Привод лебедки



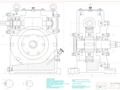
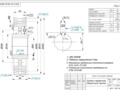
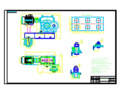
- Добавлен: 24.01.2023
- Размер: 2 MB
- Закачек: 0
Описание
Состав проекта
![]() |
![]() |
![]() ![]() ![]() |
![]() ![]() ![]() ![]() |
![]() ![]() ![]() |
![]() ![]() ![]() ![]() |
![]() ![]() ![]() |
![]() ![]() ![]() |
![]() ![]() ![]() ![]() |
![]() ![]() ![]() |
![]() ![]() ![]() |
![]() ![]() ![]() |
Дополнительная информация
Содержание.DOC
Расчет передач редуктора8
1 Выбор материала термообработки и определение допускаемых
2 Проектный расчет передач редуктора 8
3 Проверочный расчет тихоходной ступени редуктора10
4 Тепловой расчет редуктора
5 Расчет открытой цилиндрической передачи
Расчет валов привода
1 Проектный расчет валов привода
2 Проверочный расчет тихоходного вала
Подбор подшипников для валов привода
Расчет шпоночных соединений
Смазка редуктора и узлов привода
Техника безопасности
Список использованной литературы
Приложение А Расчет червячной передачи на ЭВМ
Приложение Б Спецификация к сборочному чертежу редуктора
Общий вид.dwg

Угол накл. лин. зуб.
Сталь 40Х ГОСТ4543-71
Нормальный исходный контур
Коэффициент смещения
Сталь 45 ГОСТ1050-88
Редуктор обкатать по 10-15 мин на всех режимах нагрузки
Редуктор цилиндрический двухступенчатый
ПЛ-5.25-26.03.00.00ВО
Осевое смещение валов электродвигателя и редуктора до 1 мм
Радиальное смещение валов электродвигателя и редуктора до 0
Угол перекоса валов до 30'
Технические требования
Скорость вращения барабана V =0
Общее передаточное число u =60
Окружное усилие каната Ft =5
Техническая характеристика
* Размеры для справок
Частота враения электродвигателя n=2910 обмин
Мощность электродвигателя Р=5
Приводной вал крепить к раме лебедки
Привод лебедки Чертёж общего вида
Титульник1.DOC
Министерство образования и науки Российской Федерации
Государственное учреждение высшего профессионального образования
БЕЛОРУССКО-РОССИЙСКИЙ УНИВЕРСИТЕТ
Кафедра: ”Основы проектирования машин и механизмов”
Курсовой проект по дисциплине “Детали машин”
Пояснительная записка
ПЛК-525-26.00.00.00ПЗ
Колесо.dwg

Радиусы закруглений 4 мм.
6 болтов M10х22 затянуть до упора
спилить и раскернить
Остальные технические требования по
Межосевое расстояние
Число витков сопр. червяка
Коэффициент смещения
Направление линии зуба
Колесо червячное Сборочный чертеж
Записка.doc
Основная цель курсового проекта по деталям машин – приобретение студентом навыков проектирования. Работая над проектом студент выполняет расчёты учится рациональному выбору материалов и форм деталей стремится обеспечить их высокую экономичность надёжность и долговечность. Приобретённый студентом опыт является основой для выполнения им курсовых проектов по специальным дисциплинам и для дипломного проектирования а так же всей дальнейшей конструкторской работы.
Энерго-кинематический расчет проекта
Мощность на выходном валу привода
Pp=Ft×V=525×055=289 кВт
где Ft – тяговое усилие на барабане кН;
V – окружная скорость мс.
Мощность потребляемая электродвигателем
Pэд=Ррh=289068=425 кВт
где h – общий К.П.Д. привода.
h=h3пп× hму×hчп×hцп =0993×098×078×092=068
где hпп hму hчп hцп – КПД соответственно подшипников муфты предохранительной червячной передачи и цилиндрической пары.
Определяем частоту вращения рабочего органа
nр=60000×V(p×D)=60000×055(314×220)=4775 мин-1
где D – диаметр приводного барабана мм.
Определяем оптимальную частоту вращения электродвигателя
nэд=nр×U0=4775×55=2626 мин-1
где U0 – общее ориентировочное передаточное число привода.
U0=Uред×U цп =22×25=55
где Uред – ориентировочное передаточное число редуктора.
U цп – передаточное число цилиндрической пары.
Исходя из вычисленных значений Рэд и nэд выбираем электродвигатель 4А100L2У3 с синхронной частотой вращения nд=2910 мин-1 и мощностью Рэд=55 кВт.
Определяем асинхронную частоту вращения электродвигателя
Определяем передаточное число привода
Определяем частоты вращения валов
n3=n2Uред=286524=11938 мин-1
n4=n3Uцп =1193825=4775 мин-1
Определяем мощности передаваемые валами
Р2=Р1×hпп×hму=425×099×098=412 кВт
Р3=Р2×hпп×hчп=412×099×078=318 кВт
Р4=Р3×hпп×hцп=318×099×092=29 кВт.
Определяем угловые скорости валов привода
w1=p×nд30=314×286530=300 рад-1
w3=w2Uред=30024=125 рад-1
w4=w3Uцп=12525=5 рад-1.
Определяем крутящие моменты на валах привода :
Т1=Р1w1=4250300=142 Н×м
Т2=Р2w2=4120300=137 Н×м
Т3=Р3w3=3180125=2544 Н×м
Т4=Р4w4=29005=580 Н×м
Таблица 1 – Результаты расчётов валов
Расчет передач редуктора
1 Выбор материала термообработки и определение допускаемых
Определяем скорость скольжения [2 стр. 211]:
Назначаем материал колеса БРОФ10-1 [2 табл. 9.4] при sт = 120 МПа; sв = 200 МПа; червяк – сталь 40Х закалка до 54 HRC витки шлифовать и полировать.
Определяем допускаемое контактное напряжение:
Определяем допускаемое напряжение изгиба:
2 Проектный расчет передач редуктора
По рекомендации [2 стр.201] принимаем число заходов червяка . Ориентировочно принимаем [2 стр.205].
Определяем число зубьев колеса:
Условие неподрезания зубьев выполняется.
По рекомендации [2 стр.201] учитывая стандартные значения коэффициента диаметра червяка q предварительно назначим . При этом в рекомендуемых пределах.
Находим приведенный модуль упругости по формуле [2 стр.208]
где Е1 и Е2 – модули упругости материалов червяка и колеса:
По формуле [2 стр.208] определим межосевое расстояние:
Принимаем m = 63 из стандартного ряда [2 стр.201].
Необходимый коэффициент смещения:
x = aw m – 05(q + z2) = 18863 – 05(125 +48) = -04
По условию неподрезания и незаострения зубьев значение x на практике допускают от -07 до +07.
Определяем делительные диаметры:
Определяем диаметры вершин зубьев:
Определяем диаметры впадин зубьев:
Определяем наружный диаметр колеса:
Определяем длину нарезанной части червяка:
По рекомендациям [2 табл. 9.1] принимаем мм
Определяем ширину венца колеса:
Определяем угол подъема винтовой линии:
Определяем окружную скорость червяка:
Проверяем выбранное значение vs:
Ранее было принято мс – материал БРОФ10-1 сохраняем.
3 Проверочный расчет тихоходной ступени редуктора
Определяем торцовый коэффициент перекрытия в средней плоскости червячного колеса:
Проверяем прочность по контактным напряжениям :
где - коэффициент учитывающий уменьшение длины контактной линии;
КН – расчетная нагрузка для червячных передач;
По рекомендации [2 стр.202] .
Расчетная нагрузка для червячных передач:
где коэффициент динамической нагрузки 1[2 стр.210];
коэффициент концентрации нагрузки [2 стр.210].
Прочность по контактным напряжениям соблюдается.
Определяем недогрузку.
Определяем силы в зацеплении
Окружная сила на колесе равная осевой силе на червяке:
Окружная сила на червяке равная осевой силе на колесе:
Проверяем прочность по напряжениям изгиба.
Определяем осевой модуль:
Эквивалентное число зубьев колеса:
Определяем напряжение изгиба:
где YF –коэффициент учитывающий форму зуба YF =145 [2 стр.209].
Прочность по напряжению изгиба соблюдается.
где угол трения [2 табл. 9.3].
4 Тепловой расчет редуктора.
Червячный редуктор в связи с невысоким КПД и большим выделением теплоты проверяют на нагрев.
Мощность на червяке:
Температура нагрева масла (корпуса) при установившемся тепловом режиме без искусственного охлаждения:
где =03 – коэффициент учитывающий отвод теплоты от корпуса редуктора в металлическую раму;
- максимальная допустимая температура нагрева масла;
– поверхность охлаждения корпуса
KT – коэффициент теплоотдачи для чугунных корпусов и естественного охлаждения KT=15
Естественного охлаждения достаточно нет необходимости применения искусственного охлаждения.
Расчет передачи на ЭВМ см. приложение А.
5 Расчет модуля и выбор основных параметров открытой цилиндрической передачи.
Расчетный модуль зацепления:
коэффициент учитывающий форму зуба[3 табл. 4.2.3];
- коэффициент ширины шестерни относительно ее
диаметра[3 табл. 4.2.6];
коэффициент учитывающий неравномерность распределения нагрузки по ширине венца[3 рис. 4.2.2вг];
коэффициент внешней динамической нагрузки[3 табл. 4.2.9];
Принимаем m=5 [3 табл.4.2.1]
Определяем делительные диаметры зубчатых колес:
Межосевое расстояние:
Принимаем межосевое расстояние aw = 160 мм [3 табл.4.2.2].
Определяем ширину зубчатого колеса:
b2 = ×aw = 05×160 = 80 мм
Ширина венца шестерни:
Расчет валов привода
1 Проектный расчет валов привода
Проектный расчет валов.
Материал вала – сталь 45 улучшенная; В=750МПа; Т=450МПа. Срок службы длительный нагрузка близка к постоянной допускается двукратная кратковременная перегрузка [2 табл.16.2.1]. Материал червяка Сталь 40Х.
Быстроходный вал – червяк:
Диаметр посадки полумуфты определяем по формуле из [5 стр. 15]:
Согласовав полученное значение с величиной диаметра вала электродвигателя принимаем d=18мм.
Диаметр для установки подшипников определяем по формуле из [5 стр. 15]:
Диаметр буртика для упора подшипников по формуле из [5 стр. 15]:
Средний диаметр вала при по формуле [2 стр.296]
Принимаем диаметр вала в месте посадки колеса .
Диаметр участка для постановки подшипника:
Диаметр буртика для упора колеса:
2 Проверочный расчёт тихоходного вала редуктора
Рисунок 1 – Схема нагружения тихоходного вала
;; ; ширина колеса – 60 мм; диаметр колеса (z=48;m=63); на выходном конце вала установлена шестерня; материал вала – сталь 45; улучшенная ; l=140мм а=70мм в=70мм с=115мм (Рисунок 1).
Определяем силу действующую со стороны шестерни:
Определяем реакции в опорах в вертикальной плоскости.
Строим эпюру изгибающих моментов в вертикальной плоскости.
Определяем реакции в опорах в горизонтальной плоскости.
Строим эпюру изгибающих моментов в горизонтальной плоскости.
Строим эпюру суммарных изгибающих моментов (рисунок 2).
Строим эпюру крутящих моментов (рисунок 2).
Просчитываем два предполагаемых опасных сечения I-I под колесом ослабленное шпоночным пазом и сечение II-II рядом с подшипником ослабленное галтелью.
Для второго сечения изгибающий момент Больше нагружено 2-ое сечение.
Напряжение изгиба определяется по формуле [2 стр.301]
Напряжение кручения определяется по формуле [2 стр.301]
Проверим статическую прочность вала в этом сечении по формуле [2 с.302].
Условие прочности выполняется.
Определяем запас сопротивления усталости по изгибу по формуле [2 с.299]:
где - амплитуда переменной составляющей цикла напряжений;
- постоянная составляющая;
- коэффициент корректирующий влияние постоянной составляющей цикла напряжений на сопротивление усталости;
- предел выносливости;
- масштабный фактор и фактор шероховатости поверхности;
- эффективный коэффициент концентрации напряжений при изгибе;
Определяем по формуле [2 с.300]:
Определяем предел выносливости по формуле [2 с. 300]:
Определяем запас сопротивления усталости по кручению по формуле [2 с.299]:
- эффективный коэффициент концентрации напряжений при кручении;
Определяем амплитуду переменной составляющей цикла напряжений по формуле [2 с.300]:
Определяем предел выносливости по формуле [2 с.300]:
Определяем запас сопротивления усталости по формуле [2 с.299]:
Проверяем жёсткость вала.
По условиям работы зубчатого зацепления опасным является прогиб вала под подшипником. Полярный момент инерции сечения вала:
Прогиб в вертикальной плоскости от силы Fr и Fш [2 табл. 15.2]:
Прогиб в горизонтальной плоскости от силы Ft [2 табл. 15.2]:
Т.о. условие прочности и жёсткости выполняется.
Рисунок 2 – Эпюры нагружения тихоходного вала
Подбор подшипников для валов привода
Диаметр в месте посадки подшипника d=45мм n=11938 мин-1 ресурс Ln=21000 ч. режим нагрузки II [2 рис 8.42 и табл. 16.4] допускаются двукратные кратковременные перегрузки температура подшипника t1000с .
Реакции опор по формуле [2 стр. 340]:
Предварительно назначаем роликовые конические однорядные подшипники средней узкой серии условное обозначение 7309 для которых по каталогу C=83000 Н С0=60000 Н е=034 Y=18 .
Выполняем проверочный расчёт подшипника.
Суммарная осевая составляющая по формуле [2 стр. 339]:
где е – параметр осевой нагрузки.
Принимаем [2 стр. 339].
Находим следующую осевую силу по формуле [2 стр. 339]:
Условия ; выполняются следовательно силы найдены правильно.
Определяем эквивалентную нагрузку по формуле [2 стр. 335]:
где Х – коэффициент радиальной нагрузки [2 табл. 16.5];
Y – коэффициент осевой нагрузки [2 табл. 16.5];
V – коэффициент вращения зависящий от того какое кольцо подшипника вращаетсяV=1 [2 стр. 335];
K – коэффициент безопасности учитывающий характер нагрузки K =15 [2 стр. 335];
КТ – температурный коэффициент КТ =1 [1 стр. 335].
Т.к. рассчитываем только второй подшипник.
Т.к. рассчитываем только первый подшипник.
Эквивалентная долговечность по формуле [2 стр. 336]:
где КHE – коэффициент режима нагрузки [2 табл. 8.10].
Количество оборотов по формуле [2 стр. 336]:
Динамическая грузоподъёмность по формуле [2 стр. 332]:
где а1 – коэффициент надёжности [2 стр. 333];
а2 – обобщённый коэффициент совместного влияния качества металла условий эксплуатации [2 табл. 16.3].
Рассчитанная динамическая грузоподъёмность меньше паспортного значения С. Условие по динамической грузоподъёмности выполняется.
Проверяем подшипник по статической грузоподъёмности.
Условие проверки и подбора:
При [2 стр. 337] эквивалентная статическая нагрузка с учётом двукратной перегрузки определяется по формуле [2 стр. 337]:
где Х0 Y0 – коэффициенты радиальной и осевой статических нагрузок.
Условие соблюдается.
Выбранные подшипники и их основные параметры заносим в таблицу 1.
Обозначение подшипников
Расчет шпоночных соединений
Для закрепления деталей на валах редуктора используем призматические шпонки. Размеры поперечного сечения шпонок выбираем по ГОСТ 23360-78 в соответствии с диаметром вала в месте установки шпонок. Расчётную длину округляем до стандартного значения согласуя с размером ступицы.
Выбранные шпонки проверяем на смятие по формуле [ 2с.88]:
где Т – передаваемый момент Н×м;
d – диаметр вала мм;
h – высота шпонки мм;
[sсм] – допускаемое напряжение смятия МПа;
Проверяем шпонку установленную на тихоходном валу под червячным колесом. Определяем необходимую рабочую длину шпонки:
Определяем необходимую длину шпонки
где b – ширина шпонки мм;
Остальные шпонки рассчитываем аналогичным способом.
По результатам подсчётов составляем таблицу.
Таблица 2 – Шпонки призматические ГОСТ 23360-78
Для соединения вала редуктора и вала электродвигателя применяем упругую втулочно-пальцевую муфту по ГОСТ21424-93.
Определяем расчётный момент [4с. 189]:
где =2 - коэффициент режима работы [4 с.181]
Момент передаваемый муфтой 250 Н.м
Проверим муфту по напряжениям смятия резиновых втулок [4с.189]:
где мм – диаметр окружности на которой расположены пальцы
z = 3 – число пальцев
- длина резиновой втулки
Проверка муфты по напряжению изгиба пальцев[4c.189]:
Смазка редуктора и узлов привода
Смазка осуществляется окунанием зубьев червячного колеса в масленую ванну. При верхнем расположении червяка глубина погружения колеса в масло не должна превышать высоты зуба. Следовательно величина погружения колеса в масло составляет не более 8 мм.
Для смазки червячной передачи принимается масло повышенной вязкости. Вязкость масла рекомендуется выбирать в зависимости от скорости скольжения. Принимаем для смазки редуктора масло трансмиссионное ТМ-3-9 ГОСТ 17472-85 имеющее кинетическую вязкость . В подшипники качения закладывается солидол жировой ГОСТ 1033-79.
Объём заливаемого масла определяем по формуле:
где - внутренняя длина редуктора
- внутренняя ширина редуктора
- высота масла в редукторе
Техника безопасности
При разработке редуктора учитывались требования безопасности и экологичности его работы.
На валах в крышках подшипниковых узлов предусмотрена установка уплотнений для защиты редуктора от попадания в него пыли и грязи а также для предотвращения вытекания масла из корпуса редуктора.
При выполнении курсового проекта по “Деталям машин” были закреплены знания полученные за прошедший период обучения в таких дисциплинах как: теоретическая механика сопротивление материалов материаловеденье.
В ходе решения поставленных задач была усвоена методика выбора элементов привода получены навыки проектирования позволяющие обеспечить необходимый технический уровень надёжность и долгий срок службы механизма.
Опыт и навыки полученные в ходе выполнения курсового проекта будут востребованы при выполнении как курсовых проектов по специальным дисциплинам так и при выполнении дипломного проекта.
Дунаев П.Ф.Лёликов О.П. Конструирование узлов и деталей машин.-М.: Высшая школа 1998. – 447 с.
Иванов М. Н. Детали машин. Учебник для студентов высш. техн. учеб. заведений. – 5-е изд. перераб. – М.: Высш. шк. 1991. – 383 с.: ил.
Курмаз Л. В. Проектирование. Учеб. пособие. Л. В. Курмаз А. Т. Скойбеда. – Мн.: Технопринт 2001. – 290 с.
Кузьмин А.В. Чернин И.М. Козинцев Б.С. Расчёты деталей машин. – Мн.: Выш. шк. 1986. – 400 с.
Рогачевский Н. И. Проектирование узлов и деталей машин. Техническое предложение и эскизный проект. Методические указания. – Часть 1 – Могилёв.: ММИ 1997. – 24 с.
Рогачевский Н. И. Проектирование узлов и деталей машин. Технический и рабочие проекты. Методические указания. – Часть 2 – Могилёв.: ММИ 1998. – 55 с.
Рогачевский Н. И. Проектирование узлов и деталей машин. Рабочие чертежи деталей пояснительная записка. Методические указания. – Часть 3 – Могилёв.: ММИ 1999. – 48 с.
Редуктор.dwg

Технические требования 1 *Размеры для справок 2 Поверхности соединения "корпус-крышка" перед сборкой покрыть слоем ЦИАТИМа-221 ГОСТ 9433-80 3 Покрытие наружних поверхностей: грунтовка ГФ-0119 ГОСТ 23343-78
эмаль ПФ-115 ГОСТ 6465-76
темно-серая 4 В редуктор залить масло МРТУ 38-1-185-65
в количестве 2.7 л 5 После сборки валы редуктора должны проворачи- ваться свободно без стуков и заедания
Редуктор обкатать по 15 минут на всех режимах нагрузки 7 Остальные технические требования по СТБ 1022-96
Техническая характеристика 1 Момент на тихоходном валу 254.4 Нм 2 Частота вращения быстроходного вала 2865 обмин 3 Передаточное число редуктора 24
ПЛ-5.25-26.02.00.00СБ
Моя спец.- Привод.doc
Кольцо стопорное В70
Манжета 1.1-80х105-1
Шайба концевая7019-6040
Моя спец.- Рама.doc
ПЛ-525-26.00.00.00ПЗ
Пояснительная записка
А100L2У3 ГОСТ28330-89
-4000-65-1 ГОСТ 5006-94
ПЛ-525-26.01.00.00СБ
ПЛ-525-26.02.00.00СБ
Моя спец.- Сборочн..doc
ПЛ-525-26.05.01.00СБ
ПЛ-525-26.01.02.00СБ
ПЛ-525-26.01.03.00СБ
Пробка сливного отв.
ПЛ-525-26.01.00.00СП
Подшипники ГОСТ27365-87
Шайба стопорная 52.01
Рекомендуемые чертежи
Свободное скачивание на сегодня
- 29.08.2014
- 25.01.2023