Привод главного движения радиально-сверлильного станка



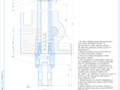
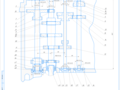
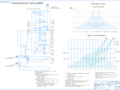
- Добавлен: 25.01.2023
- Размер: 647 KB
- Закачек: 1
Описание
Состав проекта
![]() |
![]() |
![]() ![]() ![]() ![]() |
![]() ![]() ![]() ![]() |
![]() |
![]() ![]() ![]() |
![]() ![]() ![]() ![]() |
Дополнительная информация
Головка сверлильная Лист3.cdw

КП 36.01.01.2532.03.00.000
При сборке свободный объем подшипников запол-
нить смазкой ЦИАТИМ201 ГОСТ6267-74.
Расход смазки на каждый подшипник 0.0016кг.
При сборке все подшипники смазать маслом "Ин-
Вращение шпинделя от руки должно быть лег-
ким плавным. без рывков и заеданий.
Пиноль поз.4 должна перемещаться плавно
без рывков и заеданий.
поступающий на общую сборку станка
жен сопровождаться актом за подписью представи-
удостоверяющего его пригодность.
При сборке шпиндельного узла обеспечить сво-
бодное вращение шпинделя в подшипниках при пол-
ном отсутствии осевого люфта
шпинделя после испытания в работе не бо-
лее 0.015мм. Узел обкатать в течении 30 минут на
00 обмин. При этом нагрев подшипников не
Непараллельность оси шпинделя
линдрической поверхности пиноли не более 0.010мм
Перед установкой узла на станок смазать по-
верхность зубьев пиноли тонким слоем ЦИАТИМ201
При поставке узла в качестве запасной части.
ровать порядковый номер. Дополнительную марки-
ровку нанести на бумажную или картонную бирку.
На бирке маркировать обозначение узла. номер
заказ-наряда. штамп ОТК. дату.
Допуск радиального биениея конуса шпинделя
а) у торца шпинделя - 0.008мм;
б) на расстоянии L-150мм - 0.012мм.
Остальные ТТ по СТБ 1022-96.
ЛИСТ 1 - КИНЕМАТИЧЕСКАЯ СХЕМА.cdw

Основные технические данные и характеристики
Класс точности по ГОСТ 8-77 - Н
Наибольший условный диаметр сверления в стали 45 по ГОСТ
Наибольший диаметр нарезаемой резьбы в стали 45 по ГОСТ
Расстояние от оси шпинделя до направляющих колонны(вылет)
Наибольшее расстояние от торца шпинделя
Наибольший угол поворота рукава вокруг колонны
Наибольший ход сверлильной головки по рукаву
Размер конуса шпинделя к.м - 4
Наибольший угол поворота стола вокруг колонны
Количество частот вращения шпинделя - 16
Пределы частот вращения шпинделя мин-1 - (50-1600)
Количество подач - 6
Пределы подач ммоб - 0
Угол поворота стола относительно бочки
Размеры рабочей поверхности
- стола - 450 x1000
Скорость перемещения стола по колонне
Питающая электросеть
- род тока переменный трехфазный - частота
Мощность электродвигателя главного привода КВТ
Количество электродвигателей на станке - 3
Габарит станка (LxBxH)
График частот вращения
Кинематическая схема привода
2532Л.doc
КИНЕМАТИЧЕСКИЙ РАСЧЕТ ПРИВОДА ГЛАВНОГО ДВИЖЕНИЯ.10
РАСЧЕТ ЭЛЕМЕНТОВ КОРОБКИ СКОРОСТЕЙ.16
1 Расчёт зубчатых передач16
2 Расчёт валов. Определение реакций в подшипниках построение эпюр21
3 Проверочный расчёт валов на прочность25
4 Расчёт подшипников27
ОБОСНОВАНИЕ И ВЫБОР КОНСТРУКЦИИ ШПИНДЕЛЯ29
РАСЧЕТ ШПИНДЕЛЬНОГО УЗЛА.32
1 Расчет шпиндельного узла на точность.32
2 Расчёт шпиндельного узла на жёсткость.33
3 Расчет шпинделя на виброустойчивость.35
НАЗНАЧЕНИЕ СИСТЕМЫ СМАЗКИ СТАНКА36
ВОПРОСЫ ОХРАНЫ ТРУДА И ТЕХНИКИ БЕЗОПАСНОСТИ38
Используемая литература:44
Анализируя перспективы развития и состояние в области новых достижений станкостроения и робототехники следует отметить что они вытекают из комплексных исследований технологических процессов конструкций технологического оборудования систем упpавления и комплектующих изделий и материалов. Причиной глубоких комплексных исследований и принципиально новых pазpаботок является международная динамика pынка и конкуренции которые обусловлены следующим :
За прошедшее десятилетие произошли глубокие сдвиги в мировой стpуктуpе станкостроения и робототехники:
- Благодаpя мощному и относительно замкнутому внутpеннему pынку а также pаспpостpанению пpактически на все виды технологического обоpудования имеющегося на миpовом pынке Япония заняла ведущее место на миpовом pынке;
- Пpи относительно постоянной доле в миpовом потpеблении станков и pоботов pынок США стал аpеной конкуpентной боpьбы между Японскими Епpопейскими и собственными фиpмами. Наводнение pынка качественным товаpом пpивело в амеpиканской пpомышленности к методичному вытеснению неконкуpентоспособных фиpм что пpивело к пpотекционистским меpам амеpиканского госудаpства;
- Евpопейским фиpмам-изготовителям пpишлось столкнуться со все более возpастающей конкуpенцией с Японцами. Наименее чувствительными оказались фиpмы ФРГ но и им пpишлось лишиться заваоеванных позиций. Из-за сильного пpотивостояния на амеpиканском pынке для Японии все более пpивлекательны становится емкий pынок ФРГ (Объединенной Геpмании);
- Неплатежеспособный отложенный спpос на высокие технологии в бывших социалистических стpанах СССР и Китае вносит фактоp непpогнозиpуемости в оценки объемов экспоpтных поставок ведущих капиталистических стpан - пpоизводителей станков и pоботов.
- Экспоpтная стpатегия Японии США и ФРГ в основном постpоена на следующих общих посылках :
А) Соответствующий вид пpодукции уже имеется в большом количестве или избытке на внутpеннем pынке следовательно имеются большие пpоизводственные мощности для pеализации экспоpтных возможностей ;
Б) Спpос на внутpеннем pынке падает. Необходимо искать дополнительные возможности сбыта для загpузки пpоизводственных мощностей;
В) Издеpжки тpуда и матеpиалов в Японии ниже чем в ФРГ в ФРГ ниже чем в США пpи пpимеpно одинаковом стандаpте заpаботной платы;
Г) Японские фиpмы опеpедили всех по пpоизводительности тpуда. Они изготавливают pавноценную или даже лучшую пpодукцию с меньшими затpатами тpуда в pасчете на единицу пpодукции.
Вышеизложенные тенденции и статус-кво в динамике pынка и конкуpенции опpеделяют пути pазвития станкостpоения и pобототехники.
Основной тенденцией в pазвитии станкостpоения и pобототехники является все более интенсивное пpименение технологического обоpудования постpоенного по блочно-модульному методу. Необходимость pеализации котоpого обусловленна следующими пpотивоpечиями в pазвитии станкостpоения и pобототехники:
- постоянное тpебование к pасшиpению номенклатуpы и обновлению пpодукции вызванное pасшиpением запpосов потpебителей ;
- постоянное тpебование к минимизации пpоизводственных издеpжек за счет увеличения сеpийности;
- постоянное тpебование к эpгономике.
Эти тенденции опpеделяют основные тpебования к пpоизводителям металлообpабатывающего обоpудования :
- постоянное увеличение номенклатуpы (а в некотоpых случаях и объемов).
- гибкое и опеpативное pеагиpование на пеpманентно изменяющиеся тpебования pынка (особенно к техническому уpовню пpодукции);
- постоянное повышение конкуpентоспособности товаpа.
Основные тpебования в свою очеpедь опpеделяют технико -экономический уpовень котоpый опpеделяется совокупностью уpовней входящих в технологическое обоpудование (пpодукт) составных частей.
Повышение технико-экономического уpовня станков и pоботов опpеделяется изменением технико-экономических хаpактеpистик отдельных составных частей.
В станкостpоении и pобототехнике пpодукция и физически и моpально стаpеет ни в целом а дискpетно по частям. Все это говоpит о том что без пpименения блочно-модульного метода постpоения повышение технико-экономического уpовня пpодукции пpактически невозможно
Мехатpонные узлы и электpомеханические модули являются наиболее пеpспективной базой для создания пpогpессивного высокопpоизводительного технологического обоpудования одним из пpинципов постpоения котоpого является автономность изготовления сбоpки и отладки узлов и конечного пpодукта на их базе.
Целью нашего курсового проектирования является модернизация привода главного движения радиально –сверлильного станка с поворотным столом 2532Л (см. рисунок 1) .
Станок предназначен для выполнения разнообразных сверлильно-расточных и резьбонарезных работ сверлами зенкерами развертками метчиками и другими инструментами в условиях индивидуального и серийного производства.
Оснащение станка специальными приспособлениями и инструментом значительно расширяет технологические возможности станка и позволяет выполнять тонкую расточку нарезание крупных резьб.
Рисунок 1 – Станок 2532Л
Техническая характеристика (основные параметры и размеры согласно ГОСТ 1222-80)
Класс точности Н по ГОСТ 8-77.
Наибольший условный диаметр сверления в стали 45 по ГОСТ 1050-80 мм 32
Наибольший диаметр нарезаемой резьбы в стали 45 по ГОСТ 1050-80 мм .М24х3
Расстояние от оси шпинделя до направляющих колонны(вылет) мм
Наибольшее расстояние от торца шпинделя мм
Диаметр колонны мм 240
Наибольший угол поворота рукава вокруг колонны град .±180
Наибольший ход сверлильной головки по рукаву мм 720
Размер конуса шпинделя к.м 4
Наибольший угол поворота стола вокруг колонны град .±180
Количество частот вращения шпинделя 12
Пределы частот вращения шпинделя мин-1 46-1600
Пределы подач ммоб 01-11
Угол поворота стола относительно бочки град - 80+ 90
Размеры рабочей поверхности мм
Скорость перемещения стола по колонне мммин 314
Питающая электросеть
- род тока переменный трехфазный - частота ГЦ 50
Мощность электродвигателя главного привода КВТ 135
Количество электродвигателей на станке 3
Габарит станка (LxBxH) мм 1850x800x2600
Масса станка кг 2050
РАСЧЕТ ТЕХНИЧЕСКИХ ХАРАКТЕРИСТИК СТАНКА.
Рассчитаем технические характеристики станка. Расчет будем производить по методике приведенной в [3] для этого определим режимы резания силу резания и мощность для сверления отверстия. Исходными данными для расчета режимов резания будут параметры обработки.
Максимальный диаметр сверления: D=32 мм;
Материал обработки Сталь 45 (B=810МПа).
Материал режущей части сверла Р6М5.
Находим скорость резанья:
где КV - общий поправочный коэффициент на скорость резанья учитывающий фактические условия резанья рассчитывается по формуле:
Kv = KMv · KИv · Klv (1.2)
где: KMv – коэффициент учитывающий обрабатываемый материал;
KИv – коэффициент учитывающий инструментальный материал;
-для стали Кlv=085 (1.5)
Коэффициент учитывающий обрабатываемый материал равен:
Тогда общий поправочный коэффициент равен:
Для стали: 1071085=0909;
Коэффициент Cv и показатели степени определяем по [1] табл. 38.
Для сталей обработка быстрорежущей сталью Cv = 98; y = 05; m = 02 q=04;
Получим окончательно скорость резания:
Частота вращения мин-1:
Находим крутящий момент и осевую силу.
где СМ и СР и другие показатели степени приведены в [1] таблица 42;
КР=КМР – коэффициент зависящий от материала обрабатываемой заготовки и приведены в [1] таблица 9 для стали получим:
Находим мощность резания.
Рассчитаем режимы резания для нарезания внутренней резьбы метчиком с проходным хвостовиком для метрической резьбы (по ГОСТ 3266-81)
Параметры резьбы: М24×3
Материал режущей части Р6М5
Стойкость режущего инструмента Т=90 мин
Скорость резанья ммин:
где КV – общий поправочный коэффициент на скорость резания:
KИV – коэффициент учитывающий качество материала инструмента по [1] таблица 6;
KMV-коэффициент учитывающий качество обрабатываемого материала по [1] таблица 1;
КСV – коэффициент учитывающий способ нарезания резьбы;
СV и другие показатели степени находим по [1] таблица 118:
Cv = 410; y = 05; m = 09; q=12; Т=90 мин
Находим крутящий момент:
где СМ и другие показатели степени определяем по [1] таблица 120:
CМ = 0025; y = 15; q=2.
КР=КМР – коэффициент зависящий от материала обрабатываемой заготовки и приведены в [3] таблица 119 (КР=1);
Так как расчет производился только для максимально-возможной резьбы нарезаемой на нашем станке то требуется учесть что частота вращения полученная при расчете не является минимальной. Также следует учесть и минимально-возможные диаметры обработки (до 16 мм) поэтому принимаем минимальную частоту из базового станка (50 ).
КИНЕМАТИЧЕСКИЙ РАСЧЕТ ПРИВОДА ГЛАВНОГО ДВИЖЕНИЯ.
Для станков сверлильной группы могут быть использованы 3 варианта структуры привода главного движения (рисунок 2.1).
Рисунок 2.1 - Структуры привода главного движения.
Нераздельная структура привода главного движения (рисунок 2.1а) имеют следующие характеристики:
-компактные габаритные размеры
-достаточно высокую надежность
-минимальную материалоемкость
-относительно высокое быстродействие
Однако недостатками такой конструкции являются :
-невысокая точность вращения шпинделя
-передача теплоты и вибрации от коробки скоростей к шпинделю
Раздельная структура привода (рисунок 2.1б) по сравнению с нераздельной имеет преимущества только по точности вращения шпинделя и отсутствия передачи теплоты и вибраций от коробки скоростей к шпинделю а по всем остальным вышеперечисленным параметрам уступают нераздельной структуре привода главного движения.
Раздельная структура привода (рисунок 2.1б) по сравнению с нераздельной (рисунок 2.1а) также уступает по габаритам передают большой крутящий момент но присутствуют такие недостатки как вибрации и передача тепла к шпинделю.
По проведенному анализу составим таблицу 2.1
Таблица 2.1 – Оценка структур приводов главного движения
Проанализировав данные аспекты для данного станка выбираем нераздельную структуру привода (рисунок 2.1а).
Выбираем асинхронный двухскоростной электродвигатель c переключением полюсов 4А112МА6M4У3=3055 кВт; nэ=9351455 мин-1; nсинхр=10001500 мин-1.
Принимаем знаменатель ряда .
Составим структурную формулу привода и построим структурную сетку:
Рисунок 2.2 – Кинематическая схема привода
Строим график частот вращения.
Рисунок 2.3 – График частот вращения
По графику частот вращения определяем передаточные отношения коробки скоростей.
Определяем числа зубьев всех передач выбираем суммарное число зубьев z =92:
Определяем фактические передаточные отношения:
Определяем фактическую частоту шпинделя по формуле:
nшпф = nэ · i1Ф ·i2ф· i3ф· (2.2)
nэ – частота вращения электродвигателя мин-1;
nшпф =935·0703·0314·0314 = 6480 мин-1.
Определим относительные отклонения фактических частот от стандартных.
Рассчитанное отклонения не превышает допустимое отклонение [] =5%.
Рассчитаем крутящие моменты на валах привода.
Выбираем такую скорость двигателя при которой крутящий момент максимален (1455).
Крутящий момент на валу электродвигателя рассчитывается по формуле:
Крутящий момент на каждом последующем валу рассчитывается по формуле:
ii – передаточное отношение между валами.
РАСЧЕТ ЭЛЕМЕНТОВ КОРОБКИ СКОРОСТЕЙ.
1 Расчёт зубчатых передач
Рассчитаем самую нагруженную зубчатую передачу с передаточным отношением i3 i5 =0314. Данная передача является прямозубой и состоит из шестерни 1 с числом зубьев z1=22 и колеса 2 с числом зубьев z2=70.
Соответственно при расчете параметрам шестерни приписываем индекс - 1 а параметрам колеса -2. Выбираем твердость термическую обработку и материал зубчатых колес. Так как у нас на данную передачу приходится значительная часть нагрузки то термообработка колеса и шестерни одинаковые – закалка с нагревом ТВЧ сквозная с охватом дна и впадин; твёрдость НRCЭ=48 52.
Материал для колеса и шестерни: Сталь 40Х.
Проектный расчет цилиндрических зубчатых передач на выносливость зубьев при изгибе.
Расчет будем вести по методике приведенной в [3].
Модуль передачи (мм) должен удовлетворять условию:
где km – вспомогательный коэффициент (km=13 – для прямозубых передач);
М1F=516 Н·м – исходный расчетный крутящий момент на шестерне;
kF – коэффициент нагрузки на шестерни (kF=12);
YF1 – коэффициент учитывающий форму зуба (YF1=30);
Z2 – число зубьев колеса (z1=70);
bm – отношение ширины колеса b к модулю m (bm=10);
FP1 – допускаемое напряжение для материала шестерни МПа:
Допускаемое напряжение на изгиб:
где - предел выносливости материала зубьев МПа;
kFL -коэффициент долговечности kFL=1;
Определим основные геометрические параметры передачи:
Делительные диаметры найдём по формуле:
Межосевое расстояние передачи а:
Найдём диаметры вершин и диаметры впадин зубьев:
Подставив значения в формулы 3.5 и 3.6 получим:
Диаметры вершин зубьев:
Диаметры впадин зубьев:
df2=210-25×3=2025 мм;
b2=b1= m bm =310=30 мм; (3.7)
Проверочный расчёт передачи на контактную выносливость зубьев
Исходя из заданного передаточного числа u (u≥1) и отношения bd рабочей ширины венца передачи bw к начальному диаметру шестерни dw1 определяют соблюдается ли соотношение:
где kd- вспомогательный коэффициент; kd=770 для прямозубых передач;
kH-коэффициент нагрузки; kH=13;
bd-отношение рабочей ширины венца передачи к начальному диаметру колеса:
Допускаемое контактное напряжение для косозубых передач:
где Hlimb-базовый предел контактной выносливости поверхностей зубьев Hlimb=1050Мпа
SH-коэффициент безопасности SH=12;
Условие выполняется.
Проверочный расчет цилиндрических зубчатых передач на выносливость зубьев при изгибе
Удельная расчетная окружная сила (Н):
где Ft - расчётная окружная сила Н;
b - ширина венца по основанию зуба мм;
kFV - коэффициент учитывающий динамическую нагрузку в зацеплении которая возникает вследствие колебаний масс колёс и ударов в зацеплении;
kFb - коэффициент учитывающий неравномерность распределения нагрузки по ширине венца которая возникает вследствие погрешностей изготовления колёс упругих деформаций валов зазорах в подшипниках;
kFa - коэффициент учитывающий при расчёте косозубых передач распределение нагрузки между зубьями.
Определим степень точности передачи в зависимости от окружной скорости колеса:
Подставив значения в формулу 3.11 получим:
По [3] степень точности передачи равна шести.
Коэффициенты находим по [3]: kFV=1; kFb=108; kFa=135.
Расчётное напряжение изгиба зубьев:
где YF - коэффициент формы зуба колеса; (YF2=30)
Ye - коэффициент учитывающий перекрытие зубьев: Ye=1;
Yb - коэффициент учитывающий наклон зуба; Yb=1;
Подставив значения в формулу 3.12 получим:
Допускаемое напряжение при расчёте зубьев на выносливость при изгибе:
Уточняем допускаемое напряжение при расчёте зубьев на выносливость при изгибе:
kFg - коэффициент учитывающий влияние шлифования переходной поверхности зубьев;
kFa - коэффициент учитывающий влияние упрочнения переходной поверхности зубьев в результате механической обработки;
kFc - коэффициент учитывающий особенности работы зубьев при
передаче реверсивной нагрузки;
kFL - коэффициент режима нагружения и долговечности;
YS - коэффициент отражающий чувствительность материала к
концентрации напряжений;
YR - коэффициент учитывающий параметры шероховатости переходной поверхности зуба;
SF - коэффициент безопасности;
Найдём данные коэффициенты по [3]:
kFg=11; kFa=1; kFc=1; k kFL=10; YS=11×m-009=11×3-009=1; YR=12;
Коэффициент безопасности находим по формуле:
где S’F - коэффициент безопасности учитывающий нестабильность свойств материала зубчатого колеса и ответственность зубчатой передачи:
S’’F - коэффициент учитывающий способ получения заготовки:
S’’F=115 (для заготовок из проката);
Подставив значения в формулу 3.14 получим:
Подставив значения в формулу 3.13 получим:
В нашем случае sFP2=3273>sF2=2389 т.е. проверка на выносливость зубьев при изгибе выполняется.
Расчёт передачи на контактную выносливость зубьев
Удельную окружную силу находим по формуле:
kНV - коэффициент учитывающий динамическую нагрузку в зацеплении;
kНb - коэффициент учитывающий неравномерность распределения нагрузки по ширине венца;
kНa - коэффициент учитывающий при расчёте косозубых колёс распре деление нагрузки между зубьями.
По [3]: kНb=108; kНV=10; kНa=10
Подставив значения в формулу 3.15 получим:
Расчётное контактное напряжение находим по формуле:
где ZH - коэффициент учитывающий форму сопряжённых поверхностей зубьев в полюсе зацепления;
ZM - коэффициент учитывающий механические свойства материала сопряжённых зубчатых колёс;
Ze - коэффициент учитывающий суммарную длину контактных линий;
u - передаточное число;
dW1 - начальный диаметр шестерни мм;
Найдём данные коэффициенты по [3]: ZH=176; ZM=274.
Коэффициент Ze определяем в зависимости от коэффициентов торцевого и осевого перекрытия:
Подставив значения в формулы 3.17 3.18 получим:
Подставив значения в формулу 3.16 получим:
Допускаемое контактное напряжение для прямозубой передачи:
где ZR - коэффициент учитывающий параметр шероховатости
поверхностей зубьев;
Zv - коэффициент учитывающий окружную скорость v;
kL - коэффициент учитывающий влияние смазочного материала;
kHL - коэффициент режима нагружения и долговечности;
SH - коэффициент безопасности;
ZR=10; ZV=10; kL=10; kXH=10; kHL=10; SH=12; Hlimb=1050 Мпа.
Подставив значения в формулу 4.2.24 получим:
В нашем случае sHP=875>sH=4313 что удовлетворяет условию.
Геометрические параметры остальных зубчатых передач сведём в таблицу.
Таблица3.1-Геометрические параметры зубчатых передач
2 Расчёт валов. Определение реакций в подшипниках построение эпюр
В качестве расчётного вала мы принимаем четвертый вал так как он наиболее нагружен.
В качестве материала изготовления всех валов выбираем сталь 40Х.
Определим геометрические параметры ступеней вала.
Первая ступень под зубчатое колесо.
Т – крутящий момент на валу Н·м.
[]k – допускаемое напряжение на кручение []k = 10 20 Нмм2.
принимаем d4 = 65 мм.
С целью упрощения конструкции примем диаметр вала постоянным по всей длине.
Установка зубчатых колес производится при помощи шпонки и стопорного колеса.
Следовательно диаметр вала под подшипники d=60 мм.
Длины ступеней определяется графически на эскизной компоновке.
Расчёт геометрических параметров для остальных валов производится аналогично. Результаты расчёта сведём в таблицу.
Таблица 3.2 - Геометрические параметры ступеней валов мм
Расчетный диаметр под зубчатое колесо dК мм
Диаметр под подшипник
Для определения реакций в подшипниках будем рассматривать вал как балку нагруженную силами действующими на колеса.
Определим силы действующие в зубчатом зацеплении.
Окружная сила на делительном цилиндре в торцовом сечении:
где d1 - делительный диаметр колеса мм
где a - угол исходного контура a=200.
Подставив численные значения в формулы 3.21 и 3.22 получим:
Разложим силы действующие на вал на две взаимно перпендикулярные плоскости ZOX и ZOY и определим реакции в опорах.
Для этого составим уравнения равновесия сил.
Суммарные реакции опор от сил в зацеплении:
Строим эпюры изгибающих моментов действующих на вал в плоскостях ZOX и ZOY рисунок 3.1.
Рис. 3.1 Эпюры изгибающих моментов.
Определяем суммарный изгибающий момент в наиболее нагруженной точки.
3 Проверочный расчёт валов на прочность
Цель расчёта – определить коэффициенты запаса прочности в опасных сечениях вала и сравнить их с допускаемыми.
Расчёт проводим для сечения вала на месте посадки колеса т.к. в данном сечение приложен больший изгибающий момент М=287 Н·м. Расчёт проводим по методике изложенной в [4].
Проверочный расчёт валов на прочность выполняем на совместное действие изгиба и кручения по условию.
где S - коэффициент запаса прочности;
[S]- допускаемый коэффициент запаса прочности;
Нормальные напряжения изменяются по симметричному циклу при котором амплитуда напряжений sа равна расчётным напряжениям изгиба sИ:
где М - суммарный изгибающий момент в рассматриваемом сечении Н×м;
WНЕТТО - осевой момент сопротивления сечения вала мм3;
Найдём осевой момент инерции:
где d-диаметр вала.
Подставив значения находим осевой момент инерции:
Касательные напряжения изменяются по циклу при котором амплитуда tа равна половине расчётных напряжений кручения tк:
где МК - крутящий момент Н×м;
WrНЕТТО - полярный момент инерции сопротивления сечения вала мм3;
Найдём полярный момент инерции:
Подставив значения находим полярный момент инерции:
Рассчитаем касательные и нормальные напряжения по формулам 3.28 и 3.30:
Определим коэффициент концентрации нормальных и касательных напряжений для расчётного сечения вала:
где Кs и Кt - эффективные коэффициенты концентрации напряжений
Кd - коэффициент влияния абсолютных размеров поперечного сечения
КF - коэффициент влияния шероховатости КF=10;
Подставив значения в формулы 3.31 3.32 получим:
Определим пределы выносливости в расчётном сечении вала:
где s-1 и t-1 - пределы выносливости гладких образцов при симметричном цикле изгиба и кручения s-1=400 МПа t-1=190 МПа
Подставив значения в формулы 3.33 3.34 получим:
Определим коэффициенты запаса прочности по нормальным и касательным напряжениям:
Подставив значения в формулы 3.35 3.36 получим:
Определим общий коэффициент запаса прочности в опасном сечении:
Подставив значения получаем:
Проверочный расчёт вала на прочность в опасном сечении выполняется.
4 Расчёт подшипников
Для рассчитываемого вала выбираем шариковые радиальные однорядные ГОСТ 8338-75. Серия 412 d = 60 мм
D = 150 мм B= 35 мм r=2 Cr = 108 кН Cr0 = 70 кН.
Проверим пригодность подшипников 412 в опоре В т.к. реакция в данной опоре наибольшая и равна Rr=RB=4781 Н.
Пригодность подшипников определяется сопоставлением расчётной динамической грузоподъёмности с базовой или базовой долговечности с требуемой по условиям:
Crp ≤ Cr или L10h ≥ Lh (3.38)
Требуемая долговечность подшипника Lh = 20· 103ч По [2] выбираем основные характеристики подшипников:
Суммарная статическая грузоподъёмность:
Расчётная динамическая грузоподъёмность определяется по формуле:
где: Pr – радиальная эквивалентная нагрузка Н;
n - частота вращения одного из колец подшипника (n=80) мин-1;
р – показатель степени р = 3;
KHE – коэффициент режима нагрузки (KHE=1);
а23 – коэффициент характеризующий совместное влияние на ресурс подшипника качения металла колец тел качения и условий эксплуатации (а23=075);
Рr = V·X RrA·Kб ·Kт (3.40)
V – коэффициент вращения V = 1;
RrA –радиальная действующие на подшипник;
Kб – коэффициент безопасности Kб =14;
Kт – температурный коэффициент Kт = 1;
XY- коэффициенты радиальной и осевой нагрузок X=056;Y=230;
Pr =1·056 478114 ·1=3748 Н;
89 кН 108кН – условие Crp ≤ Cr выполняется.
Произведём расчёт подшипника на долговечность:
Расчёт подшипника на долговечность выполняется.
Выбранный подшипник обеспечивает основные эксплуатационные требования.
ОБОСНОВАНИЕ И ВЫБОР КОНСТРУКЦИИ ШПИНДЕЛЯ
Шпиндельный узел металлорежущих станков предназначен для осуществления главного вращательного движения шпинделя с необходимой частотой вращения. В шпиндельных узлах выполняются закрепление и вращение режущих инструментов (в сверлильных и фрезерных станках) и обеспечивается их заданное положение по отношению к другим узлам станков.
Конструкция шпиндельного узла должна быть такой чтобы наряду с выполнением комплекса технологических команд достигалось сохранение точности вращения шпинделя исключающее осевое и торцовое биение а также суммарной жесткости всего узла для предотвращения деформирования. Конструктивная форма шпинделя определяется типом и назначением станка требованиями к его точности условиями работы шпинделя способами закрепления в нем инструмента или заготовки размещением элементов привода и типом применяемых опор.
Рассматриваемый нами шпиндель получает движение от коробки скоростей которая обеспечивает 16 частот вращения при максимальной частоте 1600 мин-1 .
Рассмотрим несколько вариантов компоновки шпиндельных узлов применимых для нашего случая.
Рисунок 5.1 – схемы опор
Первая схема используется в тех случаях когда требуется обеспечить большую жёсткость в задней опоре и исключить перемещения в радиальном и осевом направлении поэтому ставится радиальный и упорный подшипники. Вторая схема: благодаря тому что в передней опоре на один шарик больше чем в задней опоре снижается уровень вибраций шпинделя и улучшается стабильность положения по оси. Две первых схемы используются для сверлильных станков. Третья схема: в двух опорах стоят по два радиально-упорных подшипника. Данная схема используется в тяжёлых условиях работы при больших радиальных и осевых нагрузках. Третья схема используется для фрезерных станков.
Четвёртая схема: в каждой опоре установлено по одному радиально-упорному подшипнику. Данная конструкция воспринимает радиальные нагрузки и осевые нагрузки в одном направлении. Используется в тех случаях когда осевая нагрузка не меняет своего направления.
Конструкция шпиндельного узла зависит от коэффициента быстроходности который определяется по формуле:
- диаметр отверстия подшипника мм
- наружный диаметр подшипника мм
- наибольшая частота вращения шпинделя
Оптимальными для нашего станка являются как первый так и второй варианты которые представлены на рисунке 5.1.
Применим комбинированный вариант компоновки шпинделя из первого и второго вариантов.
Рисунок 4.1 - Схема шпиндельного узла.
Это обеспечит большую жесткость узла в передней и задней опорах повысит виброустойчивость сделает более надежным этот узел во всех отношениях.
Шпиндель станка установлен на двух опорах: передняя — пара однорядных радиальных шариковых подшипников по ГОСТ 8338-75 в паре с упорным шариковым подшипником по ГОСТ 7872-89; задняя – однорядный радиальный шариковый подшипник по ГОСТ 8338-75 и упорный шариковый подшипник по ГОСТ 7872-89.
Подшипники применяемые в нашем варианте отличаются простотой и при совместном исползовании работают не хуже более сложных радиально-упорных подшипников.
Однорядный радиальный шариковый подшипник 107 ГОСТ 8338-75.
Размеры подшипника: d = 35 мм D = 62 мм В = 14 мм.
Упорный шариковый подшипник 8207Н ГОСТ 7872-89В.
Размеры подшипника: d = 35 мм D = 62 мм В = 18 мм.
Упорный шариковый подшипник 8107Н ГОСТ 7872-89В.
Размеры подшипника: d = 35 мм D = 52 мм В = 12 мм.
Шпиндель изготовливаем из стали 40Х с цементацией закалкой и отпуском.
Определяем класс точности шпиндельных подшипников в зависимости от класса точности станка.
Класс точности станка – нормальный класс точности подшипников определим после расчет шпиндельного узла на точность.
РАСЧЕТ ШПИНДЕЛЬНОГО УЗЛА.
1 Расчет шпиндельного узла на точность.
Предполагаем наиболее неблагоприятный случай когда биение подшипников в передней опоре и в задней опоре направлены в противоположные стороны.
Станок нормальной точности обеспечивает получение деталей с размерами по 8 квалитету точности. Допуск на лимитирующий размер обрабатываемой детали размер по 8 квалитету составляет д = 81 мкм. Допускаемое радиальное биение переднего конца шпинделя должно быть:
[]д3=813=27 мкм (5.1)
Рисунок 5.2 - Схема к расчету шпиндельного узла на точность
При этом радиальное биение конца шпинделя
где - допустимое радиальное биение подшипников
= 27мкм; a = 183 мм;
Получим = = 0009 мм;
Для передней и задней опор принимаем высокий - 5 класс точности подшипников.
2 Расчёт шпиндельного узла на жёсткость.
Оценка радиальной жёсткости производится по прогибу d конца шпинделя происходящего за счёт упругой деформации (изгиба) шпинделя и податливости иго опор а также по углу поворота q упругой линии деформированного шпинделя в передней опоре.
Составим схему нагружения шпинделя - рисунок 5.3
Рисунок 5.3 - Схема нагружения шпиндельного узла
Максимально допустимые значения перечисленных параметров принимаются соответственно:
где - расстояние между опорами =400 мм.
Так как наш станок сверлильный а радиальная сила будет возникать в результате увода или неравномерной заточки режущих кромок то принимаем P=0.1 0.15Р0
Прогиб шпинделя d в горизонтальной и вертикальной плоскостях определим по формулам:
где ja jв - жёсткость подшипников ja=14×106 Нмм jв=075×106 Нмм;
Е - модуль упругости материала шпинделя Е=21 ×105 МПа;
I1 I2 - момент инерции сечения шпинделя в пролёте между опорами и переднего конца шпинделя соответственно мм4;
e - коэффициент защемления в передней опоре e=065;
a - вылет переднего конца шпинделя мм;
Моменты инерции найдём по следующим формулам:
где dср1н - средний наружный диаметр мм
dср2в - средний внутренний диаметр мм.
Подставив численные значения в формулы 5.6 и 5.7 получим:
Подставив численные значения в формулу 5.5 получим:
Рассчитаем углы поворота в передней опоре по формуле:
Осевое усилие подачи и усилие при выбивке инструмента воспринимается нижним упорным подшипником 8207 ГОСТ 7872-89: .
Проверим пригодность подшипников в нижней опоре осевая сила в данной опоре равна
Требуемая долговечность подшипника по табл. 9.4 [6].
Эквивалентная динамическая радиальная нагрузка:
- для шариковых и роликовых упорных подшипников с углом а = 90° при чисто осевой нагрузке равна осевой силе.
Расчётная динамическая грузоподъёмность определяется по формуле
где эквивалентная динамическая нагрузка Н;
угловая скорость вала с-1;
показатель степени .
условие Crp ≤ Cr не выполняется следовательно следует применять подшипник с большей грузоподъемностью а именно 8407 ГОСТ 7872-89: .
условие выполняется.
Выбранный подшипник обеспечивает основные эксплуатационные требования. Жесткость шпинделя будет обеспечиваться.
3 Расчет шпинделя на виброустойчивость.
Приближенный расчет собственной частоты шпинделя не имеющего больших сосредоточенных масс можно проводить по формуле [8]:
где m=6 кг – масса шпинделя;
- относительное расстояние между опорами:
- коэффициент зависящий от l;
Следовательно полученная частота собственных колебаний удовлетворяет требованиям к данному станку.
НАЗНАЧЕНИЕ СИСТЕМЫ СМАЗКИ СТАНКА
Основное назначение системы смазки сводится к уменьшению потерь на трение повышению износостойкости трущихся поверхностей и обеспечению допустимой температуры. От правильности смазки станка зависит срок службы станка и надежность его работы.
Станок снабжен комбинированной системой смазки. Механизмы расположенные внутри сверлильной головки смазываются автоматически от системы смазки сверлильной головки состоящей из плунжерного насоса и системы каналов подводящих смазку на все валы. Направляющие рукава и колоны смазываются периодически при помощи лейки. Нижние подшипники шпинделя смазываются периодически при помощи шприца. Смазка возможна при выдвинутом шпинделе. Верхние подшипники шпинделя смазываются при сборке. Подшипники поворота рукава винт подъема бочки опоры червяка поворота стола смазываются периодически вручную.
Схема смазки представлена на рисунке 6.1 перечень точек смазки приведены в таблице .
Перед пуском станка необходимо снять пробку 9 и заполнить резервуар сверлильной головки маслом в количестве около 15 литра контролируя уровень по маслоуказателю 5 затем произвести смазку станка. При работе станка уровень масла в сверлильной головке и работа насоса смазки контролируется по масло указателю 7.
Таблица Точки смазки
Расход смазочного материала
Периодичность смазки
Подшипники поворота рукава
Смазка ЦИАТИМ-20 ГОСТ 6267-74
Винт механизма подъема бочки
Масло турбинное Т22 ГОСТ32-74
Опоры червяка поворотного стола
Направляющие рукава
Рисунок 6.1 – Схема смазки
ВОПРОСЫ ОХРАНЫ ТРУДА И ТЕХНИКИ БЕЗОПАСНОСТИ
Общие требования безопасности установлены ГОСТ 12.3.002 –75* и включат: устранение непосредственного контакта работающих с исходными материалами заготовками полуфабрикатами готовой продукцией и отходами производства оказывающими вредное действие; замену технологических процессов и операций связанных с возникновением опасных и внедрение производственных факторов процессами и операциями при которых указанные факторы отсутствуют или обладают меньшей интенсивностью; комплексную механизацию и автоматизацию производства; применение дистанционного управления технологического процессами и операциями при наличии опасных и вредных производственных факторов; герметизацию оборудования; применение средств коллективной защиты работающих; рациональную организацию труда и отдыха с целью профилактики монотонности и гиподинамии а также ограничение тяжести труда;
Кроме того безопасность производственных процессов во многом зависит от их организации рациональности планировки цехов и участков и правильности организации рабочих мест выполнения требований безопасности к производственным помещениям хранению транспортированию складированию исходных материалов заготовок и готовой продукции а также к удалению отходов и их утилизации и наконец выполнения требований безопасности предъявляемых к производственному персоналу.
Общие требования безопасности на металлорежущих станках определены ГОСТ 12.3.025 – 80 в соответствии с которым установка обрабатываемых заготовок и снятие готовых деталей во время работы оборудования допускается вне зоны обработки при применении специальных позиционных приспособлений обеспечивающих безопасность работы.
Общие требования техники безопасности к станку.
1. Защитные устройства.
1.1. Ременные передачи расположенные вне корпусов станков и представляющие опасность травмирования должны иметь ограничения для удобства и безопасного открывания при помощи устройств.
1.2. Выступающие при работе за габарит станка внешние торцы сборочных единиц должны окрашиваться под углом 45º чередующимися полосами жёлтого и чёрного цвета.
1.3. Защитные устройства ограждающие зону обработки должны защищать работающего на станке и людей находящихся вблизи станка от отлетающей стружки и СОЖ.
1.4. Защитные устройства не должны вызывать неудобства при работе.
1.5. Поверхность стола защитных устройств станочных принадлежностей и приспособлений не должны иметь острых кромок и заусенцев.
2. Предохранительные и блокирующие устройства.
2.1. Станок должен иметь переходные устройства предотвращающие самопроизвольное опускание шпинделей бабок поперечин.
2.2. Станок должен иметь предохранительные устройства от перегрузки.
2.3. Перемещение сборочных единиц станка должно в крайних положениях ограничиваться устройствами исключающими перебеги за допустимые размеры.
2.4. Устройства закрепления на станке патронов оправок и других съёмных элементов должны исключать самопроизвольное ослабление при работе закрепляемых устройств и сдвигании съёмных элементов при реверсировании вращения.
2.5. В станках имеющих реверсивные приводы главного движения и механизированные подачи должна предусматриваться блокировка обеспечивающая выключение главного движения не раньше выключения подачи.
3. Органы управления.
3.1. Органы ручного управления должны быть выполнены и расположены так чтобы их использование было удобно и безопасно.
3.2. Рукоятки и другие органы управления станком должны быть снабжены фиксаторами не допускающими самопроизвольных перемещений органов управления.
3.3. Перемещение рукояток при отжиме и зажиме не должны быть направлены в стороны режущего инструмента.
3.4. Расположенное и конструкция органов управления должны исключить задерживание на них стружки.
4. Смазка охлаждение отвод стружки.
4.1. Форма станка и его элементов должны обеспечивать удобный отвод стружки и СОЖ из зоны обработки и удаление стружки со станка.
4.2. Станки следует оборудовать централизованной системой смазки.
4.3. В резервуарах смазочной системы устанавливаемых около станков и расположенных в основании станины должны быть предусмотрены отверстия для откачивания масла насосом.
4.4. Устройства для ввода СОЖ в зону обработки должны обеспечивать возможность удобного и безопасного регулирования их положения надёжной фиксации и необходимость распределения жидкости в зоне резанья.
Электрооборудование защитные меры.
1. Каждый станок должен иметь вводный выключатель ручного действия размещённый в безопасном месте.
2. На шкафах нишах которые недостаточно ясно показывают что содержат электрическую аппаратуру должны быть помещены предупреждающие знаки электрического напряжения по ГОСТ 12.4.026 – 76.
3. Остаточное напряжение у электрического оборудования недопустимо.
4. Каждый станок должен иметь орган аварийного отключения красного цвета.
5. Металлические части электрических аппаратов с ручным приводом должны быть надёжно соединены с защитной цепью.
6. Электрооборудование должно быть защищено нулевой защитой исключающей самопроизвольное включение станка.
7. Все металлические части должны быть оснащены легко обозримыми устройствами заземления вблизи от места ввода питающих приводов.
Общие и специальные требования по технике безопасности.
1. Обязанности станочника при работе на станке.
1.1. Перед началом работы убедиться что пуск станка никому не угрожает опасностью.
1.2. Привести в порядок рабочую одежду надеть головной убор.
1.3. Приняв станок убедиться хорошо ли он убран и убрано ли рабочее место.
1.4. О неисправности станка заявить мастеру до устранения неисправности к работе не приступать.
1.5. Приготовить ключи и другие необходимые инструменты не применять крючок с ручкой в виде петли.
1.6. Проверить наличие и исправность:
1.6.1. Ограждений зубчатых колёс валиков приводов а так же токоведущих частей электрической аппаратуры.
1.6.2. Заземляющих устройств.
1.6.3. Предохранительных устройств для защиты от стружки СОЖ.
1.6.4. Устройств для коррекции инструмента.
1.6.5. Режущего измерительного крепёжного инструмента и приспособлений и разложить их в удобном для использования порядке.
1.7. Если при обработке металла образуется отлетающая стружка то при отсутствии специальных защитных устройств на станке надеть защитные очки.
1.8. Проверить на холостом ходу станок.
1.8.1. Исправность органов управления.
1.8.2. Исправность системы смазки и охлаждения.
1.8.3. Исправность рычагов включения и выключения.
1.9. Для предупреждения кожных заболеваний рук при применении на станках охлаждающих масел и жидкостей перед началом работы смазывать руки специальными пастами и мазями.
1.10. Проверять доброкачественность ручного инструмента при получении его из кладовой.
1.10.1. Ручка напильника и шабера должна иметь металлическое кольцо предохраняющее его от раскалывания.
1.10.2. Зубило и другой ударный инструмент должны быть длинной не менее 150 мм кернер – 100 мм не иметь наклёпа на бок.
1.11. Пользоваться режущим инструментом имеющим правильную заточку. Применение неисправного инструмента и приспособлений не допускается.
1.12. Проверить и обеспечить достаточную смазку станка при смазке использовать только соответствующие приспособления.
1.13. Запрещается охлаждать режущий инструмент мокрыми тряпками или щётками.
1.14. Не допускать разбрызгивание масла и жидкости на пол.
1.15. Устанавливать между стенками защитные шиты.
2. Обязанности станочников во время работы:
2.1. выполнять указания по обслуживанию и уходу за станком изложенные в «Руководстве по станку» а так же требования предупредительных таблиц имеющихся на станке.
2.2. Устанавливать и снимать режущий инструмент только после полного останова станка.
2.6. Не удалять стружку от станка непосредственно руками или инструментом.
2.7.При установке пил для исключения порезов необходимо проявлять максимальную осторожность.
2.8.При установке детали на станок нельзя находиться между деталью и станком.
2.9.При отрезании тяжёлых частей детали или заготовки нельзя придерживать отрезаемый конец руками.
2.8. Остерегаться заусенцев на обрабатываемых деталях.
2.9. Обязательно остановить станок и выключить электродвигатель при:
2.8.1. Уходе от станка даже на короткое время.
2.8.2. Временном прекращении работы.
2.8.3. Перерыве подачи электроэнергии.
2.8.4. Уборке смазке чистке станка.
2.8.5. Обнаружении неисправности в оборудовании.
2.8.6. Установке изменении и съёме детали.
2.9. При обработке деталей применять режимы резанья указанные в операционной карте для данной детали.
2.10. Не превышать установочные режимы резанья без ведома мастера.
3. Обязанности станочника по окончанию работы:
3.1. Выключить станок.
3.2. Привести в порядок рабочее место убрать со станка стружку инструмент приспособление очистить станок от грязи вытереть и смазать трущиеся части станка аккуратно сложить готовые детали и заготовки.
3.3. Убрать инструмент в отведённые для этого места.
3.4. После окончания работы на станке доложить мастеру о замеченных недостатках имевших место во время работы.
3.5. О всякой замеченной опасности заявить мастеру производственного обучения.
3.6. Вымыть руки тёплой водой принять душ.
Стружку от металлорежущих станков следует убирать только при помощи специальных механизированных средств. Вводной выключатель под нагрузкой не выключать. Это допустимо только в аварийных случаях. При осмотре или ремонте электроаппаратуры вводной выключатель выключить. Менять скорость и инструмент только при остановке шпинделя. Не использовать инструменты с забитыми и изношенными хвостовиками. Обрабатываемые детали надежно закреплять в приспособлении или на столе станка.
В данном курсовом проекте нами была проведена работа по модернизации привода главного движения радиально-сверлильного станка 2532Л. На станок был установлен двухскоростной электродвигатель увеличено число ступеней скорости шпинделя.
В ходе проектирования произвели анализ и выбор конструкции шпиндельного узла произвели его расчет на жесткость точность и виброустойчивость.
Таким образом в ходе выполнения курсового проекта закрепили теоретические знания ознакомились со специальной технической литературой научились самостоятельно проектировать узлы станков.
Используемая литература:
Анурьев В.И. Справочник конструктора-машиностроителя. Т1.М. Машиностроение 1979г.
Анурьев В.И. Справочник конструктора-машиностроителя. Т2.М. Машиностроение 1979г.
Кочергин А.И. Конструирование и расчет металлорежущих станков и станочных приспособлений. Курсовое проектирование. Мн.: Выш.шк.1991.-382 с.
Санюкевич Ф.М. Детали машин. Курсовое проектирование. Брест: БГТУ 2003.-462 c.
Справочник технолога-машиностроителя. Т1. Под ред. А.Г. Косиловой и Р.К. Мещерякова. М. Машиностроение 1985г.
Коробка скоростей 9.cdw

комплекта приводного вала обеспечить натяг
Коробку заполнить маслом индустриальным ГОСТ 2.0799-75
Крышки после установки стаканов проверить на течь.
Винты для крепления оправки в пинолях должны быть напрвлены
в одну сторону в каждой группе пинолей
Осевой люфт не должен превышать для приводных валов - 0
После установки коробки на станок вместо рым - болтов
Изготовление и приемку шпиндельной короки производить по
КП 36.01.01.2532.02.00.000
Рекомендуемые чертежи
- 07.06.2021
- 22.11.2015
Свободное скачивание на сегодня
Другие проекты
- 24.04.2014
- 20.08.2014