Проектирование тележки электрического мостового крана 6 т




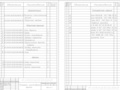
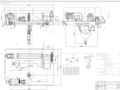
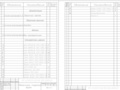
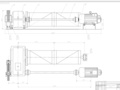
- Добавлен: 25.10.2022
- Размер: 2 MB
- Закачек: 0
Описание
Состав проекта
![]() |
![]() ![]() |
![]() ![]() |
![]() ![]() |
![]() ![]() ![]() ![]() |
![]() ![]() |
![]() ![]() ![]() ![]() |
![]() ![]() |
![]() ![]() ![]() |
![]() ![]() ![]() ![]() |
![]() ![]() |
![]() ![]() |
![]() ![]() ![]() ![]() |
![]() ![]() ![]() |
![]() ![]() ![]() ![]() |
![]() ![]() |
![]() ![]() ![]() ![]() |
![]() ![]() ![]() ![]() |
Дополнительная информация
Крюковая подвеска Силин Д.А..dwg

Общий вид Силин Д.А..dwg

Нагрузки на ходовые колеса
Схема навивки каната
* Размер для справок
Неуказанные предельные отклонения
рабочих размеров ±IT142
Высота подъема груза
Группа режима работы 6К
Грузоподъемность механизма
-передвижения тележки 45
Электродвигатель механизма
- передвижения тележки:
- передвижения тележки: Ц3вк-100
- передвижения тележки: ТКТ-100
Канат механизма подъема
ЛК-Р 6*19(1+6+66)+1о.с.
Спецификация Кр.подвески Силин Д.А..dwg

КП 23.05.01.0202.322.2020.01
КП 23.05.01.0202.322.2020.02
КП 23.05.01.0202.322.2020.03
КП 23.05.01.0202.322.2020.04
КП 23.05.01.0202.322.2020.05
КП 23.05.01.0202.322.2020.06
Механизм передвижения Силин Д.А..dwg

* Размер для справок
КП 23.05.01.0202.322.2020.02 СБ
Механизм подъема Силин Д.А..dwg

ПЗ Курсовой ГПМ Силин Д.А,.docx
РОССИЙСКОЙ ФЕДЕРАЦИИ
ФЕДЕРАЛЬНОЕ ГОСУДАРСТВЕННОЕ БЮДЖЕТНОЕ ОБРАЗОВАТЕЛЬНОЕ УЧРЕЖДЕНИЕ
«ТЮМЕНСКИЙ ИНДУСТРИАЛЬНЫЙ УНИВЕРСИТЕТ»
ПОЯСНИТЕЛЬНАЯ ЗАПИСКА
к курсовому проекту по
по дисциплине «Грузоподъемные машины»
«ПРОЕКТИРОВАНИЕ ТЕЛЕЖКИ
ЭЛЕКТРИЧЕСКОГО МОСТОВОГО КРАНА»
КП 23.05.01.0202.322.2020.00 ПЗ
Силин Дмитрий Алексеевич
к.т.н. доцент Шаруха А.В.
I. Предварительный расчет механизмов4
Механизм подъема груза4
1. Выбор крюковой подвески4
Стандартная крюковая подвеска однозначно определяет кратность полиспаста.4
3. Установка верхних блоков5
4. Установка барабана6
5. Выбор электродвигателя7
7. Выбор соединительных муфт9
Механизм передвижения11
1. Выбор кинематической схемы11
3. Определение сопротивления движению тележки12
4. Выбор электродвигателя12
5. Выбор редуктора13
Компонование тележки16
II. Проверочные расчеты механизмов подъема и передвижения20
Проверка двигателя механизма подъема на время разгона20
Проверка двигателя механизма передвижения на время разгона22
Проверка механизма передвижения тележки на отсутствие буксования без учета жесткости механизма24
III. Расчет сборочной единицы «Установка барабана»26
Определение толщины стенки барабана26
Крепление каната к барабану27
Проверка подшипников на долговечность30
Расчёт болтов соединяющих зубчатый венец с барабаном31
Спроектировать тележку электрического мостового крана. Вес поднимаемого груза F скорость подъема груза V1 высота подъема груза H скорость передвижения тележки V2 и режим работы представлены в таблице 1.
Представить расчетно-пояснительную записку с расчетом механизмов и 4 чертежа:
) общий вид тележки;
) механизм подъема груза;
) механизм передвижения тележки;
) крюковая подвеска;
I. Предварительный расчет механизмов
Механизм подъема груза
1. Выбор крюковой подвески
Выбор типоразмера крюковой подвески производится по двум условиям:
Грузоподъемность крюковой подвески не должна быть меньше заданной грузоподъёмности;
Режим работы подвески должен соответствовать режиму работы механизма.
В соответствии с тяжёлым режимом работы и грузоподъёмностью Q=6т. выбирается крюковая подвеска 2-8-500 по с ГОСТ 24.191.0881.
Стандартная крюковая подвеска однозначно определяет кратность полиспаста.
– число ветвей каната на которых висит груз;
– число ветвей каната которые навиваются на барабан.
Выбор каната производится по максимальному статическому усилию
G – вес номинального груза и крюковой подвески Н;
– число ветвей каната которые навиваются на барабан;
– кратность полиспаста;
– коэффициент полезного действия полиспаста определяется в соответствии с кратностью полиспаста.
Q – грузоподъёмность крана кг;
– масса подвески кг;
g – ускорение свободного падения мс2.
При выборе типоразмера каната должны выполняться два условия:
F0 – разрывное усилие каната в целом Н;
-коэффициент запаса прочности для подвижного каната при тяжёлом режиме нагружения;
- максимальное статическое усилие Н.
Это требование обеспечит стальной канат двойной свивки диаметром мм с разрывным усилиемН; тип каната - ЛК-Р конструкции 6х19(1+6+66)+1о.с. ГОСТ 2688-80 маркировочная группа 1372 МПа.
Чтобы канат не перегибался
-диаметр блока крюковой подвески по дну ручья мм;
Условия выполнены следовательно канат выбран правильно.
3. Установка верхних блоков
Минимальные диаметры барабана блоков и уравнительных блоков огибаемых стальными канатами определяются по формулам:
DБ – диаметр барабана мм;
D2 – диаметр блока мм;
D3 – диаметр уравнительного блока по средней линии навитого каната мм;
dk – диаметр каната.
– коэффициент выбора диаметра барабана;
– коэффициент выбора диаметра блока;
– коэффициент выбора диаметра уравнительного блока;
Коэффициенты h1 h2 h3 выбираются в соответствии с режимом работы.
При соблюдении этих условий канат может отклоняться от плоскости симметрии ручья блока на угол не более 6º.
4. Установка барабана
Полученное значение диаметра барабана следует округлять в большую сторону до стандартного значения из нормального ряда диаметров. Но исходя из конструктивных соображения для обеспечения требуемой скорости подъема груза примем
Длина барабана находится по формуле
– длина одного нарезанного участка;
– длина гладкого среднего участка;
– длина одного гладкого концевого участка.
Длина одного нарезанного участка:
– число рабочих витков для навивки половины полной рабочей длины каната;
– число неприкосновенных витков необходимых для разгрузки деталей крепления каната;
– число витков для крепления конца каната;
Число рабочих витков определяется по формуле:
Hп – высота подъема груза м.
Длина гладкого среднего участка барабана может быть определена из соотношения:
Bн – расстояние между осями наружных блоков крюковой подвески;
– минимальное расстояние между осью блоков крюковой подвески и осью барабана;
– допустимый угол отклонения каната.
Среднее значение длины гладкого среднего участка барабана
Длина гладкого концевого участка lк необходимого для закрепления барабана в станке при нарезании канавок может приниматься (4-5)dК:
В итоге длина барабана
Проверка соотношения длины и диаметра барабана:
Данное соотношение можно принять так как оно входит в рекомендованное значение 35 50.
5. Выбор электродвигателя
Группа режимов работы 6М относится к тяжелому режиму нагружения
Для этих групп режимов используются двигатели асинхронные с фазным ротором серии МТН.
Выбор двигателя производится по относительной продолжительности включения (ПВ=40% для тяжелого режима) и по необходимой статической мощности при подъеме груза максимального веса:
Vп – скорость подъема груза мс;
– КПД механизма предварительное значение которого можно принимать 085-09.
Требуемую мощность обеспечит двигатель МТН312-6 имеющий следующие параметры:
номинальная мощность двигателя Nдв = 15 кВт;
частота вращения вала двигателя nдв = 950 обмин
максимальный момент Мmax= 468 Нм
масса двигателя mдв = 230 кг.
Типоразмер редуктора выбирают по расчётному эквивалентному вращающему моменту с учётом режимы работы необходимого передаточного числа и частоты вращения быстроходного вала.
Для обеспечения заданной скорости подъёма груза редуктор должен иметь передаточное число
nДВ – частота вращения вала двигателя (с-1)
Необходимо принять стандартное передаточное число .
Отклонение расчётного значения передаточного числа от принятого составляет
== -32 % что допустимо.
Эквивалентный момент на выходном валу редуктора:
где – коэффициент интенсивности режима нагружения;
– базовое число циклов перемены напряжений; принимаем .
Параметр определяется формулой:
где KI = 3600 – коэффициент для передач с односторонней нагрузкой (механизм подъема);
n – частота вращения тихоходного вала редуктора (барабана) с-1;
nw – число зубчатых колес сцепляющихся с тихоходным колесом редуктора (для мостовых кранов nw = 1);
– норма времени работы редуктора по ГОСТ 25835-83 ч применяется в зависимости от класса использования. Тогда ; время работы – 18750 ч.
Максимальный вращающий момент на тихоходном валу рассчитывается по формуле:
где – максимальное ускорение при пуске;
Gп – вес крюковой подвески;
– КПД полиспаста и барабана соответственно.
Исходя из конструктивных соображений выбираем редуктор Ц2-500 со следующими параметрами:
вращающий момент на тихоходном валу МТ = 54 кНм U = 50 межосевое расстояние aw = 400 мм масса редуктора 317 кг.
7. Выбор соединительных муфт
Муфты выбираем в зависимости от передаваемого вращающего момента и условий работы:
Мр – расчетный вращающий момент;
К – коэффициент запаса прочности;
Мк – действующий вращающий момент;
[Мк] – допускаемый вращающий момент для муфты.
Коэффициент запаса прочности:
К1 – коэффициент учитывающий степень ответственности соединения в предварительных расчетах принимаем К1 = 18;
К2 – коэффициент режима работы принимаем К2 = 1;
К3 – коэффициент углового смещения для МЗП К3 = 125.
Подбираем муфту для быстроходного вала редуктора.
Принимаем МЗП №2 по ГОСТ 5006-55 с основными параметрами: номинальный вращающий момент .
Для тихоходного вала применяем вариант установки барабана с внешней опорой как сборочной единицы.
Расчетный тормозной момент:
где Kт – коэффициент запаса торможения; принимаем при тяжелом режиме работы Kт = 20;
Tст.т. – статический крутящий момент при торможении создаваемый весом номинального груза на валу на котором установлен тормоз.
– КПД всего механизма (равно произведению КПД полиспаста барабана и редуктора);
– передаточное число механизма
Принимаем тормоз ТКГ-200 со следующими характеристиками:
Основные размеры: L = 603 мм; H = 436 мм; E = 213 мм; T = 198 мм; B = 90 мм;
D = 200 мм; h = 170 мм.
Механизм передвижения
1. Выбор кинематической схемы
При выборе кинематической схемы механизма передвижения тележки отдаем предпочтение схеме имеющей боковой привод с тихоходным трансмиссионным валом и применением вертикальных редукторов типа Ц3вк ВК и ВКУ. Ее достоинством является малая трудоемкость работ по выверке и центровке редуктора и не требует устройства специальных опорных площадок под редуктор на раме тележки. Выбранная схема изображена на рис. 1.
рис. 1. Кинематическая схема механизма передвижения тележки
Так как номинальная грузоподъемность менее 80 тонн то число ходовых колес тележки принимаем равным четырем.
Выбор колес производится по максимальной статической нагрузке:
Gг Gт вес номинального груза главного подъема и тележки соответственно
Кн =125 коэффициент неравномерности распределения нагрузки на колеса.
По ОСТ 24.090.4482 выбираем при нагрузке от 30 до 50 кН диаметр ходового колеса Dк = 200 мм.
3. Определение сопротивления движению тележки
Полное сопротивление передвижению тележки в период разгона приведенное к ободу колеса рассчитывается по формуле:
W = Wтр+Wу+Wв+Wин+Wгиб
где Wтр сопротивление создаваемое силами трения:
где коэффициент трения качения колес по рельсу; принимаем = 03;
f коэффициент трения в подшипниках колес; принимаем f = 0015;
dц диаметр цапфы вала колеса принимаем dц = 45 мм;
Kдоп = 25 – коэффициент дополнительных сопротивлений (трения реборд и токосъемного устройства).
Wу сопротивление создаваемое уклоном пути; рассчитывается:
= 0002 уклон рельсового пути.
Wу = 0002(21000+60000)=162 Н.
Wв сопротивление создаваемое ветром; при работе крана в помещении; принимаем Wв = 0.
Wин сопротивление создаваемое инерцией вращающихся и поступательно движущихся масс тележки:
= 125 коэффициент учитывающий инерцию вращающихся масс;
mпост = 2140 кг – масса тележки;
a=(05÷1)[а]=075·022=0165 мс2 - ускорение при разгоне.
Wгиб сопротивление создаваемое раскачиванием груза на гибкой подвеске:
Q грузоподъемность крана;
Wгиб = (6000 +157)0165=1016 Н.
W =744+162+0+441+1016=2363 Н = 24 кН
4. Выбор электродвигателя
Выбор двигателя производится по относительной продолжительности включения и по необходимой мощности:
Vт – скорость тележки;
м – предварительное значение КПД механизма; предварительно принимаем
ср.п. кратность среднепускового момента двигателя по отношению к номинальному для асинхронных двигателей с фазным ротором (MTF и MTH) ср.п.=1516. Принимаем ср.п.=16.
Выбираем крановый электродвигатель серии MTF 011-6 с фазным ротором для ПВ=40 % N=14 кВт n = 885 обмин; массой m=51 кг Мmax=4 Нм.
Выбор типоразмера редуктора осуществляем по расчетному эквивалентному вращающему моменту на валу с учетом режима работы и необходимого передаточного числа.
Требуемое передаточное число передачи:
nдв – частота вращения вала двигателя обмин;
Dк – диаметр ходового колеса м;
Vт – скорость тележки ммин.
Максимальный вращающий момент на выходном валу редуктора:
где KI = 1800 – коэффициент для механизма передвижения тележки;
– норма времени работы редуктора по ГОСТ 25835-83 ч применяется в зависимости от класса использования.
Класс использования – A5 тогда ; время работы – 18750 ч. Нм.
По всем рассчитанным параметрам выбираем цилиндрический трехступенчатый редуктор типа ЦЗвк100 с параметрами:
вращающий момент на тихоходном валу МТ = 163 кНм U = 125 масса редуктора m = 45 кг.
Согласно правилам ГГТН РФ в данном механизме передвижения должен быть установлен тормоз т.к. тележка предназначенная для работы в помещении на надземном рельсовом пути перемещается со скоростью больше 053 мс (Vт = 075 мс).
Расчетный тормозной момент механизма при работе крана в закрытом помещении определяется для движения без груза под уклон в предположении что реборды колес не задевают заголовки рельсов:
Ту момент создаваемый уклоном пути:
Wу = Gт сопротивление передвижению тележки создаваемое уклоном ( уклон рельсового пути);
Wу = 0002·21000 = 42 Н;
Тин момент создаваемый инерцией:
где Wин=mта – сопротивление передвижению тележки создаваемое инерцией ( коэффициент учитывающий инерцию вращающихся масс механизма при скорости менее 1 мс =125).
Wин = 125·2363·0165 =487 Нм;
Ттр момент создаваемый трением:
сопротивление передвижению тележки создаваемое трением где
Kтрол – коэффициент учитывающий сопротивление движению тележки от троллейного токопровода (принимаем Kтрол = 125).
Т = 03+34-088=28 Н·м.
Принимаем тормоз ТКТ-100 со следующими параметрами:
Диаметр тормозного шкива – 100 мм; наибольший тормозной момент Тma масса тормоза – 125 кг. Так как ТТ≤Тmax причем номинальный тормозной момент много больше расчетного (10%) то тормоз нужно отрегулировать на значение Тmax=078 Нм.
Компонование тележки
Расположение механизмов на раме тележки (см. Приложение 1) должно обеспечить ее минимальные габариты и массу равномерную нагрузку на ходовые колеса при номинальном грузе на крюке.
Центр барабана подъема принимается за начало координат из которого проводятся главные координатные оси: хх – по оси барабана и уу – перпендикулярно оси барабана.
Симметрично относительно оси уу располагаются продольные оси подтележечных рельсов с таким расчетом чтобы продольная ось редуктора совпадала (или была близка) с одной из осей колеи тележки.
В соответствии с размерами узла ходовых колес (расстоянием между корпусами подшипников) пунктиром прочерчиваем вертикальные листы продольных балок рамы тележки. Нагрузка от веса груза через опоры барабана должна передаваться на эти балки т.е. на них должны опираться корпуса подшипников барабана.
Следует наметить место установки барабана и верхних блоков.
Привод механизма передвижения тележки располагается с учетом возможности крепления редуктора и пропуска трансмиссионного вала при уже намеченных элементах рамы тележки. Задается положение ходовых колес.
Ориентировочно контур рамы следует наметить с учетом возможности прохода обслуживающего персонала при ремонтах и регулировках оборудования.
Центр массы рамы тележки (точка Ор) который с достаточной степенью точности можно считать расположенным в геометрическом центре рамы. Вес рамы определяется разностью между ранее принятым весом тележки и суммой весов установленных на ней механизмов.
На виде тележки сверху координируются центры масс всего оборудования находящегося на раме причем вес двигателей барабана и вертикального редуктора прикладывают в геометрическом центре соответствующих изделий. Вес горизонтального редуктора прикладывают на расстояние одной трети их длины со стороны тихоходного вала. Вес тормозов промежуточных валов и муфт невелик по сравнению с весом рамы тележки и перечисленного оборудования. Поэтому при определении вертикальных усилий действующих на ходовые колеса их веса могут не учитываться.
Определение весов и координат центров тяжестей.
Значения масс весов и координат центров тяжестей сведены в таблицу 1.
Координаты центра тяжести порожней тележки:
Xi Yi координаты точек их приложения.
Чтобы определить координату Y центра тяжести груза находящегося на крюке подвески необходимо рассмотреть равновесие крюковой подвески в плоскости базы тележки (рис. 1).
Необходимо расположить подвеску между барабаном и верхним блоком на наибольшей высоте. В этом положении ось подвески находится от оси барабана на расстоянии:
где высота расположения оси вала барабана мм;
высота рамы тележки мм;
расстояние от подвески в ее верхнем положении до металлоконструкции тележки (регламентируется «Правилами» ГГТН) мм;
расстояние от оси до крайней верхней точки подвески мм.
По правилам сложения векторов находится равнодействующая сила в канатах идущих на верхние блоки и равнодействующая сила в канатах идущих к барабану. При сложении этих сил получается равнодействующая сила действующая на крюковую подвеску S.
Положение неприводных колес т.е. база тележки определяется из условия одинаковой нагрузки на приводные и неприводные колеса:
Y’ расстояние от равнодействующей веса порожней тележки до оси приводных колес мм;
Y’’ расстояние от равнодействующей веса груза до оси приводных колес.
Определяем нагрузку на ходовые колеса тележки в порожнем состоянии и от веса груза. При этом с целью упрощения расчетов делают ряд допущений – считают что все опоры тележки лежат в одной плоскости а рама представляет собой абсолютно жесткую конструкцию.
Перенеся силу тяжести порожней тележки в точку Oр и уравновесив ее получают силу в точке симметрии рамы и момент. Раскладывая последний по продольной и поперечной плоскостям определяют нагрузки на ходовые колеса от веса порожней тележки:
Нагрузки от веса груза:
– вес порожней тележки Н;
G – вес номинального груза Н;
Gп – вес подвески Н.
Статическая нагрузка на ходовые колеса в груженом положении:
Максимальная разница в нагрузках на колеса:
что является приемлемым.
Результаты расчетов сведены в таблицу 1 (Приложение 1).
II. Проверочные расчеты механизмов подъема и передвижения
Проверка двигателя механизма подъема на время разгона
Двигатель должен разгонять механизм за достаточно короткое время иначе уменьшится производительность крана. Но с другой стороны если оно будет слишком мало то разгон будет сопровождаться большим ускорением что скажется на прочности элементов устойчивости груза.
Время разгона механизма принимается равным до 2 секунд - для механизмов подъема кранов
грузоподъемностью 6 т (в соответствии с рис.2 линия 1).
Для механизма подъема груза наибольшее время разгона получается при разгоне на подъем вычисляемое по формуле:
угловая скорость двигателя радс;
JМЕХ.Р приведенный к валу двигателя момент инерции при разгоне всех движущихся частей механизма включая поступательно движущиеся массы кг·м2;
TП..СР среднепусковой момент двигателя Н·м;
TСТ.Р момент статических сопротивлений при разгоне приведенный к валу двигателя Н·м.
Среднепусковой момент двигателя определяется по формуле:
номинальный момент двигателя Н·м;
кратность среднепускового момента двигателя (для двигателей с фазным ротором =16).
– номинальная мощность двигателя при ПВ=40% Вт;
– частота вращения вала двигателя обмин;
Приведенный момент инерции определяется по формуле:
момент инерции при разгоне всех вращающихся частей механизма приведенный к валу двигателя:
- коэффициент учета инерции вращающихся масс расположенных на втором третьем и последующих валах механизма;
J1 момент инерции вращающихся масс расположенных на первом валу равный сумме моментов инерции ротора двигателя JР.ДВ муфты JМ и тормозного шкива JТ.Ш;
JПОСТ.Р – момент инерции при разгоне поступательно движущихся частей механизма плюс груза приведенный к валу двигателя.
mТ.Ш .- масса тормозного шкива;
r Т.Ш. - радиус тормозного шкива;
Т.Ш. - коэффициент учитывающий распределенность массы шкива (коэффициент приведения геометрического радиуса вращения к радиусу инерции). Принимаем
J1 = JР.ДВ + JМ + JМ.Т.Ш = 028+006+115+02=161 кг·м2;
JВР = 12·161=193 кг·м2;
JПОСТ.Р определяется по формуле:
rБ – радиус барабана по оси навиваемого каната м;
uМЕХ – полное передаточное число механизма равное произведению передаточных чисел полиспаста и лебедки;
mП - масса подвески кг;
mГР - масса груза кг;
Момент статических сопротивлений при разгоне приведенный к валу двигателя Tст.р определяется по формуле:
Полученное значение не больше рекомендуемых значений времени разгона; следовательно принятый электродвигатель обеспечит необходимую интенсивность работы.
Среднее ускорение груза при таком времени разгона равно:
Это значение не превышает рекомендуемое мс2 для крана грузоподъёмностью Q=6т.
Проверка двигателя механизма передвижения на время разгона
Наибольшее время торможения наблюдается когда кран нагружен а уклон пути и ветер препятствуют движению. Время торможения не должно превышать 5÷6 с для тележек.
Для механизма передвижения тележки наибольшее время разгона вычисляем по формуле:
JМЕХ.Р приведенный к валу двигателя момент инерции при торможении всех движущихся частей механизма включая поступательно движущиеся массы кг·м2;
TСТ.Т момент статических сопротивлений при торможении приведенный к валу двигателя Н·м.
J1 момент инерции вращающихся масс расположенных на первом валу равный сумме моментов инерции ротора двигателя JР.ДВ муфты JМ и тормозного шкива с муфтой JТ.Ш.М;
JПОСТ.Р – момент инерции при торможении поступательно движущихся частей механизма плюс груза приведенный к валу двигателя.
J1 = JР.ДВ + JМ + JМ.Т.Ш = 015+0021+021=0381 кг·м2;
JВР = 12·0381=0457 кг·м2;
JПОСТ.Т определяется по формуле:
mТ - масса тележки кг;
Момент статических сопротивлений при торможении приведенный к валу двигателя Tст.р определяется по формуле:
Полученное значение не больше рекомендуемых значений времени торможения следовательно принятый электродвигатель обеспечит необходимую интенсивность работы.
Среднее ускорение тележки при таком времени разгона равно:
Проверка механизма передвижения тележки на отсутствие буксования без учета жесткости механизма
В период пуска механизма передвижения приводные колеса взаимодействуя с рельсами приводят в движение тележку. Для получения нормальной работы при разгоне и торможении необходимо чтобы приводные колеса перекатывались по рельсам без скольжения (пробуксовки). Поэтому при расчете механизмов передвижения нужно выдержать определенное соотношение между силами сцепления ходовых колес с рельсами и движущей силой приложенной к ободьям этих колес. Расчетным случаем является работа без груза когда усилие на приводные колеса будет уменьшенным а следовательно уменьшена будет и сила сцепления колес с рельсами. Работа в период пуска без проскальзывания приводных ходовых колес обеспечивается при соблюдении неравенства:
- коэффициент запаса сцепления;
- сила сцепления колес с рельсами
- вес тележки приходящийся на приводные колеса здесь:
nПР nВСЕХ – число приводных колес и общее число колес соответственно.
-коэффициент трения в подшипниках качения (для шарикоподшипников);
dП = 45 мм-диаметр вала колеса в месте посадки подшипника;
-коэффициент трения качения стального колеса по рельсу с плоской головкой;
- коэффициент учитывающий сопротивление трения реборд колеса в зависимости от назначения механизма типа привода формы обода колеса и типа токопровода;
- сопротивление движению тележки создаваемое силой ветра.
- сопротивление от сил инерции массы тележки.
Выражая параметры формулы для WСЦ и используя вышеназванные параметры получим:
- допустимое ускорение тележки.
Тогда условием отсутствия буксования колес тележки можно считать выражение:
где - фактическое ускорение движения тележки которое определяется зависимостью:
где VТФ - фактическая скорость движения тележки;
tР – время разгона механизма.
Условие отсутствия буксования выполняется следовательно при разгоне тележки проскальзывание колес относительно рельсов будет отсутствовать.
Для проверки условия отсутствия юза (проскальзывания колес тележки по рельсам во время торможения) являются выражение аналогичные вышеприведенным но с изменением знаков поэтому:
Условие отсутствия юза выполняется следовательно при торможении тележки проскальзывание колес относительно рельсов будет отсутствовать.
III. Расчет сборочной единицы «Установка барабана»
Определение толщины стенки барабана
В качестве материала барабана примем сталь 35Л с []сж=137 МПа.
Приближенное значение толщины стенки находится по формуле:
t – расстояние между соседними витками каната м;
[]сж – допускаемое напряжение МПа.
Исходя из условий технологии изготовления для стального барабана:
Dб0 – диаметр барабана по дну канавок м;
Значение коэффициента учитывающего влияние деформаций стенки барабана и каната:
Eк – модуль упругости каната для шестипрядного каната с органическим сердечником Eк = 88260 МПа;
Fк =8628·10-6– площадь сечения всех проволок каната м2;
Eб – модуль упругости стенки барабана для литых стальных барабанов Eб = 186300 МПа;
Окончательно толщину цилиндрической стенки барабана определяем зависимостью:
Так как отношении длины барабана к его диаметру то допускаемые напряжения []сж в этой формуле следует уменьшить на C%. При навивке на барабан двух концов каната для = 01; 02; 03 можно
принять C = 5; 10; 15% соответственно где dк – диаметр каната.
. С учётом линейной интерполяции С = 845%.
С учетом уточнений толщина цилиндрической стенки будет равна:
Принимаем толщину стенки барабана м.
Крепление каната к барабану
К конструкции крепления каната на барабане предъявляют требования большой надёжности доступности для осмотра удобства смены каната. Наибольшее применение находит крепление каната планками прижимающими канат к барабану. При этом канат из крайней канавки барабана переводят сразу в третью для чего частично вырубают выступы нарезки которые разделяют канавки среднюю же канавку используют для установки крепежных болтов или шпилек.
Суммарное усилие растяжения болтов прижимающих канат:
f = 011 – коэффициент трения между канатом и барабаном;
γ – угол наклона боковой грани трапециевидного выреза в планке к вертикали;
α – угол обхвата барабана неприкосновенными витками;
e – основание натурального логарифма;
При диаметре каната до 155 мм используются болты М16.
Необходимое число болтов:
k = 15 – коэффициент запаса надежности крепления каната к барабану;
– приведенный коэффициент трения между канатом и поверхностью планки;
=0026 – расстояние от дна канавки на барабане до верхней плоскости прижимной планки м;
– допускаемые напряжения растяжения в болте;
тек = 2452 МПа – предел текучести для стали 20.
Для крепления каната к барабану требуется 4 болта.
Ось барабана испытывает напряжение изгиба от действия усилий двух ветвей каната при сдвоенном полиспасте а также от собственного веса барабана которым пренебрегаем.
Нагрузки на ступицы барабана:
предварительно можно принять l1 = 80 мм l2 = 150 мм.
Рис.3. Расчётная схема оси
Расчет оси барабана сводится к определению диаметра цапфы вала из условия работы оси на изгиб в симметричном цикле:
Mи – изгибающий момент в расчетном сечении;
W – момент сопротивления расчетного сечения при изгибе;
[-1] – допускаемое напряжение при симметричном цикле.
Допускаемое напряжение при симметричном цикле:
k0 – коэффициент учитывающий конструкцию детали (для валов осей и цапф k0 = 24);
-1 =257 – предел выносливости материала оси Сталь 45 МПа;
[n] – допускаемый коэффициент запаса прочности (для группы режима работы 5М – 17);
После определения реакций опор оси R1 и R2 можно определить изгибающие моменты в любом ее сечении. Наибольший изгибающий момент под правой ступицей M2 = R2 ·I2 а момент сопротивления этого сечения оси . Находим предварительно диаметр оси под правой ступицей:
Диаметр под правой ступицей d = 80 мм. Значит диаметр цапф вала в месте посадки подшипников с учетом ступенчатости для буртиков dЦ = 60 мм.
Проверка подшипников на долговечность
Подшипник роликовый радиальный сферический двухрядный 3512 ГОСТ 5721-75 со следующими параметрами:
d = 60 мм - диаметр вала в месте посадки подшипника;
D = 110 мм - наружный диаметр;
B = 28 мм - высота подшипника;
C = 122 кН - динамическая грузоподъёмность;
C0= 83 кН - статическая грузоподъёмность.
Расчёт подшипника следует производить для наиболее нагруженной левой опоры 1.
Реакция в опоре найдена ранее при расчёте оси барабана:
Эквивалентная динамическая нагрузка:
КТ – температурный коэффициент. При рабочей температуре подшипника t1050C КТ=1;- коэффициент безопасности в крановых механизмах =13÷15.
При вращении внутреннего кольца подшипника V=1.
Долговечность подшипника при максимальной нагрузке:
nБ = 5625 – частота вращения барабана обмин.
m = 103 – показатель степени кривой усталости для роликоподшипников.
Эквивалентная долговечность подшипника:
- коэффициент эквивалентности для режима тяжелого нагружения для роликоподшипников (рис. 4.)
Так как ч следовательно выбранный подшипник удовлетворяет заданным условиям работы и его долговечность обеспечена.
Расчёт болтов соединяющих зубчатый венец с барабаном
Соединение осуществляется болтами ГОСТ 7817-80 которые испытывают рабочие напряжения среза а также напряжения растяжения и кручения возникающие при сборке узла. Размеры венца-ступицы барабана определяются размерами зубчатого венца тихоходного вала выбранного редуктора
Материал болтов – сталь 45 (предел текучести т = 353 МПа).
Диаметр болта определяется по формуле:
m’б = 075·mб – расчетное число болтов;
mб – число установленных болтов (примем 8);
[] – допускаемое напряжение среза:
т=353МПа – предел текучести материала болтов;
k1 =13 – коэффициент безопасности соответствующий механизму подъема кранов работающих с крюком;
k2 = 12 – коэффициент нагрузки соответствующий группе режима работы 5М;
PОКР – усилие действующее на окружности установки болтов:
DБ – диаметр барабана по центру навитых канатов м;
DОКР-диаметр окружности установки болтов м;
где DЗ – наружный диаметр зубчатого венца вала редуктора м.
Принимаем диаметр болта d = 8 мм.
Курсовое проектирование грузоподъемных машин: Учеб. пособие для студентов машиностр. спец. вузовС.А. Казак В.Е. Дусье Е.С. Кузнецов и др.; Под ред. С.А. Казака. – М.: Высш. шк. 1989. – 319 с.: ил.
Подъемно-транспортные машины. Атлас конструкций. Учебное пособие для вузов. Под ред. д-ра техн. наук М.П. Александрова и д-ра техн. наук Д.Н. Решетова. М. «Машиностроение» 1973 256 с.
Грузоподъемные машины: Учебно-методическое пособие Ю.В. Наварский. Екатеринбург: ГОУ ВПО УГТУ-УПИ 2003. 100 с.
Шабашов А.П. Лысяков А.Г. Мостовые краны общего назначения. – 5-е изд. перераб. и доп. – М.: Машиностроение 1980. 304 с. ил.
Справочник по кранам: В 2 т. Т.1. Характеристики материалов и нагрузок. Основы расчета кранов их приводов и металлических конструкцийВ.И. Брауде М.М. Гохберг И.Е. Звягин и др.; Под общ. ред. М.М. Гохберга. – Л.: Машиностроение. Ленингр. отд-ние 1988. – 536 с.: ил.
Спецификация Мех.передвижения Силин Д.А,.dwg

Шайба 12 65Г ГОСТ 6402-70
КП 23.05.01.0202.322.2020.02
Болт М14х35.36 ГОСТ 7798-70
Болт М12x35.58 ГОСТ 7798-70
Болт М16х54.36 ГОСТ 7798-70
Гайка М14.5 ГОСТ 5915-70
Гайка М16.5 ГОСТ 5915-70
Шайба 12.65Г ГОСТ 6402-70
Шайба 14.65Г ГОСТ 6402-70
Шайба 16.65Г ГОСТ 6402-70
КП 23.05.01.0202.322.2020.02 СБ
КП 23.05.01.0202.322.2020.01
Спецификация Мех.подъема Силин Д.А..dwg

Болт М14х54.36 ГОСТ 7798-70
Болт М18х64.36 ГОСТ 7798-70
Болт М24х64.36 ГОСТ 7798-70
Болт М33х78.36 ГОСТ 7798-70
Гайка М14.5 ГОСТ 5915-70
Гайка М18.5 ГОСТ 5915-70
Гайка М24.5 ГОСТ 5915-70
Гайка М33.5 ГОСТ 5915-70
Шайба 14.65Г ГОСТ 6402-70
Шайба 18.65Г ГОСТ 6402-70
Шайба 24.65Г ГОСТ 6402-70
Шайба 33.65Г ГОСТ 6402-70
КП 23.05.01.0202.322.2020.01
КП 23.05.01.0202.322.2020.01 СБ
КП 23.05.01.0202.322.2020.02
КП 23.05.01.0202.322.2020.03
Спецификация ОВ Силин Д.А,.dwg

КП 23.05.01.0202.322.2020.01
Расчетно-пояснительная
Болт М10x25.58 ГОСТ 7798-70
Болт М12x35.58 ГОСТ 7798-70
Гайка М10.5 ГОСТ 5915-70
Шайба 10 65Г ГОСТ 6402-70
Канат ЛК-Р 6х19(1+6+66)+1о.с.
Шайба 12 65Г ГОСТ 6402-70
ГОСТ 2688-80 1372 МПа
-8-500 ОСТ 24.191.08-81
КП 23.05.01.0202.322.2020.00
КП 23.05.01.0202.322.2020.00 СБ
КП 23.05.01.0202.322.2020.02
КП 23.05.01.0202.322.2020.03
КП 23.05.01.0202.322.2020.04
КП 23.05.01.0202.322.2020.05
КП 23.05.01.0202.322.2020.06
КП 23.05.01.0202.322.2020.07
КП 23.05.01.0202.322.2020.08
КП 23.05.01.0202.322.2020.09
КП 23.05.01.0202.322.2020.10
КП 23.05.01.0202.322.2020.11