Проектирование цеха по производству экспанированного комбикорма




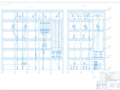
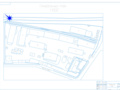
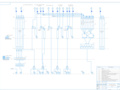

- Добавлен: 25.10.2022
- Размер: 6 MB
- Закачек: 0
Описание
Состав проекта
![]() |
![]() |
![]() ![]() |
![]() ![]() ![]() ![]() |
![]() ![]() |
![]() ![]() ![]() ![]() |
![]() ![]() |
![]() ![]() |
![]() ![]() |
![]() ![]() ![]() ![]() |
![]() ![]() ![]() ![]() |
![]() ![]() |
![]() ![]() |
![]() ![]() |
![]() ![]() ![]() ![]() |
![]() ![]() ![]() ![]() |
![]() ![]() ![]() |
![]() ![]() ![]() ![]() |
![]() ![]() |
![]() ![]() |
![]() ![]() |
![]() ![]() |
![]() ![]() |
![]() ![]() |
![]() |
![]() ![]() |
Дополнительная информация
Технологическая линия экспандирования комбикорма.dwg

экспандирования комбикорма
Охладитель ленточный
Измельчитель валковый
Технологическая линия экспандирования и гранулирования комбикорма.dwg

экспандирования и гранулирования
Охладитель ленточный
Измельчитель валковый
Разрезы производственного здания.dwg

Могококомпонентный дозатор
План 5 этажа.dwg

План 1 этажа.dwg

Технологическая схема комбикормового цеха.dwg

Наддробильные бункеры
Могококомпонентный весовой дозатор SW
Смеситель периодического действия
Наддозаторные бункеры
Могококомпонентный весовой дозатор ДК
Бункеры для рассыпного комбикорма
схема комбикормового
Многокомпонентный весовой дозатор SW
Линия подготовки зернового сырья
Линия мучнистого сырья
ПЗ Цех комбикормов.docx
Ключевые слова: ТЕХНИКО-ЭКОНОМИЧЕСКОЕ ОБОСНОВАНИЕ КОМБИКОРМ ЭКСПАНДИРОВАНИЕ ТЕХНОЛОГИЧЕСКАЯ ЛИНИЯ ГЕНЕРАЛЬНЫЙ ПЛАН.
В данной выпускной квалификационной работе разработан цех по производству экспанированного комбикорма.
Дана характеристика сырья и готовой продукции проведен анализ технологического процесса экспандирования комбикормов и разработка технологической схемы осуществлен расчет и подбор оборудования линий комбикормового цеха. Разработан генеральный план предприятия. Приведена структурная схема автоматизированной системы управления технологическим процессом линии гранулирования. Рассмотрены вопросы охраны труда. Рассчитаны капитальные затраты в сооружение цеха подсчитаны годовые эксплуатационные расходы и определен срок окупаемости который согласно расчету составил приблизительно 4 года.
Результаты работы могут быть использованы при проектировании цехов по производству экспанированного комбикорма и в учебном процессе.
ТЕХНИКО-ЭКОНОМИЧЕСКОЕ ОБОСНОВАНИЕ5
ТЕХНОЛОГИЧЕСКАЯ ЧАСТЬ11
1 Характеристика сырья и готовой продукции11
2 Анализ технологического процесса экспандирования комбикормов и разработка технологической схемы17
3 Расчет и подбор оборудования линий комбикормового цеха20
КОМПОНОВКА ОБОРУДОВАНИЯ В ПРОИЗВОДСТВЕННОМ ЗДАНИИ43
1 Проектирование коммуникаций43
ГЕНЕРАЛЬНЫЙ ПЛАН ПРЕДПРИЯТИЯ49
ТЕХНОХИМИЧЕСКИЙ КОНТРОЛЬ ПРЕДПРИЯТИЯ51
МЕРОПРИЯТИЯ ПО ОХРАНЕ ТРУДА54
1 Опасные и вредные факторы производства54
2 Условия труда на производственных участках55
3 Характеристика и нормы выдачи средств индивидуальной защиты58
ЭКОНОМИЧЕСКИЙ РАЗДЕЛ61
1 Капитальные вложения61
2 Эксплуатационные затраты62
3 Определение срока окупаемости63
СПИСОК ИСПОЛЬЗОВАННЫХ ЛИТЕРАТУРНЫХ ИСТОЧНИКОВ67
Производство комбикормов остается основным звеном в развитии агропромышленного комплекса страны. Обеспеченность комбикормами во многом определяет уровень развития и экономику животноводства особенно крупных животноводческих хозяйств и птицефабрик так как в структуре себестоимости продукции животноводства стоимость кормов составляет 65-75%.
Основное назначение предприятий кормопроизводства - приготовлять такие смеси чтобы обеспечить полностью животных питательными веществами гарантирующими их сохранность рост развитие и продуктивность.
Роль комбикормов возрастала по мере развития животноводческой отрасли. Так с созданием ферм крупных комплексов и птицефабрик стало невозможным накормить животных не используя комбикорма выработанные промышленным способом в цехах на специализированных заводах и т.п. Обеспечение всех требований животноводов также невозможно без высоких показателей качества кормов. Здесь и полное выполнение научно-обоснованных норм питательности обеспечение санитарной чистоты и безвредности корма кормление животных и птицы любого возраста и направленности от рождения до забоя. Поэтому для выработки комбикормов строятся отдельные предприятия создаются специальные машины обеспечивающие очистку сырья от различных примесей (сорных вредных металломагнитных и др.) измельчение сырья таким образом чтобы гранулометрический состав учитывал возможность полного потребления и переваривания компонентов их правильное соотношение и сочетание обоснованное научными исследованиями высокую однородность смеси гарантирующую требуемый химический состав для каждого животного. Для повышения питательной ценности ряд предприятий осуществляет дополнительную обработку: снижение содержания пленки гидротермическую обработку ввод вкусовых добавок в жидком виде санитарную обработку и др.
ТЕХНИКО-ЭКОНОМИЧЕСКОЕ ОБОСНОВАНИЕ
Работа связанная с установлением технической возможности и экономической целесообразности строительства предприятия в намеченном пункте называется технико-экономическим обоснованием строительства (ТЭО).
В ТЭО должны быть приведены:
- характеристика назначение предприятия в обеспечении снабжения продукцией потребителя краткая экономическая характеристика области и намеченного пункта строительства (развитие промышленности сельского хозяйства главным образом производство зерна и развитие животноводства);
- обоснование мощности номенклатуры продукции и пункта строительства.
Проектируемый цех по изготовлению экспандированных кормов предполагается создать для обеспечения комбикормами животноводческих подразделений.
Экономическое положение на рынке приведено на рисунке 1.1.
Динамика производства молока приведена на рисунке 1.2.
Динамика роста поголовья свиней и птицы приведена на рисунке 1.3.
Рисунок 1.1 - Экономическое положение на рынке
Рисунок 1.2 - Динамика производства молока
Рисунок 1.3 - Динамика роста поголовья свиней и птицы
Динамика роста поголовья КРС и производства комбикорма приведено на рисунке 4.
Рисунок 1.4 - Динамика роста поголовья КРС и производства комбикорма
- в результате модернизации 4-х ферм выпуск свинины планируется увеличить на 75%;
- ввод в эксплуатацию еще 2-х ферм на базе существующих позволит увеличить поголовье свиней на 78 тыс. голов в год;
- ввод в эксплуатацию новой птицефабрики позволит увеличить производство мяса птицы на 30 тыс. тонн в год;
- за 2011 – 2015 гг. поголовье КРС увеличилось на 151%. До 2020 г. поголовье КРС планируется увеличить на 15%;
- за 2011 – 2015 гг. вырос объем производства комбикорма на 38% муки на 10%;
- до 2020 г. планируется увеличить объем производства комбикорма на 41%.
Финансовые показатели хозяйственной деятельности общества приведены в таблице 1.1.
Таблица 1.1 – Финансовые показатели хозяйственной деятельности общества
Стоимость чистых активов млн. руб.
Выручка от реализации продукции работ услуг млн. руб.
Прибыль всего млн. руб.
Прибыль от реализации продукции работ услуг млн. руб.
Прибыль чистая млн. руб.
Рентабельность реализованной продукции работ услуг млн. руб.
Дебиторская задолженность млн. руб.
Кредиторская задолженность млн. руб.
Средняя заработная плата тыс. руб.
В сложившихся условиях - производственных мощностей по производству комбикормов не хватает поэтому целесообразно строительство нового цеха по производству экспандированных комбикормов мощностью 200 тсут при объеме финансирования за 2017-2019 гг. – 6462 млн. руб. при этом предполагаемый эконмический эффект от реализации проекта в 2019 году должен составить 79 тыс. долл. США на одного работающего.
ТЕХНОЛОГИЧЕСКАЯ ЧАСТЬ
1 Характеристика сырья и готовой продукции
В состав комбикормов входят следующие виды зернового сырья: пшеница ячмень тритикале кукуруза овес люпин. На производстве используют отруби как пшеничные так и ржаные. Шроты соевый и подсолнечный. Используют жмых рапсовый и масло рапсовое собственного производства кормовые зерноотходы с мукомольного завода свекловичная патока и жом. В рецептуре для молодняка животных используют заменители цельного молока. В рецептуру также входит минеральное сырье незаменимые аминокислоты премиксы.
Кукуруза - ценный зерновой корм для КРС. Кукуруза богата углеводами но бедна белком 8 - 10%. В зерне кукурузы содержатся витамины группы Ві Е РР. Из минеральных веществ преобладают фосфор и кальций а также натрий хлор и железо. Внешний вид зерна кукурузы представлен на рисунке 2.1.
Рисунок 2.1 - Кормовая кукуруза
Овес голозерный - для КРС и молодняка ценнейшая зерновая культура. Питательность голозёрного овса оказалась выше чем у овса плёнчатого по энергии на 249-268%. Показатель накопления азотистых веществ в голозёрных формах опережает фору плёнчатую по сырому протеину на 24.6-403% и переваримому протеину на 827-104%.
Это означает что голозёрный овёс введённый в рацион или комбикорм поставляет в организм в 2 раза больше переваримого протеина чем овёс плёнчатый при той же дозе введения. Кроме того с ростом накопления азотистых веществ в бесплёнчатом овсе увеличивается концентрация основных незаменимых аминокислот - лизина и метионина что указывает на существенное повышение биологической полноценности белковых веществ этой культуры.
Характерно что овёс освободившийся от плёнки естественным путём накапливает в своём составе в три с лишним раза меньше сырой клетчатки чем овёс стандартный. В бесплёнчатом овсе существенно выше концентрация сырого жира. Показатели минерального состава овсов разных форм различаются слабо. Внешний вид овса голозерного и овса пленчатого представлены на рисунке 2.2.
Рисунок 2.2 – Овес: а - овес голозерный; б - овес пленчатый
Тритикале - интерес как к кормовой культуре вызван тем что по сравнению с другими хлебными злаками он содержит больше белка с лучшим аминокислотным составом. В тритикале в среднем накапливается белка на 15% больше чем в пшенице и на 4% больше чем во ржи. Содержание белка в них составляет 18 - 19% он отличается высокой усвояемостью.
Зерно тритикале характеризуется более высоким содержанием незаменимых аминокислот чем зерно кукурузы и сорго а по содержанию лизина и триптофана тритикале значительно превосходит эти культуры. В отрубях тритикале лизина марганца железа и меди содержится больше чем в муке и цельном зерне.
Жмых рапсовый. В Беларуси рапсовый жмых все чаще используют в качестве альтернативы импортным белковым ингредиентам в том числе и в молочном скотоводстве. Он обладает целым рядом достоинств - от низкой стоимости до высокой питательной ценности. Однако для получения максимального эффекта вводить рапсовый жмых в рацион КРС нужно не бездумно а опираясь на научный опыт и используя современные кормовые добавки.
В последние годы производство рапса в Беларуси выросло многократно. Главным продуктом переработки его семян является высококачественное масло используемое в различных целях. Из каждой тонны рапса получается около 400 кг масла. Оставшийся после процесса экстракции рапсовый жмых идет на корм сельскохозяйственным животным и птице. Это позволяет резко снизить стоимость их рациона поскольку в данном случае уменьшаются затраты на импортируемые белковые ингредиенты. Поэтому многие хозяйства республики уже установили прессы для получения рапсового масла и жмыха. Подсолнечный и соевый шрот импортируемый в нашу страну не в состоянии конкурировать по цене с рапсовым жмыхом: последний значительно дешевле. Так что добавление в рацион животных и птицы продуктов переработки рапса в конечном итоге ведет к увеличению экономической эффективности хозяйства. Питательная ценность жмыха довольно высока. Аминокислотный состав рапса значительно богаче в сравнении с подсолнечником и даже соей. Так рапсовый жмых является отличным источником метионина что особенно важно при использовании в рационах кукурузного силоса. Внешний вид рапсового жмыха представлен на рисунке 2.3.
Рисунок 2.3 - Жмых рапсовый
Жмых соевый - один из наиболее ценных растительных концентратов. Служит источником лизина. Содержание сырого протеина составляет 44-46 %.
Соевый жмых - продукт полученный в результате переработки соевых бобов.
Различают полножирный и полуобезжиренный (остаточная масляничность 6-14 %) жмых:
- полножирный жмых получают в результате переработки соевых бобов без отделения масла;
- полуобезжиреный жмых - результат отжима на механическом прессе полножирного жмыха.
Используется для приготовления полноценных комбикормов кормосмесей как высококачественный белковый ингредиент при откормке сх животных и птицы может использоваться и как самостоятельный корм.
Соевый жмых привлек к себе внимание благодаря высокому содержанию белка в семенах культурной сои. Причем белок содержащийся в семенах обладает высокой биологической ценностью и усваиваемостью что делает его незаменимым для животноводов. Кроме высококачественного белка в соевом жмыхе содержатся микроэлементы - кальций железо фосфор марганец и цинк. Внешний вид соевого жмыха представлен на рисунке 2.4.
Рисунок 2.4 - Жмых соевый
Соль - является основным дополнительным источником обеспечения потребности сельскохозяйственных животных и птицы в важных макроэлементах - натрии и хлоре. Кроме того соль придает комбикормам определенный вкус вследствие чего их более охотно поедают животные.
Мел кормовой - является кальциевой подкормкой для сельскохозяйственных животных и птицы. Содержит 34% кальция 32% - фосфора 11% - марганца и другие элементы.
Характеристика готовой продукции.
Расчет рецептов комбикормов проводят руководствуясь «Методическими указаниями по расчету рецептуры качества и цен комбикормовой продукции с использованием компьютерного обеспечения» утвержденного Департаментом по хлебопродуктам 20.05.2003 г. № 40 и «Классификатором сырья и продукции комбикормового производства Республики Беларусь» утв. Минсельхозпродом Республики Беларусь 28.11.2003 г.
Ассортимент комбикормов который будет выпускаться на предприятии представлен в таблицах 2.1-2.3.
Таблица 2.1 - Рецепт полнорационного рассыпного комбикорма для молодняка КРС 116 - 400 дней (ГОСТ 9268 - 90)
жмых рапсовый II сорт
свекловичная патока (меласса)
соль поваренная пищевая экстра
мел мелкогранулированный высший
премикс ПКР - 2 телят 75 - 400 дней
Таблица 2.2 - Рецепт полнорационного гранулированного комбикорма для поросят 61-104 дней (СТБ 2111 - 2010)
шрот соевый СП 44 - 46%
шрот подсолнечный СП 35 - 38%
заменитель сухого молока «ПОРК»
монохлоргидрат лизина 98%
фосфат дефторированный
премикс КС - 3 - 3 для поросят НА
Таблица 2.3 - Рецепт кормосмеси (крупка) для откорма свиней (ТУ ВУ 600024008.134-2008)
зерноотходы ПШ до 50
зерноотходы РЖ до 30
2 Анализ технологического процесса экспандирования комбикормов и разработка технологической схемы
Экспандирование - это интенсивная механическая и гидротермическая обработка рассыпного комбикорма отдельного компонента или смеси давлением паром и температурой. Она обеспечивает позитивное воздействие на комбикорм: превращение крахмала в легкоусвояемую животными форму улучшение переваримости клетчатки некоторую денатурацию белка и инактивацию антипитательных веществ санитарную обработку - обеззараживание. Установка экспандера в линию гранулирования приводит к улучшению качества гранул.
Экспандирование комбикорма может быть организовано на отдельной линии или включено в линию гранулирования комбикорма перед прессом-гранулятором.
Самостоятельная линия экспандирования комбикорма приведена на рисунке 2.5 и включает шнековый питатель смеситель экспандер с измельчителем (структуратором) ленточный охладитель просеиватель и измельчитель крупной фракции. В смеситель вводят жидкие добавки (жир мелассу растительное масло) воду и пар в экспандер - только пар. В смесителе и экспандере продукт подвергается механическому перемешиванию с жидкостями обработке паром и высокому давлению при выдавливании его через кольцевой зазор создаваемый коническим поршнем на выходе из экспандера. После экспандирования спрессованный продукт измельчается (структурируется) и измельченная крупка поступает на охлаждение и просеивание. Режимы обработки зависят от рецептуры комбикорма и составляют: увлажнение водой и паром до 17-18% температура нагрева - 105- 110°С давление в камере - до 20 МПа время обработки в экспандере составляет 5-6 сек.
Рисунок 2.5 - Технологическая линия экспандирования комбикорма: 1 - шнековый питатель; 2 - смеситель; 3 - экспандер; 4 - структуратор; 5 - охладитель ленточный; 6 - просеиватель; 7 - измельчитель валковый
Установку экспандера в линию гранулирования (рисунок 2.6) осуществляют перед прессом-гранулятором что приводит к снижению энергоемкости процесса гранулирования повышению его производительности и улучшению качества гранул.
При выработке комбикормов для поросят и свиней достаточно использовать только экспандер а для сельскохозяйственной птицы - только гранулирование.
Совместное использование экспандирования и гранулирования определяется рецептурой комбикорма и половозрастной группой животных и птицы.
Рисунок 2.6 - Технологическая линия экспандирования и гранулирования комбикорма: 1 - шнековый питатель; 2 - смеситель; 3 - экспандер; 4 - структуратор; 5 - пресс-гранулятор; 6 - охладитель ленточный; 7 - измельчитель валковый; 8 - просеиватель
3 Расчет и подбор оборудования линий комбикормового цеха
Для расчета оборудования технологической линии необходимо знать мощность завода количество сырья (таблица 4) направляемое на данную технологическую линию (в процентах от суточной производительности завода) коэффициент использования оборудования и время его работы.
Для расчета оборудования применяется унифицированная рецепиура представленная в таблице 2.4.
Таблица 2.4 – Унифицированная рецептура для расчета оборудования
Корма животного происхождения
Производительность оборудования q (тч) технологической линии определяется по формуле (2.1):
где Q – мощность цеха тсут; а - расчетное количество перерабатываемого сырья %; tл – время работы линии ч; k – коэффициент использования оборудования (для дозирования 09 для дробления 07 и для гранулирования 08; для остального оборудования 10).
Число оборудования находим по формуле (2.2):
где qi - производительность подбираемого оборудования на данной линии тч.
Фактическое использование пм.ф. (%) производительности принятой машины определяем по формуле (2.3):
Проведем расчет и подбор оборудования для комбикормового цеха мощностью 200 тсут.
Линия подготовки зернового сырья.
Производительность дозатора для зернового сырья определяют по формуле (2.1):
Потребное число оборудования рассчитывают по формуле (2.2):
Принимаем один многокомпонентный весовой дозатор фирмы Амандус Каль производительностью 6 тч. Максимальное количество дозирования каждого компонента 3000 кг.
Фактическое использование производительности дозатора определяют по формуле (3):
Производительность смесителя определяем по формуле (2.1):
Принимаем смеситель SMW фирмы Амандус Каль (Германия) производительностью 6 тч.
Производительность магнитного сепаратора определяют по формуле (2.1):
Принимаем один магнитный сепаратору 1-БМЗ (страна-производитель: Россия) производительностью 6 тч.
Фактическое использование производительности магнитного сепаратора определяют по формуле (2.3):
Производительность молотковой дробилки (тч) определяется по формуле (1):
Принимаем 1 молотковую дробилку ДММ производительностью 8 тч.
Фактическое использование производительности дробилки определяем по формуле (2.3):
Производительность просеивателя (тч) определяем по формуле (2.1)
Принимаем один вибро-просеиватель серии SFJZ (страна- производитель: Китай) производительностью 6 тч.
Фактическое использование производительности просеивателя определяют по формуле (2.3):
Линия подготовки мучнистого сырья.
Принимаем один просеиватель А1-ДСМ (страна-производитель: Россия) производительностью 1 тч.
Принимаем один магнитный сепаратор У1-БММ (страна- производитель: Россия) производительностью 10 тч.
Линия подготовки продуктов животного происхождения
Принимаем один вибро-просеиватель серии SFJZ (страна- производитель: Китай) производительностью 4 тч.
Принимаем один магнитный сепаратор У1-БММ (страна- производитель: Россия) производительностью 20 тч.
Производительность молотковой дробилки (тч) определяется по формуле (2.1):
Потребное число оборудования рассчитывают по формуле (2):
Принимаем 1 молотковую дробилку ДММ производительностью 2 тч.
Линия подготовки шротов и жмыхов
Принимаем один магнитный сепаратор У1-БМЗ (страна- производитель: Россия) производительностью 10 тч.
Производительность дробилки (тч) определяем по формуле (2.1):
Фактическое использование производительности дробилок определяем по формуле (2.3):
Линия подготовки соли и мела.
Принимаем 1 молотковую дробилку ДММ производительностью 1 тч.
Премиксы поступают уже подготовленные сразу на линию дозирования и смешивания.
Оборудование используемое в подготовительном отделении указано в таблице 2.5.
Таблица 2.5 - Спецификация оборудования линий подготовки
Производительность тч
Линия подготовки зернового сырья
Многокомпонентный весовой дозатор
Линия подготовки мучнистого сырья
Линии подготовки шротов и жмыхов
Линия подготовки соли и мела
Расчет вместимости бункеров.
Принимаем размеры бункеров 3x3 м. Высоты бункеров принимают равными трем этажам. Высоты этажей принимаем 48 м.
При прямоугольном сечении бункера строительный объем будет равен площади основания на высоту:
где Vс – строительный объем м; а b – размеры бункера в плане м (принимаем a= b = 3 м); h – высота бункера м (принимаем h = 144 м).
Объем занимаемый продуктом будет складываться их трех объемов V1 V2 V3.
где – толщина стенки бункера м (принимаем = 0004 м); h1 – высота верхней части бункера м.
где Rэ – эквивалентный радиус; - угол естественного откоса град.
Подставим полученные данные в формулу (4):
Следовательно по формуле (2.5):
Объем 2 представляет собой объем прямоугольного параллелепипеда с размерами основания a b и высотой h2.
где h2 – высота средней части бункера м.
Для нахождения высоты h2 найдем высоту нижней части бункера:
H3=R3tga= 1692 · tg30°=09 м.(2.9)
H2=h-(h1+h3)=144-(09+09)=126 м.(2.10)
Подставим полученные данные в формулу (2.6):
V2=(3-0004)2-126 = 1131 м3.
Объем V3 представляет собой объем усеченной пирамиды с размерами основания а1 b1 и высотой h3:
где S1 - площадь большего основания пирамиды м2 (принимаем S1 =9 м2); S2 - площадь меньшего основания пирамиды м2 (принимаем S2 = 04 м2).
Суммарный полезный объем:
V0 =V1 + V2 + V3 =269+1131+57=12149 м3. (2.12)
Отсюда коэффициент использования объема бункера:
Теоретически необходимое или расчетное значение вместимости бункера:
где Q - производительность мукомольного завода тсут (по заданию на проектирование Q = 200 тсут.); Сп - нагрузка на систему %; - продолжительность оперативного хранения продукта ч ( = 30 ч); γ - объемная масса продукта кгм2.
Нагрузка на систему меняется в зависимости от процента ввода компонента по таблице 2.4.
Произведем расчет бункеров для зернового сырья кормовых продуктов животного происхождения минерального сырья шротов и жмыхов мучнистого сырья.
Бункера для зерновых продуктов.
Подставим необходимые значения в формулу (2.14):
Расчет вместимости бункеров для зерна в отрасли принято рассчитывать по пшенице.
Строительную вместимость бункера рассчитываем с учетом коэффициента использования объема:
Ес=ЕрКИ =213094=201 м3.(2.15)
Число бункеров находим в зависимости от размеров единичного бункера и строительного объема:
Принимаем 2 бункера для зерновых культур. Принимаем 2 дополнительных (резервных) бункеров для зерновых культур.
Фактическая вместимость бункера рассчитывается по формуле:
Еф = nфγКИ10-3 =4129675009410-3 =3655 м3 (17)
Строительную вместимость бункера рассчитываем по формуле (2.15):
ЕС=ЕРКИ = 79094 = 75 м3.
Число бункеров находим по формуле (2.16):
Принимаем 1 бункер для отрубей.
Фактическая вместимость бункера рассчитывается по формуле (2.17):
Еф =1129632009410-3 =39 м3
ЕС=ЕРКИ= 50094 = 47 м3
Число бункеров находим по формуле (16):
Ес = Ер · Ки =36094 = 34м3.
Еф = 1129670009410-3 =85 м3.
Бункера для мясной и мясокостной муки (корма животного происхождения)
ЕС=ЕРКИ= 70094 = 66 м3.
Принимаем 1 бункер для мясной муки и 1 резервный бункер. Фактическая вместимость бункера рассчитывается по формуле (2.17):
Еф =2129650009410-3 =122 м3.
Бункер для премиксов.
Ес = ЕрКИ = 51094 = 48 м3.
Принимаем 1 бункер для премиксов.
Еф= 1·1296·490·094·10-3 = 60 м3.
Бункеры для соли и мела.
ЕС=ЕРКИ= 192·094 = 18 м3.
Принимаем 1 бункер для соли и 1 бункер для мела.
Еф =11296130009410-3 =158 м3.
Наддробильные бункеры.
Принимаем размеры бункеров 3x3 м. Высоты бункеров принимают равными одному этажу. Высоты этажей принимаем 48 м.
с =abh = 3348 = 432 м3.
где Vс - строительный объем м3; а b - размеры бункера в плане м (принимаем а = b = 3 м); h - высота бункера м (принимаем h = 48 м).
где - толщина стенки бункера м (принимаем = 0004 м); h1 - высота верхней части бункера м.
где Rэ - эквивалентный радиус; - угол естественного откоса град.
Rэ= 0564 · а = 0564 · 3 = 1692.
h1=1692 · tg30°=09 м.
Следовательно по формуле (2):
Объем V2 представляет собой объем прямоугольного параллелепипеда с размерами основания a b и высотой h2.
где h2 - высота средней части бункера м.
h3=R3tg=1692 · tg30°=09 м.
h2 =h- (hl +h3) = 48-(09+09) = 3 м.
Подставим полученные данные в формулу (6):
V2 =(3-0004)3 = 9 м3.
Объем V3 представляет собой объем усеченной пирамиды с размерами снования а1 b1 и высотой h3:
Vо=V1+V2+V3 =269 + 9 + 57 = 173918 м3.
Наддробилъный бункер для зерновых культур.
Ес = ЕрКИ = 57 · 042 = 24 м3.
Принимаем 1 бункер наддробильный для зернового сырья. Фактическая вместимость бункера рассчитывается по формуле (2.17):
Еф =1432750· 042· 10-3 =14 м3.
Наддробильный бункер для шрота.
Ес = Ер КИ=13042 = 6 м3
Принимаем 1 бункер наддробильный для шрота.
Еф =143250004210-3 =9 м3.
Наддробильный бункер для жмыха.
Ес =ЕРКИ =95042 = 4 м3.
Принимаем 1 бункер наддробильный для жмыха.
Еф =1432700·04210-3 =13 м3.
Наддробильные бункера для соли и мела.
Ес= ЕрКИ = 052 · 042 = 023 м3
Принимаем 1 бункер наддробильный для соли и один бункер для мела. Фактическая вместимость бункера рассчитывается по формуле (2.17):
Еф =1432130004210-3 =24 м3.
Наддозаторный бункер для зерновых культур.
ЕС=ЕРКИ= 57042 = 24 м3.
Принимаем 1 бункер наддозаторный для зернового сырья. Фактическая вместимость бункера рассчитывается по формуле (2.17):
Еф =143275004210-3 =14 м3.
Наддозаторный бункер для шрота.
Ес = ЕрКи =13042 = 6 м3.
Принимаем 1 бункер наддозаторный для шрота.
Наддозаторный бункер для жмыха.
Ес = ЕрКИ =95042 = 4 м3.
Принимаем 1 бункер наддозаторный для жмыха.
Еф =143270004210-3 = 13 м3.
Наддозаторные бункера для соли и мела.
Ес = ЕрКИ = 052 · 042 = 023 м3.
Принимаем 1 бункер наддозаторный для соли и один бункер для мела. Фактическая вместимость бункера рассчитывается по формуле (2.17):
Бункеры для комбикорма.
Ес = ЕрКИ = 417094 = 392 м3.
Принимаем 3 бункера для комбикорма.
Фактическая вместимость бункера рассчитывается по формуле (2.17):
Еф =3129660009410-3 =219 м3.
Расчет и подбор технологического оборудования линий дозирования и смешивания.
Производительность главной линии дозирования - смешивания рассчитывают по вместимости смесителя Есм (т) которую определяют по формуле (2.6):
где Q - производительность завода тсут; tл - время работы линии ч; К - коэффициент использования оборудования К=09; n - число циклов в час n = 10.
Производительность весового многокомпонентного дозатора для зернового мучнистого сырья кормов животного происхождения и шротов и жмыхов определяем по формуле (2.1):
Принимаем многокомпонентный весовой дозатор 16ДК-1000 производительностью 10 тч.
Фактическое использование производительности многокомпонентного весового дозатора определяем по формуле (2.3):
Производительность многокомпонентного весового дозатора для минерального сырья премиксов биологически активных веществ определяем по формуле (2.1):
Принимаем многокомпонентный весовой дозатор 6ДК-100 производительностью 07 тч.
Производительность смесителя определяем по формуле (1):
Принимаем смеситель SMW фирмы Амандус Каль (Германия) производительностью 10 тч.
Фактическое использование производительности смесителя определяем по формуле:
Расчет и подбор технологического оборудования технологическая линия экспандирования и гранулирования комбикорма.
Производительность шнекового питателя определяем по формуле (2.1):
Принимаем 2 смесителя смеситель SMW фирмы Амандус Каль (Германия) производительностью 6 тч.
Производительность экспандера определяем по формуле (2.1):
Принимаем 1 экспандер OE 23.2 фирмы Амандус Каль (Германия) схема и общий вид на рисунке 2.5 а технические характеристики которого приведены в таблице 2.6.
Рисунок 2.7 - Экспандер Amandus Kah 6 - схема; 1 - привод; 2 - впускное устройство для сырья; 3 - форсунки; 4 - распределительное устройство; 5 - кольцевой зазор; 6. - поршень- клапан; 7 - выпускное устройство; 8 - лопасти (сегменты); 9 - смесительная часть шнека.
Таблица 2.6 - Техническая характеристика экспандера OE 23.2
Производительность кгч
Amandus Kahl (Германия)
Производительность гранулятора определяем по формуле (2.1):
Принимаем 1 гранулятор Б6-ДГВ (Россия) технические характеристики которого приведены в таблице 2.7.
Таблица 2.7 - Техническая характеристика оборудования для гранулирования приведено в таблице
Частота вращения матрицы обмин
Расход пара кгч на 1 т
Суммарная установленная мощность кВт
Габаритные размеры мм: длина
КОМПОНОВКА ОБОРУДОВАНИЯ В ПРОИЗВОДСТВЕННОМ ЗДАНИИ
1 Проектирование коммуникаций
Компоновка оборудования на этажах комбикормового завода осуществляется комплексно. Следует одновременно компоновать технологическое транспортное оборудование а также контрольноизмерительные приборы и средства автоматики. Оборудование располагают с учетом технологической схемы.
Поэтажные схемы облегчают определение высоты этажей. Если дробилку смонтировать на площадке то нужны проходы под площадкой и на ней высотой 22 м. Общая высота этажа 48 м недостаточна так как общая сумма высот для проходов и строительная часть площадки и балок превышает 48 м. Для определения высоты некоторых этажей необходимо вычертить оборудование.
Компоновку оборудования в производственном корпусе выполняют в соответствии с разработанной поэтажной схемой технологического процесса.
Размещать оборудование подготовительных технологических линий следует с тех которые имеют большее число единиц оборудования большие габариты. Для воздуховодов и самотечных труб необходимо выделять вдоль оборудования на расстоянии прохода (1м) площади шириной около 05 м. Такие места удобно оставлять в зонах расположения норийных труб вдоль колонн стен. Контроль за работой оборудования требует хорошей естественной и искусственной освещенности рабочих мест. Детали самотечного транспорта трубы норий материалопроводы имеющие большую высоту при их расположении у окон будут снижать естественную освещенность помещения и оборудования расположенного в глубине производственного здания.
На этажах оборудование располагают оставляя свободные поперечные и продольные проходы связанные непосредственно с выходом на лестничные клетки или в смежные помещения а также между группами машин не менее 1 м. Проходы между отдельными машинами должны быть не менее 07 м. Машины которые для своего обслуживания не требуют подхода со всех сторон можно размещать группами.
Для горизонтального перемещения зерна и продуктов применяют винтовые цепные конвейеры и аэрожелоба. При расположении этого оборудования около стен величина продольного прохода должна быть не менее 07 м а проход между параллельно расположенным оборудованием должен быть не менее 08 м.
На комбикормовых заводах для внутрицехового перемещения сырья и готовой продукции используют самотечный механический пневмотранспорт и аэрозольтранспорт. Самотечные трубы от машины к машине проводят согласно схеме технологического процесса под
фактическим углом который должен быть больше минимального допустимого угла.
Каждую самотечную трубу проектируют в поперечном и продольном разрезах и проставляют ее номер угол наклона этаж проверки в ведомости движения продуктов. Трубы по которым перемещаются одинаковые продукты целесообразно объединить в одну самотечную трубу после их выхода из машины учитывая что при объединении самотечных труб угол между ними не может быть прямым или тупым. Присоединение одной трубы к другой следует выполнять по ходу движения продукта под острым углом не менее 30°.
Самотечные трубы проектируют возле оборудования вертикальными по высоте от пола не менее 2 м; проводят их возле продуктопроводов норийных труб и между ними при условии что не уменьшается при этом нормативный проход.
Не допускается проводить самотечные трубы через бытовые помещения лестничные клетки мастерские распределительные пункты бункера и т.п. Применяемые на комбикормовых заводах самотечные трубы изготавливают из черной и оцинкованной стали. Самотечные трубы из оцинкованной стали применяют для незерновых продуктов.
Компоновка оборудования в производственном здании приведена на разрезах здания (рисунок 3.1).
Рисунок 3.1 - Компоновка оборудования в производственном здании: 1 – нория; 2 – магнитный сепаратор; 3 – цепной конвейер; 4 – просеиватель; 5 – молотковая дробилка; 6 – смеситель периодического действия; 7 – многокомпонентный дозатор
Коммуникацию на комбикормовом комплексе выполняют с размещения технологического оборудования в соответствии с поэтажной схемой технологического процесса. Особенность комбикормовых заводов состоит в применении двух видов транспорта - пневматического и механического а также в наличии самостоятельных технологических линий работающих параллельно от приемки до линии дозирования - смешивания компонентов.
Применяемые на комбикормовых заводах самотечные трубы изготавливают из черной и оцинкованной стали. Самотечные трубы из оцинкованной стали применяют для незерновых продуктов.
Выполняя коммуникации на комбикормовых заводах обеспечивают фактический угол (град) наклона самотечной трубы который должен быть больше минимально допустимого для зернового сырья - 36; отрубей продуктов измельчения и комбикорма - 47; мучки кормовых продуктов пищевых производств минеральных кормов отходов - 50; относов аспирационных сетей - 55.
В состав курсового проекта входит разработка внутрицеховой коммуникации самотеков и составление ведомости движения продуктов с указанием углов наклона самотеков.
Ведомость движения продуктов приведена в таблице 3.1.
Таблица 3.1 - Ведомость движения продуктов
Перемещение продукта
с какого оборудования
на какое оборудование
Конвейер для отходов III кат.
Самотеки следует размещать вдоль стен или в створе колоны с соблюдением требований промышленной эстетики.
Для этой цели рекомендуется оставлять сплошные проемы у продольных стен и в середине здания шириной 200 мм с бортиком по краю самотека промежутки между самотечными трубами после их установки следует закрывать металлической стенкой.
ГЕНЕРАЛЬНЫЙ ПЛАН ПРЕДПРИЯТИЯ
Генеральный план предприятия приведен на рисунке 4.1.
Рисунок 4.1 – Генеральный план предприятия: 1 - склад готовой продукции №10; 2 - склад готовой продукции №9; 3 - склад готовой продукции №8; 4 - склад зерна №7; 5 - склад зерна №6; 6 - склад зерна №4; 7 - мех. амбар склада №4; 8 - склад зерна №5; 8а - мех. амбар склада №567; 9 - лабораторно-складской корпус; 9а - лаборатория; 9б - гаражи легковых автомобилей; 9в - холодильные камеры; 9г - материальный склад; 10 - склад зерна №11; 11 - крупопех; 12 - котельная; 13 - гаражи; 14 - весовая; 15 - навес зерна №1; 16 - визировочная лаборатория; 17 - бытовой корпус; 18 - пожарные резервуары; 19 - фасовочный цех; 20 - административный корпус; 21 - проходная; 22 - ангар для ремонта передвижного оборудования; 23 - магазин "нива"; 24 - неиспользуемое помещение; 25 - место хранения отходов производства; 26 - емкости для временного хранения зерна и других сыпучих продуктов по 120 т каждая; 26а - емкость №1; 26б - емкость №2; 26в - емкость №3; 27 - место выгрузки из жд транспорта; 28 - автостоянка; 29 - бункер для отходов; 30 - бункер для побочного продукта; 31 - проектируемый комбикормовый цех
ТЕХНОХИМИЧЕСКИЙ КОНТРОЛЬ ПРЕДПРИЯТИЯ
Технологический процесс гранулирования с точки зрения управления является одним из наиболее сложных процессов комбикормового производства. Выполнение операций обеспечивающих перемещение рассыпного комбикорма подачу пара ввод жидких компонентов прессование охлаждение измельчение просеивание и размещение гранул в складе готовой продукции требует переработки большою объема разнообразной информации и реализации многочисленных функций контроля и управления. При этом сложная зависимость между показателями качества исходною сырья параметрами ведения технологического процесса гранулирования и показателями качества гранул значительно усложняет разработку и изготовление средств автоматики.
Автоматизированная система управления технологическим процессом (АСУ ТП) линии гранулирования.
АСУ ТП предназначена для управления основными технологическими операциями с применением методов технической кибернетики и средств вычислительной техники с целью эффективного выполнения производственной программы.
АСУ ТП реализует информационные управляющие и вспомогательные функции.
К информационным функциям системы относятся: контроль уровня продукта в емкостях; контроль состояния технологических линий отдельных механизмов приводов и регулирующих органов; контроль значений режимных параметров пресс-грануляторов; контроль выполнения производственного задания; контроль действий оператора; контроль действий обслуживающего персонала по ликвидации последствий аварийных ситуаций; предоставление оператору информации о состоянии цеха гранулирования как технологического объекта управления.
Система выполняет следующие управляющие функции: управление подачей рассыпного комбикорма в надпрессовые бункеры; управление работой пресс-грануляторов в пусковом и стационарном режимах; управление подачей гранулированного комбикорма в склад готовой продукции; управление отпуском комбикорма на автомобильный и железнодорожный транспорты; ликвидацию аварийных ситуаций.
Состав вспомогательных функций АСУ ТП: учет и хранение информации о размещении рассыпного комбикорма производственном задании и состояния его выполнения количестве и размещении готовой продукции аварийных ситуациях простоях оборудования; предоставление оператору информации о текущем состоим пи оперативной памяти ЭВМ.
Структура АСУ ТП показана на рисунке 5.1.
Рисунок 5.1 - Структура АСУ ТП
Система предназначена для работы в следующих режимах (в соответствии с приоритетом): автоматизированном с непосредственным цифровым упражнением; ручном дистанционном с групповым управлением механизмами; ручном на месте с индивидуальным управлением механизмами.
По функциональному назначению система подразделяется на: технические средства централизованного контроля и управления; промежуточные технические средства дополняющие устройство связи с объектом; дополнительные первичные технические средства; специализированные периферийные технические средства; кабельные коммуникации силовое и вспомогательное оборудование.
Основной режим работы системы - автоматизированный. Процессы обработки информации принятия решения и выдачи управляющих воздействий осуществляются автоматически с помощью машины централизованного контроля.
МЕРОПРИЯТИЯ ПО ОХРАНЕ ТРУДА
1 Опасные и вредные факторы производства
Основными вредными факторами действующими на работников произвоственных цехов и складов готовой продукции являются:
аэрозоли преимущественно фиброгенного действия (измельченные частицы зерна взвешенная пыль и мука);
шум и вибрация производимые проиводчтвенным оборудованием;
параметры микроклимата в производственных и бытовых помещениях предприятия;
параметры световой среды;
напряженность трудового процесса;
тяжесть трудового процесса.
Рассмотрим ключевые опасные производственные факторы на исследуемом производстве. Следует однако отметить что опасные зоны как правило имеют вероятностный характер возникновения.
Зоны постоянно действующих опасных производственных факторов на Предприятии преимущественно находятся вблизи производственного оборудования. Отдельно отметим работу на высоте производимую при обслуживании элеваторов.
К опасным факторам производства на Предприятии относятся:
падение материалов и конструкций;
движущиеся машины (автотранспорт с сырьем и готовой продукцией и автопогрузчики) и механизмы (нории конвейеры);
кромки и острые углы;
зоны потенциально опасных производственных факторов:
площади вблизи перемещающихся грузов а также высоких штабелей подукции;
зоны перемещения машин и иного оборудования.
Итак для ряда негативных факторов в том числе и актуальных для рассматриваемого предприятия деление производственных факторов на опасные и вредные по большей части условно так как производственных факторов определяется характером их проявления.
В результате анализа представленных выше особенностей работы производственных цехов и склада предприятия Предприятии можно просуммировать опасные и вредные производственные факторы действующие на сотрудников склада.
2 Условия труда на производственных участках
Погрузо-разгрузочные работы а также внутризаводские перевозки различных грузов - важные факторами аварийности что объясняется тремя их основными характеристиками:
- большие объемы кинетической и потенциальной энергии при транспортировке и погрузочно–разгрузочных работах способны причинять телесные повреждения и материальный ущерб.
- численность работников проводящих транспортные и погрузо-разгрузочные работы все еще достаточно велика что повышает уровень риска при выполнении указанных работ.
- при необходимости выполнения нескольких производственных операций одновременно остро чувствуется необходимость точной и своевременной связи и информации поэтому недостаточная коммуникация а также большое число ошибок и упущений создают опасные ситуации на производстве [16].
Основными причинами травматизма сотрудников производства всех пропрофессий работающих на складе предприятия в частности грузчиков кладовщика заведующего складом могут явиться неправильные приемы работ неисправность инструмента приспособлений и оборудования отсутствие технического надзора за наиболее опасными видами работ загрязнение и загромождение рабочих мест проходов и территории отсутствие или несоответствие защитных средств и ограждений нарушения трудовой дисциплины.
Условия труда при погрузочно-разгрузочных работах в складских и производственных помещениях предприятия Предприятии можно отнести к умеренно опасным.
Опасным фактором является электрический ток. Так при нарушении изоляции электрооборудования при касании возможно прохождение электрического тока через тело человека вызывающее ожоги сокращение мышц нарушающее работу сердца и кровообращение поражающее нервные центры управления работой отдельных органов.
На предприятии предприняты меры по повышению электробезопасности однако поражение электрическим током сотрудников производства предприятия возможно при повреждении электроприборов или электроизоляции при проведении погрузочно-разгрузочных работ.
Наибольшую опасность электротравматизм представляет для сотрудников производства непосредственно задействованных в погрузочно-разгрузочных работах (грузчики кладовщик).
Основным вредным фактором воздействующим на здоровье работников предприятия Предприятии является запыленность помещения склада мелкодисперсной пылью. Очень часто запыленность воздуха при недостаточном качестве уборки помещений их запыленность превышает нормативное значение в два и более раз.
Причины этого заключаются в несовершенстве технологического оборудования и зданий складов низком уровне автоматизации процессов недостаточной уборке рабочих мест и обеспыливания воздуха. Диапазон воздействия мучной пыли (в зависимости от степени ее дисперсности времени водействия концентрации и т.п.) достаточно широк: это и аллергическое фиброгенное и токсическое действие провокация головных болей дерматитов кровотечений из носа горла заболевания печени легких онкологических патологий [35 47].
Пыль раздражает кожу и слизистую оболочку. В зависимости от того попадает ли она на открытые участки кожи или вдыхается цемент по-разному воздействует на здоровье человека. При попадании в бронхи и далее при длительном воздействии мучная пыль вызывает необратимые изменения легочной ткани чтоприводит к необратимым функциональным изменениям легких. Исследования и практический опыт и наблюдения указывают на большое количество аллергических реакций и воспалительных процессов (наиболее часто - в верхних дыхательных путях) после воздействия мучной пыли. Раздражающий эффект вызванный щелочной средой мучной пыли нередко сопровождается обструкционными изменениями дыхательных путей.
Необходимо упомянуть такой вредный производственный фактор как повышенние уровня шума и вибрации на рабочем месте.
Шум на складе предприятия Предприятии носит непостоянный и неравномерный характер обуслоленный проведением разгрузочно-погрузочных работ и шумом производимым автотранспортом и перемещающимися механизмами. Воздействие шума на работников склада предприятия Предприятии в целом незначительное.
Вибрация действует на желудочно-кишечный тракт центральную нервную систему вестибулярный аппарат вызывает онемение конечностей головокружение заболевание суставов. Источником вибрации могут быть двигатели автотранспортных средств.
Микроклимат в неотапливаемых складах зависит от погодных условий. Неблагоприятный микроклимат по указанной выше причине воздействует в равной степени на всех сотрудников работающих в складских.
Работники производства предприятия работающие в складских помещениях: кладовщики грузчики водители автотранспортных средств подвержены воздействию охлаждающего микроклимата (суммарная теплоотдача в окружающую среду Qсум превышает величину теплопродукции организма).
Уровень освещенности рабочих мест на предприятии Предприятии соответствут нормам искусственного освещения изложенным в СНиП однако в силу устаревания системы складе рекомендуется провести ее модернизацию. Правильное освещение рабочих мест на предприятии имеет большое значение для создания безопасных условий труда.
Неудовлетворительное освещение может служить причиной травматизма отрицательно влияет на зрение работающих понижает производительность труда. Недостаточное освещение действует отрицательно: движения человека замедленны наступает преждевременное утомление приводящее к снижению внимания что может явиться причиной несчастного случая. При рациональном освещении глаз не утомляясь длительное время сохраняет способность устойчивого зрения. Напротив чрезмерное световое раздражение также снижает чувствительность и работоспособность глаза вызывает ослепленность.
Недостаточная освещенность вследствие наличия на предприятии морально и физически устаревшей системы освещения является негативным фактором воздействующим в равной степени на всех сотрудников производства работающих в складских помещениях и на разгрузочно-погрузочных эстакадах. Несмотря на то что класс производимой работы не относится к высокоточным у сотрудников особенно в конце рабочей смены наблюдаются симптомы зрительного перенапряжения.
Важной рекоменданцией в данном случае является замена старой системы освещения на более эффективную.
3 Характеристика и нормы выдачи средств индивидуальной защиты
Средства индивидуальной защиты в отличие от СКЗ сугубо индивидуальны и разбиты на группы каждая из которых защищает отдельные части тела человека (руки ноги туловище голова) или отдельные его органы (зрение слух дыхание) от опасных и вредных производственных факторов.
Общие требования предъявляемые к средствам защиты:
а - средства должны создавать наиболее благоприятные для организма человека соотношения с окружающей средой и обеспечивать оптимальные условия для трудовой деятельности;
б - средства защиты не должны быть источником опасностей. Они должны отвечать требованиям технической эстетики и эргономики;
в - средства защиты должны обеспечивать высокую степень защитной эффективности они должны быть удобны в эксплуатации простые в обращении прочные надежные и долговечные.
Выбор средств защиты в каждом отдельном случае осуществляется с учетом требований безопасности для данного вида оборудования. Технологического процесса или для данного вида работ.
Средства защиты оцениваются по защитным физиолого-гигиеническим и эксплуатационным показателям.
Средства индивидуальной зашиты (СИЗ) применяются в тех случаях когда безопасность работ не может быть обеспечена конструкцией и размещением оборудования организацией производственных процессов архитектурно-планировочными решениями и средствами коллективной защиты. Их отличие от коллективных средств зашиты в том что они придаются не к производственному оборудованию а непосредственно работнику.
Если коллективные средства защиты встроены в оборудование таким образом что их нельзя не использовать вывести или заблокировать без остановки производственного процесса то применение индивидуальных средств защиты во многом зависит от дисциплины работника и его мотивации. Когда они затрудняют или задерживают выполнение производственного задания рабочий может отказаться от использования СИЗ чтобы не потерять в заработке. В связи с этим одним из главных требований к средствам индивидуальной защиты является их удобство. Что касается средств индивидуальной защиты для женщин то для них немаловажным показателем является эстетичность.
Средства индивидуальной зашиты должны иметь сертификаты соответствия а значит соответствовать характеру и условиям работы обеспечивать безопасность труда отвечать требованиям ГОСТов и технических условий. Каждая партия поступивших на предприятие средств индивидуальной защиты должна быть подвергнута проверке на соответствие заявленному ассортименту по моделям ростам расцветке родовому признаку назначению. На каждой упаковке (партии) СИЗ следует проверять наличие стандартной маркировки. Средства индивидуальной защиты не должны иметь механических повреждений и других дефектов. При осмотре спецодежды спецобуви рукавиц необходимо обращать внимание на соответствие и качество применяемых материалов и фурнитуры качество строчек швов соответствие размеров изделия и т.д.
Средства защиты органов дыхания средства защиты глаз и лица предохранительные пояса должны иметь паспорта и инструкции по эксплуатации. Маркировка фильтрующих элементов средств защиты органов дыхания должна соответствовать срокам гарантированного хранения. Необходимо проверить возможность замены очковых и смотровых стекол средств защиты глаз и лица без применения специального инструмента.
Следует проконтролировать надежность и прочность фиксации несущей ленты и подбородочного ремня по размерам у средств защиты головы (касок). При оценке качества предохранительных поясов необходимо проверить надежность работы пряжки и карабина (пояс должен расстегиваться и застегиваться без затруднений раскрытие карабина должно происходить усилием одной руки только после нажатия предохранительного устройства).
ЭКОНОМИЧЕСКИЙ РАЗДЕЛ
1 Капитальные вложения
Капитальные вложения складываются из затрат связанных с приобретением оборудования затрат на строительные монтажные и наладочные работы.
Капитальные вложения включают:
где Kc – стоимость оборудования руб.;
Kрм – расходные материалы руб.;
Kт – транспортные расходы руб.;
Kм – расходы на монтаж и пусконаладочные работы;
Kпр – расходы на проектные работы.
Результаты расчетов приведены в таблице 7.1.
Таблица 7.1 - Капитальные вложения в строительство комбикормового цеха
Наименование оборудования
Оптовая цена за ед. руб
Стоимость оборудования
Расходные материалы (10 %)
Транспортные расходы (3%)
Расходы на монтаж и пусконаладочные работы включая отчисления
Стоимость проектных работ
Непредвиденные расходы
Всего капитальных вложений
2 Эксплуатационные затраты
Эксплуатационные расходы представляют собой текущие затраты связанные с эксплуатацией оборудования и поддержанием его в рабочем состоянии. Эксплуатационные расходы включают следующие статьи затрат:
- вспомогательные материалы (Cм);
- расходы на техническое обслуживание и текущий ремонт (Cтop);
- прочие расходы (Спр).
Стоимость годового расхода вспомогательных материалов: См=30000 руб.год.
Расходы на техническое обслуживание.
Расходы на текущий ремонт и техническое обслуживание могут быть определены укрупнено как 1-2% от стоимости оборудования.
Прочие расходы принимаются в размере 3-5% от суммы эксплуатационных расходов.
Результаты расчетов эксплуатационных расходов сводятся в таблицу 7.2.
Таблица 7.2 - Эксплуатационные расходы
Наименование статей расходов
Проектируемый вариант
Вспомогательные материалы руб. год
Расходы на техническое обслуживание и текущий ремонт руб. год
Прочие расходы руб. год
Всего эксплуатационные расходы руб. год
3 Определение срока окупаемости
Основные показатели экономической эффективности можно определить следующим образом:
Общие капитальные вложения Коб.
Дополнительная балансовая прибыль за счет увеличения объемов продукции животноводства Пбал.
Дополнительная чистая прибыль Пчист.
Чистый приведенный доход NPV.
Срок окупаемости дополнительных капитальных вложений Ток.
Доходы определяются экономией от увеличения объёмов продукции животноводства.
Сумма балансовой прибыли определяется как разность суммы доходов до использования собственных комбикормов и после. Согласно анализу проведенному в первом разделе оценим Пбал=1550000000 руб.год.
Сумма чистой прибыли рассчитывается по формуле:
где НП – налог на прибыль (равен 20 % от балансовой прибыли); Авн.оф – годовая сумма амортизационных отчислений.
где ам – годовая норма амортизационных отчислений %;
nоф – количество основных фондов.
Чистый приведенный доход определяется так:
где R=01 – коэффициент дисконтирования;
Результаты расчета приведены в таблице 7.3 и на рисунке 7.1.
Таблица 7.3 - Результаты расчета срока окупаемости и дохода от модернизации
Чистый приведенный доход NPV руб.
Результаты расчета экономической эффективности сведены в таблицу 7.4.
Таблица 7.4 - Результаты расчета экономической эффективности
Наименование показателя
Общие капитальные вложения Коб
Дополнительная балансовая прибыль Пбал
Дополнительная чистая прибыль Пчист
Срок окупаемости дополнительных капитальных вложений Ток
Рисунок 7.1 – Определение срока окупаемости
В результате выполнения работы было проведено технико-экономическое обоснование которое показало что в сложившихся условиях - производственных мощностей по производству комбикормов не хватает поэтому целесообразно строительство нового цеха по производству экспандированных комбикормов мощностью 200 тсут при объеме финансирования за 2017-2019 гг. – 6462 млн. руб. при этом предполагаемый эконмический эффект от реализации проекта в 2019 году должен составить 79 тыс. долл. США на одного работающего.
В технологической части работы была дана характеристика сырья и готовой продукции проведен анализ технологического процесса экспандирования комбикормов и разработка технологической схемы также осуществлен расчет и подбор оборудования линий комбикормового цеха.
Разработан генеральный план предприятия.
Приведена структурная схема автоматизированной системы управления технологическим процессом линии гранулирования.
Рассмотрены вопросы охраны труда.
В экономической части рассчитаны капитальные затраты в сооружение цеха подсчитаны годовые эксплуатационные расходы и определен срок окупаемости который согласно расчету составил приблизительно 4 года.
СПИСОК ИСПОЛЬЗОВАННЫХ ЛИТЕРАТУРНЫХ ИСТОЧНИКОВ
Бутковский В.А. Технология мукомольного крупяного и комбикормового производства В.А. Бутковский Е.М. Мельников - М.: Агропромиздат 1989. – 250 с.
Горелова Е.И. Основы хранения зерна Е.И. Горелова - М.: Агропромиздат 1986. – 305 с.
Демин Г.С. Очистка зерна на хлебоприемных предприятиях Г.С. Демин Г.Т. Павловский - М.: Колос 1968. – 276 с.
Егоров Г.А. Технология муки крупы и комбикормов Г.А. Егоров Е.М. Мельников Б.М. Максимчук - Мн.: Колос 1984. – 200 с.
Егоров Г.А. Технология и оборудование мукомольно- крупяного и комбикормового производства Г.А. Егоров Е.М. Мельников В.Ф. Журавлев - М.: Колос 1979. – 230 с.
Машков Б.М. Справочник по качеству зерна и продуктов его переработки Б.М. Машков З.И. Хазина - Мн.: Колос 1980. – 187 с.
Трисвятский Л.А. Технология приемки обработки хранения зерна и продуктов его переработки Л.А. Трисвятский Б.Е. Мельник - Мн.: Колос 1983. – 204 с.
Генеральный план.dwg

Рекомендуемые чертежи
- 18.09.2019
- 24.01.2023