Исследование и разработка технологии смазки пар трения тяжело нагруженных металлургических машин маслами с использованием




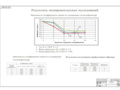
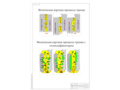
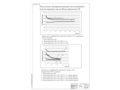
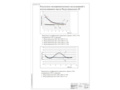
- Добавлен: 24.01.2023
- Размер: 19 MB
- Закачек: 0
Описание
Состав проекта
![]() |
![]() |
![]() ![]() ![]() ![]() |
![]() ![]() ![]() ![]() |
![]() ![]() ![]() ![]() |
![]() ![]() ![]() |
![]() ![]() ![]() ![]() |
![]() ![]() ![]() ![]() |
![]() ![]() ![]() ![]() |
![]() ![]() ![]() ![]() |
![]() ![]() ![]() ![]() |
![]() ![]() ![]() ![]() |
![]() ![]() ![]() |
![]() ![]() ![]() |
![]() ![]() ![]() |
Дополнительная информация
6И-20.dwg

2лабораторная установка.dwg

10Профилограф-профилометр 201.dwg

3образцы.dwg

5тарировка.dwg

9результаты.dwg

7И-20.dwg

1трение.dwg

8Тп-22.dwg

4схема сил.dwg

Рекомендуемые чертежи
- 24.01.2023
- 24.01.2023
- 04.11.2022
- 25.01.2023
Свободное скачивание на сегодня
Другие проекты
- 24.10.2015