Нормирование точности посадки подшипников



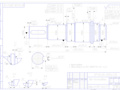
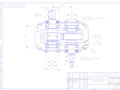
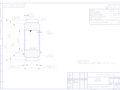
- Добавлен: 25.10.2022
- Размер: 605 KB
- Закачек: 0
Узнать, как скачать этот материал
Подписаться на ежедневные обновления каталога:
Описание
Нормирование точности посадки подшипников
Состав проекта
![]() |
![]() ![]() ![]() |
![]() ![]() |
![]() ![]() |
![]() ![]() |
![]() ![]() ![]() ![]() |
![]() ![]() ![]() ![]() |
![]() ![]() ![]() ![]() |
Дополнительная информация
Контент чертежей
Вал Сеч.dwg

колесо сечих.dwg

редуктор сечих.dwg

Рекомендуемые чертежи
Свободное скачивание на сегодня
Обновление через: 10 часов 29 минут