Привод главного движения горизонтально-фрезерного станка




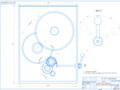
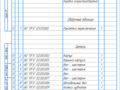
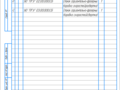
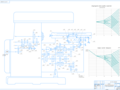
- Добавлен: 25.01.2023
- Размер: 3 MB
- Закачек: 0
Описание
Привод главного движения горизонтально-фрезерного станка
Состав проекта
![]() |
![]() |
![]() ![]() ![]() ![]() |
![]() ![]() ![]() |
![]() ![]() ![]() ![]() |
![]() ![]() ![]() ![]() |
![]() ![]() ![]() ![]() |
![]() ![]() ![]() |
![]() ![]() ![]() ![]() |
![]() ![]() ![]() ![]() |
![]() ![]() ![]() ![]() |
![]() ![]() ![]() ![]() |
![]() ![]() ![]() ![]() |
![]() |
![]() ![]() ![]() |
Дополнительная информация
Лист3.cdw

Коробка скоростей(свертка).
* размеры для справок
Для смазки узлов использовать масло И-20А ГОСТ 20799-75
Записка Иванов КИМ курсовой.doc
Проект разработал Французов Е.И. под руководством ассистента кафедры «ТиОМП» А.И. Костюченко.
Объектом курсового проектирования является универсальный токарно-винторезный станок для обработки конструкционных сталей точения наружных и внутренних поверхностей нарезания метрической резьбы.
В ходе работы над курсовым проектом станок-прототип 6Т82Г был изменен с целью увеличения его надежности.
Объем: пояснительной записки страниц;
графической части 2 листа формата А1 и 1 лист формата А2.
Курсовое проектирование – важная часть учебного процесса. В ходе курсового проектирования мы приобретаем опыт самостоятельного решения практических задач изуч
Эффективность производства его технический прогресс качество выпускаемой продукции во многом зависит от опережающего развития производства нового оборудования машин станков аппаратов от всемерного внедрения методов технико-экономического анализа. Существующий парк станков насчитывающий в настоящее время около четырех тысяч различных моделей не удовлетворяет все расширяющиеся запросы потребителей. Следовательно в будущем разнообразие станков будет все время увеличиваться и обновляться. В общем количестве станков кроме количественных происходят и качественные изменения. В современных станках широко используются как механические так и электрические гидравлические пневматические и другие устройства что приводит к усложнению их конструкции. В конструкции машин необходимо соблюдать требования технической эстетики. Машины должны иметь красивый внешний вид изящную строгую отделку.
Первоначальной базой той или иной конструкции станка является кинематическая структура станка выражаемая кинематической схемой так как назначением станка является создание относительных движений режущего инструмента и заготовки необходимых для получения в процессе резания заданных поверхностей. Следовательно и при конструировании и при эксплуатации нужно прежде всего знать кинематическую структуру станка.
Развитие производственного оборудования предполагает решение вопросов выбора и оптимизации технических характеристик станка проектирования кинематической схемы станка и его узлов обоснование выбранных конструктивных вариантов. Проектируя машину конструктор должен добиваться всемерного увеличения ее рентабельности и повышения экономического эффекта за весь период работы. Данный проект направлен на решение таких задач.
ОПРЕДЕЛЕНИЕ ТЕХНИЧЕСКИХ ХАРАКТЕРИСТИК СТАНКА
1 Основные сведения о горизонтально-фрезерном станке методах обработки и применяемом инструменте анализ способов формообразования обрабатываемых поверхностей
Горизонтально фрезерный станок 6Т82Г (6Р82Г) предназначен для выполнения разнообразных фрезерных работ цилиндрическими торцевыми концевыми фасонными и другими фрезами. Применяются для обработки горизонтальных и вертикальных плоскостей пазов рамок углов зубчатых колес спиралей моделей штампов пресс-форм и других деталей из стали чугуна цветных металлов их сплавов и других материалов.
Высокая жесткость станков позволяет применять фрезы изготовленные из быстрорежущей стали а также инструмент оснащенный пластинками из твердых и сверхтвердых синтетических материалов. Большая мощность привода главного движения и тяговое усилие продольной подачи стола позволяют производить за один проход обработку широких горизонтальных поверхностей набором цилиндрических или фасонных фрез установленных на горизонтальной оправке.
Станки моделей 6Т82 6Т82-27 и 6Т83 6Т83-27 оснащены столом поворачивающимся вокруг вертикальной оси на угол ±45° что обеспечивает возможность нарезания косозубых зубчатых колес червяков и других деталей имеющих обрабатываемую поверхность в виде спирали.
Технологические возможности станков могут быть расширены за счет применения накладной фрезерной делительной и долбежной головок круглого поворотного стола. Станки выпускаются в различных исполнениях по напряжению и частоте питающей сети. Поставляются запасные части.
Рис. 1 Схемы обработки:
а в – плоскости – цилиндрической и торцовыми фрезами; б – фасонной поверхности – набором дисковых фрез; г д – уступа – дисковой и концевой фрезами; е – паза - концевой фрезой; ж – паза – дисковой фрезой; з и – шпоночного паза –концевой и дисковыми фрезами; к – Т – образного паза концевой фрезой; л – паза типа «ласточкин хвост»; угловой фрезой; н – отрезка заготовки – дисковой фрезой
Рисунок 1 продолжение
Рис. 2 Схемы крепления инструмента на фрезерных станках:
– шпиндель; 2 - шомпол; 3 - оправка; 4 - установочные кольца; 5 – цилиндрическая фреза; 6 – серьга хобота;
А – цилиндрических фрез; б – пальцевых фрез; в – торцовых фрез
2 Технические характеристики горизонтально-фрезерного станка 6Т82Г
Размеры рабочей поверхности стола мм
Наибольшее перемещение стола мм
Поворот стола в обе стороны град
Расстояние от оси горизонтального шпинделя до рабочей поверхности стола мм
Пределы частот вращения шпинделя мин -1
Диапазон подач стола мммин:
- продольных (бесступенчато регулируемый)
- поперечных (бесступенчато регулируемый)
- вертикальных (бесступенчато регулируемый)
Ускоренное перемещение стола мммин:
Мощность электродвигателей приводов КВт
- основного шпинделя
Конус шпинделя по ГОСТ 30064-93
Максимальная масса обрабатываемой детали с приспособлением кг
Максимальное тяговое усилие приводов стола Н:
- продольное и поперечное
Габаритные размеры мм:
Масса станка с электрооборудованием кг
3 Основные узлы станка
Базовым узлом станка является станина А на которой монтируются все остальные узлы и механизмы станка (рис. 3). Станина жестко закреплена на основании Б внутренние полости которого служат резервуаром для охлаждающей жидкости.
В станине смонтирована коробка скоростей которая представляет собой пятиваловый механизм с тремя подвижными зубчатыми блоками колес на 18 ступеней скорости. Переключение скорости осуществляется селективной системой управления позволяющей выбрать требуемую скорость шпинделя без последовательного включения промежуточных ступеней.
Осмотр коробки скоростей можно произвести через окно В с правой стороны станка. Для поддержания конца фрезерной оправки станок имеет хобот Г и кронштейны Д. Хобот и кронштейн могут перемещаться и закрепляться - хобот в направляющих станины кронштейны на направляющих хобота.
С передней стороны станина имеет вертикальные направляющие типа «Ласточкин хвост» для консоли Е.
В консоли смонтирована коробка подач Ж на 18 ступеней скорости с селективной системой управления а также ряд валов зубчатых колес и муфт передающих движение от коробки подач в трех направлениях - к винтам продольной подачи стола И поперечной подачи салазок К и вертикальной подачи консоли Е механизм включения быстрого хода стола и электродвигатель подач.
Стол станка может быть повернут вокруг вертикальной оси что позволяет ему перемещаться не только перпендикулярно или параллельно оси шпинделя но и под различными углами к ней. Это дает возможность фрезеровать на станке винтовые канавки и нарезать зубчатые колеса с винтовыми зубьями.
4 Управление станком
Управление станком модели 6Т82Г - кнопочно-рукояточное. Основными движениями в станке можно управлять с двух мест - спереди и сбоку.
Включение станка в сеть осуществляется переключателем 31. По окончании работы или при продолжительном перерыве станок необходимо отключить от сети.
Включение вращения шпинделя производится кнопками 2 или 16 в зависимости от места управления станком а выключение - кнопками 1 и 17.
Реверсирование направления вращения шпинделя производится переключателем 33. Изменение скорости вращения шпинделя осуществляется перемещением рукоятки 35 вращением указателя скоростей 4 в любую сторону и включением кнопки 6.
Включение и выключение продольной подачи стола осуществляется рукояткой 11 имеющей три фиксированных положения: вправо влево среднее (нейтральное) или дублирующей рукояткой 29.
Управление поперечным перемещением салазок и вертикальным перемещение консоли производится рукояткой 23 имеющей пять фиксированных положений: среднее (нейтральное) к себе от себя -перемещение поперечных салазок; вниз вверх - перемещение консоли; или дублирующей рукояткой 30.
Изменение скорости подач стола осуществляется нажатием кнопки 24 перемещением грибка 25 и вращением указателя подач 26 в любую сторону.
Быстрые перемещения стола в трех взаимно перпендикулярных направлениях происходит при нажатии кнопок 5 или 15 и при включении рукояток 11 или 23 в направлении необходимого перемещения стола и прекращается если отпустить кнопку.
Ручные продольные поперечные и вертикальные перемещения стола осуществляются соответственно маховиком 14 или 34 маховиком 18 и рукояткой 21.
Рис. 3 Общий вид станка мод. 6Т82Г
Маховик 34 блокирован от произвольного включения его при механической подаче. Маховик 18 и рукоятка 21 при включении механической подачи отключаются и предохраняются от произвольного включения специальным блокирующим устройством. Маховик 14 отключается при включении рукоятки продольных механических перемещений стола.
Перемещение хобота и направляющих станины осуществляется вращением шестигранника 8.
С целью повышения жесткости узлов на станке предусмотрен зажим: хобота Г в направляющих станины - вращением винта 38; кронштейнов Д на направляющих хобота - гайками 9; поперечных салазок на направляющих консоли - рукояткой 28; поворотных салазок - винтами 22; консоли на направляющих станины - рукояткой 37.
Зажим стола в направляющих салазок при работе поперечной подачей или некоторый поджим стола при силовых режимах на продольной подаче осуществляется винтами 12.
Управление перемещением стола осуществляется вручную или автоматически.
При ручном управлении станком подача стола включается только после включения вращения шпинделя.
Если какая-либо из рукояток включения подачи (продольной поперечной или вертикальной) находится во включенном положении то с включением кнопок 2 и 16 - «Пуск шпинделя» одновременно включается соответствующая подача кнопками 1 или 17 отключаются все движения в станке.
РАЗРАБОТКА (ИЛИ ВЫБОР) И ОПИСАНИЕ КОМПОНОВКИ СТАНКА
Станок модели 6Т82Г по кинематической структуре относится к классу Э22 и состоит из нескольких частных структур (рис. 5). Каждая из этих структур содержит кинематические группы для двух исполнительных движений:
- движения резания ФV(В) и движения подачи - продольной ФS1 (П2) поперечной ФS2 (П3) или вертикальной ФS3(П4).
Кинематическая группа движения резания ФV(В1) - простая. Ее внутренняя связь состоит из одной кинематической вращательной пары между шпинделем фрезы и станиной. Внешняя кинематическая связь с органом настройки iV находится между источником движения Д1 и шпинделем - на схеме пунктирный отрезок 1 - 2.
Кинематическая группа движения продольной подачи ФS1 (П2) - простая с внутренней связью в виде поступательной кинематической пары между столом и поперечными салазками и внешней кинематической связью: источник движения Д2 iS4 М15ходовой винт с t1.
Кинематическая группа движения поперечной подачи Ф S2 (П 3) - тоже простая с внутренней связью в виде поступательной кинематической пары между поперечными салазками и консолью и внешней кинематической связью: источник движения Д2 iS4 М26ходовой винт с t2.
Кинематическая группа движения вертикальной подачи ФS3(П 4) - простая с внутренней связью в виде поступательной кинематической пары между консолью и станиной и внешней кинематической связью: источник движения Д2 iS4 М37ходовой винт с t3.
Рис. 5 Структурная схема горизонтального консольно-фрезерного станка
КИНЕМАТИЧЕСКИЙ РАСЧЕТ ПРИВОДА
Определяем диапазон регулирования скорости исполнительного органа по формуле
Определяем количество ступеней скорости исполнительного органа по формуле:
Пользуясь ОСТ2.Н11-1-75 принимаем значения ряда ступеней скоростей:315; 40; 50; 63; 80; 100; 125; 160; 200; 250; 315; 400; 500; 630; 800; 1000; 1250; 1600.
Оптимальная структура привода для Z=18 запишется в виде
Проверяем возможность применения простой множительной структуры. Простая множительная структура возможна при условии для последней в порядке переключения группы: Для нашего варианта: следовательно вариант осуществим.
По полученной формуле структуры строим структурную сетку привода – рис.6.
Рис. 6 Структурная сетка привода
В соответствии с компоновкой привода руководствуясь структурной сеткой рисуем кинематическую схему привода – рис.7.
Рис. 7 Кинематическая структура привода
В соответствии со структурной сеткой строим график частот вращения – рис. 8.
Определяем передаточные отношения передач привода:
Определяем числа зубьев колём привода.
Наименьшее общее кратное НОК1=18. Принимаем множитель Е=4. Тогда сумма зубьев первой группы .
Наименьшее общее кратное для передач и НОК2=18. Принимаем множитель Е=5. Тогда сумма зубьев первой группы .
Передаточное отношение передачи . Для суммы зубьев поэтому передаточному отношению наиболее близки значения чисел зубьев
Наименьшее общее кратное НОК1=15. Принимаем множитель Е=6. Тогда сумма зубьев первой группы .
Рис.8. График частот вращения привода
ДИНАМИЧЕСКИЕ И ПРОЧНОСТНЫЕ РАСЧЕТЫ УЗЛОВ РАЗРАБАТЫВАЕМЫХ КОНСТРУКЦИЙ
1 Расчет мощности двигателя и определение крутящих моментов
Необходимо отметить что при динамическом расчете привода главного движения максимальный крутящий момент на выходе коробки скоростей определяется не по номинальной а по расчетной частоте его вращения принимаю частоту расположенную в середине диапазона регулирования скоростей также принимаем частоты на валах:
Мощность на первом валу коробки скоростей определяется по формуле:
где - мощность электродвигателя
- КПД соответственно электродвигателя ременной передачи пары подшипников 3.
Таким образом мощность и угловая скорость на первом валу:
Наибольший крутящий момент:
Для того чтобы определить крутящие моменты на валах II III и IV коробки скоростей необходимо найти мощности и угловые скорости на этих валах:
Крутящие моменты на валах II III и IV:
2 РАСЧЕТ ЗУБЧАТЫХ ПЕРЕДАЧ
2.1 Выбор материала и проверка на прочность зубчатых колес
Для получения сравнительно небольших габаритов и невысокую стоимость коробки выбираем для изготовления колес и шестерен недорогую сталь 45 (поковка). Характеристики смотри в приложении.
2.2 Расчет прямозубых передач
Предварительный расчет выполняем по формуле [4 (10.18) стр. 185]
где Kd = 780 МПа стр. 186 по рекомендации [4 табл. 10.8 стр. 186] принимаем bd = 1 по графику[4 рис. 10.21 стр.180] KH = 1.07
Рабочая ширина колес
Выбираем m – по рекомендации табл. 10.9 принимаем m = 15
По [4 табл. 10.1 стр. 160] по ГОСТ 9563-60 принимаем m = 2.
Уточняем диаметры колес по известным значениям модуля и числа зубьев:
Принимаем межосевое расстояние равное 72 мм.
Принимаем ширину колеса 24 мм.
Выбираем m – по рекомендации табл. 10.9 принимаем m = 10
По [4 табл. 10.1 стр. 160] по ГОСТ 9563-60 принимаем m = 4
Принимаем межосевое расстояние равное 180 мм.
Принимаем ширину колеса 44 мм.
По [4 табл. 10.1 стр. 160] по ГОСТ 9563-60 принимаем m = 5
Принимаем межосевое расстояние равное 225 мм.
Основные размеры и характеристики зубчатых колес
Ширина зубчатых венцов мм
Выбор материала валов.
Выбираем для валов Сталь 40Х ГОСТ 4543 термообработка
закалка + высокий отпуск НВ 230 – 285.
1 Предварительный расчет валов
Диаметры валов определяем по условному расчету на кручение
где Т – крутящий момент Нмм;
[k] = 20 30 – допускаемое напряжение на кручение МПа.
Предварительные диаметры валов:
Принимаем диаметр равным 34 мм
Принимаем диаметр равным 35 мм
Принимаем диаметр равным 50 мм
Принимаем диаметр равным 54 мм
2 Проектировочный расчет вала 1
Вал передает момент [6 (11.1)]
В зацеплении со стороны шестерни действуют силы:
радиальная [6 (11.3)]
Неуравновешенная составляющая силы муфты
Опорные реакции в вертикальной плоскости:
Опорные реакции в горизонтальной плоскости:
в вертикальной плоскости
в горизонтальной плоскости
Суммарный изгибающий момент в сечении под шестерней (это самое нагруженное сечение) [6 (11.20)].
Эквивалентный момент [2 (3.24)]
Диаметр в рассчитываемом сечении (опасном) [2 (3.25)].
Окончательно принимаем по ГОСТ 6636-69 диаметр вала d = 30 мм.
Диаметр выходного конца вала [6 (11.21)]
Окончательно принимаем по ГОСТ 6636-69 диаметр выходного конца вала dк =24 мм.
dп = 28 мм – диаметр участка вала под подшипники.
Производим проверочный расчет вала на выносливость для опасного сечения. В сечении действует наибольший изгибающий момент М и крутящий момент Т концентрация напряжений вызвана наличием шпоночной канавки b t1.
Момент сопротивления сечения вала [6 (11.22)]
Амплитуда номинальных напряжений изгиба при симметричном цикле изменения напряжений изгиба [6 (11.23)]
Коэффициент безопасности в сечении по изгибу [6 (11.24)]
где К – эффективный коэффициент концентрации напряжений для вала в месте шпоночного паза [6 табл. 11.8];
– коэффициент учитывающий упрочнение поверхности [6 табл. 11.6];
– масштабный фактор в зависимости от диаметра вала [6 табл. 11.5];
= 0.12 – коэффициент характеризующий чувствительность материала к асимметрии цикла изменения напряжений для среднеуглеродистых сталей;
m = 0 – постоянная составляющая цикла изменения напряжений (при симметричном цикле изменения напряжений изгиба равна нулю).
Определяем коэффициент безопасности по кручению. Полярный момент сопротивления по опасному сечению
При нереверсивном вращении вала напряжения кручения изменяются по пульсирующему циклу поэтому переменные составляющие (амплитуды) и постоянные составляющие (среднее напряжение) цикла
Коэффициент безопасности в сечении по кручению
– коэффициент учитывающий состояние поверхности [табл. 11.6];
Общий коэффициент безопасноти по усталостной прочности для сечения [6 (11.28)]
Условие прочности выполняется.
3 Проектировочный расчет второго вала 2
Окончательно принимаем по ГОСТ 6636-69 диаметр вала d = 44 мм.
Окончательно принимаем по ГОСТ 6636-69 диаметр выходного конца вала dк =30 мм.
dп = мм – диаметр участка вала под подшипники.
4 Проектировочный расчет второго вала 3
Окончательно принимаем по ГОСТ 6636-69 диаметр вала d = 45 мм.
Окончательно принимаем по ГОСТ 6636-69 диаметр выходного конца вала dк =35 мм.
5 Проектировочный расчет второго вала 4
Окончательно принимаем по ГОСТ 6636-69 диаметр вала d = 75 мм.
Окончательно принимаем по ГОСТ 6636-69 диаметр выходного конца вала dк =50 мм.
6 Расчёт шпиндельного вала
Выбираем шпиндельныё вал с диаметром конца равным 100мм и диаметром под колесом 82 расчёт произведём с помощью программы mrs.
Выбранный вал проходит по жёсткости .5.7 Подбор шпоночных соединений
Принимаем материал шпонки Сталь 45 с
Для соединения этого вала со шкивом подбираем шпонку по [5 табл. 9.12 стр. 123] с размерами b × h = 8 × 7 t1 = 4 – глубина паза вала.
Из условия прочности определяем lр
Принимаем по СТ СЭВ 189-75 для соединения вала 1 с муфтой призматическую шпонку 8 × 7 × 22 мм
Для соединения этого вала подбираем шпонку по [5 табл. 9.12 стр. 123] с размерами b × h = 14 × 9 t1 = 5.5 – глубина паза вала.
Принимаем по СТ СЭВ 189-75 для соединения вала 2 с колесами призматическую шпонку 14 × 9 × 36 мм.
Для соединения этого вала подбираем шпонку по [5 табл. 9.12 стр. 123] с размерами b × h = 22 × 14 t1 = 9 – глубина паза вала.
Принимаем по СТ СЭВ 189-75 для соединения вала с колесами призматическую шпонку 22 × 14 × 56 мм
8 Подбор шлицевых соединений
Для соединения этого вала подбираем шлицевое соединение по [дет.маш табл. 8.11 стр. 172] с размерами z × d × D = 8 × 36 × 42
Расчетная поверхность
Для соединения этого вала подбираем шлицевое соединение по [дет.маш табл. 8.11 стр. 172] с размерами z × d × D = 16 × 62 × 72
Для соединения этого вала подбираем шлицевое соединение по [дет.маш табл. 8.11 стр. 172] с размерами z × d × D = 16 × 72 × 82
1 Расчет подшипников для первого вала привода
Определяем реакции опор [6 (12.1) (12.2)]
Желаемая долговечность L = 3500 ч.. Температура в подшипнике не превышает 100. КЕ = 0.63.
Предварительно принимаем шариковый радиальный подшипник 205 ГОСТ 8338-75.
Для этих подшипников определяем по [2 табл. 5.33 стр. 156] динамическую Cr = 14 кН и статическую Cor = 6.95 кН грузоподъемности.
Находим эквивалентную нагрузки [6 (12.3 (12.4) (12.5)]
Расчет производим для второй опоры как более нагруженной Fr = Fr2
Определяем отношение
Определяем отношение V = 1 при вращении внутреннего кольца.
При для шариковых радиальных подшипников окончательно принимаем X = 1 и Y = 0.
Эквивалентная динамическая радиальная нагрузка [6 (12.5)]
где K = 1.4 – коэффициент безопасности [6 табл. 12.2];
KT = 1 – температурный коэффициент [6 табл. 12.3].
Требуемая динамическая грузоподъемность [6 (12.6)]
р = 3 – для шариковых подшипников.
Стр = 7.354 кН Cr = 14 кН
Выбранный подшипник подходит.
2 Расчет подшипников для второго вала привода
Предварительно принимаем шариковый радиальный подшипник 106 ГОСТ 8338-75.
Для этих подшипников определяем по [2 табл. 5.33 стр. 156] динамическую Cr = 13.3 кН и статическую Cor = 6.8 кН грузоподъемности.
Стр = 3.963 кН Cr = 14 кН
3 Расчет подшипников для третьего вала привода
Предварительно принимаем шариковый радиальный подшипник 107 ГОСТ 8338-75.
Для этих подшипников определяем по [2 табл. 5.33 стр. 156] динамическую Cr = 15.9 кН и статическую Cor = 8.5 кН грузоподъемности.
Стр = 5.92 кН Cr = 15.9 кН
4 Расчет подшипников для четвертого вала привода
Предварительно принимаем шариковый радиальный подшипник 310 ГОСТ 8338-75.
Для этих подшипников определяем по [2 табл. 5.33 стр. 156] динамическую Cr = 61.8 кН и статическую Cor = 36 кН грузоподъемности.
Стр = 16.24 кН Cr = 61.8 кН
ОПИСАНИЕ КОНСТРУКЦИИ ДЛЯ СПРОЕКТИРОВАННЫХ УЗЛОВ
В данном курсовом проекте необходимо было спроектировать горизонтально-фрезерный станок размер рабочей поверхности стола 400х1600 мм мощностью 11 кВт.
Коробка скоростей представляет собой совокупность передач при помощи которых можно передать 18 частот вращения начиная от 31.5 мин-1 до 1600 мин-1. В коробке скоростей установлены шлицевые валы -шестерни на которые насажены блочные передачи. Всего в коробке три блока состоящих из трех колёс.
Так как компоновка станка не отличается от компоновки станка – прототипа те все остальные конструктивные элементы и узлы взяты из него.
Основное назначения системы смазки коробки скоростей и коробки подач сводится к уменьшению потерь мощности на трение сохранению точности работы предотвращению вибрации снижению интенсивности износа трущихся поверхностей а также к предохранению их от заедания задирав и коррозии.
В качестве смазочных материалов для подшипников возможно применение масла индустриального 20 (веретенное 3) или турбинного 30 (турбинное УТ) т.к. диаметры валов под подшипники не превышают 110 мм а число оборотов составляет 1600 мин-1.
В качестве смазочных материалов для зубчатых передач применяют жидкие минеральные масла. Выбор сорта минерального масла производится в зависимости от условий работы коробки скоростей и коробки подач передаваемой мощности окружной скорости в зацепление а также температуры масла в картере коробок.
Также значение имеет вязкость чем она меньше тем выше окружная скорость т.к. в спроектированной коробке скоростей окружная скорость не превышает 25 мс то принимаем масло цилиндровое 24 (вискозин).
Кроме вязкости масла на выбор смазки зубчатых колёс большое влияние оказывает его маслянистость – способность образовывать на поверхности трение прочные абсорбированные плёнки с пониженным сопротивление сдвига.
Учёт маслянистости при выборе масла обеспечивает минимальный износ зубчатых передач т.к. удельное давление при скорости 25-5 мс составляет 1-5 кгмм2 то выбранный сорт масла цилиндровое 24 (вискозин) удовлетворяет нашим условиям.
Все передачи и подшипники расположенные в общем корпусе целесообразно обслуживать от одно централизованной системы смазки что позволяет применить один и тот же смазочный материл.
В спроектированном станке применяем картерную систему смазки когда масло из общей ванны увлекается и разбрызгивается зубчатыми передачами образующийся при этом туман смазывает размещённые внутри коробки подшипники и передачи. Кроме того масло стекая по стенкам корпуса также попадает на подшипники качения. Зубчатое колесо разбрызгивающее масло не должно быть слишком глубоко погружено в ванну т.к. излишне высокий уровень заливки масла приводит к потерям мощности и перегреву всей системы. Зубчатые цилиндрические колёса достаточно нагружать в масло наполовину высоты зуба.
ОПИСАНИЕ СИСТЕМЫ УПРАВЛЕНИЯ СТАНКОМ
Главным движение в станке является вращение шпинделя которое он получает от электродвигателя мощностью 11 кВт через систему зубчатых передач. Вращение шпинделя осуществляется по следующей цепи зубчатых колёс: 28-44 или 32-40или 36-36 на вал III затем через колёса 19-71 или 35-55 или 50-40 движение передаётся на вал IV а затем через зубчатые передачи либо 18-72 либо 60-30 движение передаётся на шпиндель V. Переключая блоки колёс можно получить 18 вариантов зацепления.
В ходе курсового проектирования был спроектирован привод главного движения горизонтально-фрезерного станка. Он удовлетворяет поставленным требованиям т.е. диапазон частот регулирования мощность электродвигателя.
Проектирование производилось на базе горизонтально-фрезерного сстанка 6Т82Г соблюдением конструкционных особенностей и сохранением коробки подач станка.
В итоге спроектированный станок можно отнести к средним станкам.
На спроектированном станке могут выполняться все те операции которые описаны в начале записки.
СПИСОК ИСПОЛЬЗОВАННОЙ ЛИТЕРАТУРЫ
Курсовое проектирование деталей машин: Учеб. пособие С.А. Чернавский К.Н. Боков и др. – 2-е изд. перераб. и доп. – М.: Машиностроение 1988 – 416с.
Курсовое проектирование деталей машин: Справ. пособие. В 2-ух частях. В. Кузьмин Н. Н. Макейчик и др. – Мн.: Выш. школа 1982.
Конструирование узлов и деталей машин: Учеб. пособие для машиностроит. спец. вузов. – 4-е изд. Дунаев П. Ф. Леликов О. П. – М.: Выш. шк. 1985.
Детали машин. Учебник для вузов. Изд. 3-е доп. и перераб. Иванов М. Н. – М Высш. школа 1976.
Проектирование. Детали машин. 2-е изд. доп. и перераб. Курмаз Л. В. Скойбеда А. Т. – Мн. УП «Технопринт» 2002.
Практикум по курсам «Детали машин» Детали машин и подъемно-транспортные устройства» для студентов спец. 1-36 01 01 1-36 01 03 и др. А. Л. Лисовский Н. Л. Кравченко Т. В. Вигерина – УО «ПГУ» 2006.
Допуски и посадки. Справочник. В 2-х ч.В.Д. Мягков М.А. Палей и др. – 6-е изд. перераб. и доп. – Л.: Машиностроение Ленингр. отд-ние 1983. Ч. 2. 448 с.
вал 1.frw

вертикальная плоскость
результирующая эпюра
эпюра крутящих моментов
эпюра эквивалентных моментов
Ведомость.spw

УО "ПГУ" г.Новополоцк
КП КИМ-053009-ДО-2009.
Пояснительная записка
Станок горизонтально-фрезерный
Схема кинематическая
Коробка скоростей(развертка)
Коробка скоростей(свертка)
Лист2.cdw

Коробка скоростей(развертка).
КИМ Иванов гр 05ТМ.doc
Задание для варианта №16
Выполнение задания № 2
Определяем диапазон регулирования скорости исполнительного органа по формуле
Определяем количество ступеней скорости исполнительного органа по формуле
Пользуясь ОСТ2.Н11-1-75 принимаем значения ряда ступеней скоростей: 100; 125; 160; 200; 250; 313; 400; 500; 630; 800; 1000; 1250; 1600; 2000; 2500; 3150.
Оптимальная структура привода для Z=16 запишется в виде
Проверяем возможность применения простой множительной структуры. Простая множительная структура возможна при условии для последней в порядке переключения группы: Для нашего варианта: следовательно вариант осуществим.
По полученной формуле структуры строим структурную сетку привода – рис.1.
Рис.1. Структурная сетка привода
В соответствии с компоновкой привода руководствуясь структурной сеткой рисуем кинематическую схему привода – рис.2.
Рис.2. Кинематическая схема привода
В соответствии со структурной сеткой строим график частот вращения – рис.3.
Рис.3. График частот вращения для привода
Определяем передаточные отношения передач привода:
Определяем числа зубьев колём привода.
Наименьшее общее кратное НОК1=18. Принимаем множитель Е=4. Тогда сумма зубьев первой группы .
Наименьшее общее кратное НОК1=18. Принимаем множитель Е=5. Тогда сумма зубьев первой группы .
Наименьшее общее кратное НОК1=7. Принимаем множитель Е=6. Тогда сумма зубьев первой группы .
По исходным данным включающим число скоростей привода число скоростей электродвигателя и значении знаменателя составить оптимальный вариант формулы структуры привода с многоскоростным электродвигателем и по этой формуле построить структурную сетку.
Задание для варианта № 16: ; ;
Определяем место электродвигателя (электрогруппа ) в порядке переключения и характеристику этой электрогруппы.
Для порядок подключения:
Характеристика электрогруппы:
Число ступеней привода: .
Откуда число ступеней коробки:
Составляем структурную формулу привода. При этом отводим электрогруппе первое место в порядке расположения. В порядке переключения электрогруппе предшествует основная группа .
Рис.4. Структурная сетка
Строим структурную сетку привода по полученной формуле структуры привода – рис.4.
По исходным данным включающим диапазон регулирования частот вращения шпинделя диапазон регулирования двигателя (вариатора) построить структурную сетку привода главного движения с бесступенчатым регулированием.
Задание для варианта № 16: ; .
Выполнение задания № 5
Определяем диапазон регулирования шестерёнчатой коробки по формуле .
Определяем количество групп передач по формуле .
Для с=8 и - . Принимаем m=1.
Число ступеней коробки определяется по формуле .
Для и - . Принимаем z=3
Определяем знаменатель геометрического ряда чисел оборотов по формуле .
Условие выполняется разрыва в бесступенчатом регулировании не будет.
Выражаем через стандартное значение : где к – целое число. Коэффициент рассчитается по формуле .
Для и - . Принимаем к=5. Тогда
Выразим диапазон бесступенчатого регулирования через стандартное значение : где е – целое число. Коэффициент рассчитается по формуле .
Для и - . Принимаем к=8. Тогда .
Общее количество ступеней регулирования:
Составим формулу структуры шестерёнчатой коробки: .
Рис.5. Структурная сетка привода с бесступенчатым регулированием: ;
вал 4.frw

вертикальная плоскость
результирующая эпюра
эпюра крутящих моментов
эпюра эквивалентных моментов
Лист1.cdw

Схема кинематическая
График частот вращения
Структурная сетка коробки скоростей
вал 2.frw

вертикальная плоскость
результирующая эпюра
эпюра крутящих моментов
эпюра эквивалентных моментов
Спецификация на коробку.spw

Станок горизонтально-фрезерный.
Коробка скоростей(развертка)
Станок горизонтально-фрезерный
Коробка скоростей(свертка)
Рукоятка переключения
Кольцо мазеудерживающее
Винт М8х30 ГОСТ 1491-80
Винт М12х40 ГОСТ 11738-84
Винт М6х20 ГОСТ 11738-84
Гайка круглая М90х1.5 ГОСТ 11871-88
Гайка круглая М60х1.5 ГОСТ 11871-88
Манжета ГОСТ 8752-79
Подшипник 205 ГОСТ 8338-75
Подшипник 106 ГОСТ 8338-75
Подшипник 107 ГОСТ 8338-75
Подшипник 310 ГОСТ 8338-75
Подшипник 8218 ГОСТ 7872-89
Шайба пружинная 12 ГОСТ 6402-70
Шайба пружинная 6 ГОСТ 6402-70
Шпонка 8х7х22 ГОСТ 23360-78
Шпонка 12х8х32 ГОСТ 23360-78
Шпонка 14х9х36 ГОСТ 23360-78
Шпонка 20х12х56 ГОСТ 23360-78
вал 3.frw

вертикальная плоскость
результирующая эпюра
эпюра крутящих моментов
эпюра эквивалентных моментов
Записка.doc
Разработка (или выбор) и описание компоновки станка 6
Проектирование и описание кинематической схемы станка 7
Динамические прочностные и другие необходимые расчеты
проектируемых узлов и деталей станка 10
Описание конструкции и системы смазки спроектированных узлов 57
Описание системы управления станком 59
Фрезерные станки предназначены для выполнения широкого круга операций. Они позволяют обрабатывать наружные и внутренние фасонные поверхности прорезать прямые и винтовые канавки фрезеровать резьбы и зубья зубчатых колес.
Различают две основные группы фрезерных станков: универсальные (общего назначения) и специализированные. К первым относятся горизонтально – фрезерные вертикально – фрезерные и продольно – фрезерные станки ко вторым – шпоночно – фрезерные шлице – фрезерные карусельно – фрезерные и другие станки.
Вертикально – фрезерные станки строятся обычно на одной базе с горизонтально – фрезерными и поэтому имеют много унифицированных деталей и узлов. Вертикально – фрезерный станок отличается от горизонтально – фрезерного вертикальным расположением оси шпинделя в связи с чем изменена конструкция станины шпиндельного узла а в кинематической схеме главного движения добавлена пара конических зубчатых колес передающих вращение на шпиндель.
Устройство консольного стола такое же как у горизонтально – фрезерного. Исключение составляет поворотная плита которая в столах вертикально – фрезерных станков отсутствует. Существуют другие типы станков данной группы у которых шпиндель смонтирован не в станине а в специальной головке. Головка может поворачиваться в вертикальной плоскости. В этом случае ось шпинделя можно устанавливать под углом к плоскости рабочего стола. У некоторых станков головка вместе со шпинделем может перемещаться в вертикальной плоскости.
На вертикально – фрезерных станках обрабатывают: плоскости уступы пазы.
Инструмент: торцовые фрезы цилиндрические фрезы сборные дисковые фрезы концевые фрезы.
Определение технических характеристик станка.
Частота вращения шпинделя nmin
Мощность электродвигателя Nэл.
Число оборотов электродвигателя nэл.
Размеры рабочего стола
Разработка и описание компоновки станка.
Специализированный вертикально-фрезерный станок предназначен для обработки фрезами отверстий со сложными поверхностями в том числе ступенчатыми. На станке можно обрабатывать детали как из легких сплавов так и из конструкционных..
Назначение станка. Станок предназначен для фрезерования различных поверхностей в различных . На станке обрабатываются детали сравнительно небольшие размеров и веса.
Основные узлы станка.: стол; шпиндельная бабка с коробкой подач подъемным механизмом; коробка скоростей; станина (колонна); основание станины.
Органы управления.: рукоятка перемещения стола; штурвал для подъема я опускания шпинделя и для включения механической подачи.
Движения в станке. Движение резания — вращение шпинделя с режущим инструментом. Движение подачи - осевое перемещение шпинделя с режущим инструментом. Вспомогательные движения — ручные перемещения стола и шпиндельной бабки в вертикальном направлении и быстрое ручное перемещение шпинделя вдоль его основания.
Обрабатываемая деталь устанавливается на столе станка и закрепляется в машинных тисках или в специальных приспособлениях. Совмещение оси будущего отверстия с осью шпинделя осуществляется перемещением приспособления с обрабатываемой деталью на столе станка.
Режущий инструмент в зависимости от используемого хвостовика закрепляется в шпинделе станка при помощи патрона или переходных втулок. В соответствия с высотой обрабатываемой детали и длинной режущего инструмент производится установке стола и шпиндельной бабки.
Поверхности могут обрабатываться как ручным перемещением шпинделя так и механической подачей.
Конструктивные особенности. Станок обладает высокой жесткостью прочностью рабочих механизмов мощностью привода и широким диапазоном скоростей резания и подач. Позволяющим использовать режущий инструмент оснащенный твердым сплавом. Наличие реверса управляемого как автоматически так и вручную обеспечивает возможность нарезания резьбы при ручном подводе и отводе метчика.
В конструкции вертикально – фрезерного станка предусмотрено автоматическое включение движения подачи после быстрого подвода режущего инструмента к обрабатываемой детали и автоматическое выключение подачи при достижении заданной глубины резания.
Шпиндель станка смонтирован на прецизионных подшипниках качения. Нижняя опора состоит из радиального шарикового подшипника класса АВ. В верхней опоре установлен одни шариковый подшипник класса В.
Для сокращения вспомогательного времени на станке обеспечена возможность включении и выключении подачи тем же штурвалом который осуществляет ручное быстрое перемещение шпинделя
Проектирование и описание кинематической схемы станка.
Предельные значения частот вращения: n1=315 мин-1; nz=1600 мин-1; φ=1.26.
Определим диапазон регулирования Rn.
Число ступеней z скорости исполнительного органа определяется зависимостью:
Находим частоты вращения:
График частот вращения
Динамические прочностные и другие необходимые расчеты проектируемых узлов и деталей станка.
Расчет числа зубьев колес
Подбор чисел зубьев колёс
1. Определение крутящих моментов
Определяем угловые скорости вращения валов
Определяем мощности на валах привода
Определяем крутящие моменты
2 Расчет зубчатых передач
Расчёт зубчатой передачи 1
n1=1460 мин-1; n2=1250 мин-1; M1=47901 Нм; z1=30;z2=38
Модуль передачи должен удовлетворять условию
где km – вспомогательный коэффициент km=13 для прямозубых колёс; M1F – исходный расчётный крутящий момент на шестерне; kF – коэффициент нагрузки для шестерни kF =15; YF1 – коэффициент учитывающий форму зуба YF1=36; z1=48; bm – отношение ширины колеса b к модулю m bm=25; FP1 – допускаемое напряжение для материала шестерни МПа.
Допускаемое напряжение на изгиб (МПа)
kFL – коэффициент режима нагружения и долговечности учитывающий влияние режима нагружения на длительный предел выносливости при изгибе kFL=1
Следующие расчеты производим с помощью пакета KOMPAS-SHAFT 2D V6
Расчёт зубчатой передачи 2
n1=1250 мин-1; n2=500 мин-1; Т2=55161 Нм; z1=22;z2=56
где km – вспомогательный коэффициент km=13 для прямозубых колёс; M1F – исходный расчётный крутящий момент на шестерне; kF – коэффициент нагрузки для шестерни kF =15; YF1 – коэффициент учитывающий форму зуба YF1=36; z1=31; bm – отношение ширины колеса b к модулю m bm=25; FP1 – допускаемое напряжение для материала шестерни МПа.
Расчёт зубчатой передачи 3
n1=500 мин-1; n2=125 мин-1; Т1=135975 Нм; z1=19;z2=77
где km – вспомогательный коэффициент km=13 для прямозубых колёс; M1F – исходный расчётный крутящий момент на шестерне; kF – коэффициент нагрузки для шестерни kF =15; YF1 – коэффициент учитывающий форму зуба YF1=36; z1=22; bm – отношение ширины колеса b к модулю m bm=25; FP1 – допускаемое напряжение для материала шестерни МПа.
Расчёт зубчатой передачи 4
n1=125 мин-1; n2=315 мин-1; Т2=536268 Нм; z1=19;z2=76
3. Расчет валов на прочность.
Расчет первого вала.
Предварительно определяем диаметр вала.
Со стороны муфты действуют силы
- окружное усилие Н;
- диаметр расположения в муфте элементов передающих крутящий момент;
В зацеплении со стороны шестерни действуют силы:
Расстояние между опорами и закрепленными на валу деталями:
где W – ширина стенки корпуса в месте посадки подшипника выбирается в зависимости от передаваемого момента.
Определяем длину и диаметр ступицы мм:
Построение эпюр нагружения и изгибающих моментов произведем с помощью пакета KOMPAS-SHAFT 2D V6.
Принимаем следующий материал вала: сталь 45 ГОСТ 1577-93 термическая обработка – нормализация отпуск твердость – 285 НВ допускаемое напряжение при контакте допускаемое напряжение при изгибе предел прочности предел текучести .
Схема нагружения выглядит следующим образом:
Выполним расчет. Графики распределения сил:
Графики распределения моментов:
Рисунок 4.11. Графики распределения моментов
Эквивалентный момент :
Определяем допускаемое напряжение для материала вала по формуле :
где =077 =0.95 K=2.15 s=3.
Диаметр вала в опасном сечении:
Принимаем диаметр 30 мм.
Принимаем посадочный размеры по ГОСТ 6636-69.
Расчет второго вала.
В зацеплении со стороны колеса действуют силы:
W – ширина стенки корпуса в месте посадки подшипника выбирается в зависимости от передаваемого момента.
Схема нагружения второго вала
Эквивалентный момент в первой точке:
где =077 =095 K=215 s=3.
Эквивалентный момент во второй точке:
Принимаем посадочный размеры по ГОСТ 6636—69
Расчет третьего вала.
Принимаем диаметр 35 мм.
Принимаем диаметр 40 мм.
Расчет четвертого вала.
Принимаем диаметр 48 мм.
Принимаем диаметр 55 мм.
Эквивалентный момент:
Принимаем диаметр 72 мм.
4. Расчет подшипников
Расчеты подшипников производим с помощью пакета KOMPAS-SHAFT 2D V6
5. Расчет шпоночных и шлицевых соединений.
Расчет шпоночного соединения 1.
Т=51933 Н·м — момент передаваемый валом
d = 30 мм — диаметр участка вала
Принимаем материал шпонки — сталь 45 с [sсм] =100 Нмм2
Подбираем шпонку с размерами: bh = 87 мм.
Определим рабочую длину шпонки lp исходя из условия прочности на смятие:
Полная длина шпонки:
L = lp + b = 13686+8 = 21686 мм
Принимаем призматическую шпонку 8725 мм.
Расчет шпоночного соединения 2.
Т=55161 Н·м — момент передаваемый валом
d = 35 мм — диаметр участка вала
L = lp + b = 157+8 = 237 мм
Расчет шпоночного соединения 3.
Т=135975 Н·м — момент передаваемый валом
d = 40 мм — диаметр участка вала
Подбираем шпонку с размерами: bh = 108 мм.
L = lp + b = 253+10 = 353 мм
Принимаем призматическую шпонку 10836 мм.
Расчет шпоночного соединения 4.
Т=536268 Н·м — момент передаваемый валом
d = 55 мм — диаметр участка вала
Подбираем шпонку с размерами: bh = 1610 мм.
L = lp + b = 4875+16 = 647 мм
Принимаем призматическую шпонку 161065 мм.
Расчет шлицевого соединения 1.
Материал — сталь 45. [sсм] =36 Нмм2
Расчету на смятие подлежат соединения с упрочненными поверхностями (закалкой цементацией) для начального периода работы до их приработки и соединений без упрочнения рабочих поверхностей или с улучшенными поверхностями для периода работы после приработки. Расчет на износ проводится для периода работы после приработки.
Расчет соединения на смятие:
где z – количество шлицев l— рабочая длина соединения h – высота поверхности контакта зубьев dm – средний диаметр соединения.
Расчет соединения на износ:
Выбираем шлицевое соединение
Расчет шлицевого соединения 2.
d = 50 мм — диаметр участка вала
Расчет шлицевого соединения 3.
Т=209827 Н·м — момент передаваемый валом
d = 72 мм — диаметр участка вала
Описание конструкции и системы смазки спроектированных узлов.
В современных станках как правило существуют две специальные гидравлические системы – смазки и охлаждения. Система смазки должна обеспечить надежную смазку всех основных трущихся сопряжений станка. Благодаря этому резко снижается износ механизмов уменьшается шум при работе станка и возрастает его к.п.д. Охлаждение режущего инструмента и обрабатываемой заготовки значительно повышает стойкость инструмента и влияет на точность обработки уменьшая тепловые деформации заготовки и узлов станка. Чем совершеннее системы смазки и охлаждения станка тем более длительное время он сохраняет свою точность.
Смазка трущихся поверхностей станков устраняет их непосредственный контакт благодаря чему не только значительно уменьшаются силы трения но и создаются условия для устранения или резкого уменьшения износа поверхностей. В сопряжениях станков имеют место различные виды трения.
Жидкостное трение наиболее желательное может быть обеспечено двумя основными методами – гидродинамическим и гидростатическим (подача смазки под давлением). Жидкостное трение в сопряжениях станков хотя и желательно но обладает рядом недостатков: во – первых оно связано с существенным усложнением конструкции системы смазки во – вторых наличие масляного слоя между поверхностями величина которого зависит от нагрузки может нарушить точность перемещения узла.
В качестве смазочных материалов в станках применяются жидкие минеральные масла и густые (консистентные) мази. Преимущественное распространение получили минеральные масла которые лучше подходят для смазки ответственных быстроходных сопряжений и позволяют более легко осуществлять централизованную смазку с её циркуляцией и очисткой от загрязнения.
Выбор того или иного сорта смазки зависит в первую очередь от скоростей относительного скольжения и нагрузок действующих в сопряжениях. При прочих равных условиях чем выше скорость относительного скольжения и чем меньше давление в сопряжении тем меньшей вязкости должна быть выбрана смазка.
В станках выбор сорта смазки осложняется тем что имеется большое разнообразие пар трения работающих при различных скоростях и нагрузках. Применение разных смазок неоправданно усложнило бы конструкцию смазочной системы и затруднило эксплуатацию такого станка.
В станках применяются разнообразные системы смазок. Наиболее совершенна централизованная смазка которая надежно обеспечивает смазку всех основных узлов станка.
Особое значение для станков имеет смазка шпинделей направляющих скольжения. Для смазки направляющих которая способствует значительному увеличению их долговечности применяются разнообразные методы. Простейшими но менее совершенными являются смазка ручным способом и при помощи индустриальных масленок. Непрерывная подача масла может осуществляться специальными роликами помещенными в масляных карманах станины при помощи насоса или при наличии масляной ванны. Для распределения масла по всей поверхности трения на направляющих выполняют специальные смазочные канавки.
Смазка шпинделей должна обеспечить жидкостное трение для подшипников скольжения и тонкий слой масла – для подшипников качения. Если система смазки циркулярная то масло выполняет также функции охлаждения. Смазка шпинделей настолько ответственна что для этой цели часто применяют специальную систему которая обеспечивает подачу к шпиндельным подшипникам того масла которое соответствует условиям их работы. Для быстроходных шпиндельных современных станков все чаще начинают применять смазку масляным туманом. Масляный туман образуется путем раздробления или распыления механическим или пневматическим способом струи или капли масла. При этом некоторые частицы масляного тумана достигают 2 мкм в диаметре. При помощи воздушного потока (струи) частицы тумана при подаче их к трущимся парам передвигаются через систему трубопровода на расстоянии нескольких десятков метров. Чем меньше распылены частицы масла тем дальше они переносятся воздушной струей.
Для распыления масла применяются пульверизаторы инжекторы или эжекторы. Подача масла к трущимся парам в виде масляного тумана имеет то преимущество что воздух уносит тепло возникающее в результате трения а расход масла незначителен (не превышает 10-6 м3с на 1 м2 трущейся пары). Кроме того масло через зазоры практически не течет что дает возможность сократить количество уплотнительных устройств до минимума. Подача распыленного масла к трущимся парам осуществляется через влагоотделитель осушитель и маслораспределитель.
При работе смазочных систем большое значение имеет надежная фильтрация масла чтобы инородные частицы и продукты износа при его циркуляции не попадали на трущиеся поверхности так как это приведет к их интенсивному износу.
Для снижения тепловой напряженности процесса резания применяются смазывающе-охлаждающие вещества (СОВ). Чаще всего применяют жидкости- эмульсии и масла с добавками твердых смазывающих веществ (графит парафин сернистый молибден и др.). Необходимо чтобы жидкость наряду с высокими охлаждающими свойствами обладала хорошей маслянистостью и вымывающей способностью была безвредна для рабочих и оборудования.
Охлаждающе-смазочная жидкость может быть подведена в зону резания различными способами наиболее простой – полив свободно падающей струей. Однако в этом случае смазывающее действие жидкости ничтожно так как она почти не попадает в зону контакта инструмента с заготовкой и со стружкой. Кроме того возникает сильное разбрызгивание жидкости. Лучший эффект дает подача жидкости под давлением причем струя направлена в зону резания. Находит применение также подвод жидкости под давлением через отверстия в инструменте. Хороший эффект дает как правило охлаждение жидкостью распыленной при помощи струи сжатого воздуха.
Описание системы управления станком
Вертикально – фрезерные станки характеризуются вертикальным расположением шпинделя. На фундаментальной плите установлена станина внутри которой размещен механизм главного движения с приводом от электродвигателя и коробки скоростей. В вертикальных направляющих станины смонтирована консоль которая может перемещаться вертикально по направляющим станины. На горизонтальных направляющих консоли установлены поперечные салазки поворотная плита а в направляющих последней – продольный (рабочий) стол. Таким образом деталь установленная непосредственно на столе в тисках или приспособлении может получить подачу в трёх направлениях. Наличие поворотной плиты позволяет в случае необходимости поворачивать рабочий стол в горизонтальной плоскости и устанавливать его на требуемый угол. Некоторые вертикально – фрезерные станки не имеют поворотной плиты. В этом случае их называют простыми в отличие от универсальных. Привод подачи стола размещен внутри консоли и состоит из электродвигателя коробки подачи и других механизмов.
Фрезерные патроны и короткие оправки вставляют непосредственно в конусное гнездо шпинделя и закрепляют длинным болтом (шомполом) проходящим через отверстие в шпинделе. Длинные оправки требуют дополнительной опоры поэтому один конец её закрепляют в отверстие шпинделя а второй располагают в подшипнике подвески хобота. Хобот расположен в верхней части станины. В его направляющих установлена подвеска с центром (слева) или с подшипником (справа). На хоботе могут быть закреплены также две поддержки.
Привод главного движения заимствуется от электродвигателя и осуществляется 18 – ступенчатой коробкой скоростей. Вращение от вала 1 с помощью зубчатых колес 1-2 передается на одну из трех пар колес 3-4 5-6 или 7-8. Отсюда одна из передачи 9-10 11-12 или 14-13 сообщает движение валу 4 а последний по цепи колес 15-16 или 17-18 – валу 5. Вращение с вала 5 передается на 6-ой вал при помощи конических зубчатых колес 19 и 20. С 6-го вала вращение передается на шпиндельный вал при помощи зубчатых колес 21 и 22. Частота вращения шпинделя изменяется переключением колес 3 – 5 – 7 10 – 12 – 14 и
Привод механизма подачи расположен внутри консоли. Электродвигатель с помощью передач 23-24 25 – 26 вращает вал 10 и далее через зубчатые колёса 27 – 28 29 – 30 или
– 32 33-34 35-36 или 37 – 38 вращение передает валу 12. Отсюда движение на вал 13 может быть передано через пару колёс 38 – 39 (колесо 39 смещается вправо для сцепления с муфтой 70) или через перебор состоящий из колес 57 – 57 43 – 44 . Широкое колесо 39 свободно насажено на вал и передает ему вращение при включении муфты 67. При включении дисковой фрикционной муфты 67 вал 13 может получить быстрое вращение необходимое для осуществления ускоренных ходов.
При выполнения данного курсового проекта я изучил подробно назначение вертикально-фрезерного станка его структуру область применения овладел методами моделирования и оптимизации а также научился анализировать его достоинства и недостатки и делать собственные выводы.
Список используемой литературы:
Металлорежущие станки Под. ред. Тепинкиевича. М:. Машиностроение 1973.-472 с.
Металлорежущие станки Под. ред. Пуша. М. Машиностроение 1985.-256 с.
Станки с числовым программным управлением Под. ред. Лещенко. М:. Машиностроение 1988
Общемашиностроительные нормативы режимов резания для технического нормирования работ на металлорежущих станках. В 2-х частях –М.: Машиностроение1974 ч.1 - 406 с. ч.2 – 200 с.
Свирщевский Ю.Н. Макейчик Н.П. Расчет и конструирование коробок скоростей и подач. – Минск: Вышэйшая шк.1976 – 590 с.
Анурьев В.И. Справочник конструктора-машиностроителя М:. Машиностроение т.11980 – 728 с. т.2 1981 – 559 с. т.3 1982 – 557 с.
Ничипорчик. Детали машин в примерах и задачах М:. Машиностроение 1981.
Кузьмин. Расчеты деталей машин. М:. Машиностроение 1985