Разработка технологических процессов изготовления и ремонта вала-шестерни




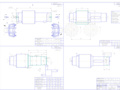
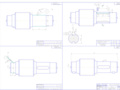
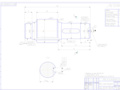
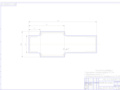
- Добавлен: 25.10.2022
- Размер: 922 KB
- Закачек: 0
Описание
Состав проекта
![]() |
![]() |
![]() ![]() |
![]() ![]() |
![]() ![]() ![]() ![]() |
![]() ![]() |
![]() ![]() ![]() ![]() |
![]() ![]() ![]() ![]() |
![]() ![]() |
![]() ![]() |
![]() ![]() |
![]() ![]() |
![]() ![]() |
![]() ![]() ![]() ![]() |
![]() |
![]() ![]() ![]() |
![]() ![]() ![]() |
Дополнительная информация
Обработка.dwg

Ремонт.dwg

вал шестерня.dwg

вал-шестерня заготовка.dwg

Рекомендуемые чертежи
- 24.01.2023
- 10.06.2015
- 24.01.2023
- 24.01.2023
- 04.02.2022
Свободное скачивание на сегодня
Другие проекты
- 29.07.2014