Технологический процесс обработки детали ступица переднего колеса с годовой программой выпуска 120000 штук




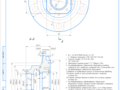
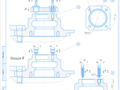
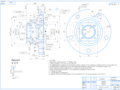
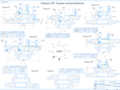
- Добавлен: 24.01.2023
- Размер: 3 MB
- Закачек: 4
Описание
Состав проекта
![]() |
![]() |
![]() |
![]() |
![]() ![]() ![]() |
![]() |
![]() |
![]() ![]() ![]() |
![]() ![]() ![]() |
![]() |
![]() |
![]() |
![]() |
![]() ![]() ![]() ![]() |
![]() ![]() ![]() ![]() |
![]() ![]() ![]() ![]() |
![]() ![]() ![]() ![]() |
![]() ![]() ![]() ![]() |
![]() ![]() ![]() ![]() |
![]() ![]() ![]() ![]() |
![]() ![]() ![]() ![]() |
![]() |
![]() |
![]() |
![]() |
Дополнительная информация
Экономика.doc
Сводная ведомость технологического оборудования на проектируемом участке
Сводная ведомость работников занятых на участке цеха.
Сводная ведомость годового фонда зарплаты основных производственных рабочих
Сводная ведомость годового фонда зарплаты вспомогательных рабочих. ИТР и СКЛ
Сводная ведомость основных фондов их стоимость и амортизационные отчисления от них
Годовая смета цеховых расходов
Калькуляция цеховой себестоимости детали на участке
Технико-экономические показатели работы участка
Экономика курсовой проэкт.DOC
Определение потребности в станочном оборудовании и промышленных роботах
Диаграмма загрузки станочного оборудования и ПР
Расчёт численности основных производственных и вспомогательных рабочих по профессиям и разрядам инженерно-технических работников и счётно-технического персонала (ИТР и СКП)
Определение годового фонда заработной платы работников проектируемого участка
Определение стоимости основных фондов
Расчёт наиболее значимых статей цеховых накладных расходов учитываемых на проектируемом участке
Составление калькуляции себестоимость детали на проектируемом участке
Технико-экономические показатели работы проектируемого участка
Список используемей литературы
Курсовая работа по предмету " Экономика в управлении машиностроительным мероприятием " базируется на исходных данных курсового проекта по предмету " Технология машиностроения " и является его продолжением.
Целью курсовой работы является определение суммы всех расходов связанное с производством заданного годового объема конкретной детали в виде себестоимости.
Одним из важнейших показателей деятельности машиностроительного предприятия является себестоимость выраженная в денежной форме. Себестоимость показывает во что обходится предприятию выпускаемая продукция. В неё включены как переменные на продукцию затраты труда так и расходы на оплату труда всех категорий работников. Чем лучше предприятие организует работу тем экономичнее расходуются материалы энергия основные и оборотные фонды а следовательно будет ниже себестоимость а чем ниже отпускная цена тем выше спрос на продукцию. Продукция выпускаемая таким предприятием будет более конкурентоспособной. Себестоимость изделий изготовленной по одним чертежам на разных заводах может характеризовать уровень технологической культуры и организацию производства. Расчёт всех затрат должен производится по возможности подробно с требуемой точностью.
В наше время государство строит новые рыночные отношения основанные на конкуренции и ведение предпринимательской деятельности. В этих условиях пересматривается отношения к качеству продукции. Это совокупность свойств продукции которая определяет степень годности по назначению. Одна из задач работы предприятия в условиях рынка - выйти со своей продукцией на мировой рынок. Поэтому продукция должна быть конкурентоспособной.
Любая продукция на мировом рынке продаётся с сертификатом качества. Это документ в котором указывается: государство предприятие - изготовитель и гарантии по качеству товара.
С 1991 года в машиностроительной промышленности был разработан сертификат качества по безопасности и эксплуатации. Это первый шаг по выходу товара на мировой рынок.
Оформление пояснительной записки согласно требованию ЕСКД: "Пояснительная записка должна состоять из титульного листа бланка задания содержания введения описания и расчетного материала необходимых таблиц и диаграмм списка используемой литературы Методических указаний и нормативно - справочного материала
Стоимость основных материалов на изготовление одной детали.
Сз=(Цз·мз-Цотх·мотх)·Кт [руб]
где Цз - цена материала заготовок [рубт]
мз - масса заготовки [т]
Цотх - цена реализуемых отходов [рубт]
мотх - масса реализуемых отходов [т]
Кт - Коэфицент учитывающий транспортно- заготовительные расходы (106 109)
Стоимость основных материалов на годовую программу
где Сз - стоимость материала на одну заготовку за вычетом реализуемых отходов [рубт]
Nг - годовая программа выпуска деталей [штгод]
Результаты выше проведённых расчетов отражены в таблице 1
Требуемое количество станков на операцию
где tшт - штучное время на операцию
t - такт выпуска деталей [мин]
где Fд - действительный годовой фонд времени оборудования в две смены (считается равным 4015ч )
Коэфицент загрузки оборудования
Где Спр - принятое количество станков на операцию [ед] (получаем путём округления расчетного значения до ближайшего большего целого числа)
Средний Коэфицент загрузки оборудования проектируемого участка
где SСрасч SСпр. сумма расчётного и сумма принятого оборудования на участке
В серийном производстве численность рабочих рассчитывается по формуле:
где Fд - действительный годовой фонд времени работы оборудования (4015 ч)
n - количество станков одновременно обслуживаемых одним рабочим
tшт - штучное время в минутах
Nг - годовая программа выпуска
Годовой фонд заработной платы по тарифу
где Рсд - сдельная расценка на данную операцию [руб]
Nг - годовая программа выпуска [шт]
где Ку - Коэфицент учитывающий условия труда
Сч.в. - часовая тарифная ставка
При многостаночном обслуживании сдельная расценка будет равна
где tшт - время наиболее длинной операции
Км - Коэфицент многостаночного обслуживания
При прямой сдельно-индивидуальной системе оплаты труда годовой сдельный заработок одного производственного рабочего (основная зарплата) определяется по формуле
При сдельно премиальной системе оплаты труда расчёт годового заработка одного производственного рабочего производится по тарифу с учётом выполнения и перевыполнения плана
ЗПосн=ЗПтар+ЗПтар×(a100) [руб]
где a - размер премирования [%]
Годовой фонд дополнительной заработной платы рассчитывается как процент от основной
ЗПдоп=ЗПосн×(b100) [руб]
где b - процент дополнительной заработной платы [%]
Отчисление на социальное страхование определяется по формуле
Нсоц=(ЗПосн+ЗПдоп)×(g100) [руб]
где g - процент отчислений на социальное страхование [%]
ЗПосн ЗПдоп смотри в таблице 5
Цеховая себестоимость детали на производственном участке определяется по формуле:
Сц=См+ЗП+Ру=100 [руб]
где См - стоимость основного материала на одну деталь [руб]
ЗП - заработная плата основных производственных рабочих (Основная дополнительная и отчисление на социальное страхование) [руб]
Ру - цеховые накладные расходы [руб]
Цеховые накладные расходы подразделяются на две группы:
А. Расходы на содержание и эксплуатацию оборудования (Рсод.об)
Б. Цеховые расходы общего характера на производственном участке (Рц.р)
Влияние расходов на эти группы определяется составлением двух смет.
затраты на силовую электроэнергию
где SNуст - мощность всех электродвигателей всех станков проектируемого участка [кВтч]
Сэ - стоимость одного киловатт часа электроэнергии [рубкВтч]
Fд.об - действительный годовой фонд работы оборудования в две смены [ч]
Кз - Коэфицент загрузки оборудования (средний)
Ко - Коэфицент одновременной работы оборудования (берётся в интервале 06 07)
Кс - Коэфицент учитывающий потери электроэнергии в силовых сетях (095)
hдв - КПД электродвигателей (068 075)
Затраты на сжатый воздух
Ссж=Скуб.сж·(01·nоб·Nг)=17100 [руб]
где Скуб.сж - стоимость одного кубометра сжатого воздуха [рубм³]
- расход сжатого воздуха на один цикл зажима - разжима заготовки [м³цикл]
nоб - количество станков (пневмоустройств) использующих сжатый воздух [шт]
затраты на технологическую воду для производственных нужд
Св=Скуб.м.в·(0001·mд·Nг)=1479379 [руб]
где Скуб.м.в - стоимость одного кубометра воды [рубм³]
01 - расход воды на промывку одной детали массой 1 кг [м³кг]
mд - масса одной детали [кг]
затраты на вспомогательные материалы
Свм=Сед·Спр=3225 [руб]
где Сед - стоимость вспомогательных материалов на единицу оборудования [руб]
Спр - принятое количество оборудования на участке
стоимость энергоносителей используемых на хозяйственные расходы и работающих на этом участке
1. Электроэнергия расходуемая на общее освещение участка
где С1кВт.ч - стоимость одного киловатта электроэнергии [рубкВт.ч]
Fо - количество часов работы освещения за год [час]
Sуч - общая площадь освещаемых участков [м²]
Qp - удельный расход мощности на освещение одного квадратного метра (принимается 25Втм²)
2. Горячая вода для отопления участка
Сот=Сот.кв.м·Fот·Sуч=1768·10 [руб]
где Сот.кв.м - стоимость отопления одного квадратного метра площади участка в сутки
Fот - длительность отопительного сезона [день]
3. Вода для хозяйственных и личных нужд
Св.х.=Скуб.м.в.х·Qв.х. ·Fн·Чр=8187509 [руб]
где Скуб.м.в.х - стоимость одного кубометра воды для хозяйственных и личных нужд
Qв.х. - расход воды на одного рабочего в день [м³день.чел.]
Fн - номинальный фонд времени
Чр - численность всех работников участка [чел]
Затраты материалов для ремонта помещений (берётся как 01% от стоимость производственной площади)
Ср.м.=(01100)·Скв.м·Sуч=65047 [руб]
где Скв.м - стоимость одного квадратного метра производственной площади [рубм²]
Затраты на текущий ремонт :
1. Помещения производственного участка
Ст.р.уч=Сркв.м·Sуч=11040 [руб]
где Сркв.м - стоимость ремонта одного квадратного метра плошадь [рубм³]
2. Производственного инвентаря (берётся как 08% от стоимости технологического оборудования)
3. Хозяйственного инвентаря
Сх.ин.=Сед·Чр=221992 [руб]
где Сед - средняя стоимость хоз-го инвентаря приходящегося на одного рабочего в год [рубчел]
Амортизационные отчисления от сибистоимости:
1. Здания участка (берётся как 25% от стоимости здания)
Азд=(25100)·Скв.м·Sуч=162618 [руб]
2. Производственного инвентаря (берётся как 2% от его стоимости)
Ап.и.=(2100)·Сп.и.=169753 [руб]
Затраты на износ малоценного инвентаря
Сиз.м.ин.=Сед·Чр=1193207
где Сед - удельная стоимость малоценного инвентаря на одного рабочего на участке [рубчел]
Вознаграждение рационализаторских изобретений рассчитывается по данным выплат приходящихся на одного рабочего на проектируемом участке
Срац=Срац.р·Чр=175004 [руб]
где Срац.р - выплата одному работнику в год [рубчел]
Затраты по защите окружающей среды (берётся как 1% от стоимости основных доходов)
Сз.о.с.=9991986 [руб]
Расходы по оздоровлению условий труда охрана труда рассчитывается по нормам на одного рабочего в час
Сох.тр.=Сох.тр.р·Чр=8837686 [руб]
где Сох.тр.р. - размер затрат на охрану труда рабочего [рубчел]
Прочие расходы (принимаются в размере 10% от суммы затрат оп статьям 11 - 21 сметы)
Спр.р.=1999583 [руб]
Итого по группе Б (сумма по статьям 11 - 21)
Цеховые накладные расходы на производственном участке по годовой смете состоит из суммы затрат по обеим группам А и Б
Процент цеховых накладных расходов
Сумма цеховых накладных расходов по производственному участку на единицу продукции
СПИСОК ИСПОЛЬЗУЕМЕЙ ЛИТЕРАТУРЫ
Данилевский В.В. "Технология машиностроения": Учебник для машиностроительных техникумов М. Высшая школа. 1984
Тросникова Н.А. Васильев М.А. "Определение себестоимости изготовления деталей на проектируемом участке цеха при выполнении курсовой работы и организационной части дипломного проекта". Методическая разработка по специальности 151001 "Технология машиностроения" ВАМК 2002
Кростелёва Е.М. "Экономика организация и планирования машиностроительного производства". М 1984
Под редакцией Горфинкеля "Экономика предприятия". М 2002
Записка ДП.doc
1 Описание назначения и условий работы детали. Технические условия на деталь. Химический состав механические свойства материала детали. Анализ технологичности детали
2. Выбор и обоснование типа производства .
3. Расчет такта выпуска деталей
4. Анализ заводского технологического процесса: ..
5. Выбор и обоснование принятого варианта заготовки .
6. Расчет межоперационных и общих припусков
межоперационных размеров и допусков по таблицам нормативов ..
7 Определение массы заготовки и коэффициента использования материала ..
8 Проектирование маршрутного технологического процесса изготовления детали включая не менее одной операции с применением станка с ПУ25
9 Выбор технологических баз и их обоснование. 26
10 Обоснование выбора оборудования. ..30
11 Назначение режимов резания (табличный расчет режимов резания на 2 операции в том числе одна на станке с ПУ)..34
12 Расчет норм времени (табличное нормирование 2-х операций). 41
13 Назначение разряда работы. 45
14 Сравнения по трудоемкости одной из измененных по сравнению с базовым техпроцессом операций. 46
15 Разработка программы на операцию выполняемую на станке с ПУ. 47
КОНСТРУКТОРСКАЯ ЧАСТЬ
1. Описание конструкции станочного приспособления.48
2 Описание контрольно-измерительного приспособления
ОРГАНИЗАЦИОННАЯ ЧАСТЬ
1. Расчет потребного кол-ва оборудования участка и его загрузка по операциям
2 Бригадная форма организации труда
3 Расчет необходимого кол-ва персонала участка. ..
3.1 Основных рабочих..
3.2 Расчет возможности применения многостаночного обслуживания и совмещения профессий..
3.3 Вспомогательных рабочих..
3.4 Инженерно-технических работников..
4 Обоснование принятого вида межоперационного транспорта..
5 Организация технического контроля..
6 Охрана труда на участке цеха. ..
7 Охрана окружающей среды..
8 Составление плана участка..
1 Расчет стоимости заготовок..
2 Расчет расценок и фондов заработной платы персонала участка..
3 Расчет стоимости основных фондов..
4 Определение накладных расходов по участку..
5 Определение себестоимости годового выпуска деталей и одной детали на участке. ..
6 Технико-экономические показатели участка..
1 Краткая характеристика основных прогрессивных решений внесенных в проект. ..
ПЕРЕЧЕНЬ ИСПОЛЬЗОВАННОЙ ЛИТЕРАТУРЫ
Развитие технологии обработки идёт в направлении повышения
производительности труда и снижения себестоимости изготовления деталей узлов и машин.
За счёт чего это можно сделать?
Прежде всего за счёт точности изготовления заготовок. Чем ближе заготовка к форме готовой детали тем меньше припуск на детали меньше нужно времени для изготовления готовой детали тем меньше зарплата рабочим меньше затраты на силовую энергию и т. д.
Сокращается количество операций значит будет меньше количество станков рабочих инструмента.
Следующий путь- внедрение нового высокопроизводительного оборудования и технологической оснастки. Новые станки новый режущий инструмент позволяют увеличить режимы резания при сохранении точности обработки.
Применение новых методов обработки так же направлено на повышение производительности труда.
Практическому широкому применению прогрессивных типов технологических процессов оснастки и оборудования средств механизации и автоматизации содействует единая система технологической подготовки производства (ЕСТПП) обеспечивающая для всех предприятий и организаций системный подход оптимизации выбора методов и средств технологической подготовки производства.
Для обработки одной и той же детали могут быть применены различные варианты технологического процесса равноценные с точки зрения технологических требований к изделию но имеющим значительные колебания по экономическим показателям. Существенное влияние на построение технологического процесса оказывает тип производства. Так в массовом и крупносерийном производстве технологический процесс строится на принципе дифференциации или концентрации операций при возможности полной их автоматизации.
При использовании принципа дифференциации технологический процесс расчленяется на элементарные операции с примерно одинаковым временем их выполнения равным такту или кратным ему; на каждом станке выполняются определённые операций преимущественно однопереходных.
При использовании принципа концентрации технологический процесс подразумевает объединение операций которые в этом случае производятся на многошпиндельных автоматах полуавтоматах агрегатных многопозиционных многорезцовых станках производящих одновременно несколько операций при малой затрате основного (технологического) времени.
1 Описание назначение условий работы детали.
Деталь 25.31.145 - ступица переднего колеса относится к классу фланцев. Она вхолит в узел переднего моста трактора Т30 и предназначена для установки колёс на передний мост трактора.
Ступица переднего колеса 25.31.145 устанавливается на подшипниках на полуосях переднего моста. На ступицу крепится обод переднего колеса.
Чертёж детали Ступица переднего колеса
Основными поверхностями детали являются внутренние отверстие под подшипниники торец "А" ступицы к которому прилегает диск обода колеса отверстие для крепления ступицы с диском обода колеса и ступицы для установки крышек.
- Ступица переднего колеса
- Полуось (на которой крепится ступица)
Передний (качающийся) мост предназначен для:
- обеспечения прямолинейного движения трактора;
- управления движением трактора;
- регулировки ширины колеи и высоты агротехнического просвета трактора.
Передний мост состоит из балансира 10 в котором закрепляются корпуса кулаков правого 9 и левого в которых размещаются оси с прикрепленными к ним полуосями и с установленными на нем рычагами и тягами рулевого управления.
Изменение ширины колеи передних колес ручное. Происходит при помощи перемещения поворотных кулаков в балансире. Управление передними колесами происходит из кабины тракториста при помощи рулевого механизма посредством продольной рулевой тяги соединенной с сошкой и рычагом осью поворотного кулака. Регулировку сходимости передних колес производят при помощи поперечной рулевой тяги путем ее удлинения или укорачивания.
Ступица переднего колеса устанавливается на полуось на 2-х подшипниках по внутренним цилиндрическим поверхностям 62 Р7 и 72 Р7 сама полуось крепится корончатой гайкой М16*1.5 которая фиксируется на валу посредством шплинта через поперечное отверстие в резьбе 4+03. Лыска на резьбе служит для установки шайбы с некруглым отверстием для исключения самоотвинчивания ступицы колеса при движении трактора. На наружной цилиндрической поверхности полуось 38-01 устанавливается уплотнение препятствующее попаданию пыли и грязи в подшипники ступицы колеса.
Технические условия на деталь.
Неуказанные линейные уклоны 1° 2°. Радиусы 3..5мм.
Точность отливки 11Т-0-0-11См 15 ГОСТ 26645-85
На необрабатываемых поверхностях допускаются раковины глубиной до 3мм. наибольшим измерением до 5мм. в количестве 6 шт.
На обрабатываемых поверхностях кроме С Д К И допускаются раковины глубиной до 3мм. в количестве не более 6 шт.
Допуск радиального биения поверхностей С и Д относительно друг друга 008мм.
Допуск непостоянства диаметров С и Д в поперечном и продольном сечениях 0015мм.
* Размеры для справок.
** Обеспечивается инструментом.
Покрытие: Эмаль КМЛ-13 тёмно серая ТУ 2312-021-16952278-95. V. У1. Система покрытия 1 ГОСТ 6572-91
Химический состав механические свойства материала детали.
станины корпуса кронштейны опоры плиты крышки траверсы колосники
Анализ технологичности конструкции детали.
Конструкция детали технологична если она обеспечивает простое и экономичное изготовление детали с минимальными затратами и высокой производительностью. Технологичность детали оценивается для конкретных условий производства.
Существует два вида оценки технологичности конструкции:
Кроме того технологичность может быть оценена дополнительными техническими показателями:
- коэффициентом использования материала;
- коэффициентом унификации и стандартизации;
- коэффициентом точности и шероховатости поверхностей
Качественный анализ технологичности детали
При проведении качественного анализа технологичности следует проанализировать возможность обработки данной детали при условии сохранения принципа единства баз.
Деталь-корпус ступицы относится к классу фланцев. Изготовлена из серого чугуна СЧ15 ГОСТ 1412-85 обрабатываемость материала удовлетворительная. Деталь не проходит термическую обработку которая может привести к ее короблению и необходимости дополнительной обработки после закалки.
Конструктивная форма детали позволяет выполнять следующие требования по технологичности механической обработки:
- возможность простого и надежного закрепления детали на станке;
- отсутствуют отверстия расположенные не перпендикулярно к плоскости входа инструмента;
- форма поверхностей и их размеры позволяют производить обработку на выпускаемых станкостроительной промышленностью моделях металлорежущих станков.
Деталь имеет снаружи 6 ступеней в отверстии 5 ступеней. Внутри на ступенях 15 имеется класс шероховатости Ra 08 (места под подшипники) подлежат растачиванию. Два торца и 5 отверстий с шероховатостью Ra 32. 8 отверстий с резьбой по 4 на каждом торце
При обработке данной детали не должно возникнуть трудностей из-за конструкции детали.
После проведения качественного анализа технологичности детали делаем вывод что конструкция детали является технологичной.
Количественный анализ технологичности детали
При проведении количественного анализа технологичности
детали определяем следующие коэффициенты:
Коэффициент уровня технологичности по шероховатости. Коэффициент шероховатости Кшо определяется по ГОСТ 14202-73 и принимается в пределах от 0 до 1.
где Бср. – средний класс шероховатости обработки данной детали
где 12 14-класс шероховатости обработки;
n1 n2 n14- количество поверхностей данного класса
- Если Кш.о. 016 – то деталь считается трудоёмкой в изготовлении;
- если Кш.о. 016 – то деталь нормальной трудоёмкости.
Т.к. расчётный Кш.о = 0253 то деталь считается нормальной трудоёмкости в изготовлении.
Уровень технологичности по точности обработки детали
Коэффициент точности КТО является относительно частым показателем технологичности конструкции и определяется по ГОСТ 14202-73.
где Аср. – средний квалитет точности обработки детали
где 67 17 – квалитеты точности изготовления;
n6 n7 n17 – количество размеров данного квалитета
-Если Кт.о. меньше 085 то деталь считается весьма точной;
-Если Кт.о. больше 085 то деталь считается нормальной точности;
Т.к. расчётный Кт.о. =0933 то деталь считается нормальной точности.
Замечания по технологичности детали:
ВЫВОД: На основании качественной и количественной оценки технологичности установлено что несмотря на ряд замечаний в целом технологичность детали удовлетворительная и таким образом чертеж детали Ступица переднего колеса 25.31.145 не должен подвергаться изменениям и пересмотру. Для повышения коэффициента использования материала требуется изменить метод получения заготовки.
2 Выбор и обоснование типа производства
Выбор типа производства существенно влияет на форму организации технологического процесса (групповая или поточная) выбор оборудования (универсальное специализированное специальное или автоматические линии) характер используемой оснастки (универсальная или специальная).
Характеристика видов производства.
Единичный тип производства характеризуется широкой номенклатурой выпуска и малым годовым объёмом выпуска применяется универсальное оборудование расположенное по групповому признаку. Применяется универсальный режущий и мерительный инструмент. Квалификация рабочих высокая. Трудоёмкость и себестоимость – высокие.
Серийный тип производства характеризуется ограниченной номенклатурой выпуска детали изготавливаются периодически повторяющимися партиями. Трудоёмкость и себестоимость ниже чем в единичном производстве. Различают мелкосерийное среднесерийное и крупносерийное типы производства. Крупносерийный тип производства характеризуется применением специализированного оборудования расположенного на участке по ходу технологического процесса. Применяется специализированный режущий и мерительный инструмент. Квалификация рабочих низкая. Применяется принцип не полной взаимозаменяемости.
Массовый тип производства характеризуется узкой номенклатурой выпускаемых изделий большим годовым объемом выпуска. Применяется специальное и специализированное оборудование расставленное на участке по ходу технологического процесса. Квалификация рабочих низкая при наличии высоко квалифицированных наладчиков оборудования. Трудоёмкость и себестоимость изготовления низкая. Используются точные индивидуальные заготовки с минимальными припусками под механическую обработку. Обработка осуществляется на предварительно налаженных специальных станках. Точность обработки обеспечивается автоматически за счет предварительной настройки оборудования возможно применение активного контроля. Рабочие приспособления неразборные специальные с механизированным зажимом заготовки. Контрольный и режущий инструмент используется в основном специальный Применяется принцип полной взаимозаменяемости. Одним из показателей характеризующих тип производства является коэффициент закрепления операции который показывает сколько операций закреплено за одним рабочим местом – это его физический смысл
- годовая программа N=
- режим работы – 2-х сменный m=
- календарный фонд времени оборудования Фд =
Таблица 1.5. Ориентировочное определение типа производства
Годовой объем выпуска
Ориентировочно по таблице определяем тип производства — массовое.
Более точно можно определить тип производства по коэффициенту закрепления операций Кз.о..
при Кз.о. = 1 - производство массовое
Кз.о. 10 – крупносерийное
Кз.о. 20 - среднесерийное
Кз.о. 40 - мелкосерийное
> Кз.о. – единичное производство.
Значение Кз.о. на стадии разработки процесса вычисляют по формуле:
Где:SО – количество операций выполняемых на участке в течение месяца
SР – количество рабочих мест на участке.
Коэффициент закрепления операций соответствует массовому типу производства (Кз.о. 1).
3. Расчет такта выпуска деталей
- Такт выпуска - это интервал времени через который с конвейера сходит готовое изделие
Определяем такт выпуска
где Фд – годовой действительный фонд времени работы оборудования.
N – годовая программа выпуска
4 Анализ заводского технологического процесса
Маршрут обработки соответствует типовому технологическому процессу обработки деталей типа «фланец». На первой операции выполняется обработка базовых поверхностей ( наибольшего диаметра ) по которой деталь будет базироваться на 010 015 операциях и черновая подрезка торца.
Таблица 1.7 - Заводской маршрут обработки детали
Наименование операции
обработка базовых поверхностей ( наибольшего диаметра ) по которой деталь будет базироваться на 010 015 операциях и черновая подрезка торца
черновая подрезка торца с другой стороны
первой обрабатывается больший торец : сверлится 4 отверстия в которых нарезается резьба М8-7Н Зенкером производится черновая обработка "центрального" отверстия под подшипник 71 и сверлятся зенкеруются разворачиваются 5 отверстий 18+0035
сверлится 4 отверстия в которых нарезается резьба М8-7Н и зенкером производится черновая обработка "центрального" отверстия под подшипник 61
производится расточка одновременно двух отверстий под подшипники
Токарный многорезцовый па 1Н713
одновременная чистовая подрезка наибольшего диаметра с 2х сторон
притупить острые кромки
Производят приёмныё контроль
Определение направлений совершенствования базового техпроцесса
Базовый технологический процесс механической обработки изготовления детали Полуось А25.31.122 разработан для условий крупносерийного поточного производства. Деталь обрабатывается на универсальных и специализированных станках со специальной наладкой работающих в полуавтоматическом цикле.
Можно отметить следующие достоинства базового техпроцесса:
а) поточная форма организации труда;
б) типовой порядок построения техпроцесса обработки детали;
в) соблюдение совмещения технологических и измерительных баз в процессе обработки детали;
д) использование предельных калибров и специальных контрольных приспособлений при контроле качества детали;
е) специальные станочные приспособления с механическим зажимом детали.
Базовый технологический процесс также следует модернизировать для улучшения технико-экономических показателей увеличения производительности труда и приведения его в соответствие с современным уровнем развития науки и техники.
В соответствии с заданием годовая программа выпуска N=120000Такт выпуска равен = 186 мин что меньше штучного времени на некоторых операциях базового техпроцесса и следует внести в него изменения для того чтобы он соответствовал годовой программе выпуска.
Предлагаемые направления изменения базового технологического процесса.
Повышение концентрации обработки на токарных операциях путём объединения их в токарную многошпиндельную которая сама по себе является более производительной.
Увеличить производительность агрегатных операций.
В место обработки поверхностей зенкерами на агрегатных операциях обрабатывать эти поверхности резцами на токарной операции.
Исправление технологических ошибок допущенных в базовом техпроцессе.
Применение смазочно-охлаждающей жидкости Аквол-10М
5 Выбор и обоснование принятого варианта заготовки
Метод получения заготовок для деталей машин определяется назначением и конструкцией детали её массой техническими требованиями масштабом и серийностью выпуска а также экономичностью изготовления.
Для изготовления заготовки 25.31.145 - ступица переднего колеса используется материал - Серый чугун СЧ15 ГОСТ 1412-85.
На базовом предприятии заготовку детали 25.31.145 - ступица переднего колеса получают методом литья в песчаные формы. Для данной деталь такой способ получения заготовки является почти единственным способом получения заготовки (при учёте годовой программы выпуска) это связано с наличием у детали в отверстии ступени большего диаметра которая не позволяет применять более экономически целесообразные методы получения заготовки такие как литьё в металлические формы.
Технические требования на заготовку.
163 - 241 HB 5(750)10 ( отп. 23 19).
Материал заменитель СЧ18 СЧ20 ГОСТ 1412-85.
Точность отливки 11Т-0-0-11См 15мм ГОСТ 26645-85.
На необрабатываемых поверхностях допускаются раковины глубиной до 3мм. наибольшим измерением 5мм. в количестве 6 шт.
На обрабатываемых поверхностях допускаются:
а) дефекты не превышающие припуск на механическую обработку;
б) остатки залива по линии разъёма высотой и толщиной не более 2мм;
в) остаток питателя высотой не более 2мм или вылом глубиной не более 1мм.
На необрабатываемых обрабатываемых поверхностях допускается остатки пригара в местах переходов и сопряжений не удаляемые дробемётной отчисткой.
На обрабатываемых поверхностях кроме С Д К И допускаются раковины глубиной до 3мм наибольшим измерением 3мм не доходящие до контуров поверхностей и отверстий ближе 3мм в количестве не более 6 шт.
На плоскости "Л" допускается наличие ужимин и скопление раковин выводимые мех. обработкой.
Допускается исправление литейных дефектов по инструкции И-7.
Покрытие грунтовка ГФ-0119 ГОСТ 23343-79.
Маркировать № модели № дублёра шрифтом h7 ГОСТ 2.304-81 углублением.
6. Расчет межоперационных и общих припусков межоперационных размеров и допусков по таблицам нормативов
Припуск — слой материала удаляемый с поверхности заготовки в целях достижения заданных свойств обрабатываемой поверхности детали. Припуск на обработку поверхностей детали может быть назначен по соответствующим справочным таблицам или на основе расчетно-аналитического метода определения припусков.
Предельные размеры заготовки определяют на основе расчета промежуточных припусков по всем технологическим переходам. Промежуточные расчетные размеры устанавливают в порядке обратном ходу технологического процесса обработки этой поверхности т.е. от размера готовой детали к размеру заготовки путем последовательного прибавления (для наружных поверхностей) к исходному размеру готовой детали промежуточных припусков или путем последовательного вычитания (для внутренних поверхностей) от исходного размера готовой детали промежуточных припусков.
Расчёт припусков производим в соответствии с методичкой [11].
Общие припуски определяют как сумму промежуточных припусков на обработку.
Сводим все расчеты в таблицу.
Припуски на механическую обработку и межоперационные размеры
а) тонкое растачивание
б) чистовое растачивание
в) черновое растачивание
а) подрезка торца чистовая
б) подрезка торца черновая
а) подрезка торца черновая
7 Определение массы заготовки и коэффициента использования материала
Определение коэфицента использования материала осуществляется по следующей формуле:
Где : Мд - масса детали
Мз - масса заготовки
Кз - Коэфицент способа получения заготовки
Так как форма заготовки является сложной то расчёт Ким производится по упрощённому методу.
Масса детали указана на чертеже детали и равна 61 кг.
Масса заготовки определяется путём её взвешивания и равна 7 кг.
Коэфицент способа получения заготовки для литья в песчаные формы равен 105.
8 Проектирование маршрутного технологического процесса изготовления детали включая не менее одной операции с применением станка с ПУ
При разработке маршрутной технологии обработки детали 25.31.145 - ступица переднего колеса ориентируемся на общие рекомендации для обработки детали типа фланец в массовом производстве. В массовом производстве рекомендуется использовать высокопроизводительное специальное и специализированное оборудование и много инструментальные станки.
На первой операции выполняется обработка базовых поверхностей. Это токарная обработка на многошпиндельном полуавтомате поверхностей по которым будет происходить базирование на следующих операциях. На второй и третей операции выполняется обработка пяти отверстий 18+0035 и восемь отверстий с резьбой (по четыре на каждом торце). На четвёртой операции происходит окончательная расточка одновременно двух отверстий под подшипники. Пятая операция - слесарная притупление острых кромок напильником. Шестая - промывка и сушка ОСМ-1. Седьмая - контрольная.
Технологическая задача: обеспечение шероховатости поверхностей С и Д Ra 08 шероховатости поверхностей И и К Ra 16 обеспечение соосности поверхностей С и Д относительно друг друга 008 биение поверхностей И и К относительно А не более 0046 биение торца Б не более 02мм. на R 52мм. биение торца А не более 02мм. на R 100мм. радиальное биение поверхности Ж не более 015мм. соосность пяти отверстий 18+0035 соосность восьми отверстий М8-7Н.
Маршрут обработки детали
24 Алмазно - расточная
ХХХХХХ стол контролёра
В соответствии с заданием необходимо разработать не менее одной операции с ЧПУ. Так как в предложенном маршруте обработки нет ни одной операции с ЧПУ то вводим в маршрут обработки альтернативную операцию 005-1 токарная с ЧПУ.
9 Выбор технологических баз и их обоснование
Выбор схемы базирования и закрепления играет решающую роль на уменьшение погрешности обработки детали. При выборе технологических баз необходимо следовать следующим правилам:
необработанные поверхности в качестве баз можно использовать только на первых операциях;
в качестве технологических баз следует принимать поверхности достаточных размеров что обеспечивает большую точность базирования и жесткость закрепления заготовки в приспособлении
базовые поверхности должны иметь более высокий класс точности и наименьшую шероховатость;.
следует соблюдать принцип единства баз т.е. совмещать технологическую измерительную и конструкторскую базы.
следует соблюдать принцип постоянства баз.
В данном случае деталь ступица переднего колеса очень сложно базировать так чтобы соблюсти принцип единства баз и постоянства баз. Это связано с тем что у детали всего один наружный диаметр по которому можно базироваться. И поверхность сама по себе не достаточно точная для того чтобы базироваться по ней на 015 и 020 операции а на агрегатных операциях (010 и 015) для базирования нужды дополнительные поверхности так как необходимо точнее разместить уши фланца для правильного расположения отверстия 18+0035 на 010 операции а на операции 015 требуется правильно расположить резьбовые отверстия относительно таких же отверстий с другой стороны.
Для того чтобы обеспечить точности обработки мною предложено следующие схемы базирования детали.
Таблица схем базирования детали
Базирование за не обработанные поверхности (обработанных пов. нету). С упором в торец наибольшего диаметра для повышения точности базирования с нарушением принципа единства баз
Базирование за обработанную поверхность наибольший диаметр с упором в торец. Принцип единства баз соблюдается.
Установка детали в плоскости x-z происходит по торцу большего диаметра. Угловое положение ушей фланца по оси y фиксируется откидной планкой. Зажим происходит за диаметр 131. (Недостающие обозначения смотри в техпроцессе.)
Базирование на второй агрегатной операции происходит по двум установочным штифтам. Это позволяет с удовлетворительной точностью установить деталь относительно обшей оси и резьбовых отверстий с противоположного торца детали. (Недостающие обозначения смотри в техпроцессе.)
Базирование на Алмазно-расточная операции происходит по двум установочным штифтам. Это позволяет с удовлетворительной точностью установить деталь относительно обшей оси и препятствует её прокручиванию во время обработки
При обработки данной детали из-за небольшого числа больших и точных поверхностей не может быть альтернативных схем базирования или эти схемы базирования не способны обеспечить точность обработки или же применения других схем базирования приведёт к удлинению процесса обработки детали и экономически нецелесообразны.
10 Обоснование выбора оборудования
Выбор оборудования определяется возможностью обеспечить определенное формообразование выполнение технических требований предъявляемых к детали в отношении точности форм расположения и шероховатости поверхностей. В рамках определенного типа оборудования выбор производится по главному параметру в наибольшей степени выявляющему его функциональное значение и технические возможности. Дополнительно при выборе оборудования учитываются следующие факторы:
- соответствие производительности станка объему и типу производства;
- возможность использования станка по мощности;
- минимальная станкоемкость и себестоимость обработки;
- реальная возможность приобретения станка.
Учитывая массовый тип производства и то что обрабатываемая деталь относится к классу фланцев выбираем соответствующие специализированные станки полуавтоматы для обработки валов.
Подготовка технологических баз – токарная обработка на токарном 8-шпиндельном полуавтомате. Шесть переходов выполняются за два установа что позволяет получать высокую геометрическую точность расположения поверхностей друг относительно друга.
Обработку тринадцати отверстий с заданной точностью и производительностью можно произвести только на агрегатных станках.
Окончательную обработку отверстий под подшипники (поверхности С Д И и К) можно произвести шлифованием или растачиванием. К этим отверстиям предъявлено требование радиальное биение поверхностей С и Д не более 008 для выполнения этого требования проще всего произвести одновременную обработку обоих отверстий которую невозможно выполнить шлифованием. Для обработки отверстий выбираем алмазно-расточной станок.
Для удаления заусенцев и острых кромок нельзя применить электрохимзачисной станок так как материал детали - чугун. Удаление заусенцев производится напильником на верстаке.
Деталь обработана и перед тем как попасть на стол контролёра должна пройти промывку. В массовом производстве деталь (если она не входит за пределы габаритов позволяет её конструкция и к ней не предъявлены особые требования) промывается в ОСМ-1.
Контроль производится на столе контролёра.
Характеристика оборудования
Уровень автоматизации
Коэффициент применения станков полуавтоматов Кпа равен:
где Спа – количество станков полуавтоматов;
Собщ – общее количество станков.
11 Выбор режимов резания для каждой операции по нормативам (с подробным расчетом на две операции)
Режимы резания металлов определяются следующими основными параметрами: глубиной резания подачей и скоростью резания. Исходными данными для выборов режимов резания являются: данные об изготовляемой детали и ее заготовке данные о применяемом инструменте и оборудовании. При много инструментальной обработке расчет режимов резания производится по лимитирующему инструменту.
Выбранный режим резания скорректированный по паспортным данным станка проверяется по мощности электродвигателя. Мощность потребная на резание должна быть меньше эффективной мощности станка.
Расчёт режимов резания на операцию 005 Токарная 8-шп.
Состояние поверхности
Материал режущей части
Зная скорость резания и диаметр обработки вычисляем обороты шпинделя.
где V - рассчитанная скорость резания
D - диаметр обработки
Полученные обороты сверяем с оборотами в паспорте станка. При необходимости уменьшаем в меньшую сторону (допускается увеличение числа оборотов шпинделя не более 5%). Зная точное число оборотов шпинделя уточняем скорость резания.
Расчёт машинного времени.
где L - длинна рабочего хода
Лимитирующий переход по времени обработка -- расточка центрального отверстия на позиции III
Режущий инструмент: 1625 ВК8
Определение частоты вращения шпинделя
Определение основного времени
Назначение режимов резания на операцию: 020 Алмазно-расточную. Станок алмазно-расточной ОС-4555. Режущий инструмент резец ВК2.
12 Расчет норм времени (табличное нормирование 2-х операций)
Технические нормы времени в условиях массового производства устанавливаются расчетно-аналитическим методом. При серийном производстве рассчитывается норма штучного времени Тшт дополнительно подготовительно-заключительное время Тп.з и штучно-калькуляционное время Тшк.
Норма штучного времени рассчитывается по следующей формуле :
Тшт=То+Тв+Ттех+Торг+ Тотд
или упрощённая формула Тшт=11(То+Тв)
То — основное технологическое время мин.; затрачивается на непосредственное осуществление технологического процесса т.е. на изменение формы размеров и качества обрабатываемой поверхности детали основное (технологическое ) время для нормируемой операции рассчитано в разделе «Расчёт режимов резания»
Тв — вспомогательное время мин.; расходуется рабочим на действия обеспечивающие выполнение основной работы. При расчете нормы штучного времени учитывается только часть вспомогательного времени не перекрываемая машинным временем
При определении нормы вспомогательного времени суммируют следующие его элементы (на многошпиндельном токарном полуавтомате время на установку и снятие детали очистку приспособления от стружки и измерение детали перекрывается машинным временем):
Время на установку и снятие детали
Время на приемы управления станком
Время на очистку приспособления от стружки
Время на измерение детали
Оперативное время Топр=То+Тв
Ттех — времени на техническое обслуживание рабочего места которое затрачивается на смену затупившегося режущего инструмента на регулировку и под наладку станка во время работы и на уборку стружки на рабочем месте во время работы. Определяется в процентах от оперативного времени Топ. (при одном инструменте)
Торг — времени на организационное обслуживание рабочего места которое требуется для раскладки инструмента в начале смены и уборки его в конце смены осмотра и опробования оборудования получения инструктажа в течение рабочего дня смазки и чистки станка в течение смены и уборки рабочего места в конце смены. Определяется в процентах от оперативного времени Топ.
Тотд — время перерывов на отдых и личные надобности мин.
Время перерывов на отдых и личные надобности зависит от веса обрабатываемой детали и определяется в процентах от оперативного времени Топ.
Нормирование 005 операции Токарная 8-шп.
мин. (лимитирующее время на операции)
времени на техническое обслуживание станка мин.
Время на смену инструмента мин.
Стойкость инструмента
Время на организационное обслуживание
Торг=17% Топр=0017×11=002 мин
время перерывов на отдых и личные надобности рабочего мин.
Тотд=6% Топр=6×11=007 мин
Нормирование 020 операции Алмазно-расточная
7 мин. (основное время на операции)
tуп =002+003+002=007 мин
Сводим все нормы времени в таблицу.
Таблица норм времени
Средний коэффициент загрузки К з.с.=0811
13 Назначение разряда работы
В предлагаемом технологическом процессе обработки детали станки работают в режиме станков-полуавтоматов. Такие станки налаживают на выполнение работы наладчики а не основные производственные рабочие.
Согласно тарифно-квалификационному справочнику работу на налаженных станках выполняют рабочие 2 разряда. На контрольные операции назначают контролеров 3-4 разрядов.
В соответствии с сегодняшним состоянием цен и уровня зарплат для улучшения качества выпускаемой продукции и увеличения заработной платы производственных рабочих работу на автоматических станках будут выполнять рабочие 4 разряда.
4 Сравнения по трудоемкости одной из измененных по сравнению с базовым техпроцессом операций
Элементы штучного времени
Базовые операции 005 010 и 030
То - основное время на операцию
Тв - вспомогательное время на операцию
Ттех - время на техническое обслуживание станка
Торг-время на организационное обслуживание рабочего места
Тотл - время на отдых и личные надобности рабочего
Штучное время на операцию
Повышение производительности труда почти в 4 раза
15 Разработка программы на операцию выполняемую на станке с ПУ
Конструкторская часть
1 Описание конструкции станочного приспособления
Приспособление предназначено для расточки одновременно двух отверстий под подшипники 62Р7 и 72Р7.
Проектируемое приспособление относится к специальным. Оно имеет постоянные установочные базы и зажимающие элементы.
Его конструкция представляет собой: корпус - 2. (литой) с профилем в виде швеллера в его основании есть 4 отверстия для крепления к столу станка. В средней части корпуса есть большое отверстие в котором четырьмя винтами - 15 закреплена установочная втулка - 3. В установочной втулке стоят два установочных штифта - 4. Выше расположена колодка - 13 которая крепится на четырёх винтах - 14. Точность расположения относительно корпуса обеспечивают два штифта - 21. К верхней части корпуса через прокладку - 9 крепится четырьмя болтами - 17 пневмоцилиндр в сборе - 1. его шток соединён с вилкой - 10 (выполняющей роль плеча) по средством оси - 20. Для лишения оси возможности свободно перемещаться в ней есть отверстие куда вставляется шплинт - 19. Для продления срока эксплуатации оси и шплинта между шплинтом и вилкой стоит шайба - 18. Для того чтобы вика могла выполнять роль плеча ей нужна точка опоры роль которой выполняет серьга - 8. Серьга соединяет вилку и колодку осями аналогичной двадцатой. Вилка соединена с рычагом - 6 по средством специального штифта - 7. который препятствуя перемещению рычага по оси y позволяет ему поворачиваться вдоль той же оси на несколько градусов. В рабочем положении деталь прижимается качалкой - 5 крепящейся к рычагу при помощи двух осей - 11. Для хорошего закрепления детали качалка качается её качание обеспечивается зазором между качалкой и рычагом. Постоянство этого зазора обеспечивается шайбой - 17 которая стоит на оси между рычагом и качалкой. Что бы ось - 11 сохраняла своё положение и не выскакивала она закреплена винтом - 16. Качалка не должна вращаться свободно иначе это может привести к её неправильному расположению и тогда это может привести к поломке режущего инструмента или приспособления. Свободное вращение качалки ограничивается штифтом - 22 который позволяет её вращаться только на несколько градусов необходимых для хорошего закрепления детали.
Работа приспособления
Деталь устанавливается на установочные штифты и упирается торцом большего диаметра в установочную втулку стоящую в корпусе приспособления. Рабочий включает зажим детали (рычагом на чертеже не показан) в правую части пневмоцилиндра поступает сжатый воздух поршень со штоком перемешаются в лево. Вилка соединенная со штоком не может свободно перемешаться так как её мешает серьга которая соединена с корпусом через колодку и другие соединительные детали. Вилка наклоняется на некоторый угол. В мессе с неё наклоняются на некоторый угол рычаг и качалка. Совместный поворот вилки рычага и качалка происходит до тех пор когда качалка не сталкивается с торцом детали. Дальше движение качалки идёт отдельно от вилки и рычага качалка благодаря специальному штифту и осям пытается занять максимально правое положение (положение наибольшего соприкосновения поверхностей качалки и детали) заняв это положение вилка рычаг и качалка останавливаются и деталь становится надёжно закрепленной.
Снятие детали происходит следующим образом. Рабочий включает разжим детали (рычагом на чертеже не показан) в левую части пневмоцилиндра поступает сжатый воздух поршень со штоком перемешаются в право тянет за собой вилку вилка рычаг и качалка наклоняются на некоторый угол. Когда поршень доходит до конца вилка рычаг и качалка занимают положение достаточное для свободного снятия детали со штифтов.
Расчёт усилий зажима
Силы резания направлены навстречу
Расчёт момента резания
Разницу в моментах резания воспринимают 2 штифта по этому усилие зажима необходимы только для того чтобы предотвратить вибрацию детали при обработке и предохранения детали от случайного сдвига.
Для зажима детали принимаем диаметр пневмоцилиндра равным D=100мм.
Определяем усилия на штоке
Где: Руд –Удельное давление воздуха в системе Па (Нм2)
Определяем усилие зажима
Спроектированное контрольное приспособление служит для:
- проверки соосности отверстий С и Д не более 008мм.
- проверки биения торцев И и К относительно А не более 0046мм.
- проверки биения торца А не более 02мм. на R 100мм.
- проверки биения торца Б не более 02мм. на R 52мм.
- радиальное биение поверхности Ж не более 015мм.
Станочное приспособления представляет собой комплект из 2-х пробок и 5-ти калибров.
Обе пробки предназначены для проверки соосности отверстий С и Д и так же в рабочем положении являются базой для измерений. Калибры нужны для проверки биения.
Пробка - 1. состоит из: пробки ручки скалки (длинная проходящая насквозь в центральное отверстие ступицы) штифт (крепит ручку и скалку в нутрии пробки).
Пробка - 2. состоит из: пробки и ручки.
Калибры - 3 4 7. состоят из: калибра в него крепятся две установочные втулки (для установки калибра на ручку пробки) одна из которых упорная (упирается в торец пробки). На внешнем диаметре калибра есть ухо на которое крепятся крепёжные детали (стойки рейки и штанги которые крепятся между собой штифтами) которые позволяют надёжно закрепить индикатор в нужном положении.
Калибры - 5 и 6 отличаются по конструкции. Они имеют ухо другой формы в которое крепится не стойка (как у калибров - 3 4 7) а втулка в паре с другой втулкой они являются корпусом для щупа (и установочным местом для индикатора). Во втулках расположена отжимающая пружина (отжимает щуп) и другие крепёжные элементы. Индикатор касается щупа который позволяет ему добраться до внутренней поверхности К (и И) и проконтролировать её.
Организационная часть
Требуемое количество станков на операцию
Ошибка! Объект не может быть создан из кодов полей редактирования.
где tшт - штучное время на операцию
t - такт выпуска деталей [мин]
где Fд - действительный годовой фонд времени оборудования в две смены (считается равным 3720ч )
Коэфицент загрузки оборудования
Где Спр - принятое количество станков на операцию [ед] (получаем путём округления расчетного значения до ближайшего большего целого числа)
Средний Коэфицент загрузки оборудования проектируемого участка
где SСрасч SСпр. сумма расчётного и сумма принятого оборудования на участке
Такт выпуска деталей уже рассчитан в пункте 1.3 и равен t=186 мин.
Диаграмма загрузки оборудования
3 Расчёт потребного количества персонала участка
3.1 Основных рабочих
Количество основных производственных рабочих принимаем по количеству станков с учётом 2-х сменной работой участка.
Данные приведены в таблице.
3.2 Расчет возможности применения многостаночного обслуживания и совмещения профессий
Расчет возможности применения многостаночного обслуживания производится для операций 010 и 015 агрегатных.
Условие многостаночного обслуживания. То > Тручн
где : Тручн - ручное время работы
Тручн =Тв+Тнавл+Тконр+Тперех
где : Тв - вспомогательное время. мин.
Тнавл - время наблюдения. мин.
Тконр - время на контроль обработанных деталей. мин.
Тперех- время перехода от станка к станку. мин.
Тручн=03+02+03+02=1 мин.
Применение многостаночного обслуживания возможно.
3.3 Количество вспомогательных рабочих
Количество вспомогательных рабочих определяется по принятым нормативам. В рамках дипломного проекта расчёт экономической части дипломного проекта производится при помощи компьютерной программы "Экономика". Все данные можно просмотреть в таблице № 3.
Так как все необходимые все необходимее расчёта сделаны программой а данные есть в таблицах нет необходимости проводить повторные расчёты.
3.4 Инженерно-технических работников
Заводской техпроцесс разработан для конкретных производственных условий с использованием оборудования имеющегося в цехах с учётом его износа.
В предлагаемом технологическом процессе в место трёх токарных операций применяется токарный 8-шп. полуавтомат.
Все принятые в процессе решения направлены на сокращение станков рабочих сокращение площади участка и затрат энергоносителей повышение производительности труда и снижение себестоимости обработки детали.
1 Краткая характеристика основных прогрессивных решений внесенных в проект
Три токарных многорезцовых операции из базового тех процесса собранны в одну токарную 8-шп. что увеличивает производительность токарной обработки почти в 4 раза по сравнению с базовым техпроцессом (обработка отверстий под подшипник была почти полностью перенесена в токарную обработку).
В место обработки поверхностей зенкерами на агрегатных операциях производится обработка эти поверхности более дешевыми резцами на токарной операции.
Список использованной литературы
Справочник технолога-машиностроителя. В 2-х т. Под ред. Косиловой А.Г. и Мещерякова Р.К.. — М.: Машиностроение 2001г.
Косилова А.Д. Мещеряков Р.К. Калинин М.А. Точность обработки заготовок и припуски в машиностроении. Справочник технолога. — М.: Машиностроение 1985г..
Барановский Ю.В. Режимы резания металлов Машиностроение 1972г.
Данилевский В.В. Технология машиностроения М.: Высшая школа 1984г.
Допуски и посадки. Справочник. В 2-х ч. В. Д. Мягков М. А. Палей А. Б. Романов и др. — Л.: Машиностроение 1983г.
Егоров М. Е. Основы проектирования машиностроительных заводов. Изд. 6-е переработ. и доп. Учебник для машиностроит. вузов. М. «Высш. школа» 1969г.
Корсаков В. С. Станочные приспособления. — М.: Машиностроение 1978г.
Нефедов Н.Л. Дипломное проектирование в машиностроительных техникумах М: Высшая школа 1986г.
Курсовое проектирование по технологии машиностроения.Под общ. ред. А. Ф. Горбацевича. — Минск: Высшая школа 1975г.
Ансеров М. А. и др. Приспособления для металлорежущих станков. М: Машиностроение 1966г.
Холщигин В.С.; Волков Н.Ф. Расчет межоперационных припусков. Методическое руководство. ВАМК 1986г.
Корчемкин. А.Д. Режимы резания металлов НИИТАВТОПРОМ Москва 1995г.
Наладка токарная 1К620 с ЧПУ.cdw

Расточной упорныый ВК8
Подрезной упорныый ВК8
Расточной упорныый ВК2
* Размер для справок
** размер обеспечиваемый режущим инструментом
Операция 005-1 Токарная мод. 16К20Ф3C32
План участка.cdw

Скребковай транспортёр
Рабочее место станочника
Путь движения детали
Площадь участка цеха 168
Удельная полщадь 28 м
Заготовка.cdw

Материал заменитель СЧ18
Точность отливки 11Т-0-0-11См 1
Неуказанные линейные уклоны 1
На необрабатываемых поверхностях допускаются раковины
наибольшим измерением 5мм.
На обрабатываемых поверхностях допускаются:
не превышающие припуск на механическую обработку;
б) остатки залива по линии разъёма высотой и толщиной
в) остаток питателя высотой не более 2мм или вылом глубиной
На необрабатываемых обрабатываемых поверхностях
допускается остатки пригара в местах переходов и сопряжений
не удаляемые дробемётной отчисткой.
На обрабатываемых поверхностях кроме С
раковины глубиной до 3мм
наибольшим измерением 3мм
дящие до контуров поверхностей и отверстий ближе 3мм
количестве не более 6 шт.
На плоскости "Л" допускается наличие ужимин и скопление
выводимые мех. обработкой.
Допускается исправление литейных дефектов по инструкции И-7.
Покрытие грунтовка ГФ-0119 ГОСТ 23343-79.
Маркировать № модели
№ дублёра шрифтом h7 ГОСТ 2.304-81
Наладка токарная 1К282.cdw

Агрегатрая.cdw

Станочное присособление.cdw

Контрольноеприспособление.cdw

оси соотведствуюшего калибра (оси дет. №2 и 17) в пределах
Износ калибров (дет. №1
и 25) суммарный люфт с
соотведствуюшими оправками более 0
Калибры дет. №1; дет. №15 и дет. №25 (в сборке с дет. №2 и 17)
притерать по соотведствуюши оправкам для лёгкого и
беззазорного движения
Конторольно измерительное
ВАМК 151001. БДП. 00-00
Деталь (Дубликат синьки + исправления).cdw

Точность отливки 11Т-0-0-11См 1
На необрабатываемых поверхностях допускаются раковины глубиной до 3мм.
наибольшим измерением до 5мм.
На обрабатываемых поверхностях кроме С
И допускаются раковины глубиной до 3мм.
в количестве не более 6 шт.
Допуск радиального биения поверхностей С и Д относительно друг друга 0
Допуск непостоянства диаметров С и Д в в поперечном и продольном сечениях 0
* Размеры для справок.
** Обеспечивается инструментом.
Покрытие: Эмаль КМЛ-13 тёмно серая ТУ 2312-021-16952278-95. V. У1. Система покрытия 1 ГОСТ 6572-91
Рекомендуемые чертежи
- 04.11.2022
- 13.03.2024
- 11.05.2024
- 01.07.2014
- 07.09.2016