Проектирование привода грузоподъемного устройства


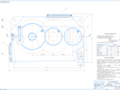
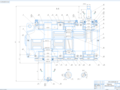
- Добавлен: 28.12.2022
- Размер: 2 MB
- Закачек: 0
Описание
В комплекте: пояснительная записку, спецификация, чертежи промежуточного вала и зубчатого колеса. Выполнено в Компасе.
Состав проекта
![]() ![]() ![]() |
![]() ![]() ![]() ![]() |
![]() ![]() ![]() ![]() |
![]() ![]() ![]() ![]() |
![]() ![]() ![]() ![]() |
Дополнительная информация
Курсач ДМ.docx
Федеральное государственное бюджетное образовательное учреждение высшего профессионального образования
Уфимский государственный авиационный технический университет
Кафедра «Механизмы и цифровое проектирование»
Проектирование привода грузоподъемного устройства
ПОЯСНИТЕЛЬНАЯ ЗАПИСКА
к курсовому проекту по деталям машин и основам конструирования
(обозначение документа)
Проектирование привода лебедки6
1Расчет диаметра грузового каната6
2Расчет диаметр барабана6
3Расчет частоты вращения барабана7
4Передаточное отношение привода. Выбор электродвигателя7
5Расчет момента на барабане лебедки9
6Расчет момента на зубчатом колесе тихоходной ступени9
7Расчет допускаемых контактных напряжений9
8Расчет коэффициента относительной ширины колес10
9Расчет эквивалентного времени работы10
10Определение кодов передач11
11Определение кода схемы11
Выбор оптимального варианта компоновки редуктора12
1Формулы необходимые для расчета12
2Расчет параметров массы и объема13
Геометрический расчет редуктора15
1Расчет быстроходной прямозубой цилиндрической передачи15
2Расчет тихоходной косозубой цилиндрической передачи16
Кинематический расчет редуктора18
1Определение частот вращения валов18
2Определение окружных скоростей в зацеплении18
Статическое исследование редуктора20
1Расчет моментов на валах и колесах редуктора20
2Определение составляющих полного усилия в зацеплениях быстроходной и тихоходной передач20
Конструирование валов редуктора23
1Конструирование быстроходного вала23
2Конструирование промежуточного вала24
3Конструирование тихоходного вал25
Предварительный подбор подшипников27
1Подбор подшипников на быстроходный и промежуточный валы27
2Подбор подшипника на тихоходный вал27
Проверка зубьев на прочность28
1Выбор материала шестерни и колеса28
2Расчет допускаемых контактных напряжений28
3Расчет допускаемых изгибных напряжений30
4Расчет прочности зубьев по контактным напряжениям32
5Расчет прочности зубьев по изгибным напряжениям33
Проверочный расчет промежуточного вала35
Проверочный расчет подшипников промежуточного вала41
Расчет на усталостную прочность42
Описание этапа проектирования редуктора44
1Определение расстояния между деталями передач44
2Расчет шпоночных соединений45
2.1Выбор призматической шпонки быстроходного колеса45
2.2Выбор призматической шпонки тихоходного колеса45
3Определение конструкции зубчатых колес46
3.1Определение конструкции быстроходного колеса47
3.2Определение конструкции тихоходного колеса47
4Определение конструкции шестерен и валов47
4.1Определение конструкции промежуточного вала-шестерни48
4.2Определение конструкции быстроходного вала-шестерни49
4.3Определение конструкции тихоходного вала51
5Проектирование дистанционных втулок на промежуточном и тихоходном валах52
6Проектирование маслоотражательных колец на быстроходном и промежуточном валах53
7Проектирование крышек подшипников54
7.1Проектирование крышек подшипников на тихоходном валу54
7.2Выбор винта для соединения крышки подшипника со стенкой корпуса55
7.3Проектирование крышек подшипников для промежуточного и тихоходного вала56
8Проектирование и конструкция бобышек57
9Проектирование концов быстроходного и тихоходного вала58
10Описание этапов расчета конструкции вида спереди59
10.1Определение конструктивных размеров винта крышки корпуса60
10.2Проектирование конструктивных размеров проушин61
10.3Проектирование конструктивных размеров крышки-отдушины62
10.4Проектирование конструктивных размеров маслосливной пробки63
10.5Проектирование конструктивных размеров маслоуказателя63
11Конструктивное оформление опорной части корпуса64
Расчет отклонений форм деталей редуктора66
1Расчет отклонений формы зубчатого колеса66
1.1Определение цилиндричности базового отверстия66
1.2Определение параллельности и симметричности расположения шпоночного паза ступицы66
1.3Определение допуска параллельности торцов ступицы колес67
2Расчет отклонений формы промежуточного вала67
2.1Определение соосности посадочных поверхностей являющимися цапфами подшипников67
2.2Определение соосности посадочных поверхностей для зубчатого колеса относительно общей оси вращения вала67
2.3Определение цилиндричности посадочных поверхностей для подшипников качения67
2.4Определение цилиндричности посадочных поверхностей вала68
2.5Определение перпендикулярности базовых торцов валов для зубчатых колес68
2.6Определение параллельности и симметричности расположения шпоночного паза вала68
Эскизы стандартных изделий70
Привод подъемно-транспортного устройства сконструирован для передачи вращающего момента на барабан канат которого перемещает груз с определенной скоростью.
Привод машины состоит из электродвигателя редуктора и барабана. Электродвигатель присоединен к редуктору при помощи муфты. Подъем груза осуществляется канатом.
Редуктор осуществляет передачу вращающего момента от электродвигателя к барабану. При этом происходит повышение значения вращающего момента за счет понижения частоты до требуемой величины. Редуктор двухступенчатый; первая ступень – прямозубое цилиндрическое зацепление; вторая ступень – косозубое цилиндрическое зацепление. Смазывание зубчатых колес и подшипников осуществляется разбрызгиванием.
Для удобства сборки корпус выполнен разъемным плоскость разъема проходит через оси валов. Лапы под фундаментные болты не выступают за предельные размеры редуктора. Проушины для подъема и транспортировки редуктора отлиты заодно с крышкой редуктора.
Проектирование привода лебедки
1Расчет диаметра грузового каната
Диаметр каната определяют исходя из условия прочности с учетом коэффициента безопасности устанавливаемого для каждой категории режима (ГОСТ 21354-87) по нормам Ростехнадзора.
В упрощенных расчетах для легкого режима диаметр каната мм можно определить по формуле:
где – номинальное натяжение каната Н;
2Расчет диаметр барабана
Диаметр грузового барабана мм лебедки предварительно назначаем из условия:
где – коэффициент диаметра барабана выбираемый в соответствии с нормами Ростехнадзора.
Так как тип грузоподъемной машины – это лебедка на электроприводе то принимаем .
Подставляем значения в формулу (1.2):
Округлив полученное значение в большую сторону до кратного 10 получаем:
3Расчет частоты вращения барабана
Частоту вращения барабана мин вычисляют по формуле:
где – скорость набегания каната на барабан;
4Передаточное отношение привода. Выбор электродвигателя
Передаточное отношение привода определяют из условия:
где – передаточное число открытой передачи принимаемое в пределах 3 6. В схемах без открытой передачи
Мощность двигателя кВт связана (с учетом допускаемой перегрузки) с потребной (крюковой) мощностью кВт соотношением:
где – мощность привода определяемая по формуле:
где – КПД учитывающий потерю мощностей в приводе.
КПД рассчитывают по формуле:
где – КПД редуктора получаемый из выражения:
где – КПД на потери в зацеплениях зубчатых передач;
– КПД в подшипниках;
– КПД на разбрызгивание масла;
В данных расчетах принимаем следующие значения:
По формуле (1.7) КПД привода лебедки равен:
Находим мощность электродвигателя подставляя полученные значения в формулу (1.6):
Выбираем подходящие электродвигатели в соответствии с мощностью по таблице П. 1.1 пособия. Необходимо взять ближайшее большее значение поэтому принимаем кВт.
Из таблицы 1 выбираем вариант с минимальным передаточным отношением но при условии что . Это двигатель типа 132S41455 поэтому принимаем и мин.
5Расчет момента на барабане лебедки
Вращающий момент на барабане лебедки Н·м:
6Расчет момента на зубчатом колесе тихоходной ступени
Момент на колесе тихоходной передачи редуктора при отсутствии открытой передачи Н·м:
7Расчет допускаемых контактных напряжений
Для схемы редуктора №20 допускаемые контактные напряжения МПа:
– для передачи тихоходной ступени
– для передачи быстроходной ступени
Подсчитанные значения удовлетворяют условиям (1.11) и (1.12). Округляем их в меньшую сторону до кратного 10 и принимаем:
8Расчет коэффициента относительной ширины колес
Для редуктора по схеме 20 коэффициент относительной ширины колес :
– для тихоходной передачи
– для быстроходной передачи
Для быстроходной передачи принимаем среднее значение коэффициента :
9Расчет эквивалентного времени работы
Эквивалентное время работы час назначают с учетом категории режима работы по ГОСТ 21354-87 в соответствии с формулой:
где – заданный срок службы час.
Коэффициент определяется по таблице 1.3 пособия. Для четвертого режима работы его значение .
10Определение кодов передач
Код передачи соответствует принятому в программе компьютера обозначению:
– прямозубая передача – 1;
– косозубая передача – 2;
– шевронная передача – 3;
– коническая прямозубая – 4.
Для редуктора по схеме 20 первая ступень – прямозубая вторая ступень – косозубая. Следовательно код передачи – 12.
11Определение кода схемы
Код схемы указывается в соответствии с заданием. В нашем случае он равен 20.
Записываем все полученные значения в таблицу 2.
Код схемы редук- тора
Выбор оптимального варианта компоновки редуктора
1Формулы необходимые для расчета
Выбор оптимального варианта компоновки редуктора осуществляют по двум критериям:
) По минимальному объему корпуса;
) По минимальной массе зубчатых колес.
Основные размеры зубчатых передач редуктора по схеме 20 рассчитывают по формулам указанным ниже.
Диаметр вершин второго колеса быстроходной передачи мм:
где – модуль зубчатого колеса мм;
– коэффициент высоты головки зуба.
Диаметр вершин второго колеса тихоходной передачи мм:
где – угол наклона зубьев на делительном диаметре колеса град.
Диаметр вершин наибольшего из колес мм:
где – наибольшая из двух величин или .
Величина зазора между корпусом и вращающимися колесами мм:
Ширина корпуса редуктора мм:
где и – ширины венцов зубчатых колес быстроходной и тихоходной
передач соответственно.
Длина корпуса редуктора мм:
где и – межосевые расстояния тихоходной и быстроходной передач соответственно мм.
Объем корпуса редуктора дм получают по формуле:
Массу заготовок кг для зубчатых колес цилиндрических редукторов характеризующую затраты на материалы можно найти по формуле:
где – коэффициент пропорциональности для стальных зубчатых колес можно принять равным 612 кгдм.
2Расчет параметров массы и объема
Для наглядного сравнения параметров различных вариантов необходимо построить график масс и объемов редукторов в зависимости от варианта компоновки.
Рисунок 2.1 График выбора варианта компоновки редуктора
По наименьшей массе и объему очевидно наилучшим выбором будет вариант №3 с массой кг и объемом дм.
Геометрический расчет редуктора
1Расчет быстроходной прямозубой цилиндрической передачи
Делительный диаметр шестерни мм:
Делительный диаметр зубчатого колеса мм:
Диаметр вершин шестерни мм:
Диаметр вершин зубчатого колеса мм:
Рассчитывается по формуле (2.1)
Диаметр впадин шестерни мм:
где – коэффициент радиального зазора;
Диаметр впадин зубчатого колеса мм:
2Расчет тихоходной косозубой цилиндрической передачи
Рассчитывается по формуле (2.2)
Коэффициент торцевого перекрытия для косозубых передач :
Коэффициент осевого перекрытия :
Суммарный коэффициент перекрытия :
Кинематический расчет редуктора
1Определение частот вращения валов
Частоты вращения валов и зубчатых колес определяются следующим образом:
– частота вращения быстроходного вала мин
– частота вращения промежуточного вала мин
где – передаточное число зубчатой пары для быстроходной передачи;
– частота вращения тихоходного вала мин
где – передаточное число зубчатой пары для тихоходной передачи;
2Определение окружных скоростей в зацеплении
Окружная скорость в зацеплении быстроходной передачи мс:
Окружная скорость в зацеплении тихоходной передачи мс:
Статическое исследование редуктора
1Расчет моментов на валах и колесах редуктора
Момент на хвостовике быстроходного вала Н·м:
Момент на шестерне быстроходной передачи Н·м:
Момент на колесе быстроходной передачи Н·м:
Момент на шестерне тихоходной передачи Н·м:
2Определение составляющих полного усилия в зацеплениях быстроходной и тихоходной передач
Окружная сила на шестерне быстроходной передачи Н:
Радиальная сила на шестерне быстроходной передачи Н:
где – угол зацепления стандартно принимается равным ;
– угол наклона зубьев для быстроходной передачи равен ;
Осевая сила на шестерне быстроходной передачи Н:
Усилия действующие на колесо быстроходной передачи Н:
Окружная радиальная и осевая силы на шестерне тихоходной передачи Н:
Усилия действующие на колесо тихоходной передачи Н:
Конструирование валов редуктора
Все последующие результаты вычислений округляются в большую сторону до линейных нормальных размеров в соответствии с ГОСТ 6636-69.
1Конструирование быстроходного вала
Диаметр входного кольца ведущего вала мм:
Согласуя с диаметром вала электродвигателя принимаем это значение равным мм.
Диаметр цапфы вала под подшипником мм:
По таблице 1.10 в соответствии с мм принимаем значения переходного радиуса заплечника и фаски равным: . Для каждого нового диаметра значения из таблицы обновляются!
Диаметр буртика для упора кольца подшипника мм:
Диаметр в месте установки зубчатых колес равен диаметру буртика для упора кольца подшипника мм.
Длина посадочного участка хвостовика мм:
Длина промежуточного участка мм:
2Конструирование промежуточного вала
Диаметр вала в месте установки зубчатых колес мм:
Диаметр цапфы вала под подшипник мм в целях унификации принимаем равным:
Диаметр буртика для упора колеса мм:
3Конструирование тихоходного вал
Диаметр входного кольца ведомого вала мм:
Диаметр цапфы вала под подшипник мм:
Предварительный подбор подшипников
Из экономических соображений и из особенностей технологии сборки предпочтительно применение шариковых однорядных подшипников легкой серии ГОСТ 8338-75. В случае если на других этапах проектирования выясняется их недостаточная грузоподъемность можно применить подшипники других типов. Выбор осуществляется при помощи таблицы П3.1 пособия.
1 Подбор подшипников на быстроходный и промежуточный валы
По диаметру мм выбираем шариковый радиальный однорядный подшипник легкой серии №208 ГОСТ 8338-75.
Динамическая нагрузка: кН.
Статическая нагрузка: кН.
Наружный диаметр: мм.
Внутренний диаметр: мм.
Радиус скругления: мм.
2Подбор подшипника на тихоходный вал
По диаметру мм выбираем шариковый радиальный однорядный подшипник тяжелой серии №410 ГОСТ 8338-75.
Проверка зубьев на прочность
1Выбор материала шестерни и колеса
Сталь 40Х ГОСТ 4543-81;
Термообработка – закалка ТВЧ;
Твердость поверхности – 45 55 HRC.
Термообработка – улучшение;
Твердость – 260 320 HB.
2Расчет допускаемых контактных напряжений
– коэффициент долговечности.
Коэффициент долговечности :
где – базовое число циклов переменных напряжений;
– эквивалентное число циклов.
По Рис. 2.3 (б) определяем что тогда .
Эквивалентное число циклов :
Базовое число циклов переменных напряжений :
Зубья проходят проверку на прочность если выполняется следующее условие:
Данное условие выполняется поскольку МПа.
3Расчет допускаемых изгибных напряжений
где – предел выносливости при изгибе;
– коэффициент долговечности;
– коэффициент учитывающий характер приложения нагрузки;
– коэффициент безопасности.
– при шероховатости мкм.
где – базовое число циклов для всех сталей;
– эквивалентное число циклов;
– для закалки (по Таблице П 1.3).
– для улучшения (по Таблице П 1.3).
4Расчет прочности зубьев по контактным напряжениям
Контактные напряжения в зацеплении:
где МПа – для стальных колес и шестерен;
Для косозубой передачи :
где – по Таблице П 2.2 в соответствии со степенью точности 8;
где – по Таблице П 2.1;
– по графику П 2.1 в соответствии с .
Условие выполняется так как .
5Расчет прочности зубьев по изгибным напряжениям
Для цилиндрической шестерни
где по Рис. П.2.2 при и
Для косозубого колеса
где и – коэффициенты определяемые по графику Рис. П. 2.2 в зависимости от значений и .
По графику Рис. П. 2.2 находим что и .
Условие изгибной выносливости шестерни выполняется.
Условие изгибной выносливости зубчатого колеса выполняется.
Проверочный расчет промежуточного вала
Расчетная схема промежуточного вала представляет собой двух опорную балку нагруженную силами возникающими в зацеплении от шестерни тихоходной ступени и на колесе быстроходной ступени.
Рис. 9.1 Расчетная схем промежуточного вала
Эпюры изгибающих моментов строят в двух взаимно перпендикулярных плоскостях. Для построения эпюры суммарного изгибающего момента используется зависимость где и – изгибающие моменты в сечении по плоскостям.
Рис. 9.2 Расчетная схема в плоскости YOX
Рис. 9.3 Расчетная схема в плоскости ZOX
Реакции в опорах определяют из условия равновесия вала составляя уравнения статики . Правильность определения реакций проверяют с помощью уравнения
Суммарные реакции в опорах:
Внутренние изгибающие моменты в поперечном сечении на каждом участке вала определяют методом сечений составляя уравнения равновесия:
Опасное сечение в сечение :
Проверочный расчет подшипников промежуточного вала
По ГОСТ 8338-75 выбираем подшипник №208.
Статическая грузоподъемность:
где – для шариковых подшипников;
– коэффициент динамической грузоподъемности;
– температурный коэффициент;
– коэффициент вращения кольца;
– коэффициент радиальной нагрузки;
– коэффициент осевой нагрузки.
Так как час то данный подшипник подходит.
Расчет на усталостную прочность
Запас сопротивления усталости только по изгибу :
Запас сопротивления только по кручению :
где и – амплитуды переменных составляющих циклов напряжений;
и – постоянные составляющие;
и – коэффициенты корректирующие влияние постоянной составляющей цикла напряжений на сопротивление усталости;
и – пределы выносливости;
и – масштабный фактор и фактор шероховатости поверхности;
и – эффективные коэффициенты концентрации напряжений.
Значения и зависят от механических характеристик материала.
Для легированных сталей ; .
Пределы выносливости равны:
По таблице 15.5 и 15.6 [1] определяем что и .
По таблице 15.1 [1] определяем что ; и .
Подставив полученные выражения в формулы (11.1) – (11.3) получаем:
Так как то условие прочности выполняется.
Описание этапа проектирования редуктора
1Определение расстояния между деталями передач
Рис. 12.1 Схема редуктора 20
Расстояние между самыми отдаленными друг от друга зубьями тихоходного колеса и быстроходной шестерни мм вычисляется по формуле:
Зазор между деталями и внутренней стенкой корпуса мм:
Зазор между зацеплениями мм принимаем равным то есть мм.
2Расчет шпоночных соединений
2.1Выбор призматической шпонки быстроходного колеса
В соответствии с ГОСТ 23360-78 геометрические размеры призматической шпонки находятся по диаметру вала на котором сидит колесо. Так как диаметр промежуточного вала на этом участке равен мм то параметры призматической шпонки:
Условие определяющее длину шпонки:
Из ряда стандартных длин для шпонок возьмем 36 мм. Эта длина меньше ширины венца зубчатого колеса ( мм) на 82 мм следовательно условие (12.3) выполняется.
Условие прочности призматической шпонки на смятие:
где – выступ шпонки от шпоночного паза;
– допускаемое напряжение на смятие для всех расчетов принимаем равным 80 МПа;
Условие (12.4) выполняется. Зубчатое колесо конструируем без удлиненной ступицы.
2.2Выбор призматической шпонки тихоходного колеса
В соответствии с ГОСТ 23360-78 (шпонка исполнения 1).
Параметры призматической шпонки:
Из ряда стандартных длин для шпонок возьмем мм. Эта длина меньше ширины венца зубчатого колеса ( мм) на 104 мм следовательно условие (12.3) выполняется.
3Определение конструкции зубчатых колес
Рис. 12.2 Эскиз зубчатых колес
Конструкция на Рис. 12.2 определяется в соответствии с литературой [1].
Ширина зубчатого венца для обоих колес соответствует распечатке.
– модуль колес по распечатке.
Остальные параметры с эскиза:
3.1Определение конструкции быстроходного колеса
3.2Определение конструкции тихоходного колеса
4Определение конструкции шестерен и валов
Обе шестерни будут элементом детали «вал-шестерня» поскольку нет необходимости в их передвижении вдоль оси вала.
4.1 Определение конструкции промежуточного вала-шестерни
Рис. 12.3 Эскиз промежуточного вала-шестерни
Диаметры участков валов конструируются по пункту 6 пояснительной записки.
Ширина зубчатого венца шестерни мм должна удовлетворять условию:
Ширина редуктора по внутренней стенке корпуса мм:
где мм – ширина венца зубчатого колеса;
мм – длина буртика для упора зубчатого колеса (зазор между зацеплениями);
мм – зазор между деталями и внутренней стенкой корпуса;
Участок вала под зубчатое колесо укорачивается на мм в месте установки дистанционной втулки. Следовательно этот участок будет иметь длину 422 мм. Шпоночный паз центрируется по размеру 442 мм!
Зазор между подшипником и внутренней стенкой корпуса принимаем равным 2 мм. Следовательно в месте установки втулки конец вала под подшипник будет иметь длину:
где мм – ширина подшипника выбранного ранее по расчетам;
Шайба маслозащитная имеет общую ширину в 6 мм и устанавливается в плотную к подшипнику. Следовательно длина буртика диаметром 50 мм будет равна 7 мм.
В месте установки шайбы маслозащитной длина участка вала под подшипник будет равна сумме ширины шайбы и ширины подшипника то есть 24 мм.
Концы валов удлиняются до нормальных линейных размеров в соответствии с ГОСТ 6636-69.
Шпонка вставляется из раздела «Стандартные изделия» по ГОСТ 23360-78. Подшипник по ГОСТ 8338-75.
4.2 Определение конструкции быстроходного вала-шестерни
Поскольку зубчатое колесо будет пересекаться с поверхностью быстроходного вала то следует выбрать конструкцию вала следующего типа:
Рис.12.4 Эскиз быстроходного вала-шестерни
Ширина зубчатого венца шестерни :
Диаметр вершины зубьев шестерни при такой геометрии совпадает с диаметром гладкой части вала. Зубья вытачиваются на поверхности вала при помощи фрезы. Для этого процесса необходима канавка для выхода фрезы. Ее диаметр определяется в соответствии с литературой [1 c. 179]. При модуле шестерни мм и степени точности 8: мм.
Глубина фрезерования соответствует диаметру впадин шестерни. Длина мм начинается на линии лежащей за 1 мм от торца сопряженного с шестерней зубчатого колеса.
Длина буртика под подшипник мм. Длина левого участка вала под подшипник равна ширине подшипника то есть 18 мм. Длина гладкого прямого участка корректируется в соответствии с шириной редуктора по внутренней стенке корпуса мм. Длину правого участка под подшипник определим после расчетов крышек подшипников.
4.3Определение конструкции тихоходного вала
Рис. 12.5 Эскиз тихоходного вала
Поскольку межосевого расстояния между промежуточным и тихоходным валом не хватает для того чтобы вместить зубчатое колесо быстроходной ступени то необходимо уменьшить диаметр тихоходного вала на некотором участке. Именно с этой целью выбирались подшипники тяжелой серии – они способны выдержать нагрузку возлагаемую на них при уменьшенном диаметре вала. При этом диаметр данного участка соответствует диаметру вала под подшипник то есть равен 50 мм.
Буртик диаметром 70 мм уменьшаем со стандартного размера в 6 мм до 5 мм чтобы вместить быстроходное колесо. Буртик у подшипника остается равным 6 мм.
Длина правого участка вала под подшипник равна ширине подшипника то есть 31 мм но удлиняется до нормального линейного размера по ГОСТ 6636-69. Длина левого участка под подшипник определяем после расчета геометрии крышек.
Слева в месте установки дистанционной втулки также присутствует зазор в 2 мм для посадки между торцем зубчатого колеса и краем вала.
5Проектирование дистанционных втулок на промежуточном и тихоходном валах
На промежуточном валу
Рис. 12.6 Эскиз втулки на промежуточном валу
Втулка проектируется в соответствии с ГОСТ 24833-81. Вся геометрия втулки определяется диаметром вала под подшипник.
Высота втулки равна расстоянию между краем подшипника и торцем зубчатого колеса.
Рис. 12.7 Эскиз втулки на тихоходном валу
6Проектирование маслоотражательных колец на быстроходном и промежуточном валах
На быстроходном валу
Рис. 12.8 Эскиз шайбы маслозащитной
Диаметр 475 мм соответствует диаметру участка вала на который упирается шайба. Диаметр 692 мм соответствует внутреннему диаметру наружного кольца подшипника.
Рис. 12.9 Эскиз шайбы маслозащитной
Диаметр 50 мм соответствует диаметру участка вала на который упирается шайба. Диаметр 692 мм соответствует внутреннему диаметру наружного кольца подшипника.
7Проектирование крышек подшипников
7.1Проектирование крышек подшипников на тихоходном валу
Две крышки на тихоходном валу будут практически идентичны. Разве что на нижней будет иметься отверстие для выхода конца тихоходного вала.
Рис. 12.10 Эскиз крышки подшипника
По литературе [1 с. 167] определяем конструктивные элементы и крышки в зависимости от внешнего диаметра подшипника мм. Где мм – толщина стенки корпуса; мм – диаметр винта к крышке; – количество винтов на одной крышке.
Подбираем внешний диаметр крышки подшипника по формуле:
Толщина крышки вычисляется по формуле:
где мм – высота головки винта;
Крышка крепится к корпусу при помощи шести винтов с шестигранным углублением под ключ по ГОСТ 11738-84.
Прокладка ставится в зазор между крышкой подшипника и стенкой корпуса. Ее толщина – 2 мм а диаметр совпадает с внешним диаметром крышки и диаметром гнезда под подшипник.
7.2Выбор винта для соединения крышки подшипника со стенкой корпуса
Рис. 12.11 Эскиз винта М10
Длина рабочей части винта находится:
Диаметр углубления под головку винта на 1 мм больше диаметра шляпки винта. Так как присутствует шайба толщиной 2 мм то винт будет выпирать от плоскости крышки на 2 мм. Из раздела «Стандартные изделия» выбираем нужный винт по ГОСТ 11738-84 и располагаем его на 2 мм выше глубины гнезда под шляпку чтобы осталось место для шайбы. Выбираем шайбу 8Л по ГОСТ 6402-70 и устанавливаем ее по нижней границе в гнездо.
До края крышки необходимо начертить зазор между крышкой и винтом. Его диаметр на 1 мм больше диаметра винта то есть 11 мм.
7.3Проектирование крышек подшипников для промежуточного и тихоходного вала
Поскольку подшипники на быстроходном и промежуточном валу идентичны то и крышки подшипников по конструкции будут схожи. Разве что с одной стороны на быстроходном валу будет иметься отверстие для выхода конца быстроходного вала.
Рис. 12.12 Эскиз крышки подшипника
Между крышкой подшипника и подшипником необходимо установить втулку. Ее диаметральные размеры совпадают с ножками крышки.
Рис. 12.13 Место стыка двух крышек
Между промежуточным и тихоходным валом необходимо срезать крышки. В таком варианте конструкции винт смещается в центральное положение относительно краев корпуса на 175 мм.
8Проектирование и конструкция бобышек
Рис. 12.14 Конструктивные размеры бобышек
Диаметр бобышки под винт:
где – момент на колесе тихоходной передачи;
Толщина стенки корпуса :
Приливы и радиусы скруглений принимаем равными 3 мм.
9Проектирование концов быстроходного и тихоходного вала
Рис. 12.15 Эскиз конца быстроходного вала
Его параметры определяются согласно ГОСТ 12081-72 литература [1 c. 475].
Диаметр хвостовика был подсчитан в пункте 6 пояснительной записки.
Длина вала от края крышки подшипника принимается равной 15 мм.
Рис. 12.16 Эскиз конца тихоходного вала
Определяется в соответствии с ГОСТ 12080-66 литературе [1 c. 475].
Призматическая шпонка по ГОСТ 23360-78 [1 с. 476].
Концевая шайба по ГОСТ 14734-69 [1 с. 477].
10Описание этапов расчета конструкции вида спереди
Расстояние между дном корпуса и поверхностью колеса .
Угол наклона дна относительно горизонта составляет .
10.1Определение конструктивных размеров винта крышки корпуса
Рис. 12.17 Винт крышки корпуса
Для соединения корпуса и крышки по всему контуру плоскости разъема редуктора выполняют специальные фланцы. Размеры конструктивных элементов:
На продольных длинных сторонах редуктора фланцы корпуса располагают внутрь от стенки корпуса а фланцы крышки – снаружи. Фланцы объединяют с приливами (бобышками) для подшипников равными 3 мм.
Для соединения крышки с корпусом используют винты с головкой с шестигранным углублением «под ключ» ГОСТ 11738–84. Размеры конструктивных элементов:
Также устанавливают дополнительные болты на фланцах той же или меньшей толщины.
10.2Проектирование конструктивных размеров проушин
Рис. 12.18 Эскиз проушины
Для подъема и транспортирования крышки корпуса и редуктора в сборе применяют проушины отливая их заодно с крышкой. Проушина выполнена в виде ребра со сквозным отверстием.
Диаметр отверстия равен:
10.3Проектирование конструктивных размеров крышки-отдушины
Для залива в редукторе контроля правильности зацепления и для внешнего осмотра деталей делают крышку-отдушину.
Рис. 12.19 Эскиз крышки-отдушины
Во внутренней штампованной крышке пробиты 2–4 отверстия диаметром 4 мм. Эта крышка окантована в двух сторон привулканизированной резиной. Наружная крышка – плоская. Вдоль длинной ее стороны выдавлены 2–3 гребня через которые внутренняя полость редуктора сообщена с внешней средой. Пространство между внутренней и внешней крышками заполнено фильтром из тонкой медной проволоки или синтетических нитей [1 с. 315].
Крышки крепят винтами.
Толщину стенок и высоту принимают для крышек:
Толщина стенок в любом сечении крышки должна быть по возможности одинаковой. Крышки усиливают ребрами жесткости.
10.4Проектирование конструктивных размеров маслосливной пробки
При работе передач продукты изнашивания постепенно загрязняют масло. С течением времени оно стареет свойства его ухудшаются. Поэтому масло залитое в корпус редуктора или коробки передач периодически меняют. Для замены масла в корпусе предусматривают сливное отверстие закрываемое пробкой с цилиндрической или конической резьбой.
Рис. 12.20 Эскиз маслосливной пробки
Размеры назначаем в соответствии с рекомендациями [1 с. 204].
10.5Проектирование конструктивных размеров маслоуказателя
Для наблюдения за уровнем масла в корпусе редуктора устанавливают маслоуказатель с масломерным стеклом.
Рис. 12.21 Эскиз маслоуказателя
Размеры назначаем в соответствии с рекомендациями [1 с. 205].
11Конструктивное оформление опорной части корпуса
Для крепления редуктора к основанию или раме применены опорные поверхности в виде нескольких небольших платиков. Крепление осуществляется с помощью болтов диаметром мм. Число болтов принимаем так как суммарное межосевое расстояние .
Диаметр винта крепления корпуса к плите:
где d– диаметр винта крепления крышки и корпуса редуктора;
Рис. 12.22 Конструктивное оформление опорной части редуктора
Высоту ниш принимаем:
Остальные размеры назначаем в соответствии с рекомендациями [1 c. 300].
Расчет отклонений форм деталей редуктора
1Расчет отклонений формы зубчатого колеса
1.1Определение цилиндричности базового отверстия
Допуск цилиндричности :
где – допуск диаметра отверстия тогда по таблице 24.2 [1 c. 452] в соответствии с квалитетом точности 7 и диаметром отверстия 42 мм::
1.2 Определение параллельности и симметричности расположения шпоночного паза ступицы
Допуск параллельности и симметричности назначают для обеспечения более равномерного контакта рабочих поверхностей шпоночного паза ступицы и шпонки по формулам:
где – допуск ширины шпоночного паза;
После округления получаем:
1.3 Определение допуска параллельности торцов ступицы колес
Допуск параллельности задают по таблице 22.8 [1 с. 399].
2Расчет отклонений формы промежуточного вала
2.1 Определение соосности посадочных поверхностей являющимися цапфами подшипников
Допуск соосности ограничивает перенос между колец подшипников. Он назначается по таблице 22.5 [1 с. 395] в зависимости от типа подшипника устанавливаемого на вал.
2.2 Определение соосности посадочных поверхностей для зубчатого колеса относительно общей оси вращения вала
Допуски соосности регламентируют нормы кинематической точности и нормы контакта колес. Они назначаются по таблице 22.7 [1 стр. 398] в зависимости от степени кинематической точности передачи:
2.3 Определение цилиндричности посадочных поверхностей для подшипников качения
Рекомендуется принимать:
2.4Определение цилиндричности посадочных поверхностей вала
2.5Определение перпендикулярности базовых торцов валов для зубчатых колес
Назначаются по таблице 22.8 [1 стр. 399].
2.6 Определение параллельности и симметричности расположения шпоночного паза вала
Дунаев П. Ф. Леликов О. П. Детали машин. Конструирование узлов и деталей машин: Москва 2009. – 496 с.
Иванов М. Н. Детали машин М.Н. Иванов В.А. Финогенов. – Москва: Высшая школа 2008. – 408 с.
С. С. Прокшин. Проектирование приводов с цилиндрическими и коническо-цилиндрическими редукторами: учеб. пособие Б. А. Беляев С. М. Минигалеев В. Р. Мухамадеев; Уфимск. гос. авиац. техн. ун-т. – Уфа: УГАТУ 2013. – 96 с.
Эскизы стандартных изделий
Манжета ГОСТ 8752–79
Подшипник ГОСТ 8338–75
Шайба концевая ГОСТ 14734–69
Шпонка призматическая ГОСТ 23360–78 мм
Штифт цилиндрический ГОСТ 3128–70
Вид спереди.cdw

Техническая хаарктеристика
Вращающий момент на выходном валу
Частота вращения выходного вала
Передаточное отношение редуктора:
быстроходной ступени 5
тихохоходной ступени 3
Основные параметры зубчатых зацеплений
Степень точности по ГОСТ 1758-81
Необработанные поверхности корпуса и крышки редуктора
покрыть грунтовкой ГФ-021 ГОСТ 25129-82
поверхности покрыть серой краской ПФ-115 ГОСТ 6465-76
внутренние поверхности - маслостойкой краской НЦ-5123
Плоскость разъема редуктора и крышки покрыть
герметиком УТ-34 ГОСТ 24285-80.
л. индустриального масла И-Г-А-68
Осевые люфты входного вала поз. 5 обеспечить
регулировкой подшипников поз. 27 в пределах 0
помощью регулировочных прокладок поз. 19.
Осевые люфты промежуточного вала поз. 6 обеспечить
Проверить вручную плавность вращения валов.
Редуктор обкатать без нагрузки при частоте n = 960мин
в течении 3-х часов.
После обкатки мао в редукторе заменить.
двухступенчатый цилиндрический
Спецификация(1).spw

Промежвал.cdw

Нормальный исходный контур
Коэффициент смещения
Обозначение чертежа
Сталь 40Х ГОСТ 4543-81
*Размер обуспечивается инструментом
Общие допуски по ГОСТ 30893.1-mK.
Колесо.cdw

Коэффициент смещения
Обозначение чертежа
Сталь 40Х ГОСТ 4543-81
*Размер обеспечить инструментом.
Неуказанные радиусы скруглений 3 7 мм.
Общие допуски по ГОСТ 30893.2-mK.
Рекомендуемые чертежи
- 29.07.2014
- 24.01.2023
Свободное скачивание на сегодня
Другие проекты
- 24.04.2014