Проектирование фасонного резца и протяжки




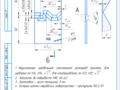
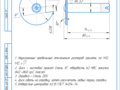
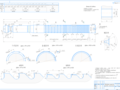
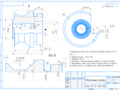
- Добавлен: 24.01.2023
- Размер: 4 MB
- Закачек: 0
Описание
Состав проекта
![]() |
![]() |
![]() |
![]() ![]() ![]() ![]() |
![]() ![]() ![]() ![]() |
![]() |
![]() |
![]() |
![]() ![]() ![]() ![]() |
![]() ![]() ![]() ![]() |
![]() |
![]() |
![]() ![]() ![]() ![]() |
![]() |
![]() ![]() ![]() |
![]() |
![]() |
![]() |
Дополнительная информация
Шаблон, контршаблон.cdw

Фасонный резец.cdw

Графическое профилирование круглого фасонного резца.cdw

Протяжка круглая групповой схемы рехания.cdw

Шаблон для контроля заточки.cdw

Рекомендуемые чертежи
- 24.01.2023