Привод лебедки




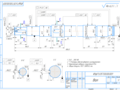
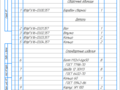
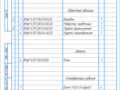
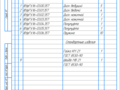
- Добавлен: 04.11.2022
- Размер: 3 MB
- Закачек: 0
Описание
Курсовой проект - Привод лебедки
Состав проекта
![]() |
![]() ![]() ![]() ![]() |
![]() ![]() ![]() ![]() |
![]() ![]() ![]() |
![]() ![]() ![]() ![]() |
![]() ![]() ![]() ![]() |
![]() ![]() ![]() ![]() |
![]() ![]() ![]() ![]() |
![]() ![]() ![]() ![]() |
Дополнительная информация
Спецификация привод.spw

ЮУрГУ.357.00.00.00 СБ
ЮУрГУ.357.00.01.00.СБ
ЮУрГУ.357.00.02.00.СБ
ЮУрГУ.357.00.03.00.СБ
ЮУрГУ.357.00.04.00.СБ
привод готовый.cdw

момент на тихоходном
ЮУрГУ.357.00.00.000 СБ
Техническая характеристика
курсач.docx
1Определение мощности на валу исполнительного механизма7
2Определение расчетной мощности на валу двигателя7
3Определение частоты вращения вала исполнительного механизма8
4Определение частоты вращения вала электродвигателя8
5Выбор электродвигателя9
1Определение передаточного отношения редуктора10
2Определение вращающих моментов10
ПРОЕКТИРОВАНИЕ ИСПОЛНИТЕЛЬНОГО ОРГАНА.14
1Определение диаметров участков вала.14
2Подбор подшипников качения15
3Подбор шпоночных соединений16
4Проектирование корпусных деталей16
5Выбор манжетного уплотнения.18
6Проверочный расчет шпоночных соединений для вала исполнительного органа18
7Проверочный расчет на статическую прочность.20
9Расчет барабана на прочность.23
ПРОЕКТИРОВАНИЕ МУФТЫ26
2.Муфта предохранительная дисковая.26
3.Выбор муфты упругой с торовой оболочкой31
В курсе «Детали машин и основы конструирования» необходимо выполнить курсовой проект по теме «привод лебедки». Целью курсового проекта является приобретение навыков расчета и конструирования деталей изучение методов норм и правил проектирования.
Основная задача – изучение методов норм и правил проектирования узлов и деталей машин приобретение практических навыков конструирования.
Привод включает в себя: двигатель электрический асинхронный с короткозамкнутым ротором муфту упругую с торовой оболочкой червячный редуктор муфту предохранительную фрикционную и барабан в качестве исполнительного механизма.
В рамках данного курсового проекта проводился расчет и выбор требуемого электродвигателя выбор редуктора и его основных характеристик расчет на прочность предохранительной фрикционной муфты муфты упругой с торовой оболочкой и расчет ее на прочность.
Электродвигатель применяемый в приводе является 3-х фазным асинхронным. Состоит из следующих основных частей: статор с трехфазной обмоткой ротор. Обмотка ротора выполнена бесконтактной (она не соединена ни с какой внешней цепью) что определяет высокую надежность такого двигателя. Асинхронный двигатель с короткозамкнутым ротором является самым распространенным из электрических двигателей применяемых в промышленности.
Упругие муфты амортизируют смягчают все удары вибрации и толчки благодаря наличию в своей конструкции упругих элементов - резиновых втулок различных пружин и т. д. Муфта упругая с торовой оболочкой служит для соединения валов двигателя и редуктора и передачи между ними вращательного момента а также делает передачу вращения мягче и долговечнее.
Червячный редуктор предназначен для передачи мощности с увеличением крутящего момента с уменьшение частоты вращения. К достоинствам червячных передач относятся: плавность зацепления и бесшумность работы; большие передаточные числа при сравнительно малых габаритах например в кинематических передачах и до 1000 в силовых чаще всего и до 80; повышенная кинематическая точность что особенно важно для делительных устройств; возможность создания самотормозящей передачи.
Недостатками червячных передач являются: ограниченная передаваемая мощность не превышающая 50 60 кВт; необходимость точной установки и жесткой осевой фиксации червячного колеса поскольку осевое смещение колеса неточности межосевого расстояния и ошибки угла скрещивания оказывают значительное влияние на величину и расположение пятен контакта а следовательно работоспособность передачи.
Для защиты от перегрузок применяется муфта предохранительная фрикционная. Достоинство данного устройства заключается в том что в него интегрирована звездочка расположенная между фрикционными дисками скользящими по диску и регулирующими крутящий момент.
Кинематическая схема привода представлена на рисунке 1. Мощность от электродвигателя через упругую муфту с торовой оболочкой передается на быстроходный вал червячного редуктора от тихоходного вала редуктора мощность через муфту предохранительную фрикционную передается на исполнительный механизм.
Рисунок 1 - Кинематическая схема привода
– Двигатель; 2 – Муфта упругая; 3 – Редуктор; 4 – Муфта предохранительная; 5 – Исполнительный механизм
КИНЕМАТИЧЕСКИЙ И СИЛОВОЙ РАСЧЕТ ПРИВОДА. ВЫБОР ЭЛЕКТРОДВИГАТЕЛЯ
Проектирование привода выполняют на основании технического задания в котором содержатся назначение основные технические характеристики режим нагружения и ресурс механизма. В качестве силовой характеристики привода в задании приведена номинальная (наибольшая длительно действующая) нагрузка на валу исполнительного механизма которая задана в виде вращающего момента Tk или окружного усилия Ft при вращающемуся исполнительном механизме (приводы конвейеров лебедок испытательных стендов) или в виде осевого усиления Fa при поступательном движении исполнительного механизма (приводы винтовых толкателей триммеров летательных аппаратов). В некоторых случаях задана непосредственно мощность Pk на валу исполнительного механизма. В качестве кинематической характеристики привода задана либо линейная скорость движения исполнительного механизма (ленты или цепи конвейера каната лебедки винта винтового толкателя и т.п) либо угловая скорость или частота вращения исполнительного механизма или вала электродвигателя.
1Определение мощности на валу исполнительного механизма
Мощность P3 кВт на валу исполнительного механизма вычисляется в зависимости от исходных данных по формуле:
где k-порядковый номер вала исполнительного механизма(k=2) согласно
кинематической схеме привода (см.рис.1);
Ft=Fk-окружное усиление на исполнительном механизме;
Vt=Vk-линейная скорость вращательного движения исполнительного механизма в направлении действия усилия Ft. Значит
2Определение расчетной мощности на валу двигателя
Расчетная мощность P1 кВт на валу двигателя определяется по мощности на
валу исполнительного механизма с учетом потерь в приводе:
где -общий КПД привода.
Общий КПД привода вычисляется как произведение КПД отдельных передач учитывающих потери во всех элементах кинематической цепи привода:
– КПД червячной передачи.
КПД червячного редуктора существенно зависит от передаточного отношения которая на данном этапе неизвестно поэтому зададимся средним значением С последующим уточнением КПД редуктора.
3Определение частоты вращения вала исполнительного механизма
Частота nk мин– 1 вращения вала исполнительного механизма вычисляется по формуле:
где z – число зубьев звездочки t – шаг зубьев звездочки 100 мм;
4Определение частоты вращения вала электродвигателя
Частота n1 мин–1 вращения вала электродвигателя определяется по формуле:
где i-передаточное отношение привода оно вычисляется во формуле:
Так как 1 передача:
5Выбор электродвигателя
В приводах общего назначения применяют в основном трехфазные асинхронные электродвигатели переменного тока с короткозамкнутым ротором серии АИР отличающиеся простотой конструкции и низкой стоимостью. Промышленностью выпускаются двигателя с синхронной частотой вращения nC магнитного поля статора 3000 1500 1000 750 мин-1.
Выбираем по двум параметрам Р1 и n1 .
Синхронная частота: nc=1000 мин-1.
P1 = 2 следовательно по таблице выбираем двигатель АИР100L6 ТУ16-525.564-84 исполнения IM1081. Мощность синхронная частота вращения равна 1000 обмин и асинхронной частотой вращения 950 мин-1.Эскиз электродвигателя указан на рисунке 2.
Рисунок 2- Эскиз двигателя
Габаритные размеры двигателя указаны в таблице 1.
1Определение передаточного отношения редуктора
После выбора электродвигателя уточняется передаточное отношение привода:
2Определение вращающих моментов
Вращающие моменты на валах определим по формуле:
Вращающий момент на 1 и 2 валу:
Вращающий момент Т Н*м
Редуктор: «Ч-125-40-51-1-У3» где
5 – межосевое расстояние;
– номинальное передаточное число;
– категория точности;
У – климатическое исп.
Допускаемый вращающий момент [2 с. 740 таб.60]
Табличные значения передаточного отношения:и
Эскиз выбранного редуктора с указанием габаритных присоединительных установочных размеров приведен на рисунке 3 параметры редуктора приведены в таблице 2.
Рисунок 3 - Схема червячного редуктора
Таблица 3 Габаритно-присоединительные размеры редуктора.
ПРОЕКТИРОВАНИЕ ИСПОЛНИТЕЛЬНОГО ОРГАНА.
1Определение диаметров участков вала.
Так как вал исполнительного механизма приводится во вращение валом редуктора через приводную муфту то желательно чтобы соединяемые участки валов были одинаковыми. Поэтому диаметр и длину сопряженного концевого участка вала исполнительного механизма целесообразно принять такими же как у вала редуктора .
Диаметр dп шейки вала для установки подшипника качения определяется по зависимости
dп>d+2t=50+2*2.8=55.6мм
где t-высота бурта. Полученный результат округляется до ближайшего значения из следующего ряда чисел: 50556065 и т.д. dп=60мм
Диаметр dбп упорного бурта подшипника рассчитывается по зависимости
dбп= dп+3r=60+3*3=69
где r – величина радиуса фаски кольца подшипника установленного на диаметре dп. После вычисления диаметра dбп округляется до ближайшего значения из стандартного ряда нормальных линейных размеров Ra40.
Диаметр dст рабочей ступени рассчитывается по зависимости
dст= dбп+3f=71+3*1.6=758мм
Округлим до dст=80мм
Значения t rи f представлены в табл. В зависимости от диаметра концевой части вала.
2Подбор подшипников качения
Ввиду радиальных нагрузок были выбраны радиальные сферические двухрядные шарикоподшипники ГОСТ 28428-90:
Подшипник средней серии диаметров серии ширин 0 с d=60мм D=130мм: Подшипник 1312 ГОСТ 28428-90.
3Подбор шпоночных соединений
Шпонка выбирается из ряда стандартных по ГОСТ 23360-80
Таблица 12 – Размеры призматических шпонок
Для фиксации полумуфты на цилиндрическом конце вала:
Шпонка 14×9×72 ГОСТ 23360-80.
Для фиксации барабана исполнительного органа на валу:
Шпонка 22×14×65 ГОСТ 23360-80.
Геометрические параметры шпоночного соединения
4Проектирование корпусных деталей
2.1.Проектирование корпуса для подшипника
Подшипники могут устанавливаться в разъемных и неразъемных корпусах. Осевая фиксация подшипников в корпусах осуществляется с помощью фланцевых или закладных крышек. Корпуса в большинстве случаев выполняются литьем из чугуна. Конструкция и основные размеры корпусов и сопрягаемых с корпусами крышек приведены в таблицах П7 П8 .
2.2.Проектирование крышек.
*) размеры: d b и D4 определяются размерами вала и манжеты.
5Выбор манжетного уплотнения.
Для предотвращения вытекания смазочного материала из подшипниковых узлов а также защиты их от попадания пыли грязи и влаги применяются уплотнительные устройства. Наиболее часто для этого используются манжетные армированные уплотнения из синтетической резины(табл. П10).
6Проверочный расчет шпоночных соединений для вала исполнительного органа
Расчет шпоночного соединения на прочность проводится по напряжениям смятия:
Рисунок 19 – Расчетная схема шпоночного соединения
– допускаемые напряжения на смятие.
Шпонка 14×9×72 ГОСТ 23360-80
Т=775 (Нм) – момент на валу;
lp – рабочая длинна шпонки:
b=14 (мм) – ширина шпонки;
d=50 (мм) – диаметр посадочной части вала;
h=9 (мм) – высота шпонки;
t=55 (мм) – глубина паза на валу.
Условие прочности выполнено запас прочности обеспечен.
Шпонка 22×14×65 ГОСТ 23360-80
b=22 (мм) – ширина шпонки;
d=80 (мм) – диаметр посадочной части вала;
h=14 (мм) – высота шпонки;
t=9 (мм) – глубина паза на валу.
7Проверочный расчет на статическую прочность.
Расчетная схема вала.
Необходимые размеры : l1=011 м l2=0138 м l3=0354 м l4=0138 м.
Сила действующая на вал муфты
Найдем реакции опор в подшипниках из уравнения моментов и суммы проекций сил на оси координат.
Максимальное эквивалентное напряжение в опасном сечении посадки левой ступицы барабана на вал Мmax=8024 Нм
Расчет на статическую прочность будем вести по теории максимальных касательных напряжений .
Предполагая что крутящий момент распределен по валу равномерно примем Ткр=600 Нм отсюда найдем касательные напряжения
Зная и найдем эквивалентное напряжение
Вычислим допустимые напряжения []
где [n]=2- запас прочности;
Kn=2- эксплуатационный коэффициент;
МПа- предел текучести материала Сталь 45.
Допустимые напряжения больше эквивалентных неравенство соблюдается значит вал достаточно прочен.
Грузовой барабан предназначен для наматывания и укладки тягового троса. На основании грузового барабана часто крепится зубчатый венец или ступица для соединения с приводным редуктором.
Барабан выбираем сварным из среднеуглеродистой 35Л.
Рис.Схема гладкого барабана.
Расчетная толщина цилиндрической стенки (обечайки) стального барабана определяется по формуле мм
где dк диаметр стального каната
9Расчет барабана на прочность.
Расчет барабана на прочность заключается в определении толщины его стенки Барабан не имеющим внутренних ребер без учета влияния торцовых стенок можно условно рассматривать как цилиндрическую трубу погруженную равномерно распределенной сжимающей нагрузкой q являющейся следствием сгибании трубы натянутым канатом и в одном сечении нагруженной сосредоточенной силой Sб равной натяжению каната (рис.)
Для определения интенсивности равномерно распределенной сжимающей нагрузки q следует рассмотреть сечение цилиндрической трубы охваченной канатом с натяжением Sб.
Определяем нормальную силу
Так как длина окружности Dб то равномерно распределенную сжимающую нагрузку q находим:
Напряжение сжатия приходящееся на единицу длины от равномерно распределенной сжимающей силы и стенке барабана при толщине ее определяется как в тонкостенном сосуде по формуле Ляме — Гадолина.
а в общем виде напряжение сжатия
где b = ширина на которой распределяется нагрузка Sб (в гладком барабане b= dк).
[сж] допускаемое напряжение определяемое по данным табл. 1 в зависимости материала барабана. Для материала стали 35Л допустимое напряжение [сж]=170МПа
Отсюда условие прочности выполняется.
Канаты предназначены для подъема опускания удерживания и перетягивания груза. Подбор стальных канатов необходимой прочности осуществляется путем определения максимальных расчетных усилий и умножением их на коэффициент запаса прочности. Полученный результат сравнивают с разрывным усилием каната. Значение допускаемого коэффициента запаса прочности стальных грузовых канатов в большинстве случаев принимают равным 5 – 6.
Т.е. Fmax*[s] ≤ Fразр.
где Fmax =4000 Н максимальное расчетное усилие
[s]- коэффициента запаса прочности
Fразр- разрывное усилие каната.
Полученный результат сравниваем с разрывным усилием каната. Для нашего случая выберем dk=69 мм
ПРОЕКТИРОВАНИЕ МУФТЫ
2.Муфта предохранительная дисковая.
Расчет предохранительной полумуфты
S=125 15 принимаем S=13
Примем наружный диаметр диска:
Внутренний диаметр диска:
Рисунок 4.1 – Ведущий и ведомый диск
Тогда приведенный радиус кольца трения:
Рассчитаем допустимую осевую силу от всех пружин:
где [р] – допускаемое давление на трущихся поверхностях МПа
Материалом трущихся поверхностей фрикционных накладок возьмем асботекстолит для которого:
коэффициент трения f = 03 [4 с.204табл.5.1]
[р] = (02 03) МПа [р] = 025 МПа [4 с.204табл.5.1]
Рассчитаем требуемое количество пар трения:
где момент трения реализуемой одной парой трения Н м
где коэффициент трения [4с.204табл.5.1]
Примем число пар трения z = 8 (до ближайшего четного).
Расчет пружин предохранительной муфты
Рисунок 4.2 – Геометрия цилиндрической витой пружины сжатия
где d – диаметр проволоки мм
D – средний диаметр пружины мм
c = – индекс пружины
t – шаг пружины в свободном состоянии мм
z0 – полное число витков
z – число рабочих витков
H0 – высота пружины в свободном состоянии мм
H3 – высота пружины при полном ее сжатии мм
l0 – длина проволоки для изготовления пружины: l =
l – длина упруго деформируемой части проволоки: l =
Характеристика пружины отражает зависимость деформации пружины λ от приложенной к пружине осевой силы F.
На графике отмечены три характерные точки:
– деформация λ1 при действии наименьшей рабочей нагрузки F1
– деформация λ2 при действии наибольшей рабочей нагрузки F2
– деформация λ3 при действии предельной нагрузки F3 при которой витки начинают соприкасаться
Определим параметры пружин из условия прочности:
где – расчетное напряжение в поперечном сечении витка
F2 – сила сжимающая пружину
k – коэффициент учитывающий влияние кривизны витков и
где с – индекс пружины:
D0 – средний диаметр пружины
d – диаметр проволоки:
Cила сжимающая пружину:
Найдем количество пружин:
Задаемся материалом пружины и выбираем величину допускаемого напряжения. Материал – стальная углеродистая проволока II класса по ГОСТ 9389-75 (=1400 1650 МПа принимаем в=1500 МПа).
Для расчета принимаем допускаемое напряжение .
Выбираем для пружин стальную углеродистую проволоку II класса по ГОСТ 9389-75.
Определим диаметр проволоки:
Тогда напряжение в поперечном сечении витка будет равно
Условие прочности выполнилось пружина работоспособна.
Определим величину осадка пружины λ2 учитывая его увеличение на3мм (3 = λ2 – λ1) при возрастании силы от F1 до F2:
где F1 – наименьшее рабочее усилие пружины
Найдем число рабочих витков пружины выразив из выражения:
где z – число рабочих витков пружины
G – модуль сдвига G = 08105 МПа
Тогда выразив z имеем:
Округлив до наибольшего целого значения получим z = 6.
Тогда полное число витков пружины:
Определим шаг пружины:
где = 01d – зазор между витками пружины тогда:
Определим высоту при полном сжатии витков:
Определим высоту свободной пружины:
Так как данное условие выполнилось то проверка пружины на устойчивость не нужна.
Так как все элементы муфты отвечают заданным условиям прочности и являются работоспособными следовательно данная муфта также является работоспособной.
3.Выбор муфты упругой с торовой оболочкой
Между двигателем и редуктором находится муфта упругая с торовой оболочкой служащая для соединения валов двигателя и редуктора и передачи между ними вращающего момента. Эти муфты просты по конструкции изготовление их не вызывает затруднений обладают высокой податливостью.
При выборе муфты ориентируются на диаметры соединяемых валов (выбор производят по большему из диаметров). В рассматриваемом случае диаметр вала двигателя d1 = 28мм диаметр вала редуктора d = 28 мм. Приняв диаметр редуктора за основной.
Рисунок 5.1 – Эскиз муфты упругой с торовой оболочкой
Муфта упругая с торообразной оболочкой мм
Е.П. Устиновский; Ю.А. Шевцов; Ю.К. Яшков; А.Г. Уланов. Многовариантное проектирование зубчатых цилиндрических конических и червячных передачь с применением ЭВМ. Учебное пособие к курсовому проектированию по деталям машин. Челибинск 1992г.
В.С.Березин; В.В.кулешов. Разработка кинематических схем приводов при курсовом проектировании по деталям машин. Учебное пособие. Челябинск 1994г.
В.А.Чурюкин; Ю.К.Яшков. Обозначение конструкторской документации. Учебное пособие. Челябинск 1996г.
П.П.Сохрин; Е.П.Устиновский; Ю.А.Шевцов. Техническая документация в курсовом проектировании по деталям машин и ПТМ. Учебное пособие. Челябинск 2001г.
Ю.А.Шевцов; А.С. Теребов. Разработка компоновки редуктора. Учебное пособие. Челябинск 2007г.
П.П.Сохрин; В.В.Кулешов. Проктирование валов. Учебное пособие. Челябинск 2000г.
П.П.Сохрин; Е.В.Вайчулис; Е.П.Устиновский и др. Разработка рабочих чертижей деталий передач. Учебное пособие. Челябинск 2000г.
Н.П. Сенигов; В.А.Пилатова; А.Л.Решетова; В.А.Краснов. Резьбы крепежные резьбовые изделия разъемные и неразъемные соединения деталей зубчатые передачи. Учебное пособие. Челябинск 2007г.
В.С. Поляков; И.Д.Барабаш; О.А.Ряховский. Справочник по муфтам. Ленинград изд. «Машиностроение» 1979г.
О.А.Ряховский; С.С.Иванов. Справочник по муфтам. Ленинград «Политех» 1991г.
Д.Н.Решетов. Детали машин. Москва «Машиностроение» 1989г.
В.И.Анухин. Допуски и посадки 4-е издание. Учебное пособие. С-Петербург изд. «Питер» 2008г.
Анурьев В.И. Справочник конструктора-машиностроителя: в 3-х т. Т.1 2 3. – 8-е изд. перераб. и доп. Под ред. И.Н. Жестковой – М.: Машиностроение 2001.
Детали машин. Курсовое проектирование: Учеб. Пособие для машиностроит. спец. учреждений среднего профессионального образования. – 3-е издание перераб. и доп. Москва изд. «Машиностроение» 2002г.
В.Н. Беляев И.С. Богатырев А.В. Буланже Детали машин: Атлас конструкций. Учебное пособие для машиностроительных вузов и др. Под ред. д-ра техн. наук проф. Д.Н. Решетова 4-е изд. перераб. и доп. Москва изд. «Машиностроение» 1979г.
П.Ф.Дунаев; О.П. Леликов. Конструирование узлов и деталей машин. Учебное пособие для машиностроительных специальностей вузов 4-е изд. перераб. и доп. Москва Высшая школа 1985г.
Вал.cdw

Неуказанные радиусы скругления R1
Общие допуски ГОСТ 30893.2-mк
Spetsifikatsia_baraban.spw

муфтаг.cdw

ЮУрГУ 457.02.01.000 СБ
Отрегулировать муфтуна величину предельного пращающего
завернув гайку и контргайку
Попадание смазки на поверхности трения дисков не допускается.
Техническая характеристика
Технические требования
барабан1.cdw

Корпуса подшипников заполнить смазкой солидол Ж ГОСТ1033-79 на
свободного пространства.
Плоскости разьема корпусов и крышек покрыть герметиком У-30М
Техническая характеристика
Spetsifikatsia_mufta.spw

Рекомендуемые чертежи
Свободное скачивание на сегодня
- 29.08.2014
- 24.01.2023
Другие проекты
- 22.12.2022