Scheme of strapping of the VPU of the heating power plant


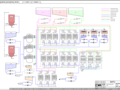
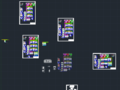
- Added: 17.04.2022
- Size: 1 MB
- Downloads: 2
Description
COURSE PROJECT ON THE DISCIPLINE "WATER TREATMENT WATER-CHEMICAL REGIME OF THERMAL POWER PLANTS"
The main reasons why water has become indispensable in thermal energy processes are the following:
- With an equal increment of temperature, it absorbs heat more than any other inorganic substance common in nature;
- In the process of evaporation, at atmospheric pressure, water increases in volume by 1600 times, forming a vapor capable of carrying a large amount of water;
- It is not scarce and relatively cheap.
For these reasons, in the energy sector, water is used in the process of electricity production, as a coolant of the working medium, raw materials, solvent, etc.
As a raw material, water serves to replenish losses in the main steam-water raw materials of KES, as well as in heat supply systems, for steam generation.
The main amount of water at the KES (98%) is used for condensation of steam spent in the turbine, in the cooling systems of the electric generator, in oil cooling systems and in other heat exchangers.
At thermal power plants, water is the working body of steam power plants, and is also used for condensation of spent steam, cooling of mechanical and electrical units, as a coolant for heat supply. There are water losses through turbine seals, with boiler purging, imperfection of heat networks, non-return of steam from production, etc., which must be replenished.
The VPU is responsible for the preparation of make-up water for boilers and heating networks. Its scheme depends on the water quality requirements for the equipment installed at the KES, as well as on the source of water supply to the IES.
In this work, it is necessary to design the water-chemical complex of the KES, which operates seven steam generators of the P-78 type (PP-1650-25-545), seven turbines of the K-500-240 type; the source of technical water supply is the lake; type of fuel - fuel oil.
For more efficient operation of the TPP equipment, an adjustment of the chemical composition of the coolant according to the established WCP is applied. In particular, the following can be dosed into the boiler water: ammonia, hydrazine, oxygen. Also, in the case of using cooling towers, water is adjusted to cool the condensers.
Project's Content
![]() ![]() ![]() |
![]() ![]() ![]() |
Additional information
Contents
Introduction
1. Selection of water supply source, analysis of source water quality indicators
2. Substantiation of the method and selection of the makeup water treatment scheme of TPP boilers
3. Sketch of selected GPU diagram and recalculation of water quality indicators change by individual treatment stages
4. Complete Process Description for Water Treatment Stages
5. Determination of capacity of water treatment plants for boiler and heating network makeup
6. Calculation of TPP water treatment plant
6.1. Calculation of demineralizing part of ERP
6.1.1. Calculation of FDS group
6.1.2. Calculation of anionite filters of the second stage A
6.1.3. Calculation of second stage cationite filters H
6.1.4. Calculation of anionite filters of the first stage A
6.1.5. Calculation of cationite filters of the first stage H
6.2. Calculation of heating system makeup diagram
6.3. Calculation of pre-cleaning scheme
6.3.1. Calculation of Clarifying Filters
6.3.2. Calculation of clarifiers
6.3.3. Calculation and selection of decarbonizer
6.4. Analysis of ERP calculation results
6.5. STP equipment layout
7. Thermal power plant water-chemical mode
7.1. Quality standards of feedwater and superheated steam at TPP
7.2. Quality standards of feed water of heating systems and network water
7.3. Main measures to maintain the selected WC TPP
7.4. Methods of coolant correction
7.5. Characteristics of condensate flows at CES and their cleaning circuits
8. Selection and description of TPP service water supply system
8.1. Purpose of the system and calculation of TPP requirements for technical water
8.2. Calculation and selection of cooling system
8.3. Selection of circulation pumps and their layout
8.4. Cooling system WC
Conclusion
Literature
Introduction
The main reasons why water has become indispensable in thermal energy processes are the following:
At an equal temperature increment, it absorbs more heat than any other naturally occurring inorganic substance;
During evaporation, at atmospheric pressure, water increases in volume by 1600 times, forming steam capable of carrying a large amount of water;
It is not scarce and relatively cheap.
For these reasons, in power engineering, water is used in the process of power generation, as coolant of working medium, raw materials, solvent, etc.
As a raw material, water serves to compensate for losses in the main steam-water raw materials of CES, as well as in heat supply systems, for steam generation.
The main amount of water at the CES (98%) is used for condensation of steam spent in the turbine, in cooling systems of the electric generator, in cooling oil systems and in other heat exchangers.
At thermal electric stations, water is the working medium of steam power plants, and is also used for condensation of spent steam, cooling of mechanical and electrical units, as a heat carrier for heat supply. There are water losses through turbine seals, with boiler blowdown, imperfection of heating networks, non-return of steam from production, etc., which need to be replenished.
The STP is responsible for the preparation of make-up water for boilers and heating networks. Its scheme depends on the water quality requirements for the equipment installed on the CES, as well as on the source of water supply to the CES.
In this work, it is necessary to design the CES water-chemical complex, which operates seven steam generators of type P78 (PP165025545), seven turbines of type K500240; technical water supply source - lake; type of fuel - fuel oil.
For more efficient operation of the TPP equipment, correction of the chemical composition of the coolant according to the installed WC is used. In particular, ammonia, hydrazine, oxygen can be dosed into pit water. Also, in the case of cooling towers, water is corrected to cool the condensers.
Cooling system WC
The quality of water used in TPP water cooling systems is not normalized by any quantitative indicators. Thus, the main requirement for the quality of cooling water, in addition to the temperature that should ensure normal cooling of the turbine condensers, is that it does not cause undesirable deposits in the cooling system, as well as corrosion of structural materials.
The purity criterion of the cooling surface of the turbine condensers and the main indicator for chemical cleaning of the pipe system of condensers is the difference between the temperature of cooling water and condensate. In order not to disturb the vital activities of organisms living in this water, the chemical treatment of cooling water must be carried out with special care. The main purpose of such treatment is to eliminate biological fouling of turbine condensers and main pipelines.
In this course project, the type of cooling system is a lake, in which the main problem is the vital activity of organisms living in this water and aquatic vegetation, which disrupts the distribution of water along the cross section of coolers, reduces the surface of the evaporation mirror, which ultimately leads to an increase in water temperature.
To combat aquatic vegetation, a biological method is used - breeding fish in cooling ponds that feed on this vegetation.
To prevent biological fouling, water is treated with oxidizing agents or toxic substances: liquid chlorine, chlorine lime, copper cuprous and the like. Water chlorination is desirable under conditions under which the HClO is mainly in molecular form, i.e. at pH < 7. The required amount of chlorine for bactericidal treatment of water is determined experimentally taking into account the specified concentration of residual free chlorine equal to 0.1-0.2 mg/dm3. Chlorine is introduced into treated water in the form of prepared chlorine water using a water jet ejector. Dosing is carried out with interruptions lasting 40-60 minutes once or three times a day, since bacteria can adapt to a change in the situation with a constant supply of chlorine.
Positive results in the fight against shell fouling are obtained by the use of cathodic protection by hanging on insulators along the axis of the pipeline of a steel rod - anode - with a diameter of 30-40 mm, to which a direct current is supplied. Current density at cathode (pipeline) in summer period should be 0.4-0.6 A/m, and in winter period - 0.16-0.25 A/m.
When treating water with potent inorganic substances, it is necessary to remember their interaction with the flora and fauna of natural reservoirs and watercourses when discharging or purging water from cooling systems. In particular, it is therefore not recommended to use CuSO4 in straight-flow cooling systems. This method is only suitable for recycled systems under strict control of the discharged water. The copper concentration in the discharge water should not exceed 0.01 mg/dm3, and free chlorine should be completely absent.
Ball cleaning of turbine condensers cooling surface is most promising. Elastic balls made of spongy rubber with diameter 1.0-1.5 mm more than diameter of cleaned tubes, when passing along them, due to tight adjoining to walls, prevent deposits of contaminants of any nature. The use of this cleaning method as a prophylactic means for maintaining the purity of the condenser tubes makes it possible to avoid the deterioration of the vacuum in the condenser due to contaminants over the entire period of operation, as well as to eliminate labor-intensive mechanical or acid cleaning of the condenser tubes.
The ball treatment system consists of a filter for preliminary purification of water from coarse debris; filter washing pump, ball catcher designed to collect and return balls into cycle; pump for circulation of balls; loading chamber for introduction of balls into circulation circuit, as well as collection and removal of spent balls; electrified valves and system automation equipment.
Balls are produced with diameters of 24, 26, 28 and 30 mm of various hardness: soft, standard hardness, hard, increased hardness and ultra-hard balls. Part of the balls can be produced with a corundum belt. The hardness of the balls is selected depending on the difference in pressure of the cooling water before and after the condenser (hydraulic resistance), the nature and intensity of deposits, equipment operation modes, etc.
The number of disposable charge balls is 8-10% of the number of tubes in the condenser. The balls can be operated continuously or periodically (1-2 hours per shift, day, etc.) depending on the type of deposits in the tubes, the intensity of pollution, the chemical composition of the cooling water.
Conclusion
In the course project, a water treatment plant was developed, selected by the WC, and the CES technical water supply system with a capacity of 3500 MW was calculated.
In the first part of the project, the parameters of the source water were studied, their recalculation into megaq/kg was made. Then a water treatment scheme was chosen: pre-treatment - coagulation, demineralizing part - ion exchange (three-stage scheme), ion exchange (Naionite filters) is used to prepare make-up water in the heating system at the second stage of treatment.
Next, the source water quality indicators were recalculated according to the individual treatment stages and a full description of the processes taking place at the ERP.
Calculated the STP scheme and determined which equipment should be installed at the station .
In the second part of the course design, water-chemical modes were described and the optimal mode for this station, water and steam quality standards, the characteristics of condensate flows and their purification methods were chosen.
As a result, neutral oxidative VCR was chosen.
In the third section, the CES service water supply scheme was calculated and described. The system requires a lake.
The system for arrangement of circulation pumps with turbine condensers is block. Therefore, it has been determined that 14 pieces of Op6185 axial circulation pumps are used.
ВХР турбины К-500-240.dwg