Development of the main gear of a caterpillar tractor (prototype dt-75)



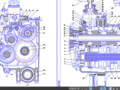
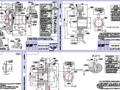
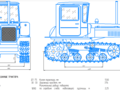
- Added: 24.12.2021
- Size: 6 MB
- Downloads: 1
Description
In this course project, a gearbox is developed. For the basic model, the gearbox of the DT-75 tractor was taken.
An analysis of the existing designs of gearboxes was carried out in the work. Also, the kinematic and energy calculations of the gears, the calculation of the parameters of the gearing of the gear train and the strength calculation of the shaft were made. Measures for operation and maintenance have been developed.
Explanatory note: pages: 54, illustrations: 12, tables: 3.
It also contains all the developed drawings of the A1 format, detailing (drawings are also presented separately) and the specification.
Project's Content
![]() ![]() ![]() ![]() |
![]() ![]() ![]() |
![]() ![]() ![]() |
![]() ![]() ![]() |
![]() ![]() ![]() ![]() |
![]() ![]() ![]() |
![]() ![]() ![]() ![]() |
![]() ![]() ![]() ![]() |
![]() ![]() ![]() ![]() |
![]() ![]() ![]() ![]() |
![]() ![]() ![]() |
![]() ![]() ![]() ![]() |
![]() ![]() ![]() ![]() |
![]() ![]() ![]() |
![]() ![]() ![]() ![]() |
![]() ![]() ![]() |
![]() ![]() ![]() ![]() |
![]() ![]() ![]() |
![]() ![]() ![]() |
![]() ![]() ![]() |
![]() ![]() ![]() |
![]() ![]() ![]() ![]() |
![]() ![]() ![]() |
![]() ![]() ![]() ![]() |
Additional information
Introduction
The increase in productivity in agricultural production, inextricably linked with the increase in speeds and energy saturation of promising tractors, requires further improvement in their operational qualities. In this regard, the use of stepless transmissions on tractors - hydromechanical and hydraulic-volume, with a high degree of automation of operation and good protective properties, ensuring a high degree of engine load and its economy - can be increasingly assumed. Especially promising are transmission data on industrial tractors operating in heavier operating conditions.
At the same time, there are even greater reserves for improving the design of mechanical transmissions, which will be widely used in the future.
Two main trends in the design of mechanical transmissions can be traced. The first is to increase the reliability and durability of gearboxes made according to the usual kinematic schemes of gear boxes within the limits due to the warranty period. The second is the use of new kinematic gearbox schemes, which, with high reliability and durability, will significantly improve the performance of the tractor and its performance, will ensure gearshift without stopping the tractor, will facilitate acceleration of the tractor unit operating at increased speeds, and will expand the range of necessary speeds.
Increased wear resistance and durability of gear gears
gearboxes are achieved by using more advanced types
correction of gear teeth and reduction of misalignments in their engagement, improvement of technological process of gear and shafts manufacturing (especially splined ones) and application of new grades of steel, which are more convenient in mechanical and chemical-thermal treatment.
The same goals are met by the work on improving the overall rigidity of the gearbox crankcase, the accuracy of centering its shafts, and the reliability of its bearing assemblies. In this regard, it is characteristic to increase the hardness of the landing surfaces and install tighter fits. There is a tendency to use constant-engagement gears with no end wear in heavily loaded transmissions of powerful tractors. Instead of conventional gear shift clutches, they increasingly use pin locking clutches that are simpler and more repairable.
The design of its control mechanism has a great influence on the reliability and durability of the gearboxes.
Preferred are designs in which the control forks are stamped integrally with the control slides. It is promising to use synchronizers on the main work and transport transmissions.
Improving the sealing of its crankcase and improving the reliability of lubrication of its parts has a very significant effect on the durability of the gearboxes. This is achieved by installation of more advanced glands, sealing gaskets, protective elastic oil-resistant covers and oil reflecting devices that facilitate the operation of gland seals. For the best lubrication of the most stressed bearing units and gear engagements, the use of special oil collecting trays, drilling in axes and shafts or the installation of special tubes is characteristic. In some cases, pressure lubrication from a separate oil pump is desirable.
Gearboxes on the go can be made according to various kinematic schemes in which either all gears are switched from a tractor stop, or only gears in a given range group, and the ranges themselves are changed as in ordinary gearboxes. In addition, transmissions can be without breaking the power flow (at the time of gear change) and with its short-term break.
When using the former, a decrease in dynamic loads in the transmission of about 1.5 times is characteristic. Transmissions with short-term rupture in flow power have the advantage only when used at transport, increased speeds and fast acceleration of the tractor unit.
In such transmissions, planetary rows, multi-disc interlocking clutches with hydraulic pressing and overtaking clutches (autologists) are widely used. Blocking sleeves operating in oil have, as a rule, metal-ceramic friction surfaces. The safety factor of such couplings is approximately the same as in clutches.
Due to the fact that in agriculture, a tractor of one brand often must operate in the range of reduced speeds, within the range of 0.01-3.6 km/h, water minimizers are needed that provide the necessary speed range. Increasingly, stepless water mixers, mainly of the hydraulic volume type, are being used to control "creeping" speeds (up to 1.0 km/h).
It is also promising to combine a stepped and stepless traveler to provide a wider range of reduced speeds not available for each type individually.
Analysis of gearbox design analogues
1.1 Gearbox purpose, classification and requirements
A gearbox is a tractor transmission unit that allows changing its gear ratio.
The gearbox serves to obtain the required amount of torque on the driving wheels of the tractor at the most rational loading of its engine and to obtain different speeds of motion of the tractor forward or backward. In addition, it allows for long-term parking of the tractor when the engine is operating.
Gearboxes can be classified according to the following main features:
a) according to the method of changing the gear ratio: stepless and stepped.
Stepless transmissions are divided into mechanical, hydraulic and electric gearboxes according to the principle of operation. In stepped transmissions, the change in the given gear ratio interval is limited by the number of possible gear-gear combinations.
Due to the fact that speed transmissions are most common, further classification is given only for them.
b) according to the method of transmission formation: gears with fixed axes and gears with planetary axes.
c) according to the method of gear engagement: with movable gears (carriages) and gears of constant engagement.
Planetary transmissions controlled by brakes and friction clutches are varieties of permanent-engaged transmissions. When using planetary gearboxes and transmissions with friction clutches, there may be no clutch clutch in the tractor transmission.
d) according to the gearshift method: with the tractor stopping (actuation without load) and without stopping the tractor (actuation under load).
e) by the number of gears: modern gearboxes have from five to sixteen forward gears. Transmissions are divided into ranges: main (working), transport and delayed (seating). The main range is used to perform agricultural and other works using maximum values of thrust forces. The number of transmissions is 3-5. The transport range ensures the performance of transport work. A slow range is necessary when the tractor performs work requiring low technological speeds. At the same time, the engine power is not fully used. The number of transmissions in these ranges is 1-4.
The number of reverse gears may vary from one to a number equal to the number of forward gears. In the latter case, the box is called a box with fully reversed gears.
f) by the location of the gearbox shafts relative to the longitudinal axis of the tractor: a gearbox with longitudinal or transverse shafts. The latter make it possible in some cases to reduce the longitudinal base of the tractor and simplify the central transmission.
g) according to the design: gearboxes made in the form of an independent unit; gearboxes mounted in front of common body of tractor rear axle and gearboxes mounted in common case of transmission together with its other mechanisms.
h) according to the kinematic scheme: two-shaft (or single-pair), three-shaft (or double-pair), compound and special.
The terms two-shaft or three-shaft are associated with the number of shafts and gear engagement pairs to form a basic range transmission. A number of other shafts and gears are provided in said gearboxes for receiving reverse, transport or downshift gears.
Composite transmissions used to increase the number of transmissions are a combination of two sequentially arranged (two-shaft or three-shaft) transmissions made in a common or separate crankcase.
Special transmissions are considered to be those in which kinematic schemes differ from the above.
Gearbox requirements. In addition to the general requirements, the gearbox has a number of specific requirements, the main of which are:
a) sufficient number of gears ensuring the tractor performance within the specified range of its traction forces;
b) rational selection of gear ratios for the most economical operation with a given complex of agricultural and other tools.
Conclusion
In this course work, the gearbox was developed. The basic model was taken as the gearbox of the DT75 tractor.
An analysis of existing gearbox designs was carried out in the work. Are carried out kinematic and power calculation of transfer and also parameters of gearing of the gear transmission and strength calculation of a shaft were calculated.
Gearbox maintenance measures have been developed. There are many possibilities to improve the operability of the structure, that is, to improve the adaptability of the car to maintenance during operation. The use of centralized lubrication and bearings with disposable seasonal lubrication, increased tightness of lubricated mechanisms, unification of lubricant grades also make it possible to drastically simplify technical care and reduce its time.
The use of automatics on cars facilitates the working conditions of the driver, as well as improves productivity and quality of work. The designer must always remember that the convenience and safety of working on machines in any branch of the national economy is one of the main criteria for the perfection of the design.
ОБЩИЙ ВИД 1к1.cdw

Кинематика.cdw

Блок шестерен (право-низ).cdw

КПП ДТ-75.dwg

Спецификация.spw

КПП 2 вида.cdw

Кинематика и граф.dwg

Колесо зубчатое (право-верх).cdw

Деталировка.dwg

Кольцо (лево-низ).cdw

3.1.17_Внешний вид трактора ДТ-75.cdw

Вал-шестерня (лево-верх).cdw

Similar materials
- 20.03.2015
- 08.06.2014
Free downloading for today
Other materials
- 23.08.2014