Проект организации участка по восстановлению распределительных валов строительной и дорожной техники





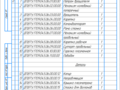
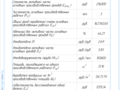
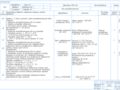
- Добавлен: 25.01.2023
- Размер: 1 MB
- Закачек: 1
Описание
Состав проекта
![]() |
![]() |
![]() |
![]() ![]() ![]() |
![]() ![]() ![]() |
![]() ![]() ![]() |
![]() ![]() ![]() |
![]() ![]() ![]() |
![]() ![]() ![]() |
![]() ![]() ![]() |
![]() ![]() ![]() |
![]() ![]() ![]() |
![]() ![]() ![]() |
![]() ![]() ![]() |
![]() ![]() ![]() |
![]() ![]() ![]() |
![]() ![]() ![]() |
![]() ![]() ![]() |
![]() ![]() ![]() |
![]() ![]() ![]() |
![]() ![]() ![]() |
![]() |
![]() |
![]() ![]() ![]() ![]() |
![]() ![]() ![]() ![]() |
![]() ![]() ![]() ![]() |
![]() ![]() ![]() ![]() |
![]() ![]() ![]() ![]() |
![]() ![]() ![]() ![]() |
![]() ![]() ![]() ![]() |
![]() ![]() ![]() ![]() |
![]() ![]() ![]() ![]() |
![]() ![]() ![]() ![]() |
![]() ![]() ![]() ![]() |
![]() ![]() ![]() ![]() |
![]() ![]() ![]() ![]() |
![]() ![]() ![]() ![]() |
![]() ![]() ![]() ![]() |
Дополнительная информация
Вал.cdw

копир.cdw

каретка.cdw

5. Компоновочный план производственного корпуса.cdw

9. Технологический процесс восстановления.cdw

3. Общий вид плазменной установки.cdw

10. Схема плазменной наплавки.cdw

11. Технико-экономические показатели.cdw

Спецификация 1.spw

8. Ремонтный чертеж распределительного вала.cdw

Спецификация 2.spw

2. Анализ технологических и технико-экономических показателей способов нанесения покрытий.cdw

7. Результаты экспериментальных исследований.cdw

6. Технологическая планировка участка.cdw

1. Общая структура дипломного проекта.cdw

Рекомендуемые чертежи
- 25.01.2023
- 11.09.2022
- 06.03.2015