Модернизация привода движения подач вертикально-сверлильного станка модели 2С132




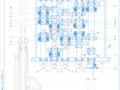

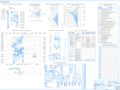
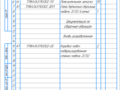
- Добавлен: 25.01.2023
- Размер: 1 MB
- Закачек: 4
Описание
Состав проекта
![]() |
![]() ![]() ![]() ![]() |
![]() ![]() ![]() |
![]() ![]() ![]() |
![]() ![]() ![]() ![]() |
![]() ![]() ![]() ![]() |
![]() ![]() ![]() |
![]() ![]() ![]() ![]() |
![]() ![]() ![]() ![]() |
![]() ![]() ![]() |
Дополнительная информация
1 лист.cdw

Конденсатор К50-31-300-22
Выключатель автоматический AK63-3
Предохранитель ПРС-6П
Реле тепловое ТРН-10
Пускатель электромагнитный ПМЕ
Пускатель электромагнитный ПМЕ-111
Пускатель электромагнитный ПМЕ-211
Реле электромагнитное РЭН-18
Резистор МЛТ-2-100 Ом
Кнопка управления КЕ
Выключатель кулачковый
Микровыключатель МП2102
Разъем штепсельный ШР48
Таблица 2 - Перечень элементов принципиальной
График чисел подач движения
подач станка до модернизации
вертикально-сверлильный
Структурная сетка после модернизации станка
График чисел подач после модернизации станка
Кинематическая схема привода подач до модернизации
Кинематическая схема станка после модернизации
Таблица 1 - Места смазки станка
Принципиальная электрическая схема
Общий вид станка с указанием мест смазки
Порядок включения электромуфт
Реферат.doc
Объект исследования и разработки - Привод движения подач вертикально-сверлильного станка модели 2С132. Цель курсового проекта - разработать подтвердить расчетами и выполнить модернизацию привода движения подач.
Проведен анализ конструкции станка прототипа выполнен кинематический расчет привода движения подач рассчитаны действительные числа подач; произведен расчет модулей зубчатых передач выполнена их проверка. Рассчитаны и проверены на прочность валы коробки подач выбраны шпоночные соединения.
Записка готовая.doc
Целью данного курсового проекта является модернизация привода главного движения подач вертикально-сверлильного станка модели 2С132 на основе критериев надежности и долговечности простоты управления и обслуживания. Модернизация коробки подач позволит расширить технологические возможности станка за счёт более точного подбора требуемой подачи при обработке заготовок что позволит более рационально использовать загрузку станка увеличить срок службы инструмента.
Назначение технологические возможности станка 2С132
1 Технологические возможности станка
Предложенный для модернизации станок 2С132 является вертикально сверлильным станком позволяющим обрабатывать отверстия различной формы мерным режущим инструментом. На станке возможна реализация следующих операций механической обработки:
нарезание внутренней резьбы метчиками
Кроме того технологические возможности станка могут быть расширены применением специального вспомогательного инструмента позволяющего например обрабатывать канавки в отверстиях фасонные пазы сферические поверхности и т.п.
Комплексная деталь с характерными для данного станка обрабатываемыми поверхностями представлена на рисунке 1.1.
Рисунок 1 – Эскиз представительной детали станка 2С132
2 Техническая характеристика станка 2С132
Основные параметры и размеры станка приведены в таблице 1.
Таблица 1 – Основные параметры и размеры станка
Параметр технической характеристики
Наибольший диаметр сверления по мягкой стали Сталь 45 ГОСТ 1050-88 мм
Наибольший ход шпинделя мм
Наибольшее расстояние от конца шпинделя до рабочей поверхности стола мм
Размер конуса шпинделя по ГОСТ 2847-67
Количество частот вращения шпинделя
Пределы частот вращения шпинделя в минуту
Наибольшее усилие подачи кГс
Подача шпинделя ммоб
Наибольшее перемещение стола мм
Габариты рабочего стола мм
Габаритные размеры станка мм
Мощность привода главного движения кВт
Анализ компоновки и кинематика разрабатываемого привода станка-прототипа его структурная формула график чисел подач система управления.
Компоновка станка представляет собой компоновку типа кронштейн что характерно для сверлильных станков. Компоновка вертикально-сверлильного станка 2С132 представлена на рисунке 2.
Рисунок 2 – Компоновка станка 2С132
На жестком основании станка закреплена вертикальная колонна 5. По направляющим колонны типа ласточкин хвост перемещается сверлильная головка 10 и подъёмный стол. На фундаментной плите внутри колонны установлен электронасос. Фундаментная плита является резервуаром для охлаждения жидкости. Коробка скоростей 2 получает вращение от вертикально расположенного электродвигателя. Переключение скоростей производится рукояткой 6 которая в зависимости от конструкции имеет четыре или пять положений по окружности и три вдоль оси. Коробка подач 4 смонтирована в отдельном корпусе и располагается в сверлильной головке. Сверлильная головка представляет собой чугунную отливку коробчатой формы в которой монтируются все основные сборочные единицы станка: коробка скоростей подач механизм подачи шпиндель противовес шпинделя механизм переключения скоростей и подач.
Спецификация основных узлов станка приведена в таблице 2.
Таблица 2 – Спецификация основных узлов станка
Механизм управления скоростями и подачами
Привод главного движения подач вертикально-сверлильного станка 2С132 состоит из:
- источника движения;
- множительной части (коробка подач);
Движение вращения от вала электродвигателя передается через постоянную передачу 3244 на входной вал коробки скоростей. Далее вращение передается через множительную часть коробки скоростей на шпиндель который в свою очередь передает вращение в коробку подач. С выходного вала коробки подач через червячную передачу крутящий момент передается на реечный механизм который передает возвратно-поступательное движение шпинделю.
Структура привода станка-прототипа – множительная.
Структурная формула имеет вид:
где φ определяется исходя из диапазона регулирования.
Диапазон регулирования станка-прототипа определяется по формуле 1
Определяется j - показатель геометрического ряда по формуле 1
где R – диапазон регулирования;
Z – число частот вращения.
График подач показан на рисунке 3.
Рисунок 3 – График частот вращения до модернизации
Кинематический расчет привода
1 Определение показателя геометрического ряда частоты вращения шпинделя.
С учетом большого числа передач (Z=19) показатель геометрического ряда принимается равным
2 Выбор электродвигателя привода главного движения
Приводом главного движения модифицированного станка является асинхронный двигатель с мощностью Nдв.=4 кВт из прототипа.
Исходя из задания на курсовой проект выбирают в качестве привода главного движения электродвигатель марки 4А100S2У3 основные характеристики которого приведены в таблице 3.
Таблица 3 – Основные характеристики двигателя 4А100S2У3
Частота вращения вала
Номинальное напряжение В
3 Определение оптимальной структурной формулы и графика частот вращения
По заданию привод должен иметь сложенную структуру и 19 чисел подач. Чтобы получить Z = 19 составляется структурная формула для Z = 21 с двумя совпадающими числами подач.
Для большей компактности коробки подач целесообразно выбрать структуру вида I это следующие структуры:
Из приведенных структур предпочтительнее является структура АI-1 (класс А вид I) . Выбирается типовая структурная формула 31 (iП + 33 27)
Определяется количество конструктивных вариантов для сложенной структуры с одной дополнительной структурой (класс А):
Ккон = mО! qО! m’! q’! (3.1)
где mО m’ - число групп передач соответственно в основной и первой дополнительной структуре;
qО q’ - число групп передач с одинаковым количеством передач соответственно в основной и первой дополнительной структуре.
Ккон = 1! 1! 2! 1! =2
т.е. возможны следующие варианты:
Из всех конструктивных вариантов дающих одно и тоже число чисел подач рациональным является тот который имеет:
наименьшее количество зубчатых колес валов блоков муфт;
более короткие кинематические цепи а значит и повышенный к.п.д.;
большее число чисел подач по короткой цепи с наименьшей протяженностью этой цепи.
В соответствии с приведенными выше рекомендациями оптимальным вариантом следует считать первый вариант.
Количество кинематических вариантов для сложенной структуры класса А всех типов определяется по формулам:
Ккин = mО! m’! (3.2)
Наиболее предпочтительным является кинематический вариант который имеет меньшие диапазоны регулирования групп передач что позволяет избежать предельных значений передаточных отношений. Этот вариант для выбранного конструктивного варианта представлен в формуле 3.3.
Определяется характеристика Х группы передач для сложенной структуры класса А (с одной дополнительной структурой):
Z==3(Х0) (1+3(Х1) 2(Х2)) (3.3)
где - основная структура;
– дополнительная структура;
Х0 Х1 Х2- характеристики основной первой и второй переборной групп соответственно.
Характеристика основной группы равна единице первой переборной - числу передач в основной группе второй переборной – произведению числа передач в основной и первой минус число лишних передач то есть две передачи.
Оптимальным вариантом структурной формулы является вариант удовлетворяющий следующим условиям:
- структурная сетка для выбранной структурной формулы имеет веерообразный вид что обеспечивается возрастанием диапазона регулирования по группам;
- желательно чтобы основная группа стояла на первом месте структурной формулы и имела наибольшее количество передач а последняя переборная находилась бы на последнем месте и имела наименьшее количество передач.
С учетом всего этого структурная формула будет иметь вид
Z=3(1) (in+3(3) 2(7))
4 Определение чисел зубьев зубчатых колес механической коробки подач.
Существует три способа определения чисел зубьев в зубчатых передачах:
-метод наименьшего кратного;
-метод задания числа зубьев наименьшего зубчатого колеса в группе передач.
Выбирается метод задания числа зубьев наименьшего зубчатого колеса в группе передач. В таблице 4 представлены числа зубьев для каждой зубчатой передачи.
Таблица 4 - Результаты расчета чисел зубьев зубчатых колес
5 Определение погрешностей частот вращения
По кинематической схеме составляется уравнение кинематического баланса и определяются действительные числа подачи шпинделя sд; вычисленное значение сравнивается со стандартным рядом значений частот вращения sст ммоб.
Вычисляется погрешность значения чисел подач от стандартных значений по формуле:
Допустимая ошибка значения частоты вращения шпинделя % определяется по формуле
Результаты расчетов сведены в таблицу 5.
Таблица 5 – Параметры чисел подач шпинделя модернизированного станка
Уравнение кинематического
Продолжение таблицы 5
Подачи 13 и 14 совпадают соответственно с подачами 11 и 12. По выполненным расчетам погрешность чисел подач шпинделя не выхо-
дит за допустимые пределы.
Силовой расчет основных элементов
Исходные данные для силового расчета:
Т – расчетное число часов работы привода Т=20000 ч;
Q – требуемое тяговое усилие Q=1500 Н.
1 Определение расчетных частот вращения валов привода
Расчетная частота вращения i-го вала привода определяется по ГЧП с помощью расчетной ветви обозначаемой на графике утолщенной линией.
Положение расчетной ветви для зависимых приводов определяется верхней линией на графике. Однако расчетные значения ni берутся не прямо с графика а находятся путем умножения частот вращения верхней линии на величину nшп определяемой по формуле
Корректируя по станку имеем nшп=9134 обмин.
Значения скоростей валов привода подач приведены в таблице 6.
Таблица 6 – Частоты вращения валов привода подач
2 Определение потребной величины мощности подачи исполнительного органа станка
Мощность определяется по формуле
где Q – требуемое тяговое усилие Q=1500 Н;
Sмин – величина минутной подачи при черновой обработке мммин. Определяется по формуле
где S – максимальная подача за 1 оборот шпинделя S=16 ммоб
3 Определение величины мощности и крутящих моментов на валах привода
Мощность на i-м валу зависимого привода определяется по формуле
где i – КПД участка кинематической цепи до i-го вала подсчитываемый как произведение КПД отдельных элементов начиная с вала тягового устройства.
- КПД зубчатой передачи =099;
- КПД червячной передачи =073;
Ниже приведен расчет мощности на валах привода.
Крутящий момент на i-м валу привода определяется по формуле
Ниже приведен расчет крутящих моментов на валах привода
В таблице 7 записаны значения частот вращения мощностей и крутящих моментов на валах привода для наиболее нагруженного режима работы.
Частота вращения вала ni обмин
Крутящий момент Mi Нм
4 Расчет модулей зубчатых колес
Последующий расчет ведут с использованием программы для ЭВМ Koleso.exe. Целью данного расчета является определение модуля зубчатых колес составляющих коробку а также основных геометрических параметров зубчатых колес.
Здесь приводится расчет наиболее нагруженных передач
Для расчета геометрических параметров зубчатых зацеплений необходимо определить 32 входных параметра которые выбирают на основе данных 4. Параметры материала зубчатых колес представлены в таблице 8.
Таблица 8 – Физические параметры материала зубчатых колес
Способ химико-термической обработки зубьев
Предел изгибной выносливости
Предел контактной выносливости
Сталь 40Х ГОСТ 4543-71
Закалка ТВЧ по всему контуру
Исходные параметры для расчета зубчатых колес представлены в таблице 9.
Таблица 9 – Исходные параметры для расчета зубчатых колес
Условное обозначение в программе
Ссылка на источник или комментарий
Прямозубое зацепление
Угол делительного конуса
Число зубьев шестерни
Исходя из расчета числа зубьев зубчатых колес произведенного в подразделе 3.5
Продолжение таблицы 9
Базовый предел выносливости для выбранного материла шестерни МПа
Базовый предел выносливости для выбранного материла колеса МПа
Твердость материла зубьев шестерни по Бриннелю
Твердость материала зубьев колеса по Бриннелю
Вспомогательный коэффициент
По таблице 1 4 стр.6 для стальных прямозубых цилиндрических колес
Коэффициент ширины зубчатого венца
Рекомендации 4 стр. 16 для стальных закаленных зубчатых колес
Коэффициент характеризующий интенсивность типовых режимов нагружения передачи
По рекомендациям 4 стр.13
По рекомендациям 4 стр.13
По данным таб. 1 4 стр.6 для стальных прямозубых цилиндрических колес
Коэффициент безопасности
По данным 4 стр.16 для реверсивной нагрузки
Коэффициент неравномерности нагрузки
По рекомендациям 4 стр.17
По рекомендациям 4 стр.14
Коэффициент учитывающий двухстороннее приложение нагрузки.
По данным 4 стр.13.
Коэффициент формы зуба
По данным таблицы 6 4 стр.13 в зависимости от среднего числа зубьев передачи
Обратная величина передаточному отношению
Мощность электродвигателя
Коэффициент полезного действия ременной передачи
По данным таблицы 10 3 стр.20
Коэффициент полезного действия пары подшипников качения
По данным таблицы 10 3 стр.20
Коэффициент полезного действия зубчатой передачи
По данным таблицы 10 3 стр.20 для колес со шлифованными зубьями
Частота вращения шестерни обмин
По данным таблицы 4.6
Число часов работы передачи за расчетный срок ч
Для станков широкого назначения по данным 3 стр.11
Базовое число циклов нагружения ч
По данным таблицы 9 4 стр.20 для твердости зубчатого венца 500 НВ
По данным таб. 94 стр.14 для твердости зубчатого венца 500 НВ
Отношение ширины зубчатого венца к величине модуля
По данным 4 стр.18 среднее значение из рекомендуемого диапазона
Ниже представлены рассчитанные параметры зубчатых передач в таблице 10.
Таблица 10 – Рассчитанные параметры зубчатых зацеплений
Модуль из расчета контактных напряжений
Модуль из расчета на изгиб
Крутящий момент на валу шестерни
Диаметр делительной окружности шестерни
Диаметр делительной окружности колеса
Диаметр вершин зубьев шестерни
Диаметр вершин зубьев колеса
Межосевое расстояние
Ширина зубчатого венца
Коэффициент ширины шестерни относительно ее диаметра
Допускаемое контактное напряжение
Окончание таблицы 10
Лимитирующее допускаемое контактное напряжение
Расчетное напряжение изгиба
Из конструктивных соображений для всех групп передач кроме принимается модуль m=2. Для передач принимается модуль 15.
Тогда геометрия первого колеса определится следующим образом:
Определяется делительный диаметр d1 шестерни Z1
d1 = m * Z1 = 2 * 22 = 44 мм (4.7)
Определяется диаметр dа выступов шестерни Z1
dа = d1 +2*m = 44 + 2*2 = 48 мм (4.8)
Определяется диаметр df впадин шестерни Z1
df = d1 – 25*m = 44 – 25*2 = 39 мм (4.9)
Определяется ширина венца b шестерни Z1
b=bd * d1 = 02 * 44 = 88 мм (4.10)
bd - - отношение ширины венца к начальному диаметру шестерни bd = 02 ([8] с. 45);
Конструктивно =18 мм принимается для колес зацеплений .
=15 мм для остальных колес.
Результаты геометрии всех колес приведены в таблице 11
Таблица 11 - Геометрические параметры зубчатых колес и шестерен
делительный диаметр мм
5 Предварительный расчет валов на прочность
Предварительный расчет валов на прочность исходя из рекомендаций 5 стр.4.
Исходя из рекомендаций диаметр вала из уравнения прочности определяют по формуле:
где: - крутящий момент на валу ;
- допускаемое напряжение на кручение определяемое исходя из рекомендаций 5 стр.3 Для всех валов принимаем .
Расчет диаметров валов проектируемой коробки скоростей представлен в таблице 12.
Таблица 12 – Расчет диаметров валов проектируемой коробки скоростей
Диаметр вала по формуле (22)
Стандартное значение диаметра вала
6 Расчет прочностных характеристик валов
6.1 Определение сил действующих на валы
На рисунке 4 приведена схема для расчета валов на прочность.
Окружную силу действующую вал на котором посажено зубчатое колесо определяют по формуле
di – делительный диаметр шестерни мм.
Радиальную силу действующую на вал по данным 5 стр.10 определяют по формуле
где - угол зацепления для прямозубых колес
Расчет сил действующих на валы приведен в таблице 13.
Рисунок 4 – Схема для расчета валов на прочность
Таблица 13 – Расчет сил действующих на валы
6.2 Расчет на прочность входного вала VIII коробки подач
Исходные данные для расчета входного вала VIII коробки подач представлены в таблице 14.
Таблица 14 - Исходные данные к расчету входного вала
Радиальная сила действующая в зацеплении колеса
Окружная сила действующая в зацеплении колеса
Радиальная сила действующая в зацеплении шестерни
Окружная сила действующая в зацеплении шестерни
Координата вала в которой действуют силы зацепления колеса
Развертка привода подач
Координата вала в которой действуют силы зацепления шестерни
Расстояние между опорами вала
Крутящий момент на валу
Из расчета (таблица 7)
Поперечная (осевая) сила действующая в зацеплении колеса
Для прямозубой зубчатой передачи осевые силы отсутствуют
Окончание таблицы 14
Делительный диаметр колеса
По данным расчета зубчатых колес (таблица 11)
Поперечная (осевая) сила действующая в зацеплении шестерни
Делительный диаметр шестерни
По данным расчета зубчатых колес (таблица 10)
Частота вращения вала
Долговечность работы подшипника
По рекомендациям 5 стр.15 для шариковых подшипников качения
Долговечность работы подшипника второй опоры
Допускаемое напряжение изгиба
По данным таблицы 1 5 стр.8 для стали 40Х подвергнутой закалке ТВЧ
Сила действующая на вал от натяжения ремней
Результаты расчета входного вала VIII с использованием программы Val.exe представлены в таблице 15.
Таблица 15 – Результаты расчета входного вала VIII
Реакция опоры 1 в горизонтальной плоскости RG1 Н
Реакция опоры 1 в вертикальной плоскости RB1 Н
Реакция опоры 2 в горизонтальной плоскости RG2 Н
Реакция опоры 2 в вертикальной плоскости RB2 Н
Равнодействующая реакция опоры 1 R1 Н
Равнодействующая реакция опоры 2 R2 Н
Окончание таблицы 15
Изгибающий момент в сечении сил действующих в зацеплении колеса в горизонтальной плоскости MG1 Н*м
Изгибающий момент в сечении сил действующих в зацеплении колеса в вертикальной плоскости MB1 Н*м
Изгибающий момент в сечении сил действующих в зацеплении шестерни в горизонтальной плоскости MG2 Н*м
Изгибающий момент в сечении сил действующих в зацеплении шестерни в вертикальной плоскости MB2 Н*м
Суммарный изгибающий момент в сечении сил действующих в зацеплении колеса SM1 Н*м
Суммарный изгибающий момент в сечении сил действующих в зацеплении шестерни SM2 Н*м
Приведенный момент в сечении от сил действующих в зацеплении колеса MP1 Н*м
Приведенный момент в сечении от сил действующих в зацеплении шестерни MP2 Н*м
Диаметр вала под колесом DB1 мм
Диаметр вала под шестерней DB2 мм
Изгибающий момент от поперечной силы действующей в зацеплении колеса MK Н*м
Изгибающий момент от поперечной силы действующей в зацеплении шестерни MH Н*м
Принятый диаметр вала под колесом DB1 мм
Принятый диаметр вала под шестерней DB2 мм
Момент сопротивления в сечении вала под колесом W1 мм
Момент сопротивления в сечении вала под шестерней W2 мм
Коэффициент работоспособности
Как видно из таблицы 15 предварительно определенный диаметр вала удовлетворяет условиям прочности.
Построение эпюр для всех валов ведется с помощью программы “Расчет деталей машин” на основе данных полученных выше. Эпюра моментов вала представлена на рисунке 5.
Рисунок 5 – Эпюры моментов входного вала VIII коробки подач
6.3 Расчет на прочность вала IX
Исходные данные для расчета вала IX представлены в таблице 16.
Таблица 16 - Исходные данные к расчету входного вала
Продолжение таблицы 16
Окончание таблицы 16
Результаты расчета вала IX с использованием программы Val.exe представлены в таблице 17.
Таблица 17 – Результаты расчета вала IX
Окончание таблицы 17
Как видно из таблицы 17 предварительно определенный диаметр вала удовлетворяет условиям прочности.
Эпюра моментов вала представлена на рисунке 6.
Рисунок 6 – Эпюры моментов вала IX коробки подач
6.4 Расчет на прочность вала X
Исходные данные для расчета вала X представлены в таблице 18.
Таблица 18 - Исходные данные к расчету входного вала
Продолжение таблицы 18
Окончание таблицы 18
Результаты расчета вала X с использованием программы Val.exe представлены в таблице 18.
Таблица 19 – Результаты расчета вала X
Окончание таблицы 19
Как видно из таблицы 19 предварительно определенный диаметр вала удовлетворяет условиям прочности.
Эпюра моментов вала представлена на рисунке 7.
Рисунок 7 – Эпюры моментов вала X коробки подач
6.5 Расчет на прочность вала XI
Исходные данные для расчета вала XI представлены в таблице 20.
Таблица 20 - Исходные данные к расчету входного вала
Продолжение таблицы 20
Окончание таблицы 20
Результаты расчета вала XI с использованием программы Val.exe представлены в таблице 21.
Таблица 21 – Результаты расчета вала XI
Окончание таблицы 21
Как видно из таблицы 21 предварительно определенный диаметр вала удовлетворяет условиям прочности.
Эпюра моментов вала представлена на рисунке 8.
Рисунок 8 – Эпюры моментов вала XI коробки подач
6.6 Расчет на прочность вала XII
Исходные данные для расчета вала XII представлены в таблице 22.
Таблица 22 - Исходные данные к расчету входного вала
Продолжение таблицы 22
Окончание таблицы 22
Результаты расчета вала XII с использованием программы Val.exe представлены в таблице 23.
Таблица 23 – Результаты расчета вала XII
Окончание таблицы 23
Как видно из таблицы 23 предварительно определенный диаметр вала удовлетворяет условиям прочности.
Эпюра моментов вала представлена на рисунке 9.
Рисунок 9 – Эпюры моментов входного вала XII коробки подач
7 Расчет шпоночных соединений
Призматические шпонки проверяются на смятие и на срез.
Проверяется шпонка на входном валу под зубчатым колесом 6х6x25 ГОСТ 23360-78.
Условие проверки шпонки по напряжениям смятия 6
где -расчетное значение напряжений смятия МПа
-допускаемое значение напряжений смятия; МПа
F-сила создаваемая шпонкой Н
где Т – передаваемый шпонкой вращающий момент Нм
d – диаметр вала под шпонкой мм
где h – высота шпонки мм
- глубина заделки шпонки в вал;
- рабочая длина шпонки мм
Условие проверки шпонки по напряжениям смятия выполняется
Условие проверки шпонки на срез
где - расчетное значение напряжений среза МПа
-допускаемое значение напряжений среза МПа
Условие проверки шпонки по напряжениям среза выоплняется:
Так как все условия проверки выполнены то шпонка окончательно принимается к исполнению.
Остальные расчеты выполнены аналогично и результаты расчетов занесены в таблицу 24.
Таблица 24 – Результаты расчетов шпоночных соединений
Как видно из таблицы все шпонки удовлетворяют условиям напряжения смятия и среза.
8 Расчет подшипников качения
Расчет подшипников ведется на динамическую грузоподъемность С Н которая определяется по формуле
где R - реакция более нагруженной подшипниковой опоры вала Н;
n - частота вращения вала обмин;
t - длительность работы подшипника t = 20000 час.
Динамическая грузоподъемность подшипника на входном валу равна
Грузоподъемность подшипников на остальных валах приведена в таблице 25.
Таблица 25 -Грузоподъемность подшипников
Выбор описание и расчёт механизмов системы управления
В соответствии с заданием было спроектировано управление коробкой подач при помощи электромуфт. Для переключения зубчатых колес были применены электромагнитные муфты которые представлены на листе ТПЖА.045110.002-СБ2. В качестве вспомогательного материала использовалось учебно-методическое указание 7.
Данные муфты устроены следующим образом. В корпусе 5 муфты встроена катушка 6 ток к которой подводится через кольцо 4. Пакет магнитопроводящих фрикционных дисков состоит из дисков двух типов. Внутренние диски расположены на эвольвентных шлицах нарезанных на втулке 1. Наружные диски имеют 5-8 пазов в которые входят выступы поводка 2 соединяющего муфту с зубчатым колесом или другой деталью привода. При подаче тока в катушку магнитный поток замыкается через корпус 5 пакет дисков и якорь 3. Диски и якорь притягиваются к корпусу в результате между дисками возникает фрикционное сцепление и от втулки через внутреннее и наружные диски крутящий момент передается на поводок и зубчатое колесо. После отключения муфты происходит ее расцепление благодаря упругости наружных дисков боковые поверхности которых не совсем плоские они имеют жесткую «волну» специальной формы. В результате якорь отходит вправо до упора в бронзовое кольцо 7.
Ток к кольцу подводится с помощью щеткодержателя конструкция которого представлена 7 с 9. Постоянный ток напряжением 24 В от положительного плюса источника питания подводится к щетке 1 установленной в корпусе 2 через наконечник 3 к которому подсоединяется токопроводящий провод. Наконечник защищен колпачком 4. Ось щеткодержателя направляют по радиусу токосъемного кольца.
В проектируемом приводе щеткодержатели крепятся к стенке корпуса коробки скоростей при помощи кронштейнов.
Система смазки станка
Система смазки станка представлена на листе ТПЖА.045110.002 ДПЛ и рисунке 10.
Нормальная работа системы смазки является непременным условием для эксплуатации станка. В случае если масло перестало поступать в контрольный маслоуказатель станок должен быть немедленно выключен и неисправность системы смазки устранена.
До первоначальной заливки смазки необходимо промыть все масляные емкости бензином либо осветительным керосином заполнить их затем сортом масла указанной в «Схеме смазки»
Уровень масла в сверлильной головке контролируется по маслоуказателю. Смену масла рекомендуется производить первый раз после 20 дней а затем через каждые три месяца.
Каждые три месяца необходимо проверять работу системы смазки. Перед началом работы на станке сразу же после включения вращения шпинделя вправо проверить работу маслонасоса. Контроль производить по указателю на передней стенке сверлильной головки. При нормальной работе насоса масло должно непрерывно попадать на указательное стекло. Только убедившись в нормальной работе насоса и смазав все остальные точки можно приступить к работе на станке. При отсутствии подачи масла на указательное стекло или в другие точки смазки необходимо немедленно остановить станок и устранить неисправность.
Схема системы смазки и карта сазки станка представлена в графической части проекта.
Система смазки модернизированной коробки скоростей аналогична станку- прототипу.
Рисунок 10 – Общий вид станка с указанием мест смазки
Описание конструкции модернизированной коробки подач
После модернизации коробки подач было получено более плотное размещение подач станка в диапазоне практически аналогичном диапазону станка- прототипа что позволяет более точно подбирать режимы резания при обработке.
В данной коробке применяется сложенная структура с использованием связанного колеса.
Для переключения подач вместо ручного управления применено электрическое управление. Данная конструкция минимизирует время на переключение с одной подачи на другую.
Принципиальная электрическая схема станка и её описание
Принципиальная электрическая схема модернизированного станка модели 2С132 представлена на рисунке 11.
Рисунок 11 – Схема электрическая принципиальная станка 2С132
Подключение станка к электросети производится вводным автоматическим выключателем .
Выбор направления вращения шпинделя осуществляется реверсивным переключателем . В случае использования в работе охлаждающей жидкости электронасос подготавливается выключателем после чего он включается одновременно с электродвигателем привода шпинделя .
Включение электродвигателя привода шпинделя и привода подач производится отдельными кнопками и при помощи магнитных пускателей и в следующей последовательности: сначала электродвигатель привода шпинделя затем электродвигатель привода подач .
При неработающем электродвигателе электродвигатель не включается.
Кнопка предназначена для кратковременного включения электродвигателя .
При нажатии на кнопку включается магнитный пускатель по цепи: .
Магнитный пускатель н. о. контактами включит реле которое отключит своим н. з. контактом пускатель .
Таким образом длительность работы электродвигателя не зависит от продолжительности нажатия кнопки .
Остановка всех электродвигателей происходит при нажатии кнопки так и при нажатии конечного выключателя .
Торможение электродвигателя привода шпинделя после отключения питания осуществляется тормозной электромагнитной муфтой . Питание к катушкам муфты поступает от селенового выпрямителя по цепи . Время нахождения тормозной муфты под напряжением определяется настройкой реле времени .
Электромагнитные муфты переключения частот вращения шпинделя включаются и выключаются контактами . Плавкий предохранитель служит для отключения питания при коротких замыканиях. При отключении муфты исчезающее магнитное поле наводит в катушках ЭДС большой величины которая может вызвать пробой изоляции катушки. Для снижения ЭДС применяют разрядные резисторы .
Диоды не пропускают ток через резисторы когда муфты выключены в результате в это время не будет потерь энергии в резисторах.
В процессе выполнения данного курсового проекта были практически закреплены теоретические знания полученные при изучении таких дисциплин как “Сопротивление материалов” “Детали машин” “Основы технологии машиностроения” и других.
В курсовом проекте была разработана модернизированная коробка подач отвечающая требованиям механической прочности долговечности простоты изготовления сборки эксплуатации и ремонта.
Был выполнен сборочный чертеж на котором были показаны все необходимые конструктивные элементы.
Модернизированный вариант коробки подач имеет преимущество по сравнению с конструкцией данного узла станка-прототипа – это более плотное размещение частот вращения в диапазоне практически аналогичном диапазону станка- прототипа что позволяет более точно подбирать режимы резания при обработке.
Также были получены навыки по кинематическому и силовому расчету привода по определению чисел зубьев передач отклонений величин подач построения по построению структурной сетки и графика чисел подач. Были произведены конструкторские расчеты: расчет передач расчет валов расчет шпоночных соединений.
Библиографический список
Казенин Г.П. Шиврин Ю.П. Методические указания по курсовому проекту курса “Металлорежущие станки” (часть 1 – кинематический расчет и анализ структурных схем). – Киров: ВятГТУ 1978. – 50с.
Земцов М.И. Казенин Г.П. Основные принципы проектирования систем дистанционного управления автоматического оборудования. Методические указания по выполнению курсового проекта по дисциплине “Металлообрабатывающее оборудование автоматизированного производства” для студентов специальности 1201 “Технология машиностроения”. – Киров: ВятГТУ 1995. – 32с.
Металлорежущие станки. Под ред. В.К. Тепинкичиева. – М. Машиностроение 1973 – 465с.
Казенин Г.П. Земцов М.И. Расчет зубчатых колес металлорежущих станков с применением ЭВМ. Методические указания по выполнению курсового проекта по дисциплине “Металлообрабатывающее оборудование автоматизированного производства” для студентов специальности 1201 “Технология машиностроения”. – Киров: ВятГТУ 1985. – 44с.
Казенин Г.П Земцов М.И. Проектирование валов их расчет на прочность с использованием ЭВМ. Методические указания к дипломному проектированию конструкторского направления и курсовому проектированию. – Киров: КирПИ 1986. – 36с.
В.И. Анурьев. Справочник конструктора – машиностроителя. Том 1. – М.Машиностроение. 1979 – 728с.
Казенин Г.П. Земцов М.И. Поляков С.М. Основные принципы проектирования систем дистанционного управления автоматизированного оборудования. Методические указания по курсовому проектированию. – Киров: ВятГТУ 1995. – 32 с.
Столбин Г.Б. Жуков К.П. Расчет и проектирование деталей машин – Москва:
Высшая школа1978. 276 с.
Власов В.А. Подбор подшипников качения. - Вятский государственный
университет 2006. – 26 с.
Спецификация.spw

ТПЖА. 045110.002-СБ2
Вал Сталь 40Х ГОСТ 4543-71
Сталь 40Х ГОСТ 4543-71
Кольца пружинные упорные
Муфты электромагнитные
многодисковые с магнито-
Э1М072-1А ГОСТ 21573-76
Подшипники ГОСТ 8338-75
Шпонки ГОСТ 23360-78
3 лист.cdw

Количество чисел подач шпинделя 19
Предельные значения подач шпинделя
Технические требования
Обеспечить плавное вращение валов без заедания и шума.
Необработанные поверхности красить нитроэмалью ХВ-24 ГОСТ
144-74 красного цвета
Титульник.doc
Государственное образовательное учреждение
высшего профессионального образования
«ВЯТСКИЙ ГОСУДАРСТВЕННЫЙ УНИВЕРСИТЕТ»
Факультет автоматизации машиностроения
Кафедра технологии машиностроения
Курсовой проект по дисциплине
«Металлорежущие станки»
«Модернизация привода движения подач вертикально-сверлильного станка модели 2С132»
Пояснительная записка
Ведомость.cdw

подач вертикально-сверлильного
Станок вертикально-сверлильный
модели 2С132 (схемы)
Пояснительная записка
2 Лист.cdw

Содержание.doc
1 Технологические возможности станка 4
2 Техническая характеристика станка 2С132 4
Анализ компоновки и кинематики разрабатываемого привода станка-прототипа его структурная формула график чисел подач система управления 6
Кинематический расчет привода .9
1 Определение показателя геометрического ряда частоты вращения
2 Выбор электродвигателя привода главного движения .. .9
3 Определение оптимальной структурной формулы и ГЧВ ..9
4 Определение числа зубьев зубчатых колес коробки подач . . .11
5 Определение погрешностей частот вращения 11
Силовой расчет основных элементов .14
1 Определение расчетных частот вращения валов привода .. .14
2 Определение потребной величины мощности подачи исполнительного органа
3 Определение величины мощности и крутящих моментов на валах привода .15
4 Расчет модулей зубчатых колес. 16
5 Предварительный расчет валов на прочность.. .23
6 Расчет прочностных характеристик валов.. .24
6.1 Определение сил действующих на валы ..24
6.2 Расчет на прочность входного вала VIII коробки подач . 26
6.3 Расчет на прочность вала IX . .29
6.4 Расчет на прочность вала X . . ..33
6.5 Расчет на прочность вала XI . 37
6.5 Расчет на прочность вала XII .. . 41
7 Расчет шпоночных соединений ..45
8 Расчёт подшипников качения .47
Выбор описание и расчет механизмов системы управления 48
Система смазки станка . .49
Описание конструкции модернизированной коробки подач 51
Принципиальная электрическая схема и ее описание 52
Приложение А (справочное). Библиографичекий список 55
Рекомендуемые чертежи
- 22.11.2015
- 07.06.2021
Свободное скачивание на сегодня
Другие проекты
- 20.08.2014