Привод главного движения вертикально-фрезерного станка





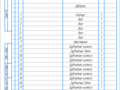
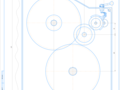
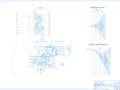
- Добавлен: 25.01.2023
- Размер: 884 KB
- Закачек: 0
Описание
Привод главного движения вертикально-фрезерного станка
Состав проекта
![]() |
![]() |
![]() ![]() ![]() ![]() |
![]() ![]() ![]() |
![]() ![]() ![]() ![]() |
![]() ![]() ![]() ![]() |
![]() ![]() ![]() ![]() |
Дополнительная информация
Развертка X1.cdw

Спецификация1.spw

Свёртка X1.cdw

Кинематическая схема.cdw

Рекомендуемые чертежи
- 07.06.2021