Modernization of Kamaz-5350 fuel system


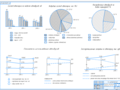
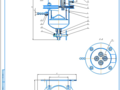
- Added: 16.01.2021
- Size: 2 MB
- Downloads: 3
Description
Detailed upgrade of Kamaz-5350 fuel system
Project's Content
![]() ![]() ![]() ![]() |
![]() ![]() ![]() ![]() |
![]() ![]() ![]() ![]() |
![]() ![]() ![]() ![]() |
![]() ![]() ![]() ![]() |
![]() ![]() ![]() ![]() |
![]() ![]() ![]() ![]() |
![]() ![]() ![]() ![]() |
![]() ![]() ![]() ![]() |
![]() ![]() ![]() ![]() |
![]() ![]() ![]() ![]() |
![]() ![]() ![]() ![]() |
![]() ![]() ![]() ![]() |
![]() ![]() ![]() ![]() |
![]() ![]() ![]() ![]() |
![]() ![]() ![]() |
![]() ![]() ![]() ![]() |
![]() ![]() ![]() ![]() |
![]() ![]() ![]() ![]() |
![]() ![]() ![]() ![]() |
![]() ![]() ![]() ![]() |
![]() ![]() ![]() ![]() |
Additional information
Report
Dear Chairman and members of the State Certification Commission. Let me present to you a diploma project on the topic: "Improvement of the power system of the KamAZ740.31 diesel engine."
At the beginning of the work on the diploma project, we conducted an analysis of production activities. As a result of the analysis, we found that the company already incurs considerable costs for repairing the fuel equipment of the new KamAZ740.31 engines.
The main reason for the decrease in resource and premature failure of fuel equipment is the low quality of diesel fuel, namely the content of water and abrasive particles of the pollutant in it. Mainly, water and particles accumulate during transportation, storage, refueling and operation. Water is the result of condensation, which occurs at temperature differences, which is characteristic of our climate. It should be noted that water is most dangerous for precision pairs of fuel equipment - nozzle sprayers and TNVD plungers.
In this regard, we conducted an analysis of the existing designs of diesel power systems and fuel purification filters. As a result, it was revealed that the most promising is the flowing diesel power system, which has the least number of disadvantages. A review and analysis of the filters of the considered power supply systems showed that conventional filters and sump filters do not provide a sufficiently high separation of water from fuel. Typically, this is a finely dispersed solution of water and fuel formed as a result of intense mixing of water and fuel in the tank and fuel lines. The most effective purification method at present is separation. Sheet No. 3 shows a diagram of the SEPAR-2000 combined filter-separator, which provides a high degree of separation of fine water from fuel, but it is expensive and its installation involves the conversion of the entire diesel power system. It should also be noted that the effect of vibration transmitted to the fine filter from the engine adversely affects the fine cleaning. This is due to the fact that particles retained in the pores of the filter element under the influence of vibration leak through the pores of the filter element, which significantly reduces the fineness of FTO purification.
As a result of the analysis, we offer an improved power supply system for the KamAZ740.31 diesel engine. It differs from the basic introduction of a filter separator on the low pressure line, which acts as a water separator and a coarse fuel filter.
The main operating element of the filter is a hydrocyclone 13. Fuel is injected into the hydrocyclone from the pressure cavity 14 through an opening 19 tangential to the circumference of the inner surface of the hydrocyclone. As a result, the fuel spins along the entire length of the hydrocyclone, resulting in centrifugal forces. The bulk of the fuel is directed through the upper outlet hole to the intake cavity 11 and further to the FTP, and about 5% of the fuel with enlarged water particles is directed to the settling cavity 16 and, after additional settling, is directed to the suction pipeline of the settling filter.
The design of the filter-separator was calculated. Calculation of the main operating element - hydrocyclone - is made on the basis of maximum fuel consumption by the engine, i.e. at its operation with maximum power. It was obtained that with an engine flow rate of 46.6 l/h, it is enough to install one hydrocyclone with a circle diameter at the location of the inlet hole of 7.5 mm. But it is known that not all fuel pumped by a low pressure fuel pump is used in engine operation. About 75% of the fuel is returned to the tank, which is characteristic of the diesel flow power system. Calculations have shown that the most effective is the use of small-diameter hydrocyclones, four hydrocyclones operating in parallel were installed in one housing. In a small-diameter hydrocyclone, higher centrifugal forces arise, and therefore higher cleaning quality. Due to the fact that part of the fuel from the hydrocyclone is forced to return to the suction pipeline, an additional inertial settler 15 is installed in the settling cavity, operating simultaneously and as a sedimentation device. The assembly drawing of the filter-separator and the working drawings of some of its parts have been compiled. As a result, we got a filter of fairly simple design, small size (163x97x80) and high throughput.
The filter-separator is mounted on the frame spar near the coarse filter. With this mounting, we undergo the smallest conversion of the basic fuel lines. The installation diagram of the filter-separator shows the main installation dimensions and changes in the connections of the fuel pipelines. Also, to eliminate the transmission of vibration from the engine to the FTO, its attachment point was transferred to the attachment frame of the radiator expansion tank, i.e., to the bus body, without changing the location of the FTO itself, which also does not require replacing the basic fuel lines with others, as if we had mounted it in a new place.
As a result of the introduction of the filter-separator, an improved maintenance flow sheet is proposed. Changes were made to daily maintenance, TO1, TO-2, which do not require a lot of labor. At ETO it is required to check in addition tightness of connections of a filtraseparator, at TO-1 - to merge a sediment, at TO-2 - to make washing and expulsion of the filter.
Measures have also been developed to ensure the safety and environmental friendliness of the project.
At the end, a technical and economic assessment of the project was carried out, from which it can be seen that with capital investments to improve the power system of one KamAZ740.31 diesel engine in 395.85 rubles, the payback period will be about 4 months.
9.ТЭП.cdw

1.АХД 2 вариант.cdw

5.Сборочный.cdw

На крышку верхнюю с докум.cdw

1.АХД.cdw

2.Обзор схем топливных систем.cdw

Уплотнение.cdw

Пластина.cdw

9.ТЭП мой.cdw

Спецификация 1.cdw

На крышку верхнюю.cdw

8.ТО.cdw

4.Предлагаемая конструкция.cdw

3.Обзор фильтров.cdw

Гидроциклон изм.cdw

Насадок изм.cdw

Крышка верхняя.cdw

Кронштейн измен.cdw

7.Общий вид 1.cdw

Спецификация 2.cdw

7.Общий вид 2.cdw
