Наклонно-горизонтальный ленточный конвейер




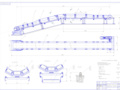
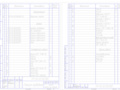
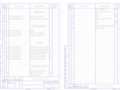
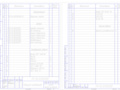
- Добавлен: 25.10.2022
- Размер: 2 MB
- Закачек: 1
Описание
Состав проекта
![]() |
![]() |
![]() ![]() |
![]() ![]() ![]() ![]() |
![]() ![]() |
![]() ![]() |
![]() ![]() |
![]() ![]() ![]() ![]() |
![]() ![]() ![]() ![]() |
![]() ![]() |
![]() ![]() ![]() ![]() |
![]() ![]() |
![]() ![]() ![]() ![]() |
![]() ![]() ![]() ![]() |
![]() ![]() |
![]() ![]() ![]() ![]() |
![]() |
![]() ![]() ![]() |
![]() ![]() ![]() |
Дополнительная информация
Спецификация к натяжной.dwg

Схема кинематическая.dwg

Общий вид.dwg

Спецификация к общему виду.dwg

Натяжная станция.dwg

Приводная станция.dwg

Спецификация к приводной.dwg

Рекомендуемые чертежи
- 24.01.2023