Проектирование привода ленточного транспортера, выполненного на базе цилиндрического двухступенчатого редуктора




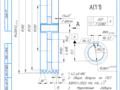
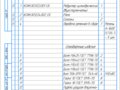
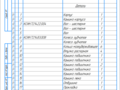
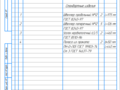
- Добавлен: 24.01.2023
- Размер: 2 MB
- Закачек: 0
Описание
Проектирование привода ленточного транспортера, выполненного на базе цилиндрического двухступенчатого редуктора
Состав проекта
![]() |
![]() |
![]() |
![]() |
![]() ![]() ![]() |
![]() |
![]() ![]() ![]() ![]() |
![]() |
![]() ![]() ![]() ![]() |
![]() ![]() ![]() ![]() |
![]() ![]() ![]() ![]() |
![]() |
![]() |
![]() ![]() ![]() ![]() |
![]() ![]() ![]() ![]() |
![]() ![]() ![]() |
![]() ![]() ![]() ![]() |
![]() |
![]() |
![]() ![]() ![]() ![]() |
![]() ![]() ![]() ![]() |
![]() |
![]() ![]() ![]() |
![]() ![]() ![]() |
![]() ![]() ![]() |
![]() ![]() ![]() |
Дополнительная информация
кп по ДМ.docx
КАФЕДРА «СПЕЦИАЛЬНЫЕ ИНЖЕНЕРНЫЕ НАУКИ»
по дисциплине «Детали машин 2»
Направление подготовки
1900.62 – Конструкторско-технологическое обеспечение машиностроительных производств
Технология машиностроения
«Проектирование привода ленточного транспортера выполненного на базе цилиндрического двухступенчатого редуктора»
студент гр. Б-05-721-1
Оценка защиты работы
Глазов 2014МИНОБРНАУКИ РОССИИ
«Проектирование привода ленточного транспортера
выполненного на базе цилиндрического двухступенчатого редуктора»
Пояснительная записка курсового проекта
Спецификация привод.spw

Редуктор цилиндрический
Передача ременная в сборе
Винт 7006-0919 ГОСТ 13434-68
Гайка 10 ГОСТ 5915-70
Гайка 18 ГОСТ 5915-70
Муфта упругая втулочно-
пальцевая по ГОСТ 21424-75
Шайба 10 ГОСТ 11371-78
Шайба 8Н ГОСТ 6402-70
Шайба 10Н ГОСТ 6402-70
Шайба 18Н ГОСТ 6402-70
Шайба 10 ГОСТ 10906-78
Шайба 18 ГОСТ 10906-78
Электродвигатель 4А112М2У3
Шкив ведомый.cdw

Сталь 40Х ГОСТ 4543-71
Общие допуски по ГОСТ
Рама.cdw

*Размеры для справок.
Общие допуски по ГОСТ 30893.1-2002:
Сварные швы термообработать для снятия внутренних
Б дефекты не допускаются.
кроме поверхностей А
Зубчатое колесо.cdw

эвольвенты в начале
рабочего участка профиля
Допуск на погрешность
Допуск на колебание длины
Коэффициент смещения
Сталь 40Х ГОСТ 4543-71
им М. Т. Калашникова)
Общие допуски по ГОСТ 30893.1-2002:
Неуказанные радиусы скруглений R2.5.
вал промежуточный.cdw

эвольвенты в начале
рабочего участка профиля
Допуск на погрешность
Допуск на колебание длины
Коэффициент смещения
Сталь 40Х ГОСТ 4543-71
им М. Т. Калашникова)
*Размер обеспечиваетя инструментом.
Общие допуски по ГОСТ 30893.1-2002:
Рама _ КСИН.301224.000.spw

Швеллер продольный №12
Швеллер поперечный №12
Уголок неравнополочный 6
ПН-0-(10) ГОСТ 19903-74
кп по ДМ1.docx
Рис. 1. Кинематическая схема привода
Рис. 2. Циклограмма переменного режима нагружения
Галкин И. В. Проектирование привода ленточного транспортера выполненного на базе двухступенчатого цилиндрического редуктора. КСИН 303122.02 ПЗ: Курсовой проектГИЭИ (филиал) ИжГТУ имени Калашникова каф. СИН; рук. А.В. Овсянников. - Глазов 2014. Гр.ч. 2 л.ф. А2 3 л. ф.1 л. ф. А4; ПЗ 43 стр. 8 рис. 5 источников.
РЕДУКТОР ЦИЛИНДРИЧЕСКИЙ ДВУХСТУПЕНЧАТЫЙ ВАЛ ШЕСТЕРНЯ ЗУБЧАТОЕ КОЛЕСО ШКИВ
Объект исследования - редуктор зубчатый цилиндрический двухступенчатый.
Цель работы: спроектировать привод ленточного транспортера выполненного на базе двухступенчатого цилиндрического редуктора рассчитать его технические характеристики и составить конструкторскую документацию.
В пояснительной записке приведен кинематический расчет привода расчет на прочность прямозубой цилиндрической передачи выбор втулочно-пальцевой муфты расчет клиноременной передачи расчет соединения вал-ступица расчет валов проверка подшипников на статическую и динамическую грузоподъемности выбор смазочных материалов и систем смазывания описаны корпусные детали конструирование сварной рамы.
В графической части работы представлены чертежи деталей: вал шестерня зубчатое колесо шкив общий вид привода редуктор и рама.
Анализ исходных данных4
Кинематический расчет привода5
1. Подбор электродвигателя5
2.Определение передаточных отношений ступеней привода 5
3.Определение частот вращения и вращающих моментов на валах6
Проектный расчёт на прочность быстроходной ступени7
1. Выбираем материал шестерни и колеса 7
2.Определение допускаемых контактных напряжений7
3.Допускаемые напряжения изгиба зубьев привода 9
4.Расчет на прочность закрытых цилиндрических зубчатых передач редукторов 9
Проектный расчет на прочность тихоходной ступени12
1. Выбираем материал шестерни и колеса 12
2. Определение допускаемых контактных напряжений12
2. Допускаемые напряжения изгиба зубьев привода 13
4. Расчет на прочность закрытых цилиндрических зубчатых передач редукторов 14
Выбор втулочно-пальцевой муфты17
Расчет клиноременной передачи17
1. Предварительный расчёт18
2. Проверочный расчёт быстроходного вала 20
3. Проверочный расчёт промежуточного вала25
4. Проверочный расчёт выходного вала29
Расчет подшипников35
2. Промежуточный вал36
Расчет соединений вал-ступица38
1. Выбор материала и методика расчета 38
Конструирование цилиндрических колёс38
1. Конструирование цилиндрического прямозубого колеса38
Конструирование корпусных деталей39
Выбор смазочных материалов и системы смазывания40
1. Смазывание зубчатых передач40
2. Смазывание подшипниковых узлов41
Конструирование сварной рамы41
Список литературы 43
В рамках данного курсового проекта рассмотрены расчеты и проектирование привода общего назначения который включает в себя электрический двигатель клиноремённую передачу и двухступенчатый цилиндрический редуктор.
Привод — совокупность устройств предназначенных для приведения в действие машин. Состоит из двигателя силовых передач и системы управления.
Силовая передача (трансмиссия) — совокупность сборочных единиц и механизмов соединяющих двигатель с рабочим органом механизма или машины. Для передач вращательного движения различают передачи трения (ременные) и передачи зацепления (зубчатые червячные цепные и др.).
Передача механической энергии осуществляемая гибкой связью за счет трения между ремнем и шкивом называется ременной. Ременная передача состоит из ведущего и ведомого шкивов расположенных на некотором расстоянии друг от друга и огибаемых приводным ремнем. В зависимости от формы поперечного сечения ремня передачи бывают: плоскоременные клиноременные и круглоременные. Наибольшее распространение в машиностроении получили плоские и клиновидные ремни.
Редуктором называют механизм состоящий из зубчатых или червячных передач выполненный в виде отдельного агрегата и служащий для передачи вращения от вала двигателя к валу рабочей машины.
Назначение редуктора – понижение угловой скорости и соответственно повышения вращающего момента ведомого вала по сравнению с ведущим.
Редуктор состоит из корпуса (литого чугунного или сварного стального) в котором помещают элементы передачи – зубчатые колеса валы подшипники и т.д. В отдельных случаях в корпусе редуктора помещают также устройства для смазывания зацеплений и подшипников (например змеевик с охлаждающей водой в корпусе червячного редуктора).
Редукторы классифицируют по следующим основным признакам: типу передачи (зубчатые червячные или зубчато-червячные); числу ступеней (одноступенчатые двухступенчатые); по типу зубчатых колес (цилиндрические конические и т.д.); относительному расположению валов редуктора в пространстве (горизонтальные вертикальные); особенностям кинематической схемы (развернутая с раздвоенной ступенью и т.д.). Редуктор проектируют либо для привода определенной машины либо по заданной нагрузке (моменту на выходном валу) и передаточному числу без указания конкретного назначения.
Основные задачи проектирования по деталям машин следующие:
Расширить и углубить знания полученные при изучении предшествующих теоретических курсов.
Закрепить навыки практических расчетов использованием вычислительных средств.
Усвоить общие принципы расчета и конструирования типовых деталей и узлов с учетом конкретных эксплуатационных и технологических требований и экономических соображений.
Ознакомиться с Государственными стандартами справочными материалами и правилами их использования. Особое значение стандартизация приобретает в машиностроении отличающемся многообразием типоразмеров и конструктивных форм изделий применяемых материалов и инструментов.
Анализ исходных данных
Частота вращения выходного вала nвых =75 обмин
Вращающий момент на выходном валу Твых =850
Годовой коэффициент использования передачи Кг =07
Суточный коэффициент использования передачи Kсут =07
Коэффициент перегрузки К=15
Срок службы зубчатой передачи Lг=6
Рис.3. Циклограмма переменного режима нагружения зубьев передачи.
Коэффициенты циклограммы:
Согласно исходной схеме в качестве редуктора выбираем двухступенчатый цилиндрический редуктор. Тогда исходная схема примет вид:
Рис.4. Исходная кинематическая схема 1-электродвигатель 2-ременная передача 3-редуктор 4-муфта втулочно-пальцевая
Рис.5. Компоновочная схема редуктора.
В данном редукторе применяются: цилиндрические пары первой и второй ступени. Принцип работы данной схемы заключается в следующем: вращающий момент с вала электродвигателя 1 передаётся через ременную передачу на быстроходный вал 2 редуктора. Быстроходный вал представляет собой цилиндрическую вал-шестерню входящую в зацепление с цилиндрическим колесом которое располагается на промежуточном валу 3. На этом же валу находится шестерня цилиндрической зубчатой передачи входящая в зацепление с цилиндрическим зубчатым колесом которое находится на выходном валу 4. На выходном валу установлена втулочно-пальцевая муфта.
Кинематический расчёт привода
1. Подбор электродвигателя
Определение мощности на выходе привода
где nвых =75 обмин; частота вращения выходного вала
T =850 Н-м; вращающий момент на выходном валу
Определение суммарного КПД привода:
где - КПД ременной передачи =095;
- КПД одной пары подшипников =099;
- КПД закрытой цилиндрической передачи =098;
- КПД закрытой муфты =098;
Определение требуемой мощности двигателя
Определение ориентировочной асинхронной частоты вращения вала двигателя
где uР - передаточное отношение ременной передачи;
uТ - передаточное отношение тихоходной ступени;
uБ - передаточное отношение быстроходной ступени;
Выбираем асинхронный электродвигатель типа 4AM112M2Y3 мощность которого =75 кВт асинхронная частота вращения вала двигателя nЭД = 2900 обмин.
Рассчитаем перегрузку двигателя она должна быть в диапазоне [P]=10..12%:
Это удовлетворяет условиям поэтому двигатель выбран верно.
2. Определение передаточных отношений ступеней привода
Определяем суммарное передаточное отношение привода:
Разбиваем суммарное передаточное отношение по ступеням:
передаточное отношение ременной передачи uр=3;
передаточное отношение двухступенчатого цилиндрического редуктора
Передаточноеотношениетихоходной ступени:
передаточное отношение быстроходной ступени:
Распределив общее передаточное число привода по ступеням определяем его расчетное значение. Отклонение от требуемого не должно превышать 4%.
3. Определение частот вращения и вращающих моментов на
3.1.Основные параметры в первом сечении (на валу электродвигателя)
где P1= РВХ= 7.5 кВт
3.2.Значения параметров во втором сечении (на быстроходном валу)
3.3.Значения параметров в третьем сечении (на промежуточном валу)
3.4.Значения параметров в четвёртом сечении (на тихоходном валу)
3.5.Значения параметров в пятом сечении (при соединении валов втулочно-пальцевой муфтой)
Проектный расчёт на прочность быстроходной ступени
1. Выбираем материал шестерни и колеса
Для изготовления шестерни и колеса по таблице выбираем одинаковую марку стали 40Х при термической обработке улучшение с твердостью сердцевины НВ 269.. .302 поверхности НВ 269.. .302.
Среднее значение твердости поверхности зубьев
2. Определение допускаемых контактных напряжений
Допускаемые напряжения для зубьев шестерни и колеса определяются по общей зависимости:
ZR - коэффициент учитывающий шероховатость рабочих поверхностей зубьев;
SH - коэффициент запаса контактной прочности;
ZN - коэффициент долговечности;
ZV–коэффициентучитывающийвлияниескорости;
- длительный предел контактной выносливости;
Nhe -эквивалентное число циклов нагружений;
– число циклов нагружния;
LГ – срок службы передачи годы;
KГ – коэффициент использования передачи в течение года;
Kсут – коэффициент использование передачи в течение суток;
Так как NHE1 > значит ZN = 1;
Для зубчатого колеса:
Так как NHE2 > значит ZN = 1;
В качестве расчетного допускаемого напряжения принимают минимального из и т.е
3. Допускаемые напряжения изгиба зубьев.
Допускаемые напряжения изгиба зубьев шестерни и колеса определяется по формуле:
– предел выносливости при «отнулевом» цикле нагружений;
SF – коэффициент запаса изгибной прочности;
– коэффициент долговечности;
mF – показатель степени кривой усталости
Так как NFE1 = 9.2 > значит YN = 1;
Так как NFE2 = > значит YN = 1;
4. Расчет на прочность закрытых цилиндрических зубчатых передач редукторов
4.1.Предварительное значение межосевого расстояния
4.2.Уточненное значение межосевого расстояния:
KH – коэффициент нагрузки;
KHV – коэффициент учитывающий внутреннюю динамическую нагрузку зависит от окружной скорости и степени точности изготовления передачи:
V – окружная скорость:
– коэффициент учитывающий неравномерность распределения нагрузки по длине контактных линий: при
– коэффициент учитывающий неравномерность распределения нагрузки между одновременно зацепляющимися парами зубьев в связи с погрешностями изготовления шестерни и колеса:
Округляем полученное значение до ближайшего из стандартного ряда:
4.3.Ширина венца колеса:
Ширина венца шестерни:
4.4.Нормальный модуль зубчатого колеса:
– минимальный модуль:
KF – коэффициент нагрузки ;
– максимальный модуль:
4.5.Число зубьев шестерни и колеса:
Суммарное число зубьев:
Число зубьев шестерни:
Число зубьев колеса:
4.6.Фактическое значение передаточного отношения:
4.7.Проверочный расчет на контактную выносливость:
Так как полученное значение находиться в интервале значит ранее принятые параметры передачи принимаем за окончательные.
4.8.Проверочный расчет на выносливость при изгибе зубьев для колеса и шестерни:
KF – коэффициент нагрузки;
KFV – коэффициент учитывающий внутреннюю динамическую нагрузку в передаче
– коэффициент учитывающий неравномерность распределения нагрузки по длине контактных линий
- коэффициент учитывающий неравномерность распределения нагрузки между одновременно зацепляющимися парами зубьев в связи с погрешностями изготовления шестерни и колеса
YFS – коэффициент учитывающий форму зуба и концентрацию напряжения;
– коэффициент учитывающий наклон зуба
– коэффициент учитывающий перекрытие зубьев
– коэффициент торцевого перекрытия:
Проверочный расчет для шестерни:
Проверочный расчет для зубчатого колеса:
Оба расчета меньше допускаемого значения.
4.9.Геометрические размеры передачи:
Делительный диаметр:
Диаметр вершин зубьев:
Диаметр впадин зубьев:
4.10.Силы зацепления:
Проектный расчет на прочность тихоходной ступени
Так как NHE3 > значит ZN = 1;
Так как NHE4 > значит ZN = 1;
Так как NFE3 = 2.5 > значит YN = 1;
Так как NFE4 = > значит YN = 1;
4.1.Предварительное значение межосевого расстояния
Так как полученное значение не находиться в интервале значит ранее принятые параметры передачи принимаем за окончательные.
Выбор втулочно-пальцевой муфты
Выбираем втулочно-пальцевую муфту по заданному передаваемому моменту T=850Н м. С учетом коэффициента перегрузки К=15 определяем допускаемый вращающий момент [T]=1.5*850=1275 Н*м. Выбираем ближайший больший допускаемый вращающий момент по ГОСТ 21424-93. Тогда [T]=2000 Н*м. Остальные параметры муфты определяем по указанному ГОСТу и вносим в таблицу 2.
Параметры втулочно-пальцевой муфты по ГОСТ 21424-93.
Допускаемое смещение
Расчет клиноременной передачи.
T1= – вращающий момент.
uр=3 – передаточное отношение ременной передачи
– диаметр ведущего шкива из стандартного ряда d1=125 мм
– диаметр ведомого шкива из стандартного ряда d2=400 мм
Межосевое расстояние апредв следует принять на интервале:
где T0=8 мм – высота сечения ремня.
Для расчета длины ремня возьмем апредв. =400мм.
по стандартному ряду L=1600 мм
Уточняем межосевое расстояние a: =; a=362мм
Найдем угол обхвата меньшего шкива:
По номограмме выбираем сечение ремня: А
Номинальная мощность P0 передаваемая одним ремнем:
Коэффициент угла обхвата: Cα=0.89
Коэффициент режима работы: Ср =1.4
Коэффициент учитывающий влияние длины ремня: CL =0.98
Коэффициент Сz учитывающий число ремней в передаче примем равным Сz =0.90
Необходимое для передачи заданной мощности P число ремней:
Предварительное натяжение ветвей клинового ремня:
Cила действующая на валы:
Расчет передачи на долговечность произведем по формуле: – допускаемая частота пробегов для клиноременных передач примерно равна 20.
Найдем частоту пробегов: =119 следовательно это гарантирует срок службы 5000 часов.
1. Предварительный расчёт
Диаметр вала электродвигателя уже определен исходя из выбранного нами типа электродвигателя. d1=32 мм.
Определяем диаметры консольных участков входного промежуточного и выходного валов редуктора.
где d - диаметр вала мм;
T - вращающий момент передаваемый валом Нм;
- допускаемое напряжение на кручение МПа;
где =16 МПа - минимальный диаметр консоли входного вала редуктора.
Выбираем цилиндрический конец вала. Длина консольного участка:
lK = 015d + 12d = 115d = 135 28 = 378 39 (мм). Принимаем lK=110 мм.
Диаметр посадочной поверхности для подшипника: dn > d2 = 38 (мм).
Так как на опоры вала не действуют осевые силы от зубчатых колес то выбираем шариковые радиальные однорядные подшипники средней серии. Из ГОСТ 8338-75 находим подшипник 308 с диаметром внутреннего кольца dn=40 мм. Диаметр наружного кольца D=90 мм ширина B=23 мм размер фаски подшипника г=25 мм.
Диаметр буртика (заплечика) для упора подшипника:
d6n = dn + 3r = 40 + 3 25 = 475 (мм). Принимаем d6n=48 мм.
Для подшипников используем пластичную смазку. В связи с этим перед подшипником первой (ближайшей к шестерне) опоры необходимо поставить мазеудерживающее кольцо которое устанавливается на вал на 1 2 мм вовнутрь от контура внутренней стенки корпуса редуктора. Толщина кольца 10 мм.
где =16 МПа - минимальный диаметр промежуточного вала
Назначаем шариковые радиальные подшипники средней серии. Из ГОСТ 8338—75 находим подшипник 309 с диаметром внутреннего кольца dn=45 мм. Диаметр наружного кольца D=100 мм ширина B=25 мм размер фаски подшипника г=25 мм.
Диаметр вала под цилиндрическое колесо: dц=dп+3r=45+3·25=525 (мм). Принимаем dц=53 мм.
Длина ступицы колеса: lст=16·dц=16·53=848 (мм). Принимаем lст=85 мм.
Диаметр буртика для упора цилиндрического колеса: d6ц≥ dц+3·f=53+3·2=59 где f – размер фаски колеса. Принимаем dбц=60 мм.
Диаметр буртика для упора подшипника (за цилиндрической шестерней): d6n≤dп+3r=45+3·25=525. Принимаем dбп=53 мм.
где =16 МПа - минимальный диаметр консоли выходного вала до и после соединения муфтой
Длину консольного участка согласовываем с длиной полумуфты типа МУВП (упругая втулочно-пальцевая): 1к=140 мм.
Момент с вала на муфту передается через шпоночное соединение. Призматическую шпонку после её посадки в паз вала вынимать нежелательно поэтому диаметр под подшипник назначают таким чтобы подшипник свободно проходил через конец вала с заранее посаженной шпонкой.
dn=d+21·c где c - размер выступающей части шпонки.
Согласно ГОСТ 23360-78 для диаметра d=63 мм назначаем призматическую шпонку размерами: b х h = 18х11 мм глубина паза вала t1=70 мм. Размер выступающей части шпонки: c=h-t1=11-70=4 (мм). Тогда dn=63+21·4=71 4 (мм).
Так как на опоры вала не действуют осевые силы от зубчатых колес то выбираем шариковые радиальные однорядные подшипники легкой серии. Из ГОСТ 8338-75 находим подшипник 215 с диаметром внутреннего кольца d=75 мм. Диаметр наружного кольца D=130 мм ширина B=25 мм размер фаски подшипника r=25 мм. Диаметр вала под цилиндрическое колесо: dц=dп+3r=75+3·2=81 (мм). Принимаем dц=85 мм.
Длина ступицы колеса: lст=16·dц=16·85=136 (мм). Принимаем lст=136 мм.
Диаметр буртика для упора цилиндрического колеса: d6ц≥ dц+3·f=85+3·2=91 где f – размер фаски колеса. Принимаем dбц=95 мм.
2. Проверочный расчёт быстроходного вала
Вал рассматриваем как балку. Подшипники одновременно воспринимающие радиальные и осевые нагрузки (шариковые радиально-упорные и конические) обозначаем шарнирно-неподвижными опорами. На расчётную схему наносим все силы нагружающие вал приводя плоскости их действия к двум взаимно перпендикулярным плоскостям (горизонтальной- Z0X и вертикальной Z0Y). Определяем силы действующие на вал. Направление окружных сил зависит от направления вращения.
В качестве консольной нагрузки принимается радиальная сила от ременной передачи направленная по оси соединяющей центры шкивов. Определяем опорные реакции. По заданным расстояниям между опорами валов и сечениями приложения нагрузок (из компоновки) используя методы сопротивления материалов определяем реакции опор в вертикальной и горизонтальной плоскостях. Опорные реакции от консольных нагрузок определяем отдельно. Суммарные реакции на опорах определяем:
где R - суммарная реакция на опоре;
RX - составляющая опорной реакции направленная по оси X;
Ry - составляющая опорной реакции направленная по оси Y;
RP- составляющая опорной реакции вызванная действием консольной нагрузки.
По предварительному расчету выбираем диаметр вала d=40 мм.
Сила действующая на вал от ременной передачи:
где - диаметр шкива.
– для клиноременной передачи.
Определяем опорные реакции в горизонтальной плоскости X0Z
Производим проверку правильности определения численных значений реакций
Определяем опорные реакции в вертикальной плоскости Y0Z
Определяем опорные реакции от консольной нагрузки по X:
Определяем суммарные реакции на опорах :
Рис. 5. Схема нагружения входного вала.
Определяем изгибающие моменты в вертикальной плоскости:
Судя по заданной схеме на втором участке
при z= l1 получится
при z= l1 +l2 получится
при z= l1 +l2+l3 получится
Определяем изгибающие моменты в горизонтальной плоскости:
Определяем изгибающие моменты от действия консольной нагрузки по X:
на первом участке момент:
Изгибающий момент в сечении O (под колесом):
Определяем максимальное значение суммарного изгибающего момента в
сечении под подшипником(сечение В - наиболее опасное т.е. в этом сечении
наиболее вероятно усталостное разрушение):
Материал вала-шестерни – сталь 40Х
- предел прочности: в = 900 МПа
- предел выносливости при изгибе -1 = 410 МПа
- предел выносливости при кручении: -1= 240 МПа
Механическая обработка вала – шлифование (под подшипниками) вал не
подвергается поверхностному упрочнению.
Расчет на сопротивление усталости
Расчет проводим для сечения B.
Коэффициент запаса прочности по напряжениям изгиба:
Коэффициент запаса прочности по напряжениям кручения:
где KL – коэффициент долговечности учитывающий режим нагружения и
KD KD – суммарный коэффициент учитывающий влияние всех факторов
на сопротивление усталости при изгибе (кручении);
a a – амплитудная составляющая цикла изменения напряжения;
m m – средняя составляющая цикла изменения напряжений;
– коэффициент характеризующий чувствительность материала к
асимметрии цикла напряжений.
Напряжения изгиба изменяются по симметричному циклу поэтому m=0.
Напряжения кручения условно изменяются по отнулевому циклу поэтому a=m.
Коэффициент долговечности:
где NE – эквивалентное число циклов нагружений.
где n – частота вращения вала обмин; Lh – требуемый ресурс ч.
Так как N E> 4*106 то KL=1.
Суммарные коэффициенты при изгибе и кручении:
где K K – эффективные коэффициенты концентрации напряжений при изгибе и кручении соответственно;
Kd – коэффициент влияния абсолютных размеров поперечного сечения вала;
KF – коэффициент влияния шероховатости поверхности;
K – коэффициент влияния упрочнения.
В рассматриваемом сечении на вал посажен подшипник качения из таблицы находим KKd=3.5 и KKd=2.5.
По таблице определяем KF=112 при шлифовании.
Из таблицы для сечения без концентраторов напряжения при поверхностной закалке с нагревом ТВЧ K=12 15. Принимаем K=13.
Амплитудные значения напряжений:
где моменты сопротивления определены по формулам:
Окончательно коэффициенты запаса:
Общий (суммарный) коэффициент запаса прочности:
Вал удовлетворяет условию прочности по сопротивлению усталости.
3.Проверочный расчёт промежуточного вала
Рис. 6. Схема нагружения промежуточного вала.
при z= l3 получится
Опасным является сечение C (под цилиндрическим колесом) так как размеры цилиндрической шестерни (сечение O) определены по результатам расчетов на прочность.
Механическая обработка вала – тонкая обточка вал не подвергается поверхностному упрочнению.
Коэффициенты запаса прочности по напряжениям изгиба и кручения:
В месте посадки колеса на вал имеется два вида концентраторов напряжений: шпоночный паз и ступенчатый переход с галтелью.
Для шпоночного паза выполненного пальцевой фрезой: K=22 и K=20.
Для ступенчатого перехода с галтелью по таблице находим высоту буртика t=4 мм и радиус галтели r=25 мм. При rdк=2553=005 и tr=425=16 используя интерполяцию определяем K=12 и K=165.
Следовательно большее влияние на прочность вала оказывает шпоночный паз.
При диаметре вала dк=53 мм находим интерполяцией Kd=0685.
Определяем KF=122 при тонком точении.
K=1 так как вал не подвергается поверхностному упрочнению.
Данное сечение ослаблено канавкой для одной стандартной шпонки с размерами b×h =12×8 по ГОСТ 23360-78.
4. Проверочный расчёт выходного вала
В качестве консольной нагрузки выступает радиальная сила Fм от соедини-
тельной муфты которая возникает в результате погрешностей монтажа ошибок
изготовления и неравномерного износа элементов муфты. Направление силы Fм
принимаем таким чтобы она увеличивала деформации и напряжения от дейст-
вующих на вал сил (в данном случае – в вертикальной плоскости по направлению
Выходной вал редуктора соединен рабочим механизмом упругой втулочно-
пальцевой муфтой (МУВП):
Определяем опорные реакции от консольной нагрузки по Y:
Рис. 7. Схема нагружения выходного вала.
Определяем изгибающие моменты от действия консольной нагрузки по Y:
Материал вала-шестерни – сталь 45
- предел прочности: в = 800 МПа
- предел выносливости при изгибе -1 = 350 МПа
- предел выносливости при кручении: -1= 210 МПа
Механическая обработка вала – шлифование (под подшипниками) тонкая обточка (под колесом) вал не подвергается поверхностному упрочнению.
a) Сечение O (под колесом)
В рассматриваемом сечении на вал посажен подшипник качения. По интерполяции находим KKd=4125 и KKd=29.
Определяем KF=111 при шлифовании.
Данное сечение ослаблено канавкой для одной стандартной шпонки с размерами b×h =22×14 по ГОСТ 23360-78.
Вал удовлетворяет условию прочности по сопротивлению усталости.
б) Сечение B (под подшипником)
Для шпоночного паза выполненного пальцевой фрезой: K=201 и K=1.88.
Для ступенчатого перехода с галтелью по таблице находим высоту буртика t=5 мм и радиус галтели r=25 мм. При rdк=2585=003 и tr=525=2 используя интерполяцию определяем K=199 и K=161.
При диаметре вала dк=53 мм находим интерполяцией Kd=073.
Вал удовлетворяет условию прочности по сопротивлению усталости
Выбор подшипников качения
Диаметр опорной части вала – d=40 мм
Радиальные нагрузки на опоры: Fr1=68137 H Fr2=181445 H
Внешняя осевая сила FA отсутствует.
Частота вращения вала – n=967 обмин
Требуемый ресурс – Lhтр=25754 ч
Режим нагружения – переменный:
)Принимаем однорядный радиальный шарикоподшипник по ГОСТ 8338-75 средней серии №308. Находим размеры: d×D×B=40×90×23 мм и характеристики:
Cr=41000 H (динамическая радиальная грузоподъемность);
Cor=22400 H (статическая радиальная грузоподъемность);
)Определяем эквивалентные динамические нагрузки
Так как осевой силы нет то Fai=0.
При вращении внутреннего кольца подшипника V=1.
Для редукторов k=13 15. Принимаем k=15.
kT=1 при температуре подшипникового узла до 100С.
Для шарикоподшипников p=3.
Наиболее нагружена опора 2 далее ведем расчет по ней.
) Определяем ресурс принятого подшипника:
- в миллионах оборотов:
Для редукторов и коробок скоростей a1=1.
Для шарикоподшипников и обычных условий эксплуатации а23=07 08. Принимаем а23=075.
)Проверка по статической грузоподъемности
Эквивалентная статическая радиальная нагрузка:
Находим X0=06 и Y0=05.
следовательно принимаем
Выбранный подшипник пригоден для данных условий эксплуатации.
2. Промежуточный вал.
Диаметр опорной части вала – d=45 мм
Радиальные нагрузки на опоры: Fr1=400839 H Fr2=336964 H
Частота вращения вала – n=261 обмин
)Принимаем однорядный радиальный шарикоподшипник по ГОСТ 8338-75 средней серии №309. Находим размеры: d×D×B=45×100×25 мм и характеристики:
Cr=52700 H (динамическая радиальная грузоподъемность);
Cor=30000 H (статическая радиальная грузоподъемность);
Наиболее нагружена опора 1 далее ведем расчет по ней.
Диаметр опорной части вала – d=75 мм
Радиальные нагрузки на опоры: Fr1=383498 H Fr2=415107 H
Частота вращения вала – n=75 обмин
)Принимаем однорядный радиальный шарикоподшипник по ГОСТ 8338-75 легкой серии №215. Находим размеры: d×D×B=75×130×25 мм и характеристики:
Cr=66300 H (динамическая радиальная грузоподъемность);
Cor=41000 H (статическая радиальная грузоподъемность);
Выбранный подшипник пригоден для данных условий эксплуатации.
Расчет соединений вал-ступица
1. Выбор материала и методика расчета
Для закрепления на валах зубчатых колес и соединительных муфт применены призматические шпонки выполненные по ГОСТ 23360-78. Материал шпонок - сталь 45 для шпонок с пределом прочности . Так как высота и ширина призматических шпонок выбираются по стандартам расчет сводится к проверке размеров по допускаемым напряжениям при принятой длине или на основании допускаемых напряжений находится ее длина.
Рабочая длина шпонки определяется по формуле:
где T - наибольший крутящий момент на валу Н*м; d - диаметр вала мм; h - высота шпонки мм; МПа – допускаемые напряжения смятия; t1 - заглубление шпонки в валу мм.
Шпонка для соединения выходного вала со шкивом
Выбираем шпонку для диаметра мм и крутящим моментом Т=70 Н*м для которой b=8 мм h=7мм t1=4мм. Определяем минимальную длину:
Полная длина шпонки
Принимаем шпонка 8770 ГОСТ 23360-78.
Проверка шпонки на прочность по напряжениям смятия:
Для посадок с натягом допускаемое напряжение на смятие []см=110 200=155 МПа
Так как см[]см то условие прочности шпонки выполняется.
Для соединения шестерни и цилиндрического колеса с промежуточным валом принимаем шпонку для диаметра d=53 мм с крутящим моментом Т=252 Н*м для которой b=16 мм h=10 мм t1=6 мм. Определяем минимальную длину:
Принимаем шпонку 161070 ГОСТ 23360-78.
Для соединения тихоходного вала с цилиндрическим колесом выбираем шпонку для диаметра d=85мм с крутящим моментом Т=853 Н*м для которой b=22 мм h=14 мм t1=9 мм. Определяем минимальную длину:
Принимаем шпонку 2214125 ГОСТ 23360-78.
Для соединения входного вала с муфтой выбираем шпонку для диаметра d=63 мм с крутящим моментом Т=828 Н*м для которой b=18 мм h=11 мм t1=7 мм Определяем минимальную длину:
Принимаем шпонку 1811125 ГОСТ 23360-78.
Конструирование цилиндрических колёс
1.Конструирование цилиндрического прямозубого колеса
Основные параметры цилиндрического колеса были определены в пункте 4 данной пояснительной записки. К ним относятся:
Делительный диаметр: d=350 мм.
Диаметр вершин зубьев: da=360 мм.
Диаметр окружности впадин зубьев: df=3385 мм.
Ширина венца: b=71 мм.
Переходим к определению остальных конструктивных параметров. Конструируем кованое зубчатое колесо со ступицей необходимой из расчета шпоночного соединения (). Тогда длина ступицы Lст=79 мм. Диаметр ступицы мм где dв=85 мм - диаметр посадочного отверстия. Это колесо довольно большого диаметра поэтому обладает большой массой следовательно в кольцевом пазу для уменьшения массы необходимо сделать отверстия. Диаметр отверстия определяется по формуле: dотв=25мм;
Определяем толщину обода S = 25m + 2; S =145 мм.
Определяем толщину диска: С =0.25 b; где b=71 мм - ширина зубчатого венца ;
Из построения определяем D0 =3095 мм
Рис. 8. Колесо зубчатое цилиндрическое прямозубое.
Конструирование корпусных деталей
Корпус предназначен для размещения в нем деталей узлов для обеспечения смазки передач и подшипников для предохранения деталей от загрязнения и для восприятия усилий возникающих при работе. Он должен быть достаточно прочным и жестким так как при деформациях корпуса возникает перекос валов который приводит к неравномерности распределения нагрузки по длине зубьев зубчатых колес.
Корпус состоит из стенок бобышек и фланцев представляющих собой единое целое и для повышения жесткости усиленное ребрами. Корпусные детали в серийном производстве изготовляют литьем из чугуна марки не ниже СЧ15.
Для удобства монтажа деталей корпус делают разъемным. В горизонтальных редукторах плоскость разъема проходит по осям валов.
Конструируем литой корпус традиционного типа (с приливами и ребрами снаружи).
Толщина стенок основания корпуса и крышки редуктора:
Толщина фланцев пояса корпуса и пояса крышки:
нижний пояс корпуса без бобышки:
Толщина ребер корпуса: m = (085 1)*= (085 1)*10 = 85 10 =10 мм;
Толщина ребер крышки: m1=(085 1)*1 = (085 1)*8 = 68 8 = 8 мм ;
Диаметр болтов крепления редуктора к раме:
принимаем болты с резьбой М20.
- диаметр стяжных болтов:
Принимаем болты с резьбой М16.
б)соединяющих основание корпуса с крышкой корпуса:
Принимаем d3=10 мм (по конструктивным соображениям) принимаем болты с резьбой М10.;
- расстояние между стяжными болтами: (10 15)d3=(10 15)*10=120 мм
Ширина фланцев: К=27d
верхнего К1=27 ·10=27 мм;
нижнего К2=27· 20=54 мм.
Толщину стенок крышек подшипников принимаем в зависимости от диаметра самого подшипника.
Минимальный зазор между внутренней стенкой корпуса и торцовой поверхностью зубчатых колес рекомендуется в пределах
Расстояние между торцами двух цилиндрических колес рекомендуется в пределах x2=(03 05)*x1. Берем х2=5 мм
Глубину основания Н определяем конструктивно исходя из следующих соображений: диаметр самого большого зубчатого колеса - это диаметр цилиндрического зубчатого колеса тихоходной ступени. Глубина корпуса считая от оси зубчатого колеса должна быть больше половины диаметра вершин зубьев этого колеса то есть Dа2=3602=180 мм. Положение дна редуктора определяем расстоянием х3>(4·х1) до вершины зуба цилиндрического колеса. Берем х3=41 мм. Исходя из этих условий определяем:
Н =(Da2) + х3 = 221 мм.
Для подъема редуктора вместо рым-болтов в литье выполняют уши. Взаимное положение основания корпуса и крышки корпуса фиксируют двумя штифтами устанавливаемыми с натягом во фланце корпуса на возможно большем расстоянии друг от друга. Диаметр штифта dшт=(05 07)d3=(05 07)·10=5 7. Назначаем по конструктивным соображениям dшт=6 мм.
Чтобы предотвратить вытекание масла через плоскость разъема места разъема смазывают герметиком. Прокладки в плоскости разъема не ставят т.к. при этом нарушается посадка подшипников в корпус.
На крышке редуктора для осмотра зацепления и заливки масла предусмотрено окно (люк). Его закрывают литой крышкой. Чтобы внутрь корпуса извне не засасывалась пыль под крышку ставят прокладку из картона толщиной 05 15 мм.
Ручка крышки люка со сверленными внутри нее отверстиями служит одновременно отдушиной предотвращая повышение давления воздушной среды внутри редуктора и просачивание воздуха со взвешенными частицами масла через уплотнительные узлы валов и места соединения деталей корпуса. Ручку закрепляют в крышке люка развальцовкой.
Для слива масла и промывки редуктора в нижней части корпуса имеется отверстие с резьбой. Отверстие закрывают пробкой с прокладкой из меди алюминия или резины.
Для контроля уровня масла используется жезловый маслоуказатель.
Выбор смазочных материалов и системы смазывания
1 Смазывание зубчатых передач
Так как окружная скорость зубчатых колес быстроходной ступени невелика (V=27 мс) то для смазывания зубчатых передач используем картерную смазочную систему. В корпус редуктора заливается масло так чтобы коническое колесо было погружено в него на всю ширину венца. Колеса при вращении увлекают масло разбрызгивая его внутри корпуса. Масло попадает на внутренние стенки корпуса откуда стекает в нижнюю его часть. Внутри корпуса образуется взвесь частиц масла в воздухе которая покрывает поверхности расположенных внутри корпуса деталей.
Чем выше окружная скорость колеса тем меньше должна быть вязкость масла и чем выше контактные давления в зацеплении тем большей вязкостью должно обладать масло.
Рекомендуемую кинематическую вязкость в зависимости от окружной скорости и контактных напряжений выбираем из таблицы. По результатам расчетов на прочность зубчатых передач наибольшее контактное напряжение действует в коническом зацеплении и составляет H=49757 МПа. Окружная скорость колес V=27 мс. Для этих данных вязкость масла при 40С равна =28 мм2с. По таблице подбираем марку масла И-Г-А-32 где И - индустриальное масло Г- группа масел по назначению (для гидравлических систем) А – группа по эксплуатационным свойствам (без присадок) 32 – класс кинематической вязкости (среднее значение вязкости в сСт при 40С).
2 Смазывание подшипниковых узлов
Оцениваем возможность смазывания подшипников промежуточного и тихоходного валов масляным туманом от разбрызгивания масла колесами при окунании их в масляную ванну редуктора. Скорость быстроходного колеса V=27 мс а масляный туман образуется при скорости более 3 мс. Следовательно смазка подшипников будет недостаточной поэтому для опор качения назначаем пластичную смазку Литол-24. В связи с этим перед подшипниками устанавливаем мазеудерживающие кольца.
Конструирование сварной рамы
При монтаже привода состоящего из электродвигателя редуктора промежуточных передач должны быть выдержаны определенные требования точности относительно положения узлов. Для этого узлы устанавливают на сварных рамах. При единичном производстве рамы сваривают из элементов сортового проката: швеллеров уголков полос листов.
В качестве опорной конструкции выбираем раму сварную. Длина рамы L=1175 мм. Высоту рамы назначим из условий жесткости H=01L=1175 мм. Для высоты рамы H=120 мм выбираем по ГОСТ 8240-72 швеллер №12 высотой h=120 мм. Для длины рамы L=1175 мм выбираем фундаментные болты диаметром М20 число болтов – 8. С целью выравнивания осей вращения ременной передачи в горизонтальной плоскости в конструкции рамы предусматриваем надстройку под установку электродвигателя. Для этого используем неравнополочный уголок 655. Межосевое расстояние ременной передачи аw=362 мм. Для натяжения ременной передачи электродвигатель устанавливаем в салазках.
Данный курсовой проект помог мне освоить опыт проектирования который является основой для дальнейшей конструкторской работы а также для выполнения курсовых проектов по специальным дисциплинам и дипломному проекту.
При самостоятельной работе над проектом у студента вырабатывается умение выбирать оптимальные варианты полученных решении (расчетов конструирования компоновки). Выполнение этой задачи значительно облегчает использование систем автоматизированного проектирования. Их применение уменьшает трудоемкость расчетов обеспечивает точность вычислений позволяет оптимизировать конструкцию по массе габаритам и другим параметрам.
В объеме курсового проекта такая оптимизация произведена при проектировании двухступенчатого редуктора с обеспечением условий равнопрочности деталей с минимальным суммарным межосевым расстоянием разбивке общего передаточного числа редуктора между отдельными его ступенями и т. д.
Данное задание является комплексной инженерной задачей включающей кинематические и силовые расчеты и компоновку составляющих элементов в едином агрегате.
В результате работы был создан пакет конструкторской документации и проведены расчеты технических характеристик привода.
Детали машин и основы конструирования Под ред. М.Н. Ерохина. - М.: КолосС 2005. - 462 с.: ил.
Дунаев П.Ф. Леликов О.П. Конструирование узлов и деталей машин: Учеб. пособие для машиностроит. спец. вузов. - 4-е изд. перераб. и доп. - М.: Высш. шк. 2005 - 416с. ил.
Трофимов В.Н. Основы конструирования машин:Методическое
руководство к курсовому проекту. - Глазов: ГФ ИжГТУ 2001. - 109 с.
Анурьев В. И. Справочник конструктора-машинострителя. В 3-х т. Т. 2.-5-е изд. перераб. и доп.-М.: Машиностроение 1979.-559 с. ил.
Дунаев П.Ф. Леликов О.П. Конструирование узлов и деталей машин:Учеб.пособие для машиностроит. спец. вузов. – 4-е изд. перераб. и доп. –М.: Высш. шк. 2005 – 416с. ил.
редуктор.cdw

Техническая характеристика.
Частота вращения выходного вала
Передаточное число редуктора 12
Вращающий момент на выходном валу
Технические требования.
Плоскость разъема корпуса и крышки редуктора покрыть
герметиком УТ-34 поГОСТ 24285-80 при окончательной сборке.
В редуктор залить масло индустриальное марки И-Г-А-35
Необработанные поверхностилитых деталей
масляной ванне редуктора
должны иметь маслостойкое покрытие
Эмаль ВЛ-515 красно-коричневая.
Допускается опорные поверхности редуктора не окрашивать.
Наружные поверхности редуктора покрыть атмосферостойким
покрытием Эмаль МЛ-152 синяя.
Для смазки подшипников применять Литол-24 ГОСТ 21150-87.
Остальные ТТ по ГОСТ Р 50891-96
*Размеры для справок.
общий вид привода.cdw

Ассинхронная частота
Двухступенчатый цилиндрический
им М. Т. Калашникова)
Технические требования.
*Размеры для справок.
Натяжение ременной передачи осуществлять путём
перемещениядвигателя по салазкам (поз. 3).
Спецификация редуктор.spw

Кольцо мазеудерживающее
Кольцо уплотнительное
Прокладка регулировочная
Болт М6х18 ГОСТ 15589-70
Болт М10х30 ГОСТ 15589-70
Болт М10х35 ГОСТ 15589-70
Болт М16х130 ГОСТ 7798-70
Гайка М10 ГОСТ 5915-70
Гайка М16 ГОСТ 5915-70
4-017-19 ГОСТ 9833-73
Манжета 1-40х62-1 ГОСТ 8752-79
Манжета 1-75х130-1 ГОСТ 8752-79
Маслоуказатель II-30 ГОСТ 380-71
Подшипник 308 ГОСТ 8338-75
Подшипник 309 ГОСТ 8338-75
Подшипник 215 ГОСТ 8338-75
Шайба 10 ГОСТ 6402-70
Шайба 16 ГОСТ 6402-70
Шпонка 12х8х80 ГОСТ 23360-78
Шпонка 22х14х125 ГОСТ 23360-78
Штифт 6х35 ГОСТ 9464-79
Масло И-Г-А-35 ГОСТ 20779-75
входной вал.frw

промежуточный вал1.frw

промежуточный вал.frw

входной вал1.frw

Рекомендуемые чертежи
- 24.01.2023
- 13.04.2024
- 24.01.2023