Проектирование главного привода горизонтально-фрезерного станка




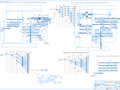
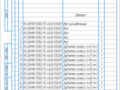
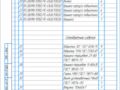
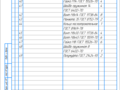
- Добавлен: 25.01.2023
- Размер: 760 KB
- Закачек: 2
Описание
Проектирование главного привода горизонтально-фрезерного станка
Состав проекта
![]() |
![]() |
![]() ![]() ![]() ![]() |
![]() ![]() ![]() ![]() |
![]() ![]() ![]() ![]() |
![]() ![]() ![]() ![]() |
![]() ![]() ![]() ![]() |
![]() ![]() ![]() ![]() |
![]() ![]() ![]() |
![]() ![]() ![]() |
Дополнительная информация
1-й лист8.cdw

Кинематические схемы
Кинематическая схема и график чисел оборотов горизонтально-фрезерного станка модели 6Р82.
Кинематическая схема и график чисел оборотов горизонтально-фрезерного станка модели 6П80Г.
График частот вращения проектируемого станка
Кинематическая схема коробки скоростей проектируемого станка
Спецификация 2.cdw

КП-206998-151002-МС-416.06.11.00.017
КП-206998-151002-МС-416.06.11.00.018
КП-206998-151002-МС-416.06.11.00.019
КП-206998-151002-МС-416.06.11.00.020
КП-206998-151002-МС-416.06.11.00.021
КП-206998-151002-МС-416.06.11.00.022
КП-206998-151002-МС-416.06.11.00.023
Крышка корпуса подшипника
Гайка М50 ГОСТ 11871-88
Винт установочный М6х8
Подшипник 307 ГОСТ 8338-75
Подшипник 7311А ГОСТ 27365-87
Крышка торцевая 21-80
Крышка торцевая 11-80x35
Кольцо 40-1 ОСТ 92-8969-78
Кольцо 35-1 ОСТ 92-8969-78
Кольцо 46-1 ОСТ 92-8969-78
КП-206998-151002-МС-416.06.11.00.024
Спецификация 3.cdw

Гайка М14 ГОСТ 15526-70
Винт М8х14 ГОСТ 11738-84
Манжета 35 ГОСТ 8752-79
Кольцо маслоотражательное
Винт М8х30 ГОСТ 11738-84
Гайка М8 ГОСТ 15526-70
Полумуфта ГОСТ 21424-93
Болт М8х45 ГОСТ 15591-70
Спецификация 1.cdw

КП-206998-151002-МС-416.06.11.00.000СБ
КП-206998-151002-МС-416.06.11.00.003
КП-206998-151002-МС-416.06.11.00.004
КП-206998-151002-МС-416.06.11.00.005
КП-206998-151002-МС-416.06.11.00.006
Зубчатое колесо z=45 m=3
КП-206998-151002-МС-416.06.11.00.007
КП-206998-151002-МС-416.06.11.00.008
КП-206998-151002-МС-416.06.11.00.009
КП-206998-151002-МС-416.06.11.00.010
КП-206998-151002-МС-416.06.11.00.011
КП-206998-151002-МС-416.06.11.00.012
КП-206998-151002-МС-416.06.11.00.013
КП-206998-151002-МС-416.06.11.00.014
Зубчатое колесо z=50 m=3
Зубчатое колесо z=37 m=3
Зубчатое колесо z=58 m=3
Зубчатое колесо z=53 m=3
Зубчатое колесо z=63 m=3
Зубчатое колесо z=68 m=3
КП-206998-151002-МС-416.06.11.00.015
Зубчатое колесо z=23 m=3
КП-206998-151002-МС-416.06.11.00.001
КП-206998-151002-МС-416.06.11.00.002
КП-206998-151002-МС-416.06.11.00.000СХ
Кинематические схемы
КП-206998-151002-МС-416.06.11.00.000ПЗ
КП-206998-151002-МС-416.06.11.00.016
Пояснительная записка
2 лист8.cdw

Минимальная частота вращения n
Максимальная частота вращения n
Мощность двигателя N
Cмазка разбрызгиванием масло Индустриальное И-20А ГОСТ
Обеспечить легкость переключения блоков зубчатых колес.
КП-206998-151002-МС-416.06.11.00.000
Технические требования:
Копия лист 2.3a.frw

Минимальная частота вращения n
Максимальная частота вращения n
Мощность двигателя N
Cмазка разбрызгиванием масло Индустриальное И-20А ГОСТ
Обеспечить легкость переключения блоков зубчатых колес.
Технические требования:
Титульник.doc
Государственное образовательное учреждение высшего профессионального образования
«Омский Государственный Технический Университет»
Кафедра: «Металлорежущие станки и инструменты»
Расчетно - пояснительная записка к курсовой
работе по дисциплине
“Металлорежущие станки и инструменты”
Пояснительная.doc
Расчет режимов обработки на консольно-фрезерных станках .6
Определение мощности двигателя . 9
Разработка кинематической схемы коробки скоростей . .. 10
Кинематический расчет 11
1 Выбор структурного варианта коробки скоростей .. .12
2 Определение чисел зубьев шестерен . 13
3 Определение мощностей на валах .14
4 Определение крутящего момента на валах 15
5 Предварительный расчет диаметров валов 15
Расчет цилиндрических прямозубых зубчатых колес 16
Расчет валов на прочность. .20
Расчет шпоночных соединений ..22
Расчет шлицевых соединений 23
Список литературы .. ..25
Создание современных точных и высокопроизводительных металлорежущих станков обуславливает повышенные требования к их основным узлам. В частности к приводам главного движения и подач предъявляются требования: по увеличению жёсткости повышению точности вращения валов шпиндельных узлов. Станки должны обеспечивать возможность высокопроизводительного изготовления без ручной последующей доводки деталей удовлетворяющих современным непрерывно возрастающим требованиям к точности.
В большинстве станков в качестве привода главного движения применяют коробки передач со ступенчатым регулированием частоты вращения соединённые с асинхронным электродвигателем. К приводам главного движения предъявляют следующие требования: обеспечение необходимой мощности резания сохранение постоянства мощности резания в коробках скоростей и крутящего момента обеспечение заданного диапазона регулирования скорости высокий КПД надёжность простота обслуживания и малые размеры.
Между наибольшей и наименьшей частотами вращения шпинделя промежуточные частоты могут быть расположены бесступенчато (плавно) или ступенчато (прерывисто). Применение бесступенчатого регулирования частоты вращения даёт возможность более просто осуществить оптимальные режимы резания. С применением бесступенчатого регулирования конструкция станка упрощается. В качестве электрического бесступенчатого привода применяют электродвигатели постоянного тока.
Ступенчатое регулирование даёт возможность установить ограниченное число частот вращения в заданных пределах. По этой причине величина регулирования не всегда может быть установлена оптимальной. Механизмы со ступенчатым регулированием компактны просты и имеют более высокий КПД по сравнению с бесступенчатым регулированием.
Анализ поверхностей детали и методы их геометрического образования
На фрезерном станке можно обрабатывать плоские поверхности. Для того чтобы получить заданные поверхности необходимо иметь образующую и направляющую линии соответствующей формы и длины.
рис.1 Цилиндрическая фреза
рис. 2 Дисковая фреза
t – продолжительность контакта зуба фрезы с заготовкой.
B – ширина фрезерования.
Проектируемый станок по кинематической структуре относится к классу Э22 и состоит из нескольких частных структур (рис. 3). Каждая из этих структур содержит кинематические группы для двух исполнительных движений:
– движения резания Фv(В) и движения подачи – продольной Фs1 (П2 ) поперечной Фs 2 (П3 ) или вертикальной Фs 3 (П4 ) .
Кинематическая группа движения резания Фv(В1) – простая. Ее внутренняя связь состоит из одной кинематической вращательной пары между шпинделем фрезы и станиной. Внешняя кинематическая связь с органом настройки iv находится между источником движения М1 и шпинделем. Кинематическая группа движения продольной подачи Фs1 (П2) – простая с внутренней связью в виде поступательной кинематической пары между столом и поперечными салазками и внешней кинематической связью: источник движения М2 iS ходовой винт с t1.
Кинематическая группа движения поперечной подачи Фs2 (П3 ) – тоже простая с внутренней связью в виде поступательной кинематической пары между поперечными салазками и консолью и внешней кинематической связью: источник движения М2 iS ходовой винт с t2.
Кинематическая группа движения вертикальной подачи Фs3 (П4 ) – простая с внутренней связью в виде поступательной кинематической пары между консолью и станиной и внешней кинематической связью: источник движения Д2 iS ходовой винт с t3.
– Источник движения (двигатель) 2 – Коробка скоростей 3 – Фреза 4 – Стол 5 –Салазки 6 –Консоль 7 –Коробка подач 8 – Реверсный механизм
рис. 3 Структурная схема проектируемого станка.
Расчет режимов обработки на консольно-фрезерных станках
Основными параметрами консольно-фрезерных станков согласно ГОСТ 165-72 являются размеры рабочей поверхности стола ВхL.
Для определения диапазона регулирования и мощности привода главного движения и привода подач необходимо установить наибольшие и наименьшие диаметры фрез которые можно закреплять в шпинделе станка.
Максимальный расчетный диаметр торцевой фрезы со вставными ножами оснащенными твердым сплавом и наименьший диаметр концевой фрезы с винтовыми пластинками из твердого сплава принимаются соответственно равными ;
Максимальный расчетный диаметр дисковой прорезной фрезы согласно ГОСТ 8529-69 и ее ширина принимаются соответственно равными
При выборе характерных операций для расчета режимов резания необходимо учитывать что приводы вертикальных и горизонтальных фрезерных станков унифицированы в связи с этим расчеты производят для следующих операций:
Черновое фрезерование плоскостей торцевыми фрезами расчетного максимального диаметра c твердым сплавом. Эта операция определяет максимальное значение сил резания и мощности привода.
Материал инструмента – твердый сплав Т5К10. Максимальная глубина резания определяется из условия снятия за один проход припуска на черновую обработку для штамповок ГОСТ 8529-69 или по эмпирической формуле:
Величину подачи скорость резания определяем по картам Ф-2Ф-4[2]:
где - коэффициент зависящий от размеров обработки;
-коэффициент зависящий от состояния обрабатываемой поверхности и ее твердости;
- коэффициент зависящий от стойкости и материала инструмента.
Фрезерование пазов концевыми фрезами минимального расчетного диаметра с пластинами из твердого сплава. Операция определяет максимальную частоту вращения шпинделя . Материал инструмента Т5К10 стойкость . Условная минимальная глубина резания принимается равной:
Скорость резания определяем по карте Ф-1[2]
Прорезка пазов или отрезка дисковыми фрезами максимального диаметра шириной из быстрорежущей стали. Эта операция определяет минимальную частоту вращения и минимальную величину подачи которая определяется из карты Ф2 [2]:
S min = 007-01 ммзуб
Расчетная глубина фрезерования принимается равной
Минимальная скорость резания определяем по карте Ф-4[2].
Минимальная и максимальная частоты вращения шпинделя определяем как:
Окружная составляющая силы резания и сила направленная вдоль подачи определяются по формулам
где - мощность резания.
Для дисковых трехсторонних цилиндрических концевых радиусных прорезных и угловых фрез
где – величина определяемая по таблице Ф-5[2] принимаем 0.5;
- скорость резания ммин;
- число зубьев фрезы принимаем равным 18;
- коэффициент зависящий от обрабатываемого материала принимаем 1.25;
- коэффициент зависящий от типа фрезы и обрабатываемого материала принимаем 1.
Сила направленная вдоль подачи
Определение мощности двигателя
Привод главного движения. Большинство приводов главного движения универсальных станков работают в повторно-кратковременном режиме при котором периоды работы под нагрузкой имеют такую длительность и так чередуются с паузами такой продолжительности что температура нагрева обмотки электродвигателя не превышает допустимой величины. Мощность электродвигателя работающего в указанном режиме определяют по формуле:
где hпр - КПД привода ориентировочно принимается hпр = 07 - 085;
Выбираем двигатель из справочника Анурьева[3] мощностью 55 кВт и числом оборотов равным 1450 обмин.
рис. 4 эскиз электродвигателя
Разработка кинематической схемы коробки скоростей
Для обеспечения кинематических расчетов сложных коробок применяется графоаналитический метод который заключается в графическом изображении чисел оборотов и передаточных отношений в виде графиков чисел оборотов и структурных сеток.
При изображении структурных сеток приняты следующие условности:
· Каждому валу коробки скоростей соответствует своя шкала чисел оборотов на которой точками отмечается число скоростей которое может иметь данный вал;
· Числа оборотов на каждой шкале изображаются в логарифмическом масштабе поэтому геометрический ряд чисел оборотов изображается в виде точек расположенных на одинаковом расстоянии (оно равно j - знаменателю геометрической прогрессии);
· Передаточные отношения изображаются в виде линий соединяющих точки соответствующих чисел оборотов соседних валов; наклон линии характеризует величину передаточного отношения параллельные линии означают одинаковые передаточные отношения.
Знаменатель геометрической прогрессии определяется по формуле:
где - максимальная чистота вращения шпинделя = 2293 обмин
- минимальная чистота вращения шпинделя = 8019обмин
z - число ступеней частот вращения = 15
Построение структурной сетки
Структурная сетка дает представление о структуре привода главного движения т.е. с её помощью можно определить какое количество валов какое количество частот вращения имеет каждый из валов в том числе и шпиндель. Какое количество ступеней переключения существует в каждой группе передач. По структурной сетке невозможно определить не конкретную частоту вращения какого-либо вала. Не величину передаточного отношения в блоке.
Вертикально проводят столько линий сколько валов имеет привод. На равном расстоянии друг от друга проводят горизонтальные линии сколько имеется главных движений. На каждом валу точками отмечаются количество частот вращения главного вала. На структурной сетки в каждой группе передач точки характеризующие частоты вращения соединяются лучами которые соответствуют количеству передаточных отношений в каждой группе передач. Принимаем z=4*2*2=16.
рис. 4 Структурная сетка привода главного движения
Кинематический расчет.
Целью кинематического расчета является определение параметров зацепления проектируемой коробки скоростей.
Сначала строится график частот вращения. Построение ведется аналогично построению структурных сеток но имеются свои особенности:
-добавляется вал электродвигателя
-построение начинается из точки соответствующей частоте вращения двигателя;
-для данного j = 126 передаточное отношение не должно превышать j3 и быть меньше j-6
Принимаем в соответствии с нормальными рядами чисел в станкостроении [1 прил. 1] следующие значения чисел оборотов шпинделя:
График частот вращения приведен на рисунке 5
рис. 5 График частот вращения.
По графику частот вращения определяется передаточное отношение через знаменатель геометрической прогрессии j и в зависимости от него определяются числа зубьев.
1 Выбор структурного варианта коробки скоростей
Из графика чисел оборотов получим следующие соотношения передаточных чисел
2 Определение чисел зубьев шестерен
Результаты приведены в таблице 1.
Чтобы проверить правильность выбора чисел зубьев зубчатых колес составляем уравнения кинематической цепи для каждой частоты вращения из которых определяются фактические частоты вращения. Также определяем относительную погрешность D
где nфакт - фактическая частота вращения обмин
nст - стандартная частота вращения обмин
Dдоп - допускаемая относительная погрешность %
Расчеты сведены в таблицу 2
Левая часть уравнения кинематической цепи
Относительная погрешность %
50*(4550)*(4253)*(5837)*(5837)
50*(4550)*(3758)*(5837)*(5837)
50*(4550)*(3263)*(5837)*(5837)
50*(4550)*(2768)*(5837)*(5837)
50*(4550)*(4253)*(3758)*(5837)
50*(4550)*(3758)*(3758)*(5837)
50*(4550)*(3263)*(3758)*(5837)
50*(4550)*(2768)*(3758)*(5837)
50*(4550)*(3758)*(5837)*(2372)
50*(4550)*(3263)*(5837)*(2372)
50*(4550)*(2768)*(5837)*(2372)
50*(4550)*( 4253)*(3758)*(2372)
50*(4550)*(3758)*( 3758)*(2372)
50*(4550)*(3263)*( 3758)*(2372)
50*(4550)*(2768)*( 3758)*(2372)
В связи с тем что погрешность величин скоростей не превышает допустимых на коробке скоростей указывается стандартные величины скоростей. Схема развертки коробки скоростей приведена на рис. 6
рис. 6 Кинематическая схема коробки скоростей проектируемого станка
3 Определение мощностей валах
Мощность на i -том валу определяется по формуле:
Где Ni -1 - мощность на предыдущем валу кВт
h1 - КПД пары подшипников h1 = 099
h2 - КПД зубчатой передачи h2 = 093
N1 = Nдв = 55*099 = 5445 Вт
N2 = Nдв =55*0992*093 =5013 Вт
N3 = Nдв =55*0993*0932 =461 Вт
N4 = Nдв =55*0994*0933 = 425 Вт
N5 = Nдв =55*0995*0934 = 391 Вт
4 Передаваемые крутящие моменты.
Крутящий момент на валах определяется:
М1 = 9550 (Nin)= 9550*(5.4451450) = 36.22 Н*м
= 9550*(50131250) = 383 Н*м
= 9550*(461500) = 88 Н*м
= 9550*(425315) = 1288 Н*м
= 9550*(391100) = 3734 Н*м
Результаты расчетов сводим в таблицу 3
Частота вращения валов обмин
Передаваемая мощность кВт
Передаваемые крутящие моменты Мкр Н*м
5 Предварительный расчет диаметров валов.
Диаметр валов при расчете на прочность приближенно определяют по следующей формуле
где С – коэффициент нагрузки С = 12 при переменной нагрузке и средних изгибающих моментах
d – диаметр вала см;
N – передаваемая мощность кВт;
n – частота вращения вала мин-1.
Расчет цилиндрических прямозубых зубчатых колес.
Основная форма расчета - расчет в форме определения модуля.
Расчет цилиндрических прямозубых колес ведется:
По напряжениям изгиба по формуле мм
По контактным напряжениям по формуле
где N - мощность передаваемая рассчитываемой шестерней определяется с учетом КПД передачи от двигателя до рассчитываемой шестерни кВт;
n - расчетная частота вращения шпинделя обмин(мин-1 ) .
где и -минимальная и максимальная частоты вращения вала на котором находится рассчитываемое зубчатое колесо;
- число зубьев рассчитываемого зубчатого колеса;
- передаточное отношение пары зубчатых колес в которой работает рассчитываемое зубчатое колесо понимаемое всегда как отношение числа зубьев большего колеса к числу зубьев меньшего колеса при зацеплении с рейкой считать равным единице.
- отношение ширины зубчатого колеса (длины зуба) к модулю (обычно принимается равным (6-10));
- коэффициент формы зуба (таб.1)[1];
- допускаемое напряжение изгиба (таб.3)[1] МПа;
- допускаемое напряжение (таб.3)[1] МПа;
- коэффициент долговечности;
- коэффициент неравномерности распределения нагрузки по длине зуба в следствии деформации валов;
- коэффициент динамичности.
Значение коэффициентов формы зуба при нормальном зацеплении представлены в таб.1[1].
Коэффициент долговечности при расчете на изгиб можно принимать равным единице; при расчете по контактным напряжениям
где - коэффициент характеризующий предполагаемое изменение мощности передаваемой рассчитываемой шестерней (табл. 3)[1].
- коэффициент характеризующий работу передачи на различных частотах вращения (табл. 5)[1];
- расчетное время работы передачи ч. Для станков средних размеров принимается: для постоянного включения передач ; для поочередно включенных передач ( -число поочередно включаемых передач между смежными валами):
- наименьшая частота вращения рассчитываемого зубчатого колеса в минуту;
- базовое число циклов нагружений для материала рассчитываемого зубчатого колеса (табл. 3)[1].
Минимальное значение коэффициента долговечности предельное минимальное . Если коэффициент долговечности получается больше единицы его следует принимать равным единице; если меньше 03 то следует принимать равным 03. Значение коэффициентов характеризующих предполагаемое изменение мощности представлены в табл. 4[1].
Значения коэффициентов характеризующих работу зубчатых колес на различных частотах вращения приведены в табл. 5[1].
Величина коэффициента неравномерности зависит от условий монтажа зубчатых колес и от размеров их: для колес расположенных между опорами на валах нормальной жесткости; для колес расположенных на консольных валах а также на жестких валах вблизи опор величина принимается в зависимости от соотношений ширины рассчитываемой шестерни и диаметра ее начальной окружности : при ; при ; для текстолитовых колес.
Коэффициент динамичности учитывает дополнительные динамические нагрузки возникающие вследствие неточности изготовления зубчатых колес.
Коэффициент динамичности определяется по формулам
для незакаленных зубчатых колес ()
для закаленных зубчатых колес
где - окружное усилие на зубе рассчитываемой шестерни;
- ширина рассчитываемой шестерни(длины зуба) мм
- динамическая нагрузка приходящаяся на 1 мм ширины шестерни Нмм;
где - окружная скорость на начальной окружности рассчитываемой шестерни мс;
- межцентровое расстояние пары мм;
- ошибка в шаге мкм (табл. 6)[1];
- передаточное отношение.
Поскольку для определения величины необходимо знать размер рассчитываемой шестерни т. е. величину ее модуля то весь расчет шестерни (при выполнении его в форме определения требуемого модуля) надо вести в следующей последовательности:
Сначала по формулам (7) и (8) найти расчетные значения считая .
По большему из полученных двух значений ( и ) путем округления его в большую сторону выбрать ближайшее нормализованное значение модуля;
В соответствии с выбранным значением т рассчитать по формулам (10) (11) и (12) величину коэффициента динамичности .
Полученное значение поставить в ту из формул (7) или (8) по которой при первоначальном вычислении было получено большее значение модуля. Если при этом расчетная величина модуля определенная с учетом будет меньше или равно принятому значению нормализованного модуля то значит принятый размер достаточен и расчет можно считать законченным. Если же она получится больше принятой нормализованной величины то надо увеличить принятую величину до ближайшего большего значения заново рассчитать величину и снова повторить расчет по формуле (7) или (8) для того чтобы убедиться в том что теперь полученная расчетная величина модуля меньше или равна принятой.
Стандартное значение т=2.5
Выбираем значение параметров:
=100 обмин(мин ) . =215 МПа;
=500 обмин(мин ) . =640 МПа;
=72; =1 (при расчете на изгиб);
Стандартное значение =2.
Выберем и проведем расчет
Полученное значение Кдин поставляем в ту из формул по которой при первоначальном вычислении было получено большее значение модуля. Если при этом расчетная величина модуля определенная с учетом Кдин будет меньше или равно принятому значению нормализованного модуля то значит принятый размер m достаточен и расчет можно считать законченным. Если же она получается больше принятой нормализованной величины m то надо увеличить принятую величину m до ближайшего большего значения по нормали заново рассчитать величину Кдин и снова повторить расчет m.
Подставляем в формулу:
5 мм меньше стандартного значения мм значит можно принять значение мм и на этом закончить расчет.
Расчет валов на прочность.
В качестве исходных условий при расчете вала следует принять те условия его работы при которых силы действующие на вал будут иметь максимальные значения.
Для валов цепи главного привода это имеет место тогда когда через вал шпинделю передаются минимальная из частот вращения при которой на него поступает полная мощность привода двигателя.
Для расчета валов составляется расчетная схема. На ней показано какие шестерни рассчитываемого вала находятся в зацеплении тогда когда на него действуют наибольшие по величине силы должны быть показаны все действующие силы и расстояния между опорами и точками приложения действующих на него сил.
Расчет выполняется в точном соответствии с методикой изучаемой в курсе "Сопротивление материалов". На основании схем нагружений строится расчетная схема в двух взаимно перпендикулярных плоскостях определяются в каждой из плоскостей реакции опор строятся эпюры изгибающих и крутящих моментов.
Основные нагрузки на валы привода - это кручение и изгиб.
Составляем уравнения для Мк Мх Qy для каждого вала
Г.У.Мх(0)=0 Мх(06)=0 Мк(0)=0 Мк(06)=0.
- момент - угол трения - угол зацепления=20 градусов.
По величинам изгибающих и крутящего моментов находится опасное сечение для которого расчитывается суммарный изгибающий момент
затем по нему и величине крутящего момента находится результирующий момент:
Необходимый момент сопротивления сечения вала определяется по формуле:
После чего определяем требуемый по условиям прочности диаметр вала:
Принимаем диаметр вала равный 40мм.
Расчет шпоночного соединения.
рис. 7 Размеры призматических шпонок.
Расчет ведется из условия что шпонки нагружены по всей длине.
Шпонки рассчитываются на смятие а в особо ответственных случаях и на срез.
Условие прочности на смятие
где P – усилие передаваемое шпонкой Н;
- площадь смятия мм2;
М – передаваемый момент Нм;
d – диаметр вала мм;
h – толщина шпонки мм;
[см] – допускаемое напряжение смятия (для стальных ступиц [см]=100-150МПа) МПа;
Рассчитаем шпонку первого вала на смятие:
По результатам расчета все шпоночные соединения выдерживают требуемую нагрузку.
Расчет шлицевых соединений.
рис. 8 . шлицевые соединения
Проверочный расчет на прочность прямобочных шлицев аналогичен расчету призматических шпонок. Расчет ведется только на смятие.
При расчете допускают что по боковым поверхностям зубьев нагрузка распределяется равномерно но из-за неточности изготовления в работе участвует 075 общего числа зубьев (т. е. коэффициент неодновременности работы зубьев ).
где М – передаваемый момент Нм;
z – число зубьев( в зависимости от d)
dср – средний диаметр соединения мм;
Fсм – площадь смятия мм2;
f – размер фаски зуба мм;
r – радиус скругления у основания зуба мм;
D – наружный диаметр мм;
d – внутренний диаметр мм;
[]см – допускаемое напряжение (для средней серии подвижного соединения под нагрузкой []см=5-15МПа
Параметры f r D d – принимаются по ГОСТ 1139-80 для прямобочных шлицевых соединений средней серии
Согласно полученным результатам расчета шлицевые соединения выдерживают заданную нагрузку.
«Приводы главного движения металлорежущих станков» методические указания Гаврилов В.А. Попов П.Е. Сергеев В.А. – изд-во ОмГТУ.2006г 38с.
Режимы резания металлов. Справочник. Барановский Ю.В. изд-во «Машиностроение» М. 1972г. 407с
Анурьев В.И. Справочник конструктора – машиностроителя. – М.: Машиностроение В 3-х томах 1979. Т1 728 с. Т2 559стр. Т3 557с
Проников А.С. Расчёт и конструирование металлорежущих станков-М: Высшая школа 1962.-421 с.
Металлорежущие станки: Альбом общих видов кинематических схем и узлов Под ред. А.М. Кучера. 3-е изд. перераб. и доп. СПб.: Машиностроение 1972. 306 с.
Пуш В.Э. Конструирование металлорежущих станков – М.: Машиностроение1987. – 390 с.