Проект АТП на 90 автомобилей ВАЗ с разработкой слесарно-механического участка


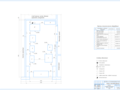
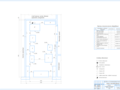
- Добавлен: 25.01.2023
- Размер: 443 KB
- Закачек: 0
Подписаться на ежедневные обновления каталога:
Описание
Проект АТП на 90 автомобилей ВАЗ с разработкой слесарно-механического участка
Состав проекта
![]() |
![]() ![]() ![]() |
![]() ![]() ![]() ![]() |
![]() ![]() ![]() ![]() |
![]() |
Дополнительная информация
Контент чертежей
1.docx
1 Расчет производственной мощности
Основные исходные данные для проектирования автотранспортного предприятия представлены в таблице 2.1.
Таблица 2.1 – Исходные данные для проектирования
Наименование показателя
Количество автомобилей
Среднесуточный пробег км
Количество рабочих дней в году дн
Категория условий эксплуатации
Расчет производственной программы по ТО и ремонту автомобилей необходимо начинать с выбора норм пробега автомобилей до ТО-1 ТО-2 и капитального ремонта (КР) с последующей их корректировкой по кратности с учетом среднесуточного пробега и между собой.
Периодичность воздействия данного вида (ТО-1 ТО-2 КР) с учетом условий эксплуатации определяется из выражения:
ki - результирующий коэффициент корректирования пробега для данного вида воздействия.
Согласно [1] принимаем следующие нормативные значения:
LТО-1н = 10000 км – периодичность ТО-1;
LТО-2н = 20000 км – периодичность ТО-2;
LКРн = 150000 км – пробег до капитального ремонта.
Корректируем пробег до капитального ремонта:
LКР = LКРн kКР = LКРн k1 k2 k3 = 150 000 08 1= 120 000 км.
где k1 = 08; k2 = 1; k3 = 1 – коэффициенты корректировки учитывающие условия эксплуатации [1 таблицы 2.7- 2.9].
Корректируем периодичности ТО:
LТО-1 = LТО-1н kТО = LТО-1н k1 k3 = 10 000 08 1 = 8000 км.
LТО-2 = LТО-2н kТО = LТО-2н k1 k3 = 20 000 08 1 = 16000км.
Количество воздействий (КР ТО-1 ТО-2 ЕО) на один автомобиль за цикл определяется из выражений:
Так как пробег автомобиля за год отличается от пробега автомобиля за цикл а производственную программу рассчитывают на год то необходимо сделать соответствующий перерасчет полученных значений от цикловой программы к годовой.
Для этого необходимо предварительно определить коэффициент технической готовности автомобиля:
где Дэц – количество дней эксплуатации за цикл;
Дрц – количество дней простоя автомобиля в ремонтах и ТО за цикл.
Количество дней простоя автомобиля в ремонте и ТО за цикл определяется из выражения:
где Дкр – простой автомобилей в капитальном ремонте дни;
ДТОТР – удельный простой автомобилей в ТО и ТР дни1000 км; ДТОТР = 048дн1000 км [4 таблица 2.4];
k4’ – коэффициент корректировки продолжительности простоев в ТО и ТР [1 таблица 2.10]; k4’ = 07.
Дкр=18 [ОргТОиР таблица 1.9]
На основании рассчитанного значения Т определяется годовой пробег автомобиля:
Lг = Дрг lcc Т (2.6)
где Дрг – количество дней работы АТП в году.
Lг = 365 100 091 = 67 033 км.
Зная цикловой Lкр и годовой Lг пробеги автомобилей определяется коэффициент перехода от цикла к году:
Годовая программа воздействий (ТО-1 ТО-2 ЕО) на один автомобиль определяется:
где Ni – количество воздействий данного вида за цикл.
NТО-1г = 65 055 =36;
NТО-2г = 55 055 =42;
NЕОг = 600 055 =335.
Количество воздействий на весь парк автомобилей в год составит:
Niг = Niг Асс. (2.9)
где Асс – списочное количество автомобилей.
NТО-1г = 363100 = 363;
NТО-2г = 42100 =419;
NЕОг = 335100 =33517.
Суточная программа воздействий определяется из выражения:
Nic = Niг Дpгi. (2.10)
где Дргi – число рабочих дней в году подразделения выполняющего тот или иной вид работ.
NТО-1c = 363365 = 099;
NТО-2c = 419365 = 115;
NЕОc = 33517365 =9183.
Число диагностирований на весь парк за год:
NД-1г = 11 N1г +N2г; (2.11)
NД-2г = 12 N2г (2.12)
где NД-1г NД-2г – годовое число воздействий ТО-1 и ТО-2 на весь парк автомобилей соответственно.
NД-1г = 11363 + 419=824;
NД-2г = 12 363 = 4357.
Суточное количество диагностирований:
NД-iс=NД-iгДрг (2.13)
Суточное количество воздействий служит основанием для выбора метода обслуживания. Техническое обслуживание и диагностирование будем проводить на универсальных постах а ежедневное обслуживание – на поточных линиях.
2 Определение годового объема работ
Нормативы трудоемкостей технических воздействий должны быть скорректированы для конкретных условий с помощью коэффициентов корректирования.
Годовой объем работ по каждому виду технического обслуживания равен:
tТО-2н = 102 чел.-ч;
ki – результирующий коэффициент корректирования трудоемкости данного вида ТО.
где k2 k5 – коэффициенты корректировки нормативного пробега до капитального ремонта: k2 = 10 [1 таблица 2.8]; k5 = 115 [1 таблица 2.11];
Подставив значения получаем:
Годовой объем работ по текущему ремонту определяется:
где tТР – удельная трудоемкость ТР чел-ч.1000 км;
kТР – результирующий коэффициент корректирования трудоемкости ТР.
В АТП дважды в год проводится также сезонное обслуживание (СО) (весной и осенью). Трудоемкость работ СО определяется из выражения:
где kсо – коэффициент учитывающий район эксплуатации kсо = 04.
где k2 k5 – коэффициенты корректировки нормативного пробега до капитального ремонта: k2 = 10 [1 таблица 2.8]; k5 = 115 [1 таблица 2.11];
Эти работы выполняются при очередном ТО-2.
Тогда общая годовая трудоемкость работ ТО-2 с учетом трудоемкости СО составит:
Годовой объем трудовых затрат на вспомогательные работы (обслуживание и ремонт оборудования и инструментов; транспортные и погрузочно-разгрузочные работы; перегон автомобиля внутри предприятия; хранение приёмка выдача материалов и запасов; уборка производственных и служебно-бытовых помещений) устанавливается в пределах 20 30% к суммарной трудоемкости ТО и ТР по АТП и определяется из выражения:
где kвсп – коэффициент учитывающий размеры АТП kвсп = 03.
Диагностические работы определяются по формулам:
где a b – соответственно доля диагностических работ в объемах работ ТО-1 и ТО-2; a = 015; b = 012 [4 таблица 2.7];
t1 t2 – скорректированные трудоемкости работ ТО-1 и ТО-2 чел-ч.
Трудоемкость диагностических работ равна:
В зависимости от метода организации диагностирование может выполняться на отдельных постах (линиях) или совмещаться с процессом ТО и ТР.
В нашем случае диагностирование будет проводиться на отдельных постах.
3 Разработка схемы организации производства
В качестве организации производства выбираем метод специализированных бригад. Этот метод представляет собой такую схему организации производства при которой работы каждого вида ТО и ТР выполняются специализированными рабочими. При такой организации работ обеспечивается технологическая однородность каждого участка (зоны) облегчается маневрирование внутри него людей инструмента оборудования упрощаются руководство и учет количества выполненных тех или иных видов технических воздействий. Схема организации производства представлена на рисунке 2.1.
В организационную структуру технической службы входят следующие подразделения: технический отдел отдел главного механика (ОГМ) отдел материально-технического снабжения (ОМТС) отдел технического контроля (ОТК).
Технический отдел разрабатывает планы и мероприятия по научной организации труда внедрению новой техники и технологии производственных процессов организует и контролирует их выполнение разрабатывает и проводит мероприятия по охране труда изучает причины производственного травматизма и принимает меры по их устранению организует изобретательскую и рационализаторскую работу на АТП составляет технические нормативы и инструкции.
Рисунок 2.1 – Структурная схема организации производства
Отдел главного механика обеспечивает содержание в технически исправном состоянии технологического оборудования зданий сооружений энергосилового и санитарно-технического хозяйства осуществляет монтаж обслуживание и ремонт производственного оборудования инструмента и контроль за правильным их использованием а также изготовление нестандартного оборудования.
Отдел материально-технического снабжения обеспечивает бесперебойное материально-техническое снабжение АТП (запасные части агрегаты горюче-смазочные материалы и др.) составляет заявки по материально-техническому снабжению и обеспечивает правильную организацию работы складского хозяйства. Отдел технического контроля осуществляет контроль за качеством работ выполняемых всеми производственными подразделениями контролирует выборочно и периодически техническое состояние подвижного состава в том числе при его приеме и выпуске на линию анализирует причины возникновения неисправностей подвижного состава. Между отделами существуют многосторонние внутренние и внешние связи.
4 Распределение объема ТО и ТР по видам работ
В соответствии с принятой системой организации и управления производством необходимо приступить к распределению годовых трудоемкостей по производственным подразделениям (комплексам зонам участкам). Результаты расчета приведенного в пункте 2.1.2 занесем в таблицу 2.2.
Таблица 2.2 – Распределение объема ТО и ТР по видам работ
Моечные (включая сушку-обтирку)
Контрольно-диагностические
Ремонтные (устранение мелких неисправностей)
Диагностирование общее (Д1)
Крепежные регулировочные смазочные и др.
Диагностирование углубленное (Д2)
Регулировочные и разборочно-сборочные работы
Сварочные работы для грузовых автомобилей с металлическими кузовами
Жестяницкие работы для грузовых автомобилей с металлическими кузовами
2 Участковые работы:
Слесарно-механические работы
Электротехнические работы
Окончание таблицы 2.2
Аккумуляторные работы
Ремонт приборов системы питания
Шиномонтажные работы
Вулканизационные работы(ремонт камер)
Кузнечно-рессорные работы
Вспомогательные работы:
Ремонт и обслуживание технологического оборудования оснастки и инструмента
Ремонт и обслуживание инженерного оборудования сетей и коммуникаций
Прием хранение и выдача материальных ценностей
Перегон подвижного состава
Уборка производственных помещений
Обслуживание компрессорного оборудования
5 Расчет численности работающих на предприятии и их распределение по производственным подразделениям
Технологически необходимое технологическое и штатное число рабочих определяется по следующим формулам:
ФН – годовой фонд времени рабочего места ч. (таблица 2.3 [5 таблица А6]);
ФД – годовой фонд времени штатного рабочего ч. (таблица 2.3 [5 таблица А6]).
Определим необходимое технологическое и штатное число рабочих для зоны ЕО:
По некоторым видам работ расчетное количество рабочих может получиться меньше единицы. В этой ситуации необходимо предусматривать объединение однородных видов работ. При этом необходимо учитывать:
- квалификацию рабочего;
- взаимное расположение соответствующих производственных подразделений (они должны располагаться как можно ближе друг к другу или же в одном помещении если это не противоречит нормативным требованиям по охране труда и противопожарной безопасности);
- режим работы АТП и его производственных подразделений.
Расчет численности рабочих сведем в таблицу 2.4.
Таблица 2.3 – Нормы для расчета годовых фондов времени рабочих
Маляры-пульверизаторщики на работе в камерах.
Аккумуляторщики заливщики баббита газосварщики кузнецы молотобойцы карбюраторщики медники паяльщики электросварщики мотористы-испытатели регулировщики при испытании автомобилей на этилированном бензине.
Вулканизаторщики грунтовщики гальванизаторы мойщики регулировщики электромонтеры термисты калильщики.
Таблица 2.4 – Результаты расчёта численности рабочих и распределение их с учетом объединения родственных работ
Наименование производственного
Элекротехнические работы
Вспомогательные работы
6 Определение количества постов в подразделениях
Количество универсальных постов для проведения ТО и Д определяется из выражения:
где - число рабочих дней в году;
- годовой объём по видам ТО и Д чел-ч.;
- коэффициент резервирования постов для компенсации неравномерной загрузки [4 табл.2.14];
- продолжительность выполнения данного вида работ в течение смены ч.;
- численность рабочих одновременно работающих на одном посту чел. [4 табл.2.15];
- коэффициент использования рабочего времени [4 табл.2.16];
- число смен работы в сутки.
По формуле (2.29) получаем:
Работы по ТО-1 и ТО-2 будем проводить в зоне ТО включающей 2 унифицированных поста (1 пост ТО-2 и 1 пост ТО-1). Работы по Д-1 и Д-2 будем проводить на 1 посту.
Для выполнения работ ЕО будем использовать поточные линии периодического действия. Количество линий обслуживания определяется из уравнения:
где – такт линии ч.;
Rп – ритм производства мин.
Исходной величиной характеризующей поток периодического действия является такт линии – интервал времени между двумя последовательно сходящими с линии автомобилями прошедшими данный вид обслуживания:
где t – трудоемкость работ при выполнении обслуживания на потоке чел-ч;
Р – общее количество технологически необходимых рабочих на линии обслуживания;
tП – время передвижения автомобиля с поста на пост мин.
kM – коэффициент механизации (kM=035)
Время передвижения автомобиля с поста на пост определяется по формуле:
где Lа – габаритная длина автомобиля Lа = 86 м;
а – расстояние между стоящими друг за другом автомобилями а = 15 м;
Vk – скорость передвижения автомобиля конвейером Vk=15 ммин.
Тогда такт линии равен:
Ритм производства определяется по формуле:
где – продолжительность работы зоны в течении суток ч.;
– число обслуживаемых единиц подвижного состава данного вида в сутки ед.
Тогда ритм линии равен:
Тогда количество линий обслуживания равно:
Рабочая длина линии обслуживания определяется из выражения:
где хпл – принятое количество постов на линии равное 3.
Количество постов текущего ремонта определяется по формуле:
– коэффициент учитывающий неравномерность поступления автомобилей на посты ремонта равный 12 15;
kТР – коэффициент равный части объема работ выполняемых на постах ТР в наиболее загруженную смену; kТР = 055;
ДР.Г – число рабочих дней в году зоны ТР; ДР.Г = 253;
Тс – продолжительность рабочей смены ч.; Тс = 8 ч.;
Рп – число рабочих на посту [4 таблица 2.15];
п – коэффициент использования рабочего времени поста [4 табл.2.16];
7 Подбор основного технологического оборудования по подразделениям
Подбор основного технологического оборудования производится в соответствии с технологическим процессом на ремонтируемый объект. Выбор оборудования производим с помощью компьютерных программ «Оборудование» и «Оборудование-2006» разработанных на кафедре «Техническая эксплуатация автомобилей» [9] [10]. С учётом перечня производственных участков и выбранного технологического оборудования заполняется сводная ведомость технологического оборудования. Сводная ведомость по основному технологическому оборудованию представлена в таблице 2.6.
Таблица 2.6 - Перечень основного оборудования
Наименование оборудования
Электротехнический участок
Верстак для электрика
Ванна моечная ОМ-1316А
Роскомсельхозтехника
Станок для проточки коллекторов и фрезерования пазов Р-105
Росавтоспецоборудование
Стенд для проверки аппаратов системы зажигания СПЗ-8М
Контрольно-испытательный стенд
Автоспецоборудование
Тиски самоцентрирующие
Продолжение таблицы 2.6
Станок вертикально- сверлильный одношпиндельный 2А55
Аккумуляторный участок
Ванна для промывки деталей АКБ 2257
Верстак для ремонта АКБ 2297
Ванна для приготовления электролита
Шкаф для зарядки АКБ 2268
Тележка для перевозки АКБ П-225
Электродистиллятор ДЭ-4
Слесарно-механический участок
Станок обдирочно-шлифовальный передвижной 382
Станок токарно-револьверный 1Д340П
Станок точильно-шливовальный для заточки металлорежущих инструментов 7А317
Станок фрезерный широкоуниверсальный 675П
Стеллаж полочный 2242
Станок поперечно-строгальный с механическим приводом
Тележка 1203.30.00.00
Установка для мойки деталей мод. 196М
Верстак слесарный 2281
Стенд для сборки и разборки КПП грузовых автомобилей Р784
Стенд для ремонта передних и задних мостов грузовых автомобилей 2450
Стенд для разборки сборки и регулировки рулевых механизмов
Стенд для сборки и разборки карданных валов
Станок на расточку тормозных барабанов и обточки накладок тормозных колодок ТО-161С
Стенд для разборки и сборки двигателей
Стеллаж секционный 2247
Стенд обкаточно-тормозной для обкатки ДВС КИ-2139
Набор инструментов и приспособлений для ручной правки кузовов автомобилей
Электроножницы 435402
Молот ковочный пневматический МА-4129
Станок настольно-сверлильный ГМ112
Верстак для жестянщика 2280
Трансформатор сварочный СТШ500
Сварочный полуавтомат
Штатив для баллонов с кислородом и ацетиленом
Стол для сварочных работ
Кузнечно – рессорный арматурный и медницко-радиаторный участок
Горн кузнечный на один огонь Р 923
Молот ковочный МА-4132
Станок вертикально-сверлильный 2А53
Плита правочная ОСТ 20149-99
Печь камерная электрическая СНО-6.12410М-1
Ванна для закалки в масле 2256
Ванна для закалки в воде 9062
Стенд для сборки разборки рессор и рихтовки рессорных листов Р278
Росавтоспец-оборудование
Стенд для комплексных работ по ремонту радиаторов Р 209
Установка для промывки и пропарки топливных баков автомобилей М424
Стенд для обивки подушек и спинок сидений автомобилей мод.3018
Польский завод им. Колинина
Машинка швейная класс 23А
Шиномонтажный и вулканизационный участок
Cтенд шиномонтажный для колес грузовых автомобилей G9756
Стеллаж для колёс и покрышек Р-528
Верстак для ремонта 2319
Электровулканизатор для ремонта наружных повреждений покрышек и камер 6140
Ванна для проверки герметичности камер
Клеть для накачки шин Р-970
Станок для балансировки колёс
Краскораспылитель мод. ИФ-06
Машинка шлифовальная ОНП-3
Вискозиметр В3-3 со столом 2245
Установка для нанесения антикоррозионного покрытия 183М
Шкаф для красок 2304
Камера окрасочная для кабин грузовых автомобилей А-110
Камера для сушки грузовых автомобилей 8042
Установка для мойки грузовых автомобилей 631
Колонка маслораздаточная с электроподогревом 3155М
Колонка воздухораздаточная С413
Росавтоспецоборудова-ние
Конвейер для перемещения автомобиля
Станция диагностики для грузовых автомобилей СДЧ-К475
Набор манометров для проверки тормозной системы автомобиля
Стенд для проверки углов установки управляемых колёс автомобилей КИ-8959-ГОСНИТИ
Прибор для определения люфтов в трансмиссии грузовых автомобилей КИ-4832-ГОСНИТИ
Прибор для проверки электрооборудования
Стенд для проверки тяговоэкономических показателей грузовых автомобилей и автобусов
Прибор для регулировки света фар
Стенд для проверки электрооборудования
Гайковёрт для гаек колёс грузовых автомобилей
Рукоятка динамометрическая
Тележка для снятия и установки колёс автомобилей
Стенд для статической балансировки колес грузовых автомобилей К-126
Смазочная установка мод.Ч-40
Установка для сбора отработавшего масла с насосом мод. “Аурас”
Бак для слива отработавшего масла
Комплект инструмента автомеханика И131
Завод механизированного инструмента
Подъемник электрогидравлический четырёхстоечный
Участок по ремонту топливной аппаратуры
Настольно сверлильный станок
Ручной пресс ОКС-318
Стенд для проверки и регулировки топливных насосов высокого давления СДТА-2
Пост для наружной мойки приборов системы питания М408А
Комплект приборов для проверки топливной аппаратуры дизельных двигателей ЯМЗ-236 и ЯМЗ-238
Пост для текущего ремонта топливных насосов высокого давления дизельных двигателей ЯМЗ и КамАЗ Р-611
Пост для текущего ремонта форсунок дизельных двигателей ЯМЗ и КамАЗ Р-610
Станция смазки для насосов ТНВД ДД-3100
Прибор для испытания и регулировки форсунок КИ562
Набор инструментов слесаря-монтажника
Подставка под двигатель
Смазочная установка У-40
Окончание таблицы 2.6
Колонка маслораздаточная с электронагревом мод.3155Н
Стеллаж для колёс 2251
Ящик для инструмента 2242
Гайковёрт для гаек колёс И 318
Тележка для снятия и установки колёс автомобиля П217
Тележка слесаря по ремонту двигателя 1115М
Подвесная кран балка М215
Установка для сбора отработавшего масла с насосом “Аурас”
Набор инструментов слесаря ремонтника
8 Определение площадей производственных помещений
Площади АТП по своему функциональному назначению подразделяются на три основные группы: производственно-складские хранения подвижного состава и вспомогательные.
Площади производственных помещений определяют по удельным площадям на единицу оборудования (автомобиля) или на каждого работающего.
Площадь зон ЕО ТО-1 ТО-2 ТР рассчитывают по формуле:
где fа – площадь занимаемая автомобилем в плане м2 fа = 715 м2;
kу – удельная площадь помещения на 1 м2 площади занимаемой автомобилем в плане зависит от типа автомобиля расположения постов их оборудования и принимается равной 4 7.
По формуле (2.37) получаем:
Площади производственных участков рассчитывают по удельной площади помещений приходящихся на единицу площади занимаемой оборудованием (таблица 2.7).
Таблица 2.7 – Результаты расчёта площадей производственных участков
Наименование производственного участка
Слесарно-механический
Кузнечно – рессорный арматурный и медницкий
Шиномонтажный вулканизационный
9 Определение площадей складских и других помещений
Расчет помещений складов определим по удельной площади на 10 единиц подвижного состава:
где – удельная нормативная площадь склада данного вида на 10 единиц ПС [4 табл.2.23];
КПР КТС КПС КВ КУ.Э. – соответственно коэффициенты корректирования в зависимости от среднесуточного пробега числа единиц ПС типа ПС высоты складирования категории условий эксплуатации [4].
Для удобства определения воспользуемся таблицей 2.8.
Таблица 2.8 – Результаты расчета площадей складов.
Наименование складских помещений сооружений
Запчастей деталей эксплуатационных материалов
Двигателей агрегатов и узлов
Смазочных материалов
Лакокрасочных материалов
Кислорода азота и ацетилена в баллонах
Металла металлолома ценного утиля
Автомобильных шин отремонтированных и подлежащих восстановлению
Подлежащих списанию ам агрегатов (на открытой площадке)
Промежуточного хранения запасных частей и материалов (участок комплектации и подготовки производства)
Площади вспомогательных помещений производственного корпуса можно определить исходя из норм и числа работающих. В этом случае площади гардероба Fг душа Fд туалета FТ и умывальника Fу равны соответственно:
При укрупненных расчетах площадь зоны хранения (стоянки) автомобилей определяется из формулы:
где fа – площадь занимаемая автомобилем в плане м2 fа=215 м2;
Аст – число автомобиле-мест хранения Аст =200;
Кп – коэффициент плотности расстановки автомобиле-мест хранения Кп=3.
15 Требования к производственному корпусу
Основой для разработки планировки зданий АТП является функциональная технологическая схема и график производственного процесса в соответствии с которыми должно обеспечиваться независимое и при необходимости последовательное прохождение автомобилем отдельных этапов ТО и ТР.
Планировочное решение главного производственного корпуса АТП должно соответствовать схеме технологических процессов ТО и ТР автомобилей результатам технологического расчета и общим требованиям унификации строительных конструкций.
При современном индустриальном строительстве здания монтируются из унифицированных главным образом железобетонных конструктивных элементов заводского изготовления (колонны фермы балки) на основе унифицированной сетки колонн. Колоны выбираем размером 400×400 мм. На чертеже ворота обозначенные цифрой 1 имеют ширину 40 м Двери обозначенные цифрой 1 – 071м цифрой 2 – 121 м цифрой 3 – 221 м . Ширина оконных проемов 24; 48; 72; 96 и 192 м. Толщину наружных стен корпуса принимаем 300 мм внутренних перегородок – 150 мм внутренних огнестойких перегородок(брандмауэров) – 300 мм.
Высоту помещений (расстояние от пола до низа конструкций покрытия перекрытия или подвесного оборудования) принимаем исходя из требований технологического процесса размещения подвесного транспортирующего оборудования и унификации строительных конструкций зданий.
Высоту помещений для постов ТО и ТР в зависимости от типа подвижного состава подвесного оборудования и обустройства постов принимают в соответствии с ОНТП-01-91. Так как на предприятии предусмотрены посты ТО ТР и Д на подъёмниках то высоту производственного корпуса принимаем высотой 72 м.
При выборе конструктивной схемы здания учитываем расчетные площади помещений габаритные размеры зон ТО и ТР и участков в которые предусматривается заезд автомобилей. Поэтому с целью определения габаритных размеров эти подразделения прорабатываются укрупнено с учетом стандартной сетки колонн.
Конструктивную схему сетку колонн и габаритные размеры здания выбирают с учетом унификации строительных конструкций габаритных размеров помещений в которые заезжают автомобили и требуемых площадей производственно-складских помещений. При этом ширина производственных помещений принята такая при которой можно разместить оборудование по крайней мере у одной из стен с соблюдением нормируемых расстояний между оборудованием оборудованием и элементами здания а также ширины проходов и проездов. Желательно чтобы отношение длины и ширины зданий имеющих прямоугольную форму в плане находилось в пределах 15 20.
Ширина проездов в зонах ТО и ТР принимается минимальной но достаточной для выполнения всех операций маневрирования. Ширину проездов принимаем равной 40 м.
При определении габаритных размеров производственных подразделений и их обустройстве необходимо учитывать также что посты уборки сушки автомобилей всех категорий должны располагаться в изолированном от других производственных подразделений помещении.
16 Расчет площади и разработка компоновочного решения производственного корпуса
В основу компоновки производственного корпуса положена функциональная схема производственного процесса в АТП представленная на рисунке 2.2
Рисунок 2.2 – Функциональная схема производственного процесса в АТП
Функциональная схема показывает возможные пути прохождения автомобилем различных этапов производственного процесса.
Перечень производственных зон и подразделений и их характеристики приведены в таблице 2.9
Участки объединены с учетом технологической совместимости и количества рабочих находящихся на участках.
Площадь производственных помещений 167104 м2.
Таблица 2.9 – Перечень производственных зон и подразделений
Наименование зоны отделения
Категория пожаробезопасности
Окончание таблицы 2.9
Краскоприготовительная
Участок слесарно-механический
Участок электротехнический
Участок аккумуляторный
Участок шиномонтажный и вулканизационный
Участок кузнечно-рессорный арматурный и медницкий
Склад лакокрасочных материалов
Склад смазочных материалов (с насосной)
Склад автомобильных шин
Склад пиломатериалов
Склад зч деталей эксплуатационных материалов
Склад двигателей агрегатов и узлов
Площадь производственных помещений увеличиваем на 15% чтобы учесть площадь межцеховых проездов.
Fпр = 177854·115 =204532 м2.
Производственный корпус разрабатываем прямоугольной формы. С учётом строительных требований принимаем сетку колонн 12×30 габаритами 36×60 и площадью 2160 м2. Производственный корпус выполнен одноэтажным с высотой помещения 72 м.
Участок слес.-мех._13_1.cdw

Станок вертикально-сверлильный
широкоуниверсальный 675П
Станок токарно-револьверный
Станок круглошлифивальный
Станок для расточки тормозных
Устновка для мойки деталей
Склад запасных частей
МГЭПТК 2-37 01 06.II-85.XXXX13 ДП - ПО
Корпус производственный
слесарно-механический
Условные обозначения
Потребитель электроэнергии
Подвод холодной воды с отводом в канализацию
Перечень технологического оборудования
Участок слес.-мех..cdw

Станок вертикально-сверлильный
широкоуниверсальный 675П
Станок токарно-револьверный
Станок круглошлифивальный
Станок для расточки тормозных
Устновка для мойки деталей
Склад запасных частей
МГЭПТК 2-37 01 06.II-85.XXXX13 ДП - ПО
Корпус производственный
слесарно-механический
Условные обозначения
Потребитель электроэнергии
Подвод холодной воды с отводом в канализацию
Перечень технологического оборудования
Рекомендуемые чертежи
- 25.01.2023
- 07.03.2016
- 25.01.2023
- 25.01.2023
Свободное скачивание на сегодня
Обновление через: 2 часа 10 минут