Разработка проекта токарно-карусельного станка 1512ФЗ



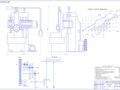
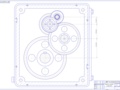
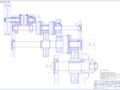
- Добавлен: 15.05.2022
- Размер: 900 KB
- Закачек: 3
Описание
Чертежи общий вид станка 1512ФЗ, Свертка чертеж, Развертка коробки скоростей чертеж. Пояснительная записка.
Состав проекта
![]() ![]() ![]() ![]() |
![]() ![]() ![]() ![]() |
![]() ![]() ![]() |
![]() ![]() ![]() ![]() |
Дополнительная информация
общий вид.cdw

Габариты станка (длина ширина высота)
Наибольший диаметр устанавливаемого изделия
Наибольшая высота устанавливаемого изделия
Наибольшая масса обрабатываемой заготовки
Наибольшее перемещение
- горизонтальное 775
Частота вращения планшайбы
обмин бесступенчатое
Регулирование подач суппорта бесступенчатое
Количество позиций револьверной головки 5
ВКР 14.15.02.01.17.01
График частот вращения
развертка коробки скоростей.cdw

Степень точности зубчатых колёс 7-Х.
Непараллельность валов не более 0
При сборке обеспечить осевой зазор в подшипниках.
При обкатке под нагрузкой
уровень шума не должен
Температура картерного масла не выше 60
ВКР 14.15.02.01.17.02
записка.docx
по дисциплине «Металлорежущие станки»
на тему «Разработка проекта токарно-карусельного станка с ЧПУ»
Пояснительная записка на 41 с. в том числе 6 рисунков 4 листа чертежей.
В проекте согласно заданию разработан привод главного движения токарно-карусельного станка мод. 1512Ф3.
Разработана кинематическая схема привода и график частот вращения привода главного движения. При этом рассмотрены и проанализированы два различных варианта структурных сеток.
Выполнены проектные расчеты зубчатых колес валов и ременной передачи. Разработана компоновочная схема коробки скоростей выбраны подшипники определены конструктивные элементы отдельных деталей.
Выполнено описание системы смазки коробки скоростей указаны применяемые смазочные материалы.
В графической части выполнен технический проект коробки скоростей. Приведено описание разработанной конструкции. Отражены преимущества и недостатки этого узла в сопоставлении с базовым вариантом.
Использование электродвигателя постоянного тока позволило существенно упростить конструкцию главного привода станка при одновременном расширении его технологических возможностей:
- бесступенчатый привода главного движения.
Обоснование исходных технических данных и техническое задание на проектирование
1 Расчет и анализ режимов резания6
2 Определение мощности электродвигателя привода главного движения и выбор его типоразмера7
3 Выбор станка прототипа9
4 Служебное назначение и технические характеристики базового станка
5 Техническое задание на модернизацию станка11
Кинематический расчет привода главного движения
1 Исходные данные для расчета12
2 Кинематический расчет12
3 Выбор оптимального варианта кинематики станка14
4 Определение чисел зубьев зубчатой передачи16
5 Разработка кинематической схемы привода19
Силовой расчет привода
1 Расчет ременной передачи20
2 Необходимая частота вращения электродвигателя24
3 Определение модуля и межцентрового расстояния25
4 Расчет геометрии цилиндрических зубчатых передач27
5 Определение диаметра валов31
6 Проектировочный расчет вала32
7 Выбор подшипников качения36
8 Выбор электромагнитных муфт37
9 Описание системы смазки38
1 Проверка шпоночного соединения39
2 Проверка шлицевого соединения39
Обоснование исходных технических данных и техническое задание на проектирование
1 Расчет и анализ режимов резания
Наименьший диаметр обработки токарно-карусельного станка определяется по формуле [1 с.10]:
где Dб – наибольший обрабатываемый диаметр мм.
При определении наибольшей скорости резания vmax следует принимать:
глубину резания и подачу наименьшими;
материал заготовки – конструкционная углеродистая сталь;
материал режущей части резца – твердый сплав при наименьшей стойкости Т=25÷30мин. [12 с. 87]
При определении наименьшей скорости резания vmin следует принимать:
глубину резания и подачу наибольшими;
материал заготовки – высокопрочная легированная сталь;
материал режущей части резца – быстрорежущая сталь при стойкости Т=60÷90мин. [12 с. 87]
Значения vmax vmin определяются при работе без охлаждения.[12 с.90]
Максимальная скорость резания для точения и растачивания диаметра Dм=500 мм определяется по формуле [12 с. 88]:
где Сv – коэффициент зависящий от свойств обрабатываемого материала;
Т – стойкость инструмента мин;
t – глубина резания мм;
НВ – твердость материала;
m x y n – показатели степени.
Минимальная скорость резания для точения и растачивания диаметра Dб=1250 мм определяется по формуле [12 с. 88]:
Максимальная скорость резания для отрезки и прорезки канавок диаметра Dм=500 мм определяется по формуле [12 с. 88]:
Минимальная скорость резания для отрезки и прорезки канавок диаметра Dб=1250 мм определяется по формуле [12 с. 88]:
Анализируя полученные результаты назначается:
за максимальную скорость резания vma
за минимальную скорость резания vmin=13ммин.
Предельные частоты вращения планшайбы nmax и nmin обмин определяются по формулам [12 с.90]:
dmax dmin – предельные диаметры обработки мм.
2 Определение мощности электродвигателя привода главного движения и выбор его типоразмера
Эффективная мощность Nэmax кВт определяется по формуле [12 с. 90]:
где Pzmax – сила определяющая нагрузку на механизм главного движения определяется при следующих условиях:
глубину резания и подача наибольшие;
материал режущей части резца – быстрорежущая сталь при стойкости Т=15÷30мин. [12 с. 90]
Максимальная сила резания определяется по формуле [5 с.271]:
где Ср – коэффициент силы резания;
n у х – показатели степени;
t – глубина резания;
Kp – общий поправочный коэффициент учитывающий фактические условия резания Кр=КмрКφрКγрКλрКrр
Кмр Кφр Кγр Кλр Кrр – поправочные коэффициенты учитывающие влияние геометрических параметров режущей части инструмента на составляющие силы резания.
V – скорость резания для условий существования Pzmax.
В соответствии с рекомендациями литературы [6 с.31] и сравнения с мощностью нескольких аналогичных станков современной конструкции для привода главного движения токарно-карусельного станка с ЧПУ назначается электродвигатель постоянного тока 4ПФ180S. Применение данного привода позволяет бесступенчато регулировать частоту вращения планшайбы повышает производительность станка благодаря точной настройке оптимальной скорости резания и ее регулирования в процессе выполнения цикла обработки.
Технические характеристики электродвигателя 4ПФ180S взяты [17]:
номинальная частота вращения nном=875 обмин;
максимальная частота вращения nma
номинальный момент 327 Нм;
Эскиз электродвигателя с габаритными присоединительными и установочными размерами изображен на рисунке 1.
b1=16 мм; b10=279 мм; b30=693 мм; b31=502 мм; d1=55 мм.
Рисунок 1 – Эскиз электродвигателя 4ПФ180S
3 Выбор станка прототипа
Основным параметром токарно-карусельного станка является наибольший диаметр устанавливаемой детали [13 с.274]. Исходя из данных в задании производится обзор существующих моделей в таблице 1.
Таблица 1 - Обзор существующих моделей
характеристика станка
Наибольший диаметр обрабатываемой заготовки мм
Наибольшая высота обрабатываемой заготовки мм
Наибольшая масса обрабатываемой заготовки кг
Наибольшее перемещение вертикального суппорта:
Частота вращения планшайбы обмин
Регулирование подач суппорта
Подача суппорта вертикальная и горизонтальная мммин
Мощность электродвигателя главного привода кВт
Сопоставив все данные по техническим характеристикам станков за базовую модель назначается 1512Ф3 т.к. данный токарно-карусельный станок подходит по основным параметрам в соответствии с заданием и имеет в наличии техническую документацию.
4 Служебное назначение и технические характеристики базового станка
Служебное назначение станка 1512Ф3
Станок предназначен для обработки различных изделий из черных и цветных металлов. На станке можно производить обтачивание и растачивание поверхностей деталей с прямолинейными и криволинейными образующими протачивание торцевых поверхностей прорезание кольцевых канавок сверление зенкерование и развертывание центральных отверстий нарезание резьб резцами.
Станок оснащен устройством ЧПУ типа Н55-2 осуществляющим автоматическое управление верхним револьверным суппортом и приводом главного движения по заданной программе вводимой с перфоленты.
Технические характеристики
Наибольший диаметр устанавливаемого изделия мм1250
Наибольший высота устанавливаемого изделия мм 1000
Диаметр планшайбы мм1120
Наибольший масса устанавливаемого изделия кг4000
Наибольшее перемещение револьверного суппорта мм
Количество позиций револьверной головки5
Наибольшая высота сечения резца мм50
Количество ступеней чисел оборотов планшайбы18
Частота вращения планшайбы обмин5-250
Регулирование подач суппортаБесступенчатое
Вертикальные и горизонтальные подачи суппорта мммин3-300
Наибольшая скорость установочных перемещений суппорта3000
Наибольший шаг нарезаемой резьбы мм40
Род токапеременный трехфазный
Мощность электродвигателя привода главного движения кВт30
5 Техническое задание на модернизацию станка
Техническое задание на модернизацию станка 1512Ф3
Полученные в ходе обоснования исходных данных технические характеристики и данные оформляются в виде технического задания которое приводится в таблице 2.
Таблица 2 – Техническое задание на разработку привода главного движения станка 1512Ф3
Наименование и область применения
Станок 1512Ф3 токарно-карусельный нормальной точности предназначен для обработки больших диаметров для выполнения чистовых и получистовых операций при токарной обработке.
Задание на проект по металлорежущим станкам.
Цель и назначение разработки
Разработка привода главного движения с целью обеспечения технических характеристик полученных в результате обоснования исходных данных.
Возможность бесступенчатого регулирования частот вращения за счет использования электродвигателя постоянного тока взамен асинхронного – установленного на базовом станке.
используемая при разработке
Паспорт станка мод. 1512Ф3
Стандарты и другая справочно-нормативная документация и техническая литература.
подлежащая разработке
Пояснительная записка кинематическая схема и график частот вращения привода главного движения сборочный чертеж коробки скоростей спецификация.
1 Исходные данные для расчета:
максимальная частота вращения двигателя nдв ma
номинальная частота вращения двигателя nдв ном=875 обмин;
максимальная частота вращения планшайбы nma
минимальная частота вращения планшайбы nm
2 Кинематический расчет
Диапазон частот вращения планшайбы Д определяется по формуле [4 с.82]:
Диапазон регулирования двигателя с постоянной мощностью Ддв. N определяется по формуле [11 с.15]:
Если φ=Ддв.N>25÷3 и это неудобно для проведения расчетов можно ввести φм= где а=2. [4 с.82]
Определяется расчётное число значений z геометрического ряда частот вращения планшайбы с принятым знаменателем φ по формуле [11 с.15]:
Определяется частота вращения планшайбы n начиная с которой и выше должна передаваться полная мощность [4 с.82]:
где – третья четвёртая или иная заданная либо принятая часть диапазона частот вращения шпинделя (по расчётному числу его ступеней z).
Определяется диапазон регулирования с постоянной мощностью ДN по формуле [4]:
Определяется число ступеней привода главного движения коробки скоростей zкс по формуле [4]:
Т.к. округление числа делается в сторону уменьшения то диапазон обеспечиваемых частот будет иметь разрывы. [11]
Определяется минимальное передаточное отношение привода imin по формуле [4]:
Определяется расчётная минимальная частота вращения вала электродвигателя по формуле [4]:
Определяется диапазон регулирования двигателя Ддв по формуле []:
Определяется диапазон регулирования при постоянном моменте Ддв.М равный ДМ по формуле [4]:
Определяется диапазон регулирования коробки скоростей Дкс по формуле [4]:
Определяются частоты вращения планшайбы с постоянным моментом Дм:
n2= n1 φ=335185=6 обмин;
n3= n2 φ=6 185=11 обмин;
n4= до 19 обмин (т.к. начинается следующий диапазон).
Определяются частоты вращения планшайбы с постоянной мощностью ДN:
n2= n1 φ=19185=36 обмин;
n3= n2 φ=36185=67 обмин;
n4= n3 φ=67185=124 обмин;
n5= n4 φ=124185=224 обмин.
3 Выбор оптимального варианта кинематики станка
При выбранном числе скоростей Zкс = 4 количество передач в каждой группе и порядок расположения групп может быть различным. Для этого рассмотрим следующие варианты структурных сеток изображенных на рисунке 2.
Рисунок 2 – Варианты структурных сеток
Из рассмотренных вариантов за исходный принимается вариант Б т.к. данный вариант позволяет понизить частоту вращения электродвигателя до требуемого значения при средних значениях межцентровых расстояний колес и их размеров.
На основании структурной сетки и кинематического расчета строится график частот вращения изображенный на рисунке 3.
Рисунок 3 – График частот вращения
График зависимости мощности от частоты вращения планшайбы изображен на рисунке 4.
Рисунок 4 – График зависимости мощности от частоты вращения планшайбы
4 Определение чисел зубьев зубчатой передачи
Исходя из постоянства межосевого расстояния определяются числа зубьев по формулам [13]:
z0 – сумма чисел зубьев сопряженных колес;
К – наименьшее кратное сумм (f
zдоп – минимальное число зубьев zдоп=17.
4.1 Определяются передаточные отношения зубчатых колес между 2 и 3 валом:
Определяется сумма числителя и знаменателя передаточного отношения:
Определяется наименьшее кратное суммы будет К = 332=18
Определяется Еmin для минимального передаточного отношения i2:
полученное значение округляется до целого числа: Е=3.
Определяется сумма чисел зубьев сопряженных колес:
полученная сумма уточняется по нормали Н21 - 5 Приложение 6. [13]
Определяются числа зубьев сопряженных колес:
4.2 Определяются передаточные отношения зубчатых колес между 3 и 4 валом:
Определяется Еmin для минимального передаточного отношения i4:
полученное значение округляется до целого числа: Е=5.
полученная сумма уточняется по нормали Н21 - 5 Приложение 17. [13]
4.3 Определяются передаточные отношения зубчатых колес между 4 и 5 валом:
Определяется Еmin для минимального передаточного отношения i6:
На основании полученных значений чисел зубьев заполняется таблица 3.
Таблица 3 – Числа зубьев и передаточные отношения
Передаточное отношение
5 Разработка кинематической схемы привода
Рисунок 5 – Кинематическая схема привода
1 Расчет ременной передачи
1.1 Выбор сечения ремня
Выбирается по номограмме [16 с. 83] сечение клинового ремня Б в зависимости от мощности передаваемой шкивом равной номинальной мощности двигателя Pном=30 кВт и его частоты вращения равной частоте вращения двигателя n = 3000 обмин.
1.2 Определяется допустимый диаметр ведущего шкива
Минимально допустимый диаметр ведущего шкива [16 с. 84].
1.3 Расчетный диаметр ведущего шкива
Для повышения срока службы ремня выбираем диаметр ведущего шкива из стандартного ряда [16 с. 426].
1.4 Определяется диаметр ведомого шкива d2 мм по формуле [16 с. 84]:
где u – передаточное число клиноременной передачи u=315;
– коэффициент скольжения [16 с. 84].
Полученной значение округляется до ближайшего стандартного [16 с. 426]: d2=500 мм.
1.5 Определяется фактическое передаточное число uф и проверяется его отклонения u от заданного u по формулам [16 с. 85]:
1.6 Определяется ориентировочное межосевое расстояния а мм по формуле [16 с. 85]:
где h – высота сечения ремня Б [16 с. 418].
1.7 Определяется расчетная длина ремня l мм по формуле [16 с. 85]:
Длина ремня l округляется до ближайшего стандартного по [16 с. 418]: l=2000 мм.
1.8 Уточняется значения межосевого расстояния а по стандартной длине l по формуле [16 с. 85]:
1.9 Определяется угол обхвата ремнем ведущего шкива α1 по формуле [16 с. 85]:
1.10 Определяется скорость ремня V мс по формуле [16 с.85]:
где n1 – частота вращения ведущего шкива обмин;
1.11 Определяется частота пробега ремня U с-1 по формуле [16 с.85]:
где [U] – допускаемая частота пробегов.
1.12 Определяется допускаемая мощность [Pп] кВт передаваемая одним клиновым ремнем по формуле [16 с. 87]:
где [P0] – допускаемая приведенная мощность передаваемая одним клиновым ремнем кВт. Назначается интерполированием по [16 с. 86];
Ср – коэффициент динамичности нагрузки и длительности работы [16 с. 78];
Сα – коэффициент угла обхвата α1 на меньшем шкиве [16 с. 79];
Cz – коэффициент числа ремней в комплекте клиноремённой передачи [16 с. 80].
1.13 Определяется количество клиновых ремней Z по формуле [16 с.87]:
где Рном - номинальная мощность двигателя кВт.
1.14 Определяется сила предварительного натяжения ремня Fо Н по формуле [16 с.88]:
1.15 Определяется окружная сила Ft Н передаваемая ремнем по формуле [16 с.88]:
1.16 Определяется сила натяжения ведущей F1 и ведомой F2 ветвей Н по формуле [16 с.88]:
1.17 Определяется сила давления ремней на вал Fоп Н по формуле [16 с.88]:
1.18 Проверочный расчет
Проверяется прочность одного клинового ремня по максимальным напряжениям max Нмм2 в сечении ведущей ветви по формуле [16 с.81]:
где 1 – напряжение растяжения Нмм2;
и – напряжение изгиба Нмм2;
v– напряжения от центробежных сил Нмм2;
[]р – допускаемое напряжение растяжения для клиновых ремней Нмм2 []р=10 Нмм2.
Напряжение растяжения 1 Нмм2 определяется по формуле [16 с.81]:
где А – площадь ремня мм2 [16 с. 418].
Напряжение изгиба И Нмм2 определяется по формуле [16 с.81]:
где Еи – модуль продольной упругости при изгибе для прорезиненных ремней Нмм2 [16 с.81];
h – высота сечения клинового ремня мм [16 с.418].
Напряжение от центробежных сил v Нмм2 определяется по формуле [16 с.81]:
где ρ – плотность материала плоского ремня кгмм3 [16 с.81].
Условие прочности выполняется следовательно принятые параметры передачи принимаются за окончательные.
2 Необходимая частота вращения электродвигателя
В соответствии с графиком частот вращения рисунок 3 принятых чисел зубьев колес характеристик ременной передачи определяется необходимая частота вращения электродвигателя представленная в виде таблицы 4.
Таблица 4 – Необходимая частота вращения электродвигателя
Фактическая частота вращения nф с nmax обмин
Необходимая частота вращения электродвигателя nэд обмин
3 Определение модуля и межцентрового расстояния
Расчеты ведутся по расчетной цепи связывающей расчетную частоту вращения шпинделя с номинальной частотой вращения электродвигателя т.е. с частоты вращения 19 обмин при которой начинает передаваться полная мощность.
Для прямозубых колёс модуль определяется по формуле [8]:
где []Н – допускаемые контактные напряжения кгмм2;
[]F – допускаемые напряжения на изгиб кгмм2;
Nэ –мощность электродвигателя кВт;
nр – расчетное число оборотов шестерни при которых передается полная мощность обмин;
z – число зубьев шестерни;
k = 1 – коэффициент динамической перегрузки;
= bm = (6 10) – коэффициент ширины зубчатого венца;
y = 011 – коэффициент формы зуба.
Допускаемые контактные напряжения []Н МПа для шестерни определяется по формуле [3]:
где КHL – коэффициент долговечности принимается КHL=1; [3]
[]НО – допускаемые напряжения соответствующие числу циклов перемены напряжений МПа.[3]
где НRCср – средняя твердость выбранной марки материала шестерни. В данном случае назначается в качестве материала сталь 40Х с термической обработкой улучшение и закалка ТВЧ твердость HRC 45 50.
Допускаемые напряжения на изгиб []F МПа для шестерни определяется по формуле [3]:
где КFL – коэффициент долговечности принимается КFL=1; [3]
[]FО – допускаемые напряжения соответствующие числу циклов перемены напряжений []FО=370 МПа.[3]
Между 2 и 3 валами:
Полученное значение модуля округляется до стандартных значений: m23 = 5 мм.
Между 3 и 4 валами:
Полученное значение модуля округляется до стандартных значений: m34 = 6 мм.
Между 4 и 5 валами:
Полученное значение модуля округляется до стандартных значений: m45 = 8 мм.
Межцентровое расстояние А мм определяется по формуле [8]:
4 Расчет геометрии цилиндрических зубчатых передач
Расчеты произведены с помощью Microsoft Excel по ГОСТ 16532-70
Расчет геометрии зубчатых зацеплений между валами представлены в таблице 4 5 6.
Таблица 4 – Расчет геометрии зубчатых зацеплений между 2 и 3 валом
Обозначения и расчётные формулы
Угол наклона зуба (град)
Коэффициент высоты головки
Коэффициент обратного смещения
Коэффициенты смещения
Коэффициент радиального зазора
Проверка на подрезание
Делительное межосевое расстояние
Коэффициент суммы смещений
invαtw=(2xΣtgα)(z4+z5)+invαt
Межосевое расстояние
aw=(z4+z5)mcosαt(2coscosαtw)
Коэффициент воспринимаемого смещения
Коэффициент уравнительного смещения
da4=d4+2(hoa+x4-Δy)m
da5=d5+2(hoa+x5-Δy)m
df4=d4-2(hoa+co-x4)m
df5=d5-2(hoa+co-x5)m
Толщина зуба по делительному диметру
Толщина зуба на диаметре вершин
Sa4=da4(S4d4+invα-invαa4)
Sa5=da5(S5d5+invα-invαa5)
Толщина зуба в основном диаметре
Таблица 5 – Расчет геометрии зубчатых зацеплений между 3 и 4 валом
Таблица 6 – Расчет геометрии зубчатых зацеплений между 4 и 5 валом
5 Определение диаметра валов
Определение диаметра валов производится по формуле [9]:
где Мкр – крутящий момент Нм;
[] – условное допускаемое напряжение при кручении []=30МПа.
Крутящий момент Мкр Нм определяется по формуле [9]:
где Р – мощность Р=30 кВт;
n – частота вращения обмин.
Для приводов с бесступенчатым регулированием расчеты ведутся по расчетной цепи связывающей расчетную частоту вращения планшайбы с номинальной частотой вращения электродвигателя [10].
Расчет диаметров валов сведен в таблицу 7.
Таблица 7 – Диаметры валов
6 Проектировочный расчет вала
Проводится расчет для одного пятого вала т.к. на пятом валу возникает наибольший крутящий момент Мкр=1507895 Нм.
6.1 Определяются силы действующие в цилиндрическом зацеплении по формуле [14 с.103]:
Радиальное усилие –
6.2 Определяются реакции в опорах тихоходного вала из Сталь 45 эпюры изгибающих и приведенных моментов по формулам [14]:
Определяются реакции опор:
Определяется изгибающий момент:
Определяется суммарный изгибающий момент:
На основе третьей гипотезы прочности приведенный момент определяется по формуле [14]:
Эпюры изгибающих и приведенных моментов вала изображены на рисунке 6.
6.3 Проверочный расчет вала
Определяется коэффициент безопасности по формуле [7 с. 278]:
где S – коэффициент безопасности по изгибу;
[S] – коэффициент безопасности для нереверсивных редукторов [S]=2;
S – коэффициент безопасности по кручению;
где а и а – переменные составляющие циклов изменения напряжений; m и m – постоянные составляющие циклов изменения напряжений;
-1 и -1 – пределы выносливости при изгибе и кручении для Сталь 45 -1=383 Нмм2 -1=226 Нмм2; [7 с. 291]
и – масштабные факторы учитывающие влияние размеров сечения вала = 073 = 078;
К и К – эффективные коэффициенты концентрации напряжений при изгибе и кручении К = 225 К = 175;
КL – коэффициент долговечности;
– коэффициент упрочнения вводимый для валов с поверхностным упрочнением = 2;
и – коэффициенты характеризующие чувствительность материала к асимметрии цикла изменения напряжений.
Концентрация напряжений:
Для шпоночный паза: К = 16; К = 14; [7 с. 278]
= 075; = 073; [7 с. 276]
Рисунок 6 – Эпюры изгибающих и приведенных моментов тихоходного вала
Определяется момент инерции и полярный момент вала по формуле [7 с. 281]:
Постоянные составляющие циклов изменения напряжений m и m и переменные составляющие а и а определяются по формулам [7 с. 281]:
Прочность вала обеспечивается
7 Выбор подшипников качения
V вал – подшипник 226
Исходные данные: внутренний диаметр d =130 мм;наружный диаметр D = 230 мм; ширина В = 40; фаска r = 4; динамическая грузоподъемность Сr = 120 кН; статическая грузоподъемность С0r = 112 кН.
Определяются суммарные реакции опор быстроходного вала по формуле [15 с. 304]:
Подшипники подбираются по наиболее нагруженной опоре 2.
Эквивалентная нагрузка определяется по формуле [15 c. 212]:
где Х Y – значения назначаются по таблице [15 с. 212];
V – коэффициент при вращении внутреннего кольца V=1;
Рг1 Ра (Fг1 Fа ) – радиальная и осевая нагрузка Н;
К КТ – коэффициенты безопасности для приводов ленточных конвейеров.
Расчетная долговечность в миллионах оборотов определяется по формуле [15 c. 211]:
где С – динамическая грузоподъемность;
Рэ – эквивалентная нагрузка;
р – показатель степени для шарикоподшипников р= 3.
Расчетная долговечность в часах определяется по формуле [15 c. 211]:
где n – частота вращения обмин.
Следовательно окончательно принимаем подшипники 226 для V вала.
Основные размеры всех подшипников легкой серии в коробке скоростей приведены в сводной таблице 8.
Таблица 8 – Сводная таблица подшипников
Основные размеры подшипника
8 Выбор электромагнитных муфт
Для удобства дистанционного и автоматического управления возможности точного регулирования передаваемого момента назначаются электромагнитные муфты контактного исполнения Э1М 2 по ГОСТ 21573-76.
Муфты назначаются по крутящему моменту вала ( таблица 7). Применяемые электромагнитные муфты для каждого вала представлены в виде сводной таблицы 9.
Таблица 9 – Сводная таблица электромагнитных муфт
Условное обозначение муфт серии ЭМ
9 Описание системы смазки
Станок имеет централизованную систему смазки. Резервуаром для масла служит нижняя внутренняя полость станины. Из резервуара масло шестеренным насосом подается через фильтры по маслопроводу в коробку скоростей через маслораспределитель в стол и под круговые направляющие планшайбы.
Для обеспечения температуры масла в коробке скоростей не более 60º и в связи с большими окружными скоростями зубчатых колёс выбираем масло с низкой вязкостью - например Индустриальное 20 ГОСТ 1707-51.
Смену масла рекомендуется производить первый раз после 10 дней работы второй раз после 20 дней а затем через каждые 3 месяца.
Проверка системы смазки каждые 3 месяца.
1 Проверка шпоночного соединения
Производится проверка шпоночного соединения для самого нагруженного вала №5.
Шпонка 36 20 180 ГОСТ 23360 – 78 – элемент открытой передачи
Напряжение смятия узких граней шпонки определяется по формуле [15 с. 170]:
где Т – передаваемый вращающий момент Нмм;
d – диаметр вала в месте установки шпонки мм;
lp=l – b =180 – 36 = 144 мм
b – ширина шпонки мм;
h – высота шпонки мм;
t1 – глубина паза на валу мм;
[см] – допускаемое напряжение смятия МПа. [16 с. 252]
Условие проверки выполняется
2 Проверка шлицевого соединения
Шлицевую посадочную поверхность имеют электромагнитные муфты.
Шлицевое соединение 10×92×102×14 по ГОСТ 1139-80 рассчитывается на смятие по формуле [2 с. 108].
Расчет производится по самому нагруженному шлицевому соединению на четвертом вале.
см = 2Мкр (hlzdс) []см [2]
где Мкр - максимальный крутящий момент Нм;
- коэффициент учитывающий неравномерность распределения усилий по рабочим поверхностям зубьев;
h – высота поверхности контакта зуба;
h=05(D-d)-2с=05(102-92)-205=4 мм
dс - средний диаметр зубчатого соединения;
dс=05(D+d)=05(102+92)=100мм
[]см - допускаемое напряжение на смятие []см = 100 140 МПа.
см = (2 430827×103) ( 075 4 128 10 100) = 224 100 МПа
Подводя итог выполненной работы на тему «Разработать токарно-карусельный одностоечный станок с ЧПУ» отметим преимущества спроектированной конструкции в сопоставлении с базовой моделью станка 1512Ф3 имеющей ступенчатое регулирование частоты вращения планшайбы.
Спроектированный узел коробки скоростей имеет бесступенчатое регулирование за счет применения двигателя постоянного тока 4ПФ180S. Основное достоинство привода с бесступенчатым регулированием – повышение производительности обработки за счет точной настройки оптимальной по режимам резания скорости возможность плавного изменения скорости во время работы простота автоматизации процесса переключения скоростей за счет применения электромагнитных муфт контактного исполнения. К недостатком можно отнести большую стоимость двигателя постоянного тока.
Гаврилин А.М. Расчет и проектирование металлорежущих станков. Орел: Орел ГТУ 2006. 228 с.
Гузенков П.Г. Детали машин. М.: Высшая школа 1982. 351 с.
Дунаев П.Ф. Детали машин. Курсовое проектирование. М.: Высшая школа 1984. 336 с.
Иноземцев А.Н. Металлорежущие станки. Тула: Тул .гос. ун-т 2002. 183с.
Косилова А.Г. Справочник технолога – машиностроителя. М.: Машиностроение 1985 496 с.
Кочергин А.И. Конструирование и расчет металлорежущих станков и станочных комплексов. Курсовое проектирование. Мн.: Выш.шк. 1991. 381 с.
Ничипорчик С.Н. Детали машин в примерах и задачах. М.: Высшая школа 1981. 432 с.
Проников А.С. Расчет и конструирование металлорежущих станков. М.: Высшая школа 1962. 413 с.
Решетов Д.Н. Детали машин. М.: Машинстроение 1989. 496 с.
Святский В.М. Металлорежущие станки: курсовой проект «Конструирование и расчет металлорежущих станков. Ижевск: ИжГТУ 2012. 37 с.
Сундуков Г.В. Методические указания по выполнению курсового проекта. Тула: Тул .гос. ун-т 2007. 31 с.
Тарзиманов Г.А. Проектирование металлорежущих станков. М.: Машиностроение 1972. 312 с.
Тарзиманов Г.А. Проектирование металлорежущих станков. М.: Машиностроение 1980. 288 с.
Устиненко В.Л. Киркач Н.Ф. Баласанян Р.А. Основы проектирования деталей машин. Харьков.: Вища школа 1983. 179 с.
Чернавский С.А. Курсовое проектирование деталей машин. М.: Высшая школа 1988. 416 с.
Шейнблит А.Е. Курсовое проектирование деталей машин. М.: Высшая школа 1991. 432 с.
Свертка чистовик.cdw

Рекомендуемые чертежи
- 24.01.2023