Проектирование основных узлов тележки мостового крана. Вариант 5.2




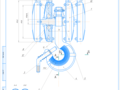
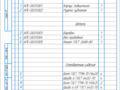
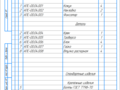
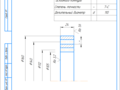
- Добавлен: 25.01.2023
- Размер: 4 MB
- Закачек: 0
Описание
Проектирование основных узлов тележки мостового крана. Вариант 5.2
Состав проекта
![]() |
![]() |
![]() |
![]() ![]() ![]() ![]() |
![]() ![]() ![]() |
![]() |
![]() ![]() ![]() ![]() |
![]() ![]() ![]() ![]() |
![]() ![]() ![]() ![]() |
![]() ![]() ![]() ![]() |
![]() |
![]() ![]() ![]() ![]() |
![]() ![]() ![]() ![]() |
![]() ![]() |
![]() |
![]() ![]() ![]() ![]() |
![]() ![]() ![]() ![]() |
![]() |
Дополнительная информация
Тележка мостового крана.cdw

Продолжительность включения ПВ = 40%
Грузоподёмность механизма
передвижения тележки 25
КП-ПТУ-02068108-260601-АПБ-00.00.000СБ-2010
Механизм передвижения
ПЗ1.docx
Применение блочных конструкций позволяет выпускать сборочные единицы механизмов «на склад» т.е. в законченном виде что приводит к специализации отдельных цехов и заводов. Специализация производства в свою очередь обеспечивает повышения качества изготовляемых сборочных единиц.
При разработке конструкций кранов следует обеспечить независимость движения механизмов крана и возможность совмещения рабочих движений в любых сочетаниях хотя допускается не совмещать работу главного и вспомогательного подъема. Взаимное расположение механизмов и их вспомогательных элементов должно обеспечить удобство монтажа обслуживания и регулировки с возможно меньшей разборкой элементов. Особое внимание надо обращать на удобство подхода к тормозам местам креплений канатов подшипникам муфтам зубчатым передачам устройствам безопасности.
Необходимо помнить что унификация элементов конструкции уменьшает количество необходимого оборудования инструмента литейных форм позволяет применять специальные приспособления повышающие производительность труда и качество изделия уменьшает необходимый парк запасных частей.
Необходимо спроектировать основные узлы тележки мостового крана изучить существующие аналоги конструкции машины и методы расчета (по атласам технической и патентной литературе) выбрать установку наиболее близкую к проектируемой. С помощью консультанта проанализировать конструкцию прототипа отметив ее достоинства и недостатки наметить пути устранения. Рассмотрение аналогов и прототипа конструкций следует сопроводить эскизами и необходимыми пояснениями.
Необходимо спроектировать основные узлы тележки мостового крана.
Схема тележки мостового крана:
-механизм подъёма груза; 2-механизм передвижения; 3-рама;
Грузоподъемность G =50 кН;
Скорость подъема груза VG = 20 ммин;
Скорость перемещения тележки V =25 ммин;
Высота подъема груза Н =5 м;
Схема полиспаста –Б.
1. Литературный обзор
Грузоподъемные машины и механизмы предназначены для перемещения грузов и людей по вертикали и передачи их из одной точки площади обслуживаемой машиной в другую. Конструкции этих машин чрезвычайно разнообразны. Их можно классифицировать по конструктивным признакам назначению характеру выполняемой ими работы.
Для подъема груза на небольшую высоту (до 1 м) служат простейшие грузоподъемные механизмы: домкраты обычно применяемые при ремонтных и монтажных работах. Привод домкратов может быть ручным и механическим. Различают винтовые рычажно-реечные зубчато-реечные и гидравлические домкраты.
К простейшим грузоподъемным механизмам относятся также и лебедки предназначенные для подъема опускания перемещения грузов по горизонтальному или наклонному пути при производстве различных погрузочно-разгрузочных ремонтных и строительно-монтажных работ так и в качестве силового оборудования для комплектации различных подъемных устройств (кранов подъемников и др.). В зависимости от исполнения лебедки можно подразделить: по типу привода-на лебедки с ручным и машинным приводом; по типу тягового элемента - на канатные и цепные; по типу установки-на неподвижные (закрепленные на полу стене потолке) и передвижные (на тележках передвигающихся по полу или по подвесным путям); по числу барабанов - на одно- двух- и многобарабанные лебедки; по типу барабана - на нарезные гладкие и фрикционные.
На рис.1 изображена лебедка с приводом от фланцевого электродвигателя 4:укрепленного на корпусе редуктора 3. Быстроходный вал редуктора соединен с валом двигателя с помощьющью зубчатой муфты расположенной внутри корпуса редуктора. На свободном конце вала двигателя установлен шкив колодочного тормоза приводимого в действие электрогидравлическим толкателем. На выходном валу редуктора установлен барабан 5 с закрепленным на нем концом каната. При включении двигателя приводится во вращение барабан 5 лебедки; при этом канат к которому прикрепляется груз наматывается на барабан или сматывается с него производя подъем или спуск груза. Направление вращения барабана изменяют путей реверсирования электродвигателя. На втором конце быстроходного вала редуктора установлен электроиндукционный (вихревой) тормоз 2 например типа ТМ-4 предназначенный для плавного регулирования скорости опускания груза. Такие лебедки широко используют при монтажных ремонтных и строительных работах.
В пассажирских подъемниках применяют лебедки с канатоведущим шкивом в ручьи которого входят ветви грузового каната и передача тяговой силы осуществляется посредством силы трения возникающей между канатом и поверхностью ручья.
Рис. 1. Лебёдка барабанная с электроприводом.
При малой грузоподъемности и скорости подъема груза применяют лебедки с ручным приводом в которых барабан вращается с помощью приводных рукояток с тормозом автоматически останавливающим барабан при прекращении вращения рукоятки.
Для внутрицехового и межцехового транспортирования грузов обслуживания поточных и автоматических линий станков и других механизмов применяют
компактные подъемные лебедки - тали имеющие ручной электрический или пневматический приводы. Тали устанавливают стационарно или на передвигающихся тележках.
Рис. 2. Таль с ручным приводом с соосной зубчатой передачей.
На рис. 2 показана таль с ручным приводом. Ее подвешивают к опоре за крюк 3. Привод тали осуществляют с помощью бесконечной цепи 7 находящейся в зацеплении с приводным колесом 4. Грузовым элементом в таких талях служит пластинчатая цепь 1 или сварная калиброванная цепь. Поднятый груз удерживают в неподвижном состоянии дисковым тормозом 5 который замыкается весом транспортируемого груза. В этом случае ступицу цепного колеса 4 выполняют в виде гайки зажимающей храповое колесо 6 тормоза. Собачку 2 тормоза укрепляют на корпусе тали.
Для перемещения груза по горизонтали тали подвешивают к тележкам перемещающимся по подвесным однорельсовым путям выполненным из проката двутаврового сечения. Тележки выполняют без привода (при грузоподъемности до 1 т их передвигают толкая подвешенный груз) а также с ручным механическим приводом. Грузоподъемность электроталей составляет от 025 до 15 т скорость подъема от 5 до 25 ммин. Скорость горизонтального передвижения талей устанавливают в зависимости от длины пути и назначения тали.
На рис. 3 представлен общий вид электротали ТЭ грузоподъемностью до 5 т обеспечивающей подъем груза на высоту от 3 до 18 м со скоростью 8 ммин; скорость передвижения (при управлении с пола) равна 20 ммин.
Рис. 3. Электроталь ТЭ.
Грузоподъемные машины предназначенные для выполнения работ требующих точности и осторожности при посадке грузов должны иметь соответствующие малые скорости механизмов подъема и передвижения. В этом случае электротали оборудуют так называемым микроприводом обеспечивающим при наличии нормальной скорости подъема и опускания также возможность работы с весьма малыми скоростями необходимыми для точной установки деталей на станках или приспособлениях для сборочных и монтажных работ. Изменение скорости подъема и опускания обеспечивается путем применения многополюсного двигателя или вспомогательного двигателя малой мощности приводящего в движение барабан через дополнительные передачи а также с помощью механического устройства - включением дополнительной передачи через фрикционную муфту.
Новая конструкция электротали ВНИИПТМАШ ТЭ-500 грузоподъемностью 5 т изображена на рис. 11 а. Барабан 2 расположен между фланцевым одно- или двухскоростным электродвигателем 1 серии 4А с пристроенным конусным тормозом и планетарным редуктором 3. Основная скорость подъема груза равна 12 ммин.
Для получения малой скорости подъема (12 ммин при двухскоростном двигателе или 75 ммин при односкоростном двигателе) электроталь снабжена дополнительным электродвигателем 4 с редуктором устанавливаемым на торце основного редуктора 4. При работе на малой скорости редуктор малой скорости работает как двухступенчатый с передачей вращения на редуктор основного подъема. При работе на основной скорости подъема включаются одновременно оба двигателя. В двухско-ростных талях между редуктором основного подъема и редуктором малой скорости устанавливается грузоупорный тормоз включаемый в работу только при спуске груза на малой скорости.
Таль выпускается для высот подъема от 63 до 32 м что осуществляется за счет изменения длины барабана и размеров корпуса тали. С целью повышения безопасности работы таль снабжена ограничителем грузоподъемности пружинно-рычажного типа с установкой уравнительного блока на эксцентриковой втулке.
Однорельсовые тележки с талями находят широкое применение для передачи грузов между цехами для подачи грузов на склад или со склада в цех для загрузки вагранок подачи земли т.п. В качестве грузозахватного приспособления электротали могут иметь крюк подъемный электромагнит или специальный захват для штучных или сыпучих грузов. Для снижения размеров зубчатых передач талей применяют высококачественные легированные стали (хромоникелевые хромистые и др.) а шестерни выполняют с малым числом зубьев профиль которого должен быть корригированным.
При скорости передвижения превышающей 32 ммин механизм передвижения тележки имеет стопорный тормоз. При меньших скоростях механизм передвижения работает без тормоза.
Все большее применение в промышленности получают тали с пневмоприводом. Имеются тали в корпусе которых представляющем собой полый цилиндр размещен полиспаст использующий в качестве тягового органа стальной канат. К одному концу каната подвешивают груз; второй конец закреплен неподвижно в корпусе тали. При подаче сжатого воздуха в цилиндр подвижные и неподвижные блоки расходятся в результате чего происходит подъем груза. При выпускании воздуха блоки сближаются под действием веса груза и груз опускается. В других типах талей с пневмоприводном применяется воздушный двигатель со звездообразно расположенными цилиндрами. Тали с пневмоприводном позволяют проводить плавное (бесступенчатое) регулирование скорости подъема и опускание груза в весьма широких пределах. Они незаменимы и при работе во взрывоопасной среде.
Рис. 4. Стрелки подвесных путей:
а и б-вращающиеся; в-рамная.
Однорельсовые пути по которым перемещаются тележки с талями иногда бывают весьма протяженными и разветвленными и могут обслуживать практически всю заводскую или складскую площадь. В этом случае они имеют специальные стрелки переводящие тележки с электроталями с одного пути на другой (рис. 4). На рис. 4 а показано устройство вращающейся стрелки позволяющей обеспечить любое направление движения тележки в месте стыка четырех путей расположенных под прямым углом один к другому (рис. 4 б). На рис. 4 в показана тройная рамная стрелка обеспечивающая при поперечном перемещении рамки 2 движение тележки с пути 1 на любое в трех направлений 3 4 5.
Наиболее широко в промышленности используют мостовые электрические краны (рис. 5) состоящие из моста 11 перемещающегося на ходовых колесах 3 установленные в концевых балках 4 моста крана по подкрановым путям 2. Эти пути уложены на подкрановых продольных балках закрепленных на консольных выступах колонн цеха. По верхнему (а в некоторых конструкциях – по нижнему) поясу балок моста поперек пролета цеха передвигается крановая тележка 8 с подъемным механизмом 7 с грузозахватным элементом. В зависимости от назначения крана на тележке можно размещать различные типы механизмов подъема или два механизма подъема один из которых является главным 7 а второй (меньшей грузоподъёмности) - вспомогательным 6. Механизм 13 передвижения крана установлен на мосту крана механизм 12 передвижения тележки - непосредственно на тележке. Управление всеми механизмами совершается из кабины 1 прикрепленной к мосту крана.
Расстояние по горизонтали между осями крановых рельсов называют пролетом а расстояние между осями передних и задних колес или балансирных тележек - базой крана.
Питание электродвигателей осуществляется от цеховых троллеев обычно изготовляемых из стали уголкового профиля и прикрепляемых к стене здания. Для подачи напряжения на кран применяют токосъемники скользящего типа прикрепляемые к металлоконструкции крана; их башмаки скользя троллеям при перемещении моста крана.
Рис.5. Мостовой электрический кран.
Для осуществления токоподвода к двигателям расположенным на тележке обычно используют троллеи из круглой или угловой стали. Для их установки требуются специальные стойки на площадке идущей вдоль главной балки. Поэтому в последних конструкциях мостовых кранов токоподвод к тележке осуществляется с помощью гибкого кабеля 5. В этом случае между двумя стойками установленными около концевых балок натягивается проволока 9 к которой на специальных подвесках подвешен гибкий кабель. Применение гибкого токопровода позволяет упростить конструкцию повысить надежность эксплуатации и снизить массу крана.
2. Описание прототипа.
Детальное расположение механизмов на тележке мостового крана грузоподъемностью 5 и 20 т показано на рис. 6.На раме 11 тележки размещены механизмы главного и вспомогательного подъемов и механизм передвижения. Расстояние между продольными осями подтележечных рельсов называют колеей тележки а расстояние между осями ходовых колёс тележки - базой тележки. Механизм главного подъема состоит из электродвигателя 9 соединенного длинным валом-вста редуктором 19. Полумуфта соединяющая вал-вставку с редуктора и расположенная на входном валу редуктора 19 служит тормозным шкивом колодочного тормоза 1 с приводом от электрогидравлического толкателя. Выходной вал редуктора 19 соединен зубчатой муфтой с барабаном 10. Опоры верхних блоков 3 полиспаста и уравнительные блоки 2 расположены на верхней поверхности рамы что облегчает их обслуживание и увеличивает возможную высоту подъема. Ограничителем высоты подъема служит шпиндельный выключатель 12 отключающий питание при достижении крюковой подвеской крайнего или нижнего положения. Вспомогательный механизм подъёма имеет аналогичную кинематическую схему (15-двигатель 18-редуктор 17- барабан 13-конечный выключатель);
Рис.6. Тележка мостового крана с главным и вспомогательным подъемом.
Оба механизма подъема оборудованы крюковыми обоймами 20 (для главного подъема) и 16 (для вспомогательного подъема). Механизм передвижения тележки состоит из двигателя 4 тормоза 5 вертикального зубчатого редуктора 6 двух ведущих 7 и двух холостых ходовых колес 14. На раме тележки укреплена линейка 8 конечного выключателя ограничивающего путь передвижения тележки.
Мостовой' кран с подвижной тележкой обслуживает практически всю площадь цеха за исключением узкой полосы вдоль стен цеха на которую кран не может подать грузозахватное приспособление. Если необходимо обслуживать всю площадь цеха и передавать грузы в соседний пролет применяют мостовые краны тележки которых имеют поворотные стрелы позволяющие объединить транспортные операции в пределах нескольких пролетов (рис. 7).
Рис.7. Применение мостовых кранов с поворотной стрелой.
Как уже указывалось мостовые краны в зависимости от назначения могут иметь различные грузозахватные приспособления: крюки подъемные электромагниты грейферы специальные захваты и др.
Предохранительное устройство для грузового крюка.
А С №415220Предохранительное устройство; опубликование описания 15.11.1974. Автор изобретения: В.Г. Кузнецов.
Известны предохранительные устройства для грузового крюка предотвращающие выпадение например стропа из зева крюка и содержащие запорные элементы.
С целью упрощения конструкции в предлагаемом предохранительном устройстве запорный элемент выполнен в виде съемного подпружиненного стержня с ручкой и фиксатором вставляемого в отверстие с продольным пазом для фиксатора выполненное в носке рога крюка.
На рис. 12 изображено описываемое устройство.
Предохранительное устройство для грузового крюка содержит запорный элемент выполненный в виде съемного стержня 1 с ручкой и фиксатором 2 вставляемого в отверстие с продольным пазом 3 для фиксатора. Отверстие выполнено в носке рога крюка на внутренней поверхности которого сделана ровная площадка или канавка. Стержень 1 подпружинен пружиной 4 и снабжен шайбой 5.
Фиксатор 2 представляет собой штифт запрессованный в отверстие стержня 1.
При закрывании зева крюка для предотвращения выпадения стропа стержень 1 вводят в отверстие выполненное в носке рога крюка при этом фиксатор 2 скользит по продольному пазу 3 отверстия. После закрытия зева крюка свободным концом стержня его поворачивают на 180°. От выпадения стержень удерживается пружиной 4 которая прижимает фиксатор 2 к внутренней поверхности носка рога крюка.
Рис. 12. Предохранительное устройство для грузового крюка.
Грузоподъёмный крюк с предохранительной накладкой.
А С №872430; Грузоподъёмный крюк.
Рис. 11. Грузоподъёмный крюк.
Известен крюк с предохранительной накладкой на рабочей поверхности зева защищающей ее от истирания. Накладка выполнена из листового металла.
Однако изготовление накладки из листа для крюков разных типоразмеров требует создания соответствующей штамповочной оснастки и затрат высококвалифицированного труда что
усложняет производство и снижает экономические показатели. Кроме того листовую накладку имеющую сложную кривизну затруднительно завести в зев крюка. Таким образом листовая накладка сложна в изготовлении и затруднителен монтаж накладки в зеве крюка также требующий затрат высококвалифицированного труда.
На рис. 11 изображен крюк общий вид. Грузоподъемный крюк имеет хвостовик 1 рог 2 и рабочую поверхность 3 зева на которую уложены вдоль плоскости зева отрезки намагниченной проволоки 4 соединенные между собой сварными прихватками 5 и удерживаемые на роге 2 скобами 6 охватывающими наружную сторону рога 2.
Из соединяемых между собой отрезков проволоки таким образом образована предохранительная накладка 7.
Грузоподъемный крюк работает следующим образом.
Присоединенный хвостовиком 1 к грузоподъемному средству (не показано на чертеже) крюк подводят к грузу (не показан на чертеже) и вводят рог 2 в отверстие любой из возможных подвесок груза при этом в процессе подъёма перемещения и опускания поверхность подвески груза при этом в процессе подъёма перемещения и опускания поверхность подвески груза контактирует с поверхностью накладки 7 которая при проскальзывании подвесок подвергается износу в первую очередь обеспечивая защиту от истирания рабочей поверхности 3 зева крюка.
В связи с этим даже в условиях тяжелых нагрузок например в металлургическом производстве срок эксплуатации крюка увеличивается в 2-3 раза. Однако изготовление и замена листовых накладок требует изготовления штамповочной оснастки и сложной подготовки накладки на крюке а проволочные накладки заменяются без оснастки и сложной подгонки на крюке.
Расчёт механизма подъёма
Принимаем сдвоенный полиспаст. Максимальное натяжение каната определяем по формуле:
где число ветвей каната навиваемых на барабан Zк.б=2; КПД полиспаста п=094; КПД уравнительного блока н.бл=096.
Выбираем канат типоразмера ЛК-Р исходя из условия:
где коэффициент использования каната zp=335.
Диаметр каната dк=69мм разрывная сила Fразр≥231кН при расчетном пределе прочности проволок при растяжении равном 1770МПа. Условное обозначение каната:
Канат 6.9-Г-В-Н-В-1770 ГОСТ2688-80.
Фактический запас прочности zр.ф.=263692=38
2.Выбор крюковой подвески и крюка
По заданной грузоподъемности G5 т и группе режима работы М2 выбираем заготовку крюка №14.
Требуемую наименьшую высоту гайки крепления хвостовика крюка с резьбой М48 рассчитываем по формуле
где внутренний диаметр резьбы d1=42587мм; отношение высоты опасного сечения витка резьбы к шагу для метрической резьбы k1=087; коэффициент неравномерности распределения нагрузки между витками kH=056 при dS=505=10>9; допускаемое напряжение []=015T=015240=36МПа.
Конструкцию крюковой подвески выбираем сравнивая два варианта.
По первому варианту – выбираем стандартную крановую подвеску. Заданной грузоподъемности кратности полиспаста и группе режимов работы соответствует крюковая крановая подвеска типа 1-5-406 с одним блоком диаметром 406 мм предназначенная для грузоподъемности 5 т.
По второму варианту – проектируем крюковую подвеску в которой диаметр блока определяем по формуле:
где диаметр каната dk=69 мм; коэффициент выбора диаметра h2=14 при режиме работы М2.
Назначаем размеры траверсы подвески: d0=42мм; b=70мм; l=148мм по аналогии со стандартной подвеской.
Принимаем материал траверсы – сталь 45 и из формулы определяем ее высоту:
где допускаемое напряжение (МПа – предел текучести для стали 45 и s=3 – коэффициент запаса). Окончательно принимаем h=60 мм.
Назначаем размеры щек обоймы подвески (=18мм; r=05h=0565=32.5мм; R=120мм) и проверяем их на прочность по формуле:
где допускаемое напряжение для стали марки Ст 3:
Проверяем выбранный упорный подшипник №8118 по ГОСТ 7872-89 под опорной гайкой крюка на статическую грузоподъемность С0:
Статистическая прочность обеспечена.
3 Определение основных размеров блоков и барабана
Диаметр уравнительно блока определяем по формуле:
где коэффициент выбора диаметра h3=125 при режиме работы М2.
Принимаем в соответствии с нормальным рядом Dур.бл.=90мм.
Определяем глубину ручья блока h=(14 19)dk=9.66 13.11 мм принимаем h=12 мм; раствор ручья b=(2 25)dk=14 1725 мм принимаем b=15 мм; радиус дна ручья R=(053 056)dk=36 39 мм принимаем R=45 мм.
Диаметр барабана по формуле:
Длину барабана рассчитываем по формуле:
где Z1 – число неприкосновенных витков шаг навивки t:
число витков каната:
Выбор толщины стенки барабана. Принимая в качестве материала барабана серый чугун СЧ18 по формуле 14 рассчитываем минимальное значение толщины стенки из условий технологии изготовления литых барабанов:
Так как отношение воспользуемся формулой (2.17) для определения требуемой толщины стенки барабана:
(где допускаемое напряжение для чугуна СЧ18 и режима работы М2 []сж=130МПа.
Выбираем из ряда нормальных линейных размеров =8 мм. Условие >min соблюдается.
4.Прочностной расчет оси барабана и выбор подшипников
Составим расчетную схему нагружения оси барабана изгибающими силами канатов Fmax
Определим следующие конструктивные размеры:
Реакции в опорах находим по формулам:
Изгибающие моменты в расчетных сечениях (под ступицами дисков барабана) получим по формулам:
Принимаем в качестве материала оси сталь 45 (предел выносливости ). Допускаемое напряжение:
где k0 – коэффициент учитывающий конструкцию детали (для валов и осей k0=20 28); принимаем k0=25; [S] – допускаемый коэффициент запаса прочности (для групп режимов работы М2 [S]=14).
Диаметр оси в наиболее опасном сечении (под левой ступицей) найдем из выражения:
С учетом ослабления сечения шпоночным пазом принимаем d=30мм и конструируем ось барабана.
Выбор подшипников. Исходя из диаметра оси под ступицей барабана d=30мм назначаем диаметр под подшипником dп=30 мм.
Учитывая невысокую точность монтажа оси барабана выбираем шариковые радиальные сферические подшипники средней серии №306 по ГОСТ 28428-90. Для принятого типоразмера подшипника выполняется условие:
где RА – радиальная нагрузка на подшипник; С0 – статическая грузоподъемность подшипника.
Таким образом статическая прочность обеспечена.
5.Выбор электродвигателя
Максимальная статическая мощность требуемая для подъема заданного груза рассчитывается по формуле:
Требуемая мощность двигателя по формуле:
Выбираем при ПВ=40% электродвигатель MTKF 411-6 мощностью Рдв=22кВт частотой вращения nдв=935 мин-1 с маховым моментом 19кгм2.
6.Выбор передаточного механизма
Требуемое передаточное число редуктора по формуле:
где частоту вращения барабана находим по формуле:
Выбор типоразмера редуктора производиться из рассмотренных условий.
Наибольший статический момент на валу барабана механизма подъема по уравнению:
Приняв коэффициент долговечности Кд=05 рассчитываем эквивалентный момент на тихоходном валу редуктора по формуле:
Выбираем редуктор ЦУ-100 с передаточным числом up=5 номинальный вращающим моментом Tн=025кНм.
Условие выбора редуктора и выполнение неравенства:
7.Уточнение выбора электродвигателя
Вычисляем частоту вращения барабана:
Определяем фактическую скорость подъема груза:
Уточняем мощность приводного электродвигателя:
Следовательно принятый ранее типоразмер электродвигателя выбран правильно.
Определим расчетный тормозной момент по формулам:
При коэффициенте запаса торможения Кт=1.5 передаточное число механизма
Выбираем автоматический нормально замкнутый тормоз с электромеханическим толкателем типа ЭМТ-2-400 у которого номинальный тормозной момент Тт.н=04кНм превышающий расчетный т.е соблюдаются требуемые условия.
9.Проверка электродвигателя на пусковые загрузки
Определение времени разгона. Продолжительность периода разгона при подъеме груза рассчитываем по формуле:
где общий маховый момент механизма с грузом из выражения:
средний пусковой момент определяемый по формуле:
(; принимаем для двигателя ( п=2);
момент статических сопротивлений при разгоне из выражения:
Полученное значение tп не превышает допускаемое [tп]=1..2c.
10.Проверка времени торможения.
Время торможения при опускании груза по аналогии с выражением
где момент от груза на тормозном валу:
Рассчитанное время торможения при опускании груза получилось меньше рекомендуемого времени разгона следовательно регулировку тормоза на больший тормозной момент не проводят.
11.Расчет крепления каната к барабану
Крепление каната к барабану осуществляем накладными планками..
Силу воспринимаемую узлом крепления каната определяем по формуле:
где коэффициент трения на соприкасающихся поверхностях деталей крепления каната ; угол обхвата барабана канатом .
Силу затяжки болтов находим по формуле:
Предварительно приняв диаметр болта dбt=8 мм (M12) и число болтов zб=6 находим суммарное напряжение возникающее в болтах крепления каната по формуле:
Допускаемое напряжение для материала болта (сталь 35)
Поскольку условие прочности выполняется.
Расчёт механизма передвижения тележки
Выбранная принципиальная кинематическая схем; передвижения тележки показана
на рис. 7 Мех. привод к валу ходового колеса от электродвигателя переменного тока через вертикальный цилиндрический редуктор широко применяемый в механизмах передвижения крановых тележек. Двухколодочный короткоходовой нормально электромагнитный тормоз установлен на валу двигате.
Рис.1. Кинематическая схема механизма передвижения
1.Выбор диаметра ходовых колес
Вес тележки при группе режима работы М2:
Принимаем вес тележки .
Диаметр колеса выбираем из условия где находим из при числе колес тележки допустимой нагрузке на одно колесо ;
Выбираем ходовое колесо .
2.Определение сопротивлений передвижению тележки
Сопротивление передвижению тележки мостового крана рассчитываем по формуле приняв коэффициент трения качения колеса по рельсу коэффициент трения в подшипниках колес и коэффициент дополнительных сопротивлений (центральный привод на ходовые колеса) при расчетном диаметре цапф колес
3.Определение мощности двигателя
При предварительно принятом значении КПД привода и кратности среднего
пускового момента двигателя по отношению к номинальному требуемая мощность электродвигателя по формуле (3.4)
Выбираем крановый асинхронный электродвигатель с короткозамкнутым ротором MTKF 011-6 мощностью частотой вращения (при ПВ=40%).
Частота вращения ходовых колес:
Требуемое передаточное число редуктора:
Выбираем редуктор типоразмера Ц2У-160-25-12К-1-У2 с передаточным числом .
Фактическая скорость тележки при этом
Уточняем значение мощности электродвигателя
5.Проверка электродвигателя на время разгона
Максимально допустимое ускорение тележки рассчитываем исходя из условия что кран работает в закрытом помещении (коэффициент сцепления ходового колеса с рельсом ) и число приводимых ходовых колес :
Минимально необходимое время пуска двигателя при полученном
Принимаем фактическое время разгона массы тележки и груза и определяем среднее ускорение:
Найденное значение ускорения меньше допустимого следовательно условие соблюдается.
6.Определение тормозного момента и подбор тормоза
Т.к скорость перемещения тележки v=041мc то по правилам Госгортехнадзора РФ тормоза в механизме устанавливать не нужно.
Техника безопасности.
Для данного типа подъемнотранспортного устройства характерно наличие следующих поражающих факторов: повышенный шум при работе механизма наличие вращающихся и движущих частей барабана оборудования наличие электрооборудования.
Вращающиеся и движущие части оборудования представляют собой большую опасность для персонала. В случае не обеспечения техники безопасности возможны несчастные случаи. На оборудовании также установлено электрооборудование большой мощности. В условиях повышенной влажности при нарушении обмотки и зацепления возможно поражение электрическим током с тяжелыми последствиями.
Наибольшую опасность представляет падение тележки. Во избежание этого должны периодически осматриваться ходовые пути тележки.
Особую осторожность необходимо соблюдать при выполнении ремонта осмотра и обслуживании устройства т.к. оно находится на высоте.
К работе на этом подъемнотранспортном механизме допускаются лица прошедшие медицинское осведетельствование инструкцию по технике безопасности на данном агрегате а также лица старше 18 лет.
Запрещается ремонт установки при ее работе.
В ходе выполнения курсового проекта по курсу «Подъемно-транспортные установки» нами была проделана очень трудоемкая и кропотливая работа. Мы получили знания по расчету и выбору элементов привода. Научились работать с научной литературой правильно пользоваться справочниками и атласами.
Отдельное место в выполненной работе занимает графическая часть. Чертежи были сделаны на компьютере в специальном приложении систем автоматизированного проектирования «КОМПАС-3D 11» что говорит о применение новых технологий в выполнение курсового проекта и повышение качества работы. Нами были закреплены основы черчения т.к. чертежи насыщены различными деталями их видами и разрезами.
Список используемой литературы.
Курсовое проектирование грузоподъемных машин: Учебное пособие для студентов машиностроительной специальности вузовС.Л. Козак В.Е. Дусье Е.С. Кузнецов и др. Под ред. С.А. Казака. – М: Выш. шк. 1989 – 319с. ил.
Примеры расчета кранов: справочник под ред. Г. Павлова М: 1982.
Александров М.П. Подъемно транспортные машины: Учебное пособие для машиностроительных специальностей вузов – 6 – е изд.. перераб. – М: высш. шк. 1985 – 520с. ил.
Крановое электрооборудование: Справочник под ред. Рабиновича А.А. М: 1979г.
Блок.cdw

Полумуфта.cdw

Сталь 35Х ГОСТ 4543-71
КП-ПТУ-02068108-260601-АПБ-00.01.002-2010
Вал приводной.cdw

Сталь 45 ГОСТ 1050-74
КП-ПТУ-02068108-260601-АПБ-00.01.004-2010
Барабан.cdw

Крюковая подвеска.cdw

Кратность полиспаста 4
Подшипники смазать литолом ЛИТОЛ-24
Неуказанные предельные отклонения размеров
КП-ПТУ-02068108-260601-АПБ-00.04.000-2010
Установка барабана.cdw

Крюковая подвеска.spw

Гайка М4 ГОСТ 5916-70
Шайба 12 65Г ГОСТ 6402-70
Установка барабана.spw

Болт ГОСТ 7798-70 М6х20
Шайба 6 ГОСТ 6402-70
Болт ГОСТ 7798-70 М10х25
Шайба 6 65Г ГОСТ 6402-70
Гайка ГОСТ 4685-70 М6
Шайба 10 ГОСТ 6402-70
Подшипник ГОСТ 8338-75 305
Подшипник ГОСТ 8338-75 306