Разработка технологического процесса ремонта стержня


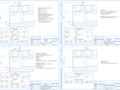
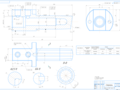
- Добавлен: 04.11.2022
- Размер: 157 KB
- Закачек: 0
Узнать, как скачать этот материал
Подписаться на ежедневные обновления каталога:
Описание
Курсовой проект - Разработка технологического процесса ремонта стержня
Состав проекта
![]() |
![]() ![]() ![]() |
![]() ![]() ![]() ![]() |
![]() ![]() ![]() ![]() |
Дополнительная информация
Контент чертежей
Карта нароботки.frw

Стержень.cdw

Рекомендуемые чертежи
- 13.12.2022
- 04.04.2015
- 13.05.2023
- 24.01.2023
- 10.06.2015
Свободное скачивание на сегодня
Обновление через: 14 часов 51 минуту