Токарный автомат на базе станка модели 1И611П для обработки детали типа валик




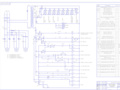
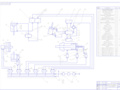
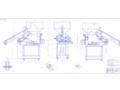
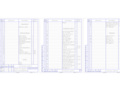
- Добавлен: 25.10.2022
- Размер: 4 MB
- Закачек: 0
Описание
Состав проекта
![]() |
![]() ![]() |
![]() ![]() |
![]() |
![]() ![]() ![]() ![]() |
![]() ![]() ![]() ![]() |
![]() ![]() ![]() ![]() |
![]() ![]() ![]() ![]() |
![]() ![]() ![]() ![]() |
![]() ![]() ![]() ![]() |
![]() ![]() ![]() ![]() |
![]() ![]() ![]() ![]() |
![]() ![]() ![]() ![]() |
![]() ![]() ![]() ![]() |
![]() ![]() ![]() ![]() |
![]() ![]() ![]() ![]() |
![]() ![]() ![]() ![]() |
![]() ![]() ![]() ![]() |
![]() ![]() ![]() ![]() |
![]() ![]() ![]() ![]() |
![]() ![]() ![]() ![]() |
![]() ![]() |
![]() ![]() |
![]() ![]() |
![]() ![]() |
![]() ![]() |
![]() ![]() |
![]() ![]() |
![]() ![]() |
![]() ![]() |
![]() ![]() |
![]() ![]() |
![]() |
![]() ![]() ![]() |
![]() ![]() ![]() |
![]() ![]() ![]() |
![]() ![]() ![]() |
![]() ![]() ![]() |
![]() ![]() ![]() |
![]() |
![]() ![]() |
![]() |
![]() ![]() ![]() |
![]() |
![]() |
![]() ![]() ![]() |
![]() ![]() ![]() |
![]() ![]() ![]() |
![]() ![]() ![]() |
![]() ![]() ![]() |
![]() ![]() ![]() |
![]() |
![]() ![]() ![]() |
![]() ![]() ![]() |
![]() ![]() ![]() |
![]() ![]() ![]() |
![]() ![]() ![]() |
![]() ![]() ![]() |
![]() ![]() ![]() |
![]() ![]() ![]() |
![]() ![]() ![]() |
![]() ![]() ![]() |
![]() ![]() |
![]() ![]() |
![]() ![]() |
![]() ![]() |
Дополнительная информация
Дипломный проект лист 2 2.dwg

Автомат для обработки валика стеклоподьемника. Схема электрическая принципиальная..dwg

валика стеклоподьемника.
Предохранители ТУ 16. 522. 112-74
Реле ТРН-10 Jнагр.=6
Реле ТРН-10 Jнагр.=0
Лампа коммутаторная ГОСТ 6940-74
Пускатель ПМЕ-112 Uk=
Реле РПУ-363 ТУ 16. 523. 20-76. Uk=110В
Реле времени РВП-72-3222-00У4 Uk=110В
Автоматич. выключатель АП-50Б-3МГ
Кнопка КЕ-011У3 исп.2
Тумблер Т3 ВРО. 360. 073 ТУ
Тумблер ТП1-2 УСО. 360. 049. ТУ
Выключатель пакетный ПВМ 3-15
Выключатель конечный ВПК-2111
Переключатель бесконтактный БВК-201-24
Выключатель бесконтактный У511-31
Выключатель бесконтактный "Bellof
Воздухораспределитель ПВ64-23м
Конденсатор КГБ 1МКФ
Выпрямительный мост диод 242Б
Реле промежуточное МКУ-48
Пускатель ПМЕ-071. Uk=
Электодвигатель РД-09 Uk=
Установка исходного положения
М1 - электродвигатель шпинделя.
М2 - электродвигатель смазки.
М3 - электродвигатель охлаждения.
М4 - электродвигатель командоаппарата.
цилиндр задней бабки
Переднее положение суппорта.
Механизм подачи детали.
Двигатель привода станка.
Автомат для обработки валика стеклоподьемника.dwg

валика стеклоподьемника
Привод поперечной подачи
Устройство бункерно-загрузочное
Модуль-командоаппарат
Пробка К38" ОСТ 2С98=3-73
Присоединение концевое
Соединение 10 АС 343-70
Хомутик ЦТ.7020-0143
Угольник К 38" П7-223-69
Фильтр-влагоотделитель
Пневмоклапан редукционный
(регулятор давления)
2-12 (12-1) ГОСТ 18468-79
-10(44-23) ГОСТ 25531-82
Арматура ЦТ.7026-001
Блок золотников 6-ПА-18
Валик Стеклоподьемника.dwg

Неуказанные радиусы закруглений до 0
Неуказанные литейные уклоны 0
Маркировать шрифтом 2
-Пр.3 ГОСТ 26.008-85.
Остальные технические требования по ОСТ 3-4224-79.
Автомат для обработки валика стеклоподьемника. Сборочный чертеж.dwg

валика стеклоподьемника
Техническая характеристика
Мощность электродвигателя
Производительность (расчетная)
Частота вращения шпинделя
Давление в пневмосистеме
Давление в гидросистеме
Наибольшее перемещение суппорта поперечной подачи
Технические требования
Размеры для справок.
Рукоятки продольной подачи и перемещения верхних салазок
после установки зафиксировать.
Рукоятки поперечной подачи
реверсирования подачи
Доработку станины станка для установки узлов поз. 3 и поз. 6
производить по месту.
Обработку отверстий для крепления лотка поз. 8 и кронштейна
Заднюю бабку поз. 1 после установки жестко закрепить на
станине болтом (принадлежность станка).
Наружные поверхности станка окрасить согласно колеру станка
Ограждение поз. 7 не показано
Автооператор Сборочный чертеж.dwg

Угол поворота штока подающей руки
Длина хода подающей руки
Давление в пневмосистеме
Технические требования
Обеспечить свободное перемещение детали поз. 1.
Обеспечить подачу деталей на линию центров шпинделя
регулировкой и подгонкой деталей поз. 11 и 47.
Обеспечить в положении загрузки параллельность рабочих
поверхностей П прижимов относительно оси шпинделя.
Шпиндельный узел с зажимом цанговым.dwg

Устройство бункерное загрузочноеСборочный чертеж.dwg

Техническая характеристика
Емкость бункера(расчетная)
Количество одновременно загружаемых деталей 408-6104036-10
Переодичность загрузки деталей (расчетная)
Технические требования
Размеры для справок.
безударное движение сектора поз. 14 со
скорстью не вызывающей подпрыгивание деталей
регулировки дросселями поз. 57.
Бабка задняя.dwg

Бабку ежедневно смазывать консистентной смазкой
ЦИАТИМ-202 ГОСТ 11110-75.
Кольцо амортизационое поз. 12 поставить на клей 88 Н
Валик Стеклоподьемника 2.dwg

Неуказанные радиусы закруглений до 0
Неуказанные литейные уклоны 0
Маркировать шрифтом 2
-Пр.3 ГОСТ 26.008-85.
Несоостность поверхностей Б и В неболее 0
Остальные технические требования по ОСТ 3-4224-79.
Дипломный проект лист 2.dwg

Организационно-экономическая часть. ТЭП..dwg

2. Коэффициент роста производительности
4. Ремонтосложность механической
Затраты на эксплуатацию
3. Техническое обслуживание и ремонт
Технико-экономические показатели проекта
Схема гидропневмо-кинематическая.dwg

Автомат для обработки валика стеклоподьемника. Схема соединений.dwg

валика стеклоподьемника.
Система подготовки воздуха
Арматура ЦТ. 7026-0001
Блок золотников 6-ПА-18
Аккумулятор пневмогидравлический
Пневмораспределитель Б63-13М
Пневмодроссель 10-2 ГОСТ 19485-81
Муфта распределительная П7-114-61
Соединение 3 7020-1619
Соединение 10 АС-343
Соединение концевое БС91-12
Соединение концевое БС91-25
Соединение концевое БС91-15
Хомутик СТ 7020-0143
Соединение концевое БС91-16
Пробка К 38" ОСТ 2С98-3-73
Рукав Г6-16-27 ГОСТ 18698-79
Автомат для обработки валика стеклоподьемника. Циклограмма..dwg

валика стеклоподьемника.
Время срабатывания пневмоприводов - Т1 цикла = 6 сек.
Привод поперечной подачи.dwg

Каретка поперечного суппорта должна свободно перемещаться
для чего матку и поперечный винт убрать.
Непараллельность плоскостей Д и Е не более 0
Отверстия под винты для крепления выключателей поз. 49
обработать по месту.
Отверстие под болт поз. 22 обработать по месту.
Кронштейн поз. 2 и опору поз. 3 после сборки и отладки
привода заштифтовать по месту.
Кинематическая схема.dwg

5 Экономика.doc
Эти требования могут быть удовлетворены (выполнены) различными путями поскольку технолог может применять различные варианты обработки детали в одинаковой мере обеспечивающие выполнение поставленных требований.
Отсюда возникает необходимость выбрать такой вариант оборудования который позволил бы добиться нужного результата в наиболее короткие сроки с наименьшими затратами труда и средств то есть экономически наиболее целесообразный.
Таким образом целью данного раздела является расчет годового экономического эффекта от принятого к внедрению варианта оборудования.
2. Выбор базы для сравнения
Проектируемый в дипломном проекте вариант оборудования рассчитан на применение в рамках отдельного конкретного предприятия то есть решается задача совершенствования (модернизации) существующего заводского варианта оборудования который и принимается за базу для сравнения.
Таким образом далее будут сравниваться два варианта которые должны удовлетворять условиям сопоставимости вариантов приведенных в [16].
Сопоставимость вариантов:
сравниваемые варианты будут сопоставимы так как:
номенклатура продукции одинакова;
объём выпуска равный;
качество получаемой продукции одинаково;
условия труда сходны;
источники информации одни и те же;
степень безопасности и экологичности на одном уровне.
Оценка экономического эффекта при совершенствовании существующего оборудования имеет целью выбор наилучшего варианта конструкции оборудования.
Металлорежущее оборудование относится к средствам труда долговременного применения. При его производстве и использовании с улучшенными качественными характеристиками (производительность долговечность издержки эксплуатации и др.) в соответствии с методикой [16] годовой и экономический эффект рассчитывается по формуле:
3. Определение нормы времени работы
и годового объема выпуска деталей
От качества нормирования времени на работу зависит правильность определения потребности в металлорежущем оборудовании и рабочей силе а следовательно достоверность расчета экономического эффекта. Применяют два основных метода установления норм времени: опытно-статистический аналитически-расчетный. В соответствии с рекомендацией данной в [16] установление норм времени лучше производить аналитически-расчетным методом.
Норма штучного времени на операцию определяется по формуле:
где – основное время; – вспомогательное время; – время технического и организационного обслуживания; – время на отдых и личные надобности; – оперативное время.
Основное время рассчитывается по формуле [29]:
где – расчетная длина обработки n – частота вращения шпинделя n = 500 обмин (см. техпроцесс); s – подача на один оборот обрабатываемой детали s = 016 мм.
Сумма нормы основного и вспомогательного времени составляет оперативное время:
В соответствии с рекомендацией данной в [29] время технического и организационного обслуживания составляет 1-6% от оперативного времени:
Время на отдых и личные надобности является последним слагаемым штучного времени. Величина его может колебаться в пределах ст 10 до 20% от оперативного времени [29] тогда:
При расчете сравнительной экономичности способов и средств нормы времени по вариантам необходимо определять одинаковыми методами. Поэтому определение нормы времени по базовому варианту следует проводить также аналитически-расчетным методом.
Определение основного времени по базовому варианту производится по той же формуле что и при расчете проектного варианта поэтому:
Вспомогательное время состоит из времени на снятие и установку обрабатываемой детали. Оно повторяется с каждой обрабатываемой деталью.
Время на обслуживание и отдых определяется по тем же формулам что и при расчете по проектному варианту.
Годовой объем продукции производимой с использованием проектируемого оборудования рассчитывается по формуле взятой из [16].
где N – годовая производительность разрабатываемого оборудования в натуральных единицах (деталях); Fд – действительный годовой фонд времени работы оборудования Fд = 1970 час (данные с завода); tc – норма времени на выполнение операции tc = 0176 мин; Кз – нормативный коэффициент загрузки металлорежущего оборудования Кз = 07 для массового производства (см. [16]); Кв – коэффициент выполнения норм (для действующего производства принимается по фактическим данным а для вновь проектируемого –по фактическим данным выполнения норм на аналогичных работах) Кв = 1.
4. Расчет сопутствующих капитальных вложений
К сопутствующим капитальным вложениям относятся:
затраты на доставку монтаж и отладку оборудования;
стоимость производственной площади занимаемой оборудованием;
стоимость служебно-бытовых помещений;
Поскольку годовой объем продукции принят исходя из годовой производительности единицы разрабатываемого оборудования то для определения сопутствующих капитальных вложений по базовому варианту необходимо сначала рассчитать потребное количество оборудования необходимого для выполнения годового объема продукции. Расчет количества металлорежущего оборудования производится по формуле взятой из [16]:
где Mp – расчетное количество единиц оборудования; tc – норма времени на выполнение операции tc = 0176 мин; N – годовой объем изготовления деталей в штуках исходя из производительности нового оборудования N = 470113 шт; Fд – действительный годовой фонд времени работы оборудования Fд = 1970 час (данные с завода); – нормативный коэффициент загрузки металлорежущего оборудования Кз = 07 для массового производства (см. [16]); Кв – коэффициент выполнения норм Кв = 1.
В массовом производстве при невозможности дозагрузки оборудования обработкой другими деталями расчетное количество единиц оборудования округляется до ближайшего целого числа и последующий расчет сопутствующих капитальных вложений и издержек производства ведется исходя из принятого количества оборудования
Затраты на доставку монтаж и отладку оборудования рассчитывается по формуле взятой из [16]:
где Кд – затраты на доставку монтаж и отладку оборудования руб; Ц – цена единицы оборудования руб; (по данным завода-изготовителя цена базового станка 1И611П составляет 120т.руб. цена разрабатываемого автомата выше на 20%); Мр – расчетное количество единиц оборудования (для базового варианта Мр = 2 для проектного Мр =1); – коэффициенты учитывающие соответственно транспортно-заготовительные расходы связанные с доставкой оборудования затраты на строительные работы и устройство фундамента для оборудования затраты на монтаж и освоение оборудования.
В соответствии с рекомендацией данной в [16] для оборудования массой менее 10т. коэффициент = 01 коэффициенты для приближенных расчетов могут быть приняты равными 005.
Проектный вариант: руб.
Базовый вариант: руб.
Стоимость производственной площади занимаемой оборудованием определяется по формуле взятой из [16]:
где Кпп – стоимость производственной площади занимаемой оборудованием руб; Sоб – производственная площадь занимаемая единицей оборудования м2; fоб – стоимость 1м2 производственной площади fоб = 1100 руб. (по данным завода); Sпл – площадь оборудования в плане с учетом вылета рабочих органов м2; Мр – расчетное количество единиц оборудования.
Руководствуясь паспортными данными станка 1И611П и чертежами общего вида площадь оборудования можно рассчитать по их габаритам.
– коэффициент учитывающий дополнительную производственную площадь равный для обоих вариантов 5 (см. приложение 2 [16]).
Стоимость служебно-бытовых помещений определяется по формуле взятой из [16]:
где Ксб – стоимость служебно-бытовых помещений руб; Sсб – площадь служебно-бытовых помещений занимаемая одним рабочим-станочником или наладчиком Sсб = 4 м2 (по данным завода); Рс – численность рабочих-станочников чел; Рн – численность наладчиков; fсб – стоимость 1 м2 служебно-бытовых помещений fсб = 1350 руб. (по данным завода).
Численность станочников и наладчиков определяется по формулам взятым из [16]:
где t – норма времени на выполнение операции t = 0176 мин. (см. техпроцесс); N – годовой объем изготовления деталей в штуках исходя из производительности нового оборудования N = 470113 шт; Ф – полезный годовой фонд времени одного рабочего равный 1970 час; Кв – коэффициент выполнения норм Кв = 1; D – число рабочих смен D = 1 ( по данным завода); Ксп – коэффициент среднесписочного состава равный 11 [16]; Н – норма обслуживания станков наладчиком Н = 2 [21 табл. 12 24].
Общие сопутствующие капитальные вложения по вариантам расчета определяются по формуле:
5. Расчет годовых эксплуатационных издержек
Заработная плата рабочих-станочников с отчислениями на социальное страхование определяется по формуле взятой из [16]:
где t – норма времени на выполнение операции =0176 мин. (см. техпроцесс); Чс – часовая тарифная ставка станочника равная 567 руб. (по данным завода); Чн – часовая тарифная ставка наладчика равная 978 руб. (по данным завода); 1 – коэффициент учитывающий дополнительную заработную плату (принимается равным 11 [16]); 2 – коэффициент учитывающий премиальные доплаты (принимается равным 14 по данным завода); 3 – коэффициент учитывающий отчисления в фонд социального страхования (принимается равным 137 [16]); 4 – районный коэффициент (в уральской зоне равен 115 [16]); N – годовой объем изготовления деталей в штуках исходя из производительности нового оборудования N = 470113 шт;
Заработная плата наладчиков с отчислениями на социальное страхование определяется по формуле взятой из [16]:
Затраты на силовую электроэнергию для металлорежущих станков определяются по формуле взятой из [16]:
где W – суммарная установленная мощность электродвигателей станка кВт.
Суммарная установленная мощность электродвигателей базового станка складывается из мощности электродвигателя привода главного движения охлаждения и смазки:
Wб = 30 + 00125 + 009 = 3215 кВт.
Суммарная установленная мощность электродвигателей проектируемого станка складывается из мощности электродвигателя привода главного движения электродвигателя командоаппарата и электродвигателя смазки:
Wп = 30 + 006 + 009 = 315 кВт;
Цэ – стоимость одного киловатт-часа электроэнергии равная 65коп.кВт (по данным завода); N – годовой объем изготовления деталей в штуках исходя из производительности нового оборудования N = 470113 шт; – средний КПД электродвигателей станка равный 095; α1 – коэффициент загрузки по мощности электродвигателей станка равный 080 [21 табл.73]; α2 – коэффициент загрузки по времени электродвигателей станка равный 05 [21 табл. 7 6]; α3 – одновременной работы электродвигателей станка равный 1; α4 – коэффициент учитывающий потери электроэнергии в сети завода равный 105 [16];
Затраты на режущий инструмент определяются по формуле взятой из [16]:
где z – цена инструмента равная 45 руб. за каждый резец с твердосплавной пластиной (данные завода); Y – затраты на одну переточку инструмента руб.;
Ориентировочно затраты на все переточки можно принять в процентах от цены инструмента [21]:
где h – число переточек до полного износа равное 10 [21 табл. 7.12]; to – основное время операции мин. равное 008125 мин.; – период стойкости инструмента между переточками равный 2 [21 табл. 7.12]; γ – коэффициент случайной убыли равный 119 [21 табл. 7.12]; N – годовой объем изготовления деталей в штуках исходя из производительности нового оборудования N = 470113 шт; m – количество наименований режущих инструментов в станке равное 2.
Т.к. резцы отличаются лишь геометрией крепежной части то затраты на них будут одинаковыми поэтому:
Затраты на режущий инструмент по базовому и проектному вариантам будут одинаковыми т.к. режущий инструмент и режимы обработки не меняются.
Затраты на техническое обслуживание и ремонт оборудования определяются по формуле взятой из [16]:
где R – ремонтосложность механической части оборудования в единицах ремонтной сложности равная 13 для базового оборудования и 14 для проектируемого (по данным завода); V – годовые затраты на обслуживание и ремонт приходящиеся на единицу КРС V = 309 руб. (данные завода); Кэ – коэффициент учитывающий затраты на ремонт электрической части оборудования равный 13 для базового оборудования и 16 для проектируемого (по данным завода).
Амортизация на полное восстановление сопутствующих капитальных вложений в оборудование определяется по формуле взятой из [16]:
где Кд – затраты на доставку монтаж и отладку оборудования руб; Мр – расчетное количество единиц оборудования; а – норма амортизационных отчислений на полное восстановление в процентах равная [16].
Затраты по амортизации и содержанию сопутствующих капитальных вложений в оборудование определяются по формуле взятой из [16]:
где Sпп – производственная площадь занимаемая оборудованием для проектного варианта Sпп = 1085 м2 для базового Sпп = 858 м2; Sсб – площадь служебно-бытовых помещений Sсб = 4 м2 (по данным завода); L – годовые затраты по амортизации и содержанию 1 м2 производственной площади и площади служебно-бытовых помещений определяется в процентном соотношении от стоимости служебно-бытовых помещений.
Для проектного варианта
Суммарные годовые издержки по вариантам расчета определяются по формуле:
В соответствии с методикой [16] годовой и экономический эффект рассчитывается по формуле:
где Ц1 и Ц2 – цена соответственно базового и нового оборудования (по данным завода-изготовителя цена базового станка 1И611П составляет Ц1 = 120 тыс. руб. цена разрабатываемого автомата выше на 20% Ц2 = 144 тыс. руб.); В – коэффициент учета роста производительности нового оборудования по сравнению с базовым. Определяется отношением штучного времени обработки детали на базовом и новом оборудовании;
Р1 и Р2 – доли отчислений от балансовой стоимости на полное восстановление соответственно базового и нового оборудования. Рассчитываются как величины обратные срокам службы оборудования определяемые с учетом их морального износа срок службы базового станка 1И611П составляет 20 лет (паспортные данные станка) нового – 15 лет поэтому Р1 = 00175 и Р2 = 00315 [16 прил. 1]; И1 и И2 – годовые эксплуатационные издержки потребителя И1 = 10762717 руб. и И2 = 691014 руб. (расчет выше); К1 и К2 – сопутствующие капитальные вложения потребителя при использовании им базового и нового оборудования в расчете на объем продукции производимый с помощью нового оборудования К1 = 77406 руб. и К2 = 47485 руб.; А2 – годовой объем производства металлорежущего оборудования в расчетном году в натуральных единицах.
Расчет показал что проектный вариант металлорежущего оборудования дает положительный экономический эффект и в данном случае является однозначно наилучшим вариантом оборудования.
Наиболее значимые различия вариантов наблюдаются при расчете сопутствующих капитальных вложений и расчете годовых эксплуатационных издержек. Это объясняется тем что в результате расчета потребное количество единиц базового оборудования равно двум поскольку годовой объем продукции принят исходя из годовой производительности единицы нового оборудования.
Таким образом расчет показал целесообразность производства и эксплуатации проектируемого оборудования.
Глава7.doc
Наименование: Общий вид станка (лист 1).
Показан главный вид станка. Приведены технические требования и техническая характеристика станка. Ограждение поз. 7 не показано.
Наименование: Общий вид станка (лист 2).
Показаны вид сзади и вид сбоку станка. Обозначены основные узлы станка. Показаны габаритные размеры станка.
Наименование: Бабка задняя.
Сборочный чертеж включает: цилиндр поз.2 поршень поз.14 шток поз.13. Главный вид выполнен в разрезе. Показаны основные размеры проставлены посадки и сформулированы технические требования. Задняя бабка выполнена телескопически. Такая конструкция обеспечивает высокую надежность узла и четкое выполнение перемещений согласно циклограмме работы станка.
Наименование: Схема электрическая принципиальная.
На чертеже показана схема всего электрооборудования станка включение электродвигателей в цепь блоки управления: механизма подачи детали 1-го цилиндра задней бабки 2-го цилиндра задней бабки зажима цанги суппорта исходного положения командоаппарата исходного положения суппорта.
На чертеж вынесена спецификация с указанием основных параметров отдельных узлов схемы.
Электродвигатели и аппаратура рассчитаны на включение в сеть напряжением 380 В и частотой 50 Гц. Напряжение в цепи управления 110В.Напряжение в цепи сигнализации 55 В. Подключение электрической части станка к сети осуществляется автоматическим выключателем АСТ-3. Вся электроаппаратура смонтирована в отдельно стоящем шкафу.
На пульте управления станка предусмотрены сигнальные лампы «Сеть» «Автомат» «Наладка» «Конец цикла» «Наличие детали». Сигнальная лампа «Наличие детали» загорается при отсутствии детали на позиции обработки. Для счета обработанных деталей на эл.шкафу смонтирован электроимпульсный счетчик.
Наименование: Циклограмма. Автомат для обработки валика стеклоподъемника.
На чертеже показана циклограмма работы станка которая показывает продолжительность каждого из переходов в цикле.
Продолжительность переходов необходимо знать при выборе электродвигателя привода главного движения.
В соответствии с циклограммой работа станка начинается с нажатия кнопки «Вкл. Автомат».
Срабатывает пневмоцилиндр Ц4 подающей руки автооператора и подает деталь на ось центров автомата. В конце хода руки срабатывает конечный выключатель SQ1 который дает команду на золотник Р6 (Y2) телескопического пневмоцилиндра задней бабки Ц6 происходит выдвижение пиноли задней бабки на 85 мм которая своим упором выталкивает деталь из подающей руки в цанговый зажим шпинделя станка. В конце хода пиноли срабатывает конечный выключатель SQ 2 подающий команду на золотник Р4 (Y1) – пневмоцилиндр Ц4 переключается на обратный ход подающая рука автооператора возвращается в исходное положение. После 35 мм хода назад подающей руки срабатывает конечный выключатель SQ3 дающий команду на золотник Р7 (Y3) телескопического цилиндра задней бабки Ц7 – происходит окончательная подача детали в цангу до упора.
В конце хода пиноли задней бабки срабатывает конечный выключатель SQ4 дающий команду на золотник Р1 (Y4); срабатывает пневмоцидиндр Ц1 цангового зажима детали. При достижении усилия зажима Рз = 180 кг (расчетное) реле давления дает команду на золотники Р6 (Y2) и происходит переключение телескопических цилиндров Ц6 и Ц7 пиноль задней бабки возвращается в исходное положение. Одновременно реле давления дает команду на электромагнитную муфту включающую вращение шпинделя и на золотник Р3 (Y5) подающий сжатый воздух в гидробак.
Масло из гидробака поступает в гидроцилиндр Ц3 перемещая каретку с резцедержателем. Холостой ход каретки и рабочий ход обеспечивается дросселем с регулятором обратным клапаном и золотником ПГ-55-62 управляемым кулачком прикрепленным на каретке станка. В конце хода каретки т.е. после окончания обработки детали срабатывает конечный выключатель SQ5. Происходит быстрый отвод суппорта поперечной подачи в конце хода которого включается конечный выключатель SQ6. Происходит разжим и удаление детали посредством выталкивающей пружины.
Далее цикл повторяется – срабатывает пневмоцилиндр Ц4 подающей руки автооператора и подает деталь на ось центров.
Наименование: Схема гидропневмокинематическая. Автомат для обработки валика стеклоподъемника.
На чертеже показаны все гидро- и пневмоцилиндры схема включения их в гидро- и пневмолинию а также регуляторы дроссели и эл. контакты обеспечивающие автоматический цикл работы станка.
Наименование: Схема кинематическая. Валик стеклоподъемника.
Представлена кинематическая схема токарного автомата с автоматическим переключением скоростей благодаря включению в схему гидроцилиндров. Проставлены позиции валов и зубчатых колес с указанием числа зубьев. Представлен график частот вращения шпинделя.
На данном листе также представлены рабочие чертежи обрабатываемых деталей. Показаны все технологические размеры проставлены отклонения шероховатости поверхностей. Дан разрез детали сформулированы технические требования.
Наименование: Автооператор.
Показан способ крепления руки автооператора к станине станка. Приведены все необходимые виды разрезы и сечения объясняющие устройство и принцип работы механизма. Проставлены основные и установочные размеры. Приведены технические требования и техническая характеристика.
Наименование: Шпиндельный узел с зажимом цанговым.
Показан шпиндельный узел токарно-винторезного станка 1И611П с зажимом цанговым работающим посредством вращающегося пневмоцилиндра. Показаны все технологические размеры проставлены отклонения. Показаны габаритные размеры шпиндельной бабки.
Наименование: Бункерное загрузочное устройство.
Показано бункерное загрузочное устройство которое обеспечивает передачу заготовок сконцентрированных в бункере навалом на ось руки автооператора. Качающийся сектор захватывает заготовки из бункера и передает их в лоток в котором заготовки перемещаются под действием собственной силы тяжести. Заготовки имея вертикальную ориентацию попадают в отсекатель который в нужный момент пропускает одну заготовку. Далее заготовка падает в стаканчик автооператора и подается на в зону обработки.
На чертеже показаны габаритные и установочные размеры изображены все необходимые виды сечения и разрезы. Приведены технические требования и техническая характеристика.
Наименование: Привод поперечной подачи. (лист 1).
Показано крепление гидроцилиндра к станине станка. Дан разрез показывающий конструкцию. Проставлены все необходимые размеры гидроцилиндра. Приведены технические требования.
Наименование: Привод поперечной подачи. (лист 2).
Показан вид сверх и вид сзади стака. Вынесены сечения показывающие крепление штока гидроцилиндра к каретке резцедержателя. Проставлены все необходимые размеры.
Наименование: Схема соединений.
Показана схема питания пневмо и гидроцилиндров. Сжатый воздух от источника питания через фильтр-влагоотделитель ВД редукционный клапан РД маслораспылитель МР поступает на вход пневмораспределителей. Откуда воздух по пневмолиниям поступает в полости цилиндров. Скорость потока воздуха регулируется дросселями.
Наименование: Организационно-экономическая часть.
Чертеж представляет собой таблицу технико-экономических показателей дипломного проекта.
В ходе выполнения дипломного проекта был разработан специальный токарный автомат на базе одношпиндельного токарно-винторезного станка 1И611П. Разработка данного автомата выполнена с целью повышения производительности станка (400-600 детчас) и как следствие повышение производительности труда рабочего. При этом рабочий освобождается от непосредственного участия в процессе обработки детали от однообразных повторяющихся движений от монотонных нервных и физических напряжений. Вместе с тем повышается технический уровень обслуживания станка при его подготовке к производству – наладке и во время его эксплуатации. Модернизация станка вносит ритмичность в процесс обработки и способствует стабильности качества.
В ходе работы выполнено следующее:
Модернизирована задняя бабка с целью автоматизации перемещения пиноли посредством пневмопривода.
Разработан цанговый зажим который служит для автоматического зажима детали и удаления ее после обработки посредством выталкивающей пружины. Цанговый зажим установленный в шпинделе станка работает с помощью вращающегося пневмоцилиндра.
Разработаны автоматические бункерно-загрузочное устройство и автооператор которые обеспечивают нужную ориентацию заготовки в пространстве и передачу её в зону обработки. В качестве приводного механизма также используется пневматика.
Спроектирован автоматизированный привод поперечной подачи работа которого осуществляется посредством гидравлики поскольку применение пневматики в данном механизме не может обеспечить заданный закон движения и стабильность скорости движения выходного звена.
Выполнены все необходимые расчеты предусмотренные методическими указаниями по выполнению дипломного проекта.
Представлен рабочий маршрутно-технологический процесс детали 408-6104036-10 «валик стеклоподъемника».
Произведен расчет экономического эффекта от производства и эксплуатации проектируемого автомата.
В соответствии с заданием по охране труда обеспечены все требования безопасности при разработке нового оборудования.
Анурьев В.И. Справочник конструктора – машиностроителя: В 3 т. М. 1979 – 1982. т. 1 – 728 с. т.2 – 559 с. т. 3 – 557 с.
Безопасность технологических процессов и производств: Охрана труда: Учебн. пособие для вузов. Кукин П.П. Лапин В.Л. и др. – Мн.: Выш.школа 2001. – 320 с. ил.
Бобров В.П. Проектирование загрузочно-транспортных устройств. –М.: Машиностроение 1964. – 291с.: ил.
Волкевич Л.И. Усов Б.А. Автооператоры – М.: Машиностроение 1963. – 299 с.: ил.
В помощь конструктору – станкостроителю В.И. Калинин В.Н. Никифоров Н.Я. Аникеев и др. М.: Машиностроение 1983. – 288 с. ил.
Выбор конструкции и расчет шпиндельных узлов металлорежущих станков: Методические указания. ч.2 Ижевск. мех. ин-т; Сост. В.В. Пузанов Ф.Ю. Свитковский. Ижевск 1990. 32с.
Выбор двигателей приводов станков: Методические указания. ч.2 Ижевск. мех. ин-т; Сост. В.В. Пузанов Ф.Ю. Свитковский. Ижевск 1990.
Гидравлика гидромашины и гидропроводы: Учебник для машиностроительных вузов Т.М. Башта С.С. Руднев Б.Б. Некрасов и др. – 2-е изд. перераб. и доп. – М.: Машиностроение 1982. – 423с. ил.
Гидроприводы и гидропневмоавтоматика станков: Метод. указания к курсовому проектированию (для специальностей 1201. 1202) Ижевск. мех. ин-т; Сост. Б.Н. Зенков. Ижевск 1990 36 с.
Гидроприводы и гидропневмоавтоматика станков: Метод. руководство для самостоятельного изучения общих сведений технической гидромеханики гидропривода и гидропневмоавтоматики станков. ч.5. Элементы пневмоаппаратуры высокого давления (для специальностей 1201 1202) Ижевск. мех. ин-т; Сост. Б.Н. Зенков Р.С. Музафаров. Ижевск 1993.
Горбацевич А.Ф. Шкред В.А. – Курсовое проектирование по технологии машиностроения: [Учебное пособие для машиностроит. спец. вузов]. – 4-е изд. перераб. и доп. – Мн.: Выш.школа 1983. – 256 с. ил.
Горошкин А.К. – Приспособление для металлорежущих станков: Справочник. – 7-е изд. перераб. и доп. – М.: Машиностроение 1979. – 303 с. ил.
Иванов М.Н. Детали машин. М. 1984. 399 с.
Кочергин А.И. Конструирование и расчет металлорежущих станков и станочных комплексов. Курсовое проектирование: Учебн. пособие для вузов. – Мн.; Выш. шк. 1991. – 382.; ил.
Кузнецов Ю.И. Маслов А.Р. Байков А.Н. Оснастка для станков с ЧПУ: Справочник. – М.: Машиностроение 1983. – 359 с.: ил.
Кучер И.М. и Кучер А.М.- Модернизация и автоматизация станков – Л.: Машгиз 1958. – 299 с.: ил.
Малов А.Н. Загрузочные устройства для металлорежущих станков. – М.: Машиностроение 1979. – 399 с.: ил.
Медвидь М.Н. Автоматические ориентирующие загрузочные устройства. – М.: Машиностроение 1963. – 299 с.: ил.
Металлорежущие станки Н.С. Ачеркан. В 2-х т.; Под ред. Н.С. Ачеркана. – 2-е изд. перераб. и доп. – М.: Машиностроение 1965. – 764 с.: ил.
Методические указания к дипломному проектированию по металлорежущим станкам и металлорежущему инструменту Ижевск. мех. ин-т; Сост. В.В. Пузанов А.А. Модзелевский Ю.Г. Глухов. Ижевск 1983.
Методические указания к лабораторной работе «Реализация цикла движений узлов станка с ЧПУ модели 1И611ПФЗ средствами гидроавтоматики» Ижевск. мех. ин-т; Сост. В.Ф. Иванов Р.С. Музафаров. Ижевск 1989.
Методические указания по кинематическому расчету приводов станков и построению их кинематических схем. Ижевск. мех. ин-т; Сост. В.В. Пузанов Ижевск 1989.
Методические указания по проведению патентных исследований при курсовом и дипломном проектировании по металлорежущим станкам и инструментам. Ижевск. мех. ин-т; Сост. А.И. Хватов Ижевск 1986.
Методические указания по расчету экономического эффекта при разработке металлорежущего оборудования в процессе дипломного проектирования студентов специальности 12.02 Ижевск. мех. ин-т; Сост. А.С. Севрюгин. Ижевск 1991. 20с.
Общемашиностроительные нормативы времени для нормирования многостаночных работ на металлорежущих станках. М.: Экономика1997.
Оформление расчетно-пояснительных записок к курсовому и дипломному проектам: Методические указания для студентов заочного обучения Ижевск. мех. ин-т; Сост. Ф.Ю. Свитковский. Ижевск 1989 16 с.
Охрана труда в машиностроении: Учебник для машиностроительных вузов Е.Я. Юдин С.В. Белов С.К. Баланцев и др.; Под. ред. Е.Я.Юдина С.В.Белова – 2 -е изд. перераб. и доп.-М.: Машиностроение 1983. – 432 с. ил.
Проектирование металлорежущих станков и станочных систем: Справочник-учебник. В 3-х т. Т.2. Расчет и конструирование узлов и элементов станков А.С. Проников Е.И. Борисов В.В. Бушуев и др.; Под общ. ред. А.С. Проникова. – М.: Издательство МГТУ им. Баумана: Машиностроение 1995. – 371 с.: ил.
Проектирование механических передач: Учебно-справочное пособие для втузов С.А. Чернавский Г.А. Снесарев Б.С. Козинцов и др. – 5-е изд. перераб. и доп. – М.: Машиностроение 1984. – 560 с. ил.
Расчеты экономической эффективности новой техники: Справочник Под ред. К.М. Великанова – Л .: Машиностроение. Ленингр. отд-ние 1990. – 439 с.: ил.
Решетов Д.Н. Учебник для студентов машиностроительных и механических специальностей вузов. – 4-е изд. прераб. и доп. М.: Машиностроение 1989. – 496с.: ил.
Свешников В.К. Усов А.А. Станочные гидроприводы: Справочник. – М.: Машиностроение 1982. – 464 с. ил.
Свирщевский Ю. И. Расчет и конструирование коробок и скоростей подач. Минск.:Высшая школа. 1976. – 590 с.ил.
Соколов Н.Г. и Елисеев В.А. Расчеты по автоматизированному электроприводу металлорежущих станков. М. «Высшая школа» 1969. 296 с.
Справочник нормировщика Под. общ. ред. А.В. Ахумова. Л.: Машиностроение. Ленингр. отд-ние 1986.
Справочник технолога-машиностроителя. В 2-х т. Т. 2 Под ред. А.Г. Косиловой и Р.К. Мещерякова. – 4-е изд. перераб. и доп. – М.: Машиностроение1986. 496с. ил.
Стародуб Н.П. Автоматизция токарной обработки при помощи пневмоустройств. – Мн.: Выш.школа 1979. – 143 с. ил.
Экономика и организация производства в дипломных проектах: Учебник для машиностроительных вузов К.М. Великанов Э.Г. Васильева В.Ф. Власов и др.; Под общ. ред. К.М. Великанова – 4-е изд. перераб. и доп. – Л.: Машиностроение. Ленингр. отд-ние 1982. – 423 с.: ил.
доклад.doc
Автомат спроектирован для эксплуатации на Автозаводе с учетом использования имеющегося оборудования за базу принят ток-вин станок 1И611П.
В д. проектировании поставлена следующая цель:
-увеличить производительность обработки детали «валик стекл. Автомобиля ИЖ2126» на операции точение для сокращения потребного количества единиц оборудования.
В соответствии с целью поставлены сл. Задачи:
- осуществить автоматизацию рабочих и вспомогат. ходов цикла обработки детали;
- осуществить автоматизацию загрузки выгрузки станка;
-обеспечить требования предъявляемые к детали.
При автоматизации цикла обработки за базу принята система управления с упорами. Принцип формообразования поверхностей при обработке заключается в том. что заготовка осущ. вращ. движение а инструмент в виде Фасонно-отрезного резца имеет движение попер. подачи.
состоит из станка 1И611П и из следующих узлов: БЗУ которое служит для загрузки заготовок Автооператор для передачи заготовки в зону обработки Бабка задняя подающая заготовку в цанг.зажим Зажим цанговый для автоматич. зажима загот. и удаления её после обработки Привод поперечной подачи для производства точения и электрооборудование управляющее этими узлами.
В основном Автоматизация проектируемых механизмов осуществляется пневматич. системой за исключением ппп где используется гидропривод т.к. пневматика не может обеспечить заданный закон движения вых. звена. (можно дать осн дост и недостатки).
Основные достоинства пневматических приводов следующие:
)возможность питания от на значительные расстояния;
)высокие скорости срабатывания исполнительных устройств;
) пожаро- и взрывобезопасность;
)возможность работы в шир диапазоне раб температур в усл запылени вибраций радиации;
)простота конструкции и высокая надежность пневматических устройств;
)простота ухода и обслуживания;
)относительно низкая стоимость и быстрая окупаемость.
К недостаткам пневматических приводов относятся:
)сравнительно высокая стоимость энергии сжатого воздуха что сказывается при непрерывном потреблении сжатого воздуха и больших его расходах;
)невозможность обеспечить заданный закон движения выходного звена;
)нестабильность скорости движения выходного звена;
) плохие условия смазки трущихся пов-стей подвижных элементов пнев устройств;
)низкий КПД пневматических приводов;
)необходимость защиты элементов привода от коррозии.
Бункерное загрузочное устройство.
Служит для захвата из бункера заготовок и передачи их в автоопер. Состоит из бункера качающегося сектора приводимого в движение пневмоцилиндром и лотка ориентирующего детали. Ёмкость бункера - 150Работой качающегося сектора управляют два пневмоклапана поз.54.
Автооператор. Служит для подачи детали из лотка загруз. устройства в зону обработки.
Автооператор состоит из кронштейна на котором крепится направляющая для перемещения штока поз.10 со стаканом поз.23; Шток имеет байонетный паз благодаря которому стаканчик с заготовкой поворачивается на 900. При этом ось заготовки совпадает с осью шпинделя.
Крайние положения корпуса руки фиксируются конечными выключателями смонтированными на направляющих.
Задняя бабка. Задняя бабка служит для подачи детали из автооператора в цанговый зажим для обработки. Установлена на направляющих станины. Состоит из корпуса с укрепленными на нем конечными выключателями и пиноли перемещающейся от пневмоцилиндров установленных в корпусе телескопически. Такая конструкция позволяет четко перемещать упор поз. 5 за два хода: первый ход цилиндра поз.2 на 85мм. и второй ход поршня поз.14 на 55мм.
Цанговый зажим установлен в шпинделе станка 1И611П. Состоит из цанги поз.8 тяги поз.1 и силового привода в кач-ве которого используется вращ цилиндр. Зажим цанговый снабжен пружинным выталкивателем поз.6 и реле давления.
Служит для зажима детали и удаления ее после обработки посредством выталкивающей пружины после чего деталь попадает в склиз и падает в тару.
Цанга изготовлена из стали марки У8А с термической обработкой конусной поверхности до твердости HRC 58-62 а хвостовика – до HRC 40-45.
Лепестки цанг при закалке немного разводятся чтобы подаваемая заготовка свободно проходил между ними. Угол при вершине конуса цанг делается 30°. Цанга имеет три прорези.
Можно выделить следующие достоинства зажима с затяжной цангой (с обратным конусом):
-конус цанги прилегает непосредственно к конической расточке в шпинделе что обеспечивает хорошее центрирование заготовки;
- осевая составляющая силы резания усиливает зажим прутка;
- лепестки цанги растягиваются а не сжимаются при зажиме и цанга и её конус мало деформируются;
-малые радиальные габариты
Цанга является основным исполнительным элементом в зажимном механизме и от ее характеристик во многом зависит работоспособность как зажимного устройства так и автомата в целом.
Привод поперечной подачи.
Служит для перемещения каретки с резцедержателем в поперечном направлении. Состоит из каретки поперечного суппорта и резцедержателя станка 1И611П перемещающихся от гидроцилиндра смонтированного сзади станка. Применение гидроцилиндра необходимо поскольку пневмоцилиндр не обеспечивает заданный закон движения выходного звена.
Холостой ход каретки 20 мм и рабочий ход 10 мм обеспечиваются дросселем с регулятором обратным клапаном и золотником ПГ-55-62 смонтированным на одном кронштейне с гидроцилиндром сзади станка.
Давление в гидросистеме 4 6 кгсм2. Включение и отключение дросселя обеспечивается кулачком закрепленным на каретке поперечного суппорта. Исходное и конечное положение каретки фиксируются конечными выключателями смонтированными на станине станка.
Гидробак поперечной подачи.
Служит в качестве емкости и для подачи масла под давлением 4 6 кгсм2 в гидроцилиндр. Состоит из двух форкамер куда подается сжатый воздух под давлением 4 6 кгсм2. Масло из форкамеры к золотнику с обратным клапаном ПГ-55-62 поступает через дроссель с регулятором смонтированным на боковой стенке гидробака. Гидробак монтируется на кронштейне и крепится на станине сзади станка 1И611П.
Электрооборудование.
На станке установлены два трехфазных асинхронных электродвигателя:
)Электродвигатель вращения шпинделя М1 и Электродвигатель смазки М2.
Электродвигатели и аппаратура рассчитаны на включение в сеть напряжением 380 В и частотой 50 Гц. Напряжение в цепи управления 110В. Напряжение в цепи сигнализации 55В. Подключение электрической части станка к сети осуществляется автоматическим выключателем АСТ-3. Вся электроаппаратура смонтирована в отдельно стоящем шкафу. Станок имеет автоматический и наладочный циклы работ. При нажатии кнопки S1 на пульте управления включается автоматическая работа станка и электродвигатель смазки М2.
Станок имеет наладочный и автоматичиский циклы работы. В наладочном режиме производится проверка работы каждого узла автомата. Пульт управления автоматом смонтирован на дверке электрошкафа. После подготовки автомата к работе включить кран управления бункерного загрузочного устройства. Начинает работать пневмоцилиндр Ц2 в автоматическом цикле. Сектор совершает качательные движения при этом нож сектора захватывает 1 или несколько заготовок и подает их в лоток. В крайних положених сектора установлены распределители переключающие ход штока на обратный. Т.о. обеспечивается автоматич. работа БЗУ.
В лотке заготовки перемещаются вниз под собст силой тяжести. В нижней части лотка смонтирован отсекатель кот в нужный момент пропускает 1 заг и она падает в стакан автооператора
Далее срабатывает пневмоцилиндр Ц4 подающей руки автооператора и подает деталь на ось центров автомата поворачивая заготовку на 90°. В конце хода руки срабатывает конечный выключатель SQ1 который дает команду на золотник Р6(У2) телескопического пневмоцилиндра задней бабки Ц6 происходит выдвижение пиноли задней бабки на 85 мм которая своим упором выталкивает деталь из подающей руки в цанговый зажим. В конце хода пиноли срабатывает конечный выключатель SQ 2 подающий команду на золотник Р4(У1) - пневмоцилиндр Ц4 переключается на обратный ход подающая рука автооператора возвращается в исходное положение.
После 35 мм хода назад подающей руки срабатывает конечный выключатель SQ3 дающий команду на золотник Р7(У3) телескопического цилиндра задней бабки Ц7 - происходит окончательная подача детали в цангу до упора.
В конце хода пиноли задней бабки срабатывает конечный выключатель SQ4 дающий команду на золотник Р1(У4); срабатывает пневмоцидиндр Ц1 цангового зажима детали. При достижении усилия зажима Рз = 180 кг (расчетное) реле давления дает команду на золотники Р6(У2) и происходит переключение телескопических цилиндров Ц6 и Ц7 пиноль задней бабки возвращается в исходное положение. Одновременно реле давления дает команду на электромагнитную муфту включающую вращение шпинделя и на золотник РЗ(У5) подающий сжатый воздух в гидробак.
Масло из гидробака поступает в гидроцилиндр Ц3 перемещая каретку с резцедержателем. Холостой ход каретки и рабочий ход обеспечивается дросселем с регулятором обратным клапаном и золотником ПГ-55-62 управляемым кулачком прикрепленным на каретке станка. В конце хода каретки т.е. после окончания обработки детали срабатывает конечный выключатель SQ 5.
Происходит быстрый отвод суппорта поперечной подачи в конце хода которого включается конечный выключатель SQ 6..
Далее цикл повторяется - Следущая заготовка падает в стакан автоопер и срабатывает пневмоцилиндр Ц4 подающей руки автооператора и подает деталь на ось центров.
Согласно поставленным задачам был автоматизирован весь цикл обработки. При этом увеличилась производительность обработки станка и как следствие увеличилась производительность труда рабочего. При этом рабочий освобождается от непосредственного участия в процессе обработки детали и появляется возможность многостаночного обслуживания. Облегчается физический труд рабочего он освобождается от однообразных повторяющихся движений от монотонных нервных и физических напряжений.
Благодаря повышению производительности станка при автоматизации уменьшается необходимое количество единиц оборудования с единицы площади цеха снимается больше продукции. Автоматизация вносит ритмичность в процесс обработки и способствует стабильности качества заготовок.
Тех задание.doc
на специальное и специализированное оборудование
агрегатные станки и автоматические линии
(наименование оборудование)
(разработано в соответствии с ГОСТ 15.001-73)
(наименование СКБ номер и дата протокола)
Экономические показатели:
(прочие показатели: экономия энергии материалов)
(рабочей силы и др.)
Исходные данные заказчика :
1. Изделие (деталь) обрабатываемое на данном оборудовании.
3. Данные характеризующие существующий технологический процесс.
(наличие СОЖ расход СОЖ использование воды пара воздуха и т.п.)
4. Напряжение электросети заказчика 380220 вольт частота 50 герц.
Требования предъявляемые к заказываемому оборудованию.
(наличие автоматической загрузки и разгрузки наличие активного контроля
необходимость наладочного режима и т п.)
рецензия.doc
Кафедра «Проектирование и эксплуатация машин и оборудования»
(должность место работы)
Проект на тему: «Спроектировать токарный автомат на базе станка модели 1И611П для обработки детали типа валик стеклоподъемника легкового автомобиля ИЖ-212»
Выполнен студентом дипломником Салимовым Наилем Вагизовичем.
Объем выполненной работы:
Расчетно-пояснительная записка на 142 листах 14 листов графической части выполненной в системе автоматизированного проектирования «КОМПАС 5.11».
Краткая аннотация проекта:
Проект посвящен разработке токарного автомата с одновременной модернизацией станка 1И611П.
За счет применения новых автоматических устройств и приводов станка повышается производительность обработки деталей до 400 - 600 дет.час.
Разработаны автоматические бункерно-загрузочное устройство и автооператор которые обеспечивают передачу заготовок в зону обработки.
Модернизирована задняя бабка с целью автоматизации перемещения пиноли.
Разработан цанговый зажим который служит для автоматического зажима детали и удаления ее после обработки.
Спроектирован автоматизированный привод поперечной подачи работа которого осуществляется посредством гидравлики.
Положительные стороны проекта:
- решается актуальная задача увеличения производительности что способствует сокращению устаревшего непроизводительного оборудования;
- отлично выполнена графическая часть проекта;
- в пояснительной записке присутствует большое количество рисунков и схем облегчающих понимание раскрываемой темы;
- разработанный автомат предполагается внедрить в производственный процесс.
Недостатки имеющиеся в проекте:
- на страницах 27 и 29 имеются опечатки затрудняющие понимание раскрываемой темы;
- несколько завышен диаметр пневмоцилиндра цангового зажима;
В целом проект заслуживает оценки «отлично» а его автор достоин присвоения звания инженер-механик.
6 Охрана труда.doc
В настоящее время основным направлением решения проблем охраны труда является переход от техники безопасности обеспечивающей безопасность при эксплуатации заведомо опасных машин и оборудования к безопасной технике. Это в полной мере относится и к производственному оборудованию предприятий машиностроения.
Научно-технический прогресс приводит к появлению новых материалов и реактивов новых источников шумов вибрации производственных излучений что приводит к необходимости разработки принципиально новых средств защиты. Его развитие в части автоматизации механизации и роботизации производства изменяет направленность охраны труда. На смену проблем физических перегрузок приходят проблемы нервно-психических перегрузок человека-оператора воспринимающего объем информации который может превышать величину возможную для восприятия и анализа. Что может привести к принятию неверных управленческих решений.
Основные направления работ по охране труда
Обеспечение охраны труда связано с профилактикой травматизма и заболеваемости а также созданием условий труда для сохранения работаю-щими высокого уровня работоспособности в течение всего рабочего дня.
Работоспособность человека в процессе труда характеризуется предельными возможностями его организма связанными с выполнением конкретной работы.
Кардинальным решением проблемы тяжелого физического труда и работ с вредными условиями является механизация автоматизация и роботизация производства. В случае когда это невозможно осуществить определяющим является внедрение безопасной техники и технологии в частности применение средств коллективной защиты обеспечение безопасности зданий и сооружений а также надлежащих санитарно-гигиенических условий труда.
Понятие причины возникновения
и физические характеристики вибраций
В промышленности и на транспорте широкое применение получили машины и оборудование создающие вибрацию неблагоприятно воздействующую на человека. Это прежде всего все транспортные средства а также ручные машины. Увеличение производительности и как следствие этого рост мощностей и быстроходности технологического оборудования при одновременном снижении его материалоемкости уменьшение статических нагрузок на человека сопровождаются нежелательным побочным эффектом-усилением вибраций. Воздействие вибраций не только ухудшает самочувствие работающего и снижает производительность труда но часто приводит к тяжелому профессиональному заболеванию – виброболезни. Поэтому вопросам борьбы с вибрацией придается огромное значение.
В соответствии с ГОСТ 24346–80 (СТ СЭВ 1926– 79) «Вибрация. Термины и определения» под вибрацией понимается движение точки или механической системы при котором происходит поочередное возрастание и убывание во времени значений по крайней мере одной координаты.
Причиной возбуждения вибраций являются возникающие при работе машин и агрегатов неуравновешенные силовые воздействия. В одних случаях их источниками являются возвратно-поступательные движущиеся системы (кривошипно-шатунные механизмы ручные перфораторы вибротрамбовки агрегаты виброформования и т. п.); в других случаях неуравновешенные вращающиеся массы (ручные электрические и пневматические шлифовальные машины режущий инструмент станков и т. п.). Иногда вибрации создаются ударами деталей (зубчатые зацепления подшипниковые узлы и т.п.). Величина дисбаланса во всех случаях приводит к появлению неуравновешенных сил вызывающих вибрацию. Причиной дисбаланса может явиться неоднородность материала вращающегося тела несовпадение центра массы тела и оси вращения деформация деталей от неравномерного нагрева при горячих и холодных посадках и т. п.
Воздействие вибраций на человека чаше всего связано с колебаниями обусловленными внешним переменным силовым воздействием на машину либо на отдельную ее систему. Возникновение такого рода колебаний может быть связано не только с силовым но и с кинематическим возбуждением например в транспортных средствах при их движении по неровному пути.
Воздействие вибраций на человека. Нормирование вибраций
Различают общую и локальную вибрации. Общая вибрация вызывает сотрясение всего организма местная вовлекает в колебательное движение отдельные части тела. Общей вибрации подвергаются транспортные рабочие операторы мощных штампов грузоподъемных кранов и некоторых других видов оборудования. Локальной вибрации подвергаются работающие с ручным электрическим и пневматическим механизированным инструментом (зачистка сварных швов обрубка отливок клепка шлифование и т. п.).
Общая вибрация с частотой менее 07 Гц (качка) хотя и неприятна но не приводит к вибрационной болезни. Следствием такой вибрации является морская болезнь происходящая из-за нарушения нормальной деятельности органов равновесия (вестибулярного аппарата) по причине резонансных явлений.
Различные внутренние органы и отдельные части тела (например голову и сердце) можно рассматривать как колебательные системы с определенной массой соединенные между собой «пружинами» с определенными упругими свойствами и параллельно включенными сопротивлениями. Очевидно что такая система обладает рядом резонансов частоты которых определяющие субъективное восприятие вибраций зависят также от положения тела работающего (работа стоя или сидя).
Собственные частоты плечевого пояса бедер и головы относительно опорной поверхности (положение «стоя») составляют 4–6 Гц головы относительно плеч (положение «сидя») – 25–30 Гц. Для большинства внутренних органов собственные частоты лежат в диапазоне 6–9 Гц. Колебания рабочих мест с указанными частотами весьма опасны так как могут вызвать механическое повреждение или даже разрыв этих органов. Систематическое воздействие общих вибраций характеризующихся высоким уровнем виброскорости может быть причиной вибрационной болезни – стойких нарушений физиологических функций организма обусловленных преимущественно воздействием вибраций на центральную нервную систему. Эти нарушения проявляются в виде головных болей головокружений плохого сна пониженной работоспособности плохого самочувствия нарушений сердечной деятельности.
Вибрация может не вызывать болезненных ощущений но затруднить проведение производственных процессов.
Локальная вибрация вызывает спазмы сосудов которые начинаются с концевых фаланг пальцев и распространяются на всю кисть предплечье захватывают сосуды сердца. Вследствие этого происходит ухудшение снабжения конечностей кровью. Одновременно наблюдается воздействие вибрации на нервные окончания мышечные и костные ткани выражающееся в нарушении чувствительности кожи окостенении сухожилий мышц и отложениях солей в суставах кистей рук и пальцев что приводит к болям деформациям и уменьшению подвижности суставов. Все указанные изменения усиливаются в холодный и уменьшаются в теплый период года. При локальной вибрации наблюдаются нарушения деятельности центральной нервной системы как и при общей вибрации.
Виброболезнь относится к группе профзаболеваний эффективное лечение которых возможно лишь на ранних стадиях. Восстановление нарушенных функций протекает очень медленно а в особо тяжелых случаях в организме наступают необратимые изменения приводящие к инвалидности.
Различают гигиеническое и техническое нормирование вибраций.
В первом случае производят ограничение параметров вибрации рабочих мест и поверхности контакта с руками работающих исходя из физиологических требований исключающих возможность возникновения вибрационной болезни. Во втором случае осуществляют ограничение параметров вибрации с учетом не только указанных требований но и технически достижимого на сегодняшний день для данного вида машин уровня вибрации. При этом учитывают условия установки и режим работы стационарного виброактивного технологического оборудования в цехах условия эксплуатации ручного механизированного инструмента.
В соответствии с ГОСТ 12.1.012–78* «Система стандартов безопасности труда. Вибрация общие требования безопасности» установлены допустимые значения и методы оценки гигиенических характеристик вибраций определяющих ее воздействие на человека. Нормируемыми параметрами при гигиенической оценке вибрации являются средние квадратические значения виброскоростей v (и их логарифмические уровни ) или виброускорения для локальных вибраций в октавных полосах частот а для общей вибрации в октавных или 'з октавных полосах. Возможна интегральная оценка вибраций по частоте нормируемого параметра а также по дозе вибрации.
Гигиенические нормы вибрации установлены для длительности рабочей смены 8 ч. Для видов вибрации (или особых условий ее воздействия) не нашедших отражение в ГОСТ 12.1.012–78* (например при совместном действии локальной и общей вибрации шума и вибрации и др.) допустимые величины уровня вибраций должны быть приведены в стандартных или технических условиях на конкретные виды оборудования.
Методы снижения вибраций машин и оборудования
Основными методами борьбы с вибрациями машин и оборудования являются:
) снижение вибраций воздействием на источник возбуждения (посредством снижения или ликвидации вынуждающих сил);
) отстройка от режима резонанса путем рационального выбора массы или жесткости колеблющейся системы;
) вибродемпфирование-увеличение механического импеданса колеблющихся конструктивных элементов путем увеличения диссипативных сил при колебаниях с частотами близкими к резонансным;
) динамическое гашение колебаний-присоединение к защищаемому объекту системы реакции которой уменьшают размах вибрации объекта в точках присоединения системы;
) изменение конструктивных элементов машин и строительных конструкций.
Средства индивидуальной защиты от вибраций
При работе с ручным механизированным электрическим и пневматическим инструментом применяют средства индивидуальной защиты рук от воздействия вибраций. К ним относят рукавицы перчатки а также виброзащитные прокладки или пластины которые снабжены креплениями в руке. Общие технические требования к средствам индивидуальной защиты рук от вибраций определены ГОСТ 12.4.002–74. Учитывая неблагоприятное воздействие холода на развитие виброболезни при работе в зимнее время рабочих надо обеспечивать теплыми рукавицами.
Обеспечение требований безопасности к зажимным механизмам
Усилия закрепления берутся с коэффициентом запаса К = 25.
Зажимные рукоятки не создают опасности при работе станка.
Обеспечение требований безопасности к органам управления
Органы управления имеют блокирующее устройство для автоматического отключения немеханизированного привода при включении механизированного привода.
Высота от уровня пола (рабочей площадки) до органов управления составляет 1200 мм.
Требования к контрольным и сигнальным устройствам предупредительным надписям таблицам и т. п. соответствуют ГОСТ 21829-76 и ГОСТ 12.4.026-76; к направлению движения рукояток органов управления – ГОСТ 9146-79; к формам и размерам органов управления зажимным рукояткам а также к усилиям к ним прикладываемым – ГОСТ 21752-76 ГОСТ 21753-76 ГОСТ 22129-76 и ГОСТ 12.2.009-80.
Обеспечение требований безопасности к гидроприводам
Требования к гидроприводам по ГОСТ 12.3.001-73 ГОСТ 12.2.040-79 ГОСТ 12.2.009-80.
Гидроприводы оборудованы устройствами для защиты рабочей среды от загрязнения; от возбуждения давления превышающего максимально допустимое значение и от падения давления в рабочей полости цилиндра при прекращении подачи или мгновенном падении давления рабочей среды.
После окончательной наладки СП следует опломбировать элементы гидроприводов разрегулирование которых ведет к аварийной ситуации.
Головки выводных устройств сливные пробки окрашивают в красный цвет. Корпусы кранов управления гидроприводом должны иметь отличительную окраску. Устройства гидроприводов должны иметь обозначение направления потока рабочей среды и маркировку по ГОСТ 15108-82. При наличии нескольких трубопроводов с различным давлением каждый из них должен иметь отличительную окраску по ГОСТ 22133-76 и маркировку присоединительных элементов по ГОСТ 15108-82.
Не допускаются отброс на рабочего стружки и пыли струей отработанного воздуха а также загрязнение рабочей зоны (пространство высотой до 2000 мм от уровня пола).
Обеспечение требований безопасности к средствам защиты
входящим в конструкцию приспособления
Открытые элементы СП перемещающиеся со скоростью более 0.15 мс имеют ограждение (ГОСТ 12.2.009-80) или предупредительную окраску (ГОСТ 12.4.026-76) а вращающиеся СП являющиеся источником опасности – предохранительные кожухи.
Уровень вибрации СП с силовым приводом к нему на рабочем месте ГОСТ 12.2.009-80. Шумовые характеристики СП соответствуют санитарным нормам. Установка СП не повышает октановых уровней звуковой мощности станка.
Обеспечение требований безопасности к транспортированию
сборке ремонту хранению
Конструкция СП является безопасной при складировании и транспортировке.
Выступание штифтов над поверхностью соединяемых деталей а также концов винтов и шпилек над гайкой на размер больший половины диаметра резьбы отсутствуют. Для предупреждения самоотвинчивания винтов и гаек используются контргайки шплинты и др.
He допускаются ремонт и техническое обслуживание СП во время работы станков. Приспособления должны храниться на стеллажах в шкафах обеспечивающих соблюдение всех требований безопасности складирования и хранения грузов.
Контроль выполнения требований безопасности
Контролю выполнения требований безопасности должны подвергать вновь изготовленные модернизированные и прошедшие ремонт СП в ходе приемочных приемосдаточных или периодических испытаний (ГОСТ 15.001-73). Виды испытаний определяются по ГОСТ 16504-81 и по чертежу на СП. Объем испытаний и контроля должен устанавливаться государственными стандартами и нормативно-техническими документами на конкретное приспособление (ГОСТ 12.2.029-77).
Обеспечение требований электробезопасности
Удельный вес электротравматизма среди других его видов невысок но из-за высокого процента случаев со смертельным исходом этому виду травматизма уделяется серьёзное внимание. Наиболее тяжёлой формой электрической травмы является электрический удар при котором нарушается деятельность органов дыхания кровообращения и центральной нервной системы.
Электробезопасность проектируемого станка обеспечивается следующими мероприятиями:
Заземление корпусов электродвигателей и электрошкафа (сопротивление заземления с изолированной нейтралью не превышает 4 Ом).
Местное освещение согласно норм для автоматических цехов осуществляется переменным током напряжением 36 В. для наладочных работ предусмотрено дополнительное переносное освещение напряжением 12 В. норма освещённости при работе линии металлообрабатывающих станков-автоматов составляет не менее 150 лк. При лампах накаливания и люминесцентных лампах 300 лк.
На станках с целью повышения безопасности принято: кнопка «пуск» вращения шпинделя и привода подач – чёрного цвета утоплены на 3-5 мм. Кнопки «стоп» отключения вращения шпинделя и привода подач – красного цвета и выступают на 3 мм. На пульте управления имеется лампочка сигнализирующая о наличии напряжения в цепи питания. Кнопка «общий стоп» – грибкового типа красного цвета.
Электропроводка выполнена закрытой в герметичных бронеруковах.
Цвет оборудования в цехе должен быть светло-серый эмаль 810. цвет проёмов в станке – кремовый согласно нормам HOG-2 «Окраска металлорежущих станков (заточные станки)» что значительно уменьшает утомляемость рабочего.
Известно что шум вредно влияет на здоровье работающих. Допустимый уровень шума для рабочих зон в производственных помещениях составляет 85 дбл ГОСТ12.1.003-76 (по шкале А – уровень эквивалентного шума).
При работе на станке средства индивидуальной защиты от шума не предусматриваются. Шумовые характеристики замеряются шумомером ШУМ-1М.
В разделе рассмотрены некоторые проблемы охраны труда на производстве. Эти проблемы невозможно решить только лишь соблюдением мер безопасности обязательных для технологического процесса необходимо проводить комплексные мероприятия по устроению неблагоприятного влияния тех или иных опасных факторов начиная с этапа планирования. Только в этом случае можно учесть все требования производственного процесса будь то освещение рабочего места или использования индивидуальных средств защиты. Правильное с точки зрения охраны труда построение производственного процесса требует вложения некоторых материальных средств. Окупаются они косвенно буть то работоспособность и здоровье рабочего или минимальные потери при пожаре и т.д. а если рассматривать жизнь человека как наивысшую ценность учёт охраны труда становится непременным условием построения производственного процесса.
экономика.doc
Эти требования могут быть удовлетворены (выполнены) различными путями поскольку технолог может применять различные варианты обработки детали в одинаковой мере обеспечивающие выполнение поставленных требований.
Отсюда возникает необходимость выбрать такой вариант оборудования который позволил бы добиться нужного результата в наиболее короткие сроки с наименьшими затратами труда и средств то есть экономически наиболее целесообразный.
Таким образом целью данного раздела является расчет годового экономического эффекта от принятого к внедрению варианта оборудования.
ВЫБОР БАЗЫ ДЛЯ СРАВНЕНИЯ.
Проектируемый в дипломном проекте вариант оборудования рассчитан на применение в рамках отдельного конкретного предприятия то есть решается задача совершенствования (модернизации) существующего заводского варианта оборудования который и принимается за базу для сравнения.
Таким образом далее будут сравниваться два варианта которые должны удовлетворять условиям сопоставимости вариантов приведенных в[16].
Сопоставимость вариантов:
сравниваемые варианты будут сопоставимы так как:
-номенклатура продукции одинакова;
-объём выпуска равный;
-качество получаемой продукции одинаково;
-условия труда сходны;
-источники информации одни и теже;
-степень безопасности и экологичности на одном уровне.
Оценка экономического эффекта при совершенствовании существующего оборудования имеет целью выбор наилучшего варианта конструкции оборудования.
Металлорежущее оборудование относится к средствам труда долговременного применения. При его производстве и использовании с улучшенными качественными характеристиками (производительность долговечность издержки эксплуатации и др.) в соответствии с методикой [16] годовой и экономический эффект рассчитывается по формуле:
ОПРЕДЕЛЕНИЕ НОРМЫ ВРЕМЕНИ РАБОТЫ И ГОДОВОГО ОБЪЕМА ВЫПУСКА ДЕТАЛЕЙ.
От качества нормирования времени на работу зависит правильность определения потребности в металлорежущем оборудовании и рабочей силе а следовательно достоверность расчета экономического эффекта. Применяют два основных метода установления норм времени: опытно-статистический аналитически-расчетный. В соответствии с рекомендацией данной в [16] установление норм времени лучше производить аналитически-расчетным методом.
Норма штучного времени на операцию определяется по формуле:
где: -основное время;
-вспомогательное время;
-время технического и организационного обслуживания;
-время на отдых и личные надобности;
Основное время рассчитывается по формуле (4.7) [29]:
где: -расчетная длина обработки мм (см. рабочий чертеж детали);
-число проходов резца =1;
-частота вращения шпинделя обмин (см. техпроцесс);
-подача на один оборот обрабатываемой детали мм.
=4с=00666мин. (см. ч-ж «Циклограмма»).
Сумма нормы основного и вспомогательного времени составляет оперативное время:
В соответствии с рекомендацией данной в [29] время технического и организационного обслуживания составляет 1-6% от оперативного времени:
Время на отдых и личные надобности является последним слагаемым штучного времени. Величина его может колебаться в пределах ст10 до 20% от оперативного времени [29] тогда:
При расчете сравнительной экономичности способов и средств нормы времени по вариантам необходимо определять одинаковыми методами. Поэтому определение нормы времени по базовому варианту следует проводить также аналитически-расчетным методом.
Определение основного времени по базовому варианту производится по той же формуле что и при расчете проектного варианта поэтому:
Вспомогательное время состоит из времени на снятие и установку обрабатываемой детали. Оно повторяется с каждой обрабатываемой деталью.
Время на обслуживание и отдых определяется по тем же формулам что и при расчете по проектному варианту.
Годовой объем продукции производимой с использованием проектируемого оборудования рассчитывается по формуле взятой из [16].
-годовая производительность разрабатываемого оборудования в натуральных единицах (деталях);
-действительный годовой фонд времени работы оборудования
=1970 час (данные с завода);
-норма времени на выполнение операции =0176 мин;
- нормативный коэффициент загрузки металлорежущего оборудования=07 для массового производства (см. [16]);
-коэффициент выполнения норм (для действующего производства принимается по фактическим данным а для вновь проектируемого –по фактическим данным выполнения норм на аналогичных работах) =1.
РАСЧЕТ СОПУТСТВУЮЩИХ КАПИТАЛЬНЫХ ВЛОЖЕНИЙ.
К сопутствующим капитальным вложениям относятся:
- затраты на доставку монтаж и отладку оборудования;
-стоимость производственной площади занимаемой оборудованием;
-стоимость служебно-бытовых помещений;
Поскольку годовой объем продукции принят исходя из годовой производительности единицы разрабатываемого оборудования то для определения сопутствующих капитальных вложений по базовому варианту необходимо сначала рассчитать потребное количество оборудования необходимого для выполнения годового объема продукции. Расчет количества металлорежущего оборудования производится по формуле взятой из [16]:
где: -расчетное количество единиц оборудования;
N-годовой объем изготовления деталей в штуках исходя из производительности нового оборудования N=470113 шт;
-коэффициент выполнения норм =1.
В массовом производстве при невозможности дозагрузки оборудования обработкой другими деталями расчетное количество единиц оборудования округляется до ближайшего целого числа и последующий расчет сопутствующих капитальных вложений и издержек производства ведется исходя из принятого количества оборудования
Затраты на доставку монтаж и отладку оборудования рассчитывается по формуле взятой из [16]:
- затраты на доставку монтаж и отладку оборудования руб;
-цена единицы оборудования руб; (по данным завода-изготовителя цена базового станка 1И611П составляет 120т.руб. цена разрабатываемого автомата выше на 20%);
-расчетное количество единиц оборудования (для базового варианта =2 для проектного =1);
-коэффициенты учитывающие соответственно транспортно- заготовительные расходы связанные с доставкой оборудования затраты на строительные работы и устройство фундамента для оборудования затраты на монтаж и освоение оборудования.
В соответствии с рекомендацией данной в [16] для оборудования массой менее 10т. коэффициент =01 коэффициенты для приближенных расчетов могут быть приняты равными 005.
Стоимость производственной площади занимаемой оборудованием определяется по формуле взятой из [16]:
-стоимость производственной площади занимаемой оборудованием руб;
- производственная площадь занимаемая единицей оборудования м2;
-стоимость 1м2 производственной площади =1100 руб. (по данным завода);
-площадь оборудования в плане с учетом вылета рабочих органов м2;
-расчетное количество единиц оборудования;
Руководствуясь паспортными данными станка 1И611П и чертежами общего вида площадь оборудования можно рассчитать по их габаритам.
-коэффициент учитывающий дополнительную производственную площадь равный для обоих вариантов 5 (см. приложение 2 [16] ).
Стоимость служебно-бытовых помещений определяется по формуле взятой из [16]:
- стоимость служебно-бытовых помещений руб;
-площадь служебно-бытовых помещений занимаемая одним рабочим –станочником или наладчиком =4м2 (по данным завода);
-численность рабочих- станочников чел;
- численность наладчиков;
-стоимость 1м2 служебно-бытовых помещений =1350 руб. (по данным завода);
Численность станочников и наладчиков определяется по формулам взятым из [16]:
-норма времени на выполнение операции =0176 мин. (см. техпроцесс);
-полезный годовой фонд времени одного рабочего равный 1970 час;
-число рабочих смен =1 ( по данным завода);
-коэффициент среднесписочного состава равный 11 [16];
-норма обслуживания станков наладчиком =2 [21 табл.1224].
Общие сопутствующие капитальные вложения по вариантам расчета определяются по формуле:
РАСЧЕТ ГОДОВЫХ ЭКСПЛУАТАЦИОННЫХ ИЗДЕРЖЕК.
Заработная плата рабочих-станочников с отчислениями на социальное страхование определяется по формуле взятой из [16]:
-часовая тарифная ставка станочника равная 567руб. (по данным завода);
-часовая тарифная ставка наладчика равная 978руб. (по данным завода);
-коэффициент учитывающий дополнительную заработную плату (принимается равным 11[16]);
- коэффициент учитывающий премиальные доплаты (принимается равным 14 по данным завода);
- коэффициент учитывающий отчисления в фонд социального страхования (принимается равным 137 [16]);
-районный коэффициент (в уральской зоне равен 115 [16]);
-годовой объем изготовления деталей в штуках исходя из производительности нового оборудования N=470113 шт;
Заработная плата наладчиков с отчислениями на социальное страхование определяется по формуле взятой из [16]:
Затраты на силовую электроэнергию для металлорежущих станков определяются по формуле взятой из [16]:
-суммарная установленная мощность электродвигателей станка кВт;
Суммарная установленная мощность электродвигателей базового станка складывается из мощности электродвигателя привода главного движения охлаждения и смазки: =30+00125+009=3215 кВт;
Суммарная установленная мощность электродвигателей проектируемого станка складывается из мощности электродвигателя привода главного движения электродвигателя командоаппарата и электродвигателя смазки: =30+006+009=315 кВт;
-стоимость одного киловатт-часа электроэнергии равная 65коп.кВт (по данным завода);
-годовой объем изготовления деталей в штуках исходя из производительности нового оборудования =470113 шт;
-средний КПД электродвигателей станка равный 095.
-коэффициент загрузки по мощности электродвигателей станка равный 080 [21 табл.73];
- коэффициент загрузки по времени электродвигателей станка равный 05 [21 табл.76];
- одновременной работы электродвигателей станка равный 1;
- коэффициент учитывающий потери электроэнергии в сети завода равный 105 [16];
Затраты на режущий инструмент определяются по формуле взятой из [16]:
z-цена инструмента равная 45 руб. за каждый резец с твердосплавной пластиной (данные завода);
Y-затраты на одну переточку инструмента руб.;
Ориентировочно затраты на все переточки можно принять в процентах от цены инструмента: [21];
-число переточек до полного износа равное 10 [21 табл. 712];
-основное время операции мин. равное 008125 мин.;
-период стойкости инструмента между переточками равный 2 [21 табл.712]
-коэффициент случайной убыли равный 119 [21 табл.712];
m-количество наименований режущих инструментов в станке равное 2.
Т.к. резцы отличаются лишь геометрией крепежной части то затраты на них будут одинаковыми поэтому:
Затраты на режущий инструмент по базовому и проектному вариантам будут одинаковыми т.к. режущий инструмент и режимы обработки не меняются.
Затраты на техническое обслуживание и ремонт оборудования определяются по формуле взятой из [16]:
R- ремонтосложность механической части оборудования в единицах ремонтной сложности равная 13 для базового оборудования и 14 для проектируемого (по данным завода);
V-годовые затраты на обслуживание и ремонт приходящиеся на единицу КРС V=309 руб. (данные завода);
-коэффициент учитывающий затраты на ремонт электрической части оборудования равный 13 для базового оборудования и 16 для проектируемого (по данным завода);
Амортизация на полное восстановление сопутствующих капитальных вложений в оборудование определяется по формуле взятой из [16]:
а- норма амортизационных отчислений на полное восстановление в процентах равная [16 приложение 5].
Затраты по амортизации и содержанию сопутствующих капитальных вложений в оборудование определяются по формуле взятой из [16]:
- производственная площадь занимаемая оборудованием для проектного варианта для базового -;
-площадь служебно-бытовых помещений =4м2 (по данным завода);
L-годовые затраты по амортизации и содержанию 1м2 производственной площади и площади служебно-бытовых помещений определяется в процентном соотношении от стоимости служебно-бытовых помещений.
Для проектного варианта для базового -
Суммарные годовые издержки по вариантам расчета определяются по формуле:
В соответствии с методикой [16] годовой и экономический эффект рассчитывается по формуле:
- цена соответственно базового и нового оборудования (по данным завода-изготовителя цена базового станка 1И611П составляет Ц1= 120т.руб. цена разрабатываемого автомата выше на 20% Ц2=144т.руб.);
В- коэффициент учета роста производительности нового оборудования по сравнению с базовым. Определяется отношением штучного времени обработки детали на базовом и новом оборудовании;
Р1 и Р2 –доли отчислений от балансовой стоимости на полное восстановление соответственно базового и нового оборудования. Рассчитываются как величины обратные срокам службы оборудования определяемые с учетом их морального износа.
Срок службы базового станка 1И611П составляет 20 лет (паспортные данные станка) нового- 15 лет поэтому Р1=00175 и Р2=00315 [16 прил.1].
И1 и И2- годовые эксплуатационные издержки потребителя
И1=10762717 руб. и И2=691014 руб.(расчет выше).
К1 и К2-сопутствующие капитальные вложения потребителя при использовании им базового и нового оборудования в расчете на объем продукции производимый с помощью нового оборудования.
К1=77406 руб. и К2= 47485 руб.
А2- годовой объем производства металлорежущего оборудования в расчетном году в натуральных единицах.
Расчет показал что проектный вариант металлорежущего оборудования дает положительный экономический эффект и в данном случае является однозначно наилучшим вариантом оборудования.
Наиболее значимые различия вариантов наблюдаются при расчете сопутствующих капитальных вложений и расчете годовых эксплуатационных издержек. Это объясняется тем что в результате расчета потребное количество единиц базового оборудования равно двум поскольку годовой объем продукции принят исходя из годовой производительности единицы нового оборудования.
Таким образом расчет показал целесообразность производства и эксплуатации проектируемого оборудования.
формы для диплома.doc
РАСЧЕТНО-ПОЯСНИТЕЛЬНАЯ ЗАПИСКА К ДИПЛОМНОМУ ПРОЕКТУ (РАБОТЕ)
ТЕМА:« Разработка токарного автомата для обработки детали типа валик стеклоподъемника на базе станка модели 1И611П».
Дипломник студент гр. 10-34-1 Корнилвский О.А.
Руководитель дипломного проекта к.т.н. доц. Батинов И.В.
экономической части Ф И.О уч. степень звание
безопасности жизнедеятельности Ф И.О уч степень звание
Представитель контроля выполнения к.т.н. доц. Зеленин В.Н.
НОРМ ЕСТД И ЕСКД доцент Иванов В.Ф.
Представитель технологического к.т.н. доц. Шитова Т.В.
контроля к.т.н. доц. Каракулова М.Л.
ДИПЛОМНЫЙ ПРОЕКТ (РАБОТА)
Выполнение дипломного проекта или работы является заключительным и наиболее важным этапом учебного процесса в вузе.
В дипломном проекте предусматривается разработка конструкций станков станочных роботизированных модулей и автоматических линий со всеми необходимыми расчетами или же разработка конструкции режущего инструмента и прогрессивной технологии для его производства.
В дипломной работе предусматривается проведение научно-исследовательской работы в области обработки резанием материалов разработка и исследование узлов станков и станочных комплексов.
Тема проекта (работы) как правило является актуальной для промышленности и внедрение ее обязательно связано с получением экономической и технологической эффективности.
ОБЪЕМ ДИПЛОМНОГО ПРОЕКТА (РАБОТЫ)
1. Пояснительная записка содержит 110 130 стр. рукописного текста формата А4.
2. Графическая часть содержит 12 15 листов чертежей формата А1 выполненных карандашом тушью или с использованием компьютерной графики.
3. Разработка технологического процесса для обработки заготовки (детали) с 5 7 операциями - для станочных дипломных проектов.
СОДЕРЖАНИЕ ПОЯСНИТЕЛЬНОЙ ЗАПИСКИ
1. Титульный лист (образец титульного листа пояснительной записки приведен ниже).
3. Техническое задание.
5. Патентно-информационные исследования; обзор и анализ литературы по теме проекта (работы).
6. Выбор компоновки проектируемого станка ГПМ АЛ конструкции проектируемого инструмента.
7. Определение объема исследований (в случае выполнения научно-исследовательской работы).
8. Кинематические прочностные и силовые расчеты.
9. Составление спецификаций.
10. Эффективность экономического расчета и самоокупаемость от проектирования и внедрения нового станка инструмента результаты основных научных исследований.
Создание условий безопасной жизнедеятельности и труда.
СОДЕРЖАНИЕ ГРАФИЧЕСКОЙ ЧАСТИ ПРОЕКТА (РАБОТЫ)
1. Общий вид конструкций станков ГПМ АЛ (2-3 листа формата А 1).
2. Разрезы узлов станка ГПМ АЛ со спецификацией на один из узлов (6-7 листов формата А 1).
3. Технико-экономические показатели проекта (работы) (1 -2 листа формата А 1)
ТЕХНОЛОГИЧЕСКИЙ ПРОЦЕСС МЕХАНИЧЕСКОЙ ОБРАБОТКИ ДЕТАЛИ на 5-7 операций оформленный на картах установленного образца.
Образцы чертежей проекта (работы) титульного листа пояснительной записки титульного листа тех. процесса представлены на стендах.
Дипломный проект студента очного (заочного очно-заочного) обучения специальности 120200 Корниловского О.А.
на тему « Разработка токарного автомата для обработки детали типа валик стеклоподъемника на базе станка модели 1И611П».
Проект посвящен разработке токарного автомата с одновременной модернизацией станка 1И611П.
За счет применения новых автоматических устройств и приводов станка повышается производительность обработки деталей до
Модернизирована задняя бабка с целью автоматизации перемещения пиноли.
Разработан цанговый зажим который служит для автоматического зажима детали и удаления ее после обработки посредством выталкивающей пружины.
Разработаны автоматические бункерно-загрузочное устройство и автооператор которые обеспечивают нужную ориентацию заготовок в пространстве и передачу их в зону обработки.
Спроектирован автоматизированный привод поперечной подачи работа которого осуществляется посредством гидравлики.
Выполнены все необходимые расчеты предусмотренные методическими указаниями по выполнению дипломного проекта.
В графической части проекта представлены:
- механизированная задняя бабка с автоматическим перемещением пиноли;
- кинематическая схема;
- гидропневматическая схема;
- электрическая схема;
- рабочий чертеж детали 408-6104036-10;
-технико-экономические показатели;
-циклограмма работы станка;
-привод поперечной подачи;
-бункерно - загрузочное устройство.
Техническое задание __
Обзор существующих токарных станков __
Патентный поиск обзор и анализ литературных источников
Кинематический расчет __
Расчет мощности резания при точении __
Выбор электродвигателя главного движения __
Разработка привода главного движения __
Расчет эффективного крутящего момента на шпинделе __
Расчет радиальной жесткости комплекса __
Расчет цилиндрических передач коробки скоростей подач __
Расчет шлицевого соединения __
Расчет шпоночного соединения __
Выбор подшипников шпиндельного узла __
Расчет зубчатой ременной передачи __
Технологическая часть __
1.Расчет режимов резания __
2.Расчет технических норм времени _
Организация и экономический анализ роботизированного производ-
Расчет экономической эффективности от внедрения комплекса __
Экология и безопасность жизнедеятельности __
Перевод иностранного текста по теме проекта (работы)
НА ВЫПОЛНЕННЫЙ ДИПЛОМНЫЙ ПРОЕКТ (РАБОТУ) ЗА 3 ДНЯ ДО ЗАЩИТЫ ПРЕДСТАВЛЯЕТСЯ РЕЦЕНЗИЯ НАПИСАННАЯ НЕЗАВИСИМЫМ ЭКСПЕРТОМ-СПЕЦИАЛИСТОМ.
(БЛАНК РЕЦЕНЗИИ ПРЕДСТАВЛЕН НА СТЕНДЕ)
ИЖЕВСКИЙ ГОСУДАРСТВЕННЫЙ ТЕХНИЧЕСКИЙ УНИВЕРСИТЕТ
Кафедра «Проектирование и эксплуатация машин и оборудования»
ТЕХНОЛОГИЧЕСКИЙ ПРОЦЕСС
НА ИЗГОТОВЛЕНИЕ ДЕТАЛИ
шифр и наименование детали
Ф.И.О. уч. степень звание
ФИО. уч. степень звание
СОГЛАСОВАНО УТВЕРЖДАЮ Главный инженер Зам. руководителя
на специальное и специализированное оборудование агрегатные станки и автоматические линии
(наименование оборудование)
(разработано в соответствии с ГОСТ 15.001-73)
(НАИМКНиВАНИК СКЬ. НОМЕР И ДАТА ПКУГиКОЛА) ^
Экономические показатели:
(прочие показатели: экономия энергии материалов)
(рабочей силы и др.)
Исходные данные заказчика :
1. Изделие (деталь) обрабатываемое на данном оборудовании.
2. Содержание операций подлежащих выполнению на заказываемом оборудовании
3. Данные характеризующие существующий технологический процесс.
(наличие СОЖ расход СОЖ использование воды пара воздуха и т.п.)
4. Напряжение электросети заказчика 380220 вольт частота 50 герц.
Требования предъявляемые к заказываемому оборудованию.
(наличие автоматической загрузки и разгрузки наличие активного контроля необходимость наладочного режима и т п.)
Ижевский государственный технический университет
(должность место работы)
Проект на тему «Разработка токарного автомата для обработки детали типа валик стеклоподъемника на базе станка модели 1И611П»
Выполнен студентом дипломникомгр. 10-34-1 Корнилвским О.А.
Объем выполненной работы:
Рецензия должна содержать:
) краткое описание выполненной работы;
) степень новизны в решении поставленной задачи;
) оригинальность технических решений;
) актуальность и соответствие требованиям предъявляемым к дипломным проектам;
) реальность проекта и отдельных его частей с точки зрения возможности использования на производстве.
рецензия.doc
Кафедра «Проектирование и эксплуатация машин и оборудования»
(должность место работы)
Проект на тему: «Разработка токарного автомата для обработки деталей типа валик стеклоподъемника на базе станка модели 1И611П»
Выполнен студентом дипломникомгр. 10-34-1 Корнилвским О.А.
Объем выполненной работы:
Расчетно-пояснительная записка на 140 листах 14 листов графической части выполненной в системе автоматизированного проектирования «КОМПАС 5.11».
Краткая аннотация проекта:
Проект посвящен разработке токарного автомата с одновременной модернизацией станка 1И611П.
За счет применения новых автоматических устройств и приводов станка повышается производительность обработки деталей до 400 - 600 дет.час.
Разработаны автоматические бункерно-загрузочное устройство и автооператор которые обеспечивают передачу заготовок в зону обработки.
Модернизирована задняя бабка с целью автоматизации перемещения пиноли.
Разработан цанговый зажим который служит для автоматического зажима детали и удаления ее после обработки.
Спроектирован автоматизированный привод поперечной подачи работа которого осуществляется посредством гидравлики.
Положительные стороны проекта:
-решается актуальная задача увеличения производительности что способствует сокращению устаревшего непроизводительного оборудования;
-отлично выполнена графическая часть проекта;
-в пояснительной записке присутствует большое количество рисунков и схем облегчающих понимание раскрываемой темы;
- разработанный автомат предполагается внедрить в производственный процесс.
Недостатки имеющиеся в проекте:
-на страницах 27 и 29 имеются опечатки затрудняющие понимание раскрываемой темы;
-неправильные ссылки на литературу на страницах 4796 и 104 поясительной записки;
-несколько завышен диаметр пневмоцилиндра цангового зажима;
В целом проект заслуживает оценки «отлично» а его автор достоин присвоения звания инженер-механик.
бланк-патент.doc
На провеление потентного поиска по теме:
токарного автомата с применением пневматики
стадия:Дипломное проектирование
Начало поиска10.03.02 г.
предъявление справки о поиске13.03.02 г.
Руководитель проектирования
РЕГЛАМЕНТ ПАТЕНТНОГО ПОИСКА
Предмет поиска (тема объект его составные части)
Цель поиска информации
Страна поиска начиная с СССР
Классификационные индексы
Ретроспективность (глубина поиска)
Наименование источников по которым проводится поиск
Гиросистема осевого зажима
металлорежущго станка
тяжелого токарного станка
Гидромеханический привод пиноли
металлорежуего станка
решение конструкций узлов и механизмов для использования при разработке токарного автомата.
Задание на проведение патентного поиска
Поиск проведен по следующим материалам
Предмет поиска (объект и его составные части)
По фонду какой организации проведен поиск
Источники информации
Науч.-техн. документация. Наименование дата публикации выходные данные с указанием пределов просмотра (от и до)
Патент. документация наименование пат. бюллетеня журналов охранных документов номера и даты их публикации с указанием пределов просмотра (от и до)
«Станки и инструменты»
Патентная документация отобранная для последующего анализа
Страна выдачи вид и номер охранного документа классификационный индекс
Заявитель с указанием страны номер заявки дата приоритета дата публикации
Сущность заявленного технического решения и цель его создания (по описанию изобретения или опубликованной заявки)
Сведения о действии охранного документа или причина аннулирования
О.Н. Мазаник и А.Н. Исаев
Цель – упрощение конструкции при одновременном уменьшении габаритов
Цель-повышение надежности путем обеспеченияпостоянного низкого давления в напорной магистрали устройство создания высокого давления выполнено в виде 2-х манипуляторов.
Цель- расширение технологических возможностей путем обеспечения автоматического съема обработанной детали
Цель-автоматизация пиноли с относительно низкими затратами.
Цель-повышение производительности путем автоматизации процесса настройки устройства для определения положения пиноли.
Научно-техническая документация отобранная для последующего анализа
Наименование источника информации
Год место и орган издания
Станочные гидроприводы
Конструирование и расчет металлорежущих станков и станочных комплексов. Курсовое проектирование
В помощь конструктору – станкостроителю
Гидравлика гидромашины и гидроприводы
Гидроприводы и гидропневмоавтоматика
Металлорежущие станки
Свешников В.К. Усов А.А.
В.И. Калинин В.Н. Никифоров Н.Я. Аникеев и др.
Справочник. - М.: Машиностроение 1982.-464 с. ил.
Учебн. пособие для вузов. – Мн.; Выш. шк. 1991. – 382.;ил.
Учебн. пособие для вузов. М.: Машиностроение 1983. – 288 с. ил.
Учебник для машиностроительных вузов.- М.: Машиностроение 1982. – 423 с. ил.
Учебник для машиностроительных вузов.- М.: Машиностроение 1971. – 672 с. ил.
Учебник для машиностроительных вузов.- М.: Машиностроение 1965. – 763 с. ил.
Выводы из патентного поиска.
Информационный поиск отечественной и иностранной литературы проведен по фонду Удм. ЦНТИ и предприятия с 1980 по 1996 г.
Патентный поиск проведен по странам: Япония США ФРГ ГДР Великобритания и Франция.
В результате поиска было найдено множество хороших конструкционных решений которые были использованы мной в ходе работы.
Наиболее удачным вариантом для решения поставленной задачи мне показалось изобретение В.И.Сергина а.с.№1838050 А3.
Изобретение относится к устройствам поджима с гидравлическим или пневматическим приводом перемещения пиноли задней бабки. Задняя бабка содержащая корпус пиноль гидро- или пневмопривод для перемещения пиноли в полости корпуса имеет гидро- или пневмопривод образованный пинолью в виде поршня с внутреннего конца соединенный штоком с поршнем соосно расположенный гидро- или пневмоцилиндр полости которого соединены для подвода и отвода рабочего тела с распределителями с подводом рабочего тела через редукционные клапаны в полость пиноли и полости цилиндра раздельно с тремя положениями распределителей: подача тела в полость пиноли подвода тела в бесштоковую полость цилиндра для поджима пиноли к детали подвода рабочего тела в штоковую полость цилиндра для перемещения пиноли от детали в исходное положение.
Особенность данного узла заключается в том что с целью упрощения конструкции при одновременном уменьшении габаритов пиноли задней бабки выполнена в виде поршня жестко связанного со штоком привода а система управления снабжена редукционными клапанами и распределителями предназначенными для подачи рабочего тела в трех положениях описанных выше.
ОБЛОЖКА.doc
КОНСТРУКТОРСКАЯ ЧАСТЬ.
ТЕХНОЛОГИЧЕСКАЯ ЧАСТЬ.
ЭКОНОМИЧЕСКАЯ ЧАСТЬ.
СОДЕРЖАНИЕ ГРАФИЧЕСКОЙ ЧАСТИ.
рпз4.doc
Обзор и анализ литературных источников
1.Обзор существующих токарных автоматов
2.Патентный поиск .. .
3.Перевод иностранного текста по теме проекта ..
4.Выводы по обзору .
1.Назначение и область применения . .
2.Устройство и работа станка .
Конструкторская часть
1. Расчет мощности резания при точении .
2.Выбор электродвигателя главного движения
3.Прочностной расчет коробки скоростей
3.1.Расчет валов коробки скоростей
3.2.Расчет цилиндрических передач коробки скоростей ..
3.3.Расчет шпоночного соединения
4.Расчет цангового зажима .
5.Расчет бункерного загрузочного устройства .
6.Расчет автооператора
7.Расчет задней бабки
8.Расчет привода поперечной подачи
Технологическая часть
1.Расчет режимов резания .
Экономическая часть .
1.Расчет экономической эффективности от внедрения оборудования
Содержание графической части дипломного проекта ..
ЗНАЧЕНИЕ И РАЗВИТИЕ АВТОМАТИЗАЦИИ СТАНКОВ.
При автоматизации станка производительность труда рабочего возрастает вследствие увеличения производительности станка. Рабочий освобождается от непосредственного участия в процессе обработки детали и появляется возможность многостаночного обслуживания технологического процесса.
Автоматизация облегчает физический труд рабочего освобождает его от однообразных повторяющихся движений от монотонных нервных и физических напряжений. Вместе с тем автоматизация повышает технический уровень обслуживания станка при его подготовке к производству – наладке и во время его эксплуатации. Таким образом автоматизация облегчает физический труд рабочего за счет увеличения доли умственного труда и создает предпосылки для постепенного сглаживания различий между физическим и умственным трудом.
Благодаря повышению производительности станков при автоматизации уменьшается необходимое количество единиц оборудования с единицы площади цеха снимается больше продукции. Автоматизация вносит ритмичность в процесс обработки и способствует стабильности качества заготовок и деталей на всех этапах их обработки.
1. Обзор существующих токарных автоматов.
Значительную долю в парке металлорежущего оборудования составляет большая группа токарных станков. Она включает девять типов станков различающихся по назначению области применения технологическим возможностям конструктивной компоновке степени автоматизации и некоторым другим признакам. Внутри каждого типа станки различаются по своим характерным размерам и конструкции.
В машиностроении токарные автоматы получили наибольшее распространение. Автоматом называется станок в котором автоматизированы все основные и вспомогательные движения необходимые для выполнения технологического цикла обработки заготовки а также загрузка заготовки и выгрузка обработанной детали. Обслуживание автомата сводится к периодической подаче материала-заготовки или прутка и контролю обработанных деталей.
Полуавтоматом называется станок в котором автоматизированы все основные и вспомогательные движения составляющие цикл обработки одной заготовки. По окончании цикла полуавтомат останавливается; для повторения никла необходимо снять готовую деталь поставить и закрепить новую заготовку и пустить станок.
Токарные автоматы предназначены для изготовления деталей сложной конфигурации путем обработки заготовки несколькими (многими) инструментами.
Автоматизация цикла работы современных станков осуществляется на основе использования средств механики гидравлики электротехники и электроники пневматики или на комбинированной базе.
Станки с механической базой автоматизации производительны и надежны в эксплуатации. Однако на переналадку таких автоматов затрачивается много времени. Поэтому автоматы с механической базой автоматизации используют как правило в условиях массового производства.
Особое место занимают станки с числовым (цифровым) программным управлением циклом. Такие станки могут быть эффективно использованы для изготовления деталей мелких и средних серий.
Токарные автоматы подразделяют по различным признакам:
а) назначению – на универсальные и специализированные;
б) виду заготовки – на прутковые и патронные;
в) количеству шпинделей – на одно- и многошпиндельные;
г) расположению шпинделей – на горизонтальные и вертикальные.
Более подробно проведем обзор токарных одношпиндельных автоматов.
ОДНОШПИНДЕЛЬНЫЕ ТОКАРНЫЕ АВТОМАТЫ.
Наиболее распространенными типами одношпиндельных токарных автоматов являются: фасонно-отрезные автоматы автоматы фасонно-продольного точения часто называемые также автоматами продольного точения н тока рно-револьверные автоматы.
Фасонно-отрезные автоматы предназначаются для изготовления из прутка (или бунта) коротких деталей малого диаметра и простой формы в условиях крупносерийного и массового производства. Схема работы такого автомата показана на рис. 1.
Материал закрепляется во вращающемся шпинделе 1 с помощью цангового патрона. Станок имеет два-четыре суппорта 2 перемещающихся только в поперечном направлении и несущих фасонные и отрезные резцы. Для получения детали заданной длины станок снабжен подвижным упором 3 автоматически устанавливающимся по оси шпинделя после окончания цикла. Материал подается с помощью механизма подачи до соприкосновения с упором.
Станок относится к автоматам первой группы.
Главным движением (v) в этих станках является вращение шпинделя движения подачи (s) – перемещения поперечных суппортов.
Некоторые модели фасонно-отрезных автоматов имеют продольный суппорт перемещающийся вдоль оси шпинделя позволяющий производить сверление отверстий. Некоторые характерные детали обрабатываемые на фасонно-отрезных автоматах показаны на рис. 2.
Рис. 2. Типовые детали изготовляемые на фасонно-отрезных автоматах.
Автоматы продольного точения предназначены для изготовления длинных деталей малого диаметра из прутка или бунта в условиях массового производства. Эти автоматы используются главным образом на предприятиях точной индустрии например в часовой промышленности приборостроении радиотехнической промышленности и т. п.
Высокие требования к точности и чистоте поверхности обрабатываемых деталей предъявляемые точной индустрией обусловили ряд конструктивных особенностей автоматов продольного точения. На рис. 3 дана схема работы автомата. Заготовка закрепляется во вращающемся шпинделе 1 при помощи цангового патрона. Шпиндельная бабка 2 перемещается по направляющим станины сообщая тем самым заготовке движение подачи (s1) относительно неподвижного резца 8 закрепленного в суппорте 9. Суппорт сообщает резцу установочные перемещения при переходе на обработку ступени другого
Рис. 3. Схема работы автомата фасонно-продольного точения.
диаметра и движение поперечной подачи (s2) при отрезке и фасонном обтачивании. Станок имеет два-три вертикальных суппорта и суппорт
балансирного типа 4 несущий два резца и совершающий качательное движение вокруг оси 5. Расположение суппортов показано на рис. 4.
Рис. 4. Расположение суппортов в автоматах фасонно-продольного точения:
а – суппорт балансирного типа; б – вертикальные суппорты.
Обработка центрального отверстия – сверление зенкерование нарезание резьбы метчиками и плашками и т. д: – производится с помощью специальных приспособлений 7 устанавливаемых на левой стороне станины.
Шпиндели приспособлений часто имеют независимое поступательное (Sз) и вращательное движения. Для уменьшения прогиба и вибрации прутка под действием сил резания передний конец его пропускается через калиброванное отверстие люнета 6 закрепленного на суппортной стойке 3 установленной на станине. Такая компоновка обеспечивает высокопроизводительную обработку деталей значительной длины без опасения возникновения значительного прогиба и вибраций.
При этом достигается высокая точность и чистота обработанных поверхностей.
Следует отметить что к прутковым заготовкам обрабатываемым на этих автоматах предъявляются повышенные требования по точности.
Главным движением (v) в этих автоматах является вращение шпинделя. При цилиндрическом обтачивании движением продольной подачи S1 является перемещение шпиндельной бабки при отрезке – поперечная подача s2 осуществляемая перемещением вертикальных суппортов или поворотом суппорта балансирного типа. При фасонной обработке подача получается как геометрическая сумма продольной и поперечной подачи (s1 и s2).
При сверлении зенкеровании развертывании продольная подача представляет собой алгебраическую сумму продольных подач шпинделя станка s1 и шпинделя приспособления s3.
Автоматы продольного точения имеют один распределительный вал управляющий рабочими и холостыми движениями (автоматы первой группы).
Характерные детали обрабатываемые на таких автоматах показаны на рис. 5.
Рис. 5. Примеры типовых деталей изготовляемых на автоматах фасонно-продольного точения.
Основным размером автоматов продольного точения является наибольший диаметр обрабатываемого прутка.
В табл. 1 приведены основные технические параметры современных отечественных автоматов продольного точения.
Наибольший диаметр обра-батываемого прутка в мм
Скорости главного движения в обмин
Мощность приводного электродвигателя в кет
* Станок имеет револьверную головку.
Патентный поиск отечественной и иностранной литературы проводится по теме: Создание задней бабки с автоматическим перемещением пиноли для токарного автомата с применением пневматики. (см. приложение 1).
96116 MACHINE WITH TA1LSTOCK
Henry W. Spretecr Shaker Heights. Ohio. assignor U The Waraer Л Smey Coopuy Ckvel—d. Ohio FB*d Nov. 71972. S*r. No. 304.408 Int. CL B23b 2J00. 7104 U.S. 0.82-2 R 17Chbn*
An improved machine tool includes a taibtock having a center assembly which u movable between operating and retracted pout ions by a piston and cylinder auembly. When the center auembly is in the operating pout ion a main axis of the center aoembly is aligned with the axis of rotation of a workpiece. In the retracted position the center assembly is ofhtt to one side of the work piece.
When the center assembly is in the operating position a tailstock motor is activated to press the center assembly against the outer end of the work-piece to thereby support the workpiece in a known manner. A control system coordinates movement of the center assembly with movement of a turret to avoid interference between the taibtock and tools mounted on the turret.
МКИB23b 2300. 704 США ПАТЕНТ № 3796II6
НКИ82-2R. Публикация 1974 г. 12 марта. Том 920 № 2
УДК62I.91I-229 (088.8)
Усовершенствованный металлорежущий станок содержит заднюю бабку в которой выдвижение центра в рабочее положение и отведение его назад осуществляется при помощи силового цилиндра. Когда центр находится в рабочем выдвинутом положении его ось совпадает с осью вращения заготовки. В отведенном положении центр смещен относительно заготовки. Когда центр находится в рабочем положении включается двигатель задней бабки осуществляющий поджим центра задней бабки к наружному торцу заготовки обеспечивая ее закрепление. В станке предусмотрена система управления координирующая перемещение центра задней бабки и револьверной головки. Такая система позволяет избегать столкновения задней бабки с инструментом установленным в револьверной головке.
Переводчик Айзеншток Г.И. Редактор Щукина Т.М.
(51)МКИ В 23 В 2300 1902
(11) заявка № 59-29364
Публик.№ 840720 М 2-735 (22) (21)
Заявлено 75. 01. 23 57-161609 (62) 50-9376 (71)
Заявитель Индексверке КГ Гаи унд Тескки (33)(32)(31)
Приоритет ФРГ 74. 03. 06. Р 2410540.6
(54) ЗАДНЯЯ БАБКА ТОКАРНОГО СТАНКА
Переводчик Е.П. Комарова
H30(AuZ4)V 15800. 20.1.59-24.5.67 49. 2601 - В 23В
Reitstock fiir Werkzeugniaschinen
VEB Zahnschneidcmaschincnfabrik Modul Karl-Marx-Stadt Emsiedler Str.
Als Erfinder benannt:
Erhard Vcttcnnann Meinersdorf (Erzgeb.)
Reitstock fiir Werkzeugniaschinen mit hy-draulisch oder pneumatisch belatigter Pinole dadurch gekennzeichnet daB der mit dem Reitstockgehause (1) losbar verbundene Tragkorper (2) eine in Langsrichtung durch-gehende Bohmng aufweist in der ein fest-stehender Zylinder(4) mit beweglichem Kolben (12) angeordnet ist dessen Kolbenstange test mit der Pinole (15) verbunden ist daB die Pinole (15) von hydraulisch betatiglen Spannelementen (23 24) umgeben ist. deren Dnickraume mit dem auf der Riickseite des Kolbens (12) befindlichen Dnickraum (9) dcs Zylinders (4) abschlieBbar in VerbindunR stehen und daB in der Pinole (15) Oder an einem mit dieser fe&lverbundenen Teil ein in Abhangigkeit vom hydraulischeo Druck und einer dagegen wirkcnden Feder (19) betatig-les Keilgesperre (18 22) angeordnet ist.
УДК 621-229.332(088.8)
ФРГ заявка №1241230 КЛ. ФРГ 49а2601 Публикация 1967 № 21(24.5)
ЗАДНЯЯ БАБКА ДЛЯ МЕТАЛЛОРЕЖУЩЕГО СТАНКА
Задняя бабка для металлорежущего станка с гидравлически или пневматически перемещающейся пинолью отличается тем что несущая часть (2) разъемно соединенная с корпусом задней бабки (I) имеет отверстие в котором расположен неподвижный цилиндр (4) с подвижным поршнем (12). Шток поршня жестко соединен с пинолью (15) таким образом что пиноль (15) окружена гидравлически действующими зажимными элементами(23 24) полости нагнетания которых соединены с рабочей полостью (9) цилиндра (4) расположенной с задней стороны поршня (12). В пиноли (15) или на элементе неподвижно соединенном с ней расположен клиновой стопорный механизм (1822) действующий в зависимости от гидравлического давления против пружины (19).
Переводчик Вильнер Г.С. Научный редактор Янина Т.А.
3. Перевод иностранного текста по теме проекта.
Inventions treat to machine-tool construction in particular to devices of a clip with a hydraulic or pneumatic drive of migration of a movable sleeve of a footstock. The footstock containing a body movable sleeve hydraulic drive or pneumodrive for migration of a movable sleeve in a cavity of a body with an opportunity of migration has her(it) on magnitude of a wear of the central hole of a detail hydraulic drive or pneumodrive formed(educated) by a movable sleeve as the piston from the internal end joint rod with the piston an axes the located actuator or pneumocylinder which cavities are connected for lead and tap of a working body to allocators with lead of a working body through reduction valves in a cavity of a movable sleeve and cavity of the cylinder separately with three positions of allocators: Feedinges of a body in a cavity of a movable sleeve for migration of a movable sleeve to a detail with a tap of a working body at the end of lead for a stopping of a movable sleeve lead of a body in a rodless cavity of the cylinder for a clip of a movable sleeve to a detail lead of a working body in a rod a cavity of the cylinder for migration of a movable sleeve from a detail in a home position. 3 silts.
The invention treats to machine-tool construction in particular to footstocks with a hydraulic or pneumatic drive of migration of a movable sleeve of a footstock and can be used in machine tools and other devices for example in devices for monitoring a condition of frictionless bearings when it is required to ensure(supply) often change of work pieces.
The purpose of the invention is the simplification of a construction at simultaneous reduction of dimensions.
On a f on a f on a figure 3 - footstock at a tap of a movable sleeve from a detail (in the beginning of driving).
The footstock contains a body 1 in which cavity the movable sleeve 2 with the centre 3 joint rod 4 with the piston 5 axeses located with a cavity of a movable sleeve an actuator or pneumocylinder 6 is. The cavity of a movable sleeve is connected by channels 7 and 8 to the allocator 9 with lead of a working body (hydrofluid or air) under pressure (from the pump) through the channel 10 reduction valve 11 both channel 12 and tap of a working body from a cavity of a movable sleeve through channels 7 and 8 cavity of the allocator 9 and channel 13 in a tank or atmosphere. The cavities of the cylinder 6 are connected to the allocator 14: a rod - channel 15 rodless - channel 16 with lead of a working body under pressure through the channel 17 reduction valve 18 both channel 19 and tap of a working body from a cavity of the cylinder through channels 15 and 16 cavity of the allocator 14 channel 20 in a tank or atmosphere.
The hydraulic drive or pneumodrive of a movable sleeve 2 footstocks works as follows. In a home position the movable sleeve 2 is pushed in a cavity of a body 1. In this position the removal of a treated detail and installation of other detail in the centres is made. For lead of a movable sleeve 2 to a work piece the allocators 9 and 14 are established in a position: " of lead of a movable sleeve to a detail " (figure 1). Thus a working body under pressure through the channel 10 reduction valve 11 channel 12 through cavities of the allocator 9 the channel 8 acts in a cavity of a movable sleeve and creates effort to a movable sleeve 2 necessary for driving a movable sleeve 2 in a cavity of a body.
The movable sleeve 2 displaces to a work piece. The magnitude of effort is regulated by regulation of pressure of a working body by the reduction valve 11. At reaching by the centre of 3 central holes of a work piece the movable sleeve 2 opens the channel 7. Thus a working body from a cavity of a movable sleeve through the channel 7 cavities of the allocator 9. channels 13 act in a tank or atmosphere. After migration of a movable sleeve 2 4 pistons 5 cylinders 6 displace connected with it(her) by a rod. Thus the working body from a rod of a cavity of the cylinder 6 displaces on the channel 15 in the allocator 14 channel 16 in a rodless cavity of the cylinder 6.
For a clip of a movable sleeve 2 with the centre 3 to a work piece with effort necessary at handling for a detail the allocators 9 and 14 are established in a position:
Clip of a movable sleeve to a detail (figure 2). Thus the working body under pressure acts through the channel 10 reduction valve 11 channel 12. cavities of the allocator 9 channels 7 and 8 in a cavity of a movable sleeve 2 and creates adjusted by the reduction valve 11 having strengthened on a movable sleeve 2 necessary for movement of a movable sleeve 2 in a cavity of a body 1 and through the channel 17 reduction valve 18 channel 19. cavities of the allocator 14 the channel 16 in a rodless cavity of the cylinder 6 and creates adjusted by the reduction valve 18 efforts through the piston 5. rods 4 movable sleeve 2 centres 3 on a detail necessary for its(her) handling.
At migration of the piston 5 a working body from a rod of a cavity of the cylinder 6 through the channel 15 cavity of the allocator 14 and the channel 20 acts in a tank or atmosphere For a tap of a movable sleeve 2 from a detail after its(her) handling in a home position the allocators 9 and 14 establish in a position: a tap of a movable sleeve from a detail (figure З). Thus the working body under pressure acts through the channel 17 reduction valve 18 turnpike 19 cavity of the allocator 14 the channel 15 in a rod the cavity of the cylinder 6 and creates adjusted by the reduction valve 18 efforts to the piston 5 displacing a movable sleeve 2 from a detail in a home position. The working body from a rodless cavity of the cylinder 6 through the channel 16 cavity of the allocator 14. channels 20 and from a cavity of a movable sleeve through channels 7 and 8 cavity of the allocator 9 channel 13 acts in a tank or atmosphere. The formula of the invention a Footstock containing established(installed) in body with an opportunity of established(installed) in an a body with the centre and a hydraulic drive or a pneumodrive. Executed as an axes of the cylinder located with a movable sleeve with the piston. By a rod and channels of lead tap of a working body. And also control system. Distinguished of themes that with the purpose of simplification of a construction at simultaneous reduction of dimensions the movable sleeve of a slide is executed as the piston rigidly connected to a rod of a drive and the control system is supplied with reduction valves and allocators intended for feeding of a working body in three positions: at lead of a movable sleeve to a detail - in a cavity of a movable sleeve (with a tap of a working body and end of a cycle) at a clip of a detail - in a rodless cavity of the cylinder and at a tap of a movable sleeve from a detail - in a rod a cavity of the cylinder.
Изобретение относится к станкостроению в частности устройствам поджима с гидравлическим или пневматическим приводом перемещения пиноли задней бабки. Задняя бабка содержащая корпус пиноль гидро-или пневмопривод для перемещения пиноли в полости корпуса с возможностью перемещения ее на величину износа центрового отверстия детали имеет гидро- или пневмопривод образованный пинолью в виде поршня с внутреннего конца соединенный штоком с поршнем соосно расположенный гидро- или пневмоцилиндр полости которого соединены для подвода и отводи рабочего тела с распределителями с подводом рабочего тела через редукционные клапаны в полость пиноли и полости цилиндра раздельно с тремя положениями распределителей: подачи тела в полость пиноли для перемещения пиноли к детали с отводом рабочего тела в конце подвода для остановки пиноли подвода тела в бесштоковую полость цилиндра для поджима пиноли к детали подвода рабочего тела в штоковую полость цилиндра для перемещения пиноли от детали в исходное положение. 3 ил.
Изобретение относится к станкостроению в частности к задним бабкам с гидравлическим или пневматическим приводом перемещения пиноли задней бабки и может быть использовано в станках и других устройствах например в устройствах для контроля состояния подшипников качения когда требуется обеспечить частую смену обрабатываемых деталей.
Целью изобретения является упрощение конструкции при одновременном уменьшении габаритов.
На рис.1 изображена задняя бабка при подводе пиноли к детали в момент остановки пиноли перед деталью; на рис.2 - задняя бабка при поджиме детали; на рис.З - задняя бабка при отводе пиноли от детали (в начале движения).
Задняя бабка содержит корпус 1 в полости которого находится пиноль 2 с центром 3 соединенная штоком 4 с поршнем 5 соосно расположенного с полостью пиноли гидро- или пневмоцилиндра 6. Полость пиноли соединена каналами 7 и 8 с распределителем 9 с подводом рабочею тела (гидрожидкости или воздуха) поддавлением (от насоса) через канал 10 редукционный клапан 11 и канал 12 и отводом рабочего тела из полости пиноли через каналы 7 и 8 полости распределителя 9 и канал 13 в бак или атмосферу. Полости цилиндра 6 соединены с распределителем 14: штоковая - каналом 15 бесштоковая - каналом 16 с подводом рабочего тела под давлением через канал 17 редукционный клапан 18 и канал 19 и отводом рабочего тела из полости цилиндра через каналы 15 и 16 полости распределителя 14 канал 20 в бак или атмосферу.
Гидро- или пневмопривод пиноли 2 задней бабки работает следующим образом. В исходном положении пиноль 2 вдвинута в полость корпуса 1. В этом положении производится снятие обработанной детали и установка другой детали в центры. Для подвода пиноли 2 к обрабатываемой детали распределители 9 и 14 устанавливаются в положение: "подвода пиноли к детали" (рис.1). При этом рабочее тело под давлением через канал 10 редукционный клапан 11 канал 12 через полости распределителя 9 канал 8 поступает в полость пиноли и создает усилие на пиноль 2 необходимое для движения пиноли 2 в полости корпуса.
Пиноль 2 перемещается к обрабатываемой детали. Величина усилия регулируется регулировкой давления рабочего тела редукционным клапаном 11. При достижении центром 3 центрового отверстия обрабатываемой детали пиноль 2 открывает канал 7. При этом рабочее тело из полости пиноли через канал 7 полости распределителя 9. канал 13 поступает в бак или атмосферу. Вслед за перемещением пиноли 2 перемещается связанный с ней штоком 4 поршень 5 цилиндра 6. При этом рабочее тело из штоковой полости цилиндра 6 перемещается по каналу 15 в распределитель 14 канал 16 в бесштоковую полость цилиндра 6.
Для поджима пиноли 2 с центром 3 к обрабатываемой детали с усилием необходимым при обработке детали распределители 9 и 14 устанавливаются в положение:
поджима пиноли к детали (рис.2). При этом рабочее тело под давлением поступает через канал 10 редукционный клапан 11 канал 12. полости распределителя 9 каналы 7 и 8 в полость пиноли 2 и создает отрегулированное редукционным клапаном 11 усилив на пиноль 2 необходимое для передвижения пиноли 2 в полости корпуса 1 а через канал 17 редукционный клапан 18 канал 19. полости распределителя 14 канал 16 в бесштоковую полость цилиндра 6 и создает отрегулированное редукционным клапаном 18 усилие через поршень 5. шток 4 пииоль 2 центр 3 на деталь необходимое для ее обработки.
При перемещении поршня 5 рабочее тело из штоковой полости цилиндра 6 через канал 15 полости распределителя 14 и канал 20 поступает в бак или атмосферу Для отвода пиноли 2 от детали после ее обработки в исходное положение распределители 9 и 14 устанавливают в положение: отвода пиноли от детали (рис.З). При этом рабочее тело под давлением поступает через канал 17 редукционный клапан 18 магистраль 19 полости распределителя 14 канал 15 в штоковую полость цилиндра 6 и создает отрегулированное редукционным клапаном 18 усилие на поршень 5 перемещающее пиноль 2 от детали в исходное положение. Рабочее тело из бесштоковой полости цилиндра 6 через канал 16 полости распределителя 14. канал 20 а из полости пиноли через каналы 7 и 8 полости распределителя 9 канал 13 поступает в бак или атмосферу. Формула изобретения Задняя бабка содержащая установленную в корпусе с возможностью осевого перемещения пиноль с центром и гидро- или пневмопривод. выполненный в виде соосно расположенного с пинолью цилиндра с поршнем. штоком и каналами подвода отвода рабочего тела. а также систему управления. отличающаяся тем что с целью упрощения конструкции при одновременном уменьшении габаритов пиноль бабки выполнена в виде поршня жестко связанного со штоком привода а система управления снабжена редукционными клапанами и распределителями предназначенными для подачи рабочего тела в трех положениях:
при подводе пиноли к детали - в полость пиноли (с отводом рабочего тела а конце цикла) при поджиме детали - в бесштоковую полость цилиндра и при отводе пиноли от детали - в штоковую полость цилиндра.
4. Выводы по обзору.
Информационный поиск отечественной и иностранной литературы проведен по фонду Удм. ЦНТИ и предприятия с 1980 по 1996 г.
Патентный поиск проведен по странам: Япония США ФРГ ГДР Великобритания и Франция.
В результате поиска было найдено множество хороших конструкционных решений которые были использованы мной в ходе работы.
Наиболее удачным вариантом для решения поставленной мне задачи показалось изобретение В.И.Сергина а.с.№1838050 А3.
Изобретение относится к устройствам поджима с гидравлическим или пневматическим приводом перемещения пиноли задней бабки. Задняя бабка содержащая корпус пиноль гидро- или пневмопривод для перемещения пиноли в полости корпуса имеет гидро- или пневмопривод образованный пинолью в виде поршня с внутреннего конца соединенный штоком с поршнем соосно расположенный гидро- или пневмоцилиндр полости которого соединены для подвода и отвода рабочего тела с распределителями с подводом рабочего тела через редукционные клапаны в полость пиноли и полости цилиндра раздельно с тремя положениями распределителей: подача тела в полость пиноли подвода тела в бесштоковую полость цилиндра для поджима пиноли к детали подвода рабочего тела в штоковую полость цилиндра для перемещения пиноли от детали в исходное положение.
Особенность данного узла заключается в том что с целью упрощения конструкции при одновременном уменьшении габаритов пиноли задней бабки выполнена в виде поршня жестко связанного со штоком привода а система управления снабжена редукционными клапанами и распределителями предназначенными для подачи рабочего тела в трех положениях описанных выше.
1. Назначение и область применения.
Токарный автомат представляет собой модернизированный станок 1И611П (см. рис.6) и предназначен для обработки деталей типа валик стеклоподъемника 408-6104036-10 (см. раб. чертеж детали).
Автомат состоит из станка 1И611П и из следующих модернизированных и вновь созданных узлов (см. таблицу 2 и рис.7).
Привод поперечной подачи
Бункерное загрузочное
Гидробак поперечной подачи
Рис. 7. Токарный автомат для обработки деталей типа «валик стеклоподъемника».
(см. чертеж «схема гидропневмокинематическая»).
Станок имеет наладочный и автоматичиский циклы работ.
В наладочном режиме производится проверка работы каждого узла автомата. Пульт управления автоматом смонтирован на дверке электрошкафа. После подготовки автомата к работе включить кран управления бункерного загрузочного устройства. Начинает работать пневмоцилиндр Ц2 в автоматическом цикле. Сектор загрузочного устройства подает детали в лоток где деталь ориентируется в положение обработки. После заполнения лотка деталями нажать на кнопку "автомат" на пульте управления.
Срабатывает пневмоцилиндр Ц4 подающей руки автооператора и подает деталь на ось центров автомата. В конце хода руки срабатывает конечный выключатель SQ1 который дает команду на золотник Р6(У2) телескопического пневмоцилиндра задней бабки Ц6 происходит выдвижение пиноли задней бабки на 85 мм которая своим упором выталкивает деталь из подающей руки в цанговый зажим шпинделя станка. В конце хода пиноли срабатывает конечный выключатель SQ 2 подающий команду на золотник Р4(У1) - пневмоцилиндр Ц4 переключается на обратный ход подающая рука автооператора возвращается в исходное положение. После 35 мм хода назад подающей руки срабатывает конечный выключатель SQ3 дающий команду на золотник Р7(У3) телескопического цилиндра задней бабки Ц7 - происходит окончательная подача детали в цангу до упора.
В конце хода пиноли задней бабки срабатывает конечный выключатель SQ4 дающий команду на золотник Р1(У4); срабатывает пневмоцидиндр Ц1 цангового зажима детали. При достижении усилия зажима Рз = 180 кг (расчетное) реле давления дает команду на золотники Р6(У2) и происходит переключение телескопических цилиндров Ц6 и Ц7 пиноль задней бабки возвращается в исходное положение. Одновременно реле давления дает команду на электромагнитную муфту включающую вращение шпинделя и на золотник РЗ(У5) подающий сжатый воздух в гидробак.
Масло из гидробака поступает в гидроцилиндр Ц3 перемещая каретку с резцедержателем. Холостой ход каретки и рабочий ход обеспечивается дросселем с регулятором обратным клапаном и золотником ПГ-55-62 управляемым кулачком прикрепленным на каретке станка. В конце хода каретки т.е. после окончания обработки детали срабатывает конечный выключатель SQ 5. Происходит быстрый отвод суппорта поперечной подачи в конце хода которого включается конечный выключатель SQ 6.
Далее цикл повторяется - срабатывает пневмоцилиндр Ц4 подающей руки автооператора и подает деталь на ось центров.
Электрооборудование.
На станке установлены два трехфазных асинхронных электродвигателя:
)Электродвигатель вращения шпинделя М1
)Электродвигатель смазки М2.
Электродвигатели и аппаратура рассчитаны на включение в сеть напряжением 380 В и частотой 50 Гц. Напряжение в цепи управления 110В. Напряжение в цепи сигнализации 55В. Подключение электрической части станка к сети осуществляется автоматическим выключателем АСТ-3. Вся электроаппаратура смонтирована в отдельно стоящем шкафу. Станок имеет автоматический и наладочный циклы работ. При нажатии кнопки S1 на пульте управления включается автоматическая работа станка и электродвигатель смазки М2.
Последовательность работы автоматического цикла.
(см. чертеж «схема электрическая принципиальная»).
Подается питание автоматическим выключателем Q. Загорается лампа «Сеть». Далее нажимаем кнопку «Пуск автомат» S4 на пульте управления
и катушка реле К11 становится на самоблокировку (цепь 9-16). Подается питание на выпрямительный мост командоаппарата. Начинает вращаться двигатель М4 (цепь 15- 4). Нажимаем кнопку «Пуск двигателя» S2 получает питание электромагнитный пускатель К10 (цепь 9- 13).
Бесконтактный выключатель 1SQ включает катушку К1 контакт которой замыкает цепь воздухораспределителя механизма подачи детали (цепь 15- 4). Затем бесконтактный выключатель 2SQ включает реле катушки К2 контакт которой замыкает цепь 15- 29 - 4. Происходит выдвижение 1-го цилиндра задней бабки (золотник У2) и одновременно с этим срабатывает бесконтактный выключатель 3SQ который включает реле К3. Включается 2-ой цилиндр задней бабки (цепь 15- 29 -31- 4). Происходит выдвижение 2-го цилиндра задней бабки (золотник У3). После чего включается бесконтактный выключатель 4SQ который включает реле К4 и происходит включение зажима Y4 (цепь 15-33- 4). Происходит зажим цанги. 1-ый и 2-ой цилиндр задней бабки возвращаются в исходное положение. Затем включается бесконтактный выключатель 5SQ который включает катушку реле К5 которая в свою очередь включает электромагнит Y5 (цепь 15-27- 4).
Происходит обработка детали. После обработки детали происходит разжим цанги. Под действием выталкивающей пружины деталь удаляется из зоны обработки через склиз. Командоаппарат становится в исходное положение. Когда суппорт возвращается в исходное положение SQ3 включает К8 и цепь 15- 24-25- 4 получает питание. Срабатывает механизм подачи детали.
Имеется кнопка S3 «Исходное положение командоаппарата» которая позволяет установить командоаппарат в исходное положение в случае сбоя автоматического цикла.
Предусмотрен тормоз двигателя М4 который включается когда командоаппарат становится в исходное положение.
На двигатели М4 имеется колодка с 4-мя выводами обмотки которые включаются в цепь согласно схеме.
Защита электрооборудования от коротких замыканий обеспечивается плавкими предохранителями F1 F5 и автоматическим выключателем Q.
Защита электродвигателей от перегрузок обеспечивается тепловыми реле FF1FF2.
Технологическая часть.
Расчет режимов резания.
В условиях массового производства в качестве режущего инструмента
следует выбрать резцы с твердосплавными пластинами (по рекомендациям данным в [1]).
При обработке алюминиевого сплава ЦА4М1 в качестве инструментального материала выбираем ВК-8.
Рабочая подача S=016 ммоб.(см.табл.15 [1] ).
Глубина резания t=35мм.
Ширина срезаемого слоя резцом ЦТ2112-4010 a=65мм.
Ширина срезаемого слоя резцом ЦТ2112-4029 а=15мм.
Скорость резания вычисляется по формуле:
S - подача ммоб. Определяется из табл.15[1].
Т - период стойкости инструмента мин.
-произведение коэффициентов учитывающих влияние материала заготовки состояния поверхности материла инструмента. Определяется из табл. 1-8 [1]. Значение коэффициента показателей степени y и m приведены в табл. 17[1].
Частота вращения шпинделя вычисляется по формуле:
v - скорость резания ммин.
d – обрабатываемый диаметр заготовки мм.
Конструкторская часть.
При работе в продолжительном режиме (S2) двигатель выбирают по требуемой мощности исходя из режимов резания и преодоления сил трения. Мощность двигателя в приводе главного движения может быть определена по зависимости:
Ргл.=Рр.+Рх.х.+Рдоп.
где Рх.х.- мощность затрачиваемая на холостом ходу;
Рр.- мощность затрачиваемая на процесс резания;
Рдоп.- мощность затрачиваемая на преодоление дополнительных потерь под нагрузкой.
Мощность потребная на резание при точении определяется по формуле:
Fz = Fz 1+Fz 2(Н) поэтому:
Fz 1-тангенциальная сила резания при точении паза резцом ЦТ2112-4010 (см. тех.процесс).
Fz 2 - тангенциальная сила резания при снятии фаски резцом ЦТ2112-4029.
V – скорсть резания ммин;
- значение коэффициента и показателя степени приведены в табл. 17[1].
- длина лезвия первого и второго инструмента мм.
- коэффициент характеризующий влияние геометрии инструмента на силы резания.
Рх.х. и Рдоп. Не превышают 15 20% от Рр. и с удовлетворительной точностью могут быть учтены коэффициентом полезного действия привода главного движения- поэтому:
где:К- коэффициент кратковременной перегрузки допускаемой стандартными двигателями;
- КПД привода главного движения станка.
- КПД зубчатой и клиноременной передачи соответственно.
По рассчитанной мощности выбирается конкретный асинхронный двигатель по каталогу [2].
Выбираем асинхронный двигатель 4А100 4У3:
мощность при n = 1500 обмин –30 кВт
под нагрузкой – 1434 обмин.
Прочностной расчет коробки скоростей.
Валы предназначены для поддержания насаженных на них тел вращения и передачи крутящего момента вдоль вала.
Расчет вала производится с целью обеспечения их прочности жесткости и отсутствии недопустимых колебаний. В редукторах вследствие сравнительно небольшой частоты вращения вала (до1500 обмин) и небольших расстояний между опорами расчет на жесткость и колебания обычно не проводят и таким образом основным расчетом является прочностной расчет вала.
Нагрузкой на вал являются силы от зубчатых передач натяжение ремня клиноременной передачи и крутящий момент. Собственной массой вала и деталей насаженных на вал обычно пренебрегают. Принято считать что нагрузки прикладываются не по всей ширине детали а в одной точке в середине ширины детали. Место приложения нагрузки выбирается в соответствии с кинематической схемой редуктора и всего привода. Направление сил должно выбираться таким образом чтобы получить наихудшие условия загружения вала из всех возможных вариантов.
Производится проверочный расчет вала IV ( см. чертеж «Кинематическая схема»)
ОПРЕДЕЛЕНИЕ ПЕРЕДАТОЧНОГО ОТНОШЕНИЯ КАЖДОЙ ПЕРЕДАЧИ
ОПРЕДЕЛЕНИЕ ЧАСТОТ ВРАЩЕНИЯ НА КАЖДОМ ВАЛУ
ОПРЕДЕЛЕНИЕ МОЩНОСТИ НА КАЖДОМ ВАЛУ
ОПРЕДЕЛЕНИЕ КРУТЯЩЕГО МОМЕНТА НА ВАЛУ
ОРИЕНТИРОВОЧНЫЙ РАСЧЕТ ВАЛА
Ориентировочный расчет производится с целью уточнения исходных данных и в частности для определения приближенно диаметра и межопорного расстояния вала так как без этих данных не могут быть проведены последующие расчеты. Этот расчет обычно производится из условия статической прочности на чистое кручение по пониженным допускаемым напряжениям кручения так как еще не полностью ясен вопрос о величине возникающих в вале изгибных напряжений.
Диаметр вала определяется из условия:
Т - крутящий момент на рассматриваемом валу;
- допускаемое напряжение на кручение принимаемое равным 15 МПа;
В зубчатых и червячных передачах в зоне зацепления действует сила направленная по линии зацепления. Эту силу с целью определения взаимного расположения нагрузок действующих на вел обычно представляют двумя (для прямозубой цилиндрической передачи) или тремя (для остальных передач) составляющими. Величина составляющих место их приложения и направление для соответствующих передач определяется так как указано ниже. При этом следует помнить что силы действующие со стороны ведущих элементов на ведомые являются активными те. окружные силы совпадают по направлению с окружной скоростью а силы. действующие со стороны ведомых элементов на ведущие- реактивными т.ч. окружные силы и окружная скорость направлены противоположно.
T1 – крутящий момент на валу;
- диаметр начальной окружности колеса на этом же валу равный (m- модуль зацепления; z - число зубьев шестерни).
- угол зацепления равный 20°.
Окружная сила приложена на плече относительно оси вала равном перпендикулярно к оси вала и вызывает изгиб вала и его кручение. Радиальная сила направлена перпендикулярно и оси вала через эту ось и вызывает изгиб вала. От этих сил в вале также возникают перерезывающие силы которыми обычно пренебрегают ввиду их малого влияния на общие напряжения в вале.
Сила Fв на вал от натяжения ветвей определяется
Kf - коэффициент зависящий от расположения ременной передачи в пространстве; для вертикальной передачи Kf = 1;
q - масса погонного метра ремня;
g – ускорение силы тяжести;
a – межосевое расстояние м.
Составляем расчетные схемы вала в координатах.
При этом за неподвижную шарнирную принимают опору где установлен подшипник воспринимающий радиальное и осевое усилие или любую опору при неизвестных вышеприведенных данных.
Вычерчиваем расчетную схему вала в двух проекциях – в вертикальной и горизонтальной – с простановкой на них сил. При этом следует помнить что если рассматривать силы приложенные в одной точке то радиальная и осевая силы всегда лежат в одной плоскости а окружная – в перпендикулярной к ней плоскости.
Определяем опорные реакции в горизонтальной и вертикальной плоскостях.
Для этого составляем уравнения моментов относительно одной и другой опор. В заключение этого пункта обязательно проведим проверку полученных значений реакции по условию; сумма всех сил на ось у или z должна быть равна нулю. Если наблюдается неравенство то расчет неверен и его следует повторить. Направление реакций задаем произвольно.
Реакция направлена в другую сторону; в дальнейших расчетах будем брать направление реакции вениз.
Определяем суммарные реакции в опоре А и В:
Подбор подшипников здесь не проводим считаем что они подобраны правильно вследствие чего размеры вала были приняты верными.
Строим эпюры изгибающих моментов в 2-х плоскостях:
На участке от Fay до Fr
На участке от Fr до Fby
На участке от Fby до Fв
На участке от Fax до Ft
На участке от Ft до Fbx
Строим эпюру суммарного изгибающего момента по зависимости:
Под силой Fbx и Fby:
Строим эпюру крутящего момента равного
УТОЧНЕННЫЙ РАСЧЕТ ВАЛА
Уточненный расчет вала производится с целью нахождения истинного значения запаса прочности вала.
Установлено что работоспособность вала из условия усталостной прочности будет обеспечена если
S - фактический (расчетный) коэффициент запаса прочности;
[S] - допускаемый коэффициент запаса прочности обычно принимаемый для валов редуктора в пределах 15 5.
Уточненный расчет вала проводится с учетом воздействия на него переменных нагрузок из условия его усталостной прочности.
Выбираем материал вала.
Назначаем для вала сталь марки Сталь 45. Для этой стали предел прочности ; пределы выносливости ; коэффициент чувствительности к ассиметрии цикла .
Опеределяем запас прочности вала.
При действии на вал только напряжений изгиба или напряжений кручения коэффициенты запаса усталостной прочности соответственно по изгибу и кручению определяются по зависимостям:
При совместном действии на вал напряжений изгиба и кручения коэффициент запаса прочности определяется по выражению:
В этих формулах обозначено:
- пределы выносливости при изгибе и кручении для симметричного цикла;
- эффективные коэффициенты концентрации напряжений при изгибе и кручении принимаемые по [4 табл. 15.1];
- масштабный фактор и фактор качества поверхности определяются по графикам рис. 15.5 и 15.6 [4];
- переменные составляющие циклов напряжений.
М и Т - соответственно изгибающий и крутящий моменты в рассматриваемом сечении вала;
- моменты сопротивления на изгиб и кручение этого же сечения.
что в пределах нормы.
ПРОВЕРКА ВАЛА ПО СТАТИЧЕСКОЙ ПРОЧНОСТИ
Эту проверку производят в целях предупреждения пластических деформаций и разрушений с учетом кратковременных перегрузок.
Статическая прочность вала обеспечена.
РАСЧЕТ ЗУБЧАТОЙ ПЕРЕДАЧИ.
По таблице рекомендуемых сочетаний материалов для зубчатых колес и шестерен принимаем для шестерни Сталь 40ХН HB1=270
для колеса Сталь 40Х HB2=260 ([5] табл. 3.3)
Определение допускаемых напряжений
Определение допускаемых напряжений производится в зависимости от механических характеристик материала колес и вида термообработки состояния рабочей поверхности зуба и переходной поверхности базового числа циклов для материала колес действительного числа циклов нагружения вызванных постоянной или переменной нагрузкой. Статическая прочность зубьев определяется значением наибольшей нагрузки. Если передачи работают в условиях переменных напряжений вызванных постоянным или переменным режимом нагружения то необходимо учитывать суммарный эффект на усталостную прочность различных по величине и продолжительности нагрузок. Расчет передач по наибольшей нагрузке если принять ее постоянно действующей в течение всего срока службы приведет к избыточной прочности и утяжелению деталей увеличению габаритов и стоимости.
Допускаемое усталостное контактное напряжение:
zR – коэффициент учитывающий шероховатость = 095;
zv – коэффициент окружной скорости = 1;
SH – коэффициент запаса прочности; при улучшении = 12; при закалке = 13;
zN – коэффициент долговечности;
NHG – базовое число циклов;
NHЕ – эквивалентное число циклов;
eH – коэффициент эквивалентности = 025;
t – время работы в часах;
n – частота вращения зубчатого колеса;
m – степень кривой усталости = 6;
- предел контактной выносливости;
Допускаемое расчетное контактное напряжение для расчетов принимается наименьшее из двух:
Определение коэффициента нагрузки
В расчетные уравнения для определения размеров передачи и действительных изгибных и контактных напряжений подставляется наибольшая длительно действующая мощность с учетом сил инерции возникающих в станке при пусках и остановках торможении и изменении режимов резания припусков и т. п.
Однако в передачах возникают дополнительные динамические нагрузки обусловленные внутренними причинами передач и кроме того концентрация нагрузки вдоль контактных линий. Учет этих нагрузок производится введением в расчетные уравнения коэффициента нагрузки.
Для предварительных расчетов при несимметричном расположениии колес на валах принимаем коэффициент нагрузки КН = 15 (с.124 [5])
Определение межосевого расстояния
Межосевое расстояние определяется из условия контактной прочности:
Геометрический расчет зубчатой передачи
Делительные диаметры
Проверка межосевого расстояния
Диаметры вершин зубьев
d 12 – делительные диаметры;
m – расчетный модуль.
Ширина венца зубчатого колеса
- межосевое расстояние;
- коэффициент ширины венца зубчатого колеса;
Коэффициент торцевого перекрытия
Определение степени точности колеса
Степень точности зависит от окружной скорости
По приложению 19 [5] принимаем 8 степень точности.
Определение коэффициентов нагрузки по контактным напряжениям
- коэффициенты внутренней динамической нагрузки; (с. 181 [6])
- коэффициенты концентрации нагрузки; (с. 182 [6])
- коэффициенты распределения нагрузки между зубьями;
Проверка по контактным напряжениям
zE – коэффициент материала (для стали = 190);
ze – коэффициент учета суммарных длин контактных линий;
zН – коэффициент формы сопряженных поверхностей (с. 167 [6]); т.к. ;
изменение в допустимых пределах .
РАСЧЕТ ШПОНОЧНОГО СОЕДИНЕНИЯ
Производится расчет шпоночного соединения на валу IV обеспечивающего передачу крутящего момента на шкив 160.
Размеры шпонок выбираются в зависимости от принятого диаметра вала по таблицам ГОСТа а затем производится условный расчет на смятие в предположении что напряжения на узких рабочих гранях шпонки и паза распределяются равномерно.
Т – передаваемый крутящий момент;
h – высота сечения шпонки = 11 мм;
- рабочая длина = 40 мм;
t – глубина паза = 33 мм;
- допускаемое напряжение смятия; = 600 800 МПа.
что в пределах нормы. Описание кинематической схемы.
(см. чертеж – «Кинематическая схема»).
Главное движение – вращение шпинеделя с частотой - от асинхронного двигателя М1 ( N=3 кВт n=1430 об.мин.) с помощью восьмиступенчатого редуктора и клиноременной передачи 13-14 передается на шпиндель VII при включенной зубчатой муфте 16 с внутренним зацеплением. При этом шпиндель может иметь восемь частот вращения от 400 обмин до 2000 обмин. Это «верхний поддиапозон» регулирования скорости вращения шпинделя.
Низкие частоты вращения шпинделя от 50 обмин до 250 обмин сообщаются шпинделю через «перебор» состоящий из двух передач 15-19 и 20-18 i переб. =(30:80)х(18:72)=18.
Таким образом шпиндель может иметь 16 различных частот вращения однако в рамках курсового проекта требуется обеспечить лишь одну частоту вращения n=500 обмин.
Данная частота вращения обеспечивается следующим образом:
Вращение с электродвигателя передается на вал 1 с помощью зубчатой муфты далее через зубчатую пару 2-5 (27:39) на вал 2. С вала 2 через зубчатую пару 6-8 (26:44) на вал 3. С вала 3 на вал 4 вращение передается зубчатой парой 10-11 (35:45). Далее через клиноременную передачу 13-14 (160:125) на вал 5. Вал 5 передает вращение на шпиндель с помощью зубчатой муфты. «Перебор» в работе не участвует.
График частот вращения приведен на чертеже «Кинематическая схема».
Применение пневмоприводов в станкостроении и робототехнике.
Пневматические приводы широко используются для автоматизации и механизации производственных процессов в различных отраслях промышленности. Установившаяся область их применения - машиностроение в том числе станкостроение.
Между пневматическими и гидравлическими объемными приводами существуют глубокие аналогии (по принципу действия по конструкции и функциям их элементов). Принципиально отличаются только рабочие среды - воздух обладающий большой сжимаемостью и малой вязкостью и вязкая практически несжимаемая жидкость. Различие рабочих сред существенно сказывается на динамических характеристиках приводов прежде всего на характеристиках исполнительных устройств. В отличие от гидравлических аналогов пневмодвигатели с возвратно-поступательным движением выходного звена являются типично дискретными устройствами. Движение поршня пневмоцилиндра характеризуется малой продолжительностью высокими и нестабильными скоростями. Поршень имеет только два фиксированных (крайних) положения определяемых жесткими упорами.
Точно остановить его в каком-либо промежуточном положении невозможно. Например при прекращении подачи воздуха или запирании обеих полостей пневмоцилиндра движущийся поршень остановится не мгновенно из-за упругости рабочей среды и инерционности подвижных масс.
Дискретным характером работы пневмодвигателей с возвратно-поступательным движением выходного звена обусловлено их применение для механизации и автоматизации таких технологических операций которые не требуют строго заданного закона движения и допускают нестабильность скорости подвижных элементов. Применительно к металлорежущим станкам это операции зажима поворота фиксации кантования транспортировки загрузки-выгрузки ориентации установки переключения. Несмотря на почти релейный характер срабатывания пневмоприводов реализующих такие операции рациональным выбором их конструктивных размеров и применением регулирующих устройств можно активно воздействовать на их динамику добиваясь требуемых эксплуатационных характеристик. Например дроссельным регулированием можно в широком диапазоне изменять время срабатывания действующие скорости и ускорения стабилизировать скорость движения рабочих органов. Применение тормозных устройств позволяет при высоких скоростях движения на основном участке хода ограничить или исключить удар в конце хода при остановке на жестком упоре. Все это расширяет функциональные возможности и область применения пневматических приводов в металлорежущих станках и автоматических станочных линиях.
В настоящее время свыше 50 % используемых в промышленности манипуляторов и роботов первых поколений пневматические. Разработка конструкций пневматических позиционеров шаговых и цифровых приводов дает основание рассчитывать на конкурентоспособность пневматических приводов с электро- и гидроприводами и при создании роботов новых поколений.
Достоинства и недостатки пневматических приводов.
Основные достоинства пневматических приводов следующие:
)возможность питания от централизованной сети при относительной легкости транспортировки энергии сжатого воздуха на значительные расстояния;
)высокие скорости срабатывания исполнительных устройств (пневмодвигателей и др.);
)пожаро- и взрывобезопасность обеспечиваемые без применения защитных средств;
)возможность работы в широком диапазоне рабочих температур в условиях запыленности вибраций радиации;
)простота конструкции и высокая надежность пневматических устройств;
)простота ухода и обслуживания;
)относительно низкая стоимость и быстрая окупаемость.
К недостаткам пневматических приводов относятся:
)сравнительно высокая стоимость энергии сжатого воздуха что сказывается при непрерывном потреблении сжатого воздуха и больших его расходах;
)невозможность без применения специальных устройств или конструкций обеспечить заданный закон движения выходного звена пневмодвигателя;
)нестабильность скорости движения выходного звена пневмодвигателя особенно при переменных нагрузках;
)плохие условия смазки трущихся поверхностей подвижных элементов пневматических устройств;
)низкий КПД пневматических приводов;
)необходимость защиты элементов привода от коррозии.
( см. чертеж «Шпиндельная бабка с зажимом цанговым»).
Цанговый зажим установлен в шпинделе станка 1И611П. Состоит из цанги поз.8 тяги поз.1 и силового привода. Зажим цанговый снабжен пружинным выталкивателем и реле давления рассчитанным на определенное усилие зажима детали.
Цанговый зажим должен удовлетворять следующим требованиям:
-концентричный зажим при радиальном биении не больше 001-004 мм;
-надежный зажим при нормальных погрешностях заготовок – в пределах 5-го класса точности;
- постоянство длины подаваемого прутка;
- постоянство упругих свойств цанги износостойкость губок цанги (зажим 50000-100000заготовок до выхода из строя).
Цанги изготавливают из сталей марок У8А У10А 65Г с термической обработкой конусной поверхности до твердости HRC 58-62 а хвостовика – до HRC 40-45.
Лепестки цанг при закалке немного разводятся чтобы подаваемый пруток свободно проходил между ними. Угол при вершине конуса цанг делается 30°. Число прорезей у цанги – от двух до шести в зависимости от диаметра заготовки. При диаметре свыше 20 мм рекомендуется три прорези.
Можно выделить следующие достоинства зажимов с затяжной цангой (с обратным конусом):
-конус цанги прилегает непосредственно к конической расточке в шпинделе что обеспечивает хорошее центрирование заготовки;
- исключено заклинивание во время подачи прутка;
- осевая составляющая силы резания усиливает зажим прутка;
- лепестки цанги растягиваются а не сжимаются при зажиме и цанга и её конус мало деформируются;
-малые радиальные габариты
Цанга является основным исполнительным элементом в зажимном механизме и от ее характеристик во многом зависит работоспособность как зажимного устройства так и автомата в целом.
Для вращающихся обрабатываемых заготовок сравнительно высокой жесткости необходимую силу зажима определяют при соблюдении следующих трех условий:
Момент закрепления должен быть больше крутящего момента возникающего от составляющих сил резания стремящихся повернуть заготовку вокруг оси вращения ().
При отсутствии упора суммарная осевая сила сцепления должна быть больше суммарной осевой силы резания .
Момент зажима возникающего от силы сцепления должен быть больше изгибающего момента от составляющих сил резания стремящихся вывернуть заготовку относительно точки опоры .
Суммарная радиальная сила зажима прижимающая губки цанги к заготовке определяется по формуле взятой из [28].
Для нашей схемы работы зажима (см. рис.8) осевая сила может быть вычислена по формуле (табл. 7.19. [28])
где:: -коэффициент запаса;
-коэффициент сцепления между губками цанги и заготовкой;
-составляющие силы резания;
-крутящий момент при сверлении;
-диаметр заготовки в месте зажима и диаметр обработки соответсвенно;
-приведенный угол трения.
Рис. 8. Схема действия осевой силы при одинарном зажиме.
Суммарная радиальная сила зажима прижимающая губки цанги к заготовке равна:
Зная суммарную осевую силу зажима в цанговом патроне можно перейти непосредственно к расчету пневмоцилиндра.
Расчет пневмоцилиндра.
Основные параметры поршневого цилиндра с односторонним штоком
связаны между собой следующими соотношениями [32]:
При движении поршня вправо когда поршневая камера соединена с напорной линией а штоковая – со сливной
F1F2- площадь поршневой и штоковой полости мм2;
р1р2- давление в поршневой и штоковой полости кгссм2;
Р1Р2- полезная нагрузка Н;
V1V2- скорость перемещения штока ммин;
Q1Q2 – расход воздуха лмин;
=09-098 – коэффициент учитывающий потери на трение в цилиндре;
При движении поршня влево когда штоковая камера соединена с напорной линией а поршневая – со сливной
Диаметр пневмоцилиндра определяется по формуле взятой из [9]::
- технологическая (полезная) нагрузка Н;
- масса всех подвижных элементов связанных с поршнем кг;
g -ускорение свободного падения мс2;
- подводимое абсолютное давление сжатого воздуха кгссм2;
Вес подвижных частей ± mg учитывают при вертикальном или наклонном расположении пневмоцилиндра. Знак «+» ставят тогда когда вес уменьшает зажимное усилие. В расчетной формуле принято что требуемое усилие зажима создается при давлении 09 чем обеспечивается некоторый его запас. Т.к. пневмоцилиндр расположен горизонтально то сила ± mg в формуле равна нулю.
Найденное значение D округляют до ближайшего из нормального ряда диаметров цилиндров по ГОСТ 6540-68: 25 32 40 50 63 80 100 125 160 200 250 320 360 400 мм.
Следовательно диаметр пневмоцилиндра цангового зажима следует принять равным 200 мм.
Диаметр штока определяют из соотношения:
d = (025 . . . 032) D
и округляют до ближайшего значения взятого из ряда 10 12 16 25 32 40 50 63 80 90 мм.
Исходя из конструктивных соображений принимаем диаметр штока равным 25мм.
Условный проход присоединительных отверстий пневмоцилиндра рекомендуется принимать из соотношения dy = 01D. Обычно такой же условный проход имеют присоединяемые воздухопроводы и установленные на них элементы пневмоаппаратуры. Однако выбирая величину dy необходимо также учитывать длину хода поршня и требуемое быстродействие привода. При малых длинах ходов условный проход уменьшают.
Принимаем dy равным 15мм.
Рассчитаем рабочую площадь поршня в поршневой 1 и штоковой 2 областях соответственно.
При движении поршня вправо когда поршневая камера соединена с напорной линией а штоковая – со сливной:
Требуемое усилие на штоке цангового зажима обеспечено.
5. Бункерное загрузочное устройство.
Автоматизация производственных процессов является характерной чертой современного прогресса. Без автоматизации невозможны высокие темпы дальнейшего роста производительности труда. Одной из основных проблем при автоматизации технологического оборудования и в частности металлорежущих станков является автоматизация загрузки заготовок и разгрузки (съема) обработанных деталей а при создании автоматических линий кроме того и автоматизация транспортных перемещений между станками.
Автоматизация загрузки и разгрузки оборудования находящегося в эксплуатации позволяет изменить процесс труда повысить безопасность и коэффициент использования оборудования а в некоторых случаях интенсифицировать режим его работы; полуавтоматические станки и станки с ручным управлением можно превратить в автоматы снизив тем самым штучное время обработки и широко использовать многостаночное обслуживание
Мнение что автоматизация загрузки-разгрузки оборудования ранних лет выпуска целесообразна только в условиях массового производства является ошибочным. Оснащение производства станками и технологической оснасткой сборно-разборной конструкции позволяет автоматизировать технологический процесс в условиях серийного и мелкосерийного производства и при частой смене объектов производства. В условиях серийного производства автоматизации производства должна предшествовать типизация технологических процессов или разработка групповых методов обработки.
В бункерных загрузочных устройствах заготовки в бункере (емкости) сосредоточены навалом. Захват из бункера и ориентация заготовок в положение требуемое для обработки или удобное для загрузки и все последующие перемещения осуществляются автоматически.
Загрузочные устройства эффективны если они повышают коэффициент использования станков (автоматических линий) на которых они установлены и производительность а также облегчают условия труда; не повреждают поверхность подаваемых заготовок или удаляемых со станка обработанных деталей; имеют простую конструкцию и минимальное количество деталей; состоят из нормализованных деталей; удобны в эксплуатации и дешевы в изготовлении; позволяют легко заменять быстроизнашивающиеся детали устройств.
Независимо от типа различают универсальные универсально-наладочные и специальные загрузочные устройства; первые два типа с помощью переналадки или подналадки а также замены некоторых деталей могут быть использованы для загрузки заготовок отличающихся размером а иногда и формой; устройства третьего типа применяют только для загрузки заготовок определенного типа. Загрузочные устройства только загружают заготовки а снимают (разгружают) обработанные детали толкатели станка или детали поступают в приемный лоток под действием собственного веса (силы тяжести).
Загрузочно-разгрузочные устройства (автооператоры или механические руки) специальными механизмами не только загружают но и разгружают заготовки.
Конструкторы разработали основы теории проектирования загрузочно-разгрузочных устройств и создали оригинальные конструкции устройств эксплуатируемые на заводах. Дальнейшему появлению новых и высокопроизводительных загрузочно-разгрузочных устройств будет способствовать разработка и исследование: механизмов ориентации используемых для заготовок повышенной сцепляемости; механизмов ориентации заготовок в магнитном поле и систем логической ориентации механизмов вторичной ориентации.
Расчет бункерного загрузочного приспособления.
В бункерных загрузочных устройствах основной запас изделий сосредоточивается в емкостях сделанных в виде коробов различной формы или широких лотков.
Размеры бункеров в машиностроении ограничиваются большим давлением изделий на стенки емкости и друг на друга так как вследствие этого затрудняется извлечение их из емкости.
В процессе работы в автоматических бункерах изделия захватываются и транспортируются в накопитель в ориентированном положении.
Изделия при этом подвергаются ударам и трению друг о друга и о захват транспортирующего механизма. Поэтому если повреждения недопустимы или изделия недостаточно жестки и сложны настолько что возможно сцепление их между собой применение бункерных загрузочных устройств с движущимся захватом исключается.
Емкости автоматических бункеров для штучных изделий имеют сходство с обычными бункерами для насыпных грузов. Под бункером принято понимать емкость имеющую относительно малую высоту по
-Бункер 2-Сектор 3-Лоток.
сравнению с размерами поперечного сечения бункера. К бункерам относят все емкости в которых плоскость обрушения (рис.9) пересекает свободную поверхность материала (в зоне бункера). Аналитически это выражается следующим образом:
Практически высота обычного бункера не превышает двух поперечников что характеризуется соотношением .
В соответствии с рекомендациями данными в [28] размеры секторного бункера берутся в зависимости от наибольшего поперечника изделия. Для бункера с центральным сектором эти зависимости имеют вид:
Ширина бункера В=(12-15)l;
Производительность бункера считается по формуле взятой из [28]:
где: z-число секторов;
р-коэффициент захватывания который берется в зависимости от формы и конфигурации изделия.
Работоспособность бункера зависит от степени взаимоподвижности изделии в бункере под действием внешних сил т. е. сыпучести изделий. В свою очередь сыпучесть изделий зависит от материала веса чистоты обработки загрязненности конфигурации а также от количества и высоты слоя изделий в емкости.
Основное влияние на сыпучесть изделий оказывает вес и размеры последних чем крупнее и тяжелее изделия тем сыпучесть ниже. Изделия следует загружать небольшим слоем так как действие веса ухудшает работоспособность бункера.
Сыпучесть характеризуется углом естественного откоса образованного при свободном набросе изделий в кучу на плоскости. Наибольшей сыпучестью обладают шарообразные изделия так как образуют наименьший угол естественного откоса. Сыпучесть в бункере зависит и от отношения всего объема бункера к объему занимаемому изделиями.
На рис.10 показана экспериментальная кривая по которой можно определить высоту слоя изделий в бункер. По оси абсцисс отложены наибольшие размеры изделий от 25 до 250 мм а по оси ординат–высота слоя изделий выраженная количеством поперечника (числом рядов) загружаемого изделия.
Рис. 10. Экспериментальная кривая определяющая зону применения бункеров в зависимости от размеров изделий.
Из графика видно что чем меньше поперечник изделия тем допускается больше количество рядов их в бункере. Для крупных изделий начиная от 150 мм допускается один ряд. В тех случаях когда высота или длина изделия равна 09–01 наибольшего поперечника рекомендуется применять магазин или штабельник.
Давление изделий на стенки бункера.
Давления воспринимаемые стенками автоматического бункера без учета трения изделий и стенки и конфигурации бункера определяются на основе теории сыпучих тел Вертикальное давление Ру на горизонтальную плоскость расположенную на высоте у от верхнего уровня засыпки материала выражается как гидростатическое давление.
где: q – насыпной вес материала в кГсм3.
Горизонтальное (боковое) давление в любой точке по высоте бункера определяется как результат действия клина нагруженного собственным весом Q при отсутствии трения материала на стенке. Горизонтальное давление на высоте у от поверхности засыпки определяется по формуле:
Рx = R · Ру = R ·q · у (40)
Из уравнения видно что горизонтальное давление на любом уровне пропорционально вертикальному давлению на том же уровне и составляет его долю определяемую коэффициентом R зависящим от степени сыпучести материала и определяемого по формуле:
где: -угол естественного откоса.
Толщина стенок бункеров практически берется в зависимости от веса Q в кг загружаемых изделий:
Учитывая что количество одновременно загружаемых деталей n=150шт. а масса одной детали m=0053кг получаем:
Принимаем толщину стенок равную 1мм.
Плотность насыпки изделий и их насыпной вес.
Изделия засыпанные в бункер располагаются в нем с различной степенью плотности которая характеризуется отношением суммы объектов пустых пространств остающихся между изделиями ко всему объему;
где:: V1-общий объем занимаемый изделиями (емкость бункера кучи);
V2-объем самих изделий (по внешней конфигурации);
V3 =V1-V2- объем пустых пространств.
Зная расчетную емкость бункера V1=4500 см3 и объем всех деталей равный »4000 см3 найдем V3=4500-4000=500 см3 тогда:
Сектор совершает возвратно-поступательные движения захватывая заготовки и подавая их в лоток. Лоток выполнен наклонным благодаря чему заготовки могут перемещаться за счет собственной силы тяжести.
Найдем теоретическую производительность бункера:
Захват деталей из бункера поз. 1 (см. рис.11) производится с помощью сектора поз. 2 который движется от пневмоцилиндра поз. 4.
Интенсивность поступления деталей из бункера поз.1 в лоток поз.3 регулируется дросселями поз.5 на пневмоцилиндре бункерного загрузочного изделия.
Рис. 11. Бункерное загрузочное устройство.
Основные параметры поршневого цилиндра с односторонним штоком связаны между собой следующими соотношениями [32]:
Диаметр пневмоцилиндра определяется по формуле взятой из [9]:
где: - технологическая (полезная) нагрузка;
- масса всех подвижных элементов связанных с поршнем;
g-ускорение свободного падения;
- подводимое абсолютное давление сжатого воздуха;
Вес подвижных частей ± mg учитывают при вертикальном или наклонном расположении пневмоцилиндра. В расчетной формуле принято что требуемое усилие зажима создается при давлении 09 чем обеспечивается некоторый его запас.
Следовательно диаметр пневмоцилиндра бункерного загрузочного устройства следует принять равным 63 мм.
Поэтому принимаем диаметр штока равным 25мм.
Требуемое усилие на штоке обеспечено.
Скорость перемещения штока регулируется дросселями поз.3 (см. рис. ).
Служит для подачи детали из лотка загрузочного устройства в зону обработки. Автооператор состоит из кронштейна на котором крепятся:
-Направляющая для перемещения штока со стаканом;
-Шток перемещается пневмоцилиндром 63;
-Корпус нa котором крепится направляющая для перемещения корпуса руки.
Шток перемещаясь поворачивается на 900 по байонетному пазу и подает деталь на ось центров.
К корпусу руки крепится губка для западания в нее детали из лотка загрузочного устройства. Крайние положения корпуса руки и штока фиксируются конечными выключателями смонтированными на направляющих.
Рис. 12. Автооператор.
Основные параметры поршневого цилиндра с односторонним штоком (см. рис. 12) связаны между собой следующими соотношениями [32]:
где:: - технологическая (полезная) нагрузка;
Вес подвижных частей ± mg учитывают при вертикальном или наклонном расположении пневмоцилиндра. В расчетной формуле принято что требуемое усилие зажима создается при давлении 09 чем обеспечивается некоторый его запас. Т.к. пневмоцилиндр расположен горизонтально то сила ± mg в формуле равна нулю.
Поэтому принимаем диаметр штока равным 25мм.
Найдем скорость перемещения штока:
t- время срабатывания с.
V= S:t = 016:(03:60) = 32ммин;
Зная скорость перемещения штока найдем расход воздуха:
Пиноль задней бабки перемещается от механизма шаговой подачи который содержит силовые цилиндры с полым поршнем установленными в корпусе телескопически.
(см. рис. ) связаны между собой следующими соотношениями:
где: =09-098 – коэффициент учитывающий потери на трение в цилиндре;
Расчет пневмоцилиндров.
Диаметр пневмоцилиндров определяется по формуле взятой из [9]:
Поскольку конструкция задней бабки нестандартная то диаметры цилиндров не следует округлять до ближайшего из нормального ряда диаметров цилиндров.
D1= 60мм-диаметр первого цилиндра задней бабки.
D2 = 75мм-диаметр второго цилиндра задней бабки.
d = 20мм – диаметр штока.
t = 03с- время хода второго цилиндра задней бабки.
p11=p12= 4-6 кгсм2- давление воздуха в поршневой области первого и второго цилиндра.
p21=p22 =15 кгсм2- давление воздуха в штоковой области.
S1=35мм - ход поршня.
S2=85мм- ход цилиндра.
Требуемое усилие Р1=800Н на штоке задней бабки обеспечено.
V= S:t = 085:(03:60) = 17ммин;
8. Привод поперечной подачи.
(см. чертежи «Привод поперечной подачи»).
Служит для перемещения каретки с резцедержателем в поперечном направлении. Состоит из каретки поперечного суппорта и резцедержателя станка 1И611П перемещающихся от гидроцилиндра смонтированного сзади станка. Холостой ход каретки 20 мм и рабочий ход 10 мм обеспечиваются дросселем с регулятором обратным клапаном и золотником ПГ-55-62 смонтированным на одном кронштейне с гидроцилиндром сзади станка.
Давление в гидросистеме 4 6 кгсм 2. Включение и отключение дросселя обеспечивается кулачком закрепленным на каретке поперечного суппорта. Исходное и конечное положение каретки фиксируются конечными выключателями смонтированными на станине станка.
Выбор гидроцилиндра.
Для автоматизации привода поперечной подачи нельзя использовать пневмоцилиндр поскольку он:
- не может обеспечить заданный закон движения выходного звена;
-имеет нестабильность скорости движения выходного звена.
В связи с этим следует использовать гидравлику.
При обработке валика стеклоподъемника 4086104036 согласно назначенным режимам сила подачи Рх=350Н однако следует предусматреть другие варианты обработки при которых эта сила намного больше.
В соответствии рекомендациям [32] в качестве привода поперечной подачи выбираем гидроцилиндр с двусторонним штоком по ОСТ 2 Г22-2-73.
Диаметр цилиндра:80мм;
Номинальный расход: 50лмин;
Максимальное (теоретическое) усилие на штоке
без учета сил трения: 564 кН;
Максимальное давление холостого хода: 047Мпа;
Утечка масла через уплотнения поршня
при номинальном давлении: 4см3мин
Содержание графической части дипломного проекта.
Наименование: Общий вид станка (лист 1).
Показан главный вид станка. Приведены технические требования и техническая характеристика станка. Ограждение поз. 7 не показано.
Наименование: Общий вид станка(лист 2).
Показаны вид сзади и вид сбоку станка. Обозначены основные узлы станка. Показаны габаритные размеры станка.
Наименование: Бабка задняя.
Сборочный чертеж включает: цилиндр поз.2 поршень поз.14 шток поз.13. Главный вид выполнен в разрезе. Показаны основные размеры проставлены посадки и сформулированы технические требования. Задняя бабка выполнена телескопически. Такая конструкция обеспечивает высокую надежность узла и четкое выполнение перемещений согласно циклограмме работы станка.
Наименование: Схема электрическая принципиальная.
На чертеже показана схема всего электрооборудования станка включение электродвигателей в цепь блоки управления: механизма подачи детали 1-го цилиндра задней бабки 2-го цилиндра задней бабки зажима цанги суппорта исходного положения командоаппарата исходного положения суппорта.
На чертеж вынесена спецификация с указанием основных параметров отдельных узлов схемы.
Электродвигатели и аппаратура рассчитаны на включение в сеть напряжением 380 В и частотой 50 Гц. Напряжение в цепи управления 110В.Напряжение в цепи сигнализации 55В. Подключение электрической части станка к сети осуществляется автоматическим выключателем АСТ-3. Вся электроаппаратура смонтирована в отдельно стоящем шкафу.
На пульте управления станка предусмотрены сигнальные лампы "Сеть" "Автомат" "Наладка" "Конец цикла" "Наличие детали". Сигнальная лампа "Наличие детали" загорается при отсутствии детали на позиции обработки. Для счета обработанных деталей на эл.шкафу смонтирован электроимпульсный счетчик.
Наименование: Циклограмма. Автомат для обработки валика стеклоподъемника.
На чертеже показана циклограмма работы станка которая показывает продолжительность каждого из переходов в цикле.
Продолжительность переходов необходимо знать при выборе электродвигателя привода главного движения.
В соответствии с циклограммой работа станка начинается с нажатия кнопки «Вкл. Автомат».
Масло из гидробака поступает в гидроцилиндр Ц3 перемещая каретку с резцедержателем. Холостой ход каретки и рабочий ход обеспечивается дросселем с регулятором обратным клапаном и золотником ПГ-55-62 управляемым кулачком прикрепленным на каретке станка. В конце хода каретки т.е. после окончания обработки детали срабатывает конечный выключатель SQ 5. Происходит быстрый отвод суппорта поперечной подачи в конце хода которого включается конечный выключатель SQ 6. Происходит разжим и удаление детали посредством выталкивающей пружины.
Лист 6: формат А 23.
Наименование: Схема гидропневмокинематическая. Автомат для обработки валика стеклоподъемника.
На чертеже показаны все гидро- и пневмоцилиндры схема включения их в гидро- и пневмолинию а также регуляторы дроссели и эл. контакты обеспечивающие автоматический цикл работы станка.
Наименование: Схема кинематическая. Валик стеклоподъемника.
Представлена кинематическая схема токарного автомата с автоматическим переключением скоростей благодаря включению в схему гидроцилиндров. Проставлены позиции валов и зубчатых колес с указанием числа зубьев. Представлен график частот вращения шпинделя.
На данном листе также представлены рабочие чертежи обрабатываемых деталей. Показаны все технологические размеры проставлены отклонения шероховатости поверхностей. Дан разрез детали сформулированы технические требования.
Наименование: Автооператор.
Показан способ крепления руки автооператора к станине станка. Приведены все необходимые виды разрезы и сечения объясняющие устройство и принцип работы механизма. Проставлены основные и установочные размеры. Приведены технические требования и техническая характеристика.
Наименование: Шпиндельный узел с зажимом цанговым.
Показан шпиндельный узел токарно-винторезного станка 1И611П с зажимом цанговым работающим посредством вращающегося пневмоцилиндра. Показаны все технологические размеры проставлены отклонения. Показаны габаритные размеры шпиндельной бабки.
Лист 10: формат А23.
Наименование: Бункерное загрузочное устройство.
Показано бункерное загрузочное устройство которое обеспечивает передачу заготовок сконцентрированных в бункере навалом на ось руки автооператора. Качающийся сектор захватывает заготовки из бункера и передает их в лоток в котором заготовки перемещаются под действием собственной силы тяжести. Заготовки имея вертикальную ориентацию попадают в отсекатель который в нужный момент пропускает одну заготовку. Далее заготовка падает в стаканчик автооператора и подается на в зону обработки.
На чертеже показаны габаритные и установочные размеры изображены все необходимые виды сечения и разрезы. Приведены технические требования и техническая характеристика.
Наименование: Привод поперечной подачи. (лист 1).
Показано крепление гидроцилиндра к станине станка. Дан разрез показывающий конструкцию. Проставлены все необходимые размеры гидроцилиндра. Приведены технические требования.
Лист 12: формат А23.
Наименование: Привод поперечной подачи. (лист 2).
Показан вид сверх и вид сзади стака. Вынесены сечения показывающие крепление штока гидроцилиндра к каретке резцедержателя. Проставлены все необходимые размеры.
Наименование: Схема соединений.
Показана схема питания пневмо и гидроцилиндров. Сжатый воздух от источника питания через фильтр-влагоотделитель ВД редукционный клапан РД маслораспылитель МР поступает на вход пневмораспределителей. Откуда воздух по пневмолиниям поступает в полости цилиндров. Скорость потока воздуха регулируется дросселями.
Наименование: Организационно-экономическая часть.
Чертеж представляет собой таблицу технико-экономических показателей дипломного проекта.
Анурьев В.И. Справочник конструктора – машиностроителя: В 3 т. М. 1979-1982. Т. 1-728с. Т.2-559 с. Т. 3-557с.
Безопасность технологических процессов и производств: Охрана труда: Учебн. пособие для вузов. Кукин П.П. Лапин В.Л. и др. -Мн.: Выш.школа 2001.-320с. ил.
Бобров В.П.- Проектирование загрузочно-транспортных устройств.-М.: Машиностроение 1964.-291с.: ил.
Волкевич Л.И. Усов Б.А. - Автооператоры-М.: Машиностроение 1963.-299с.: ил.
В помощь конструктору – станкостроителю В.И. Калинин В.Н. Никифоров Н.Я. Аникеев и др. М.: Машиностроение 1983. – 288 с. ил.
Выбор конструкции и расчет шпиндельных узлов металлорежущих станков: Методические указания. Ч. 2 Ижевск. мех. ин-т ;Сост. В.В. Пузанов Ф.Ю. Свитковский. Ижевск 1990. 32с.
Выбор двигателей приводов станков: Методические указания. Ч. 2 Ижевск. мех. ин-т ;Сост. В.В. Пузанов Ф.Ю. Свитковский. Ижевск 1990.
Гидравлика гидромашины и гидропроводы: Учебник для машиностроительных вузовТ.М.Башта С.С.Руднев Б.Б.Некрасов и др.-2-е изд. перераб. и доп.-М.: Машиностроение 1982.-423с. ил.
Гидроприводы и гидропневмоавтоматика станков: Метод. указания к курсовому проектированию (для специальностей 1201. 1202) Ижевск. мех. ин-т ;Сост. Б.Н. Зенков. Ижевск 1990.36с.
Гидроприводы и гидропневмоавтоматика станков: Метод. руководство для самостоятельного изучения общих сведений технической гидромеханики гидропривода и гидропневмоавтоматики станков. Ч. 5. Элементы пневмоаппаратуры высокого давления (для специальностей 1201. 1202) Ижевск. мех. ин-т ;Сост. Б.Н. ЗенковР.С. Музафаров. Ижевск 1993.
Горбацевич А.Ф. Шкред В.А.- Курсовое проектирование по технологии машиностроения:[Учебное пособие для машиностроит. спец. вузов].-4-е изд. перераб. и доп.-Мн.: Выш.школа 1983.-256с. ил.
Горошкин А.К. –Приспособление для металлорежущих станков: Справочник.-7-е изд. перераб. и доп.-М.: Машиностроение 1979.-303с. ил.
Иванов М.Н. Детали машин. М. 1984. 399с.
Кочергин А.И. Конструирование и расчет металлорежущих станков и станочных комплексов. Курсовое проектирование: Учебн. пособие для вузов. – Мн.; Выш. шк. 1991. – 382.;ил.
Кузнецов Ю.И. Маслов А.Р. Байков А.Н.-Оснастка для станков с ЧПУ: Справочник.-М.: Машиностроение 1983.-359с.: ил.
Кучер И.М. и Кучер А.М.- Модернизация и автоматизация станков -Л.: Машгиз 1958.-299с.: ил.
Малов А.Н.- Загрузочные устройства для металлорежущих станков.-М.: Машиностроение 1979.-399с.: ил.
Медвидь М.Н.- Автоматические ориентирующие загрузочные устройства.-М.: Машиностроение 1963.-299с.: ил.
Металлорежущие станки Н.С. Ачеркан. В 2-х т.; Под ред. Н.С. Ачеркана. -2-е изд. перераб. и доп.-М.: Машиностроение 1965.-764с.: ил.
Методические указания к дипломному проектированию по металлорежущим станкам и металлорежущему инструменту Ижевск. мех. ин-т; Сост. В.В. Пузанов А.А. Модзелевский Ю.Г. Глухов. Ижевск 1983.
Методические указания к лабораторной работе «Реализация цикла движений узлов станка с ЧПУ модели 1И611ПФЗ средствами гидроавтоматики» Ижевск. мех. ин-т; Сост. В.Ф. Иванов Р.С. Музафаров. Ижевск 1989.
Методические указания по кинематическому расчету приводов станков и построению их кинематических схем. Ижевск. мех. ин-т; Сост. В.В. Пузанов Ижевск 1989.
Методические указания по проведению патентных исследований при курсовом и дипломном проектировании по металлорежущим станкам и инструментам. Ижевск. мех. ин-т; Сост. А.И. Хватов Ижевск 1986.
Методические указания по расчету экономического эффекта при разработке металлорежущего оборудования в процессе дипломного проектирования студентов специальности 12.02 Ижевск. мех. ин-т; Сост. А.С. Севрюгин. Ижевск 1991. 20с.
Общемашиностроительные нормативы времени для нормирования многостаночных работ на металлорежущих станках. М.: Экономика1997.
Оформление расчетно-пояснительных записок к курсовому и дипломному проектам: Методические указания для студентов заочного обучения Ижевск. мех. ин-т ;Сост. Ф.Ю. Свитковский. Ижевск 1989.16 с.
Охрана труда в машиностроении: Учебник для машиностроительных вузовЕ.Я.Юдин С.В.Белов С.К. Баланцев и др.; Под. ред. Е.Я.Юдина С.В.Белова-2-е изд. перераб. и доп.-М.: Машиностроение 1983.-432с. ил.
Проектирование металлорежущих станков и станочных систем: Справочник-учебник. В 3-х т. Т.2. Расчет и конструирование узлов и элементов станков А.С. Проников Е.И. Борисов В.В. Бушуев и др.; Под общ. ред. А.С. Проникова.-М.: Издательство МГТУ им. Баумана: Машиностроение 1995.-371с.: ил.
Проектирование механических передач: Учебно-справочное пособие для втузов С.А. Чернавский Г.А. Снесарев Б.С. Козинцов и др. – 5-е изд. перераб. и доп. – М.: Машиностроение 1984.-560с. ил.
Расчеты экономической эффективности новой техники: Справочник Под ред. К.М. Великанова-Л.: Машиностроение. Ленингр. отд-ние 1990.-439с.: ил.
Решетов Д.Н. Учебник для студентов машиностроительных и механических специальностей вузов. – 4-е изд. прераб. и доп. М.: Машиностроение 1989.-496с.: ил.
Свешников В.К. Усов А.А. Станочные гидроприводы: Справочник. - М.: Машиностроение 1982.-464 с. ил.
Свирщевский Ю. И. Расчет и конструирование коробок и скоростей подач. Минск.:Высшая школа. 1976. –590 с.ил.
Соколов Н.Г. и Елисеев В.А. Расчеты по автоматизированному электроприводу металлорежущих станков. М. «Высшая школа» 1969. 296с.
Справочник нормировщика Под. общ. ред. А.В. Ахумова. Л.: Машиностроение. Ленингр. отд-ние 1986.
Справочник технолога – машиностроителя. В 2-х т. Т. 2Под ред. А.Г. Косиловой и Р.К. Мещерякова. – 4-е изд. перераб. и доп. – М.: Машиностроение1986. 496с. ил.
Стародуб Н.П.- Автоматизция токарной обработки при помощи пневмоустройств. -Мн.: Выш.школа 1979.-143с. ил.
Экономика и организация производства в дипломных проектах: Учебник для машиностроительных вузовК.М. Великанов Э.Г. Васильева В.Ф. Власов и др.; Под общ. ред. К.М. Великанова -4-е изд. перераб. и доп.-Л.: Машиностроение. Ленингр. отд-ние 1982.-423с.: ил.
В ходе выполнения дипломного проекта был разработан специальный токарный автомат на базе одношпиндельного токарно-винторезного станка 1И611П. Разработка данного автомата выполнена с целью повышения производительности станка (400-600детчас) и как следствие повышение производительности труда рабочего. При этом рабочий освобождается от непосредственного участия в процессе обработки детали от однообразных повторяющихся движений от монотонных нервных и физических напряжений. Вместе с тем повышается технический уровень обслуживания станка при его подготовке к производству – наладке и во время его эксплуатации. Модернизация станка вносит ритмичность в процесс обработки и способствует стабильности качества.
В ходе работы выполнено следующее:
-Модернизирована задняя бабка с целью автоматизации перемещения пиноли посредством пневмопривода;
-Разработан цанговый зажим который служит для автоматического зажима детали и удаления ее после обработки посредством выталкивающей пружины. Цанговый зажим установленный в шпинделе станка работает с помощью вращающегося пневмоцилиндра;
- Разработаны автоматические бункерно-загрузочное устройство и автооператор которые обеспечивают нужную ориентацию заготовки в пространстве и передачу её в зону обработки. В качестве приводного механизма также используется пневматика;
-Спроектирован автоматизированный привод поперечной подачи работа которого осуществляется посредством гидравлики поскольку применение пневматики в данном механизме не может обеспечить заданный закон движения и стабильность скорости движения выходного звена ;
-Выполнены все необходимые расчеты предусмотренные методическими указаниями по выполнению дипломного проекта;
-Представлен рабочий маршрутно-технологический процесс детали 408-6104036-10 «валик стеклоподъемника»;
-Произведен расчет экономического эффекта от производства и эксплуатации проектируемого автомата;
-В соответствии с заданием по охране труда обеспечены все требования безопасности при разработке нового оборудования.
доклад3.doc
Автомат спроектирован для эксплуатации на Автозаводе с учетом использования имеющегося оборудования за базу принят ток-вин станок 1И611П.
В д. проектировании поставлена следующая цель:
-увеличить производительность обработки детали «валик стекл. Автомобиля ИЖ2126» на операции точение для сокращения потребного количества единиц оборудования.
В соответствии с целью поставлены сл. Задачи:
- осуществить автоматизацию рабочих и вспомогат. ходов цикла обработки детали;
- осуществить автоматизацию загрузки выгрузки станка;
-обеспечить требования предъявляемые к детали.
При автоматизации цикла обработки за базу принята система управления с упорами. Принцип формообразования поверхностей при обработке заключается в том. что заготовка осущ. вращ. движение а инструмент в виде Фасонно-отрезного резца имеет движение попер. подачи.
состоит из станка 1И611П и из следующих узлов: БЗУ которое служит для загрузки заготовок Автооператор для передачи заготовки в зону обработки Бабка задняя подающая заготовку в цанг.зажим Зажим цанговый для автоматич. зажима загот. и удаления её после обработки Привод поперечной подачи для производства точения и электрооборудование управляющее этими узлами.
В основном Автоматизация проектируемых механизмов осуществляется пневматич. системой за исключением ппп где используется гидропривод т.к. пневматика не может обеспечить заданный закон движения вых. звена. (можно дать осн дост и недостатки).
Основные достоинства пневматических приводов следующие:
)возможность питания от на значительные расстояния;
)высокие скорости срабатывания исполнительных устройств;
) пожаро- и взрывобезопасность;
)возможность работы в шир диапазоне раб температур в усл запылени вибраций радиации;
)простота конструкции и высокая надежность пневматических устройств;
)простота ухода и обслуживания;
)относительно низкая стоимость и быстрая окупаемость.
К недостаткам пневматических приводов относятся:
)сравнительно высокая стоимость энергии сжатого воздуха что сказывается при непрерывном потреблении сжатого воздуха и больших его расходах;
)невозможность обеспечить заданный закон движения выходного звена;
)нестабильность скорости движения выходного звена;
) плохие условия смазки трущихся пов-стей подвижных элементов пнев устройств;
)низкий КПД пневматических приводов;
)необходимость защиты элементов привода от коррозии.
Бункерное загрузочное устройство.
Служит для захвата из бункера заготовок и передачи их в автоопер. Состоит из бункера качающегося сектора приводимого в движение пневмоцилиндром и лотка ориентирующего детали. Ёмкость бункера - 150Работой качающегося сектора управляют два пневмоклапана поз.54.
Автооператор. Служит для подачи детали из лотка загруз. устройства в зону обработки.
Автооператор состоит из кронштейна на котором крепится направляющая для перемещения штока поз.10 со стаканом поз.23; Шток имеет байонетный паз благодаря которому стаканчик с заготовкой поворачивается на 900. При этом ось заготовки совпадает с осью шпинделя.
Крайние положения корпуса руки фиксируются конечными выключателями смонтированными на направляющих.
Задняя бабка. Задняя бабка служит для подачи детали из автооператора в цанговый зажим для обработки. Установлена на направляющих станины. Состоит из корпуса с укрепленными на нем конечными выключателями и пиноли перемещающейся от пневмоцилиндров установленных в корпусе телескопически. Такая конструкция позволяет четко перемещать упор поз. 5 за два хода: первый ход цилиндра поз.2 на 85мм. и второй ход поршня поз.14 на 55мм.
Цанговый зажим установлен в шпинделе станка 1И611П. Состоит из цанги поз.8 тяги поз.1 и силового привода в кач-ве которого используется вращ цилиндр. Зажим цанговый снабжен пружинным выталкивателем поз.6 и реле давления.
Служит для зажима детали и удаления ее после обработки посредством выталкивающей пружины после чего деталь попадает в склиз и падает в тару.
Цанга изготовлена из стали марки У8А с термической обработкой конусной поверхности до твердости HRC 58-62 а хвостовика – до HRC 40-45.
Лепестки цанг при закалке немного разводятся чтобы подаваемая заготовка свободно проходил между ними. Угол при вершине конуса цанг делается 30°. Цанга имеет три прорези.
Можно выделить следующие достоинства зажима с затяжной цангой (с обратным конусом):
-конус цанги прилегает непосредственно к конической расточке в шпинделе что обеспечивает хорошее центрирование заготовки;
- осевая составляющая силы резания усиливает зажим прутка;
- лепестки цанги растягиваются а не сжимаются при зажиме и цанга и её конус мало деформируются;
-малые радиальные габариты
Цанга является основным исполнительным элементом в зажимном механизме и от ее характеристик во многом зависит работоспособность как зажимного устройства так и автомата в целом.
Привод поперечной подачи.
Служит для перемещения каретки с резцедержателем в поперечном направлении. Состоит из каретки поперечного суппорта и резцедержателя станка 1И611П перемещающихся от гидроцилиндра смонтированного сзади станка. Применение гидроцилиндра необходимо поскольку пневмоцилиндр не обеспечивает заданный закон движения выходного звена.
Холостой ход каретки 20 мм и рабочий ход 10 мм обеспечиваются дросселем с регулятором обратным клапаном и золотником ПГ-55-62 смонтированным на одном кронштейне с гидроцилиндром сзади станка.
Давление в гидросистеме 4 6 кгсм2. Включение и отключение дросселя обеспечивается кулачком закрепленным на каретке поперечного суппорта. Исходное и конечное положение каретки фиксируются конечными выключателями смонтированными на станине станка.
Гидробак поперечной подачи.
Служит в качестве емкости и для подачи масла под давлением 4 6 кгсм2 в гидроцилиндр. Состоит из двух форкамер куда подается сжатый воздух под давлением 4 6 кгсм2. Масло из форкамеры к золотнику с обратным клапаном ПГ-55-62 поступает через дроссель с регулятором смонтированным на боковой стенке гидробака. Гидробак монтируется на кронштейне и крепится на станине сзади станка 1И611П.
Электрооборудование.
На станке установлены два трехфазных асинхронных электродвигателя:
)Электродвигатель вращения шпинделя М1 и Электродвигатель смазки М2.
Электродвигатели и аппаратура рассчитаны на включение в сеть напряжением 380 В и частотой 50 Гц. Напряжение в цепи управления 110В. Напряжение в цепи сигнализации 55В. Подключение электрической части станка к сети осуществляется автоматическим выключателем АСТ-3. Вся электроаппаратура смонтирована в отдельно стоящем шкафу. Станок имеет автоматический и наладочный циклы работ. При нажатии кнопки S1 на пульте управления включается автоматическая работа станка и электродвигатель смазки М2.
Станок имеет наладочный и автоматичиский циклы работы. В наладочном режиме производится проверка работы каждого узла автомата. Пульт управления автоматом смонтирован на дверке электрошкафа. После подготовки автомата к работе включить кран управления бункерного загрузочного устройства. Начинает работать пневмоцилиндр Ц2 в автоматическом цикле. Сектор совершает качательные движения при этом нож сектора захватывает 1 или несколько заготовок и подает их в лоток. В крайних положених сектора установлены распределители переключающие ход штока на обратный. Т.о. обеспечивается автоматич. работа БЗУ.
В лотке заготовки перемещаются вниз под собст силой тяжести. В нижней части лотка смонтирован отсекатель кот в нужный момент пропускает 1 заг и она падает в стакан автооператора
Далее срабатывает пневмоцилиндр Ц4 подающей руки автооператора и подает деталь на ось центров автомата поворачивая заготовку на 90°. В конце хода руки срабатывает конечный выключатель SQ1 который дает команду на золотник Р6(У2) телескопического пневмоцилиндра задней бабки Ц6 происходит выдвижение пиноли задней бабки на 85 мм которая своим упором выталкивает деталь из подающей руки в цанговый зажим. В конце хода пиноли срабатывает конечный выключатель SQ 2 подающий команду на золотник Р4(У1) - пневмоцилиндр Ц4 переключается на обратный ход подающая рука автооператора возвращается в исходное положение.
После 35 мм хода назад подающей руки срабатывает конечный выключатель SQ3 дающий команду на золотник Р7(У3) телескопического цилиндра задней бабки Ц7 - происходит окончательная подача детали в цангу до упора.
В конце хода пиноли задней бабки срабатывает конечный выключатель SQ4 дающий команду на золотник Р1(У4); срабатывает пневмоцидиндр Ц1 цангового зажима детали. При достижении усилия зажима Рз = 180 кг (расчетное) реле давления дает команду на золотники Р6(У2) и происходит переключение телескопических цилиндров Ц6 и Ц7 пиноль задней бабки возвращается в исходное положение. Одновременно реле давления дает команду на электромагнитную муфту включающую вращение шпинделя и на золотник РЗ(У5) подающий сжатый воздух в гидробак.
Масло из гидробака поступает в гидроцилиндр Ц3 перемещая каретку с резцедержателем. Холостой ход каретки и рабочий ход обеспечивается дросселем с регулятором обратным клапаном и золотником ПГ-55-62 управляемым кулачком прикрепленным на каретке станка. В конце хода каретки т.е. после окончания обработки детали срабатывает конечный выключатель SQ 5.
Происходит быстрый отвод суппорта поперечной подачи в конце хода которого включается конечный выключатель SQ 6..
Далее цикл повторяется - Следущая заготовка падает в стакан автоопер и срабатывает пневмоцилиндр Ц4 подающей руки автооператора и подает деталь на ось центров.
Согласно поставленным задачам был автоматизирован весь цикл обработки. При этом увеличилась производительность обработки станка и как следствие увеличилась производительность труда рабочего. При этом рабочий освобождается от непосредственного участия в процессе обработки детали и появляется возможность многостаночного обслуживания. Облегчается физический труд рабочего он освобождается от однообразных повторяющихся движений от монотонных нервных и физических напряжений.
Благодаря повышению производительности станка при автоматизации уменьшается необходимое количество единиц оборудования с единицы площади цеха снимается больше продукции. Автоматизация вносит ритмичность в процесс обработки и способствует стабильности качества заготовок.
Охрана труда1.doc
В настоящее время основным направлением решения проблем охраны труда является переход от техники безопасности обеспечивающей безопасность при эксплуатации заведомо опасных машин и оборудования к безопасной технике. Это в полной мере относится и к производственному оборудованию предприятий машиностроения.
Научно-технический прогресс приводит к появлению новых материалов и реактивов новых источников шумов вибрации производственных излучений что приводит к необходимости разработки принципиально новых средств защиты. Его развитие в части автоматизации механизации и роботизации производства изменяет направленность охраны труда. На смену проблем физических перегрузок приходят проблемы нервно-психических перегрузок человека-оператора воспринимающего объем информации который может превышать величину возможную для восприятия и анализа. Что может привести к принятию неверных управленческих решений.
Основные направления работ по охране труда.
Обеспечение охраны труда связано с профилактикой травматизма и заболеваемости а также созданием условий труда для сохранения работаю-щими высокого уровня работоспособности в течение всего рабочего дня.
Работоспособность человека в процессе труда характеризуется предельными возможностями его организма связанными с выполнением конкретной работы.
Кардинальным решением проблемы тяжелого физического труда и работ с вредными условиями является механизация автоматизация и роботизация производства. В случае когда это невозможно осуществить определяющим является внедрение безопасной техники и технологии в частности применение средств коллективной защиты обеспечение безопасности зданий и сооружений а также надлежащих санитарно-гигиенических условий труда.
Понятие причины возникновения и физические характеристики вибраций.
В промышленности и на транспорте широкое применение получили машины и оборудование создающие вибрацию неблагоприятно воздействующую на человека. Это прежде всего все транспортные средства а также ручные машины. Увеличение производительности и как следствие этого рост мощностей и быстроходности технологического оборудования при одновременном снижении его материалоемкости уменьшение статических нагрузок на человека сопровождаются нежелательным побочным эффектом-усилением вибраций. Воздействие вибраций не только ухудшает самочувствие работающего и снижает производительность труда но часто приводит к тяжелому профессиональному заболеванию - виброболезни. Поэтому вопросам борьбы с вибрацией придается огромное значение.
В соответствии с ГОСТ 24346–80 (СТ СЭВ 1926– 79) «Вибрация. Термины и определения» под вибрацией понимается движение точки или механической системы при котором происходит поочередное возрастание и убывание во времени значений по крайней мере одной координаты.
Причиной возбуждения вибраций являются возникающие при работе машин и агрегатов неуравновешенные силовые воздействия. В одних случаях их источниками являются возвратно-поступательные движущиеся системы (кривошипно-шатунные механизмы ручные перфораторы вибротрамбовки агрегаты виброформования и т. п.); в других случаях неуравновешенные вращающиеся массы (ручные электрические и пневматические шлифовальные машины режущий инструмент станков и т. п.). Иногда вибрации создаются ударами деталей (зубчатые зацепления подшипниковые узлы и т.п.). Величина дисбаланса во всех случаях приводит к появлению неуравновешенных сил вызывающих вибрацию. Причиной дисбаланса может явиться неоднородность материала вращающегося тела несовпадение центра массы тела и оси вращения деформация деталей от неравномерного нагрева при горячих и холодных посадках и т. п.
Воздействие вибраций на человека чаше всего связано с колебаниями обусловленными внешним переменным силовым воздействием на машину либо на отдельную ее систему. Возникновение такого рода колебаний
может быть связано не только с силовым но и с кинематическим возбуждением например в транспортных средствах при их движении по неровному пути.
Воздействие вибраций на человека. Нормирование вибраций.
Различают общую и локальную вибрации. Общая вибрация вызывает сотрясение всего организма местная вовлекает в колебательное движение отдельные части тела. Общей вибрации подвергаются транспортные рабочие операторы мощных штампов грузоподъемных кранов и некоторых других видов оборудования. Локальной вибрации подвергаются работающие с ручным электрическим и пневматическим механизированным инструментом (зачистка сварных швов обрубка отливок клепка шлифование и т. п.).
Общая вибрация с частотой менее 07 Гц (качка) хотя и неприятна но не приводит к вибрационной болезни. Следствием такой вибрации является морская болезнь происходящая из-за нарушения нормальной деятельности органов равновесия (вестибулярного аппарата) по причине резонансных явлений.
Различные внутренние органы и отдельные части тела (например голову и сердце) можно рассматривать как колебательные системы с определенной массой соединенные между собой «пружинами» с определенными упругими свойствами и параллельно включенными сопротивлениями. Очевидно что такая система обладает рядом резонансов частоты которых определяющие субъективное восприятие вибраций зависят также от положения тела работающего (работа стоя или сидя).
Собственные частоты плечевого пояса бедер и головы относительно опорной поверхности (положение «стоя») составляют 4–6 Гц головы относительно плеч (положение «сидя») – 25–30 Гц. Для большинства внутренних органов собственные частоты лежат в диапазоне 6–9 Гц. Колебания рабочих мест с указанными частотами весьма опасны так как могут вызвать механическое повреждение или даже разрыв этих органов. Систематическое воздействие общих вибраций характеризующихся высоким уровнем виброскорости может быть причиной вибрационной болезни – стойких нарушений физиологических функций организма обусловленных преимущественно воздействием вибраций на центральную нервную систему. Эти нарушения проявляются в виде головных болей головокружений плохого сна пониженной работоспособности плохого самочувствия нарушений сердечной деятельности.
Вибрация может не вызывать болезненных ощущений но затруднить проведение производственных процессов.
Локальная вибрация вызывает спазмы сосудов которые начинаются с концевых фаланг пальцев и распространяются на всю кисть предплечье захватывают сосуды сердца. Вследствие этого происходит ухудшение снабжения конечностей кровью. Одновременно наблюдается воздействие вибрации на нервные окончания мышечные и костные ткани выражающееся в нарушении чувствительности кожи окостенении сухожилий мышц и отложениях солей в суставах кистей рук и пальцев что приводит к болям деформациям и уменьшению подвижности суставов. Все указанные изменения усиливаются в холодный и уменьшаются в теплый период года. При локальной вибрации наблюдаются нарушения деятельности центральной нервной системы как и при общей вибрации.
Виброболезнь относится к группе профзаболеваний эффективное лечение которых возможно лишь на ранних стадиях. Восстановление нарушенных функций протекает очень медленно а в особо тяжелых случаях в организме наступают необратимые изменения приводящие к инвалидности.
Различают гигиеническое и техническое нормирование вибраций.
В первом случае производят ограничение параметров вибрации рабочих мест и поверхности контакта с руками работающих исходя из физиологических требований исключающих возможность возникновения вибрационной болезни. Во втором случае осуществляют ограничение параметров вибрации с учетом не только указанных требований но и технически достижимого на сегодняшний день для данного вида машин уровня вибрации. При этом учитывают условия установки и режим работы стационарного виброактивного технологического оборудования в цехах условия эксплуатации ручного механизированного инструмента.
В соответствии с ГОСТ 12.1.012–78* «Система стандартов безопасности труда. Вибрация общие требования безопасности» установлены допустимые значения и методы оценки гигиенических характеристик вибраций определяющих ее воздействие на человека. Нормируемыми параметрами при гигиенической оценке вибрации являются средние квадратические значения виброскоростей v (и их логарифмические уровни ) или виброускорения для локальных вибраций в октавных полосах частот а для общей вибрации в октавных или 'з октавных полосах. Возможна интегральная оценка вибраций по частоте нормируемого параметра а также по дозе вибрации.
Гигиенические нормы вибрации установлены для длительности рабочей смены 8 ч. Для видов вибрации (или особых условий ее воздействия) не нашедших отражение в ГОСТ 12.1.012–78* (например при совместном действии локальной и общей вибрации шума и вибрации и др.) допустимые величины уровня вибраций должны быть приведены в стандартных или технических условиях на конкретные виды оборудования.
Методы снижения вибраций машин и оборудования.
Основными методами борьбы с вибрациями машин и оборудования являются:
) снижение вибраций воздействием на источник возбуждения (посредством снижения или ликвидации вынуждающих сил);
) отстройка от режима резонанса путем рационального выбора массы или жесткости колеблющейся системы;
) вибродемпфирование-увеличение механического импеданса колеблющихся конструктивных элементов путем увеличения диссипативных сил при колебаниях с частотами близкими к резонансным;
) динамическое гашение колебаний-присоединение к защищаемому объекту системы реакции которой уменьшают размах вибрации объекта в точках присоединения системы;
) изменение конструктивных элементов машин и строительных конструкций.
Средства индивидуальной защиты от вибраций.
При работе с ручным механизированным электрическим и пневматическим инструментом применяют средства индивидуальной защиты рук от воздействия вибраций. К ним относят рукавицы перчатки а также виброзащитные прокладки или пластины которые снабжены креплениями в руке. Общие технические требования к средствам индивидуальной защиты рук от вибраций определены ГОСТ 12.4.002–74. Учитывая неблагоприятное воздействие холода на развитие виброболезни при работе в зимнее время рабочих надо обеспечивать теплыми рукавицами.
Обеспечение требований безопасности к зажимным механизмам.
Усилия закрепления берутся с коэффициентом запаса К = 2.5.
Зажимные рукоятки не создают опасности при работе станка.
Обеспечение требований безопасности к органам управления.
Органы управления имеют блокирующее устройство для автоматического отключения немеханизированного привода при включении механизированного привода.
Высота от уровня пола (рабочей площадки) до органов управления составляет 1200 мм.
Требования к контрольным и сигнальным устройствам предупредительным надписям таблицам и т. п. соответствуют ГОСТ 21829-76 и ГОСТ 12.4.026-76; к направлению движения рукояток органов управления - ГОСТ 9146-79; к формам и размерам органов управления зажимным рукояткам а также к усилиям к ним прикладываемым - ГОСТ 21752-76 ГОСТ 21753-76 ГОСТ 22129-76 и ГОСТ 12.2.009-80.
Обеспечение требований безопасности к гидроприводам.
Требования к гидроприводам по ГОСТ 12.3.001-73 ГОСТ 12.2.040-79 ГОСТ 12.2.009-80.
Гидроприводы оборудованы устройствами для защиты рабочей среды от загрязнения; от возбуждения давления превышающего максимально допустимое значение и от падения давления в рабочей полости цилиндра при прекращении подачи или мгновенном падении давления рабочей среды.
После окончательной наладки СП следует опломбировать элементы гидроприводов разрегулирование которых ведет к аварийной ситуации.
Головки выводных устройств сливные пробки окрашивают в красный цвет. Корпусы кранов управления гидроприводом должны иметь отличительную окраску. Устройства гидроприводов должны иметь обозначение направления потока рабочей среды и маркировку по ГОСТ 15108-82. При наличии нескольких трубопроводов с различным давлением каждый из них должен иметь отличительную окраску по ГОСТ 22133-76 и маркировку присоединительных элементов по ГОСТ 15108-82.
Не допускаются отброс на рабочего стружки и пыли струей отработанного воздуха а также загрязнение рабочей зоны (пространство высотой до 2000 мм от уровня пола).
Обеспечение требований безопасности к средствам защиты входящим в конструкцию приспособления.
Открытые элементы СП перемещающиеся со скоростью более 0.15 мс имеют ограждение (ГОСТ 12.2.009-80) или предупредительную окраску (ГОСТ 12.4.026-76) а вращающиеся СП являющиеся источником опасности - предохранительные кожухи.
Уровень вибрации СП с силовым приводом к нему на рабочем месте ГОСТ 12.2.009-80. Шумовые характеристики СП соответствуют санитарным нормам. Установка СП не повышает октановых уровней звуковой мощности станка.
Обеспечение требований безопасности к транспортированию сборке ремонту хранению.
Конструкция СП является безопасной при складировании и транспортировке.
Выступание штифтов над поверхностью соединяемых деталей а также концов винтов и шпилек над гайкой на размер больший половины диаметра резьбы отсутствуют. Для предупреждения самоотвинчивания винтов и гаек используются контргайки шплинты и др.
He допускаются ремонт и техническое обслуживание СП во время работы станков. Приспособления должны храниться на стеллажах в шкафах обеспечивающих соблюдение всех требований безопасности складирования и хранения грузов.
Контроль выполнения требований безопасности.
Контролю выполнения требований безопасности должны подвергать вновь изготовленные модернизированные и прошедшие ремонт СП в ходе приемочных приемосдаточных или периодических испытаний (ГОСТ 15.001-73). Виды испытаний определяются по ГОСТ 16504-81 и по чертежу на СП. Объем испытаний и контроля должен устанавливаться государственными стандартами и нормативно-техническими документами на конкретное приспособление (ГОСТ 12.2.029-77).
Обеспечение требований электробезопасности.
Удельный вес электротравматизма среди других его видов невысок но из-за высокого процента случаев со смертельным исходом этому виду травматизма уделяется серьёзное внимание. Наиболее тяжёлой формой электрической травмы является электрический удар при котором нарушается деятельность органов дыхания кровообращения и центральной нервной системы.
Электробезопасность проектируемого станка обеспечивается следующими мероприятиями:
Заземление корпусов электродвигателей и электрошкафа (сопротивление заземления с изолированной нейтралью не превышает 4 Ом).
Местное освещение согласно норм для автоматических цехов осуществляется переменным током напряжением 36 В. для наладочных работ предусмотрено дополнительное переносное освещение напряжением 12 В. норма освещённости при работе линии металлообрабатывающих станков-автоматов составляет не менее 150 лк. При лампах накаливания и люминесцентных лампах 300 лк.
На станках с целью повышения безопасности принято: кнопка «пуск» вращения шпинделя и привода подач - чёрного цвета утоплены на 3-5 мм. Кнопки «стоп» отключения вращения шпинделя и привода подач - красного цвета и выступают на 3 мм. На пульте управления имеется лампочка сигнализирующая о наличии напряжения в цепи питания. Кнопка «общий стоп» - грибкового типа красного цвета.
Электропроводка выполнена закрытой в герметичных бронеруковах.
Цвет оборудования в цехе должен быть светло-серый эмаль 810. цвет проёмов в станке - кремовый согласно нормам HOG-2 «Окраска металлорежущих станков (заточные станки)» что значительно уменьшает утомляемость рабочего.
Известно что шум вредно влияет на здоровье работающих. Допустимый уровень шума для рабочих зон в производственных помещениях составляет 85 дбл ГОСТ12.1.003-76 (по шкале А - уровень эквивалентного шума).
При работе на станке средства индивидуальной защиты от шума не предусматриваются. Шумовые характеристики замеряются шумомером ШУМ-1М.
В разделе рассмотрены некоторые проблемы охраны труда на производстве. Эти проблемы невозможно решить только лишь соблюдением мер безопасности обязательных для технологического процесса необходимо проводить комплексные мероприятия по устроению неблагоприятного влияния тех или иных опасных факторов начиная с этапа планирования. Только в этом случае можно учесть все требования производственного процесса будь то освещение рабочего места или использования индивидуальных средств защиты. Правильное с точки зрения охраны труда построение производственного процесса требует вложения некоторых материальных средств. Окупаются они косвенно буть то работоспособность и здоровье рабочего или минимальные потери при пожаре и т.д. а если рассматривать жизнь человека как наивысшую ценность учёт охраны труда становится непременным условием построения производственного процесса.
титул+аннотация.doc
ИЖЕВСКИЙ ГОСУДАРСТВЕННЫЙ ТЕХНИЧЕСКИЙ УНИВЕРСИТЕТ
Кафедра «Проектирование и эксплуатация машин и оборудования»
Зав. кафедрой д.т.н. профессор
РАСЧЕТНО-ПОЯСНИТЕЛЬНАЯ ЗАПИСКА К ДИПЛОМНОМУ ПРОЕКТУ
ТЕМА:« Разработка токарного автомата для обработки детали типа валик стеклоподъемника на базе станка модели 1И611П».
Дипломник студент гр. 10-34-1 Корниловский О.А.
Руководитель дипломного проекта к.т.н. доц. Батинов И.В.
Консультант по организационно-
экономической части доц. Янцен Т.В.
Консультант по экологии
безопасности жизнедеятельности к.т.н. доц. Глухов Ю.Г.
Представитель контроля выполнения
НОРМ ЕСТД И ЕСКД доцент Иванов В.Ф.
Представитель технологического
контроля к.т.н. доц. Шитова Т.В.
Дипломный проект студента очного обучения специальности 120200 Корниловского О.А.
на тему: « Разработка токарного автомата для обработки детали типа валик стеклоподъемника на базе станка модели 1И611П».
Проект посвящен разработке токарного автомата с одновременной модернизацией станка 1И611П.
За счет применения новых автоматических устройств и приводов станка повышается производительность обработки деталей до 400 - 600 дет.час.
Модернизирована задняя бабка с целью автоматизации перемещения пиноли.
Разработан цанговый зажим который служит для автоматического зажима детали и удаления ее после обработки посредством выталкивающей пружины.
Разработаны автоматические бункерно-загрузочное устройство и автооператор которые обеспечивают нужную ориентацию заготовки в пространстве и передачу её в зону обработки.
Спроектирован автоматизированный привод поперечной подачи работа которого осуществляется посредством гидравлики.
Выполнены все необходимые расчеты предусмотренные методическими указаниями по выполнению дипломного проекта.
В графической части проекта представлены:
- механизированная задняя бабка с автоматическим перемещением пиноли;
- кинематическая схема;
- гидропневматическая схема;
- электрическая схема;
- рабочий чертеж детали 408-6104036-10;
- технико-экономические показатели;
- циклограмма работы станка;
- привод поперечной подачи;
- бункерно - загрузочное устройство.
Глава3,4.doc
При работе в продолжительном режиме (S2) двигатель выбирают по требуемой мощности исходя из режимов резания и преодоления сил трения. Мощность двигателя в приводе главного движения может быть определена по зависимости:
Ргл = Рр + Рхх + Рдоп
где Рхх – мощность затрачиваемая на холостом ходу; Рр – мощность затрачиваемая на процесс резания; Рдоп – мощность затрачиваемая на преодоление дополнительных потерь под нагрузкой.
Мощность потребная на резание при точении определяется по формуле:
где Fz1 – тангенциальная сила резания при точении паза резцом ЦТ2112-4010 (см. тех. процесс); Fz2 – тангенциальная сила резания при снятии фаски резцом ЦТ2112-4029; V – скорсть резания ммин; cp t1 t2 – длина лезвия первого и второго инструмента мм; S – подача ммоб определяется из табл. 15 [36]; Kp – коэффициент характеризующий влияние геометрии инструмента на силы резания.
Рхх и Рдоп не превышают 15 20% от Рр и с удовлетворительной точностью могут быть учтены коэффициентом полезного действия привода главного движения – поэтому:
где К – коэффициент кратковременной перегрузки допускаемой стандартными двигателями; – КПД привода главного движения станка.
зп кр – КПД зубчатой и клиноременной передачи соответственно.
По рассчитанной мощности выбирается конкретный асинхронный двигатель по каталогу [1].
Выбираем асинхронный двигатель 4А100 4У3:
мощность при n = 1500 обмин – 30 кВт;
nэд под нагрузкой – 1434 обмин.
2. Прочностной расчет коробки скоростей
Валы предназначены для поддержания насаженных на них тел вращения и передачи крутящего момента вдоль вала.
Расчет вала производится с целью обеспечения их прочности жесткости и отсутствии недопустимых колебаний. В редукторах вследствие сравнительно небольшой частоты вращения вала (до 1500 обмин) и небольших расстояний между опорами расчет на жесткость и колебания обычно не проводят и таким образом основным расчетом является прочностной расчет вала.
Нагрузкой на вал являются силы от зубчатых передач натяжение ремня клиноременной передачи и крутящий момент. Собственной массой вала и деталей насаженных на вал обычно пренебрегают. Принято считать что нагрузки прикладываются не по всей ширине детали а в одной точке в середине ширины детали. Место приложения нагрузки выбирается в соответствии с кинематической схемой редуктора и всего привода. Направление сил должно выбираться таким образом чтобы получить наихудшие условия загружения вала из всех возможных вариантов.
Производится проверочный расчет вала IV (см. чертеж «Кинематическая схема»)
Определение передаточного отношения каждой передачи:
Определение частот вращения на каждом валу:
Определение мощности на каждом валу:
О0пределение крутящего момента на валу
Ориентировочный расчет вала
Ориентировочный расчет производится с целью уточнения исходных данных и в частности для определения приближенно диаметра и межопорного расстояния вала так как без этих данных не могут быть проведены последующие расчеты. Этот расчет обычно производится из условия статической прочности на чистое кручение по пониженным допускаемым напряжениям кручения так как еще не полностью ясен вопрос о величине возникающих в вале изгибных напряжений.
Диаметр вала определяется из условия:
где Т – крутящий момент на рассматриваемом валу; [] – допускаемое напряжение на кручение принимаемое равным 15 МПа;
В зубчатых и червячных передачах в зоне зацепления действует сила направленная по линии зацепления. Эту силу с целью определения взаимного расположения нагрузок действующих на вал обычно представляют двумя (для прямозубой цилиндрической передачи) или тремя (для остальных передач) составляющими. Величина составляющих место их приложения и направление для соответствующих передач определяется так как указано ниже. При этом следует помнить что силы действующие со стороны ведущих элементов на ведомые являются активными т.е. окружные силы совпадают по направлению с окружной скоростью а силы действующие со стороны ведомых элементов на ведущие – реактивными т.е. окружные силы и окружная скорость направлены противоположно.
где T1 – крутящий момент на валу; dw – диаметр начальной окружности колеса на этом же валу равный m z (m – модуль зацепления; z – число зубьев шестерни).
где α – угол зацепления равный 20°.
Окружная сила приложена на плече относительно оси вала равном dw2 перпендикулярно к оси вала и вызывает изгиб вала и его кручение. Радиальная сила направлена перпендикулярно и оси вала через эту ось и вызывает изгиб вала. От этих сил в вале также возникают перерезывающие силы которыми обычно пренебрегают ввиду их малого влияния на общие напряжения в вале.
Сила Fв на вал от натяжения ветвей определяется
где Kf – коэффициент зависящий от расположения ременной передачи в пространстве; для вертикальной передачи Kf = 1; q – масса погонного метра ремня; g – ускорение силы тяжести; a – межосевое расстояние м.
Составляем расчетные схемы вала в координатах
При этом за неподвижную шарнирную принимают опору где установлен подшипник воспринимающий радиальное и осевое усилие или любую опору при неизвестных вышеприведенных данных.
Вычерчиваем расчетную схему вала в двух проекциях – в вертикальной и горизонтальной – с простановкой на них сил. При этом следует помнить что если рассматривать силы приложенные в одной точке то радиальная и осевая силы всегда лежат в одной плоскости а окружная – в перпендикулярной к ней плоскости.
Определяем опорные реакции в горизонтальной
и вертикальной плоскостях
Для этого составляем уравнения моментов относительно одной и другой опор. В заключение этого пункта обязательно проведем проверку полученных значений реакции по условию; сумма всех сил на ось у или z должна быть равна нулю. Если наблюдается неравенство то расчет неверен и его следует повторить. Направление реакций задаем произвольно.
Реакция направлена в другую сторону; в дальнейших расчетах будем брать направление реакции вениз.
Определяем суммарные реакции в опоре А и В:
Подбор подшипников здесь не проводим считаем что они подобраны правильно вследствие чего размеры вала были приняты верными.
Строим эпюры изгибающих моментов в 2-х плоскостях:
На участке от Fay до Fr:
при Х1 = 0 ; при Х1 = 70 мм .
На участке от Fr до Fby:
На участке от Fby до Fв:
На участке от Fax до Ft:
при Х1 = 0 ; при Х1 = 70 мм .
На участке от Ft до Fbx:
Строим эпюру суммарного изгибающего момента по зависимости:
Под силой Fax и Fay: M = 0.
Под силой Fbx и Fby:
Строим эпюру крутящего момента равного .
Уточненный расчет вала
Уточненный расчет вала производится с целью нахождения истинного значения запаса прочности вала.
Установлено что работоспособность вала из условия усталостной прочности будет обеспечена если
где S – фактический (расчетный) коэффициент запаса прочности; [S] – допускаемый коэффициент запаса прочности обычно принимаемый для валов редуктора в пределах 15 5.
Рис. 8. Эпюры нагружения вала
Уточненный расчет вала проводится с учетом воздействия на него переменных нагрузок из условия его усталостной прочности.
Выбираем материал вала. Назначаем для вала сталь марки Сталь 45. Для этой стали предел прочности в = 900 МПа; пределы выносливости –1 = 380 МПа –1 = 230 МПа; коэффициент чувствительности к ассиметрии цикла = 005.
Определяем запас прочности вала. При действии на вал только напряжений изгиба или напряжений кручения коэффициенты запаса усталостной прочности соответственно по изгибу и кручению определяются по зависимостям:
При совместном действии на вал напряжений изгиба и кручения коэффициент запаса прочности определяется по выражению:
В этих формулах обозначено: –1 –1 – пределы выносливости при изгибе и кручении для симметричного цикла; K K – эффективные коэффициенты концентрации напряжений при изгибе и кручении принимаемые по [13 табл. 15.1]; Kd KF – масштабный фактор и фактор качества поверхности определяются по графикам рис. 15.5 и 15.6 [13]; а а – переменные составляющие циклов напряжений.
где М и Т – соответственно изгибающий и крутящий моменты в рассматриваемом сечении вала; Wи Wкр – моменты сопротивления на изгиб и кручение этого же сечения.
где d – диаметр вала.
что в пределах нормы.
Проверка вала по статистической прочности
Эту проверку производят в целях предупреждения пластических деформаций и разрушений с учетом кратковременных перегрузок.
Статическая прочность вала обеспечена.
2.2. Расчет цилиндрических передач коробки скооростей
Определение допускаемых напряжений
Определение допускаемых напряжений производится в зависимости от механических характеристик материала колес и вида термообработки состояния рабочей поверхности зуба и переходной поверхности базового числа циклов для материала колес действительного числа циклов нагружения вызванных постоянной или переменной нагрузкой. Статическая прочность зубьев определяется значением наибольшей нагрузки. Если передачи работают в условиях переменных напряжений вызванных постоянным или переменным режимом нагружения то необходимо учитывать суммарный эффект на усталостную прочность различных по величине и продолжительности нагрузок. Расчет передач по наибольшей нагрузке если принять ее постоянно действующей в течение всего срока службы приведет к избыточной прочности и утяжелению деталей увеличению габаритов и стоимости.
Допускаемое усталостное контактное напряжение:
где zR – коэффициент учитывающий шероховатость zR = 095; zv – коэффициент окружной скорости zv = 1; SH – коэффициент запаса прочности; при улучшении SH = 12; при закалке SH = 13; zN – коэффициент долговечности;
где NHG – базовое число циклов;
NHЕ – эквивалентное число циклов;
где eH – коэффициент эквивалентности eH = 025; t – время работы в часах; n – частота вращения зубчатого колеса; m – степень кривой усталости = 6;
– предел контактной выносливости;
Допускаемое расчетное контактное напряжение для расчетов принимается наименьшее из двух:
Определение коэффициента нагрузки
В расчетные уравнения для определения размеров передачи и действительных изгибных и контактных напряжений подставляется наибольшая длительно действующая мощность с учетом сил инерции возникающих в станке при пусках и остановках торможении и изменении режимов резания припусков и т. п.
Однако в передачах возникают дополнительные динамические нагрузки обусловленные внутренними причинами передач и кроме того концентрация нагрузки вдоль контактных линий. Учет этих нагрузок производится введением в расчетные уравнения коэффициента нагрузки.
Для предварительных расчетов при несимметричном расположении колес на валах принимаем коэффициент нагрузки КН = 15 ([33] с. 124).
Определение межосевого расстояния
Межосевое расстояние определяется из условия контактной прочности:
Геометрический расчет зубчатой передачи
Делительные диаметры:
Проверка межосевого расстояния:
Диаметры вершин зубьев:
где d12 – делительные диаметры; m – расчетный модуль.
Ширина венца зубчатого колеса:
где аw – межосевое расстояние; а – коэффициент ширины венца зубчатого колеса;
Коэффициент торцевого перекрытия:
Определение степени точности колеса
Степень точности зависит от окружной скорости:
По приложению 19 [33] принимаем 8 степень точности.
Определение коэффициентов нагрузки по контактным напряжениям
где KHv KFv – коэффициенты внутренней динамической нагрузки KHv =105; KFv =11 ([31] с. 181); KH KF – коэффициенты концентрации нагрузки; KH = 104; KF =1 ([31] с. 182); KHα KFα – коэффициенты распределения нагрузки между зубьями KHα = KFα =1.
Проверка по контактным напряжениям
где zE – коэффициент материала (для стали = 190); ze – коэффициент учета суммарных длин контактных линий; Ft – окружная сила;
Изменение в допустимых пределах .
2.3. Расчет шпоночного соединения
Производится расчет шпоночного соединения на валу IV обеспечивающего передачу крутящего момента на шкив 160.
Размеры шпонок выбираются в зависимости от принятого диаметра вала по таблицам ГОСТа а затем производится условный расчет на смятие в предположении что напряжения на узких рабочих гранях шпонки и паза распределяются равномерно.
где Т – передаваемый крутящий момент; d – диаметр вала; h – высота сечения шпонки = 11 мм; t – глубина паза = 33 мм; []см – допускаемое напряжение смятия; []см = 600 800 МПа.
(см. чертеж «Шпиндельная бабка с зажимом цанговым»)
Цанговый зажим установлен в шпинделе станка 1И611П. Состоит из цанги поз. 8 тяги поз. 1 и силового привода. Зажим цанговый снабжен пружинным выталкивателем и реле давления рассчитанным на определенное усилие зажима детали.
Цанговый зажим должен удовлетворять следующим требованиям:
концентричный зажим при радиальном биении не больше 001-004 мм;
надежный зажим при нормальных погрешностях заготовок – в пределах 5-го класса точности;
постоянство длины подаваемого прутка;
постоянство упругих свойств цанги износостойкость губок цанги (зажим 50000-100000заготовок до выхода из строя).
Цанги изготавливают из сталей марок У8А У10А 65Г с термической обработкой конусной поверхности до твердости HRC 58-62 а хвостовика – до HRC 40-45.
Лепестки цанг при закалке немного разводятся чтобы подаваемый пруток свободно проходил между ними. Угол при вершине конуса цанг делается 30°. Число прорезей у цанги – от двух до шести в зависимости от диаметра заготовки. При диаметре свыше 20 мм рекомендуется три прорези.
Можно выделить следующие достоинства зажимов с затяжной цангой (с обратным конусом):
конус цанги прилегает непосредственно к конической расточке в шпинделе что обеспечивает хорошее центрирование заготовки;
исключено заклинивание во время подачи прутка;
осевая составляющая силы резания усиливает зажим прутка;
лепестки цанги растягиваются а не сжимаются при зажиме и цанга и её конус мало деформируются;
малые радиальные габариты.
Цанга является основным исполнительным элементом в зажимном механизме и от ее характеристик во многом зависит работоспособность как зажимного устройства так и автомата в целом.
3.1. Расчет сил зажима
Для вращающихся обрабатываемых заготовок сравнительно высокой жесткости необходимую силу зажима TΣ определяют при соблюдении следующих трех условий:
Момент закрепления Мпр должен быть больше крутящего момента Мр возникающего от составляющих сил резания стремящихся повернуть заготовку вокруг оси вращения (Мпр > Мр).
При отсутствии упора суммарная осевая сила сцепления Pпр должна быть больше суммарной осевой силы резания P0 (Pпр > P0).
Момент зажима Мв возникающего от силы сцепления должен быть больше изгибающего момента Ми от составляющих сил резания стремящихся вывернуть заготовку относительно точки опоры (Мв > Мв).
Суммарная радиальная сила зажима прижимающая губки цанги к заготовке определяется по формуле взятой из [28].
Для нашей схемы работы зажима (см. рис.8) осевая сила S2 может быть вычислена по формуле ([28] табл. 7.19 стр. 142):
где Кзап – коэффициент запаса; – коэффициент сцепления между губками цанги и заготовкой; Р Мсв – крутящий момент при сверлении; d d φ пр – приведенный угол трения (рис. 8).
Рис. 8. Схема действия осевой силы при одинарном зажиме.
Суммарная радиальная сила зажима прижимающая губки цанги к заготовке равна:
Зная суммарную осевую силу зажима в цанговом патроне можно перейти непосредственно к расчету пневмоцилиндра.
3.2. Расчет пневмоцилиндра
Основные параметры поршневого цилиндра с односторонним штоком
связаны между собой следующими соотношениями [32]:
При движении поршня вправо когда поршневая камера соединена с напорной линией а штоковая – со сливной:
где F1 F2 – площадь поршневой и штоковой полости мм2; р1 р2 – давление в поршневой и штоковой полости кгссм2; Р1 Р2 – полезная нагрузка Н; V1 V2 – скорость перемещения штока ммин; Q1 Q2 – расход воздуха лмин; kтр = 09-098 – коэффициент учитывающий потери на трение в цилиндре;
При движении поршня влево когда штоковая камера соединена с напорной линией а поршневая – со сливной:
Диаметр пневмоцилиндра определяется по формуле взятой из [9]:
где Р2 – технологическая (полезная) нагрузка Н; т – масса всех подвижных элементов связанных с поршнем кг; g – ускорение свободного падения мс2; рт – подводимое абсолютное давление сжатого воздуха кгссм2;
Вес подвижных частей ±mg учитывают при вертикальном или наклонном расположении пневмоцилиндра. Знак «+» ставят тогда когда вес уменьшает зажимное усилие. В расчетной формуле принято что требуемое усилие зажима создается при давлении 09рт чем обеспечивается некоторый его запас. Т.к. пневмоцилиндр расположен горизонтально то сила ±mg в формуле равна нулю.
Найденное значение D округляют до ближайшего из нормального ряда диаметров цилиндров по ГОСТ 6540-68: 25 32 40 50 63 80 100 125 160 200 250 320 360 400 мм.
Следовательно диаметр пневмоцилиндра цангового зажима следует принять равным 200 мм.
Диаметр штока определяют из соотношения:
d = (025 . . . 032) D
и округляют до ближайшего значения взятого из ряда 10 12 16 25 32 40 50 63 80 90 мм.
Исходя из конструктивных соображений принимаем диаметр штока равным 25мм.
Условный проход присоединительных отверстий пневмоцилиндра рекомендуется принимать из соотношения dy = 01D. Обычно такой же условный проход имеют присоединяемые воздухопроводы и установленные на них элементы пневмоаппаратуры. Однако выбирая величину dy необходимо также учитывать длину хода поршня и требуемое быстродействие привода. При малых длинах ходов условный проход уменьшают.
Принимаем dy равным 15мм.
Рассчитаем рабочую площадь поршня в поршневой 1 и штоковой 2 областях соответственно.
Требуемое усилие на штоке цангового зажима обеспечено.
4. Бункерное загрузочное устройство
Автоматизация производственных процессов является характерной чертой современного прогресса. Без автоматизации невозможны высокие темпы дальнейшего роста производительности труда. Одной из основных проблем при автоматизации технологического оборудования и в частности металлорежущих станков является автоматизация загрузки заготовок и разгрузки (съема) обработанных деталей а при создании автоматических линий кроме того и автоматизация транспортных перемещений между станками.
Автоматизация загрузки и разгрузки оборудования находящегося в эксплуатации позволяет изменить процесс труда повысить безопасность и коэффициент использования оборудования а в некоторых случаях интенсифицировать режим его работы; полуавтоматические станки и станки с ручным управлением можно превратить в автоматы снизив тем самым штучное время обработки и широко использовать многостаночное обслуживание
Мнение что автоматизация загрузки-разгрузки оборудования ранних лет выпуска целесообразна только в условиях массового производства является ошибочным. Оснащение производства станками и технологической оснасткой сборно-разборной конструкции позволяет автоматизировать технологический процесс в условиях серийного и мелкосерийного производства и при частой смене объектов производства. В условиях серийного производства автоматизации производства должна предшествовать типизация технологических процессов или разработка групповых методов обработки.
В бункерных загрузочных устройствах заготовки в бункере (емкости) сосредоточены навалом. Захват из бункера и ориентация заготовок в положение требуемое для обработки или удобное для загрузки и все последующие перемещения осуществляются автоматически.
Загрузочные устройства эффективны если они повышают коэффициент использования станков (автоматических линий) на которых они установлены и производительность а также облегчают условия труда; не повреждают поверхность подаваемых заготовок или удаляемых со станка обработанных деталей; имеют простую конструкцию и минимальное количество деталей; состоят из нормализованных деталей; удобны в эксплуатации и дешевы в изготовлении; позволяют легко заменять быстроизнашивающиеся детали устройств.
Независимо от типа различают универсальные универсально-наладочные и специальные загрузочные устройства; первые два типа с помощью переналадки или подналадки а также замены некоторых деталей могут быть использованы для загрузки заготовок отличающихся размером а иногда и формой; устройства третьего типа применяют только для загрузки заготовок определенного типа. Загрузочные устройства только загружают заготовки а снимают (разгружают) обработанные детали толкатели станка или детали поступают в приемный лоток под действием собственного веса (силы тяжести).
Загрузочно-разгрузочные устройства (автооператоры или механические руки) специальными механизмами не только загружают но и разгружают заготовки.
Конструкторы разработали основы теории проектирования загрузочно-разгрузочных устройств и создали оригинальные конструкции устройств эксплуатируемые на заводах. Дальнейшему появлению новых и высокопроизводительных загрузочно-разгрузочных устройств будет способствовать разработка и исследование: механизмов ориентации используемых для заготовок повышенной сцепляемости; механизмов ориентации заготовок в магнитном поле и систем логической ориентации механизмов вторичной ориентации.
4.1. Расчет бункерного загрузочного приспособления
В бункерных загрузочных устройствах основной запас изделий сосредоточивается в емкостях сделанных в виде коробов различной формы или широких лотков.
Размеры бункеров в машиностроении ограничиваются большим давлением изделий на стенки емкости и друг на друга так как вследствие этого затрудняется извлечение их из емкости.
В процессе работы в автоматических бункерах изделия захватываются и транспортируются в накопитель в ориентированном положении.
Изделия при этом подвергаются ударам и трению друг о друга и о захват транспортирующего механизма. Поэтому если повреждения недопустимы или изделия недостаточно жестки и сложны настолько что возможно сцепление их между собой применение бункерных загрузочных устройств с движущимся захватом исключается.
Рис. 9. Бункер: 1 – бункер 2 – сектор 3 – лоток
Емкости автоматических бункеров для штучных изделий имеют сходство с обычными бункерами для насыпных грузов. Под бункером принято понимать емкость имеющую относительно малую высоту по сравнению с размерами поперечного сечения бункера. К бункерам относят все емкости в которых плоскость обрушения (рис.9) пересекает свободную поверхность материала (в зоне бункера). Аналитически это выражается следующим образом:
Практически высота обычного бункера не превышает двух поперечников что характеризуется соотношением hmax = 2m.
В соответствии с рекомендациями данными в [28] размеры секторного бункера берутся в зависимости от наибольшего поперечника изделия. Для бункера с центральным сектором эти зависимости имеют вид:
ширина бункера В = (12-15)l;
глубина h = (14-13)l;
Производительность бункера считается по формуле взятой из [28]:
где z – число секторов; р – коэффициент захватывания который берется в зависимости от формы и конфигурации изделия.
4.2. Сыпучесть изделий
Работоспособность бункера зависит от степени взаимоподвижности изделии в бункере под действием внешних сил т. е. сыпучести изделий. В свою очередь сыпучесть изделий зависит от материала веса чистоты обработки загрязненности конфигурации а также от количества и высоты слоя изделий в емкости.
Основное влияние на сыпучесть изделий оказывает вес и размеры последних чем крупнее и тяжелее изделия тем сыпучесть ниже. Изделия следует загружать небольшим слоем так как действие веса ухудшает работоспособность бункера.
Сыпучесть характеризуется углом естественного откоса образованного при свободном набросе изделий в кучу на плоскости. Наибольшей сыпучестью обладают шарообразные изделия так как образуют наименьший угол естественного откоса. Сыпучесть в бункере зависит и от отношения всего объема бункера к объему занимаемому изделиями.
На рис. 10 показана экспериментальная кривая по которой можно определить высоту слоя изделий в бункер. По оси абсцисс отложены наибольшие размеры изделий от 25 до 250 мм а по оси ординат–высота слоя изделий выраженная количеством поперечника (числом рядов) загружаемого изделия.
Рис. 10. Экспериментальная кривая определяющая зону применения бункеров в зависимости от размеров изделий.
Из графика видно что чем меньше поперечник изделия тем допускается больше количество рядов их в бункере. Для крупных изделий начиная от 150 мм допускается один ряд. В тех случаях когда высота или длина изделия равна 09-01 наибольшего поперечника рекомендуется применять магазин или штабельник.
4.3. Давление изделий на стенки бункера
Давления воспринимаемые стенками автоматического бункера без учета трения изделий и стенки и конфигурации бункера определяются на основе теории сыпучих тел Вертикальное давление Ру на горизонтальную плоскость расположенную на высоте у от верхнего уровня засыпки материала выражается как гидростатическое давление.
где q – насыпной вес материала в кГсм3.
Горизонтальное (боковое) давление в любой точке по высоте бункера определяется как результат действия клина нагруженного собственным весом Q при отсутствии трения материала на стенке. Горизонтальное давление на высоте у от поверхности засыпки определяется по формуле:
Рx = R · Ру = R ·q · у (40)
Из уравнения видно что горизонтальное давление на любом уровне пропорционально вертикальному давлению на том же уровне и составляет его долю определяемую коэффициентом R зависящим от степени сыпучести материала и определяемого по формуле:
где φ – угол естественного откоса.
Толщина стенок бункеров практически берется в зависимости от веса Q в кг загружаемых изделий:
Учитывая что количество одновременно загружаемых деталей n=150шт. а масса одной детали m = 0053 кг получаем:
Принимаем толщину стенок равную 1мм.
4.4. Плотность насыпки изделий и их насыпной вес
Изделия засыпанные в бункер располагаются в нем с различной степенью плотности которая характеризуется отношением суммы объектов пустых пространств остающихся между изделиями ко всему объему;
где V1 – общий объем занимаемый изделиями (емкость бункера кучи); V2 – объем самих изделий (по внешней конфигурации); V3 = V1 – V2 – объем пустых пространств.
Зная расчетную емкость бункера V1=4500 см3 и объем всех деталей равный » 4000 см3 найдем V3 = 4500 – 4000 = 500 см3 тогда:
Сектор совершает возвратно-поступательные движения захватывая заготовки и подавая их в лоток. Лоток выполнен наклонным благодаря чему заготовки могут перемещаться за счет собственной силы тяжести.
Найдем теоретическую производительность бункера:
Захват деталей из бункера поз. 1 (см. рис. 11) производится с помощью сектора поз. 2 который движется от пневмоцилиндра поз. 4.
Интенсивность поступления деталей из бункера поз. 1 в лоток поз. 3 регулируется дросселями поз. 5 на пневмоцилиндре бункерного загрузочного изделия.
Рис. 11. Бункерное загрузочное устройство.
4.5. Расчет пневмоцилиндра
Основные параметры поршневого цилиндра с односторонним штоком связаны между собой следующими соотношениями [32]:
При движении поршня вправо когда поршневая камера соединена с напорной линией а штоковая – со сливной
При движении поршня влево когда штоковая камера соединена с напорной линией а поршневая – со сливной
где P2 – технологическая (полезная) нагрузка; m – масса всех подвижных элементов связанных с поршнем; g – ускорение свободного падения; pm – подводимое абсолютное давление сжатого воздуха;
Вес подвижных частей ±mg учитывают при вертикальном или наклонном расположении пневмоцилиндра. В расчетной формуле принято что требуемое усилие зажима создается при давлении 09pm чем обеспечивается некоторый его запас.
Следовательно диаметр пневмоцилиндра бункерного загрузочного устройства следует принять равным 63 мм.
d = (025 . . . 032) D;
d = 032 × 63 = 2016 мм
и округляют до ближайшего значения взятого из ряда 10 12 16 25 32 40 50 63 80 90 мм. Поэтому принимаем диаметр штока равным 25мм.
Требуемое усилие на штоке обеспечено.
Скорость перемещения штока регулируется дросселями поз. 3 (см. рис. 11).
Служит для подачи детали из лотка загрузочного устройства в зону обработки. Автооператор состоит из кронштейна на котором крепятся:
направляющая для перемещения штока со стаканом;
шток перемещается пневмоцилиндром 63;
корпус нa котором крепится направляющая для перемещения корпуса руки.
Шток перемещаясь поворачивается на 900 по байонетному пазу и подает деталь на ось центров.
К корпусу руки крепится губка для западания в нее детали из лотка загрузочного устройства. Крайние положения корпуса руки и штока фиксируются конечными выключателями смонтированными на направляющих.
Рис. 12. Автооператор
5.1. Расчет пневмоцилиндра
Основные параметры поршневого цилиндра с односторонним штоком (см. рис. 12) связаны между собой следующими соотношениями [32]:
где F1 F2 – площадь поршневой и штоковой полости мм2; р1 р2 – давление в поршневой и штоковой полости кгссм2; Р1 Р2 – полезная нагрузка Н; V1 V2 – скорость перемещения штока ммин; Q1 Q2 – расход воздуха лмин; kтр = 09-098 – коэффициент учитывающий потери на трение в цилиндре.
где Р2 – технологическая (полезная) нагрузка;m – масса всех подвижных элементов связанных с поршнем; g – ускорение свободного падения; рm – подводимое абсолютное давление сжатого воздуха;
Вес подвижных частей ±mg учитывают при вертикальном или наклонном расположении пневмоцилиндра. В расчетной формуле принято что требуемое усилие зажима создается при давлении 09рm чем обеспечивается некоторый его запас. Т.к. пневмоцилиндр расположен горизонтально то сила ±mg в формуле равна нулю.
и округляют до ближайшего значения взятого из ряда 10 12 16 25 32 40 50 63 80 90 мм. Поэтому принимаем диаметр штока равным 25мм.
Найдем скорость перемещения штока:
V = S : t = 016 : (03 : 60) = 32ммин
где S – ход поршня мм; t – время срабатывания с.
Зная скорость перемещения штока найдем расход воздуха:
Пиноль задней бабки перемещается от механизма шаговой подачи который содержит силовые цилиндры с полым поршнем установленными в корпусе телескопически.
Основные параметры поршневого цилиндра с односторонним штоком (см. рис. 13) связаны между собой следующими соотношениями:
где kтр = 09-098 – коэффициент учитывающий потери на трение в цилиндре;
Рис. 13. Основные параметры пневмоцилиндра
6.1. Расчет пневмоцилиндров
Диаметр пневмоцилиндров определяется по формуле взятой из [9]:
Поскольку конструкция задней бабки нестандартная то диаметры цилиндров не следует округлять до ближайшего из нормального ряда диаметров цилиндров.
Параметры цилиндров: D1 = 60 мм – диаметр первого цилиндра задней бабки; D2 = 75 мм –диаметр второго цилиндра задней бабки; d = 20 мм – диаметр штока; t = 03 с – время хода второго цилиндра задней бабки; p11 = p12 = 4-6 кгсм2 – давление воздуха в поршневой области первого и второго цилиндра; p21 = p22 = 15 кгсм2 – давление воздуха в штоковой области; S1 = 35мм – ход поршня; S2 = 85 мм – ход цилиндра.
Требуемое усилие Р1 = 800Н на штоке задней бабки обеспечено.
V = S : t = 085 : (03 : 60) = 17 ммин.
7. Привод поперечной подачи
(см. чертежи «Привод поперечной подачи»)
Служит для перемещения каретки с резцедержателем в поперечном направлении. Состоит из каретки поперечного суппорта и резцедержателя станка 1И611П перемещающихся от гидроцилиндра смонтированного сзади станка. Холостой ход каретки 20 мм и рабочий ход 10 мм обеспечиваются дросселем с регулятором обратным клапаном и золотником ПГ-55-62 смонтированным на одном кронштейне с гидроцилиндром сзади станка.
Давление в гидросистеме 4 6 кгсм2. Включение и отключение дросселя обеспечивается кулачком закрепленным на каретке поперечного суппорта. Исходное и конечное положение каретки фиксируются конечными выключателями смонтированными на станине станка.
7.1. Выбор гидроцилиндра
Для автоматизации привода поперечной подачи нельзя использовать пневмоцилиндр поскольку он:
не может обеспечить заданный закон движения выходного звена;
имеет нестабильность скорости движения выходного звена.
В связи с этим следует использовать гидравлику.
При обработке валика стеклоподъемника 4086104036 согласно назначенным режимам сила подачи Рх = 350 Н однако следует предусматреть другие варианты обработки при которых эта сила намного больше.
В соответствии рекомендациям [32] в качестве привода поперечной подачи выбираем гидроцилиндр с двусторонним штоком по ОСТ 2 Г22-2-73.
Диаметр цилиндра: 80 мм
Диаметр штока: 32 мм
Номинальный расход: 50 лмин
Максимальное (теоретическое) усилие на штоке
без учета сил трения: 564 кН
Максимальное давление холостого хода: 047 МПа
Утечка масла через уплотнения поршня
при номинальном давлении: 4 см3мин
ТЕХНОЛОГИЧЕСКАЯ ЧАСТЬ
1. Расчет режимов резания
В условиях массового производства в качестве режущего инструмента
следует выбрать резцы с твердосплавными пластинами (по рекомендациям данным в [36]).
При обработке алюминиевого сплава ЦА4М1 в качестве инструментального материала выбираем ВК-8.
Рабочая подача S = 016 ммоб. ([36] см. табл. 15).
Глубина резания t = 35мм.
Ширина срезаемого слоя резцом ЦТ2112-4010 a = 65мм.
Ширина срезаемого слоя резцом ЦТ2112-4029 а = 15мм.
Определяем скорость резания [16 стр. 283]:
где S – подача ммоб. определяется из табл. 15 [36]; Т – период стойкости инструмента мин.; Кv – произведение коэффициентов учитывающих влияние материала заготовки состояния поверхности материла инструмента. Определяется из табл. 1-8 [36]. Значение коэффициента cv показателей степени y и m приведены в табл. 17 [36].
Частота вращения шпинделя вычисляется по формуле:
где v – скорость резания ммин; d – обрабатываемый диаметр заготовки мм.
Определяем действительную скорость резания:
Рассчитываем силу резания [16 стр. 282]:
где – коэффициент учитывающий влияние качества обрабатываемого материала на силовые зависимости.
Крутящий момент на шпинделе [16 стр. 290]:
Мощность резания [16 стр. 290]:
аннотация.doc
Проект содержит 14 листов формата А1 142 листов записки и технологический процесс на 5 операций.
Проект посвящен разработке токарного автомата с одновременной модернизацией станка 1И611П.
За счет применения новых автоматических устройств и приводов станка повышается производительность обработки деталей до 400 – 600 дет.час.
Модернизирована задняя бабка с целью автоматизации перемещения пиноли.
Разработан цанговый зажим который служит для автоматического зажима детали и удаления ее после обработки посредством выталкивающей пружины.
Разработаны автоматические бункерно-загрузочное устройство и автооператор которые обеспечивают нужную ориентацию заготовки в пространстве и передачу её в зону обработки.
Спроектирован автоматизированный привод поперечной подачи работа которого осуществляется посредством гидравлики.
Выполнены все необходимые расчеты предусмотренные методическими указаниями по выполнению дипломного проекта.
В графической части проекта представлены:
механизированная задняя бабка с автоматическим перемещением пиноли;
кинематическая схема;
гидропневматическая схема;
электрическая схема;
рабочий чертеж детали 408-6104036-10;
технико-экономические показатели;
циклограмма работы станка;
привод поперечной подачи;
бункерно-загрузочное устройство.
Глава2.doc
Токарный автомат представляет собой модернизированный станок 1И611П (см. рис.6) и предназначен для обработки деталей типа валик стеклоподъемника 408-6104036-10 (см. раб. чертеж детали).
Рис. 6. Токарно-винторезный станок 1И611П
Автомат состоит из станка 1И611П и из следующих модернизированных и вновь созданных узлов (см. таблицу 2 и рис.7).
Привод поперечной подачи
Бункерное загрузочное
Гидробак поперечной подачи
Рис. 7. Токарный автомат для обработки деталей типа «валик стеклоподъемника».
1.2. Применение пневмоприводов в станкостроении
Пневматические приводы широко используются для автоматизации и механизации производственных процессов в различных отраслях промышленности. Установившаяся область их применения – машиностроение в том числе станкостроение.
Между пневматическими и гидравлическими объемными приводами существуют глубокие аналогии (по принципу действия по конструкции и функциям их элементов). Принципиально отличаются только рабочие среды – воздух обладающий большой сжимаемостью и малой вязкостью и вязкая практически несжимаемая жидкость. Различие рабочих сред существенно сказывается на динамических характеристиках приводов прежде всего на характеристиках исполнительных устройств. В отличие от гидравлических аналогов пневмодвигатели с возвратно-поступательным движением выходного звена являются типично дискретными устройствами. Движение поршня пневмоцилиндра характеризуется малой продолжительностью высокими и нестабильными скоростями. Поршень имеет только два фиксированных (крайних) положения определяемых жесткими упорами.
Точно остановить его в каком-либо промежуточном положении невозможно. Например при прекращении подачи воздуха или запирании обеих полостей пневмоцилиндра движущийся поршень остановится не мгновенно из-за упругости рабочей среды и инерционности подвижных масс.
Дискретным характером работы пневмодвигателей с возвратно-поступательным движением выходного звена обусловлено их применение для механизации и автоматизации таких технологических операций которые не требуют строго заданного закона движения и допускают нестабильность скорости подвижных элементов. Применительно к металлорежущим станкам это операции зажима поворота фиксации кантования транспортировки загрузки-выгрузки ориентации установки переключения. Несмотря на почти релейный характер срабатывания пневмоприводов реализующих такие операции рациональным выбором их конструктивных размеров и применением регулирующих устройств можно активно воздействовать на их динамику добиваясь требуемых эксплуатационных характеристик. Например дроссельным регулированием можно в широком диапазоне изменять время срабатывания действующие скорости и ускорения стабилизировать скорость движения рабочих органов. Применение тормозных устройств позволяет при высоких скоростях движения на основном участке хода ограничить или исключить удар в конце хода при остановке на жестком упоре. Все это расширяет функциональные возможности и область применения пневматических приводов в металлорежущих станках и автоматических станочных линиях.
В настоящее время свыше 50 % используемых в промышленности манипуляторов и роботов первых поколений пневматические. Разработка конструкций пневматических позиционеров шаговых и цифровых приводов дает основание рассчитывать на конкурентоспособность пневматических приводов с электро- и гидроприводами и при создании роботов новых поколений.
1.3. Достоинства и недостатки пневматических приводов
Основные достоинства пневматических приводов следующие:
возможность питания от централизованной сети при относительной легкости транспортировки энергии сжатого воздуха на значительные расстояния;
высокие скорости срабатывания исполнительных устройств (пневмодвигателей и др.);
пожаро- и взрывобезопасность обеспечиваемые без применения защитных средств;
возможность работы в широком диапазоне рабочих температур в условиях запыленности вибраций радиации;
простота конструкции и высокая надежность пневматических устройств;
простота ухода и обслуживания;
относительно низкая стоимость и быстрая окупаемость.
К недостаткам пневматических приводов относятся:
сравнительно высокая стоимость энергии сжатого воздуха что сказывается при непрерывном потреблении сжатого воздуха и больших его расходах;
невозможность без применения специальных устройств или конструкций обеспечить заданный закон движения выходного звена пневмодвигателя;
нестабильность скорости движения выходного звена пневмодвигателя особенно при переменных нагрузках;
плохие условия смазки трущихся поверхностей подвижных элементов пневматических устройств;
низкий КПД пневматических приводов;
необходимость защиты элементов привода от коррозии.
2. Устройство станка
Задняя бабка установлена на направляющих станины станка 1И611П. Она состоит из корпуса с укрепленными на нем конечными выключателями пиноли перемещающейся от механизма шаговой подачи который содержит силовые цилиндры с полым поршнем установленными в корпусе телескопически. Такая конструкция позволяет четко перемещать упор поз. 5 за два хода: первый ход поршня поз. 14 на 55 мм и второй ход цилиндра поз. 2 на 85 мм. Задняя бабка служит для подачи детали из автоопреатора в цанговый зажим для обработки.
Зажим цанговый установлен в шпинделе станка 1И611П. Он состоит из цанги тяги и силового привода. Зажим цанговый снабжен пружинным выталкивателем и реле давления рассчитанным на определенное усилие зажима детали. Зажим цанговый служит для зажима детали и удаления ее после обработки посредством выталкивающей пружины после чего деталь попадает в скиз и падает в тару.
2.3. Привод поперечной подачи
Привод поперечной подачи служит для перемещения каретки с резцедержателем в поперечном направлении. Привод состоит из каретки поперечного суппорта и резцедержателя станка 1И611П перемещающихся от гидроцилиндра смонтированного сзади станка. Холостой ход каретки 20 мм и рабочий ход 10 мм обеспечиваются дросселем с регулятором обратным клапаном и золотником ПГ-55-62 смонтированным на одном кронштейне с гидроцилиндром сзади станка.
Давление в гидросистеме 4 6 кгсм2. Включение и отключение дросселя обеспечиваются кулачком закрепленным на каретке поперечного суппорта. Исходное и конечное положение каретки фиксируются конечными выключателями смонтированными на станине станка.
Служит для подачи детали из лотка загрузочного устройства в зону обработки. Автооператор состоит из кронштейна на котором крепятся:
направляющая для перемещения штока со стаканом;
шток перемещается пневмоцилиндром 60 × 60;
корпус на котором крепится направляющая для перемещения корпуса руки.
Корпус руки перемещается от пневмоцилиндра 60 × 100.
Шток перемещаясь поворачивается на 60° по байонетному пазу и подает деталь на ось центров.
К корпусу руки крепится губка для западания в нее детали из лотка загрузочного устройства. Крайние положения корпуса руки и штока фиксируются конечными выключателями смонтированными на направляющих.
2.5. Бункерное загрузочное устройство
Бункерное загрузочное устройство служит для захвата из бункера заготовок и ориентации их в положение обработки. Состоит из бункера качающегося сектора приводимого в движение цилиндром и лотка ориентирующего детали.
Емкость бункера – 150деталей 408-6104036-10. Монтируются на крышке передней бабки станка 1И611П. Работает бункерное загрузочное устройство полностью от пневматики. Работой качающегося сектора управляют два пневмоклапана В76-21 поз. 54. Для пуска устройства служит кран управления В71-23.
2.6. Гидробак поперечной подачи
Гидробак поперечной подачи служит в качестве емкости масла под давлением 4 6 кгсм2 в гидроцилиндр. Состоит из двух форкамер в которые подается сжатый воздух под давлением 4 6 кгсм2. Масло из форкамеры к золотнику с обратным клапаном ПГ-55-62 поступает через дроссель с регулятором Г-55-25 смонтированным на боковой стенке гидробака. Гидробак монтируется на кронштейне и крепится на станине сзади станка 1И611П.
(см. чертеж «схема гидропневмокинематическая»)
Станок имеет наладочный и автоматичиский циклы работ. В наладочном режиме производится проверка работы каждого узла автомата. Пульт управления автоматом смонтирован на дверке электрошкафа. После подготовки автомата к работе включить кран управления бункерного загрузочного устройства. Начинает работать пневмоцилиндр Ц2 в автоматическом цикле. Сектор загрузочного устройства подает детали в лоток где деталь ориентируется в положение обработки. После заполнения лотка деталями нажать на кнопку «автомат» на пульте управления.
Срабатывает пневмоцилиндр Ц4 подающей руки автооператора и подает деталь на ось центров автомата. В конце хода руки срабатывает конечный выключатель SQ1 который дает команду на золотник Р6 (У2) телескопического пневмоцилиндра задней бабки Ц6 происходит выдвижение пиноли задней бабки на 85 мм которая своим упором выталкивает деталь из подающей руки в цанговый зажим шпинделя станка. В конце хода пиноли срабатывает конечный выключатель SQ2 подающий команду на золотник Р4 (У1) – пневмоцилиндр Ц4 переключается на обратный ход подающая рука автооператора возвращается в исходное положение. После 35 мм хода назад подающей руки срабатывает конечный выключатель SQ3 дающий команду на золотник Р7 (У3) телескопического цилиндра задней бабки Ц7 – происходит окончательная подача детали в цангу до упора.
В конце хода пиноли задней бабки срабатывает конечный выключатель SQ4 дающий команду на золотник Р1 (У4); срабатывает пневмоцидиндр Ц1 цангового зажима детали. При достижении усилия зажима Рз = 180 кг (расчетное) реле давления дает команду на золотники Р6 (У2) и происходит переключение телескопических цилиндров Ц6 и Ц7 пиноль задней бабки возвращается в исходное положение. Одновременно реле давления дает команду на электромагнитную муфту включающую вращение шпинделя и на золотник РЗ(У5) подающий сжатый воздух в гидробак.
Масло из гидробака поступает в гидроцилиндр Ц3 перемещая каретку с резцедержателем. Холостой ход каретки и рабочий ход обеспечивается дросселем с регулятором обратным клапаном и золотником ПГ-55-62 управляемым кулачком прикрепленным на каретке станка. В конце хода каретки т.е. после окончания обработки детали срабатывает конечный выключатель SQ5. Происходит быстрый отвод суппорта поперечной подачи в конце хода которого включается конечный выключатель SQ6.
Далее цикл повторяется – срабатывает пневмоцилиндр Ц4 подающей руки автооператора и подает деталь на ось центров.
3.1. Электрооборудование
На станке установлены два трехфазных асинхронных электродвигателя:
) Электродвигатель вращения шпинделя М1.
) Электродвигатель смазки М2.
Электродвигатели и аппаратура рассчитаны на включение в сеть напряжением 380 В и частотой 50 Гц. Напряжение в цепи управления 110 В. Напряжение в цепи сигнализации 55 В. Подключение электрической части станка к сети осуществляется автоматическим выключателем АСТ-3. Вся электроаппаратура смонтирована в отдельно стоящем шкафу. Станок имеет автоматический и наладочный циклы работ. При нажатии кнопки S1 на пульте управления включается автоматическая работа станка и электродвигатель смазки М2.
3.2. Последовательность работы автоматического цикла.
(см. чертеж «схема электрическая принципиальная»).
Подается питание автоматическим выключателем Q. Загорается лампа «Сеть». Далее нажимаем кнопку «Пуск автомат» S4 на пульте управления
и катушка реле К11 становится на самоблокировку (цепь 9-16). Подается питание на выпрямительный мост командоаппарата. Начинает вращаться двигатель М4 (цепь 15-4). Нажимаем кнопку «Пуск двигателя» S2 получает питание электромагнитный пускатель К10 (цепь 9-13).
Бесконтактный выключатель 1SQ включает катушку К1 контакт которой замыкает цепь воздухораспределителя механизма подачи детали (цепь 15-4). Затем бесконтактный выключатель 2SQ включает реле катушки К2 контакт которой замыкает цепь 15-29-4. Происходит выдвижение 1-го цилиндра задней бабки (золотник Y2) и одновременно с этим срабатывает бесконтактный выключатель 3SQ который включает реле К3. Включается 2-ой цилиндр задней бабки (цепь 15-29-31-4). Происходит выдвижение 2-го цилиндра задней бабки (золотник Y3). После чего включается бесконтактный выключатель 4SQ который включает реле К4 и происходит включение зажима Y4 (цепь 15-33-4). Происходит зажим цанги. 1-ый и 2-ой цилиндр задней бабки возвращаются в исходное положение. Затем включается бесконтактный выключатель 5SQ который включает катушку реле К5 которая в свою очередь включает электромагнит Y5 (цепь 15-27- 4).
Происходит обработка детали. После обработки детали происходит разжим цанги. Под действием выталкивающей пружины деталь удаляется из зоны обработки через склиз. Командоаппарат становится в исходное положение. Когда суппорт возвращается в исходное положение SQ3 включает К8 и цепь 15-24-25-4 получает питание. Срабатывает механизм подачи детали. Цикл повторяется.
Имеется кнопка S3 «Исходное положение командоаппарата» которая позволяет установить командоаппарат в исходное положение в случае сбоя автоматического цикла.
Предусмотрен тормоз двигателя М4 который включается когда командоаппарат становится в исходное положение.
На двигатели М4 имеется колодка с 4-мя выводами обмотки которые включаются в цепь согласно схеме.
Защита электрооборудования от коротких замыканий обеспечивается плавкими предохранителями F1 F5 и автоматическим выключателем Q.
Защита электродвигателей от перегрузок обеспечивается тепловыми реле FF1 FF2.
3.4. Описание кинематической схемы.
(см. чертеж – «Кинематическая схема»).
Главное движение – вращение шпинеделя с частотой nшп – от асинхронного двигателя М1 (N = 3 кВт n = 1430 об.мин.) с помощью восьмиступенчатого редуктора и клиноременной передачи 13-14 передается на шпиндель VII при включенной зубчатой муфте 16 с внутренним зацеплением. При этом шпиндель может иметь восемь частот вращения от 400 обмин до 2000 обмин. Это «верхний поддиапозон» регулирования скорости вращения шпинделя.
Низкие частоты вращения шпинделя от 50 обмин до 250 обмин сообщаются шпинделю через «перебор» состоящий из двух передач 15-19 и 20-18 i переб. = (30:80) х (18:72) = 18.
Таким образом шпиндель может иметь 16 различных частот вращения однако в рамках курсового проекта требуется обеспечить лишь одну частоту вращения n = 500 обмин.
Данная частота вращения обеспечивается следующим образом:
Вращение с электродвигателя передается на вал 1 с помощью зубчатой муфты далее через зубчатую пару 2-5 (27:39) на вал 2. С вала 2 через зубчатую пару 6-8 (26:44) на вал 3. С вала 3 на вал 4 вращение передается зубчатой парой 10-11 (35:45). Далее через клиноременную передачу 13-14 (160:125) на вал 5. Вал 5 передает вращение на шпиндель с помощью зубчатой муфты. «Перебор» в работе не участвует.
График частот вращения приведен на чертеже «Кинематическая схема».
Введение+Глава1.doc
РОССИЙСКОЙ ФЕДЕРАЦИИ
ИЖЕВСКИЙ ГОСУДАРСТВЕННЫЙ ТЕХНИЧЕСКИЙ УНИВЕРСИТЕТ
Кафедра «Автомобили и металлообрабатывающее оборудование»
Зав. кафедрой к.т.н. доцент
РАСЧЕТНО-ПОЯСНИТЕЛЬНАЯ ЗАПИСКА К
ТЕМА: «Спроектировать токарный автомат на базе станка
модели 1И611П для обработки детали типа валик
стеклоподъемника легкового автомобиля ИЖ-2126».
Дипломник Салимов Н.В.
Руководитель дипломного проекта ст. преподаватель
Консультант по организационно-
экономической части
Консультант по экологии
безопасности жизнедеятельности к.т.н. доц. Глухов Ю.Г.
Представитель контроля выполнения
норм ЕСТД и ЕСКД к.т.н. доц. Иванов В.Ф.
Представитель технологического
контроля к.т.н. доц. Шитова Т.В.
ОБЗОР И АНАЛИЗ ЛИТЕРАТУРНЫХ ИСТОЧНИКОВ ..7
1. Обзор существующих токарных автоматов 8
1.1. Одношпиндельные токарные автоматы 9
1.2. Автоматы продольного точения ..10
2. Патентный поиск .. ..14
3. Перевод иностранного текста по теме проекта 25
4. Выводы по обзору 32
1. Назначение и область применения . 34
1.1. Состав станка .35
1.2. Применение пневмоприводов в станкостроении и
1.3. Достоинства и недостатки пневматических приводов ..37
2. Устройство станка .38
2.1. Задняя бабка 38
2.2. Зажим цанговый 39
2.3. Привод поперечной подачи ..39
2.4. Автооператор .39
2.5. Бункерное загрузочное устройство .40
2.6. Гидробак поперечной подачи ..40
3. Работа станка .41
3.1. Электрооборудование 42
3.2. Последовательность работы автоматического цикла 42
3.4. Описание кинематической схемы 44
КОНСТРУКТОРСКАЯ ЧАСТЬ .46
1. Выбор электродвигателя 47
2. Прочностной расчет коробки скоростей 48
2.1. Расчет вала .48
2.2. Расчет цилиндрических передач коробки скоростей 57
2.3. Расчет шпоночного соединения 63
3. 3ажим цанговый .63
3.1. Расчет сил зажима .65
3.2. Расчет пневмоцилиндра 66
4. Бункерное загрузочное устройство .68
4.1. Расчет бункерного загрузочного приспособления .70
4.2. Сыпучесть изделий 72
4.3. Давление изделий на стенки бункера ..73
4.4. Плотность насыпки изделий и их насыпной вес 74
4.5. Расчет пневмоцилиндра 75
5. Автооператор ..78
5.1. Расчет пневмоцилиндра 78
6.1. Расчет пневмоцилиндров ..83
7. Привод поперечной подачи ..85
7.1. Выбор гидроцилиндра ..85
ТЕХНОЛОГИЧЕСКАЯ ЧАСТЬ .87
1. Расчет режимов резания 88
ЭКОНОМИЧЕСКАЯ ЧАСТЬ .89
2. Выбор базы для сравнения 90
3. Определение нормы времени работы и годового объема
4. Расчет сопутствующих капитальных вложений 94
5. Расчет годовых эксплуатационных издержек .97
СОДЕРЖАНИЕ ГРАФИЧЕСКОЙ ЧАСТИ ДИПЛОМНОГО
ЗНАЧЕНИЕ И РАЗВИТИЕ АВТОМАТИЗАЦИИ СТАНКОВ
При автоматизации станка производительность труда рабочего возрастает вследствие увеличения производительности станка. Рабочий освобождается от непосредственного участия в процессе обработки детали и появляется возможность многостаночного обслуживания технологического процесса.
Автоматизация облегчает физический труд рабочего освобождает его от однообразных повторяющихся движений от монотонных нервных и физических напряжений. Вместе с тем автоматизация повышает технический уровень обслуживания станка при его подготовке к производству – наладке и во время его эксплуатации. Таким образом автоматизация облегчает физический труд рабочего за счет увеличения доли умственного труда и создает предпосылки для постепенного сглаживания различий между физическим и умственным трудом.
Благодаря повышению производительности станков при автоматизации уменьшается необходимое количество единиц оборудования с единицы площади цеха снимается больше продукции. Автоматизация вносит ритмичность в процесс обработки и способствует стабильности качества заготовок и деталей на всех этапах их обработки.
ОБЗОР И АНАЛИЗ ЛИТЕРАТУРНЫХ ИСТОЧНИКОВ
1. Обзор существующих токарных автоматов
Значительную долю в парке металлорежущего оборудования составляет большая группа токарных станков. Она включает девять типов станков различающихся по назначению области применения технологическим возможностям конструктивной компоновке степени автоматизации и некоторым другим признакам. Внутри каждого типа станки различаются по своим характерным размерам и конструкции.
В машиностроении токарные автоматы получили наибольшее распространение. Автоматом называется станок в котором автоматизированы все основные и вспомогательные движения необходимые для выполнения технологического цикла обработки заготовки а также загрузка заготовки и выгрузка обработанной детали. Обслуживание автомата сводится к периодической подаче материала-заготовки или прутка и контролю обработанных деталей.
Полуавтоматом называется станок в котором автоматизированы все основные и вспомогательные движения составляющие цикл обработки одной заготовки. По окончании цикла полуавтомат останавливается; для повторения никла необходимо снять готовую деталь поставить и закрепить новую заготовку и пустить станок.
Токарные автоматы предназначены для изготовления деталей сложной конфигурации путем обработки заготовки несколькими (многими) инструментами.
Автоматизация цикла работы современных станков осуществляется на основе использования средств механики гидравлики электротехники и электроники пневматики или на комбинированной базе.
Станки с механической базой автоматизации производительны и надежны в эксплуатации. Однако на переналадку таких автоматов затрачивается много времени. Поэтому автоматы с механической базой автоматизации используют как правило в условиях массового производства.
Особое место занимают станки с числовым (цифровым) программным управлением циклом. Такие станки могут быть эффективно использованы для изготовления деталей мелких и средних серий.
Токарные автоматы подразделяют по различным признакам:
а) назначению – на универсальные и специализированные;
б) виду заготовки – на прутковые и патронные;
в) количеству шпинделей – на одно- и многошпиндельные;
г) расположению шпинделей – на горизонтальные и вертикальные.
Более подробно проведем обзор токарных одношпиндельных автоматов.
1.1. Одношпиндельные токарные автоматы
Наиболее распространенными типами одношпиндельных токарных автоматов являются: фасонно-отрезные автоматы автоматы фасонно-продольного точения часто называемые также автоматами продольного точения н тока рно-револьверные автоматы.
Фасонно-отрезные автоматы предназначаются для изготовления из прутка (или бунта) коротких деталей малого диаметра и простой формы в условиях крупносерийного и массового производства. Схема работы такого автомата показана на рис. 1.
Рис. 1. Схема работы фасонно-отрезного автомата
Материал закрепляется во вращающемся шпинделе 1 с помощью цангового патрона. Станок имеет два-четыре суппорта 2 перемещающихся только в поперечном направлении и несущих фасонные и отрезные резцы. Для получения детали заданной длины станок снабжен подвижным упором 3 автоматически устанавливающимся по оси шпинделя после окончания цикла. Материал подается с помощью механизма подачи до соприкосновения с упором.
Станок относится к автоматам первой группы.
Главным движением (v) в этих станках является вращение шпинделя движения подачи (s) – перемещения поперечных суппортов.
Некоторые модели фасонно-отрезных автоматов имеют продольный суппорт перемещающийся вдоль оси шпинделя позволяющий производить сверление отверстий. Некоторые характерные детали обрабатываемые на фасонно-отрезных автоматах показаны на рис. 2.
Рис. 2. Типовые детали изготовляемые на фасонно-отрезных автоматах
1.2. Автоматы продольного точения
Автоматы продольного точения предназначены для изготовления длинных деталей малого диаметра из прутка или бунта в условиях массового производства. Эти автоматы используются главным образом на предприятиях точной индустрии например в часовой промышленности приборостроении радиотехнической промышленности и т. п.
Высокие требования к точности и чистоте поверхности обрабатываемых деталей предъявляемые точной индустрией обусловили ряд конструктивных особенностей автоматов продольного точения.
Рис. 3. Схема работы автомата фасонно-продольного точения
На рис. 3 дана схема работы автомата. Заготовка закрепляется во вращающемся шпинделе 1 при помощи цангового патрона. Шпиндельная бабка 2 перемещается по направляющим станины сообщая тем самым заготовке движение подачи (s1) относительно неподвижного резца 8 закрепленного в суппорте 9. Суппорт сообщает резцу установочные перемещения при переходе на обработку ступени другого диаметра и движение поперечной подачи (s2) при отрезке и фасонном обтачивании. Станок имеет два-три вертикальных суппорта и суппорт балансирного типа 4 несущий два резца и совершающий качательное движение вокруг оси 5. Расположение суппортов показано на рис. 4.
Обработка центрального отверстия – сверление зенкерование нарезание резьбы метчиками и плашками и т. д: – производится с помощью специальных приспособлений 7 устанавливаемых на левой стороне станины.
Шпиндели приспособлений часто имеют независимое поступательное (s3) и вращательное движения. Для уменьшения прогиба и вибрации прутка под действием сил резания передний конец его пропускается через калиброванное отверстие люнета 6 закрепленного на суппортной стойке 3 установленной на станине. Такая компоновка обеспечивает высокопроизводительную обработку деталей значительной длины без опасения возникновения значительного прогиба и вибраций. При этом достигается высокая точность и чистота обработанных поверхностей.
Рис. 4. Расположение суппортов в автоматах фасонно-продольного точения: а) – суппорт балансирного типа; б) – вертикальные суппорты.
Следует отметить что к прутковым заготовкам обрабатываемым на этих автоматах предъявляются повышенные требования по точности.
Главным движением (v) в этих автоматах является вращение шпинделя. При цилиндрическом обтачивании движением продольной подачи s1 является перемещение шпиндельной бабки при отрезке – поперечная подача s2 осуществляемая перемещением вертикальных суппортов или поворотом суппорта балансирного типа. При фасонной обработке подача получается как геометрическая сумма продольной и поперечной подачи (s1 и s2).
При сверлении зенкеровании развертывании продольная подача представляет собой алгебраическую сумму продольных подач шпинделя станка s1 и шпинделя приспособления s3.
Автоматы продольного точения имеют один распределительный вал управляющий рабочими и холостыми движениями (автоматы первой группы).
Характерные детали обрабатываемые на таких автоматах показаны на рис. 5.
Рис. 5. Примеры типовых деталей изготовляемых на автоматах фасонно-продольного точения
Основным размером автоматов продольного точения является наибольший диаметр обрабатываемого прутка.
В табл. 1 приведены основные технические параметры современных отечественных автоматов продольного точения.
Наибольший диаметр обрабатываемого прутка мм
Скорости главного движения обмин
Мощность приводного электродвигателя кВт
* Станок имеет револьверную головку.
Патентный поиск отечественной и иностранной литературы проводится по теме: Создание задней бабки с автоматическим перемещением пиноли для токарного автомата с применением пневматики. (см. приложение 1).
96116 MACHINE WITH TA1LSTOCK
Henry W. Spretecr Shaker Heights. Ohio. assignor U The Waraer Л Smey Coopuy Ckvel – d. Ohio FB*d Nov. 71972. S*r. No. 304.408 Int. CL B23b 2J00. 7104 U.S. 0.82-2 R 17Chbn*
An improved machine tool includes a taibtock having a center assembly which u movable between operating and retracted pout ions by a piston and cylinder auembly. When the center auembly is in the operating pout ion a main axis of the center aoembly is aligned with the axis of rotation of a workpiece. In the retracted position the center assembly is ofhtt to one side of the work piece.
When the center assembly is in the operating position a tailstock motor is activated to press the center assembly against the outer end of the work-piece to thereby support the workpiece in a known manner. A control system coordinates movement of the center assembly with movement of a turret to avoid interference between the taibtock and tools mounted on the turret.
МКИB23b 2300. 704 США ПАТЕНТ № 3796II6
НКИ82-2R. Публикация 1974 г. 12 марта. Том 920 № 2
УДК62I.91I-229 (088.8)
Усовершенствованный металлорежущий станок содержит заднюю бабку в которой выдвижение центра в рабочее положение и отведение его назад осуществляется при помощи силового цилиндра. Когда центр находится в рабочем выдвинутом положении его ось совпадает с осью вращения заготовки. В отведенном положении центр смещен относительно заготовки. Когда центр находится в рабочем положении включается двигатель задней бабки осуществляющий поджим центра задней бабки к наружному торцу заготовки обеспечивая ее закрепление. В станке предусмотрена система управления координирующая перемещение центра задней бабки и револьверной головки. Такая система позволяет избегать столкновения задней бабки с инструментом установленным в револьверной головке.
Переводчик Айзеншток Г.И.
Редактор Щукина Т.М.
(51)МКИ В 23 В 2300 1902
(11) заявка № 59-29364
Публик.№ 840720 М 2-735 (22) (21)
Заявлено 75. 01. 23 57-161609 (62) 50-9376 (71)
Заявитель Индексверке КГ Гаи унд Тескки (33)(32)(31)
Приоритет ФРГ 74. 03. 06. Р 2410540.6
(54) ЗАДНЯЯ БАБКА ТОКАРНОГО СТАНКА
Переводчик Е.П. Комарова
H30(AuZ4)V 15800. 20.1.59-24.5.67 49. 2601 – В 23В
Reitstock fiir Werkzeugniaschinen
VEB Zahnschneidcmaschincnfabrik Modul Karl-Marx-Stadt Emsiedler Str.
Als Erfinder benannt:
Erhard Vcttcnnann Meinersdorf (Erzgeb.)
Reitstock fiir Werkzeugniaschinen mit hy-draulisch oder pneumatisch belatigter Pinole dadurch gekennzeichnet daB der mit dem Reitstockgehause (1) losbar verbundene Tragkorper (2) eine in Langsrichtung durch-gehende Bohmng aufweist in der ein fest-stehender Zylinder(4) mit beweglichem Kolben (12) angeordnet ist dessen Kolbenstange test mit der Pinole (15) verbunden ist daB die Pinole (15) von hydraulisch betatiglen Spannelementen (23 24) umgeben ist. deren Dnickraume mit dem auf der Riickseite des Kolbens (12) befindlichen Dnickraum (9) das Zylinders (4) abschlieBbar in VerbindunR stehen und daB in der Pinole (15) Oder an einem mit dieser fe&lverbundenen Teil ein in Abhangigkeit vom hydraulischeo Druck und einer dagegen wirkcnden Feder (19) betatig-les Keilgesperre (18 22) angeordnet ist.
УДК 621-229.332(088.8)
ФРГ заявка №1241230 КЛ. ФРГ 49а2601
Публикация 1967 № 21(24.5)
ЗАДНЯЯ БАБКА ДЛЯ МЕТАЛЛОРЕЖУЩЕГО СТАНКА
Задняя бабка для металлорежущего станка с гидравлически или пневматически перемещающейся пинолью отличается тем что несущая часть (2) разъемно соединенная с корпусом задней бабки (I) имеет отверстие в котором расположен неподвижный цилиндр (4) с подвижным поршнем (12). Шток поршня жестко соединен с пинолью (15) таким образом что пиноль (15) окружена гидравлически действующими зажимными элементами(23 24) полости нагнетания которых соединены с рабочей полостью (9) цилиндра (4) расположенной с задней стороны поршня (12). В пиноли (15) или на элементе неподвижно соединенном с ней расположен клиновой стопорный механизм (1822) действующий в зависимости от гидравлического давления против пружины (19).
Переводчик Вильнер Г.С.
Научный редактор Янина Т.А.
фамилия имя отчество
На проведение патентного поиска по теме:
Создание бабки с автоматическим перемещением пиноли для токарного .
способ или объект проектирования
автомата с применением пневматики .
курсовое или дипломное проектирование
Начало поиска10.03.03 г.
предъявление справки о поиске13.03.03 г.
РЕГЛАМЕНТ ПАТЕНТНОГО ПОИСКА
стадия:Дипломное проектирование .
Предмет поиска (тема объект его составные части)
Цель поиска информации
Страна поиска начиная с СССР
Классификационные индексы
Ретроспективность (глубина поиска)
Наименование источников по которым проводится поиск
Гиросистема осевого зажима детали
Задняя бабка металлорежущего станка
Задняя бабка токарного станка
Задняя бабка тяжелого токарного станка
Гидромеханический привод пиноли
Найти решение конструкций узлов и механизмов для использования при разработке токарного автомата.
Бюллетень «Открытие изобретения» 1980-1986 г.г.
Бюллетень регистрации НИР и ОКР 1980-1986 г.г.
Задание на проведение патентного поиска
Начало поиска 10.03.02 окончание поиска 13.03.02
Поиск проведен по следующим материалам
Предмет поиска (объект и его составные части)
По фонду какой организации проведен поиск
Источники информации
Науч.-техн. документация. Наименование дата публикации выходные данные с указанием пределов просмотра (от и до)
Патент. документация наименование пат. бюллетеня журналов охранных документов номера и даты их публикации с указанием пределов просмотра (от и до)
Гидросистема осевого зажима детали
тяжелого токарного станка
металлорежущего станка
Главная справочная картотека
Бюллетень регистрации НИР и ОКР
«Станки и инструменты»
Изобретения в СССР и за рубежом
Патентная документация отобранная для последующего анализа
Страна выдачи вид и номер охранного документа классификационный индекс
Заявитель с указанием страны номер заявки дата приоритета дата публикации
Сущность заявленного технического решения и цель его создания (по описанию изобретения или опубликованной заявки)
Сведения о действии охранного документа или причина аннулирования
а.с.№1838050В23В 2300
а.с.№1450913В23В 2300
О.Н. Мазаник и А.Н. Исаев
Цель – упрощение конструкции при одновременном уменьшении габаритов
Цель-повышение надежности путем обеспеченияпостоянного низкого давления в напорной магистрали устройство создания высокого давления выполнено в виде 2-х манипуляторов.
Цель- расширение технологических возможностей путем обеспечения автоматического съема обработанной детали
Цель-автоматизация пиноли с относительно низкими затратами.
Цель-повышение производительности путем автоматизации процесса настройки устройства для определения положения пиноли.
Научно-техническая документация отобранная для последующего анализа
Наименование источника информации
Год место и орган издания
Станочные гидроприводы
Конструирование и расчет металлорежущих станков и станочных комплексов. Курсовое проектирование
В помощь конструктору – станкостроителю
Гидравлика гидромашины и гидроприводы
Гидроприводы и гидропневмоавтоматика
Металлорежущие станки
Свешников В.К. Усов А.А.
В.И. Калинин В.Н. Никифоров Н.Я. Аникеев и др.
Справочник. – М.: Машиностроение 1982.-464 с. ил.
Учебн. пособие для вузов. – Мн.; Выш. шк. 1991. – 382.; ил.
Учебн. пособие для вузов. М.: Машиностроение 1983. – 288 с. ил.
Учебник для машиностроительных вузов.- М.: Машиностроение 1982. – 423 с. ил.
Учебник для машиностроительных вузов.- М.: Машиностроение 1971. – 672 с. ил.
Учебник для машиностроительных вузов.- М.: Машиностроение 1965. – 763 с. ил.
Выводы из патентного поиска
Информационный поиск отечественной и иностранной литературы проведен по фонду Удм. ЦНТИ и предприятия с 1980 по 1996 г. Патентный поиск проведен по странам: Япония США ФРГ ГДР Великобритания и Франция.
В результате поиска было найдено множество хороших конструкционных решений которые были использованы мной в ходе работы. Наиболее удачным вариантом для решения поставленной задачи мне показалось изобретение В.И. Сергина а.с.№1838050 А3.
Изобретение относится к устройствам поджима с гидравлическим или пневматическим приводом перемещения пиноли задней бабки. Задняя бабка содержащая корпус пиноль гидро- или пневмопривод для перемещения пиноли в полости корпуса имеет гидро- или пневмопривод образованный пинолью в виде поршня с внутреннего конца соединенный штоком с поршнем соосно расположенный гидро- или пневмоцилиндр полости которого соединены для подвода и отвода рабочего тела с распределителями с подводом рабочего тела через редукционные клапаны в полость пиноли и полости цилиндра раздельно с тремя положениями распределителей: подача тела в полость пиноли подвода тела в бесштоковую полость цилиндра для поджима пиноли к детали подвода рабочего тела в штоковую полость цилиндра для перемещения пиноли от детали в исходное положение.
Особенность данного узла заключается в том что с целью упрощения конструкции при одновременном уменьшении габаритов пиноли задней бабки выполнена в виде поршня жестко связанного со штоком привода а система управления снабжена редукционными клапанами и распределителями предназначенными для подачи рабочего тела в трех положениях описанных выше.
3. Перевод иностранного текста по теме проекта
Inventions treat to machine-tool construction in particular to devices of a clip with a hydraulic or pneumatic drive of migration of a movable sleeve of a footstock. The footstock containing a body movable sleeve hydraulic drive or pneumodrive for migration of a movable sleeve in a cavity of a body with an opportunity of migration has her(it) on magnitude of a wear of the central hole of a detail hydraulic drive or pneumodrive formed(educated) by a movable sleeve as the piston from the internal end joint rod with the piston an axes the located actuator or pneumocylinder which cavities are connected for lead and tap of a working body to allocators with lead of a working body through reduction valves in a cavity of a movable sleeve and cavity of the cylinder separately with three positions of allocators: Feedinges of a body in a cavity of a movable sleeve for migration of a movable sleeve to a detail with a tap of a working body at the end of lead for a stopping of a movable sleeve lead of a body in a rodless cavity of the cylinder for a clip of a movable sleeve to a detail lead of a working body in a rod a cavity of the cylinder for migration of a movable sleeve from a detail in a home position. 3 silts.
The invention treats to machine-tool construction in particular to footstocks with a hydraulic or pneumatic drive of migration of a movable sleeve of a footstock and can be used in machine tools and other devices for example in devices for monitoring a condition of frictionless bearings when it is required to ensure(supply) often change of work pieces.
The purpose of the invention is the simplification of a construction at simultaneous reduction of dimensions.
On a f on a f on a figure 3 – footstock at a tap of a movable sleeve from a detail (in the beginning of driving).
The footstock contains a body 1 in which cavity the movable sleeve 2 with the centre 3 joint rod 4 with the piston 5 axeses located with a cavity of a movable sleeve an actuator or pneumocylinder 6 is. The cavity of a movable sleeve is connected by channels 7 and 8 to the allocator 9 with lead of a working body (hydrofluid or air) under pressure (from the pump) through the channel 10 reduction valve 11 both channel 12 and tap of a working body from a cavity of a movable sleeve through channels 7 and 8 cavity of the allocator 9 and channel 13 in a tank or atmosphere. The cavities of the cylinder 6 are connected to the allocator 14: a rod – channel 15 rodless – channel 16 with lead of a working body under pressure through the channel 17 reduction valve 18 both channel 19 and tap of a working body from a cavity of the cylinder through channels 15 and 16 cavity of the allocator 14 channel 20 in a tank or atmosphere.
The hydraulic drive or pneumodrive of a movable sleeve 2 footstocks works as follows. In a home position the movable sleeve 2 is pushed in a cavity of a body 1. In this position the removal of a treated detail and installation of other detail in the centres is made. For lead of a movable sleeve 2 to a work piece the allocators 9 and 14 are established in a position: « of lead of a movable sleeve to a detail « (figure 1). Thus a working body under pressure through the channel 10 reduction valve 11 channel 12 through cavities of the allocator 9 the channel 8 acts in a cavity of a movable sleeve and creates effort to a movable sleeve 2 necessary for driving a movable sleeve 2 in a cavity of a body.
The movable sleeve 2 displaces to a work piece. The magnitude of effort is regulated by regulation of pressure of a working body by the reduction valve 11. At reaching by the centre of 3 central holes of a work piece the movable sleeve 2 opens the channel 7. Thus a working body from a cavity of a movable sleeve through the channel 7 cavities of the allocator 9. channels 13 act in a tank or atmosphere. After migration of a movable sleeve 2 4 pistons 5 cylinders 6 displace connected with it(her) by a rod. Thus the working body from a rod of a cavity of the cylinder 6 displaces on the channel 15 in the allocator 14 channel 16 in a rodless cavity of the cylinder 6.
For a clip of a movable sleeve 2 with the centre 3 to a work piece with effort necessary at handling for a detail the allocators 9 and 14 are established in a position:
Clip of a movable sleeve to a detail (figure 2). Thus the working body under pressure acts through the channel 10 reduction valve 11 channel 12. cavities of the allocator 9 channels 7 and 8 in a cavity of a movable sleeve 2 and creates adjusted by the reduction valve 11 having strengthened on a movable sleeve 2 necessary for movement of a movable sleeve 2 in a cavity of a body 1 and through the channel 17 reduction valve 18 channel 19. cavities of the allocator 14 the channel 16 in a rodless cavity of the cylinder 6 and creates adjusted by the reduction valve 18 efforts through the piston 5. rods 4 movable sleeve 2 centres 3 on a detail necessary for its(her) handling.
At migration of the piston 5 a working body from a rod of a cavity of the cylinder 6 through the channel 15 cavity of the allocator 14 and the channel 20 acts in a tank or atmosphere For a tap of a movable sleeve 2 from a detail after its(her) handling in a home position the allocators 9 and 14 establish in a position: a tap of a movable sleeve from a detail (figure З). Thus the working body under pressure acts through the channel 17 reduction valve 18 turnpike 19 cavity of the allocator 14 the channel 15 in a rod the cavity of the cylinder 6 and creates adjusted by the reduction valve 18 efforts to the piston 5 displacing a movable sleeve 2 from a detail in a home position. The working body from a rodless cavity of the cylinder 6 through the channel 16 cavity of the allocator 14. channels 20 and from a cavity of a movable sleeve through channels 7 and 8 cavity of the allocator 9 channel 13 acts in a tank or atmosphere. The formula of the invention a Footstock containing established(installed) in body with an opportunity of established(installed) in an a body with the centre and a hydraulic drive or a pneumodrive. Executed as an axes of the cylinder located with a movable sleeve with the piston. By a rod and channels of lead tap of a working body. And also control system. Distinguished of themes that with the purpose of simplification of a construction at simultaneous reduction of dimensions the movable sleeve of a slide is executed as the piston rigidly connected to a rod of a drive and the control system is supplied with reduction valves and allocators intended for feeding of a working body in three positions: at lead of a movable sleeve to a detail – in a cavity of a movable sleeve (with a tap of a working body and end of a cycle) at a clip of a detail – in a rodless cavity of the cylinder and at a tap of a movable sleeve from a detail – in a rod a cavity of the cylinder.
Изобретение относится к станкостроению в частности устройствам поджима с гидравлическим или пневматическим приводом перемещения пиноли задней бабки. Задняя бабка содержащая корпус пиноль гидро-или пневмопривод для перемещения пиноли в полости корпуса с возможностью перемещения ее на величину износа центрового отверстия детали имеет гидро- или пневмопривод образованный пинолью в виде поршня с внутреннего конца соединенный штоком с поршнем соосно расположенный гидро- или пневмоцилиндр полости которого соединены для подвода и отводи рабочего тела с распределителями с подводом рабочего тела через редукционные клапаны в полость пиноли и полости цилиндра раздельно с тремя положениями распределителей: подачи тела в полость пиноли для перемещения пиноли к детали с отводом рабочего тела в конце подвода для остановки пиноли подвода тела в бесштоковую полость цилиндра для поджима пиноли к детали подвода рабочего тела в штоковую полость цилиндра для перемещения пиноли от детали в исходное положение. 3 ил.
Изобретение относится к станкостроению в частности к задним бабкам с гидравлическим или пневматическим приводом перемещения пиноли задней бабки и может быть использовано в станках и других устройствах например в устройствах для контроля состояния подшипников качения когда требуется обеспечить частую смену обрабатываемых деталей.
Целью изобретения является упрощение конструкции при одновременном уменьшении габаритов.
На рис.1 изображена задняя бабка при подводе пиноли к детали в момент остановки пиноли перед деталью; на рис.2 – задняя бабка при поджиме детали; на рис. 3 – задняя бабка при отводе пиноли от детали (в начале движения).
Задняя бабка содержит корпус 1 в полости которого находится пиноль 2 с центром 3 соединенная штоком 4 с поршнем 5 соосно расположенного с полостью пиноли гидро- или пневмоцилиндра 6. Полость пиноли соединена каналами 7 и 8 с распределителем 9 с подводом рабочею тела (гидрожидкости или воздуха) поддавлением (от насоса) через канал 10 редукционный клапан 11 и канал 12 и отводом рабочего тела из полости пиноли через каналы 7 и 8 полости распределителя 9 и канал 13 в бак или атмосферу. Полости цилиндра 6 соединены с распределителем 14: штоковая – каналом 15 бесштоковая – каналом 16 с подводом рабочего тела под давлением через канал 17 редукционный клапан 18 и канал 19 и отводом рабочего тела из полости цилиндра через каналы 15 и 16 полости распределителя 14 канал 20 в бак или атмосферу.
Гидро- или пневмопривод пиноли 2 задней бабки работает следующим образом. В исходном положении пиноль 2 вдвинута в полость корпуса 1. В этом положении производится снятие обработанной детали и установка другой детали в центры. Для подвода пиноли 2 к обрабатываемой детали распределители 9 и 14 устанавливаются в положение: «подвода пиноли к детали» (рис.1). При этом рабочее тело под давлением через канал 10 редукционный клапан 11 канал 12 через полости распределителя 9 канал 8 поступает в полость пиноли и создает усилие на пиноль 2 необходимое для движения пиноли 2 в полости корпуса.
Пиноль 2 перемещается к обрабатываемой детали. Величина усилия регулируется регулировкой давления рабочего тела редукционным клапаном 11. При достижении центром 3 центрового отверстия обрабатываемой детали пиноль 2 открывает канал 7. При этом рабочее тело из полости пиноли через канал 7 полости распределителя 9. канал 13 поступает в бак или атмосферу. Вслед за перемещением пиноли 2 перемещается связанный с ней штоком 4 поршень 5 цилиндра 6. При этом рабочее тело из штоковой полости цилиндра 6 перемещается по каналу 15 в распределитель 14 канал 16 в бесштоковую полость цилиндра 6.
Для поджима пиноли 2 с центром 3 к обрабатываемой детали с усилием необходимым при обработке детали распределители 9 и 14 устанавливаются в положение поджима пиноли к детали (рис.2). При этом рабочее тело под давлением поступает через канал 10 редукционный клапан 11 канал 12. полости распределителя 9 каналы 7 и 8 в полость пиноли 2 и создает отрегулированное редукционным клапаном 11 усилив на пиноль 2 необходимое для передвижения пиноли 2 в полости корпуса 1 а через канал 17 редукционный клапан 18 канал 19. полости распределителя 14 канал 16 в бесштоковую полость цилиндра 6 и создает отрегулированное редукционным клапаном 18 усилие через поршень 5. шток 4 пииоль 2 центр 3 на деталь необходимое для ее обработки.
При перемещении поршня 5 рабочее тело из штоковой полости цилиндра 6 через канал 15 полости распределителя 14 и канал 20 поступает в бак или атмосферу Для отвода пиноли 2 от детали после ее обработки в исходное положение распределители 9 и 14 устанавливают в положение: отвода пиноли от детали (рис. 3). При этом рабочее тело под давлением поступает через канал 17 редукционный клапан 18 магистраль 19 полости распределителя 14 канал 15 в штоковую полость цилиндра 6 и создает отрегулированное редукционным клапаном 18 усилие на поршень 5 перемещающее пиноль 2 от детали в исходное положение. Рабочее тело из бесштоковой полости цилиндра 6 через канал 16 полости распределителя 14. канал 20 а из полости пиноли через каналы 7 и 8 полости распределителя 9 канал 13 поступает в бак или атмосферу. Формула изобретения Задняя бабка содержащая установленную в корпусе с возможностью осевого перемещения пиноль с центром и гидро- или пневмопривод. выполненный в виде соосно расположенного с пинолью цилиндра с поршнем. штоком и каналами подвода отвода рабочего тела. а также систему управления. отличающаяся тем что с целью упрощения конструкции при одновременном уменьшении габаритов пиноль бабки выполнена в виде поршня жестко связанного со штоком привода а система управления снабжена редукционными клапанами и распределителями предназначенными для подачи рабочего тела в трех положениях: при подводе пиноли к детали – в полость пиноли (с отводом рабочего тела а конце цикла) при поджиме детали – в бесштоковую полость цилиндра и при отводе пиноли от детали – в штоковую полость цилиндра.
Информационный поиск отечественной и иностранной литературы проведен по фонду Удм. ЦНТИ и предприятия с 1980 по 1996 г.
Патентный поиск проведен по странам: Япония США ФРГ ГДР Великобритания и Франция.
В результате поиска было найдено множество хороших конструкционных решений которые были использованы мной в ходе работы.
Наиболее удачным вариантом для решения поставленной мне задачи показалось изобретение В.И. Сергина а.с.№1838050 А3.
Диплом.doc
ИЖЕВСКИЙ ГОСУДАРСТВЕННЫЙ ТЕХНИЧЕСКИЙ УНИВЕРСИТЕТ
Кафедра «Проектирование и эксплуатация машин и оборудования»
Зав. кафедрой д.т.н. профессор
РАСЧЕТНО-ПОЯСНИТЕЛЬНАЯ ЗАПИСКА К
ТЕМА: «Разработка токарного автомата для обработки детали
типа валик стеклоподъемника на базе станка модели 1И611П».
Дипломник студент гр. 10-34-1 Корниловский О.А.
Руководитель дипломного проекта к.т.н. доц. Батинов И.В.
Консультант по организационно-
экономической части доц. Янцен Т.В.
Консультант по экологии
безопасности жизнедеятельности к.т.н. доц. Глухов Ю.Г.
Представитель контроля выполнения
НОРМ ЕСТД И ЕСКД доцент Иванов В.Ф.
Представитель технологического
контроля к.т.н. доц. Шитова Т.В.
ОБЗОР И АНАЛИЗ ЛИТЕРАТУРНЫХ ИСТОЧНИКОВ ..
1. Обзор существующих токарных автоматов .
2. Патентный поиск .. .
3. Перевод иностранного текста по теме проекта ..
4. Выводы по обзору .
1. Назначение и область применения . .
2. Устройство станка
КОНСТРУКТОРСКАЯ ЧАСТЬ
1. Расчет мощности резания при точении .
2. Выбор электродвигателя главного движения
3. Прочностной расчет коробки скоростей
3.1. Расчет валов коробки скоростей
3.2. Расчет цилиндрических передач коробки скоростей ..
3.3. Расчет шпоночного соединения
4. Расчет цангового зажима .
5. Расчет бункерного загрузочного устройства .
6. Расчет автооператора
7. Расчет задней бабки
8. Расчет привода поперечной подачи
ТЕХНОЛОГИЧЕСКАЯ ЧАСТЬ
1. Расчет режимов резания .
ЭКОНОМИЧЕСКАЯ ЧАСТЬ
1. Расчет экономической эффективности от внедрения оборудования
СОДЕРЖАНИЕ ГРАФИЧЕСКОЙ ЧАСТИ ДИПЛОМНОГО
ЗНАЧЕНИЕ И РАЗВИТИЕ АВТОМАТИЗАЦИИ СТАНКОВ
При автоматизации станка производительность труда рабочего возрастает вследствие увеличения производительности станка. Рабочий освобождается от непосредственного участия в процессе обработки детали и появляется возможность многостаночного обслуживания технологического процесса.
Автоматизация облегчает физический труд рабочего освобождает его от однообразных повторяющихся движений от монотонных нервных и физических напряжений. Вместе с тем автоматизация повышает технический уровень обслуживания станка при его подготовке к производству – наладке и во время его эксплуатации. Таким образом автоматизация облегчает физический труд рабочего за счет увеличения доли умственного труда и создает предпосылки для постепенного сглаживания различий между физическим и умственным трудом.
Благодаря повышению производительности станков при автоматизации уменьшается необходимое количество единиц оборудования с единицы площади цеха снимается больше продукции. Автоматизация вносит ритмичность в процесс обработки и способствует стабильности качества заготовок и деталей на всех этапах их обработки.
ОБЗОР И АНАЛИЗ ЛИТЕРАТУРНЫХ ИСТОЧНИКОВ
1. Обзор существующих токарных автоматов
Значительную долю в парке металлорежущего оборудования составляет большая группа токарных станков. Она включает девять типов станков различающихся по назначению области применения технологическим возможностям конструктивной компоновке степени автоматизации и некоторым другим признакам. Внутри каждого типа станки различаются по своим характерным размерам и конструкции.
В машиностроении токарные автоматы получили наибольшее распространение. Автоматом называется станок в котором автоматизированы все основные и вспомогательные движения необходимые для выполнения технологического цикла обработки заготовки а также загрузка заготовки и выгрузка обработанной детали. Обслуживание автомата сводится к периодической подаче материала-заготовки или прутка и контролю обработанных деталей.
Полуавтоматом называется станок в котором автоматизированы все основные и вспомогательные движения составляющие цикл обработки одной заготовки. По окончании цикла полуавтомат останавливается; для повторения никла необходимо снять готовую деталь поставить и закрепить новую заготовку и пустить станок.
Токарные автоматы предназначены для изготовления деталей сложной конфигурации путем обработки заготовки несколькими (многими) инструментами.
Автоматизация цикла работы современных станков осуществляется на основе использования средств механики гидравлики электротехники и электроники пневматики или на комбинированной базе.
Станки с механической базой автоматизации производительны и надежны в эксплуатации. Однако на переналадку таких автоматов затрачивается много времени. Поэтому автоматы с механической базой автоматизации используют как правило в условиях массового производства.
Особое место занимают станки с числовым (цифровым) программным управлением циклом. Такие станки могут быть эффективно использованы для изготовления деталей мелких и средних серий.
Токарные автоматы подразделяют по различным признакам:
а) назначению – на универсальные и специализированные;
б) виду заготовки – на прутковые и патронные;
в) количеству шпинделей – на одно- и многошпиндельные;
г) расположению шпинделей – на горизонтальные и вертикальные.
Более подробно проведем обзор токарных одношпиндельных автоматов.
ОДНОШПИНДЕЛЬНЫЕ ТОКАРНЫЕ АВТОМАТЫ
Наиболее распространенными типами одношпиндельных токарных автоматов являются: фасонно-отрезные автоматы автоматы фасонно-продольного точения часто называемые также автоматами продольного точения н тока рно-револьверные автоматы.
Фасонно-отрезные автоматы предназначаются для изготовления из прутка (или бунта) коротких деталей малого диаметра и простой формы в условиях крупносерийного и массового производства. Схема работы такого автомата показана на рис. 1.
Рис. 1. Схема работы фасонно-отрезного автомата
Материал закрепляется во вращающемся шпинделе 1 с помощью цангового патрона. Станок имеет два-четыре суппорта 2 перемещающихся только в поперечном направлении и несущих фасонные и отрезные резцы. Для получения детали заданной длины станок снабжен подвижным упором 3 автоматически устанавливающимся по оси шпинделя после окончания цикла. Материал подается с помощью механизма подачи до соприкосновения с упором.
Станок относится к автоматам первой группы.
Главным движением (v) в этих станках является вращение шпинделя движения подачи (s) – перемещения поперечных суппортов.
Некоторые модели фасонно-отрезных автоматов имеют продольный суппорт перемещающийся вдоль оси шпинделя позволяющий производить сверление отверстий. Некоторые характерные детали обрабатываемые на фасонно-отрезных автоматах показаны на рис. 2.
Рис. 2. Типовые детали изготовляемые на фасонно-отрезных автоматах
Автоматы продольного точения предназначены для изготовления длинных деталей малого диаметра из прутка или бунта в условиях массового производства. Эти автоматы используются главным образом на предприятиях точной индустрии например в часовой промышленности приборостроении радиотехнической промышленности и т. п.
Высокие требования к точности и чистоте поверхности обрабатываемых деталей предъявляемые точной индустрией обусловили ряд конструктивных особенностей автоматов продольного точения.
Рис. 3. Схема работы автомата фасонно-продольного точения
На рис. 3 дана схема работы автомата. Заготовка закрепляется во вращающемся шпинделе 1 при помощи цангового патрона. Шпиндельная бабка 2 перемещается по направляющим станины сообщая тем самым заготовке движение подачи (s1) относительно неподвижного резца 8 закрепленного в суппорте 9. Суппорт сообщает резцу установочные перемещения при переходе на обработку ступени другого диаметра и движение поперечной подачи (s2) при отрезке и фасонном обтачивании. Станок имеет два-три вертикальных суппорта и суппорт балансирного типа 4 несущий два резца и совершающий качательное движение вокруг оси 5. Расположение суппортов показано на рис. 4.
Обработка центрального отверстия – сверление зенкерование нарезание резьбы метчиками и плашками и т. д: – производится с помощью специальных приспособлений 7 устанавливаемых на левой стороне станины.
Шпиндели приспособлений часто имеют независимое поступательное (s3) и вращательное движения. Для уменьшения прогиба и вибрации прутка под действием сил резания передний конец его пропускается через калиброванное отверстие люнета 6 закрепленного на суппортной стойке 3 установленной на станине. Такая компоновка обеспечивает высокопроизводительную обработку деталей значительной длины без опасения возникновения значительного прогиба и вибраций. При этом достигается высокая точность и чистота обработанных поверхностей.
Рис. 4. Расположение суппортов в автоматах фасонно-продольного точения: а – суппорт балансирного типа; б – вертикальные суппорты.
Следует отметить что к прутковым заготовкам обрабатываемым на этих автоматах предъявляются повышенные требования по точности.
Главным движением (v) в этих автоматах является вращение шпинделя. При цилиндрическом обтачивании движением продольной подачи s1 является перемещение шпиндельной бабки при отрезке – поперечная подача s2 осуществляемая перемещением вертикальных суппортов или поворотом суппорта балансирного типа. При фасонной обработке подача получается как геометрическая сумма продольной и поперечной подачи (s1 и s2).
При сверлении зенкеровании развертывании продольная подача представляет собой алгебраическую сумму продольных подач шпинделя станка s1 и шпинделя приспособления s3.
Автоматы продольного точения имеют один распределительный вал управляющий рабочими и холостыми движениями (автоматы первой группы).
Характерные детали обрабатываемые на таких автоматах показаны на рис. 5.
Рис. 5. Примеры типовых деталей изготовляемых на автоматах фасонно-продольного точения
Основным размером автоматов продольного точения является наибольший диаметр обрабатываемого прутка.
В табл. 1 приведены основные технические параметры современных отечественных автоматов продольного точения.
Наибольший диаметр обра-батываемого прутка в мм
Скорости главного движения в обмин
Мощность приводного электродвигателя в кет
* Станок имеет револьверную головку.
Патентный поиск отечественной и иностранной литературы проводится по теме: Создание задней бабки с автоматическим перемещением пиноли для токарного автомата с применением пневматики. (см. приложение 1).
96116 MACHINE WITH TA1LSTOCK
Henry W. Spretecr Shaker Heights. Ohio. assignor U The Waraer Л Smey Coopuy Ckvel – d. Ohio FB*d Nov. 71972. S*r. No. 304.408 Int. CL B23b 2J00. 7104 U.S. 0.82-2 R 17Chbn*
An improved machine tool includes a taibtock having a center assembly which u movable between operating and retracted pout ions by a piston and cylinder auembly. When the center auembly is in the operating pout ion a main axis of the center aoembly is aligned with the axis of rotation of a workpiece. In the retracted position the center assembly is ofhtt to one side of the work piece.
When the center assembly is in the operating position a tailstock motor is activated to press the center assembly against the outer end of the work-piece to thereby support the workpiece in a known manner. A control system coordinates movement of the center assembly with movement of a turret to avoid interference between the taibtock and tools mounted on the turret.
МКИB23b 2300. 704 США ПАТЕНТ № 3796II6
НКИ82-2R. Публикация 1974 г. 12 марта. Том 920 № 2
УДК62I.91I-229 (088.8)
Усовершенствованный металлорежущий станок содержит заднюю бабку в которой выдвижение центра в рабочее положение и отведение его назад осуществляется при помощи силового цилиндра. Когда центр находится в рабочем выдвинутом положении его ось совпадает с осью вращения заготовки. В отведенном положении центр смещен относительно заготовки. Когда центр находится в рабочем положении включается двигатель задней бабки осуществляющий поджим центра задней бабки к наружному торцу заготовки обеспечивая ее закрепление. В станке предусмотрена система управления координирующая перемещение центра задней бабки и револьверной головки. Такая система позволяет избегать столкновения задней бабки с инструментом установленным в револьверной головке.
Переводчик Айзеншток Г.И.
Редактор Щукина Т.М.
(51)МКИ В 23 В 2300 1902
(11) заявка № 59-29364
Публик.№ 840720 М 2-735 (22) (21)
Заявлено 75. 01. 23 57-161609 (62) 50-9376 (71)
Заявитель Индексверке КГ Гаи унд Тескки (33)(32)(31)
Приоритет ФРГ 74. 03. 06. Р 2410540.6
(54) ЗАДНЯЯ БАБКА ТОКАРНОГО СТАНКА
Переводчик Е.П. Комарова
H30(AuZ4)V 15800. 20.1.59-24.5.67 49. 2601 – В 23В
Reitstock fiir Werkzeugniaschinen
VEB Zahnschneidcmaschincnfabrik Modul Karl-Marx-Stadt Emsiedler Str.
Als Erfinder benannt:
Erhard Vcttcnnann Meinersdorf (Erzgeb.)
Reitstock fiir Werkzeugniaschinen mit hy-draulisch oder pneumatisch belatigter Pinole dadurch gekennzeichnet daB der mit dem Reitstockgehause (1) losbar verbundene Tragkorper (2) eine in Langsrichtung durch-gehende Bohmng aufweist in der ein fest-stehender Zylinder(4) mit beweglichem Kolben (12) angeordnet ist dessen Kolbenstange test mit der Pinole (15) verbunden ist daB die Pinole (15) von hydraulisch betatiglen Spannelementen (23 24) umgeben ist. deren Dnickraume mit dem auf der Riickseite des Kolbens (12) befindlichen Dnickraum (9) dcs Zylinders (4) abschlieBbar in VerbindunR stehen und daB in der Pinole (15) Oder an einem mit dieser fe&lverbundenen Teil ein in Abhangigkeit vom hydraulischeo Druck und einer dagegen wirkcnden Feder (19) betatig-les Keilgesperre (18 22) angeordnet ist.
УДК 621-229.332(088.8)
ФРГ заявка №1241230 КЛ. ФРГ 49а2601
Публикация 1967 № 21(24.5)
ЗАДНЯЯ БАБКА ДЛЯ МЕТАЛЛОРЕЖУЩЕГО СТАНКА
Задняя бабка для металлорежущего станка с гидравлически или пневматически перемещающейся пинолью отличается тем что несущая часть (2) разъемно соединенная с корпусом задней бабки (I) имеет отверстие в котором расположен неподвижный цилиндр (4) с подвижным поршнем (12). Шток поршня жестко соединен с пинолью (15) таким образом что пиноль (15) окружена гидравлически действующими зажимными элементами(23 24) полости нагнетания которых соединены с рабочей полостью (9) цилиндра (4) расположенной с задней стороны поршня (12). В пиноли (15) или на элементе неподвижно соединенном с ней расположен клиновой стопорный механизм (1822) действующий в зависимости от гидравлического давления против пружины (19).
Переводчик Вильнер Г.С.
Научный редактор Янина Т.А.
3. Перевод иностранного текста по теме проекта
Inventions treat to machine-tool construction in particular to devices of a clip with a hydraulic or pneumatic drive of migration of a movable sleeve of a footstock. The footstock containing a body movable sleeve hydraulic drive or pneumodrive for migration of a movable sleeve in a cavity of a body with an opportunity of migration has her(it) on magnitude of a wear of the central hole of a detail hydraulic drive or pneumodrive formed(educated) by a movable sleeve as the piston from the internal end joint rod with the piston an axes the located actuator or pneumocylinder which cavities are connected for lead and tap of a working body to allocators with lead of a working body through reduction valves in a cavity of a movable sleeve and cavity of the cylinder separately with three positions of allocators: Feedinges of a body in a cavity of a movable sleeve for migration of a movable sleeve to a detail with a tap of a working body at the end of lead for a stopping of a movable sleeve lead of a body in a rodless cavity of the cylinder for a clip of a movable sleeve to a detail lead of a working body in a rod a cavity of the cylinder for migration of a movable sleeve from a detail in a home position. 3 silts.
The invention treats to machine-tool construction in particular to footstocks with a hydraulic or pneumatic drive of migration of a movable sleeve of a footstock and can be used in machine tools and other devices for example in devices for monitoring a condition of frictionless bearings when it is required to ensure(supply) often change of work pieces.
The purpose of the invention is the simplification of a construction at simultaneous reduction of dimensions.
On a f on a f on a figure 3 – footstock at a tap of a movable sleeve from a detail (in the beginning of driving).
The footstock contains a body 1 in which cavity the movable sleeve 2 with the centre 3 joint rod 4 with the piston 5 axeses located with a cavity of a movable sleeve an actuator or pneumocylinder 6 is. The cavity of a movable sleeve is connected by channels 7 and 8 to the allocator 9 with lead of a working body (hydrofluid or air) under pressure (from the pump) through the channel 10 reduction valve 11 both channel 12 and tap of a working body from a cavity of a movable sleeve through channels 7 and 8 cavity of the allocator 9 and channel 13 in a tank or atmosphere. The cavities of the cylinder 6 are connected to the allocator 14: a rod – channel 15 rodless – channel 16 with lead of a working body under pressure through the channel 17 reduction valve 18 both channel 19 and tap of a working body from a cavity of the cylinder through channels 15 and 16 cavity of the allocator 14 channel 20 in a tank or atmosphere.
The hydraulic drive or pneumodrive of a movable sleeve 2 footstocks works as follows. In a home position the movable sleeve 2 is pushed in a cavity of a body 1. In this position the removal of a treated detail and installation of other detail in the centres is made. For lead of a movable sleeve 2 to a work piece the allocators 9 and 14 are established in a position: « of lead of a movable sleeve to a detail « (figure 1). Thus a working body under pressure through the channel 10 reduction valve 11 channel 12 through cavities of the allocator 9 the channel 8 acts in a cavity of a movable sleeve and creates effort to a movable sleeve 2 necessary for driving a movable sleeve 2 in a cavity of a body.
The movable sleeve 2 displaces to a work piece. The magnitude of effort is regulated by regulation of pressure of a working body by the reduction valve 11. At reaching by the centre of 3 central holes of a work piece the movable sleeve 2 opens the channel 7. Thus a working body from a cavity of a movable sleeve through the channel 7 cavities of the allocator 9. channels 13 act in a tank or atmosphere. After migration of a movable sleeve 2 4 pistons 5 cylinders 6 displace connected with it(her) by a rod. Thus the working body from a rod of a cavity of the cylinder 6 displaces on the channel 15 in the allocator 14 channel 16 in a rodless cavity of the cylinder 6.
For a clip of a movable sleeve 2 with the centre 3 to a work piece with effort necessary at handling for a detail the allocators 9 and 14 are established in a position:
Clip of a movable sleeve to a detail (figure 2). Thus the working body under pressure acts through the channel 10 reduction valve 11 channel 12. cavities of the allocator 9 channels 7 and 8 in a cavity of a movable sleeve 2 and creates adjusted by the reduction valve 11 having strengthened on a movable sleeve 2 necessary for movement of a movable sleeve 2 in a cavity of a body 1 and through the channel 17 reduction valve 18 channel 19. cavities of the allocator 14 the channel 16 in a rodless cavity of the cylinder 6 and creates adjusted by the reduction valve 18 efforts through the piston 5. rods 4 movable sleeve 2 centres 3 on a detail necessary for its(her) handling.
At migration of the piston 5 a working body from a rod of a cavity of the cylinder 6 through the channel 15 cavity of the allocator 14 and the channel 20 acts in a tank or atmosphere For a tap of a movable sleeve 2 from a detail after its(her) handling in a home position the allocators 9 and 14 establish in a position: a tap of a movable sleeve from a detail (figure З). Thus the working body under pressure acts through the channel 17 reduction valve 18 turnpike 19 cavity of the allocator 14 the channel 15 in a rod the cavity of the cylinder 6 and creates adjusted by the reduction valve 18 efforts to the piston 5 displacing a movable sleeve 2 from a detail in a home position. The working body from a rodless cavity of the cylinder 6 through the channel 16 cavity of the allocator 14. channels 20 and from a cavity of a movable sleeve through channels 7 and 8 cavity of the allocator 9 channel 13 acts in a tank or atmosphere. The formula of the invention a Footstock containing established(installed) in body with an opportunity of established(installed) in an a body with the centre and a hydraulic drive or a pneumodrive. Executed as an axes of the cylinder located with a movable sleeve with the piston. By a rod and channels of lead tap of a working body. And also control system. Distinguished of themes that with the purpose of simplification of a construction at simultaneous reduction of dimensions the movable sleeve of a slide is executed as the piston rigidly connected to a rod of a drive and the control system is supplied with reduction valves and allocators intended for feeding of a working body in three positions: at lead of a movable sleeve to a detail – in a cavity of a movable sleeve (with a tap of a working body and end of a cycle) at a clip of a detail – in a rodless cavity of the cylinder and at a tap of a movable sleeve from a detail – in a rod a cavity of the cylinder.
Изобретение относится к станкостроению в частности устройствам поджима с гидравлическим или пневматическим приводом перемещения пиноли задней бабки. Задняя бабка содержащая корпус пиноль гидро-или пневмопривод для перемещения пиноли в полости корпуса с возможностью перемещения ее на величину износа центрового отверстия детали имеет гидро- или пневмопривод образованный пинолью в виде поршня с внутреннего конца соединенный штоком с поршнем соосно расположенный гидро- или пневмоцилиндр полости которого соединены для подвода и отводи рабочего тела с распределителями с подводом рабочего тела через редукционные клапаны в полость пиноли и полости цилиндра раздельно с тремя положениями распределителей: подачи тела в полость пиноли для перемещения пиноли к детали с отводом рабочего тела в конце подвода для остановки пиноли подвода тела в бесштоковую полость цилиндра для поджима пиноли к детали подвода рабочего тела в штоковую полость цилиндра для перемещения пиноли от детали в исходное положение. 3 ил.
Изобретение относится к станкостроению в частности к задним бабкам с гидравлическим или пневматическим приводом перемещения пиноли задней бабки и может быть использовано в станках и других устройствах например в устройствах для контроля состояния подшипников качения когда требуется обеспечить частую смену обрабатываемых деталей.
Целью изобретения является упрощение конструкции при одновременном уменьшении габаритов.
На рис.1 изображена задняя бабка при подводе пиноли к детали в момент остановки пиноли перед деталью; на рис.2 – задняя бабка при поджиме детали; на рис. 3 – задняя бабка при отводе пиноли от детали (в начале движения).
Задняя бабка содержит корпус 1 в полости которого находится пиноль 2 с центром 3 соединенная штоком 4 с поршнем 5 соосно расположенного с полостью пиноли гидро- или пневмоцилиндра 6. Полость пиноли соединена каналами 7 и 8 с распределителем 9 с подводом рабочею тела (гидрожидкости или воздуха) поддавлением (от насоса) через канал 10 редукционный клапан 11 и канал 12 и отводом рабочего тела из полости пиноли через каналы 7 и 8 полости распределителя 9 и канал 13 в бак или атмосферу. Полости цилиндра 6 соединены с распределителем 14: штоковая – каналом 15 бесштоковая – каналом 16 с подводом рабочего тела под давлением через канал 17 редукционный клапан 18 и канал 19 и отводом рабочего тела из полости цилиндра через каналы 15 и 16 полости распределителя 14 канал 20 в бак или атмосферу.
Гидро- или пневмопривод пиноли 2 задней бабки работает следующим образом. В исходном положении пиноль 2 вдвинута в полость корпуса 1. В этом положении производится снятие обработанной детали и установка другой детали в центры. Для подвода пиноли 2 к обрабатываемой детали распределители 9 и 14 устанавливаются в положение: «подвода пиноли к детали» (рис.1). При этом рабочее тело под давлением через канал 10 редукционный клапан 11 канал 12 через полости распределителя 9 канал 8 поступает в полость пиноли и создает усилие на пиноль 2 необходимое для движения пиноли 2 в полости корпуса.
Пиноль 2 перемещается к обрабатываемой детали. Величина усилия регулируется регулировкой давления рабочего тела редукционным клапаном 11. При достижении центром 3 центрового отверстия обрабатываемой детали пиноль 2 открывает канал 7. При этом рабочее тело из полости пиноли через канал 7 полости распределителя 9. канал 13 поступает в бак или атмосферу. Вслед за перемещением пиноли 2 перемещается связанный с ней штоком 4 поршень 5 цилиндра 6. При этом рабочее тело из штоковой полости цилиндра 6 перемещается по каналу 15 в распределитель 14 канал 16 в бесштоковую полость цилиндра 6.
Для поджима пиноли 2 с центром 3 к обрабатываемой детали с усилием необходимым при обработке детали распределители 9 и 14 устанавливаются в положение поджима пиноли к детали (рис.2). При этом рабочее тело под давлением поступает через канал 10 редукционный клапан 11 канал 12. полости распределителя 9 каналы 7 и 8 в полость пиноли 2 и создает отрегулированное редукционным клапаном 11 усилив на пиноль 2 необходимое для передвижения пиноли 2 в полости корпуса 1 а через канал 17 редукционный клапан 18 канал 19. полости распределителя 14 канал 16 в бесштоковую полость цилиндра 6 и создает отрегулированное редукционным клапаном 18 усилие через поршень 5. шток 4 пииоль 2 центр 3 на деталь необходимое для ее обработки.
При перемещении поршня 5 рабочее тело из штоковой полости цилиндра 6 через канал 15 полости распределителя 14 и канал 20 поступает в бак или атмосферу Для отвода пиноли 2 от детали после ее обработки в исходное положение распределители 9 и 14 устанавливают в положение: отвода пиноли от детали (рис.З). При этом рабочее тело под давлением поступает через канал 17 редукционный клапан 18 магистраль 19 полости распределителя 14 канал 15 в штоковую полость цилиндра 6 и создает отрегулированное редукционным клапаном 18 усилие на поршень 5 перемещающее пиноль 2 от детали в исходное положение. Рабочее тело из бесштоковой полости цилиндра 6 через канал 16 полости распределителя 14. канал 20 а из полости пиноли через каналы 7 и 8 полости распределителя 9 канал 13 поступает в бак или атмосферу. Формула изобретения Задняя бабка содержащая установленную в корпусе с возможностью осевого перемещения пиноль с центром и гидро- или пневмопривод. выполненный в виде соосно расположенного с пинолью цилиндра с поршнем. штоком и каналами подвода отвода рабочего тела. а также систему управления. отличающаяся тем что с целью упрощения конструкции при одновременном уменьшении габаритов пиноль бабки выполнена в виде поршня жестко связанного со штоком привода а система управления снабжена редукционными клапанами и распределителями предназначенными для подачи рабочего тела в трех положениях: при подводе пиноли к детали – в полость пиноли (с отводом рабочего тела а конце цикла) при поджиме детали – в бесштоковую полость цилиндра и при отводе пиноли от детали – в штоковую полость цилиндра.
Информационный поиск отечественной и иностранной литературы проведен по фонду Удм. ЦНТИ и предприятия с 1980 по 1996 г.
Патентный поиск проведен по странам: Япония США ФРГ ГДР Великобритания и Франция.
В результате поиска было найдено множество хороших конструкционных решений которые были использованы мной в ходе работы.
Наиболее удачным вариантом для решения поставленной мне задачи показалось изобретение В.И.Сергина а.с.№1838050 А3.
Изобретение относится к устройствам поджима с гидравлическим или пневматическим приводом перемещения пиноли задней бабки. Задняя бабка содержащая корпус пиноль гидро- или пневмопривод для перемещения пиноли в полости корпуса имеет гидро- или пневмопривод образованный пинолью в виде поршня с внутреннего конца соединенный штоком с поршнем соосно расположенный гидро- или пневмоцилиндр полости которого соединены для подвода и отвода рабочего тела с распределителями с подводом рабочего тела через редукционные клапаны в полость пиноли и полости цилиндра раздельно с тремя положениями распределителей: подача тела в полость пиноли подвода тела в бесштоковую полость цилиндра для поджима пиноли к детали подвода рабочего тела в штоковую полость цилиндра для перемещения пиноли от детали в исходное положение.
Особенность данного узла заключается в том что с целью упрощения конструкции при одновременном уменьшении габаритов пиноли задней бабки выполнена в виде поршня жестко связанного со штоком привода а система управления снабжена редукционными клапанами и распределителями предназначенными для подачи рабочего тела в трех положениях описанных выше.
1. Назначение и область применения
Токарный автомат представляет собой модернизированный станок 1И611П (см. рис.6) и предназначен для обработки деталей типа валик стеклоподъемника 408-6104036-10 (см. раб. чертеж детали).
Рис. 6. Токарно-винторезный станок 1И611П
2. Устройство станка
Автомат состоит из станка 1И611П и из следующих модернизированных и вновь созданных узлов (см. таблицу 2 и рис.7).
Привод поперечной подачи
Бункерное загрузочное
Гидробак поперечной подачи
Рис. 7. Токарный автомат для обработки деталей типа «валик стеклоподъемника».
(см. чертеж «схема гидропневмокинематическая»)
Станок имеет наладочный и автоматичиский циклы работ. В наладочном режиме производится проверка работы каждого узла автомата. Пульт управления автоматом смонтирован на дверке электрошкафа. После подготовки автомата к работе включить кран управления бункерного загрузочного устройства. Начинает работать пневмоцилиндр Ц2 в автоматическом цикле. Сектор загрузочного устройства подает детали в лоток где деталь ориентируется в положение обработки. После заполнения лотка деталями нажать на кнопку «автомат» на пульте управления.
Срабатывает пневмоцилиндр Ц4 подающей руки автооператора и подает деталь на ось центров автомата. В конце хода руки срабатывает конечный выключатель SQ1 который дает команду на золотник Р6 (У2) телескопического пневмоцилиндра задней бабки Ц6 происходит выдвижение пиноли задней бабки на 85 мм которая своим упором выталкивает деталь из подающей руки в цанговый зажим шпинделя станка. В конце хода пиноли срабатывает конечный выключатель SQ2 подающий команду на золотник Р4 (У1) – пневмоцилиндр Ц4 переключается на обратный ход подающая рука автооператора возвращается в исходное положение. После 35 мм хода назад подающей руки срабатывает конечный выключатель SQ3 дающий команду на золотник Р7 (У3) телескопического цилиндра задней бабки Ц7 – происходит окончательная подача детали в цангу до упора.
В конце хода пиноли задней бабки срабатывает конечный выключатель SQ4 дающий команду на золотник Р1 (У4); срабатывает пневмоцидиндр Ц1 цангового зажима детали. При достижении усилия зажима Рз = 180 кг (расчетное) реле давления дает команду на золотники Р6 (У2) и происходит переключение телескопических цилиндров Ц6 и Ц7 пиноль задней бабки возвращается в исходное положение. Одновременно реле давления дает команду на электромагнитную муфту включающую вращение шпинделя и на золотник РЗ(У5) подающий сжатый воздух в гидробак.
Масло из гидробака поступает в гидроцилиндр Ц3 перемещая каретку с резцедержателем. Холостой ход каретки и рабочий ход обеспечивается дросселем с регулятором обратным клапаном и золотником ПГ-55-62 управляемым кулачком прикрепленным на каретке станка. В конце хода каретки т.е. после окончания обработки детали срабатывает конечный выключатель SQ5. Происходит быстрый отвод суппорта поперечной подачи в конце хода которого включается конечный выключатель SQ6.
Далее цикл повторяется – срабатывает пневмоцилиндр Ц4 подающей руки автооператора и подает деталь на ось центров.
Электрооборудование.
На станке установлены два трехфазных асинхронных электродвигателя:
) Электродвигатель вращения шпинделя М1
) Электродвигатель смазки М2.
Электродвигатели и аппаратура рассчитаны на включение в сеть напряжением 380 В и частотой 50 Гц. Напряжение в цепи управления 110 В. Напряжение в цепи сигнализации 55В. Подключение электрической части станка к сети осуществляется автоматическим выключателем АСТ-3. Вся электроаппаратура смонтирована в отдельно стоящем шкафу. Станок имеет автоматический и наладочный циклы работ. При нажатии кнопки S1 на пульте управления включается автоматическая работа станка и электродвигатель смазки М2.
Последовательность работы автоматического цикла.
(см. чертеж «схема электрическая принципиальная»).
Подается питание автоматическим выключателем Q. Загорается лампа «Сеть». Далее нажимаем кнопку «Пуск автомат» S4 на пульте управления
и катушка реле К11 становится на самоблокировку (цепь 9-16). Подается питание на выпрямительный мост командоаппарата. Начинает вращаться двигатель М4 (цепь 15- 4). Нажимаем кнопку «Пуск двигателя» S2 получает питание электромагнитный пускатель К10 (цепь 9-13).
Бесконтактный выключатель 1SQ включает катушку К1 контакт которой замыкает цепь воздухораспределителя механизма подачи детали (цепь 15- 4). Затем бесконтактный выключатель 2SQ включает реле катушки К2 контакт которой замыкает цепь 15- 29 – 4. Происходит выдвижение 1-го цилиндра задней бабки (золотник У2) и одновременно с этим срабатывает бесконтактный выключатель 3SQ который включает реле К3. Включается 2-ой цилиндр задней бабки (цепь 15- 29 -31- 4). Происходит выдвижение 2-го цилиндра задней бабки (золотник У3). После чего включается бесконтактный выключатель 4SQ который включает реле К4 и происходит включение зажима Y4 (цепь 15-33- 4). Происходит зажим цанги. 1-ый и 2-ой цилиндр задней бабки возвращаются в исходное положение. Затем включается бесконтактный выключатель 5SQ который включает катушку реле К5 которая в свою очередь включает электромагнит Y5 (цепь 15-27- 4).
Происходит обработка детали. После обработки детали происходит разжим цанги. Под действием выталкивающей пружины деталь удаляется из зоны обработки через склиз. Командоаппарат становится в исходное положение. Когда суппорт возвращается в исходное положение SQ3 включает К8 и цепь 15- 24-25- 4 получает питание. Срабатывает механизм подачи детали.
Имеется кнопка S3 «Исходное положение командоаппарата» которая позволяет установить командоаппарат в исходное положение в случае сбоя автоматического цикла.
Предусмотрен тормоз двигателя М4 который включается когда командоаппарат становится в исходное положение.
На двигатели М4 имеется колодка с 4-мя выводами обмотки которые включаются в цепь согласно схеме.
Защита электрооборудования от коротких замыканий обеспечивается плавкими предохранителями F1 F5 и автоматическим выключателем Q.
Защита электродвигателей от перегрузок обеспечивается тепловыми реле FF1 FF2.
Технологическая часть.
Расчет режимов резания.
В условиях массового производства в качестве режущего инструмента
следует выбрать резцы с твердосплавными пластинами (по рекомендациям данным в [1]).
При обработке алюминиевого сплава ЦА4М1 в качестве инструментального материала выбираем ВК-8.
Рабочая подача S=016 ммоб.(см.табл.15 [1] ).
Глубина резания t=35мм.
Ширина срезаемого слоя резцом ЦТ2112-4010 a=65мм.
Ширина срезаемого слоя резцом ЦТ2112-4029 а=15мм.
Скорость резания вычисляется по формуле:
S – подача ммоб. Определяется из табл.15[1].
Т – период стойкости инструмента мин.
-произведение коэффициентов учитывающих влияние материала заготовки состояния поверхности материла инструмента. Определяется из табл. 1-8 [1]. Значение коэффициента показателей степени y и m приведены в табл. 17[1].
Частота вращения шпинделя вычисляется по формуле:
v – скорость резания ммин.
d – обрабатываемый диаметр заготовки мм.
Конструкторская часть.
При работе в продолжительном режиме (S2) двигатель выбирают по требуемой мощности исходя из режимов резания и преодоления сил трения. Мощность двигателя в приводе главного движения может быть определена по зависимости:
Ргл.=Рр.+Рх.х.+Рдоп.
где Рх.х.- мощность затрачиваемая на холостом ходу;
Рр.- мощность затрачиваемая на процесс резания;
Рдоп.- мощность затрачиваемая на преодоление дополнительных потерь под нагрузкой.
Мощность потребная на резание при точении определяется по формуле:
Fz = Fz 1+Fz 2(Н) поэтому:
Fz 1-тангенциальная сила резания при точении паза резцом ЦТ2112-4010 (см. тех.процесс).
Fz 2 – тангенциальная сила резания при снятии фаски резцом ЦТ2112-4029.
V – скорсть резания ммин;
- значение коэффициента и показателя степени приведены в табл. 17[1].
- длина лезвия первого и второго инструмента мм.
– коэффициент характеризующий влияние геометрии инструмента на силы резания.
Рх.х. и Рдоп. Не превышают 15 20% от Рр. и с удовлетворительной точностью могут быть учтены коэффициентом полезного действия привода главного движения- поэтому:
где:К- коэффициент кратковременной перегрузки допускаемой стандартными двигателями;
– КПД привода главного движения станка.
- КПД зубчатой и клиноременной передачи соответственно.
По рассчитанной мощности выбирается конкретный асинхронный двигатель по каталогу [2].
Выбираем асинхронный двигатель 4А100 4У3:
мощность при n = 1500 обмин –30 кВт
под нагрузкой – 1434 обмин.
Прочностной расчет коробки скоростей.
Валы предназначены для поддержания насаженных на них тел вращения и передачи крутящего момента вдоль вала.
Расчет вала производится с целью обеспечения их прочности жесткости и отсутствии недопустимых колебаний. В редукторах вследствие сравнительно небольшой частоты вращения вала (до1500 обмин) и небольших расстояний между опорами расчет на жесткость и колебания обычно не проводят и таким образом основным расчетом является прочностной расчет вала.
Нагрузкой на вал являются силы от зубчатых передач натяжение ремня клиноременной передачи и крутящий момент. Собственной массой вала и деталей насаженных на вал обычно пренебрегают. Принято считать что нагрузки прикладываются не по всей ширине детали а в одной точке в середине ширины детали. Место приложения нагрузки выбирается в соответствии с кинематической схемой редуктора и всего привода. Направление сил должно выбираться таким образом чтобы получить наихудшие условия загружения вала из всех возможных вариантов.
Производится проверочный расчет вала IV ( см. чертеж «Кинематическая схема»)
ОПРЕДЕЛЕНИЕ ПЕРЕДАТОЧНОГО ОТНОШЕНИЯ КАЖДОЙ ПЕРЕДАЧИ
ОПРЕДЕЛЕНИЕ ЧАСТОТ ВРАЩЕНИЯ НА КАЖДОМ ВАЛУ
ОПРЕДЕЛЕНИЕ МОЩНОСТИ НА КАЖДОМ ВАЛУ
ОПРЕДЕЛЕНИЕ КРУТЯЩЕГО МОМЕНТА НА ВАЛУ
ОРИЕНТИРОВОЧНЫЙ РАСЧЕТ ВАЛА
Ориентировочный расчет производится с целью уточнения исходных данных и в частности для определения приближенно диаметра и межопорного расстояния вала так как без этих данных не могут быть проведены последующие расчеты. Этот расчет обычно производится из условия статической прочности на чистое кручение по пониженным допускаемым напряжениям кручения так как еще не полностью ясен вопрос о величине возникающих в вале изгибных напряжений.
Диаметр вала определяется из условия:
Т – крутящий момент на рассматриваемом валу;
– допускаемое напряжение на кручение принимаемое равным 15 МПа;
В зубчатых и червячных передачах в зоне зацепления действует сила направленная по линии зацепления. Эту силу с целью определения взаимного расположения нагрузок действующих на вел обычно представляют двумя (для прямозубой цилиндрической передачи) или тремя (для остальных передач) составляющими. Величина составляющих место их приложения и направление для соответствующих передач определяется так как указано ниже. При этом следует помнить что силы действующие со стороны ведущих элементов на ведомые являются активными те. окружные силы совпадают по направлению с окружной скоростью а силы. действующие со стороны ведомых элементов на ведущие- реактивными т.ч. окружные силы и окружная скорость направлены противоположно.
T1 – крутящий момент на валу;
– диаметр начальной окружности колеса на этом же валу равный (m- модуль зацепления; z – число зубьев шестерни).
– угол зацепления равный 20°.
Окружная сила приложена на плече относительно оси вала равном перпендикулярно к оси вала и вызывает изгиб вала и его кручение. Радиальная сила направлена перпендикулярно и оси вала через эту ось и вызывает изгиб вала. От этих сил в вале также возникают перерезывающие силы которыми обычно пренебрегают ввиду их малого влияния на общие напряжения в вале.
Сила Fв на вал от натяжения ветвей определяется
Kf – коэффициент зависящий от расположения ременной передачи в пространстве; для вертикальной передачи Kf = 1;
q – масса погонного метра ремня;
g – ускорение силы тяжести;
a – межосевое расстояние м.
Составляем расчетные схемы вала в координатах.
При этом за неподвижную шарнирную принимают опору где установлен подшипник воспринимающий радиальное и осевое усилие или любую опору при неизвестных вышеприведенных данных.
Вычерчиваем расчетную схему вала в двух проекциях – в вертикальной и горизонтальной – с простановкой на них сил. При этом следует помнить что если рассматривать силы приложенные в одной точке то радиальная и осевая силы всегда лежат в одной плоскости а окружная – в перпендикулярной к ней плоскости.
Определяем опорные реакции в горизонтальной и вертикальной плоскостях.
Для этого составляем уравнения моментов относительно одной и другой опор. В заключение этого пункта обязательно проведим проверку полученных значений реакции по условию; сумма всех сил на ось у или z должна быть равна нулю. Если наблюдается неравенство то расчет неверен и его следует повторить. Направление реакций задаем произвольно.
Реакция направлена в другую сторону; в дальнейших расчетах будем брать направление реакции вениз.
Определяем суммарные реакции в опоре А и В:
Подбор подшипников здесь не проводим считаем что они подобраны правильно вследствие чего размеры вала были приняты верными.
Строим эпюры изгибающих моментов в 2-х плоскостях:
На участке от Fay до Fr
На участке от Fr до Fby
На участке от Fby до Fв
На участке от Fax до Ft
На участке от Ft до Fbx
Строим эпюру суммарного изгибающего момента по зависимости:
Под силой Fbx и Fby:
Строим эпюру крутящего момента равного
УТОЧНЕННЫЙ РАСЧЕТ ВАЛА
Уточненный расчет вала производится с целью нахождения истинного значения запаса прочности вала.
Установлено что работоспособность вала из условия усталостной прочности будет обеспечена если
S – фактический (расчетный) коэффициент запаса прочности;
[S] – допускаемый коэффициент запаса прочности обычно принимаемый для валов редуктора в пределах 15 5.
Уточненный расчет вала проводится с учетом воздействия на него переменных нагрузок из условия его усталостной прочности.
Выбираем материал вала.
Назначаем для вала сталь марки Сталь 45. Для этой стали предел прочности ; пределы выносливости ; коэффициент чувствительности к ассиметрии цикла .
Опеределяем запас прочности вала.
При действии на вал только напряжений изгиба или напряжений кручения коэффициенты запаса усталостной прочности соответственно по изгибу и кручению определяются по зависимостям:
При совместном действии на вал напряжений изгиба и кручения коэффициент запаса прочности определяется по выражению:
В этих формулах обозначено:
– пределы выносливости при изгибе и кручении для симметричного цикла;
- эффективные коэффициенты концентрации напряжений при изгибе и кручении принимаемые по [4 табл. 15.1];
– масштабный фактор и фактор качества поверхности определяются по графикам рис. 15.5 и 15.6 [4];
– переменные составляющие циклов напряжений.
М и Т – соответственно изгибающий и крутящий моменты в рассматриваемом сечении вала;
– моменты сопротивления на изгиб и кручение этого же сечения.
что в пределах нормы.
ПРОВЕРКА ВАЛА ПО СТАТИЧЕСКОЙ ПРОЧНОСТИ
Эту проверку производят в целях предупреждения пластических деформаций и разрушений с учетом кратковременных перегрузок.
Статическая прочность вала обеспечена.
РАСЧЕТ ЗУБЧАТОЙ ПЕРЕДАЧИ.
По таблице рекомендуемых сочетаний материалов для зубчатых колес и шестерен принимаем для шестерни Сталь 40ХН HB1=270
для колеса Сталь 40Х HB2=260 ([5] табл. 3.3)
Определение допускаемых напряжений
Определение допускаемых напряжений производится в зависимости от механических характеристик материала колес и вида термообработки состояния рабочей поверхности зуба и переходной поверхности базового числа циклов для материала колес действительного числа циклов нагружения вызванных постоянной или переменной нагрузкой. Статическая прочность зубьев определяется значением наибольшей нагрузки. Если передачи работают в условиях переменных напряжений вызванных постоянным или переменным режимом нагружения то необходимо учитывать суммарный эффект на усталостную прочность различных по величине и продолжительности нагрузок. Расчет передач по наибольшей нагрузке если принять ее постоянно действующей в течение всего срока службы приведет к избыточной прочности и утяжелению деталей увеличению габаритов и стоимости.
Допускаемое усталостное контактное напряжение:
zR – коэффициент учитывающий шероховатость = 095;
zv – коэффициент окружной скорости = 1;
SH – коэффициент запаса прочности; при улучшении = 12; при закалке = 13;
zN – коэффициент долговечности;
NHG – базовое число циклов;
NHЕ – эквивалентное число циклов;
eH – коэффициент эквивалентности = 025;
t – время работы в часах;
n – частота вращения зубчатого колеса;
m – степень кривой усталости = 6;
– предел контактной выносливости;
Допускаемое расчетное контактное напряжение для расчетов принимается наименьшее из двух:
Определение коэффициента нагрузки
В расчетные уравнения для определения размеров передачи и действительных изгибных и контактных напряжений подставляется наибольшая длительно действующая мощность с учетом сил инерции возникающих в станке при пусках и остановках торможении и изменении режимов резания припусков и т. п.
Однако в передачах возникают дополнительные динамические нагрузки обусловленные внутренними причинами передач и кроме того концентрация нагрузки вдоль контактных линий. Учет этих нагрузок производится введением в расчетные уравнения коэффициента нагрузки.
Для предварительных расчетов при несимметричном расположениии колес на валах принимаем коэффициент нагрузки КН = 15 (с.124 [5])
Определение межосевого расстояния
Межосевое расстояние определяется из условия контактной прочности:
Геометрический расчет зубчатой передачи
Делительные диаметры
Проверка межосевого расстояния
Диаметры вершин зубьев
d 12 – делительные диаметры;
m – расчетный модуль.
Ширина венца зубчатого колеса
– межосевое расстояние;
– коэффициент ширины венца зубчатого колеса;
Коэффициент торцевого перекрытия
Определение степени точности колеса
Степень точности зависит от окружной скорости
По приложению 19 [5] принимаем 8 степень точности.
Определение коэффициентов нагрузки по контактным напряжениям
– коэффициенты внутренней динамической нагрузки; (с. 181 [6])
– коэффициенты концентрации нагрузки; (с. 182 [6])
– коэффициенты распределения нагрузки между зубьями;
Проверка по контактным напряжениям
zE – коэффициент материала (для стали = 190);
ze – коэффициент учета суммарных длин контактных линий;
zН – коэффициент формы сопряженных поверхностей (с. 167 [6]); т.к. ;
изменение в допустимых пределах .
РАСЧЕТ ШПОНОЧНОГО СОЕДИНЕНИЯ
Производится расчет шпоночного соединения на валу IV обеспечивающего передачу крутящего момента на шкив 160.
Размеры шпонок выбираются в зависимости от принятого диаметра вала по таблицам ГОСТа а затем производится условный расчет на смятие в предположении что напряжения на узких рабочих гранях шпонки и паза распределяются равномерно.
Т – передаваемый крутящий момент;
h – высота сечения шпонки = 11 мм;
– рабочая длина = 40 мм;
t – глубина паза = 33 мм;
– допускаемое напряжение смятия; = 600 800 МПа.
)что в пределах нормы.
( см. чертеж «Шпиндельная бабка с зажимом цанговым»).
Цанговый зажим установлен в шпинделе станка 1И611П. Состоит из цанги поз.8 тяги поз.1 и силового привода. Зажим цанговый снабжен пружинным выталкивателем и реле давления рассчитанным на определенное усилие зажима детали.
Цанговый зажим должен удовлетворять следующим требованиям:
-концентричный зажим при радиальном биении не больше 001-004 мм;
-надежный зажим при нормальных погрешностях заготовок – в пределах 5-го класса точности;
- постоянство длины подаваемого прутка;
- постоянство упругих свойств цанги износостойкость губок цанги (зажим 50000-100000заготовок до выхода из строя).
Цанги изготавливают из сталей марок У8А У10А 65Г с термической обработкой конусной поверхности до твердости HRC 58-62 а хвостовика – до HRC 40-45.
Лепестки цанг при закалке немного разводятся чтобы подаваемый пруток свободно проходил между ними. Угол при вершине конуса цанг делается 30°. Число прорезей у цанги – от двух до шести в зависимости от диаметра заготовки. При диаметре свыше 20 мм рекомендуется три прорези.
Можно выделить следующие достоинства зажимов с затяжной цангой (с обратным конусом):
-конус цанги прилегает непосредственно к конической расточке в шпинделе что обеспечивает хорошее центрирование заготовки;
- исключено заклинивание во время подачи прутка;
- осевая составляющая силы резания усиливает зажим прутка;
- лепестки цанги растягиваются а не сжимаются при зажиме и цанга и её конус мало деформируются;
-малые радиальные габариты
Цанга является основным исполнительным элементом в зажимном механизме и от ее характеристик во многом зависит работоспособность как зажимного устройства так и автомата в целом.
Для вращающихся обрабатываемых заготовок сравнительно высокой жесткости необходимую силу зажима определяют при соблюдении следующих трех условий:
Момент закрепления должен быть больше крутящего момента возникающего от составляющих сил резания стремящихся повернуть заготовку вокруг оси вращения ().
При отсутствии упора суммарная осевая сила сцепления должна быть больше суммарной осевой силы резания .
Момент зажима возникающего от силы сцепления должен быть больше изгибающего момента от составляющих сил резания стремящихся вывернуть заготовку относительно точки опоры .
Суммарная радиальная сила зажима прижимающая губки цанги к заготовке определяется по формуле взятой из [28].
Для нашей схемы работы зажима (см. рис.8) осевая сила может быть вычислена по формуле (табл. 7.19. [28])
где:: -коэффициент запаса;
-коэффициент сцепления между губками цанги и заготовкой;
-составляющие силы резания;
-крутящий момент при сверлении;
-диаметр заготовки в месте зажима и диаметр обработки соответсвенно;
-приведенный угол трения.
Рис. 8. Схема действия осевой силы при одинарном зажиме.
Суммарная радиальная сила зажима прижимающая губки цанги к заготовке равна:
Зная суммарную осевую силу зажима в цанговом патроне можно перейти непосредственно к расчету пневмоцилиндра.
Расчет пневмоцилиндра.
Основные параметры поршневого цилиндра с односторонним штоком
связаны между собой следующими соотношениями [32]:
При движении поршня вправо когда поршневая камера соединена с напорной линией а штоковая – со сливной
F1F2- площадь поршневой и штоковой полости мм2;
р1р2- давление в поршневой и штоковой полости кгссм2;
Р1Р2- полезная нагрузка Н;
V1V2- скорость перемещения штока ммин;
Q1Q2 – расход воздуха лмин;
=09-098 – коэффициент учитывающий потери на трение в цилиндре;
При движении поршня влево когда штоковая камера соединена с напорной линией а поршневая – со сливной
Диаметр пневмоцилиндра определяется по формуле взятой из [9]::
- технологическая (полезная) нагрузка Н;
- масса всех подвижных элементов связанных с поршнем кг;
g -ускорение свободного падения мс2;
- подводимое абсолютное давление сжатого воздуха кгссм2;
Вес подвижных частей ± mg учитывают при вертикальном или наклонном расположении пневмоцилиндра. Знак «+» ставят тогда когда вес уменьшает зажимное усилие. В расчетной формуле принято что требуемое усилие зажима создается при давлении 09 чем обеспечивается некоторый его запас. Т.к. пневмоцилиндр расположен горизонтально то сила ± mg в формуле равна нулю.
Найденное значение D округляют до ближайшего из нормального ряда диаметров цилиндров по ГОСТ 6540-68: 25 32 40 50 63 80 100 125 160 200 250 320 360 400 мм.
Следовательно диаметр пневмоцилиндра цангового зажима следует принять равным 200 мм.
Диаметр штока определяют из соотношения:
d = (025 . . . 032) D
и округляют до ближайшего значения взятого из ряда 10 12 16 25 32 40 50 63 80 90 мм.
Исходя из конструктивных соображений принимаем диаметр штока равным 25мм.
Условный проход присоединительных отверстий пневмоцилиндра рекомендуется принимать из соотношения dy = 01D. Обычно такой же условный проход имеют присоединяемые воздухопроводы и установленные на них элементы пневмоаппаратуры. Однако выбирая величину dy необходимо также учитывать длину хода поршня и требуемое быстродействие привода. При малых длинах ходов условный проход уменьшают.
Принимаем dy равным 15мм.
Рассчитаем рабочую площадь поршня в поршневой 1 и штоковой 2 областях соответственно.
При движении поршня вправо когда поршневая камера соединена с напорной линией а штоковая – со сливной:
Требуемое усилие на штоке цангового зажима обеспечено.
5. Бункерное загрузочное устройство.
Автоматизация производственных процессов является характерной чертой современного прогресса. Без автоматизации невозможны высокие темпы дальнейшего роста производительности труда. Одной из основных проблем при автоматизации технологического оборудования и в частности металлорежущих станков является автоматизация загрузки заготовок и разгрузки (съема) обработанных деталей а при создании автоматических линий кроме того и автоматизация транспортных перемещений между станками.
Автоматизация загрузки и разгрузки оборудования находящегося в эксплуатации позволяет изменить процесс труда повысить безопасность и коэффициент использования оборудования а в некоторых случаях интенсифицировать режим его работы; полуавтоматические станки и станки с ручным управлением можно превратить в автоматы снизив тем самым штучное время обработки и широко использовать многостаночное обслуживание
Мнение что автоматизация загрузки-разгрузки оборудования ранних лет выпуска целесообразна только в условиях массового производства является ошибочным. Оснащение производства станками и технологической оснасткой сборно-разборной конструкции позволяет автоматизировать технологический процесс в условиях серийного и мелкосерийного производства и при частой смене объектов производства. В условиях серийного производства автоматизации производства должна предшествовать типизация технологических процессов или разработка групповых методов обработки.
В бункерных загрузочных устройствах заготовки в бункере (емкости) сосредоточены навалом. Захват из бункера и ориентация заготовок в положение требуемое для обработки или удобное для загрузки и все последующие перемещения осуществляются автоматически.
Загрузочные устройства эффективны если они повышают коэффициент использования станков (автоматических линий) на которых они установлены и производительность а также облегчают условия труда; не повреждают поверхность подаваемых заготовок или удаляемых со станка обработанных деталей; имеют простую конструкцию и минимальное количество деталей; состоят из нормализованных деталей; удобны в эксплуатации и дешевы в изготовлении; позволяют легко заменять быстроизнашивающиеся детали устройств.
Независимо от типа различают универсальные универсально-наладочные и специальные загрузочные устройства; первые два типа с помощью переналадки или подналадки а также замены некоторых деталей могут быть использованы для загрузки заготовок отличающихся размером а иногда и формой; устройства третьего типа применяют только для загрузки заготовок определенного типа. Загрузочные устройства только загружают заготовки а снимают (разгружают) обработанные детали толкатели станка или детали поступают в приемный лоток под действием собственного веса (силы тяжести).
Загрузочно-разгрузочные устройства (автооператоры или механические руки) специальными механизмами не только загружают но и разгружают заготовки.
Конструкторы разработали основы теории проектирования загрузочно-разгрузочных устройств и создали оригинальные конструкции устройств эксплуатируемые на заводах. Дальнейшему появлению новых и высокопроизводительных загрузочно-разгрузочных устройств будет способствовать разработка и исследование: механизмов ориентации используемых для заготовок повышенной сцепляемости; механизмов ориентации заготовок в магнитном поле и систем логической ориентации механизмов вторичной ориентации.
Расчет бункерного загрузочного приспособления.
В бункерных загрузочных устройствах основной запас изделий сосредоточивается в емкостях сделанных в виде коробов различной формы или широких лотков.
Размеры бункеров в машиностроении ограничиваются большим давлением изделий на стенки емкости и друг на друга так как вследствие этого затрудняется извлечение их из емкости.
В процессе работы в автоматических бункерах изделия захватываются и транспортируются в накопитель в ориентированном положении.
Изделия при этом подвергаются ударам и трению друг о друга и о захват транспортирующего механизма. Поэтому если повреждения недопустимы или изделия недостаточно жестки и сложны настолько что возможно сцепление их между собой применение бункерных загрузочных устройств с движущимся захватом исключается.
Емкости автоматических бункеров для штучных изделий имеют сходство с обычными бункерами для насыпных грузов. Под бункером принято понимать емкость имеющую относительно малую высоту по
-Бункер 2-Сектор 3-Лоток.
сравнению с размерами поперечного сечения бункера. К бункерам относят все емкости в которых плоскость обрушения (рис.9) пересекает свободную поверхность материала (в зоне бункера). Аналитически это выражается следующим образом:
Практически высота обычного бункера не превышает двух поперечников что характеризуется соотношением .
В соответствии с рекомендациями данными в [28] размеры секторного бункера берутся в зависимости от наибольшего поперечника изделия. Для бункера с центральным сектором эти зависимости имеют вид:
Ширина бункера В=(12-15)l;
Производительность бункера считается по формуле взятой из [28]:
где: z-число секторов;
р-коэффициент захватывания который берется в зависимости от формы и конфигурации изделия.
Работоспособность бункера зависит от степени взаимоподвижности изделии в бункере под действием внешних сил т. е. сыпучести изделий. В свою очередь сыпучесть изделий зависит от материала веса чистоты обработки загрязненности конфигурации а также от количества и высоты слоя изделий в емкости.
Основное влияние на сыпучесть изделий оказывает вес и размеры последних чем крупнее и тяжелее изделия тем сыпучесть ниже. Изделия следует загружать небольшим слоем так как действие веса ухудшает работоспособность бункера.
Сыпучесть характеризуется углом естественного откоса образованного при свободном набросе изделий в кучу на плоскости. Наибольшей сыпучестью обладают шарообразные изделия так как образуют наименьший угол естественного откоса. Сыпучесть в бункере зависит и от отношения всего объема бункера к объему занимаемому изделиями.
На рис.10 показана экспериментальная кривая по которой можно определить высоту слоя изделий в бункер. По оси абсцисс отложены наибольшие размеры изделий от 25 до 250 мм а по оси ординат–высота слоя изделий выраженная количеством поперечника (числом рядов) загружаемого изделия.
Рис. 10. Экспериментальная кривая определяющая зону применения бункеров в зависимости от размеров изделий.
Из графика видно что чем меньше поперечник изделия тем допускается больше количество рядов их в бункере. Для крупных изделий начиная от 150 мм допускается один ряд. В тех случаях когда высота или длина изделия равна 09–01 наибольшего поперечника рекомендуется применять магазин или штабельник.
Давление изделий на стенки бункера.
Давления воспринимаемые стенками автоматического бункера без учета трения изделий и стенки и конфигурации бункера определяются на основе теории сыпучих тел Вертикальное давление Ру на горизонтальную плоскость расположенную на высоте у от верхнего уровня засыпки материала выражается как гидростатическое давление.
где: q – насыпной вес материала в кГсм3.
Горизонтальное (боковое) давление в любой точке по высоте бункера определяется как результат действия клина нагруженного собственным весом Q при отсутствии трения материала на стенке. Горизонтальное давление на высоте у от поверхности засыпки определяется по формуле:
Рx = R · Ру = R ·q · у (40)
Из уравнения видно что горизонтальное давление на любом уровне пропорционально вертикальному давлению на том же уровне и составляет его долю определяемую коэффициентом R зависящим от степени сыпучести материала и определяемого по формуле:
где: -угол естественного откоса.
Толщина стенок бункеров практически берется в зависимости от веса Q в кг загружаемых изделий:
Учитывая что количество одновременно загружаемых деталей n=150шт. а масса одной детали m=0053кг получаем:
Принимаем толщину стенок равную 1мм.
Плотность насыпки изделий и их насыпной вес.
Изделия засыпанные в бункер располагаются в нем с различной степенью плотности которая характеризуется отношением суммы объектов пустых пространств остающихся между изделиями ко всему объему;
где:: V1-общий объем занимаемый изделиями (емкость бункера кучи);
V2-объем самих изделий (по внешней конфигурации);
V3 =V1-V2- объем пустых пространств.
Зная расчетную емкость бункера V1=4500 см3 и объем всех деталей равный »4000 см3 найдем V3=4500-4000=500 см3 тогда:
Сектор совершает возвратно-поступательные движения захватывая заготовки и подавая их в лоток. Лоток выполнен наклонным благодаря чему заготовки могут перемещаться за счет собственной силы тяжести.
Найдем теоретическую производительность бункера:
Захват деталей из бункера поз. 1 (см. рис.11) производится с помощью сектора поз. 2 который движется от пневмоцилиндра поз. 4.
Интенсивность поступления деталей из бункера поз.1 в лоток поз.3 регулируется дросселями поз.5 на пневмоцилиндре бункерного загрузочного изделия.
Рис. 11. Бункерное загрузочное устройство.
Основные параметры поршневого цилиндра с односторонним штоком связаны между собой следующими соотношениями [32]:
Диаметр пневмоцилиндра определяется по формуле взятой из [9]:
где: - технологическая (полезная) нагрузка;
- масса всех подвижных элементов связанных с поршнем;
g-ускорение свободного падения;
- подводимое абсолютное давление сжатого воздуха;
Вес подвижных частей ± mg учитывают при вертикальном или наклонном расположении пневмоцилиндра. В расчетной формуле принято что требуемое усилие зажима создается при давлении 09 чем обеспечивается некоторый его запас.
Следовательно диаметр пневмоцилиндра бункерного загрузочного устройства следует принять равным 63 мм.
Поэтому принимаем диаметр штока равным 25мм.
Требуемое усилие на штоке обеспечено.
Скорость перемещения штока регулируется дросселями поз.3 (см. рис. ).
Служит для подачи детали из лотка загрузочного устройства в зону обработки. Автооператор состоит из кронштейна на котором крепятся:
-Направляющая для перемещения штока со стаканом;
-Шток перемещается пневмоцилиндром 63;
-Корпус нa котором крепится направляющая для перемещения корпуса руки.
Шток перемещаясь поворачивается на 900 по байонетному пазу и подает деталь на ось центров.
К корпусу руки крепится губка для западания в нее детали из лотка загрузочного устройства. Крайние положения корпуса руки и штока фиксируются конечными выключателями смонтированными на направляющих.
Рис. 12. Автооператор.
Основные параметры поршневого цилиндра с односторонним штоком (см. рис. 12) связаны между собой следующими соотношениями [32]:
где:: - технологическая (полезная) нагрузка;
Вес подвижных частей ± mg учитывают при вертикальном или наклонном расположении пневмоцилиндра. В расчетной формуле принято что требуемое усилие зажима создается при давлении 09 чем обеспечивается некоторый его запас. Т.к. пневмоцилиндр расположен горизонтально то сила ± mg в формуле равна нулю.
Поэтому принимаем диаметр штока равным 25мм.
Найдем скорость перемещения штока:
t- время срабатывания с.
V= S:t = 016:(03:60) = 32ммин;
Зная скорость перемещения штока найдем расход воздуха:
Пиноль задней бабки перемещается от механизма шаговой подачи который содержит силовые цилиндры с полым поршнем установленными в корпусе телескопически.
(см. рис. ) связаны между собой следующими соотношениями:
где: =09-098 – коэффициент учитывающий потери на трение в цилиндре;
Расчет пневмоцилиндров.
Диаметр пневмоцилиндров определяется по формуле взятой из [9]:
Поскольку конструкция задней бабки нестандартная то диаметры цилиндров не следует округлять до ближайшего из нормального ряда диаметров цилиндров.
D1= 60мм-диаметр первого цилиндра задней бабки.
D2 = 75мм-диаметр второго цилиндра задней бабки.
d = 20мм – диаметр штока.
t = 03с- время хода второго цилиндра задней бабки.
p11=p12= 4-6 кгсм2- давление воздуха в поршневой области первого и второго цилиндра.
p21=p22 =15 кгсм2- давление воздуха в штоковой области.
S1=35мм – ход поршня.
S2=85мм- ход цилиндра.
Требуемое усилие Р1 = 800Н на штоке задней бабки обеспечено.
V = S : t = 085 : (03 : 60) = 17 ммин;
8. Привод поперечной подачи
(см. чертежи «Привод поперечной подачи»)
Служит для перемещения каретки с резцедержателем в поперечном направлении. Состоит из каретки поперечного суппорта и резцедержателя станка 1И611П перемещающихся от гидроцилиндра смонтированного сзади станка. Холостой ход каретки 20 мм и рабочий ход 10 мм обеспечиваются дросселем с регулятором обратным клапаном и золотником ПГ-55-62 смонтированным на одном кронштейне с гидроцилиндром сзади станка.
Давление в гидросистеме 4 6 кгсм2. Включение и отключение дросселя обеспечивается кулачком закрепленным на каретке поперечного суппорта. Исходное и конечное положение каретки фиксируются конечными выключателями смонтированными на станине станка.
Для автоматизации привода поперечной подачи нельзя использовать пневмоцилиндр поскольку он:
не может обеспечить заданный закон движения выходного звена;
имеет нестабильность скорости движения выходного звена.
В связи с этим следует использовать гидравлику.
При обработке валика стеклоподъемника 4086104036 согласно назначенным режимам сила подачи Рх = 350Н однако следует предусматреть другие варианты обработки при которых эта сила намного больше.
В соответствии рекомендациям [32] в качестве привода поперечной подачи выбираем гидроцилиндр с двусторонним штоком по ОСТ 2 Г22-2-73.
Диаметр цилиндра: 80 мм
Диаметр штока: 32 мм
Номинальный расход: 50 лмин
Максимальное (теоретическое) усилие на штоке
без учета сил трения: 564 кН
Максимальное давление холостого хода: 047 МПа
Утечка масла через уплотнения поршня
при номинальном давлении: 4 см3мин
СОДЕРЖАНИЕ ГРАФИЧЕСКОЙ ЧАСТИ ДИПЛОМНОГО ПРОЕКТА
Наименование: Общий вид станка (лист 1).
Показан главный вид станка. Приведены технические требования и техническая характеристика станка. Ограждение поз. 7 не показано.
Наименование: Общий вид станка (лист 2).
Показаны вид сзади и вид сбоку станка. Обозначены основные узлы станка. Показаны габаритные размеры станка.
Наименование: Бабка задняя.
Сборочный чертеж включает: цилиндр поз.2 поршень поз.14 шток поз.13. Главный вид выполнен в разрезе. Показаны основные размеры проставлены посадки и сформулированы технические требования. Задняя бабка выполнена телескопически. Такая конструкция обеспечивает высокую надежность узла и четкое выполнение перемещений согласно циклограмме работы станка.
Наименование: Схема электрическая принципиальная.
На чертеже показана схема всего электрооборудования станка включение электродвигателей в цепь блоки управления: механизма подачи детали 1-го цилиндра задней бабки 2-го цилиндра задней бабки зажима цанги суппорта исходного положения командоаппарата исходного положения суппорта.
На чертеж вынесена спецификация с указанием основных параметров отдельных узлов схемы.
Электродвигатели и аппаратура рассчитаны на включение в сеть напряжением 380 В и частотой 50 Гц. Напряжение в цепи управления 110В.Напряжение в цепи сигнализации 55 В. Подключение электрической части станка к сети осуществляется автоматическим выключателем АСТ-3. Вся электроаппаратура смонтирована в отдельно стоящем шкафу.
На пульте управления станка предусмотрены сигнальные лампы «Сеть» «Автомат» «Наладка» «Конец цикла» «Наличие детали». Сигнальная лампа «Наличие детали» загорается при отсутствии детали на позиции обработки. Для счета обработанных деталей на эл.шкафу смонтирован электроимпульсный счетчик.
Наименование: Циклограмма. Автомат для обработки валика стеклоподъемника.
На чертеже показана циклограмма работы станка которая показывает продолжительность каждого из переходов в цикле.
Продолжительность переходов необходимо знать при выборе электродвигателя привода главного движения.
В соответствии с циклограммой работа станка начинается с нажатия кнопки «Вкл. Автомат».
Срабатывает пневмоцилиндр Ц4 подающей руки автооператора и подает деталь на ось центров автомата. В конце хода руки срабатывает конечный выключатель SQ1 который дает команду на золотник Р6 (У2) телескопического пневмоцилиндра задней бабки Ц6 происходит выдвижение пиноли задней бабки на 85 мм которая своим упором выталкивает деталь из подающей руки в цанговый зажим шпинделя станка. В конце хода пиноли срабатывает конечный выключатель SQ 2 подающий команду на золотник Р4 (У1) – пневмоцилиндр Ц4 переключается на обратный ход подающая рука автооператора возвращается в исходное положение. После 35 мм хода назад подающей руки срабатывает конечный выключатель SQ3 дающий команду на золотник Р7 (У3) телескопического цилиндра задней бабки Ц7 – происходит окончательная подача детали в цангу до упора.
В конце хода пиноли задней бабки срабатывает конечный выключатель SQ4 дающий команду на золотник Р1 (У4); срабатывает пневмоцидиндр Ц1 цангового зажима детали. При достижении усилия зажима Рз = 180 кг (расчетное) реле давления дает команду на золотники Р6 (У2) и происходит переключение телескопических цилиндров Ц6 и Ц7 пиноль задней бабки возвращается в исходное положение. Одновременно реле давления дает команду на электромагнитную муфту включающую вращение шпинделя и на золотник Р3 (У5) подающий сжатый воздух в гидробак.
Масло из гидробака поступает в гидроцилиндр Ц3 перемещая каретку с резцедержателем. Холостой ход каретки и рабочий ход обеспечивается дросселем с регулятором обратным клапаном и золотником ПГ-55-62 управляемым кулачком прикрепленным на каретке станка. В конце хода каретки т.е. после окончания обработки детали срабатывает конечный выключатель SQ5. Происходит быстрый отвод суппорта поперечной подачи в конце хода которого включается конечный выключатель SQ6. Происходит разжим и удаление детали посредством выталкивающей пружины.
Наименование: Схема гидропневмокинематическая. Автомат для обработки валика стеклоподъемника.
На чертеже показаны все гидро- и пневмоцилиндры схема включения их в гидро- и пневмолинию а также регуляторы дроссели и эл. контакты обеспечивающие автоматический цикл работы станка.
Наименование: Схема кинематическая. Валик стеклоподъемника.
Представлена кинематическая схема токарного автомата с автоматическим переключением скоростей благодаря включению в схему гидроцилиндров. Проставлены позиции валов и зубчатых колес с указанием числа зубьев. Представлен график частот вращения шпинделя.
На данном листе также представлены рабочие чертежи обрабатываемых деталей. Показаны все технологические размеры проставлены отклонения шероховатости поверхностей. Дан разрез детали сформулированы технические требования.
Наименование: Автооператор.
Показан способ крепления руки автооператора к станине станка. Приведены все необходимые виды разрезы и сечения объясняющие устройство и принцип работы механизма. Проставлены основные и установочные размеры. Приведены технические требования и техническая характеристика.
Наименование: Шпиндельный узел с зажимом цанговым.
Показан шпиндельный узел токарно-винторезного станка 1И611П с зажимом цанговым работающим посредством вращающегося пневмоцилиндра. Показаны все технологические размеры проставлены отклонения. Показаны габаритные размеры шпиндельной бабки.
Лист 10: формат А23.
Наименование: Бункерное загрузочное устройство.
Показано бункерное загрузочное устройство которое обеспечивает передачу заготовок сконцентрированных в бункере навалом на ось руки автооператора. Качающийся сектор захватывает заготовки из бункера и передает их в лоток в котором заготовки перемещаются под действием собственной силы тяжести. Заготовки имея вертикальную ориентацию попадают в отсекатель который в нужный момент пропускает одну заготовку. Далее заготовка падает в стаканчик автооператора и подается на в зону обработки.
На чертеже показаны габаритные и установочные размеры изображены все необходимые виды сечения и разрезы. Приведены технические требования и техническая характеристика.
Наименование: Привод поперечной подачи. (лист 1).
Показано крепление гидроцилиндра к станине станка. Дан разрез показывающий конструкцию. Проставлены все необходимые размеры гидроцилиндра. Приведены технические требования.
Лист 12: формат А23.
Наименование: Привод поперечной подачи. (лист 2).
Показан вид сверх и вид сзади стака. Вынесены сечения показывающие крепление штока гидроцилиндра к каретке резцедержателя. Проставлены все необходимые размеры.
Наименование: Схема соединений.
Показана схема питания пневмо и гидроцилиндров. Сжатый воздух от источника питания через фильтр-влагоотделитель ВД редукционный клапан РД маслораспылитель МР поступает на вход пневмораспределителей. Откуда воздух по пневмолиниям поступает в полости цилиндров. Скорость потока воздуха регулируется дросселями.
Наименование: Организационно-экономическая часть.
Чертеж представляет собой таблицу технико-экономических показателей дипломного проекта.
В ходе выполнения дипломного проекта был разработан специальный токарный автомат на базе одношпиндельного токарно-винторезного станка 1И611П. Разработка данного автомата выполнена с целью повышения производительности станка (400-600детчас) и как следствие повышение производительности труда рабочего. При этом рабочий освобождается от непосредственного участия в процессе обработки детали от однообразных повторяющихся движений от монотонных нервных и физических напряжений. Вместе с тем повышается технический уровень обслуживания станка при его подготовке к производству – наладке и во время его эксплуатации. Модернизация станка вносит ритмичность в процесс обработки и способствует стабильности качества.
В ходе работы выполнено следующее:
Модернизирована задняя бабка с целью автоматизации перемещения пиноли посредством пневмопривода.
Разработан цанговый зажим который служит для автоматического зажима детали и удаления ее после обработки посредством выталкивающей пружины. Цанговый зажим установленный в шпинделе станка работает с помощью вращающегося пневмоцилиндра.
Разработаны автоматические бункерно-загрузочное устройство и автооператор которые обеспечивают нужную ориентацию заготовки в пространстве и передачу её в зону обработки. В качестве приводного механизма также используется пневматика.
Спроектирован автоматизированный привод поперечной подачи работа которого осуществляется посредством гидравлики поскольку применение пневматики в данном механизме не может обеспечить заданный закон движения и стабильность скорости движения выходного звена.
Выполнены все необходимые расчеты предусмотренные методическими указаниями по выполнению дипломного проекта.
Представлен рабочий маршрутно-технологический процесс детали 408-6104036-10 «валик стеклоподъемника».
Произведен расчет экономического эффекта от производства и эксплуатации проектируемого автомата.
В соответствии с заданием по охране труда обеспечены все требования безопасности при разработке нового оборудования.
Анурьев В.И. Справочник конструктора – машиностроителя: В 3 т. М. 1979 – 1982. т. 1 – 728 с. т.2 – 559 с. т. 3 – 557 с.
Безопасность технологических процессов и производств: Охрана труда: Учебн. пособие для вузов. Кукин П.П. Лапин В.Л. и др. – Мн.: Выш.школа 2001. – 320 с. ил.
Бобров В.П. Проектирование загрузочно-транспортных устройств. –М.: Машиностроение 1964. – 291с.: ил.
Волкевич Л.И. Усов Б.А. Автооператоры – М.: Машиностроение 1963. – 299 с.: ил.
В помощь конструктору – станкостроителю В.И. Калинин В.Н. Никифоров Н.Я. Аникеев и др. М.: Машиностроение 1983. – 288 с. ил.
Выбор конструкции и расчет шпиндельных узлов металлорежущих станков: Методические указания. ч.2 Ижевск. мех. ин-т; Сост. В.В. Пузанов Ф.Ю. Свитковский. Ижевск 1990. 32с.
Выбор двигателей приводов станков: Методические указания. ч.2 Ижевск. мех. ин-т; Сост. В.В. Пузанов Ф.Ю. Свитковский. Ижевск 1990.
Гидравлика гидромашины и гидропроводы: Учебник для машиностроительных вузов Т.М. Башта С.С. Руднев Б.Б. Некрасов и др. – 2-е изд. перераб. и доп. – М.: Машиностроение 1982. – 423с. ил.
Гидроприводы и гидропневмоавтоматика станков: Метод. указания к курсовому проектированию (для специальностей 1201. 1202) Ижевск. мех. ин-т; Сост. Б.Н. Зенков. Ижевск 1990 36 с.
Гидроприводы и гидропневмоавтоматика станков: Метод. руководство для самостоятельного изучения общих сведений технической гидромеханики гидропривода и гидропневмоавтоматики станков. ч.5. Элементы пневмоаппаратуры высокого давления (для специальностей 1201 1202) Ижевск. мех. ин-т; Сост. Б.Н. Зенков Р.С. Музафаров. Ижевск 1993.
Горбацевич А.Ф. Шкред В.А. – Курсовое проектирование по технологии машиностроения: [Учебное пособие для машиностроит. спец. вузов]. – 4-е изд. перераб. и доп. – Мн.: Выш.школа 1983. – 256 с. ил.
Горошкин А.К. – Приспособление для металлорежущих станков: Справочник. – 7-е изд. перераб. и доп. – М.: Машиностроение 1979. – 303 с. ил.
Иванов М.Н. Детали машин. М. 1984. 399 с.
Кочергин А.И. Конструирование и расчет металлорежущих станков и станочных комплексов. Курсовое проектирование: Учебн. пособие для вузов. – Мн.; Выш. шк. 1991. – 382.; ил.
Кузнецов Ю.И. Маслов А.Р. Байков А.Н. Оснастка для станков с ЧПУ: Справочник. – М.: Машиностроение 1983. – 359 с.: ил.
Кучер И.М. и Кучер А.М.- Модернизация и автоматизация станков – Л.: Машгиз 1958. – 299 с.: ил.
Малов А.Н. Загрузочные устройства для металлорежущих станков. – М.: Машиностроение 1979. – 399 с.: ил.
Медвидь М.Н. Автоматические ориентирующие загрузочные устройства. – М.: Машиностроение 1963. – 299 с.: ил.
Металлорежущие станки Н.С. Ачеркан. В 2-х т.; Под ред. Н.С. Ачеркана. – 2-е изд. перераб. и доп. – М.: Машиностроение 1965. – 764 с.: ил.
Методические указания к дипломному проектированию по металлорежущим станкам и металлорежущему инструменту Ижевск. мех. ин-т; Сост. В.В. Пузанов А.А. Модзелевский Ю.Г. Глухов. Ижевск 1983.
Методические указания к лабораторной работе «Реализация цикла движений узлов станка с ЧПУ модели 1И611ПФЗ средствами гидроавтоматики» Ижевск. мех. ин-т; Сост. В.Ф. Иванов Р.С. Музафаров. Ижевск 1989.
Методические указания по кинематическому расчету приводов станков и построению их кинематических схем. Ижевск. мех. ин-т; Сост. В.В. Пузанов Ижевск 1989.
Методические указания по проведению патентных исследований при курсовом и дипломном проектировании по металлорежущим станкам и инструментам. Ижевск. мех. ин-т; Сост. А.И. Хватов Ижевск 1986.
Методические указания по расчету экономического эффекта при разработке металлорежущего оборудования в процессе дипломного проектирования студентов специальности 12.02 Ижевск. мех. ин-т; Сост. А.С. Севрюгин. Ижевск 1991. 20с.
Общемашиностроительные нормативы времени для нормирования многостаночных работ на металлорежущих станках. М.: Экономика1997.
Оформление расчетно-пояснительных записок к курсовому и дипломному проектам: Методические указания для студентов заочного обучения Ижевск. мех. ин-т; Сост. Ф.Ю. Свитковский. Ижевск 1989 16 с.
Охрана труда в машиностроении: Учебник для машиностроительных вузов Е.Я. Юдин С.В. Белов С.К. Баланцев и др.; Под. ред. Е.Я.Юдина С.В.Белова – 2 -е изд. перераб. и доп.-М.: Машиностроение 1983. – 432 с. ил.
Проектирование металлорежущих станков и станочных систем: Справочник-учебник. В 3-х т. Т.2. Расчет и конструирование узлов и элементов станков А.С. Проников Е.И. Борисов В.В. Бушуев и др.; Под общ. ред. А.С. Проникова. – М.: Издательство МГТУ им. Баумана: Машиностроение 1995. – 371 с.: ил.
Проектирование механических передач: Учебно-справочное пособие для втузов С.А. Чернавский Г.А. Снесарев Б.С. Козинцов и др. – 5-е изд. перераб. и доп. – М.: Машиностроение 1984. – 560 с. ил.
Расчеты экономической эффективности новой техники: Справочник Под ред. К.М. Великанова – Л .: Машиностроение. Ленингр. отд-ние 1990. – 439 с.: ил.
Решетов Д.Н. Учебник для студентов машиностроительных и механических специальностей вузов. – 4-е изд. прераб. и доп. М.: Машиностроение 1989. – 496с.: ил.
Свешников В.К. Усов А.А. Станочные гидроприводы: Справочник. – М.: Машиностроение 1982. – 464 с. ил.
Свирщевский Ю. И. Расчет и конструирование коробок и скоростей подач. Минск.:Высшая школа. 1976. – 590 с.ил.
Соколов Н.Г. и Елисеев В.А. Расчеты по автоматизированному электроприводу металлорежущих станков. М. «Высшая школа» 1969. 296 с.
Справочник нормировщика Под. общ. ред. А.В. Ахумова. Л.: Машиностроение. Ленингр. отд-ние 1986.
Справочник технолога-машиностроителя. В 2-х т. Т. 2Под ред. А.Г. Косиловой и Р.К. Мещерякова. – 4-е изд. перераб. и доп. – М.: Машиностроение1986. 496с. ил.
Стародуб Н.П. Автоматизция токарной обработки при помощи пневмоустройств. – Мн.: Выш.школа 1979. – 143 с. ил.
Экономика и организация производства в дипломных проектах: Учебник для машиностроительных вузовК.М. Великанов Э.Г. Васильева В.Ф. Власов и др.; Под общ. ред. К.М. Великанова – 4-е изд. перераб. и доп. – Л.: Машиностроение. Ленингр. отд-ние 1982. – 423 с.: ил.