Наклонно - горизонтальный пластинчатый конвейер для транспортирования калийной руды




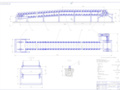
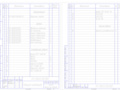
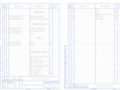
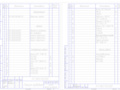
- Добавлен: 25.10.2022
- Размер: 3 MB
- Закачек: 1
Описание
Состав проекта
![]() |
![]() |
![]() ![]() ![]() ![]() |
![]() ![]() ![]() |
![]() |
![]() ![]() ![]() ![]() |
![]() ![]() ![]() ![]() |
![]() ![]() ![]() |
![]() ![]() ![]() |
![]() ![]() ![]() |
![]() ![]() ![]() |
![]() ![]() ![]() |
![]() ![]() ![]() |
![]() ![]() ![]() ![]() |
![]() ![]() ![]() ![]() |
![]() ![]() ![]() |
![]() ![]() ![]() |
![]() ![]() ![]() ![]() |
![]() |
![]() ![]() ![]() ![]() |
Дополнительная информация
Stantsia_natyazhnaya.cdw

Spetsifikatsia_k_obschemu_vidu.spw

Skhema_kinematicheskaya_2.cdw

Spetsifikatsia_k_privodnoy.spw

Stantsia_privodnaya.cdw

Spetsifikatsia_k_natyazhnoy.spw

Obschy_vid.cdw

Рекомендуемые чертежи
- 24.01.2023