Привод главного движения вертикально-сверлильного станка




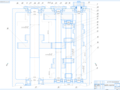
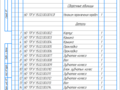
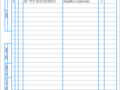
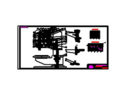
- Добавлен: 25.01.2023
- Размер: 2 MB
- Закачек: 0
Описание
Привод главного движения вертикально-сверлильного станка
Состав проекта
![]() |
![]() |
![]() ![]() ![]() ![]() |
![]() ![]() ![]() |
![]() ![]() ![]() ![]() |
![]() ![]() ![]() ![]() |
![]() ![]() ![]() ![]() |
![]() ![]() ![]() |
Дополнительная информация
Ведомость.spw

Пояснительная записка
УО "ПГУ".15.01.00.000.КЗ
Кинематическая схема
УО "ПГУ".15.02.00.000.
Посн записка.doc
Разработка и описание компоновки станка. 7
Проектирование и описание кинематической
Динамические и прочностные расчеты 15
1. Определение крутящих моментов ..15
2. Расчет зубчатой передачи . ..16
3. Расчет зубчатой передачи . . .20
4. Расчет зубчатой передачи . . .23
5. Расчет вала I на прочность. .27
6. Расчет вала II на прочность. 31
7. Расчет вала III на прочность. 35
8 Расчет вала IV на прочность .39
9. Подбор и проверочный расчет соединений 43
9.1. Соединение зубчатое колесо-вал 1 . .. 43
9.2. Соединение блок зубчатых колес-вал I.. .44
9.3. Соединение зубчатое колесо-вал II . .45
9.4. Соединение зубчатое колесо-вал III 46
9.5. Соединение блок зубчатых колес-вал IV.. . .47
10. Выбор подшипников .. 48
10.1. Вал 1 коробки скоростей .. ..48
10.2. Вал 2 коробки скоростей .. .. 49
10.3. Вал 3 коробки скоростей .. .. 49
10.4. Вал 4 коробки скоростей .. .. 50
Выбор вида смазывания передач и подшипников уплотняющих
Описание проектируемого узла. 52
Совершенствование конструкции машин методов их расчета и введение новых стандартов должно находить отражение в курсовом проектировании.
Цель курсового проектирования – приобретение навыков проектирования. Работая над проектом мы выполняем расчеты учимся рационально выбирать материалы и форму деталей стремясь обеспечить их высокую экономичность надежность и долговечность. В проектировании широко используются ГОСТы учебная и справочная литература. Приобретенный в результате проектирования опыт будет являться основой дипломного проекта а также для всей дальнейшей конструкторской деятельности.
Проект состоит из пояснительной записки спецификации и графической части. Объем этих документов этих документов зависит от объема всего проекта установленного учебной программой. Объем графической части составляет три листа формата А1.
Определение технических характеристик станка.
Частота вращения шпинделя nmin
Мощность электродвигателя Nэл.
Наибольший условный диаметр сверления
Разработка и описание компоновки станка.
Вертикально-сверлильный станок предназначен для обработки отверстий. На станке можно обрабатывать детали как из легких сплавов так и из конструкционных.
Назначение станка. Станок предназначен для сверления (рассверливания) отверстий в различных материалах. На станке обрабатываются детали сравнительно небольшие размеров и веса.
Рис. 2.1 Компоновка вертикально-сверлильного станка.
Основные узлы станка: 1. сверлильная бабка; 2. рукоятка переключения скоростей; 3. линейка; 4. сверлильный шпиндель; 5. стол; 6. маховик; 7. колонна; 8. плита.
На рис. 1 приведен общий вид вертикально-сверлильного станка. Поперечное сечение колонны 7 представляет собой коробчатый прямоугольник передняя сторона которого является направляющей для перемещения сверлильной (шпиндельной) бабки и стола 5. Стол перемещают по направляющим колонны вручную с помощью винтового механизма маховичком 6. Стол станка имеет три Т-образных паза ширина рабочей поверхности выполнена по ГОСТ 6569 — 70. В сверлильной головке расположены механизм главного движения управляемый с помощью рукоятки 2 и штурвал 3 для управления механизмом подач сверлильного шпинделя 4. Колонна станка прикреплена к фундаментной плите 8 (основанию). В этой плите размещается бак для эмульсии которая подается электронасосом 9.
Движения в станке. Движение резания — вращение шпинделя с режущим инструментом. Движение подачи - осевое перемещение шпинделя с режущим инструментом. Вспомогательные движения — ручные перемещения стола и шпиндельной бабки в вертикальном направлении.Обрабатываемая деталь устанавливается на столе станка и закрепляется в машинных тисках или в специальных приспособлениях. Совмещение оси будущего отверстия с осью шпинделя осуществляется перемещением приспособления с обрабатываемой деталью на столе станка.
Режущий инструмент в зависимости от используемого хвостовика закрепляется в шпинделе станка при помощи патрона или переходных втулок. В соответствия с высотой обрабатываемой детали и длинной режущего инструмент производится установке стола и шпиндельной бабки.
Поверхности могут обрабатываться как ручным перемещением шпинделя так и механической подачей.
Диапазон регулирования Rn частоты вращения исполнительного органа привода определяется по формуле:
Предельные частоты вращения принимаются равными nmax=4500 мин-1 и nmin=450 мин-1 (по заданию на проектирование). С учетом этого диапазон регулирования:
Число ступеней частоты вращения выходного вала определяется по формуле:
Тогда число ступеней:
Число ступеней не может быть дробным поэтому для обеспечения возможности регулирования скорости вращения во всем диапазоне частот принимается z=12.
Тогда формула структуры привода z=3(1)2(3)2(6)
Рис. 3.1. Структурная сетка
Затем строится график частот вращения (см. рис. 3.2).
Рис. 3.2. График частот вращения
По этому графику определяются передаточные отношения всех передач и проставляем их на графике: .
Произведём расчет чисел зубьев колес для основной группы аналитическим способом.
Формулы для расчета чисел зубьев колес аналитическим способом имеют вид:
где а и b – взаимно простые числа через которые выражается данное
передаточное отношение т. е.
- сумма чисел зубьев в рассматриваемой группе (определяется
наименьшее общее кратное сумм этой группы)
Тогда для основной группы:
Следовательно а наименьшее общее кратное сумм равно 18 (примем 54) которое присвоим Тогда числа зубьев колес передачи составят
Тогда для первой переборной группы:
Следовательно а наименьшее общее кратное сумм равно 6 (примем 54) которое присвоим Тогда числа зубьев колес передачи составят
Тогда для второй переборной группы:
Следовательно а наименьшее общее кратное сумм равно 126 которое присвоим Тогда числа зубьев колес передачи составят
Следует иметь в виду что рассчитанные из кинематических условий числа зубьев колес в дальнейшем при разработке конструкции привода могут быть изменены при сохранении значений передаточных отношений.
Рис. 3.3 Схема коробки скоростей
Привод подач заимствуем у станка-прототипа. Кинематическая схема представлена на рисунке 3.4.
Рис. 3.4 Кинематическая схема
Описание кинематической схемы станка. Кинематические цепи проектируемого станка позволяют осуществлять следующие движения:
главное движение – вращение шпинделя;
движение подачи – вертикальное механической перемещение;
ручное перемещение шпинделя;
ручное перемещение стола станка (установочное);
ручное перемещение сверлильной головки (установочное);
ручное вращение стола (установочное).
Главное движение шпинделя осуществляется от асинхронного электродвигателя через передачу привода 1(z=25) – 2(z=28) на вал I коробки скоростей цилиндрическую зубчатую передачу 3(z=24) – 8(z=30) либо 5(z=30) – 7(z=24) либо 4(z=27) – 6(z=27)на вал II коробки скоростей далее через цилиндрическую зубчатую передачу 9(z=18) – 11(z=36) либо 10(z=27) – 12(z=27) на вал III коробки скоростей далее через цилиндрическую зубчатую передачу 13(z=36) – 15(z=90) либо 14(z=77) – 16(z=49) на шпиндель IV.
Привод подачи осуществляется от выходного вала коробки скоростей через коробку подач и механизм подачи на рейку-гильзу шпинделя. Движение на коробку подач поступает через одиночную цилиндрическую зубчатую передачу 17(z=22) – 18(z=42) на вал V коробки подач далее через тройной блок зубчатых колес 19(z=29) – 22(z=19) либо 20(z=24) – 23(z=24) либо 21(z=16) – 24(z=32) на вал VI и далее через одиночную передачу 22(z=19) – 25(z=34) и 26(z=17) – 27(z=44) на рейку-гильзу шпинделя. Таким образом вращательное движение преобразуется в поступательное движение шпинделя.
Ручное перемещение шпинделя осуществляется при помощи штурвала.
Подъем и опускание стола производится при помощи червяка 36(k=1) червячного колеса 38(z=48) шестерни 39(z=28) и рейки.
Подъем и опускание сверлильной головки производится при помощи червяка 41(k=1) червячного колеса 40(z=20) шестерни 34(z=14) и рейки 35.
Для облегчения поворота стола на нижнем конце рейки имеется ролик который катится по нижнему фланцу колонны.
ДИНАМИЧЕСКИЕ И ПРОЧНОСНЫЕ РАСЧЕТЫ
1. Определение крутящих моментов
Следует отметить что при динамическом расчете привода главного движения максимальный крутящий момент на выходе коробки скоростей определяется не по номинальной а по расчетной частоте его вращения которая принимается равной первой ступени второй четверти диапазона регулирования скорости т.е. n4=800 обмин а также исходя из расчета наиболее нагруженных передач за расчетные принимаются частоты на валах: nI=2500 мин-1 nII=2000 мин-1 nIII=2000 мин-1 nIV=800 мин-1.
Мощность на первом валу коробки скоростей определяется по формуле:
РI=Pэд×hэд×hр.п×hп×hзп ; (4.1)
где Pэд=055 кВт мощность электродвигателя принимается из задания на проектирование.
hэд=097 hм.=098 hп=099 hзп=096 КПД соответственно электродвигателя муфты пары подшипников и зубчатой передачи 8 табл. 5.4.
Тогда мощность и угловая скорость на первом валу:
РI =055×097×098×099×096=04969 кВт;
Теперь можно определить наибольший крутящий момент по формуле:
Мощность на втором валу коробки скоростей:
Тогда мощность и угловая скорость на втором валу:
РII =04969×096×099=0472 кВт;
Мощность и угловая скорость на третьем валу:
РIII =0472×096×099=0448 кВт;
Мощность на шпинделе:
Тогда мощность и угловая скорость на шпинделе:
РIV =0448×096×099=0425 кВт;
Наибольший крутящий момент:
2. Расчет зубчатой передачи.
Для понижающей зубчатой передачи (2430) принимается прямозубая цилиндрическая передача как наиболее простая в изготовлении. Принимается для изготовления колес передачи для уменьшения номенклатуры сталь 40Х (улучшение) со следующими механическими характеристиками:
для ведущего колеса sв=830 Нмм2 sт=540 Нмм2 НВ=240 290;
для ведомого колеса sв=930 Нмм2 sт=690 Нмм2 НВ=260 300.
Пределы контактной выносливости по [9] табл. 9.11:
для ведомого колеса: s Нlimb=2×HB+70=2×295+70=660 Hмм 2
для ведущего колеса: s Нlimb=2×HB+70=2×285+70=640 Hмм 2
Расчетное число циклов перемены напряжений определяется по формуле [9 с. 193 форм. 9.32]:
где n1 частота вращения ведущего колеса n1=2500 обмин;
с число колес находящихся в зацеплении с рассчитываемым принимается с=1.
Lh расчетный срок службы передачи определяется по формуле [9 с. 14]:
Lh=8760×L×Kг×Кс; (4.4)
где L долговечность принимается равной 10 годам.
Кг коэффициент использования в течении года принимается Кг=066.
Кс коэффициент использования в течении суток принимается Кс=025.
Lh=8760×10×066×025=14454 ч ;
NH=60×2500×1×14454=21×10 9;
Для ведущего колеса и тем более для ведомого NH >NHO=18×10 7 поэтому принимаем коэффициент долговечности KHL=1 [9 с.191]
Допускаемые контактные напряжения при расчете на выносливость по формуле [9 с. 192 форм. 9.30]
где SH для улучшенных зубьев по [9 с. 192] SH=11.
для ведомого колеса: Hмм 2
для ведущего колеса: Hмм 2
Так как передача прямозубая расчет ведем по s НР наименьшему.
Допускаемые напряжения изгиба по формуле [9 с. 193 форм. 9.35]:
для ведомого колеса: s Flimb=260+HB=260+295=555 Hмм 2
для ведущего колеса: s Flimb=260+HB=260+285=545 Hмм 2
Допускаемые напряжения при SF=2 и KFC=1 односторонняя нагрузка по [9 с. 193] КFL=1 т.к. NFE=60×Lh×n1×с =60×14454×2500×1=21×109>NF0=4×106
Ориентировочное значение модуля по формуле [9 с. 184 форм. 9.5]:
где ybd коэффициент ширины шестерни относительно диаметра принимается ybd=04;
YF1 коэффициент учитывающий форму зуба по [9 с. 184 рис. 9.6] принимается YF1=39;
KFb коэффициент учитывающий неравномерность распределения нагрузки по ширине венца по [9 с. 182 рис. 9.5] принимается KFb=102;
Km вспомогательный коэффициент для прямозубых передач принимается Km=14;
Число зубьев колес принимаются по п. 3.3: z1=24 z2=30;
Уточняем диаметры колес по [9 с. 176]:
da1=d1+2×m=24+2×1=26 мм
da2=d2+2×m=30+2×1=32 мм (4.8)
df1=d1–2.5×m=24–2.5×1=215 мм
df2=d2–2.5×m=30–2.5×1=295 мм
Межосевое расстояние:
Рабочая ширина зацепления:
bw=ybd×d1=04×24=96 мм принимаем bw=10 мм . (4.10)
Проверочный расчет на выносливость по контактным напряжениям. Окружная сила:
По [9 с. 187 табл. 9.10] назначаем восьмую степень точности. По [9 с. 186 табл. 9.9] принимаем g 0=56. По [9 с. 186 табл. 9.7] dН=0006.
Удельная расчетная окружная сила в зоне ее наибольшей концентрации рассчитывается по формуле: [9] форм. 9.10:
KНb коэффициент учитывающий неравномерность распределения нагрузки по ширине венца по [9 с. 182 рис. 9.5] принимается KFb=101.
передаточное отношение.
Коэффициент учитывающий динамическую нагрузку возникающую в зацеплении определяем по формуле [9 с. 188 форм.9.15]:
Удельная расчетная окружная сила по формуле [9 с. 185 форм. 9.8]:
Расчетное контактное напряжение по формуле [9 с. 185 форм. 9.7]:
где zH коэффициент учитывающий форму сопряженных поверхностей в полюсе зацепления по [9] стр.185:
zМ – коэффициент учитывающий механические свойства материалов колес по[9 с. 185] zМ=275 Мпа.
ze коэффициент учитывающий суммарную длину контактных линий по [9 с. 185]:
где ea коэффициент торцового перекрытия по [9 с. 174 табл. 9.1]:
Следовательно условие прочности выполнено.
Проверка по напряжениям изгиба. Расчетное напряжение изгиба на переходной поверхности зуба по [9 с. 187 форм. 9.11]:
где YF1=39 коэффициент учитывающий форму зуба по [9 с. 184 рис. 9.6];
YF2=38 коэффициент учитывающий форму зуба по [9 с. 184 рис. 9.6];
Yb=1-b140=1 коэффициент учитывающий наклон зуба по [9 с.187];
Ye=1 коэффициент учитывающий перекрытие зубьев по [9 с.187];
Определяем менее прочное звено:
ведущее колесо менее прочное.
Расчет производим по ведущему колесу.
Из графика [9 с. 182 рис.9.5] коэффициент концентрации нагрузки КFb=105.
По [9с. 185 форм. 9.10]:
где dF=0016 коэффициент учитывающий влияние вида зубчатой передачи и модификации профиля головок зубьев по [9 с 186 табл. 9.8].
По [9 с. 188 форм. 9.16]:
Коэффициент динамической нагрузки по [9 с. 188 форм. 9.15]:
Удельная расчетная окружная сила по [9] форм. 9.12:
где КFa=1 для прямозубых передач по [9 с.188].
sF=39×1×1×3321=1296sFP=2775 Нмм 2
Напряжение изгиба действующее в зацеплении меньше допускаемого значит условие прочности выполнено.
3. Расчет зубчатой передачи.
Для зубчатой передачи (2727) принимается прямозубая цилиндрическая передача как наиболее простая в изготовлении. Принимается для изготовления колес передачи для уменьшения номенклатуры сталь 40Х (улучшение) со следующими механическими характеристиками:
где n1 частота вращения ведущего колеса n1=2000 обмин;
NH=60×2000×1×14454=17×10 9;
Допускаемые напряжения при SF=2 и KFC=1 односторонняя нагрузка по [9 с. 193] КFL=1 т.к. NFE=60×Lh×n1×с =60×14454×2000×1=173×109>NF0=4×106
YF1 коэффициент учитывающий форму зуба по [9 с. 184 рис. 9.6] принимается YF1=385;
Число зубьев колес принимаются по п. 3.3: z1=27 z2=27;
da1=d1+2×m=27+2×1=29 мм
da2=d2+2×m=27+2×1=29мм
df1=d1–2.5×m=27–25×1=245 мм
df2=d2–2.5×m=27–25×1=245 мм
bw=ybd×d1=04×27=108 мм принимаем bw=11 мм .
По [9 с. 187 табл. 9.10] назначаем девятую степень точности. По [9 с. 186 табл. 9.9] принимаем g 0=73. По [9 с. 186 табл. 9.7] dН=0006.
где YF1=385 коэффициент учитывающий форму зуба по [9 с. 184 рис. 9.6];
YF2=385 коэффициент учитывающий форму зуба по [9 с. 184 рис. 9.6];
ведомое колесо менее прочное.
Расчет производим по ведомому колесу.
Из графика [9 с. 182 рис.9.5] коэффициент концентрации нагрузки КFb=102.
Удельная расчетная окружная сила по [9] форм. 9.12 :
sF=385×1×1×3241=1247sFP=2775 Нмм 2
4. Расчет зубчатой передачи.
Для понижающей зубчатой передачи (3690) принимается прямозубая цилиндрическая передача как наиболее простая в изготовлении. Принимается для изготовления колес передачи для уменьшения номенклатуры сталь 40Х (улучшение) со следующими механическими характеристиками:
Допускаемые напряжения при SF=2 и KFC=1 односторонняя нагрузка по [9 с. 193] КFL=1 т.к. NFE=60×Lh×n1×с =60×14454×2000×1=17×109>NF0=4×106
YF1 коэффициент учитывающий форму зуба по [9 с. 184 рис. 9.6] принимается YF1=375;
Число зубьев колес принимаются по п. 3.3: z1=36 z2=90;
da1=d1+2×m=36+2×1=38 мм
da2=d2+2×m=90+2×1=92мм
df1=d1–2.5×m=36–25×1=345 мм
df2=d2–2.5×m=90–25×1=875 мм
bw=ybd×d1=04×36=144 мм принимаем bw=15 мм .
YF2=355 коэффициент учитывающий форму зуба по [9 с. 184 рис. 9.6];
sF=375×1×1×5041=1893sFP=2775 Нмм 2
5. Расчет вала I на прочность.
Составляем расчетную схему где вал рассматриваем как балку лежащую на шарнирных опорах и намечаем расстояние между опорами.
Окружное усилие в зацеплении:
Ft21 = 2 * Т1 d1 = 2 * 19 0024 = 1583 Н;
Радиальное усилие в том же зацеплении:
Fr21 = Ft21 * tg200 = 1583 · 0364 = 576 H;
На вал I со стороны привода действует сила F которая определяется по формуле: Ft = 2 * Тэд d0 = 2 * 187 0025 = 1496 Н;
Fr = Ft * tg200 = 1496 · 0364 = 544 H;
где Тэд=Рэд=055293=187 Нм;
Строим схему нагружения вала 1 рис. 4.1.
Определяем опорные реакции в вертикальной плоскости (ZOY):
M A = 0: RBy *185 + Ft * 30 – Fr21 * 40 = 0;
M B = 0: RAy * 185 - Ft * 215 + Fr21 * 145 = 0;
Определяем опорные реакции в горизонтальной плоскости (ZOX):
Принимаем с учетом рекомендаций по 9 стр. 291 материал вала – сталь 45. По 9 табл. 12.13 для стали 45 : s -1 = 432 Нмм 2 t -1 = 255 Нмм 2 – пределы выносливости материала вала при симметричных циклах изгиба и кручения s B = 883 Нмм 2 – предел прочности. По 9 табл. 12.2 es= 0.8 – коэффициент учитывающий снижение механических свойств материала с увеличением размера заготовок для углеродистых сталей. По 9 табл. 12.5 Кs= 1.9 – эффективный коэффициент концентрации напряжений для валов в месте шпоночного паза. По 9 стр. 275: S = 3 – коэффициент безопасности при симметричном изменении напряжения изгиба и кручения. По 9 табл. 12. 9 b = 2 – коэффициент учитывающий упрочнение поверхности при поверхностной закалке.
Эквивалентное число циклов :
N LE = NH = 60 * 2500 * 1 * 14454 = 21 * 10 9 ;
Коэффициент долговечности:
где m = 9 – показатель степени кривой усталости по 9 стр.275.
N 0 = 5 * 10 6 – базовое число циклов перемены напряжений по 9 стр275.
Допускаемый предел выносливости при симметричных циклах изгиба по 9 форм. 12.3:
Рис. 4.1. Схема нагружения вала I
Суммарный изгибающий момент в опасных сечениях:
Эквивалентный момент в опасных сечениях по 9 стр.185 :
ME I = T = 1900 Н*мм
Диаметр в опасных сечениях по 9 форм. 12.2:
d I = 8 мм – диаметр вала под полумуфту.
d II = 10 мм – диаметр вала под подшипниками.
d III = 11 мм – диаметр вала под зубчатым колесом.
Нормальные напряжения возникающие в поперечном сечении вала от изгиба изменяется по симметричному циклу по 8 форм.14.14 :
где W – момент сопротивления вала со шлицами(6х11х14):
Где – для шлицев легкой серии – для шлицев средней серии наружный диаметр d = 14 мм.
s а = М ЕIII W = 8414 2692 = 3125 Мпа
Так как момент передаваемый валом является переменным то при расчете примем для касательных напряжений наиболее благоприятный знакопостоянный цикл – отнулевой по 8 форм. 14.15:
t а = t m = Т (2*WK) ; (4.29)
t а = t m = 1900 (2*649) = 146 Мпа
Коэффициент запаса прочности по нормальным напряжениям по 8 форм. 14.9:
где e s = 0.8 - масштабный фактор по 8 табл. 14.
По 8 табл. 14.2 для шлицевых валов К s = 1.75 – эффективный коэффициент концентрации напряжений при изгибе. По 8 табл. 14.4 y s = 0.2 – коэффициент учитывающий влияние постоянной составляющей цикла на усталость вала.
где e t = 0.8 - масштабный фактор по 9 табл. 14.3.
По 8 табл. 14.2 К t = 28 – эффективный коэффициент концентрации напряжений при изгибе. По 8 табл. 14.4 y t = 0.2 – коэффициент учитывающий влияние постоянной составляющей цикла на усталость вала.
Условие прочности по 8 форм. 14.8:
где [S] = 1.3 1.5 – требуемый коэффициент запаса для обеспечения прочности.
Прочность вала в опасном сечении обеспечена.
6. Расчет вала II на прочность.
Ft32 = 2 * Т2 d2 = 2 * 225 0027 = 1666 Н;
Fr32 = Ft32 * tg200 = 1666 · 0364 = 606 H;
M A = 0: -RBy*160+Fr32*145- Ft12*55=0;
M B = 0: -RAy*160-Fr32*15+ Ft21*105=0;
Принимаем с учетом рекомендаций по 9 стр. 291 материал вала – сталь 45. По 9 табл. 12.13 для стали 45 : s -1 = 432 Нмм 2 t -1 = 255 Нмм 2 – пределы выносливости материала вала при симметричных циклах изгиба и кручения s B = 883 Нмм 2 – предел прочности. По 9 табл. 12.2 es= 0.8 – коэффициент учитывающий снижение механических свойств материала с увеличением размера заготовок для углеродистых сталей. По 9 табл. 12.5 Кs= 1.9 – эффективный коэффициент концентрации напряжений для шлицевых валов. По 9 стр. 275: S = 3 – коэффициент безопасности при симметричном изменении напряжения изгиба и кручения. По 9 табл. 12. 9 b = 2 – коэффициент учитывающий упрочнение поверхности при поверхностной закалке.
Эквивалентное число циклов:
N LE = NH = 60 * 2000 * 1 * 14454 = 173 * 10 9 ;
Рис. 4.2. Схема нагружения вала II
d I = 8 мм – диаметр вала под подшипниками.
d II = 11 мм – диаметр вала под зубчатым колесом.
где W – момент сопротивления вала со шлицами и полостью d = 55 мм:
Где – для шлицев легкой серии – для шлицев средней серии наружный диаметр = 14 мм.
s а = М ЕIII W = 5976 2692= 222 Мпа
Так как момент передаваемый валом является переменным то при расчете примем для касательных напряжений наиболее благоприятный знакопостоянный цикл – отнулевой по 8 форм. 14.15 :
t а = t m = Т (2*WK) ;
t а = t m = 2250 (2*649) = 173 Мпа
По 8 табл. 14.2 К s = 1.75 – эффективный коэффициент концентрации напряжений при изгибе. По 8 табл. 14.4 y s = 0.2 – коэффициент учитывающий влияние постоянной составляющей цикла на усталость вала.
По 8 табл. 14.2 для шлицев К t = 28 – эффективный коэффициент концентрации напряжений при изгибе. По 8 табл. 14.4 y t = 0.2 – коэффициент учитывающий влияние постоянной составляющей цикла на усталость вала.
Условие прочности по 8 форм. 14.8 :
7. Расчет вала III на прочность.
Ft43 = 2 * Т3 d3 = 2 * 214 0036 = 1188 Н;
Fr43 = Ft43 * tg200 = 1188 · 0364 = 432 H;
M A = 0: RBy*190+Fr43*90- Ft32*55=0;
M B = 0: -RAy*190-Fr43*100+ Ft32*135=0;
Рис. 4.3. Схема нагружения вала III
s а = М ЕIII W = 5778 2692=214 Мпа
t а = t m = 2140 (2*649) = 165 Мпа
8. Расчет вала IV на прочность.
Окружное усилие в зацеплении 1872:
Ft43 = 2 * Т3 d = 2 * 2.14 0036 = 1188 Н;
Окружное усилие в зацеплении 2242:
Ft54 = 2 * Т4 d = 2 * 508 000275 = 370 Н;
Fr54 = Ft54 * tg200 = 370 · 0364 = 1347 H;
M A = 0: -RBy*190+Ft54*220-Fr43*100=0;
M B = 0: -RAy*190+Ft54*30+ Fr43*90=0;
Принимаем с учетом рекомендаций по 9 стр. 291 материал вала – сталь 45. По 9 табл. 12.13 для стали 45: s -1 = 432 Нмм 2 t -1 = 255 Нмм 2 – пределы выносливости материала вала при симметричных циклах изгиба и кручения s B = 883 Нмм 2 – предел прочности. По 9 табл. 12.2 es= 0.8 – коэффициент учитывающий снижение механических свойств материала с увеличением размера заготовок для углеродистых сталей. По 9 табл. 12.5 Кs= 1.9 – эффективный коэффициент концентрации напряжений для валов в месте шпоночного паза. По 9 стр. 275: S = 3 – коэффициент безопасности при симметричном изменении напряжения изгиба и кручения. По 9 табл. 12. 9 b = 2 – коэффициент учитывающий упрочнение поверхности при поверхностной закалке.
N LE = NH = 60 * 800 * 1 * 14454 = 69 * 10 8 ;
ME I = T = 2140 Н*мм
Рис. 4.4. Схема нагружения вала IV
d I = 15 мм – диаметр вала под подшипниками.
d II = 16 мм – диаметр вала под зубчатым колесом.
где W – момент сопротивления вала со шлицами (6х16х20) и полостью d = 20 мм:
Где – для шлицев легкой серии – для шлицев средней серии наружный диаметр = 20 мм.
s а = М ЕIII W = 12004 883=136 Мпа
t а = t m = 2140 (2*17662) = 06 Мпа
9. Подбор и проверочный расчет соединений.
8.1. Соединение зубчатое колесо-вал 1.
Выбираем по стандарту призматическую шпонку для соединения зубчатого колеса с валом d = 8 мм. Материал шпонки – Сталь 20 передаваемый момент Т = 19 Н*м соединение работает при переменной нагрузке. По ГОСТ 23360-78 выбираем шпонку призматическую обыкновенную (исполнение А) со следующими размерами:
B = 3 мм ; h = 3 мм ; t 1 = 18 мм ; t 2 = 1.4 мм ;
Находим допускаемое напряжение смятия по [8] табл. 5.1:
Определяем рабочую длину шпонки по [8]форм. 5.1:
где k – рабочая высота k = 0.4 * h = 0.4 * 3 = 12 мм.
Находим общую длину шпонки:
L = l P + b = 33 + 3 = 66 мм (4.34)
Принимаем: шпонка 3 3 10 ГОСТ 23360-78
8.2. Соединение блока зубчатых колес – вал 1.
Для соединения блока зубчатых колес с валом 1 принимается шлицевое соединение 6 х 11 х 14 по ГОСТ 1139-58. По [8] табл. 4.5 определяется суммарный статический момент площади рабочих поверхностей соединения относительно оси вала sF = 34 мм2 мм и средний диаметр dm = 0.5 * ( D + d ) = 0.5 * ( 11 + 14 ) = 125 мм.
Среднее давление по [9] форм. 5.8:
Допускаемое давление на смятие по [9] форм. 5.10:
Где sТ — предел текучести материала шлицев по [9] табл.12.13 принимается sТ = 638 Нмм2 .
КСМ — общий коэффициент концентрации нагрузки при расчете на смятие по [9] стр.87:
КСМ = Кз * Кпр * Кп ;
Кз — коэффициент неравномерности распределения нагрузки между шлицами определяется в зависимости от параметра:
по [9] табл.5.7 Кз = 21.
Кпр — коэффициент продольной концентрации нагрузки ( по длине соединения) по [9] стр.83:
Значение коэффициента Ккр определяется по [9] табл.5.8 в зависимости от lD = 5714 = 407 и принимается Ккр = 27.
Значение коэффициента концентрации давления Ке от относительного смещения нагрузки определяется в зависимости от параметра e по [9] стр. 88:
для прямозубых колес b = 0 е = 24 мм — расстояние от середины посадочной поверхности до середины венца зубчатого колеса тогда по [9] рис.5.12 Ке = 19.
Кпр = 27 + 19 – 1 = 36
Кп = 1.1 — для закаленных сталей.
Тогда коэффициент концентрации нагрузки при расчете на смятие:
Ксм = 21 * 36 * 11 = 83
КД = 1.5 — коэффициент динамичности нагрузки.
Тогда допускаемое давление на смятие:
Соединение удовлетворяет условию прочности на смятие т.к. s = 1 [s] = 274 Нмм2 .
9.3. Соединение зубчатого колеса – вал 2.
Для соединения блока зубчатых колес с валом 2 принимается шлицевое соединение 6 х 11 х 14 по ГОСТ 1139-58. По [8] табл. 4.5 определяется суммарный статический момент площади рабочих поверхностей соединения относительно оси вала sF = 34 мм2 мм и средний диаметр dm = 0.5 * ( D + d ) = 0.5 * ( 11 + 14 ) = 125 мм.
по [9] табл.5.7 Кз = 20.
Значение коэффициента Ккр определяется по [9] табл.5.8 в зависимости от lD = 1014 = 07 и принимается Ккр = 084.
для прямозубых колес b = 0 е = 24 мм — расстояние от середины посадочной поверхности до середины венца зубчатого колеса тогда по [9] рис.5.12 Ке = 22.
Кпр = 084 + 22 – 1 = 204
Ксм = 20 * 204 * 11 = 45
Соединение удовлетворяет условию прочности на смятие т.к. s = 66 [s] = 506 Нмм2 .
9.4. Соединение зубчатое колесо-вал 3.
Для соединения блока зубчатых колес с валом 3 принимается шлицевое соединение 6 х 11 х 14 по ГОСТ 1139-58. По [8] табл. 4.5 определяется суммарный статический момент площади рабочих поверхностей соединения относительно оси вала sF = 34 мм2 мм и средний диаметр dm = 0.5 * ( D + d ) = 0.5 * ( 11 + 14 ) = 125 мм.
где sТ — предел текучести материала шлицев по [9] табл.12.13 принимается sТ = 638 Нмм2 .
по [9] табл.5.7 Кз = 17.
Значение коэффициента Ккр определяется по [9] табл.5.8 в зависимости от lD = 1514 = 107 и принимается Ккр = 16.
для прямозубых колес b = 0 е = 75 мм — расстояние от середины посадочной поверхности до середины венца зубчатого колеса тогда по [9] рис.5.12 Ке = 185.
Кпр = 16 + 185 – 1 = 255
Ксм = 17 * 245 * 11 = 46
КД = 2 — коэффициент динамичности нагрузки.
Соединение удовлетворяет условию прочности на смятие т.к. s = 42 [s] = 495 Нмм2 .
9.5. Соединение блок зубчатых колес-вал 4.
Для соединения блока зубчатых колес с валом 4 принимается шлицевое соединение 6 х 21 х 25 по ГОСТ 1139-58. По [8] табл. 4.5 определяется суммарный статический момент площади рабочих поверхностей соединения относительно оси вала sF = 97 мм2 мм и средний диаметр dm = 0.5 * ( D + d ) = 0.5 * ( 21 + 25 ) = 23 мм.
по [9] табл.5.7 Кз = 356.
Значение коэффициента Ккр определяется по [9] табл.5.8 в зависимости от lD = 3625 = 144 и принимается Ккр = 14.
для прямозубых колес b = 0 е = 285 мм — расстояние от середины посадочной поверхности до середины венца зубчатого колеса тогда по [9] рис.5.12 Ке = 3.
Кпр = 14 + 3 – 1 = 34
Ксм = 356 * 34 * 11 = 133
Соединение удовлетворяет условию прочности на смятие т.к. s = 145 [s] = 171 Нмм2 .
10. Выбор подшипников.
10.1. Вал 1 коробки скоростей.
Диаметр шейки вала d = 10 мм частота вращения n = 2500 мин –1. По [9] табл. 14.18 Кs = 1.2 – коэффициент безопасности.
Требуемая динамическая грузоподъемность для роликовых подшипников вала по [9] стр.358:
где V – коэффициент учитывающий вращение кольца по [9] стр.348 для вращающегося внутреннего кольца V = 1.
X – коэффициент радиальной нагрузки по [9] табл. 14.14 Х = 1.
К Т – температурный коэффициент если она превышает 398.15 0К то по [9] табл. 14.19 К Т = 1.05.
n – частота вращения вала 1.
L h – долговечность подшипника L h = 14454 ч.
Р – степенной показатель для шариковых по [9] стр. 334 р = 3.
Для данного d = 10 мм подшипника по ГОСТ 8338-75 динамическая грузоподъемность С = 3340 Н что больше требуемой поэтому принимается радиальный шариковый подшипник 1000900 который соответствует требуемой долговечности и выдержит прикладываемую опорную реакцию.
10.2. Вал 2 коробки скоростей.
Диаметр шейки d = 10 мм частота вращения n = 2000 мин –1. По [9] табл. 14.18 Кs = 1.2 – коэффициент безопасности.
Требуемая динамическая грузоподъемность для шариковых подшипников вала по [9] стр.358 :
10.3. Вал 3 коробки скоростей.
Требуемая динамическая грузоподъемность для шариковых подшипников вала по [9] стр.358:
10.4. Вал 4 коробки скоростей.
Диаметр шейки d = 20 мм частота вращения n = 800 мин –1. По [9] табл. 14.18 Кs = 1.2 – коэффициент безопасности.
Для данного d = 20 мм подшипника по ГОСТ 8338-75 динамическая грузоподъемность С = 6550 Н что больше требуемой поэтому принимается радиальный шариковый подшипник 1000904 который соответствует требуемой долговечности и выдержит прикладываемую опорную реакцию.
Выбор вида смазывания передач и
подшипников уплотняющих средств
Смазочной системой называют совокупность устройств для подачи смазочного материала к трущимся поверхностям и возврата его в резервуар. Систему смазывания жидким материалом выбирают исходя из требуемой быстроходности механизмов исходя из их расположения конструкции уплотнений. Для данной коробки скоростей лучше использовать циркуляционное смазывание т.к. оно обладает рядом преимуществ: используется один и тот же объем масла что уменьшает стоимость оборудования осуществляется подвод смазки ко всем трущимся поверхностям одновременно что обеспечит независимую смазку каждого узла. Данная система смазки использует струйную подачу смазочного материала к зубчатым передачам посредством трубок. Опоры валов смазываются маслом которое подается в подшипник по валам.
Определим производительность насоса смазочной системы по формуле(10. стр. 704):
Где коэффициент принимают равным 1-3.
N – мощность привода кВт. (N=0.55) - к.п.д. привода.
В соответствии с п. 4.1
=097×098×099×096×096×099×096×099×096×099=0775
Объем резервуара отстойника принимают равным производительности насоса за 5-6 минут работы. Принимаем объем резервуара равным 22 л. Сорт масла используем как у станка прототипа И-20 ГОСТ 20799-88.
Описание проектируемого узла.
Описание коробки скоростей чертеж которой представлен на чертеже УО "ПГУ".15.02.00.000.Сб.
Движение на коробку скоростей поступает от асинхронного электродвигателя через колесо 7 зубчатой передачи привода. На первом валу коробки скоростей размещен блок зубчатых колес 10 посредством которого расширяется диапазон регулирования частоты вращения шпинделя. Первый вал установлен на шариковых радиальных подшипниках 35 которые фиксируются стопорным кольцом 33 и крышкой 20. Для регулировки предусмотрено кольцо 19. Второй вал установлен на шариковых радиальных подшипниках 35 которые фиксируются стопорными кольцами 31 и 33. На втором валу коробки скоростей зубчатые колеса фиксируются в осевом направлении стопорными кольцами 32. Третий вал установлен на шариковых радиальных подшипниках 35 которые фиксируются стопорным кольцом 34 и крышкой 24. На третьем валу коробки скоростей размещен блок зубчатых колес 15 и зубчатые колеса 9 и 14 которые фиксируются в осевом направлении стопорными кольцами 32. Четвертый вал установлен на шариковым радиальном подшипнике 36 и роликовом радиально-упорном подшипнике 37 которые фиксируются стопорным кольцом 34 и крышкой 25. На четвертом валу коробки скоростей размещен блок зубчатых колес 18.
Перемещение блока зубчатых колес 15 осуществляется механизмом переключения передач 1.
При выполнения данного курсового проекта я изучил подробно назначение вертикально-сверлильного станка его структуру область применения овладел методами моделирования и оптимизации а также научился анализировать его достоинства и недостатки и делать собственные выводы.
Ачеркан Н.С. Металлорежущие станки. Т1. М.- Машиностроение. 1965г.
Общемашиностроительные нормативы расчета режимов резания.
Тарзиманов Г.А. Проектирование металлорежущих станков. М. “Машиностроение” 1972 312 стр.
Данилов В.А. Методические указания к курсовому проекту. Новополоцк – 1987.
Справочник технолога- машиностроителя. В 2-х т. Под ред. А.Г. Косиловой – 4-е изд. перераб. и доп. - М.: Машиностроение 1986 ил.
Анурьев В.И. “Справочник конструктора-машиностроителя”: В 3-х т.- 5-е изд. перераб. и доп.- М.: Машиностроение 1979 ил.
Кочергин А.И. Конструирование и расчет металлорежущих станков и станочных комплексов. Курсовое проектирование: Учеб. пособие для вузов. - Мн.: Выш. шк. 1991. - 382 с.: ил.
Кузьмин А.В. Расчеты деталей машин: Справ. пособие. - 3-е изд. перераб. и доп. - Мн.: Выш. шк. 1986. - 400 с.: ил.
Детали машин в примерах и задачах Под ред. С.Н. Ничипорчика. - 2-е изд. - Мн.: Выш. школа 1981 – 432 с. ил.
Кучер И. М. Металлорежущие станки. – Л.: Машиностроение 1971г. 720 с.
Кинематика.dwg

Кинематическая схема
УО "ПГУ".15.01.00.000.К3
График частот вращения
Чертеж.cdw

Спецификация1.spw

УО "ПГУ".15.02.00.000.Сб
УО "ПГУ".15.02.00.001.Сб
Механизм переключения передач
УО "ПГУ".15.02.00.002.
УО "ПГУ".15.02.00.003.
УО "ПГУ".15.02.00.004.
УО "ПГУ".15.02.00.005.
УО "ПГУ".15.02.00.006.
УО "ПГУ".15.02.00.007.
УО "ПГУ".15.02.00.008.
УО "ПГУ".15.02.00.009.
УО "ПГУ".15.02.00.010.
УО "ПГУ".15.02.00.011.
УО "ПГУ".15.02.00.012.
УО "ПГУ".15.02.00.013.
УО "ПГУ".15.02.00.014.
УО "ПГУ".15.02.00.015.
УО "ПГУ".15.02.00.016.
УО "ПГУ".15.02.00.017.
УО "ПГУ".15.02.00.018.
УО "ПГУ".15.02.00.019.
Кольцо регулировочное
УО "ПГУ".15.02.00.020.
УО "ПГУ".15.02.00.021.
УО "ПГУ".15.02.00.022.
УО "ПГУ".15.02.00.023.
УО "ПГУ".15.02.00.024.
УО "ПГУ".15.02.00.025.
УО "ПГУ".15.02.00.026.
УО "ПГУ".15.02.00.027.
Винт М4х8 ГОСТ 11738-74
Кольцо 10 ГОСТ 13942-68
Кольцо 14 ГОСТ 13942-68
Кольцо 22 ГОСТ 13943-68
Кольцо 47 ГОСТ 13943-68
Подшипник 1000900 ГОСТ 8338-75
Подшипник 1000904 ГОСТ 8338-75
Подшипник 7204 ГОСТ 27365-87
Манжета 10 ГОСТ 8752-79
Шпонка 2х2х8 ГОСТ 23360-78
Кинематика.doc
Цель курсового проектирования – приобретение навыков проектирования. Работая над проектом мы выполняем расчеты учимся рационально выбирать материалы и форму деталей стремясь обеспечить их высокую экономичность надежность и долговечность. В проектировании широко используются ГОСТы учебная и справочная литература. Приобретенный в результате проектирования опыт будет являться основой дипломного проекта а также для всей дальнейшей конструкторской деятельности.
Проект состоит из пояснительной записки спецификации и графической части. Объем этих документов этих документов зависит от объема всего проекта установленного учебной программой. Объем графической части составляет три листа формата А1.
Определение технических характеристик станка.
Частота вращения шпинделя nmin
Мощность электродвигателя Nэл.
Наибольший условный диаметр сверления
Разработка и описание компоновки станка.
Вертикально-сверлильный станок предназначен для обработки отверстий. На станке можно обрабатывать детали как из легких сплавов так и из конструкционных.
Назначение станка. Станок предназначен для сверления (рассверливания) отверстий в различных материалах. На станке обрабатываются детали сравнительно небольшие размеров и веса.
Рис. 2.1 Компоновка вертикально-сверлильного станка.
Основные узлы станка: 1. сверлильная бабка; 2. рукоятка переключения скоростей; 3. линейка; 4. сверлильный шпиндель; 5. стол; 6. маховик; 7. колонна; 8. плита.
На рис. 1 приведен общий вид вертикально-сверлильного станка. Поперечное сечение колонны 7 представляет собой коробчатый прямоугольник передняя сторона которого является направляющей для перемещения сверлильной (шпиндельной) бабки и стола 5. Стол перемещают по направляющим колонны вручную с помощью винтового механизма маховичком 6. Стол станка имеет три Т-образных паза ширина рабочей поверхности выполнена по ГОСТ 6569 — 70. В сверлильной головке расположены механизм главного движения управляемый с помощью рукоятки 2 и штурвал 3 для управления механизмом подач сверлильного шпинделя 4. Колонна станка прикреплена к фундаментной плите 8 (основанию). В этой плите размещается бак для эмульсии которая подается электронасосом 9.
Движения в станке. Движение резания — вращение шпинделя с режущим инструментом. Движение подачи - осевое перемещение шпинделя с режущим инструментом. Вспомогательные движения — ручные перемещения стола и шпиндельной бабки в вертикальном направлении.Обрабатываемая деталь устанавливается на столе станка и закрепляется в машинных тисках или в специальных приспособлениях. Совмещение оси будущего отверстия с осью шпинделя осуществляется перемещением приспособления с обрабатываемой деталью на столе станка.
Режущий инструмент в зависимости от используемого хвостовика закрепляется в шпинделе станка при помощи патрона или переходных втулок. В соответствия с высотой обрабатываемой детали и длинной режущего инструмент производится установке стола и шпиндельной бабки.
Поверхности могут обрабатываться как ручным перемещением шпинделя так и механической подачей.
Проектирование и описание кинематической
Диапазон регулирования Rn частоты вращения исполнительного органа привода определяется по формуле:
Предельные частоты вращения принимаются равными nmax=4500 мин-1 и nmin=450 мин-1 (по заданию на проектирование). С учетом этого диапазон регулирования:
Число ступеней частоты вращения выходного вала определяется по формуле:
Тогда число ступеней:
Число ступеней не может быть дробным поэтому для обеспечения возможности регулирования скорости вращения во всем диапазоне частот принимается z=12.
Тогда формула структуры привода z=3(1)2(3)2(6)
Рис. 3.1. Структурная сетка
Затем строится график частот вращения (см. рис. 3.2).
Рис. 3.2. График частот вращения
По этому графику определяются передаточные отношения всех передач и проставляем их на графике: .
Произведём расчет чисел зубьев колес для основной группы аналитическим способом.
Формулы для расчета чисел зубьев колес аналитическим способом имеют вид:
где а и b – взаимно простые числа через которые выражается данное
передаточное отношение т. е.
- сумма чисел зубьев в рассматриваемой группе (определяется
наименьшее общее кратное сумм этой группы)
Тогда для основной группы:
Следовательно а наименьшее общее кратное сумм равно 18 (примем 54) которое присвоим Тогда числа зубьев колес передачи составят
Тогда для первой переборной группы:
Следовательно а наименьшее общее кратное сумм равно 6 (примем 54) которое присвоим Тогда числа зубьев колес передачи составят
Тогда для второй переборной группы:
Следовательно а наименьшее общее кратное сумм равно 126 которое присвоим Тогда числа зубьев колес передачи составят
Следует иметь в виду что рассчитанные из кинематических условий числа зубьев колес в дальнейшем при разработке конструкции привода могут быть изменены при сохранении значений передаточных отношений.
Рис. 3.3 Схема коробки скоростей
Привод подач заимствуем у станка-прототипа. Кинематическая схема представлена на рисунке 3.4.
Рис. 3.4 Кинематическая схема
Описание кинематической схемы станка. Кинематические цепи проектируемого станка позволяют осуществлять следующие движения:
главное движение – вращение шпинделя;
движение подачи – вертикальное механической перемещение;
ручное перемещение шпинделя;
ручное перемещение стола станка (установочное);
ручное перемещение сверлильной головки (установочное);
ручное вращение стола (установочное).
Главное движение шпинделя осуществляется от асинхронного электродвигателя через передачу привода 1(z=25) – 2(z=28) на вал I коробки скоростей цилиндрическую зубчатую передачу 3(z=24) – 8(z=30) либо 5(z=30) – 7(z=24) либо 4(z=27) – 6(z=27)на вал II коробки скоростей далее через цилиндрическую зубчатую передачу 9(z=18) – 11(z=36) либо 10(z=27) – 12(z=27) на вал III коробки скоростей далее через цилиндрическую зубчатую передачу 13(z=36) – 15(z=90) либо 14(z=77) – 16(z=49) на шпиндель IV.
Привод подачи осуществляется от выходного вала коробки скоростей через коробку подач и механизм подачи на рейку-гильзу шпинделя. Движение на коробку подач поступает через одиночную цилиндрическую зубчатую передачу 17(z=22) – 18(z=42) на вал V коробки подач далее через тройной блок зубчатых колес 19(z=29) – 22(z=19) либо 20(z=24) – 23(z=24) либо 21(z=16) – 24(z=32) на вал VI и далее через одиночную передачу 22(z=19) – 25(z=34) и 26(z=17) – 27(z=44) на рейку-гильзу шпинделя. Таким образом вращательное движение преобразуется в поступательное движение шпинделя.
Ручное перемещение шпинделя осуществляется при помощи штурвала.
Подъем и опускание стола производится при помощи червяка 36(k=1) червячного колеса 38(z=48) шестерни 39(z=28) и рейки.
Подъем и опускание сверлильной головки производится при помощи червяка 41(k=1) червячного колеса 40(z=20) шестерни 34(z=14) и рейки 35.
Для облегчения поворота стола на нижнем конце рейки имеется ролик который катится по нижнему фланцу колонны.
ДИНАМИЧЕСКИЕ И ПРОЧНОСНЫЕ РАСЧЕТЫ
1. Определение крутящих моментов
Следует отметить что при динамическом расчете привода главного движения максимальный крутящий момент на выходе коробки скоростей определяется не по номинальной а по расчетной частоте его вращения которая принимается равной первой ступени второй четверти диапазона регулирования скорости т.е. n4=800 обмин а также исходя из расчета наиболее нагруженных передач за расчетные принимаются частоты на валах: nI=2500 мин-1 nII=2000 мин-1 nIII=2000 мин-1 nIV=800 мин-1.
Мощность на первом валу коробки скоростей определяется по формуле:
РI=Pэд×hэд×hр.п×hп×hзп ; (4.1)
где Pэд=055 кВт мощность электродвигателя принимается из задания на проектирование.
hэд=097 hм.=098 hп=099 hзп=096 КПД соответственно электродвигателя муфты пары подшипников и зубчатой передачи 8 табл. 5.4.
Тогда мощность и угловая скорость на первом валу:
РI =055×097×098×099×096=04969 кВт;
Теперь можно определить наибольший крутящий момент по формуле:
Мощность на втором валу коробки скоростей:
Тогда мощность и угловая скорость на втором валу:
РII =04969×096×099=0472 кВт;
Мощность и угловая скорость на третьем валу:
РIII =0472×096×099=0448 кВт;
Мощность на шпинделе:
Тогда мощность и угловая скорость на шпинделе:
РIV =0448×096×099=0425 кВт;
Наибольший крутящий момент:
2. Расчет зубчатой передачи.
Для понижающей зубчатой передачи (2430) принимается прямозубая цилиндрическая передача как наиболее простая в изготовлении. Принимается для изготовления колес передачи для уменьшения номенклатуры сталь 40Х (улучшение) со следующими механическими характеристиками:
для ведущего колеса sв=830 Нмм2 sт=540 Нмм2 НВ=240 290;
для ведомого колеса sв=930 Нмм2 sт=690 Нмм2 НВ=260 300.
Пределы контактной выносливости по [9] табл. 9.11:
для ведомого колеса: s Нlimb=2×HB+70=2×295+70=660 Hмм 2
для ведущего колеса: s Нlimb=2×HB+70=2×285+70=640 Hмм 2
Расчетное число циклов перемены напряжений определяется по формуле [9 с. 193 форм. 9.32]:
где n1 частота вращения ведущего колеса n1=2500 обмин;
с число колес находящихся в зацеплении с рассчитываемым принимается с=1.
Lh расчетный срок службы передачи определяется по формуле [9 с. 14]:
Lh=8760×L×Kг×Кс; (4.4)
где L долговечность принимается равной 10 годам.
Кг коэффициент использования в течении года принимается Кг=066.
Кс коэффициент использования в течении суток принимается Кс=025.
Lh=8760×10×066×025=14454 ч ;
NH=60×2500×1×14454=21×10 9;
Для ведущего колеса и тем более для ведомого NH >NHO=18×10 7 поэтому принимаем коэффициент долговечности KHL=1 [9 с.191]
Допускаемые контактные напряжения при расчете на выносливость по формуле [9 с. 192 форм. 9.30]
где SH для улучшенных зубьев по [9 с. 192] SH=11.
для ведомого колеса: Hмм 2
для ведущего колеса: Hмм 2
Так как передача прямозубая расчет ведем по s НР наименьшему.
Допускаемые напряжения изгиба по формуле [9 с. 193 форм. 9.35]:
для ведомого колеса: s Flimb=260+HB=260+295=555 Hмм 2
для ведущего колеса: s Flimb=260+HB=260+285=545 Hмм 2
Допускаемые напряжения при SF=2 и KFC=1 односторонняя нагрузка по [9 с. 193] КFL=1 т.к. NFE=60×Lh×n1×с =60×14454×2500×1=21×109>NF0=4×106
Ориентировочное значение модуля по формуле [9 с. 184 форм. 9.5]:
где ybd коэффициент ширины шестерни относительно диаметра принимается ybd=04;
YF1 коэффициент учитывающий форму зуба по [9 с. 184 рис. 9.6] принимается YF1=39;
KFb коэффициент учитывающий неравномерность распределения нагрузки по ширине венца по [9 с. 182 рис. 9.5] принимается KFb=102;
Km вспомогательный коэффициент для прямозубых передач принимается Km=14;
Число зубьев колес принимаются по п. 3.3: z1=24 z2=30;
Уточняем диаметры колес по [9 с. 176]:
da1=d1+2×m=24+2×1=26 мм
da2=d2+2×m=30+2×1=32 мм (4.8)
df1=d1–2.5×m=24–2.5×1=215 мм
df2=d2–2.5×m=30–2.5×1=295 мм
Межосевое расстояние:
Рабочая ширина зацепления:
bw=ybd×d1=04×24=96 мм принимаем bw=10 мм . (4.10)
Проверочный расчет на выносливость по контактным напряжениям. Окружная сила:
По [9 с. 187 табл. 9.10] назначаем восьмую степень точности. По [9 с. 186 табл. 9.9] принимаем g 0=56. По [9 с. 186 табл. 9.7] dН=0006.
Удельная расчетная окружная сила в зоне ее наибольшей концентрации рассчитывается по формуле: [9] форм. 9.10:
KНb коэффициент учитывающий неравномерность распределения нагрузки по ширине венца по [9 с. 182 рис. 9.5] принимается KFb=101.
передаточное отношение.
Коэффициент учитывающий динамическую нагрузку возникающую в зацеплении определяем по формуле [9 с. 188 форм.9.15]:
Удельная расчетная окружная сила по формуле [9 с. 185 форм. 9.8]:
Расчетное контактное напряжение по формуле [9 с. 185 форм. 9.7]:
где zH коэффициент учитывающий форму сопряженных поверхностей в полюсе зацепления по [9] стр.185:
zМ – коэффициент учитывающий механические свойства материалов колес по[9 с. 185] zМ=275 Мпа.
ze коэффициент учитывающий суммарную длину контактных линий по [9 с. 185]:
где ea коэффициент торцового перекрытия по [9 с. 174 табл. 9.1]:
Следовательно условие прочности выполнено.
Проверка по напряжениям изгиба. Расчетное напряжение изгиба на переходной поверхности зуба по [9 с. 187 форм. 9.11]:
где YF1=39 коэффициент учитывающий форму зуба по [9 с. 184 рис. 9.6];
YF2=38 коэффициент учитывающий форму зуба по [9 с. 184 рис. 9.6];
Yb=1-b140=1 коэффициент учитывающий наклон зуба по [9 с.187];
Ye=1 коэффициент учитывающий перекрытие зубьев по [9 с.187];
Определяем менее прочное звено:
ведущее колесо менее прочное.
Расчет производим по ведущему колесу.
Из графика [9 с. 182 рис.9.5] коэффициент концентрации нагрузки КFb=105.
По [9с. 185 форм. 9.10]:
где dF=0016 коэффициент учитывающий влияние вида зубчатой передачи и модификации профиля головок зубьев по [9 с 186 табл. 9.8].
По [9 с. 188 форм. 9.16]:
Коэффициент динамической нагрузки по [9 с. 188 форм. 9.15]:
Удельная расчетная окружная сила по [9] форм. 9.12:
где КFa=1 для прямозубых передач по [9 с.188].
sF=39×1×1×3321=1296sFP=2775 Нмм 2
Напряжение изгиба действующее в зацеплении меньше допускаемого значит условие прочности выполнено.
3. Расчет зубчатой передачи.
Для зубчатой передачи (2727) принимается прямозубая цилиндрическая передача как наиболее простая в изготовлении. Принимается для изготовления колес передачи для уменьшения номенклатуры сталь 40Х (улучшение) со следующими механическими характеристиками:
где n1 частота вращения ведущего колеса n1=2000 обмин;
NH=60×2000×1×14454=17×10 9;
Допускаемые напряжения при SF=2 и KFC=1 односторонняя нагрузка по [9 с. 193] КFL=1 т.к. NFE=60×Lh×n1×с =60×14454×2000×1=173×109>NF0=4×106
YF1 коэффициент учитывающий форму зуба по [9 с. 184 рис. 9.6] принимается YF1=385;
Число зубьев колес принимаются по п. 3.3: z1=27 z2=27;
da1=d1+2×m=27+2×1=29 мм
da2=d2+2×m=27+2×1=29мм
df1=d1–2.5×m=27–25×1=245 мм
df2=d2–2.5×m=27–25×1=245 мм
bw=ybd×d1=04×27=108 мм принимаем bw=11 мм .
По [9 с. 187 табл. 9.10] назначаем девятую степень точности. По [9 с. 186 табл. 9.9] принимаем g 0=73. По [9 с. 186 табл. 9.7] dН=0006.
где YF1=385 коэффициент учитывающий форму зуба по [9 с. 184 рис. 9.6];
YF2=385 коэффициент учитывающий форму зуба по [9 с. 184 рис. 9.6];
ведомое колесо менее прочное.
Расчет производим по ведомому колесу.
Из графика [9 с. 182 рис.9.5] коэффициент концентрации нагрузки КFb=102.
Удельная расчетная окружная сила по [9] форм. 9.12 :
sF=385×1×1×3241=1247sFP=2775 Нмм 2
4. Расчет зубчатой передачи.
Для понижающей зубчатой передачи (3690) принимается прямозубая цилиндрическая передача как наиболее простая в изготовлении. Принимается для изготовления колес передачи для уменьшения номенклатуры сталь 40Х (улучшение) со следующими механическими характеристиками:
Допускаемые напряжения при SF=2 и KFC=1 односторонняя нагрузка по [9 с. 193] КFL=1 т.к. NFE=60×Lh×n1×с =60×14454×2000×1=17×109>NF0=4×106
YF1 коэффициент учитывающий форму зуба по [9 с. 184 рис. 9.6] принимается YF1=375;
Число зубьев колес принимаются по п. 3.3: z1=36 z2=90;
da1=d1+2×m=36+2×1=38 мм
da2=d2+2×m=90+2×1=92мм
df1=d1–2.5×m=36–25×1=345 мм
df2=d2–2.5×m=90–25×1=875 мм
bw=ybd×d1=04×36=144 мм принимаем bw=15 мм .
YF2=355 коэффициент учитывающий форму зуба по [9 с. 184 рис. 9.6];
sF=375×1×1×5041=1893sFP=2775 Нмм 2
5. Расчет вала I на прочность.
Составляем расчетную схему где вал рассматриваем как балку лежащую на шарнирных опорах и намечаем расстояние между опорами.
Окружное усилие в зацеплении:
Ft21 = 2 * Т1 d1 = 2 * 19 0024 = 1583 Н;
Радиальное усилие в том же зацеплении:
Fr21 = Ft21 * tg200 = 1583 · 0364 = 576 H;
На вал I со стороны привода действует сила F которая определяется по формуле: Ft = 2 * Тэд d0 = 2 * 187 0025 = 1496 Н;
Fr = Ft * tg200 = 1496 · 0364 = 544 H;
где Тэд=Рэд=055293=187 Нм;
Строим схему нагружения вала 1 рис. 4.1.
Определяем опорные реакции в вертикальной плоскости (ZOY):
M A = 0: RBy *185 + Ft * 30 – Fr21 * 40 = 0;
M B = 0: RAy * 185 - Ft * 215 + Fr21 * 145 = 0;
Определяем опорные реакции в горизонтальной плоскости (ZOX):
Принимаем с учетом рекомендаций по 9 стр. 291 материал вала – сталь 45. По 9 табл. 12.13 для стали 45 : s -1 = 432 Нмм 2 t -1 = 255 Нмм 2 – пределы выносливости материала вала при симметричных циклах изгиба и кручения s B = 883 Нмм 2 – предел прочности. По 9 табл. 12.2 es= 0.8 – коэффициент учитывающий снижение механических свойств материала с увеличением размера заготовок для углеродистых сталей. По 9 табл. 12.5 Кs= 1.9 – эффективный коэффициент концентрации напряжений для валов в месте шпоночного паза. По 9 стр. 275: S = 3 – коэффициент безопасности при симметричном изменении напряжения изгиба и кручения. По 9 табл. 12. 9 b = 2 – коэффициент учитывающий упрочнение поверхности при поверхностной закалке.
Эквивалентное число циклов :
N LE = NH = 60 * 2500 * 1 * 14454 = 21 * 10 9 ;
Коэффициент долговечности:
где m = 9 – показатель степени кривой усталости по 9 стр.275.
N 0 = 5 * 10 6 – базовое число циклов перемены напряжений по 9 стр275.
Допускаемый предел выносливости при симметричных циклах изгиба по 9 форм. 12.3:
Рис. 4.1. Схема нагружения вала I
Суммарный изгибающий момент в опасных сечениях:
Эквивалентный момент в опасных сечениях по 9 стр.185 :
ME I = T = 1900 Н*мм
Диаметр в опасных сечениях по 9 форм. 12.2:
d I = 8 мм – диаметр вала под полумуфту.
d II = 10 мм – диаметр вала под подшипниками.
d III = 11 мм – диаметр вала под зубчатым колесом.
Нормальные напряжения возникающие в поперечном сечении вала от изгиба изменяется по симметричному циклу по 8 форм.14.14 :
где W – момент сопротивления вала со шлицами(6х11х14):
Где – для шлицев легкой серии – для шлицев средней серии наружный диаметр d = 14 мм.
s а = М ЕIII W = 8414 2692 = 3125 Мпа
Так как момент передаваемый валом является переменным то при расчете примем для касательных напряжений наиболее благоприятный знакопостоянный цикл – отнулевой по 8 форм. 14.15:
t а = t m = Т (2*WK) ; (4.29)
t а = t m = 1900 (2*649) = 146 Мпа
Коэффициент запаса прочности по нормальным напряжениям по 8 форм. 14.9:
где e s = 0.8 - масштабный фактор по 8 табл. 14.
По 8 табл. 14.2 для шлицевых валов К s = 1.75 – эффективный коэффициент концентрации напряжений при изгибе. По 8 табл. 14.4 y s = 0.2 – коэффициент учитывающий влияние постоянной составляющей цикла на усталость вала.
где e t = 0.8 - масштабный фактор по 9 табл. 14.3.
По 8 табл. 14.2 К t = 28 – эффективный коэффициент концентрации напряжений при изгибе. По 8 табл. 14.4 y t = 0.2 – коэффициент учитывающий влияние постоянной составляющей цикла на усталость вала.
Условие прочности по 8 форм. 14.8:
где [S] = 1.3 1.5 – требуемый коэффициент запаса для обеспечения прочности.
Прочность вала в опасном сечении обеспечена.
6. Расчет вала II на прочность.
Ft32 = 2 * Т2 d2 = 2 * 225 0027 = 1666 Н;
Fr32 = Ft32 * tg200 = 1666 · 0364 = 606 H;
M A = 0: -RBy*160+Fr32*145- Ft12*55=0;
M B = 0: -RAy*160-Fr32*15+ Ft21*105=0;
Принимаем с учетом рекомендаций по 9 стр. 291 материал вала – сталь 45. По 9 табл. 12.13 для стали 45 : s -1 = 432 Нмм 2 t -1 = 255 Нмм 2 – пределы выносливости материала вала при симметричных циклах изгиба и кручения s B = 883 Нмм 2 – предел прочности. По 9 табл. 12.2 es= 0.8 – коэффициент учитывающий снижение механических свойств материала с увеличением размера заготовок для углеродистых сталей. По 9 табл. 12.5 Кs= 1.9 – эффективный коэффициент концентрации напряжений для шлицевых валов. По 9 стр. 275: S = 3 – коэффициент безопасности при симметричном изменении напряжения изгиба и кручения. По 9 табл. 12. 9 b = 2 – коэффициент учитывающий упрочнение поверхности при поверхностной закалке.
Эквивалентное число циклов:
N LE = NH = 60 * 2000 * 1 * 14454 = 173 * 10 9 ;
Рис. 4.2. Схема нагружения вала II
d I = 8 мм – диаметр вала под подшипниками.
d II = 11 мм – диаметр вала под зубчатым колесом.
где W – момент сопротивления вала со шлицами и полостью d = 55 мм:
Где – для шлицев легкой серии – для шлицев средней серии наружный диаметр = 14 мм.
s а = М ЕIII W = 5976 2692= 222 Мпа
Так как момент передаваемый валом является переменным то при расчете примем для касательных напряжений наиболее благоприятный знакопостоянный цикл – отнулевой по 8 форм. 14.15 :
t а = t m = Т (2*WK) ;
t а = t m = 2250 (2*649) = 173 Мпа
По 8 табл. 14.2 К s = 1.75 – эффективный коэффициент концентрации напряжений при изгибе. По 8 табл. 14.4 y s = 0.2 – коэффициент учитывающий влияние постоянной составляющей цикла на усталость вала.
По 8 табл. 14.2 для шлицев К t = 28 – эффективный коэффициент концентрации напряжений при изгибе. По 8 табл. 14.4 y t = 0.2 – коэффициент учитывающий влияние постоянной составляющей цикла на усталость вала.
Условие прочности по 8 форм. 14.8 :
7. Расчет вала III на прочность.
Ft43 = 2 * Т3 d3 = 2 * 214 0036 = 1188 Н;
Fr43 = Ft43 * tg200 = 1188 · 0364 = 432 H;
M A = 0: RBy*190+Fr43*90- Ft32*55=0;
M B = 0: -RAy*190-Fr43*100+ Ft32*135=0;
Рис. 4.3. Схема нагружения вала III
s а = М ЕIII W = 5778 2692=214 Мпа
t а = t m = 2140 (2*649) = 165 Мпа
8. Расчет вала IV на прочность.
Окружное усилие в зацеплении 1872:
Ft43 = 2 * Т3 d = 2 * 2.14 0036 = 1188 Н;
Окружное усилие в зацеплении 2242:
Ft54 = 2 * Т4 d = 2 * 508 000275 = 370 Н;
Fr54 = Ft54 * tg200 = 370 · 0364 = 1347 H;
M A = 0: -RBy*190+Ft54*220-Fr43*100=0;
M B = 0: -RAy*190+Ft54*30+ Fr43*90=0;
Принимаем с учетом рекомендаций по 9 стр. 291 материал вала – сталь 45. По 9 табл. 12.13 для стали 45: s -1 = 432 Нмм 2 t -1 = 255 Нмм 2 – пределы выносливости материала вала при симметричных циклах изгиба и кручения s B = 883 Нмм 2 – предел прочности. По 9 табл. 12.2 es= 0.8 – коэффициент учитывающий снижение механических свойств материала с увеличением размера заготовок для углеродистых сталей. По 9 табл. 12.5 Кs= 1.9 – эффективный коэффициент концентрации напряжений для валов в месте шпоночного паза. По 9 стр. 275: S = 3 – коэффициент безопасности при симметричном изменении напряжения изгиба и кручения. По 9 табл. 12. 9 b = 2 – коэффициент учитывающий упрочнение поверхности при поверхностной закалке.
N LE = NH = 60 * 800 * 1 * 14454 = 69 * 10 8 ;
ME I = T = 2140 Н*мм
Рис. 4.4. Схема нагружения вала IV
d I = 15 мм – диаметр вала под подшипниками.
d II = 16 мм – диаметр вала под зубчатым колесом.
где W – момент сопротивления вала со шлицами (6х16х20) и полостью d = 20 мм:
Где – для шлицев легкой серии – для шлицев средней серии наружный диаметр = 20 мм.
s а = М ЕIII W = 12004 883=136 Мпа
t а = t m = 2140 (2*17662) = 06 Мпа
9. Подбор и проверочный расчет соединений.
9.1. Соединение зубчатое колесо-вал 1.
Выбираем по стандарту призматическую шпонку для соединения зубчатого колеса с валом d = 8 мм. Материал шпонки – Сталь 20 передаваемый момент Т = 19 Н*м соединение работает при переменной нагрузке. По ГОСТ 23360-78 выбираем шпонку призматическую обыкновенную (исполнение А) со следующими размерами:
B = 3 мм ; h = 3 мм ; t 1 = 18 мм ; t 2 = 1.4 мм ;
Находим допускаемое напряжение смятия по [8] табл. 5.1:
Определяем рабочую длину шпонки по [8]форм. 5.1:
где k – рабочая высота k = 0.4 * h = 0.4 * 3 = 12 мм.
Находим общую длину шпонки:
L = l P + b = 33 + 3 = 66 мм (4.34)
Принимаем: шпонка 3 3 10 ГОСТ 23360-78
9.2. Соединение блока зубчатых колес – вал 1.
Для соединения блока зубчатых колес с валом 1 принимается шлицевое соединение 6 х 11 х 14 по ГОСТ 1139-58. По [8] табл. 4.5 определяется суммарный статический момент площади рабочих поверхностей соединения относительно оси вала sF = 34 мм2 мм и средний диаметр dm = 0.5 * ( D + d ) = 0.5 * ( 11 + 14 ) = 125 мм.
Среднее давление по [9] форм. 5.8:
Допускаемое давление на смятие по [9] форм. 5.10:
Где sТ — предел текучести материала шлицев по [9] табл.12.13 принимается sТ = 638 Нмм2 .
КСМ — общий коэффициент концентрации нагрузки при расчете на смятие по [9] стр.87:
КСМ = Кз * Кпр * Кп ;
Кз — коэффициент неравномерности распределения нагрузки между шлицами определяется в зависимости от параметра:
по [9] табл.5.7 Кз = 21.
Кпр — коэффициент продольной концентрации нагрузки ( по длине соединения) по [9] стр.83:
Значение коэффициента Ккр определяется по [9] табл.5.8 в зависимости от lD = 5714 = 407 и принимается Ккр = 27.
Значение коэффициента концентрации давления Ке от относительного смещения нагрузки определяется в зависимости от параметра e по [9] стр. 88:
для прямозубых колес b = 0 е = 24 мм — расстояние от середины посадочной поверхности до середины венца зубчатого колеса тогда по [9] рис.5.12 Ке = 19.
Кпр = 27 + 19 – 1 = 36
Кп = 1.1 — для закаленных сталей.
Тогда коэффициент концентрации нагрузки при расчете на смятие:
Ксм = 21 * 36 * 11 = 83
КД = 1.5 — коэффициент динамичности нагрузки.
Тогда допускаемое давление на смятие:
Соединение удовлетворяет условию прочности на смятие т.к. s = 1 [s] = 274 Нмм2 .
9.3. Соединение зубчатого колеса – вал 2.
Для соединения блока зубчатых колес с валом 2 принимается шлицевое соединение 6 х 11 х 14 по ГОСТ 1139-58. По [8] табл. 4.5 определяется суммарный статический момент площади рабочих поверхностей соединения относительно оси вала sF = 34 мм2 мм и средний диаметр dm = 0.5 * ( D + d ) = 0.5 * ( 11 + 14 ) = 125 мм.
по [9] табл.5.7 Кз = 20.
Значение коэффициента Ккр определяется по [9] табл.5.8 в зависимости от lD = 1014 = 07 и принимается Ккр = 084.
для прямозубых колес b = 0 е = 24 мм — расстояние от середины посадочной поверхности до середины венца зубчатого колеса тогда по [9] рис.5.12 Ке = 22.
Кпр = 084 + 22 – 1 = 204
Ксм = 20 * 204 * 11 = 45
Соединение удовлетворяет условию прочности на смятие т.к. s = 66 [s] = 506 Нмм2 .
9.4. Соединение зубчатое колесо-вал 3.
Для соединения блока зубчатых колес с валом 3 принимается шлицевое соединение 6 х 11 х 14 по ГОСТ 1139-58. По [8] табл. 4.5 определяется суммарный статический момент площади рабочих поверхностей соединения относительно оси вала sF = 34 мм2 мм и средний диаметр dm = 0.5 * ( D + d ) = 0.5 * ( 11 + 14 ) = 125 мм.
где sТ — предел текучести материала шлицев по [9] табл.12.13 принимается sТ = 638 Нмм2 .
по [9] табл.5.7 Кз = 17.
Значение коэффициента Ккр определяется по [9] табл.5.8 в зависимости от lD = 1514 = 107 и принимается Ккр = 16.
для прямозубых колес b = 0 е = 75 мм — расстояние от середины посадочной поверхности до середины венца зубчатого колеса тогда по [9] рис.5.12 Ке = 185.
Кпр = 16 + 185 – 1 = 255
Ксм = 17 * 245 * 11 = 46
КД = 2 — коэффициент динамичности нагрузки.
Соединение удовлетворяет условию прочности на смятие т.к. s = 42 [s] = 495 Нмм2 .
9.5. Соединение блок зубчатых колес-вал 4.
Для соединения блока зубчатых колес с валом 4 принимается шлицевое соединение 6 х 21 х 25 по ГОСТ 1139-58. По [8] табл. 4.5 определяется суммарный статический момент площади рабочих поверхностей соединения относительно оси вала sF = 97 мм2 мм и средний диаметр dm = 0.5 * ( D + d ) = 0.5 * ( 21 + 25 ) = 23 мм.
по [9] табл.5.7 Кз = 356.
Значение коэффициента Ккр определяется по [9] табл.5.8 в зависимости от lD = 3625 = 144 и принимается Ккр = 14.
для прямозубых колес b = 0 е = 285 мм — расстояние от середины посадочной поверхности до середины венца зубчатого колеса тогда по [9] рис.5.12 Ке = 3.
Кпр = 14 + 3 – 1 = 34
Ксм = 356 * 34 * 11 = 133
Соединение удовлетворяет условию прочности на смятие т.к. s = 145 [s] = 171 Нмм2 .
10. Выбор подшипников.
10.1. Вал 1 коробки скоростей.
Диаметр шейки вала d = 10 мм частота вращения n = 2500 мин –1. По [9] табл. 14.18 Кs = 1.2 – коэффициент безопасности.
Требуемая динамическая грузоподъемность для роликовых подшипников вала по [9] стр.358:
где V – коэффициент учитывающий вращение кольца по [9] стр.348 для вращающегося внутреннего кольца V = 1.
X – коэффициент радиальной нагрузки по [9] табл. 14.14 Х = 1.
К Т – температурный коэффициент если она превышает 398.15 0К то по [9] табл. 14.19 К Т = 1.05.
n – частота вращения вала 1.
L h – долговечность подшипника L h = 14454 ч.
Р – степенной показатель для шариковых по [9] стр. 334 р = 3.
Для данного d = 10 мм подшипника по ГОСТ 8338-75 динамическая грузоподъемность С = 3340 Н что больше требуемой поэтому принимается радиальный шариковый подшипник 1000900 который соответствует требуемой долговечности и выдержит прикладываемую опорную реакцию.
10.2. Вал 2 коробки скоростей.
Диаметр шейки d = 10 мм частота вращения n = 2000 мин –1. По [9] табл. 14.18 Кs = 1.2 – коэффициент безопасности.
Требуемая динамическая грузоподъемность для шариковых подшипников вала по [9] стр.358 :
10.3. Вал 3 коробки скоростей.
Требуемая динамическая грузоподъемность для шариковых подшипников вала по [9] стр.358:
10.4. Вал 4 коробки скоростей.
Диаметр шейки d = 20 мм частота вращения n = 800 мин –1. По [9] табл. 14.18 Кs = 1.2 – коэффициент безопасности.
Для данного d = 20 мм подшипника по ГОСТ 8338-75 динамическая грузоподъемность С = 6550 Н что больше требуемой поэтому принимается радиальный шариковый подшипник 1000904 который соответствует требуемой долговечности и выдержит прикладываемую опорную реакцию.
Выбор вида смазывания передач и
подшипников уплотняющих средств
Смазочной системой называют совокупность устройств для подачи смазочного материала к трущимся поверхностям и возврата его в резервуар. Систему смазывания жидким материалом выбирают исходя из требуемой быстроходности механизмов исходя из их расположения конструкции уплотнений. Для данной коробки скоростей лучше использовать циркуляционное смазывание т.к. оно обладает рядом преимуществ: используется один и тот же объем масла что уменьшает стоимость оборудования осуществляется подвод смазки ко всем трущимся поверхностям одновременно что обеспечит независимую смазку каждого узла. Данная система смазки использует струйную подачу смазочного материала к зубчатым передачам посредством трубок. Опоры валов смазываются маслом которое подается в подшипник по валам.
При выборе сорта масла особое внимание необходимо уделить вязкости. Для этого учитывается частота вращения деталей их конструкция и температура. Согласно вышеизложенному целесообразно применить масло марки И-30А.
При выполнения данного курсового проекта я изучил подробно назначение вертикально-сверлильного станка его структуру область применения овладел методами моделирования и оптимизации а также научился анализировать его достоинства и недостатки и делать собственные выводы.
СПИСОК ИСПОЛЬЗОВАННЫХ ИСТОЧНИКОВ
Ачеркан Н.С. Металлорежущие станки. Т1. М.- Машиностроение. 1965г.
Общемашиностроительные нормативы расчета режимов резания.
Тарзиманов Г.А. Проектирование металлорежущих станков. М. “Машиностроение” 1972 312 стр.
Данилов В.А. Методические указания к курсовому проекту. Новополоцк – 1987.
Справочник технолога- машиностроителя. В 2-х т. Под ред. А.Г. Косиловой – 4-е изд. перераб. и доп. - М.: Машиностроение 1986 ил.
Анурьев В.И. “Справочник конструктора-машиностроителя”: В 3-х т.- 5-е изд. перераб. и доп.- М.: Машиностроение 1979 ил.
Кочергин А.И. Конструирование и расчет металлорежущих станков и станочных комплексов. Курсовое проектирование: Учеб. пособие для вузов. - Мн.: Выш. шк. 1991. - 382 с.: ил.
Кузьмин А.В. Расчеты деталей машин: Справ. пособие. - 3-е изд. перераб. и доп. - Мн.: Выш. шк. 1986. - 400 с.: ил.
Детали машин в примерах и задачах Под ред. С.Н. Ничипорчика. - 2-е изд. - Мн.: Выш. школа 1981 – 432 с. ил.
Рекомендуемые чертежи
- 07.06.2021