Резьбовой автомат на базе универсального вертикально-сверлильного станка модели 2А135




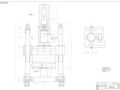
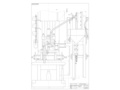
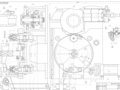
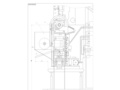
- Добавлен: 25.10.2022
- Размер: 837 KB
- Закачек: 0
Описание
Состав проекта
![]() |
![]() |
![]() ![]() ![]() ![]() |
![]() ![]() ![]() ![]() |
![]() ![]() ![]() ![]() |
![]() |
![]() ![]() ![]() ![]() |
![]() ![]() ![]() ![]() |
![]() ![]() ![]() ![]() |
![]() ![]() ![]() ![]() |
![]() ![]() ![]() ![]() |
![]() ![]() ![]() ![]() |
![]() ![]() ![]() ![]() |
![]() ![]() ![]() ![]() |
![]() ![]() ![]() ![]() |
![]() ![]() ![]() ![]() |
![]() ![]() ![]() ![]() |
![]() ![]() ![]() ![]() |
![]() ![]() ![]() ![]() |
![]() ![]() ![]() ![]() |
![]() ![]() ![]() ![]() |
![]() ![]() ![]() ![]() |
![]() |
![]() ![]() ![]() |
Дополнительная информация
Автомат для накатки резьбы.dwg

Циклограмма работы автомата.dwg

Державка сборочный чертеж.dwg

Лист 1.dwg

Лист 7.dwg

Лист 3.dwg

Лист 6.dwg

Лист 4.dwg

Лист 8.dwg

Лист 9.dwg

Лист 5.dwg

Державка 2.dwg

Лист 2.dwg

Державка 1.dwg

Державка 2.dwg

Автомат лист 2.dwg

Автомат для накатки резьбы 3.dwg

Державка 1.dwg

Автомат лист 3.dwg

Рекомендуемые чертежи
Свободное скачивание на сегодня
Другие проекты
- 24.04.2014