Проектирование коробки скоростей вертикально-сверлильного станка(на базе 2н135)




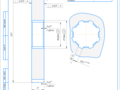
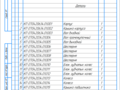
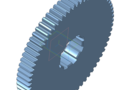
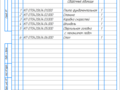
- Добавлен: 24.01.2023
- Размер: 10 MB
- Закачек: 1
Описание
Проектирование коробки скоростей вертикально-сверлильного станка(на базе 2н135)
Состав проекта
![]() |
![]() |
![]() |
![]() ![]() ![]() ![]() |
![]() ![]() ![]() ![]() |
![]() ![]() ![]() ![]() |
![]() ![]() ![]() ![]() |
![]() ![]() ![]() ![]() |
![]() ![]() ![]() |
![]() ![]() ![]() ![]() |
![]() ![]() ![]() ![]() |
![]() ![]() ![]() ![]() |
![]() |
![]() |
![]() ![]() |
![]() ![]() |
![]() ![]() |
![]() ![]() |
![]() |
![]() ![]() |
![]() ![]() |
![]() ![]() |
![]() |
![]() ![]() |
![]() ![]() |
![]() |
![]() ![]() |
![]() ![]() |
![]() ![]() |
![]() ![]() |
![]() ![]() |
![]() ![]() |
![]() ![]() ![]() ![]() |
![]() ![]() |
![]() ![]() ![]() ![]() |
![]() ![]() |
![]() ![]() |
![]() ![]() |
![]() ![]() |
![]() ![]() |
![]() |
![]() ![]() |
![]() ![]() |
![]() ![]() |
![]() ![]() |
![]() ![]() |
![]() ![]() |
![]() ![]() |
![]() ![]() |
![]() ![]() |
![]() ![]() |
![]() |
![]() |
![]() |
![]() ![]() |
![]() ![]() |
![]() ![]() |
![]() ![]() |
![]() ![]() |
![]() ![]() |
![]() ![]() |
![]() ![]() |
![]() ![]() |
![]() ![]() |
![]() ![]() |
![]() |
![]() ![]() |
![]() ![]() |
![]() ![]() |
![]() ![]() |
![]() ![]() |
![]() ![]() |
![]() ![]() |
![]() ![]() |
![]() ![]() |
![]() ![]() |
![]() ![]() |
![]() ![]() |
![]() |
![]() ![]() ![]() |
![]() ![]() ![]() |
![]() ![]() ![]() |
Дополнительная информация
Блок колес А3.cdw

Коэффициент смещения
Обозначение сопряженого
Сталь 40Х ГОСТ 4543-71
Неуказанные пред. откл. размеров: валов -t
Вал промежуточный А3.cdw

Сталь 45 ГОСТ 1050-88
Неуказанные пред. откл. размеров: валов -t
Колесо 12 А3.cdw

Коэффициент смещения
Обозначение сопряженого
Сталь 40Х ГОСТ 4543-71
Неуказанные пред. откл. размеров: валов -t
вид общий.spw

СБ.spw

Болт М10-8g x 18.109.30ХГСА (S16) ГОСТ 15589-70
Болт М10-8g x 50.109.30ХГСА (S16) ГОСТ 15589-70
Кольцо A 34.65Г ГОСТ 13942-86
Кольцо A 72.65Г ГОСТ 13942-86
Манжета 1.1-25 x52-1 4 ГОСТ 8752-79
Подшипник305 ГОСТ 8338-75
Подшипник 1027312А ГОСТ 27365-87
Шпонка 8 x 7 x 18 ГОСТ 23360-78
Шпиндель А2.cdw

Сталь 40Х ГОСТ 4543-71
Неуказанные пред. откл. размеров: валов -t
вид общий А2.cdw

СБ А1.cdw

вал II.m3d

вал IV.m3d

вал III.m3d

вал I.m3d

Кольцо уплотнительное.m3d

Корпуса крышка.m3d

Кольцо уплотнительное Б.m3d

Ремень.m3d

крышка подшипника вх.m3d

шкив 2.m3d

крышка подшипника.m3d

коробка.m3d

Шпиндельный Узел.spw

Подшипник 8214Н ГОСТ 7872-89
Подшипник 1027313А ГОСТ 27365-87
Подшипник 1027314А ГОСТ 27365-87
Чертеж.cdw

Пиноль.m3d

крышка входного вала.m3d

крышка подшипника вых.m3d

шкив 1.m3d

коробка1.m3d

электродвигатель.m3d

Шпиндель Sol.m3d

Шпиндель.m3d

Крышка пиноли.m3d

Шайба.m3d

Кольцо войлочное.m3d

прокладка.m3d

блок z4-z5.m3d

блок z8-z9.m3d

z10.m3d

z3.m3d

z7.m3d

z6.m3d

z1.m3d

z2.m3d

z12.m3d

блок z11-z13.m3d

z14.m3d

ПЗ.docx
Обоснование технической характеристики станка
1 Виды работ выполняемых на Радиально-сверлильных станках
2 Выбор и расчет режимов резания
3. Диапазон регулирования
4. Диапазон регулирования скоростей
5. Диапазон частот вращения шпинделя
6. Расчет мощности привода и выбор электродвигателя
Кинематический расчет привода главного движения
1 Разработка структурной сетки коробки скоростей
2 Разработка кинематической схемы проектируемого станка
3 Построение графика частот вращения шпинделя
4 Определение передаточных отношений и чисел зубьев
5 Определение фактических частот вращения и величин погрешностей
Силовой расчет элементов коробки скоростей
1 Определение момента на валах
2 Расчет модулей зубчатых колес
3 Построение зубчатых колес в среде КОМПАС Shaft и их расчет на прочность.
4 Конструирование и расчет валов
4.1 Определение минимальных диаметров валов
5 Выбор и расчет подшипников на долговечность.
6 Расчет шпоночных и шлицевых соединений на смятие.
Проектирование и расчёт шпиндельного узла
Металлорежущий станок является основой для построения современных технологических систем и автоматизированных производств.
При создании станков используются все достижения машиностроения и приборостроения электротехники и электроники автоматики и информатики.
Поиск новых решений для достижения прецизионности производительности надежности приводит к частой смене моделей станков. Поэтому создатели новой техники должны использовать все достижения науки о станках применять справочные материалы и стандарты для обеспечения высших технических характеристик создаваемых моделей станков.
АНАЛИЗ СУЩЕСТВУЮЩИХ КОНСТРУКЦИЙ И ВЫБОР СТАНКА ПРОТОТИПА.
Проанализировав параметры аналогичных станков в качестве прототипа выбирается станок 2Н135. Так как на нем можно сверлить отверстие согласно заданию (диаметр 35 мм) и он имеет минимальные габариты потребляемую мощность по сравнению с аналогами.
- Наибольший условный диаметр сверления в стали мм - 35
- Рабочая поверхность стола мм – 450 Х 500
- Расстояние от торца шпинделя до рабочей поверхности стола мм – 750
- Вылет шпинделя мм – 300
- Наибольшее вертикальное перемещение (стола) мм – 300
- Конус Морзе отверстия шпинделя – 4
- Число скоростей шпинделя Zv – 12
- Частота вращения шпинделя мин-1 – 31 – 1400
- Число подачи шпинделя Zs – 9
- Подача шпинделя ммоб – 01 – 16
- Мощность электродвигателя привода главного движения кВт – 4
- Габаритные размеры (длина х ширина х высота) мм – 1030 Х 825 Х 2535
ОБОСНОВАНИЕ ТЕХНИЧЕСКОЙ ХАРАКТЕРИСТИКИ СТАНКА.
1 Виды работ выполняемых на станках заданного типа.
Виды работ которые будут выполняться на проектируемом станке аналогичны работам которые выполняются на станке-прототипе а именно: сверление зенкерование и развертывание отверстий в различных деталей торцевания и нарезания резьб.
2 Выбор и расчет режимов резания.
Режимы резания выбираются по таблицам (по экспериментальным данным).
Полученные значения скоростей резания V (ммин) оформляются в виде графика (рис. 1).
Рис. 1. Скорости резания по видам работ
СТАЛЬ (Конструкционная углеродистая и низколегированная ).
Зенкеры твердосплав.
Развертки быстрореж.
Развертки твердосплав.
Развертки конические
Подрезка торцов под головку болта
Зенкеры торцовые и пластины подрезные
И так: Минимальная скорость резания Vmin= 2 ммин
Максимальная скорость резания Vmax= 80 ммин
Определяем частоты вращения шпинделя
Минимальная скорость
Максимальная скорость
где - минимальная скорость при обработке максимального диаметра детали;
- максимальная скорость при обработке минимального диаметра детали.
3. Диапазон регулирования.
Диапазон обрабатываемых деталей:
4. Диапазон регулирования скоростей.
5. Диапазон частот вращения шпинделя.
6. Расчет мощности привода и выбор электродвигателя.
Мощность двигателя в приводе станка расходуется на создание рабочих сил и преодоление различных сопротивлений и определяется по формуле.
где Nэф - полезная мощность.
где Мкр момент кручения
где - поправочные коэффициенты зависящие от вида работы и от материалов; s – подача(0409 ммоб);
Cм=00345; q=2;S=.04;у=08;Кр=08.
Cv=9.8;q=0.4;T=70;y=0.5;m=0.2;Kv=0.8
Расчет мощности электродвигателя:
Исходя из полученных потребностей мощности выбираем электродвигатель 4А100L4У3:
Частота вращения n (мин-1)
КИНЕМАТИЧЕСКИЙ РАСЧЕТ ПРИВОДА ГЛАВНОГО ДВИЖЕНИЯ.
Первой стадией проектирования станка является разработка его кинематической схемы с помощью которой реализуются кинематические связи различных элементов и механизмов станка.
Для передачи движений в станках применяют ременные цепные зубчатые червячные реечные винтовые и другие передачи.
1 Разработка структурной сетки коробки скоростей.
Проанализировав варианты структурных сеток коробок скоростей я остановился на варианте с веерообразном графиком. При применении этого варианта в области высоких частот вращения работает большее число передач. Благодаря этому коробка скоростей будет более компактной. Кроме того небольшие передаточные отношения в области высоких частот вращения шпинделя обеспечивают лучшие условия для работы зубчатых передач т.е. улучшаются динамические показатели станков.
В ходе выполнения курсовой работы была разработана структурная сетка коробки скоростей:
Рис. 2. Структурная сетка
2 Разработка кинематической схемы проектируемого станка.
Выбрав вариант структурной сетки приступают к разработке кинематической схемы привода главного движения станка оставляя остальные цепи без изменения. При этом анализируют кинематическую схему привода главного движения станка-прототипа.
Рис. 3. Кинематическая схема привода
3 Построение графика частот вращения шпинделя.
График частот вращения шпинделя строят в полном соответствии с принятой структурной сеткой и разработанной кинематической схемой проектируемого станка.
4 Определение передаточных отношений и числа зубьев зубчатых колес.
5 Определение фактических частот вращения и величин погрешностей.
СИЛОВОЙ РАСЧЕТ ЭЛЕМЕНТОВ КОРОБКИ СКОРОСТЕЙ.
1 Определение момента на валах.
N=4 кВт; nэ.д.= 1426 обмин.
2.Расчет модулей зубчатых колес.
Модули передач можно рассчитать в программном продукте АРМ Trans
Для расчета потребуются ранее определенные данные таблиц 5 и 6.
Пример расчета z1-z2
Войдя в программу АРМ Trans выбираем: Тип передачи – прямозубое внешнего зацепления;
Тип расчета – Проектировочный; В диалоговом окне «Основные данные» вводим данные для расчета:
в закладке «Еще » вводим числа зубьев передач.
После ввода данных для расчета рассчитываем зубчатую передачу нажатием кнопки .
Полученные результаты вносим в таблицу:
Передаточное отношение i1
Передаточное отношение i6
3.Построение зубчатых колес в среде КОМПАС Shaft и их расчет на прочность.
Пример расчета z3-z4.
Для построения колес потребуются данные таблицы №1. В программе КОМПАС входим «Менеджер библиотек - Расчет и построение – КОМПАС SHAFT 2D – Построение модели».
В элементах механических передач выбираем: Шестерня цилиндрической зубчатой передачи – Запуск расчета – Геометрический расчет – По межосевому расстоянию». В диалоговом окне «Геометрический расчет; закладка Станица 1» вводим требующиеся для расчета данные:
На закладке «Страница 2» производим расчет передачи кнопкой затем заканчиваем расчеты и выбираем объект построения передачи:
Для расчета зубчатых колес на прочность необходимо в «Страница 2» нажатием вернуться в главное окно где станет активен «Расчет на прочность». При вводе данных задаем максимальную нагрузку. Выбираем материал схему расположения передачи а так же задаемся расчетной нагрузкой и числом оборотов на ведущем колесе.
4.Конструирование и расчет валов.
4.1 Определение минимальных диаметров валов.
Минимальный диаметр валов находится по формуле:
После расчетов согласно справочника 3 с.17 принимаем минимальные диаметры валов:
вал: 175 мм (Диаметр подшипника 25)
вал: 1685 мм (Диаметр под подшипник 25 мм)
вал: 183 мм (Диаметр под подшипник 28 мм)
Пример расчета вала №3
После сборки колес в среде КОМПАС геометрические параметры вала можно определить конструируя его «по месту» в сечении самой сборки. После окончательного построения вала требуется произвести проверочный расчет
Проверочный расчет валов коробки скоростей рассчитывается в программном продукте АРМ Shaft.
На рабочем поле операцией «Цилиндр» выстраивается конструкция рассчитываемого вала задаются опоры. С помощью инструментальной панели расставляются силы и моменты кручения в точке их приложения по расчетной цепи:
Во вкладке Материал выбираем конструкционную сталь Ст45 используемую для изготовления валов. В команде «Рассчитать – Общий расчет вала » вводим частоту вращения вала и задаемся ресурсом работы изделия и во вкладке Результаты просматриваем интересующие нас рассчитанные программой характеристики по результатам расчета которых оценивается вал.
Перемещения в вертикальной плоскости
Коэффициент запаса по усталостной прочности
5.Выбор и расчет подшипников на долговечность.
Расчет подшипников можно реализовать в программном продукте АРМ Bear.
Требуемая долговечность подшипника [Lh] = 20000 часов.
Расчет на долговечность подшипников 305 ГОСТ 8338-75.
Для пар подшипников рассчитывается один наиболее нагруженный подшипник.
Подшипники 305 ГОСТ 8338-75 находятся на первом ичетвёртом валу коробки скоростей. В строке состояния АРМ Bear находится вкладка «Данные» в нее последовательно вводим требующиеся для расчета параметры:
Выбираем тип подшипника – «Радиальный подшипник – Тип установки одиночный»
В строке «Геометрия » с помощью имеющихся баз данных выбираем требуемый подшипник. Характеристика рассчитываемого подшипника автоматически выводиться в диалоговое окно:
Затем во вкладке «Условия работы » вводим следующие данные
Рассчитываем и выводим результаты расчета .
Условие выбора подшипников при расчете на долговечность:
Подшипник принимается в том случае если его долговечность больше требуемой т.е.: [Lh]Lh. В нашем случае рассчитанная долговечность выполняет заданное условие:
[Lh] = 20000 часов Lh = 21134454часов.
Аналогично рассчитываются и другие подшипники коробки скоростей.
Все подшипники коробки скоростей согласны условию [Lh]Lh.
27312А ГОСТ 27365-87
6.Расчет шпоночных и шлицевых соединений на смятие.
Шлицевое соединения можно рассчитать в программном продукте . АРМ Joint
Задаем тип соединения и вводим данные:
Производим расчет соединения. Программа предлагает возможные варианты шлицевых соединений которые можно применить в конструкции.
По предложенным результатам выберем шлицевое соединение средней серии.
ПРОЕКТИРОВАНИЕ И РАСЧЁТ ШПИНДЕЛЬНОГО УЗЛА.
Шпиндель расчитываем при помощи метода конечных элементов.
Метод конечных элементов – численный метод. Относится к исследованию сложных систем по частям (диакоптика). Вариационный метод – частный случай метода Ритца..
Анализ проводим в среде – COSMOSWorks. Программа COSMOS Works полностью интегрирована с программой трехмерного моделирования SolidWorks. COSMOS Works применяется для решение задач по нахождению напряжений смещений деформаций температурных полей и оптимизации. Используя COSMOSFFE (Быстрые Конечные Элементы) технологию COSMOS Works позволяет решать сложные инженерные задачи на персональных компьютерах. Оптимизация применяется для поиска оптимальной разработки удовлетворяющей определенным требованиям.
Программа может выполнить:
Линейный статический анализ чтобы вычислять смещения деформации и напряжения;
Линеаризированный анализ продольного изгиба (выпуклый) для вычисления критических нагрузок продольного изгиба и соответствующих форм;
Частотный анализ для вычисления резонансных частот и соответствующих форм колебаний;
Анализ установившихся и переходных состояний термических процессов для вычисления температуры температурные градиенты и изменения потоков тепла;
Оптимизационное проектирование;
Расширенный динамический анализ линейных систем с различными видами нагрузок во времени и частотами воздействия;
Нелинейный статическийдинамический анализ;
Расчет потоков жидкости;
Низкочастотный анализ электромагнитных систем;
Высокочастотный анализ электромагнитных систем;
Оптимизация с использованием
Процесс дискретизации формы детали (разбиение на элементы) выполняется в автоматическом режиме.
Программа анализа методом конечных элементов создает математическую модель объекта таким образом что можно имитировать поведение объекта в его рабочей среде. Метод конечных элементов моделирует геометрию модели и ее материалы а также встречающиеся нагрузки и ограничения. В процессе анализа модели автоматически создается система уравнений решение которой дает информацию о поведении модели под нагрузкой. Можно представить результаты в графических или табличных форматах.
Для анализа шпинделя необходимо его модель полученная средствами КОМПАС импортировать в стреду COSMOS Works для этого используем формат Parasolid. После импортирования детали расставляем опоры и нагрузки. После чего выбираем материал из которого будет изготовлен шпиндель и получаем сетку на твердом теле.
Рис. 18 Запас прочности
В ходе курсового проекта произвели необходимые расчеты при проектировании заданного технологического металлообрабатывающего оборудования (станка); проанализировали существующие конструкции аналогичных станков и выбрали из них станок-прототип; обосновали техническую характеристику станка; произвели кинематический расчет привода главного движения и расчет основных деталей привода; выбрали схему шпиндельного узла и произвели расчеты его основных параметров.
По расчетным данным вычертили развертку коробки скоростей шпиндельный узел и деталировку нескольких деталей. За общий вид проектируемого станка принимается общий вид станка-прототипа.
СПИСОК ИСПОЛЬЗОВАННЫХ ИСТОЧНИКОВ
«Проектирование технологического металлообрабатывающего оборудования»: метод. указ. к выполнению курсового проекта Сост. Н.А. Кутний. – Хабаровск: Изд-во Хабар. гос. техн. ун-та 2002. – 79с.
Справочник технолога-машиностроителя. В 2-х т. Под ред. А.Г. Косиловой и Р.К. Мещерякова. – М.: Машиностроение 1985. 496 с.
«Расчет режимов резания»: метод. указ. по курсовому проекту по металлорежущим станкам Сост. В.В. Жуловян. – ХПИ. Хабаровск 1992.
Биргер И. А. Шорр Б. Ф. Шнейдерович Р. И. Расчет на прочность деталей машин: Справочное пособие.- М. 1966. – 616 с.
Детали и механизмы металлорежущих станков Под ред. Д. Н. Решетова: В 2 т. – М. 1972. Т. 2. – 520 с.
Детали машин: Атлас конструкций Под ред. Д. Н. Решетова. – М. 1979. – 367 с.
Кучер И. М. Металлорежущие станки. Основы конструирования и расчета. – Л. 1969. – 720 с.
Лизогуб В. А. Конструирование и расчет шпиндельных узлов направляющих и механизмов подач металлорежущих станков: Учеб. пособие. – М. 1985. – 90 с.
Подшипники качения: Справочник-каталог Под ред. В. Н Нарышкина Р.В. Коросташевского. – М. 1984. – 280 с.
Проектирование металлорежущих станков и станочных систем: Справочник-учебник Под ред. А. А. Проникова: В 3 т. – М.1998. Т. 1. – 444 с.
Реферат.DOC
СТАНОК УЗЕЛ ШПИНДЕЛЬНЫЙ ВАЛ ОСЬ КОЛЕСО ПОДШИПНИК ПОСАДКА МОДУЛЬ БОЛТ ГАЙКА КОРОБКА СКОРОСТЕЙ КРЫШКА.
Целью курсового проекта является проектирование основных узлов станка: коробки скоростей шпиндельного узла. Указанная цель достигается выполнением расчетов режимов резания кинематического расчета расчетом основных деталей привода и изображение их на чертежах. Использованы наиболее простые и удобные в изготовлении детали. Проведен анализ различных кинематических схем коробки скоростей.
Титульный.doc
Государственное образовательное учреждение высшего профессионального образования «Тихоокеанский государственный университет»
Кафедра «Компьютерное Проектирование и Сертификация Машин»
СТАНОК ВЕРТИКАЛЬНО-СВЕРЛИЛЬНЫЙ
Расчетно-пояснительная записка к курсовому проекту
по дисциплине «Системы автоматизированного проектирования»
КП 070420634.00.000 ПЗ
Сарапкин Андрей Анатольевич
Руководитель проекта:
Кулик Виктор Иванович