Проектирование коробки скоростей радиально-сверлильного станка




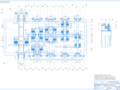
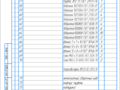
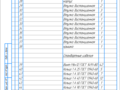
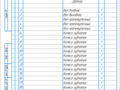
- Добавлен: 25.01.2023
- Размер: 1020 KB
- Закачек: 0
Описание
Проектирование коробки скоростей радиально-сверлильного станка
Состав проекта
![]() |
![]() |
![]() ![]() ![]() ![]() |
![]() ![]() ![]() |
![]() ![]() ![]() |
![]() |
![]() |
![]() |
![]() |
![]() |
![]() |
![]() |
![]() |
![]() |
![]() |
![]() |
![]() |
![]() |
![]() ![]() ![]() ![]() |
![]() ![]() ![]() ![]() |
![]() ![]() ![]() ![]() |
![]() ![]() ![]() ![]() |
![]() ![]() ![]() ![]() |
Дополнительная информация
L2.cdw

Специф 2.cdw

Специф 3.cdw

L1.cdw

Специф 1.cdw

L3.cdw

Рекомендуемые чертежи
- 29.05.2015