Проектирование ленточного транспортера


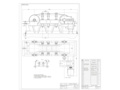
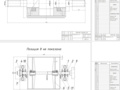
- Добавлен: 25.10.2022
- Размер: 466 KB
- Закачек: 0
Узнать, как скачать этот материал
Подписаться на ежедневные обновления каталога:
Описание
Проектирование ленточного транспортера
Состав проекта
![]() |
![]() |
![]() ![]() ![]() ![]() |
![]() ![]() ![]() ![]() |
![]() |
![]() ![]() ![]() |
Дополнительная информация
Контент чертежей
rrr.r113.r2.dwg

rrr.r113.r1.dwg

Рекомендуемые чертежи
- 04.06.2015
- 24.01.2023
Свободное скачивание на сегодня
Обновление через: 2 часа 37 минут