Дипломный проект по Машинам непрерывного транспорта



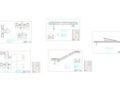
- Добавлен: 25.01.2023
- Размер: 2 MB
- Закачек: 0
Описание
Состав проекта
![]() |
![]() ![]() ![]() |
![]() ![]() ![]() |
![]() |
![]() ![]() ![]() ![]() |
![]() ![]() ![]() |
![]() ![]() ![]() |
![]() ![]() ![]() |
![]() ![]() ![]() |
![]() ![]() ![]() |
![]() ![]() ![]() ![]() |
![]() ![]() ![]() |
![]() ![]() ![]() |
![]() |
![]() ![]() ![]() |
![]() ![]() ![]() |
Дополнительная информация
ДИПЛОМ Технология теория.doc
Технологический комплекс перегрузки минеральных удобрений на территории Восточного района Новороссийского морского порта предназначен для выгрузки минеральных удобрений из железнодорожных вагонов и погрузки их в морские суда.
Грузооборот технологического комплекса - 2 млн. тгод.
Режим работы технологического комплекса круглогодичный трехсменный продолжительность смены - 7 часов 30 минут.
Погрузка минеральных удобрений на технологическом комплексе осуществляется в морские суда дедвейтом до 50 тыс. т.
Основные характеристики максимального расчетного типа судна и размеры приведены в таблице 1.1.
Наименование показателей
Основные размерения:
Технологический комплекс предназначен для перегрузки сыпучих гранулированных минеральных удобрений в том числе: карбамида (50-60%) аммиачной селитры (30-35%) и сложных азотно-фосфорных и азотно-фосфорно-калийных удобрений (15-25%).
Минеральные удобрения транспортируются и перегружаются навалом. Физико-химические свойства удобрений приведены в таблице 1.2.
Массовая плотность гсм3
Объемная плотность гсм3
Класс опасности по ГОСТ 19433-88
Класс 9 подкласс 9.1 категория 9.14 группа 91.43
Доставка минеральных удобрений в порт осуществляется по железной дороге в вагонах-минераловозах. Минераловозы представляют собой саморазгружающиеся вагоны с нижней разгрузкой через люки щелевого типа.
Вагон-хоппер для перевозки минеральных удобрений имеет грузоподъемность 70 т и предназначен для бестарной перевозки гранулированных крупнозернистых кристаллических минеральных удобрений.
Конструкция четырех разгрузочных люков хоппера в виде наклонных днищ обеспечивает полную разгрузку удобрения в сторону от пути. Люки могут открываться пневмоприводом одновременно все или попарно. Предусмотрена возможность ручного открывания. Блокирующие устройства предотвращают самопроизвольное открывание люков в пути и на стоянке.
Характеристика вагона-минераловоза и его основные размеры приведены в таблице 1.3.
Характеристика железнодорожного вагона
Ширина максимальная мм
Высота от уровня головки рельса мм
Размер разгрузочного люка в свету мм
Количество разгрузочных люков
По конструктивным характеристикам кузов хоппера является недостаточно герметичным; имеется практическая возможность выхода газов при возможности начала разложения селитры.
Перед погрузкой минеральных удобрений на заводах-изготовителях вагоны-хопперы освобождаются от предыдущих остатков удобрения и проверяются на отсутствие посторонних предметов в том числе и металлических промасленной ветоши бумаги. Этому уделяется особое внимание перед погрузкой аммиачной селитры. Сырые погрузочные места осушаются горячим воздухом. Таким образом создаются условия исключающие возможность термического разложения продукта при погрузо-разгрузочных операциях и транспортировке вагонов.
2. Механизация и технология перегрузочных работ.
Технологический комплекс состоит из следующих основных узлов:
- станции разгрузки вагонов;
- береговой механизации для погрузки судов;
- транспортной системы в составе конвейерных галерей перегрузочных и приводной станций.
В состав технологического комплекса входит следующее основное технологическое оборудование:
- судопогрузочная машина оборудованная пылеподавляющей насадкой;
- система ленточных конвейеров и пересыпных устройств обеспечивающих транспортировку минеральных удобрений;
- оборудование центрального пульта управления технологическим комплексом;
- оборудование для уборки пыли и просыпей;
- оборудование для измерения и регистрации в автоматическом режиме массы груза проходящего по технологическому варианту работы;
- оборудование для улавливания металлических и неметаллических посторонних предметов;
- маневровый локомотив.
В состав комплекса входят также оборудование и системы обеспечивающие надежную экологически чистую и безопасную эксплуатацию:
вентиляционное оборудование; системы аспирации и пылеулавливания;
системы пожаротушения связи и сигнализации в том числе пожарной сигнализации;
система автоматизированного управления технологическим процессом и др.
При проектировании технологического комплекса принято электрооборудование во взрывозащищенном исполнении с целью обеспечения его наибольшей степени защиты от пыли.
На технологическом комплексе предусмотрена работа по прямому варианту вагон-судно вагон – склад склад – судно и их совмещение.
По технологической линии включающей в себя питатели ленточные ПЛ(1-6) и конвейеры ленточные КЛ1 КЛ2 и КЛЗ осуществляется подача груза от станции разгрузки вагонов на судно.
На чертежах приняты условные обозначения:
- ПЛ - питатель ленточный;
- КЛ - конвейер ленточный;
- СпМ - судопогрузочная машина;
- ПС - пересыпная станция;
ПрС - приводная станция;
- СРВ - станция разгрузки вагонов;
- БПГ - береговая погрузочная галерея.
3. Станция разгрузки вагонов.
Разгрузка вагонов осуществляется на станции разгрузки вагонов (СРВ) располагаемой на двух железнодорожных тупиковых путях при этом разгрузка осуществляется последовательно по 3 вагона на одном пути.
Подача вагонов от железнодорожного парка "Восточный" на разгрузочные железнодорожные пути СРВ и вывод порожних вагонов на выставочные железнодорожные пути производится маневровым локомотивом порта.
На каждый железнодорожный путь СРВ осуществляется подача груженых 27-ми вагонов-минераловозов. В СРВ осуществляется последовательная разгрузка по 3 вагона. По окончании разгрузки 3-его вагона тягачем осуществляется протягивание под разгрузку следующих 3-х вагонов и отвод 3-х порожних вагонов на свободный железнодорожный путь. По окончании разгрузки подачи из 27 вагонов маневровым локомотивом подается следующая подача из 27 груженых вагонов а порожние вагоны отводятся на резервный путь Восточного парка.
Время разгрузки одного вагона с учетом времени на открытие и закрытие разгрузочных люков подтвержденное практическим хронометражем на действующих терминалах составляет в среднем 3-4 минуты соответственно время разгрузки одной группы из трех вагонов от 10-12 до 15 минут.
При ограниченности времени выгрузки минеральных удобрений исключаются условия для уплотнения значительных масс удобрений и самоускоряющихся процессов их теплового разложения. Соответственно в мировой практике подобные явления не зарегистрированы они не отмечены и при транспортировке этих продуктов железнодорожным транспортом.
Станция разгрузки вагонов располагается на двух железнодорожных путях под которыми находятся шесть металлических бункеров по 65 м3 каждый. Бункеры закрыты сверху решеткой с ячейкой размерами 200х200 мм.
В заглубленной части СРВ под приемными бункерами установлены 6 ленточных питателей для равномерной перегрузки удобрений из бункеров на магистральный конвейер КЛ1.
Питатели работают только попарно (ПЛ12; ПЛЗ4; ПЛ56)с производительностью каждого 300 тчас. Скорость движения ленты на питателях переменная что позволяет иметь производительность на магистральном конвейере КЛ1 - 600 тчас независимо от вида перегружаемого минерального удобрения.
Станция разгрузки вагонов и пересыпные рукава с питателей на магистральный конвейер КЛ 1 оборудованы аспирационными установками.
Категория помещений станции разгрузки вагонов по степени взрывопожарной опасности - В2.
4. Береговая механизация для погрузки судов.
Береговая механизация включает в себя судопогрузочную машину и береговую погрузочную галерею в которой расположен конвейер ленточный КЛЗ подающий груз на машину для загрузки судна.
Категория помещений береговой погрузочной галереи по степени взрыво-пожарной опасности - ВЗ.
Техническая производительность судопогрузочной машины 1200 тчас.
Судопогрузочная машина представляет собой металлоконструкцию портального типа передвигающуюся по рельсам вдоль причала.
Колея причала 105 м.
В береговой погрузочной галерее минеральные удобрения с ленточного конвейера КЛ 3 при помощи сбрасывающей тележки двигающейся по специальным рельсовым путям передается на судопогрузочную машину. Хвостовая часть судопогрузочной машины механически соединена со сбрасывающей тележкой ленточного конвейера. Подобная конструкция предотвращает просыпи на причале уменьшает пыление в узле передачи груза с берегового ленточного конвейера на ленточный конвейер расположенный на судопогрузочной машине. Подъемная стрела судопогрузочной машины шарнирно прикреплена к порталу машины и оборудована специальной телескопической трубой через которую происходит сброс груза в трюм судна.
Пересыпной рукав с конвейера КЛЗ расположенного в береговой погрузочной галерее на конвейер принадлежащий судопогрузочной машине оборудован аспирационным устройством. Это аспирационное устройство является составной частью судопогрузочной машины. Также аспирационным устройством оснащен пересыпной рукав с конвейера на конвейер судопогрузочной машины.
С целью уменьшения пыления при погрузке судна судопогрузочная машина оборудована пылеподавляющей насадкой.
Передача минеральных удобрений с ленточного конвейера расположенного в береговой погрузочной галерее на судопогрузочную машину осуществляется через продольную непрерывную щель предусмотренную конструкцией береговой погрузочной галереи и имеющую по всей длине укрытие из резиновой ткани.
Управление судопогрузочной машиной предусмотрено из кабины оператора или с переносного пульта в режиме ручного управления.
Механизм передвижения снабжен противоугонными рельсовыми захватами с приводом управляемым из кабины оператора и ручным приводом на каждом захвате. Для предотвращения движения судопогрузочной машины под действием ураганного ветра дополнительно предусмотрены стопорные устройства.
Интенсивность обработки судна с учетом производственных стоянок -9100 тсут.
Расчетное время погрузки судовой партии 50 тыс. т с учетом времени на швартовкуотшвартовку оформления грузовых таможенных и пограничных документов составляет 5.5 суток.
5. Конвейерная система.
Конвейерная система осуществляет транспортировку минеральных удобрений между станцией разгрузки вагонов и береговой погрузочной галереей обеспечивая перегрузку груза по технологическому варианту вагон-судно.
Ширина ленты В= 1400мм.
Для предотвращения просыпа удобрений с конвейерных лент установлены верхние трехроликовые опоры с желобчатостью 30°.
Угол наклона конвейеров не превышает 15°. В наклонных конвейерах установлены устройства предотвращающие обратное движение ленты.
Техническая производительность конвейеров КЛ 1 2 - 600 тчас конвейера КЛЗ - 1200 тчас (в связи с возможностью приема минеральных удобрений со склада).
Конвейер ленточный КЛ 1 перемещает груз от станции разгрузки вагонов в пересыпную станцию ПС 1 в которой осуществляется передача груза с КЛ 1 на КЛ 2. Через пересыпную станцию ПС 2 конвейером КЛ 2 происходит доставка минеральных удобрений к береговой погрузочной галерее до конвейера КЛЗ. Конвейер КЛ 3 подает груз на конвейер принадлежащий судопогрузочной машине. Судопогрузочная машина осуществляет погрузку минеральных удобрений в трюм судна.
Каждый пересыпной рукав с конвейера на конвейер оборудован аспирационным устройством более подробно аспирационное оборудование см. раздел 5 Инженерное обеспечение.
Каждый конвейер оборудован аппаратами обеспечивающими безаварийную работу конвейерной системы.
На каждом конвейере установлены:
- датчик нулевой скорости;
- датчик схода ленты;
- датчик завала и переполнения пересыпных рукавов.
На всех конвейерах предусмотрены устройства немедленной аварийной остановки их с любого места вдоль конвейерной ленты.
Перед пуском конвейера автоматически подается звуковой и световой сигнал слышимый и видимый по всей длине конвейерного маршрута.
Конвейерная система оборудована счетчиками длительности работы маршрута.
Для очистки барабанов и ленты предусмотрены эффективные очистные устройства
Все весовые приборы и аппараты автоматизированы и не требуют присутствия человека в процессе работы. Точность взвешивания составляет 05%.
В составе конвейерной системы предусмотрено оборудование для улавливания металлических и неметаллических посторонних предметов.
При переходе с одного сорта груза на другой предусмотрен сначала холостой прогон конвейерных лент для очистки их скребками а затем несколько минут конвейеры работают на сброс в емкость установленную в приводной станции ПрС 1. Очистка пересыпных рукавов бункеров и решеток станции разгрузки вагонов) предусматривается вручную.
Собранные остатки удобрений предполагается возвращать на заводы-изготовители или реализовывать на месте. Для реализации на месте предусмотрена фасовка удобрений в 50-ти килограммовые мешки с использованием имеющейся фасовочной машины.
Категория помещений по степени взрывопожарной опасности:
- конвейерных галерей - ВЗ;
- пересыпных станций ПС1 ПС2 - ВЗ;
- приводной станции ПрС1 - ВЗ.
Характеристика основного технологического оборудования представлена в таблице 1.4.
Улавливатель неметал. предметов
Маневровый локомотив
6. Численность обслуживающего персонала.
Расчетная численность управленческого и производственного персонала для обеспечения работы технологического комплекса приведена в таблице 1.5.
Наименование должностей
Начальник технологического комплекса
Зам. начальника по производству
На технологическом комплексе
Начальник смены старший технолог-оператор перегрузки
Оператор центрального пульта управления
Аппаратчик-бункеровщик станции разгрузки вагонов
Аппаратчик-бункеровщик конвейеров
Уборщик конвейерных галерей
LK_корд.doc
Род груза: минеральные удобрения
Производительность: переменная 600 – 1200 тч. Расчёт ведём по максимальной производительности производительность регулируем скоростью движения ленты.
Длина трассы: Lk=185 м
Насыпной вес груза:
Коэффициент разрыхления:
Угол естественного откоса:
Коэффициент трения груза по стали:
Коэффициент трения груза по ленте:
Условия работы: конвейер находится в технологической цепи; загрузка производится с ленточного конвейера; разгрузка производится разгрузочным устройством на ленту погрузочной машины; конвейер установлен стационарно; привод расположен в концевой части конвейера; натяжное устройство – грузовое расположено в загрузочной части конвейера.
Рис. 3.1 Схема прикордонного ленточного конвейера
Коэффициент производительности:
Коэффициент корректировки расчётной производительности:
Ширина ленты: В=0.97 м
Принимаем согласно ГОСТ 20-76:
Для определения натяжений в ленте применяем метод тягового расчёта по контуру.
Принимаем привод с одним ведущим барабаном угол обхвата которого 180о. Поверхность барабана футерована резиной.
Натяжение в набегающей ветви ленты ( точка 9) согласно формуле Эйлера:
В данном уравнении два неизвестных члена S1 и S9. Для составления второго уравнения обходим тяговый контур от точки 1 до точки 9 выражая натяжение во всех точках через натяжение в точке 1 – S1.
Для последующего расчёта необходимы погонные нагрузки:
Нагрузки от транспортируемого груза:
Нагрузки от вращающихся частей роликов:
Вес вращающихся частей роликоопор рабочей ветви: Gp1 = 25 кг
Расстояние между роликоопорами рабочей ветви: lp1 = 1.3 м
Вес вращающихся частей роликоопор холостой ветви: Gp2 = 25 кг
Расстояние между роликоопорами холостой ветви: lp2 = 2.6 м
Нагрузки от веса ленты:
принимаем число прокладок
принимаем толщину прокладки:
принимаем толщину верхней обкладки:
принимаем толщину нижней обкладки:
удельный вес ленты:
Натяжения в характерных точках тягового контура:
где ki – коэффициент увеличения натяжения в ленте при огибании барабана k=1.04 так как угол огибания равен 90о.
S3=S2+W2-3=1.04S1+(q0+qp2)L2-3`= 1.04S1+(16+9.6)*180*0.035=1.04S1+161
S4=k4S3=1.05(1.04S1+161)=1.092S1+169
S5=k5S4=1.04(1.092S1+169)=1.14S1+176
S6=k6S5=1.05(1.14S1+176)=1.197S1+185
При крайнем положении тележки L6-7 принимаем равным 170 м.
S7=S6+W6-7+ Wзагр = (1.197S1+185)+( (q+q0+qp1)L6-7`)+(с*P*f1(2gh)123.6 )=
=(1.197S1+185)+((120+16+19.2)*170*0.035)+(1.5*1200*2.75*0.56х
х(2*10*1.5)12)3.6) = 1.197S1 + 5326
S8=S7+W7-8=S7+(q+q0)L7-8(`cos+sin)+qp L7-8`=1.197S1 + 5326+
+(120+16)*18*(0.035*0.9+0.2)+19.2*18*0.035= 1.197S1+5904
S9=k9S8=1.03(1.197S1+5904)=1.23S1+ 6081
S10= k10S9=1.03(1.23S1+ 6081)=1.27S1+6264
S11= k11S10=1.04(1.27S1+6264)=1.32S1+6514
S12= k12S11=1.05(1.32S1+6514)=1.4S1+6840
где: Wi-j – сопротивление движению ленты на участке i-j.
Li-j – длина участка i-j
`- коэффициент сопротивления движению ленты зависящий от
типа подшипника смазки уплотнения и др. `= 0.035 (принимаем
для условий с повышенной влажностью и большим количеством
h = 1.5 м - высота падения груза на ленту
с = 1.5 – коэффициент учитывающий сопротивление движению от трения
груза о плужковый сбрасыватель и о ленту от движения ленты в
разгрузочной и разгрузочнойчасти.
Получаем систему из двух уравнений:
Определяем числовые значения натяжения ленты в характерных точках:
S2 = k2S1 = 1.04S1=1643 H
S3= 1.04S1+161=1804 H
S4= 1.092S1+169=1894 H
S5= 1.14S1+176=1977 H
S6= 1.197S1+185=2076 H
S7= 1.197S1 + 5326=7217 H
S8= 1.197S1+5904=7795 H
S9=1.23S1+ 6081=8024 H
S10=1.27S1+6264=8812 H
S11=1.32S1+6514=8600 H
Рис. 3.2. Диаграмма натяжения в ленте
Сопротивление передвижению ленты:
W0=S12-S1=9051-1580=7471Н
Расчётная мощность привода ленточного конвейера:
Np=W0v 102 = 7471*2.75 1000*0.9 = 23 кВт
где =0.9 – КПД привода.
Установочная мощность привода:
N0 = nуNp = 1.1 * 23 = 25 кВт
где nу=1.1 – коэффициент запаса мощности.
По ГОСТ 19523-81 выбираем трёхфазный асинхронный короткозамкнутый двигатель серии 4А: 4A200L6Y3. N = 30 кВт n = 975 обмин.
Выбираем ленту с прокладками из синтетической ткани – капрона с пределом прочности р = 180 кгссм прокладки. Лента воспринимает максимальное натяжение Smax= S12 = 9051 Н запас прочности n=10.
Число прокладок в ленте:
i = Smaxn рB = 9051*10 180*100 = 5
Принимаем ленту с 5-ю основными прокладками. Так как первоначально для расчёта была принята лента с шестью прокладками то пересчитывать конвейер не нужно.
Диаметр приводного барабана:
Dб = а1i = 220*5 = 1100 мм
где а1=220 – эмпирический коэффициент.
По ГОСТ 22644-77 принимаем диаметр приводного барабана Dб=1000 мм.
Диаметр концевого и натяжного барабанов:
D1 = 0.8 Dб = 0.8*880 = 704 мм.
Принимаем D1 = 900 мм
Диаметр отклоняющих барабанов:
D2 = 0.65 Dб = 0.65*880 = 572 мм
Принимаем D2 = 630 мм
Lб= В + аб = 1000 + 150 = 1150 мм
где аб = 150 – эмпирический коэффициент.
Частота вращения приводного барабана:
nб = 60v D = 60*2.75 3.14*1.056 = 49.3 мин-1
где D = Dб + 2Δф = 1 + 2*0.028 = 1.056 м
Δф= 0.028 м – толщина резиновой футеровки.
Передаточное число редуктора привода конвейера:
uр.р. = nnб = 98549.3 = 20
Расчётная мощность редуктора:
Nред = k`pNp = 1.25*25 = 31.25 кВт
где k`p=1.25 – коэффициент условий работы.
По каталогу выбираем редуктор ЦД2-100М-16-I двухступенчатый с межосевым расстоянием между быстроходным и тихоходным валами Ас=1000 мм с передаточным числом up=16; номер схемы сборки I; с циллиндрическим концом выходного вала.
Для обеспечения производительности P=600 тч подключаем электродвигатель ЭД-2 как показанно на схеме рис.3.1.2 При работе одного двигателя второй отключается или работает в генераторном режиме.
Определим характеристики электродвигателя ЭД-2:
n2=n2=14652=732 обмин
N2 N2 = 312 = 15.5 кВт
По ГОСТ 19523-81 выбираем электродвигатель 4А180М8У3 N=15 кВт n=730 обмин.
Konveer2.dwg

(Modell- oder Gesenk-Nr)
Нач. КБ. Гребенников
Технические требования.
Предельные отклонения размеров диаметров: по H14
Предельные отклонения размеров: ±IT142.
Неуказанные педельные отклонения размеров диаметров: H14
Сварные швы выполнить по ГОСТ 5264-80 и ГОСТ 11534-75 электродом
Контроль качества сварных швов выполнить внешним осмотром
с измерением по ГОСТ 3242-79.
Металлоконструкцию очистить от ржавчины и окалины
грунтовкой ВЛ-02 ГОСТ 12707-77 и покрыть эмалью ПФ-115 ГОСТ 6465-76.
Цвет согласовать с заказчиком.
Развернутая длина поз. 1 L=0000мм.
* Размер для справок.
* Размеры для справок.
** Размеры уточнить при сборке.
*** Выполнить совместно с деталью N° 0000.
Неуказанные литейные радиусы 3 5мм.
Острые кромки притупить.
Испытать согласно действующих "Правил устройства и безопасной
эксплуатации грузоподъемных кранов.
Маркировать: инвентарный номер
клеймо технического контроля.
защищенном от атмосферных осадков.
Производительность- 600 тч
Мощность двигателя- 15 кВт
Редуктор ЦД2-100М-16-1
Промежуточный ленточный
Отклоняющий барабан 4
Натяжное устройство 1
Разгрузочная тележка
прикордонного конвейера.
Прикордонный конвейер.
Техническая характеристика:
Стойка с подшипником
Муфта предельного момента
Размеры для справок.
Длина трассы - 24.6 м
Мощность двигателя- 37 кВт
Грузовое натяжное устр-во
Ролик холостой ветви
Ролик грузовой ветви
Промежуточный наклонный
Привод конвеера переменной
Длина трассы - 185 м
Двигатель 4A200M6Y3.
Мощность двигателя- 22 кВт
Мощность двигателя поз.2- 37 кВт
Двигатели 4A250S8Y3 - оба.
Мощность двигателя поз.1- 37 кВт
Частота вращения двигателя поз.2- 735 1мин
Частота вращения двигателя поз.1- 1470 1мин
LK_ТЫЛ_испр.doc
Род груза: минеральные удобрения (берутся их показатели требующие максимальной мощности привода).
Производительность: Производительность: переменная 600 – 1200 тч. Расчёт ведём по максимальной производительности производительность регулируем скоростью движения ленты.
Длина трассы: l = 50.8 м
Насыпной вес груза:
Коэффициент разрыхления:
Угол естественного откоса:
Коэффициент трения груза по стали:
Коэффициент трения груза по ленте:
Условия работы: конвейер находится в технологической цепи; загрузка производится с ленточного конвейера; разгрузка производится однобарабанным разгрузочным устройством в бункер загрузочного устройства следующего конвейера; конвейер установлен стационарно; привод расположен в разгрузочной части конвейера; натяжное устройство – грузовое расположено в головной части конвейера.
Рис. 3.2.1 Схема ленточного конвейера
Коэффициент производительности:
Коэффициент корректировки расчётной производительности:
Ширина ленты: B=0.974 м
Принимаем согласно ГОСТ 20-76:
Для определения натяжений в ленте применяем метод тягового расчёта по контуру.
Принимаем привод с одним ведущим барабаном угол обхвата которого 180о. Поверхность барабана футерована резиной.
Натяжение в набегающей ветви ленты ( точка 9) согласно формуле Эйлера:
В данном уравнении два неизвестных члена S1 и S9. Для составления второго уравнения обходим тяговый контур от точки 1 до точки 9 выражая натяжение во всех точках через натяжение в точке 1 – S1.
Для последующего расчёта необходимы погонные нагрузки:
Нагрузки от транспортируемого груза:
Нагрузки от вращающихся частей роликов:
Вес вращающихся частей роликоопор рабочей ветви:
Расстояние между роликоопорами рабочей ветви:
Вес вращающихся частей роликоопор холостой ветви:
Расстояние между роликоопорами холостой ветви: м
Нагрузки от веса ленты:
принимаем число прокладок
принимаем толщину прокладки:
принимаем толщину верхней обкладки:
принимаем толщину нижней обкладки:
удельный вес ленты:
Натяжения в характерных точках тягового контура:
где ki – коэффициент увеличения натяжения в ленте при огибании барабана k=1.04 так как угол огибания равен 90о. Далее – по табл.3.1.1
Таблица 3.1.1 Значение коэффициента ki
Угол обхвата лентой отклоняющего барабана о
S3=S2+W2-3=1.04S1+(q0+qp2)L2-3`= 1.04S1+(16+9.615)*47*0.035=1.04S1+42
S4=k4S3=1.05(1.04S1+42)=1.092S1+44
S5=k5S4=1.04(1.092S1+44)=1.14S1+46
S6=k6S5=1.05(1.14S5+46)=1.197S1+48
S7=S6+W6-7+Wзагр= (1.197S1+23)+( (q+q0+qp1)L6-7`)+(с*P*v*g36 )=
(1.197S1+41)+((120+16+19.23)*51*0.035)+(1.5*1200*2.7536) = 1.197S1+455
S8=k8S7=1.04(1.197S1+455)=1.23S1+474
S9=k9S8=1.05(1.23S1+474)=1.29S1+497
где: Wi-j – сопротивление движению ленты на участке i-j.
Li-j – длина участка i-j
`- коэффициент сопротивления движению ленты зависящий от
типа подшипника смазки уплотнения и др. `= 0.035 (принимаем
для условий с повышенной влажностью и большим количеством пыли).
с = 1.5 – коэффициент учитывающий сопротивление движению от трения
груза о боковые стенки загрузочной воронки и о ленту от движения
ленты в загрузочной части.
Получаем систему из двух уравнений:
Определяем числовые значения натяжения ленты в характерных точках:
S3 = 1.04S1+42 = 158 Н
S4 = 1.092S1+44= 166 Н
S5 = 1.14S1+46 = 174 Н
S6 = 1.197S1+48= 182 Н
S7 = 1.197S1+455 = 589 Н
S8 = 1.29S1+474 = 618 Н
Рис. 3.2.2 Диаграмма натяжения в ленте
Сопротивление передвижению ленты:
W0=S9-S1=641-112=529 Н
Расчётная мощность привода ленточного конвейера:
Np=W0v 1000 = 529*2.75 1000*0.9 = 1.6 кВт
где =0.9 – КПД привода.
Установочная мощность привода:
N0 = nуNp = 1.1 * 1.5 = 2 кВт
где nу=1.1 – коэффициент запаса мощности.
По ГОСТ 19523-81 выбираем трёхфазный асинхронный короткозамкнутый двигатель серии 4А: 4A160M6Y3. N = 15 кВт n = 985 обмин.
Выбираем ленту с прокладками из синтетической ткани – капрона с пределом прочности р = 180 кгссм прокладки. Лента воспринимает максимальное натяжение Smax= S9 = 3398 кН запас прочности n=10.
Число прокладок в ленте:
i = Smaxn рB = 6043*10 180*80 4
Принимаем ленту с 4-мя основными прокладками. Так как первоначально для расчёта была принята лента с шестью прокладками то пересчитывать конвейер не нужно.
Диаметр приводного барабана:
Dб = а1i = 220*4 = 880 мм
где а1=220 – эмпирический коэффициент.
По ГОСТ 22644-77 принимаем диаметр приводного барабана Dб=1000 мм.
Диаметр концевого и натяжного барабанов:
D1 = 0.8 Dб = 0.8*880 = 700 мм.
Принимаем D1 = 800 мм
Диаметр отклоняющих барабанов:
D2 = 0.65 Dб = 0.65*880 = 570 мм
Принимаем D2 = 630 мм
Lб= В + аб = 800 + 150 = 950 мм
где аб = 150 – эмпирический коэффициент.
Частота вращения приводного барабана:
nб = 60v D = 60*2.75 3.14*0.865 = 61.4 мин-1
где D = Dб + 2Δф = 0.8 + 2*0.028 = 0.856 м
Δф= 0.028 м – толщина резиновой футеровки.
Передаточное число редуктора привода конвейера:
uр.р. = nnб = 98561.4 = 16
Расчётная мощность редуктора:
Nред = k`pNp = 1.25*15 = 19 кВт
где k`p=1.25 – коэффициент условий работы.
По каталогу выбираем редуктор ЦД2-100М-16-I двухступенчатый с межосевым расстоянием между быстроходным и тихоходным валами Ас=1000 мм с передаточным числом up=16; номер схемы сборки I; с циллиндрическим концом выходного вала.
Использование редуктора ЦД2-100М со схемой сборки III даёт возможность расположить электродвигатель по одну а редутор по другую сторону конвейера что уменьшит габариты приводной станции (Рис 3.1.3.)
ДИПЛОМ_Введение.doc
Экспортные возможности российской промышленности минеральных удобрений обеспечиваются обширными залежами фосфоритных и азотосодержащих руд а также природного газа. В настоящий момент объем экспорта минеральных удобрений составляет свыше 74 млрд ам. долларов в год и является третьим по величине в структуре российского бизнеса. До 2005 года ожидается рост мирового потребления удобрений примерно на 29 млн. тонн из которых на 16 млн. тонн претендуют страны Юго-Восточной Азии 6 млн. тонн - страны Центральной и Восточной Европы и на 7 млн. тонн - прочие страны. В этой связи будет также наблюдаться значительный рост спроса на морские перевозки удобрений который в ближайшее десятилетие составит примерно 170 миллиардов тонно-миль. Из них почти 72 % придется на Азиатские рынки и 185% на рынки Латинской Америки.
) отправлять груз маленькими партиями (максимум 7000 т ) что приводит в конце концов к большой цене перевозки морем и становится невыгодным импортеру или экспортеру;
) использовать порты Украины при экспорте удобрений так как они имеют специализированные терминалы для хранения груза и поэтому заводы-экспортеры могут накапливать груз в портах погрузки.
Таким образом можно сделать вывод что для привлечения устойчивых грузопотоков отечественных заводов-экспортеров порту Новороссийск необходим специализированный комплекс переработки минеральных удобрений с накопительным терминалом. Новый терминал должен обеспечивать высокую норму грузовых работ что существенно будет снижать долю расходов на перевозку грузов морем.
Диплом М.doc
Технологический комплекс перегрузки минеральных удобрений на территории Восточного района Новороссийского морского порта предназначен для выгрузки минеральных удобрений из железнодорожных вагонов и погрузки их в морские суда.
Грузооборот технологического комплекса - 2 млн. тгод.
Режим работы технологического комплекса круглогодичный трехсменный продолжительность смены - 7 часов 30 минут.
Погрузка минеральных удобрений на технологическом комплексе осуществляется в морские суда дедвейтом до 50 тыс. т.
Основные характеристики максимального расчетного типа судна и размеры приведены в таблице 1.1.
Наименование показателей
Основные размерения:
Технологический комплекс предназначен для перегрузки сыпучих гранулированных минеральных удобрений в том числе: карбамида (50-60%) аммиачной селитры (30-35%) и сложных азотно-фосфорных и азотно-фосфорно-калийных удобрений (15-25%).
Минеральные удобрения транспортируются и перегружаются навалом. Физико-химические свойства удобрений приведены в таблице 1.2.
Массовая плотность гсм3
Объемная плотность гсм3
Класс опасности по ГОСТ 19433-88
Класс 9 подкласс 9.1 категория 9.14 группа 91.43
Доставка минеральных удобрений в порт осуществляется по железной дороге в вагонах-минераловозах. Минераловозы представляют собой саморазгружающиеся вагоны с нижней разгрузкой через люки щелевого типа.
Вагон-хоппер для перевозки минеральных удобрений имеет грузоподъемность 70 т и предназначен для бестарной перевозки гранулированных крупнозернистых кристаллических минеральных удобрений.
Конструкция четырех разгрузочных люков хоппера в виде наклонных днищ обеспечивает полную разгрузку удобрения в сторону от пути. Люки могут открываться пневмоприводом одновременно все или попарно. Предусмотрена возможность ручного открывания. Блокирующие устройства предотвращают самопроизвольное открывание люков в пути и на стоянке.
Характеристика вагона-минераловоза и его основные размеры приведены в таблице 1.3.
Характеристика железнодорожного вагона
Ширина максимальная мм
Высота от уровня головки рельса мм
Размер разгрузочного люка в свету мм
Количество разгрузочных люков
По конструктивным характеристикам кузов хоппера является недостаточно герметичным; имеется практическая возможность выхода газов при возможности начала разложения селитры.
Перед погрузкой минеральных удобрений на заводах-изготовителях вагоны-хопперы освобождаются от предыдущих остатков удобрения и проверяются на отсутствие посторонних предметов в том числе и металлических промасленной ветоши бумаги. Этому уделяется особое внимание перед погрузкой аммиачной селитры. Сырые погрузочные места осушаются горячим воздухом. Таким образом создаются условия исключающие возможность термического разложения продукта при погрузо-разгрузочных операциях и транспортировке вагонов.
2. Механизация и технология перегрузочных работ.
Технологический комплекс состоит из следующих основных узлов:
- станции разгрузки вагонов;
- береговой механизации для погрузки судов;
- транспортной системы в составе конвейерных галерей перегрузочных и приводной станций.
В состав технологического комплекса входит следующее основное технологическое оборудование:
- судопогрузочная машина оборудованная пылеподавляющей насадкой;
- система ленточных конвейеров и пересыпных устройств обеспечивающих транспортировку минеральных удобрений;
- оборудование центрального пульта управления технологическим комплексом;
- оборудование для уборки пыли и просыпей;
- оборудование для измерения и регистрации в автоматическом режиме массы груза проходящего по технологическому варианту работы;
- оборудование для улавливания металлических и неметаллических посторонних предметов;
- маневровый локомотив.
В состав комплекса входят также оборудование и системы обеспечивающие надежную экологически чистую и безопасную эксплуатацию:
вентиляционное оборудование; системы аспирации и пылеулавливания;
системы пожаротушения связи и сигнализации в том числе пожарной сигнализации;
система автоматизированного управления технологическим процессом и др.
При проектировании технологического комплекса принято электрооборудование во взрывозащищенном исполнении с целью обеспечения его наибольшей степени защиты от пыли.
На технологическом комплексе предусмотрена работа по прямому варианту вагон-судно вагон – склад склад – судно и их совмещение.
По технологической линии включающей в себя питатели ленточные ПЛ(1-6) и конвейеры ленточные КЛ1 КЛ2 и КЛЗ осуществляется подача груза от станции разгрузки вагонов на судно.
На чертежах приняты условные обозначения:
- ПЛ - питатель ленточный;
- КЛ - конвейер ленточный;
- СпМ - судопогрузочная машина;
- ПС - пересыпная станция;
ПрС - приводная станция;
- СРВ - станция разгрузки вагонов;
- БПГ - береговая погрузочная галерея.
3. Станция разгрузки вагонов.
Разгрузка вагонов осуществляется на станции разгрузки вагонов (СРВ) располагаемой на двух железнодорожных тупиковых путях при этом разгрузка осуществляется последовательно по 3 вагона на одном пути.
Подача вагонов от железнодорожного парка "Восточный" на разгрузочные железнодорожные пути СРВ и вывод порожних вагонов на выставочные железнодорожные пути производится маневровым локомотивом порта.
На каждый железнодорожный путь СРВ осуществляется подача груженых 27-ми вагонов-минераловозов. В СРВ осуществляется последовательная разгрузка по 3 вагона. По окончании разгрузки 3-его вагона тягачем осуществляется протягивание под разгрузку следующих 3-х вагонов и отвод 3-х порожних вагонов на свободный железнодорожный путь. По окончании разгрузки подачи из 27 вагонов маневровым локомотивом подается следующая подача из 27 груженых вагонов а порожние вагоны отводятся на резервный путь Восточного парка.
Время разгрузки одного вагона с учетом времени на открытие и закрытие разгрузочных люков подтвержденное практическим хронометражем на действующих терминалах составляет в среднем 3-4 минуты соответственно время разгрузки одной группы из трех вагонов от 10-12 до 15 минут.
При ограниченности времени выгрузки минеральных удобрений исключаются условия для уплотнения значительных масс удобрений и самоускоряющихся процессов их теплового разложения. Соответственно в мировой практике подобные явления не зарегистрированы они не отмечены и при транспортировке этих продуктов железнодорожным транспортом.
Станция разгрузки вагонов располагается на двух железнодорожных путях под которыми находятся шесть металлических бункеров по 65 м3 каждый. Бункеры закрыты сверху решеткой с ячейкой размерами 200х200 мм.
В заглубленной части СРВ под приемными бункерами установлены 6 ленточных питателей для равномерной перегрузки удобрений из бункеров на магистральный конвейер КЛ1.
Питатели работают только попарно (ПЛ12; ПЛЗ4; ПЛ56)с производительностью каждого 300 тчас. Скорость движения ленты на питателях переменная что позволяет иметь производительность на магистральном конвейере КЛ1 - 600 тчас независимо от вида перегружаемого минерального удобрения.
Станция разгрузки вагонов и пересыпные рукава с питателей на магистральный конвейер КЛ 1 оборудованы аспирационными установками.
Категория помещений станции разгрузки вагонов по степени взрывопожарной опасности - В2.
4. Береговая механизация для погрузки судов.
Береговая механизация включает в себя судопогрузочную машину и береговую погрузочную галерею в которой расположен конвейер ленточный КЛЗ подающий груз на машину для загрузки судна.
Категория помещений береговой погрузочной галереи по степени взрыво-пожарной опасности - ВЗ.
Техническая производительность судопогрузочной машины 1200 тчас.
Судопогрузочная машина представляет собой металлоконструкцию портального типа передвигающуюся по рельсам вдоль причала.
Колея причала 105 м.
В береговой погрузочной галерее минеральные удобрения с ленточного конвейера КЛ 3 при помощи сбрасывающей тележки двигающейся по специальным рельсовым путям передается на судопогрузочную машину. Хвостовая часть судопогрузочной машины механически соединена со сбрасывающей тележкой ленточного конвейера. Подобная конструкция предотвращает просыпи на причале уменьшает пыление в узле передачи груза с берегового ленточного конвейера на ленточный конвейер расположенный на судопогрузочной машине. Подъемная стрела судопогрузочной машины шарнирно прикреплена к порталу машины и оборудована специальной телескопической трубой через которую происходит сброс груза в трюм судна.
Пересыпной рукав с конвейера КЛЗ расположенного в береговой погрузочной галерее на конвейер принадлежащий судопогрузочной машине оборудован аспирационным устройством. Это аспирационное устройство является составной частью судопогрузочной машины. Также аспирационным устройством оснащен пересыпной рукав с конвейера на конвейер судопогрузочной машины.
С целью уменьшения пыления при погрузке судна судопогрузочная машина оборудована пылеподавляющей насадкой.
Передача минеральных удобрений с ленточного конвейера расположенного в береговой погрузочной галерее на судопогрузочную машину осуществляется через продольную непрерывную щель предусмотренную конструкцией береговой погрузочной галереи и имеющую по всей длине укрытие из резиновой ткани.
Управление судопогрузочной машиной предусмотрено из кабины оператора или с переносного пульта в режиме ручного управления.
Механизм передвижения снабжен противоугонными рельсовыми захватами с приводом управляемым из кабины оператора и ручным приводом на каждом захвате. Для предотвращения движения судопогрузочной машины под действием ураганного ветра дополнительно предусмотрены стопорные устройства.
Интенсивность обработки судна с учетом производственных стоянок -9100 тсут.
Расчетное время погрузки судовой партии 50 тыс. т с учетом времени на швартовкуотшвартовку оформления грузовых таможенных и пограничных документов составляет 5.5 суток.
5. Конвейерная система.
Конвейерная система осуществляет транспортировку минеральных удобрений между станцией разгрузки вагонов и береговой погрузочной галереей обеспечивая перегрузку груза по технологическому варианту вагон-судно.
Ширина ленты В= 1400мм.
Для предотвращения просыпа удобрений с конвейерных лент установлены верхние трехроликовые опоры с желобчатостью 30°.
Угол наклона конвейеров не превышает 15°. В наклонных конвейерах установлены устройства предотвращающие обратное движение ленты.
Техническая производительность конвейеров КЛ 1 2 - 600 тчас конвейера КЛЗ - 1200 тчас (в связи с возможностью приема минеральных удобрений со склада).
Конвейер ленточный КЛ 1 перемещает груз от станции разгрузки вагонов в пересыпную станцию ПС 1 в которой осуществляется передача груза с КЛ 1 на КЛ 2. Через пересыпную станцию ПС 2 конвейером КЛ 2 происходит доставка минеральных удобрений к береговой погрузочной галерее до конвейера КЛЗ. Конвейер КЛ 3 подает груз на конвейер принадлежащий судопогрузочной машине. Судопогрузочная машина осуществляет погрузку минеральных удобрений в трюм судна.
Каждый пересыпной рукав с конвейера на конвейер оборудован аспирационным устройством более подробно аспирационное оборудование см. раздел 5 Инженерное обеспечение.
Каждый конвейер оборудован аппаратами обеспечивающими безаварийную работу конвейерной системы.
На каждом конвейере установлены:
- датчик нулевой скорости;
- датчик схода ленты;
- датчик завала и переполнения пересыпных рукавов.
На всех конвейерах предусмотрены устройства немедленной аварийной остановки их с любого места вдоль конвейерной ленты.
Перед пуском конвейера автоматически подается звуковой и световой сигнал слышимый и видимый по всей длине конвейерного маршрута.
Конвейерная система оборудована счетчиками длительности работы маршрута.
Для очистки барабанов и ленты предусмотрены эффективные очистные устройства
Все весовые приборы и аппараты автоматизированы и не требуют присутствия человека в процессе работы. Точность взвешивания составляет 05%.
В составе конвейерной системы предусмотрено оборудование для улавливания металлических и неметаллических посторонних предметов.
При переходе с одного сорта груза на другой предусмотрен сначала холостой прогон конвейерных лент для очистки их скребками а затем несколько минут конвейеры работают на сброс в емкость установленную в приводной станции ПрС 1. Очистка пересыпных рукавов бункеров и решеток станции разгрузки вагонов) предусматривается вручную.
Собранные остатки удобрений предполагается возвращать на заводы-изготовители или реализовывать на месте. Для реализации на месте предусмотрена фасовка удобрений в 50-ти килограммовые мешки с использованием имеющейся фасовочной машины.
Категория помещений по степени взрывопожарной опасности:
- конвейерных галерей - ВЗ;
- пересыпных станций ПС1 ПС2 - ВЗ;
- приводной станции ПрС1 - ВЗ.
Характеристика основного технологического оборудования представлена в таблице 1.4.
Улавливатель неметал. предметов
Маневровый локомотив
6. Численность обслуживающего персонала.
Расчетная численность управленческого и производственного персонала для обеспечения работы технологического комплекса приведена в таблице 1.5.
Наименование должностей
Начальник технологического комплекса
Зам. начальника по производству
На технологическом комплексе
Начальник смены старший технолог-оператор перегрузки
Оператор центрального пульта управления
Аппаратчик-бункеровщик станции разгрузки вагонов
Аппаратчик-бункеровщик конвейеров
Уборщик конвейерных галерей
7 Расчёт действительной производительности перегрузочного комплекса.
Комплекс по перегрузке минеральных удобрений рассчитан на годовой грузооборот Qpгод=2 млн.тгод.
)Суточный расчётный грузооборот причала составляет:
Qpсут= Qpмес (30.5-tн.р)=0.16(30.5-3)=0.0058 млн.тсут = 5800 тсут
где: tн.р=3 cут – количество нерабочих дней по метеоусловиям в наиболее
Qpмес= Qpгод12 = 212=0.16 млн.тмес – месячный грузооборот комплекса.
Принимаем что через склад проходит годового грузопотока т.е.
Коэффициент складочности: αск= Qск Qн= 0.5
где Qн= Qpгод – навигационный грузооборот.
)Транспортные средства их характеристика режим поступления под обработку условия грузовой обработки в порту.
Фактическая загрузка судна:
Dф=c D = 0.8* 500000= 40000 т
где: c=0.8 – коэффициент использования грузоподъёмности судна.
Среднее количество судов поступающих под обработку в порт в течении суток:
nc=QнКн DфTн = 2000000* 1 40000*360 = 0.14
Средний интервал времени между судами:
Тис=24nc=240.14=172.8 часа
Число вагонов подаваемых на причал под обработку в течении суток:
nв=QнКнТнGф = 2000000*1 360*56 = 100 вагонов
где: Gф= в GB = 0.8*70= 56 т - фактическая загрузка вагона.
GB=70 т – паспортная загрузка вагона.
в=0.8 – коэффициент использования грузоподъёмности вагона.
Число подач вагонов в сутки:
mпод= nв nпод= 10020=5 подач
где: nпод=20 – число вагонов в подаче.
Средний интервал между подачами:
ив=24 mпод = 245 = 4.8 часа
)Определение вместимости и площади склада:
Расчётную вместимость склада принимаем равной вместимости максимального расчётного судна т.е. Еск=50000 т
Foc=Eск Киqск = 50000 0.85*10 6000 м2
где: Ки=0.85 – коэффициент использования основной площади склада.
qск=10 тм2 – допустимая нагрузка на причал.
Принимаем склад 200х30 м ( 4 бункера по 50х30 м каждый). Каждый бункер рассчитан на 15000 т удобрений.
)Пропускная способность и минимально необходимая интенсивность обработки транспортных средств на причале.
Нормативная пропускная способность:
[Пс]=24Dф[Тс]=24*40000417=2302 тсутки
где: [Tc] = [Tгр]+Tвсп = 412+4.5=417 часов – норма времени стоянки судна у
[Tгр] = Dф [J] = 40000 97 =412 часов – норма времени стоянки судна под
[J] = 97 тчас – судо-часовая норма интенсивности грузовых работ.
Твсп = 4.5 часов – норма времени на выполнение маневровых и
вспомогательных операций с судами.
Принимаем [Пс]= мах (Qpc [Пс]) = 5800 тсутки.
Минимальная необходимая интенсивность грузооброботки судна:
Jc=Прс Кивtоп=5800 0.98*19=311.5 тчас
где: Кив= [Tгр] ([Tгр] + Tвсп) = 0.98 – коэффициент использования причала по
tоп=Кпзtсм = 0.85*3*7.5 = 19 часов – эффективное время работы
оборудования причала в течении суток при трёхсменной работе.
tсм=7.5 часа – продолжительность смены.
Для обработки на причале расчетного грузооборота поступающего в железнодорожных вагонах пропускная способность перегрузочного оборудования фронта обработки вагонов должна быть достаточной чтобы было выполнено условие:
где: [Пв] – нормативная пропускная способность при обработке вагонов.
[Пв]=24nвпGф [в] = 20*56*241.6 = 16800 тсутки
где: [в] = 1.6 часа – норма времени обработки подачи вагонов.
Пв= Qcp = 5800 т сутки
Минимальная интенсивность оборудования занятого на обработке подач вагонов необходимая для обеспечения переработки расчётного суточного грузооборота по прибытию в железнодорожных вагонах и выполнения норм времени обработки подачи вагонов:
Jв=Пвр Кивtоп = 5800 1*19 = 305 тчас
)Продолжительность стоянки судна у причала под грузовой обработкой.
Продолжительность стоянки судна складывается из затрат времени на швартовые операции погрузку судна с учётом технологических перерывов в процессе грузовой обработки и оформление документов.
а) Продолжительность стоянки судна при производительности комплекса
00 т час (после модернизации):
Тс= Тгр + Т всп = 36.7 + 4.5 = 41.22 часа=1.7 суток
где: Тгр= Dф( NфрРсtопК1К2) = 40000(1*1200*22.5*0.97)=1.53 суток = 36.7 часа
Твсп=4.5 часа – норма времени на вспомогательные операции.
б) Продолжительность стоянки судна при производительности комплекса
0 тчас (до модернизации):
Тс= Тгр + Т всп = 73.3 + 4.5 = 77.8 часа
Тгр= Dф( NфрРсtопК1К2) = 40000(1*600*22.5*0.97)=3.05 суток = 73.3 часа
)Пропускная способность причала:
а) С использованием склада:
Пс=DфТс=400001.7=23529 тсутки
б) Без использования склада:
Пс=DфТс=400003.05=13114 тсутки
)Коэффициент резерва пропускной способности:
а) С использованием склада:
Крез=ПсQpc = 235295800=4.0
Крез=ПсQpc = 131145800=2.26
Технико-экономическое и конструктивно-техническое обоснование параметров перегрузочного комплекса.
В мире распространено два основных способа перевалки минеральных удобрений в портах погрузки:
Рассмотрим эти два пути перевалки минеральных удобрений для примера возьмем сульфат аммония так как этот груз соответствует теме дипломной работы и проведем сравнительный анализ экологичности и экономического эффекта получаемого в результате использования более современного перегрузочного оборудования.
Рассмотрим первый вариант погрузки удобрений.
Удобрения поступающие в специализированных крупнотоннажных контейнерах и вагонах минераловозах грузятся на судно по прямому варианту. Груз высыпается из контейнера (вагона) через специализированный разгрузочный люк краном работающим в грейферном режиме и оснащенным специальной траверсой и грузовыми стропами с крючьями. Траверса навешивается на канаты с помощью скоб. Для использования данного метода перевалки необходимо задействовать девятерых докеров ~ механизаторов и одного крановщика. Четыре докера-механизатора на берегу снимают специализированный контейнер со штыков железнодорожной платформы. Крановщик приподнимает контейнер над платформой и убедившись в надежности застропки и в том что он снят со штыков переносит его на судно. Затем устанавливает контейнер перпендикулярно левому или правому борту комингса трюма на расстоянии 02-03 м ниже верхней кромки и прекращает работу. Четыре докера -механизатора помогают ему установить контейнер точно над необходимым местом выгрузки в трюме с помощью строп прикрепленных заранее к контейнеру. Затем докер - механизатор находясь на палубе судна надевает рычаг и движением вниз открывает замок торцевой люк отходит и груз начинает высыпаться из контейнера (21).
Таким образом видим что данный способ технологически сложен трудоемок требует большого опыта докеров-механизаторов и соответственно имеет низкую эффективность так как обеспечивает низкую норму грузовых работ( около 2000 тсутки). Кроме этого не выполняются экологические нормативы так как на практике запорное устройство замка вагонов – минераловозов и специализированных контейнеров для перевозки сульфата аммония в 90 случаях из 100 находится в неисправном техническом состоянии поэтому необходимо его предварительное ослабление на причале в результате чего высыпается в среднем около 50 кг груза из одного вагона или контейнера. Соответственно грузоотправитель несет материальные издержки за потерю груза. Для примера возьмем партию в 10 000 т для ее перевозки необходимо задействовать 200 вагонов или около 550 контейнеров следовательно отправитель теряет около 10 т груза только в процессе перегрузки.
Кроме этого часть груза просыпается за борт судна и развеивается по ветру (порядка 50 кг из одного вагона и грузоотправитель теряет еще 10 т груза) что отрицательно влияет на окружающую среду. Потому что в соответствии с правилами грузовых работ они должны опускать вагон в трюм и только после этого открывать запорное устройство на выгрузочном люке вагона. При работе с последними вагонами на погрузке судна они не имеют такой возможности из-за того что трюма практически заполнены и они вынуждены открывать и выгружать вагоны и контейнеры над люком. При открытии люков докеры — механизаторы также открывают вагоны над трюмом. Таким образом при восточном юго-восточном ветре часть груза попадает в город. С учетом того что в соответствии с договорными ценами уборка одной тонны стоит 10 амм.долл. определим потери отправителя из расчета стоимости 1 тонны удобрений 60 амм.долл.
где П - потери грузоотправителя при погрузке
Уг - стоимость уборки одной тонны удобрений с причала. Цфоб - цена товара на условиях ФОБ - порт погрузки.
П = (60+10)*20 = 1400 амм.долл
Рассмотрим второй вариант погрузки минеральных удобрений.
Однако при использовании специального терминала повышаются расходы на обеспечение безопасности труда они составляют около 500 ам.доллмесяц при использовании обычного варианта перегрузки они составляют 200 ам.доллмесяц.. В эти расходы при использовании специального терминала входят обслуживание очищающих кондиционеров в накопительном бункере проведение инструктажа по технике безопасности обеспечение индивидуальными средствами защиты.
Рассчитаем экономический эффект от использования специального терминала:
Ээк = (П+Ртб) - (Птерм + Ртбт) (20)
где Ээк - экономический эффект от использования терминала ам.доллмесяц
Ртб - расходы на технику безопасности при использовании обычного варианта
Птерм - технологическая убыль при использовании терминала ам.доллмесяц
Ртбт - расходы на технику безопасности при использовании терминала
Ээк = (1400+200)-(300+500) = 800 ам.доллтонна.
Итак согласно проведенным расчетам можно сделать вывод что экономический эффект от перевалки 10000 тонн нитроаммофоски при использовании специального терминала составляет порядка 800 амм.долл только из-за уменьшения потерь груза и обеспечения чистоты окружающей среды. Поэтому в мире наблюдается тенденция планирования и постройки специализированных терминалов и причалов для грузовых работ которые обеспечивают -
) Высокую норму грузовых работ.
) Минимальные потери груза при погрузке.
) Высокую защиту окружающей среды.
Определение рациональных параметров перегрузочного комплекса.
1 Расчёт прикордонной конвейерной линии .
Род груза: минеральные удобрения
Производительность: переменная 600 – 1200 тч. Расчёт ведём по максимальной производительности производительность регулируем скоростью движения ленты.
Длина трассы: Lk=185 м
Насыпной вес груза:
Коэффициент разрыхления:
Угол естественного откоса:
Коэффициент трения груза по стали:
Коэффициент трения груза по ленте:
Условия работы: конвейер находится в технологической цепи; загрузка производится с ленточного конвейера; разгрузка производится разгрузочным устройством на ленту погрузочной машины; конвейер установлен стационарно; привод расположен в концевой части конвейера; натяжное устройство – грузовое расположено в загрузочной части конвейера.
Рис. 3.1 Схема прикордонного ленточного конвейера
Коэффициент производительности:
Коэффициент корректировки расчётной производительности:
Ширина ленты: В=0.97 м
Принимаем согласно ГОСТ 20-76:
Для определения натяжений в ленте применяем метод тягового расчёта по контуру.
Принимаем привод с одним ведущим барабаном угол обхвата которого 180о. Поверхность барабана футерована резиной.
Натяжение в набегающей ветви ленты ( точка 9) согласно формуле Эйлера:
В данном уравнении два неизвестных члена S1 и S9. Для составления второго уравнения обходим тяговый контур от точки 1 до точки 9 выражая натяжение во всех точках через натяжение в точке 1 – S1.
Для последующего расчёта необходимы погонные нагрузки:
Нагрузки от транспортируемого груза:
Нагрузки от вращающихся частей роликов:
Вес вращающихся частей роликоопор рабочей ветви: Gp1 = 25 кг
Расстояние между роликоопорами рабочей ветви: lp1 = 1.3 м
Вес вращающихся частей роликоопор холостой ветви: Gp2 = 25 кг
Расстояние между роликоопорами холостой ветви: lp2 = 2.6 м
Нагрузки от веса ленты:
принимаем число прокладок
принимаем толщину прокладки:
принимаем толщину верхней обкладки:
принимаем толщину нижней обкладки:
удельный вес ленты:
Натяжения в характерных точках тягового контура:
где ki – коэффициент увеличения натяжения в ленте при огибании барабана k=1.04 так как угол огибания равен 90о.
S3=S2+W2-3=1.04S1+(q0+qp2)L2-3`= 1.04S1+(16+9.6)*180*0.035=1.04S1+161
S4=k4S3=1.05(1.04S1+161)=1.092S1+169
S5=k5S4=1.04(1.092S1+169)=1.14S1+176
S6=k6S5=1.05(1.14S1+176)=1.197S1+185
При крайнем положении тележки L6-7 принимаем равным 170 м.
S7=S6+W6-7+ Wзагр = (1.197S1+185)+( (q+q0+qp1)L6-7`)+(с*P*f1(2gh)123.6 )=
=(1.197S1+185)+((120+16+19.2)*170*0.035)+(1.5*1200*2.75*0.56х
х(2*10*1.5)12)3.6) = 1.197S1 + 5326
S8=S7+W7-8=S7+(q+q0)L7-8(`cos+sin)+qp L7-8`=1.197S1 + 5326+
+(120+16)*18*(0.035*0.9+0.2)+19.2*18*0.035= 1.197S1+5904
S9=k9S8=1.03(1.197S1+5904)=1.23S1+ 6081
S10= k10S9=1.03(1.23S1+ 6081)=1.27S1+6264
S11= k11S10=1.04(1.27S1+6264)=1.32S1+6514
S12= k12S11=1.05(1.32S1+6514)=1.4S1+6840
где: Wi-j – сопротивление движению ленты на участке i-j.
Li-j – длина участка i-j
`- коэффициент сопротивления движению ленты зависящий от
типа подшипника смазки уплотнения и др. `= 0.035 (принимаем
для условий с повышенной влажностью и большим количеством
h = 1.5 м - высота падения груза на ленту
с = 1.5 – коэффициент учитывающий сопротивление движению от трения
груза о плужковый сбрасыватель и о ленту от движения ленты в
разгрузочной и разгрузочнойчасти.
Получаем систему из двух уравнений:
Определяем числовые значения натяжения ленты в характерных точках:
S2 = k2S1 = 1.04S1=1643 H
S3= 1.04S1+161=1804 H
S4= 1.092S1+169=1894 H
S5= 1.14S1+176=1977 H
S6= 1.197S1+185=2076 H
S7= 1.197S1 + 5326=7217 H
S8= 1.197S1+5904=7795 H
S9=1.23S1+ 6081=8024 H
S10=1.27S1+6264=8812 H
S11=1.32S1+6514=8600 H
Рис. 3.2. Диаграмма натяжения в ленте
Сопротивление передвижению ленты:
W0=S12-S1=9051-1580=7471Н
Расчётная мощность привода ленточного конвейера:
Np=W0v 102 = 7471*2.75 1000*0.9 = 23 кВт
где =0.9 – КПД привода.
Установочная мощность привода:
N0 = nуNp = 1.1 * 23 = 25 кВт
где nу=1.1 – коэффициент запаса мощности.
По ГОСТ 19523-81 выбираем трёхфазный асинхронный короткозамкнутый двигатель серии 4А: 4A200L6Y3. N = 30 кВт n = 975 обмин.
Выбираем ленту с прокладками из синтетической ткани – капрона с пределом прочности р = 180 кгссм прокладки. Лента воспринимает максимальное натяжение Smax= S12 = 9051 Н запас прочности n=10.
Число прокладок в ленте:
i = Smaxn рB = 9051*10 180*100 = 5
Принимаем ленту с 5-ю основными прокладками. Так как первоначально для расчёта была принята лента с шестью прокладками то пересчитывать конвейер не нужно.
Диаметр приводного барабана:
Dб = а1i = 220*5 = 1100 мм
где а1=220 – эмпирический коэффициент.
По ГОСТ 22644-77 принимаем диаметр приводного барабана Dб=1000 мм.
Диаметр концевого и натяжного барабанов:
D1 = 0.8 Dб = 0.8*880 = 704 мм.
Принимаем D1 = 900 мм
Диаметр отклоняющих барабанов:
D2 = 0.65 Dб = 0.65*880 = 572 мм
Принимаем D2 = 630 мм
Lб= В + аб = 1000 + 150 = 1150 мм
где аб = 150 – эмпирический коэффициент.
Частота вращения приводного барабана:
nб = 60v D = 60*2.75 3.14*1.056 = 49.3 мин-1
где D = Dб + 2Δф = 1 + 2*0.028 = 1.056 м
Δф= 0.028 м – толщина резиновой футеровки.
Передаточное число редуктора привода конвейера:
uр.р. = nnб = 98549.3 = 20
Расчётная мощность редуктора:
Nред = k`pNp = 1.25*25 = 31.25 кВт
где k`p=1.25 – коэффициент условий работы.
По каталогу выбираем редуктор ЦД2-100М-16-I двухступенчатый с межосевым расстоянием между быстроходным и тихоходным валами Ас=1000 мм с передаточным числом up=16; номер схемы сборки I; с циллиндрическим концом выходного вала.
Для обеспечения производительности P=600 тч подключаем электродвигатель ЭД-2 как показанно на схеме рис.3.1.2 При работе одного двигателя второй отключается или работает в генераторном режиме.
Определим характеристики электродвигателя ЭД-2:
n2=n2=14652=732 обмин
N2 N2 = 312 = 15.5 кВт
По ГОСТ 19523-81 выбираем электродвигатель 4А180М8У3 N=15 кВт n=730 обмин.
2. Расчёт тыловой конвейерной линии
Род груза: минеральные удобрения (берутся их показатели требующие максимальной мощности привода).
Производительность: P= 600 тч
Длина трассы: l = 50.8 м
Условия работы: конвейер находится в технологической цепи; загрузка производится с ленточного конвейера; разгрузка производится однобарабанным разгрузочным устройством в бункер загрузочного устройства следующего конвейера; конвейер установлен стационарно; привод расположен в разгрузочной части конвейера; натяжное устройство – грузовое расположено в головной части конвейера.
Рис. 3.2.1 Схема ленточного конвейера
Вес вращающихся частей роликоопор рабочей ветви:
Расстояние между роликоопорами рабочей ветви:
Вес вращающихся частей роликоопор холостой ветви:
Расстояние между роликоопорами холостой ветви: м
где ki – коэффициент увеличения натяжения в ленте при огибании барабана k=1.04 так как угол огибания равен 90о. Далее – по табл.3.1.1
Таблица 3.1.1 Значение коэффициента ki
Угол обхвата лентой отклоняющего барабана о
S3=S2+W2-3=1.04S1+(q0+qp2)L2-3`= 1.04S1+(12.76+9.615)*47*0.035=1.04S1+36
S4=k4S3=1.05(1.04S1+36)=1.092S1+38
S5=k5S4=1.04(1.092S1+38)=1.14S1+39
S6=k6S5=1.05(1.14S5+39)=1.197S1+41
S7=S6+W6-7+Wзагр= (1.197S1+23)+( (q+q0+qp1)L6-7`)+(с*P(v+f1(2gh)-123.6 )=
(1.197S1+41)+((60+12.76+19.23)*51*0.035)+(1.5*600(2.75+
+0.56(2*10*6.6)12)3.6) = 1.197S1+4288
S8=k8S7=1.04(1.197S1+4288)=1.23S1+4460
S9=k9S8=1.05(1.23S1+4460)=1.29S1+4683
для условий с повышенной влажностью и большим количеством пыли).
h = 6.6 м - высота падения груза на ленту
груза о боковые стенки загрузочной воронки и о ленту от движения
ленты в загрузочной части.
S2 = 1.04S1 = 1096 Н
S3 = 1.04S1+36= 1176 Н
S4 = 1.092S1+38= 1322 Н
S5 = 1.14S1+39 = 1546 Н
S6 = 1.197S1+41= 1891 Н
S7 = 1.197S1+4288 = 5549 Н
S8 = 1.29S1+4683 = 6042 Н
Рис. 3.2.2 Диаграмма натяжения в ленте
W0=S9-S1=6043-1054=4989 Н
Np=W0v 1000 = 4989*2.75 1000*0.9 = 15 кВт
N0 = nуNp = 1.1 * 15 = 16 кВт
По ГОСТ 19523-81 выбираем трёхфазный асинхронный короткозамкнутый двигатель серии 4А: 4A160M6Y3. N = 15 кВт n = 985 обмин.
Выбираем ленту с прокладками из синтетической ткани – капрона с пределом прочности р = 180 кгссм прокладки. Лента воспринимает максимальное натяжение Smax= S9 = 3398 кН запас прочности n=10.
i = Smaxn рB = 6043*10 180*80 4
Принимаем ленту с 4-мя основными прокладками. Так как первоначально для расчёта была принята лента с шестью прокладками то пересчитывать конвейер не нужно.
Dб = а1i = 220*4 = 880 мм
D1 = 0.8 Dб = 0.8*880 = 700 мм.
Принимаем D1 = 800 мм
D2 = 0.65 Dб = 0.65*880 = 570 мм
Lб= В + аб = 800 + 150 = 950 мм
nб = 60v D = 60*2.75 3.14*0.865 = 61.4 мин-1
где D = Dб + 2Δф = 0.8 + 2*0.028 = 0.856 м
uр.р. = nnб = 98561.4 = 16
Nред = k`pNp = 1.25*15 = 19 кВт
Использование редуктора ЦД2-100М со схемой сборки III даёт возможность расположить электродвигатель по одну а редутор по другую сторону конвейера что уменьшит габариты приводной станции (Рис 3.1.3.)
4.3 Расчёт конвейерной линии LKs3.
Производительность: P=600000 кгч – 1200000 кгч
Длина трассы: Lk=185 m
Условия работы: конвейер находится в технологической цепи; загрузка производится с ленточного конвейера; разгрузка производится однобарабанным разгрузочным устройством в бункер загрузочного устройства следующего конвейера; конвейер установлен стационарно; привод расположен в разгрузочной части конвейера; натяжное устройство – грузовое расположено в головной части конвейера. Загрузка может производиться только из одного бункера склада.
Рис. 3.4.6 Схема ленточного конвейера
Расчёт ведём для максимальной производительности конвейера:
Р=1200 тч производительность Р=600 тч обеспечим уменьшением скорости конвейера.
где ki – коэффициент увеличения натяжения в ленте при огибании барабана k=1.04 так как угол огибания равен 90о. Далее – по табл.3.4.1
S3=S2+W2-3=1.04S1+(q0+qp2)L2-3`= 1.04S1+(15.95+9.615)*170*0.035=1.04S1+152
S4=k4S3=1.05(1.04S1+152)=1.092S1+159
S5=k5S4=1.04(1.092S1+159)=1.14S1+166
S6=k6S5=1.05(1.14S5+166)=1.197S1+174
S7=S6+W6-7+Wзагр=(1.197S1+174)+((q+q0+qp1)L6-7`)+(с*P(v+f1(2gh)123.6 )=
(1.197S1+174)+((121+159.5+19.23)*180*0.035)+(1.5*1200(2.75+
+0.56(2*10*1)12)3.6) = 1.197S1+3785
S8=k8S7=1.04(1.197S1+3785)=1.23S1+3936
S9=k9S8=1.05(1.23S1+3936)=1.29S1+4133
S3= 1.04S1+152 = 1113 Н
S4= 1.092S1+159 = 1177 Н
S5= 1.14S1+166 = 1227 Н
S6= 1.197S1+174 = 1288 Н
S7= 1.197S1+ 3785 = 4899 Н
S8= 1.23S1+3936 = 5081 Н
Рис. 3.4.7. Диаграмма натяжения в ленте
W0=S9-S1=5334 -931=4403 Н
Np=W0v 1000 = 4403*2.75 1000*0.9 = 14 кВт
N0 = nуNp = 1.1 * 14 = 15 кВт
По ГОСТ 19523-81 выбираем трёхфазный асинхронный короткозамкнутый двигатель серии 4А: 4A160S4Y3. N = 15 кВт n = 1465 обмин.
Выбираем ленту с прокладками из синтетической ткани – капрона с пределом прочности р = 180 кгссм прокладки. Лента воспринимает максимальное натяжение Smax= S9 = 5334 кН запас прочности n=10.
i = Smaxn рB = 5334*10 180*80 = 3.7
D1 = 0.8 Dб = 0.8*880 = 880 мм.
D2 = 0.65 Dб = 0.65*880 = 715 мм
uр.р. = nnб = 146561.4 = 24
По каталогу выбираем редуктор Ц2-400М-25-III двухступенчатый с межосевым расстоянием между быстроходным и тихоходным валами Ас=1000 мм с передаточным числом up=25; номер схемы сборки I; с циллиндрическим концом выходного вала.
Для обеспечения производительности P=600 тч подключаем электродвигатель ЭД-2 как показанно на схеме рис.3.4.8 При работе одного двигателя второй отключается или работает в генераторном режиме.
1.5 Расчёт конвейерной линии LKs4.
Длина трассы (в проекции на горизонталь): Lk=30 m
Условия работы: конвейер находится в технологической цепи; загрузка производится с ленточного конвейера; разгрузка производится однобарабанным разгрузочным устройством в бункер загрузочного устройства следующего конвейера; конвейер установлен стационарно; привод расположен в загрузочной части конвейера; натяжное устройство – грузовое расположено в загрузочной части конвейера.
Рис. 3.1.5.1 Схема ленточного конвейера LKs4
Так как один из участков конвейера крутонаклонный (30) то по ГОСТ 20-76 принимаем конвейерную ленту с выступом тип ленты 2М класс прочности резины наружной обкладки - В предварительно лента имеет 6 прокладок из синтетической ткани номинальная прочность прокладки 400 Нмм толщина тканевых прокладок резинотканевых лент пт=2.0 мм толщина обкладок рабочих поверхностей р=4.5 мм нерабочих – н=2 мм высота выступов h=7 мм ширина выступов b= 600 мм угол образуемый выступом и продольной осью ленты α=30.
B= Р = 1200 = 1.3 м
В данном уравнении два неизвестных члена S1 и S13. Для составления второго уравнения обходим тяговый контур от точки 1 до точки 13 выражая натяжение во всех точках через натяжение в точке 1 – S1.
Для последующего расчёта необходимы погонные нагрузки.
Нагрузки от транспортируемого груза (для прямолинейного участка):
q0=1.1*[ B(пт*z + р + н) + 2hbsinα] = 44.8 (кгм)
Теперь определим нагрузки от транспортируемого груза и роликоопор на наклонном участке конвейера:
Нагрузки от транспортируемого груза на наклонном участке:
qн=B2[0.15ktg(0.35*f0)+0.05]ypkг=123 кгм
где: k=0.86 – коэффициент учитывающий уменьшение площади
поперечного сечения груза на наклонном участке.
kг=0.95 – геометрический коэффициент.
S3=1.05S2=1.05(1.04S1)=1.092S1
S4=S3+W3-4+Wзагр =1.092S1+(q+q0+qp)L3-4г`+(с*P(v+f1(2gh)123.6 )= 1.092S1+(121+44.8+19.2)*6*0.035+(1.5*1200(2.75+0.56(2*10*1)12)3.6)= =1.092S1+6241
S5=S4+ W4-5=1.092S1+6241+((qн+q0+qp)L4-5`+qнH)=1.092S1+6241+
+((123+44.8+19.23)*27*0.035+123*14)=1.092S1+8139
S6=k6S5=1.05(1.092S1+8139)=1.15S1+8546
S7=1.03(1.15S1+8546)=1.18S1+8802
S8=S7+W7-8=1.18S1+8802+ (q0+qp)L4-5`=
=1.18S1+8802+(44.8+19.23)*27*0.035=1.18S1+8863
S9=k9S8=1.04(1.18S1+8863)=1.23S1+9217
S10=k10S9=1.05(1.23S1+9217)=1.29S1+9678
S11=k11S10=1.04(1.29S1+9678)=1.34S1+10065
S12=k12S11=1.04(1.34S1+10065)=1.4S1+10468
S13=k13S12=1.05(1.4S1+10468)=1.47S1+10991
S4=1.092S1+6241=9058 H
S5= 1.092S1+8139=10956 H
S6= 1.15S1+8546=11513 H
S7=1.18S1+8802=11846 H
S8= 1.18S1+8863=11907 H
S9= 1.23S1+9217=12390 H
S10= 1.29S1+9678=13006 H
S11= 1.34S1+10065=13522 H
S12= 1.4S1+10468=14080 H
Рис. 3.1.5.2. Диаграмма натяжения в ленте
W0=S13-S1=14783 -2580=12203 Н
Np=W0v 1000 = 12203*2.75 1000*0.9 = 37 кВт
N0 = nуNp = 1.1 * 37 = 41 кВт
По ГОСТ 19523-81 выбираем трёхфазный асинхронный короткозамкнутый двигатель серии 4А: 4A200M4Y3. N = 37 кВт n = 1470 обмин.
i = Smaxn рB = 14783*10 400*140 = 2.7 3
Принимаем ленту с 3-мя основными прокладками. Так как первоначально для расчёта была принята лента с шестью прокладками то пересчитывать конвейер не нужно.
Dб = а1i = 220*3 = 660 мм
По ГОСТ 22644-77 принимаем диаметр приводного барабана Dб=630 мм.
D1 = 0.8 Dб = 0.8*660 = 530 мм.
Принимаем D1 = 500 мм
D2 = 0.65 Dб = 0.65*660 = 430 мм
Принимаем D2 = 400 мм
Lб= В + аб = 1400 + 150 = 1550 мм
nб = 60v D = 60*2.75 3.14*1.465 = 35.8 мин-1
где D = Dб + 2Δф = 1.4 + 2*0.028 = 1.456 м
uр.р. = nnб = 147035.8 = 41
Nред = k`pNp = 1.25*37 = 46 кВт
По каталогу выбираем редуктор ЦД2-500-16-I двухступенчатый с межосевым расстоянием между быстроходным и тихоходным валами Ас=1000 мм с передаточным числом up=40; номер схемы сборки I; с циллиндрическим концом выходного вала.
Для обеспечения производительности P=600 тч подключаем электродвигатель ЭД-2 как показанно на схеме рис.3.1.5.3 При работе одного двигателя второй отключается или работает в генераторном режиме.
n2=n2=14702=735 обмин
По ГОСТ 19523-81 выбираем электродвигатель 4 N=37 kВт n=735 обмин
Проверка привода LKs1 на пуск и торможение
)Определение сопротивления движению ленты в период пуска (после длительной остановки).
Коэффициент сопротивления движению ленты в пусковой момент:
п`=`kп=0.035*1.5=0.0525
где kп=1.5 – коэффициент увеличения статических сопротивлений при пуске.
Натяжение в точках контура возрастёт из-за увеличения `:
S3=S2+W2-3=1.04S1+(q0+qp2)L2-3`= 1.04S1+(12.76+9.615)*25*0.0525=1.04S1+29
S4=k4S3=1.05(1.04S1+29)=1.092S1+31
S5=k5S4=1.04(1.092S1+31)=1.14S1+32
S6=k6S5=1.05(1.14S5+32)=1.197S1+34
S7=S6+W6-7+Wзагр= (1.197S1+34)+( (q+q0+qp1)L6-7`)+(с*P(v+f1(2gh)-123.6 )=
(1.197S1+34)+((60+12.76+19.23)*29*0.0525)+(1.5*600(2.75+
+0.56(2*10*6.6)12)3.6) = 1.197S1+2470
S8=k8S7=1.04(1.197S1+2470)=1.23S1+2569
S9=k9S8=1.05(1.23S1+2569)=1.29S1+2698
S3= 1.04S1+29= 661 Н
S4= 1.092S1+31= 695 Н
S5= 1.14S1+32= 725 Н
S6= 1.197S1+34=762 Н
S7= 1.197S1+2470 = 3198 Н
S8= 1.23S1+2569=3317 Н
W0П=S9-S1=3482-608=2874 Н
Статический момент при пуске приведенный к валу двигателя:
Мст.п= W0ПD(2upп)= 2874*0.856(2*16*0.865)=90 Н*м
где: п – КПД в период пуска
п= 1- (1-м)kпст=1-(1-0.85)*1.5*0.6=0.865
ст=0.55 0.6 – коэффициент возможного уменьшения сопротивления движению ленты.
Момент инерции всех движущихся масс конвейера приведенный к валу двигателя:
Jпр=(Jp+Jм)+mkR2up2п= 1.15(0.182+0.037)+1670*0.4282162*0.865=2.24
где: Jp=0.182 кг*м2 – момент инерции ротора
Jм=0.037 кг*м2 - момент инерции муфты
=1.15 – коэффициент учитывающий момент инерции деталей
привода вращающихся медленнее чем вал двигателя.
mк – приведенная масса движущихся частей конвейера и груза на нём.
mк=ky[(q+2q0)L+kcGp]= 0.5[(60+2*12.76)*29+0.8*1076]=1670 кг
где: ky=0.5 – коэффициент учитывающий упругое удлинение ленты в
результате чего не все массы конвейера приходят в движение
kс=0.8 – коэффициент учитывающий что окружная скорость части масс
Gp- масса вращающихся частей роликов и барабанов конвейера.
Gp=(qp1+ qp2)L + ΣGб=(19.23+9.615)29+240 = 1076 кг
Средний пусковой момент двигателя:
Мп.ср=(Мп.мах + Мп.min)2 = (2.0Мн + 1.1Мн)2=1.55 Мн=
=1.55*974*16985=24 Нм
Время пуска конвейера:
tп= Jпр(Мп.ср - Мст.п)= 2.24*105.8(90-24)= 3.6 (с)
Рассчитываемый конвейер предназначенный для работы в транспортной цепи должен иметь путь движения конвейерной ленты не более 2.5 м (во избежание засыпки узла перегрузки). С целью уменьшения пути выбега ленты используем принудительное торможение конвейера установив для этого тормоз на быстроходном валу привода.
Принимая изменение скорости ленты от v=2.75 мс до v0=0 линейным получаем необходимое время торможения:
tт= 2lт (v+v0)= 2*2.52.75 = 1.82 (c)
Статический момент на валу двигателя при торможении:
Мст.т= W0Dм2*up= 2805*0.856*0.852*16=63 Нм
Момент инерции всех движущихся масс конвейера приведенный к валу двигателя (при торможении):
Jпр.т=*Jр.м. + mкR2мup2 = 1.15*0.219+ 1670*0.4282*0.85162=1.26 НМс2
Время торможения конвейера:
tт= Jпр.т(Мт + Мст.т) отсюда:
Необходимый тормозной момент:
Мт= Jпр.тtт - Мст.т = 1.26*105.81.82 – 63 = 10.3 Нм
Выбираем колодочный электромагнитный тормоз ТКТ-100 с диаметром тормозного шкива 100 мм и наибольшим тормозным моментом при ПВ = 100% Мт = 11 Нм
Техническя эксплуатация и ремонт оборудования перегрузочного комплекса.
1 Работа и управление машинами специализированных конвейерных комплексов для навалочных грузов (СККН).
1.1 Все перегрузочные машины на рельсовом ходу по окончании работы должны устанавливаться на противоугонные устройства а их рабочие органы - в нерабочее положение в соответствии с требованиями заводской (фирменной) документации обеспечивающее возможность осмотра безопасной стоянки и работы других машин. При отсутствии соответствующих требований в заводской (фирменной) документации необходимо установить:
- стрелу реклаймера - в горизонтальной плоскости под углом 15-20° от оси складского конвейера а роторный захват опереть не оставляя его на весу;
- стрелу стакера - в горизонтальной плоскости в опущенном положении под углом 15-20° от оси складского конвейера;
- стрелу (консоль) судовой погрузочной машины - в максимально поднятом (втянутом) положении. При этом передвижная тележка телескопической трубы должна отгоняться в крайнее заднее положение а телескопическая труба - полностью втягиваться.
1.2 Система централизации и блокировки (СЦБ) на участке разгрузки вагонов должна эксплуатироваться в соответствии с требованиями заводской (фирменной) документации. При отсутствии таких требований следует руководствоваться положениями Инструкции по техническому обслуживанию устройств сигнализации централизации и блокировки (М.: Транспорт 1989).
1.3 Механизированные и автоматизированные устройства на путях откатки а также железнодорожные пути должны эксплуатироваться в соответствии с требованиями заводской (фирменной) документации. При отсутствии таких требований следует руководствоваться положениями Инструкции по техническому обслуживанию устройств механизированных и автоматизированных сортировочных горок (М.: Транспорт 1991) Инструкции по техническому содержанию клещевидно-весовых вагонных замедлителей типа КВ-62М (М.: Транспорт 1975) Инструкции по текущему содержанию железнодорожного пути (М.: Транспорт 1974).
1.4 Размораживающие устройства должны эксплуатироваться в соответствии с требованиями Типовой инструкции по обслуживанию конвективных и комбинированных размораживающих устройств (тепляков) на тепловых электростанциях (М.: Союзтехэнерго 1981).
1.5 Оборудование для заливки масла в буксы в пунктах технического осмотра железнодорожных вагонов должно эксплуатироваться в соответствии с требованиями заводской (фирменной) документации а также Инструкции по ремонту и обслуживанию букс вагонов с подшипниками скольжения
(М.:Транспорт 1977) Правил технической эксплуатации металлических резервуаров и инструкции по их ремонту (М.:Недра 1971).
1.6 Кусковатость смерзшегося и слежавшегося груза в случае необходимости его перегрузки на СККН должна быть в пределах допускаемых требованиями заводской (фирменной) документации на перегрузочные машины. При несоблюдении этого условия работа машин должна быть прекращена.
2 Неисправности при которых работа перегрузочных машин СККН должна быть прекращена
2.1 Работа конвейеров не допускается при:
а) истекшем сроке технического освидетельствования;
б) возникновении неисправностей аналогичных указанным в 9.3.1;
в) продольном порыве ленты длиной более 200 мм при пробоине размером более 50х50 мм;
г) пробуксовке ленты на приводных барабанах;
д) неисправности натяжных устройств (например заедании балласта сходе с рельсов натяжной тележки износе канатов цепей выходящем за пределы допускаемых норм сходе канатов с блоков);
е) неисправности роликовых опор грузовой и холостой ветвей;
ж) неисправности тормозов и устройств аварийной остановки;
и) неисправности устройств по очистке ленты;
к) неисправности громкоговорящей связи и сигнализации о запуске конвейеров;
л) неисправности реле скорости датчиков завала фотореле и других элементов автоматизации и контроля.
2.2 Работа стакера реклаймера кратцер-крана машины МВС и судовой погрузочной машины не допускается при:
а) возникновении неисправностей аналогичных указанным в 10.2.1;
б) неисправности клапанов предельного давления измерительных приборов гидросистем и гидропривода роторного колеса реклаймера;
д) неисправности звуковой сигнализации;
е) сломанных зубьях ковшей роторного колеса реклаймера деформированных пластинах и скребках кратцер-крана витков спиралей и режущих зубцов шнеков;
ж) неисправности устройства выравнивания хода кратцер-крана;
и) неисправности привода выдвижения телескопической трубы судовой погрузочной машины.
2.3 Работа вагоноопрокидывателя электротележки-толкатепя и маневрового устройства не допускается при:
а) возникновении неисправностей аналогичных указанным в 9.3.1;
б) повреждении стенок разгружаемых вагонов неисправностях их ходовой
в) неисправностях приводной системы зажимов;
г) заедании платформы при опрокидывании;
д) неисправности световой и звуковой сигнализации;
е) других неисправностях указанных в заводской (фирменной) документации угрожающих безаварийной работе вагоноопрокидывателя электротележки-толкателя маневрового устройства и безопасной работе людей.
2.4 Работа маршрутов ' не допускается при:
а) неисправностях любой из перегрузочных машин составляющих маршрут согласно 5.2.1; 5.2.2; 5.2.3;
б) невозможности осуществить последовательный запуск или остановку маршрута;
в) неисправностях системы централизованного управления машинами в ЦПУ;
г) неисправностях системы оповещения и связи с машинами;
д) других неисправностях указанных в заводской (фирменной) документации.
3 Техническое обслуживание перегрузочных машин СККН
3.1 Периодическое техническое обслуживание перегрузочных машин должно состоять из ТО-1 и ТО-2. Состав и периодичность ТО-1 приведены 5.6.2.2
3.2 В состав ТО-2 должны входить следующие работы:
а) проверка технического состояния составных частей перегрузочной машины в объеме проверок при ТО-1 и опробование их в работе;
б) замена быстроизнашивающихся деталей: отдельных роликов устройств по очистке лент конвейеров футеровочных листов пересыпных устройств
других деталей и оборудования машин.
3.3 Примерный состав проверочных работ при периодическом техническом обслуживании составных частей перегрузочных машин приведен в приложении и включает только работы специфичные для перегрузочных
машин СККН. Состав проверочных работ при периодическом техническом обслуживании этих машин должен уточняться портами с учетом требовании заводской (фирменной) документации.
3.4 Техническое состояние отдельных элементов перегрузочных машин должно определяться в соответствии с требованиями заводской (фирменной) документации а при отсутствии указанных требований допускается использовать соответствующие нормы дефектации.
3.5 Для сокращения сроков простоя перегрузочных машин следует выводить на техническое обслуживание группы технологически связанных перегрузочных машин.
3.6 Периодичность и продолжительность выполнения ТО-2 маршрутов такие же как для кранов и перегружателей в соответствии с 5.2.1.
4 Технический надзор и техническое освидетельствование
4.1 Технический надзор за содержанием машин СККИ должен производиться в соответствии с указаниями раздела 6.
4.2 Дополнительно к перечисленным в 6.1.4 ответственными по надзору в порту должны быть назначены:
- за безопасной эксплуатацией рельсовых путей сбрасывающих тележек пути которых установлены на раме металлоконструкции конвейера - инженерно-технические работники отдела механизации;
- за исправностью и безопасной эксплуатацией телефонной и громкоговорящей связи системы промышленного телевидения - инженерно-технические работники участка связи порта.
4.3 Технический надзор за исправностью и безопасной эксплуатацией систем вентиляции и аспирации должен осуществляться в соответствии с требованиями ГОСТ 12.4.021.
4.4 При укладке и содержании рельсового пути передвижных конвейеров и сбрасывающих тележек на конвейерах должны выдерживаться допуски указанные в таблице 5.1.
4.5 Виды технических освидетельствовании должны соответствовать указаниям 6.4.3.
4.6 При техническом освидетельствовании перегрузочные машины подвергаются осмотру опробованию вхолостую и под нагрузкой.
4.7 При опробовании перегрузочной машины вхолостую необходимо проверить работу:
- каждого механизма машины в отдельности путем раздельного включения соответствующих приводов;
- тормозных устройств всех механизмов;
- всех механизмов устройств и блокировок обеспечивающих безопасную работу машины: конечных выключателей всех механизмов сигнальной аппаратуры аварийного выключателя и аварийных кнопок и других.
4.8 При опробовании вхолостую перегрузочной машины на рельсовом ходу должны быть выполнены следующие рабочие циклы на минимальной и максимальной скоростях:
- подъем и опускание стрелы на всю высоту подъема (выдвижение консоли на всю длину) до срабатывания конечных выключателей;
- передвижение машины на расстояние не менее 50 м в оба конца;
- вращение поворотной части на максимально возможный угол в обе стороны;
-раскрытие и закрытие противоугонных устройств.
Таблица 5.1 Допуски на укладку и при эксплуатации рельсовых путей передвижных конвейеров и сбрасывающих тележек мм
Отклонение от прямолинейности на 1 м длины рельсового пути
То же на 25 м длины рельсового пути
Отклонение от номинальной ширины колеи
Разность отметок головок рельсов в одном поперечном сечении
Зазор в стыках рельсов
Взаимное смещение торцов стыкуемых рельсов в плане и по высоте
4.9 При опробовании вхолостую отдельных механизмов перегрузочной машины их технические характеристики должны соответствовать требованиям заводской (фирменной) документации. Кроме индивидуального опробования отдельных механизмов необходимо произвести опробование перегрузочной машины вхолостую при совмещении движений механизмов оговоренных в заводской (фирменной) документации. При этом должна проверяться блокировка механизмов.
4.10 По окончании опробования вхолостую перегрузочная машина подвергается опробованию в составе маршрута как вхолостую так и под нагрузкой. Опробование перегрузочной машины под нагрузкой следует производить при работе с максимальной производительностью.
4.11 Порядок опробования в работе а также состав регулировочных работ должны уточняться с учетом указаний заводской (фирменной) документации.
5 Особенности технического освидетельствования конвейера
5.1 При техническом освидетельствовании конвейера должны проверяться очистные устройства бункеры с нагревателями и вибраторами пересыпные станции питатели улавливатели посторонних предметов.
5.2 Опробование конвейера вхолостую и под нагрузкой необходимо производить при минимальной и максимальной скоростях движения ленты.
5.3 При опробовании конвейера вхолостую и под нагрузкой необходимо проверить выдержку времени включения каждого последующего конвейера.
Выдержка времени необходимая для разгона тягового органа предыдущего конвейера должна соответствовать данным приведенным в заводской (фирменной) документации на СККН.
5.4 При опробовании вхолостую и под нагрузкой ленточного конвейера проверяются установка роликоопор положение ленты на барабанах и роликах в движении ход натяжной станции работа тормоза и рельсовых захватов сбрасывающей тележки работа блокировки реле скорости датчиков завала сигнализации при запуске. Величина схода ленты в поперечном направлении запас хода барабана натяжной станции должны соответствовать указаниям заводской (фирменной) технической документации. При отсутствии таких данных величина схода ленты в сторону не должна превышать 40 мм при условии отсутствия касания металлоконструкции а запас хода барабана в сторону груза или натяжного винта должен быть не менее 23 длины общего перемещения барабана.
5.5 При опробовании вхолостую и под нагрузкой скребкового конвейера кратцер-крана пластины цепей не должны касаться боковых поверхностей зубьев звездочек а втулки должны скользить по направляющим без зазора.
5.6 Опробование вхолостую и под нагрузкой ленточных и пластинчатых питателей следует производить по аналогии с соответствующими конвейерами. При опробовании под нагрузкой вибрационного питателя он должен обеспечивать заданную производительность на соответствующих режимах работы.
5.7 Время опробования вхолостую и под нагрузкой (в составе маршрута) конвейеров и питателей приведено в табл. 5.2.
Таблица 5.2 Время опробывания вхолостую и под нагрузкой конвейеров питателей и других устройств часы
Тип перегрузочной машины
Конвейер с зачистным устройством пересыпной станцией бункером нагревателем вибратором
Питатель ленточный пластинчатый лопастной
6 ТЕХНИЧЕСКОЕ ОБСЛУЖИВАНИЕ И ОБЯЗАННОСТИ ПО СОДЕРЖАНИЮ ПОДЪЕМНО-ТРАНСПОРТНОГО ОБОРУДОВАНИЯ В ИСПРАВНОМ СОСТОЯНИИ
6.1.1 Техническое обслуживание подъемно-транспортного оборудования подразделяется на:
- техническое обслуживание при использовании
- техническое обслуживание при хранении
- техническое обслуживание при транспортировании.
6.1.2 Состав периодичность порядок выполнения и меры безопасности при проведении технического обслуживания подъемно-транспортного оборудования должны соответствовать указаниям приведенным в инструкции по эксплуатация этого оборудования или в другой технической документации завода-изготовителя. При отсутствии таких указаний они должны быть разработаны:
- для перегрузочного оборудования подконтрольного Госгортехнадзору - специализированной организацией в соответствии с Правилами Госгортехнадзора.
- для оборудования не подконтрольного Госгортехнадзору - портом или по его поручению другой организацией.
6.2 Техническое обслуживание при использовании подъемно- транспортного оборудования
6.2.1 Техническое обслуживание при использовании машин состоит из:
) ТО-1 которое включает в себя все виды обслуживания с периодичностью менее месяца а именно: ежесменное ежесуточное еженедельное и т.п. Эти виды обслуживания проводятся во время приема и сдачи смены в период отсутствия грузовых работ а также с выводом машины из эксплуатации но не более чем на 8 ч (одна дневная смена);
- по кранам и перегружателям всех типов включая зерновые с периодичностью 1 раз в месяц и длительностью не более 2 суток а 1 раз в 3 месяца (при необходимости) длительностью до 40 ч (пять дневных смен);
- по машинам внутрипортовой механизации - через 150-200 ч работы машины но не реже чем через месяц если в заводских инструкциях не оговорены иные сроки. Длительность ТО-2 этих машин не должна превышать:
для машин с двигателем внутреннего сгорания и грузоподъемностью до 10 т - 16 ч (две дневные смены) грузоподъемностью 10 т и более - 24ч (три дневные смены);
для машин с электроприводом - 8 ч (одна дневная смена).
6.2.2 В состав ТО-1 входят следующие работы:
- проверка перегрузочной машины и ее механизмов
- уборочно-моечные работы
- опробование механизмов агрегатов и систем в действии
- проверка в действии блокировочных устройств и приборов безопасности
- регулировочные работы
- снабжение топливом смазкой водой
- устранение повреждений.
Ежесменное техническое обслуживание выполняют докеры-механизаторы управляющие машиной при приеме и сдаче смены
Ежесуточное еженедельное и другие виды обслуживания входящие в ТО-1 выполняют рабочие по техническому обслуживанию и ремонту.
Перечень работ и проверок выполняемых при ТО-1 на конкретных машинах устанавливает порт на основании заводских инструкций по эксплуатации машины. Докерам- механизаторам управляющим перегрузочными машинами и рабочим по техническому обслуживанию и ремонту запрещается самостоятельно без указания группового механика (электромеханика) или сменного механика разбирать и регулировать:
- аппаратуру гидравлического и пневматического управления;
- предохранительные приборы и приборы безопасности;
- топливные насосы регуляторы и форсунки дизелей;
- защитные фрикционы механизмов поворота;
- весовые устройства ограничители грузоподъемности и указатели вылета стрелы;
- приборы автоматизации электронного оборудования сигнализации и речевой связи;
- тормоза с автоматическим устройством для компенсации износа фрикционных обкладок тормоза механизма подъема контейнерных кранов и перегружателей;
- запорное устройство подъемной консоли перегружателя;
- устройства для подогрева и охлаждения рабочей гидравлической жидкости.
Приведенный перечень таких работ дополняется портом в зависимости от конструктивных особенностей машин.
Категорически запрещается производить регулирование тормоза механизма подъема при поднятом грузе или грейфере (грузоподъемном электромагните) а также устанавливать различные приспособления для растормаживания тормоза вручную.
При ежесуточном техническом обслуживании производится контроль качества выполнения и оформления ежесменного технического обслуживания.
Ежесуточное еженедельное и другие виды обслуживания машин входящие в ТО-1 проводятся в течение времени отведенного для выполнения ежесменного обслуживания а также в обеденные и межсменные перерывы и в периоды отсутствия грузовых работ.
О состоянии перегрузочных машин и выполненных работах рабочие делают запись в вахтенном журнале машины.
Организация ежесменного обслуживания и контроль за его выполнением являются обязанностью сменного механика остальных видов обслуживания -
инженерно-технических работников ответственных за содержание перегрузочных машин в исправном состоянии.
6.2.3 ТО-2 является основным видом технического обслуживания и включает в себя следующие работы состав которых уточняется портом с учетом конструкции машин в соответствии с 5.1.2:
- проверку технического состояния машины;
- при необходимости замену быстроизнашивающихся деталей: резьбовых соединений канатов тормозных обкладок пальцев и упругих втулок муфт манжет и уплотнений гидросистемы контактов гибких соединений и пружин командоаппаратов контакторов и реле щеток и щеткодержателей электродвигателей и кольцевых токоприемников питающего шлангового кабеля других деталей и оборудования;
- восстановление надежности всех соединений элементов металлоконструкций деталей механизмов электрического гидравлического и пневматического оборудования а также устранение неисправностей. В случае применения сварки при восстановлении несущих металлоконструкций кранов работа должна быть выполнена в соответствии с Правилами Госгортехнадэора по кранам;
- регулирование устройств механизмов схем и систем;
- очистку механизмов и оборудования от пыли грязи и отработавшей
-смазывание узлов механизмов.
ТО-2 проводят по квартальным графикам которые утверждает заместитель начальника района по механизации. Отклонение от сроков выполнения ТО-2 предусмотренных графиком допускается в исключительных случаях по разрешению руководителя утвердившего график но не более чем на 5 дней.
Перенос срока должен быть оформлен записью разрешения в журнале группового механика.
Ответственность за проведение ТО-2 возлагается на инженерно-технического работника ответственного за содержание машины в исправном состоянии. Запись о постановке перегрузочной машины на ТО-2 а также о пуске ее в работу после технического обслуживания производит указанное лицо в вахтенном журнале машины.
О выполненных работах ТО-2 должна быть сделана запись в журнале группового механика (электромеханика). Контроль за выполнением графика осуществляет инженерно-технический работник по надзору за безопасной эксплуатацией перегрузочных машин.
6.2.4 Для обеспечения бесперебойной работы перегрузочных машин на каждом грузовом районе должен быть предусмотрен дежурный персонал для технического обслуживания и ремонта перегрузочных машин подчиненный сменному механику.
6.2.5 Перегрузочные машины должны быть закреплены:
- за рабочими по техническому обслуживанию и ремонту - для обеспечения технического обслуживания с периодичностью 1 сутки и более а также для выполнения ремонтных работ. Закрепление оформляется распоряжением заместителя начальника района по механизации;
- за рабочими комплексных бригад (докерами-механизаторами)-для обеспечения управления и ежесменного обслуживания машины. Закрепление оформляется распоряжением начальника района.
Докеры механизаторы в период работы на перегрузочных машинах подчиняются инженерно-техинческим работникам механизации в том числе и ответственному за содержание перегрузочных машин в исправном состоянии и выполняют все их указания в части технической эксплуатации машин. Докеры-механизаторы управляющие перегрузочными машинами должны участвовать в работах по техническому обслуживанию и ремонту перегрузочных машин и производить замену грузозахватных органов с учетом 5.7.2.
Бригадир комплексной бригады обязан обеспечить постоянное участие рабочих в техническом обслуживании перегрузочных машин в соответствии с графиком ТО-2 и с учетом закрепления машин за рабочими комплексных бригад.
Выдачу задания докерам-механизаторам и рабочим по техническому обслуживанию и ремонту на выполнение работ по техническому обслуживанию производит групповой или сменный механик после инструктажа по технике безопасности.
6.2.6 Докеры-механизаторы управляющие перегрузочными машинами обязаны при приеме смены проверять техническое состояние машины. Проверка должна осуществляться в соответствии с указаниями приведенными в производственной инструкции докера-механизатора или в инструкции по охране труда при работе на конкретной машине. При обнаружении неисправности при приемке или во время работы машины докер-механизатор управляющий машиной должен соответственно не начинать либо прекратить работу и доложить об этом сменному механику. Машина может быть использована для работы только после устранения неисправностей и получения разрешения сменного механика которое должно быть записано им в вахтенном журнале машины а если на машине журнал не предусмотрен - в вахтенном журнале сменного механика.
После окончания работы докер-механизатор управляющий машиной обязан:
- произвести очистку машины и при необходимости заправить ее топливом водой и маслом;
- сделать запись в вахтенном журнале машины если он предусмотрен в соответствии с формой журнала;
- поставить машину в отведенное для стоянки место а краны и перегружатели установить на противоугонные захваты;
- сдать машину (ключи) сменному механику.
6.2.7 Администрация порта обязана предоставить докерам-механизаторам управляющим перегрузочными машинами 20 мин для приемки-сдачи перегрузочной машины и выполнения ежесменных работ
6.2.8 Передача в период рабочей смены управления перегрузочной машиной одним докером-механизатором другому без разрешения сменного механика и записи в вахтенном журнале сменного механика запрещается.
6.2.9 При осмотре и техническом обслуживании перегрузочной машины с электроприводом должны быть выполнены мероприятия обеспечивающие безопасность работ в соответствии с 13.2.1.3.
6.2.10 На каждом кране перегружателе и машине специализированного перегрузочного комплекса должны быть:
- вахтенный журнал перегрузочной машины;
- комплект инструментов приспособлений и инвентаря а также расходные материалы необходимые для ежесменного и ежесуточного технического обслуживания.
На кранах и перегружателях а также в гаражах и на постах технического обслуживания должны быть вывешены карты смазки механизмов машин и необходимые данные для регулировочных работ.
6.2.11 Выбор контроль качества и учет расхода горюче-смазочных материалов порт должен осуществлять в соответствии с указаниями заводской (фирменной) документации и картой смазки составленной с учетом рекомендаций РД 31.44.08-93.
6.2.12 Выбор стальных канатов для перегрузочных машин и техническое обслуживание стальных канатов следует производить с учетом указаний Правил Госгортехнадзора по кранам и рекомендаций приведенных в приложении В к настоящим ПТЭ.
6.3 Техническое обслуживание при хранении подъемно-транспортного оборудования
6.3.1 Перегрузочные машины сменные грузозахватные органы съемные грузозахватные приспособления и средства укрупнения в периоды когда они не эксплуатируются подлежат хранению. В зависимости от продолжительности такого периода они могут находиться на оперативном или длительном хранении.
Оперативному хранению подлежат перегрузочные машины сменные грузозахватные органы съемные грузозахватные приспособления и средства укрупнения предназначенные для выполнения сменно-суточного плана а в случаях когда они не потребуются более месяца- длительному хранению.
Постановка на длительное хранение перегрузочных машин и сменных грузозахватных органов при сроке хранения менее 3 месяцев производится распоряжением начальника грузового района.
Постановка портальных кранов перегружателей всех типов и машин специализированных конвейерных комплексов для навалочных грузов на хранение более чем на 3 месяца производится приказом начальника порта. Постановка на длительное хранение съемных грузозахватных приспособлений и средств укрупнения производится распоряжением руководителя подразделения-владельца.
6.3.2 При оперативном хранении должны быть обеспечены условия для счета выдачи приема и технического обслуживания оборудования для чего:
- электро- и автопогрузчики и их сменные грузозахватные органы должны храниться в помещениях;
- портальные контейнерные автопогрузчики и портовые тягачи должны храниться на специальных площадках а обслуживаться в закрытых боксах оснащенных всеми необходимыми приспособлениями и средствами механизации для производства работ по техническому обслуживанию;
- однотипные низкорамные полуприцепы без выносного опорно-сцепного устройства могут устанавливаться в несколько ярусов (не более пяти). При этом под колеса полуприцепов должны быть установлены упорные колодки;
- контейнерные и трубные захваты следует хранить на специальных подставках обеспечивающих сохранность замковых устройств при этом отверстия гидросистемы должны быть заглушены;
- машины непрерывного транспорта а также сменные грузозахватные органы грузоподъемных кранов должны храниться на специально предназначенных для этой цели и оборудованных площадках;
- съемные грузозахватные приспособления следует хранить в специальных помещениях и под навесами;
- средства укрупнения должны храниться на грузовых складах.
6.3.3. В целях защиты от коррозии длительное хранение машин внутрипортовой механизации сменных грузозахватных органов с электрическим или гидравлическим приводом съемных грузозахватных приспособлений и средств укрупнения должно осуществляться на складах под навесом или под водонепроницаемыми чехлами в соответствии с указаниями заводских инструкций по эксплуатации и техническому обслуживанию. Перегрузочные машины сменные грузозахватные органы съемные грузозахватные приспособления и средства укрупнения находящиеся на длительном хранении разукомплектовывать категорически запрещается. Ответственность за сохранность перегрузочных машин сменных грузозахватных органов съемных грузозахватных приспособлений и средств укрупнения при длительном и оперативном хранении возлагается на начальника грузового района или руководителя подразделения-владельца оборудования.
6.3.4. Техническое обслуживание перегрузочных машин находящихся на оперативном хранении осуществляется так же как и техническое обслуживание при использовании машин (см. 5.2).
6.3.5 Техническое обслуживание перегрузочных машин при длительном хранении включает в себя работы по обслуживанию при подготовке к хранению в процессе хранения а также работы при подготовке к использованию после хранения. При подготовке перегрузочной машины к длительному хранению необходимо:
- произвести мойку и очистку
- выполнить все работы ТО-2
- устранить неисправности (восстановить герметичность кожухов крышек н дверей оборудования остеклить кабину и т.д.);
-произвести консервацию. Консервацию производят в зависимости от конструктивных особенностей машин требуемых сроков защиты и условий хранения в соответствии с ГОСТ 9.014 и указаниями заводских инструкций по эксплуатации машин.
БЖД. Охрана окружающей среды.
Расчет концентраций загрязняющих веществ в ливневых стоках перегрузочного комплекса.
1. Количество минеральных удобрений осаждающееся на территории причала N 5 составляет 10 гм2 в месяц (письмо проектной фирмы IGP N 2204 от 15.07.96. ).
2. Распределение грузопотоков по видам удобрений:
карбамид (ГОСТ 2081-92) - 60% аммиачная селитра (ГОСТ 2-85) - 30%
нитроаммофоска (ГОСТ 19691-84) - 10%
аммофос (ГОСТ 18918-85)
Влияние на водные объекты
При попадании в поверхностные воды карбамида аммиачной селитры аммофоса и сложных азотно-фосфорно-калийных удобрений ввиду их хорошей растворимости последние поставляют в воду соединения азота (аммоний нитраты) фосфора (фосфаты) калия.
Эти вещества являясь биогенами при высоких концентрациях могут приводить к эвтрофированию водного объекта связанного с интенсивным ростом фитопланктона и водной растительности снижением содержания растворенного кислорода и угнетением водной фауны.
1. Предельно допустимые концентрации (ПДК) N Р и К для морских вод представлены в табл.2.1.
ПДК для морских вод гм3
2. Расход дождевых вод определяется выражением:
где Нмес - слой осадков за месяц мм;
- коэффициент стока = 0.95;
F - площадь водосбора причала N5 га; F = 3.5 га.
Объемы поверхностного стока а также суммарные расчетные концентрации растворенных минеральных удобрений смываемых одним дождем ( за одни сутки) с территории причала по месяцам представлены в табл.2.2. Содержание нормируемых ингредиентов отдельно по видам минеральных удобрений и во всем стоке отражено в табл.2.3. За основу принята максимальная концентрация растворенных минеральных удобрений (234.2 гм3) за май и сентябрь - ноябрь.
ных мин.удобрений за 1 дождь
Максимальное содержание нормируемых ингредиентов в поверхностном стоке
Процентное содержание в стоке %
Концент рация минер. Удобрения гм3
Концентрация примесей
Расчет разбавления ливневых стоков при сбросе их в акваторию
1. Условия сброса ливневых поверхностных вод
При сбросе ливневых стоков в акваторию порта происходит естественное разбавление в морской воде за счет процессов турбулентной диффузии.
Поскольку азот аммонийный фосфор фосфатов и калий относятся к группе веществ с одинаковым лимитирующим признаком вредности (ЛПВ) (см.табл.2.1) то сумма отношений фактических концентраций в месте контроля к соответствующим предельно допустимым концентрациям (ПДК) не должна превышать единицы.
В табл.3.1 представлены допустимые концентрации нормируемых примесей в контрольном створе расположенном не далее 500 м от места выпуска с учетом условия для ЛПВ а также необходимая степень разбавления для достижения допустимых концентраций.
2. Расчет кратности разбавления
Расчет кратности разбавления поверхностных сточных вод от выпуска причала N 5 произведен по методике Баранника В.А. и Кресина B.C. рекомендованной Методикой расчета предельно допустимых сбросов (ПДС) веществ в водные объекты со сточными водами (М. 1993 г.) для условий сосредоточенного выпуска сточных вод в море.
В основе методики лежит аналитическое решение уравнения турбулентной диффузии с выводом выражения для основного разбавления в виде:
I - расстояние от места выпуска до контрольного створа или
произвольного участка м;
U - скорость течения мс;
Нср - средняя глубина района разбавления м;
Dr Da - горизонтальный и вертикальный коэффициенты диффузии м2с;
Пн - кратность начального разбавления;
q - расход сточных вод м2с;
Io - расстояние выпуска от берега м.
Для условий выпуска стоков от причала N 5 имеем:
Пн = 1 (безнапорный выпуск);
q = 0.0022 м3с (соответствует суточному расходу 187 м3сут для максимально загрязненного поверхностного стока);
Io = 0 (береговой выпуск)
Результаты расчета кратности разбавления поверхностных сточных вод на расстояниях I от места выпуска представлены в табл.3.2.
Расстояние от места выпуска I м
Кратность основного
Сравнивая полученные результаты с требуемой степенью необходимого разбавления (табл.3.1) можно отметить что для наиболее концентрированного поверхностного стока формирующегося в мае и сентябре - ноябре нормативное качество поверхностных вод будет соблюдаться на расстоянии 15 м от места выпуска.
Оценка разбавления поверхностных сточных вод показывает что необходимая зона смешения не превышает радиуса 15 м от места выпуска.
В этой связи специальных мероприятий по очистке поверхностного стока в проекте не предусматривается.
В проекте комплекса перегрузки минеральных удобрений предусмотрены технологические решения и мероприятия по созданию условий и обеспечению безопасности труда рабочих и служащих по предотвращению воздействия на работающих опасных и вредных производственных факторов по устранению тяжелых операций при выполнении работ и обслуживании оборудования меры по предупреждению взрывов и пожаров безопасное расположение оборудования для обслуживания и прохода людей безопасное расположение рабочих; - мест обеспечение санитарно-гигиенических условий работающим.
Мероприятия по охране труда сохранению здоровья и работоспособности людей в процессе производственной деятельности на перегрузочном комплексе предусмотрены в соответствии с "Требованиями безопасности труда которые должны учитываться при проектировании новых реконструкции и модернизации действующих морских портов перегрузочных комплексов и отдельных объектов порта" (РД 31.82.01-95) "Правилами охраны труда в морских портах" (ПОТ РО-152-31.82.03.-96) руководящими нормативными документами (РД) строительными и санитарными нормами и правилами (СНиП) нормами технологического проектирования (НТП) и системой стандартов по безопасности труда (ССБТ) приведенными в приложении.
Охрана труда работающих на промышленном объекте осуществляется следующими видами обеспечения безопасности работ в соответствии с РД 31.80.11-95:
- технологическое обеспечение безопасности работ предусматриваемое в проектеи осуществляемое в строительстве;
конструктивное обеспечение безопасности оборудования осуществляемое при разработке конструкторской документации и при изготовлении оборудования машин механизмов устройств и аппаратов;
- организационное обеспечение безопасности работ заключающееся в поддержке оборудования в исправном состоянии и в осуществлении комплекса мероприятий по подготовке к производству работ а также в необходимом надзоре за выполнением правил и инструкций по безопасности труда в период эксплуатации объекта.
- обеспечение безопасности передвижения людей по территории объекта и путям сообщения осуществляемое комплексом организационных и конструктивных мер в период строительства и эксплуатации объекта;
обучение по охране труда рабочих и служащих а также пропаганда безопасных методов труда непосредственно на рабочих местах.
Основные направления разработки мероприятий предусмотренных в технологических решениях по обеспечению безопасности работ по предотвращению воздействия на работающих опасных и вредных производственных факторов с учетом специфики работ на комплексе:
внедрение наиболее механизированной технологии перегрузочных работ;
- применение типового оборудования;
меры по предупреждению взрывов и пожаров;
- безопасное расположение оборудования устройств и конструкций для прохода людей для производства работ для обслуживания и текущего ремонта;
- безопасное расположение и устройство рабочих мест в зонах с удобным доступом и возможностью быстрой эвакуации людей;
- обеспечение санитарно-гигиенических условий: норм освещенности устранения пыли снижения шума и вибрации до санитарных норм обеспечение требуемых парамётров воздуха; эстетизация производственной среды создание оптимального цветоклимата рациональность оборудования и производственной мебели.
Опасные и вредные производственные факторы
На комплексе предусматривается перегрузка следующих минеральных удобрений:
- карбамид (ГОСТ 2081-92) - азотное (466%) удобрение гранулированное белого цвета растворимое в воде. Обладает высокой гигроскопичностью. Не токсичен не взрывоопасен.
- аммиачная селитра (ГОСТ 2-85) - азотное (350%) удобрение гранулированное белого цвета растворимое в воде гигроскопично. При хранении слеживается. При длительном хранении в состоянии слеживаемости постепенно разогревается до разложения и в смеси с горючими веществами может привести к взрыву. Не токсична.
- нитроаммофоска (ГОСТ 19691-84) - сложное азотно" фосфорно". калиевое (по 160%) удобрение гранулированное розового цвета. Не токсичное безопасное. При высокой температуре разлагается.
- аммофос (ГОСТ 18918-85) - фосфорно (500%)-азотное (120%) удобрение гранулированное белого цвета. Обладает высокой гигроскопичностью. Едкое и коррозионное в присутствии влаги вещество. Раздражает кожу человека и слизистые оболочки глаз. При повышенной температуре аммофос выделяет раздражающий газ аммиак.
Вредным производственным фактором для здоровья людей на комплексе у перечисленных минеральных удобрений при нормальных климатических условиях является их пылевыделение в процессе перегрузочных операций: разгрузки ж.д. вагонов загрузки ленточных конвейеров перегрузки (пересыпки) с конвейера на конвейер загрузки (засыпки) удобрений в трюмы судна.
Основные вредные и опасные производственные факторы для здоровья и жизни работников на проектируемых объектах комплекса перегрузки минеральных удобрений (По ГОСТ 12.0.003-74 и по Приказу Минздравмедпрома России и Госкомсанэпиднадзора России от 05.10.95 №28088):
Движущиеся железнодорожные вагоны (Железнодорожные пути станция разгрузки вагонов).
Подвижные части производственного оборудования (Станция разгрузки вагонов перегрузочные станции ленточные конвейеры судопогрузочная машина).
Повышенная запыленность (взвешенные вещества) воздуха рабочей зоны (Станция разгрузки вагонов перегрузочные станции конвейерные галерей судопогрузочная машина трюмы судов);
Повышенный 'уровень шума (Компрессорная лстанция вентиляционные камеры').
Повышенный уровень вибрации - (Компрессорная станция воздушные вентиляторы).
Опасный уровеньнапряжения электрического тока (Линии и сети электроснабжения и электропитания электрорборудование и эектроаппаратура электрическое освещение .наружное и внутреннее пульты .управления трансформаторная подстанция).
Повышенный уровень статического электричества (Технологическое оборудование электрическое оборудование и установки).
Предусмотренные в проекте мероприятия по снижению пылевыделения на комплексе приведены в арх. № 61139 (Том 1. Пояснительная записка п. 5.25).
Мероприятия по снижению шумаи вибрации на объектах комплекса приведены втомжеарх.№61139(п.4.73).
Санитарно-бытовое обслуживание работников комплекса представлено также в арх. №61139(п.4.9.1).
В нижеследующих разделах приведено описание разработанных в проекте основных мероприятий по охране труда работающих на отдельных объектах комплекса.
В тексте в конце предложений в скобках приведены ссылки на нормативные документы и номер пункта на основании требований которых разработано конкретное мероприятие по обеспечению безопасности и охраны труда.
Основные мероприятия по охране труда работающих
1. Генеральный план и транспорт
Для создания условий по обеспечению безопасности людей здания и сооружения комплекса по перегрузке минудобрений сгруппированы с учетом их общности назначения и функций (РД 31.82.01-95 п. 1.2.6).
Железнодорожные пути для подачи груженых вагонов и отправления порожних расположены на горизонтальных площадках.
Здания сооружения и устройства расположены на расстоянии более 61 м от железнодорожных путей (ГОСТ 9238-83).
Выходы из зданий находящихся вблизи ж.д. путей предусмотрены в сторону от них (ПОТ РО-152-31.82.03-96 п.2111).
Рычагй управления ж.д. стрелками- имеют удобный подход к ним и расположены на безопасном расстоянии от прилегающих путей. Рычаги стрелок в нерабочем положении не выступают выше уровня покрытия территории. Стрелочные переводы закрытого типа;
К зданиям и сооружениям по всей их длине обеспечен подъезд пожарных автомобилей (СНиП 11-89-80 п.3.46).
На территории комплекса предусмотрена надежная система водоотвода гарантирующая отвод поверхностных вод в систему канализации сточных вод. Для обеспечения отвода поверхностных (дождевых) вод приняты уклоны (0005-002) поверхности территории (РД 31.3.01.01-93). У всех канализационных люков и колодцев предусмотрены закрытия (ПОТ РО-152-31.82.03-96).
2. Станция разгрузки вагонов
Станция размещается в закрытом здании оборудованном со стороны въезда и выезда вагонов кирпичными тамбурами. Для предотвращения выделения пыли из станции в тамбурах устанавливаются 4 ряда гибких шторных укрытий.
Бункеры для ссыпки удобрений из вагонов закрыты сверху металлическими решетками с ячейками 200 х 200 мм (ПОТ РО-152-31.82.03-96 п.4.5.5).
Станция разгрузки вагонов и пересыпные рукава с питателей на магистральный конвейер оборудованы аспирационными установками для обеспыливания воздуха.
Помещение служб инженерного обеспечения управления производственным процессом санузел и помещение обогрева для работников выделены в изолированную блок-пристройку имеющую обособленные выходы наружу вне зоны пыления.
Для защиты органов дыхания и кожных покровов обслуживающий персонал внутри станции (в зоне пылевыделения) должен работать в пыленепроницаемой спецодежде и в противоаэрозольных фильтрующих респираторах (ПОТ РО-152-31.82.03-96 Приложение 8п.5.1 и табл. 2). В связи с концентрацией пыли в воздухе рабочей зоны внутри станции разгрузки вагонов достигающей по расчету 168 мгм3 рабочими должны применяться респираторы марок ПРШ-471 Астра-2 или Ф-62Ш.
3. Перегрузочные работы -
Все перегрузочные работы на комплексе минудобрений запроектированы с применением специализированного перегрузочного оборудования в соответствии с требованиями "Правил охраны труда в морских портах" (ПОТ РО-152-31.82.03-96 пп.4.1 4.5 и 13.12) "Руководства по технологическому проектированию морских портов" (РД31.3.01-93) и "Системы стандартов безопасности труда". -
Для обеспечения безопасности и охраны труда работающих в соответствиис "Санитарными нормами проектирования промышленных предприятий" (СН 245-71 раздел 1 п. 1.5) в проекте перегрузочного комплекса предусмотрено:
комплексная механизация автоматизация и дистанционное управление перегрузочным процессом;
- размещение конвейеров в закрытых галереях;
- автоматическая сигнализация об аварийных ситуациях на конвейерных линиях и перегрузочных машинах;
- максимальное уплотнение стыков и соединений в технологическом оборудовании в конвейерных галереях и перегрузочных узлах для предотвращения пылевыделения в процессе производства.
Проект стационарных ленточных конвейеров (конвейерных линий) и необходимых сооружений и устройств (галерей разгрузочных перегрузочных и погрузочных станций) выполнен с соблюдением норм и правил СНиП 2.05.07-91 (раздел 8 п.8.36) которыми для обеспечения безопасности работ в системах конвейерных линий предусмотрено:
централизованное управление и контроль за отдельными установками и системой в целом (диспетчерское управление);
возможность местного управления конвейерами во время ремонтных и наладочных работ;
местная блокировка предотвращающая дистанционный пуск конвейера с пульта управления;
- устройства для контроля натяжения обрыва пробуксовки и схода ленты;
- громкоговорящая связь;
- телефонная связь между пультами управления конвейерами;
подача предупредительного звукового сигнала при пуске конвейеров;
- сигнализация о работе механизмов на центральном пульте управления;
- последовательный запуск приводов конвейерной линии в направлении противоположном потоку транспортируемого груза;
- возможность остановки каждого конвейера аварийными выключателями из любого уголка конвейерной линии со стороны основного прохода;
- остановка конвейера при обрыве или сходе ленты с барабана;
- остановка конвейера работающего на спуск при превышении номинальной скорости ленты;
автоматическая остановка всех предыдущих конвейеров при аварийной остановке любого конвейера а также при превышении допустимого уровня груза в бункерах или в местах пересыпок.
Ленточные конвейеры размещаются внутри закрытых галерей. Для безопасности обслуживания конвейеров в галереях предусматриваются с .обеих сторон проходы шириной075 м. (ПОТ РО-152-31.82.03-96 п: 4.5.1).
Для обеспечения естественной вентиляции в галереях предусмотрены открывающиеся окна со стороны основного прохода (СНиП 2.05.07-91 п. 823)
В необходимых местах предусмотрены эвакуационные выходы из галерей и переходные мостики над конвейерами шириной 10 м со сплошным--настилом с отбортовкой по низу на высоту 015 м и с ограждающими перилами высотой 1.0 м (СНиП 2.05.07-91 п. 8.25).
Перегрузочные (пересыпные) станции размещены в крытых зданиях.
В проекте предусмотрено оснащение перегрузочныхмашин необходимыми элементами системы технических средств безопасности: оградительными предохранительными и тормозными устройствами блокировками сигнализаторами опасности опознавательной окраской и предупреждающими знаками дистанционным управлением . специальными средствами обеспечения электробезопасности и другими средствами защиты (РД 31.82.01-95 п. 1.6.1).
Ко всем механизмам предусмотрен безопасный подход. Все движущиеся и вращающиеся части прикрыты съемными кожухами и ограждениями допускающими удобный осмотр смазку и ремонт (ПОТ РО-152-31.82.03-96 п. 4.1.5). Головные и хвостовые барабаны конвейеров имеют ограждения препятствующие доступу людей к ним во время работы конвейеров (СНиП 2.05.07-91 п. 8.21).
В концевых частях конвейеров устанавливаются кнопки "Стоп" ярко-красного цвета и розетки для подключения низковольтного освещения при осмотре и ремонте (ПОТ РО-152-31.82.023-96 п. 4.5.8).
Приводы натяжные устройства конвейеров и места перехода груза с одной ленты на другую оборудуются легкосъемными ограждениями сблокированными с приводами конвейера для его отключения при снятии ограждения (ПОТ РО-152-31.82.03-96 п. 4.5.10).
Для устранения пылевыделения каждый пересыпной рукав с конвейера на конвейер перегрузочных станций оборудован аспирационным устройством (ПОТ РО-152-31.82.03-96 п. 4.5.7). Аспирационные установки размещены в одних зданиях с перегрузочными станциями.
В связи с высокой концентрацией пыли в воздухе рабочей зоны внутри перегрузочных станций достигающей по расчету 719 мгм3 обслуживающий персонал должен работать в пыленепроницаемой спецодежде ив противоаэрозольных фильтрующих респираторах марки ПРШ-471 для защиты органов дыхания.
В береговой погрузочной галерее для уменьшения пылевыделения в узле передачи груза с берегового конвейера на судопогрузочную машину хвостовая часть машины соединена со сбрасывающей тележкой ленточного конвейера.
У судопогрузочной машины передвигающейся по наземным рельсовым путям расстояние от нижней габаритной точки машины до пола составляет более 20 м а расстояние от нижних выступающих частей машины до расположенного в зоне ее действия оборудования превышает 07 м (РД 31.82.01 -95 п. 1.6.9) что обеспечивает безопасный проход для людей. Движущиеся токоведущие нагревающиеся части судопогрузочной машины прочно закрыты укрепленными съемными ограждениями допускающими удобный осмотр и "проведение ремонтных работ (ПОТ: РО-152- 31.82.03-96 п. 4.1.5).
Все площадки и проходы расположенные на высоте и предназначённыё для обслуживания механизмов перегрузочных машин имеют леерное ограждение высотой 10 м со сплошной зашивкой по низу высотой 0151м с промежуточным леером на высоте 05 м (Правила У и БЭ п. 4.133).
Для обслуживания перегрузочного оборудования на высоте более 10 м и доступа к нему предусматриваются стационарные лестницы и площадки с ограждением.
Для уменьшения пылевыделения в процессе работы продольная щель береговой погрузочной галереи имеет по всей длине укрытие из прорезиненной ткани а судопогрузочная машина оборудована телескопической трубой с пылеподавляющей насадкой.
Не допускается нахождение людей в трюмах во время погрузки.
4. Компрессорная станция
Компрессорная станция размещена в пристройке к зданию станции разгрузки вагонов в отдельном помещении изолированном от здания глухой несгораемой стеной (152 РО-31.83.01-96 п. 1.20.2).
Двери и окна компрессорной станции открываются наружу. Полы - ровные с нескользящей поверхностью из несгораемого твердого материала.
Движущиеся части компрессоров и электродвигателей защищены кожухами с металлическими ограждениями высотой 10 м со сплошной защитой в нижней части на высоту 0 15 м.
Все каналы и приямки перекрыты плитами из рифленой стали.
Для обеспечения безопасности проходов людей и обеспечения возможности монтажа оборудования компрессора и электродвигателя в машинном зале предусмотрены проходы шириной не менее 15 м а между оборудованием и стенами здания - не менее 10 м (152 РО-31.83.01-96 п. 1.20.8).
У всасывающих трубопроводах предусмотрена теплоизоляция.
Для уменьшения шума предусматривается звукоизоляция трубопроводов сжатого воздуха пусковых трубопроводов и трубопроводов концевых холодильников и выпуск воздуха при пуске компрессора в продувочный бак а из него в
шумопоглащающий выхлопной трубопровод в атмосферу (152 РО-31.83.01-96 п.п. 1.20.9 и 1.20.10).
Для оператора предусматривается изолированное от шума помещение.
Для снижения влияния вибрации компрессоры устанавливаются на демпферирующие (виброгасящие) фундаментные прокладки.
Воздухосборники вынесены наружу компрессорной станции.
5. Электробезопасность
Для обеспечениябезопасности работающих от повышенного напряжения электрического тока впроекте предусмотрено применением подземной (в траншеях) кабельной прокладки линий и сетей электроснабжения; безопасная изоляция и заземление металлических корпусов и частей электрооборудования в соответствии с требованиями ПУЭ Правил ТБ при эксплуатации электроустановок .потребителей СН 174-75 ГОСТ 12:1.019-79 ГОСТ 12.1.030-81 ГОСТ 2.2.061-81 и ГОСТ 12.3.002-75.
У зданий сооружений и перегрузочного оборудования предусмотрена молниезащита от атмосферного электричества путем молниеотводов (заземлйтелей) в соответствии с Указаниями СН 305-77.
Узлы управления автоматического пожаротушения размещены в изолированных помещениях.
Аварийная ДЭС установлена в отдельном помещении здания станции разгрузки вагонов.
Для подключения переносных светильников ремонтного освещения в галереях и перегрузочных станциях предусмотрены низковольтные розетки 36 В.
Для защиты людей от статического электричества у технологического оборудования и электроустановок предусмотрены заземляющие устройства для снятия зарядов у всех металлических и электропроводящих частей оборудования в соответствии с требованиями ПУЭ 152 РО-31.83.01-96 (п. 27) СН 305-77 ГОСТ 12.1.030-81 ГОСТ 12.2.061-81 ГОСТ 12.4.124-83. Заземляющие устройства для защиты от статического электричества объединены с заземляющими устройствами для электрооборудования (СН 102-76).
Работа персонала в зоне опасного уровня напряжения электрического тока и при обслуживании технологического оборудования и электроустановок с повышенным уровнем статического электричества должна производиться с применением средств индивидуальной защиты: спецодежды изолирующей обуви и резиновых перчаток (ГОСТ 12.4.011-89 ГОСТ 12.4.103-83 и ГОСТ 12.4.104-83).
Внедрение и выполнение предусмотренных в проекте технологических мероприятий по охране труда и применение соответствующих должностных инструкций обеспечит создание необходимых условий труда безопасность жизни и здоровье работников комплекса в процессе их трудовой деятельности в соответствии с "Основами законодательства Российской Федерации об охране труда" (1993г.) по осуществлению прав работников на охрану труда (Статья 4) и исполнению обязанностей работодателей по обеспечению охраны труда на предприятии (Статья 9).
1. ОСНОВНЫЕ НАПРАВЛЕНИЯ ЭКСПОРТНЫХ ГРУЗОПОТОКОВ МИНЕРАЛЬНЫХ УДОБРЕНИЙ
Промышленный потенциал России по производству минеральных удобрений может полностью удовлетворить потребности сельского хозяйства страны и ежегодно экспортировать продукцию на сумму около двух миллиардов долларов. Однако в настоящее время в связи с отсутствием платежеспособного спроса со стороны сельхозпроизводителей поставки минеральных удобрений селу сократились в десять раз. В целях недопущения снижения плодородия почв и обеспечения проведения агротехнических мероприятий Правительство Российской Федерации приняло постановление предусматривающее проведение конкурса среди производителей минеральных удобрений на право поставки средств химизации сельскохозяйственным товаропроизводителям. Постановлением установлено что цены и тарифы на природный газ и электрическую энергию потребляемую победителями конкурса а также на сырье для производства удобрений будут понижены до 50 %. Министерству путей сообщения предписано снизить тарифы на железнодорожные перевозки на 30%.
предыдущего года соответственно на 385% и 865%.За первые пять месяцев текущего года на предприятии выработано 133 млн.т аммиака и 4513 млн.т. карбамида. Наибольшие объемы данного минерального сырья отправлены в Мексику Гондурас Бразилию.
Экспортные возможности российской промышленности минеральных удобрений обеспечиваются обширными залежами фосфоритных и азотосодержащих руд а также природного газа. В настоящий момент объем экспорта минеральных удобрений составляет свыше 74 млрд ам. долларов в год и является третьим по величине в структуре российского бизнеса.
В настоящий момент при условии повышения платежеспособности российских сельскохозяйственных предприятий существует перспектива увеличения внутреннего потребления удобрений поскольку в последние годы наблюдался спад объемов вноса удобрений на гектар посевной площади до 85 кг на гектар в то время. Как скажем в Китае в почву вносится до 300 кг удобрений на гектар. Этот фактор может повлиять на экмпорт удобрений в долгосрочной перспективе. Однако его влияние может быть значительно сокращено появлением и значительным ростом рынков минеральных удобрений в частности в Южной и Юго-Восточной Азии и Южной Америке.
Крупнейшими импортерами поташа из стран СНГ в 2000 году являлись Бразилия (546 000 тыс.т) Бельгия (286 000 тыс.т) Италия (226 000 тыс.т) Малайзия (303 000 тыс.т) Финляндия (320 000 тыс.т.) Япония (206 000 тыс т.) Индия (200 000 тыс.т) и Польша (183 000 тыс.т).
Как следует из оценки специалистов компании Осеап 8Ыррш§ Соп-зи11ап15 в кратко- и среднесрочной перспективе спрос на минеральные удобрения на внешнем рынке в ближайшие десять лет останется достаточно высоким хотя в отношении России на этот прогноз повлияет состояние сельского хозяйства Внутренний спрос на продовольствие и что немаловажно обменный курс рубля как впрочем и в отношении всех остальных составляющих российской внешней торговли.
Наибольший спрос на минеральные удобрения в ближайшее деся-тилентие ожидается со стороны развивающихся стран даже несмотря на значительные инвестиции в их собственные производственные мощности. Рост населения посевных площадей и среднего ВНП на душу населения безусловно ведут к росту потребления минеральных удобрений в Южной и Восточной Азии а также в Латинской Америке Африке и на
ближнем Востоке т.е. в регионах геогрефически тяготеющих к портам Черного моря.
До 2005 года ожидается рост мирового портебления удобрений (см.таб.№7) примерно на 29 млн. тонн из которых на 16 млн. тонн претендуют страны Юго-Восточной Азии 6 млн. тонн - страны Центральной и Восточной Европы и на 7 млн. тонн - прочие страны. В этой связи будет также наблюдаться значительный рост спроса на морские перевозки удобрений который в ближайшее десятилетие составит примерно 170 миллиардов тонно-миль. Из них почти 72 % придется на Азиатские рынки и 185% на рынки Латинской Америки (8).
Прогнозируемый мировой спрос на минеральные удобрения к 2005 году млн.тонн
Несмотря на значительные мощности по производству минеральных удобрений у СССР не имелось достаточного количества специализированных глубоководных терминалов по обработке этих грузов. На Дальнем Востоке у России имелся единственный такой терминал на причале №2 в порту Находка. Однако в 80-х он был снесен и отправка минеральных удобрений через него в северокорейский порт Найджин была прекращена. Однако позднее в порту Ванино на территории крытого склада был сооружен небольшой причальный комплекс для выгрузки удобрений из жд вагонов и последующей погрузки их в трюма с помощью портальных кранов.
Проектная мощность этого комплекса - 150 000 тонн удобрений в год.
На Балтике основным'портом по перевалке калийных удобрений является латвийский порт Вентспилс. Специализированный комплекс по переработке удобрений в этом порту был пущен в эксплуатацию в конце 1970-х годов. С того времени по 1995 год им были обработаны свыше 32 млн. тонн грузов. При этом в 1994 и 1995 годах были переработаны соответственно 38 и 43 млн. тонн удобрений. На этом терминале ежегодно обрабатываются 40 - 60 000 вагонов с калийными удобрениями следующими из России и Белоруссии. Комплекс по перевалке удобрений включает станцию по разгрузке жд вагонов рассчитанную на единовременную обработку 12 вагонов а также крытые склады для хранения двух видов удобрений вместимостью соответственно 88 000 и 81 000 тонн. На терминале производится погрузка судов дедвейтом до 45 000 тонн до осадки 135 метров. Погрузка осуществляется двумя погрузочными машинами РНВ производительностью 6000 -12 000 тонн в сутки.
В 1995 году в порту Клайпеда вступил в эксплуатацию мини-терминал по обработке минеральных удобрений с оборудованием и конвейерными линиями поставленными компанией Eurotrans cont. Этот комплекс предназначен для обработки вагонов по прямому варианту и имеет производительность 300 тонн в час. На Севере России планируется реконструкция причала 1419 для переработки минеральных удобрений в объеме 2 млн.тонн в год.
Крупнейшим комплексом по переработке удобрений на Черноморском бассейне является порт Южный. Он имеет две погрузочные линии для обработки аммиака и две линии для обработки мочевины мощностью соответственно 4 и 2 млн. тонн в год. В 1995 году через Южный было экспортировано 07 млн. тонн аммиака Тольяттинского химкомбината и 06 млн. тонн метанола других российских предприятий. Комплекс включает два крытых склада рассчитанных на 45 000 тонн мочевины каждый конвейерные линии общей длиной около 16 км а также станцию разгрузки жд вагонов. Погрузочные машины имеют производительность до 700 тч и 300 тч для навалочных и тарированых грузов. На терминале могут обрабатываться суда осадкой до 125 метров дедвейтом до 55-60 000 тонн.
Обработка удобрений с использованием специализированных двадцатифутовых контейнеров ведется на причале К4 Одесского порта стивидорной компанией Sderotgide int.. Мощности причала позволяют обрабатывать ежесуточно 300 - 500 контейнеров мочевины. Глубина у причала составляет 115 метров длина причала - 290 метров.
2 . ВЫВОДЫ И ПРЕДЛОЖЕНИЯ
) отправлять груз маленькими партиями ( максимум 7000 т ) что приводит в конце концов к большой цене перевозки морем и становится невыгодным импортеру (если контракт заключен на условиях ФОБ - Новороссийск) или экспортеру ( если контракт заключен на условиях СИФ -порт направления);
) использовать порты Украины при экспорте удобрений так как они имеют специализированные терминалы для хранения груза и поэтому заводы-экспортеры могут накапливать груз в портах погрузки.
Таким образом можно сделать вывод что для привлечения устойчивых грузопотоков отечественных заводов-экспортеров порту Новороссийск необходим специализированный комплекс переработки минеральных удобрений с накопительным терминалом.
Ток = Стн ((Прн-Пвт)*Нпн) (1)
где Ток - период окупаемости нового накопителя лет.
Стн - стоимость постройки накопителяам.доллтонна.
Прн - производительность накопителя тоннгод.
Нпн - норма прибыли ам.доллтонна.
Ток = 4 000 000 ((2 000 000-600 000)* 114) = 25 года.
Таким образом видим что новый накопитель для удобрений окупится менее чем через три года после ввода его в эксплуатацию.
Рассчитаем ежегодный экономический эффект от ввода в эксплуатацию накопителя совместно с терминалом по формуле (2):
Энак = (При - Пвт)*Нпн (2)
где Энак - ежегодный экономический эффект от ввода в эксплуатацию накопителя совместно с терминалом ам.долл.
Энак = (2 000 000 - 600 000)* 114 = 1 596 000 ам.долл.
Кроме этого в свете сделанных выводов можно представить следующие замечания по их практическому применению:
) Необходимо создание единой базы данных для отслеживания грузопотоков следующих через Новороссийский порт анализа качественного уровня обслуживания клиентов в порту и их прибыльность для порта.
) На основании данных требуется сформировать стратегию развития компании которая смогла бы определить приоритеты и цели привлечения и обработки в порту конкретных грузопотоков а также развития мощностей порта и его организации в соответствующем направлении.
Что касается порта С.-Петербург он в настоящее время уже начал реализацию программы строительства специализированных комплексов. За счет кредита Российского Сбербанка в объеме 15 млн. долларов США выделенного на пять лет в порту начаты работы по строительству нового терминала для минеральных удобрений производительностью 3 млн. тонн в год. Притоку удобрений в порт способствуют более приемлемые по сравнению со странами Балтии железнодорожные тарифы МПС.
При возможном снижении железнодорожных тарифов и реализации указанного выше у портов Новороссийск и С.- Петербург имеются все возможности для обработки грузопотоков экспортных минеральных удобрений причем для российских экспортеров они будут более благоприятны чем порты стран Балтии и Украины.
Однако для строительства указанных терминалов для хранения и перевалки грузов необходима государственная поддержка и долгосрочное финансирование проектов.
3 ОБОСНОВАНИЕ ИНВЕСТИЦИЙ В СТРОИТЕЛЬСТВО ПЕРЕВАЛОЧНОГО КОМПЛЕКСА МИНЕРАЛЬНЫХ УДОБРЕНИЙ
3.1 Оценка эффективности мероприятий по охране окружающей среды
Погрузочно-разгрузочные работы с массовыми навалочными и насыпными грузами большинство из которых являются пылящими доставляют много хлопот операторам и портовым администрациям. В процессе работы пыль наиболее интенсивно образуется при сбросе груза с ленты транспортера (или другого устройства) в трюм судна. При погрузке крупнотоннажных судов высота падения груза может достигать 20 м. При этом неизбежны не только интенсивное пылеобразование но и изменение физических свойств груза — измельчение что не всегда приветствуется потребителями.
Проблеме пылеобразования при погрузке судов уделяется повышенное внимание разработано много конструкций пылеподавляющих устройств. Обязательными элементами в большинстве из них являются мощные вентиляторы или компрессоры циклоны системы фильтров механизмы и трубопроводы для отвода запыленного воздуха и возврата регенерированного продукта в грузовое помещение и т. д.
В целях защиты ОС от пыли загрязнения водной среды и шума применяется перегрузочное оборудование оснащаемое специальными устройствами в том числе:
- грейферные перегружатели с экранированием или герметизацией грейфера автоматическим регулированием уровня заполнения грейфера и высоты его над грузом с увлажнением груза водой или водным раствором химических веществ с пылеулавливающими устройствами;
- перегружатели непрерывного действия считающиеся более безопасными в экологическом отношении чем машины циклического действия обеспечивающие меньший уровень пылеобразования оснащаемые пылеулавливающими устройствами и защитными кожухами а также форсунками для увлажнения груза;
- приемные бункеры на причале в тыловых грузовых фронтах перегрузочных комплексов оснащаемые пылеулавливающими устройствами отражательными экранами форсунками для увлажнения груза.
На станциях погрузки и разгрузки вагонов вагоноопрокидывателях обеспылевание обеспечивается наличием крытых помещений использованием увлажнения груза установкой отражательных экранов пылеуловителей мойкой порожних вагонов и поддержанием минимальной высоты падения груза. Территория дороги и проезды комплексов как правило имеют твердое водоустойчивое покрытие с уклонами в сторону водоприемных люков оснащаются разбрызгивателями у бордюрных камней и убираются моечными машинами. Для приема моечных и ливневых вод предусматривается ливнесточная сеть.
Для защиты портовых и грунтовых вод в системе ливнестоков предусматриваются отстойные и очистные бассейны устройства для очистки канализационных вод глубоководные водосбросы очищенных вод в море защитные экраны для предотвращения загрязнения грунтовых вод. На перегрузочных комплексах постройки последних лет применяется закольцованная система водоснабжения в которой очищенные воды используются для увлажнения груза и моечных операций.
Мерами защиты от шумовых воздействий работающего комплекса являются в первую очередь усовершенствованные технические решения перегрузочного оборудования (применение амортизаторов оптимального подбора режима работы двигателя). Природоохранные требования включаются в технические условия на поставку технологического оборудования для перегрузочных комплексов.
Реализация мер по охране окружающей среды при строительстве и эксплуатации комплексов по перевалке навалочно-насыпных грузов сопряжена с затратами целесообразность которых требует экономического обоснования.
В общем плане экономическая целесообразность затрат на природоохранные мероприятия определяется их соотношением с возможными издержками на устранение нанесенного ущерба окружающей среде. Поэтому оценка возможного ущерба окружающей среде и разработка методов планирования эффективных по затратам и надежных мер его снижения считается весьма важным этапом для принятия решения по строительству комплексов.
При определении затрат на защиту водной среды подлежат учету все источники ее возможного загрязнения: суда комплексы склады. При оценке экономических последствий воздействий на окружающую среду подлежат учету затраты на ликвидацию аварийных и структурных загрязнений за год или период реализации природоохранных мер.
Определение экономических последствий воздействий на окружающую среду следует производить с учетом анализа рисков включающих вероятность (частоту) и воздействия (последствия):
Степень риска=частота* объем загрязнения
Общие затраты на природоохранные мероприятия включают прямые и косвенные. К прямым относятся: расходы па подготовку персонала приобретение и обслуживание соответствующего оборудования разработка правил и нормативных актов. Косвенные затраты могут быть связаны с задержками и перерывами в эксплуатационной деятельности комплекса и доставке грузов ужесточением нормативных требований по охране окружающей среды.
Стоимость природоохранных технологий по комплексу составляет 1200000 долларов то есть 10% от общей стоимости строительства. На комплексе абсолютно герметичные конвейерные галереи исключающие попадание пыли в атмосферу. Предполагается сделать абсолютно герметичным и склад. Судопогрузочное оборудование убрано в галереи а судопогрузчики снабжены так называемым желобом 'Кливлендкаскад' опускающимся непосредственно в трюм судна. Кроме пассивной защиты комплекс оборудуется установкой реагентного пылеподавления и мощным блоком аспирационных систем (систем воздухоочистки). Установлено оборудование для очистки сточных и ливневых вод специально для того чтобы предотвратить попадание вместе со сточными водами в почву и акваторию порта тех возможных загрязнений которые гипотетически могут иметь место.
Стоимость оборудования для охраны окружающей среды по составляющим долл. США
Установка пылеподавления
Система воздухоочистки
Установка для очистки сточных вод
В процессе перегрузки на комплексе имеют место прямые затраты связанные с оплатой сбора за загрязнение окружающей среды приведенные из расчета на 1 тонну перегруженных минеральных удобрений и составляющие 0.01% от стоимости перевалки:
Зос=Д*С=13000000*0.01=130000 долларов США в год
где Зос- затраты на охрану окружающей среды;
Д - доход от перевалки;
С - коэффициент сбора за загрязнение окружающей среды. Затраты на приобретение и обновление спецодежды респираторов страховочных поясов проведение инструктажей по технике безопасности по комплексу составляют 0.001% от стоимости перевалки:
=U*C1=13000000*0.001=13000 долларов США в год
где 31 - затраты на приобретение спецодежды проведение инструктажей;
C1 - процент отчисляемый на приобретение спецодежды и проведения инструктажей. Итого затраты:
Sк=3oc+31 =30000+13000=143000 долларов США в год
где Sк - сумма затрат по комплексу;
Зос- затраты на охрану окружающей среды;
- затраты на приобретение спецодежды проведение инструктажей.
При непредвиденных авариях в результате которых окружающей среде может быть нанесен ущерб суммы необходимые для уплаты штрафов и ликвидацию последствий загрязнений будут изыматься из резервного фонда составляющего 5% от прибыли:
Фрк=П*Пр=1686800*0.05=84340 долларов США в год
где Фрк- резервный фонд;
Пр - процент отчисления с прибыль в резервный фонд. После введения в строй склада затраты на окружающую среду также увеличатся и составят:
Зос=Д*С=16250000*0.01=162500 долларов США в год
В связи с увеличением прибыли резервный фонд также увеличится и составит:
Фрк=П*Пр=2594000*0.05=129700 долларов США в год
Значит при непредвиденных авариях суммы на оплату штрафов и устранение загрязнений могут составить 129700 долларов США.
Так как склад сам является потенциальным источником опасности с него также будет взиматься сбор на охрану окружающей среды в размере 0.01% от стоимости хранения груза на складе:
Зосск=Д1*С=2500000*0.01=25000 долларов США в год
где Зосек- затраты на охрану окружающей среды по складу;
Д1 - доход отхранения;
С - коэффициент сбора за загрязнение окружающей среды.
Затраты на приобретение спецодежды и инструктажей по технике безопасности по складу составят:
=Д1*С2=2500000*0.001=2500 долларов США в год
где 32 - затраты на приобретение спецодежды проведение инструктажей по складу;
Д1 - доход от перевалки после строительства склада;
C1 - процент отчисляемый на приобретение спецодежды и проведения инструктажей.
Общие затраты на охрану окружающей среды по комплексу после введения в строй склада составят:
Зобщ=3оск+3осск+31+32=162500+25000+13000+2500=203000 долларов США в год
где Зобщ - общие затраты на охрану окружающей среды;
Зос- затраты на охрану окружающей среды по комплексу;
Зосек- затраты на охрану окружающей среды по складу;
- затраты на приобретение спецодежды проведение инструктажей по комплексу
З2 - затраты на приобретение спецодежды проведение инструктажей по складу.
Таблица 10.3 Затраты на охрану окружающей среды (тыс. долларов в год)
Вследствие введения в строй склада увеличится прибыль и количество переваливаемого груза а следовательно и затраты на охрану окружающей среды так как суммы отчисляемые на охрану среды напрямую зависят от количества переваливаемого груза. Возрастет также и резервная сумма для устранения последствий загрязнений и оплаты штрафов за загрязнения так как она напрямую зависит от прибыли. В то же время в связи с увеличивающимся на 500000 тонн грузопотоком возрастает и вероятность загрязнений. Затраты на окружающую среду по комплексу в целом увеличатся на 60000 долларов США в год резервный фонд увеличится на 45360 долларов в год.
3.2 Финансирование и стоимость строительства период окупаемости комплекса
Стоимость первой очереди строительства комплекса (без склада) составляет 12000000 долларов США включая:
Таблица 10.4 Стоимость строительства комплекса по составляющим (USD)
Оборудование и строительные материалы
Строительство и монтаж
Железнодорожные пути
Подготовка стройплощадки
Инженерные коммуникации
Пуско-наладочные работы
Реконструкция железнодорожной станции «Новороссийская»
Практика показывает что стоимость строительства 1 м2 склада под ключ для минеральных удобрений составляет (с учетом стоимости стройматериалов) около 1000 долларов США. Таким образом общая стоимость строительства склада составит:
С строительства=Sск*Скв=6000*1000=6 000 000 долл. США
где С строительства - стоимость строительства склада;
Sck - площадь склада;
Скв - стоимость строительства 1м2.
Общие затраты на строительство комплекса в этом случае составят 137000000 долларов США а с учетом процентов по кредиту - 14300000 долларов США.
Финансовые результаты строительства всего комплекса составлены на основании прогнозных оценок. Все расчеты приведены в долларах США.
Услуги по перегрузке сыпучих минеральных удобрений как экспортируемые за пределы СНГ налогом на добавленную стоимость не облагаются. Расчеты налога на прибыль приведены с учетом трехлетнего льготного периода по уплате налога так как комплекс является новым производством выделенным в обособленное структурное подразделение на базе новых (приобретенных или сооруженных) производственных мощностей стоимость которых превышает 20 млн. рублей и имеется технико-экономическое обоснование согласованное с государственными органами исполнительной власти субъектов Российской Федерации. Налог на вмененный доход считался с учетом понижающих коэффициентов.
В процессе перегрузки имеют место прямые издержки связанные с оплатой сбора за загрязнение окружающей среды приведенные из расчета на 1 тонну перегруженных сыпучих минеральных удобрений и составляющие 0.01% от стоимости перевалки.
Финансовый результат рассчитывался при следующих предположениях:
Для осуществления строительства перегрузочного комплекса получен кредит коммерческого банка в размере 2000000 долларов США под 15% годовых. Иностранные инвестиции в строительство составляют 5000000 3000000 выделяют производители минеральных удобрений 2000000 долларов вкладывают в комплекс экспедиторы которые будут заниматься отгрузкой удобрений на экспорт.
Начало функционирования комплекса 01.01.2001 года. Ежегодно до введения в строй склада перегружается 2 млн. тонн удобрений после постройки склада - 2.5 млн. тонн удобрений. Стоимость услуги по перегрузке составляет 6.5 доллара США за 1 тонну затраты на осуществление перегрузки составляют 4 доллара США за 1 тонну. Стоимость хранения 1 тонны груза на складе в течение месяца составит 5 долларов США при себестоимости хранения 3.2 доллара США. Общий объем хранимого на складе груза за год достигает 500000 тонн. Сумма необходимая на строительство склада будет изыматься из прибыли от перевалки удобрений после окупаемости самого комплекса. Амортизация комплекса составит 500000 долларов США ежегодно амортизация склада 150000 долларов США.
Финансовые результаты представлены в таблице.
Таблица 10.5 Отчет о прибылях и убытках по комплексу (долл. США)
Доход после выплаты налога
Затраты на перевалку
Затраты на охрану окружающей среды
Убытки предыдущих периодов
Прибыль до выплаты налога
Таким образом строительство склада можно начать на пятый год после завершения строительства комплекса. Полностью комплекс окупит себя через 4 года после начала функционирования. Однако окупаемость напрямую зависит от объема перевалки поэтому если объем перевалки будет более 2000000 тонн в год то соответственно период окупаемости уменьшится.. После строительства склада объем перегружаемых удобрений может увеличиться увеличив тем самым и прибыль.
Однако практика показывает что строительство склада необходимо начать как можно раньше. С этой целью необходимо произвести расчет финансового результата предусматривающего начало строительства склада сразу после возврата банковского кредита и процентов по кредиту.
Таблица 10.6 Отчет о прибылях и убытках по комплексу и складу (долл. США)
Возврат кредита и процентов
Затраты на строительство склада
Период окупаемости из-за дополнительных затрат на постройку склада практически не меняется зато введение в строй склада увеличивает грузооборот комплекса что в свою очередь увеличивает прибыль поэтому более целесообразным представляется второй вариант который предусматривает начало строительства склада после выплаты кредита и 'процентов то есть в первый же год после начала функционирования.
Надо учитывать и то что склад сам сможет приносить прибыль от хранения груза. Период окупаемости самого склада и предполагаемая прибыль указаны в таблице:
Таблица 10.7 Отчет о прибылях и убытках по складу (долл. США)
Доход от хранения груза
Таким образом самостоятельно склад окупит себя через 3.5 года после ввода в эксплуатацию. Однако . прибыль получаемая в результате его функционирования может уменьшить период окупаемости всего проекта. Финансовый результат проекта представлен в табл. 10.8:
Таблица 10.8 Период окупаемости проекта
Прибыль от перевалки
Прибыль от хранения груза
Затраты на строительство
Уже на третий год комплекс вместе со складом даст прибыль в 448000 долларов США. В результате ввода в строй склада период перевалки уменьшится на 1 год объем перевалки возрастет на 500000 тонн в год. Таким образом быстрое строительство склада несмотря на затраты позволит уменьшить период окупаемости.
ДИПЛОМ БОЛЬШАЯ ЭКОНОМИККА.doc
3.1 Оценка эффективности мероприятий по охране окружающей среды
Погрузочно-разгрузочные работы с массовыми навалочными и насыпными грузами большинство из которых являются пылящими доставляют много хлопот операторам и портовым администрациям. В процессе работы пыль наиболее интенсивно образуется при сбросе груза с ленты транспортера (или другого устройства) в трюм судна. При погрузке крупнотоннажных судов высота падения груза может достигать 20 м. При этом неизбежны не только интенсивное пылеобразование но и изменение физических свойств груза — измельчение что не всегда приветствуется потребителями.
Проблеме пылеобразования при погрузке судов уделяется повышенное внимание разработано много конструкций пылеподавляющих устройств. Обязательными элементами в большинстве из них являются мощные вентиляторы или компрессоры циклоны системы фильтров механизмы и трубопроводы для отвода запыленного воздуха и возврата регенерированного продукта в грузовое помещение и т. д.
В целях защиты ОС от пыли загрязнения водной среды и шума применяется перегрузочное оборудование оснащаемое специальными устройствами в том числе:
- грейферные перегружатели с экранированием или герметизацией грейфера автоматическим регулированием уровня заполнения грейфера и высоты его над грузом с увлажнением груза водой или водным раствором химических веществ с пылеулавливающими устройствами;
- перегружатели непрерывного действия считающиеся более безопасными в экологическом отношении чем машины циклического действия обеспечивающие меньший уровень пылеобразования оснащаемые пылеулавливающими устройствами и защитными кожухами а также форсунками для увлажнения груза;
- приемные бункеры на причале в тыловых грузовых фронтах перегрузочных комплексов оснащаемые пылеулавливающими устройствами отражательными экранами форсунками для увлажнения груза.
На станциях погрузки и разгрузки вагонов вагоноопрокидывателях обеспылевание обеспечивается наличием крытых помещений использованием увлажнения груза установкой отражательных экранов пылеуловителей мойкой порожних вагонов и поддержанием минимальной высоты падения груза. Территория дороги и проезды комплексов как правило имеют твердое водоустойчивое покрытие с уклонами в сторону водоприемных люков оснащаются разбрызгивателями у бордюрных камней и убираются моечными машинами. Для приема моечных и ливневых вод предусматривается ливнесточная сеть.
Для защиты портовых и грунтовых вод в системе ливнестоков предусматриваются отстойные и очистные бассейны устройства для очистки канализационных вод глубоководные водосбросы очищенных вод в море защитные экраны для предотвращения загрязнения грунтовых вод. На перегрузочных комплексах постройки последних лет применяется закольцованная система водоснабжения в которой очищенные воды используются для увлажнения груза и моечных операций.
Мерами защиты от шумовых воздействий работающего комплекса являются в первую очередь усовершенствованные технические решения перегрузочного оборудования (применение амортизаторов оптимального подбора режима работы двигателя). Природоохранные требования включаются в технические условия на поставку технологического оборудования для перегрузочных комплексов.
Реализация мер по охране окружающей среды при строительстве и эксплуатации комплексов по перевалке навалочно-насыпных грузов сопряжена с затратами целесообразность которых требует экономического обоснования.
В общем плане экономическая целесообразность затрат на природоохранные мероприятия определяется их соотношением с возможными издержками на устранение нанесенного ущерба окружающей среде. Поэтому оценка возможного ущерба окружающей среде и разработка методов планирования эффективных по затратам и надежных мер его снижения считается весьма важным этапом для принятия решения по строительству комплексов.
При определении затрат на защиту водной среды подлежат учету все источники ее возможного загрязнения: суда комплексы склады. При оценке экономических последствий воздействий на окружающую среду подлежат учету затраты на ликвидацию аварийных и структурных загрязнений за год или период реализации природоохранных мер.
Определение экономических последствий воздействий на окружающую среду следует производить с учетом анализа рисков включающих вероятность (частоту) и воздействия (последствия):
Степень риска=частота* объем загрязнения
Общие затраты на природоохранные мероприятия включают прямые и косвенные. К прямым относятся: расходы па подготовку персонала приобретение и обслуживание соответствующего оборудования разработка правил и нормативных актов. Косвенные затраты могут быть связаны с задержками и перерывами в эксплуатационной деятельности комплекса и доставке грузов ужесточением нормативных требований по охране окружающей среды.
Стоимость природоохранных технологий по комплексу составляет 1200000 долларов то есть 10% от общей стоимости строительства. На комплексе абсолютно герметичные конвейерные галереи исключающие попадание пыли в атмосферу. Предполагается сделать абсолютно герметичным и склад. Судопогрузочное оборудование убрано в галереи а судопогрузчики снабжены так называемым желобом 'Кливлендкаскад' опускающимся непосредственно в трюм судна. Кроме пассивной защиты комплекс оборудуется установкой реагентного пылеподавления и мощным блоком аспирационных систем (систем воздухоочистки). Установлено оборудование для очистки сточных и ливневых вод специально для того чтобы предотвратить попадание вместе со сточными водами в почву и акваторию порта тех возможных загрязнений которые гипотетически могут иметь место.
Стоимость оборудования для охраны окружающей среды по составляющим долл. США
Установка пылеподавления
Система воздухоочистки
Установка для очистки сточных вод
В процессе перегрузки на комплексе имеют место прямые затраты связанные с оплатой сбора за загрязнение окружающей среды приведенные из расчета на 1 тонну перегруженных минеральных удобрений и составляющие 0.01% от стоимости перевалки:
Зос=Д*С=13000000*0.01=130000 долларов США в год
где Зос- затраты на охрану окружающей среды;
Д - доход от перевалки;
С - коэффициент сбора за загрязнение окружающей среды. Затраты на приобретение и обновление спецодежды респираторов страховочных поясов проведение инструктажей по технике безопасности по комплексу составляют 0.001% от стоимости перевалки:
=U*C1=13000000*0.001=13000 долларов США в год
где 31 - затраты на приобретение спецодежды проведение инструктажей;
C1 - процент отчисляемый на приобретение спецодежды и проведения инструктажей. Итого затраты:
Sк=3oc+31 =30000+13000=143000 долларов США в год
где Sк - сумма затрат по комплексу;
Зос- затраты на охрану окружающей среды;
- затраты на приобретение спецодежды проведение инструктажей.
При непредвиденных авариях в результате которых окружающей среде может быть нанесен ущерб суммы необходимые для уплаты штрафов и ликвидацию последствий загрязнений будут изыматься из резервного фонда составляющего 5% от прибыли:
Фрк=П*Пр=1686800*0.05=84340 долларов США в год
где Фрк- резервный фонд;
Пр - процент отчисления с прибыль в резервный фонд. После введения в строй склада затраты на окружающую среду также увеличатся и составят:
Зос=Д*С=16250000*0.01=162500 долларов США в год
В связи с увеличением прибыли резервный фонд также увеличится и составит:
Фрк=П*Пр=2594000*0.05=129700 долларов США в год
Значит при непредвиденных авариях суммы на оплату штрафов и устранение загрязнений могут составить 129700 долларов США.
Так как склад сам является потенциальным источником опасности с него также будет взиматься сбор на охрану окружающей среды в размере 0.01% от стоимости хранения груза на складе:
Зосск=Д1*С=2500000*0.01=25000 долларов США в год
где Зосек- затраты на охрану окружающей среды по складу;
Д1 - доход отхранения;
С - коэффициент сбора за загрязнение окружающей среды.
Затраты на приобретение спецодежды и инструктажей по технике безопасности по складу составят:
=Д1*С2=2500000*0.001=2500 долларов США в год
где 32 - затраты на приобретение спецодежды проведение инструктажей по складу;
Д1 - доход от перевалки после строительства склада;
C1 - процент отчисляемый на приобретение спецодежды и проведения инструктажей.
Общие затраты на охрану окружающей среды по комплексу после введения в строй склада составят:
Зобщ=3оск+3осск+31+32=162500+25000+13000+2500=203000 долларов США в год
где Зобщ - общие затраты на охрану окружающей среды;
Зос- затраты на охрану окружающей среды по комплексу;
Зосек- затраты на охрану окружающей среды по складу;
- затраты на приобретение спецодежды проведение инструктажей по комплексу
З2 - затраты на приобретение спецодежды проведение инструктажей по складу.
Таблица 11.3 Затраты на охрану окружающей среды (тыс. долларов в год)
Вследствие введения в строй склада увеличится прибыль и количество переваливаемого груза а следовательно и затраты на охрану окружающей среды так как суммы отчисляемые на охрану среды напрямую зависят от количества переваливаемого груза. Возрастет также и резервная сумма для устранения последствий загрязнений и оплаты штрафов за загрязнения так как она напрямую зависит от прибыли. В то же время в связи с увеличивающимся на 500000 тонн грузопотоком возрастает и вероятность загрязнений. Затраты на окружающую среду по комплексу в целом увеличатся на 60000 долларов США в год резервный фонд увеличится на 45360 долларов в год.
3.2 Финансирование и стоимость строительства период окупаемости комплекса
Стоимость первой очереди строительства комплекса (без склада) составляет 12000000 долларов США включая:
Таблица 10.4 Стоимость строительства комплекса по составляющим (USD)
Оборудование и строительные материалы
Строительство и монтаж
Железнодорожные пути
Подготовка стройплощадки
Инженерные коммуникации
Пуско-наладочные работы
Реконструкция железнодорожной станции «Новороссийская»
Практика показывает что стоимость строительства 1 м2 склада под ключ для минеральных удобрений составляет (с учетом стоимости стройматериалов) около 1000 долларов США. Таким образом общая стоимость строительства склада составит:
С строительства=Sск*Скв=6000*1000=6 000 000 долл. США
где С строительства - стоимость строительства склада;
Sck - площадь склада;
Скв - стоимость строительства 1м2.
Общие затраты на строительство комплекса в этом случае составят 137000000 долларов США а с учетом процентов по кредиту - 14300000 долларов США.
Финансовые результаты строительства всего комплекса составлены на основании прогнозных оценок. Все расчеты приведены в долларах США.
Услуги по перегрузке сыпучих минеральных удобрений как экспортируемые за пределы СНГ налогом на добавленную стоимость не облагаются. Расчеты налога на прибыль приведены с учетом трехлетнего льготного периода по уплате налога так как комплекс является новым производством выделенным в обособленное структурное подразделение на базе новых (приобретенных или сооруженных) производственных мощностей стоимость которых превышает 20 млн. рублей и имеется технико-экономическое обоснование согласованное с государственными органами исполнительной власти субъектов Российской Федерации. Налог на вмененный доход считался с учетом понижающих коэффициентов.
В процессе перегрузки имеют место прямые издержки связанные с оплатой сбора за загрязнение окружающей среды приведенные из расчета на 1 тонну перегруженных сыпучих минеральных удобрений и составляющие 0.01% от стоимости перевалки.
Финансовый результат рассчитывался при следующих предположениях:
Для осуществления строительства перегрузочного комплекса получен кредит коммерческого банка в размере 2000000 долларов США под 15% годовых. Иностранные инвестиции в строительство составляют 5000000 3000000 выделяют производители минеральных удобрений 2000000 долларов вкладывают в комплекс экспедиторы которые будут заниматься отгрузкой удобрений на экспорт.
Начало функционирования комплекса 01.01.2001 года. Ежегодно до введения в строй склада перегружается 2 млн. тонн удобрений после постройки склада - 2.5 млн. тонн удобрений. Стоимость услуги по перегрузке составляет 6.5 доллара США за 1 тонну затраты на осуществление перегрузки составляют 4 доллара США за 1 тонну. Стоимость хранения 1 тонны груза на складе в течение месяца составит 5 долларов США при себестоимости хранения 3.2 доллара США. Общий объем хранимого на складе груза за год достигает 500000 тонн. Сумма необходимая на строительство склада будет изыматься из прибыли от перевалки удобрений после окупаемости самого комплекса. Амортизация комплекса составит 500000 долларов США ежегодно амортизация склада 150000 долларов США.
Финансовые результаты представлены в таблице.
Таблица 11.5 Отчет о прибылях и убытках по комплексу (долл. США)
Доход после выплаты налога
Затраты на перевалку
Затраты на охрану окружающей среды
Убытки предыдущих периодов
Прибыль до выплаты налога
Таким образом строительство склада можно начать на пятый год после завершения строительства комплекса. Полностью комплекс окупит себя через 4 года после начала функционирования. Однако окупаемость напрямую зависит от объема перевалки поэтому если объем перевалки будет более 2000000 тонн в год то соответственно период окупаемости уменьшится.. После строительства склада объем перегружаемых удобрений может увеличиться увеличив тем самым и прибыль.
Однако практика показывает что строительство склада необходимо начать как можно раньше. С этой целью необходимо произвести расчет финансового результата предусматривающего начало строительства склада сразу после возврата банковского кредита и процентов по кредиту.
Таблица 11.6 Отчет о прибылях и убытках по комплексу и складу (долл. США)
Возврат кредита и процентов
Затраты на строительство склада
Период окупаемости из-за дополнительных затрат на постройку склада практически не меняется зато введение в строй склада увеличивает грузооборот комплекса что в свою очередь увеличивает прибыль поэтому более целесообразным представляется второй вариант который предусматривает начало строительства склада после выплаты кредита и 'процентов то есть в первый же год после начала функционирования.
Надо учитывать и то что склад сам сможет приносить прибыль от хранения груза. Период окупаемости самого склада и предполагаемая прибыль указаны в таблице:
Таблица 11.7 Отчет о прибылях и убытках по складу (долл. США)
Доход от хранения груза
Таким образом самостоятельно склад окупит себя через 3.5 года после ввода в эксплуатацию. Однако . прибыль получаемая в результате его функционирования может уменьшить период окупаемости всего проекта. Финансовый результат проекта представлен в табл. 10.8:
Таблица 11.8 Период окупаемости проекта
Прибыль от перевалки
Прибыль от хранения груза
Затраты на строительство
Уже на третий год комплекс вместе со складом даст прибыль в 448000 долларов США. В результате ввода в строй склада период перевалки уменьшится на 1 год объем перевалки возрастет на 500000 тонн в год. Таким образом быстрое строительство склада несмотря на затраты позволит уменьшить период окупаемости.
ДИПЛОМ ООСиТБ.doc
1 Охрана окружающей среды.
Расчет концентраций загрязняющих веществ в ливневых стоках перегрузочного комплекса.
1. Количество минеральных удобрений осаждающееся на территории причала N 5 составляет 10 гм2 в месяц (письмо проектной фирмы IGP N 2204 от 15.07.96. ).
2. Распределение грузопотоков по видам удобрений:
карбамид (ГОСТ 2081-92) - 60% аммиачная селитра (ГОСТ 2-85) - 30%
нитроаммофоска (ГОСТ 19691-84) - 10%
аммофос (ГОСТ 18918-85)
Влияние на водные объекты
При попадании в поверхностные воды карбамида аммиачной селитры аммофоса и сложных азотно-фосфорно-калийных удобрений ввиду их хорошей растворимости последние поставляют в воду соединения азота (аммоний нитраты) фосфора (фосфаты) калия.
Эти вещества являясь биогенами при высоких концентрациях могут приводить к эвтрофированию водного объекта связанного с интенсивным ростом фитопланктона и водной растительности снижением содержания растворенного кислорода и угнетением водной фауны.
1. Предельно допустимые концентрации (ПДК) N Р и К для морских вод представлены в табл.2.1.
ПДК для морских вод гм3
2. Расход дождевых вод определяется выражением:
где Нмес - слой осадков за месяц мм;
- коэффициент стока = 0.95;
F - площадь водосбора причала N5 га; F = 3.5 га.
Объемы поверхностного стока а также суммарные расчетные концентрации растворенных минеральных удобрений смываемых одним дождем ( за одни сутки) с территории причала по месяцам представлены в табл.2.2. Содержание нормируемых ингредиентов отдельно по видам минеральных удобрений и во всем стоке отражено в табл.2.3. За основу принята максимальная концентрация растворенных минеральных удобрений (234.2 гм3) за май и сентябрь - ноябрь.
ных мин.удобрений за 1 дождь
Максимальное содержание нормируемых ингредиентов в поверхностном стоке
Процентное содержание в стоке %
Концент рация минер. Удобрения гм3
Концентрация примесей
Расчет разбавления ливневых стоков при сбросе их в акваторию
1. Условия сброса ливневых поверхностных вод
При сбросе ливневых стоков в акваторию порта происходит естественное разбавление в морской воде за счет процессов турбулентной диффузии.
Поскольку азот аммонийный фосфор фосфатов и калий относятся к группе веществ с одинаковым лимитирующим признаком вредности (ЛПВ) (см.табл.2.1) то сумма отношений фактических концентраций в месте контроля к соответствующим предельно допустимым концентрациям (ПДК) не должна превышать единицы.
В табл.3.1 представлены допустимые концентрации нормируемых примесей в контрольном створе расположенном не далее 500 м от места выпуска с учетом условия для ЛПВ а также необходимая степень разбавления для достижения допустимых концентраций.
2. Расчет кратности разбавления
Расчет кратности разбавления поверхностных сточных вод от выпуска причала N 5 произведен по методике Баранника В.А. и Кресина B.C. рекомендованной Методикой расчета предельно допустимых сбросов (ПДС) веществ в водные объекты со сточными водами (М. 1993 г.) для условий сосредоточенного выпуска сточных вод в море.
В основе методики лежит аналитическое решение уравнения турбулентной диффузии с выводом выражения для основного разбавления в виде:
где I - расстояние от места выпуска до контрольного створа или
произвольного участка м;
U - скорость течения мс;
Нср - средняя глубина района разбавления м;
Dr Da - горизонтальный и вертикальный коэффициенты диффузии м2с;
Пн - кратность начального разбавления;
q - расход сточных вод м2с;
Io - расстояние выпуска от берега м.
Для условий выпуска стоков от причала N 5 имеем:
Пн = 1 (безнапорный выпуск);
q = 0.0022 м3с (соответствует суточному расходу 187 м3сут для
максимально загрязненного поверхностного стока);
Io = 0 (береговой выпуск)
Результаты расчета кратности разбавления поверхностных сточных вод на расстояниях I от места выпуска представлены в табл.3.2.
Расстояние от места выпуска I м
Кратность основного
Сравнивая полученные результаты с требуемой степенью необходимого разбавления (табл.3.1) можно отметить что для наиболее концентрированного поверхностного стока формирующегося в мае и сентябре - ноябре нормативное качество поверхностных вод будет соблюдаться на расстоянии 15 м от места выпуска.
Оценка разбавления поверхностных сточных вод показывает что необходимая зона смешения не превышает радиуса 15 м от места выпуска.
В этой связи специальных мероприятий по очистке поверхностного стока в проекте не предусматривается.
2. Охрана труда и ТБ.
В проекте комплекса перегрузки минеральных удобрений предусмотрены технологические решения и мероприятия по созданию условий и обеспечению безопасности труда рабочих и служащих по предотвращению воздействия на работающих опасных и вредных производственных факторов по устранению тяжелых операций при выполнении работ и обслуживании оборудования меры по предупреждению взрывов и пожаров безопасное расположение оборудования для обслуживания и прохода людей безопасное расположение рабочих; - мест обеспечение санитарно-гигиенических условий работающим.
Мероприятия по охране труда сохранению здоровья и работоспособности людей в процессе производственной деятельности на перегрузочном комплексе предусмотрены в соответствии с "Требованиями безопасности труда которые должны учитываться при проектировании новых реконструкции и модернизации действующих морских портов перегрузочных комплексов и отдельных объектов порта" (РД 31.82.01-95) "Правилами охраны труда в морских портах" (ПОТ РО-152-31.82.03.-96) руководящими нормативными документами (РД) строительными и санитарными нормами и правилами (СНиП) нормами технологического проектирования (НТП) и системой стандартов по безопасности труда (ССБТ) приведенными в приложении.
Охрана труда работающих на промышленном объекте осуществляется следующими видами обеспечения безопасности работ в соответствии с РД 31.80.11-95:
- технологическое обеспечение безопасности работ предусматриваемое в проектеи осуществляемое в строительстве;
конструктивное обеспечение безопасности оборудования осуществляемое при разработке конструкторской документации и при изготовлении оборудования машин механизмов устройств и аппаратов;
- организационное обеспечение безопасности работ заключающееся в поддержке оборудования в исправном состоянии и в осуществлении комплекса мероприятий по подготовке к производству работ а также в необходимом надзоре за выполнением правил и инструкций по безопасности труда в период эксплуатации объекта.
- обеспечение безопасности передвижения людей по территории объекта и путям сообщения осуществляемое комплексом организационных и конструктивных мер в период строительства и эксплуатации объекта;
обучение по охране труда рабочих и служащих а также пропаганда безопасных методов труда непосредственно на рабочих местах.
Основные направления разработки мероприятий предусмотренных в технологических решениях по обеспечению безопасности работ по предотвращению воздействия на работающих опасных и вредных производственных факторов с учетом специфики работ на комплексе:
внедрение наиболее механизированной технологии перегрузочных работ;
- применение типового оборудования;
меры по предупреждению взрывов и пожаров;
- безопасное расположение оборудования устройств и конструкций для прохода людей для производства работ для обслуживания и текущего ремонта;
- безопасное расположение и устройство рабочих мест в зонах с удобным доступом и возможностью быстрой эвакуации людей;
- обеспечение санитарно-гигиенических условий: норм освещенности устранения пыли снижения шума и вибрации до санитарных норм обеспечение требуемых парамётров воздуха; эстетизация производственной среды создание оптимального цветоклимата рациональность оборудования и производственной мебели.
Опасные и вредные производственные факторы
На комплексе предусматривается перегрузка следующих минеральных удобрений:
- карбамид (ГОСТ 2081-92) - азотное (466%) удобрение гранулированное белого цвета растворимое в воде. Обладает высокой гигроскопичностью. Не токсичен не взрывоопасен.
- аммиачная селитра (ГОСТ 2-85) - азотное (350%) удобрение гранулированное белого цвета растворимое в воде гигроскопично. При хранении слеживается. При длительном хранении в состоянии слеживаемости постепенно разогревается до разложения и в смеси с горючими веществами может привести к взрыву. Не токсична.
- нитроаммофоска (ГОСТ 19691-84) - сложное азотно" фосфорно". калиевое (по 160%) удобрение гранулированное розового цвета. Не токсичное безопасное. При высокой температуре разлагается.
- аммофос (ГОСТ 18918-85) - фосфорно (500%)-азотное (120%) удобрение гранулированное белого цвета. Обладает высокой гигроскопичностью. Едкое и коррозионное в присутствии влаги вещество. Раздражает кожу человека и слизистые оболочки глаз. При повышенной температуре аммофос выделяет раздражающий газ аммиак.
Вредным производственным фактором для здоровья людей на комплексе у перечисленных минеральных удобрений при нормальных климатических условиях является их пылевыделение в процессе перегрузочных операций: разгрузки ж.д. вагонов загрузки ленточных конвейеров перегрузки (пересыпки) с конвейера на конвейер загрузки (засыпки) удобрений в трюмы судна.
Основные вредные и опасные производственные факторы для здоровья и жизни работников на проектируемых объектах комплекса перегрузки минеральных
удобрений (По ГОСТ 12.0.003-74 и по Приказу Минздравмедпрома России и Госкомсанэпиднадзора России от 05.10.95 №28088):
Движущиеся железнодорожные вагоны (Железнодорожные пути станция разгрузки вагонов).
Подвижные части производственного оборудования (Станция разгрузки вагонов перегрузочные станции ленточные конвейеры судопогрузочная машина).
Повышенная запыленность (взвешенные вещества) воздуха рабочей зоны (Станция разгрузки вагонов перегрузочные станции конвейерные галерей судопогрузочная машина трюмы судов);
Повышенный 'уровень шума (Компрессорная лстанция вентиляционные камеры').
Повышенный уровень вибрации - (Компрессорная станция воздушные вентиляторы).
Опасный уровеньнапряжения электрического тока (Линии и сети электроснабжения и электропитания электрорборудование и эектроаппаратура электрическое освещение .наружное и внутреннее пульты .управления трансформаторная подстанция).
Повышенный уровень статического электричества (Технологическое оборудование электрическое оборудование и установки).
Предусмотренные в проекте мероприятия по снижению пылевыделения на комплексе приведены в арх. № 61139 (Том 1. Пояснительная записка п. 5.25).
Мероприятия по снижению шумаи вибрации на объектах комплекса приведены втомжеарх.№61139(п.4.73).
Санитарно-бытовое обслуживание работников комплекса представлено также в арх. №61139(п.4.9.1).
В нижеследующих разделах приведено описание разработанных в проекте основных мероприятий по охране труда работающих на отдельных объектах комплекса.
В тексте в конце предложений в скобках приведены ссылки на нормативные документы и номер пункта на основании требований которых разработано конкретное мероприятие по обеспечению безопасности и охраны труда.
Основные мероприятия по охране труда работающих
1. Генеральный план и транспорт
Для создания условий по обеспечению безопасности людей здания и сооружения комплекса по перегрузке минудобрений сгруппированы с учетом их общности назначения и функций (РД 31.82.01-95 п. 1.2.6).
Железнодорожные пути для подачи груженых вагонов и отправления порожних расположены на горизонтальных площадках.
Здания сооружения и устройства расположены на расстоянии более 61 м от железнодорожных путей (ГОСТ 9238-83).
Выходы из зданий находящихся вблизи ж.д. путей предусмотрены в сторону от них (ПОТ РО-152-31.82.03-96 п.2111).
Рычагй управления ж.д. стрелками- имеют удобный подход к ним и расположены на безопасном расстоянии от прилегающих путей. Рычаги стрелок в нерабочем положении не выступают выше уровня покрытия территории. Стрелочные переводы закрытого типа;
К зданиям и сооружениям по всей их длине обеспечен подъезд пожарных автомобилей (СНиП 11-89-80 п.3.46).
На территории комплекса предусмотрена надежная система водоотвода гарантирующая отвод поверхностных вод в систему канализации сточных вод. Для обеспечения отвода поверхностных (дождевых) вод приняты уклоны (0005-002) поверхности территории (РД 31.3.01.01-93). У всех канализационных люков и колодцев предусмотрены закрытия (ПОТ РО-152-31.82.03-96).
2. Станция разгрузки вагонов
Станция размещается в закрытом здании оборудованном со стороны въезда и выезда вагонов кирпичными тамбурами. Для предотвращения выделения пыли из станции в тамбурах устанавливаются 4 ряда гибких шторных укрытий.
Бункеры для ссыпки удобрений из вагонов закрыты сверху металлическими решетками с ячейками 200 х 200 мм (ПОТ РО-152-31.82.03-96 п.4.5.5).
Станция разгрузки вагонов и пересыпные рукава с питателей на магистральный конвейер оборудованы аспирационными установками для обеспыливания воздуха.
Помещение служб инженерного обеспечения управления производственным процессом санузел и помещение обогрева для работников выделены в изолированную блок-пристройку имеющую обособленные выходы наружу вне зоны пыления.
Для защиты органов дыхания и кожных покровов обслуживающий персонал внутри станции (в зоне пылевыделения) должен работать в пыленепроницаемой спецодежде и в противоаэрозольных фильтрующих респираторах (ПОТ РО-152-31.82.03-96 Приложение 8п.5.1 и табл. 2). В связи с концентрацией пыли в воздухе рабочей зоны внутри станции разгрузки вагонов достигающей по расчету 168 мгм3 рабочими должны применяться респираторы марок ПРШ-471 Астра-2 или Ф-62Ш.
3. Перегрузочные работы -
Все перегрузочные работы на комплексе минудобрений запроектированы с применением специализированного перегрузочного оборудования в соответствии с требованиями "Правил охраны труда в морских портах" (ПОТ РО-152-31.82.03-96 пп.4.1 4.5 и 13.12) "Руководства по технологическому проектированию морских портов" (РД31.3.01-93) и "Системы стандартов безопасности труда". -
Для обеспечения безопасности и охраны труда работающих в соответствиис "Санитарными нормами проектирования промышленных предприятий" (СН 245-71 раздел 1 п. 1.5) в проекте перегрузочного комплекса предусмотрено:
комплексная механизация автоматизация и дистанционное управление перегрузочным процессом;
- размещение конвейеров в закрытых галереях;
- автоматическая сигнализация об аварийных ситуациях на конвейерных линиях и перегрузочных машинах;
- максимальное уплотнение стыков и соединений в технологическом оборудовании в конвейерных галереях и перегрузочных узлах для предотвращения пылевыделения в процессе производства.
Проект стационарных ленточных конвейеров (конвейерных линий) и необходимых сооружений и устройств (галерей разгрузочных перегрузочных и погрузочных станций) выполнен с соблюдением норм и правил СНиП 2.05.07-91 (раздел 8 п.8.36) которыми для обеспечения безопасности работ в системах конвейерных линий предусмотрено:
централизованное управление и контроль за отдельными установками и системой в целом (диспетчерское управление);
возможность местного управления конвейерами во время ремонтных и наладочных работ;
местная блокировка предотвращающая дистанционный пуск конвейера с пульта управления;
- устройства для контроля натяжения обрыва пробуксовки и схода ленты;
- громкоговорящая связь;
- телефонная связь между пультами управления конвейерами;
подача предупредительного звукового сигнала при пуске конвейеров;
- сигнализация о работе механизмов на центральном пульте управления;
- последовательный запуск приводов конвейерной линии в направлении противоположном потоку транспортируемого груза;
- возможность остановки каждого конвейера аварийными выключателями из любого уголка конвейерной линии со стороны основного прохода;
- остановка конвейера при обрыве или сходе ленты с барабана;
- остановка конвейера работающего на спуск при превышении номинальной скорости ленты;
автоматическая остановка всех предыдущих конвейеров при аварийной остановке любого конвейера а также при превышении допустимого уровня груза в бункерах или в местах пересыпок.
Ленточные конвейеры размещаются внутри закрытых галерей. Для безопасности обслуживания конвейеров в галереях предусматриваются с .обеих сторон проходы шириной075 м. (ПОТ РО-152-31.82.03-96 п: 4.5.1).
Для обеспечения естественной вентиляции в галереях предусмотрены открывающиеся окна со стороны основного прохода (СНиП 2.05.07-91 п. 823)
В необходимых местах предусмотрены эвакуационные выходы из галерей и переходные мостики над конвейерами шириной 10 м со сплошным--настилом с отбортовкой по низу на высоту 015 м и с ограждающими перилами высотой 1.0 м (СНиП 2.05.07-91 п. 8.25).
Перегрузочные (пересыпные) станции размещены в крытых зданиях.
В проекте предусмотрено оснащение перегрузочныхмашин необходимыми элементами системы технических средств безопасности: оградительными предохранительными и тормозными устройствами блокировками сигнализаторами опасности опознавательной окраской и предупреждающими знаками дистанционным управлением . специальными средствами обеспечения электробезопасности и другими средствами защиты (РД 31.82.01-95 п. 1.6.1).
Ко всем механизмам предусмотрен безопасный подход. Все движущиеся и вращающиеся части прикрыты съемными кожухами и ограждениями допускающими удобный осмотр смазку и ремонт (ПОТ РО-152-31.82.03-96 п. 4.1.5). Головные и хвостовые барабаны конвейеров имеют ограждения препятствующие доступу людей к ним во время работы конвейеров (СНиП 2.05.07-91 п. 8.21).
В концевых частях конвейеров устанавливаются кнопки "Стоп" ярко-красного цвета и розетки для подключения низковольтного освещения при осмотре и ремонте (ПОТ РО-152-31.82.023-96 п. 4.5.8).
Приводы натяжные устройства конвейеров и места перехода груза с одной ленты на другую оборудуются легкосъемными ограждениями сблокированными с приводами конвейера для его отключения при снятии ограждения (ПОТ РО-152-31.82.03-96 п. 4.5.10).
Для устранения пылевыделения каждый пересыпной рукав с конвейера на конвейер перегрузочных станций оборудован аспирационным устройством (ПОТ РО-152-31.82.03-96 п. 4.5.7). Аспирационные установки размещены в одних зданиях с перегрузочными станциями.
В связи с высокой концентрацией пыли в воздухе рабочей зоны внутри перегрузочных станций достигающей по расчету 719 мгм3 обслуживающий персонал должен работать в пыленепроницаемой спецодежде ив противоаэрозольных фильтрующих респираторах марки ПРШ-471 для защиты органов дыхания.
В береговой погрузочной галерее для уменьшения пылевыделения в узле передачи груза с берегового конвейера на судопогрузочную машину хвостовая часть машины соединена со сбрасывающей тележкой ленточного конвейера.
У судопогрузочной машины передвигающейся по наземным рельсовым путям расстояние от нижней габаритной точки машины до пола составляет более 20 м а расстояние от нижних выступающих частей машины до расположенного в зоне ее действия оборудования превышает 07 м (РД 31.82.01 -95 п. 1.6.9) что обеспечивает безопасный проход для людей. Движущиеся токоведущие нагревающиеся части судопогрузочной машины прочно закрыты укрепленными съемными ограждениями допускающими удобный осмотр и "проведение ремонтных работ (ПОТ: РО-152- 31.82.03-96 п. 4.1.5).
Все площадки и проходы расположенные на высоте и предназначённыё для обслуживания механизмов перегрузочных машин имеют леерное ограждение высотой 10 м со сплошной зашивкой по низу высотой 0151м с промежуточным леером на высоте 05 м (Правила У и БЭ п. 4.133).
Для обслуживания перегрузочного оборудования на высоте более 10 м и доступа к нему предусматриваются стационарные лестницы и площадки с ограждением.
Для уменьшения пылевыделения в процессе работы продольная щель береговой погрузочной галереи имеет по всей длине укрытие из прорезиненной ткани а судопогрузочная машина оборудована телескопической трубой с пылеподавляющей насадкой.
Не допускается нахождение людей в трюмах во время погрузки.
4. Компрессорная станция
Компрессорная станция размещена в пристройке к зданию станции разгрузки вагонов в отдельном помещении изолированном от здания глухой несгораемой стеной (152 РО-31.83.01-96 п. 1.20.2).
Двери и окна компрессорной станции открываются наружу. Полы - ровные с нескользящей поверхностью из несгораемого твердого материала.
Движущиеся части компрессоров и электродвигателей защищены кожухами с металлическими ограждениями высотой 10 м со сплошной защитой в нижней части на высоту 0 15 м.
Все каналы и приямки перекрыты плитами из рифленой стали.
Для обеспечения безопасности проходов людей и обеспечения возможности монтажа оборудования компрессора и электродвигателя в машинном зале предусмотрены проходы шириной не менее 15 м а между оборудованием и стенами здания - не менее 10 м (152 РО-31.83.01-96 п. 1.20.8).
У всасывающих трубопроводах предусмотрена теплоизоляция.
Для уменьшения шума предусматривается звукоизоляция трубопроводов сжатого воздуха пусковых трубопроводов и трубопроводов концевых холодильников и выпуск воздуха при пуске компрессора в продувочный бак а из него в
шумопоглащающий выхлопной трубопровод в атмосферу (152 РО-31.83.01-96 п.п. 1.20.9 и 1.20.10).
Для оператора предусматривается изолированное от шума помещение.
Для снижения влияния вибрации компрессоры устанавливаются на демпферирующие (виброгасящие) фундаментные прокладки.
Воздухосборники вынесены наружу компрессорной станции.
5. Электробезопасность
Для обеспечениябезопасности работающих от повышенного напряжения электрического тока впроекте предусмотрено применением подземной (в траншеях) кабельной прокладки линий и сетей электроснабжения; безопасная изоляция и заземление металлических корпусов и частей электрооборудования в соответствии с требованиями ПУЭ Правил ТБ при эксплуатации электроустановок .потребителей СН 174-75 ГОСТ 12:1.019-79 ГОСТ 12.1.030-81 ГОСТ 2.2.061-81 и ГОСТ 12.3.002-75.
У зданий сооружений и перегрузочного оборудования предусмотрена молниезащита от атмосферного электричества путем молниеотводов (заземлйтелей) в соответствии с Указаниями СН 305-77.
Узлы управления автоматического пожаротушения размещены в изолированных помещениях.
Аварийная ДЭС установлена в отдельном помещении здания станции разгрузки вагонов.
Для подключения переносных светильников ремонтного освещения в галереях и перегрузочных станциях предусмотрены низковольтные розетки 36 В.
Для защиты людей от статического электричества у технологического оборудования и электроустановок предусмотрены заземляющие устройства для снятия зарядов у всех металлических и электропроводящих частей оборудования в соответствии с требованиями ПУЭ 152 РО-31.83.01-96 (п. 27) СН 305-77 ГОСТ 12.1.030-81 ГОСТ 12.2.061-81 ГОСТ 12.4.124-83. Заземляющие устройства для защиты от статического электричества объединены с заземляющими устройствами для электрооборудования (СН 102-76).
Работа персонала в зоне опасного уровня напряжения электрического тока и при обслуживании технологического оборудования и электроустановок с повышенным уровнем статического электричества должна производиться с применением средств индивидуальной защиты: спецодежды изолирующей обуви и резиновых перчаток (ГОСТ 12.4.011-89 ГОСТ 12.4.103-83 и ГОСТ 12.4.104-83).
Внедрение и выполнение предусмотренных в проекте технологических мероприятий по охране труда и применение соответствующих должностных инструкций обеспечит создание необходимых условий труда безопасность жизни и здоровье работников комплекса в процессе их трудовой деятельности в соответствии с "Основами законодательства Российской Федерации об охране труда" (1993г.) по осуществлению прав работников на охрану труда (Статья 4) и исполнению обязанностей работодателей по обеспечению охраны труда на предприятии (Статья 9).
Drawing3.dwg

грунтовкой ВЛ-02 ГОСТ 12707-77 и покрыть эмалью ПФ-115 ГОСТ 6465-76.
Металлоконструкцию очистить от ржавчины и окалины
с измерением по ГОСТ 3242-79.
Контроль качества сварных швов выполнить внешним осмотром
Сварные швы выполнить по ГОСТ 5264-80 и ГОСТ 11534-75 электродом
Неуказанные педельные отклонения размеров диаметров: H14
Предельные отклонения размеров: ±IT142.
Предельные отклонения размеров диаметров: по H14
Технические требования.
Редуктор ЦД2-100М-16-1
Мощность двигателя- 15 кВт
Производительность- 600 тч
Натяжное устройство 1
Отклоняющий барабан 4
Промежуточный ленточный
Частота вращения двигателя поз.1- 1470 1мин
Частота вращения двигателя поз.2- 735 1мин
Двигатели 4A250S8Y3 - оба.
Мощность двигателя поз.1- 37 кВт
Мощность двигателя поз.2- 37 кВт
Техническая характеристика:
Привод конвеера переменной
Муфта предельного момента
Стойка с подшипником
Промежуточный наклонный
Мощность двигателя- 37 кВт
Длина трассы - 24.6 м
Размеры для справок.
Ролик грузовой ветви
Ролик холостой ветви
Грузовое натяжное устр-во
Мощность двигателя- 22 кВт
Длина трассы - 185 м
Двигатель 4A200M6Y3.
ДИПЛОМ экономика.doc
Промышленный потенциал России по производству минеральных удобрений может полностью удовлетворить потребности сельского хозяйства страны и ежегодно экспортировать продукцию на сумму около двух миллиардов долларов. Однако в настоящее время в связи с отсутствием платежеспособного спроса со стороны сельхозпроизводителей поставки минеральных удобрений селу сократились в десять раз. В целях недопущения снижения плодородия почв и обеспечения проведения агротехнических мероприятий Правительство Российской Федерации приняло постановление предусматривающее проведение конкурса среди производителей минеральных удобрений на право поставки средств химизации сельскохозяйственным товаропроизводителям. Постановлением установлено что цены и тарифы на природный газ и электрическую энергию потребляемую победителями конкурса а также на сырье для производства удобрений будут понижены до 50 %. Министерству путей сообщения предписано снизить тарифы на железнодорожные перевозки на 30%.
предыдущего года соответственно на 385% и 865%.За первые пять месяцев текущего года на предприятии выработано 133 млн.т аммиака и 4513 млн.т. карбамида. Наибольшие объемы данного минерального сырья отправлены в Мексику Гондурас Бразилию.
Экспортные возможности российской промышленности минеральных удобрений обеспечиваются обширными залежами фосфоритных и азотосодержащих руд а также природного газа. В настоящий момент объем экспорта минеральных удобрений составляет свыше 74 млрд ам. долларов в год и является третьим по величине в структуре российского бизнеса.
В настоящий момент при условии повышения платежеспособности российских сельскохозяйственных предприятий существует перспектива увеличения внутреннего потребления удобрений поскольку в последние годы наблюдался спад объемов вноса удобрений на гектар посевной площади до 85 кг на гектар в то время. Как скажем в Китае в почву вносится до 300 кг удобрений на гектар. Этот фактор может повлиять на экмпорт удобрений в долгосрочной перспективе. Однако его влияние может быть значительно сокращено появлением и значительным ростом рынков минеральных удобрений в частности в Южной и Юго-Восточной Азии и Южной Америке.
Крупнейшими импортерами поташа из стран СНГ в 2000 году являлись Бразилия (546 000 тыс.т) Бельгия (286 000 тыс.т) Италия (226 000 тыс.т) Малайзия (303 000 тыс.т) Финляндия (320 000 тыс.т.) Япония (206 000 тыс т.) Индия (200 000 тыс.т) и Польша (183 000 тыс.т).
Как следует из оценки специалистов компании Осеап 8Ыррш§ Соп-зи11ап15 в кратко- и среднесрочной перспективе спрос на минеральные удобрения на внешнем рынке в ближайшие десять лет останется достаточно высоким хотя в отношении России на этот прогноз повлияет состояние сельского хозяйства Внутренний спрос на продовольствие и что немаловажно обменный курс рубля как впрочем и в отношении всех остальных составляющих российской внешней торговли.
Наибольший спрос на минеральные удобрения в ближайшее деся-тилентие ожидается со стороны развивающихся стран даже несмотря на значительные инвестиции в их собственные производственные мощности. Рост населения посевных площадей и среднего ВНП на душу населения безусловно ведут к росту потребления минеральных удобрений в Южной и Восточной Азии а также в Латинской Америке Африке и на
ближнем Востоке т.е. в регионах геогрефически тяготеющих к портам Черного моря.
До 2005 года ожидается рост мирового портебления удобрений (см.таб.№7) примерно на 29 млн. тонн из которых на 16 млн. тонн претендуют страны Юго-Восточной Азии 6 млн. тонн - страны Центральной и Восточной Европы и на 7 млн. тонн - прочие страны. В этой связи будет также наблюдаться значительный рост спроса на морские перевозки удобрений который в ближайшее десятилетие составит примерно 170 миллиардов тонно-миль. Из них почти 72 % придется на Азиатские рынки и 185% на рынки Латинской Америки (8).
Прогнозируемый мировой спрос на минеральные удобрения к 2005 году млн.тонн
Несмотря на значительные мощности по производству минеральных удобрений у СССР не имелось достаточного количества специализированных глубоководных терминалов по обработке этих грузов. На Дальнем Востоке у России имелся единственный такой терминал на причале №2 в порту Находка. Однако в 80-х он был снесен и отправка минеральных удобрений через него в северокорейский порт Найджин была прекращена. Однако позднее в порту Ванино на территории крытого склада был сооружен небольшой причальный комплекс для выгрузки удобрений из жд вагонов и последующей погрузки их в трюма с помощью портальных кранов.
Проектная мощность этого комплекса - 150 000 тонн удобрений в год.
На Балтике основным'портом по перевалке калийных удобрений является латвийский порт Вентспилс. Специализированный комплекс по переработке удобрений в этом порту был пущен в эксплуатацию в конце 1970-х годов. С того времени по 1995 год им были обработаны свыше 32 млн. тонн грузов. При этом в 1994 и 1995 годах были переработаны соответственно 38 и 43 млн. тонн удобрений. На этом терминале ежегодно обрабатываются 40 - 60 000 вагонов с калийными удобрениями следующими из России и Белоруссии. Комплекс по перевалке удобрений включает станцию по разгрузке жд вагонов рассчитанную на единовременную обработку 12 вагонов а также крытые склады для хранения двух видов удобрений вместимостью соответственно 88 000 и 81 000 тонн. На терминале производится погрузка судов дедвейтом до 45 000 тонн до осадки 135 метров. Погрузка осуществляется двумя погрузочными машинами РНВ производительностью 6000 -12 000 тонн в сутки.
В 1995 году в порту Клайпеда вступил в эксплуатацию мини-терминал по обработке минеральных удобрений с оборудованием и конвейерными линиями поставленными компанией Eurotrans cont. Этот комплекс предназначен для обработки вагонов по прямому варианту и имеет производительность 300 тонн в час. На Севере России планируется реконструкция причала 1419 для переработки минеральных удобрений в объеме 2 млн.тонн в год.
Крупнейшим комплексом по переработке удобрений на Черноморском бассейне является порт Южный. Он имеет две погрузочные линии для обработки аммиака и две линии для обработки мочевины мощностью соответственно 4 и 2 млн. тонн в год. В 1995 году через Южный было экспортировано 07 млн. тонн аммиака Тольяттинского химкомбината и 06 млн. тонн метанола других российских предприятий. Комплекс включает два крытых склада рассчитанных на 45 000 тонн мочевины каждый конвейерные линии общей длиной около 16 км а также станцию разгрузки жд вагонов. Погрузочные машины имеют производительность до 700 тч и 300 тч для навалочных и тарированых грузов. На терминале могут обрабатываться суда осадкой до 125 метров дедвейтом до 55-60 000 тонн.
Обработка удобрений с использованием специализированных двадцатифутовых контейнеров ведется на причале К4 Одесского порта стивидорной компанией Sderotgide int.. Мощности причала позволяют обрабатывать ежесуточно 300 - 500 контейнеров мочевины. Глубина у причала составляет 115 метров длина причала - 290 метров.
2 . ВЫВОДЫ И ПРЕДЛОЖЕНИЯ
) отправлять груз маленькими партиями ( максимум 7000 т ) что приводит в конце концов к большой цене перевозки морем и становится невыгодным импортеру (если контракт заключен на условиях ФОБ - Новороссийск) или экспортеру ( если контракт заключен на условиях СИФ -порт направления);
) использовать порты Украины при экспорте удобрений так как они имеют специализированные терминалы для хранения груза и поэтому заводы-экспортеры могут накапливать груз в портах погрузки.
Таким образом можно сделать вывод что для привлечения устойчивых грузопотоков отечественных заводов-экспортеров порту Новороссийск необходим специализированный комплекс переработки минеральных удобрений с накопительным терминалом.
Ток = Стн ((Прн-Пвт)*Нпн) (1)
где Ток - период окупаемости нового накопителя лет.
Стн - стоимость постройки накопителяам.доллтонна.
Прн - производительность накопителя тоннгод.
Нпн - норма прибыли ам.доллтонна.
Ток = 4 000 000 ((2 000 000-600 000)* 114) = 25 года.
Таким образом видим что новый накопитель для удобрений окупится менее чем через три года после ввода его в эксплуатацию.
Рассчитаем ежегодный экономический эффект от ввода в эксплуатацию накопителя совместно с терминалом по формуле (2):
Энак = (При - Пвт)*Нпн (2)
где Энак - ежегодный экономический эффект от ввода в эксплуатацию накопителя совместно с терминалом ам.долл.
Энак = (2 000 000 - 600 000)* 114 = 1 596 000 ам.долл.
Кроме этого в свете сделанных выводов можно представить следующие замечания по их практическому применению:
) Необходимо создание единой базы данных для отслеживания грузопотоков следующих через Новороссийский порт анализа качественного уровня обслуживания клиентов в порту и их прибыльность для порта.
) На основании данных требуется сформировать стратегию развития компании которая смогла бы определить приоритеты и цели привлечения и обработки в порту конкретных грузопотоков а также развития мощностей порта и его организации в соответствующем направлении.
Что касается порта С.-Петербург он в настоящее время уже начал реализацию программы строительства специализированных комплексов. За счет кредита Российского Сбербанка в объеме 15 млн. долларов США выделенного на пять лет в порту начаты работы по строительству нового терминала для минеральных удобрений производительностью 3 млн. тонн в год. Притоку удобрений в порт способствуют более приемлемые по сравнению со странами Балтии железнодорожные тарифы МПС.
При возможном снижении железнодорожных тарифов и реализации указанного выше у портов Новороссийск и С.- Петербург имеются все возможности для обработки грузопотоков экспортных минеральных удобрений причем для российских экспортеров они будут более благоприятны чем порты стран Балтии и Украины.
Однако для строительства указанных терминалов для хранения и перевалки грузов необходима государственная поддержка и долгосрочное финансирование проектов.
ДИПЛОМ Технология.doc
Комплекс по перегрузке минеральных удобрений рассчитан на годовой грузооборот Qpгод=2 млн.тгод.
)Суточный расчётный грузооборот причала составляет:
Qpсут= Qpмес (30.5-tн.р)=0.16(30.5-3)=0.0058 млн.тсут = 5800 тсут
где: tн.р=3 cут – количество нерабочих дней по метеоусловиям в наиболее
Qpмес= Qpгод12 = 212=0.16 млн.тмес – месячный грузооборот комплекса.
Принимаем что через склад проходит годового грузопотока т.е.
Коэффициент складочности: αск= Qск Qн= 0.5
где Qн= Qpгод – навигационный грузооборот.
)Транспортные средства их характеристика режим поступления под обработку условия грузовой обработки в порту.
Фактическая загрузка судна:
Dф=c D = 0.8* 500000= 40000 т
где: c=0.8 – коэффициент использования грузоподъёмности судна.
Среднее количество судов поступающих под обработку в порт в течении суток:
nc=QнКн DфTн = 2000000* 1 40000*360 = 0.14
Средний интервал времени между судами:
Тис=24nc=240.14=172.8 часа
Число вагонов подаваемых на причал под обработку в течении суток:
nв=QнКнТнGф = 2000000*1 360*56 = 100 вагонов
где: Gф= в GB = 0.8*70= 56 т - фактическая загрузка вагона.
GB=70 т – паспортная загрузка вагона.
в=0.8 – коэффициент использования грузоподъёмности вагона.
Число подач вагонов в сутки:
mпод= nв nпод= 10020=5 подач
где: nпод=20 – число вагонов в подаче.
Средний интервал между подачами:
ив=24 mпод = 245 = 4.8 часа
)Определение вместимости и площади склада:
Расчётную вместимость склада принимаем равной вместимости максимального расчётного судна т.е. Еск=50000 т
Foc=Eск Киqск = 50000 0.85*10 6000 м2
где: Ки=0.85 – коэффициент использования основной площади склада.
qск=10 тм2 – допустимая нагрузка на причал.
Принимаем склад 200х30 м ( 4 бункера по 50х30 м каждый). Каждый бункер рассчитан на 15000 т удобрений.
)Пропускная способность и минимально необходимая интенсивность обработки транспортных средств на причале.
Нормативная пропускная способность:
[Пс]=24Dф[Тс]=24*40000417=2302 тсутки
где: [Tc] = [Tгр]+Tвсп = 412+4.5=417 часов – норма времени стоянки судна у
[Tгр] = Dф [J] = 40000 97 =412 часов – норма времени стоянки судна под
[J] = 97 тчас – судо-часовая норма интенсивности грузовых работ.
Твсп = 4.5 часов – норма времени на выполнение маневровых и
вспомогательных операций с судами.
Принимаем [Пс]= мах (Qpc [Пс]) = 5800 тсутки.
Минимальная необходимая интенсивность грузооброботки судна:
Jc=Прс Кивtоп=5800 0.98*19=311.5 тчас
где: Кив= [Tгр] ([Tгр] + Tвсп) = 0.98 – коэффициент использования причала по
tоп=Кпзtсм = 0.85*3*7.5 = 19 часов – эффективное время работы
оборудования причала в течении суток при трёхсменной работе.
tсм=7.5 часа – продолжительность смены.
Для обработки на причале расчетного грузооборота поступающего в железнодорожных вагонах пропускная способность перегрузочного оборудования фронта обработки вагонов должна быть достаточной чтобы было выполнено условие:
где: [Пв] – нормативная пропускная способность при обработке вагонов.
[Пв]=24nвпGф [в] = 20*56*241.6 = 16800 тсутки
где: [в] = 1.6 часа – норма времени обработки подачи вагонов.
Пв= Qcp = 5800 т сутки
Минимальная интенсивность оборудования занятого на обработке подач вагонов необходимая для обеспечения переработки расчётного суточного грузооборота по прибытию в железнодорожных вагонах и выполнения норм времени обработки подачи вагонов:
Jв=Пвр Кивtоп = 5800 1*19 = 305 тчас
)Продолжительность стоянки судна у причала под грузовой обработкой.
Продолжительность стоянки судна складывается из затрат времени на швартовые операции погрузку судна с учётом технологических перерывов в процессе грузовой обработки и оформление документов.
а) Продолжительность стоянки судна при производительности комплекса
00 т час (после модернизации):
Тс= Тгр + Т всп = 36.7 + 4.5 = 41.22 часа=1.7 суток
где: Тгр= Dф( NфрРсtопК1К2) = 40000(1*1200*22.5*0.97)=1.53 суток = 36.7 часа
Твсп=4.5 часа – норма времени на вспомогательные операции.
б) Продолжительность стоянки судна при производительности комплекса
0 тчас (до модернизации):
Тс= Тгр + Т всп = 73.3 + 4.5 = 77.8 часа
Тгр= Dф( NфрРсtопК1К2) = 40000(1*600*22.5*0.97)=3.05 суток = 73.3 часа
)Пропускная способность причала:
а) С использованием склада:
Пс=DфТс=400001.7=23529 тсутки
б) Без использования склада:
Пс=DфТс=400003.05=13114 тсутки
)Коэффициент резерва пропускной способности:
а) С использованием склада:
Крез=ПсQpc = 235295800=4.0
Крез=ПсQpc = 131145800=2.26
ДИПЛОМ ТО-1.doc
1 Работа и управление машинами специализированных конвейерных комплексов для навалочных грузов (СККН).
1.1 Все перегрузочные машины на рельсовом ходу по окончании работы должны устанавливаться на противоугонные устройства а их рабочие органы - в нерабочее положение в соответствии с требованиями заводской (фирменной) документации обеспечивающее возможность осмотра безопасной стоянки и работы других машин. При отсутствии соответствующих требований в заводской (фирменной) документации необходимо установить:
- стрелу реклаймера - в горизонтальной плоскости под углом 15-20° от оси складского конвейера а роторный захват опереть не оставляя его на весу;
- стрелу стакера - в горизонтальной плоскости в опущенном положении под углом 15-20° от оси складского конвейера;
- стрелу (консоль) судовой погрузочной машины - в максимально поднятом (втянутом) положении. При этом передвижная тележка телескопической трубы должна отгоняться в крайнее заднее положение а телескопическая труба - полностью втягиваться.
1.2 Система централизации и блокировки (СЦБ) на участке разгрузки вагонов должна эксплуатироваться в соответствии с требованиями заводской (фирменной) документации. При отсутствии таких требований следует руководствоваться положениями Инструкции по техническому обслуживанию устройств сигнализации централизации и блокировки (М.: Транспорт 1989).
1.3 Механизированные и автоматизированные устройства на путях откатки а также железнодорожные пути должны эксплуатироваться в соответствии с требованиями заводской (фирменной) документации. При отсутствии таких требований следует руководствоваться положениями Инструкции по техническому обслуживанию устройств механизированных и автоматизированных сортировочных горок (М.: Транспорт 1991) Инструкции по техническому содержанию клещевидно-весовых вагонных замедлителей типа КВ-62М (М.: Транспорт 1975) Инструкции по текущему содержанию железнодорожного пути (М.: Транспорт 1974).
1.4 Размораживающие устройства должны эксплуатироваться в соответствии с требованиями Типовой инструкции по обслуживанию конвективных и комбинированных размораживающих устройств (тепляков) на тепловых электростанциях (М.: Союзтехэнерго 1981).
1.5 Оборудование для заливки масла в буксы в пунктах технического осмотра железнодорожных вагонов должно эксплуатироваться в соответствии с требованиями заводской (фирменной) документации а также Инструкции по ремонту и обслуживанию букс вагонов с подшипниками скольжения
(М.:Транспорт 1977) Правил технической эксплуатации металлических резервуаров и инструкции по их ремонту (М.:Недра 1971).
1.6 Кусковатость смерзшегося и слежавшегося груза в случае необходимости его перегрузки на СККН должна быть в пределах допускаемых требованиями заводской (фирменной) документации на перегрузочные машины. При несоблюдении этого условия работа машин должна быть прекращена.
2 Неисправности при которых работа перегрузочных машин СККН должна быть прекращена
2.1 Работа конвейеров не допускается при:
а) истекшем сроке технического освидетельствования;
б) возникновении неисправностей аналогичных указанным в 9.3.1;
в) продольном порыве ленты длиной более 200 мм при пробоине размером более 50х50 мм;
г) пробуксовке ленты на приводных барабанах;
д) неисправности натяжных устройств (например заедании балласта сходе с рельсов натяжной тележки износе канатов цепей выходящем за пределы допускаемых норм сходе канатов с блоков);
е) неисправности роликовых опор грузовой и холостой ветвей;
ж) неисправности тормозов и устройств аварийной остановки;
и) неисправности устройств по очистке ленты;
к) неисправности громкоговорящей связи и сигнализации о запуске конвейеров;
л) неисправности реле скорости датчиков завала фотореле и других элементов автоматизации и контроля.
2.2 Работа стакера реклаймера кратцер-крана машины МВС и судовой погрузочной машины не допускается при:
а) возникновении неисправностей аналогичных указанным в 10.2.1;
б) неисправности клапанов предельного давления измерительных приборов гидросистем и гидропривода роторного колеса реклаймера;
д) неисправности звуковой сигнализации;
е) сломанных зубьях ковшей роторного колеса реклаймера деформированных пластинах и скребках кратцер-крана витков спиралей и режущих зубцов шнеков;
ж) неисправности устройства выравнивания хода кратцер-крана;
и) неисправности привода выдвижения телескопической трубы судовой погрузочной машины.
2.3 Работа вагоноопрокидывателя электротележки-толкатепя и маневрового устройства не допускается при:
а) возникновении неисправностей аналогичных указанным в 9.3.1;
б) повреждении стенок разгружаемых вагонов неисправностях их ходовой
в) неисправностях приводной системы зажимов;
г) заедании платформы при опрокидывании;
д) неисправности световой и звуковой сигнализации;
е) других неисправностях указанных в заводской (фирменной) документации угрожающих безаварийной работе вагоноопрокидывателя электротележки-толкателя маневрового устройства и безопасной работе людей.
2.4 Работа маршрутов ' не допускается при:
а) неисправностях любой из перегрузочных машин составляющих маршрут согласно 8.2.1; 8.2.2; 8.2.3;
б) невозможности осуществить последовательный запуск или остановку маршрута;
в) неисправностях системы централизованного управления машинами в ЦПУ;
г) неисправностях системы оповещения и связи с машинами;
д) других неисправностях указанных в заводской (фирменной) документации.
3 Техническое обслуживание перегрузочных машин СККН
3.1 Периодическое техническое обслуживание перегрузочных машин должно состоять из ТО-1 и ТО-2. Состав и периодичность ТО-1 приведены 5.6.2.2
3.2 В состав ТО-2 должны входить следующие работы:
а) проверка технического состояния составных частей перегрузочной машины в объеме проверок при ТО-1 и опробование их в работе;
б) замена быстроизнашивающихся деталей: отдельных роликов устройств по очистке лент конвейеров футеровочных листов пересыпных устройств
других деталей и оборудования машин.
3.3 Примерный состав проверочных работ при периодическом техническом обслуживании составных частей перегрузочных машин приведен в приложении и включает только работы специфичные для перегрузочных
машин СККН. Состав проверочных работ при периодическом техническом обслуживании этих машин должен уточняться портами с учетом требовании заводской (фирменной) документации.
3.4 Техническое состояние отдельных элементов перегрузочных машин должно определяться в соответствии с требованиями заводской (фирменной) документации а при отсутствии указанных требований допускается использовать соответствующие нормы дефектации.
3.5 Для сокращения сроков простоя перегрузочных машин следует выводить на техническое обслуживание группы технологически связанных перегрузочных машин.
3.6 Периодичность и продолжительность выполнения ТО-2 маршрутов такие же как для кранов и перегружателей в соответствии с 5.2.1.
4 Технический надзор и техническое освидетельствование
4.1 Технический надзор за содержанием машин СККИ должен производиться в соответствии с указаниями раздела 8.
4.2 Дополнительно к перечисленным в 8.1.4 ответственными по надзору в порту должны быть назначены:
- за безопасной эксплуатацией рельсовых путей сбрасывающих тележек пути которых установлены на раме металлоконструкции конвейера - инженерно-технические работники отдела механизации;
- за исправностью и безопасной эксплуатацией телефонной и громкоговорящей связи системы промышленного телевидения - инженерно-технические работники участка связи порта.
4.3 Технический надзор за исправностью и безопасной эксплуатацией систем вентиляции и аспирации должен осуществляться в соответствии с требованиями ГОСТ 12.4.021.
4.4 При укладке и содержании рельсового пути передвижных конвейеров и сбрасывающих тележек на конвейерах должны выдерживаться допуски указанные в таблице 5.1.
4.5 Виды технических освидетельствовании должны соответствовать указаниям 8.4.3.
4.6 При техническом освидетельствовании перегрузочные машины подвергаются осмотру опробованию вхолостую и под нагрузкой.
4.7 При опробовании перегрузочной машины вхолостую необходимо проверить работу:
- каждого механизма машины в отдельности путем раздельного включения соответствующих приводов;
- тормозных устройств всех механизмов;
- всех механизмов устройств и блокировок обеспечивающих безопасную работу машины: конечных выключателей всех механизмов сигнальной аппаратуры аварийного выключателя и аварийных кнопок и других.
4.8 При опробовании вхолостую перегрузочной машины на рельсовом ходу должны быть выполнены следующие рабочие циклы на минимальной и максимальной скоростях:
- подъем и опускание стрелы на всю высоту подъема (выдвижение консоли на всю длину) до срабатывания конечных выключателей;
- передвижение машины на расстояние не менее 50 м в оба конца;
- вращение поворотной части на максимально возможный угол в обе стороны;
-раскрытие и закрытие противоугонных устройств.
Таблица 8.1 Допуски на укладку и при эксплуатации рельсовых путей передвижных конвейеров и сбрасывающих тележек мм
Отклонение от прямолинейности на 1 м длины рельсового пути
То же на 25 м длины рельсового пути
Отклонение от номинальной ширины колеи
Разность отметок головок рельсов в одном поперечном сечении
Зазор в стыках рельсов
Взаимное смещение торцов стыкуемых рельсов в плане и по высоте
4.9 При опробовании вхолостую отдельных механизмов перегрузочной машины их технические характеристики должны соответствовать требованиям заводской (фирменной) документации. Кроме индивидуального опробования отдельных механизмов необходимо произвести опробование перегрузочной машины вхолостую при совмещении движений механизмов оговоренных в заводской (фирменной) документации. При этом должна проверяться блокировка механизмов.
4.10 По окончании опробования вхолостую перегрузочная машина подвергается опробованию в составе маршрута как вхолостую так и под нагрузкой. Опробование перегрузочной машины под нагрузкой следует производить при работе с максимальной производительностью.
4.11 Порядок опробования в работе а также состав регулировочных работ должны уточняться с учетом указаний заводской (фирменной) документации.
5 Особенности технического освидетельствования конвейера
5.1 При техническом освидетельствовании конвейера должны проверяться очистные устройства бункеры с нагревателями и вибраторами пересыпные станции питатели улавливатели посторонних предметов.
5.2 Опробование конвейера вхолостую и под нагрузкой необходимо производить при минимальной и максимальной скоростях движения ленты.
5.3 При опробовании конвейера вхолостую и под нагрузкой необходимо проверить выдержку времени включения каждого последующего конвейера.
Выдержка времени необходимая для разгона тягового органа предыдущего конвейера должна соответствовать данным приведенным в заводской (фирменной) документации на СККН.
5.4 При опробовании вхолостую и под нагрузкой ленточного конвейера проверяются установка роликоопор положение ленты на барабанах и роликах в движении ход натяжной станции работа тормоза и рельсовых захватов сбрасывающей тележки работа блокировки реле скорости датчиков завала сигнализации при запуске. Величина схода ленты в поперечном направлении запас хода барабана натяжной станции должны соответствовать указаниям заводской (фирменной) технической документации. При отсутствии таких данных величина схода ленты в сторону не должна превышать 40 мм при условии отсутствия касания металлоконструкции а запас хода барабана в сторону груза или натяжного винта должен быть не менее 23 длины общего перемещения барабана.
5.5 При опробовании вхолостую и под нагрузкой скребкового конвейера кратцер-крана пластины цепей не должны касаться боковых поверхностей зубьев звездочек а втулки должны скользить по направляющим без зазора.
5.6 Опробование вхолостую и под нагрузкой ленточных и пластинчатых питателей следует производить по аналогии с соответствующими конвейерами. При опробовании под нагрузкой вибрационного питателя он должен обеспечивать заданную производительность на соответствующих режимах работы.
5.7 Время опробования вхолостую и под нагрузкой (в составе маршрута) конвейеров и питателей приведено в табл. 5.2.
Таблица 8.2 Время опробывания вхолостую и под нагрузкой конвейеров питателей и других устройств часы
Тип перегрузочной машины
Конвейер с зачистным устройством пересыпной станцией бункером нагревателем вибратором
Питатель ленточный пластинчатый лопастной
6 ТЕХНИЧЕСКОЕ ОБСЛУЖИВАНИЕ И ОБЯЗАННОСТИ ПО СОДЕРЖАНИЮ ПОДЪЕМНО-ТРАНСПОРТНОГО ОБОРУДОВАНИЯ В ИСПРАВНОМ СОСТОЯНИИ
6.1.1 Техническое обслуживание подъемно-транспортного оборудования подразделяется на:
- техническое обслуживание при использовании
- техническое обслуживание при хранении
- техническое обслуживание при транспортировании.
6.1.2 Состав периодичность порядок выполнения и меры безопасности при проведении технического обслуживания подъемно-транспортного оборудования должны соответствовать указаниям приведенным в инструкции по эксплуатация этого оборудования или в другой технической документации завода-изготовителя. При отсутствии таких указаний они должны быть разработаны:
- для перегрузочного оборудования подконтрольного Госгортехнадзору - специализированной организацией в соответствии с Правилами Госгортехнадзора.
- для оборудования не подконтрольного Госгортехнадзору - портом или по его поручению другой организацией.
6.2 Техническое обслуживание при использовании подъемно- транспортного оборудования
6.2.1 Техническое обслуживание при использовании машин состоит из:
) ТО-1 которое включает в себя все виды обслуживания с периодичностью менее месяца а именно: ежесменное ежесуточное еженедельное и т.п. Эти виды обслуживания проводятся во время приема и сдачи смены в период отсутствия грузовых работ а также с выводом машины из эксплуатации но не более чем на 8 ч (одна дневная смена);
- по кранам и перегружателям всех типов включая зерновые с периодичностью 1 раз в месяц и длительностью не более 2 суток а 1 раз в 3 месяца (при необходимости) длительностью до 40 ч (пять дневных смен);
- по машинам внутрипортовой механизации - через 150-200 ч работы машины но не реже чем через месяц если в заводских инструкциях не оговорены иные сроки. Длительность ТО-2 этих машин не должна превышать:
для машин с двигателем внутреннего сгорания и грузоподъемностью до 10 т - 16 ч (две дневные смены) грузоподъемностью 10 т и более - 24ч (три дневные смены);
для машин с электроприводом - 8 ч (одна дневная смена).
6.2.2 В состав ТО-1 входят следующие работы:
- проверка перегрузочной машины и ее механизмов
- уборочно-моечные работы
- опробование механизмов агрегатов и систем в действии
- проверка в действии блокировочных устройств и приборов безопасности
- регулировочные работы
- снабжение топливом смазкой водой
- устранение повреждений.
Ежесменное техническое обслуживание выполняют докеры-механизаторы управляющие машиной при приеме и сдаче смены
Ежесуточное еженедельное и другие виды обслуживания входящие в ТО-1 выполняют рабочие по техническому обслуживанию и ремонту.
Перечень работ и проверок выполняемых при ТО-1 на конкретных машинах устанавливает порт на основании заводских инструкций по эксплуатации машины. Докерам- механизаторам управляющим перегрузочными машинами и рабочим по техническому обслуживанию и ремонту запрещается самостоятельно без указания группового механика (электромеханика) или сменного механика разбирать и регулировать:
- аппаратуру гидравлического и пневматического управления;
- предохранительные приборы и приборы безопасности;
- топливные насосы регуляторы и форсунки дизелей;
- защитные фрикционы механизмов поворота;
- весовые устройства ограничители грузоподъемности и указатели вылета стрелы;
- приборы автоматизации электронного оборудования сигнализации и речевой связи;
- тормоза с автоматическим устройством для компенсации износа фрикционных обкладок тормоза механизма подъема контейнерных кранов и перегружателей;
- запорное устройство подъемной консоли перегружателя;
- устройства для подогрева и охлаждения рабочей гидравлической жидкости.
Приведенный перечень таких работ дополняется портом в зависимости от конструктивных особенностей машин.
Категорически запрещается производить регулирование тормоза механизма подъема при поднятом грузе или грейфере (грузоподъемном электромагните) а также устанавливать различные приспособления для растормаживания тормоза вручную.
При ежесуточном техническом обслуживании производится контроль качества выполнения и оформления ежесменного технического обслуживания.
Ежесуточное еженедельное и другие виды обслуживания машин входящие в ТО-1 проводятся в течение времени отведенного для выполнения ежесменного обслуживания а также в обеденные и межсменные перерывы и в периоды отсутствия грузовых работ.
О состоянии перегрузочных машин и выполненных работах рабочие делают запись в вахтенном журнале машины.
Организация ежесменного обслуживания и контроль за его выполнением являются обязанностью сменного механика остальных видов обслуживания -
инженерно-технических работников ответственных за содержание перегрузочных машин в исправном состоянии.
6.2.3 ТО-2 является основным видом технического обслуживания и включает в себя следующие работы состав которых уточняется портом с учетом конструкции машин в соответствии с 5.1.2:
- проверку технического состояния машины;
- при необходимости замену быстроизнашивающихся деталей: резьбовых соединений канатов тормозных обкладок пальцев и упругих втулок муфт манжет и уплотнений гидросистемы контактов гибких соединений и пружин командоаппаратов контакторов и реле щеток и щеткодержателей электродвигателей и кольцевых токоприемников питающего шлангового кабеля других деталей и оборудования;
- восстановление надежности всех соединений элементов металлоконструкций деталей механизмов электрического гидравлического и пневматического оборудования а также устранение неисправностей. В случае применения сварки при восстановлении несущих металлоконструкций кранов работа должна быть выполнена в соответствии с Правилами Госгортехнадэора по кранам;
- регулирование устройств механизмов схем и систем;
- очистку механизмов и оборудования от пыли грязи и отработавшей
-смазывание узлов механизмов.
ТО-2 проводят по квартальным графикам которые утверждает заместитель начальника района по механизации. Отклонение от сроков выполнения ТО-2 предусмотренных графиком допускается в исключительных случаях по разрешению руководителя утвердившего график но не более чем на 5 дней.
Перенос срока должен быть оформлен записью разрешения в журнале группового механика.
Ответственность за проведение ТО-2 возлагается на инженерно-технического работника ответственного за содержание машины в исправном состоянии. Запись о постановке перегрузочной машины на ТО-2 а также о пуске ее в работу после технического обслуживания производит указанное лицо в вахтенном журнале машины.
О выполненных работах ТО-2 должна быть сделана запись в журнале группового механика (электромеханика). Контроль за выполнением графика осуществляет инженерно-технический работник по надзору за безопасной эксплуатацией перегрузочных машин.
6.2.4 Для обеспечения бесперебойной работы перегрузочных машин на каждом грузовом районе должен быть предусмотрен дежурный персонал для технического обслуживания и ремонта перегрузочных машин подчиненный сменному механику.
6.2.5 Перегрузочные машины должны быть закреплены:
- за рабочими по техническому обслуживанию и ремонту - для обеспечения технического обслуживания с периодичностью 1 сутки и более а также для выполнения ремонтных работ. Закрепление оформляется распоряжением заместителя начальника района по механизации;
- за рабочими комплексных бригад (докерами-механизаторами)-для обеспечения управления и ежесменного обслуживания машины. Закрепление оформляется распоряжением начальника района.
Докеры механизаторы в период работы на перегрузочных машинах подчиняются инженерно-техинческим работникам механизации в том числе и ответственному за содержание перегрузочных машин в исправном состоянии и выполняют все их указания в части технической эксплуатации машин. Докеры-механизаторы управляющие перегрузочными машинами должны участвовать в работах по техническому обслуживанию и ремонту перегрузочных машин и производить замену грузозахватных органов с учетом 5.7.2.
Бригадир комплексной бригады обязан обеспечить постоянное участие рабочих в техническом обслуживании перегрузочных машин в соответствии с графиком ТО-2 и с учетом закрепления машин за рабочими комплексных бригад.
Выдачу задания докерам-механизаторам и рабочим по техническому обслуживанию и ремонту на выполнение работ по техническому обслуживанию производит групповой или сменный механик после инструктажа по технике безопасности.
6.2.6 Докеры-механизаторы управляющие перегрузочными машинами обязаны при приеме смены проверять техническое состояние машины. Проверка должна осуществляться в соответствии с указаниями приведенными в производственной инструкции докера-механизатора или в инструкции по охране труда при работе на конкретной машине. При обнаружении неисправности при приемке или во время работы машины докер-механизатор управляющий машиной должен соответственно не начинать либо прекратить работу и доложить об этом сменному механику. Машина может быть использована для работы только после устранения неисправностей и получения разрешения сменного механика которое должно быть записано им в вахтенном журнале машины а если на машине журнал не предусмотрен - в вахтенном журнале сменного механика.
После окончания работы докер-механизатор управляющий машиной обязан:
- произвести очистку машины и при необходимости заправить ее топливом водой и маслом;
- сделать запись в вахтенном журнале машины если он предусмотрен в соответствии с формой журнала;
- поставить машину в отведенное для стоянки место а краны и перегружатели установить на противоугонные захваты;
- сдать машину (ключи) сменному механику.
6.2.7 Администрация порта обязана предоставить докерам-механизаторам управляющим перегрузочными машинами 20 мин для приемки-сдачи перегрузочной машины и выполнения ежесменных работ
6.2.8 Передача в период рабочей смены управления перегрузочной машиной одним докером-механизатором другому без разрешения сменного механика и записи в вахтенном журнале сменного механика запрещается.
6.2.9 При осмотре и техническом обслуживании перегрузочной машины с электроприводом должны быть выполнены мероприятия обеспечивающие безопасность работ.
6.2.10 На каждом кране перегружателе и машине специализированного перегрузочного комплекса должны быть:
- вахтенный журнал перегрузочной машины;
- комплект инструментов приспособлений и инвентаря а также расходные материалы необходимые для ежесменного и ежесуточного технического обслуживания.
На кранах и перегружателях а также в гаражах и на постах технического обслуживания должны быть вывешены карты смазки механизмов машин и необходимые данные для регулировочных работ.
6.2.11 Выбор контроль качества и учет расхода горюче-смазочных материалов порт должен осуществлять в соответствии с указаниями заводской (фирменной) документации и картой смазки составленной с учетом рекомендаций РД 31.44.08-93.
6.2.12 Выбор стальных канатов для перегрузочных машин и техническое обслуживание стальных канатов следует производить с учетом указаний Правил Госгортехнадзора по кранам и рекомендаций приведенных в приложении В к настоящим ПТЭ.
6.3 Техническое обслуживание при хранении подъемно-транспортного оборудования
6.3.1 Перегрузочные машины сменные грузозахватные органы съемные грузозахватные приспособления и средства укрупнения в периоды когда они не эксплуатируются подлежат хранению. В зависимости от продолжительности такого периода они могут находиться на оперативном или длительном хранении.
Оперативному хранению подлежат перегрузочные машины сменные грузозахватные органы съемные грузозахватные приспособления и средства укрупнения предназначенные для выполнения сменно-суточного плана а в случаях когда они не потребуются более месяца- длительному хранению.
Постановка на длительное хранение перегрузочных машин и сменных грузозахватных органов при сроке хранения менее 3 месяцев производится распоряжением начальника грузового района.
Постановка портальных кранов перегружателей всех типов и машин специализированных конвейерных комплексов для навалочных грузов на хранение более чем на 3 месяца производится приказом начальника порта. Постановка на длительное хранение съемных грузозахватных приспособлений и средств укрупнения производится распоряжением руководителя подразделения-владельца.
6.3.2 При оперативном хранении должны быть обеспечены условия для счета выдачи приема и технического обслуживания оборудования для чего:
- электро- и автопогрузчики и их сменные грузозахватные органы должны храниться в помещениях;
- портальные контейнерные автопогрузчики и портовые тягачи должны храниться на специальных площадках а обслуживаться в закрытых боксах оснащенных всеми необходимыми приспособлениями и средствами механизации для производства работ по техническому обслуживанию;
- однотипные низкорамные полуприцепы без выносного опорно-сцепного устройства могут устанавливаться в несколько ярусов (не более пяти). При этом под колеса полуприцепов должны быть установлены упорные колодки;
- контейнерные и трубные захваты следует хранить на специальных подставках обеспечивающих сохранность замковых устройств при этом отверстия гидросистемы должны быть заглушены;
- машины непрерывного транспорта а также сменные грузозахватные органы грузоподъемных кранов должны храниться на специально предназначенных для этой цели и оборудованных площадках;
- съемные грузозахватные приспособления следует хранить в специальных помещениях и под навесами;
- средства укрупнения должны храниться на грузовых складах.
6.3.3. В целях защиты от коррозии длительное хранение машин внутрипортовой механизации сменных грузозахватных органов с электрическим или гидравлическим приводом съемных грузозахватных приспособлений и средств укрупнения должно осуществляться на складах под навесом или под водонепроницаемыми чехлами в соответствии с указаниями заводских инструкций по эксплуатации и техническому обслуживанию. Перегрузочные машины сменные грузозахватные органы съемные грузозахватные приспособления и средства укрупнения находящиеся на длительном хранении разукомплектовывать категорически запрещается. Ответственность за сохранность перегрузочных машин сменных грузозахватных органов съемных грузозахватных приспособлений и средств укрупнения при длительном и оперативном хранении возлагается на начальника грузового района или руководителя подразделения-владельца оборудования.
6.3.4. Техническое обслуживание перегрузочных машин находящихся на оперативном хранении осуществляется так же как и техническое обслуживание при использовании машин (см. 5.2).
6.3.5 Техническое обслуживание перегрузочных машин при длительном хранении включает в себя работы по обслуживанию при подготовке к хранению в процессе хранения а также работы при подготовке к использованию после хранения. При подготовке перегрузочной машины к длительному хранению необходимо:
- произвести мойку и очистку
- выполнить все работы ТО-2
- устранить неисправности (восстановить герметичность кожухов крышек н дверей оборудования остеклить кабину и т.д.);
- произвести консервацию. Консервацию производят в зависимости от конструктивных особенностей машин требуемых сроков защиты и условий хранения в соответствии с ГОСТ 9.014 и указаниями заводских инструкций по эксплуатации машин.
LK_ТЫЛ.doc
Род груза: минеральные удобрения (берутся их показатели требующие максимальной мощности привода).
Производительность: P= 600 тч
Длина трассы: l = 50.8 м
Насыпной вес груза:
Коэффициент разрыхления:
Угол естественного откоса:
Коэффициент трения груза по стали:
Коэффициент трения груза по ленте:
Условия работы: конвейер находится в технологической цепи; загрузка производится с ленточного конвейера; разгрузка производится однобарабанным разгрузочным устройством в бункер загрузочного устройства следующего конвейера; конвейер установлен стационарно; привод расположен в разгрузочной части конвейера; натяжное устройство – грузовое расположено в головной части конвейера.
Рис. 3.2.1 Схема ленточного конвейера
Коэффициент производительности:
Коэффициент корректировки расчётной производительности:
Принимаем согласно ГОСТ 20-76:
Для определения натяжений в ленте применяем метод тягового расчёта по контуру.
Принимаем привод с одним ведущим барабаном угол обхвата которого 180о. Поверхность барабана футерована резиной.
Натяжение в набегающей ветви ленты ( точка 9) согласно формуле Эйлера:
В данном уравнении два неизвестных члена S1 и S9. Для составления второго уравнения обходим тяговый контур от точки 1 до точки 9 выражая натяжение во всех точках через натяжение в точке 1 – S1.
Для последующего расчёта необходимы погонные нагрузки:
Нагрузки от транспортируемого груза:
Нагрузки от вращающихся частей роликов:
Вес вращающихся частей роликоопор рабочей ветви:
Расстояние между роликоопорами рабочей ветви:
Вес вращающихся частей роликоопор холостой ветви:
Расстояние между роликоопорами холостой ветви: м
Нагрузки от веса ленты:
принимаем число прокладок
принимаем толщину прокладки:
принимаем толщину верхней обкладки:
принимаем толщину нижней обкладки:
удельный вес ленты:
Натяжения в характерных точках тягового контура:
где ki – коэффициент увеличения натяжения в ленте при огибании барабана k=1.04 так как угол огибания равен 90о. Далее – по табл.3.1.1
Таблица 3.1.1 Значение коэффициента ki
Угол обхвата лентой отклоняющего барабана о
S3=S2+W2-3=1.04S1+(q0+qp2)L2-3`= 1.04S1+(12.76+9.615)*47*0.035=1.04S1+36
S4=k4S3=1.05(1.04S1+36)=1.092S1+38
S5=k5S4=1.04(1.092S1+38)=1.14S1+39
S6=k6S5=1.05(1.14S5+39)=1.197S1+41
S7=S6+W6-7+Wзагр= (1.197S1+23)+( (q+q0+qp1)L6-7`)+(с*P(v+f1(2gh)-123.6 )=
(1.197S1+41)+((60+12.76+19.23)*51*0.035)+(1.5*600(2.75+
+0.56(2*10*6.6)12)3.6) = 1.197S1+4288
S8=k8S7=1.04(1.197S1+4288)=1.23S1+4460
S9=k9S8=1.05(1.23S1+4460)=1.29S1+4683
где: Wi-j – сопротивление движению ленты на участке i-j.
Li-j – длина участка i-j
`- коэффициент сопротивления движению ленты зависящий от
типа подшипника смазки уплотнения и др. `= 0.035 (принимаем
для условий с повышенной влажностью и большим количеством пыли).
h = 6.6 м - высота падения груза на ленту
с = 1.5 – коэффициент учитывающий сопротивление движению от трения
груза о боковые стенки загрузочной воронки и о ленту от движения
ленты в загрузочной части.
Получаем систему из двух уравнений:
Определяем числовые значения натяжения ленты в характерных точках:
S2 = 1.04S1 = 1096 Н
S3 = 1.04S1+36= 1176 Н
S4 = 1.092S1+38= 1322 Н
S5 = 1.14S1+39 = 1546 Н
S6 = 1.197S1+41= 1891 Н
S7 = 1.197S1+4288 = 5549 Н
S8 = 1.29S1+4683 = 6042 Н
Рис. 3.2.2 Диаграмма натяжения в ленте
Сопротивление передвижению ленты:
W0=S9-S1=6043-1054=4989 Н
Расчётная мощность привода ленточного конвейера:
Np=W0v 1000 = 4989*2.75 1000*0.9 = 15 кВт
где =0.9 – КПД привода.
Установочная мощность привода:
N0 = nуNp = 1.1 * 15 = 16 кВт
где nу=1.1 – коэффициент запаса мощности.
По ГОСТ 19523-81 выбираем трёхфазный асинхронный короткозамкнутый двигатель серии 4А: 4A160M6Y3. N = 15 кВт n = 985 обмин.
Выбираем ленту с прокладками из синтетической ткани – капрона с пределом прочности р = 180 кгссм прокладки. Лента воспринимает максимальное натяжение Smax= S9 = 3398 кН запас прочности n=10.
Число прокладок в ленте:
i = Smaxn рB = 6043*10 180*80 4
Принимаем ленту с 4-мя основными прокладками. Так как первоначально для расчёта была принята лента с шестью прокладками то пересчитывать конвейер не нужно.
Диаметр приводного барабана:
Dб = а1i = 220*4 = 880 мм
где а1=220 – эмпирический коэффициент.
По ГОСТ 22644-77 принимаем диаметр приводного барабана Dб=1000 мм.
Диаметр концевого и натяжного барабанов:
D1 = 0.8 Dб = 0.8*880 = 700 мм.
Принимаем D1 = 800 мм
Диаметр отклоняющих барабанов:
D2 = 0.65 Dб = 0.65*880 = 570 мм
Принимаем D2 = 630 мм
Lб= В + аб = 800 + 150 = 950 мм
где аб = 150 – эмпирический коэффициент.
Частота вращения приводного барабана:
nб = 60v D = 60*2.75 3.14*0.865 = 61.4 мин-1
где D = Dб + 2Δф = 0.8 + 2*0.028 = 0.856 м
Δф= 0.028 м – толщина резиновой футеровки.
Передаточное число редуктора привода конвейера:
uр.р. = nnб = 98561.4 = 16
Расчётная мощность редуктора:
Nред = k`pNp = 1.25*15 = 19 кВт
где k`p=1.25 – коэффициент условий работы.
По каталогу выбираем редуктор ЦД2-100М-16-I двухступенчатый с межосевым расстоянием между быстроходным и тихоходным валами Ас=1000 мм с передаточным числом up=16; номер схемы сборки I; с циллиндрическим концом выходного вала.
Использование редуктора ЦД2-100М со схемой сборки III даёт возможность расположить электродвигатель по одну а редутор по другую сторону конвейера что уменьшит габариты приводной станции (Рис 3.1.3.)
Рекомендуемые чертежи
- 29.07.2014