаметр d – ø26 Н7 ширина шлица b – 8 F8f7.
Приведем стандартное обозначение выбранного шлицевого соединения шлицевого вала и шлицевой втулки [5]:
D – 6 х 26 Н7g6 х 30 Н7 n6 х 6
D – 6 х 26 g6 х 30 n6 х 6
D – 6 х 26 Н7 х 30 Н7 х 6F8.
Обозначение шлицевого соединения указывается на сборочном чертеже.
Дадим схемы расположения допусков сопрягаемых поверхностей для размеров: центрирующего наружного диаметра D и ширины шлица b.
Схема расположения полей допусков шлицевого соединения
для центрирующего наружного диаметра D
Схема расположения полей допусков шлицевого соединения
3. Расчёт параметров резьбового соединения
Цель: выбрать размеры и класс точности резьбового соединения; назначить поля допусков и степени точности изготовления элементов наружной резьбы (болта) d d2 d1 и внутренней резьбы (гайки) D D2 D1.
В ГОСТ 11708-66 приведены все основные определения резьбы.
Основными параметрами метрической резьбы являются: шаг резьбы Р; угол профиля α наружные диаметры резьбы болта и гайки соответственно обозначают d и D средние диаметры – d2 и D2 внутренние диаметры – d1 и высота витка – Н резьбы – это полуразность наружного и внутреннего диаметров резьбы (D–D1) 2.
Корпус узла «Мотор-редуктор» и крышки подшипниковых узлов стянуты винтами. В корпусе нарезана резьба. Винт образует резьбовое соединение в данном случае – М5. Основное требование предъявляемое к резьбовому соединению – это не допустить осевого смещения подшипниковых узлов в процессе эксплуатации. Для нашего случая выберем средний класс точности резьбы – 6-я степень точности характер сопряжения болта (винта) и гайки (корпус) – Hg и длина свинчивания – 30 мм.
У резьбы М5 – шаг равен Р = 08 мм.
Исходя из установленных условий найдем номинальные диаметры резьбы предельные отклонения на диаметры и предельные размеры которые сведём в таблицу.
Результаты расчетов параметров резьбы
Стандартное обозначение резьбового соединения: М5 – 6H6g.
Схема расположения полей допусков для наружной резьбы
Схема расположения полей допусков для внутренней резьбы
Схема расположения полей допусков для резьбового соединения
Расчет размерных цепей
Цель: Установить допуски и предельные отклонения на составляющие звенья размерной цепи.
Размерной цепью называют совокупность взаимосвязанных размеров образующих замкнутый контур и определяющих взаимное расположение поверхностей одной или нескольких деталей. (ГОСТ 16319–80)..
Размеры составляющие размерную цепь называют звеньями. В размерную цепь могут входить размеры любого типа: линейные размеры – диаметральные осевые расстояния между осями поверхностями зазоры натяги отклонения формы и отклонения расположения поверхностей и т. п.; угловые размеры – углы между плоскостями осями между осью и плоскостью и т. п.
Звенья размерной цепи подразделяют на составляющие звенья и на замыкающее звено (исходное). Замыкающее звено – это звено которое при сборке является последним или изготавливается последним. При расчете размерной цепи к этому звену предъявляются основные требования в отношении точности данной сборки или данной детали.
Остальные звенья составляющие цепь по своему влиянию оказываемому на замыкающее звено делятся на увеличивающие и на уменьшающие. Увеличивающие – это звенья при увеличении которых увеличивается и замыкающее звено. Уменьшающие – это звенья при увеличении которых уменьшается замыкающее звено.
Сборочная размерная цепь – это цепь звеньями которой являются размеры отдельных деталей. такая цепь определяет точность расположения заданных поверхностей данной сборочной единицы или всей машины.
Линейная размерная цепь – это цепь звеньями которой являются линейные размеры расположенные на параллельных прямых линиях.
Угловая размерная цепь – это цепь звеньями которой являются угловые размеры расположенные в одной плоскости и имеющие общую вершину.
Плоская размерная цепь – это цепь звеньями которой являются линейные и угловые размеры расположенные в одной или нескольких параллельных плоскостях.
Пространственная размерная цепь – это цепь звеньями которой являются линейные и угловые размеры расположенные в пространстве произвольно.
Метод max-min – метод пригонки – метод компенсации накопленных погрешностей в размерных цепях. Сборочную единицу собирают по методу полной взаимозаменяемости деталей являющихся составляющими звеньями без увязывающего звена и измеряют получившийся при сборке действительный зазор замыкающего звена А. Потом компенсируют накопленную погрешность пригонкой размера увязывающего звена А увяз так чтобы получился требуемый размер зазора замыкающего звена А с допуском требуемым по чертежу. Разумеется что предварительный размер увязывающего звена назначается с припуском под пригонку [6].
Составим схему размерной цепи (рис. 5.1). Размерная цепь указанная в задании является конструкторской сборочной линейной. Она состоит из шести звеньев А1 А2 А4 А5 А6 и замыкающего звена А. Замыкающим звеном является зазор между крышкой подшипникового узла и пдшипником необходимый для обеспечения нормальных условий работы подшипника.
Звено А6 является увеличивающим так как при его увеличении увеличивается замыкающее звено А. а звенья А1 А2А4 А5 являются уменьшающими так как при их увеличении уменьшается замыкающее звено А.
Номинальные размеры составляющих звеньев известны по заданию:
А1 = 16 мм; А2 = 23–012 мм;
А3 = 8 мм; А4 = 30 мм;
А5 = 23–012 мм; А6 = 100 мм.
Предельные размеры замыкающего звена также заданы: А = 0+08 мм.
Решим прямую задачу т.е. назначим допуски и предельные отклонения на составляющие звенья размерной цепи используя метод max-min.
Среднюю точность составляющих звеньев определим по числу единиц допуска:
где а – число единиц допуска;
ТА – допуск замыкающего звена мкм;
n – число составляющих звеньев.
Величину допуска замыкающего звена определим по формуле:
ТА = А max – А min = 08 – 0 = 08 мм = 800 мкм.
Единицы допусков для составляющих звеньев iк найдем в зависимости от номинальных размеров [6]:
Определим ближайший более точный квалитет которым является 11-й при а = 100. Поля допусков охватывающих размеров назначим как на основные отверстия – Н11 а на охватываемые размеры как на основной вал – h11. Допуски и предельные отклонения не указывают на одно из составляющих звеньев называемое увязывающим обычно самое простое в изготовлении. В данной конструкции в качестве увязывающего звена примем = 8мм.
С учетом вышеизложенного имеем составляющие звенья с предельными отклонениями:
А1 = 16 h11– 0110 мм;
А2 = 23– 0120 мм (по заданию);
А4 = 30 h11– 0130 мм;
А5 = 23 –0120 (по заданию);мм;
А6 = 100 Н11+0220 мм.
Номинальный размер замыкающего звена А определим по формуле:
Аiум – номинальные размеры уменьшающих звеньев.
А = 100 – (16 + 23 + 8 + 30 + 23) = 0 мм.
Предельные отклонения и допуск замыкающего звена по заданию составляют:
ТА = ЕSА – ЕIА = 08 – 0 = 08 мм.
Допуск и предельные отклонения увязывающего звена определим из выражений:
ТА3 увяз = ТА – ТАiув – ТАiум = ТА – ТА6 – (ТА1 + ТА2 + ТА4 + ТА5)
= 08 – 0220 – (0110 + 0120 + 0130 + 0120) = 01 мм.
ЕSА3 увяз = ЕIАiув – ЕSАiум – ЕIА = ЕIА6 – (ЕSА1 + ЕSА2 + ЕSА4 + ЕSА5) –
– ЕIА = 0 – (0 + 0 + 0 + 0) – 0 = 0 мм.
ЕIА3 увяз = ЕSАiув – ЕIАiум – ЕSА = ЕSА6 – (ЕIА1 + ЕIА2 + ЕIА4 + ЕIА5) –
– ЕSА = 0220 + (0110 + 0120 + 0130 + 0120) – 08 =
ТА3 = ЕSА3 – ЕIА3 = 01 – (– 01) = 02 мм.
Таким образом допуски и предельные отклонения назначены на все размеры входящие в размерную цепь.
Решим обратную задачу.
Имеем номинальные размеры составляющих звеньев с предельными отклонениями:
А1 = 16 h11– 0110 мм; А2 = 23– 0120 мм (по заданию);
А4 = 30 h11– 0130 мм; А5 = 23 –0120 (по заданию) мм; А6 = 100 Н11+0220 мм.
Проведем расчёт взяв значения ЕSА3 и ЕIА3 и преобразуя формулы из прямой задачи. Тогда:
ЕSА = ЕSАiув – ЕIАiум – ЕIА3 = ЕSА6 – (ЕIА1 + ЕIА2 + ЕIА4 + ЕIА5) –
– ЕIА3 = 0220 + (0110 + 0120 + 0130 + 0120) – (– 01) = 08 мм.
ЕIА = ЕIАiув – ЕSАiум – ЕSА3 = ЕIА6 – (ЕSА1 + ЕSА2 + ЕSА4 + ЕSА5) –
– ЕSА3 = 0 – (0 + 0 + 0 + 0) – 0 = 0 мм.
ТА = ЕSА – ЕIА = 08 – 0 = 08 мм.
Сравним полученное значение ТА с помощью расчета: ТА = 08 мм
и значение ТА имеющееся по заданию: ТА = 08 мм.
Они равны. Следовательно – задача решена верно.
Окончательные значения размеров запишем в таблицу
Параметры звеньев размерной цепи
Обозначения размеров
Правила нормы требования к определенному объекту (в приведенных примерах объектами являлись линейные размеры поля допусков основных отверстий и валов) оформляются в виде документа называемого стандартом. Соответственно установление и применение указанных правил норм требований т.е. стандартов называется стандартизацией.
Стандартизация основывается на объединенных достижениях науки техники и передового производственного опыта. Применительно к рассматриваемым нами вопросам она определяет не только сегодняшнее состояние науки о точности исполнения размеров и ее применение при изготовлении изделий но и ее будущее развитие.
В более общем случае стандартизация предусматривает установление единых физических величин терминов и обозначений требований к продукции и производственным процессам (выбор и определение характеристик и качественных показателей продукции методов контроля и измерения технологических процессов и т.п.) а также требований обеспечивающих безопасность труда и сохранность материальных ценностей.
В Системе сертификации ГОСТ Р предусмотрен следующий порядок проведения сертификации:
Принятие решения по декларации – заявке. Для проведения сертификации по правилам Системы отечественный или иностранный заявитель направляет декларацию – заявку установленного образца в ОС который в течение 3-х дней сообщает заявителю основные условия сертификации ИЛ (или их перечень для выбора заявителем) где будут проводиться испытания.
Анализ полученных результатов и принятие решения о возможности выдачи сертификата соответствия.
Выдача сертификата соответствия и внесение этой продукции в Государственный Реестр Системы.
Система имеет право признания иностранных сертификатов на продукцию подлежащую обязательной сертификации. Решение об этом принимает ОС.
Современное машиностроение основано на взаимозаменяемости обладает высокой производительностью точностью и высоким качеством изготовления.
Из изученного курса становится ясно что современные измерительные средства благодаря своей точности обеспечивают взаимозаменяемость без которой невозможно изготовление размеров в пределах допусков система которых является основой взаимозаменяемости. Современные средства измерения в автоматизированном производстве машин становятся управляющими регулирующими технологический процесс. Эта роль средств измерения по мере автоматизации производства будет возрастать.
Характерной особенностью современного машиностроения является широкая автоматизация и роботизация использование гибких автоматизированных производств. В них на качество продукции особенно влияют соблюдение условий взаимозаменяемости рациональное назначение допусков и посадок правильный выбор средств измерения в устройстве которых все шире применяется микропроцессорная вычислительная техника цифровая индикация автоматизация как самого процесса измерения так и математической обработки результатов измерения и оценка годности контролируемого размера.
В данной курсовой работе были привиты навыки пользования нормативно-технической документации и освоена правильность применения полученных знаний по выбору сопряжений и расчёту их параметров при решении конкретных инженерных задач.
Список использованных источников
Анухин В.И. Допуски и посадки: учебное пособие для вузов .В.И. Анухин. – 3-е изд. – СПб: Питер 2005. –206 с.
Анурьев В.И. Справочник конструктора-машиностроителя. Т. 1 2 3. – М.: Машиностроение 2001.
Димов Ю.В. Метрология стандартизация и сертификация: учебник для вузов Ю.В. Димов. – 2-е изд. – М.: Питер 2004. – 432 с.
Никифоров А.Д. Взаимозаменяемость стандартизация и технические измерения: учебное пособие А.Д. Никифоров. – 2-е изд. стереотип. – М.: Высш. школа 2002. –510 с.
Романов А.Б. Таблицы и альбом по допускам и посадкам: справ. пособие А.Б. Романов В.Н. Фёдоров В.Н. Кузнецов.– СПб: Политехник 2005. – 88 с.
Якушев А.И. Взаимозаменяемость стандартизация и технические измерения А.И. Якушев и др. – М.: Машиностроение 1987. – 352 с
МИНИСТЕРСТВО ОБРАЗОВАНИЯ И НАУКИ РФ
Федеральное государственное образовательное учреждение
высшего профессионального образования
«Сибирский федеральный университет»
РАСЧЁТНО-ПОЯСНИТЕЛЬНАЯ ЗАПИСКА
«Метрология стандартизация и сертификация»
тема «Расчёт и выбор посадок для сопряжений
сборочного узла «Мотор – редуктор»»
Спецификация.docx.doc
Колесо зубчатое (Z2)
Колесо зубчатое (Z3)
Винт М5х6g-30 ГОСТ 1491-87
Подшипник 7204 ГОСТ 333-79
Подшипник 7308 ГОСТ 333-79
Шпонка 14х9х25 ГОСТ 23360-78
Рекомендуемые чертежи
Свободное скачивание на сегодня
- 23.02.2023