Проектирование фасонного резца и протяжки круглой





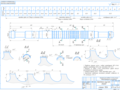
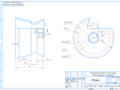
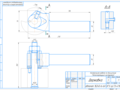
- Добавлен: 24.01.2023
- Размер: 129 KB
- Закачек: 0
Описание
Состав проекта
![]() |
![]() ![]() ![]() ![]() |
![]() ![]() ![]() ![]() |
![]() ![]() ![]() ![]() |
![]() ![]() ![]() ![]() |
![]() ![]() ![]() |
Дополнительная информация
державка.cdw

резец.cdw

протяжка.cdw

Чертеж.cdw

Рекомендуемые чертежи
- 24.01.2023