Проектирование привода цепного транспортёра




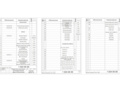
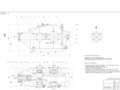
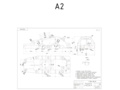
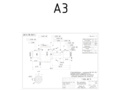
- Добавлен: 24.01.2023
- Размер: 2 MB
- Закачек: 0
Описание
Состав проекта
![]() |
![]() |
![]() ![]() ![]() ![]() |
![]() |
![]() ![]() ![]() ![]() |
![]() |
![]() ![]() ![]() ![]() |
![]() ![]() ![]() |
![]() ![]() ![]() ![]() |
![]() |
![]() |
![]() ![]() ![]() ![]() |
![]() |
Дополнительная информация
Промежуточный вал.dwg

Степень точности по ГОСТ 1643-81
Изм. № документа Дата
Вал-шестерня промежуточный
Сталь 45 ГОСТ 1050-74
Острые кромки скруглить R 0
Термообработка - улучшение HB 220 230
Неуказанные предельные отклонения размеров отверстий H14
Крышка редуктора.dwg

Отливка 3 класс ГОСТ 977-86 Точность отливки 10-00-10 ГОСТ 26645-85 2. Общие допуски по ГОСТ 308931 h14 3. Неуказанные литейные радиусы 3мм 4. неуказанные литейные уклоны 5 град. 5. Элемнты
размеры которых указаны в квадратных скобках обрабатывать в сборе с корпусом
Быстроходное колесо.dwg

Колесо коническое быстроходной ступени
Сталь 40Х ГОСТ 4543-71
Острые кромки скруглить R 0
Термообработка - улучшение HB 260 280
Неуказанные предельные отклонения размеров отверстий H14
Коэффициент смещения исходного контура
Степень точности по ГОСТ 1643-81
Пояснительная Записка.docx
Федеральное агентство по образованию
ИРКУТСКИЙ ГОСУДАРСТВЕННЫЙ ТЕХНИЧЕСКИЙ УНИВЕРСИТЕТ
Руководитель Зайцев В. И.
Проектирование привода цепного транспортера
ПОЯСНИТЕЛЬНАЯ ЗАПИСКА
к курсовому проекту по дисциплине
«Детали машин и основы конструирования»
студент группы СМ-07-2Полканов А. С.
Доцент к. т. н.3айцев В. И.
Курсовой проект защищен
Задание на курсовое проектирование
1.Кинематическая схема привода ..
2.График нагрузки .
4.Постановка задачи .
Выбор электродвигателя .
Расчет основных параметров редуктора .
Расчет конической зубчатой передачи .
1.Материал колеса и шестерни
2.Допускаемые напряжения
3.Внешний делительный диаметр колес
4.Внешний окружной модуль числа зубьев колеса и шестерни ширина зубчатого колеса
5.Углы делительных конусов .
6.Внешнее делительное конусное расстояние ширина колеса ..
7.Внешний делительный диаметр шестерни внешние диаметры вершин шестерни и колеса .
8.Средний окружной модуль ..
9.Проверка зубьев шестерни и колеса на выносливость по контактным напряжениям
10.Силы в зацеплении
Расчет цилиндрической зубчатой передачи .
2.Расчет допускаемых контактных напряжений
3.Расчет геометрических параметров цилиндрической зубчатой передачи
4.Проверка прочности зубьев второй ступени
Предварительный расчет валов
Конструктивные размеры корпуса редуктора ..
Первый этап компоновки редуктора
Проверка долговечности подшипников .
Второй этап компоновки редуктора
Проверка прочности шпоночных соединений
Уточненный расчет валов
Посадка деталей редуктора. Шероховатость поверхностей
Список используемой литеретуры
Задание на курсовое проектирование
1.Кинематическая схема привода
Скорость транспортера
Число зубьев звездочки
Коэффициент суточного использования
Коэффициент годового использования
Приводной вал транспортера со звездочкой и муфтой
Рабочие чертежи деталей редуктора
Выбор электродвигателя
Мощность на выходном валу
гдеV – окружная скорость (мс);
F – окружное усилие (Н).
– КПД пары подшипников;
– КПД зубчатой пары;
Требуемая мощность двигателя
Так как двигатель часть времени перегружен а часть времени недогружен что видно из графика нагрузки нет необходимости выбирать двигатель по потребной мощности. Вместо этого с помощью данных графика нагрузки рассчитывается эквивалентный крутящий момент:
Из графика нагрузки (стр.3)
Эквивалентная мощность
Из каталога электродвигателей выбирается ближайший больший по мощности двигатель т.е. двигатель мощностью 3кВт. Возможные варианты:
Так как в двигателях присутствует эффект проскальзывания номинальная частота вращения несколько меньше синхронной частоты данной в паспорте:
Для сокращения числа вариантов двигателей рассчитаем требуемые передаточные отношения для каждого из них и выберем наиболее легко осуществимые. Для этого рассчитывается частота вращения выходного вала
гдеV – окружная скорость транспортера (стр. 4);
D – делительный диаметр звездочки.
Передаточное отношение для различных вариантов электродвигателей:
Для первого двигателя необходимо реализовать достаточно большое передаточное отношение. Для второго довольно сложно обеспечить точность передаточного отношения. Наиболее выгодным является третий вариант двигателя поскольку передаточное отношение довольно небольшое и его легко разбить между двумя ступенями.
Согласно рекомендациям для коническо-цилиндрических редукторов:
передаточное число тихоходной ступени редуктора:
передаточное число быстроходной ступени редуктора:
Передаточное число редуктора:
Таким образом окончательно принимается двигатель 4А112MA6.
Так как потребная мощность а располагаемая то во время работы двигатель не перегружен т.е. подходит для данного привода.
Расчет основных параметров редуктора
Передаточное отношение редуктора (стр. 9)
Передаточное отношение ступеней редуктора (стр.8) по ГОСТ 21426-75
Частоты вращения и угловые скорости валов.
Крутящие моменты валов.
где - крутящий момент на валу двигателя:
Результаты расчетов сводятся в табл. 2.
Расчет конической зубчатой передачи
– вращающий момент на шестерне;
– вращающий момент на колесе;
– частота вращения шестерни;
– частота вращения колеса;
– передаточное число.
1.Материалы колеса и шестерни
Шестерня - Ст. 40Х. Применяем термообработку колеса: улучшение: твердость НВ=270.
Колесо - Ст. 40Х. Применяем термообработку колеса: улучшение : твердость НВср=245.
2.Допускаемые напряжения
Допускаемые контактные напряжения:
где – предел контактной выносливости:
– коэффициент запаса прочности минимальное значение 11 принимаем ;
– коэффициент долговечности:
где – базовое число циклов перемен напряжений:
– эквивалентное число циклов перемен напряжений:
где – коэффициент приведения: ;
– ресурс редуктора (ч.):
3.Внешней делительный диаметр колеса
где – коэффициент для колес с круговым зубом: ;
– коэффициент нагрузки; при консольном расположении шестерни ;
– коэффициент ширины венца по отношению к внешнему конусному расстоянию: ;
– передаточное отношение: ;
по ГОСТ 12289-76 принимаем .
4.Внешний окружной модуль числа зубьев колеса и шестерни ширина зубчатого колеса
Примем число зубьев шестерни .
Число зубьев колеса .
Тогда отклонение от заданного .
Внешний окружной модуль выбираем из соотношения:
по ГОСТ 9563-80 принимаем
Уточняем значение отклонение от заданного .
5.Углы делительных конусов
6.Внешнее делительное конусное расстояние ширина колеса
7.Внешний делительный диаметр шестерни внешние диаметры вершин шестерни и колеса
Внешний делительный диаметр шестерни:
Средний делительный диаметр шестерни и колеса:
Внешние диаметры окружностей вершин шестерни и колеса:
8.Средний окружной модуль окружная скорость
Средний нормальный модуль
Средняя окружная скорость
Для конических передач обычно назначают 7-ю степень точности.
9.Проверка зубьев шестерни и колеса на выносливость по контактным напряжениям
Коэффициент ширины шестерни по среднему диаметру
Уточняем значение коэффициента нагрузки
т.к. (табл.3.5 [8]).
10.Силы в зацеплении
– угол зацепления; по ГОСТ 13755-81.
Радиальная для шестерни равная осевое колеса
Осевая для шестерни равная радиальной для колеса
11.Проверка зубьев на выносливость по напряжениям изгиба
где – коэффициент нагрузки;
– коэффициент формы зуба;
– коэффициент учитывающий понижение нагрузочной способности .
Коэффициент нагрузки определяется аналогично коэффициенту
т.к. (табл.3.7 [8]).;
Для определения коэффициентов формы зуба находим эквивалентные числа зубьев шестерни и колеса
где т.к. колесо с круговым зубом ;
Допускаемые напряжения изгиба
Для колес из стали 40Х улучшенной по табл. 3.9. [8] значение
Коэффициент запаса прочности
где - коэффициент учитывающий нестабильность свойств
материалов зубчатых колес.
- коэффициент учитывающий способ получения заготовки.
Принимаются следующие значения коэффициентов:
(стр. 44 [8] для поковок).
Дальнейший расчет необходимо вести для того зубчатого колеса для которого отношение меньше.
дальнейший расчет проводится для колеса.
Результаты расчетов сводятся в табл. 3.
Основные параметры быстроходной ступени Табл.3.
Геометрические параметры быстроходной передачи
Внешний делительной диаметр мм
Внешний торцовый модуль мм
Внешнее конусное расстояние мм
Средний нормальный модуль мм
Средний угол наклона зуба град
Угол делительного конуса град
Расчет цилиндрической зубчатой передачи
– вращающий момент на колеса;
Для шестерни – сталь 45 термическая обработка – улучшение твердость после термической обработки НВ230;
Для колеса – сталь 45 термическая обработка – улучшение твердость после термической обработки НВ200 (принимается ниже чем для шестерни).
2. Расчет допускаемых контактных напряжений.
Допускаемые контактные напряжения определяются по формуле
где - предел контактной выносливости при базовом числе циклов;
- коэффициент долговечности при расчете по контактным напряжениям;
– коэффициент запаса контактной прочности.
Согласно табл. 3.2. [8] при твердости HB350 и термообработке улучшение предел контактной выносливости
Коэффициент долговечности
где – базовое число циклов;
– эквивалентное число циклов перемены напряжений;
В среднем можно принять
где – ресурс редуктора (мин);
Для случая если то принимается поэтому
(для колес из улучшенной стали). Таким образом
Расчетное допускаемое контактное напряжение для непрямозубых колес
После расчета необходимо проверить выполнение условия
расчет выполнен верно.
3.Расчет геометрических параметров цилиндрической зубчатой передачи
Межосевое расстояние
Коэффициент для косозубых колес принимается равным 430 (стр. 32[8]). Коэффициент ширины для косозубых колес рекомендуется принимать в пределах 025÷04. Принимается коэффициент Из табл. 3.1. [8] при несимметричном расположении зубчатых колес относительно опор твердости зубьев HB350 принимается .
Согласно ГОСТ 2185 – 81 принимается ближайшее стандартное межосевое расстояние
Модуль зацепления нормальный
Согласно ГОСТ 9563 – 80 принимается стандартное значение модуля из второго ряда
Предварительно задаемся углом наклона зуба (согласно стр. 14 [3] в пределах 8÷18)
Уточняем угол наклона зуба .
Делительные диаметры
Проверка межосевого расстояния
Значения сходятся без погрешностей следовательно расчет выполнен верно.
Диаметры окружностей вершин зубьев
Согласно ряду 5 предпочтительных чисел ширина колеса принимается равной
Коэффициент ширины шестерни по диаметру
Окружная скорость зубчатых колес
Согласно табл. 3.6. [8] при скоростях до 5мс назначается восьмая степень точности.
4.Проверка прочности зубьев второй ступени
По контактным напряжениям
Коэффициент нагрузки
Контактные напряжения
Относительное перенапряжение
что в пределах допустимого.
По напряжениям изгиба
где - коэффициент нагрузки.
-коэффициент учитывающий форму зуба и зависящий от эквивалентного числа зубьев;
-коэффициент учитывающий погрешности расчетной схемы зуба;
-коэффициент учитывающий неравномерность распределения нагрузки между зубьями.
где – коэффициент неравномерности распределения нагрузки;
– коэффициент динамичности.
(табл. 37. [8] при );
(табл. 3.8. [8] при твердости HB350 скорости до 3мс).
Эквивалентные числа зубьев
Для колес из стали 45 с термообработкой улучшение по табл. 3.9. [8] значение
Дальнейший расчет необходимо вести для того зубчатого колеса для которого отношение больше.
Запас изгибной прочности может быть равным 10 для закрытых зубчатых передач. В данном случае
Результаты расчетов сводятся в табл. 4.
Основные параметры тихоходной ступени Табл.4.
Геометрические параметры тихоходной передачи
Межосевое расстояние мм
Модуль зацепления нормальный мм
Угол наклона зубьев град
Делительный диаметр мм
В ходе расчетов производились некоторые округления например чисел зубьев которые могли изменить кинематику редуктора. Поэтому следует проверить действительное передаточное отношение
Как видно реальное передаточное отношение более точно нежели теоретическое (14) рассчитанное в начале (требуемое передаточное отношение – 1433).
Предварительный расчет валов
Так как на данном этапе неизвестны расстояния между опорами расчет валов ведется на чистое кручение. Допускаемые напряжения для любого материала принимаются заниженными в пределах 15-25МПа. В данном случае примем
Минимальный диаметр вала
Этот вал соединяется с валом двигателя муфтой МУВП. Диаметр вала двигателя Из табл. 20.6.3 [4] видно что полумуфту с отверстием такого диаметра можно включать в пару с полумуфтой с минимальным диаметром отверстия Поэтому диаметр вала увеличим до 25мм. Окончательно
Диаметр вала под подшипники
Длина ступицы шестерни
Шестерня выполняется заодно с валом.
Диаметр вала под зубчатым колесом
Диаметр ступицы колеса (быстроходного)
Длина ступицы колеса
Диаметр вала под муфту
Диаметр ступицы колеса (тихоходного)
В массовом производстве цилиндрические колеса при нарезании зубьев обрабатываются «пакетами» по два и более. При этом ступица не должна выступать за торец венца табл. 10.1 [8] т.е. .
Конструктивные размеры корпуса редуктора
Толщина стенки корпуса согласно табл. 102 [8]
Толщина фланцев поясов корпуса и крышки:
верхнего пояса корпуса и пояса крышки
нижнего пояса корпуса
Диаметр болтов: фундаментных ;
принимаем болты с резьбой М18;
Крепящих крышку к корпусу у подшипников
принимаем болты с резьбой М14;
Соединяющих крышку с корпусом
принимаем болты с резьбой М10.
Первый этап компоновки редуктора
Первый этап компоновки проводится для определения приближенного положения зубчатых колес редуктора относительно опор. Это позволит определить опорные реакции и произвести выбор подшипников.
Компоновочная схема выполнена в системе AutoCAD. Изначально проводятся три вертикальные линии через центры валов на расстоянии соответствующем межосевым расстояниям. Затем проводится горизонтальная линия проходящая через центры шестерни и колеса первой ступени. Упрощенно в виде прямоугольников вычерчиваются шестерня и колесо первой ступени. Вычерчивается ступица колеса выполненная несимметричной в целях уменьшения ширины редуктора. На расстоянии 10мм от венца колеса проводится горизонтальная линия соответствующая торцовой поверхности венца тихоходной ступени. Упрощенно вычерчиваются шестерня и колесо второй ступени. Вычерчивается внутренняя стенка корпуса. Принимаются следующие величины зазоров:
а)зазор между торцом шестерни первой ступени и торцом колеса второй ступени
где - толщина стенки корпуса согласно стр.31: .
б)зазор от окружности вершин колеса второй ступени до стенки корпуса
Предварительно для первого вала назначаются шарикоподшипники конические легкой серии . Для второго вала – шарикоподшипники конические средней серии . Для третьего вала примем радиально-упорные шарикоподшипники средней узкой серии т. к. более легкой серии подшипников на валы такого диаметра по каталогу нет. Основные характеристики и размеры подшипников заносятся в табл. 5. Радиально-упорные подшипники устанавливаем по схеме «враспор».
Основные параметры выбранных подшипников Табл.5.
Условное обозначение подшипника
Для смазки подшипников принимается пластичный смазочный материал. Поэтому для предотвращения вымывания смазки и протекания ее внутрь корпуса устанавливаем мазеудерживающие кольца. Толщину колец примем одинаковой на всех валах и равной 11 мм. Кольца на валах устанавливаются таким образом чтобы они заходили внутрь полости корпуса на 2 мм (для проявления эффекта маслоотбрасывания).
Расстояние между точкой пересечения нормалей и торцом подшипника для однорядных конических роликоподшипников:
Размер между реакциями подшипников ведущего вала:
После нанесения линий контуров деталей измерениями устанавливаются расстояния .
Снятые с компоновочной схемы расстояния заносятся в табл.6.
Расстояния между силовыми участками валов Табл.6.
Расстояние между опорами валов мм
Длины силовых участков мм
Проверка долговечности подшипников
Силы действующие в зацеплении:
Реакции опор в плоскости XOZ:
Реакции опор в плоскости YOZ:
Осевые составляющие радиальных реакций конических подшипников:
Осевые нагрузки подшипников при ; (табл.921 [8]):
Рассмотрим левый подшипник2.
Отношение поэтому следует учитывать осевую нагрузку.
Эквивалентная нагрузка:
где - коэффициент радиального нагружения: (табл.918 [8]);
– коэффициент вращения одного из колец: ;
- коэффициент осевого нагружения: (П.6[8]);
- коэффициент безопасности: (табл.919 [8]);
– температурный коэффициент: (табл.920 [8]).
Расчетная долговечность (млн. об. для шарикоподшипников)
где – динамическая грузоподъемность по каталогу;
– эквивалентная (приведенная) нагрузка на подшипник.
Расчетная долговечность в часах:
Ресурс редуктора определен на стр.12 и составляет 141912 часов. Как видно долговечность подшипника выше срока службы поэтому подшипник принимается окончательно.
Рассмотрим правый подшипник 1.
Отношение поэтому при подсчете эквивалентной нагрузки осевые силы не учитывают.
Рассмотрим левый подшипник 3.
Рассмотрим правый подшипник 4.
Проверка подшипников производится по наиболее нагруженной опоре 5.
Величина осевых составляющих (для шарикоподшипников)
(согласно табл. 9.18. [8] для подшипников с углом контакта 26º).
В данном случае поэтому осевая нагрузка на подшипники (согласно табл. 9.21. [2]):
Рассмотрим левый подшипник 5.
Отношение осевую нагрузку не следует учитывать при расчете долговечности.
Эквивалентная нагрузка на подшипник
(всегда при вращении внутреннего кольца);
(табл. 9. 20. [8] при температуре 125ºC);
Ресурс редуктора определен на стр. 12 и составляет 141912 часов. Как видно долговечность подшипника значительно выше срока службы поэтому подшипник принимается окончательно
Рассмотрим правый подшипник 6.
Отношение осевую нагрузку следует учитывать при расчете долговечности.
Второй этап компоновки редуктора
Второй этап компоновки имеет целью конструктивно оформить зубчатые колеса валы и подготовить данные для проверки их на выносливость а так же шпоночных соединений на смятие.
На всех валах в местах перехода от участков посадки подшипников и колес к другим участкам выполняются канавки для выхода шлифовального круга. Это связано с требованиями к низкой шероховатости поверхности (по ГОСТ 2789 – 73 Ra=04 – 16 мкм) в этих местах. Размеры канавок принимаются по табл. 6.9. [3].
Радиусы галтелей принимаются по рекомендациям стр. 95 [6].
Размеры крышек подшипников и их крепежных болтов а так же количество крепежных болтов приняты согласно рекомендациям §15 [3]. Все фланцы крышек подшипников расположим на одном уровне.
Длины консольных участков валов предназначенных для установки полумуфт (измеряемых от соответствующих крышек подшипников):
а) входного вала – 85мм;
б) выходного вала – 110 мм.
Принимаются призматические шпонки со скругленными торцами по ГОСТ 23360 – 78. Длины принимаются из стандартного ряда на 5 – 10 мм меньше чем длина участка вала.
В сквозные крышки подшипников устанавливаются резиновые армированные манжеты. Их размеры принимаются по табл. 9.16. [8].
Указываются необходимые размеры для опасных сечений (см. схему окончательной компоновки).
Проверка прочности шпоночных соединений
Материал шпонок – сталь 45 нормализованная. Шпоночные соединения рассчитываются на смятие. Условие прочности на смятие:
где - высота шпонки;
- глубина паза вала.
(при стальной ступице колеса).
(при чугунной ступице колеса или полумуфты).
Шпонка 1 (в соответствии с схемой окончательной компоновки)
прочность обеспечена.
Уточненный расчет валов
Проверка прочности валов проводится для определения действительных коэффициентов запаса выносливости. При этом принимается что нормальные напряжения изменяются по симметричному циклу а касательные – по отнулевому. Проверка проводится для предположительно опасных сечений обозначенных на окончательной компоновочной схеме. Расстояния до этих сечений от опор (необходимы для определения изгибающих моментов) так же обозначены на схеме.
Материал вала – сталь 40Х.
Предел прочности стали (согласно табл. 3.3. [8]);
Предел выносливости по нормальным напряжениям
Предел выносливости по касательным напряжениям
Это сечение ослаблено шпоночным пазом который к тому же вызывает концентрацию напряжений.
Коэффициент запаса прочности по касательным напряжениям
где - амплитудное напряжение цикла;
- среднее напряжение цикла;
– эффективный коэффициент концентрации кастельных напряжений;
– масштабный фактор для кастельных напряжений;
- коэффициент чувствительности материала к асимметрии цикла.
Для отнулевого цикла
Размеры вала и шпоночной канавки обозначены на схеме.
Столь большой коэффициент запаса объясняется тем что размер вала значительно больше чем тот что получился из прочностных расчетов.
Согласно ГОСТ 16162 – 78 конструкция вала должна предусматривать возможность радиальной консольной нагрузки приложенной к началу посадочной части вала. Величина этой нагрузки на быстроходном валу должна быть при 25Нм250Нм.
Изгибающий момент в сечении А-А.
Коэффициент запаса прочности по нормальным напряжениям
– эффективный коэффициент концентрации нормальных напряжений;
– масштабный фактор для нормальных напряжений;
Для симметричного цикла
Результирующий коэффициент запаса прочности
В этом опасном сечении действуют максимальные изгибающие моменты и крутящий момент.
Суммарный изгибающий момент
Момент сопротивления сечения
Амплитуда нормальных напряжений
Полярный момент сотротивления
Амплитуда и среднее напряжение цикла касательных напряжений
Для обеспечения прочности коэффициент запаса должен быть не меньше . Учитывая требования жесткости рекомендуют . Полученное значение достаточно.
В связи с большими запасами прочности проверять сечение В-В нет необходимости. К тому же в сечении В-В вал имеет большой диаметр.
Материал вала – сталь 45.
Предел прочности стали (тадл.3.3 [8]);
Предел выносливости по нормальным напряжениям ;
Предел выносливости по касательным напряжениям .
Коэффициент запаса прочности по касательным напряжениям.
Изгибающий момент возьмем из эпюры моментов (стр.39)
В связи с большими запасами прочности проверять сечения Б-Б и Е-Е нет необходимости. К тому же в сечении Д-Д вал имеет большой диаметр а в сечении Е-Е отсутствует крутящий момент.
Это сечение ослаблено шпоночной канавкой.
Изгибающий момент возьмем из эпюры моментов (стр.42)
Определение коэффициента запаса прочности по касательным напряжениям.
Изгибающий момент в сечении З-З.
Результаты расчетов для всех сечений сводятся в табл. 7.
Коэффициенты запаса прочности в различных сечениях Табл. 7.
Коэффициент запаса s
В качестве прототипа корпуса взят корпус из [7] стр. 124. Толщина стенки корпуса (стр. 31) . Согласно табл. 9.2. [3] диаметр винтов соединяющих крышку и корпус принимается . Количество винтов – 10шт. Диаметр отверстия под винт в крышке корпуса принимается .
Зазоры между окружностями вершин зубчатых колес и внутренней стенкой редуктора принимаются равной толщине стенки
Ширина фланца крышки и корпуса
Толщина фланца крышки и корпуса
Высота бобышки под болт принимается минимальной для возможности установки болта между приливами под подшипник:
Толщина ребер жесткости принимается равной толщине стенки:
Диаметр фрезерованного углубления под болт
Винты пружинные шайбы штифты принимаются стандартными из [1].
Диаметр фундаментных болтов и их количество принимаются по табл. 9.3. [3]количество болтов
Толщина фланца для крепления к фундаменту
Размеры маслоуказателя принимаются согласно табл. 55 [7]. Длина стержня маслоуказателя составляет 230мм. Диамтр резьбы пробки – 16мм диаметр стержня маслоуказателя 6мм. На стержне нанесены метки в соответствии с нижним и верхним уровнями масла.
Для заливки масла и выхода расширяющегося воздуха устанавливается смотровой люк а в нем – пробка-отдушина. Размеры крышки и пробки-отдушины а так же крепежных винтов принимаются по табл. 10.12. [8].
В нижней части редуктора устанавливается пробка для слива отработанного масла М20 с шестигранной головкой.
Посадки деталей редуктора. Шероховатости поверхностей
Посадки деталей назначаются согласно табл. 10.13. [8].
Допуск вала для посадки внутренних колец подшипников – k6.
Посадки мазеудерживающих колец – H7k6.
Посадки зубчатых колес на валы - H7p6.
Допуск отверстий в корпусе редуктора под наружные кольца подшипников - H7.
Допуск на диаметр вала под полумуфту - n6.
Посадки крышек подшипников в отверстиях - H7h8.
Допуск отверстий под установку резиновых манжет принимается равным допуску на диаметр вала под полумуфту – n6.
Выбор шероховатостей производится согласно табл 16.3. [3] (параметр Ra).
Опорные поверхности под головки болтов и гаек – 63.
Поверхности фланцев крышки и картера – 25.
Внутренние поверхности камер подшипников – 125.
Неответственные поверхности для крепления через прокладки (например крышки смотрового окна) – 10.
Поверхности торцов камер подшипников – 63.
Центрирующие отверстия (под штифты) – 125.
Посадочные поверхности – 125.
Торцевые упорные поверхности рабочие поверхности шпоночных пазов – 32.
Шероховатость поверхностей зубьев восьмой степени точности – 16.
Смазывание зубчатых зацеплений производится окунанием зубчатых колес в масло заливаемое внутрь корпуса редуктора до уровня обеспечивающего погружение малого колеса примерно на (15÷3) m – т.е. на 5 – 8 мм.
Согласно табл. 10.8 [8] при контактных напряжениях 600МПа (действительное значение – 406МПа) и скорости от 2 до 5 мс (действительное значение – 39 мс) вязкость масла должна составлять 28 сСт. По табл. 10.10. [8] принимается масло индустриальное И-30А.
Камеры подшипников заполняются пластичным смазочным материалом – «Литол-24». Смазка в камерах подшипников периодически пополняется через снятые крышки.
Перед сборкой внутреннюю полость корпуса редуктора тщательно очищают и покрывают маслостойкой краской.
Сборка производится в соответствии со сборочным чертежом редуктора начиная с узлов валов:
на ведущий вал напрессовываются прдеварительно нагретые в масле до 100ºC мазеудерживающие кольца и подшипники;
в промежуточный и ведомый валы закладываются соответствующие шпонки затем напрессовываются соответствующие зубчатые колеса до упора в бурты валов. После этого напрессовываются предварительно разогретые в масле мазеудерживающие кольца и подшипники.
Фланец картера покрывается герметиком после чего в него укладываются валы в сборе.
Устанавливается крышка корпуса которая центрируется с помощью штифтов. Крышка притягивается к картеру винтами.
В камеры подшипников закладывается смазка (литол-24). В сквозные крышки подшипников с помощью оправки запрессовываются манжеты. На все крышки устанавливается набор регулировочных прокладок. Крышки пошипников устанавливают в камеры и прикручивают винтами.
Проверяется возможность проворачивания валов (от руки).
Устанавливается пробка маслоспускного отверстия и жезловый маслоуказатель. Через смотровое окно заливается масло (И-30А).
Устанавливается крышка смотрового окна с прокладкой и закрепляется винтами. Ввинчивается пробка-отдушина.
Собранный редуктор обкатывают и подвергают испытанию на стенде по программе устанавливаемой техническими условиями.
Список используемой литературы:
Анурьев В. И. Справочник конструктора – машиностроителя: В 3-х т. Т. 1. – 6-е изд. перераб. и доп. – М.: Машиностроение 1982. – 736 с. ил.
Ачеркан Н. С. Детали машин. Справочник: В 3-х т. Т. 1 2 3. – 3-е изд. перераб. и доп. – М.: Машиностроение 1969. ил.
Дунаев П. Ф. Леликов О. П. Детали машин. Курсовое проектирование: Учеб. пособие для машиностроит. спец. Техникумов. – М.: Высш. шк. 1984. – 336 с. ил.
Еремеев В. К. Горнов Ю. Н. Детали машин. Курсовое проектирование: Метод. указания и задания к проектам. – Иркутск: Изд-во ИрГТУ 2006. – 144 с.
Левятов Д. С. Расчеты и конструирование деталей машин: Учебник для техн. училищ. – 2-е изд. перераб. и доп. – М.: Высш. школа 1979. – 303 с. ил. – (Профтехобразование. Детали машин).
Иванов М. Н. Детали машин: Учеб. для студентов высш. техн. учеб. заведений. – 5-е изд. перераб. – М.: Высш. шк. 1991. – 383 с.: ил.
Цехнович Л. И. Петриченко И. П. Атлас конструкций редукторов.: Учеб. пособие. – 2-е изд. перераб. и доп. – К :Выща шк. 1990. – 151 с.: ил.
Парышев С. В. Вязкова Л. П. Черненко А. Г. Пример расчета конической зубчатой передачи: Метод. указания по курсам «Детали машин и основы конструирования» и «Механика». – Екатеринбург: Изд-во ГОУ ВПО УГТУ-УПИ 2002. – 16 с.
Спецификация.dwg

Колесо коническое быстроходное
Колесо цилиндрическое тихоходное
Крышка подшипника глухая
Пояснительная записка
Крышка стакана сквозная
Крышка подшипника сквозная
Мазеудерживающее кольцо
Манжета 45 ГОСТ 8752-79
Гайка М8 ГОСТ 5915-70
Подшипник 7206 ГОСТ 333-79
Подшипник 7307 ГОСТ 333-79
Подшипник 46310 ГОСТ 831-75
Манжета 25 ГОСТ 8752-79
Штифт 8 h8x24 ГОСТ 3128-70
Штифт 8 h8x70 ГОСТ 3128-70
Шпонка ГОСТ 23360-78
Редуктор.dwg

внутри редуктотра маслосттойкой краской
Необработанные поверхности красить
Плоскость разьема покрыть герметиком при окончательной сборке
Частота вращения быстроходного вала n=970 обмин.
Крутящий момент на тихоходном валу Т=962000 Нмм.
Технические требования
снаружи - серой нитроэмалью
Передаточное число редуктора u=9
Техническая характеристика
Допускается эксплотировать редуктор с отклонением от горизон-
тального положения на угол до 5°. При этом должен быть обеспечен
достаточным для смазки зацепления.
Изм. № документа Дата
Характеристика зацепления
Частота вращения быстроходного вала n=953 обмин.
Крутящий момент на тихоходном валу Т=376713 Нмм.
Передаточное число редуктора u=14
Рекомендуемые чертежи
- 02.10.2019
- 25.10.2022