Проектирование фасонного резца и державки


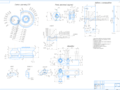
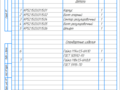
- Добавлен: 04.11.2022
- Размер: 3 MB
- Закачек: 0
Узнать, как скачать этот материал
Подписаться на ежедневные обновления каталога:
Описание
Курсовой проект - Проектирование фасонного резца и державки
Состав проекта
![]() |
![]() ![]() ![]() |
![]() ![]() ![]() ![]() |
![]() ![]() ![]() ![]() |
Дополнительная информация
Контент чертежей
Общий чертеж форм..cdw

Spetsifikatsia.cdw

Рекомендуемые чертежи
Свободное скачивание на сегодня
Обновление через: 15 часов 16 минут