Проектирование вертикально-сверлильного станка




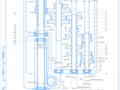
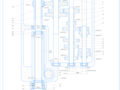
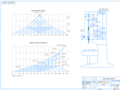
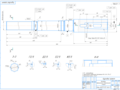
- Добавлен: 25.01.2023
- Размер: 1 MB
- Закачек: 0
Описание
Состав проекта
![]() |
![]() |
![]() |
![]() ![]() ![]() ![]() |
![]() |
![]() ![]() ![]() ![]() |
![]() ![]() |
![]() ![]() ![]() ![]() |
![]() ![]() ![]() ![]() |
![]() ![]() ![]() |
![]() ![]() |
![]() |
Дополнительная информация
Чертеж шпинделя.cdw

Сталь 40Х2ГМ ГОСТ 4543-71
Конус Морзе №4 ГОСТ 24644-81
Неуказанные предельные отклонения H14
Коробка скоростей (уменьшеная).cdw

D8x32x36H7js6x6F8js6
D8x36x40H7js6x7F8js6
После сборки коробку обкатать в течение
Температура нагрева подшипников не более 50
В коробку скоростей залить масло
И-Г-С-46 ГОСТ 17479.8-87
Покрыть нерабочие поверхности эмалью серой
ХС-710 ГОСТ 9.032-74
вертикально-сверлильного
Допуск радиального биения шпинделя 0.006
Уровень шума не более 80дБ
Допуск осевого биения шпинделя 0.010
Точность зубчатых передач 7-В
Коробка скоростей.cdw

Кинематическая схема.cdw

вертикально-сверлильного
График частот вращения
МРС записка.docx
Описание служебного назначения проектируемого станка .5
Выбор станка аналога ..6
Определение технических характеристик главного привода .7
1 Расчет режимов резания 7
2 Выбор электродвигателя .10
Разработка кинематической схемы ..11
1 Выбор структурной сетки .. .11
2 Кинематическая схема коробки скоростей.. .13
3 График чисел оборотов . .14
4 Определение передаточных отношений 14
5. Определение количества зубьев зубчатых колес ..14
6. Расчет действительных значений частоты вращения ..15
7. Расчет погрешности частоты вращения .15
Расчет на прочность элементов привода 17
1. Определение КПД привода 17
2. Определение мощностей на валах 17
3. Определение крутящих моментов на валах .17
4. Определение параметров зубчатых колес ..17
4.1. Расчет модуля ..17
4.2 Определение геометрических параметров зубчатых колес .18
5 Проверочный расчет 21
5.1 Проверка контактных напряжений 21
5.2 Проверка напряжений изгиба зубьев ..23
6 Нагрузка валов .26
6.1 Предварительный расчет валов на кручение .26
6.2 Определение сил в зацеплении 27
6.3 Выбор подшипников качения .28
6.4 Уточненный расчет валов 29
6.5 Проверка шпоночных соединений 30
6.6 Проверка шлицевых соединений 30
Описание разработанной конструкции ..34
Список используемой литературы .36
Служебное назначение
Вертикально-сверлильный станок используется для сверления отверстий диаметром от 5 до 40 мм в деталях относительно небольшого размера в условиях единичного и мелкосерийного производства.
Мощность двигателя Pдв=2 кВт максимальное число оборотов шпинделя nmax=1600 обмин φ=126.
Станок предназначен для обработки деталей из стали HB≤240 и серого чугуна HB≤190. Класс точности станка – Н. Материал режущего инструмента - быстрорежущие стали твердосплавной инструмент не используется т.к. мощность резания превышает мощность двигателя.
Станок предназначен для работы в умеренном климате при:
- температуре окружающего воздуха +50С +250С;
-влажности не более 50-70%;
-уровнь запыленности 5-6 мгсм3.
Выбор станка аналога
Сверлильный станок 2Т140 предназначен для
Обработка на вертикально-сверлильных станках 2Т140 производится как с ручной так и с механической подачей шпинделя. На станках допускается нарезание резьб с ручным управлением реверсирования шпинделя и в автоматическом режиме.
Наиболее эффективно станки 2Т140 можно использовать в условиях индивидуального и мелкосерийного производства а при соответствующем оснащении - в крупносерийном и массовом.
Таблица 2.1. Технические данные и характеристики вертикального сверлильного станка
Наибольший условный диаметр сверления мм в стали
Наибольший диаметр нарезаемой резьбы в стали
Расстояние от оси шпинделя до
образующей колонны (вылет) мм
Наибольшее перемещение шпинделя мм
Расстояние от торца шпинделя до стола мм
Наибольшее расстояние от торца шпинделя до плиты мм
Наибольшее перемещение сверлильной головки мм
Наибольшее перемещение стола мм
Размеры рабочей поверхности мм:
Количество скоростей шпинделя
Пределы частот вращения шпинделя обмин
Количество подач шпинделя
Величина подач шпинделя ммоб
Мощность привода главного движения кВт
Габариты станка (LxBxH) мм не более
Масса станка с охлаждением кг не более
Определение технических характеристик главного привода
1. Расчет режимов резания
Таблица 3.1.Расчет режимов резания [5]
Режимы резания по стали НВ≤203
Спиральные сверла с режущей частью из быстрорежущей стали d=5
Спиральные сверла с режущей частью из быстрорежущей стали d=40
Черновое зенкерование
Зенкер из быстрорежущей стали d=40
Получистовое зенкерование
Черновое развертывание
Развертка черновая из быстрорежущей стали d=40
Чистовое развертывание
Развертка чистовая из быстрорежущей стали d=40
Режимы резания по серому чугуну НВ≤190
Спиральные сверла с режущей частью из твердого сплава d=5
Спиральные сверла с режущей частью из твердого сплава d=40
По нормали Н11-1 скорость шпинделя принимает следующие значения:
2. Выбор электродвигателя
Выбираем асинхронный двигатель АИР90L4:
Габаритные размеры мм
Установочные размеры мм
Разработка кинематической схемы
1. Выбор структурной сетки
Вариант 1 – Z=16=40×21×22
Вариант 2 – Z=16=40×22×21
Вариант 3 – Z=16=21×22×40
Вариант 4 – Z=16=22×40×21
Вариант 5 – Z=16=22×21×40
Вариант 6 – Z=14=21×40×22
Из предложенных вариантов выбираем первый так как по этой структурной сетке снижение передаточного отношения происходит наиболее плавно.
2. Кинематическая схема коробки скоростей
3. График чисел оборотов
4. Определение передаточных отношений.
5. Определение количества зубьев зубчатых колес
Для i=07 Sz=51 – 2130.
Для первой группы Sz=104:
Для второй группы Sz=74:
Для третьей группы Sz=85:
6. Расчет действительных значений частоты вращения
7. Расчет погрешности частоты вращения
Расчет на прочность элементов привода
1. Определение КПД привода
– среднее значение КПД зубчатой передачи;
– среднее значение КПД подшипников;
– число зубчатых передач;
γ – число подшипников;
2. Определение мощностей на валах
3. Определение крутящих моментов на валах
4. Определение параметров зубчатых колес
Полученные значения округляем до стандартного по ГОСТ 9563-60.
Принимаем материал сталь 20Х.
Вид термообработки – цементация с закалкой.
Предел выносливости зубьев lim b=1300 (Мпа)
Колеса 5252 4658 4064 3569:
4.2. Расчет геометрических параметров зубчатых колес
5 Проверочный расчет
5.1 Проверка контактных напряжений
К=436 – вспомогательный коэффициент (для прямозубых колес) [4];
- окружная сила в зацеплении;
– коэффициент учитывающий распределение нагрузки между зубьями (для прямозубых колес);
– коэффициент неравномерности нагрузки по длине;
5.2 Проверка напряжений изгиба зубьев
и - коэффициенты формы зуба колеса и шестерни [4];
6.1 Предварительный расчет валов на кручение
В качестве материала для валов применяется Сталь 45 термическая обработка - улучшение.
Проверочный расчет валов выполняется по напряжениям кручения т. е. при этом не учитываются напряжения изгиба концентрации напряжений и переменность напряжений во времени. Поэтому допускаемые напряжения на кручение применяются заниженными: . Результатом является минимальное значение диаметра вала [4]. Полученные значения диаметров валов округляем до нормальных линейных размеров по ГОСТ 6636-69.
Примем диаметр вала по стандартному ряду dв1=30 мм.
Диаметр вала под блок колес dбк2=30 (шлица 6х26х30 ГОСТ 1139-80).
Диаметр вала примем dв2=30 мм.
Диаметр вала примем dв3=36 мм.
Диаметр вала под блок колес dбк4=36 (шлица 8х32х36 ГОСТ 1139-80).
Диаметр вала dв4=40 мм (шлица 8х36х40 ГОСТ 1139-80).
6.2. Определение сил в зацеплении
6.3 Выбор подшипников качения
Схема нагружения валов
Rb =( F2*ad-F1*ac )ab
По максимальному значению найденной силы определяется пригодность подшипника
Rb=(398077*290-4867*22)545= 1922 Н
Ra=398077-4867+1922=1036 Н
3610000 10000Н-грузоподъемность по ГОСТ 8388-75;
Принимаются подшипники 205 ГОСТ 8388-75
Ra=605Н;60511000 Принимаются подшипники 205 ГОСТ 8388-75
Ra=2523Н;252311000 Принимаются подшипники 206 ГОСТ 8388-75
Ra=8544Н; 85443122800 Принимаются подшипники 212 ГОСТ 8388-75
6.4. Уточненный расчет валов
Уточненный расчет валов производится на ЭВМ с помощью программы «VAL»
Исходными данными для расчета служат:
Материал вала и []: Сталь45 в=640МПа т=350МПа;
Термообработка вала: улучшение НВ200;
Вид концентратора напряжения в опасном сечении;
Параметры концентратора напряжения;
Суммарный запас статической прочности
Суммарный запас усталостной прочности
6.5 Проверка шпоночных соединений
Шпонка 7х7х16 (вал двигателя)
Шпонка 6х6х18 (1й вал)
6.6 Проверка шлицевых соединений
-расчетная поверхность смятия;
В целях защиты от коррозии снижения коэффициента трения отвода тепла и продуктов износа от трущихся поверхностей применяется смазка.
Смазывание коробки скоростей:
Т. К. зубчатые зацепления в коробке скоростей работают при больших окружных скоростях при тяжелых условиях работы то для смазывания следует применить масло И-Г-С-46 ГОСТ 17479.8-87 [2]
Смазывание шпиндельного устройства:
Т.к. станок расположен вертикально то шпиндель смазывается солидолом жировой (ГОСТ 1033-79) [1].
Описание разработанной конструкции
В проектируемой коробке скоростей применяется 3-фазный асинхронный электродвигатель АИР90L4 с синхронной частотой вращения 1500 обмин и следующими характеристиками Рном=22кВт nном=1425 обмин.
Передача движения от двигателя на коробку скоростей осуществляется с помощью пары зубчатых колес .
Данный привод главного движения является нераздельным приводом со ступенчатым регулированием и последовательно соединенными групповыми передачами.
В ходе выполнения курсового проекта был проведен анализ назначения и условий работы проектируемого станка наиболее рациональные конструктивные решения с учетом технологических монтажных эксплуатационных и экономических требований; кинематические расчеты ;
определение сил действующих на детали и узлы; расчеты конструкции на прочность; выбор материалов.
Список используемой литературы
Кочергин А. И. Конструирование и расчет металлорежущих станков и станочных комплексов А. И. Кочергин. – Минск: Высш. шк. 1991.
Колесов М. И. Основы технологии машиностроения: учебник для машиностроительных вузов М. И. Колесов. – М.: Машиностроение1988.
Курсовое проектирование деталей машин: Учебное пособие С. А. Чернавский К. Н. Боков [и др.]. – М.:ООО ТИД «Альянс» 2005.– 416 с.
Шейнблит А. Е. Курсовое проектирование деталей машин: Учеб.пособие.Изд-е 2-е перераб. и дополн. – Калининград: Янтар. Сказ 2002. – 454 с.:ил. черт. – Б.ц.
Общемашиностроительные нормативы режимов резания
Рекомендуемые чертежи
- 07.06.2021
Свободное скачивание на сегодня
- 23.02.2023