Тележка электрического мостового крана грузоподъёмностью 14 т.




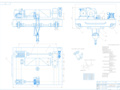
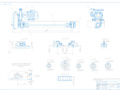
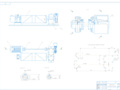
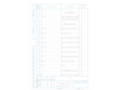
- Добавлен: 25.10.2022
- Размер: 2 MB
- Закачек: 1
Описание
Состав проекта
![]() |
![]() |
![]() ![]() ![]() ![]() |
![]() ![]() |
![]() ![]() ![]() ![]() |
![]() ![]() ![]() ![]() |
![]() ![]() ![]() ![]() |
![]() ![]() ![]() ![]() |
![]() ![]() |
![]() ![]() |
![]() ![]() ![]() ![]() |
![]() ![]() |
![]() ![]() |
![]() ![]() |
![]() ![]() ![]() |
Дополнительная информация
Механизм передвижения спец.dwg

Механизм передвижения тележки
Муфта зубчатая МЗП-1
Редуктор Ц3ВК(ф)-250-12
Механизм подъёма.dwg

Тележка спец.dwg

грузоподъёмностью 14 т.
Тележка электрического мостового
крана грузоподъёмностью 14 т.
Колесо неприводное в сборе
Колесо приводное в сборе
Механизм подъема тележки
Механизм передвижения тележки
Канат ЛК-14 ГОСТ 2688-80
Механизм передвижения.dwg

монтажа механизма передвижения
Рабочие размеры с неуказанным предельным отклонением выполнить по
*Размеры для справок
Механизм передвижения
Механизм подъёма спец.dwg

Тележка.dwg

Передаточное число U=12
Тележка электрического
грузоподъёмностью 14 т.
Техническая характеристика тележки
Скорость передвижения тележки Vт=36 ммин.
Частота вращения n=955 обмин.
Электродвигатель механизма передвижения тележки:
Частота вращения n=700 обмин.
Тормозной момент Мт=100 Нм.
Тормоз механизма передвижения тележки:
Тормозной момент Мт=1500 Нм.
Канат двойной свивки типа ЛК-Р
Диаметр колеса D=200 мм.
Грузоподъемность Q=14 тонн.
Высота подъема груза Н=16 м.
Группа режима работы - 4К.
Продолжительность включения ПВ=25%.
Скорость подъема груза Vп=12 ммин.
Электродвигатель механизма подъема груза:
Редуктор механизма подъема груза:
Передаточное число U=50.
Редуктор механизма передвижения тележки:
Тормоз механизма подъема груза:
Схема навивки каната на барабан
Нагрузки на ходовые колеса
Пояснительная записка.docx
РОССИЙСКОЙ ФЕДЕРАЦИИ
ФЕДЕРАЛЬНОЕ ГОСУДРАСТВЕННОЕ БЮДЖЕТНОЕ ОБРАЗОВАТЕЛЬНОЕ УЧЕРЕЖДЕНИЕ ВЫСШЕГО ОБРАЗОВАНИЯ
по дисциплине: «Грузоподъёмные машины и оборудование»
на тему: «Проектировка тележки электрического мостового крана грузоподъёмностью 14 т.»
Расчёт механизма подъёма2
1. Выбор крюковой подвески2
2. Определение кратности полиспаста2
4. Расчёт верхних блоков2
6. Выбор электродвигателя2
8. Выбор соединительных муфт2
Расчёт механизма передвижения2
1. Выбор кинематической схемы2
2. Определение статической нагрузки на колеса2
4. Определение сопротивления движению тележки2
5. Выбор электродвигателя2
8 Выбор соединительных муфт2
Компонование тележки мостового крана2
1. Определение весов и координат центров тяжестей2
2. Определение нагрузки на ходовые колеса.2
Проверочные расчёты механизмов2
1. Проверка надёжности пуска двигателя механизма подъёма2
2. Проверка электродвигателя механизма передвижения тележки на время разгона2
3. Проверка ходовых колёс на контактные напряжения обода и рельс2
4. Проверка тележки на отсутствие буксования при перемещении2
Список использованной литературы2
Подъемно-транспортные машины важнейшим оборудованием
для механизации работ во всех отраслях народного хозяйства:
в промышленности строительстве на транспорте в сельскохозяйственном производстве. Применяются для перемещения людей на коротких трассах
в вертикальном горизонтальном и наклоном направлениях.
Современные поточные технологические и автоматизированные линии межцеховой и внутрицеховой транспорт погрузочно-разгрузочные операции на складах и перевалочных пунктах органически связаны с применением разнообразных типов подъемно транспортных машин и механизмов обеспечивающих непрерывность и ритмичность производственных процессов. Поэтому применение данного оборудования во многом определяет эффективность современного производства а уровень механизации технического производства степень совершенства и производительность предприятия. При современной интенсивности производства нельзя обеспечить его устойчивый ритм без согласованной и безотказной работы средств транспортирования сырья полуфабрикатов и готовой продукции на всех стадиях обработки и складирования. Одним из разновидностей подъемно транспортных машин является краны мостового типа.
Мостовым краном называется грузоподъемная машина передвигающаяся по рельсам на некотором расстоянии от земли (пола)
и обеспечивающая перемещение груза в трех взаимно перпендикулярных направлениях. Мостовые краны являются одним из наиболее распространенных средств механизации различных производств погрузочно-разгрузочных и складских работ. Перемещаясь по путям расположенным над землей они не занимают полезной площади цеха или склада обеспечивая
в то же время обслуживание практически любой их точки.
Мостовой кран представляет собой жесткую металлическую раму состоящую из двух пролетных и двух концевых балок коробчатого сечения. Вдоль пролетных балок расположены площадки обслуживания. Кран перемещается вдоль цеха или рабочей площадки по подкрановым путям проложенным на подкрановых балках или колоннах. Подъем и перемещение грузов в поперечном направлении осуществляются подвижной тележкой установленной на мосту крана. Тележка состоит из сварной рамы
с механизмами подъема груза и передвижения. Механизмы подъема различных видов кранов принципиально одинаковы и состоят
из электродвигателя тормоза редуктора барабана и полиспаста. Электродвигатель соединен с редуктором при помощи зубчатых муфт
Задание: спроектировать тележку электрического мостового крана грузоподъёмностью 14 т.
Механизм: тележка электрического мостового крана.
Исходные данные приведены в таблице 1.1.
Наименование величины
Вес поднимаемого груза
Скорость подъёма груза
Скорость передвижение тележки
Режим работы крана – 4К. Ток переменный. Все зубчатые передачи перемещены в закрытые корпуса.
Расчёт механизма подъёма
1. Выбор крюковой подвески
Выбор типоразмера крюковой подвески производится по двум условиям:
ее грузоподъемность не должна быть меньше заданной;
режим работы подвески должен соответствовать режиму работы механизма.
По ГОСТ 24.191.08-81 выбираем крюковую крановую подвеску 2-10-406.
2. Определение кратности полиспаста
По выбранной крюковой подвеске определяем кратность полиспаста:
где – число ветвей каната на которых висит груз; – число ветвей каната которые навиваются на барабан.
Кратность полиспаста равна:
Расчет каната сводится к выбору по ГОСТ минимально допустимого диаметра при котором его разрывное усилие не может быть меньше значения расчетного разрывного усилия .
где – статическое натяжение ветви каната Н; – коэффициент запаса прочности .
Статическое натяжение ветви каната определяется по формуле:
где – вес номинального груза и крюковой подвески Н; – число полиспастов на которых висит груз ; – КПД полиспаста .
Вес номинального груза и крюковой подвески рассчитывается по формуле:
где – масса крюковой подвески ; – ускорение свободного падения
Рассчитаем вес номинального груза и крюковой подвески по формуле 2.4:
Тогда статическое натяжение ветви каната согласно формуле 2.3 равняется:
Канат выбирается из условия что разрывное усилие в целом больше произведения максимального статического усилия на коэффициент запаса прочности т.е. неравенство 2.2 примет вид:
Итак выбираем канат ЛК-14-Г-В-1370 ГОСТ 2688-80 диаметр которого маркировочная группа разрывное усилие
4. Расчёт верхних блоков
Минимальные диаметры барабанов блоков и уравнительных блоков огибаемых стальными канатами определяются по формуле:
где – коэффициент выбора диаметров (для барабанов для блоков для уравнительных блоков ).
Диаметр барабана по оси навиваемого каната примем по конструктивным особенностям .
Длина барабана рассчитывается по формуле:
где – длина одного нарезанного участка м; – длина гладкого среднего участка м; – длина одного гладкого участка м.
Длина одного нарезанного участка:
где – шаг навивки каната ; – число рабочих витков для навивки половины рабочей длины каната – число неприкосновенных витков необходимых для разгрузки деталей крепления каната на барабане ; – число витков
для крепления конца барабана .
Тогда длина одного нарезанного участка согласно формуле 2.7 равно:
Длина гладкого среднего участка определяется согласно условиям неравенства:
где – расстояние между осями наружных блоков крюковой подвески (табличное значение ); – минимальное расстояние между осью блоков крюковой подвески и осью барабана – допустимый угол отклонения каната .
Тогда неравенство 2.8 примет вид:
Длина гладкого концевого участка необходимого для закрепления барабана в станке при нарезании канавок:
Тогда по формуле 2.9:
Вернёмся к формуле 2.6 и рассчитаем длину барабана:
Соотношение длины барабана к его диаметру равно
Толщину нарезанной цилиндрической части барабана по дну канавки определяется только по напряжениям сжатия:
где – допускаемое напряжение для Ст3 (барабан)
6. Выбор электродвигателя
Выбор электродвигателей для механизма подъема осуществляется
по расчетной мощности которая должна быть равна соответствующему значению номинальной мощности:
– коэффициент использования электродвигателей в зависимости от типа поднимаемого груза: для крюкового крана – коэффициент запаса определяемый условиями работы при повышенной температуре окружающей среды: для механизмов режимных групп М1 М5; – коэффициент использования электродвигателей при регулировании скорости. Для систем
с параметрическим регулированием скорости значения ;
– коэффициент относительной продолжительности включения; – коэффициент дополнительных пускотормозных нагрузок ; – мощность статической нагрузки при подъеме номинального груза с номинальной скоростью кВт.
Мощность статической нагрузки при подъеме номинального груза
с номинальной скоростью определяется по формуле:
где – предварительное КПД привода
Найдём мощность статической нагрузки согласно формуле 2.12:
Тогда по формуле 2.11 определим расчётную мощность двигателя:
Выбираем двигатель типа 4MTМ 225 М6 его параметры представлены в таблице 2.1:
Характеристики выбранного электродвигателя подъёма
Номинальная мощность двигателя кВт
Частота вращения обмин
Относительная продолжительность включения двигателя
Момент инерции ротора или якоря
Диаметр конца вала мм
Типоразмер редуктора выбираем по расчетному эквивалентному вращающему моменту на валу с учетом режима работы необходимого передаточного числа и частоты вращения быстроходного вала.
Требуемое передаточное число передачи определяется как:
Эквивалентный момент на выходном валу редуктора определяется
где – коэффициент долговечности; – крутящий момент на тихоходном валу редуктора
Максимальный крутящий момент на тихоходном валу редуктора определяет по формуле:
Коэффициент долговечности определяется как произведение коэффициента переменности нагрузки и коэффициента срока службы:
где – коэффициент переменности нагрузки; – коэффициент срока службы.
Коэффициент переменности нагрузки определяется как:
где – коэффициент нагружения для ПВ=25% .
Тогда коэффициент переменности нагрузки равен:
Коэффициент срока службы рассчитывается по формуле:
где – суммарное число циклов контактных напряжений зуба шестерни тихоходной ступени редуктора оно равно числу циклов нагружения
на тихоходном валу редуктора ; – базовое число циклов контактных напряжений его выбирают исходя из характеристик материала колес твердость рабочей поверхности зубьев колес редуктора HB = 260 следовательно принимаем .
Число циклов нагружения на тихоходном валу редуктора определяется по формуле:
где – частота вращения тихоходного вала редуктора – частота вращения барабана; – машинное время работы механизма
Частота вращения барабана рассчитывается по формуле:
Зная значение частоты вращения барабана определим по формуле 2.19 число циклов нагружения на тихоходном валу редуктора:
Коэффициент срока службы согласно формуле 2.18 будет равен:
Тогда коэффициент долговечности по формуле 2.16 будет равен:
Крутящий максимальный момент на тихоходном валу редуктора по формуле 2.15:
Эквивалентный момент на выходном валу редуктора согласно формуле 2.14:
По рассчитанным параметрам выбираем цилиндрический двухступенчатый редуктор типа Ц2-500-50 его характеристики приведены в таблице 2.2:
Основные характеристики выбранного редуктора
Номинальный крутящий момент на выходном валу
Диаметр быстроходного вала мм
Диаметр тихоходного вала мм
8. Выбор соединительных муфт
Муфты выбирают по наибольшему диаметру концов соединяемых валов. Затем проверяют прочность муфты из условия:
где – номинальный передаваемый крутящий момент муфты ;
– расчетный передаваемый крутящий момент муфты .
Расчетный передаваемый крутящий момент муфты определяется
где – коэффициент ответственности (если при поломке муфты произойдет остановка машины то ; произойдет авария машины – ; будут человеческие жертвы - ); – коэффициент условий работы машины (при спокойной работе ; при переменной работе ; при тяжелой работе с ударами и реверсами ); – коэффициент углового смещения ( при угле перекоса валов ;
при ; при ); – крутящий момент при подъёме груза .
Крутящий момент Т определяется при подъеме максимального (номинального) веса груза с постоянной скоростью определяется по формуле:
где – КПД механизма подъёма
Тогда крутящий момент будет равен:
Расчетный передаваемый крутящий момент муфты по формуле 2.22 равняется:
Выбираем зубчатую муфту МЗП-2-50 её характеристики представлены
Характеристики муфты
Проверка условия 2.21:
условие выполняется муфта способна выдержать крутящий момент.
КПД всего механизма:
Для выбора тормоза необходимо определить необходимый тормозной момент:
где – коэффициент запаса торможения при среднем режиме работы
; – статический крутящий момент при торможении создаваемый весом номинального груза на валу на котором установлен тормоз.
Статический крутящий момент при торможении рассчитывается
Необходимый тормозной момент по формуле 2.24 будет равен:
По рассчитанным параметрам и в соответствии с продолжительностью включения выбираем колодочный тормоз с электромагнитным приводом постоянного тока ТКП-400 его технические характеристики приведены в таблице 2.4.
Характеристики тормоза
Электромагнитный постоянного тока
Диаметр тормозного шкива мм
Масса тормозного шкива кг
Момент инерции тормозного шкива
Расчёт механизма передвижения
1. Выбор кинематической схемы
При выборе кинематической схемы механизма передвижения тележки отдают предпочтение схеме имеющей боковой привод с тихоходным трансмиссионным валом и применением вертикальных редукторов типа Ц3вк.
Т.к. номинальная грузоподъемность менее 80 тонн то число ходовых колес тележки принимаем равным четырем.
2. Определение статической нагрузки на колеса
Выбор колес производится по максимальной статической нагрузке которая для тележек определяется по формуле:
где – вес тележки для среднего режима работы при предварительных расчётах принимают ; – число колёс ; – коэффициент распределения нагрузки на колёса .
Тогда максимальная статическая нагрузка на колёса будет равна:
По ОСТ 24.090.44-82 выбираем при нагрузке до 50 кН диаметр ходового колеса . Затем по ОСТ 24.090.09-75 подбираем соответствующую единицу «Колесо в сборе» и определяем основные размеры колеса.
Характеристики выбранного колеса
Максимальная статическая нагрузка кН
Тип рельса с выпуклой головкой
Ширина плоского рельса мм
4. Определение сопротивления движению тележки
Полное сопротивление передвижению тележки в период разгона приведенное к ободу колеса рассчитывается по формуле:
где сопротивление создаваемое силами трения Н;
сопротивление создаваемое уклоном пути Н; сопротивление создаваемое ветром при работе крана в помещении ;
– сопротивления создаваемые силой инерции Н; – сопротивление создаваемое раскачиванием груза на гибкой подвеске Н.
Сопротивление создаваемое силами трения определяется по формуле:
где – коэффициент трения в подшипниках колёс ; – диаметр цапфы вала колеса ; – коэффициент трения качения колёс по рельсу ; – коэффициент дополнительных сопротивлений .
Сопротивление создаваемое уклоном пути рассчитывается по формуле:
где – уклон рельсового пути .
На данном этапе можно определить полное статическое сопротивление:
Сопротивления создаваемые силой инерции определяются согласно:
где – коэффициент учитывающий инерцию вращающих частей механизма ; – масса поступательно движущего объекта кг;
– допускаемое ускорение
Масса поступательно движущего объекта представляет собой разность от массы тележки и подвески:
Тогда сопротивления создаваемые силой инерции согласно формуле 3.6 равны:
Сопротивление создаваемое раскачиванием груза на гибкой подвеске определяется по формуле:
Определим полное сопротивление по формуле 3.2:
5. Выбор электродвигателя
Исходными данными при выборе электродвигателя являются статические и динамические нагрузки приведенные к валу двигателя параметры режима работы время приложения статической и динамических нагрузок. Выбор электродвигателя производится в соответствии
с ОСТ 24.090.85-88 который предусматривает вычисления расчетной мощности необходимой для разгона крана (тележки):
– предварительное КПД механизма ; – кратность среднепускового момента двигателя по отношению к номинальному
По этим параметрам выбираем крановый электродвигатель серии MTКН-311-8 с фазным ротором его характеристики приведены в таблице 3.2.
Характеристики выбранного электродвигателя движения тележки
Момент инерции якоря или ротора
Передачу выбирают исходя из предварительно намеченной кинематической схемы механизма.
Требуемое передаточное число передачи:
где – частота вращения колеса обмин.
Частота вращения колеса определяется согласно формуле:
тогда требуемое передаточное число передачи по формуле 3.10:
Проверим допустимость отклонения:
отклонение в пределах допустимых для двухступенчатого и трёхступенчатого редукторов.
Крутящий момент на тихоходном валу редуктора определяет
Где – максимальный пусковой момент ; – КПД редуктора.
Максимальный пусковой момент равен:
где – номинальный момент движения ; – кратность максимального пускового момента .
Номинальный момент движения определяется:
где – номинальная угловая скорость двигателя
на тихоходном валу редуктора ; – базовое число циклов контактных напряжений его выбирают исходя из характеристик материала колес твердость рабочей поверхности зубьев колес редуктора HB = 250 следовательно принимаем .
где – частота вращения тихоходного вала редуктора ;
– машинное время работы механизма
Зная значение частоты вращения барабана определим по формуле 3.19 число циклов нагружения на тихоходном валу редуктора:
Коэффициент срока службы согласно формуле 3.18 будет равен:
Тогда коэффициент долговечности по формуле 3.16 будет равен:
Номинальный момент движения согласно формуле 3.15 равен:
Максимальный пусковой момент определим по формуле 3.14:
Расчетный крутящий момент на тихоходном валу редуктора согласно формуле 3.13:
По рассчитанным параметрам выбираем цилиндрический двухступенчатый редуктор типа ЦЗВК(ф)-250-125 его характеристики приведены в таблице 3.3:
Фактическая скорость тележки будет равняться:
Согласно правилам ГГТН РФ в данном механизме передвижения должен быть установлен тормоз т.к. тележка предназначенная для работы
в помещении на надземном рельсовом пути.
Расчетный тормозной момент механизма при работе крана в закрытом помещении определяется для движения без груза под уклон в предположении что реборды колес не задевают заголовки рельсов:
где момент создаваемый уклоном пути ; – момент создаваемый инерцией; – момент создаваемый трением.
Момент создаваемый уклоном пути определяется следующим выражением:
где – сопротивление создаваемое уклоном Н.
Сопротивление создаваемое уклоном определяется по формуле:
Тогда момент создаваемый уклоном пути согласно формуле 3.21 будет равен:
Момент создаваемый инерцией равен:
где – сопротивление создаваемое силами инерции Н.
Сопротивление создаваемое силами инерции рассчитывается
Тогда момент создаваемый инерций согласно формуле 3.23 будет равен:
Момент создаваемый трением определяется формулой:
где – сопротивление сил трения Н.
Сопротивление сил трения рассчитывается по формуле:
где – коэффициент учитывающий сопротивление движению тележки при троллейном токопроводе.
Тогда сопротивление сил трения будет равно:
Момент создаваемый трением по формуле 3.25:
Расчетный тормозной момент механизма согласно формуле 3.20:
По рассчитанным параметрам выбираем колодочный тормоз
с электромагнитным приводом переменного тока ТКГ-160 характеристики которого представлены в таблице 3.4
Электромагнитный переменного тока
8 Выбор соединительных муфт
при ; при ); – крутящий момент при перемещении тележки .
Крутящий момент Т определяется при перемещении тележки
с постоянной скоростью определяется по формуле:
Расчётный крутящий момент согласно формуле 3.29 будет равен:
Момент действующий на быстроходный вал:
Принимаем следующие муфты:
для тихоходного вала редуктора: МЗП-2-50;
для быстроходного вала редуктора: МЗП-1.
Уст. на быстроходный вал
Проверка условия 3.28:
для тихоходного вала редуктора:
условие выполняется муфта способна выдержать крутящий момент;
для быстроходного вала редуктора:
Компонование тележки мостового крана
Расположение механизмов на раме тележки должно обеспечить
ее минимальные габариты массу и равномерную нагрузку на ходовые колеса при номинальном грузе на крюке.
1. Определение весов и координат центров тяжестей
Значения масс весов и координат центров тяжестей сведены в таблицу 4.1 (вес тормоза привода передвижения промежуточных валов и муфт невелик по сравнению с весом рамы тележки и остального оборудования поэтому
их можно в расчет не принимать).
Механизм подъема груза
Механизм передвижения тележки
Определяем координаты центра тяжести порожней тележки
по формулам в них веса отдельных сборочных единиц;
координаты точек их приложения:
Определяем положение неприводных колес т.е. базу тележки из условия одинаковой нагрузки на приводные и неприводные колеса:
Примечание: здесь вес тележки; – вес груза; расстояние от равнодействующей веса порожней тележки и груза соответственно до оси приводных колес
Окончательно принимаем:
2. Определение нагрузки на ходовые колеса.
Определяем нагрузку на ходовые колеса тележки от веса порожней тележки:
Нагрузка на ходовые колеса от веса груза:
Суммарные статические нагрузки на ходовые колеса:
Максимальная разница в нагрузках на колеса:
т.к. разница в статической нагрузке на колеса составляет менее 15% изменение расположения колес не требуется.
Проверочные расчёты механизмов
1. Проверка надёжности пуска двигателя механизма подъёма
Двигатель должен разгонять механизм за достаточно короткое время иначе уменьшится производительность крана. Но с другой стороны если оно будет слишком мало то разгон будет сопровождаться большим ускорением что скажется на прочности элементов устойчивости груза и т.д. Время разгона механизма принимают равным от 1 до 2 секунд.
Для механизма подъема груза наибольшее время разгона получается при разгоне на подъем вычисляемое по формуле:
где – момент инерции при разгоне всех вращающихся частей механизма приведенный к валу двигателя; среднепусковой момент двигателя;
момент статических сопротивлений приведенный к валу двигателя.
Момент инерции при разгоне всех вращающихся частей механизма определяется по формуле:
где момент инерции вращающихся масс расположенных на первом валу (он равен сумме моментов инерции ротора двигателя муфт и тормозного шкива) – коэффициент учета инерции вращающихся масс расположенных на втором третьем и последующих валах механизма .
Момент инерции вращающихся масс рассчитывается по формуле:
где – момент инерции ротора (см. таблицу 2.1); – момент инерции муфты (см. таблицу 2.3); – момент инерции тормоза (см. таблицу 2.4).
Тогда момент инерции вращающихся масс будет равен:
Тогда момент инерции при разгоне всех вращающихся частей механизма по формуле 5.2 будет равен:
Среднепусковой момент двигателя определяется по формуле:
где – номинальный момент двигателя ; – кратность среднепускового момента двигателя .
Номинальный момент двигателя определяется формулой:
Тогда среднепусковой момент двигателя согласно формуле 5.4 равен:
Момент статических сопротивлений рассчитывается по формуле:
Тогда фактическое время разгона согласно формуле 5.1 будет равно:
Полученное значение находится в диапазоне рекомендуемых значений времени разгона (12 с).
Среднее ускорение груза при таком времени разгона равно:
Это значение не превышает рекомендуемое (020 мс2) для кранов работающих в механосборочных цехах.
2. Проверка электродвигателя механизма передвижения тележки
Для механизма передвижения тележки наибольшее время разгона получается при разгоне тележки вычисляемое по формуле:
где – момент инерции при разгоне всех вращающихся частей механизма приведенный к валу двигателя; среднепусковой момент двигателя; момент статических сопротивлений приведенный к валу двигателя.
где – момент инерции ротора (см. таблицу 3.2); – момент инерции муфты (см. таблицу 3.5); – момент инерции тормоза (см. таблицу 3.6).
Полученное значение находится в диапазоне рекомендуемых значений времени разгона; следовательно принятый электродвигатель обеспечит необходимую интенсивность работы.
Среднее ускорение тележки при таком времени разгона равно:
3. Проверка ходовых колёс на контактные напряжения обода и рельс
Определяются напряжения в контакте обода колеса с головкой рельса
где – коэффициент зависящий от отношения радиуса закругления головки рельса к диаметру колеса ; – коэффициент учитывающий влияние касательной нагрузки на напряжения в контакте ;
– коэффициент динамичности пары колесо-рельс
Тогда напряжения в контакте обода колеса с головкой рельса будет равно:
Контактные напряжения не должны превышать допускаемые
при приведенном за срок службы числа оборотов колеса N:
где – допускаемое напряжение при ; – полное число оборотов колеса за срок службы.
Приведённое и полное число оборотов колеса за срок службы определяются соответственно по формулам:
где – коэффициент приведённого числа оборотов колеса; – усредненная скорость движения.
Усредненная скорость движения определяется по формуле:
где – коэффициент зависящий от отношения времени неустановившегося движения (суммарное время торможения и разгона) к полному времени передвижения .
Найдём значение усреднённой скорость по формуле 5.20:
Полное число оборотов колеса за срок службы при машинном времени определим по формуле 5.19:
Значение коэффициента определяется зависимостью отношения минимальной нагрузки на колесо к максимальной:
при отсутствии исходных данных по нагрузке колеса можно принять
в зависимости от отношения минимальной нагрузки на колеса
к максимальной тогда .
Воспользуемся формулой 5.18 и определим приведённое число оборотов колеса за срок службы:
тогда по формуле 5.17:
Проверим условие 5.16:
условие прочности выполняется.
4. Проверка тележки на отсутствие буксования при перемещении
В период пуска механизма передвижения приводные колеса взаимодействуя с рельсами приводят в движение тележку. Для получения нормальной работы при разгоне и торможении необходимо чтобы приводные колеса перекатывались по рельсам без скольжения (пробуксовки). Поэтому при расчете механизмов передвижения нужно выдержать определенное соотношение между силами сцепления ходовых колес с рельсами и движущей силой приложенной к ободьям этих колес. Расчетным случаем является работа без груза когда усилие на приводные колеса будет уменьшенным
а следовательно уменьшена будет и сила сцепления колес с рельсами. Работа в период пуска без проскальзывания приводных ходовых колес обеспечивается при соблюдении неравенства:
где – коэффициент запаса сцепления ; – сила сцепления колес с рельсами Н; – максимальная сила статического сопротивления Н; – сопротивление от сил инерции массы тележки.
Сила сцепления колес с рельсами рассчитывается по формуле:
где – сила сцепления колес с рельсами Н; – коэффициент сцепления колеса с рельсом при работе крана в помещении .
Сила сцепления колес с рельсами определяется формулой:
где – вес тележки приходящийся на приводные колеса Н; – число приводных колёс и общее число колёс соответственно.
Тогда согласно формуле 5.24 сила сцепления колес с рельсами равна:
Максимальная сила статического сопротивления находится по формуле:
Сопротивление от сил инерции массы тележки рассчитывается
Проверим выполнение условие 5.23:
условие выполняется.
Допустимое ускорение тележки вычисляется по формуле:
было определено по формуле 5.14 .
Для проверки буксования при начале движения тележки должно выполняться условие:
условие отсутствия буксования соблюдается.
Допустимое замедление тележки вычисляется по формуле:
можно принять равным .
Для проверки отсутствия юза при торможении тележки должно выполняться условие:
условие отсутствия юза соблюдается значит при торможении
тележки проскальзывания колес относительно рельсов будет отсутствовать.
В данной работе была рассчитана и спроектирована тележка электрического мостового крана грузоподъёмностью 14 т.
Как показали проектные и расчетные данные выбранные узлы
и механизмы тележки электрического мостового крана отвечают правилам
и нормам Ростехнадзора и обеспечивают выполнение основных положений технического задания.
Конструкция тележки спроектирована с учетом специфики эксплуатации механизма и требований предъявляемых к прочности надежности и долговечности данных изделий.
Следовательно можно сделать вывод: спроектированная тележка электрического мостового крана отвечает необходимым критериям работоспособности и обеспечивает выполнение требований технического задания.
Список использованной литературы
Проектирование механизмов мостовых кранов. Наварский Ю.В. Жегульский В.П. учебное пособие Екатеринбург: УГТУ-УПИ 2009
Александров М.П. Подъемнотранспортные машины: Учеб. для машиностроит. спец. вузов. 6е изд. перераб. М.: Высшая школа 1985.
Курсовое проектирование грузоподъемных машин. Руденко Н.Ф. Александров М.П. и Лысяков А.Г. Изд. 3е перераб. и доп. М.: Машиностроение 1971.
Курсовое проектирование грузоподъемных машин: Учеб. пособие для студентов машиностроит. спец. вузов С.А. Казак В.Е. Дусье Е.С. Кузнецов и др.; под ред. С.А. Казака. М.: Высшая школа 1989.
Курсовое проектирование деталей машин. С.А. Чернавский К.Н. Боков И.М. Чернин и др. 2е изд. перераб. и доп. М.: Машиностроение 1988.
Металлургические подъемнотранспортные машины: Методические указания к курсовому проектированию Ю.В. Наварский. Екатеринбург: УГТУ 2001.
Подъемнотранспортные машины. Атлас конструкций под ред. М.П. Александрова и Д.Н. Решетова. М. 1973.
Справочник конструктора-машиностроителя. В.И. Анурьев – в трех томах – 5-е изд. перераб. и доп. – М.: Машиностроение 1978.