Тележка электрического мостового крана гп 16 тонн




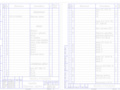
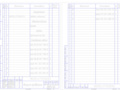
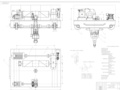
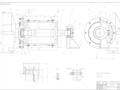
- Добавлен: 25.10.2022
- Размер: 2 MB
- Закачек: 0
Описание
Состав проекта
![]() |
![]() ![]() |
![]() |
![]() ![]() ![]() ![]() |
![]() ![]() ![]() ![]() |
![]() ![]() |
![]() ![]() |
![]() ![]() |
![]() ![]() |
![]() ![]() |
![]() ![]() ![]() ![]() |
![]() ![]() ![]() |
![]() ![]() |
![]() ![]() ![]() |
![]() |
![]() ![]() |
![]() ![]() |
![]() ![]() |
![]() ![]() ![]() ![]() |
![]() ![]() ![]() ![]() |
![]() ![]() |
![]() ![]() ![]() ![]() |
![]() ![]() |
![]() ![]() ![]() ![]() |
![]() ![]() |
![]() ![]() |
![]() ![]() ![]() |
![]() ![]() |
![]() |
![]() ![]() |
![]() ![]() ![]() ![]() |
![]() ![]() ![]() ![]() |
![]() ![]() |
![]() ![]() |
![]() ![]() |
Дополнительная информация
Лист 3.dwg

Крышка опоры барабана
Корпус опоры барабана
радиальный сферический
Шпилька ГОСТ22032-76
Барабан.dwg

кафедра ПТМиР гр. М-47041
Рабочие размеры с неуказанным предельным отклонением
Компоновка тележки_Механикс.dwg

центра тяжести груза на крюке
крюке механизма подъема.
центра тяжести груза на
Определение координаты
ПЗмоя.doc
- двигатель соединен с редуктором зубчатой муфтой с промежуточным валом;
- роль тормозного шкива выполняет одна из полумуфт;
- отсутствуют открытые зубчатые передачи;
- концы быстроходного и тихоходного вала редуктора выходят в одну сторону;
- конец тихоходного вала редуктора имеет зубчатый венец и расточку под опорный подшипник оси барабана;
- для выравнивания длины канатов двух параллельно-установленных полиспастов служит уравнительный блок.
Далее выполняются предварительные расчеты с целью определения основных параметров изделий входящих в состав механизмов. Параметры стандартизированных изделий определяем с учетом Госгортехнадзора: крюковая подвеска канат уравнительные блоки. При выборе крюковой подвески учтены два условия: 1) грузоподъемность ее должна быть не меньше заданной; 2) режим работы должен соответствовать режиму работы механизма. Расчет каната сводится к выбора по ГОСТ минимально допустимого диаметра при котором его разрывное усилие не может быть меньше значения расчетного разрывного усилия. Для кранов следует выбирать канаты как правило с маркировочной группой по временному сопротивлению разрыву 1764 МПа.
Выбор двигателя механизма подъема определяется с учетом группы режима работы а также осуществляется по расчетной мощности которая должна быть равна соответствующему значению номинальной мощности электродвигателя. По имеющимся рекомендациям был выбран двигатель повышенной надежности 4МТМ ПНД. Следует отметить что двигатель обладает перегрузочной способностью и может быть выбран мощностью на 20-30% меньше расчетной. В зависимости от параметра цена-качество двигатель может быть выбран и более низкого класса но с учетом режима работы механизма.
При выборе двигателя механизма передвижения были учтены условия соответствия относительной продолжительности включения электродвигателя и самого механизма а также номинальная мощность должна быть равна или несколько больше расчетной.
Выбор редукторов для механизма подъема и передвижения производился по эквивалентному моменту и по требуемому передаточному числу для данного механизма. Для механизма подъема был выбран горизонтальный цилиндрический редуктор типа Ц2У для механизма передвижения – вертикальный редуктор типа ВКУ закрепленный на вертикальной плите.
Муфты для соединения валов двигателей с редукторами редукторов с колесами были выбраны по диаметрам концов валов соединяемых данной муфтой. Параметры муфт также должны соответствовать передаваемому вращающему моменту который должен быть не ниже допускаемого.
При выборе тормоза механизма подъема при заданном режиме работы М5 рекомендуется применять тормоза с электрогидравлическим приводом типа ТКГ или ТКТГ. Тормоз механизма передвижения выбирался с учетом работы крана в закрытом помещении. Расчетный тормозной момент определяется для движения без груза под уклон в положении когда реборды колес не задевают за головки рельсов.
Компонование механизмов на раме тележки должно обеспечить ее минимальные габариты и массу равномерную нагрузку на ходовые колеса при номинальном грузе на крюке.
Далее были выполнены чертежи общего вида тележки (Лист 1) сборочный чертеж механизма подъема (Лист 2) а также сборочный чертеж барабана (Лист 3).
Также были проведены проверочные расчеты. Для двигателей произвели проверку на время разгона которая должна быть в пределах допустимых значений. После определили величину ускорения в период пуска. Ускорение не должно быть ниже определенной величины так как значение ускорения влияет на прочность выбранных составных частей механизмов.
Для тележки выполнили проверку запаса сцепления колес тележки при разгоне с целью убедиться что тележка не будет буксовать при работе с грузом и без груза.
В самом конце были составлены спецификации к соответствующим чертежам.
Механизм: тележка мостового электрического крана.
Все исходные данные сведены в таблицу 1.
Наименование величины
Обозначение величины
Скорость передвижения тележки
Режим работы крана - 5М (Тяжёлый). Ток переменный. Все зубчатые передачи помещены в закрытые корпуса.
II Предварительные расчеты механизмов
Выбор крюковой подвески.
Выбор типоразмера крюковой подвески производится по двум условиям:
)ее грузоподъемность не должна быть меньше заданной;
)режим работы подвески должен соответствовать режиму работы механизма.
Выбрана крюковая подвеска: 4-16-406 по ОСТ 24.191.08-81.
Определение кратности полиспаста.
По выбранной крюковой подвеске (см. рис. 1) мы определяем кратность полиспаста:
где ZK - число ветвей каната на которых висит груз;
ZК.Б. - число ветвей каната которые навиваются на барабан.
Выбор каната производят по максимальному статическому усилию которое рассчитывается по формуле:
где G - вес номинального груза и крюковой подвески;
hП - к.п.д. полиспаста.
G = (16000 + 368)×9 81=160570 08 Н.
Канат выбирается из условия что разрывное усилие в целом F больше произведения максимального статического усилия Smax на коэффициент запаса прочности zР=710 т.е.:
F ³ 7 10×20692 02 =146913 34 кН.
Итак выбираем канат двойной свивки типа ЛК-Р конструкции 6x19 (1+6+66)+1о.с. ГОСТ 2688-80 диаметр которого dК=165 мм разрывное усилие 152 кН.
Второе условие – должно выполняться соотношение между диаметром выбранного каната и диаметром блока крюковой подвески:
где Dбл – диаметр блока по дну ручья;
h2 =25 – коэффициент регламентируемый нормалями ГГТН и зависящий от режима работы.
Установка верхних блоков
Минимальные диаметры барабанов блоков и уравнительных блоков огибаемых стальными канатами определяются по формулам:
где Dб D2 D3 – диаметры соответственно барабана блока уравнительного блока по средней линии навитого каната;
h1 h2 h3 – коэффициент выбора диаметров соответственно барабана блока и уравнительного блока;
dk – диаметр каната.
Минимальные коэффициенты для выборов диаметров барабана блока и уравнительного блока:
Размеры профиля ручья (см. рис.1) Рис.1 Профиль ручья блока
должны соответствовать следующим
R = (0 530 56)×16 5 = 8 75 9 24 = 9 мм;
Н = (1 41 9)×16 5 =23 1 31 35 = 30 мм;
r = 0 2×dК r=0 2×16 5 = 3 3 мм.
При соблюдении этих условий
канат может отклоняться от
плоскости симметрии ручья не
Длина барабана рассчитывается по формуле:
lK - длина одного гладкого концевого участка.
длина одного нарезанного участка:
Здесь: t=dK+(2 3) - шаг навивки каната t=16 5 +2 = 18 5 мм;
zРВ= - число рабочих витков для навивки половины рабочей длины каната.
zРВ=25 4 Принимаем zРВ=25.
zНВ=5 6 - число неприкосновенных витков необходимых для разгрузки деталей крепления каната на барабане;
zКР=3 4 - число витков для крепления конца барабана.
lH = 18 5×(25 + 5 +3) = 617 9 мм.
длина гладкого среднего участка определяется по формуле:
BH ≤ l0 BH + 2×hmin×tgg.
Здесь: BH - расстояние между осями наружных блоков крюковой подвески (табличное значение) BH =260 мм;
g=60 - допустимый угол отклонения каната.
0 ≤ l0 260+2×1200×tg60 = 512 мм.
Принимаем l0=400 мм.
длина гладкого концевого участка необходимого для закрепления барабана в станке при нарезании канавок:
lK = (45)×dK lK = (45)×16 5 = 66 82 5 мм.
Длина барабана: LБ=2×617 9 + 400 + 2×66 = 1767 8 мм.
Отношение длины барабана к его диаметру:
LБDБ = 1767 8400 = 4 41 что вполне приемлемо.
Выбор электродвигателя.
Выбор двигателя производится по относительной продолжительности включения (при тяжёлом режиме работы - 60%) и по необходимой статической мощности при подъеме груза максимального веса:
- коэффициент использования ЭД в зависимости от типа поднимаемого груза;
- коэффициент запаса определяемый условиями работы при высокой температуре среды;
- коэффициент использования ЭД при регулировании скорости;
- коэффициент дополнительных пускотормозных нагрузок;
- коэффициент относительной продолжительности включения;
- мощность статической нагрузки при подъеме номинального груза с номинальной скорость.ю;
Для режима работы 5М:
По этим параметрам выбираем крановый электродвигатель серии 4MTМ225 М6 с фазным ротором; мощность на валу N = 37 кВт частота вращения выходного вала 955 обмин масса т = 360 кг.
Типоразмер редуктора выбираем по расчетному эквивалентному вращающему моменту на валу Ме с учетом режима работы необходимого передаточного числа и частоты вращения быстроходного вала.
Требуемое передаточное число передачи:
Эквивалентный момент на выходном валу редуктора:
kД – коэффициент долговечности;
kQ – коэффициент переменности нагрузки;
kt – коэффициент срока службы.
где k – коэффициент нагружения.
И так для тяжелого режима работы:
класс нагружения – В4 В4 = 1 00;
класс использования –t = 6300 ч.
где zp – суммарное число циклов контактных напряжений зуба шестерни тихоходной ступени редуктора;
z0 – базовое число циклов контактных напряжений для типажных редукторов z0 = 125106;
где zТ – число циклов нагружения на тихоходном валу редуктора;
UТ – передаточное число тихоходной ступени редуктора; принимаем его как UТ=5.
Значение zТ определяем как:
где - частота вращения тихоходного вала редуктора;
- машинное время работы механизма ч.
n= 1с - частота вращения тихоходного вала редуктора
nW = 1 - число зубчатых колес сцепляющихся с тихоходным колесом редуктора;
kД = kQkt = 0 73 1 = 0 73.
Максимальный вращающий момент на тихоходном валу рассчитывается по формуле:
GП= mП ×g - вес крюковой подвески GП=368×9 81=3 61 кН;
hП hБ - к.п.д. полиспаста и барабана соответственно (при установке барабана на подшипники качения его к.п.д. принимают 098).
По всем рассчитанным параметрам выбираем цилиндрический двухступенчатый редуктор типа Ц2У-315 с характеристиками: ином=31 5 Tном=8 6 кН×м h=096 m=510 кг n=1000 обмин.
Расчетный тормозной момент:
где - коэффициент запаса торможения кранов общего назначения;
- статический крутящий момент при торможении создаваемый весом номинального груза на валу на котором установлен тормоз. Рассчитывается по формуле:
Здесь hМ=hП×hБ×hР - к.п.д. всего механизма (равно произведению к.п.д. полиспаста барабана и редуктора) hМ=096×098×096=09;
ИМ=КП×иР - передаточное число механизма от барабана до вала иМ=4×31 5=126.
ТТ.Р.1 5 × 229 38 = 334 07 Н×м.
По рассчитанным параметрам выбираем колодочный тормоз с электромагнитным приводом переменного тока ТКГ-300 со следующими характеристиками: Тном=800 Н×м m=55кг.
Выбор соединительных муфт
Муфты выбираем по наибольшему диаметру концов соединяемых валов.
Затем проверяют прочность муфты из условия:
где - номинальный крутящий момент;
- передаваемый крутящий момент;
- коэффициент ответственности равный 1;
- коэффициент условий работы машины равный 1 2;
- коэффициент углового смещения равный 1 25.
Номинальный крутящий момент рассчитывается по формуле:
Для соединения валов двигателя и редуктора выбираем тип муфты – зубчатую с промежуточным валом. Такая муфта хорошо компенсирует возможные неточности монтажа и может передавать большие крутящие моменты.
Диаметры концов валов: Выбираем типоразмер: муфта 2-го типа МЗП-4 с Тном=5600Нм; n =3350обмин.
Механизм передвижения
Определение статической нагрузки на колеса
Выбор колес производится по максимальной статической нагрузке которая для тележек определяется по формуле:
где GГ GТ - вес номинального груза главного подъема и тележки соответственно. Вес тележки для легкого режима работы в предварительных расчетах принимают » (0 40 5)×GГ:
GТ = (0 250 35)×156 94×103=(39 2454 94)×103 принимаем GТ=49 05 кН.
КН =1 2 - коэффициент неравномерности распределения нагрузки на колеса.
По ОСТ 24.090.44-82 выбираем при нагрузке (50100) кН диаметр ходового колеса DК=400 мм. Затем по ОСТ 24.090.09-75 подбираем соответствующую единицу «Колесо в сборе» и определяем основные размеры колеса:
В=70 – ширина головки рельса см;
В0=55 – ширина плоского рельса см;
r=30 – радиус закругления головки см.
Определение сопротивления движению тележки
Полное сопротивление передвижению тележки в период разгона приведенное к ободу колеса рассчитывается по формуле:
WТР - сопротивление создаваемое силами трения определяется по формуле:
Здесь: m = 06 мм - коэффициент трения качения колес по рельсу;
f = 0015 - коэффициент трения в подшипниках колес;
d - диаметр посадки подшипника на вал ходового колеса;
=25 - коэффициент дополнительных сопротивлений (трения реборд и токосъемного устройства).
WУ - сопротивление создаваемое уклоном пути; рассчитывается:
где a = 0002 - уклон рельсового пути.
WВ - сопротивление создаваемое ветром. При работе крана в помещении WВ=0.
Wстат=0 478+3 58 = 4 058 кН.
Определим сопротивление создаваемое при разгоне силами инерции. При скорости движения тележки меньше 1мс =1 25.тележки равна 8т. Находим массу поступательно движущегося объекта:
По таблице 2.16 принимаем значение:
Сопротивление создаваемое силами инерции определяют по формуле:
где - коэффициент учитывающий инерцию вращающихся частей механизма;
а – ускорение при разгоне.
Значение а можно предварительно принять равным а = (05 10) где - допускаемое ускорение .
Сопротивление создаваемое раскачиванием груза на гибкой подвеске:
где - угол отклонения груза от вертикали;
где - масса груза и масса подвески соответственно.
Учитывая что кран работает в помещении полное сопротивление передвижению находится по формуле:
Выбор электродвигателя
Необходимую мощность двигателя определяют по формуле:
где =08 09 - предварительное значение к.п.д. механизма; - кратность среднепускового момента двигателя по отношению к номинальному.
Предварительное значение к.п.д. механизма примем равным а значение =1 55.
Выбираем крановый электродвигатель серии MTН 112-6 с фазным ротором: мощность на валу P = 3 6 кВт частота вращения выходного вала 930 обмин; масса т = 88кг.
Передачу выбирают исходя из предварительно намеченной кинематической схемы механизма.
Типоразмер редуктора выбираем по расчетному эквивалентному вращающему моменту на выходном валу с учетом режима работы необходимого передаточного числа и частоты вращения быстроходного вала.
Определим эквивалентный момент на выходном валу редуктора:
М – группа режима работы;
В4 – класс нагружения;
А3 – класс использования.
При этом К=1 КQ=1 tмаш=6300ч.
- частота вращения тихоходного вала редуктора с-1:
- суммарное число циклов контактных напряжений тихоходного зубчатого колеса редуктора определяют по формуле:
zp – суммарное число циклов контактных напряжений зуба шестерни тихоходной ступени:
kД = kQkt = 0 605 1 = 0 605.
По условию kД принимается не меньше 0 63 следовательно принимаем kД равным 0 63.
Расчетный крутящий момент на тихоходном валу рассчитывается по формуле: ;
где - максимальный момент двигателя:
- номинальный момент двигателя.
По всем рассчитанным параметрам выбираем цилиндрический двухступенчатый редуктор типа ВК-610М с характеристиками: ином=31 5 Мном= 6 кН×м h=091 m=450 кг.
Отклонение расчетного значения передаточного числа от принятого составляет:
D==1 26% что допустимо.
Согласно правилам ГГТН РФ в данном механизме передвижения должен быть установлен тормоз т.к. тележка предназначенная для работы в помещении на надземном рельсовом пути.
Расчетный тормозной момент механизма при работе крана в закрытом помещении определяется для движения без груза под уклон в положении когда реборды колес не задевают за головки рельсов:
где - соответственно моменты приведенные к валу тормоза создаваемые уклоном инерцией тележки и силами трения в ходовых колесах.
Эти параметры можно определить по следующим зависимостям:
где - сопротивление передвижению тележки без груза создаваемое уклоном (a - уклон рельсового пути) инерцией тележки и трением в ходовых колесах соответственно; - передаточное число редуктора; - КПД редуктора.
Сопротивления движения тележки определяются:
Тогда тормозной момент будет равен:
По рассчитанным параметрам выбираем колодочный тормоз с электромагнитным приводом переменного тока ТКГ-160-У2-50-380-40 со следующими характеристиками: Тном=100Н×м m=215кг..
Муфты выбираем в зависимости от передаваемого вращающего момента и условий работы по формуле:
где МР - расчетный вращающий момент;
К - коэффициент запаса прочности;
МКР - действующий вращающий момент;
[МКР] - допускаемый вращающий момент для муфты.
Коэффициент запаса прочности: К=К1×К2×К3 (В этой формуле: К1 - коэффициент учитывающий степень ответственности соединения К2 - коэффициент режима работы К3 - коэффициент углового смещения).
К = К1×К2×К3 = 18×10×10 = 18.
для быстроходного вала редуктора: K=1 8×1×1 5=27 .
МКР== 118 Н×м тогда МР = 2 7× 118 = 318 6 Н×м
муфта зубчатая 2-ого типа №2 и муфта зубчатая №1 с тормозным шкивом по ГОСТ 5006-55.
для тихоходного вала редуктора: K=1 8×1×1 5=2 7.
МКР=×uР МКР = 118× 31 5 = 3717 Н×м
тогда МР = 2 7× 3717 = 10035 Н×м муфта зубчатая 2-ого типа №6 по ГОСТ 5006-55.
Компонование тележки мостового крана
Расположение механизмов на раме тележки должно обеспечить ее минимальные габариты массу и равномерную нагрузку на ходовые колеса при номинальном грузе на крюке.
Определение весов и координат центров тяжестей
Значения масс весов и координат центров тяжестей сведены в таблицу 2 (вес тормоза привода передвижения промежуточных валов и муфт невелик по сравнению с весом рамы тележки и остального оборудования поэтому их можно в расчет не принимать):
Механизм подъема груза
Механизм передвижения тележки
Определяем координаты центра тяжести порожней тележки по формулам:
Здесь G - веса отдельных сборочных единиц; X Y - координаты точек их приложения.
Координаты ОГР: YГР=-240 мм XГР=0
Определяем положение неприводных колес т.е. базу тележки из условия одинаковой нагрузки на приводные и неприводные колеса:
где GТ - вес тележки;
Y Y - расстояние от равнодействующей веса порожней тележки и груза соответственно до оси приводных колес. Окончательно принимаем Вт=2100 мм.
Определение нагрузки на ходовые колеса.
Определяем нагрузку на ходовые колеса тележки от веса порожней тележки:
Нагрузка на ходовые колеса от веса груза:
Р1G=37 86 кН = Р2 G;
Суммарные статические нагрузки на ходовые колеса:
Р1=24 5 + 37 86 = 62 3 кН;Р3 =13 5 + 42 43 = 55 93 кН;
Р2=26 + 37 86 = 63 86 кН;Р4 =15 2 + 42 43 = 57 63 кН.
Максимальная разница в нагрузках на колеса:
Т.к. разница в статической нагрузке на колеса составляет менее 15% изменение расположения колес не требуется.
III Проверочные расчеты механизмов
Проверка надежности пуска электродвигателя на время разгона
Двигатель должен разгонять механизм за достаточно короткое время иначе уменьшится производительность крана. Но с другой стороны если оно будет слишком мало то разгон будет сопровождаться большим ускорением что скажется на прочности элементов устойчивости груза и т.д. Время разгона механизма принимают равным от 1 до 2 секунд.
Для механизма подъема груза наибольшее время разгона получается при разгоне на подъем вычисляемое по формуле:
где - момент инерции при разгоне всех вращающихся частей механизма приведенный к валу двигателя;
ТСР. П. - среднепусковой момент двигателя;
ТСТ - момент статических сопротивлений приведенный к валу двигателя.
где I1 - момент инерции вращающихся масс расположенных на первом валу (он равен сумме моментов инерции ротора двигателя муфт и тормозного шкива)
g=1112 - коэффициент учета инерции вращающихся масс расположенных на втором третьем и последующих валах механизма.
где и - соответственно масса и радиус тормозного шкива а - коэффициент учитывающий распределенность массы шкива можно принять как равным 0 6.
Среднепусковой момент двигателя определяется по формуле:
ТСР П.=ТДВ.Н.×yСР П = 37015*155 = 573 73 Н×м.
где ТДВН - номинальный момент двигателя:
ТДВН= ТДВН== 370 15 Н×м;
yПСР - кратность среднепускового момента двигателя (для двигателей с фазным ротором yПСР=155).
Момент статических сопротивлений при разгоне:
Тогда фактическое время разгона:
Полученное значение находится в диапазоне рекомендуемых значений времени разгона (12 с).
Среднее ускорение груза при таком времени разгона равно:
Это значение не превышает рекомендуемое (020 мс2) для кранов работающих в механосборочных цехах.
Проверка электродвигателя на время разгона:
ТСР П.=ТДВ.Н.×yСР П ;
ТСР П.=36 971 55 = 57 3 Нм;
Момент статических сопротивлений определяем по формуле:
где WСТ=WТР+WУ - статические сопротивления: WТР - от сил трения WУ - от уклона.
WСТ = 3 58 + 0 478 = 4 058 кН.
Полученное значение не превышает допускаемое (56 с) следовательно выбранный двигатель обеспечивает необходимую интенсивность разгона.
Среднее ускорение при разгоне:
Это значение так же не превышает рекомендуемого (020 мс2).
Проверка механизма передвижения тележки на отсутствие буксования
Работа в период пуска без проскальзывания приводных ходовых колес обеспечивается при соблюдении неравенства:
где - коэффициент запаса сцепления;
- вес тележки приходящийся на приводные колеса;
- число приводных колес и общее число колес соответственно;
- максимальная сила статического сопротивления;
- сопротивление от сил инерции массы тележки;
- коэффициент сцепления колеса с рельсом при работе крана в помещении;
Принимаем что =0 и =0 получаем допустимое ускорение тележки - jдоп:
Условие отсутствия буксования: где - фактическое ускорение движения тележки которое определяется зависимостью здесь - фактическая скорость движения тележки; - время разгона механизма.
Допустимое замедление тележки при торможении (исключение явления юза) можно определить по формуле:
Условие отсутствия юза:
Проверка ходовых колес на контактные напряжения обода и рельса
Напряжение МПа в контакте обода колеса и рельса с плоским рельсом определяется по формуле:
где - коэффициент неравномерности распределения нагрузки по ширине колеса принимают = 20; - ширина рельса см; - рабочая ширина плоского рельса см; - коэффициент учитывающий влияние касательной нагрузки на напряжение в контакте равный 1 05 при ; - максимальная статическая нагрузка на колеса кН; - коэффициент динамичности пары «колеса-рельс».
Контактные напряжения не должны превышать допускаемые напряжения МПа при приведенном за срок службы числе оборотов колеса N: где - допускаемые напряжения при
Приведенное и полное число оборотов колеса за срок службы определяют соответственно по формулам:
В этих зависимостях - коэффициент приведенного числа оборотов колеса; - средняя скорость передвижения колеса мc; - номинальная скорость передвижения мc; - коэффициент зависящий от отношения времени неустановившегося движения tН (суммарное время торможения и разгона) к полному времени передвижения t:
принимаю равным 0 6 соответственно коэффициент =07.
- машинное время работы колеса ч за срок службы в зависимости от группы режима работы: принимаем = 12500 часов.
Значения определяют зависимостью:
где - число оборотов колеса под нагрузкой соответственно.
При отсутствии исходных данных по нагрузке колеса значения можно принять в зависимости от отношения минимальной нагрузки на колеса к максимальной нагрузке P: тогда получаем что = 0 5.
Находим контактные напряжения
Проверяем по условию:
Таким образом условие выполняется
Напряжениями изгиба и кручения в стенке барабана можно пренебречь.
Напряжения сжатия в стенке барабана:
где - максимальное статическое усилие каната
- толщина стенки (для стали )
Прочность барабана обеспечена.
При выполнении данного курсового проекта в разделе выбора электродвигателя для механизма передвижения по одной методике которая брала за основу сравнение расчетной мощности с номинальной мощностью по каталогу на первой стадии а далее с учетом теплового режима для принятой системы электропривода и заданного режима работы т.е.: получаемая мощность оказывалась достаточно большой. Что далее в проверочных расчетах на время разгона механизма передвижения давало значение времени слишком маленькое примерно равное 25 сек что вело к увеличению ускорения выше допускаемой величины т.е. появлению нежелательных динамических нагрузок.
Вследствие этого был выбран другой вариант выбора электродвигателя основанный на достаточно простой формуле которая учитывала полное сопротивление передвижению тележки скорость передвижения к.п.д. механизма и кратность среднепускового момента двигателя по отношению к номинальному. В итоге была получена мощность в 2 раза ниже полученной по вышеприведенному методу время разгона находилось в диапазоне рекомендуемых значений ускорение не превысило допускаемого. Таким образом удалось получить менее габаритный и менее дорогостоящий электродвигатель который также облегчил конструкцию.
Была проведена проверка прочности барабана полученное значение не превысило допустимого.
Данный курсовой проект дал возможность освоить навыки технического проектирования разработки технической документации а также получить представления о принятии технико-экономических решений.
При проектировании того или иного механизма необходимо учитывать помимо технических обоснований экономические аспекты которые могут повлиять на выбор того или иного параметра а также значительно расширить диапазон получаемых вариантов.
IV Список используемой литературы
Александров М.П. Подъемно-транспортные машины: Учеб. для машиностроит. спец. вузов. - 6-е изд. перераб. - М.: Высш. шк. 1985.
Курсовое проектирование грузоподъемных машин: Учеб. пособие для студентов машиностроит. спец. вузов С.А. Казак В.Е. Дусье Е.С. Кузнецов и др.; под ред. С.А. Казака. - М.: Высш. шк. 1989.
Курсовое проектирование деталей машин. С.А. Чернавский К.Н. Боков И.М. Чернин и др. - 2-е изд. перераб. и доп. - М.: Машиностроение 1988.
Металлургические подъемно-транспортные машины: Методические указания к курсовому проектированию Ю.В. Наварский. Екатеринбург: УГТУ 2001.
Подъемно-транспортные машины. Атлас конструкций под ред. М.П. Александрова и Д.Н. Решетова. - М. 1987.
тиутул.doc
имени Первого Президента России Б. Н. Ельцина
Кафедра “Подъемно транспортные машины и роботы”
Расчетно-пояснительная записка
Тема: Проектирование тележки электрического мостового крана
гр. М-47041: Макарова Э. С.
Преподаватель: Миронов В. И.
Екатеринбург-2010 г.
Спецификация.dwg

ФАО "УрФУ" им. Б.Н. Ельцина
Колесо неприводное в сборе
Колесо приводное в сборе
Механизм подъема тележки
Механизм передвижения тележки
лист1 на печать.dwg

Передаточное число U=31
Техническая характеристика тележки
Скорость передвижения тележки Vт=37 ммин.
Частота вращения n=955 обмин.
Электродвигатель механизма передвижения тележки:
Частота вращения n=930 обмин.
Тормозной момент Мт=100 Нм.
Тормоз механизма передвижения тележки:
Тормозной момент Мт=300 Нм.
Канат двойной свивки типа ЛК-Р
Диаметр колеса D=400 мм.
Грузоподъемность Q=16 тонн.
Высота подъема груза Н=8 м.
Группа режима работы - 5М.
Продолжительность включения ПВ=60%.
Скорость подъема груза Vп=10 ммин.
Электродвигатель механизма подъема груза:
Редуктор механизма подъема груза:
Редуктор механизма передвижения тележки:
Тормоз механизма подъема груза:
ФАО УрФУ" им. Б. Н. Ельцина
Схема навивки каната на барабан
Нагрузки на ходовые колеса
Барабан.dwg

кафедра ПТМиР гр. М-47041
Рабочие размеры с неуказанным предельным отклонением
Содержание.dwg

Выбор крюковой подвески 5
Определение кратности полиспаста 5
Установка верхних блоков 6
Установка барабана 7
Выбор электродвигателя 8
Выбор соединительных муфт 11
Механизм передвижения 11
Определение статической нагрузки на колеса 11
Определение сопротивления движению тележки 11
Выбор электродвигателя 13
Выбор соединительных муфт 15
Компонование тележки 16
III Проверочные расчеты механизмов 18
Проверка электродвигателя на время разгона 19
Мехнизм передвижения 19
Проверка на отсутствие буксования 21
Проверка ходовых колес на контактные напряжения обода
Прочность барабана 23
IV Список используемой литературы 25
Компоновка.dwg

Лебедка.dwg

ФАО "УрФУ"им. Б.Н. Ельцина
Схема расположения отверстий под болты
Спецификация2.dwg

ФАО "УрФУ" им. Б. Н. Ельцина
Болт М12-50 ГОСТ 7798-70
Болт М16-60 ГОСТ 7798-70
Болт М20-30 ГОСТ 7798-70
Болт М36-80 ГОСТ 7798-70
Гайка М12 ГОСТ 5915-70
Гайка М16 ГОСТ 5915-70
Гайка М20 ГОСТ 5915-70
Гайка М36 ГОСТ 5915-70
Шайба М12 ГОСТ 6958-78
Шайба М16 ГОСТ 6958-78
Рекомендуемые чертежи
Свободное скачивание на сегодня
- 24.01.2023