Проектирование технологического процесса изготовления детали корпус развертки




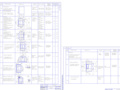
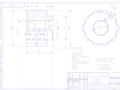
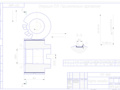
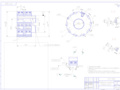
- Добавлен: 25.10.2022
- Размер: 3 MB
- Закачек: 0
Описание
Состав проекта
![]() |
![]() |
![]() ![]() ![]() ![]() |
![]() ![]() ![]() ![]() |
![]() |
![]() ![]() ![]() |
![]() ![]() ![]() |
![]() ![]() ![]() |
![]() ![]() ![]() |
![]() ![]() ![]() |
![]() ![]() ![]() |
![]() ![]() ![]() |
![]() ![]() ![]() ![]() |
![]() ![]() ![]() ![]() |
![]() ![]() ![]() ![]() |
![]() ![]() ![]() |
![]() |
![]() |
![]() ![]() ![]() |
![]() ![]() |
![]() ![]() |
![]() ![]() ![]() |
![]() ![]() |
![]() ![]() |
![]() ![]() |
![]() ![]() |
![]() ![]() |
![]() ![]() ![]() |
![]() ![]() ![]() |
![]() ![]() ![]() |
![]() ![]() ![]() |
![]() ![]() ![]() |
![]() ![]() ![]() |
![]() ![]() ![]() |
![]() ![]() ![]() |
![]() ![]() ![]() |
![]() ![]() ![]() ![]() |
![]() |
![]() ![]() ![]() ![]() |
![]() ![]() ![]() ![]() |
![]() |
![]() ![]() ![]() ![]() |
![]() ![]() ![]() ![]() |
![]() |
![]() |
![]() |
![]() |
![]() |
![]() |
![]() |
![]() |
![]() |
![]() |
![]() |
![]() |
![]() |
![]() |
![]() |
![]() |
![]() |
![]() |
![]() |
![]() |
![]() ![]() ![]() |
Дополнительная информация
Корпус.frw

Чертеж развертки.cdw

Обратная конусность цилиндрической части развертки
Развертка должна быть острозаточена
выкрошенные места на режущих кромках не допускаются.
Эскиз030.frw

Эскиз020.frw

Эскиз035.frw

Эскиз 005.frw

Эскиз040.frw

Эскиз025.frw

Эскиз050.frw

Эскиз015.frw

Эскиз.frw

карта наладки.cdw

НАЛАДКА СВ..BAK.CDW

Чертеж развертки.dwg
Обратная конусность цилиндрической части развертки
Развертка должна быть острозаточена
выкрошенные места на режущих кромках не допускаются.
НАЛАДКА СВ..BAK.dwg
Вертикально сверлильный 2А135
корпус развертки.dwg
Плотность материала
Масса M = 4407.494288 г
Площадь S = 75311.041694 мм2
Объем V = 563618.195334 мм3
Сталь 40 ГОСТ 1050-88
технологический процесс.dwg
отрезки с одной стороны
Сверлить сквозное отв.
Развернуть конусное
Горизонтально-расточная
Расточить внутреннюю
выдерживая размеры 1
Горизонтально-фрезерная
под крепление режущих ножей
Вертикально-сверлильная
Нарезать резьбу в размер 2
приттупить острые кромки
Снять заусенцы после
Снять фаску на ребрах паза.
Наменование операций
корпус развертки.cdw

Плотность материала
Масса M = 4407.494288 г
Площадь S = 75311.041694 мм2
Объем V = 563618.195334 мм3
Сталь 40 ГОСТ 1050-88
Спецификация Развертка.spw

технологический процесс.cdw

отрезки с одной стороны
Сверлить сквозное отв.
Развернуть конусное
Горизонтально-расточная
Расточить внутреннюю
выдерживая размеры 1
Горизонтально-фрезерная
под крепление режущих ножей
Вертикально-сверлильная
Нарезать резьбу в размер 2
приттупить острые кромки
Снять заусенцы после
Снять фаску на ребрах паза.
Наменование операций
Наладка на шлифовальную операцию.cdw

Заготовка - прокат.cdw

РГР ТИРИ.docx
Кафедра Технології машинобудування
Дисципліна Технологія обробки типових деталей та складання машин
Спеціальність 6.090202 – Технологія машинобудування
Курс 4 Група 4С2 Семестр 8
на розрахунково-графічну роботу студента
Владимирова Любомира Спасовича
(прізвище ім’я по-батькові)
Тема проекту (роботи) Розробка проекту технологічного процесу виготовлення деталі ріжучого інструмента.
Термін захисту студентом закінченого проекту (роботи) 20.05.09.
Вихідні дані до проекту (роботи)
Робочі креслення деталі:
) креслення Розвертки насадної310 2371-5020СБ.
) Програма випуску Nгод. = 200 шт.
Зміст розрахунково-пояснювальної записки (перелік питань що розроблюються) Визначення типу виробництва;
опис конструкції деталі та аналіз її на технологічність;
складання та обрунтування технологічного процесу механічної обробки;
розрахунок загальних та між операційних припусків режимів різання технічного нормування та інші технологічні і організаційні показники;
розробка операційних карт механічної обробки деталі.
Перелік графічного матеріалу (з точним переліком обов’язкових креслень)
креслення заготівки;
креслення технологічних схем механічної обробки;
розгорнутий технологічний процес з операційними ескізами основних операцій.
Найменування етапів курсового
Термін виконання етапів проекту (роботи)
Визначення типу виробництва;
опис конструкції деталі та аналіз її
Техніко-економічне обрунтування
методу отримання заготівки;
складання та обрунтування
технологічного процесу
розрахунок загальних та між
операційних припусків режимів
різання технічного нормування;
Оформлення технологічної
(підпис)(Прізвище ім’я по-батькові)
Расчетно-графическая работа состоит из графической части: 3 чертежа формата А1.
Первый лист – чертеж детали чертеж заготовки; чертеж инструмента;
Второй лист – технологические наладки на механические операции;
Третий лист – развернутый техпроцесс с операционными эскизами основных операций указанием оборудования инструментов второго порядка режимов резания приспособлений;
Пояснительной записки объемом страниц машинописного текста.
В качестве детали выбран и утвержден корпус инструмента Развертка насадная
Назначение инструмента
Анализ технологичности конструкции детали
Определение типа производства
Технико-экономическое обоснование способа получения заготовки
Проектирование маршрутного технологического процесса
Обоснование последовательности операций технологического процесса
Обоснование выбора технологических баз
Обоснование метода обработки и оборудования
Расчет припусков на механическую обработку
Расчет режимов резания
Техническое нормирование
Определение количества оборудования
Список использованной литературы
Задачей данной расчетно-графической работы является освоение и углубление знаний полученных при изучении курсов «Технология изготовления режущих инструментов» и «Режущий инструмент» а также приобретение навыков в практическом применении объема знаний курса «Технология машиностроения» и использовании их с учетом специфики инструментального производства.
Качество металлорежущего инструмента зависит не только от его конструкции и материала но и во многом от технологии его изготовления. Основополагающими технологическими направлениями развития инструментального производства являются приближение формы заготовки к форме готового изделия за счет применения специального профиля проката и биметаллических заготовок использования порошковой металлургии новых высокоэффективных СОТС с подводом их непосредственно в зону резания использования синтетических сверхтвердых абразивных и поликристаллических материалов и т.д.
Широкое применение инструментов с механическим креплением МНП из твердого сплава и композитных сверхтвердых материалов диктует применение некоторых специальных технологических операций – обработка методами горячей и холодной пластической деформации (прессование редуцирование продольно-винтовое прокатывание и др.) расширение области применения электрофизических и электрохимических методов обработки.
Важным резервом в повышении стойкости и эффективности режущего инструмента являются новые технологии нанесения износостойких покрытий модифицированных на атомном уровне с помощью нанотехнологий и позволяющих достичь повышения прочностных характеристик не снижая твердости покрытия.
Развертывание представляет собой процесс обработки отверстий с целью получения повышенной чистоты и точности.
Как известно развертка – многозубый режущий инструмент который в процессе обработки вращается вокруг своей оси и поступательно перемещается вдоль оси совершая движение подачи.
Развертки цельные являются наиболее простыми по конструкции но не имеют возможности регулировки по диаметру. В связи с этим широко применяются сборные развертки с быстрорежущими и твердосплавными вставными зубьями которые после износа и переточек сохраняют возможность регулировки на требуемый размер что в свою очередь повышает срок их службы.
Для обеспечения возможности восстановления размера диаметра по мере износа применена конструкция сборной насадной развертки с креплением зубьев в корпусе с помощью винтов.
Данный инструмент применим для обработки внутренней цилиндрической поверхности детали Ступица ККП-3.07.101.
Материал корпуса развертки – Сталь 40 ГОСТ 1050-88.
Схема развертывания внутренней цилиндрической поверхности
При анализе технологичности конструкции детали – корпус развертки цилиндрической насадной определили что деталь в целом технологична:
- деталь имеет удобные поверхности для ее установки и закреплении в приспособлении;
- деталь состоит из простых геометрических фигур;
- возможно использования стандартного инструмента;
- деталь состоит из однородного материала;
- материал из которого состоит деталь вполне удовлетворительно обрабатывается;
- имеется свободный доступ к обрабатываемым поверхностям режущим и измерительным инструментом;
- имеется возможность обработки нескольких поверхностей за один проход;
- деталь изменяется в размере от конца к центру от меньшего к большему.
Но также имеются и не технологические поверхности – большой перепад диаметров.
Конструкция насадной сборочной развертки и ее корпуса
Тип производства определяется по коэффициенту серийности но в виду отсутствия значений норм штучного времени на обработку на всех операциях тип производства может быть определен после разработки технологического процесса. В начальной стадии проектирования тип производства устанавливаем ориентировочно в зависимости от годовой программы запуска деталей и веса по табл.1.
Определение типа производства по программе запуска и весу детали
Количество обрабатываемых в год деталей одного наименования
По массе детали и программе запуска принимаем ориентировочно мелкосерийный тип производства (масса детали m=44 кг количество обрабатываемых в год деталей Nг=200шт.).
Одной из основных характеристик типа производства является коэффициент закрепления операций (Кз.о.) который указывает на количество операций выполняемых на одном станке.
На начальной стадии выполнения курсового проекта определить Кз.о. невозможно поэтому на этом этапе целесообразно пользоваться табличным методом с последующим его уточнением по Кз.о.
Рассчитаем такт выпуска деталей по формуле:
где - действительный годовой фонд времени работы оборудования в часах.
- годовая программа выпуска деталей в штуках.
Поскольку количество рабочих дней составляет 254 дня с учетом 8-ми часового рабочего дня =254×8=2032 часа производим расчет:
При мелкосерийном производстве определяется количество деталей в партии одновременно запускаемых в производство по формуле:
где f – необходимый запас деталей на складе (для легких 5-10 дней);
Q=254 – число рабочих дней в году.
На основании возможных методов получения заготовки выбираем два из них с учетом конструкции детали и типа производства.
Заготовка изготовленная методом свободной ковки.
Заготовка изготовленная из проката.
Выбранные методы получения заготовок оцениваются:
- по стоимости заготовки;
- по степени использования металла.
Стоимость заготовки поковки определяем по формуле:
Кт=1 4 стр. 39 - коэффициент зависящий от класса точности;
Км=118 4 стр. 40 - коэффициент зависящий от массы;
Кс=087 4 стр. 40 - коэффициент зависящий от группы сложности;
Кв=1 4 стр. 39 - коэффициент зависящий от марки материала;
Кп=1 4 стр. 39 - коэффициент зависящий от объема производства заготовок.
Q=5 кг – масса заготовки;
q=45 кг – масса детали;
Sотх=950 грн – цена 1 тонны отходов;
Стоимость заготовки из проката
где =65– масса заготовки кг;
=196 – цена 1 кг материала грн.;
=45 – масса готовой детали кг;
=950 – цена 1 т отходов грн.
Годовую экономию по стоимости заготовок определяю по формуле [2]:
Годовую экономию материала определяю по формуле [2]:
где = 088 – коэффициент использования метала при первом методе получения заготовки;
= 069 – коэффициент использования метала при втором методе получения заготовки.
Из приведенного расчёта следует что годовая экономия по стоимости получения заготовки при использовании проката вместо поковки составляет 920 грн соответственно с экономической точки зрения выгоднее получать заготовки из круглого проката вместе с тем при использовании заготовки из проката увеличивается количество металла уходящего в стружку в связи с меньшим коэффициентом использования материала по сравнению с поковкой поэтому сознательно принимаем метод получения заготовки из проката в виду преобладания финансовой экономии над экономией металла.
Проектирование маршрутного технологического процесса
Пило-отрезной станок
Снять остаток после обрезки с одной стороны
Обработать отверстие и первый торец
)Подрезать торец предварительно;
)Проточить по наружному диаметру
)Сверлить насквозь; подрезать торец окончательно; снять фаску;
)Развернуть конусное отверстие предварительно;
)Развернуть конусное отверстие окончательно.
Токарный полуавтомат
Обработать второй торец и наружный диаметр.
)Проточить по наружному диаметру предварительно;
)Подрезать торец окончательно
)Прорезать паз по наружному диаметру;
)Проточить по наружному диаметру окончательно;
)Зенковать фаску в отверстии.
Проточенная часть наружного диаметра
Фрезеровать шпоночный паз
Торец наружный диаметр
Фрезерный полуавтомат
Фрезеровать канавки под режущие ножи
)Сверлить отверстия под винты;
)Нарезать резьбу в отверстиях.
Снять заусенцы после фрезерования. Снять фаску на ребрах шпоночного паза.
Внутришлифовальн. полуавтомат
Полуавтоматический агрегат
Последовательность операций технологического процесса спроектирована в соответствии со следующими рекомендациями [1]:
На первых операциях количество которых обычно находится в пределах от 1 до 3 планируют обработку поверхностей составляющих комплект чистовых баз. Поскольку у заготовки ещё нет обработанных поверхностей то на этой стадии проектирования выбирают комплект черновых технологических баз.
Затем проектируют операции для черновой обработки детали при этом рекомендуется предусматривать сначала обработку неответственных а потом ответственных поверхностей.
На следующих операциях планируют чистовую а при отсутствии термообработки и отделочную обработку ответственных поверхностей.
Операции по обработке второстепенных поверхностей (отверстий под болты и резьбовых отверстий лысок и т. д.) распределяют между основными или их выносят в конец перед термообработкой.
В маршрутном технологическом процессе указывают место и определяют основное содержание операций по термической обработке детали.
После термической обработки следуют операции предназначенные для отделочной обработки ответственных поверхностей детали. При этом в первую очередь обрабатываются поверхности комплекта чистовых технологических баз. Другие отделочные операции проектируют с учётом точности обработки элементарных поверхностей. Сначала проектируют обработку поверхностей с меньшей точностью; наиболее ответственную и точную поверхность рекомендуется обрабатывать последней.
Разработку маршрутной технологии в указанной последовательности производят для подавляющего большинства деталей. Однако в некоторых случаях нецелесообразно а иногда и невозможно придерживаться указанных соображений.
Черновую технологическую базу выбираю согласно следующим требованиям [4]:
в комплект черновых технологических баз включают поверхности остающиеся после обработки детали в чёрном виде;
для детали обрабатываемой кругом за черновую технологическую базу принимают поверхность с наименьшим припуском;
в комплект черновых технологических баз включают поверхности с которых при последующей обработке должен быть снят равномерный припуск.
Выбирая чистовые технологические базы руководствуются двумя следующими принципами [4]:
принципом совмещения баз;
принципом постоянства баз.
Обоснование методов обработки и оборудования
Выбор методов обработки и оборудования может быть обоснован:
- типом производства;
- сравнительным анализом существующих методов обработки элементарных поверхностей;
- стремлением повысить производительность труда путём использования метода концентрации операций одновременной обработки нескольких деталей;
- конструктивными особенностями детали которые определяют метод обработки и необходимость использования определённого оборудования.
Расчет припусков производим аналитическим методом
Для расчета припусков аналитическим методом выбираем наружную цилиндрическую поверхность Ra=25 мкм.
Технологический маршрут обработки поверхности состоит из чернового и чистового точения выполняемых при одной установке.
Минимальный припуск для наружных цилиндрических поверхностей рассчитывается по формуле:
-высота неровностей профиля на предшествующем переходе мкм [1табл.19]
-суммарные отклонения расположения поверхности и в некоторых случаях отклонения формы поверхности на предыдущем переходе;
-суммарное значение пространственных отклонений для заготовки данного типа выражается формулой:
- коробление заготовки
- смещение заготовки
d=120 мм-диаметр обрабатываемого отверстия;
Т= 35 мкм-допуск на базовый размер по квалитету точности.
В итоге суммарное значение пространственных отклонений:
Величина остаточного пространственного отклонения:
после чернового точения:
После чистового точения:
Погрешность установки заготовки определяется по формуле:
- погрешность базирования мкм
- погрешность закрепления мкм
Погрешность базирования определяем исходя из закрепления заготовки в патроне тогда погрешность базирования выражается формулой:
где – минимальный гарантированный зазор;
допуск на размер базового отверстия;
допуск на размер кулачков патрона.
Погрешность закрепления заготовки принимаем согласно
[1 доп.5 табл.25]тогда
при черновой обработке:
При чистовом точении:
На основании рассчитанных данных выполняем расчет минимальных значений межоперационных припусков:
По расчетному (чертежному) размеру после обработки (точение чистовое 119976 мм) для чернового точения[1]:
Значения допусков определяем по таблицам исходя из показателя квалитета точности обработки. Таким образом для чистового точения допуск Т=35 мкм (чертежный размер); для чернового точения допуск Т=140 мкм; для заготовки согласно ГОСТ 1855-85 допуск Т=400 мкм.
Для чистового точения наибольший предельный размер
Для чернового точения наибольший предельный размер
Для заготовки наибольший предельный размер
Минимальные предельные значения припусков:
Для чистового точения
Для чернового точения
Выполняем проверку правильности проведенных расчетов исходя из условия:
Результаты проведенных расчетов заносим в таблицу
На остальные обрабатываемые поверхности припуски выбираем табличным методом (согласно ГОСТ 1855-85) и заносим их значения в таблицу[7]:
Припуски на механическую обработку
Припуск на мех. обработку мм
Развернуть отверстие
Фрезеровать шпон. паз
Схема припуска на механическую обработку поверхности
Режимы резания рассчитываем на операцию 015 – Токарная. Станок токарный полуавтомат модели 1А240П-6.
Выбираем подачу согласно[5] ;
Скорость резания ммин определяем по формуле:
где коэффициент [5 с. 269];
показатели степени [5 с. 269];
период стойкости инструмента [5 с. 268];
поправочный коэффициент [2 с. 268]:
Рассчитываем скорость резания:
Частота вращения шпинделя.
Частота вращения шпинделя определяется по формуле:
где диаметр обрабатываемой детали.
Пересчитаем скорость резания по формуле:
Силу резания определяем по формуле :
де постоянна сил резания [2 с. 273];
показатели степени [2 с. 273];
поправочный коэффициент[2 с. 271];
Рассчитываем силу резания:
Мощность резания рассчитывается по формуле:
Сверлить отверстие сквозное
Выбираем подачу согласно[5табл.25] ;
Где согласно [5табл.28] значение коэффициента 98
Показатели степени: q=04; y=05; m=02;
Период стойкости сверла Т=60 мин [5табл.30];
Общий поправочный коэффициент
Подставляем данные в формулу нахождения скорости резания:
Крутящий момент Нм рассчитываем по формуле:
Где согласно [5табл.32] значение коэффициента 00345;
Показатели степени: q=2; y=08;
Подставляем значения в формулу нахождения крутящего момента:
Осевую силу рассчитываем согласно формуле:
Где согласно [5табл.32] значение коэффициента 68;
Показатели степени: q=1; y=07;
Подставляем значения в формулу нахождения осевой силы:
Для определения мощности резания используем формулу:
Частота вращения инструмента обмин
Принимаем ближайшее стандартное значение ;
Находим мощность резания:
Развертывание конусного отверстия
Выбираем подачу согласно[5табл.26] ;
С учетом поправочного коэффициента Коs=08;
Где согласно [6табл.28] значение коэффициента 105
Показатели степени: q=03;х=02; y=065; m=04;
Период стойкости развертки Т=120 мин [5табл.30];
Sz=sz=005-подача на один зуб инструмента Z=4-число зубьев развертки;
согласно [5табл.22] значение коэффициента 67;
Показатели степени: y=065;
Для определения мощности резания используем формулу
Пересчитаем скорость резания по формуле:
Результаты расчёта режимов резания
Частота оборотов n обмин
Режимы резания на механическую обработку
После определения содержания операций и расчёта режимов резания нормы времени определяются в такой последовательности:
На основании рассчитанных режимов резания работы оборудования по каждому переходу вычисляется основное (технологическое) время .
По содержанию каждого перехода устанавливается необходимый комплекс приемов вспомогательной работы и определяется вспомогательное время с учётом возможных и целесообразных совмещений и перекрытий.
По нормативам в зависимости от операций и оборудования устанавливается время на обслуживание рабочего места отдых и естественные надобности и .
Определяется норма штучного времени
Для серийного производства устанавливается состав подготовительно - заключительной работы вычисляется подготовительно - заключительное время и штучно-калькуляционное
)Поскольку предыдущее определение типа производства показало что мы имеем серийное производство то нормой времени будет штучно-калькуляционное время Тшт. к
Минимальное значение основного времени То конкретными видами обработки будем находить пользуясь данными [3]
)Вспомогательное время расходуется рабочим на действия обеспечивающие выполнение основной работы. Вместе с основным временем оно составляет оперативное время. При расчёте нормы штучного времени учитывается только часть вспомогательного времени не перекрываемая машинным временем. При определении нормы вспомогательного времени суммируют следующие его элементы: время на установку и снятие детали время на приемы управления станком. Сюда входит время затрачиваемое на пуск и остановку станка включение и выключение подачи изменение числа оборотов шпинделя и др. время на измерение деталей (если оно не может быть перекрыто машинным).
Выбор вспомогательного времени ведём по [7стр.84]. Выбранное вспомогательное время заносим в операционную карту.
) Время на обслуживание рабочего места в серийном производстве задаётся в процентах от оперативного времени (суммы вспомогательного и основного времени).
) Время на отдых зависит от веса обрабатываемой детали процента машинного времени величины оперативного времени характера подачи (ручная или механическая) и определяется в процентах от оперативного времени как в массовом так и в серийном производстве.
) Подготовительно заключительное время нормируется на партию деталей и часть его приходящейся на одну деталь включается в норму штучно - калькуляционного времени (только при серийном и единичном производстве). В состав подготовительно заключительного времени входит ознакомление с работой настройка оборудования на выполнение данной работы настройка оборудования на выполнение данной работы и на требуемые режимы резания пробная обработка деталей получение сдача продукции. Подготовительно-заключительное время задается по нормативам в минутах и зависит от характера и объема подготовительных работ. Выбор подготовительно-заключительного времени производим согласно [3]. Выбранное время заносим в операционную карту.
Результаты по техническому нормированию
Расчетное количество станков определяется для мелкосерийного производстве согласно формуле:
Где - штучно-калькуляционное время в мин. ;
Расчет проводим на операцию 015
Принятое число станков () определяем путём округления расчетного количества обычно в сторону увеличения =1.
Степень занятости оборудования на каждой из операций определяется коэффициентом загрузки оборудования (станков) по формуле:
Подставляем необходимые данные в формулу:
Коэффициент загрузки станка увеличиваем за счет догрузки другими деталями.
В серийном производстве среднее значение коэффициента загрузки должно быть в пределах при догрузки другими деталями =075 – 085.
Коэффициент использования оборудования по основному времени свидетельствует о доле машинного времени в общем времени работы станка
Подставляем данные:
По выше изложенной методике рассчитываем количество требуемого оборудования на остальные операции и заносим результаты в таблицу 8
Степень использования оборудования по основному времени
Схема загрузки оборудования по основному времени
При выполнении расчетно-графической работы была проанализирована конструкция корпуса насадной сборной развертки описано назначение режущего инструмента спроектирован технологический процесс обработки детали корпус развертки рассчитаны и назначены припуски на механическую обработку рассчитаны режимы резания и нормы времени на обработку.
Результатом выполнения расчетно-графической работы является разработанный с помощью программы САПР-АВТОПРОЕКТ технологический процесс механической обработки детали «Корпус развертки».
Методичні рекомендації для курсового проектування по дисципліні «Технологія виготовлення різальних інструмент».Г.Е. Діневич С.Г. Кондрашов А.В. Малигін И.П. Сімінченко. 2008 р.
Курсове проектування з технології машинобудування Навчальний посібник - Херсон ХНТУ: 2008 - 133 с. Ю.П. Білоус С.Г. Кондрашов О.В. Малигін.
Общемашиностроительные нормативы времени для технического нормирования работ на металлорежущих станках. Часть 1 и 2. М.: Машиностроение 1967.
Палей М.М. Технология производства режущих инструментов. М. Машиностроение 1982-256с.
Косилова А.Г. Мещеряків Р.К. Довідник технолога машинобудівника Т2 М. : Машинобудування 1985 496с.
Довідник технолога-машинобудівника. Т. 1Під ред А.Г. Косиловой і Р.К. Мещерякова. - 4-е изд. перераб. і доп. - М.: Машинобудування 1985.
Данилевский В.В. Справочник молодого машиностроителя. Изд.
-едоп. и перераб. М. «Высш. Школа»1973.
Рекомендуемые чертежи
- 24.01.2023
- 24.01.2023
- 24.01.2023
- 24.01.2023
- 01.07.2014