Технология монтажа движительного комплекса судна


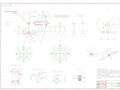
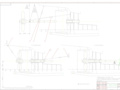
- Добавлен: 25.10.2022
- Размер: 2 MB
- Закачек: 2
Получить бесплатный доступ добавив свой материал или получить скидку оплатив сразу нескольких материалов
Подписаться на ежедневные обновления каталога:
Описание
Технология монтажа движительного комплекса судна
Состав проекта
![]() |
![]() ![]() ![]() ![]() |
![]() ![]() ![]() ![]() |
![]() ![]() ![]() |
Дополнительная информация
Контент чертежей
Дейдвуд1.dwg

Труба оптическая ППС-11
Схема пробивки оптической оси
Схема погрузки гр. в.2.dwg

места сварки зачистить.
Диплом.doc
2.Современные способы монтажа движительного комплекса. 10
3. Общие сведения о движительном комплексе. 20
4.Современные способы монтажа движительного комплекса.22
Разработка технологии монтажа движительного комплекса.32
1.Общие технические требования.33
2.Технологический процесс. 36
2.1. Пробивка оси линии вала под установку яблока ахтерштевня. -
2.2. Установка яблока ахтерштевня.37
2.3. Монтаж подшипника.44
2.4. Установка вварыша и дейдвудной трубы.45
2.5. Подготовка поверхностей приготовление полимерного материала
заполнение монтажного зазора.49
2.6. Монтаж гребного вала с ВРШ.53
2.7. Монтаж полумуфты.55
2.8. Проверка параметров центровки гребной вал-редуктор.59
2.9. Проверка зазоров между насадкой и лопастями ВРШ.61
2.10. Последовательность монтажа МИШ.62
2.10.1. Последовательность монтажа маслораспределительной коробки. -
2.10.2.Соединение внутренних подвижных маслопроводов.63
2.10.3. Регулировка шага во время сборки. -
2.11. Монтаж дейдвудного сальника.64
2.12. Монтаж тормоза.65
2.13. Проверка центровки валопровода на плаву.66
2.14. Монтаж кожуха. -
3.Средства технологического оснащения применяемые при монтаже. 68
Специальная часть. 70
1.Разработка технолого-нормировочной карты монтажа
движительного комплекса траулера. -
2. Расчёт массы компонентов для приготовления полимерного
материала заливаемого в монтажные зазоры.75
3. Расчёт технических параметров напрессовки фланцевой
4. Расчёт влияния температуры на размеры капролоновых
подшипников при их монтаже.82
5. Обоснование отказа от имитации недостающего оборудования.83
Технико-экономические обоснование проекта.86
1.Расчет себестоимости монтажа по статьям калькуляции.87
2. Расчёт сравнительной экономической эффективности
разработанного технологического процесса.93
3.Описание участка монтажа основных элементов валопровода.96
4. Разработка мероприятий по обеспечению качества монтажа.98
Требования техники безопасности при выполнении работ
по монтажу движительного комплекса. 103
1. Техника безопасности при выполнении работ по монтажу
движительного комплекса. 104
1.1. Основные положения. -
1.2. Техника безопасности при работах с применением растворителей. 109
1.3. Техника безопасности при гидравлических испытаниях
напрессовке и спрессовке. 111
1.4. Техника безопасности при работе с механизированным инструментом. 112
1.5. Техника безопасности при работах по погрузке выгрузке перемещению
сборочных единиц и деталей движительного комплекса. 113
2. Противопожарные мероприятия при монтаже
движительного комплекса. 115
3. Охрана окружающей среды. 116
В настоящее время в России на предприятиях ВПК идет интенсивный переход на выпуск продукции гражданского назначения. Это обусловлено тем что оборонная промышленность испытала тяжелый кризис в связи с переходом страны к рыночной экономике. И это не могло не отразиться на жизнедеятельности предприятия. Госзаказ был значительно сокращен а оставшиеся работы оплачивались с большим опозданием. Невозможность регулярных выплат работникам предприятия потеря квалифицированных кадров моральный и физический износ основных средств – это лишь часть тех трудностей которые потребовали поиска других заказов помимо государственного.
Учитывая важность включения России в систему международного разделения труда необходима комплексная стратегия формирования гибкого национального экономического организма эффективно встроенного в систему мирохозяйственных связей.
ФГУП «МП «Звездочка» успешно развивает выпуск продукции по экспортным заказам различного назначения. Зарубежные заказы требуют выполнение работ в жестко установленные сроки и в соответствии с международными стандартами качества. Для успешного выполнения этих заказов требуется проведение следующих мероприятий:
-внедрение современных автоматизированных систем планирования проектирования и контроля;
-повышение квалификации рабочих и инженерно-технических работников;
-реконструкция и техперевооружение предприятия.
В 1998 году ФГУП «МП «Звездочка» в сотрудничестве с норвежской компанией “Kvaerner Kimek” по программе «Возрождение рыболовного флота Архангельского региона» построен головной траулер проекта 50010 а в 2001 году спущен на воду и отбуксирован в Норвегию для установки рыболовного оборудования второй корпус траулера который в настоящее время также эксплуатируется. Серия строящихся судов данного проекта является лучшей в своем классе из когда-либо производившихся в России.
Цель дипломного проекта – разработка технологии монтажа движительного комплекса в соответствии с международными стандартами качества при одновременном сокращении трудоемкости и сроков постройки.
В общей части дипломного проекта изложены основные данные по проекту; рассмотрены современные способы монтажа; описаны конструктивные особенности движительного комплекса и принципы работы его составляющих.
Технологическая часть содержит принципиальную технологию монтажа движительного комплекса с учетом изменений принятых на основании анализа постройки головного судна серии а также дополнена инструкциями по монтажу основных элементов системы ВРШ.
В специальной части произведен расчет необходимой массы компонентов для приготовления полимерного материала под заливку монтажных зазоров при монтаже дейдвудного устройства и вварыша расчет параметров напрессовки фланцевой полумуфты на вал расчет температуры охлаждения капролонового подшипника для скользящей посадки в дейдвудную трубу а также произведена разработка технолого-нормировочной карты монтажа и приведено обоснование отказа от имитации недостающего оборудования при монтаже дейдвудного устройства.
В экономической части произведена оценка экономической эффективности разработанного технологического процесса на основании проведенного расчета стоимости монтажа движительного комплекса по статьям калькуляции обозначены основные направления по обеспечению и повышению качества производимых работ.
В разделе «Охрана труда» рассмотрены основные требования техники безопасности пожарной безопасности и охраны окружающей среды при монтаже движительного комплекса.
Сокращения используемые в пояснительной записке:
Отдел Главного Технолога
Конструкторский Отдел
Отдел Контроля Качества
Отдел Главного Сварщика
Бюро технологической подготовки производства
Технолого-нормировочная карта
Доково - опорное устройство
Дизель - редукторный агрегат
Винт регулируемого шага
1. Основные данные по проекту.
Тип судна : траулер.
-классификационное общество: Регистр РФ
-класс : КМ А3Л3рыболовный
(макс.длительная) : 1000 кВт.
(норм. экспл.) : 780 кВт.
-число оборотов двигателя : 1000 (обмин)
Скорость судна : 112 узлов
-диаметр гребного винта : 2700 мм
-тип ступицыдиаметр : D650 мм
-количество лопастей : 4 шт.
-число оборотов гребного винта : 1625 (обмин)
-направление вращения : против часовой стрелки
Винт вращается в фиксированной направляющей насадке.
-внешний диаметр корманос : 220210 мм
-корм. оконечность гребного вала : сплошной фланец
-нос. оконечность гребного вала : фланцевая муфта
-бронзовая втулка в корме
внешний диаметр : 250 мм
-бронзовая втулка в носу
Маслораспределительная коробка
-Место установки : носовая оконечность редуктора.
2. Современные способы монтажа движительного комплекса.
Судовой движительный комплекс - один из жизненно важных узлов СЭУ. Его отказ может повлечь за собой частичную или полную потерю судном хода и создать угрозу безопасности судна особенно при штормовой погоде. Поэтому к судовому движительному комплексу предъявляются очень жесткие требования в отношении надежности которая определяется не только его конструкцией но и во многом закладывается на этапе монтажа. По этой причине весьма важным является разработка грамотной технологии монтажа.
Задачей технологии как науки является выявление закономерностей позволяющих использовать на практике наиболее эффективные и экономичные производственные процессы требующие наименьших затрат времени и материальных ресурсов. Рациональная технология монтажа судового механического оборудования предусматривает решение целого комплекса вопросов включающего в частности:
-создание технологичных конструкций соединения механизмов и устройств с фундаментами;
-расчетное определение конструктивно-технологических параметров элементов соединения механического оборудования с фундаментами;
-разработку прогрессивной технологии непосредственно монтажа;
-выявление эффективных средств выполнения и контроля основных и вспомогательных операций механомонтажных работ.
Только при выполнении всех указанных условий может быть сформирован высокоэкономичный производственный процесс.
Изменение условий выполнения монтажных операций путем перенесения их из судовых помещений в цехи верфи и параллельное осуществление корпусных и монтажных работ делают особо актуальной задачу максимального сокращения трудоемкости механомонтажных операций которая зависит от количества соединений механизмов с фундаментами от размеров и технологичности составляющих их элементов от принятой технологии монтажа и применяемых технических средств.
Имеется широкая номенклатура технических средств выполнения и контроля операций механомонтажных работ. Средства механизации и контроля применяемые на разных предприятиях различаются техническими характеристиками; большая масса и недостаточная точность и универсальность ограничивают возможности их применения. Рекомендации по рациональному использованию существующих и заново разрабатываемых технических средств а также по применению универсальных унифицированных технических средств практически отсутствуют. Ограничение номенклатуры технических средств путем их унификации и универсализации снижения массы и повышения точности должно привести к сокращению затрат на их проектирование и изготовление и повысить производительность труда.
В сложившихся условиях механомонтажные работы относят к категории тяжелых или особо тяжелых. Между тем расширение номенклатуры судового механического оборудования рост энерговооруженности судов а также напряженности современных машин и механизмов приводит к увеличению объема механомонтажных работ и к повышению их удельного веса в общей трудоемкости постройки судна. В то же время растут требования к эффективности качеству монтажных работ и культуре производства в целом.
Основным узлом движительного комплекса является валопровод. Он испытывает комплексное воздействие напряжений от различных нагрузок: касательных от крутящего момента главного двигателя и от крутильных колебаний; нормальных в результате деформаций корпуса и прогиба валов от их массы; сжатия; от осевой силы упора движителя.
Применявшаяся ранее прямолинейная укладка валов как показали исследования не удовлетворяла условиям правильного распределения нагрузок на подшипники. Установка валопровода с монтажным изгибом учитывающая все факторы загрузки подшипников повышает работоспособность всей энергетической установки в целом.
До начала установки опор гребных валов т. е. кронштейнов мортир яблока ахтерштевня приварной дейдвудной трубы вварыша (приварыша) должны быть выполнены следующие работы:
-закончены основные сборочно-сварочные работы обеспечивающие общую прочность корпуса (блока) судна в районе расположения валопровода и МО;
-выправлен и испытан на водонепроницаемость корпус и корпусные цистерны в районе расположения валопровода и МО (места корпуса где ввариваются опоры гребного вала или их элементы испытываются после приварки опор);
-освобождена от упоров неводоизмещающая часть кормы проверено и зафиксировано актом положение корпуса (блока) на стапеле;
-нанесены точки теоретической оси валопровода по плазовым координатам; при установленных фундаментах под базовый механизм кормовую опору или неподвижную насадку гребного винта. Контрольные точки оси валопровода должны наноситься с учетом их фактического положения.
В районе мест расположения кронштейнов и дейдвудного устройства (по всей высоте судна) должны быть погружены все основные судовые механизмы и устройства масса которых более 2 % массы ГД а также имитирующие грузы на места расположения отсутствующих механизмов и балласта. Допускается не производить имитации если контрольные измерения формы и расположения посадочных поясов кронштейнов мортир яблока ахтерштевня и вварыша (приварыша) при погрузке имитирующего груза подтверждают сохранение технологических параметров в допускаемых пределах или позволяют предупредить их изменения.
Готовность судна к монтажу валопровода определяется на основании перечня закрытых построечных удостоверений помещений корпусных конструкций и цистерн в районе расположения валопровода и ГД а также перечня погруженных на судно механизмов устройств и имитирующего груза с указанием их массы. При изменении объема законченных работ по формированию корпуса (блока) массы и количества погруженных тяжелых механизмов и устройств до начала монтажа валопровода должен быть представлен протокол согласования этих изменений с проектантом Регистром и заказчиком.[5].
В период монтажа валопровода на стапеле корпус судна должен находиться на одной стапельной позиции менять которую допускается после монтажа подшипников и дейдвудного устройства до центровки валопровода и крепления опорных и упорных подшипников. Изменение положения корпуса судна зафиксированное в начале работы по высоте относительно базовой плоскости в районе расположения валопровода и ГД на одной стапельной позиции не должно превышать ±3 мм.
Положение корпуса судна (блока) на стапеле (в доке) к началу монтажа валопровода а также в процессе выполнения работ проверяется как правило не реже одного раза в сутки и контролируется по записям в стапельном журнале.
Кронштейны мортиры приварные дейдвудные трубы и яблоко ахтерштевня поступающие на установку без расточки на стапеле должны быть полностью собраны испытаны и окончательно обработаны.
Расточка по линии вала. Расточку кронштейнов мортир дейдвудных труб вварышей и яблока ахтерштевня выполняют переносными расточными станками типа ЛР. Наибольшее применение получили станки ЛР-203 и ЛР-248.
В судостроительной промышленности разработано большое количество переносных станков расточных приспособлений и устройств для расточки элементов корпуса по линии вала. Расточку элементов корпуса производят в два этапа. При черновой расточке снимают металл оставляя припуск 2—3 мм на последующие проходы. При чистовой расточке за каждый проход снимают не более 03—05 мм. Режимы резания различны. Черновая расточка — скорость резания 15—20 ммин подача до 12 ммоб на втором этапе скорость резания — 80 ммин подача до 1 ммоб.
К точности расточки предъявляются следующие требования: овальность не более 008 ммм конусообразность не более 005 мм на длине растачиваемого пояска; несоосность растачиваемых поясков до 002 L (L — длина дейдвудной трубы м); неперпендикулярность подрезки торцов не более 005 ммм. Шероховатость обработанной поверхности должна быть не выше Rz= 20 мкм.
После выполнения каждого этапа проверяют точность расточки — совпадение осей расточки с контрольными окружностями и вносят корректировку. По окончании расточки снимают замеры расточенных поясков заносят данные в формуляр который передают в механический цех для окончательной обработки дейдвудной трубы и втулок кронштейнов.
Установка опор гребного вала. Так как расточка отверстий на построечном месте связана с высокой трудоемкостью по установке переносных расточных станков а качество расточки ниже чем при работе на стационарном оборудовании разработан ряд методов установки опор окончательно обработанных в цехе. Погрешности корпусных работ компенсируют за счет заполнения установочных зазоров полимерными материалами. К числу таких способов относится установка дейдвудной трубы на пластмассе К 153.
Яблоко ахтерштевня 1 (рис.2) и вварыш ахтерштевневой переборки 9 растачивают на 5—7 мм больше диаметров посадочных поясов ориентируют на оси валопровода и приваривают. Дейдвудную трубу 8 устанавливают с помощью регулировочных винтов 10 с центровкой по оси валопровода оптическим способом. Зазоры уплотняют резиновым шнуром 5. Пластмассу 6 заливают под давлением через отверстие 2 до появления выхода пластмассы из отверстия 7. Кормовой конец трубы крепят к торцу яблока ахтерштевня гайкой 4 с уплотнением прокладкой 3.
Рис. 2. Установка дейдвудной трубы на пластмассе
Для измерения и изготовления пригоночных прокладок (клиньев) для монтажа например тормоза или подшипников применяют специальные приспособления.
Так на некоторых заводах для снятия размеров клина применяют приспособление (рис. 3.а) состоящее из пластинки с винтами закладываемой между лапой подшипника и фундаментом. Винты подворачивают до соприкосновения с лапой подшипника и устанавливают размер а с наружной стороны подшипника. Затем пластинку закладывают в кондуктор (рис.3.б) и укладывают на нее заготовку клина обработанной поверхностью вниз. Верхнюю поверхность шлифуют до получения размера а.
После подгонки клиньев через отверстия в лапах подшипников сверлят отверстия под фундаментные болты в клиньях и в полке фундамента. Эти отверстия сверлят диаметром на 05 мм. меньше чем указано в чертеже и подшипники временно крепят на клиньях маломерными болтами. Затем еще раз проверяют центровку валопровода и (при удовлетворительных результатах) развертывают отверстия под фундаментные болты после чего окончательно закрепляют подшипники на фундаменте. После закрепления всех опорных подшипников и установки их крышек производят окончательную проверку изломов и смещений и предъявляют монтаж валопровода ОКК.[21].
Рис.3. Приспособление для снятия размеров изготовления клиньев:
а - снятие размеров; б – изготовление клина. 1 - пластинка; 2 - винты;
–лапа подшипника; 4 - фундамент; 5 - заготовка клина; 6 - кондуктор.
Центровка валопроводов. Центровка заключается в совмещении осей отдельных валов с осью валопровода. При расчете ее технологических параметров следует учитывать все многообразие факторов влияющих на правильную эксплуатацию валопровода. Корпус судна не остается статичным как в процессе постройки так и в процессе эксплуатации. В результате возникающих изменений происходит перераспределение нагрузок на опоры валопровода. Влияние общего изгиба корпуса оценивают по напряжениям в валах и нагрузкам на подшипники возникающим в валопроводе.
В зависимости от способа центровки производят определение технологических параметров которыми являются: изломы и смещения измеренные на фланцах валов; расчетные нагрузки на подшипники; соосность подшипников валопровода.
Окончательная центровка валопровода проводится на плаву судна водоизмещение которого должно быть не менее 85 % от водоизмещения порожнем при погруженных основных тяжеловесных механизмах массой более 1% общей массы механизмов и устройств в районе машинного одним из следующих согласованных с заказчиком способов: по нагрузкам на подшипниках по изломам и смещениям в соединениях валов оптическим способом. при погруженных основных тяжеловесных механизмах массой более 1% общей массы механизмов и устройств в районе машинного отделения.
Допускается по согласованию с заказчиком меньшее водоизмещение если расчеты упругих деформаций корпуса или контрольные измерения технологических параметров центровки выполненные не менее чем на трех судах серии подтверждают такую возможность.
Центровка валопровода на стапеле (в доке) допускается на судах водоизмещением менее 80 т или длиной менее 20 м а также в случаях согласованных с Регистром и заказчиком когда контрольные измерения технологических параметров центровки валопровода подтверждают сохранение их значений в допускаемых пределах после спуска судна на воду. Положение корпуса судна на стапеле в процессе приемки центровки валопровода контролируется по записям в стапельном журнале. Приемка центровки валопровода в плавучих доках не допускается.
Готовность судна к приемке центровки валопровода проверяется на основании перечня погруженных на судно механизмов устройств и масс имитирующего груза. Положение корпуса судна на плаву в процессе приемки центровки валопровода контролируется по действительному водоизмещению судна.
Центровка валопроводов по изломам и смещениям. Этот способ центровки может быть применен только для жестких валов. Если прогиб конца вала от собственного веса превышает 03 мм то устанавливают дополнительные монтажные подшипники или применяют другой способ центровки.
Контроль изломов и смещений осуществляют по линейке и щупу или с помощью парных стрел с индикаторами. Величину смещения и излома определяют в горизонтальной и вертикальной плоскостях для чего снимают по два замера в каждой плоскости отдельно для излома и для смещения. Задачей центровки является регулировка положения опорных подшипников до тех пор пока фактические изломы и смещения не войдут в пределы допускаемых которые определяют по расчетным перемещениям подшипников.
При центровке валопровода по изломам и смещениям в соединениях валов должны быть обеспечены расчетные значения изломов и смещений с отклонениями не превышающими допускаемые пределы их изменений.
При приемке центровки валопровода выполненной оптическим способом положение подшипников относительно теоретической оси валопровода (оси ГД) должно соответствовать расчетным ординатам с отклонениями не превышающими допускаемые пределы их изменений. Перекос осей подшипников относительно оси отсчета не должен превосходить 06 ммм. Контрольные измерения технологических параметров центровки валопровода производятся после установки выравнивающих подкладок в узлах крепления подшипников к фундаментам.[5].
Применение лазерной установки для центровки.
Одним из путей снижения трудоемкости при одновременном повышении качества монтажа является применение современных технических средств. Так для центровки возможно применение лазерной системы.
Появление промышленных лазеров привело к созданию лазерно-оптической системы для определения теоретической оси валопровода а также для центровки главных двигателей и подшипников гребного вала. Лазерно-оптическая система обеспечивает рост производительности труда на операциях по определению теоретической оси валопровода и его центровки в 18 раза.
В состав оборудования лазерно-оптической системы входят оптический генератор фотоэлектрические мишени приборы блока индикации. Оптический генератор устанавливают за кормой судна на специальном кронштейне а во все размечаемые места — фотоэлектрические мишени. В процессе работы фотоэлектрические мишени последовательно устанавливают по энергетической оси луча излучателя с оценкой качества центровки в вертикальной и горизонтальной плоскостях по показаниям приборов блока индикации.
Одной из таких систем является система DIGILASER которая структурно состоит из лазера- источника и детектора соединенного с блоком дисплея.
Измерительная система DIGILASER:
-выверка валопроводов;
-выверка положения подшипников качения;
-выверка соосности отверстий;
-плоскосность фундаментов;
-прямолинейность направляющих;
-параллельность направляющих;
Лазер-источник представляет собой лазер диодного типа Класса 2 (мощность менее 05 мВт) видимого частотного диапазона (длина волны 67 мм). Питание от АС адаптера или от аккумуляторной батареи.
Рис.4. Лазер излучатель FL 11 с адаптером.
Двухосевой детектор PSD (Position sensitive detector) имеет фотоэлектрический чувствительный элемент. Система фильтров пропускает только излучение от лазера -источника. Электрический сигнал зависит от положения пятна лазерного луча на его поверхности. Разрешающая способность - не хуже 1 мкм. Сигнал обрабатывается блоком дисплея. Питание от аккумуляторной батареи встроенной в блок дисплея.
Рис.5 . Детектор FD 11 с блоком дисплея.
Мощность источника и чувствительность детектора позволяют производить измерения на расстоянии до 100м (в стандартном исполнении 50м) с точностью 001 мм (0001 мм при использовании компьютера).
Блок дисплея имеет два дисплея - X и Y с разрешением 001 мм и две регулировочных ручки для электрического обнуления. Каналы X и Y регулируются независимо друг от друга.
Измерения с помощью DIGILASER
При выполнении измерений с помощью системы DIGILASER в качестве системы отсчета используется линия лазерного луча или плоскость образованная при повороте лазерного луча. Соответственно для образования опорной линии необходимо выбрать две нулевые точки а для образования опорной плоскости - три.
Лазер-источник устанавливается неподвижно на детали (поверхности) машины (например на одной из подшипниковых опор) относительно которой производится выверка положения остальных деталей (поверхностей) или вне выверяемой машины но в точке которая не находится в относительном движении с выверяемой машиной. Первая нулевая точка образуется электрическим обнулением показаний на дисплее с помощью регулировочных ручек. Таким образом электрический центр детектора помещается в точку на его поверхности через которую фактически проходит луч.
DeltaFixtureTM-универсальное крепление для проведения измерений на внутренних диаметрах отверстий. При использовании с прибором Digilaser оно представляет собой мощную измерительную систему позволяющую пользователю производить сложные точные измерения при простом и быстром монтаже на объекте измерения. Комплект крепления выполнен из анодированного алюминия и состоит из четырех центральных оснований и 12 наборов плеч для применения на диаметрах 150-550 мм.
Рис.6 . Крепление DeltaFixture.
Основание 2. Регулируемые плечи 3. Направляющие валики
Винты крепления детектора 5. Винты регулируемых плеч 6. Винт эксцентрика
Винты крепления лазера 8. Скобы крепления лазера.
Крепление ориентируется при установке в осевом направлении с помощью двух направляющих валиков и в горизонтальном направлении с помощью уровня. Скользящий эксцентрик установленный на одном из регулируемых выдвижных плеч фиксирует крепление внутри кольца подшипника. Крепление легко адаптируется к каждому новому диаметру с помощью выдвижных плеч. DeltaFixture разработано как для монтажа детектора FD11 так и для монтажа лазера передатчика FL11. Сборка с лазером-источником может быть установлена или внутри опорного диаметра с помощью направляющих валиков или снаружи на магнитных призмах. Таким образом пользователь получает возможность выбора в различных случаях применения. Вся система поставляется в прочном переносном кейсе что делает ее законченной профессиональной системой для выполнения измерений на профессиональном уровне.
При использовании DeltaFixture для измерения прямолинейности необходимо знать отклонения диаметра и овальность данного кольца подшипника для того чтобы впоследствии внести необходимые поправки в результаты измерений. Измерения на разъемных подшипниках скольжения должны быть уточнены проверкой и уменьшением влияния сдвига колец на результаты выверки.
Крепление состоит из различных частей которые должны быть собраны до начала процедуры измерения. В переносном кейсе находятся четыре различных основания и 12 комплектов выдвижных плеч различной длины. Каждый комплект состоит из трех одинаковых плеч. Перед сборкой необходимо определиться с требуемой для данной задачи длиной. Начинайте с монтажа лазера или детектора на основании а затем установите плечи. Абсолютно необходимо использовать оба фиксирующих винта на каждом из плеч чтобы предотвратить смещение при измерениях. Далее установите контактные направляющие валики на два плеча и эксцентрик на третье. Выдвиньте плечи на одинаковое расстояние и зафиксируйте с помощью винтов. Длина плеча с эксцентриком требует наиболее тщательной подборки. Установите сборку внутри кольца подшипника и подгоните длину так чтобы эксцентрик с трудом проворачивался усилием одной руки.
Ни в коем случае нельзя использовать никаких механических приспособлений. Необходимо чтобы усилие фиксации было одинаковым в каждой точке измерения.
Закупка подобной установки в рамках одного проекта экономически невыгодна так как требует значительных кап. вложений которые невозможно амортизировать за счет одного проекта. Но учитывая универсальность описанной установки и потребность в ней при строительстве и ремонтах на других проектах имеет смысл рассмотреть возможность её приобретения.
3.Общие сведения о движительном комплексе.
На судне устанавливается один валопровод в составе гребного винта регулируемого шага (ВРШ) дейдвудного устройства системы смазки дейдвудного устройства.
Вал соединяется с редуктором при помощи фланцевой муфты и плотно пригнанных болтов.
Предусматривается тормозное устройство для предотвращения проворачивания валопровода при буксировке судна и ремонтных работах на ДРА (дизель редукторном агрегате).
Главный упорный подшипник встроен в редуктор ДРА.
Для поддержания гребного вала предусматривается опорный подшипник скольжения в дейдвудном устройстве.
Дейдвудная труба стальная подшипник дейдвудной трубы из капролона.
Для смазки дейдвудного подшипника предусматривается прокачка забортной водой дейдвудного устройства от системы охлаждения главного двигателя.
При длительной стоянке судна в зимних условиях предусматривается обогрев дейдвудного устройства путем подачи пара в трубопровод прокачки дейдвуда.
Валоповоротное устройство ручное через маховик ГД. Поставляется с ДРА.
На соединительном фланце будет установлено зубчатое кольцо снабженное датчиком скорости для дистанционного определения числа оборотов.
Установка ВРШ состоит из следующих компонентов:
-Ступица гребного винта с лопастями
-Линия гребного вала
-Сервопривод управления шагом винта
-Комплектующие линии вала
-Гидравлическое оборудование.
4.Конструктивные особенности движительного комплекса и описание принципов работы его составляющих.
В данной части объясняются принципы работы линии гребного вала и системы гидравлики а также связанных с ними подсистем.
Линия гребного вала.
Линия гребного вала для установки ВРШ состоит из следующих элементов в направлении с кормы в нос:
ступица гребного винта с лопастями;
гребной вал с бронзовыми втулками и покрытием фланцевой муфтой с гидравлической напрессовкой;
(передаточный вал) сервопривод управления шагом.
Ступица соединена с фланцем гребного вала при помощи болтов и штифтов защищенных кожухом фланца который снабжен уплотнительными шайбами и заполнен минеральной смазкой. Лопасти гребного винта вращаются при помощи кулисного привода и гидравлического поршня – цилиндра внутри ступицы. Осевое движение кулисы превращается во вращательное движение лопастей винта.
Валы внутри полые для установки в них труб систем гидравлики. Трубы состоят из двух соосных трубопроводов. Внутренний подвижный трубопровод соединяет цилиндрическую кулису ступицы с механизмом подачи обратного сигнала в сервопривод управления шагом. Указанный трубопровод передает положение цилиндрической кулисы для установки шага переднего хода.
Внешний неподвижный трубопровод установлен во внутреннем отверстии вала и подает масло в заднюю часть цилиндрической кулисы для сохранения положения лопасти или установки шага заднего хода.
Между неподвижным трубопроводом и внутренней стенкой валов имеется третий канал. Этот канал соединяет ступицу с напорной емкостью. Напорная емкость расположена на определенном расстоянии над линией гребного вала так чтобы поддерживать постоянное избыточное давление в смазочной системе ступицы. Внутренний трубопровод где требуется имеет патрубки с продольными фланцами для крепления выходящих концов. Для той же цели внешний маслопровод имеет приваренные продольные полосы.
Масло которое изменяет положение гидравлического поршня закачивается через или снаружи вдоль подвижного маслопровода в линии гребного вала.
Съемное демонтажное кольцо из двух половин входит в линию гребного вала для доступа к ближайшему соединению трубопроводов.
Внутренний трубопровод оборудован встроенным запорным клапаном. Клапан удерживает постоянный шаг гребного винта когда изменение шага не требуется а также в аварийных ситуациях. Управляемый невозвратный клапан приводится в действие давлением масла в трубопроводе или поршнем за счет давления снаружи трубопровода в зависимости от требуемого направления потока масла.
Для смазки ступицы используется масло системы гидравлики. Расстояние между неподвижным маслопроводом и валом заполнено маслом и соединяет полость ступицы с маслораспределительной коробкой.
Ступица гребного винта с лопастями. (ДП.141200-03-164.01.03СБ).
Гребной винт регулируемого шага (ВРШ) имеет следующие характеристики:
Конструкция механизма ступицы очень компактная и содержит минимальное количество деталей. Последнее делает ее более надежной в эксплуатации.
Корпус ступицы (поз.2) отлит одной цельной частью с большими опорными муфтами чтобы гасить нагрузку от лопастей и кривошипно-шатунного механизма.
Каждая лопасть соединена со своим несущим элементом при помощи болтов (поз.28) и штифтов (поз.3). Болты имеют головки под шестигранный гаечный ключ подголовками находятся уплотнительные шайбы. Затягивать болты следует ключом с динамометром.
Вращение лопастей и их несущих элементов осуществляется за счет дополнительной движущейся кулисы (поз.22) через кривошипно-шатунный механизм. Отверстия расположены в кулисе. Штифты кривошипа являются частью несущих элементов лопастей винта и расположены под выходящей кромкой лопастей. Штифты снабжены высокопрочными бронзовыми скользящими блоками (поз.24).
Кулиса движется по оси через два поршня. Передний поршень составляет одно целое с гребным валом а кормовой поршень является частью кулисы. В кормовой части корпуса ступицы кормовой поршень поддерживается цилиндром который составляет с ним одно целое.
Когда масло закачивается по внутреннему маслопроводу к переднему цилиндру ступица перемещается назад вращая лопасти что приводит к увеличению шага гребного винта. Масло можно закачать к заднему цилиндру чтобы ступица переместилась вперед что приведет к вращению лопастей в сторону установки шага заднего хода. Шаг лопастей гребного винта передается на систему управления через внутренний трубопровод соединенный с подвижной кулисой.
Гидродинамическая конструкция лопасти такова что крутящий момент относительно оси поворота лопасти всегда действует в корму. Как следствие давление которое устанавливает лопасти на передний ход всегда будет больше чем давление которое устанавливает лопасти на задний ход. Во внутреннем маслопроводе установленный запорный клапан автоматически закрывается. Благодаря тому что лопасти стремятся вращаться в корму шаг гребного винта будет удерживаться за счет замкнутого объема масла в переднем цилиндре.
Для смазки механизма внутри ступицы используется масло системы гидравлики. Внутренняя полость ступицы соединена с маслораспределительной коробкой маслопроводным каналом который проходит между внешним неподвижным трубопроводом и внутренним отверстием валов. При помощи напорной емкости соединенной с маслораспределительной коробкой внутри ступицы поддерживается постоянное давление. Предусматривается возможность деаэрации полости ступицы и заднего цилиндра.
Уплотнения лопастей (поз.26) представляют собой резиновые армированные уплотнительные кольца установленные под фланцем лопасти. Уплотнительные кольца и канавки имеют такие размеры что легко позволяют компенсировать допуски в размерах подшипника лопасти через необходимый затяг при герметизации. На уплотнительные шайбы лопастей действует только давление масла напорной системы. На них не действует давление приводящее в действие механизм перемены шага. Во время остановки системы гидравлики уплотнительная шайба лопасти остается под давлением которое превышает давление окружающей лопасть воды так как напорная емкость будет размещена над ватерлинией.
Сервопривод управления шагом. (ДП.141200-03-164.01.04СБ).
Маслораспределительная коробка используется для подачи гидравлического масла во вращающийся вал. Кроме того она используется для передачи сигнала о изменении шага винта от внутреннего подвижного вращающегося маслопровода.
В целом сервопривод управления шагом состоит из направляющей втулки (поз.35) закрепленной на корпусе редуктора. Направляющая втулка также служит опорой для внешнего неподвижного маслопровода. Крутящий момент связан с редуктором т.е. судно не требуется.
Используется три плавающих уплотнения высокого давления (поз.41) запрессованные между корпусом (поз.32) шайбами (поз.10 поз.20) и фланцем (поз.4). Уплотнения могут перемещаться в радиальном направлении причем цилиндрические штифты (поз.6) не дают им вращаться. Между передней и средней шайбами к переднему концу гидравлического цилиндра через подвижный маслопровод закачивается масло; между средней и задней шайбами к заднему цилиндра масло закачивается через канал расположенный между маслопроводом и валом. За уплотнительным кольцом со стороны кормы судна установлен масляный затвор высокого давления (поз.5). Корпус маслораспределительной коробки используется для сбора протечек масла вытекшего из плавающих уплотнений и канала между неподвижной трубой и валом. Маслораспределительная коробка соединена с силовым блоком системы гидравлики трубопроводами.
Установка шага винта в аварийной ситуации может осуществляться в случае снижения давления в системе гидравлики или неисправности системы управления гидравликой.
Пробка (поз.43) заменяется вставкой с самозакрывающейся быстросрабатывающей соединительной муфтой. Вставка закрывает соединение с пропорциональным клапаном и таким образом с емкостью силового блока системе гидравлики. Шланг аварийного насоса можно соединить через муфту чтобы закачивать масло через вставку в ступицу. Для продолжения работы в нормальном режиме следует вернуться в начальное состояние т.е. специальная пробка должна быть демонтирована а на ее место должна быть установлена первоначальная пробка.
Передаточная коробка прикреплена к корпусу маслораспределительной коробки. При помощи контактного кольца (поз.7) закрепленного на подвижном маслопроводе и скользящем блоке (поз.19) который прикреплен к рычагу подачи сигнала (поз.17) сигнал об изменении шага винта (поз.16) и передаточную коробку. Внутри коробки находятся два потенциометра: один – для приемки сигнала установленного шага второй – для системы слеженияуказания величины шага.
Гидравлическое оборудование.
Гидравлическое оборудование состоит из следующего:
сборка поршень-цилиндрическая кулиса внутри ступицы;
трубопроводы внутри гребного вала с запорным клапаном в подвижном маслопроводе;
сервопривод управления шагом с маслораспределительной коробкой которая имеет встроенный механический индикатор шага передаточную коробку шага и в том числе соединение для аварийной установки шага;
силовой блок системы гидравлики с емкостью;
Силовой блок устанавливаемой системы гидравлического управления шагом гребного винта сервопривода управления шагом состоит из масляной емкости с находящимся сверху резервным электронасосом сдвоенного возвратного фильтра и клапана для гидравлического управления шагом а также одного отдельного насосного агрегата с механизмом отбора мощности. Насос с механизмом отбора мощности является главным насосом.
В случае отказа главного насоса производится включение резервного насоса и отключение главного. Если давление будет низким в течении длительного времени то специальный переключатель включит сигнал тревоги.
При необходимости изменить шаг гребного винта электроприводом включается клапан управления шагом. Через этот клапан один из насосов подает масло в кольцеобразную камеру соответствующую этому клапану в маслораспределительной коробке. Затем через подвижный маслопровод или через полость снаружи этого маслопровода масло подается с определенной стороны поршня в ступице для того чтобы изменить шаг. Отработанное масло из поршня стекает в маслораспределительную коробку и вместе с протечками масла собирается в емкости силового блока системы гидравлики.
Клапан управления шага представляет собой 4х ходовой управляемый распределитель. Степень открытия клапана регулируется встроенным управляемым клапаном. Величина на которую открыт управляемый клапан в свою очередь пропорционально соответствует электрическому сигналу посылаемому с системы дистанционного управления который регулирует постоянный уровень изменения шага.
Энергия требуемая для регулировки положения лопастей (шага винта) вырабатывается гидравлическим насосом который подает масло через маслораспределительную коробку во вращающийся гребной вал. Масло направляется либо внутрь либо снаружи вдоль подвижного маслопровода и таким образом попадает в заднюю или переднюю часть силового цилиндра. Когда шаг винта не меняется гидравлическое масло в линии гребного вала удерживается запорным клапаном внутри подвижного маслопровода.
Система гидравлики удерживается под статическим давлением при помощи напорной емкости которая должна быть установлена над линией гребного вала на расстоянии как указано на схеме системы гидравлики.
Протечки масла из маслораспределительной коробки стекает в напорную емкость. Излишки масла из напорной емкости стекают в нижнюю емкость.
Напорная емкость оборудована воздушным фильтром переключателем низкого уровня масла и измерительным штоком.
Детали линии гребного вала.
Демонтажное кольцо – это разделительное кольцо установленное между двумя подходящими фланцами вала. Кольцо обеспечивает соединениеразъединение маслопроводов внутри полых валов без изменения продольного положения гребного вала.
Тормоз валопровода (см. рис.10.) размещается на одном из фланцевых соединений валов. Причем один из фланцев используемый в качестве тормозного диска специально изготовляют несколько большим по диаметру и с достаточно широким ободом. Тормозной диск охватывается бугелями внутренние поверхности которых облицованы фрикционными накладками а в верхней части имеются отверстия с противоположной резьбой. Затормаживание вала осуществляется обжатием тормозного диска бугелями которые стягиваются винтом. Крепление тормоза валопровода к фундаменту должно удерживать тормоз от проворачивания вместе с заторможенным валом.
Рис. 10. Тормоз валопровода
Фланцевая муфта с гидравлической напрессовкой.
Фланцевая муфта в данном проекте – это муфта прессового типа. Крепежные пазы создающие концентрацию напряжений отсутствуют. Это является значительным преимуществом так как в прошлом было много случаев когда валы получали сильные повреждения из-за концентрации напряжений. Еще одним преимуществом является то что демонтаж муфты можно произвести гидравликой. Такой метод позволяет хорошо управлять процессом монтажадемонтажа.
При методе крепления закачкой масла гидравлики когда отсутствуют крепежные пазы масло подается под давлением между муфтой и валом при помощи насосов которые питают систему канавок в отверстии муфты. Канавки обеспечивают распространение масла между поверхностями и таким образом в процессе напрессовки временно снижают коэффициент трения до менее 002. Таким образом при помощи гидравлического устройства очень легко запрессовать муфту в конус чтобы обеспечить достаточную прочность посадки.
Муфта запрессовывается на заранее заданное расстояние. Это расстояние должно обеспечивать достаточный запас прочности при передаче крутящего момента. Конструкция муфты такова что избыточные напряжения не образуются.
Для точного определения окончательного положения муфты на вал нанесена метка. Положение метки указано на чертеже (ДП.141200-03-164.01.08СХ).
В окончательном положении метка должна находиться точно на 30 мм в корму от кормовой стороны муфты. Положение метки было определено на заводе-изготовителе после первой посадки муфты. Расстояние указанное на чертеже дано только для справки. Может оказаться что измеренное расстояние будет как-то отличаться от указанного на чертеже. Причина такого расхождения в разбросе в начальной точке. Из-за малого угла конуса начальное положение очень зависит от того как муфта расположена на валу.
Разработка технологии монтажа движительного комплекса.
Разработанная в данном проекте технологическая инструкция в дальнейшем ТИ определяет порядок и технологическую последовательность монтажа движительного комплекса и центровки валопровода судов проекта 50010 и может быть применима в качестве руководящего документа для цехов и отделов ГМП «Звездочка».
ТИ откорректирована и дополнена с учетом накопленного опыта выполнения работ на первых судах серии.
При выполнении работ совместно с данной ТИ руководствоваться требованиями следующих отраслевых документов:
- ОСТ5.4110-87Механизмы и фундаменты судовые. Общие технические требования к монтажу.
- ОСТ 5.4368-81Валопроводы судовые движительных установок. Монтаж. Технические требования правила приемок и методы контроля.
- ОСТ 5.4405-84Валопроводы судовых движительных установок. Монтаж. Типовой технологический процесс.
- ОСТ5.4183-76Подшипники гребных и дейдвудных валов капролоновые. Общие технические условия.
- ОСТ5.9966-85Устройства опорные гребных валов. Типовой технологический процесс монтажа с применением полимерных материалов.
- 610.02-С1.008.00Формирование корпуса судна проекта 50010. Технологическая инструкция.
- НЯДИ.000.0308.00.002Системы устройства механизмы и оборудование судов и плавучих сооружений. Требования по безопасности труда и охране окружающей среды при выполнении работ верфи. Инструкция.
-Регистр. Руководство по техническому надзору за постройкой судов и изготовлением материалов и изделий. Часть 4. Надзор за постройкой судов.
- НЯДИ.0000308.00.003Спецпокрытия стеклопластик. Типовые требования безопасности и охраны окружающей среды при демонтаже и восстановлении. Инструкция.
Последовательность выполнения работ по монтажу валопровода определена сетевым графиком черт. ДП.141200-03-164.01.09.СХ
1. Общие технические требования.
До начала работ по монтажу валопровода должны быть закончены следующие работы:
) закончены основные сборочно-сварочные работы по корпусу судна или кормового блока включая работы по фундаментам под главные механизмы и монтаж насадки;
) завершены испытания всех отсеков и цистерн в районе расположения валопровода и машинного отделения без испытания дейдвудного отсека;
) погружено основное крупногабаритное оборудование (массой более 270 кг.) или установлены грузы имитирующие их и раскреплен балласт в дейдвудном отсеке и под фундаментом редуктора. Установка балласта в дейдвудном отсеке должна быть произведена после приварки вварыша на 52 шп. до погрузки дейдвудной трубы под окончательный монтаж;
) выполнена расточка яблока ахтерштевня по теоретической оси валопровода;
) произведена установка фундаментов под ДРА относительно теоретической оси линии вала (пробитой по плазовой разметке);
) проверено и зафиксировано актом или в журнале ДОУ положение корпуса или блока на стапеле относительно базовой плоскости. Измерение положения корпуса (блока) от зафиксированного на начало работ не должно превышать 30 мм.
Контроль готовности судна к монтажу валопровода следует выполнять на основании перечня закрытых построечных удостоверений помещений корпусных конструкций цистерн и т.д.
Окончательный монтаж тормоза и дейдвудного сальника выполнять после центровки валопровода и фиксации положения его опор.
Строповку и перемещение гребного вала его поддержание в помещении технологическим монтажным подшипником выполнять в соответствии со схемой. ДП.141200-03-164.01.07.СХ. Тросы применяемые для строповки должны иметь защитную оплетку.
Перед заводкой вала испытать дейдвудный отсек проверить чистоту поверхностей гребного вала и дейдвудной трубы покрыть солидолом ГОСТ 1033 поверхность подшипника и вала. Слой солидола должен быть равномерно нанесен и не иметь сгустков и подтеков.
В процессе погрузки и перемещения гребного вала вести постоянный контроль за его положением по зазорам в подшипнике по кормовому наружному торцу. Не допускать перекоса вала.
До начала монтажа тормоза должен быть изготовлен фундамент с чистотой обработки опорных поверхностей не менее Rz 40 по ГОСТ 2789. Отклонение от плоскостности обработанных поверхностей проверять щупом и линейкой или проверочной плитой на «краску». При проверке с помощью щупа и линейки пластина щупа толщиной 01 мм не должна проходить между проверочной линейкой. При проверке на «краску» обеспечить не менее одного пятна на площади 25х25 мм при этом отсутствие пятен по краю контролируемой поверхности не допускается. Полки опорных поверхностей до монтажа покрыть консервационной смазкой и закрыть от механических повреждений фанерными заглушками или асбестовой тканью.
Отверстия под болты повышенной точности штифты обрабатывать одновременно через весь набор монтажного узла (лапа механизма прокладка полка фундамента). Болты повышенной точности штифты изготовить по размерам окончательно выполненных отверстий. Допускается увеличение диаметра отверстий до 10%.
На окончательно выполненных отверстиях допускаются отдельные кольцевые риски от развертки в количестве не более трех на расстоянии не менее 15 мм друг от друга.
Установку призонных болтов выполнять в присутствии контрольного мастера ОКК. Перед установкой посадочные поверхности смазать солидолом или графитной смазкой ГОСТ 3333.
Центровку валопровода с главным двигателем выполнять по стрелам на стапеле с окончательной центровкой на плаву.
В период центровки валопровода на стапеле осуществлять ежедневную проверку положения корпуса судна или кормового блока с занесением результатов проверки в стапельный журнал. Отклонения замеров от зафиксированных перед началом работ по центровке валопровода не должны превышать 3 мм не считая общей просадки корпуса на кильблоках.
В период центровки валопровода и заполнения монтажного зазора полимерным материалом не допускается передвижка судна или блока.
Допускается передвижка корпуса до окончательного закрепления подшипника при этом подшипник должен быть застопорен отжимными болтами и зафиксирован эл. прихватками.
После центровки валопровода минимальный зазор между дейдвудной трубой и яблоком ахтерштевня должен быть не менее 2 мм.
Перед установкой в опоры дейдвудной трубы поверхности яблока ахтерштевня и дейдвудной трубы контактирующие с полимерным материалом должны быть обработаны дробеструйным способом до второй степени очистки в соответствии с ОСТ5.9829.
Заварку съемных листов в районе МО выполнять по отдельной технологии исключающей деформации корпуса.
Приемка монтажа осуществляется путем пооперационного контроля работ и производится в первую очередь службой ОКК которая затем предъявляет эти работы представителям Регистра и заказчика. Результаты приемки оформляются формуляром в котором должно быть отмечено выполнение работ по монтажу и приведен перечень актов (протоколов) пооперационной приемки.
2. Технологический процесс.
2.1. Пробивка оси линии вала под установку
Разметить места установки кронштейнов изготовить и установить кронштейны в районе 39455259шп.
Заварить установленные конструкции.
Выполнить проверочные работы по разметке:
-на установленных кронштейнах
-ахтерштевне (снаружи изнутри)
-оси линии вала в виде перекрестий горизонтальных и вертикальных линий (выполнить чертилкой и керном).
Разметку выполнить с помощью шлангового уровня рулетки и отвеса.
При разметки взять за базу контрольные линии нанесенные на корпус судна.
В период разметки оси Л.В. производить периодические проверки положения корпуса судна по крену и дифференту крен корпуса не более 2мм. На ширину судна.
Проверку положения производить шланговым уровнем. Проверяется совмещение в одной горизонтальной плоскости 3х точек расположенных на контрольной ватерлинии 2700мм от ОП в районе 39шп. по Л.Б. и ахтерштевня. Дифферент на этой длине не более 3мм. Периодичность проверок один раз в неделю.
Кроме периодических проверок проверку положения по крену и дифференту производить:
при пробивке оси линии вала
перед расточкой отверстия и после расточки отверстия под яблоко ахтерштевня.
при установке: перед сдачей под сварку и после приварки яблока.
перед расточкой и после расточки торцов яблока
перед установкой насадки и после монтажа насадки.
В случае одновременности выполнения различных видов работ требующих проверки положения корпуса судна достаточно провести одну такую проверку.
Рекомендуется совмещать проверки.
Пробивку оси линии вала производить натянутой струной между кронштейнами согласно схемы натяжения струн по осям линии вала. Усилие для натяжения струны обеспечить в зависимости от ее диаметра согласно таблицы:
Усилия натяжения струны в зависимости от ее диаметра.
Натяжение струны обеспечить подвешиванием груза (балластин). Снятие струны натянутой в координатах оси линии вала и предъявленной ОКК производить только в случаях оговоренных в настоящем тех. процессе.
Пробивку оси линии вала производить также оптическим методом при помощи визирной трубы ППС-11. Допускаемое отклонение оси линии вала от прямолинейности измеренное на промежуточных переборках и стойках должно составлять не более ±1 мм.
Сдать ОКК разметку оси Л.В. Допуск на отклонение разметки по высоте и по пшироте ±2мм.
Установить на кронштейнах в районе 595245шп. приспособления для установки мишеней вскрыв газом предварительно отверстия в кронштейнах и ахтерштевне под ось Л.В. (в ахтерштевне вскрывается маломерное отверстие Ф200мм.) В приспособления 5245шп. вставить мишени а в приспособление 59шп. мишень «глухую» для натягивания струны. Натянуть струну имитирующую ось Л.В. с помощью шлангового уровня рулетки отвеса отцентровать приспособление на 59шп. струну по оси Л.В. Допуск ±2мм.
Установку сдать ОКК запломбировать приспособление 59шп. Снять струну и мишень на 59шп. Вставить трубу ППС-11 в приспособление на 59шп. Отцентровать трубу ППС-11 на 59шп. по перекрестию оси Л.В. на 39шп. а мишени 4552шп. по оси трубы ППС.
Предъявить ОКК пробивку оси Л.В. запломбировать приспособления 45-52шп. трубу ППС-11 и мишени снять с приспособлений.
Установить в приспособление на 59шп. «глухую» мишень натянуть струну между кронштейнами 39шп. и 59шп.
2.2. Установка яблока ахтерштевня.
От струны разметить отверстие в ахтерштевне под яблоко нанести контрольные линии на ахтерштевне согласно Рис. 11.
-разметить контур отверстия Ф540мм. для вскрытия его газом
-разметить точки пересечения контура отверстия Ф552мм. с его вертикальной и горизонтальной осями на деталях с наружной и внутренней стороны – для вскрытия отверстия станком
-разметить контрольные линии Ф560мм аналогично разметки под расточку.
Рис. 11. Разметка ахтерштевня.
Разметку кернить сдать ОКК снять струны «глухую» мишень в кронштейне 59шп.
Примечание: разрешается дальнейшее выполнение работ по монтажу насадки или совместно с этим пунктами (монтажом насадки) а также дальнейший монтаж яблока ахтерштевня производить относительно от оси Л.В.
Вскрыть газом отверстия Ф540мм. в ахтерштевне под яблоко. Сдать ОКК под расточку.
Установить кронштейны к кормовому подзору для установки расточного станка.
Установить расточной станок отцентровать его по контрольным линиям на ахтерштевне согласно Рис. 11.
Проверить центровку станка установив и отцентровав трубу ППС-11 в кронштейн 59шп. по перекрестию 39шп.
Перекрестия мишеней в бабке станка должны совпадать с оптической осью Л.В. заданной трубой ППС-11.
В случае не совпадения получить решение ОГТ выполнив которое сдать установку станка ОКК.
Демонтировать трубу ППС-11 и мишени.
Расточить ахтерштевень с допуском +0мм. -1мм. Сдать ОКК.
Демонтировать расточной станок.
Разметить и разделать газорезкой и наждачным камнем кромки выреза в ахтерштевне.
Установить трубу ППС-11 в кронштейн на 59шп. и мишени на 5245шп.
Отцентровать трубу ППС-11 по перекрестию 39шп. закрепить. Проверить мишени 4552шп. по оси Л.В. Все несовпадения мишеней 45.52шп. оформить в журнале проверочных работ с соответствующим решением ОГТ Сдать ОКК.
Завести яблоко с дополнительной обработкой кромок при необходимости выреза в ахтерштевне наждачным камнем. Установить крестовины с мишенями (по торцам яблока). Отцентровать крестовины штангенциркулем с точностью ±05мм. Яблоко выровнять относительно оптической оси Л.В.
Положение яблока: по длине ±1мм. по высоте ±05мм от оптической оси Л.В.
Рис. 12. Приварка яблока ахтерштевня.
2 – очередность постановки прихваток .
I II – очередность сварки.
Перед установкой яблока на деталях 5 и 18 вскрыть технологические выреза для приварки наружной обшивки к яблоку по узлу Т6 ГОСТ 5264. Установить яблоко на прихватках в указанной последовательности:
- прихватки 1 и 2 выполнить двумя сварщиками одновременно (смотри рисунок 13 а.).
- установку прихваток выполнять в среде СО проволокой Св-08Г2С или покрытыми электродами марки УОНИИ 1355Р диаметром З мм. Длина прихваток 15-20 мм (расположение смотри рисунок № 13 а.)
- провести контроль положения яблока.
- по результатам контроля провести дальнейшую установку яблока на прихватках с внутренней стороны обшивки в последовательности показанной на рисунке № 13 а. Ввиду стесненности в месте выполнения работ установку прихваток внутри производит один сварщик.
- провести контроль положения яблока относительно осевой Л.В. с занесением результатов измерения в журнал проверочных работ с предъявлением ОКК. Допуск + 1мм.
Примечание: В случае выхода результатов замеров за пределы указанного допуска решение о продолжении дальнейших работ принимается оперативной группой.
Установку яблока сдать ОКК.
Приварку яблока выполнять по узлу Т8 ГОСТ5264-80 под наблюдением технолога цеха и с соблюдением следующих требований:
-произвести разбивку сварных соединений на участки длиной 100-120 мм (4 участка снаружи 4 участка внутри) согласно рисунок 14 а.
-сварку участков выполнять обратноступенчатым методом с общим направлением сварки: снаружи — от НО в корму внутри — от НО в нос.
-валики таврового соединения с каждой стороны выполнять участками в диаметрально противоположных направлениях одновременно (два сварщика снаружи) и последовательно (один сварщик — внутри) согласно примеру на рис.14 б.
-наложение последующего прохода (слоя) сварного соединения начинать после остывания предыдущего до температуры 50°С (тёплый на ощупь).
-осуществлять постоянный контроль за положением яблока в процессе сварки.
-В случаях отклонений в положении яблока изменять порядок сварки по указаниям технологической службы.
Рис. 13. Схема постановки прихваток.
Общий порядок сварки яблока с дет. поз.5 и 18 следующий:
-заварить первых два прохода с двух сторон каждого соединения снаружи.
-провести контроль положения яблока с занесением результатов измерения в журнал проверочных работ.
-заполнить разделку сварных соединений заподлицо снаружи.
-выполнить первых два прохода с обеих сторон каждого соединения внутри.
-заполнить разделку сварных соединений заподлицо внутри.
-выполнить усиление швов сварных соединений снаружи.
-выполнить усиление швов сварных соединений внутри.
-Примечание: В случае выхода результатов замеров за пределы допуска решение о продолжении дальнейших работ принимается ОГСв и БТПП цеха с оформлением в журнале проверочных работ.
Рис.14. Последовательность сварки яблока с деталями 518.
Установку яблока на прихватках к НО (наружной обшивке) выполнить в последовательности:
- снаружи прихватки 1 и 2 выполнить двумя сварщиками одновременно (смотри рисунок 13 б.). Последовательность постановки прихваток может быть изменена по результатам измерений.
- установку прихваток выполнять в среде СО проволокой Св-08Г2С или покрытыми электродами марки УОНИИ-1355Р диаметром 3 мм. длина прихваток 15-20 мм (расположение смотри рисунок 13 б.).
- провести контроль положения яблока с занесением результатов измерения в журнал проверочных работ с предъявлением ОКК.
В случае выхода результатов замеров за пределы допуска решение о продолжении дальнейших работ принимается ОГСв и БТПП цеха с оформлением в журнале проверочных работ.
Рис.15. Последовательность сварки яблока с НО.
Приварку яблока к НО выполнить по узлу Т4 ГОСТ11534-75 под наблюдением технолога цеха и с соблюдением следующих требований.
-произвести разбивку сварных соединений на участки внутри и снаружи согласно рис. 15.
-сварку участков выполнять в диаметрально противоположных направлениях одновременно (два сварщика - снаружи) и последовательно (один сварщик — внутри) согласно последовательности показанной на рис.15.
-наложение последующего прохода (слоя) сварного соединения начинать после остывания предыдущего до температуры 500С (тёплый на ощупь).
-в случаях отклонений в положении яблока изменять порядок сварки по указаниям технологической службы.
Общий порядок сварки яблока с НО следующий:
-заварить первый проход соединения снаружи.
-заполнить разделку сварного соединения снаружи заподлицо.
-выполнить усиление шва сварного соединения снаружи.
-выполнить подварочный шов внутри в последовательности показанной на рисунке 15.
Примечание: В случае выхода результатов замеров за пределы допуска решение о продолжении дальнейших работ принимается ОГСв и БТПП цеха с оформлением в журнале проверочных работ.
Провести окончательный контроль положения яблока с занесением результатов измерения в журнал проверочных работ сдать ОКК. Результаты замеры передать в ОГТ КО.
По положительному заключению о положении яблока сварные швы по визуальному контролю и измерениям сдать ОКК.
Сварные швы приварки НО к яблоку испытать смачиванием керосином и предъявить ОКК.
Замерить положение оси яблоко относительно оси Л.В. Допуск ±2мм. Сдать ОКК сварку и положение ахтерштевня.
2.3. Монтаж подшипника.
Монтаж подшипника (запрессовку и раскрепление) в дейдвудную трубу выполняют в механомонтажном цехе по отдельной технологии в соответствии с ОСТ5.4183-76 [15].
Запрессовка подшипников должна производиться плавно без перекосов.
Измерить внутренний диаметр подшипника после запрессовки для определения фактического водяного зазора по разнице диаметров подшипника и рубашки вала.
После запрессовки подшипник застопорить от проворачивания и осевого смещения механически винтами. Стопорные винты подшипников должны быть равномерно затянуты до отказа ключом с плечом рычага от 150 до 200 мм и раскернены.
Техническим контролем должна производиться приемка качества сборки запрессовки стопорения подшипников и соблюдения натягов и зазоров в соединениях после их запрессовки.
Действительные натяги усилия запрессовки монтажные зазоры и температура при которой производились замеры и запрессовка должны быть отражены в формуляре валопровода.
Размеры овальность конусность посадочных поясков подшипников и сопрягаемых с ними поясков посадочных отверстий должны быть проверены не менее чем в двух местах по диаметру и в двух местах по длине.
Зазор между облицовкой вала и подшипником должен проверятся набором щупов по ГОСТ 882-75.
Погрузку дейдвудной трубы на судно выполнять в сборе с подшипником.
2.4. Установка вварыша и дейдвудной трубы.
Примечание: Установку и приварку вварыша производить без имитации недостающего оборудования.
После получения извещения от ц.10 о пробивке оптической оси и нанесения контрольных окружностей под вскрытие отверстий под яблоко и вварыш выполнить расточку отверстий и установку яблока и вварыша.
Для расточки отверстий в ахтерштевне и переборке 52 шп. выполнить следующие операции:
) установить фундаменты под расточное устройство согласно схемы расточки;
) установить и отцентровать бабку расточного станка относительно оптической оси. При этом станок считать сцентрированным по оси валопровода если несовпадение перекрестий мишеней и оптического прибора не превышает толщины линии перекрестий. Собрать расточное устройство;
) выполнить расточку отверстия в ахтерштевне под яблоко. Переместить станок на фундамент установленный в районе переборки 52 шп.;
) установить и отцентровать станок по оптической оси линии вала в районе 52 шп. по п.2);
) выполнить расточку отверстия под вварыш с обработкой кромок под сварку. Проверить перпендикулярность носового торца яблока ахтерштевня. Для проверки перпендикулярности использовать борштангу расточного устройства и индикаторную головку. Отклонение от перпендикулярности торца вварыша относительно оси не должно превышать 02 ммм. Демонтировать станок фундамент.
) завести дейдвудную трубу в яблоко ахтерштевня продвинуть до выхода носового конца из яблока на 250 мм.
) навесить на дейдвудную трубу неразъемные детали уплотнения торцов монтажных зазоров: гайки (29) с прокладками (31) вварыш (30) черт. ДП.141200-03-164.01.02.СБ
) установить в монтажный зазор между вварышем и дейдвудной трубой технологическое центрирующее полукольцо. Закрепить вварыш на дейдвудной трубе с помощью гаек (29);
) завести дейдвудную трубу совместно с вварышем в отверстие на переборке до упора кормового фланца трубы в яблоко согласно схемы ДП.141200-03-164.01.05.СХ. При этом выдержать размер от носового торца дейдвудной трубы до торца вварыша (вид «Г» черт. ДП.141200-03-164.01.02.СБ) в пределах 63-64 мм. Отцентровать дейдвудную трубу по оптической оси линии вала выдержав при этом зазор между вварышем и дейдвудной трубой не менее 20 мм. При установке ось дейдвудной трубы должна совпадать с осью линии вала или быть параллельна ей;
) прихватить вварыш к переборке на электроприхватках; в точках затем в точках б-б одновременно двумя сварщиками l пр. = 5-10 мм снять замеры и сдать ОКК. Установить 4 индикатора ИЧ-10 со стороны машинного отделения. Сдать ОКК.
) отвинтить носовую гайку крепления вварыша вынуть технологическое центрирующее полукольцо. Снять замеры положения вварыша по индикаторам.
) приварить вварыш к переборке в соответствии с требованиями черт.ДП.141200-03-164.01.02.СБ и технологии на сварку. Влиять на положение вварыша в процессе приварки следует изменением направления и режимов сварки. Контроль положения вварыша в процессе сварки осуществлять с помощью 4 индикаторов ИЧ-10 (поз.11) устанавливаемых в вертикальной и горизонтальной плоскостях согласно схемы ДП.141200-03-164.01.05.СХ.
Порядок сварки назначается в зависимости от положения вварыша по показаниям индикаторов (см. рис 16). Общая последовательность:
-одновременно двумя сварщиками выполнить один проход узким валиком на участках 1-1. После полного остывания проверить положение. Если положение не изменилось и удовлетворительное (по заключению технолога цеха) выполнить второй проход на участке 1-1. Дать остыть. Проверить положение. По решению технолога одним сварщиком поочередно выполнить по одному проходу на участках 2-21 . После каждого валика давать полное остывание шва. Уточнить положение по индикаторам. Сварку с обратной стороны выполнять одним сварщиком с остыванием после каждого валика. Сварку выполнять узким валиком по одному валику в последовательности 3-31; 4-41 . Последовательность сварки уточняется технологом по показаниям индикатора. Сварной шов испытать смачиванием керосином сдать ОКК.
Рис.16. Приварка вварыша.
После окончания сварки вварыша со стороны машинного отделения выдвинуть дейдвудную трубу в корму для обеспечения приварки вварыша со стороны ахтерпика или выгрузить полностью с заказа.
) завести дейдвудную трубу в вварыш в штатное положение. Навинтить гайки крепления дейдвудной трубы к вварышу. Измерить кольцевой зазор между гайками и вварышем который должен быть не более 01 мм. В случае увеличения зазора более допустимого комиссии в составе представителей КО ОГТ технологической службы цеха принять решение о дальнейшем продолжении работ. Предъявить ОКК установку вварыша под монтаж дейдвудной трубы.
Примечание: Допускается заменить метод контроля вварыша индикаторами на контроль положения носовой мишени дейдвудной трубы относительно оси линии вала по схеме .ДП.141200-03-164.01.05.СХ Для чего:
приварку вварыша начинать после простановки прихваток (см. выше) при плотно зажатой гайками дейдвудной трубе по указаниям технолога по сварке;
измерение положения носовой мишени дейдвудной трубы компенсировать последовательностью сварки по указаниям технолога по сварке;
последовательность сварки вварыша согласно данной ТИ;
после окончания сварки со стороны машинного отделения отвинтить носовую гайку выдвинуть дейдвудную трубу в корму до обеспечения возможности приварки вварыша со стороны ахтерпика;
заварить по указаниям технолога по сварке вварыш со стороны ахтерпика предварительно испытав выполненный сварной шов керосином на мел. Сдать испытание и сварку ОКК – визуально;
дальнейшие работы по контролю прилегания гаек дейдвудной трубы к вварышу согласно данной технологии.
Непосредственно перед заводкой дейдвудной трубы удалить защитные покрытия и произвести визуальный контроль контактирующих с полимерным материалом поверхностей. При обнаружении на поверхностях пятен грязи коррозии или масла удалить их чистой ветошью смоченной уайт-спиритом а затем спиртом ГОСТ 18300. Отдельные пятна ржавчины удалить пневмощетками при покрытии коррозией или замасливании более 10% дробеструйных поверхностей дробеструйную обработку повторить.
Завести дейдвудную трубу в опоры (яблоко ахтерштевня и вварыш).
Навесить на дейдвудную трубу неразъемные детали уплотнения торцев монтажных зазоров гайки (29) с прокладками (31).
Установить в дейдвудную трубу мишени по схеме черт.ДП.141200-03-164.01.05.СХ отцентровать дейдвудную трубу по оптической оси валопровода с помощью отжимных болтов при этом ось трубы должна совпадать с оптической осью линии вала. Дейдвудная труба считается сцентрированной по оси линии вала если несовпадение перекрестий мишеней установленных в дейдвудной трубе и прибора не превышает толщины линий перекрестий. Положение дейдвудной трубы предъявить ОКК.
Измерить монтажный кольцевой зазор под заливку полимерным материалом. Измерения выполнять с носового торца яблока ахтерштевня и кормового и носового торца вварыша. Наименьший кольцевой зазор под заливку полимерным материалом 2 мм. Зафиксировать положение дейдвудной трубы отжимными болтами. Болты надежно обжать и застопорить от отвинчивания эл. прихватками.
Уплотнить монтажные зазоры между дейдвудной трубой и яблоком вварышем с помощью гаек (29) с прокладками (31). При этом пластина щупа толщиной 01 мм не должна проходить между сопрягаемыми поверхностями по всему периметру. Разметить на торце носовой гайки крепления вварыша 8 отверстий под крепление крышки сальника. Свинтить носовую гайку крепления вварыша отправить на обработку отверстий. Получить гайку после обработки отверстий навинтить.
Погрузить и установить по оптической оси валопровода технологический монтажный подшипник по схеме черт.ДП.141200-03-164.01.06.СБ для поддержания конца вала от провисания и последующей центровки редуктора с гребным валом. Положение подшипника предъявить ОКК.
В литник заложить силикагель ГОСТ 3956 в мешочке в количестве 300г. и все отверстия закрыть пробками. Межоперационный период времени между заводкой дейдвудной трубы в опоры и заполнения монтажного зазора полимерным материалом не должен превышать 15 дней при установленных уплотнениях. Непосредственно перед заливкой силикагель удалить.
Выдать заявку ц.45 на подготовку полимерных материалов не менее чем за 10 суток до планируемой заливки монтажных зазоров.
Непосредственно перед началом крепления дейдвудной трубы проверить:
) выемку силикагеля;
) установку уплотнений монтажных зазоров;
) фиксацию положения дейдвудной трубы;
) установку и подключение схемы заливки пластмассы;
) выдачу извещения ц.45 за подписью мастера ОКК
) наличие отверстий на гайке крепления вварыша и дейдвудного сальника.
Приготовление пластмассы и порядок заливки монтажных зазоров согласно раздела 4 данной технологии.
2.5. Подготовка поверхностей приготовление полимерного материала заполнение монтажного зазора.
Подготовка поверхностей контактирующих с полимерным материалом.
Внутренние поверхности опор и наружные поверхности дейдвудной трубы контактирующие с полимерным материалом очистить от грязи жировых и масляных пятен промыть уайт-спиритом (ГОСТ 3134) или ацетоном (ГОСТ 2768).
Перед заводкой в опоры поверхности опорных устройств контактирующие с полимерным материалом обработать дробеструйным способом до второй степени тщательности очистки (эталон Б-1б) аппаратом "Каскад" дробью ДЧК 1- 08.
Предъявить ОКК с оформлением в ЖОК (журнал операционного контроля) по Форме 1302948.
Подготовленные поверхности защитить от попадания на них воды масел грязи:
-наружные очищенные поверхности обернуть чистой бумагой затем полиэтиленовой пленкой;
-внутренние поверхности закрыть технологическими заглушками.
Приготовление полимерного материала
)Состав полимерного материала для заполнения монтажного зазора должен соответствовать составу приведенному в таблице 7.
Для уменьшения вязкости полимерного материала добавить в полимерный материал этиловый спирт высшего сорта по ГОСТ 18300 в количестве 3% от массы эпоксидного материала.
)Компоненты проверить путем замешивания пробы из части материала по рецептуре приведенной в таблице и определения предела прочности на сжатие отвержденного материала в соответствии с требованиями ГОСТ 4651.
Проверку выполнять следующим образом:
В емкости объемом от 08 до 10 литра последовательно смешать 300 г смолы 300 грамм пылевидного кварца и 36 грамм полиэтилен-полиамина взвешенных с погрешностью не более 5грамм. После введения каждого компонента смесь перемешивать в течение от 5 до 10 минут шпателем до получения однородной массы.
Приготовленную смесь разлить в формы обеспечивающие изготовление образцов в соответствии с требованиями ГОСТ 4651. Перед заполнением формы смазать антиадгезионным составом.
Формы с полимером поместить для отверждения в отапливаемое помещение с температурой воздуха не ниже 200С.
После отверждения полимера изготовить из него 5 образцов Ф10 мм высотой 15 мм и испытать их на сжатие в соответствии с требованиями ГОСТ 4651.
Результаты испытаний оформить протоколом ЦЗЛ(центральная заводская лаборатория). Если при испытании образцов через трое суток после приготовления пробы средняя величина предела прочности материала на сжатие будет менее 50 МПа произвести подбор компонентов из другой партии поставки материалов.
)Подготовка компонентов.
Кварц пылевидный перед использованием просушить при температуре не ниже 150С не менее трех часов и просеять через сито с сеткой 08 или 1 по ГОСТ 6633 или ГОСТ 3826.
Смолу хранившуюся при температуре ниже 15С предварительно разогреть до 25-40С поместив закрытую емкость со смолой в отапливаемое помещение или горячую воду с температурой 35-40С.
)Приготовление полимерного состава.
Приготовление пластмассы для заливки монтажного зазора производить в два этапа:
-предварительное приготовление смеси без отвердителя (полиэтилен-полиамина) в цехе 45;
-окончательное приготовление с введением в смесь отвердителя выполняемое в непосредственной близости от места заливки.
Предварительное приготовление смеси:
-взвесить компоненты необходимые для замеса порции полимерного материала (кроме полиэтиленполиамина). При взвешивании рекомендуется под эпоксидную смолу использовать бак (емкость) для перемешивания компонентов.
-засыпать в бак с эпоксидной смолой пылевидный кварц размешать его деревянными шпателями до смачивания пыли жидкотекучими компонентами затем перемешать смесь механизированным способом от 5 до 10 минут до получения однородной массы.
-прикрепить к баку отличительную бирку (этикетку) с указанием количественного состава компонентов смеси даты приготовления. Тару опечатать.
Межоперационное хранение смеси без полиэтиленполиамина в упакованном виде выполнять в закрываемом помещении при положительной температуре окружающего воздуха.
Длительность хранения перед дальнейшим использованием смеси должна быть не менее 3 и не более 30 суток.
Окончательное приготовление полимерного материала
При окончательном приготовлении полимерного материала на заказе выполнить последовательно следующие операции:
-проверить температуру смеси компонентов при необходимости довести ее до 18-25°С подогревом или охлаждением смеси;
-ввести в смесь этиловый спирт перемешать смесь (7-10 минут) механизированным способом до получения однородной массы;
-отмерить в мерной посуде или заранее оттарированной таре полиэтиленполиамин (отвердитель) залить отвердитель в бак и перемешать механизированным способом в течении от 7 до 10 минут до получения однородной массы контролируя температуру смеси при необходимости охладить.
Полимерный материал имеющий температуру выше 30 С к заполнению монтажного зазора не допускается.
Примечание: Спирт по ГОСТ 18300 добавляемый в пластмассу получить на складе в присутствии технолога цеха с проверкой плотности опечатав емкость со спиртом пломбиром. Вскрыть непосредственно перед заливкой в присутствии технолога цеха.
Заполнение монтажного зазора полимерным материалом
Заполнение монтажного зазора производить при температуре опорного устройства не менее 5С. При более низкой температуре металлических поверхностей контактирующих с полимерным материалом их необходимо подогреть теплым воздухом от калориферов или другим способом. Подогрев следует выполнять до температуры не выше 45С.
При температуре металлических поверхностей от 5 до 15С обеспечить температуры полимерного материала в пределах от 23 до 26 С.
Заполнение монтажного зазора производить принудительной подачей полимерного материала поршневым прессом. Пресс устанавливать вблизи от опорного устройства так чтобы длина гибкого шланга соединяющая его с литником была минимальной и не превышала 15-20 м.
Работу выполнять цеху 45 совместно с цехом монтажником (цех монтажник устанавливает выпоры подсоединяет пресс к литнику устраняет протечки полимерного материала.
Во время заполнения монтажного зазора следить за отсутствием протечек полимерного материала через уплотнения протечки устранять поджатием уплотнений конопаткой асбестовым шнуром по ГОСТ 1779 или чистой ветошью по ТУ 63-178-77 или другим способом.
Заполнение монтажного зазора следует заканчивать после появления полимерного материала из всех выпоров.
После заполнения монтажного зазора осмотреть уплотнение зазора по всем торцам убедится в отсутствии протечек полимерного материала шланг отсоединить от пресса и надежно закрепить выше верхней точки заполненного зазора до отверждения полимерного материала заполнить его остатками формы которые хранить в районе расположения опорного устройства до отверждения полимерного материала.
По истечении трех суток часть образцов отправить на испытание по ГОСТ 4651. Разрушающее напряжение при сжатии должно быть не менее 50 МПа. Если предел прочности при сжатии не будет соответствовать указанному испытания повторить через 7 суток.
Входной и операционный контроль осуществляется представителем ОКК с последующим предъявлением представителям осуществляющим надзор за постройкой судна.
Поступившие от предприятий-изготовителей материалы должны иметь документы подтверждающие соответствие их качества требованиям технических условий и стандартов.
Качество материалов на соответствие требованиям технических условий и стандартов контролировать:
-при получении от предприятий-изготовителей;
-перед выдачей со склада в цех спецпокрытий в течении гарантийного срока хранения;
-по истечении срока хранения.
Перечень операций подлежащих контролю по разделу 2.8. приведен в таблице 4.
Замеры температуры компонентов готовой полимерной смеси выполнять термометром фирмы ELCOMETER модель 113-1 все замеры заносить в графу «температура пластмассы».
Контролируемая операция
Подготовка контактирующих
с полимерным материалом
Визуальный с эталонным
Пригодность компонентов
в соответствии с требованиями
Проверка сертификатов
и паспортов испытание на
прочность с определением
разрушающего напряжения
Количественный состав
соответствии с расчетом
Взвешивание компонентов
с погрешностью не более
Приготовление полимерного
материала в соответствии
с требованиями п. 2.8.2
Визуальный измерительный
Заполнение монтажного
зазора в соттветствии с
требованиями п. 2. 8.3.
Качество отвержденного
полимерного материала в мон-
Испытание на прочность
образцов путем определе-
ния разрушающего напря-
ГОСТ 4651 которое не
должно быть менее 50 МПа
2.6. Монтаж гребного вала с ВРШ.
Гребной вал поставляется с установленной ступицей гребного винта и маслопроводами а фланцевая муфта вала поставляется незатянутой. Центр тяжести сборки указан на чертеже ДП.141200-03-164.01.07СХ. Подъем можно осуществить при помощи стропов и крана по схеме показанной на том же чертеже.
Установить приспособления для погрузки гребного вала проверить установку технологического монтажного подшипника ДП.141200-03-164.01.06.СБ по оси валопровода и положение фундамента под ДГ по полушироте.
На период транспортировки гребной вал надлежащим образом защищается посредством применения антикоррозионного состава и деревянной обрешетки. Размещение подъемных строп отмечено на деревянной обрешетке.
Перед установкой гребного вала вся упаковка должна быть снята.
Расконсервировать гребной вал необходимо тщательно очистить от антикоррозионного защитного состава промыть шейку гребного вала уайт-спиритом ГОСТ 3134 покрыть солидолом ГОСТ 1033 и проверить на наличие повреждений полученных при транспортировке. После проверки вал необходимо вставлять с чистым маслом. После снятия антикоррозионного покрытия необходимо как можно скорее установить вал в дейдвудной трубе.
Вал устанавливается в дейдвудной трубе в его окончательное осевое положение посредством блоков и строп. Соприкосновения стальных строп с валом не допускается. Во время установки необходимо обратить особое внимание на втулки дейдвудной трубы и на защитную трубу датчика температуры.
Погрузить гребной вал по схеме погрузки черт.ДП.141200-03-164.01.07.СХ. При заводке вала не допускать подрыва рабочей поверхности подшипника торцем облицовки (шейки) вала. Постоянно вести контроль по водяному зазору между валом и подшипником. Установить на вал неразъемные детали дейдвудного сальника. Уложить вал в технологический монтажный подшипник предварительно выставленный по оси линии вала.
Запрещается крепить тали лебедки или другие подъемные устройства к тяге осевой передачи усилий или к маслопроводу в переднем конце вала. Это может привести к повреждению системы регулируемого шага винта.
Измерить верхний водяной зазор между валом и подшипником и прилегание вала к подшипнику в нижней части. Величину зазоров и прилегание проверять с кормы. Величина монтажного зазора между гребным валом и подшипником должна быть в пределах 15-18 мм при этом разность боковых зазоров не должна превышать половины верхнего водяного зазора.
Сдвинуть гребной вал в корму на 500 мм для установки и напрессовки полумуфты.
Гребной вал должен быть отмаркирован внутри судна чтобы определить правильное осевое положение относительно переборки. Вал должен быть закреплен в его окончательном положении. Это можно сделать с помощью нейлоновых строп.
Установка лопастей винта.
Гребные винты поставляются со ступицей установленной на гребной вал при установленных лопастях. Если же лопасти не установлены то необходимо осуществить монтаж лопастей к ступице до установки гребного вала.
Во время транспортировки временные защитные пластины оберегают места уплотнения лопастей винта в ступице. После снятия этих пластин чрезвычайно важно не допустить попадания грязи в ступицу. Грязь может вызвать повреждение уплотнения и как следствие утечку масла.
Перед установкой лопастей резьба на дисках кривошипа и на болтах лопастей должна быть очищена и содержаться в чистоте. Для лопастей должны применяться надлежащие подъемные тали.
Необходимо тщательно очистить и высушить паз для сальника комля лопасти в ступице. Нужно нанести немного смазочного масла на уплотнительное кольцо. После чего устанавливают уплотнительное кольцо в паз и наносят немного минеральной смазки на беговые поверхности сальника комля лопасти.
Устанавливают лопасть в положение на ступице и наносят минеральную смазку на уплотнительные кольца болтов лопасти.
Болты крепления лопасти (6 шт.) устанавливают в соответствии с крутящим моментом указанным на чертеже ступицы винта.
Крепежную деталь устанавливают как можно ближе на комле лопасти у каждого болта лопасти и приваривают ее к лопасти.
2.7. Монтаж полумуфты.
Промыть посадочные поверхности ступицы полумуфты и вала уайт-спиритом и протереть бязевыми салфетками. Смазать посадочные поверхности ступицы и вала турбинным маслом Т-46 или индустриальным ГОСТ 20799.
Развернуть гребной вал так чтобы риска спаривания находилась вертикально вверху. Установить на конус вала полумуфту продвинуть до упора. Риски спаривания на валу и полумуфте должны находиться на одной линии.
Установить прокладку (8) навинтить гайку (10) предварительно смазав резьбу на валу графитной смазкой затянуть гайку (10) черт. ДП.141200-03-164.01.08.СХ.
Подключить пневмогидравлический насос (5) (поставляемый в комплекте с ВРШ) к отверстию (2) на полумуфте (черт.ДП.141200-03-164.01.08.СХ) свинтить вторую пробку для вентиляции и закачать масло в камеру соединительного фланца. Закачку выполнять до тех пор пока из вентиляционного отверстия не начнет выходить масло без воздуха. Навинтить на вентиляционное отверстие пробку (9) черт. ДП.141200-03-164.01.02.СБ
Поднять давление в камере соединительного фланца до 100-120 кгссм2.
Проверить герметичность уплотнительного узла.
Установить на кормовой торец полумуфты индикатор ИЧ-10 часового типа на магнитной стойке (4) черт.ДП.141200-03-164.01.08.СХ для замера осевого перемещения полумуфты относительно вала.
Установить и подключить масляный инжектор (1) (поставляемый в комплекте с ВРШ) в отверстие (5) черт.ДП.141200-03-164.01.02.СБ и закачать масло. Закачку продолжить до тех пор пока оно не выступит на кормовой стороне муфты по всему периметру.
Установить стрелку индикатора в нулевое положение. Продолжить напрессовку полумуфты на конус вала гидропрессовым способом с одновременной подачей масла на сопрягаемые поверхности инжектором. Контроль напрессовки производить по величине осевого перемещения.
Полумуфта считается напрессованой если расстояние отметки на валу до кормового торца полумуфты будет равным 300 мм а торец стопорной гайки и фланца полумуфты должны находиться на одной линии.
После окончательной напрессовки полумуфты снять давление масла с сопрягаемых конических поверхностей для чего открыть перепускной клапан на инжекторе. Через 10-15 мин снять давление с гидронасоса демонтировать гидронасос установить на место пробки (5 9) черт. ДП.141200-03-164.01.02.СБ.
Завинтить круглую гайку на фланце муфты.
Просверлить два отверстия разнесенных на 180 0 нарезать резьбу М8 на глубину 10 мм согласно узла Б черт.ДП.141200-03-164.01.08.СХ для стопорения гайки (10) от самопроизвольного отвинчивания. Ввинтить стопорные винты (9).
Параметры напрессовки полумуфты:
) осевое перемещение – 136 мм;
) давление подаваемое на сопрягаемые поверхности - 800 кгсм2;
) максимально допустимое давление на сопрягаемые поверхности – 1020 кгсм2. Допускается увеличение давления подаваемого на сопрягаемые поверхности до 10% .
Результаты напрессовки полумуфты и предъявить ОКК.
По окончании напрессовки развернуть фланец полумуфты относительно фланца редуктора по рискам спаривания.
Проверить установку гребного вала по растяжке. При этом кольцевой зазор между торцом дейдвудной трубы и кормовым торцом фланца гребного вала должен быть в пределах 50 100 мм.
В качестве среды давления используйте чистое минеральное масло SAЕ 20ISO VG 46. Сборка должна производиться при комнатной температуре. Если температура ниже 5-10 градусов С нагрейте муфту по крайней мере до 20 градусов С.
Данная процедура полностью противоположна процедуре установки. Чтобы предотвратить загрязнение совмещающихся поверхностей тщательно очистите вал перед отведением муфты. Выполняйте смазку вала маслом не содержащим антифрикционных добавок.
Последовательность демонтажа полумуфты. ДП.141200-03-164.01.08СХ.
В процессе монтажа движительного комплекса требуется спрессовка полумуфты которую следует произвести в соответствии со следующими рекомендациями:
Сначала необходимо проверить следующее:
Наличие сжатого воздуха под давлением 6-7 бар как вариант можно использовать азот из баллона с таким же давлением после редуктора.
Наличие масла для инжектора и гидравлического насоса
Снять стопорные винты; убедится что фланец муфты и вал замаркированы(см. чертеж).
Подключить гидравлический насос с пневмоприводом со стороны фланца открыть вентиляционное отверстие и закачивать масло в камеру фланца муфты до тех пор пока чистое масло без воздуха не будет выходить из вентиляционного отверстия; затем закрыть вентиляционное отверстие.
Подключить масляный инжектор в соответствующее отверстие
Запустить гидравлический насос с пневмоприводом. Медленно отвернуть круглую гайку до положения: (длина посадки + 5мм). См. чертеж ДП.141200-03-164.01.08СХ. Закачку масла в камеру фланца муфты для того чтобы уплотнительная шайба постепенно двигалась вместе с круглой гайкой.
Прокачивать масло между конусов при помощи инжектора масла до тех пор пока оно полностью не покроет все соприкасающиеся поверхности и начнет выступать по периметру ступицы.
С кормовой стороны фланца муфты установить индикатор часового типа с делением 001 мм на магнитной подставке.
Увеличивать давление гидравлического насоса пока фланец муфты не отойдет вверх приблизительно на 02 мм.
Постепенно открыть возвратную линию пневмоприводного насоса и продолжать закачивать масло инжекторами так чтобы муфта медленно сползла с вала.
Если будет трудно освободить фланец муфты необходимо использовать в масляных инжекторах масло большей вязкости.
Демонтируйте круглую гайку и уплотнительную шайбу. Не снимайте шайбу пока полностью не ослабите соединение. Необходимо следить чтобы фланец муфты не соскользнул с вала.
Установка соединительных болтов.
Соединительные болты сконструированы с небольшим допуском для посадки (болт f6 отверстия Н7). Поэтому важно строго следовать инструкции по затяжке болта.
Перед установкой болтов убедитесь что:
- фланцевая муфта находится в своем крайнем положении на валу
- маслопровод внутри муфты подсоединен (если применяется)
- уплотнительное кольцо установлено на поверхности фланца
- вся работа по центровке закончена и очищена
Поместите домкрат под фланец вала и отрегулируйте высоту фланца чтобы она соответствовала положению прилегающего фланца.
Проворачивайте прилегающий фланец пока не совпадут отверстия.
Установите болт в одно из отверстий которые размещаются приблизительно в горизонтальном положении. Если необходимо отрегулируйте высоту с помощью домкрата. Для выполнения горизонтальной регулировки пользуйтесь деревянной доской.
Нанесите графитную смазку на верхнюю часть болтов на резьбу и под гайки.
При установке болтов не следует прилагать чрезмерное усилие.
Установите болт расположенный диаметрально противоположно первому. Если необходимо подгоните с помощью домкрата.
Установите болты в верхней и нижней части фланца. Если необходимо подгоните с помощью домкрата.
Слегка затяните все 4 болта.
Сейчас домкрат можно убрать и установить все остальные болты. Не забывайте использовать графитную смазку - наносите на головки болтов на резьбу и под гайки.
Производите затяжку болтов (гаек) крест-накрест с помощью ключа на котором установлена величина усилия соответствующая моменту вращения указанному на чертеже соединительных болтов.
Чтобы убедиться что поверхности фланца полностью соединены обстучите головки болтов молотком и проверьте еще раз предварительно установленное усилие на ключе.
Окончательное усилие затяжки болта может быть достигнуто или затяжкой с контролируемым углом или затяжкой с контролируемым моментом вращения. Фактическая величина момента вращения и величина угла крутящего момента указаны в чертеже для болтов.
Затяжка с контролируемым моментом вращения
Затяните болты (гайки) крест-накрест при помощи ключа с установленным усилием момента вращения на величину указанную в чертеже для болтов.
Затяжка с контролируемым углом
Отмаркируйте угол момента вращения снаружи гайки и затяните болты (гайки) крест-накрест с помощью инструментов какие вам удобно.
Если производится замена этим соединительным болтом существующего болта данная инструкция и чертеж заменяют соответствующую инструкцию в документации поставленной для установки узла винта.
2.8. Проверка параметров центровки гребной вал-редуктор.
Проверить параметры центровки гребной вал - редуктор. Проверку выполнять по излому и смещению с помощью двух пар стрел устанавливаемых на фланцы полумуфты и редуктора. При необходимости выполнить подцентровку редуктора к гребному валу за счет перемещения редуктора (гребной вал является базовым).
Порядок центровки редуктора относительно гребного вала:
)установить стрелы для проверки центровки с индикаторами;
)выставить стрелки индикаторов в нулевое положение с предварительным натягом 4-5 мм;
)вращая одновременно гребной вал и редуктор отцентровать редуктор в допуски (см. технологию на монтаж редуктора). Замеры снимать при повороте валов на 3600 через каждые 900 – верх низ Пр.Б. Л.Б; Результаты центровки занести в таблицу 3 и предъявить службе технического контроля.
)при проверке центровки конец вала находится в монтажном технологическом подшипнике предварительно отцентрованном по оптической оси.
Не допускается проворачивание валов производить без предварительной смазки посадочной поверхности технологического монтажного подшипника – для исключения повреждения облицовки вала.
Окончательный демонтаж подшипника выполнять после сдачи окончательной центровки на плаву и сборки фланцевых соединений гребной вал-редуктор.
Центровка валопровода с редуктором по двум парам стрел.
Деистви-тельная величина зазора
2.9. Проверка зазоров между насадкой и лопастями ВРШ.
При проверке зазоров между кромками лопастей винта и внутренней обшивкой насадкидолжен быть в пределах 16-18 мм. В соответствии с проектными данными:
-диаметр внутренней обшивки
в плоскости диска винтаD27320 мм
-диаметр входной кромкиDI31360 мм
-диаметр выходной кромкиDII28960 мм
-длина профиля насадкиl15550 мм
Сечение по диску винта
Рис.17. Схема замеров движительного комплекса винт-насадка.
Условные обозначения:
- зазоры между конечными кромками лопастей винта и внутренней обшивкой насадки в районе диска винта замеренные при положении лопасти №1 вертикально вниз;
- вышеобозначенный зазор замеряемый постановкой лопасти №1 последовательно в положения от 2го до 12го;
- длина профиля насадки в сечении определяемом номером радиуса;
- диаметр внутренней обшивки насадки в плоскости диска винта (для ВРШ при развороте лопастей в положение соответствующее максимальному диаметру винта) в сечении определяемом номерами радиусов;
- диаметр входной кромки насадки в сечении определяемом номерами радиусов;
- диаметр выходной кромки насадки в сечении определяемом номерами радиусов.
2.10. Последовательность монтажа МИШ.
2.10.1. Последовательность монтажа маслораспределительной коробки.
Монтаж и демонтаж маслораспределительной коробки лучше производить когда труба подачи масла находится в самом ближнем к корме положении т.к. для монтажа требуется место. Выполнять монтаж следет в следующем порядке:
Снять маслораспределительную коробку с трубки подачи масла.
Нанести стопорный состав Loctite и установить винты поз.38 (См. чертеж ДП.141200-03-164.01.04СБ)
Нанести стопорный состав Loctite и установить винты поз.11.
Нанести стопорный состав Loctite и установить крышку поз.33 при помощи винтов поз.25.
Подсоединить трубы и электрокабели.
Установить пробку сливного отверстия поз.2.
В случае необходимости демонтажа маслораспределительную коробку демонтируют в следующей последовательности:
Установить внутреннюю трубу подачи масла в крайнее кормовое положение.
Слить масло из напорной емкости системы гидравлики.
Слить масло системы гидравлики сняв пробку сливного отверстия поз.2.
Отсоединить трубы и электрокабели.
Снять крышку поз.33 с винтами поз.25.
Теперь маслораспределительная коробка может скользить и ее можно снять.
2.10.2.Соединение внутренних подвижных маслопроводов.
Трубы масла должны выступать из одного из валов на расстояние необходимое для подсоединения.
Подвижный маслопровод внутри гребного вала может вращаться по отношению к цилиндрической кулисе в ступице.
Для выполнения операции необходимо использовать ключ для соединения трубопроводов и удерживайте противоположный подвижный маслопровод ключом до тех пор пока его срез выступает.
Необходимо использовать требуемый момент затяжки чтобы быть уверенным в том что муфта соединения трубопроводов и подвижный маслопровод плотно зажаты.
Зафиксировать муфту соединения трубопроводов и подвижный маслопровод установочным винтом. Это производится следующим образом:
-В муфте соединения трубопроводов просверлено отверстие с нарезанной резьбой если потребуется произвести прогонку резьбы;
-Убедиться что внутри вала не осталось никаких частиц металла;
-Застопорить установочный винт стопорным составом Loctite и закернить его ручным керном в 2-х местах.
Работу следует производить очень осторожно чтобы не повредить детали и не нарушить калибровку.
2.10.3. Регулировка шага во время сборки.
Чтобы изменить шаг до требуемого положения подвижный маслопровод должен быть временно соединен с трубой в редукторе. Для регулировки применяется подсобный инструмент. Посредством последнего масло может быть закачено в вал насосом высокого давления с пневмоприводом который используется для установкидемонтажа гидравлически устанавливаемой муфты.
Подвижный маслопровод в гребном вале должен находится в крайнем переднем положении (лопасти винта в положении шага полный назад) для (повторной) сборки и фиксации с маслопроводом в сервоприводе управления шагом. Если по какой-то причине маслопровод не будет находиться в указанном положении то его следует установить в это положение.
Для того чтобы установить шаг винта в требуемое положение подвижный маслопровод временно нужно соединить с трубкой в редукторе. Направляющая втулка сервопривода управления шагом (поз.35) ДП.141200-03-164.01.04 СБ и трубка подачи масла (поз.34) должны быть уже смонтированы. При помощи механизма для аварийной регулировки шага винта масло может закачиваться в вал насосом высокого давления с пневмоприводом который используется для монтажа фланцевой муфты с гидравлической напрессовкой. Однако давление воздуха (6-8 бар) подающегося судовым насосом должно быть снижено до 2-х бар. Если не соблюсти это условие то слишком высокое давление масла в системе гидравлики приведет к повреждению. Затем можно достигнуть правильного положения цилиндрической кулисы а следовательно внутреннего маслопровода. Переходник к соединительному штуцеру насоса поставляется вместе с инструментом.
2.11. Монтаж дейдвудного сальника
Монтаж дейдвудного сальника производить после окончательного закрепления дейдвудной трубы и сдачи центровки валопровода на стапеле.
До начала монтажа сальника проверить перпендикулярность торца дейдвудной трубы относительно оси вала. Не перпендикулярность не должна превышать 0.2 ммм. Результаты измерений занести в таблицу.
Сдвинуть корпус сальника до упора в торец дейдвудной трубы. Ввинтить болты крепления дейдвудного сальника к трубе.
Измерить диаметральный кольцевой зазор под набивку между валом и корпусом. Разность зазоров измеренных в четырех взаимно-перпендикулярных точках по окружности не должна отличаться более чем на 25 % диаметрального зазора между корпусом и валом.
Установить в зазор сальниковую набивку. Стыки колец сальниковой набивки должны быть обрезаны под углом 900. Набивку уложить так чтобы стыки были расположены под углом не менее 900 .
Сдвинуть по валу кольцо уплотнительное установить в корпусе сальника установить фланец. Ввинтить шпильки болты крепления фланца к корпусу сальника. Навинтить гайки.
Сдвинуть по валу и установить на шпильки втулку промежуточную. Установить в зазор сальниковую набивку.
Сдвинуть по валу втулку нажимную сальника завести шпильки в корпус сальника навинтить гайки равномерно обжать. Контроль обжатия втулки нажимной осуществлять измерением размера между торцом втулки и торцом втулки нажимной .
Проверить легкость вращения зубчатого соединения: собранное зубчатое соединение должно свободно вращаться от руки.
Предъявить ОКК и Регистру окончательный монтаж дейдвудного сальника.
2.12. Монтаж тормоза.
Погрузить в помещение тормоз.
Разогнуть и вынуть шплинты выбить одну нижнюю ось вывинтить ось-гайку снять тормозную ленту.
Установить тормоз на фланец полумуфты. Собрать тормозную ленту вставить оси зашплинтовать.
Затянуть ленту тормоза стяжным винтом заданным усилием 20 кН.м (2000 кгс.м). Проверить прилегание тормозной ленты к фланцу вала. При этом пластина щупа толщиной 01 мм не должна проходить по всему периметру. Измерить расстояние между фундаментом и опорными лапами тормоза в местах расположения выравнивающих прокладок. Измерения выполнять по четырем углам каждой полки фундамента. Результаты измерений высоты прокладки занести в таблицу. Изготовить выравнивающие прокладки с припуском 01 мм маркировать местом их установки. Маркировку нанести на торце прокладки.
Пригнать выравнивающие прокладки по месту. При этом при незатянутых крепежных элементах по периметру между прокладками и фундаментом а также между прокладками и опорными лапами тормоза зазор не должен превышать 01 мм. Допускается на 13 периметра прохождение пластины щупа толщиной 03 мм.
Закрепить с помощью электросварки выравнивающие прокладки к фундаменту.
Просверлить отверстия через лапы подшипников в прокладках и фундаменте диаметром 26 мм. Закрепить тормоз на фундаменте двумя болтами.
Развернуть два отверстия в лапе тормоза прокладке и фундаменте до 28 мм под призонные болты с припуском под чистовую развертку. Развернуть чистовой разверткой отверстия до 28Н7. Измерить длину и диаметр призонной части болтов изготовить болты. Предъявить ОКК отверстия и призонные болты.
Протереть чистой бязевой салфеткой отверстия и призонные болты смазать цилиндрические поверхности и резьбу болтов графитной смазкой ГОСТ 1033. Запрессовать призонные болты. Согласно маркировке в отверстия. Работы по запрессовке призонных болтов выполнять в присутствии ОКК.
Навинтить и обжать гайки крепления тормоза. Окончательный монтаж тормоза предъявить ОКК и Регистру.
2.13. Проверка центровки валопровода на плаву.
После спуска судна на воду выполнить проверку центровки валопровода с ДРА.
Проверку центровки валопровода на плаву производить при водоизмещении 85% водоизмещения судна при погруженных основных тяжеловесных механизмах массой более 1% общей массы механизмов и устройств в районе машинного отделения.
Разобрать соединение: полумуфта гребного вала и редуктор. Проверить центровку. При необходимости подцентровать редуктор относительно полумуфты гребного вала. Работу выполнять по технологии на монтаж ДРА. Результаты измерений предъявить ОКК и Регистру. Собрать фланцевое соединение гребного вала и редуктора. Демонтировать технологический монтажный подшипник.
Термическое расширение влияющее на центровку редуктора.
Для достижения центровки в горячих рабочих условиях корпус редуктора следует установить ниже общего эквивалента термического подъема. Термическое расширение редуктора взято как 008 мм при подъеме температуры от 20 º до 70 ºС.
Когда температура редуктора отличается от предполагаемой в этом отчете правильное значение смещения может определяться интерполяцией теплового расширения редуктора. Разница сдвига между существующей и предполагаемой температурой может быть добавлена к значению смещения. Значение излом неизменно для всех температурных режимов.
2.14. Монтаж кожуха.
Измерить расстояние от торца фланца дейдвудной трубы до наружной поверхности яблока ахтерштевня. Измерения выполнять через 300 в районе расположения бонок кожуха. Результаты измерений занести в таблицу 4. Вычислить зазор между обтекателем и ступицей гребного винта для определения высоты пяты (бонки).
Маркировать бонки местом их установки на кожухе. Пример маркировки: 1В- где 1 номер по порядку; В-бонка верхней половины кожуха.
Подогнать бонки по размерам полученным при вычислении.
В случае если зазор более допустимого по чертежу выполнить подрезку бонок. Если зазор меньше допустимого бонки изготовить новые по фактическим размерам.
Установить и закрепить на половинах кожуха бонки (2) с помощью болтов согласно маркировки нанесенной на бонках и кожухе.
Установить верхнюю половину кожуха на торец яблока ахтерштевня Поджать половину кожуха
Установить нижнюю половину кожуха на торец яблока ахтерштевня. Поджать половину кожуха к яблоку и прихватить три бонки на эл.прихватках. Измерить зазор между ступицей гребного винта и обтекателем в районе расположения бонок. При этом зазор должен быть в пределах 12+10 мм.
Срубить эл.прихватки демонтировать половины кожуха
Приварить бонки к кожуху.
Установить половины кожуха на торец яблока ахтерштевня согласно нанесенной маркировки. Приварить бонки к торцу яблока ахтерштевня согласно т.тр. черт.
Предъявить ОКК установку кожуха и зазор между ступицей гребного винта и кожухом.
Результаты замеров.
Примечание. Высота бонки по чертежу - 400 мм.
3.Средства технологического оснащения
применяемые при монтаже.
Перечень применяемой оснастки.
Оснастка для пробивки оптической оси.
Кронштейн для трубы ППС
Крестовина для крепления мишеней
Опора временная для центровки валов
Стрелы для центровки
Схема заливки пластмассы
Оснастка для смешивания и заливки пластмассы
Оснастка для укупорки торцев подшипников при заливке полимерного материала
Пневматические развертки
Ключи с заданным крутящим моментом
Машинки пневматические зачистные.
Ручной гидравлический насос
Индикатор часового типа ИЧ-10
Нутромер микрометрический
Штатив магнитный ШМ 11 Н-8
Кран мостовой гп 15 т (Цех 10)
Аппарат дробеструйной очистки
Радиостанция (транковая связь)
1.Разработка технолого-нормировочной карты
монтажа движительного комплекса траулера.
ТНК(технолого-нормировочная карта) разрабатывается технологическими службами. В них технологами проставляется содержание работ по операциям объём работ и другие данные. Отнормированное ТНК утверждается директором предприятия и служит основным документом для выполнения рабочих нарядов.
Составим ТНК на монтаж валопровода траулера пр.50010.
Технолого-нормировочная карта монтажа.
Наименование операции
Кол-во работающих (челразряд)
Продолжительность работы (дни)
Пробивка оси линии вала
Разметка мест установки кронштейнов изготовление и установка кронштейнов в районе 39 45 52 59 шп.
Установка мишеней в кронштейны натяжение струны имитирующей ось линии вала. Центровка оправы установленной в кронштейн на 59шп.Разметка нанесение контрольных окружностей на торце ахтерштевня
Снятие струны установка оптической трубы ППС. Центровка трубы ППС по оси линии вала. Центровка промежуточных мишеней (45 52шп) по оси трубы ППС
Установка фундаментов под расточной станок установка расточного станка центровка по контрольной окружности на ахтерштевне и оси линии вала
Демонтаж трубы ППС расточка ахтерштевня под установку яблока ахтерштевня
Установка трубы ППС центровка по перекрестию мишени на 39 шп.. Установка промежуточных мишеней центровка по оси трубы
Установка приварка яблока ахтерштевня
Установка яблока в расточку ахтерштевня. Установка крестовин с мишенями по торцам яблока. Центровка яблока ахтерштевня относительно оси ЛВ
Приварка яблока ахтерштевня по технологии отдела главного сварщика с контролем положения яблока при сварке
Монтаж (приварка) насадки ( по технологии корпусо-сборочного производства)
Пробивка (проверка) оптической оси ЛВ
Изготовление расточка посадочных поверхностей подшипника
Дробеструйная очистка внутренней поверхности дейдвудной трубы
Дробеструйная очистка наружной поверхности подшипника
Напрессовка и крепление подшипника в дейдвудную трубу
Установка дейдвудной трубы и монтажного технологического подшипника по оси линии вала.
Установка теодолита проверка положения корпуса судна в районе машинного отделения до монтажа дейдвудной трубы
Установка грузов имитирующих недостающее оборудование в районе машинного отделения
Проверка положения корпуса судна в районе машинного отделения до монтажа дейдвудной трубы
Заводка дейдвудной трубы в яблоко ахтерштевня с неразъемными деталями (гайки крепления дейдвудной трубы) и вварышем
Центровка дейдвудной трубы по оси линии вала
Предварительный монтаж вварыша к переборке ( приварка вварыша к переборке в 4х точках)
Окончательная приварка вварыша к переборке
Окончательная заводка дейдвудной трубы в штатное положение.
Снятие имитирующих грузов
Фиксация дейдвудной трубы отжимными болтами
Проверка положения корпуса судна в районе машинного отделения после монтажа дейдвудной трубы.
Установка оснастки под заливку пластмассы. Уплотнение торцев дейдвудной трубы и вварыша.
Приготовление пластмассы под заливку монтажных зазоров взятие образцов пластмассы для испытания
Заливка пластмассы в зазоры расточки ахтерштевня вварыша и дейдвудной трубы
Спресовка полумуфты консервация посадочных поверхностей.
Установка оснастки под погрузку гребного вала.
Погрузка гребного вала с ВПЛ установка неразъемных деталей дейдвудного сальника
Расконсервация напрессовка полумуфты
Установка оснастки для проверки центровки редуктора с гребным валом
Проверка центровки гребной вал-редуктор проверка водяных зазоров подш. зазоры между насадкой и лопастями ВПЛ
Окончательная фиксация и срезка отжимных болтов дейдвудной трубы и вварыша. Обварка
Крепление дейдвудной трубы к торцу яблока ахтерштевня
Сборка внутреннего трубопровода МИШ
Монтаж маслораспределительной коробки
Сборка внутреннего трубопровода МИШ с регулировкой положения лопастей ВРШ
Проверка центровки гребной вал-редуктор подцентровка.
Предварительный монтаж дейдвудного сальника проверка перпендикулярности и соосности корпуса относительно вала
Окончательный монтаж дейдвудного сальника
Приварка платиков фундамента тормоза обработка платиков
Предварительный монтаж тормоза измерение пригоночных прокладок
Изготовление пригоночных прокладок
Окончательный монтаж тормоза
Пригонка и монтаж кожуха
Закрытие построечного документа
Проверка центровки подцентровка редуктора относительно гребного вала окончательный монтаж линии вала
В том числе по разрядам:
Трудоёмкость измеряют в нормо-часах. Нормо-час выражает произведение нормированной продолжительности работы в часах на число рабочих необходимых для выполнения этой работы.
Норма времени должна предусматривать наиболее экономичный способ выполнения заданной работы отвечающей современному уровню техники рациональной организации производства и передовым методам труда.
По мере развития техники совершенствования технологического процесса и организации производства повышается производительность труда и соответственно изменяются нормы времени.
При определении трудоемкости (нормы времени) выполнения работ по предусмотренным технологическим операциям применяются технические обоснованные нормы времени определяемые на основании действующих на судостроительном предприятии нормативах.
Таблицы нормативов времени coдержaт штучно-калькуляционное время которое включает в себя следующие составные части:
-подготовительно-заключительное время;
-время организационно-технического обслуживания рабочего места;
-время на отдых и личные надобности.
Подготовительно-заключительное время включает затраты на:
-получение и сдачу задания наряда технологической документации инструмента приспособлений и оснастки;
-ознакомление с заданием технологической документацией чертежами;
-получение инструктажа мастера перед началом работы;
-подключение и отключение инструмента и осветительной сети перед началом работы и в конце смены;
-уборку рабочего времени в конце смены.
Оперативное время включает затраты на выполнение работы предусмотренной заданием и состоит из суммы основного и вспомогательного времени.
Время организационно-технического обслуживания рабочего места включает затраты на:
-переходы в процессе работы;
-подключение и отключение механизированного инструмента и осветительной сети в процессе работы;
- регулирование наладку и смазку оборудования в процессе работы;
- обеспечение безопасных условий труда на рабочем месте;
- раскладку инструмента и уборку его в процессе работы в течение смены;
-смену смазку и заточку инструмента;
-уборку рабочего места в течение смены;
- инструктаж мастера в процессе работы.
Время на отдых и личные надобности установлено в размере 8% (на работы связанные с применением виброопасного инструмента - 13%) от оперативного времени и учитывает время производственной гимнастики.
2. Расчёт массы компонентов
для приготовления полимерного материала
заливаемого в монтажные зазоры.
Масса компонента Мi в г. необходимая для приготовления полимерного материала в соответствии с ОСТ.5.99.66-85 [19] определяется по формуле:
m - количество компонентов в полимерном материале;
V - заполняемый объём состоящий из объёма монтажного зазора и объёма шланга соединяющего пресс с литником см3.
Коэффициент n принимается равным 115-125 при этом большие значения коэффициента должны соответствовать меньшим значениям заливаемого объёма.
Вкладная дейдвудная труба устанавливается в яблоке ахтерштевня и в вварыше.
Так как диаметр гребного вала до 250 мм то в соответствии с ОСТ 5.9966-85 величина монтажного зазора 10-15мм.
Характеристики компонентов для приготовления полимерного материала
Модифицированная К-153
По формуле (2) найдем объем монтажного зазора между яблоком ахтерштевня и дейдвудной трубой.
V=314 × 990(202-192) = 314 × 990 × 39 = 121297см3.
Определим массу компонентов для заполнения этого монтажного зазора по формуле (1).
Смола эпоксидная модифицированная К-153
M1=120 × 121297 = 10594 г = 1059кг.
Кварц молотый пылевидный
M2=120 × 121297 = 10152 г = 1059кг.
M3=120 × 121297 = 1271г = 127кг.
Найдем массу полимерного материала необходимого для заливки монтажного зазора между яблоком ахтерштевня и дейдвудной трубой:
MЯ.А. = M1 + M2 + M3 = 1059 + 1059 + 127 = 2245 кг
Найдем объем монтажного зазора между вварышем и дейдвудной трубой.
V=314 × 150(202-192) = 314 × 150(400 - 361) = 18378см3.
Определим массу компонентов для заполнения этого монтажного зазора.
M1=120 × 18378 = 1605 г = 161кг.
M2=120 × 18378 = 1605 г = 161кг.
M3=120 × 18378 = 1926г = 019кг.
Найдем массу полимерного материала необходимого для заливки монтажного зазора между вварышем и дейдвудной трубой
M В.= M1 + M2 + M3 = 161 + 161 + 019 = 341 кг
Найдем объем потерь полимерного материала в шланге при его длине 150 см и диаметре 30 см. :
V= 314 × 152 × 150 = 1060 см3.
Определим массу компонентов.
M1=120 × 1060 = 926 г = 093 кг.
M2=120 × 1060 = 926 г = 093 кг.
M3=120 × 1065 = 112 г = 001кг
Найдем массу полимерного материала теряемого в шланге.
M Ш.= M1 + M2 + M3 = 093 + 093 + 001 = 187 кг
Общая масса компонентов для полимерного материала:
M1= 1059 + 161 + 093 = 1313 кг
M2= 1059 + 161 + 093 = 1313 кг
M3= 127 + 019 + 001 = 147 кг
Масса компонентов необходимых для приготовления полимерного материала.
Кварц молотый пылевидный
Полиэтилен - полиамин
Общая масса полимерного материала
Примечание: масса указана с учетом запаса на потери.
3. Расчёт технических параметров
напрессовки фланцевой полумуфты.
Для расчёта технических параметров напрессовки полумуфт валопровода необходимы следующие исходные данные:
-номинальный крутящий момент на валу (М) по расчету.
-большой диаметр конуса вала (D) – 210 мм;
-диаметр расточки конуса вала (d) - 100мм
-длина контакта сопрягаемых конических поверхностей (L) – 380 мм;
-конусность соединения (к) - 0014
-средний диаметр конуса вала (D ср.) - 206 мм
-наружный диаметр полумуфты в среднем сечении (D н) - 345 мм
-материал вала – 38Х2Н2МА;
-материал полумуфты - 40ХН2МА
-коэффициент запаса несущей способности соединения для судна с ледовым усилением Л3 в соответствии с ОСТ5.9670-92 (Приложение 1)[18] n = 42.
Определим номинальный крутящий момент на валу:
гдеN – мощность на валу Вт
n – число оборотов гребного вала обмин.
Расчёт технических параметров напрессовки полумуфт валопровода ведётся в соответствии с ОСТ5.9670-92 (Приложение 6).
Момент сопротивления вала кручению в сечении по среднему диаметру конуса для полого вала определяется по формуле
Напряжение кручения в материале вала в сечении по среднему диаметру конуса от действия номинального крутящего момента:
где М – номинальный крутящий момент Нм;
W – момент сопротивления вала кручению в сечении по среднему диаметру конуса для полого вала.
Величина контактного давления на сопрягаемых конических поверхностях определяют по формуле:
где Lф - фактическая длина контакта сопрягаемых конических поверхностей учитывающая уменьшение длины соединения за счет маслораспределительных канавок проточек и т.д. м
fT – коэффициент трения при осевом смещении деталей по ОСТ5.9670-92 Приложение 1 табл. 2 принимаем для пары трения сталь-сталь fT = 015.
Из условия обеспечения стабильности коэффициента трения при сборке и эксплуатации бесшпоночных соединений деталей валопроводов значение контактного давления на сопрягаемых
поверхностях q должно быть во всех случаях не менее 40 МПа.
Величина диаметрального натяга в соединении определяется по формуле:
где – диаметральный натяг в соединении м;
Е1 Е2 – модули упругости материала вала и охватывающей детали (соответственно) МПа;
С1 С2 – коэффициенты жесткости вала и охватывающей детали
С1=А - 1 С2=В - 2 ;(9)
где1 2 – коэффициенты Пуассона материала вала и охватывающей детали
А В – безразмерные коэффициенты зависящие от степени расточки вала и охватывающей детали можно определить по формулам:
В соответствии с формулой (8):
Осевое перемещение полумуфты по конусу вала при окончательной насадке определяют по формуле:
где – величина диаметрального натяга
k – конусность соединения
В соответствии с формулой (10):
S=k=13610-40014=13610-4м= 136мм
Усилие предварительной напрессовки полумуфты на конус вала для определения начального положения определяют по формуле
где Fф – фактическая площадь контакта Fф сопрягаемых конических поверхностей м2.
Для бесшпоночного соединения определяется по формуле:
Fф=3140206035=0226 м2
Усилие окончательной напрессовки полумуфты с подачей масла на сопрягаемые конические поверхности определяют по формуле
где Р – давление масла на сопрягаемых конических поверхностях бесшпоночного соединения МПа.
По ОСТ 5.9670-92 Приложение 1 табл. 4 [19]принимаем Р = 120q= 708 МПа;
fM – коэффициент трения при осевом смещении охватывающей детали при насадке с подачей масла на сопрягаемые конические поверхности
Приведенное напряжение на внутренней поверхности вала:
Из условия прочности 2 04Rp02В.1545 360 МПа
Приведенное напряжение на внутренней поверхности полумуфты
Из условия прочности 3 04Rp02М. 1554 360 МПа
Расчет выполнен в соответствии с ОСТ 5.9670-92 [19].
Усилие окончательной напрессовки муфты (Q) и давление масла (Р) подаваемого на сопрягаемые конические поверхности являются вспомогательными параметрами и должны быть заданы в технической документации как справочные.
При сборке конических соединений деталей валопроводов основным параметром характеризующим ее качество следует считать величину осевого перемещения.
Отсчет величины осевого перемещения в процессе сборки соединения следует производить во всех случаях после установки муфты в начальное положение осевым усилием (QН) при этом установку деталей для определения начального положения производят без подачи масла на сопрягаемые конические поверхности.
4. Расчёт влияния температуры на размеры капролоновых подшипников при их монтаже.
Величина необходимого кольцевого зазора в соединении подшипник - дейдвудная труба для скользящей посадки не менее = 009. Определим необходимую температуру до которой должен быть охлажден подшипник для обеспечения требуемого кольцевого зазора.
Для этого на основании ОСТ.5.4183-76 [15] выведем формулу.
где ТП - температура до которой нужно охладить подшипник для обеспечения требуемого натяга С;
ТН - температура при которой должен быть обеспечен гарантированный размер подшипника (нормальная температура по ГОСТ 9249 т.е. 20С);
Тд.тр - температура дейдвудной трубы С (принимается равной температуре в цехе где проводятся работы);
D - наружный диаметр подшипника при температуре 20С мм;
Dд.тр. - внутренний диаметр посадочного гнезда мм;
a П - коэффициент линейного расширения капролона;
a д.тр.- коэффициент линейного расширения материала дейдвудной трубы;
– величина кольцевого зазора в соединении подшипник – дейдвудная труба.
Выделим из формулы (16) ТП математическим путем:
Исходные данные: Тд.тр = 16С; D = 31555 мм; Dд.тр = 315 мм; a П = 73× × 10-5;
a д.тр.= 115 × 10-6; = - 009.
Таким образом на основании расчета для скользящей посадки капролонового подшипника с кольцевым зазором = - 009 его необходимо охладить до температуры - 84 С. Это реализуется либо помещением подшипника в морозильный ящик либо углекислотными огнетушителями либо в зимних условиях охлаждать на улице.
Данная процедура позволяет запрессовывать подшипник в дейдвудную трубу скользящей посадкой при помощи расточного станка (перемещением бабки) при этом для исключения повреждения материала подшипника используется проставочное кольцо.
Применение расточного станка для запрессовки копролонового подшипника позволяет отказаться от затрат на создание специальной оснастки.
5. Обоснование отказа от имитации недостающего оборудования.
В соответствии с требованиями ОСТ5.9966-85 пункты 1.8. и 1.9. и ОСТ 5.4368-81 пункты 2.1.1-2.1.4 к началу монтажа дейдвудной трубы требуется имитация отсутствующих в районе валопровода и главного двигателя тяжеловесных механизмов и оборудования массой более 2% от массы главного двигателя (это относится как к оборудованию и механизмам машинного отделения так и оборудованию расположенному в рыбоцехе и на верхней палубе).
Учитывая достаточно высокую конструктивную жесткость корпуса на заказе было принято решение провести пробную имитацию имевшей целью отказаться от полной имитации отсутствующих грузов при центровке. Так как ОСТ 5.4368-81 пункт 2.1.2. предусматривает такую возможность если контрольные измерения формы и расположения посадочных поясков мортир яблока ахтерштевня вварыша при погрузке имитирующего груза подтверждают сохранение технологических параметров центровки расположения осевой линии вала.
В процессе пробной имитации необходимо выполнить следующие работы:
Вынести теоретическую ось валопровода на наружную обшивку корпуса на шп. №34495458.
Нанести контрольные точки расположения оси валопровода на независимые конструкции стапеля цеха.
Зафиксировать положение судна.
Выставить дейдвудную трубу на отжимных болтах относительно оси валопровода (по световой). Записать положение (отклонение) по торцам трубы.
Установить грузы в соответствии со схемой имитации
Зафиксировать изменившееся положение:
2. Дейдвудной трубы относительно световой.
3. Изменение положения оси линии вала по местам на наружной обшивке корпуса.
Произвести погрузку валопровода в сборе с винтом на штатное место. Имитацию грузов согласно схеме восстановить если она временно демонтировалась под погрузку валопровода.
2.Оси валопровода по меткам на корпусе.
Составить карту замеров и предоставить в КО на заключение.
Работы по пробной имитации совместить с работами по монтажу дейдвудной трубы.
Была проведена пробная имитация грузом 3000 кг приложенным в районе оси баллера руля. Положение оси линии вала зафиксированное по мишеням установленным в дейдвудной трубе (545шп. и 52шп.) и на 45шп. при приложении груза 3000 кг не изменилось.
Проведение пробной имитации было согласовано с представителем Регистра и проектантом.
По результатам проверки положения оси линии вала траулера проекта 50010 при проведении пробной имитации до и после имитации был составлен технический акт.
Ниже представлено положение дейдвудной трубы технологического монтажного подшипника и мишени на 45 шп. Относительно оптической оси линии вала:
Носовая мишень:по высоте – 0
Кормовая мишень:по высоте – 0
Технологический подшипник
Ниже представлено положение оси линии вала после установки имитирующего груза 3000 кг по схеме ДП.141200-03-164.01.10.СХ:
Кормовая мишень:по высоте – 01 мм
На основании проведенной имитации по завершении корпусо-сварочных работ в районе кормовой оконечности а также окончании испытаний корпусных цистерн и установке штатного балласта в кормовой оконечности по согласованию с Морским Регистром судоходства получено разрешение о монтаже дейдвудных труб монтаже и центровке валопровода и механизмов ДРА в машинном отделении без имитации веса отсутствующих механизмов и оборудования в кормовой оконечности (в районе ВРШ и МО).
Технико-экономические обоснование проекта.
1.Расчет себестоимости монтажа по статьям калькуляции.
Себестоимость - это сумма всех денежных затрат предприятия связанных с производством и реализацией продукции или с монтажом ремонтом деталей оборудования и систем.
Себестоимость является показателем производственно-хозяйственной деятельности предприятия отражающей уровень производительности труда состояние организации производства степень использования основных и оборотных фондов.
Для учета однородных затрат используется понятие – статья калькуляции – группировка затрат по экономическим элементам.
Статья 1 «Основные материалы»
Это материалы которые непосредственно участвуют при монтаже системы.
Для определения затрат по статье необходимо определить расход материалов.
Расход крепежного материала.
Наименование материалов
Вес единиц измерения
Болт 2М10-6ДХ30 ГОСТ 7805-70
Болт 3М16-6ДХ18 ГОСТ 7805-70
Болт М16-6ДХ55 ГОСТ 7805-70
Болт М24-6ДХ130 ГОСТ 7805-70
Болт М27-6ДХ130 ГОСТ 7805-70
Гайка М10-7Н ГОСТ 5927-70
Гайка М24-6Н ГОСТ 5927-70
Гайка М27-6Н ГОСТ 5927-70
Винт М12-6gx20 ГОСТ 1481-84
Винт М16-6gx40 ГОСТ 1481-84
Винт ВМ20-6gx100 ГОСТ 1481-84
Шайба 16 ВСТ3СП2 ГОСТ 13463-78
Расчёт стоимости основных материалов
Цена за единицу (руб)
Уайт-спирит (нефрас) ГОСТ 3134-78
Смола эпоксидная марки К-153АТ6-05-1584-77
Кварц молотый пылевидный ГОСТ9077-82
Полиэтиленполиамин (отвердитель) ТУ6-02-594-85
Спирт этиловый ГОСТ18300
Набивка многослойного плетения марки ППФ 22х22
Набивка многослойного плетения марки ППФ 35х35
Парусина СКПВ Шир.74 ГОСТ 15530-93 + парусина полульняная
Проволока 2 Л63 ГОСТ 1066-80
Лист СТ3сп ГОСТ 19903-74
Лента СТ3пс ГОСТ6009-74
Пруток 20 БРАЖНМЦ9-4-4-1 ТУ48-21-249-72
Швелер 16 ГОСТ 8240-89 Ст3
Смазка графитная ГОСТ 1033
Турбинное масло ГОСТ 20799
Таким образом стоимость основных материалов З мат.= 976076 руб.
Транспортно-заготовительные расходы (ТЗР) составляют 10% от стоимости основных материалов.
ТЗР = 01 × З мат. = 01 × 976076 = 97608 руб.
Затраты по статье 1 (Зст1) составляют:
Зст1 = З мат.+ТЗР= 976076 + 97608 = 1073684 руб.
Статья 2. «Стоимость вспомогательных материалов комплектующих изделий»
В статью входят затраты связанные с приобретением покупных изделий полуфабрикатов запасных частей и определяются расчётным путём 10% от стоимости затрат по статье 1.
З всп. = 3ст1. × 01 = 1073684 × 01 = 107369 руб.
Статья 3. «Основная заработная плата рабочих»
Заработная плата – вознаграждение работнику за использование его рабочей силы.
Основная заработная плата (ЗП осн.) начисляется по сделанным или по временным расценкам а также включены доплаты за руководство бригадой обучение учеников за работу в выходные дни а также в вечернее и ночное время.
Исходя из средней стоимости 1 нч равного 2233 руб (Ст НЧср.) и трудоемкости по разработанной в проекте ТНК (Тр) основную заработную плату можно вычислить следующим образом:
ЗП осн.= Тр × Ст НЧср. = 864 × 2233 = 1929216 руб.
Статья 4. «Дополнительная заработная плата основных рабочих»
Статья учитывает: оплату отпусков компенсации за отпуск внутрисменные простои командировки за работу в ночное время и др.
И составляет в среднем 54 %.
ЗП доп. = 054 × ЗП осн.= 054 × 1929216 = 1035866 руб.
Следующие статьи калькуляции не связаны прямо с калькулируемой продукцией поэтому на себестоимость конкретного изделия они относятся пропорционально заработной зарплате.
Статья 5. «Отчисления на социальные нужды»
К отчислениям на социальные нужды (О соц.) относятся: единый социальный налог 356% и социальное страхование от несчастного случая и проф. заболеваний который для МП «Звездочка» составляет 11%.
О соц.= 0367 × ЗП = 0367 × (ЗП осн.+ ЗП доп.) = 0367 × (1929216 + 1035866) = 1088185 руб.
Статья 6. «Общехозяйственные расходы»
Затраты по статье включают содержание заводоуправления освещения услуги связи охрана предприятия экологические платежи лицензии рекламу консультационные юридические аудиторские услуги а также расходы указанные в статье 6 которые нельзя отнести к конкретному заказу.
Общехозяйственные расходы (З ох) по данным планово-экономического отдела (ПЭО) составляют 180% от основной заработной платы.
З ох = 18 × ЗП осн = 18 × 1929216 = 3482235 руб.
Статья 7. «Общепроизводственные расходы».
Общепроизводственные расходы (Зоп) включают в себя содержание управленческого состава затраты по содержанию цехов – коммунальные услуги поддержания чистоты и порядка в помещениях и на территории выполнение текущих расходов по содержанию цехов на ремонт(текущий и капитальный) амортизацию оборудования канцелярские расходы затраты по охране труда и технике безопасности.
Эти затраты по данным планово-экономического отдела (ПЭО) составляют 18239 % от основной заработной платы.
З оп = 18239 × ЗП осн.= 18239 × 1929216 = 3518666 руб.
Статья 8. «Прочие специальные расходы».
Затраты по статье (З проч.) включают аттестацию работников таможенное оформление спецпитание (гуммировщиков) освидетельствование МРС и др.
Затраты по статье на основании опыта постройки головного судна составляют 9% от общей суммы затрат по статьям с 1 по 7ю ( 1-7 =1223522).
З проч. = 009 × 1-7 =009 × 1223522 = 109965 руб.
Статья 9. «Прибыль».
Прибыль- это превышение доходов над расходами.
Составляет 30% от производственной себестоимости (Сб произв.) по данным ПЭО.
Пр= 030 × Сб произв.= 030 × 13334871 = 17335332 руб.
Сводная таблица по расчёту контрактной цены.
Коплектующие изделия запчасти вспомогательные материалы
Дополнительная ЗП рабочих
Отчисления в социальные фонды
Общехозяйственные расходы
Общепроизводственные расходы
Прочие специальные расходы
Производственная себестоимость
2. Расчёт сравнительной экономической эффективности разработанного технологического процесса.
Существует несколько путей для снижения затрат на монтаж: уменьшение трудоёмкости применение более дешевых материалов снижение затрат на оснастку.
В операциях 1 8.5 21.2 31 снижение трудоёмкости можно добиться тем что применить пневматический гайковерт с регулируемым шагом и гидравлический ключ с регулируемым усилием затяжки кроме того применение универсального опорного устройства позволяет немного снизить трудоемкость при проведении операций по центровке валопровода. При этом кроме снижения трудоемкости повышается качество (точность и надежность) монтажа. Снижение трудоёмкости составит 16 нч
В соответствии с пунктом 3.4 Работы по имитации недостающего оборудования не производим в связи с этим снижение трудоемкости составит 44нч (п.п. 8.2 8.3 8.9 8.12 разработанной ТНК (приведена выше)).
При общей трудоёмкости 864 нч.
( 60 : 864) × 100 = 7 %
Необходимо пересчитать статьи где изменяете значение.
Статья 1- без изменения
Статья 2-без изменения
Статья 3 – ЗП осн. после внедр. = ЗП осн. до внедр. × (100% - 7%)= 1929216 × 093= 1794171 руб.
Статья 4.- ЗП доп.= ЗП осн. после внедр. × 054 = 1794171 × 054 = 968852 руб.
Статья 5.- О соц.= 0367( ЗП осн. + ЗП доп.) = (1794171 + 968852) × 0367 = =101403 руб.
Статья 6.- З ох = 18 × ЗП осн. после внедр.= 18 × 1794171 = 3229508 руб.
Статья 7.- З оп = 18239 × ЗП осн. после вн.=18239 × 1794171 = 3272388 руб.
Статья 8.- З проч = 009 × 1-7 = 009 × 11460001 = 1031400 руб.
Статья 9. - Пр = 030 × сб произв. = 030 × 12491401 = 3747420 руб.
Цена без НДС= сб полн. + прибыль = 12491401 + 3747420 = 16238821 руб.
Сравнительная таблица затрат на изготовление продукции.
Затраты до внедрения
Затраты после внедрения
Экономический эффект (Эк. Эф.) определяется как разница между затратами до внедрения и после внедрения.
Эк. Эф.= Сбпроизв.(до внедр.) – Сбпроизв.(после внедр.) = 13334871 – 12491401 = 84347 руб.
При этом снижение прибыли составит:
Прпотери = Пр до внедр - Пр после внедр = 400046 – 374742 = 253040 руб.
Экономический эффект с учетом снижения прибыли составит:
Эк. Эф.Чист. = Эк. Эф. - Прпотери = 84347 - 253040 = 59043 руб.
При этом снижение контрактной цены составит:
Цконтр.(сниж..) = Цконтр.(до внедр.) - Цконтр.(после внедр.) = 20802398 - 19486585 = 1315813 руб.
Вывод: Снижение трудоемкости на 60 нч позволит снизить затраты на 84347 руб.
Рис .18. Расходы до и после внедрения в % от контрактной цены до внедрения.
3.Описание участка монтажа основных элементов валопровода.
При организации участка учитывается что в основе организации производственного процесса любого промышленного объекта лежит рациональное сочетание во времени и пространстве основных вспомогательных и обслуживающих процессов с целью наиболее эффективного использования материальных и трудовых ресурсов производственного участка.
Несмотря на многообразие производственных процессов при их организации должен соблюдаться ряд основных общих приципов. Специализация и кооперирование (закрепление за участком работ по монтажу и взаимосвязь функционирования участка с другими участками (цехами) по части обеспечения деталями энергетическими ресурсами средствами технологического оснащения и т.д.) параллельность (одновременное выполнение стадий и операций по ходу производственного процесса) прямоточность (последовательность стадий изготовления деталей корпуса изготовления секций формирование судна в целом) непрерывность (обеспечение максимально возможного сокращения времени перерывов между стадиями постройки судна и достижение бесперебойной работы оборудования и рабочих) ритмичность (обеспечение повторяемости процессов через равные промежутки времени).
При организации участка используются прогрессивные формы организации труда необходимые средства механизации и автоматизации производственных процессов прогрессивные формы организации ремонтного обслуживания рабочих мест.
Тип производства на участке единичный.
Для участка по монтажу характерен комплексно – бригадный метод работы при сдельно – премиальной оплате труда. К работам по монтажу механизмов допускаются лица не моложе 18 лет прошедшие специальное производственное обучение сдавшие экзамен на право производства этих работ на право пользования грузоподъемными механизмами имеющие соответствующие удостоверения установленного на ГМП "Звездочка" образца а также не имеющие медицинских противопоказаний.
Руководство работами по подготовке к монтажу демонтажу механизмов осуществляет ответственное лицо назначенное из числа руководителей и специалистов прошедших проверку знаний правил ТБ заводской комиссией назначенной приказом руководителя предприятия.
Если работа выполняется звеном то в звене должен быть назначен старший из более опытных и квалифицированных рабочих. Совместные действия выполняются только по команде старшего.
Все рабочие проходят инструктаж и должны быть аттестованы к проведению данных работ. Ответственным за проведение работ является производственный мастер.
При проведении работ по монтажу движительного комплекса рекомендуется бригадная форма организации труда со сдельно-премиальной оплатой по конечным результатам. Размер премии рассчитывается исходя из заработной платы сдельщика с учетом общего процента премии предусмотренного положениями о премировании.
Бригада возглавляется бригадиром который относится к категории рабочих и работает наравне с другими членами бригады. Бригада приступает к очередному производственному заданию только при наличии полного комплекта комплектующих деталей организованного энергоснабжения подготовленных подъемно-транспортных операций изученных условий выполнения заданного технологического процесса рабочего наряда на оплату и стимулирование труда.
Нормирование оплаты труда определяется разрядом работ в соответствии с «тарифно-квалификационным справочником» тарифной сеткой и нормой времени на выполнение данных работ.
В процессе проведения работ по монтажу движительного комплекса существует распределение работ между цехами.
Основную работу выполняет монтажный цех (Цех 10) где размещен заказ на котором производятся работы по монтажу движительного комплекса. На Рис.20. показана схема постройки траулеров проекта 50010 поточно-позиционным методом:
Рис.19. Схема размещения траулеров пр.50010
Позиция 1 – формирование корпуса;
Позиция 2 – монтаж механизмов оборудования и систем;
Позиция 3 – достройка окраска.
Монтаж движительного комплекса производится на второй позиции.
Ряд работ производятся в механообрабатывающем цехе (Цех 4). В частности в нем производятся расточка посадочных поверхностей подшипника дробеструйная очистка внутренней поверхности дейдвудной трубы запрессовка и крепление подшипника в дейдвудную трубу и др.
Работы по приготовлению и заливке монтажных зазоров пластмассой выполняются цехом покрытий (Цех 45).
Такое разделение работ между цехами позволяет сократить время и количество работ на стапеле и повысить качество выполняемых работ.
4. Разработка мероприятий по обеспечению качества монтажа.
Под качеством продукции понимается степень пригодности изделия к удовлетворению определенных запросов заказчика. Качество каждого вида продукции характеризуется соответствием всех его параметров назначению продукции; долговечностью или ресурсом работы; надежностью т.е. непрерывностью использования до первого отказа. Необходимо учитывать также влияние продукции на окружающую среду (экологические требования) эстетические данные и другие характеристики позволяющие определить в какой степени продукция отвечает требованиям заказчика.
Основными факторами определяющими качество монтажа движительного комплекса являются:
-уровень конструкторской и технологической подготовки производства;
-профессиональный и квалификационный состав кадров их отношение к труду;
-состав и состояние оборудования инструментов и приспособлений;
-состояние конструкторской и технологической дисциплины;
-организация производства и труда;
-стандартизация применяемых элементов;
-материальное обеспечение производства;
-методы организации контроля качества;
-система управления коллективом трудящихся включая управление повышением качества.
При выборе используемого оборудования определяются те их качества которые в наибольшей мере обеспечивают качество монтажа производимого с их применением.
Главная целевая установка системы качества функционирующей на предприятии и построенной на основе стандартов ИСО серии 9000 - обеспечение качества продукции требуемого заказчиком (потребителем) и предоставление ему доказательств в способности машиностроительного предприятия и его подразделений это сделать.
На ГМП «Звездочка» принята модель системы качества по ИСО 9002-94 и ГОСТ Р ИСО 9002-96 (Модель для обеспечения качества при производсиве монтаже и обслуживании).
Высокое качество обеспечивается наличием технического контроля (входной пооперационный приемочный) на всех стадиях технологического цикла а также проведением ежегодной аттестацией рабочего персонала квалификационной комиссией.
Контроль и пооперационная приемка выполняемые в соответствии с согласованной конструкторской и технологической документацией и требованиями нормативных документов должны обеспечивать тщательную проверку качества и правильности всех монтажных и регулировочных работ.
Обеспечение контроля качества работ осуществляется последовательно производственным мастером мастером ОКК представителем заказчика. Приемка выполнения работ по каждой из операций осуществляется оформлением извещений вышеуказанными должностными лицами.
В процессе выполнения работ на мастеров ОКК возлагается также выборочный профилактический контроль.
Приемка осуществляется производственным мастером мастером ОКК или представителем заказчика с отметкой в журнале приемки. После приемки работы от производственного мастера ОКК выписывают извещения о предъявлении работы представителю заказчика который совместно с контрольным мастером оформляет удостоверение приемки на отдельном бланке.
Предусмотрено материальное стимулирование работников производственного участка работников службы технического контроля в виде выплаты премий за качество выполненных работ.
Мотивация труда работников как способ повышения качества.
В условиях рыночной экономики решение вопросов оплаты труда перенесено из компетенции государственных органов власти на уровень предприятий. Однако вышеприведенные положения свидетельствуют об утрате заработной платой своих функций в том числе стимулирующей которая выступает одним из условий мотивации труда. В этой связи для предприятий очень важно иметь четкое представление о направлениях усиления мотиваций совершенствовании процесса стимулирования в деле достижения лучших конечных результатов деятельности предприятия. Сегодня ведется поиск различных эффективных способов управления трудом обеспечивающих активизацию человеческого фактора. Это одно из основных направлений стабилизации экономического роста в стране.
Решающее значение в деле обеспечения стремления работников к повышению результативности своей деятельности имеет создание действенных мотивов.
Понятие «мотивация» (от греч. motif от лат. moveo - двигаю) представляет собой внешнее или внутреннее побуждение экономического субъекта к деятельности во имя достижения определенных целей наличия интереса к такой деятельности и способов ее инициирования побуждения. Необходимо добиться чтобы такое воздействие носило постоянный характер.
Мотивацию нельзя сводить только к стимулированию. В настоящее время стимулирование ориентировано на краткосрочные экономические цели на достижение определенного результата за установленный период. Такой подход не обеспечивает заинтересованности работников в постоянном повышении своей квалификации в самосовершенствовании. В этом случае вряд ли можно успешно использовать данную систему как важный резерв повышения эффективности производства.
Система оплаты труда.
Для правильной организации заработной платы на МП «Звездочка» применяется система тарификации труда с более высокой оплатой квалифицированного а также тяжелого труда.
Существует шесть тарифных разрядов оплачиваемых по тарифным ставкам возрастающим вместе с номером разряда.
Тарифный коэффициент
Рассчитаем средний тарифный коэффициент работ на основании ТНК:
где Тр1 Тр2 Трn – трудоемкость по разрядам соответственно по расчетным данным ТНК
k1 k2 kn – тарифный коэффициент по разрядам соответственно.
Разряд присваиваемый рабочему в определенной степени обуславливает возможный уровень его заработной платы и таким образом стимулирует его повышать свою квалификацию для дальнейшего улучшения условий жизни.
Основной формой заработной платы является прямая сдельная оплата труда состоящая в том что рабочему оплачивают по установленной расценке за каждую единицу сделанной им продукции.
В отдельных случаях для оплаты работ от которых непосредственно зависит выполнение плана применяется сдельно-прогрессивная система оплаты труда. Данная система отличается тем что за выработку сверх определенной нормы рабочий получает не по нормальным а по завышенным расценкам чем выше переработка норм тем выше расценка.
В тех случаях когда установить нормы выработки и учитывать выполняемую работу очень сложно применяется повременная или премиальная системы оплаты. При повременной системе оплата производится по отработанному времени в зависимости от квалификации (разряда) рабочего. Премиальная система оплаты отличается от повременной тем что кроме оплаты за отработанное время рабочему выплачивается специально установленная премия за своевременное или досрочное выполнение работы.
Нормы времени проставляемые в нарядах для рабочих-сдельщиков делятся на три категории: расчетные закрепленные и временные. Расчетные нормы используются для нормирования часто повторяющихся работ. Для нормирования редко повторяющихся работ применяются закрепленные нормы. Если работы являются новыми для цеха то они нормируются по временным нормам.
Очень важно создать условия при которых человек ощущает значимость своего труда испытывая чувство причастности к определенному коллективу доволен общением и дружескими отношениями с коллегами. И решающая роль принадлежит здесь внешнему признанию значимости труда через заработную плату продвижение по службе символы служебного статуса и престижа.[23].
На основании факторов определяющих качество монтажа движительного комплекса в целях обеспечения требуемого качества считаю необходимым провести следующие мероприятия:
Постоянная подготовка и повышение квалификации рабочих и специалистов их обучение передовым приемам и методам труда и управления.
Внедрение новейших технологий и применение современного высокоточного оборудования. В частности рассмотреть вопрос о возможной закупке для центровки лазерной системы DIGILASER применение которой позволит снизить трудоемкость при одновременном повышении качества и точности центровки (описание системы произведено в пункте 1.2.).
Обеспечение условий личной материальной заинтересованности каждого работника в качестве производимых работ.
Пооперационный контроль качества производимых работ и обеспечение качества в соответствии с принятой на предприятии системы качества.
Выполнение разработанных мероприятий должно обеспечить удовлетворение требований заказчика в отношении обеспечения качества что в свою очередь создаст репутацию необходимую для закрепления на международном рынке и обеспечит устойчивое финансовое положение предприятия для решения задач собственного социально-экономического развития.
по монтажу движительного комплекса.
При организации работ на судне руководители и специалисты должны руководствоваться следующими нормативными документами и общими требованиями:
«Безопасность труда при строительстве и ремонте судов. Основные положения» РД5.0241 разделы 1 3 5 6 9 приложения 1 3 4 10 11;
«ССБТ. Погрузочно-разгрузочные работы при строительстве и ремонте судов. Требования безопасности» ОСТ5.0330 разделы 1 2 4;
«ССБТ. Освещение искусственное на судостроительных предприятиях. Общие требования» РД5.0308 разделы 1 2 3 4;
«Техническое обеспечение строящихся переоборудуемых и ремонтируемых судов. Системы вентиляции судовых помещений». РД5.9971 разделы 1 3 4 5;
«Правила пожарной безопасности для строящихся и ремонтируемых судов» ППБО-130;
«Правила пожарной безопасности в Российской Федерации» ППБ-01 разделы 1 16;
«Леса для постройки и ремонта судов. Общие технические условия». ОСТ5.2029 разделы 8.3;
«Общие указания по охране водных объектов от загрязнений при постройке судов» РД5.ЕДИВ.059;
1. Техника безопасности при выполнении работ
по монтажу движительного комплекса.
1.1. Основные положения.
К самостоятельной работе по демонтажу монтажу механизмов допускаются лица не моложе 18 лет прошедшие специальное производственное обучение. Лучшие и сдавшие экзамен на право производства этих работ на право пользования грузоподъемными механизмами имеющие соответствующие удостоверения установленного на ГМП "Звездочка" образца а также не имеющие медицинских противопоказаний.
Если работа выполняется звеном в звене должен быть назначен старший из более опытных и квалифицированных рабочих. Совместные действия выполняются только по команде старшего.
Уровни шума на рабочем месте должны соответствовать требованиям ГОСТ 12.1.003 предельно допустимые уровни шума не более 80 дБ.
Перед началом новой работы рабочие должны быть проинструктированы о безопасных способах ее выполнения в объеме необходимых инструкций по охране труда.
На все пожароопасные работы необходимо оформить разрешение по установленной на ГМП «Звездочка» форме.
Перед началом работ с виброопасным инструментом рабочий должен ознакомиться с условиями его эксплуатации и продолжительностью выполнения рабочего процесса с использованием инструмента данного типа согласно «Положению о порядке работы с ручным механизированным инструментом» 600.26509-001; утвержденному УГИ ГМП «Звездочка» 21.10.96г. и введенному в действие ПРИ N 587.
Сигнальные цвета и знаки безопасности должны соответствовать ГОСТ 12.4.026.
Рабочие должны быть обеспечены средствами индивидуальной защиты согласно «Перечню » 501.0-028 и «Типовым отраслевым нормам бесплатной выдачи специальной одежды специальной обуви и других средств индивидуальной защиты (СИЗ)».
Контроль соблюдения требований безопасности и производственной санитарии при работе на судне осуществляет производственный мастер или лицо назначенное приказом начальника цеха.
При работе на лесах настилах необходимо:
-пользоваться инструментальными ящиками или сумками для переноса и хранения инструмента и крепежных изделий;
-привязывать инструмент во время работы в целях предупреждения его падения;
-спускать вниз необходимые на ходу работы предметы по специально устроенным спускам желобам или при помощи веревки.
Одновременная работа отдельных лиц или бригад друг над другом на разных ярусах по одной вертикали должна быть по возможности исключена в противном случае должны быть устроены леса или навесы предохраняющие работающих внизу от возможного падения предметов.
При передвижении по вертикальным трапам должны быть свободными обе руки держаться нужно за вертикальные части трапа необходимо постоянно контролировать действия впереди и сзади идущих перед началом движения следует убедиться в надежности крепления трапа.
На проведение погрузочно-разгрузочных работ с тяжелыми сборочными единицами и деталями не имеющими схем строповки руководителю работ необходимо оформить наряд-допуск по установленной на предприятии форме как на работы с повышенной опасностью.
Рабочие места где выполняются погрузочно-разгрузочные такелажные работы связанные с демонтажом монтажом механизмов должны быть оборудованы знаками безопасности по ГОСТ 12.4.026.
При выполнении погрузочно-разгрузочных работ при демонтаже монтаже механизмов - нахождение людей не занятых на этих работах в районе погрузки-выгрузки не допускаются.
Нахождение людей под грузом при его перемещении - запрещается. Запрещается оставлять груз (механизм агрегат) в подвешенном состоянии при перерывах в работе.
При монтаже демонтаже механизмов необходимо пользоваться только исправными инструментами исправными грузозахватными приспособлениями исправными стропами грузоподъемными механизмами имеющими бирки грузоподъемности и даты испытаний.
Перед началом работы следует проверить надежность креплений; настилов в рабочей зоне организовать освещение убрать из рабочей зоны посторонние предметы шланги трубы. Если над рабочим местом находится открытое пространство а на выше расположенных ярусах будут вестись работы лица работающие как наверху и внизу должны быть предупреждены обо всех работах выполняемых над и под ними.
Перед началом работы следует проверить надежность крепления оборудования в рабочей зоне. Включение вентиляции судовых помещений производится не менее чем за 15 минут до входа рабочих в помещение.
После окончания работ с применением растворителей в судовых помещениях вентиляция должна работать в течение времени указанного в технологической документации а после окончания сварочных и газорезательных работ в судовых помещениях вентиляция должна работать не менее 20 минут.
При отключении вентиляции работы в судовых помещениях должны быть немедленно прекращены а рабочие должны выйти из помещения. Содержание в воздухе судовых помещений пыли газов и паров растворителей должно систематически контролироваться. Порядок и сроки проведения контрольных замеров устанавливает администрация по согласованию с органами санитарного и пожарного надзоров.
При работах на судне по демонтажу монтажу механизмов слесарь-монтажник должен применять следующие средства индивидуальной защиты:
-очки типа 3HP3-T ГОСТ 12.4.013;
-рукавицы специальные ГОСТ 12.4.010;
-СИЗОД-ФП-110 респиратор ШБ-1 "Лепесток-40" ГОСТ 12.4.028;
-противошумные вкладыши "Беруши" ТУ6-16-2402;
-каску по ГОСТ 12.4.087.
Работающий персонал обязан не допускать возникновения травмоопасных ситуаций в процессе работы при обнаружении и возникновении подобных ситуаций немедленно принять меры к их устрашению.
При выполнении сварочных работ в рабочей зоне судна должны быть выполнены требования безопасности в соответствии с инструкцией НЯДИ.000.25.00.131 "Техника безопасности и охрана природной среды при выполнении сборочно-сварочных работ в условиях заказа".
Шланги к пневмоинструменту кабели к переноскам не должны перекрывать проходы по возможности должны крепиться на переборках или подволоке.
Инструмент на рабочем месте хранить в сумке или металлическом ящике инструмент должен лежать надежно не падать вниз при случайном задевании. Рабочая одежда должна быть чистой и целой.
При передвижении по палубам судна следует не спешить внимательно смотреть под ноги держаться за леера поручни не занимать обе руки переносимым грузом - одна рука должна быть свободна.
Механизмы и оборудование трубопроводы перед выгрузкой должны быть осушены.
Все части механизмов должны быть по возможности надежно закреплены. Незакрепленные детали должны быть сняты.
Не допускается открывать закрывать арматуру систем незнакомых работающему не имеющих отношения к его работе при течи рабочей жидкости следует вернуть механизм в исходное положение доложить старшему по работе.
При транспортировке на судне механизмов для крепления талей стропов должны использоваться обуха с маркированной грузоподъемностью и изготовленные по чертежу.
Механизмы необходимо стропить за штатные обуха или применять специальную оснастку.
Оценка опасности работ
Выполнению работ по монтажу движительного комплекса сопутствуют опасные и вредные производственные факторы которые могут воздействовать на работающего на судне человека носят физический и химический характер:
)движущиеся грузоподъёмные машины перемещение сборочных единиц и деталей валопровода при погрузочно-разгрузочных и такелажных работах;
)создание избыточного давления при гидравлических испытаниях при напрессовке спрессовке полумуфты;
)запылённость шум и вибрация при работе с пневмоинструментом;
)токсичные и раздражающие компоненты уайт-спирита и др. веществ применяемых в процессе проведения работ по монтажу движетельного комплекса;
)внезапное вращение сборочных единиц валопроводов при их проворачивании;
)затеснённость при проведении монтажных работ.
Предельно-допустимые концентрация опасных
химических веществ применяемых в процессе проведения работ
Предельно-допустимая
Концентрация в рабочей
Уайт-спирит(нефрас) ГОСТ 3134
Смазка графитная ГОСТ 3333
Этиловый спирт ГОСТ 18300
Примечание: Толуол и эпихлоргидрин – вещества выделяемые эпоксидными смолами.
Характер действия вредных веществ на организм человека.
При попадании на кожу нефраса и уайт-спирита вызывают сухость дерматиты экземы. Пары обладают наркотическим действием. При воздействии на кожу наблюдаются острые отравления и экземы. Накапливаясь в организме выводятся медленно что способствует хроническому отравлению.
Этиловый спирт действует отрицательно на нервную систему вызывает отравление оказывает наркотическое действие.
Селикагель не является токсичным веществом. Пыль селикагеля вдыхаемая человеком способна вызывать изменения в легких вследствие токсичного действия двуокиси кремния.
При работе с селикагелем обязательное пользование респираторами для защиты органов дыхания.
При приготовлении полимерного материала для отверждения применяют полиэтиленполиамин – маслянистая жидкость со специфическим запахом. При длительном воздействии на кожный покров он способен вызвать дерматит при попадании в глаза – гнойный коньюктивит. Длительное вдыхание малых концентраций может вызвать реакцию типа бронхиальной астмы. Попадая через органы дыхания в больших концентрациях нарушает дыхание угнетает нервную систему.
Эпихлоргидрин выделяемый эпоксидной смолой раздражает слизистые оболочки вызывает дерматиты экземы влияет на кроветворные органы печень почки вызывают острое хроническое отравление.
Требования по обеспечению санитарно-гигиенических условий труда в соответствии с РД 2.2.755.
Запрещается хранение и прием пищи на рабочих местах.
При одновременном содержании в воздухе рабочей зоны нескольких вредных веществ однонаправленного действия (по заключению органов гос. санитарного надзора) сумма отношений фактических концентраций каждого из них в воздухе к их ПДК(предельно допустимых концентраций) не должна превышать единицы.
1.2. Техника безопасности при работах с применением растворителей.
При работе с растворителями применять следующие средства индивидуальной защиты:
)перчатки резиновые ГОСТ 20010;
)перчатки хлопчатобумажные или трикотажные ГОСТ 5007.
Резиновые перчатки следует надевать на хлопчатобумажные или трикотажные. При отсутствии перчаток могут применяться «биологические перчатки»;
)Герметичные защитные очки типа Г ГОСТ 12.4.003;
)СИЗОД-ФГП-310 респиратор фильтрующий газопылезащитный ГОСТ 17269;
)СИЗОД-ФГ-310 респиратор фильтрующий противогазовый РПГ-68 марки А ГОСТ 12.4.004.
В помещении где проводятся работы с применением растворителей и герметика (герметизация разъемов линии вала и др.) и смежных с ним помещениях запрещается выполнять сварочные и другие огнеопасные работы о чем должны быть вывешены предупреждающие надписи. На работы с применением растворителей герметика необходимо оформить наряд-допуск на выполнение работ с повышенной опасностью по форме принятой на ГМП "Звездочка".
К месту где проводятся работы с применением огнеопасных технических моющих средств (очистителей растворителей) и их компонентов должны быть подведены по заявке мастера шланги вытяжной вентиляции по схеме утвержденной для места расположения судна по стапельному расписанию ГМП "Звездочка".
Растворители герметики должны отпускаться на рабочее место в количестве не превышающем потребности половины одной смены работы.
При выполнении работ по расконсервации оборудования и механизмов при нанесении герметика растворители должны доставляться на рабочее место и находиться в герметичных бачках (в количестве не более 1 л). Герметик должен храниться в герметичной таре.
Разлив растворителей и других материалов содержащих токсичные компоненты необходимо выполнять в вытяжных шкафах. Растворители необходимо разливать в тару исключающую их непроизвольное проливание.
В случае разлива на пол леса растворителей и др. материалов их нужно немедленно убрать ветошью в отдельную тару соблюдая меры предосторожности. Место разлива засыпать песком с последующим удалением.
Производственные отходы (ветошь обтирочный материал и др.) следует собирать в контейнер с плотно закрывающейся крышкой. Отходы выносить в течение и в конце каждой рабочей смены в специально отведенные места. Допускается загрязненный растворителями герметиком обтирочный материал-ветошь собирать на рабочих местах в пластиковые мешки и выносить с заказа при оставлении рабочего места.
При попадании растворителей на открытые участки тела необходимо их удалить и промыть кожу тёплой водой с мылом; при попадании на слизистую оболочку глаз – обильно промыть водой
Для уменьшения электризации нефраса при обезжиривании различных поверхностей следует уменьшить его удельное электрическое сопротивление введением антистатических присадок АСП-1(ТУ38-101538) или «Сигбол» (ТУ38-101741) в количесте 001% и 0002% (по массе) соответственно.
Протирочный материал (ветошь бязь и т.п.) смоченный нефрасом отжимать слегка выкручивание недопускается.
Одновременное выполнение на одном и том же участке или в одном и том же районе корпуса работ по нанесению покрытий обезжириванию с работами вызывающими искрообразование (дробеструйная обработка сварка газорезка обработка металла наждачными кругами и т.п.) разрешается производить не ближе 15 м по горизонтали.
В замкнутых труднодоступных помещениях необходимо применять переносные светильники во взрывозащищенном исполнении. Переносные светильники должны иметь защитную сетку и шланговый привод. Напряжение питания не должно превышать 12 В. Штепсельные розетки переносных светильников должны быть расположены вне судовых помещений.
Для автоматической сигнализации наличия в помещении взрывоопасных концентраций паров растворителей и их смеси применяют переносной индикатор взрывоопасности ПИВ-2У4.
Знаки безопасности в соответствии с ГОСТ Р12.4.026-2001.
1.3. Техника безопасности при гидравлических испытаниях напрессовке и спрессовке.
К проведению гидравлических испытаний спрессовке и напрессовке полумуфт подшипников допускаются рабочие не моложе 18 лет не имеющие медицинских противопоказаний прошедшие инструктаж по технике безопасности и противопожарной безопасности с регистрацией в журнале под расписку имеющие удостоверение на право проведения работ.
Гидравлические и пневматические испытания проводить в строгом соответствии с требованиями чертежей.
На проведение гидравлических испытаний на работы по спрессовке и напрессовке полумуфт болтов повышенной точности должен быть оформлен наряд-допуск по инструкции «О порядке оформления наряд-допуска на производство работ с повышенной опасностью» как на работы повышенной опасности.
При проведении испытаний а так же спрессовке напрессовке полумуфт на границе зоны испытаний установить предупредительные надписи:
«Запретная зона» «Проход закрыт» «Идут испытания».
Ответственным руководителем работ за подготовку и безопасное проведение испытаний является производственный мастер.
Перед началом испытаний руководитель работ должен:
)провести подробный инструктаж с персоналом участвующим в испытаниях о мерах безопасности и порядке проведения испытаний;
)проверить наличие документов о готовности изделий к испытаниям;
)убедиться в исправности контрольно-измерительной аппаратуры и приборов арматуры оснастки сигнализации защитных устройств.
При испытаниях в районе проведения работ не должны находиться лица не занятые данной работой.
При испытаниях следует применять щитки защитные НБТ для защиты лица и глаз.
Испытания должны быть прекращены и давление снижено до нуля атмосфер в случаях:
)нарушения герметичности трубопроводов;
)возрастания давления выше разрешённого.
Устранение неисправностей должно производиться с разрешения руководителя испытаний после снижения давления до нуля атмосфер.
1.4. Техника безопасности при работе с механизированным инструментом.
К выполнению работ с механизированным пневматическим инструментом допускаются рабочие не моложе 18 лет не имеющие медицинских противопоказаний прошедшие обучение инструктаж по технике безопасности и противопожарной безопасности с регистрацией в журнале под расписку имеющие удостоверение на право проведения этих работ.
При работе с механизированным пневматическим инструментом применять следующие средства индивидуальной защиты:
)очки типа ЗНЗ-Т ГОСТ 12.4.013 с небьющимися стеклами «Триплекс»;
)рукавицы виброзащитные;
)респиратор ШБ-1 «Лепесток-200» ГОСТ 12.4.028 или другие имеющиеся в наличии;
)противошумные вкладыши «Беруши» по ТУ 6-16-2402.
Пневматический инструмент должен соответствовать требованиям ГОСТ 12.2.010.
Клапан включения пневматического инструмента должен легко и быстро открываться и закрываться и не пропускать воздух в закрытом положении.
Шлифовальные машины должны иметь защитное ограждение рабочей части.
Перед началом работ с пневмоинструментом необходимо предупредить рядом работающих о возможности попадания в них кусков металла искр от рабочего инструмента и при необходимости установить защитный экран.
Запрещается выполнять очистку поверхности дробеструйными аппаратами при неплотном прилегании щетки рабочей головки к очищаемой поверхности.
Ремонт и наладку дробеструйного аппарата разрешается выполнять только ремонтному персоналу после отключения аппарата от воздушной магистрали.
Для защиты от статического электричества должны устраиваться заземленные зоны.
Предотвращение опасного и вредного воздействия на людей электрического тока электрической дуги и электромагнитного поля осуществлять в соответствии с требованиями ГОСТ 12.1.019.
1.5. Техника безопасности при работах по погрузке выгрузке перемещению сборочных единиц и деталей движительного комплекса.
К выполнению погрузочно-разгрузочных и такелажных работ допускаются рабочие не моложе 18 лет не имеющие медицинских противопоказаний прошедшие обучение инструктаж по технике безопасности и противопожарной безопасности с регистрацией в журнале под расписку имеющие удостоверение на право проведения этих работ.
Погрузочно-разгрузочные и такелажные работы должны проводиться под руководством лиц ответственных за безопасное перемещение грузов кранами назначенных приказом.
При проведении работ связанных с подъёмом опусканием перемещением установкой сборочных единиц и деталей валопровода соблюдать требования безопасности ОСТ5.0330 РД5.0364.
На проведение погрузочно-разгрузочных и такелажных работ с тяжеловесными сборочными единицами и деталями (массой свыше 5 тонн) необходимо оформлять наряд-допуск по установленной на предприятии форме как на работы с повышенной опасностью.
При выполнении погрузочно-разгрузочных и такелажных работ нахождение людей под грузом при его подъеме опускании перемещении а также нахождение людей не занятых на этих работах в районе погрузки-выгрузки не допускается.
Запрещается оставлять груз в подвешенном состоянии при перерывах в работе.
Рабочие места где выполняются погрузочно-разгрузочные и такелажные работы должны быть оборудованы знаками безопасности по ГОСТ 12.4.026.
Погрузочно-разгрузочные работы должны быть максимально механизированы.
При производстве этих работ не допускается превышать предельные нормы переноски тяжестей рабочими установленные санитарными нормами и правилами.
Механизированный способ погрузки перемещения является обязательным при массе более 50 кг и подъеме на высоту более 3 метров.
2. Противопожарные мероприятия
при монтаже движительного комплекса.
Основные организационные и технические мероприятия по обеспечению безопасного выполнения работ и пожарной безопасности:
Общее руководство по выполнению работ по настоящему КТД возлагается на производственного мастера.
При выполнении работ с применением ручного переносного электрифицированного инструмента использовать с напряжением не более 36 В. Переносные светильники должны быть напряжением не более 12 В и защищены предохранительными сетками.
Помещения в которых выполняются работы по монтажу валопровода должны быть оборудованы приточно-вытяжной вентиляцией в соответствии с требованиями РД5.9971. Приточно-вытяжную вентиляцию следует включить через 30 минут до начала работы и выключать через 15 минут после окончания работы.
Рабочие места должны быть оборудованы настилами трапами и переходами. Деревянные настилы должны быть выполнены из пиломатериалов прошедших огнезащитную обработку.
Рабочие места должны быть обеспечены первичными средствами пожаротушения.
На проведение пожароопасных работ (работа шлифовальными машинками электросварочные работы работы с уайт-спиритом шпатлёвкой) оформлять разрешение по установленной на предприятии форме.
При выполнении электросварочных работ соблюдать требования безопасности РД5.9823.
Для защиты рабочих не связанных со сварочными работами от действия сварочной дуги места сварки должны ограждаться ширмами. На местах сварки необходимо вывешивать плакаты предупреждающие об опасности облучения глаз и кожи.
Мероприятия по обеспечению пожарной безопасности также описаны в разделе «Работа с растворителями».
3. Охрана окружающей среды.
При проведении работ по демонтажу-монтажу движительного комплекса выполнять требования следующих нормативно технических документов по охране окружающей среды:
-РД 5.ЕДИВ.059 разделы 3 4;
-РД 5.9971 разделы 2.2 4 5. приложение 1. 20 21;
-СанПиН №2.1.6.1032-01;
-"Правила охраны поверхностных вод" 1991 г;
-"Временные правила охраны окружающей среды от отходов производства и потребления в РФ" 1994 г
-"Порядок накопления транспортировки обезвреживания и захоронения токсичных промышленных отходов. Санитарные правила" 1985 г.
Ветошь загрязнённую уайт-спиритом складировать для хранения и транспортировки в герметичные контейнеры отходов с последующей их отправкой в места хранения специально отведённые для данных целей.
Общие требования к контролю и методы контроля опасных и вредных производственных факторов должны соответствовать РД5.0281.
Вредные выбросы в соответствии с РД5.ЕДИВ.059 в открытые водоёмы и канализацию отсутствуют.
Выбросы в атмосферу не должны превышать установленные нормативы предельно допустимых концентраций вредных веществ на границе санитарной защитной зоны.
Необходимость очистки вентиляционных выбросов указывается в конкретном технологическом документе на основании расчета рассеивания вредных веществ в атмосфере в соответствии с СанПиН № 2.1.6.1032-01 и "Методикой расчета концентраций в атмосферном воздухе вредных веществ содержащихся в выбросах предприятий" ОМД 86.
Требования к эксплуатации установок очистки газа (воздуха) определяются "Правилами эксплуатации установок очистки газа" утвержденными Главным Государственным инспектором по контролю за работой газоочистных и пылеулавливающих установок 28.11.1983 г.
Количество вредных веществ в воздухе выбрасываемом в атмосферу при выполнении работ указывать в технологической инструкции в таблице "Охрана воздушного бассейна".
При выполнении механомонтажных работ соблюдать требования "Инструкции по обращению с отходами на ГМП "Звездочка" 585.03-05.
Отходы представляющие собой нефтепродукты собирать в специальную тару и использовать в соответствии с "Инструкцией об организации сбора и рационального использования отработанных нефтепродуктов на ГМП "Звездочка" 585.04-04.
По окончании работ после которых образуются отходы произвести их первичную сортировку по видам и классам опасности (токсичности) согласно "Классификатору производственных отходов ГМП "Звездочка" 585.03-03 и "Методическим рекомендациям по проведению инвентаризации и классификации промышленных отходов" утвержденным Председателем комитета охраны окружающей среды Архангельской области 11.07.96 г.
Первичную сортировку производит рабочий выполняющий технологические операции с образованием отходов. Рабочий должен быть проинструктирован о способах первичной сортировки отходов.
Сбор отходов осуществляется следующим образом:
-отходы 1го класса (чрезвычайно опасные) - в стальные баллоны или герметичные металлические контейнеры;
-отходы 2го класса (высокоопасные) - в полиэтиленовые мешки и далее в контейнеры;
-отходы 3го класса (умеренно опасные) - в бумажные мешки и далее в контейнеры;
-отходы 4го класса (малоопасные) и нетоксичные подвергаются первичной сортировке только в случае дальнейшего использования отдельных их видов в качестве вторичных
материальных ресурсов.
Отходы 4 класса собирать в контейнеры и мусоросборники различных типов обеспечивающие возможность легкой разгрузки и удобной транспортировки. Отдельно собирать отходы масляной ветоши и бытового мусора.
Ответственность за природоохранную деятельность цеха возлагается на специалиста из числа инженерно-технических работников в соответствии с "Положением о лице ответственном за природоохранную деятельность подразделения предприятия (цеха)" 507.585-006.
Охрана воздушного бассейна
Наименование оборудование
Количество используемого
Протирочная ветошь и бязь используемые для протирки оборудования
Куски металла не пригодные для дальнейшего использования
для последующей переплавки
Уайт-спирит (нефрас) ГОСТ 3134
Слив в специальные емкости для легко воспламеняющихся продуктов
Примечание: в таблице 15 не указаны отходы материалов незначительные по своему количеству вопрос об их утилизации решается по мере накопления в контейнерах.
В процессе работы над дипломом проведен всесторонний анализ существующих способов монтажа элементов движительного комплекса (Дв.К.) имеющихся технологических инструкций (ТИ) документов и инструкций от заказчиков. На основании чего выполнена разработка технологической инструкции которая может быть использована при монтаже Дв.К. на траулерах проекта 50010. Разработанная ТИ учитывает опыт монтажа Дв.К на головном судне а также в проекте произведены:
-разработка технолого-нормировочной карты на монтаж движительного комплекса;
-расчет необходимого количества полимерного материала для заливки монтажных зазоров при монтаже дейдвудной трубы (результаты использовались при выдаче материалов цеху производителю работ);
-расчет технологических параметров напрессовки фланцевой полумуфты (ранее предоставлялся заказчиков);
-расчёт влияния температуры на размеры капролоновых подшипников при их монтаже.
-обоснование отказа от имитации недостающего к началу монтажа дейдвудной трубы оборудования.
-расчет себестоимости проведения работ по монтажу Дв.К. по статьям калькуляции и сравнительной экономической эффективности разработанного технологического процесса;
-обозначены основные направления по обеспечению и повышению качества производимых работ;
После всех проведенных мероприятий производственная себестоимость работ по монтажу Дв.К. снизилась на 63 %.
Проведенный анализ в отношении применяемой оснастки показал возможность применения более современных технических средств при осуществлении работ по монтажу Дв.К. однако учитывая их высокую стоимость и универсальность необходимо произвести расчет экономической целесообразности их закупки в рамках всего завода для применения на разных проектах что выходит за рамки рассматриваемого в дипломе вопроса. И все же применение современных средств в частности лазерной установки для центровки позволит снизить трудоемкость при одновременном повышении качества выполняемых работ.
В качестве современных средств при планировании осуществления работ в проекте применена программа MS Project 2000. В которой произведено построение диаграммы Ганта для проведения работ по монтажу Дв.К. Она отображает в наглядном виде трудоемкость работ их параллельное осуществление (где это возможно) количество и разряд работающих по каждой конкретной операции и календарный график проведения работ. Построение подобных технологических документов позволяет найти пути снижения затрат времени на проведение работ.
При написании дипломной работы были выявлены пути снижения себестоимости производимых работ при одновременном совершенствовании технологической документации и методов проведения работ по монтажу Дв.К. Часть из них уже нашла реальное воплощение при работах на проекте.
Анурьев В.И. Справочник конструктора-машиностроителя. Том 1. М.: Машиностроение 1982. 734с.
Балацкий Л.Т. Бегагоен Т.Н. Дейдвудные устройства морских судов. М.: Транспорт 1980. 192с.
ГОСТ 12.1.005-88 Система стандартов безопасности труда. Общие санитарно-гигиенические требования к воздуху рабочей зоны.
Гультяев А.К. Управление проектами MS Project 2000. С-Пб.: Корона 2002. 368с.
Захаров Б.Н. Шмелев А.В. Наблюдение за постройкой испытания и приемка судов. Л.: Судостроение 1991. 506с.
Коршунов Л.П. Энергетические установки промысловых судов. Л.: Судостроение 1991. 355с.
Кузьменко В.К. Охрана труда в судостроении. Л.: Судостроение 1990. 254с.
Леонтьев В.М. Фролов Н.Ф. Технология постройки судов и судоремонт. Л.: Судостроение 1971. 384с.
Лукьянов И.С. Центровка валопроводов судов промыслового флота. М.: Пищевая промышленность 1979. 368с.
Морской Регистр Судоходства. Правила классификации и постройки морских судов. Том 2. 1995. 443с.
Нефтепродукты масла смазки присадки. Часть 2. М.: Издательство стандартов 1987.
НЯДИ.000.0308.00.002 Системы устройства механизмы и оборудования судов и плавучих сооружений. Требования по безопасности труда и охране окружающей среда при выполнении работ верфи. Инструкция.
НЯДИ.0000308.00.003Спецпокрытия стеклопластик. Типовые требования безопасности и охраны окружающей среды при демонтаже и восстановлении. Инструкция.
ОСТ5.4110-87Механизмы и фундаменты судовые. Общие технические требования к монтажу.
ОСТ5.4183-76Подшипники гребных и дейдвудных валов капролоновые. Общие технические условия.
ОСТ 5.4368-81Валопроводы судовые движительных установок. Монтаж. Технические требования правила приемок и методы контроля.
ОСТ 5.4405-84 Валопроводы судовых движительных установок. Монтаж. Типовой технологический процесс.
ОСТ5.9670-92Соединения конические судовых валопроводов.Типовые технологические процессы сборки и разборки.
ОСТ5.9966-85Устройства опорные гребных валов. Типовой технологический процесс монтажа с применением полимерных материалов.
ОСТ5Р.4471.0 – 91Уплотнения валов судовых валопроводов. Общие технические условия.
Пираниан Б.Н. Баранов В.В. Технология монтажа и ремонт судовых энергетических установок. Л.: Судостроение 1985. 244с.
Раздрогин Ю.В. Справочник по современным судостроительным материалам. Л.: Судостроение 1981. 198с.
Раицкий К.А. Экономика предприятия. М.: Информационно-внедренческий центр «Маркетинг» 2000. 696с.
Регистр. Руководство по техническому надзору за постройкой судов и изготовлением материалов и изделий. Часть 4. Надзор за постройкой судов.1992. 442с.
Рубин М.Б. Подшипники в судовой технике Л. Судостроение 1990.342 с.
Русинова Ф.М. Каменицера С.Е. Организация планирование и управление деятельностью промышленных предприятий. М.: Высшая школа 1984. 336с.
Справочник по современным судостроительным материалам. Л.: Судостроение 1979. 584с.
Формирование корпуса судна проекта 50010. Технологическая инструкция. 610.02-С1.008.00
Шенинг З.Р. Модульно-агрегатный метод монтажа судового оборудования. Л.: Судостроение 1991. 232с.
Шинкаренко В.И. Создание и развитие флота рыбной промышленности Судостроение 1996 октябрь.
Рекомендуемые чертежи
Свободное скачивание на сегодня
Обновление через: 10 часов 31 минуту