Разработка технологического процесса восстановления задней полуоси погрузчика ТО-49



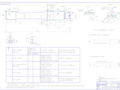
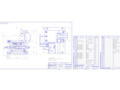
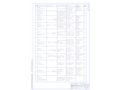
- Добавлен: 25.10.2022
- Размер: 2 MB
- Закачек: 3
Описание
Состав проекта
![]() |
![]() |
![]() ![]() ![]() ![]() |
![]() ![]() ![]() ![]() |
![]() ![]() |
![]() ![]() |
![]() ![]() |
![]() ![]() ![]() ![]() |
![]() |
![]() ![]() ![]() |
![]() ![]() ![]() |
![]() ![]() ![]() |
![]() ![]() ![]() |
![]() ![]() ![]() |
![]() ![]() ![]() |
Дополнительная информация
Маршрутный технологический процесс восстановления полуоси.dwg

Основное оборудование
Машина моечная ОМ-15429
токарно-винторезный
-наплавить наружные
Установка для наплавки
- точить наплавленные
Станок токарно-винторезный
генциркуль ШЦ-1-150-0
-контролировать восста-
новленные поверхности
- шлифовать поверхности
Маршрутный технологический
процесс восстановления полуоси
Ремонтный чертеж.dwg

Износ поверхности под
нарезать новую резьбу
Наплавка электроконтактная
механическая обработка
Технологический процесс: наплавить
(Деф.1); наплавить (Деф.2;3;4); точить (Деф.1);точить (Деф.2;3;4); фрезеровать (Деф.1); фрезеровать (Деф. 3);
закалка (Деф.1;2;3) шлифовальная (Деф. 2); контроль.
точении и шлифовании
Сталь 45Х ГОСТ 4543-71
*Размеры для справок.
Ресурс восстановленной полуоси должен быть равным ресурсу
Остальные ТТ по СТБ 1014-95.
Полуось бракуется при скручивании и усталостном износе.
Схемы базирования полуоси:
-при фрезеровании шлицев
ЛИСТ №3 (Приспособа).dwg

Размеры для справок.
Трущиеся поверхности смазать смазкой ЦИАТИМ - 201 ГОСТ
Остальные ТТ по СТБ 1022-96.
Опер. карта - токарная-1.doc
Наименование операции
Оборудование устройство ЧПУ
Обозначение программы
Установить деталь и закрепить.
Точить поверхности резец 2140-0001 ВК4 ГОСТ 18882-73
Снять полуось контролировать все обработанные поверхности: штангенциркуль ШЦ-1-150-01ГОСТ166-80 линейка стальная 500мм.
ОПЕРАЦИОННАЯ КАРТА МЕХАНИЧЕСКОЙ ОБРАБОТКИ
Точить поверхности выдерживая размеры 1 и 2.
Титульник1.doc
Белорусский Национальный Технический Университет
Факультет транспортных коммуникаций
Кафедра “Строительные дорожные машины”
Пояснительная записка
по дисциплине:”технология производства и ремонта машин”
«Разработка технологического процесса восстановления задней полуоси погрузчиа ТО-49»
ПЗ полуось.DOC
Ресурсы на ремонт и восстановление требуют намного меньше средств чем покупка новых деталей. Поэтому целью данной курсовой работы является разработка технологического процесса восстановления вала задней полуоси погрузчика ТО-49.
Анализ условий работы и дефектов полуоси
Вал задний устанавливается в заднем мосте и служит для передачи крутящего момента от дифференциала к бортовой передаче (рис.1). В процессе эксплуатации вал испытывает знакопеременные нагрузки и подвергается абразивному износу наружных поверхностей за счет попадания в сопряжения абразивных частиц через масло и т.п.
Рисунок 1 – Полуось в сборе
На ремонт вал поступил со следующими дефектами:
Износ наружной поверхности под подшипиник;
Износ (срыв) резьбы.
Полуось изготовлена из стали 45Х ГОСТ 4543-71.
На рисунке 2 представлен эскиз полуоси с указанием дефектных поверхностей и их номинальных размеров.
Рисунок 1 – Дефекты полуоси.
Анализ литературных и патентных источников по способам восстановления валов
Основным способом восстановления изношенных поверхностей цилиндрических деталей является наплавка.
При восстановлении ремонте наплавку выполняют примерно тем же металлом из которого изготовлено изделие однако такое решение не всегда целесообразно. Иногда при изготовлении новых деталей (и даже при ремонте) целесообразней на поверхности получить металл отличающийся от металла детали.
Действительно в ряде случаев условия эксплуатации поверхностных слоев значительно отличаются от условий эксплуатации всего остального материала изделия. Так например если деталь (изделие) должна определять общую прочность которая зависит от свойств металла и его сечения то поверхностные слои часто дополнительно должны работать на абразивный или абразивно-ударный износ (направляющие станин зубья ковшей землеройных орудий желоба валков канатно-подъемных устройств и др.). Условия работы могут усложняться повышенной температурой эрозионно-коррозионным воздействием окружающей среды (морской воды различных реагентов в химических производствах и др.). В качестве примера можно указать клапаны двигателей уплотнительные поверхности задвижек поверхности валков горячей прокатки и т.п.
Иногда такие детали и изделия целиком изготовляют из металла который обеспечивает и требования к эксплуатационной надежности работы его поверхностей. Однако это не всегда наилучшее и как правило не экономичное решение. Часто оказывается целесообразней все изделие изготовлять из более дешевого и достаточно работоспособного металла для конкретных условий эксплуатации и только на поверхностях работающих в особых условиях иметь необходимый по толщине слой другого материала. Иногда это достигается применением биметаллов (низкоуглеродистая сталь + коррозионно-стойкая сталь; сталь + титан и др.) а также поверхностным упрочнением (поверхностной закалкой электроискровой обработкой и др.) нанесением тонких поверхностных слоев (металлизацией напылением и пр.) или наплавкой слоев значительной толщины на поверхность.
Дуговой наплавкой под слоем флюса восстанавливают и упрочняют детали с достаточно большими износами (до 3 5 мм). При восстановлении изношенных деталей задача заключается в получении широкого слоя за один проход выполняя наращивание "гребенкой" – нанесением параллельно расположенного наплавленного металла.
Наплавочная головка состоит из механизма подачи проволоки изменяющего ступенчато или плавно скорости подачи электрода мундштука для подвода проволоки к детали флюсоапарата представляющего собой бункер с задвижкой для регулирования количества подаваемого флюса.
Наибольшее распространение получила наплавка на постоянном токе так как она способствует получению более высокой стабильности и качества процесса. Источниками постоянного тока служат сварочные преобразователи и выпрямители с пологопадающими или жесткой характеристиками рассчитанные на номинальный ток до 500 А.
При наплавке обычно применяют обратную полярность т.е. на деталь подается отрицательный потенциал а на электрод – положительный что уменьшает ее нагрев и позволяет более рационально использовать теплоту.
При наплавке деталей из низкоуглеродистых сталей применяют марганцовистые высококремнистые флюсы (АН-348А ОСЦ-45 и др.) обеспечивающие качественное раскисление металла шва. При наплавке легированных сталей для снижения угара легирующих элементов применяют флюсы с малым содержанием кремния (АН-20).
Электродная проволока при наплавке подбирается в зависимости от материала восстанавливаемой детали и предъявляемых к ней требованиям в условиях эксплуатации. Для наплавки деталей изготовленных из углеродистых сталей 30 40 45 используют проволоку из углеродистых сталей Нп-30 Нп-40 Нп-50 Нп-65. Наплавку деталей из сталей 30Х 35Х 40Х и других низколегировнных сталей производят проволокой Нп-З0ХГСА или других марок.
Для наплавки под слоем флюса используют наплавочные головки А-384 А-409 ABC устанавливаемые на обычные токарные станки или специализированные наплавочные полуавтоматы типов А580М А1408 А1409 и др.
Наплавка в среде защитных газов. В качестве защитных газов при ремонте деталей сваркой используются преимущественно углекислый газ и аргон. Наплавка в среде СО2 постепенно вытесняет вибродуговую наплавку и частично наплавку под слоем флюса. Производительность такого процесса на 25 30 % выше чем производительность наплавки под слоем флюса. Отпадает необходимость удаления шлака. При уменьшении зоны термического влияния можно восстанавливать детали малого диаметра (практически начиная с 10 мм).
В случае сварки в защитном газе с плавящимся электродом при помощи роликов электродная проволока подается к детали. Через наконечник горелки ток подводится к сварочной проволоке. Через сопло горелки в дуговое пространство поступает защитный газ который окружает электрическую дугу и предохраняет сварной шов от воздействия воздуха. Сварку и наплавку плавящимся электродом производят постоянным током обратной полярности. Сварка неплавящимся электродом может быть выполнена как постоянным так и переменным токами.
Аппараты для сварки и наплавки в защитных газах обеспечивают выполнение следующих операции; зажигание дуги в начале или наплавки подачу плавящегося электрода в дуговое по мере его расходования регулирование заданных параметров дуги передвижение электрической дуги по поверхности детали по мере плавления присадочного материала прекращение процесса сварки или наплавки.
Схема установки для сварки и наплавки в среде СО2 представлена на рис. 3. Один полюс источника постоянного тока 1 через аппарат управления 13 соединяется со сварочной горелкой 11 а другой полюс – со свариваемым или наплавляемым изделием 12. Газ из баллона 2 через подогреватель 3 глушитель 4 редуктор 5 ротаметр 6 газовый клапан 7 поступает в горелку. Углекислый газ в баллоне находится в жидком состоянии и при открытии вентиля сильно расширяется что приводит к значительному охлаждению СО2 поэтому подогреватель 3 является обязательным элементом установки (8 – сварочная проволока; 9 – ролики; 10 – наконечник горелки). Баллон вмещает 25 кг жидкой углекислоты а при испарении ее обеспечивает отбор 20 25 дм3мин для сварки. Перед подачей газа в горелку необходимо его осушить пропусканием через силикагель регенерированный при температуре t«300 °С. Высокое давление газа в системе снижается до рабочего при помощи редуктора типов РК-53 РДК-8 и др.
Рисунок 3 – Схема установки для сварки и наплавки в среде защитных газов.
Электроконтактная наплавка порошковой лентой. До 70 % деталей дорожной и строительной техники имеют износы не превышающие 05 мм. Применение для их восстановления процессов основанных на дуговой сварке (наплавка под слоем флюса в среде защитных газов) не совсем целесообразно поскольку получаемые приращения (2 3мм и более) требуют больших затрат на последующую механическую обработку. Кроме того наблюдаются значительный нагрев деталей и их деформация. Для электроконтактной приварки характерны высокая производительность (до 100 см2мин) минимальные потери присадочного материала (до 5 %) и припуск на последующую механическую обработку за счет возможности регулирования толщины наваренного слоя (03 15 мм). При минимальном термическом влиянии на деталь (до 03 мм) можно восстанавливать как наружные так и внутренние поверхности деталей из различных марок сталей чугунов цветных металлов и сплавов.
Сущность процесса заключается в следующем: электрический ток силое 8000 20 000 А и напряжением 15 40 В подают от трансформатора на деталь и присадочную ленту через медный электрод-ролик . За счет наличия в установке специального прерывателя или мощных конденсаторов ток подается импульсами. В местах контакта тонкие слои поверхности детали и присадочного материала расплавляются а под воздействием усилия от электрода-ролика пластически деформируются и свариваются. Усилие прижатия ролика к ленте 14 16 кН. Окружную скорость поверхности детали устанавливают такой чтобы площади сварочных точек перекрывали друг друга не менее чем на 25 %. В процесе приварки ленты чтобы получить 6 7 сварочных точек на 1 см шва скорость наплавки должна быть 2 4 ммин а длительность импульсов тока – 008 012 с.
Достоинство способа – возможность получения наваренных слоев с заданными трибологическими свойствами что в несколько раз повышает износостойкость деталей их коррозионную стойкость и другие свойства.
При высокой скорости протекающих при наварке процессов можно обойтись без защитных газов и флюсов. Прочная связь между присадочным материалом и основой достигается вследствие частичного плавления тончайших слоев металла в зоне контакта и диффузионными явлениями.
В качестве навариваемого материала применяют ленты проволоки а также порошки различного состава (процесс напекания). Чтобы интенсифицировать процесс на деталь следует подавать охлаждающую жидкость.
Кроме описанных выше основных способов наплавки достаточно широко применяемых в промышленности имеется ряд других имеющих ограниченное применение. Это наплавка с разделенными процессами тепловой подготовки наплавляемого металла и наплавляемой детали наплавка токами высокой частоты вибродуговая вакуумно-дуговая испаряющимся электродом газотермическая наплавка и напыление с использованием гибких шнуровых материалов электрошлаковая наплавка плазменная наплавка и напыление.
Наплавку с разделенными процессами тепловой подготовки применяют в основном при наплавке более легкоплавкого сплава (например на основе меди) на сталь.
В настоящее время процесс реализуется в виде выливания расплавленного в тигле наплавляемого металла на предварительно заформованную (для соответствующего фиксирования месторасположения жидкогонаплавляемого металла) деталь предварительно отдельно подогретую в печи. Для обеспечения смачивания и сцепления наплавляемого металла с деталью наплавляемую поверхность при нагреве детали в печи защищают от окисления флюсом. Способ трудно поддается механизации трудоемкий но обеспечивает хорошее качество наплавленного слоя.
Наплавка токами высокой частоты осуществляется расплавлением наложенной на наплавляемую поверхность смеси флюса и порошка наплавочного сплава (например зернистого сормайта) посредством подводимого индуктора обеспечивающего выделение достаточной тепловой мощности. Сормайт нагревается до температуры его плавления -1150 °С. Толщина получаемого слоя более 04 мм. Производительность наплавки довольно высока.
Разработаны способы наплавки в вакууме испаряющимся и полым накаливающимся электродом.
В настоящее время для решения вопросов защиты поверхности деталей от износа а также ремонта изношенных деталей с одновременным улучшением эксплуатационных свойств поверхности нашли широкое применение защитные покрытия наносимые на обрабатываемую поверхность различными методами газотермического напыления или наплавки. Обеспечение заданных свойств покрытий для конкретных условий эксплуатации деталей возможно при газотермическом напылении или наплавке как отдельных композиционных порошковых материалов так и многокомпонентных механических смесей порошков различного гранулометрического состава.
Недостатками любого метода газотермического напыления или наплавки использующего для нанесения покрытий порошковые материалы является сложность обеспечения стабильности свойств и надлежащего уровня качества покрытий получаемых из многокомпонентных механических смесей порошков что вызвано сегрегацией компонентов при смешивании и транспортировании смеси из дозирующих устройств в струю. Сегрегация приводит к неравномерности формирования структуры увеличению пористости снижению прочности и ухудшению эксплуатационных характеристик покрытий.
Указанных недостатков лишены системы газопламенного напыления использующие в качестве распыляемого материала стержни изготовленные высокотемпературным спеканием или экструзией порошков со связующим. Малая длина стержней не дает возможности выполнять процесс напыления непрерывно что ограничивает возможности применения данного метода.
Получение покрытий с заданными свойствами в том числе и из многокомпонентных механических смесей порошков различного гранулометрического состава обеспечивается при использовании гибких шнуровых материалов (ГШМ). Они специально разработаны для использования в системах газопламенного напыления а также для ручной газопламенной наплавки и представляют собой получаемый экструзией композиционный материал шнурового типа состоящий из порошкового наполнителя и органического связующего полностью исчезающего при нанесении покрытия - связующее сублимирует в процессе нагрева при температуре 400 °С без какого-либо отложения на подложку. Прочность и эластичность гибких шнуров позволяет пользоваться ими так же как и проволокой и наносить покрытия с помощью газопламенных аппаратов проволочного типа. Метод газопламенного напыления отличается экономичностью простотой аппаратурного оформления и надежностью оборудования для нанесения покрытий что позволяет использовать его там где требуется соблюдение непрерывности и стабильности технологического процесса. В цеховых условиях процесс газопламенного напыления может быть механизирован или автоматизирован. Кроме того небольшая масса и мобильность ручных аппаратов позволяет использовать их для обработки крупногабаритных деталей и металлоконструкций в полевых условиях.
Технология изготовления гибких шнуровых материалов позволяет получать в составе шнуров практически любые сочетания различных порошковых материалов отличающихся по гранулометрическому составу. Стабильная подача шнурового материала в высокотемпературную зону газового потока по оси струи аналогично достигаемой при распылении стержней и проволок а также правильный подбор состава компонентов порошковых смесей и размера частиц порошков гарантирует расплавление всех составляющих порошкового наполнителя шнура в том числе и керамики. Это обеспечивает получение следующих преимуществ по сравнению с традиционными методами газотермического напыления и наплавки:
- повышение коэффициента использования напыляемого материала;
- повышение прочности сцепления покрытий с основой при напылении (адгезия);
- повышение прочности сцепления напыленных частиц между собой (когезия);
- повышенная скорость распыляемых частиц в газовом потоке позволяет наносить покрытия с пониженной пористостью достигаемой при использовании газопламенного порошкового напыления;
- катушечная намотка гибкого шнура позволяет автоматизировать операцию напыления.
Сущность вибродуговой наплавки заключается в том что в процессе наплавки при каждом импульсе тока расплавляются и переносятся с плавящегося электрода на изделие небольшие порции материала. Периодическое замыкание и размыкание электрической цепи в местах контакта электродной проволоки с изделием осуществляется вибраторами. Наплавка ведется в воздушно среде с целью уменьшения теплового воздействия электрического разряда на деталь (рис.4).
Рисунок 4 - Вибродуговая наплавка:
- наплавляемое изделие; 2 - сопло для подачи охлаждающей изделие жидкости;3 - сопло для подачи жидкости в зону сварки;4 - электродная проволока; 5 - электродоподающие ролики;6 - электромагнитный вибратор; 7 – пружина
Метод требует дефицитных наплавочных материалов обеспечивает получение твердости наплавленного слоя 50-58 HRC последующей термической обработки поэтому применение вибродуговой наплавки эффективно при восстановлении сложных по конфигурации и трудоемких деталей имеющих износ отдельных поверхностей. Затраты на восстановление в этом случае снижаются в 3-8 раз по сравнению с изготовлением новых изделий. Вибродуговую наплавку успешно применяют при ремонте автомобилей станочного кузнечно-прессового литейного подъемно-транспортного и другого оборудования.
При использовании ГШМ достигается высокая производительность и экономичность напыления и наплавки. Этот факт подтверждается возрастающим в мире спросом на шнуровые материалы особенно на материалы из оксидной керамики и карбида вольфрама.
Технологический процесс производства деталей с покрытиями получаемыми с помощью шнуровых материалов включает операции предварительной мойки обезжиривания абразивно-струйной обработки заготовок газопламенного напыления сплавления покрытий (при использовании гибких шнуровых материалов на основе самофлюсующихся сплавов системы Ni(Co)-Cr-B-Si) и последующей размерной обработки деталей. Операция газопламенного напыления может быть заменена на операции газопламенной плазменной или электродуговой неплавящимся электродом наплавки. При этом можно использовать стандартное промышленное оборудование.
Плазменная наплавка применяется при восстановлении изношенных деталей когда необходимо восстановить размеры деталей и по возможности приблизить металл наплавленного слоя к основному металлу по твердости и другим механическим свойствам. Она также применяется при изготовлении новых деталей для придания им рабочих поверхностям определенных свойств: жаропрочных кислотостойких износостойких и других. В этих случаях основа изделия состоит из наиболее дешевых материалов (например из обычной низкоуглеродистой стали) а поверхность - из сплава со специальными свойствами.металла наплавки в таких изделиях составляет несколько процентов от их массы а работоспособность значительно выше чем у аналогичных изделий из однородных материалов.
Рисунок 5 - Схема установки «ТЕХНИКОРД ТОП-ЖЕТ2» для газопламенного напыления:
– пистолет-распылитель; 2 – стойка для катушек и пульта; 3 – пульт управления; 4– блок подготовки воздуха; 51013 – регуляторырасхода соответственно воздуха кислорода и горючего газа;6811 – регуляторы давления соответственно воздуха кислорода игорючего газа; 7 912 – манометры соответственносжатого воздуха кислорода и горючего газа;1415- штуцеры входа соответственно горючего газа и кислорода;161718- штуцеры выхода соответственно горючего газакислорода и воздуха; 19 – пламягасители;2021 22 – шланги соответственно горючего газа кислорода и сжатого воздуха;23 – баллон для горючего газа; 24 – редуктор горючего газа;25 – кислородный баллон; 26 – кислородный редуктор.
При плазменной наплавке стремятся обеспечить минимальный переход основного металла в наплавленный и более высокие свойства как металла наплавки так и соединения в целом.
Рисунок 6 - Схемы плазменной наплавки:
а - плазменной струей с токоведущей присадочной проволокой; б - плазменной дугой с нейтральной присадочной проволокой; в - комбинированный (двойной) дугой одной проволокой; г - то же с двумя проволоками; д - горячими проволоками;
е - плавящимся электродом; ж - с внутренней подачей порошка в дугу; з - с внешней подачей порошка в дугу;
- защитное сопло;2 - сопло плазмотрона; 3 - защитный газ; 4 - плазмообразующий газ; 5 - электрод; 6 - присадочная проволока; 7 - изделие; 8 - источник питания косвенной дуги; 9 - источник питания дуги прямого действия; 10 - трансформатор; 11 - источник питания дуги плавящегося электрода; 12 - порошок; 13 - порошок твердого сплава.
Плазменная наплавка обладает такими важными преимуществами как высокая производительность широкая возможность легирования слоев наплавки большой диапазон регулирования ввода теплоты в основной и наплавочный металлы возможность применения любых наплавочных металлов.
Перечисленные положительные стороны способов плазменной наплавки не только существенно расширяют технологические возможности их применения но и позволяют получать значительный экономический эффект за счет наплавки слоев с минимальной глубиной проплавления и сохранения первоначальных физико-механических свойств при меньшем количестве наплавленного металла; изготовления деталей из низкоуглеродистых сталей с поверхностями упрочненными твердыми сплавами вместо дорогих легированных сталей; применения износостойких порошковых сплавов повышающих срок службы наплавленных деталей; уменьшения припуска на механическую обработку. Тенденция развития машиностроения строительных дорожных сельскохозяйственных и других машин требует применения износостойких покрытий.
Повышение интереса в нашей стране и за рубежом к плазменной наплавке как способу нанесения износостойких покрытий с целью упрочнения новых и восстановления изношенных деталей объясняется тем что работающие в соединениях детали сельскохозяйственных строительных горно-рудных дорожных и других машин подвергаются как правило знакопеременным нагрузкам и быстро выходят из строя.
Для увеличения срока службы необходимо наносить износостойкие покрытия на поверхность таких деталей с учетом условий их работы вида износа и обеспечивать высокую прочность сцепления наплавляемого слоя с основным металлом. При этом плазменной наплавкой можно наплавлять не только дорогие сплавы никеля и кобальта но и дешевые - на основе железа.
С помощью легирования ферромарганцевых феррохромовых сплавов можно эффективно упрочнять и восстанавливать большую номенклатуру деталей работающих при температуре не превышающей 500 °С. Твердость слоев наплавленных сплавами на железной основе составляет HRC 50-60 при хорошем сочетании вязкости износостойкости.
В зарубежной практике плазменную наплавку широко применяют при упрочнении следующих деталей: седел клапанов химического оборудования; внутренних поверхностей ротационных насосов из стального литья; клапанов автотракторных двигателей; изнашивающихся поверхностей деталей атомного реактора; барабанов бумагоделательных машин; режущих кромок шнекобурильных машин долот для вращательного бурения зубьев экскаваторов.
При восстановлении изношенных деталей плазменную наплавку применяют для деталей типа "вал".
Промышленное применение плазменной наплавки токоведущей присадочной проволоки началось в середине 60-х годов с наплавки медными сплавами Бр КМцЗ-1 и МНЖКТ5-1-02-02 уплотнительных поверхностей стальных фланцев и колец. Затем была освоена плазменная наплавка этими же проволоками стальных цилиндрических изделий диаметром от 60 до 170мм (штоки валики поршни и т.д.) сплавами на основе меди.
Для осуществления наплавки плазменной струей с токоведущей присадочной проволокой используется после некоторой модернизации стандартное сварочное оборудование.
В настоящее время серийно выпускают установки для плазменного напыления (УМП-5 УМП-6 УПУ-3 УПУ-5) плазменной сварки (УПС-301 УПС-403 УПС-804) плазменной наплавки (УПН-303 УПН-602) а также установки для плазменной наплавки фасок клапанов. Сварочные плазменные установки также можно применять для наплавки. Установки для плазменного напыления могут быть использованы при плазменной наплавке после изменения электрической схемы и замены напыляющего плазмотрона плазмотроном для наплавки. Схема установки для плазменной наплавки с подачей порошка в сварочную ванну представлена на рисунке 7. Стабильность и ресурс работы установки предназначенной для плазменной наплавки порошковыми материалами в первую очередь зависят от надежности работы плазмотрона и порошкового питателя.
Рисунок 7 – Схема плазменной наплавки с подачей порошка
- источник питания 2 - вращатель 3 - наплавляемая деталь 4 - порошковый питатель 5 - плазмотрон 6 - пульт управления 7 - баллоны с газом 8 - балластный реостат 9 – дроссель.
В качестве автомата для наплавки может быть применен любой сварочный автомат (лучше предназначенный для сварки в защитных газах). Переделка автомата заключается в следующем. Вместо обычной сварочной головки устанавливается плазменная головка. Поскольку угол наклона плазменной головки к изделию оказывает существенное влияние на процесс наплавки на автомате обязательно должен иметься поворотный механизм позволяющий устанавливать головку под любым углом к поверхности изделия в вертикальной плоскости.
На автомате устанавливаются коммуникации для подвода к плазменной головке плазмообразующего и защитного газов и охлаждающей воды.
Токоведущая (электродная) присадочная проволока подается непосредственно под плазменную головку. Торец токоведущего мундштука располагается на расстоянии около 15мм от плазменной струи. Мундштук для подачи проволоки следует изготавливать массивным чтобы предотвратить его случайное обгорание. Токоподводящие мундштуки изготавливаются сменными для подачи присадочной проволоки различных диаметров: от 10 до 50мм.
Проектирование технологического процесса восстановления полуоси
С учетом имеющихся дефектов последовательность технологического процесса восстановления вала следующую:
Очистить вал от грязи
Выявить дефекты вала
Наплавить наружные поверхности с одной стороны
Наплавить наружные поверхности с другой стороны
Точить наружные поверхности с одной стороны
Точить наружные поверхности с другой стороны и нарезать резьбу
Фрезеровать шлицы с одной стороны
Фрезеровать шлицы с другой стороны
Закалить наружные поверхности
Шлифовать поверхность под подшипник
Контролировать восстановленные поверхности.
Технологический маршрут восстановления полуоси с указанием схем базирования применяемого оборудования и режимов обработки представлен в Приложении А к курсовой работе.
Выбор способа восстановления полуоси.
Для обеспечения высокой надежности и долговечности капитально отремонтированных машин большое значение имеет правильный выбор способа восстановления деталей.
Выбор способа зависит от конструктивно-технологических особенностей детали условий ее работы величины износов характера дефектов и особенностей самих способов восстановления определяющих долговечность отремонтированных деталей и себестоимость ремонта.
Конструктивно-технологические особенности деталей определяются их формой размерами материалом видом термообработки точностью изготовления шероховатостью поверхности типом посадок видом трения и величиной допустимого и предельного износа при эксплуатации.
Зная конструктивно-технологические особенности детали и условия ее работы а также эксплуатационные свойства различных способов ремонта можно в первом приближении решить вопрос о применении того или иного способа восстановления для данной детали.
Таким образом можно установить какие из деталей могут ремонтироваться несколькими способами а какие допускают только один способ восстановления. Данный критерий позволяет определить применимость способов восстановления к конкретным деталям и называется технологическим критерием или критерием применимости.
Окончательное решение вопроса о выборе рационального способа восстановления принимается при помощи технико-экономического критерия связывающего долговечность отремонтированной детали с себестоимостью ее восстановления.
Проведя анализ способов восстановления валов наружные поверхности вала заднего восстанавливаем автоматической наплавкой в среде углекислого газа с последующей механической обработкой.
Основное преимущество этого процесса – небольшой нагрев детали (не более 100º С) и возможность регулирования твердости наплавленного слоя от 180 НВ до 54 HRC в зависимости от марки наплавочной проволоки и использования охлаждения при наплавке а также высокая производительность до 25 кгч.
При ремонте деталей из стали используется проволока с повышенным содержанием углерода Нп-50. Если не требуется высокая твердость наплавленного металла применяется проволока Нп-30 при наплавке резьбовых поверхностей – проволока Св-08 и Св-10. Обычно используется проволока диаметром 15 20 мм.
Наплавка ведется постоянным током при обратной полярности при напряжении 12 28 В. Низкое напряжение используется при наплавке деталей малого диаметра высокое – при слое наплавки 15 30 мм.
После наплавки производим механическую обработку поочередно с двух сторон.
Выбор оборудования для восстановления полуоси
При выборе оборудования для каждой технологической операции необходимо учитывать назначение обработки габаритные размеры деталей размер партии обрабатываемых деталей расположение обрабатываемых поверхностей требования к точности и качеству обрабатываемых поверхностей.
Оборудование для автоматической наплавки: токарный станок с понижающим редуктором (дополнительно); установка для наплавки УД 609.06.
Для токарной обработки выбираем токарно-винторезный станок 1К62 с частотой вращения шпинделя (при бесступенчатом регулировании) 30 – 3000 обмин мощность электродвигателя 15 кВт. Токарную обработку производим проходным резцом 2140-0001 Т15К6 и резец 2140-0042 ВК6 ГОСТ 18882-73.
Шлицы фрезеруем на фрезерном станке 6Т82 Фреза дисковая 2254- 1456 2 ГОСТ 2679-93.
Для закалки печь отпускная сопротивления СШ3-667 и 3 УХЛ2.
Полуось шлифуем на круглошлифовальном станке 3Б161 с частотой вращения шпинделя с заготовкой (бесступенчатое регулирование) 100 800 обмин частота вращения шпинделя с шлифовальным кругом 2300;2700 обмин мощность электродвигателя 5 кВт. Шлифование производим кругом шлифовальный ПП 55х20х30 24А 10-П С2 7 КПГ ГОСТ 2424-83 зернистость 50-6.
Для контроля используется штангенциркуль ШЦ-1-150-01 ГОСТ 165-80 калибры для шлицев ГОСТ 7951-81 линейка стальная и индикатор часового типа для контроля биений.
Расчет режимов обработки и норм времени
Операция 020 – наплавочная.
Шаг наплавки должен быть в 1 3 раза больше диаметра наплавочной проволоки. Выбираем проволоку для наплавки в зависимости от диаметра заготовки: все восстанавливаемые поверхности имеют диаметры которые входят в диапазон размеров 60 80 мм поэтому проволока для наплавки – Нп-50 диаметром 20 мм. Тогда шаг наплавки будет равен:
где - диаметр наплавочной проволоки мм ().
Амплитуда вибрации электродной проволоки равна:
Скорость наплавки определяется в зависимости от требуемой толщины наплавленного слоя по формуле:
где - скорость подачи проволоки ммин;
- толщина наплавляемого слоя мм;
- шаг наплавки мм ();
- коэффициент учитывающий угар ().
Скорость подачи проволоки:
где - напряжение наплавки В ();
Толщина наплавленного слоя:
где - скорость вращения детали ммин( );
- коэффициент формирования шва ().
Зная скорость подачи проволоки и толщину наплавляемого слоя находим скорость наплавки:
Зная скорость вращения детали и ее средний диаметр определяем необходимую частоту вращения по формуле:
где - диаметр наплавляемой поверхности мм () .
Угол подачи проволоки к детали 45º расход газа 001 лмин.
Особенность нормирования при автоматической наплавке на специальной установке или приспособленном токарном станке состоит в необходимости учета как факторов сварочного процесса так и режимов используемых при токарной обработке.
Норма штучно-калькуляционного времени:
где - основное время мин;
- вспомогательное время мин;
- время обслуживания рабочего места мин;
- подготовительно-заключительное время на одну деталь мин.
В зависимости от того какие параметры процесса автоматической наплавки известны определение нормы времени осуществляется по формуле:
- при известной скорости наплавки и шаге наплавки:
где - шаг наплавки мм ();
- скорость наплавки ммин ();
- общая длина наплавляемых поверхностей мм ();
- число проходов при наплавке ();
- диаметр наплавляемой поверхности мм ()
- толщина наплавляемого слоя за один проход мм ();
- коэффициент учитывающий время обслуживания рабочего места отдых и личные надобности рабочего;
- вспомогательное время на установку закрепление и снятие детали мин ();
- время на очистку и контроль погонного метра наплавленного валика мин ();
- длина валика наплавленного валика м:
- подготовительно-заключительное время на ознакомление с работой наладку оборудования и сдачу наплавленных деталей и оснастки мин ().
Тогда норма штучно-калькуляционного времени будет равно:
Операция 025 – токарная:
Токарную обработку вала после наплавке производим на токарно-винторезном станке 1К62 с частотой вращения шпинделя 30 – 3000 обмин мощность электродвигателя 15 кВт.
Произведем расчет режимов резания при обтачивании поверхности под подшипник. После наплавки диаметр поверхности составляет 50 мм длина наплавленного участка 63 мм. Обработку поверхности производим резцом 2140-0001 Т15К6 ГОСТ 18882-73.
В результате расчета необходимо рассчитать необходимую мощность резания и сопоставить ее с мощностью станка на котором будет произведена данная обработка.
Мощность расходуемая на обтачивание наружной поверхности будет равна:
где - сила резания Н;
- фактическая скорость резания ммин.
Скорость резания определяется из следующего выражения:
где - коэффициенты и показатели степеней которые характеризуют условия обработки. Для обтачивания резцом Т15К6 их значения будут следующими ();
- период стойкости резца мин ();
- толщина стружки снимаемой за один проход инструмента мм().
Тогда скорость резания равна:
По расчётному значению скорости резания определяется частота вращения шпинделя с закреплённой деталью:
где dв – наружный диаметр детали мм(dв=50мм).
Частота вращения шпинделя регулируется бесступенчато поэтому .
где - коэффициенты и показатели степеней учитывающие условия обработки ()
Тогда необходимая мощность резания будет равна:
Согласно полученной мощности резания токарную обработку можно производить на выбранном станке так мощность токарного станка равна 15 кВт.
Основное технологическое время в интервале скоростей резания 20 220 ммин рассчитывается по формуле:
где длина обрабатываемого участка мм ();
- частота вращения шпинделя обмин ();
- число проходов ().
Вспомогательное время составляет .
Конструкторская разработка приспособления для фрезерования
Основную группу технологической оснастки составляют приспособления механосборочного производства. Приспособлениями в машиностроении называют вспомогательные устройства к технологическому оборудованию используемые при выполнении операций обработки сборки и контроля.
Применение приспособлений позволяет:
- устранить разметку заготовок перед обработкой повысить ее точность;
- увеличить производительность труда на операции;
- снизить себестоимость продукции;
- облегчить условия работы и обеспечить ее безопасность;
- расширить технологические возможности оборудования;
- организовать многостаночное обслуживание;
- применить технически обоснованные нормы времени и сократить число рабочих необходимых для выпуска продукции.
Частая смена объектов производства связанная с нарастанием темпов технического прогресса требует создания конструкций приспособлений методов их расчета проектирования и изготовления обеспечивающих неуклонное сокращение сроков подготовки производства.
Затраты на изготовление технологической оснастки составляют 15 20 % от затрат на оборудование для технологического процесса обработки деталей машин или 10-24 % от стоимости машины. Станочные приспособления занимают наибольший удельный вес по стоимости и трудоемкости изготовления в общем количестве различных типов технологической оснастки.
Классификацию приспособлений проводят по следующим признакам:
По целевому назначению приспособления делят на пять групп:
- станочные приспособления для установки и закрепления обрабатываемых заготовок на станках. В зависимости от вида обработки различают токарные фрезерные сверлильные расточные шлифовальные и другие приспособления;
- приспособления для крепления режущего инструмента. Они характеризуются большим числом нормализованных деталей и конструкций что объясняется нормализацией и стандартизацией самих режущих инструментов;
- сборочные приспособления используют при выполнении сборочных операций требующих большой точности сборки и приложения больших усилий;
- контрольно-измерительные приспособления применяют для контроля заготовок промежуточного и окончательного контроля а также для проверки собранных узлов и машин. Контрольные приспособления служат для установки мерительного инструмента;
- приспособления для захвата перемещения и перевертывания обрабатываемых заготовок а также отдельных деталей и узлов при сборке.
По степени специализации приспособления делят на универсальные специализированные и специальные.
Универсальные приспособления (УП) используют для расширения технологических возможностей металлорежущих станков. К ним относятся универсальные поворотные делительные столы; самоцентрирующие патроны.
Универсальные безналадочные приспособления (УБП) применяются для базирования и закрепления однотипных заготовок в условиях единичного и мелкосерийного производства. К этому типу принадлежат универсальные патроны с неразъемными кулачками универсальные фрезерные и слесарные тиски.
Универсально-наладочные приспособления (УНП) используют для базирования и закрепления заготовок в условиях многономенклатурного производства. К ним относятся универсальные патроны со сменными кулачками универсальные тиски скальчатые кондукторы.
Специализированные безналадочные приспособления (СБП) используют для базирования и закрепления заготовок близких по конструктивным признакам и требующих одинаковой обработки. К таким приспособлениям принадлежат приспособления для обработки ступенчатых валиков втулок фланцев дисков корпусных деталей и др.
Специализированные наладочные приспособления (СНП) применяют для базирования и закрепления заготовок близких по конструктивно-технологическим признакам и требующих для их обработки выполнения однотипных операций и специальных наладок.
Универсально-сборные приспособления (У СП) применяют для базирования и закрепления конкретной детали. Из комплекта УСП собирают специальное приспособление которое затем разбирают а элементы УСП многократно используют для сборки других приспособлений.
Специальные приспособления (СП) используют для выполнения определенной операции и при обработке конкретной детали. Такие приспособления называются одноцелевыми. Их применяют в крупносерийном и массовом производстве.
По функциональному назначению элементы приспособлений делят на установочные зажимные силовые приводы элементы для направления режущего инструмента вспомогательные механизмы а также вспомогательные и крепежные детали (рукоятки сухари шпонки). Все эти элементы соединяются корпусными деталями.
По степени механизации и автоматизации приспособления подразделяют на ручные механизированные полуавтоматические и автоматические.
Обрабатываемую заготовку шток устанавливают на постоянные опоры (призмы) фиксация заготовки производится при помощи прихвата.
Рисунок 8 - Приспособление для фрезерования
- цилиндр2- шток3- прихватом 4- деталь.
Сжатый воздух цилиндра 1 через поршни передает усилие на шток 2 соединенный с прихватом 3 который закрепляет обрабатываемую деталь 4.
Составляющая Rнаправлена к опорам а составляющая R стремится сдвинуть шток в боковом направлении.
где R-сила резания и ее составляющиеН;
и - коэффициенты трения в местах контакта штока с опорами и зажимом механизма; и жесткости зажимного механизма и опор соответственно:
K- коэффициента надежности закрепления детали
где К0 – гарантированный коэффициент запаса;
К1 – коэффициент учитывающий состояние поверхности заготовки;
К2 - коэффициент учитывающий увеличения сил резания от прогрессирующего затупления инструмента;
К3 – коэффициент учитывающий изменение сил резания при обработке прерывистых поверхностей;
К4 – коэффициент учитывающий непостоянство сил при зацеплении;
К5 – коэффициент учитывающий непостоянство сил зажимных устройств с ручным приводом;
К6 - коэффициент учитывающий неопределенность мест контакта плоских базовых поверхностей 3ГЗГ - заготовка с плоскими поверхностями Ц.Э. Ц.Э. – центрирующий элемент
т.к. K25 принимаем K=25.
= ((25·1000+016·2000)·03- (016·2000)·06) (016+016)= 20 кН
-сила закрепления -сила среза -плечо -плечо .
где –допускаемое напряжение на срез (=130 MPа для Ст5)
-диаметр пальца принимаем =15 мм
где= 280 допускаемое напряжение на смятиеh-толщина соединяемых деталей.
В данной курсовой работе был разработан технологический процесс восстановления полуоси погрузчика ТО-49. Проведена дефектация детали. Также был произведён расчёт режима обработки и норм времени разработано приспособление для фрезерования. Основные данные расчёта: скорость наплавки v=12 ммин
частота вращения детали n=6.05 ммин
норма времени t=27 мин
скорость резания v=2356 ммин
сила резания P=2759.2 Н
мощность резания N=10.6 кв
вспомогательное время t=18 мин
Список использованных источников
Есенберлин Р.Е. Восстановление деталей сваркой наплавкой и пайкой. М.:Транспорт 1994. 256 с.
Каракозов Э.С. Мустафаев Р.И. Справочник молодого электросварщика. М.: Высшая школа 1992. 304 с.
Микотин В.Я. Технология ремонта машин и оборудования. М.: Колос 2000. 368 с. 6.Малдык Н.В. Зелкин А.С. Восстановление деталей машин: Справочник. – М.: Машиностроение 1989 – 420 с.
Основы технологии производства и ремонта машин: Метод. указания.Сост. А.Д. Полканов ВоГТУ: - Вологда 1999 г.
Справочник технолога-машиностроителя. Т. 1Под редакцией А.Г. Косиловой и Р.К. Мещерякова. – М.: Машиностроение 1972 г.
Справочник технолога-машиностроителя. Т. 2Под редакцией А.Н. Малого. – М.: Машиностроение 1972 г.
Техпроцесс.DOC
Министерство Образования Республики Беларусь
Белорусский национальный технический университет
Консультант М.М. Гарост
ТЕХНОЛОГИЧЕСКОГО ПРОЦЕССА ВОССТАНОВЛЕНИЯ
ПОЛУОСИ ЭКСКАВАТОРА-ПОГРУЗЧИКА ТО-49
ГОСТ 3.118-82 форма 1
Код наименование операции
Обозначение документации
Код наименование оборудования
Машина моечная ОМ-15429 «Лабомид -312» ТУ38-30728-71 ветошь 25 ГОСТ 5354 перчатки ГОСТ 124015-82 1-2
Стол дефектовщика станок токарно-винторезный 1К62штангенциркуль ШЦ-1-150-01 ГОСТ 166-80 индикатор часового типа линейка
Установка для наплавки УД 609.06 станок токарно-винторезный 1К62 центр неподвижный центр вращающийся щетка металлическая
штангенциркуль ШЦ-1-150-01 ГОСТ 166-80 линейка стальная 500 мм
Наименование детали сборочной единицы или материала
Станок токарно-винторезный 1К62 центр неподвижный центр вращающийся резец 2140-0001 ВК4 ГОСТ 18882-73
Станок токарно-винторезный 1К62 центр неподвижный центр вращающийся резец 2140-0001 ВК4 ГОСТ 18882-73
Станок фрезерный 6Т82 приспособление фреза дисковая 2254-1456 2 ГОСТ 2679-93 штангенциркуль ШЦ-1-150-01 ГОСТ 166-80 линейка
Печь отпускная сопротивления СШ3-667 и3 клещи пресс Роквелла.
Станок круглошлифовальный 3Б161 центр неподвижный центр вращающийся круг шлифовальный ПП 55х20х30 24А 10-П С2 7 КПГ ГОСТ
24-83 зернистость 50-6 ШЦ-1-150-01 ГОСТ 166-89 линейка стальная 500 мм.
Опер.карта - Наплавка.doc
Обозначение документации
Код наименование оборудования
Наименование детали сборочной единицы или материала
Пl I U Vнап S ЧП dэ hэ lэ
Устанока УД 609.06 токарный станок 1К62
Нп-30ХГСА ГОСТ 2424-86
Установить деталь и закрепить.
Наплавить поверхность выдерживая размеры
Снять полуось деталь и контролировать наплавленные поверхности
Щетка металлическая штангенциркуль ШЦ-1-150-01 ГОСТ 166-89.
0А 28В 19 мин 40мм 20 мм 102 мм 63 мм
ОПЕРАЦИОННАЯ КАРТА НАПЛАВКИ
“Строительные и дорожные машины”
Наплавить поверхности выдерживая размеры 1 и 2.
СОДЕРЖАНИЕ.doc
Анализ литературных и патентных источников ..7
Проектирование технологического процесса восстановления полуоси 23
Выбор способа восстановления полуоси 24
Выбор оборудоваеия для восстановления полуоси .26
Расчёт режимов обработки и норм времени 27
Конструкторская разработка приспособления для фрезерования .. 28
Список использованных источников
Пояснительная записка
Рекомендуемые чертежи
- 25.10.2022
- 22.07.2023
- 25.10.2022
- 04.06.2024
- 20.03.2015
- 24.01.2020