Проектирование тележки электрического мостового двухбалочного крана




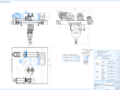
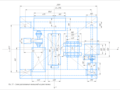
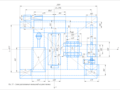
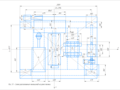
- Добавлен: 25.01.2023
- Размер: 834 KB
- Закачек: 0
Описание
Состав проекта
![]() |
![]() |
![]() ![]() ![]() ![]() |
![]() ![]() ![]() ![]() |
![]() ![]() ![]() ![]() |
![]() ![]() ![]() ![]() |
![]() |
![]() ![]() ![]() ![]() |
![]() |
![]() |
![]() ![]() ![]() |
![]() ![]() ![]() ![]() |
Дополнительная информация
Фрагмент3.frw

Чертеж2.cdw

КР.190205.015. 125.00.00.00.
Нагрузки на ходовые колеса
Схема навивки каната
Высота подъема груза
Продолжительность включения
Передвижения тележки
Фрагмент.frw

Фрагмент2.frw

Фрагмент 5.frw

КП ГПМ.docx
ФЕДЕРАЛЬНОЕ АГЕНТСТВО ЖЕЛЕЗНОДОРОЖНОГО ТРАНСПОРТА
ФЕДЕРАЛЬНОЕ ГОСУДАРСТВЕННОЕ БЮДЖЕТНОЕ ОБРАЗОВАТЕЛЬНОЕ УЧРЕЖДЕНИЕ ВЫСШЕГО ПРОФЕССИОНАЛЬНОГО ОБРАЗОВАНИЯ
САМАРСКИЙ ГОСУДАРСТВЕННЫЙ УНИВЕРСИТЕТ ПУТЕЙ СООБЩЕНИЯ
Кафедра строительных дорожных машин и технологии машиностроения
по дисциплине: «Грузоподъемные машины»
на тему: «Проектирование тележки электрического мостового двухбалочного крана»
Расчет механизма подъема груза5
2Выбор кинематической схемы механизма
3 Выбор крюковой подвески
4Уточнение схемы полиспаста и определение его кратности
6Определение основных размеров сборочной единицы «Установка верхних блоков»
7 Определение основных размеров сборочной единицы «Установка барабана»
12Проверка двигателя механизма подъема по времени разгона
Расчет механизма передвижения тележки17
1Кинематическая схема передвижения выбор колесных установок и рельса
2Определение сопротивлений передвижению
4Выбор редуктора муфт и тормоза
5Проверка двигателя на время разгона
6Проверка времени торможения
7Проверка запаса сцепления колес с рельсами
Компоновка тележки28
Грузоподъемные машины – высокоэффективное средство комплексной механизации и автоматизации подъемно-транспортных погрузочно-разгрузочных и складских (ПРТС) работ. Применение таких машин уменьшает объем использования тяжелых ручных операций и способствует резкому повышению производительности труда. Автоматизация ГПМ позволяет включить ее в поточную линию а универсальность использования – сделать составным элементом гибкого автоматизированного производства.
Курсовое проектирование ГПМ основываясь на практике ранее выполнявшихся студентом графических и расчетных работ по черчению начертательной геометрии теории механизмов и машин деталям машин призвано выработать навыки проектирования машины в целом.
Практическая самостоятельная работа студента над темой курсового проекта будет эффективной только в том случае если обучающийся твердо усвоит основные теоретические положения ранее изучавшегося лекционного материала успешно выполнит расчетный и лабораторный практикумы. Курсовое проектирование способствует практическому закреплению ранее приобретенных знаний и навыков. Вместе с этим курсовое проектирование вводит студента в круг вопросов которые он будет изучать в будущих спецдисциплинах. Хорошо подготовленные студенты могут выполнять реальные проекты выдвигаемые производством.
Расчет механизма подъема груза
Исходными данными к выполнению курсового проекта согласно индивидуальному заданию являются: грузоподъемность Q =17 т; максимальная высота подъема Н=12 м; скорость подъема груза vгр=019 мс; скорость передвижения тележки vт=08 мс; класс нагружения В1 и класс использования машины(режим работы механизмов по Правилам ГГТН или группа режима работы по ГОСТ 25835-83); продолжительность включения электрооборудования ПВэл=40 %.
2 Выбор кинематической схемы механизма
Так как скорость подъема небольшая передаточное число механизма будет большим. Принимаем за основу кинематическую схему изображенную на рисунке 1.1 в которой двигатель соединен с редуктором при помощи зубчатой муфты с промежуточным валом. Преимущества такого компонования - компактность блочность и передача крутящего момента непосредственно с редуктора на барабан минуя ось барабана. Выбираем схему полиспаста (рисунок 1.2 ). Уравнительный балансир и уравнительный блок в данной схеме не используются (кинематическую схему механизма подъема груза и схему полиспаста - зарисовываем).
По нормали ПО «Сибтяжмаш» выбираем крюковую подвеску типоразмера 4-20-406 (рисунок А.1.1 в; таблица А.1.1) имеющую следующие параметры: QП =20 т; режим работы - средний; Zбл = 4; D = 406 мм; В1 = 152 мм; В2 = 16 мм; В3 = 76 мм; В4 = 92 мм; В = 445 мм; Н1 = 292 мм; Н2 = 440 мм; Н = 1187 мм; L1 = 540 мм; L = 220 мм; d1 = 170 мм; d3 = 110 мм; d = 110 мм; dк = 14 17 мм; тп = 318 кг.
Начертим в масштабе упрощенный габаритный чертеж («габаритку») крюковой подвески (рисунок 1.3).
Рисунок 1.2 – Схемы сдвоенных полиспастов
4 Уточнение схемы полиспаста и определение его кратности
Число блоков выбранной крюковой подвески соответствует числу блоков на кинематической схеме поэтому схема запасовки канатов в полиспасте сохраняется. Его передаточное число (кратность) равно 4.
Максимальное статическое усилие в канате определяется :
где G - вес номинального груза и крюковой подвески Н; тгр - масса груза кг; тп - масса крюковой подвески кг; g - ускорение свободного падения мс2; ZK - число ветвей каната навиваемых на барабан; ип - кратность полиспаста определяемая как отношение числа ветвей каната на которых подвешен груз к числу ветвей идущих на барабан (или равная числу подвижных блоков); цп - КПД полиспаста (таблица 1.2 [1]).
Выбираем тип каната ЛК-Р619(1+6+66)+1о.с. ГОСТ 2688-80 (рисунок А.2.1) имеющий линейное касание проволок и разные диаметры проволок в верхнем слое пряди. Диаметр каната dK выбирается по соотношению:
Sразр = Smax кзап = 22121 · 5 = 110605 Н
где Spaзp - разрывное усилие каната в целом (таблицы А.2.1 и А.2.2) Н; кзап - коэффициент запаса прочности каната (для режима работы 3М кзап = 5).
Из таблицы А.2.1 выбираем типоразмер каната.
Канат 14-Г-В-С-О-Н-1862-ГОСТ 2688-80 имеет параметры:
Spaзp = 112500 Н; dк = 14 мм; Fк = 7440 мм2; назначение каната - грузовой; марка проволоки - высшая;
расчетный предел прочности проволок на разрыв - 1862 МПа;
вид покрытия проволоки - оцинкованная для среднеагрессивных условий работы;
сочетание направлений свивки элементов - одностороннее;
способ свивки каната - нераскручивающийся;
направление свивки каната: для одной половины полиспаста - правое для другой - левое.
Проверим перегиб каната на блоках подвески по условию:
где Dбл - диаметр блока измеряемый по средней линии навитого каната мм; е - коэффициент зависящий от типа машины (для режима работы 3М мостовых кранов е =20).
При этом диаметр блока по средней линии каната определяется
Dбл = D + dк = 406 +14 = 420 мм а 420 > 14 · 20 = 280 мм
где D - диаметр блока измеряемый по дну канавки (рисунок А.1.1 и А.1.2 таблица А.1.1).
Следовательно условие проверки выполняется. Оставляем выбранный канат - Канат 14-Г-В-С-О-Н-1862-ГОСТ 2688-80.
6 Определение основных размеров сборочной единицы «Установка верхних блоков»
Диаметры верхних блоков по дну канавки D и средней линии навитого каната Dбл можно принять такими же как в крюковой подвеске т. е.
а максимальный диаметр блока при диаметре каната до 285 мм рассчитываем по формуле:
Dmax = D + 2h2 = 406 + 2 · 22 = 450 мм
где h2 - глубина канавки блока (рисунок А.3.2 таблица А.3.1) мм.
Из стандартного номинального ряда значений Dma 380; 450; 530; 630;
0; 900 мм принимаем Dmax = 450 мм.
Тогда окончательно D = 450 – 2 · 14 = 422 мм; Dбл = D+dк = 422+14 = 436 мм. Диаметр уравнительных блоков по средней линии навиваемого каната принимается на 20 % меньше чем диаметры обычных блоков.
Конструкция сборочной единицы «Установка верхних блоков» может быть выполнена по разным вариантам. На рисунке 1.4 [1] (или на рисунках П.3.1 и П.3.2 [2]) приведен пример компоновки верхних блоков и основные размеры при использовании в механизме подъема с трехблочной крюковой подвеской (рисунок 1.2 в [1]).
По таблице 1.3 [1] определяем размеры показанные на рисунке 1.4 [1]:
Lв.бл = 115Dбл = 115 · 436 = 5014 мм; примем Lв.бл = 500 мм;
Вв.бл = 115Dбл = 13 · 436 = 5668 мм; примем Вв.бл = 560 мм;;
Нв.бл = 125Dбл = 125 · 436 = 545 мм; примем Нв.бл = 550 мм;
hв.бл = 06Dбл = 06 · 436= 2616 мм; примем Нвбл = 260 мм;
Ав.бл = 08Dбл = 08 · 436= 3488 мм; примем Ав.бл = 260 мм;
L0 = (06 07) Lв.бл = (06 07) · 500 = 300 350 мм; примем: L0 = 300 мм.
Расстояние между осями присоединительных отверстий с1 с2 назначаем конструктивно исходя из удобства размещения болтов и закручивания гаек: с1 = 120 мм; с2 = 420 мм.
После определения размеров установки верхних блоков вычерчиваем ее «габаритку» с указанием полученных размеров.
На рисунке 1.5 [1] представлен один из возможных вариантов установки барабана предназначенного для сдвоенного полиспаста и показаны основные размеры.
Диаметр барабана по средней линии навиваемого каната принимается на 15 % меньше чем диаметры обычных блоков:
Dб = 085 · Dбл = 085 · 436 = 3706 мм.
Принимаем Dб = 400 мм в соответствии со стандартным рядом размеров барабана (160; 200; 250; 320; 400; 450; 500; 560; 630; 710; 800; 900 и 1000 мм).
Определяется диаметр барабана по дну канавок:
D0 = Dб – dк= 400 - 14 = 386 мм.
Максимальный диаметр окружности описываемой крайней точкой установки барабана предварительно принимается по соотношению
D = (11 13)Dб = 12 · 400 = 480 мм.
Рабочая длина каната:
Lк.р= Нип = 12 · 4= 48 м где Н - высота подъема груза м; ип - кратность полиспаста.
Число рабочих витков определяют по соотношению
Шаг нарезки определяем по формуле:
t = (110 123)dк = (110 123) · 14 = 154 1722 = 16 мм.
Длина одного нарезного участка барабана равна:
lн = t (zр + zнепр + zкр ) = 16 · (382 +15 + 3) = 376 мм
где t - шаг нарезки мм; zp - число рабочих витков для навивки половины полной рабочей длины каната; zнепр = 15 - число неприкосновенных витков каната необходимых для разгрузки деталей крепления каната на барабане; zкр = 3 4 - число витков для крепления конца каната.
Минимально допускаемое расстояние между осью блоков крюковой подвески и осью барабана:
hmin.б = 3 · Dб = 3 · 400 = 1200 мм.
Длина гладкого среднего участка может быть определена по формуле:
где Внар - расстояние между осями наружных блоков выбранной крюковой подвески (Внар=2В3=2 · 76=152 мм рисунок А.1.1 в); [у] = 6° - максимально принимаемое при предварительных расчетах значение угла отклонения каната от оси ручья блока.
Принимаем длину гладкого среднего участка l0 = 200 мм.
Длину одного гладкого концевого участка определим как
принимаем lK = 70 мм.
Определим длину барабана:
Lб = 2(l н + l к)+ lо + Вз.в = 2(376 + 70) + 200 + 0 = 1092 мм.
Длина барабана превышает его диаметр в 273 раза (1092400) что вполне приемлемо (до 3.4).
Используя соотношения подобия полученные путем анализа существующих конструкций определяют следующие размеры показанные на рисунке 1.4: ширину опоры Воп зазор между барабаном и опорой ширину основания опоры Восн.оп длину основания опоры Lосн.оп а также размеры l1 и l2.
Воп = 02Dб = 02·400 = 80 мм; Восн.оп = (1 12)Воп = (1 12)·80 = 80 96 =
При компоновании механизма требуется определить длину установки барабана Lуст.б и длину основания опоры Lосн.оп мм
Lосн оп = (07 08) Dб = (07 08)· 400 = 266 320 =280 мм.
Высота оси барабана относительно основания внешней опоры может быть принята по соотношению:
h = (03 06) Dб = (03 06) · 400 = 114 228 =180 мм.
Расстояния между присоединительными отверстиями вычисляются по формулам:
С1 = (02 03)Восн = (02 03) · 80 = 20 25 = 20 мм
С2 =(05 08)Lосн оп = (05 08) · 280 = 140 224 = 220 мм.
После определения основных размеров установки барабана вычерчивается ее габаритная схема (рисунок 1.5 [1]).
Максимальная статическая мощность которую должен иметь механизм во время установившегося движения при подъеме номинального груза кВт
где мех = 080 085 – предварительное значение КПД механизма.
Выбираем серию двигателя МТВ отличающуюся высоким классом нагревостойкости изоляции. С учетом коэффициента использования мощности
Выбираем двигатель типа МТВ 412-8 ГОСТ 185-70 (рисунок А.4.1
таблицы А.4.1 - А.4.4) имеющий параметры: Nдв = 28 кВт; ПВдв = 15 %; пдв= 705 мин-1; длина L = 9525 мм высота H = 524 мм ширина. B1 = 440 мм d = 65 мм; d2 = М42×2; расстояние между отверстиями крепления 2С1 = 420 мм и 2С = 330 мм; тдв = 375 кг; КПД = 085; момент инерции ротора Iр.дв = 3 кг·м ; максимальный момент Тдв.тах = 840 Н·м (84 кгс·м).
Выбор типоразмера редуктора производится по значению расчетного эквивалентного момента на тихоходном валу Трэ Н·м требуемому передаточному числу механизма ир.тр и частоте вращения ротора электродвигателя пдв.
Для определения эквивалентного момента определим следующие параметры:
- коэффициент переменности нагрузки kQ по формуле:
где k - коэффициент нагружения зависящий от класса нагружения (таблица 1.4 [1]);
- частота вращения барабана определяется:
- число циклов нагружения на тихоходном валу редуктора zm:
где tмаш - машинное время работы механизма (таблица 1.5 [1] согласно заданию) ч;
- суммарное число циклов контактных напряжений зуба шестерни тихоходной ступени редуктора zр :
zр = zм · ит = 849 · 106 · 5 = 4245 · 106
где ит=5 - среднее значение передаточного числа тихоходной ступени редуктора;
- коэффициент срока службы kt:
где zр – суммарное число циклов контактных напряжений зуба шестерни тихоходной ступени редуктора; z0=125106 – базовое число циклов контактных напряжений типажных редукторов;
- коэффициент долговечности составляет:
кд = kQ ·kt = 05 · 070 =035;
- расчетный крутящий момент на тихоходном валу редуктора при подъеме
номинального груза в период установившегося движения Н·м:
где пб = 099 - КПД опор барабана;
- эквивалентный момент равен:
Тр.э = kд · Тр = 035 · 826744 = 2894 Н·м.
Требуемое передаточное число редуктора находится по соотношению:
где пдв - действительная частота вращения вала электродвигателя мин-1.
Предварительно выбираем редуктор Ц2У-315Н (рисунок А.5.1 таблицы А. 5.1 - А.5.3) имеющий передаточное отношение ир = 20 и допускаемый крутящий момент на тихоходном валу Тр.н = 86 кН·м.
При выборе редуктора должно соблюдаться условие
где Трн - номинальный крутящий момент на тихоходном валу редуктора по паспорту Н·м.
Тихоходный вал данного редуктора выполнен в виде части зубчатой муфты. Передаточное число выбранного редуктора up отличается от требуемого передаточного числа uр.тр на
что значительно меньше 15 %. Поэтому оставляем предварительно выбранный редуктор Ц2У-315Н имеющий следующие технические характеристики: передаточное отношение ир = 20; допускаемый крутящий момент на тихоходном валу Трн = 86 кН·м; суммарное межосевое расстояние аw.с=315+200=515 мм; диаметры концов тихоходного dma габаритные размеры (L×H×B)1040×685×395 мм; масса редуктора тр = 510 кг.
Фактическая скорость подъема груза:
Фактический КПД механизма подъема:
= рбп = 096 · 099 · 096 = 091
где пр - максимально возможное значение КПД для выбранного цилиндрического редуктора (для двухступенчатого Ц2У-315Н - р=096.. .097).
Для соединения валов двигателя и редуктора выбираем тип муфты - зубчатая с промежуточным валом (рисунки А.6.1 и А.6.2). Такая муфта хорошо компенсирует возможные неточности монтажа и может передавать большие крутящие моменты.
Типоразмер муфт выбирают по диаметрам концов валов соединяемых данной муфтой.
Диаметр концов валов: dв.быстр = 50 мм (редуктор) d2 = 65 мм - конусный вал (электродвигатель).
По таблице А.6.1. выбираем зубчатую муфту с тормозным шкивом. Данная муфта имеет следующие параметры: диаметр тормозного шкива должен соответствовать допустимому диаметру расточки большему или равному по значению чем диаметр вала электродвигателя (принимаем шкив диаметром D1= 150 мм с диаметром расточки до 65 мм). В полумуфтах допускается выполнять максимальные диаметры расточек во втулках под концы валов dлев.ma номинальный крутящий момент Тм.н = 4000 Н·м; масса тм = 152 кг; момент инерции JM = 0015 кг·м (динамический момент JM = 015 Н·м )
При этом расчетный момент муфты Тр.м должен удовлетворять условию
Далее рекомендуется также начертить «габаритку» муфты.
Определим максимальное значение КПД механизма на участке кинематической цепи от крюка до тормоза:
' = рбп = 096 · 099 · 096 = 091
Статический крутящий момент при торможении создаваемый весом номинального груза на валу на котором устанавливается тормоз
где G - вес груза и крюковой подвески (G= 17318 Н).
Расчетный тормозной момент определяем по формуле:
Tт.р = кт · Тст.т = 15 · 389 = 5974 = 60 Н·м
где кт - коэффициент запаса торможения назначаемый правилами Госгортехнадзора (для режима работы 2М кт = 15).
По расчетному тормозному моменту выбирается автоматический нормально
замкнутый тормоз. При этом должно выполняться условие:
где Тт.н - номинальный тормозной момент тормоза Н·м.
Значению большему чем Тт.р = 400 Н-м соответствует тормоз ТКТ-200 конструкции «ВНИИПМАШ» (рисунок А.7.1) со следующими параметрами (таблицы А.7.1 А.7.2): номинальный тормозной момент Тт.н = 160 Н·м (16 кгс·м); относительная продолжительность включения катушки электромагнита ПВк.эл = 25 %; максимальный ход штока толкателя hшm.ma требуемый диаметр тормозного шкива Dm.ш = 200 мм; ширина колодок Вк = 90 мм; масса тормоза ттор = 37 кг габариты A×H×E = 591×480×177 мм. Начертим «габаритку» тормоза.
12 Проверка двигателя механизма подъема по времени разгона
Наибольшее время разгона получается при разгоне на подъеме и определяется по формуле с
где Jмех.р – приведенный к валу двигателя момент инерции при разгоне всех движущихся частей механизма включая поступательно движущиеся массы кг·м2; Тп.ср. – среднепусковой момент двигателя Н·м; Тст.р. – момент статических сопротивлений при разгоне приведенный к валу двигателя Н·м.
Значение Тп.ср. определяют по формуле Н·м
где Тдв.н – номинальный момент двигателя механизма подъема Нм; п.ср – кратность среднепускового момента двигателя к номинальному (таблица 1.6 [1]).
Значение Jмех.р равно кг·м2
Jмех.р = Jвр +Jпост.р
где Jвр - момент инерции при разгоне всех вращающихся частей механизма кг·м2; Jпост.р - момент инерции при разгоне поступательно движущихся частей механизма плюс груза приведенный к валу двигателя кг·м2.
Величина Jпост.р определяется по формуле
Величина Jвр определяется
где γ=11 12 – коэффициент учета инерции вращающихся масс расположенных на втором третьем и последующих валах механизма; Jт.ш –момент инерции тормозного шкива кг·м2.
Значение Jт.ш определяется по приближенной формуле кг·м2
где mт.ш = 25 кг – масса тормозного шкива (таблица 1.7[1]) кг; Dт.ш – диаметр тормозного шкива (таблицы III.38 III.40 страница 228 [3]) м; т.ш06 – коэффициент учитывающий распределение массы шкива (коэффициент приведения геометрического радиуса вращения к радиусу инерции).
Момент инерции муфты с тормозным шкивом
Jм.быстр= Jм 2+Jт.шк = 00152 + 022 = 02275 кг·м2
Jвр =115· (3 + 0015 + 022)= 372 кг·м2
Jмех.р = 372 + 0119 = 384 кг·м2.
Момент статических сопротивлений при разгоне приведенный к валу двигателя
Наибольшее время разгона
РАСЧЕТ МЕХАНИЗМА ПЕРЕДВИЖЕНИЯ ТЕЛЕЖКИ
1 Кинематическая схема механизма передвижения выбор колесных установок и рельса
Как правило механизм передвижения тележек имеет центральный привод с тихоходным трансмиссионным валом (рисунок 2.1 [1]). Общее количество ходовых колес nх.к зависит от грузоподъемности и при Q≤160 т предварительно принимается равным четырем.
Максимальная статическая нагрузка на ходовое колесо тележки определяется по формуле Н
где 11 – коэффициент неравномерности нагружения колес; G – вес груза и крюковой подвески (G= Н); Gт – вес порожней тележки определяется по таблице 2.1 (для Q=17 т – Gт=52500 Н).
Таблица 2.1 – Вес порожней тележки Gт (кН) в зависимости от грузоподъемности
По таблице 2.1 [1] используя значение Рст. max выбираем диаметр колес Dк=320 мм.
По диаметру колеса выбираем стандартные колесные установки (рисунок П.8.1; таблицы П.8.1 П8.3) с двухребордными колесами типа К2Р и выписываем их основные параметры: диаметр качения колеса Dк=320 мм диаметр цапфы dц=70 мм ширина дорожки катания В=80 мм масса приводного колеса mк.пр=8502 кг и неприводного – mк.непр=7716 кг габариты колесной установки (D1×А1=360×292 мм).
Выбираем типоразмер рельса КР80 (таблицы 2.1 [1] и П.9.1) с шириной головки рельса b=50 мм. Для тележечных двухребордных колес ширина их дорожек катания В=80 мм должно быть больше ширины головки рельса b=50 мм на 30 мм. Из вышеприведённых размеров видим что данное условие
выполняется. Если же его не выполнять то не будет компенсироваться неточность установки колес и укладки рельсов.
Выписываем следующие параметры рельса (таблицы П.9.1 и П.9.2): номинальную ширину головки b1=55 мм радиус головки R=300 мм ширину основания рельса b2=90 мм расстояние от основания до нейтральной оси У1 =432 мм; площадь поперечного сечения F=38 см2; момент инерции сечения Ух=35754 см2; погонная масса рельса mпог=2985 кгм.
2 Определение сопротивлений передвижению
Полное сопротивление передвижению тележки складывается из нескольких составляющих
где Wтр – сопротивление создаваемое силами трения Н; Wу – сопротивление создаваемое уклоном подтележечного пути Н; Wин – сопротивление создаваемое инерцией вращающихся и поступательно движущихся масс Н.
Сопротивление от сил трения определяется по формуле
где – коэффициент трения качения колеса по рельсу (таблица 2.2 [1]) м; f=0015 – приведенный коэффициент трения скольжения в подшипниках колес; dц – диаметр цапфы колеса м; Dк – диаметр колеса м.
Сопротивление создаваемое уклоном находим по выражению:
где α – уклон рельсового пути составляющий для тележки принимается 0002.
Сопротивление создаваемое силами инерции
где mпост – масса поступательно движущихся частей крана (тележки 6180 кг и груза с подвеской 17318 кг); – коэффициент учитывающий инерцию вращающихся частей механизма (при скорости передвижения тележки менее 1 мc – =125; а – ускорение при разгоне мc2.
Ускорение а предварительно принимаем равным
а=(05 10)[а]=1001=01 мс2
где [а] – допустимое ускорение мc2 (предварительно принимаются при грузоподъемности более 125 т [а]=01 мc2).
Полное сопротивление передвижению тележки составит:
W=3262+451+2821 =6534Н.
Необходимую мощность двигателя механизма передвижения тележки с учётом перегрузки определяем по формуле кВт
п..ср – кратность среднепускового момента двигателя к номинальному принимается по любому значению из диапазона указанного в таблица 1.6 [1]).Выбираем двигатель типа МТК 12-6 ГОСТ 185-70 имеющий параметры (рисунок П.4.2; таблицы П.4.3 П.4.4): NДВ=35 кВт; ПВДВ=25%; nДВ=875 мин-1; длина – 525 мм высота – 353 мм ширина – 290 мм d =35 мм; расстояние между отверстиями крепления 2С1=205 мм (с боковой стороны) и 2С=220 мм; масса mдв=98 кг; отношение максимально момента к номинальному Тma КПД=085; момент инерции ротора Jр.дв=0042 кгм2 (маховый момент составляет 025 кгм2) .
4 Выбор редуктора муфт и тормоза
Выбор типоразмера редуктора производится по значению расчетного эквивалентного момента на тихоходном валу Тр.э (Нм) требуемому передаточному числу механизма uр.тр и частоте вращения ротора электродвигателя.
– коэффициент переменности нагрузки – kQ по формуле:
где k – коэффициент зависящий от класса нагружения (таблица 1.4 [1]);
– частота вращения приводных колёс мин-1:
– число циклов нагружения на тихоходном валу редуктора zт:
где tмаш – машинное время работы механизма (таблица 1.5 [1] согласно условиям задачи) ч;
– суммарное число циклов контактных напряжений зуба шестерни тихоходной ступени редуктора zр:
где uт=5 – среднее значение передаточного числа тихоходной ступени редуктора;
– коэффициент срока службы kt:
где z0 = 63106 – базовое число циклов контактных напряжений типажных редукторов;
– коэффициент долговечности составляет:
– требуемое передаточное число редуктора находим по соотношению:
где nдв – частота вращения вала электродвигателя мин-1;
– расчетный крутящий момент на тихоходном валу редуктора при перемещении тележки с номинальным грузом в период установившегося движения Нм:
где мех = 0940995099=092 – КПД муфты – редуктора – подшипников колеса
– эквивалентный момент равен:
Предварительно выбираем редуктор вертикальный ВКУ-500М (рисунок П.5.3; таблицы П.5.6 П5.9) имеющий следующие параметры: передаточное отношение uр=20; мощность подводимую к редуктору при числе оборотов не менее 1000 мин-1 ПВ=25% мощность Nр=76 186 кВт; диаметр быстроходного вала d=40 мм; тихоходного d=65 мм.
где Тр.н – номинальный крутящий момент на тихоходном валу редуктора по паспорту Нм.
Передаточное число выбранного редуктора uр отличается от требуемого передаточного числа uр.тр на
Оставляем редуктор ВКУ-500М имеющий также: суммарное межосевое расстояние аw.с=500 мм; масса редуктора mp=330 кг; габариты – L×H×B=840×475×320 мм (рисунок П.5.3 таблицы П.5.6 П.5.9).
Фактическая скорость передвижения тележки мс:
Для соединения валов двигателя и редуктора выбираем зубчатую муфту с
промежуточным валом. Такая муфта хорошо компенсирует возможные неточности монтажа и может передавать большие крутящие моменты.
Типоразмер муфт выбирают по диаметрам концов соединяемых данной муфтой валов.
Диаметры концов валов: dв.быстр=40 мм (редуктор); d2=35 мм (электродвигатель).
По таблице П.6.1 выбираем зубчатую муфту с тормозным шкивом. Данная муфта имеет параметры: диаметр тормозного выбираем исходя из диаметра расточки который должен быть больше диаметра вала электродвигателя. Принимаем шкив с диаметром D1=105 мм с расточкой до 40 мм. Полумуфта для соединения вала электродвигателя и редуктора – зубчатая с допустимым диаметром расточки d≤40 мм; Тм.н=1000 Нм; mм=67 кг; момент инерции Iм=0005 кгм2 (динамический момент 005 Нм2).
Расчетный момент муфты Тр.м удовлетворяет условию:
В полумуфтах соединения выходного вала редуктора с приводными колёсами тележки допускается выполнять максимальные диаметры расточек во втулках под концы валов dлев.max=dправ.max≤65 мм.
Расчетный крутящий момент на тихоходном валу редуктора механизма передвижения тележки определяют по формуле
По таблице П.6.1 выбираем зубчатую муфту со следующими характеристиками Тм.н=2500 Нм; mм=102 кг; Iм=0008 кгм2 (динамический момент 008 Нм2). Расчетный момент данной муфты Тр.м так же должен удовлетворять условию
Определим максимальное значение КПД механизма на участке кинематической цепи от колёс до тормоза:
Расчетный тормозной момент механизма передвижения тележки определяется по формуле:
где Wин.0 – сопротивление создаваемое силами инерции при движении тележки без груза Н; Wтр.0 – сопротивление создаваемое силами трения при движении тележки без груза Н; Wу.0 – сопротивление создаваемое уклоном подтележечного пути при движении тележки без груза Н.
где mт – масса тележки без груза кг; а и – см. П.2.2.
Сопротивление создаваемое уклоном находится по выражению
Расчетный тормозной момент механизма передвижения тележки равен:
Значению больше чем = 19 Нм и диаметру шкива 105 мм соответствует тормоз ТКТ-100 конструкции «ВНИИПМАШ» (рисунок П.7.1; таблицы П.7.1 и П.7.2) со следующими параметрами: номинальный тормозной момент Тт.н=20 Нм (2 кгс·м); относительная продолжительность включения катушки электромагнита ПВк.эл=25%; максимальный ход штока толкателя
hшт.ma требуемый диаметр тормозного шкива Dт.ш=70 мм; ширина колодок Вк=70 мм; масса тормоза mтор=12 кг; габариты – A×H×E=360×250×130 мм.
5 Проверка двигателя на время разгона
Наибольшее время разгона тележки наблюдается когда она нагружена а уклон пути препятствует движению:
где – приведенный к валу двигателя момент инерции при разгоне всех движущихся частей механизма передвижения включая поступательно движущиеся массы кг·м2; – среднепусковой момент двигателя механизма передвижения Н·м; – момент статических сопротивлений при разгоне механизма передвижения приведенный к валу двигателя Н·м.
Значение определяют по формуле Н·м
где – номинальный момент двигателя механизма передвижения тележки Нм
Значение момента инерции полумуфты с тормозным шкивом определяется по приближенной формуле кг·м2
где =42 кг – масса тормозного шкива механизма передвижения (таблица 1.7 [1]) кг; – диаметр тормозного шкива механизма передвижения (таблица П.6.1) м.
Момент инерции муфты механизма передвижения определим как:
де – момент инерции ротора электродвигателя механизма передвижения кг·м2; – момент инерции тормозного шкива механизма передвижения кг·м2.
Момент инерции при разгоне поступательно движущихся частей тележки приведенный к валу двигателя будет равен:
где mт – масса тележки кг.
Значение равно кг·м2
Наибольшее время разгона тележки будет равно:
Значение фактического ускорения при пуске aпер мc2 соответствует следующему условию:
Электродвигатель по времени разгона подобран правильно.
6 Проверка времени торможения
Время торможения должно быть примерно равно его фактическому значению
где – момент статических сопротивлений при торможении тележки приведенный к первому валу механизма Нм; – момент инерции всех движущихся масс механизма и поступательно движущихся объектов при торможении приведенный к первому валу механизма кг·м2.
Величина определяется по формуле кг·м2
где – момент инерции при торможении поступательно движущихся частей тележки приведенный к валу двигателя кг·м2.
Определим сопротивление от трения при торможении Н.
Статическое сопротивление при торможении тележки Н
где Wу=451 Н – статическое сопротивление от уклона Н.
Момент статических сопротивлений при торможении приведенный к валу двигателя Нм
Время торможения тележки укладывается в допустимые пределы.
7 Проверка запаса сцепления колес с рельсами
Проверка запаса сцепления колес тележки с рельсами при пуске двигателя производится по формуле
где =02 – коэффициент сцепления в закрытом помещении; – число приводных колёс; – число холостых колёс; =12 – наименьший допустимый запас сцепления.
Запас сцепления колёс тележки с рельсами достаточен.
Расположение механизмов подъёма груза и передвижения тележки хорошо изложено в методических указаниях № 2141 [1]. Пользуясь вышеуказанными рекомендациями нанеся координатные оси xx и yy (рисунок 3.1) помещаем центр барабана механизма подъема в начало координат.
В связи с тем что межцентровое расстояние редуктора маленькое размещаем установку верхних блоков в противоположную сторону от оси быстроходного вала редуктора. Примем место схода канатов со стороны быстроходного вала редуктора избегая тем самым S-образного перегибы каната.
Устанавливаем редуктор непосредственно соединив его тихоходный вал с полумуфтой барабана.
Двигатель механизма подъема располагаем ближе к правой хребтовой балке тележки применяя промежуточный вал вставку.
Тормоз механизма подъема устанавливаем таким образом чтобы в качестве его тормозного шкива можно было использовать одну из полумуфт.
Хребтовые балки тележки образуемые вертикальными листами (пунктирные линии) располагаем из условия опирания на них барабана и центра тяжести редуктора механизма подъема. Расстояние между листами l1=200 мм берем из выбранной колесной установки т.е. равной расстоянию L=200 мм (таблица П.8.1) между осями букс на месте которых имеются приспособления для крепления к торцам балок.
Намечаем пунктиром поперечные листы рамы тележки таким образом чтобы они воспринимали вертикальную нагрузку от верхних блоков двигателей и тормозов.
Привод механизма передвижения располагаем со стороны установки верхних блоков.
Ориентировочно намечаем положение неприводных колес и контур рамы тележки (длина рамы составит 2559 мм). Геометрический центр рамы принимаем за центр тяжести – точка Gр на рисунке 3.1. Вес рамы определяется разностью между ранее принятым весом тележки и весом оборудования установленного на ней.
Gр= Gт – G=525 – 319=206 кН.
Определяем координату угp центра тяжести груза (точка Gгр) находящегося на крюке главного подъема по положению крюковой подвески (ее цент располагается по середине между сбегающими ветвями каната с барабана и с верхних блоков) таким образом угp=3075 мм.
На виде сверху (рисунок 3.1) отмечаем центры тяжести всего оборудования и проставляем габаритные размеры.
Определяем координаты центра тяжести порожней тележки и их значения заносим в таблицу 3.1 и на рисунок 3.2.
Определяем положение неприводных колес т.е. базу тележки из условия одинаковой нагрузки на приводные и холостые колеса м:
где у' и у'' – расстояния от равнодействующих веса порожней тележки и груза соответственно до оси приводных колес мм (рисунок 3.2); Gт=Сj – вес порожней тележки Н.
Принимаем базу тележки – 2100 мм и поскольку база изменилась (относительно принятой 2194 мм) менее чем на 5% то уточнений в положении центров тяжести тележки и груза не производим.)
Соответственно от веса груза
Статическая нагрузка на ходовые колеса в груженом положении Н
Как уже отмечалось в методике выполнения курсового проекта при компоновке тележки стремятся к равномерному распределению нагрузок на колеса. Поэтому если разница в статической нагрузке на колеса составляет более 20% изменяют расположение неприводных ходовых колес или верхних блоков. Наиболее существенное перераспределение нагрузок на ходовые колеса может быть осуществлено за счет изменения места расположения верхних блоков опоры которых воспринимают нагрузку от веса груза примерно в ип–1 раз больше чем опоры барабана (ип – кратность полиспаста).
В нашем примере разница в статической нагрузке на колеса составляет около 40%. Поэтому для перераспределения нагрузки производим одновременное смещение механизма подъема и установки верхних блоков на 200 мм в сторону неприводных колес. Так же сместим электродвигатель с тормозом механизма подъема на 100 мм в сторону правого неприводного
колеса так чтобы одна из его опор полностью заходила на правые хребтовые балки. Эти смещения приведут так же к изменению координаты груза угp=107 мм и к увеличению длины рамы тележки на 197 мм со стороны неприводных колес (до размера 2759 мм).
Значения координат центров тяжести оборудования после перекомпановки содержатся в таблице 3.2 и на рисунке 3.3.
Производим перерасчет координат центра тяжести тележки.
где у' и у'' – расстояния от равнодействующих веса порожней тележки и груза соответственно до оси приводных колес мм; Gт=Сj – вес порожней тележки Н.
Принимаем базу тележки – BТ=2300 мм и поскольку база изменилась (относительно принятой 2394 мм) не более 5% то необходимости в уточнении положений центров тяжести тележки и груза нет.
Размеры колеи 1577 мм тележки становятся известны после окончания размещения колес. Принимаем LТ=1500 мм.
В нашем примере разница в статической нагрузке на колеса составляет около 17%. Поэтому перераспределения центров тяжести узлов больше не производим. Окончательно прорабатывают раму тележки при этом обязательно должно быть обеспечено отсутствие задевания канатов за вертикальные листы рамы. Проставляют габариты и установочные размеры определяющие положение механизмов на раме.
Чертёж крановой тележки грузоподъёмностью 15 тонн и высотой подъёма груза 15 метров приведён далее.
Таблица 3.1 – Координаты центров тяжести оборудования тележки.
Редуктор + +муфта=G2
Тормоз+ полумуфта+ +тормозной шкив=G3
Электро-двигатель=G4
Крюковая подвеска=G7
еха-низм пере-движе-ния
тормозной шкив+полумуфта==G9
Трансмиссионные валы с муфтами=G15
Таблица 3.2 – Координаты центров тяжести оборудования тележки (после перерасчета[1]).
Электро-двигатель= G4
Меха-низм пере-движе-ния
Фрагмент4.frw
