Проектирование привода грузоподъемного устройства




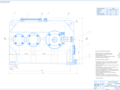
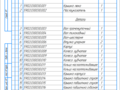
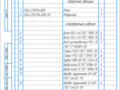
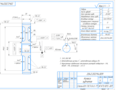
- Добавлен: 24.01.2023
- Размер: 2 MB
- Закачек: 0
Описание
Проектирование привода грузоподъемного устройства
Состав проекта
![]() |
![]() |
![]() ![]() ![]() ![]() |
![]() ![]() ![]() ![]() |
![]() |
![]() ![]() ![]() |
![]() ![]() ![]() |
![]() ![]() ![]() |
![]() ![]() ![]() |
![]() ![]() ![]() |
![]() ![]() ![]() |
![]() ![]() ![]() |
![]() ![]() ![]() |
![]() ![]() ![]() |
![]() ![]() ![]() |
![]() ![]() ![]() |
![]() ![]() ![]() |
![]() ![]() ![]() |
![]() ![]() ![]() ![]() |
![]() ![]() ![]() ![]() |
![]() ![]() ![]() ![]() |
![]() ![]() ![]() ![]() |
![]() ![]() ![]() ![]() |
![]() ![]() ![]() ![]() |
Дополнительная информация
редуктор вид сбоку.cdw

Вращающий момент на тихоходном валу
Частота вращения тихоходного вала
Общее передаточное число 105
Степень точности изготовления зубчатых передач 8-В
Коэффициент полезного действия 0
Технические требования к редуктору:
Необработанные поверхности литых деталей
красить маслостойкой красной эмалью
НЦ-5123 ГОСТ 7462-73.
Наружные поверхности корпуса красить серой эмалью ПФ-115
Плоскость разъема покрыть тонким слоем герметика УТ-34
ГОСТ 24285-80 при окончательной сборке.
Валы должны проворачиваться от руки плавно
Осевой люфт подшипников поз. 27
обеспечить регулировкой деталей поз 12.
Залить в редуктор масло И-Л-А-22 ГОСТ 20799-88 в
количестве 7 литров.
Редуктор обкатать при частоте вращения входного вала
30 обмин в течении трех часов
после чего масло заменить.
* Размер для справок
Вал.cdw

Сталь40X ГОСТ4543-71
Технические требования.
*Размер обеспечивается инструментом.
Неуказанные пердельные отклонения размеров: валов h14
Центровые отверстия А5 по ГОСТ 14034-81.
Неуказанные радиусы скругления R1.
ПЗ.docx
1. Выбор электродвигателя.
1.1. Определение потребляемой мощности для подъема груза.
Пощность привода определяемая по формуле:
Значение потерь мощности учитывается КПД рассчитываемым по универсальной формуле:
гдеоп - КПД открытой передачи принимаемый равным 094 096;
бар - КПД барабана учитывающий потери за счет внутреннего трения в канате и трения каната в контакте с барабаном. Обычно бар = 085 095;
м - потери в муфтах соединяющих валы электродвигателя и редуктора м = 098 ;
т б - КПД тихоходной и быстроходной передачи принимаем их равным 097 ;
1.2. Определение диапазона частот вращения вала электродвигателя обеспечивающее применение двухступенчатого цилиндрического редуктора.
где iдр- передаточное отношение цилиндрического редуктора
iозп- передаточное отношение открытой зубчатой передачи
nэ = 2693 *(8 25)*(25 5)=64632 336625 обмин.
Выбираем двигатель АИР 100S4 ТУ16-525.564-84 с номинальными оборотами
2. Расчет эквивалентного времени работы.
Эквивалентное время работы Lhe назначают с учетом категории режима работы по ГОСТ 21354-87 по формуле:
где H - коэффициент зависящий от режима работы
Lh - заданный срок службы час .
Lhe=025*14500=3625 ч.
Выбор оптимального варианта компоновки редуктора.
Условие для выбора наилучшего варианта разбивки отношения редуктора.
)=aWT -D2Б2- dвых210 .. 15 мм ;
)D2T > D2Б - для обеспечения условий смазки ;
)D2T должно быть близко по значению к D2Б .
Значения для выбора наиболее рационального варианта разбивки редуктора представлены в распечатке.
) =150 -112352- 422=72825 мм
) =150 -122412- 422=67795 мм
). =140 -134192- 422=51905 мм
Выбираем оптимальный вариант 5.
Статический расчет редуктора.
1.Расчет частоты вращения валов.
Частоты вращения валов и зубчатых колес определяются следующим образом:
- частота вращения быстроходного вала - из предварительного расчета принимаем
n1 = n1Б = 1440 мин-1;
- частота вращения промежуточного вала
n1Т = n2Б = n1Б uБ=1440521=27639 мин-1;
где uБ - принятое значение передаточного числа для быстроходной передачи ;
- частота вращения тихоходного вала
n2Т = n1Б (uБ * uТ)=14402157=6676 мин-1;
2.Расчет моментов на валах.
Момент на хвостовике быстроходного вала Нм
Момент на шестерне полушеврона быстроходной передачи
Момент на колесе полушеврона быстроходной передачи имеющем ширину зубчатого венца указанную в распечатке
Момент на шестерне тихоходной передачи редуктора
3.Определение усилий в зацеплении зубчатых передач.
Окружная сила на шестерне быстроходной передачи Н
Радиальная сила на шестерне быстроходной передачи
где - угол наклона зубьев (указан в распечатке); w - угол зацепления определенный в п. 1.3.6.
Осевая сила на шестерне быстроходной передачи
Усилия действующие на колесо быстроходной передачи:
Окружная радиальная и осевая силы на шестерне тихоходной передачи:
Усилия действующие на колесо тихоходной передачи:
Разработка эскизного проекта редуктора.
1.Определение диаметров валов.
Диаметры участков валов можно определить по формулам:
-для быстроходного вала:
Полученный размер согласовываем с диаметром вала электродвигателя dэд.:
-для тихоходного вала:
В целях унификации для быстроходного и промежуточного вала примем одинаковые значения dп. Следовательно диаметры быстроходного и промежуточного вала равны dб = dп =40 (мм).
Для других валов диаметры определяются по формулам имеющие рекомендательный характер поскольку результаты получаемые при их использовании могут войти в противоречие с требованиями предъявляемые к конкретному валу.
Для валов можно принять:
-диаметр цапфы быстроходного вала и промежуточного вала под подшипник:
-диаметр цапфы тихоходного вала:
полученные значения следует округлить до кратного пяти в соответствии с диаметрами внутренних колес подшипников качения:
dп = 35 (мм)-для быстроходного и промежуточного валов;
dп = 60 (мм)-для тихоходного вала;
-диаметр буртика для упора кольца подшипника быстроходного и промежуточного валов:
-диаметр буртика для упора кольца подшипника тихоходного вала:
Длина посадочного участка быстроходного вала:
Длина посадочного участка тихоходного вала:
Длина промежуточного участка быстроходного вала:
- принимаем равное 56 (мм).
Длина промежуточного участка тихоходного вала:
- принимаем равное 70 (мм).
2.Геометрический расчет зубчатых колес.
Геометрический расчет выполняется в минимальном объеме. Определению подлежат: делительные d1 и d2 и начальные dw1 и dw2 диаметры колес; коэффициенты смещения X1 и диаметры окружностей вершин da1 и угол зацепления w; коэффициент торцевого перекрытия ; коэффициент осевого перекрытия для косозубых колес. Все колеса нарезаются реечным инструментом или долбяком с исходным контуром по ГОСТ 13755-81 с параметрами: угол профиля = 20; коэффициентом головки (ножки) зуба ; коэффициент радиального зазора с* = 025.
2.1.Прямозубое колесо.
Суммарный коэффициент смещения X = X1 + X2 = X задан в распечатке. Далее:
- делительные диаметры приводятся в распечатке. Тем не менее:
- начальные диаметры:
- коэффициент перекрытия:
- для каждого из колес.
2.2.Косозубое колесо.
Расчет основных размеров проводят по формулам п. 4.2.1. за исключением диаметров d1 и d2. Принимают:
Коэффициент торцового перекрытия для косозубых передач:
Коэффициент осевого перекрытия:
Суммарный коэффициент перекрытия:
3.Определение расстояния между деталями передач.
4.Выбор подшипников.
Быстроходный вал - подшипник 208 легкой серии.
d = 40 (мм); D = 80 (мм);
B = 18 (мм); r = 2 (мм);
Сr = 256 (кН); Сrо = 181 (кН).
Промежуточный вал - подшипник с коротким цилиндр роликом №42306 средней серии.
d = 30 (мм); D = 72 (мм);
B = 19 (мм); r = 2 (мм);
Сr = 301 (кН); Сor = 206 (кН).
Тихоходный вал – подшипник № 312 средней серии.
d = 60 (мм); D = 130 (мм);
B = 31 (мм); r = 25 (мм);
Сr = 641(кН); Сor = 494 (кН).
5.Конструирование зубчатых колес.
На рис.1. изображена обобщенная конструкция зубчатых колес. Основные элементы зубчатых колес - обод (или зубчатый венец) диск и ступица.
Обод воспринимает нагрузку от зубьев и должен быть достаточно прочным. В то же время он должен быть податливым чтобы способствовать равномерному распределению нагрузки по длине зуба.
Рекомендуют выполнять
Ступица служит для соединения колеса с валом. В конструкциях зубчатых колес длину ступицы варьируют в широких пределах:
Наружный диаметр ступицы
Диск соединяет обод и ступицу. Рекомендуют:
Иногда в дисках выполняют 46 отверстий. Эти отверстия используют при транспортировке и обработке колеса а при больших размерах и для уменьшения массы.
Уклоны и радиусы необработанных поверхностей:
- штамповочные уклоны рекомендуют принимать равными 50;
- радиусы закруглений:
Фаски по торцам зубчатого венца
5.1.Косозубое колесо.
5.2.Прямозубое колесо.
Проверочный расчет редуктора.
1. Подбор материала твердости и термообработки зубчатых колес.
Зубчатые колеса редукторов изготавливают из сталей с твердостью H 350 HB или H > 350 HB. В первом случае заготовки для колес подвергают нормализации или улучшению во втором - после нарезания зубьев различным видам термической и химико-термической обработки: объемной закалке поверхностной закалке ТВЧ цементации азотированию нитроцементации и т.д. обеспечивающим высокую твердость поверхности зуба. Относительно низкая твердость H 350 HB допускает возможность зубонарезания с достаточной точностью (степень точности 8 и 7 по ГОСТ 1643-81) без отделочных операций что используется как средство для снижения затрат. Применение других видов термообработки вызывает заметное искажение размеров и формы зубьев (коробление). При высоких требованиях к точности такие колеса подвергают отделочным операциям - зубошлифованию притирке на специальных станках обкатке и т.п. что повышает стоимость колес в десятки раз.
Зубчатые колеса с низкой твердостью хорошо прирабатываются особенно если зубья шестерни имеют твердость больше чем у колес на (80 200) HB. У косозубых колес перепад твердости выше. Хорошие результаты обеспечивает закалка ТВЧ зубьев шестерен с HRC 45 55 и термоулучшение колес до 280 350 HB.
При выборе материалов необходимо руководствоваться информацией указанной в табл. 2 и стремиться к получению допускаемых напряжений возможно близких к ним величин [H]Б и [H]Т.
Термообработка или хим.терм.обработка
Х 40ХН 35ХМ 45ХЦ Сталь 45
поверхность 45 55 HRC
сердцевина 240 300 HB
поверхность 60 63 HRC
сердцевина 300 400 HRC
Х 20ХНМ 18ХГТ 12ХН3А
выбрали сталь 40ХН - для тихоходной передачи. Для колеса прямозубой передачи с твердостью НВ=270 а для шестерни с твердостью НВ=300.
Для быстроходной передачи выберем туже сталь 40ХН. Для колеса косозубой передачи с твердостью НВ=380 а для шестерни с твердостью НВ=395.
2. Проверочный расчет промежуточного вала.
2.1. Расчет допускаемых контактных напряжений.
) Допускаемые контактные напряжения для шестерни [H]1 или колеса [H]2 быстроходной ступени :
где SH - коэффициент безопасности (табл. 2); H0 - предел контактной выносливости. Для наиболее применяемых материалов и термообработки показан в табл. 2; ZN - коэффициент учитывающий срок службы (ресурс) и режим работы определяемый из условия для шестерни или колеса (индекс опущен):
где NH0 - базовое число циклов перемены напряжений определяемое по графику (рис. 8.40 [2]) или по формуле
NH01 = 30HBш24=3030024=264107 12107;
NH02 = 30HBк24=3027024=205107 12107.
NHE - эквивалентное число циклов соответствующее
NHE = NH KHE = 60 nw n LhЕ
где nw - число зацеплений в которое входит шестерня или колесо за один оборот в нашем случае nw = 1; n - соответствующая частота вращения мин-1; Lh - ресурс привода час; H - коэффициент режима определяемый по табл. 8.10 [2] в зависимости от категории режима.
NHE1 = 60 nw n LhЕ = 60 1 12500 025 27639 = 518107;
NHE2 = 60 nw n LhЕ = 60 1 12500 025 1440 = 27107;
Так как zN находится в пределах (1zN18) принимаем zN1=1.
Так как zN находится в пределах (1zN18) принимаем zN2=1.
Допускаемое контактное напряжение для шестерни и для колеса:
Допускаемое контактное напряжение для быстроходной передачи принимаем равным допускаемому контактному напряжению шестерни тихоходной передачи
) Допускаемые контактные напряжения для шестерни [H]1 или колеса [H]2 тихоходной ступени :
NH01 = 30HBш24=3039524=46107 12107;
NH02 = 30HBк24=3038024=51107 12107.
NHE1 = 60 nw n LhЕ = 60 1 12500 025 27639 = 91107;
NHE2 = 60 nw n LhЕ = 60 1 12500 025 1440 = 518107;
Так как zN находится в пределах (1zN18) принимаем zN1=11.
Допускаемое контактное напряжение для тихоходной передачи принимаем равным допускаемому контактному напряжению шестерни тихоходной передачи
2.2. Расчет допускаемых напряжений изгиба.
) Допускаемые напряжения изгиба определяются для шестерни [F]1 и колеса [F]2 быстроходной ступени :
где F0 - предел изгибной выносливости определяемый по табл. 2; SF - коэффициент безопасности приведенный в табл. 2; YА - коэффициент учитывающий влияние двухстороннего приложения нагрузки. В нашем случае YА = 1;
YN - коэффициент учитывающий срок службы передачи и переменность режима нагружения рассчитываемый по формуле:
где NF0 - базовое число циклов. Для всех сталей NF0 = 4106; NFE- эквивалентное число циклов:
NFE = NF F = 60 nw n Lh F
где nw - число зацеплений в которое входит шестерня или колесо за один оборот в нашем случае nw = 1; n - соответствующая частота вращения мин-1.
YR - коэффициент учитывающий шероховатость переходной кривой. YR = 1 при шероховатости RZ 40 мкм.
NFE1 = 60 nw n Lh F = 60 1 27639 12500 025 = 518 107;
NFE2 = 60 nw n Lh F = 60 1 1440 12500 025 = 27 107;
Из условия (1YN2.5) принимаем YN=1.
Допускаемое напряжение изгиба для шестерни и для колеса:
) Определим допускаемые напряжение изгиба для тихоходной передачи.
2.3. Расчет рабочих контактных напряжений.
Контактное напряжение в зацеплении определяется по формуле
Для прямозубой передачи принимают ZH = 1 подставляя следующие значения параметров:
Eпр - приведенный модуль упругости. Для стальных колес и шестерен
Т1 - момент на шестерни передачи Нм. Для тихоходной передачи - Т1(Т);
dw1 - начальный диаметр шестерни мм;
bw - ширина зубчатого венца колеса мм;
w - угол зацепления;
u - передаточное число передачи u = z2 z1 .
Определим степень точности (nст) редуктора коэффициент распределения нагрузки между зубьями (K) коэффициент концентрации нагрузки (KH) и коэффициент динамической нагрузки (KV).
Степень точности выбирают в зависимости от назначения и условий работы передачи. В нашем случае редуктор будет работать при повышенных нагрузках и умеренных скоростях поэтому степень точности выбрали nст=8.
Для нахождения коэффициента распределения нагрузки между зубьями KH воспользуемся формулой :
)для быстроходной ступени
Коэффициент нагрузки KH представляется в виде
где KH - коэффициент учитывающий распределение нагрузки по ширине венца находится по графикам на рис. 8.15 [2] в зависимости от схемы редуктора от параметра bd = bw dw1 и от сочетания твердости зубьев шестерни и колеса;
KHV - коэффициент учитывающий динамическую нагрузку в зацеплении зависящий от вида передачи степени точности и окружной скорости V и назначаемый по табл. 8.3 [2].
KH = KHТ KHVТ = 1 · 12 = 12.
Контактное напряжение для шестерни быстроходной передачи:
Контактное напряжение удовлетворяет условию
)для тихоходной ступени
KH = KHТ KHVТ = 102 · 106 = 108.
Контактное напряжение для шестерни тихоходной передачи:
2.4. Расчет рабочих напряжений при изгибе.
Напряжения при изгибе в основании зубьев прямозубых шестерн (F1) и колесе (F2) определяют по формулам:
F1 = YF1 Ft KF (bw m) МПа;
где YF1 и YF2 - коэффициенты учитывающие форму зубьев соответственно шестерни и колеса назначаемые по графику рис. 8.20 [2] в зависимости от числа зубьев z и коэффициента смещения X;
Ft - окружная сила в зацеплении bw - ширина зубчатого венца; m - модуль зацепления.
KFT = 124 13 112 = 18.
Рабочее напряжение при изгибе в шестерне тихоходной передачи:
Рабочее напряжение при изгибе в колесе тихоходной передачи:
2.5. Проверка прочности по контактным и изгибным напряжениям.
Передача считается прочной и работоспособной если выполняются следующие условия:
) контактная выносливость поверхностей зубьев быстроходной ступени
контактная выносливость поверхностей зубьев тихоходной ступе ни
276 (МПа) 7818 (МПа);
) изгибная выносливость зубьев шестерни быстроходной ступени
914 (МПа) 32914 (МПа);
изгибная выносливость зубьев шестерни тихоходной ступени
33 (МПа) 4063 (МПа);
) изгибная выносливость зубьев колеса быстроходнй ступени
46 (МПа) 3188 (МПа).
изгибная выносливость зубьев колеса тихоходной ступени
97 (МПа) 3908 (МПа).
Так как все условия выполняются наша передача является прочной и работоспособной.
Расчет промежуточного вала на прочность
Рис. 2. Расчетная схема промежуточного вала.
1 Определение моментов действующих на промежуточный вал.
Определим координаты средних плоскостей подшипников и зубчатых колес:
Соответственно: L1 = L4 = e = 35мм; L2 = L3 = c = 49мм.
Определим реакции в опорах:
Определим моменты в вертикальной плоскости и построим эпюру моментов:
Рис 3. Эпюра моментов вертикальной плоскости.
Определим моменты в горизонтальной плоскости и построим эпюру моментов:
Рис 4. Эпюра моментов горизонтальной плоскости.
Определим суммарный изгибающий момент в опасных сечениях:
Можно выделить три опасных сечения C D E т.к. в них изгибающие моменты имеют наибольшее значение.
Рис. 5. Суммарный изгибающий момент.
2 Определение фактического запаса прочности промежуточного вала
где и - коэффициенты запаса по нормальным и касательным напряжениям.
где и - амплитуды запаса напряжений;
и - средние напряжения циклов;
и - переделы выносливости гладких образцов при симметричном цикле изгиба и кручения;
и - эффективные коэффициенты концентрации напряжений;
Кd – коэффициент влияния шероховатости;
и - коэффициенты чувствительности материала.
Материал: Сталь 40ХН
Выбираем значения коэффициентов: [ Л стр. 146 табл. 106]
В опасных сечениях С и Е S=7 что больше минимально допустимого [S]=15 следовательно работоспособность обеспечена.
3. Проверка промежуточного вала.
3.1. Определение запаса прочности вала.
3.2. Проверка правильности выбора подшипников.
Подшипник промежуточного вала с коротким цилиндрическим роликом №42307 средней серии. Его характеристики:
- динамическая грузоподъемность Сr = 302 (кН);
- статическая грузоподъемность Сor = 206 (кН).
р - эквивалентная нагрузка;
а1 - коэффициент надежности;
а2 - обобщенный коэффициент совместного влияния на условия эксплуатации.
Для шариковых подшипников степень р = 3.
а). Определение эквивалентных нагрузок действующих на опоры А и В.
РА = (ХА V A + YA FA) Kб KT .
РВ = (ХА V A + YA FA) Kб KT.
К - коэффициент безопасности принимаем равным 13;
KT - температурный коэффициент принимаем равным 1;
V - коэффициент вращения принимаем равным 1.
Так как сила FA = 0 то коэффициенты Х и Y соответственно равны 1 и 0.
Найдем эквивалентные нагрузки действующие на опоры:
РА = (1 1 30637) 1 13 = 398281 (Н);
РВ = (1 1 30637) 1 13 = 398281 (Н).
Так как опоры А и В являются одинаково нагруженными то расчет ведем по любой опоре.
б). Определение ресурса подшипника.
LE = 60 10-6 276 12500 = 207 (млн.обр.).
Так как выше указанное условие выполняется значит подшипник подобран верно.
4. Подбор и расчет шпоночных соединений.
Шпонки под колесами промежуточного вала.
d = 36 (мм); b = 12 (мм);
t1 = 5 (мм); t2 = 3 (мм):
«Шпонка 12х8х36 ГОСТ 23360-78».
Рассчитаем напряжение смятия:
где Т - моменты на валах и колесах редуктора;
d - диаметр вала под колесом или под муфтой.
Шпонка под колесом тихоходного вала.
d = 40 (мм); b = 12 (мм);
t1 = 5 (мм); t2 = 33 (мм):
«Шпонка 12х8х40 ГОСТ 23360-78».
Шпонка на входном валу.
d = 52 (мм); b = 10 (мм);
«Шпонка 10х8х28 ГОСТ 23360-78».
Шпонка на выходном валу.
d = 60 (мм); b = 18 (мм);
t1 = 7 (мм); t2 = 44 (мм):
«Шпонка 18х11х50 ГОСТ 23360-78».
Содержание - 2 лист.docx
Конструирование рамы
Список использованной литературы
Эскизы стандартных изделий
Спецификация на редуктор
Спецификация на приводную станцию
Содержание.docx
Проектирование привода
1Расчет рабочего органа машины
2Подбор электродвигателя .
3Определение передаточного отношения .
4Разработка исходных данных для ввода в ЭВМ .
5Анализ полученных результатов и выбор наиболее оптимального варианта .
Геометрический расчет редуктора ..
1Прямозубая передача ..
2Косозубая передача ..
Статический расчет редуктора ..
1Расчет частот вращения валов ..
2Расчет вращающих моментов на валах
3Расчет усилий в зацеплениях быстроходной и тихоходной передач передачи
Расчет на прочность зубчатых передач редуктора .
1Определение материалов и термообработки
2Допускаемые контактные напряжения .
3Допускаемые напряжения изгиба .
4Контактные напряжения в зацеплении передачи
5Напряжение изгиба в зубьях шестерни и колеса ..
6Заключение о работоспособности передачи ..
Разработка эскизного проекта редуктора ..
1Конструирование валов редуктора привода .
2Определение расстояния между деталями ..
3Выбор подшипников ..
Расчет промежуточного вала на прочность ..
1Определение моментов действующих на промежуточный вал .
2Определение фактического запаса прочности промежуточного вала
Проверочный расчет подшипников промежуточного вала .
Расчет шпоночного соединения
Расчет открытой передачи ..
Конструирование корпусных деталей и крышек .
1Корпус редуктора ..
3Выбор крышек подшипника .
Расчет отклонений размеров зубчатого колеса промежуточного вала ..
Компоновка приводной станции .
1Конструирование рамы
Список использованной литературы
Эскизы стандартных изделий
Спецификация на редуктор
Спецификация на приводную станцию .
Конструирование корпусных деталей.docx
1. Корпус редуктора.
1.1. Выбор крышек подшипников.
Для данного редуктора целесообразно применение глухих закладных крышек подшипников изготовленных из серого чугуна марки СЧ21 [2 стр. 150].
Основные размеры крышек приведены на рисунке 4.
Рисунок 4 – крышка подшипника.
Диаметр D крышки равен диаметру внешнего кольца подшипника. Диаметр DМ равен внешнему диаметру манжетного уплотнения.Размеры 1 диаметры и количество винтов крепления крышки принимаем исходя из рекомендаций [2 стр. 151]. Для быстроходного вала: = 8 мм 1 = 6 мм S= 6 мм С= 3 мм l=5 мм b= 5 мм
Для промежуточного вала: = 6 мм 1 = 6 мм S= 6 мм С= 3 мм l=5 мм b= 6 мм
Для тихоходного вала: = 5 мм 1 = 5 мм S= 5 мм С= 3 мм l=6 мм b= 8 мм
1.2. Конструктивное оформление стенок редуктора.
В нашем случае при среднесерийном производстве целесообразно и экономически выгодно изготавливать крышки и корпус редуктора методом литья из серого чугуна марки СЧ20.
Толщину стенок корпуса принимаем
В нашем случае принимаем .
Данная толщина отвечает требованиям технологии литья и необходимой жесткости корпуса редуктора [2 стр. 234].
Остальные размеры стенок корпуса показаны на рисунке 5 и определяются по формулам:
Рисунок 5 – Стенки корпуса редуктора.
1.3. Конструктивное оформление приливов для
подшипниковых гнезд и винтов крепления крышки
Крышка корпуса крепится к основанию винтами с шестигранной головкой диаметр которых определяем исходя из рекомендаций [2 стр 240]. Определим диаметр винта опираясь на формулу:
Используем винты М14 с шестигранной головкой длиной 70 мм. (длина определяется конструктивно с учетом материала из которого выполнен корпус в нашем случае это чугун и винты должны быть закручен на расстояние не меньшее чем 15 диаметра).
Диаметры фланцевых винтов определяется по формуле dф = (06 07)d = (10 12) мм. Принимаем dф равным 10 мм.
Приливы в которых располагаются подшипники и отверстия под винты крепления крышки корпуса конструктивно оформлены в соответствии с рекомендациями [2 стр. 238 - 245] и изображены на рисунке 6.
Внутренний диаметр отверстия D определяется для опоры каждого вала диаметром внешнего кольца подшипника:
для опор быстроходного вала – 110 мм.
для опор промежуточного вала – 100 мм.
для опор тихоходного вала – 170 мм.
Радиусы скруглений R и r зависят от толщины стенок корпуса и равны 12 мм. [2 стр. 239]
Высоту h c которой начинается уклон корпуса в 45° определяется как 05H Н – высота крышки корпуса равная 158 мм. отсюда h = 79 мм.
Рисунок 6 – конструкция приливов подшипниковых гнезд.
Высоту h’ прилива в крышке под стягивающий болт определяем графически исходя из условия размещения головки болта на плоской опорной поверхности. В нашем случае крышка редуктора крепится болтами с шестигранной головкой М14 поэтому принимаем h’ равной 70 мм.
Ширину фланца l принимаем равной (2 22) т.е. 14 мм.
Длина l2 подшипниковых гнезд определяется конструктивно шириной подшипников в опорах высотой крышки и расстоянием от подшипника до внутреннего края прилива равного 2 мм. В нашем случае l2 постоянна для всех гнезд и равна 57 мм.
Ширина фланца l3 равна длине подшипниковых гнезд за вычетом припуска на обработку h равного 05 т.е. 3 мм. l2 постоянна для всех гнезд и равна 54 мм.
2. Выбор уплотнений.
Для предохранения вытекания смазочного материала из подшипниковых узлов а также для защиты их от попадания извне пыли и влаги используем армированные манжетные уплотнения из бензомаслостойкой резины. В нашем случае достаточно установить манжеты без пыльника и в один ряд так как уровень масла не доходит до уровня манжеты и редуктор не предназначен для работы в запыленной внешней среде.
На быстроходном валу устанавливаем манжету 32х52 на тихоходном 60х85. Установленные манжеты соответствуют ГОСТ 8752-79.
Эскизы стандартных изделий.docx
Подшипники шариковые радиальные однорядные
Винты с цилиндрической головкой и шестигранным углублением под ключ (ГОСТ 11738-84) мм.
Болты с шестигранной головкой (ГОСТ 15589-70) мм.
Шпонки призматические (ГОСТ 23360-78) мм.
Штифты конические (ГОСТ 3129-70) мм.
Шайбы пружинные нормальные (ГОСТ 6402-70).
Номинальный диаметр резьбы
Шайба концевая 7019-0631 (ГОСТ 14734-69) мм.
Шайба стопорная (ГОСТ 13464-77) мм.
Прокладки уплотнительные паронитовые (ГОСТ 15180-86) мм.
Гайка шестигранная с уменьшенным размером «под ключ» (ГОСТ 15522-70) мм.
Резиновые армированные манжеты для валов
Маслосливная пробка (ГОСТ 9347-74) мм.
Муфта упругая втулочно-пальцевая МУВП-28
Приводная станция.doc
1. Конструирование рамы.
При монтаже приводов состоящих из электродвигателя и редуктора должны быть выдержаны определенные требования точности относительно положения узлов. Для этого узлы привода устанавливают на сварных рамах или литых плитах.
В нашем случае целесообразно и вполне оправдано применение сварной рамы.
Применим раму из двух продольно расположенных швеллеров и приваренных к ним трех расположенных поперечно. Это обеспечит необходимую жесткость опорных поверхностей при сравнительной простоте изготовления. Используем швеллеры №10У [2 стр. 372] Конструкция рамы показана на рисунке 7.
Для создания базовых поверхностей под двигатель и редуктор на раме размещаем платики в виде узких полос толщиной 5 мм. Размеры платиков: под двигатель – два платика 280х60 мм. под редуктор – два платика 300х65 мм. [2 стр. 372].
Рисунок 8 – сварная рама привода.
Для соединения электродвигателя со входным валом редуктора используем упругую втулочно-пальцевую муфту т.к. эти муфты достаточно просты по конструкции удобны при замене упругих элементов и не имеется жестких требований к компенсирующей способности.
Предварительно выбираем муфту МУВП-32 соответствующую стандарту ГОСТ 2096-64.
Выполним проверочный расчет упругих элементов муфты на смятие и пальцев муфты на изгиб.
Допуская что нагрузка между пальцами распределена равномерно можем использовать следующую формулу для расчета упругих элементов муфты на смятие:
где Tk – вращающий момент Нм.
dп – диаметр пальца; dп = 14 мм.;
zc – число пальцев zc = 6;
D0 – диаметр окружности расположения пальцев для муфты МУВП-28 D0 = 82 мм.;
Вращающий момент определяем по формуле
где Тн – номинальный длительно действующий момент.
К– коэффициент режима работы. При равномерной нагрузке
см=21033136(6821428) = 04 МПа
Пальцы муфты изготавливают из стали 45 и рассчитывают на изгиб:
и=2103 Tк (05lвт+с)(zcD001dп3) ≤ [и]
где с – зазор между полумуфтами равный 5 мм.
где т – предел текучести материала пальцев. Для стали 40 т = 750 МПа. [4 том 1 стр. 88].
[и] = 045750 = 2205 МПа
и=2103 3136 (0528+5)(68201143) = 8827 МПа
Отсюда делаем вывод о том что выбранная муфта работоспособна и применима в нашем случае.
Для муфты МУВП-32 по ГОСТ 2096-64 предельные смещения валов следует принимать:
радиальные Δ = 010 015 мм.
угловые γ = 06100 мммм.
Титульный лист.docx
Российской Федерации
УФИМСКИЙ ГОСУДАРСТВЕННЫЙ АВИАЦИОННЫЙ ТЕХНИЧЕСКИЙ УНИВЕРСИТЕТ
Кафедра «Основы конструирования механизмов и машин»
ПРОЕКТИРОВАНИЕ ПРИВОДА ГРУЗОПОДЪЕМНОГО УСТРОЙСТВА
ПОЯСНИТЕЛЬНАЯ ЗАПИСКА
по дисциплине «Детали машин и основы конструирования»
КонсультантС.В. Чертовских
Список литературы.docx
Прокшин С.С. Беляев Б.А. Методические указания к курсовому проектированию по дисциплине «Детали машин и основы конструирования»: Уфимск. гос. авиац. техн. ун-т. – Уфа 2006. – 58 с.
Дунаев П.Ф. Леликов О.П. Конструирование узлов и деталей машин: учебное пособие. – 9-е изд. перераб. и доп. – М.: Академия 2006. – 496 с.
Ноготков О.Ф. Измерительные размеры зубчатых колес: Методические указания к курсовому проектированию по деталям машин и основам конструирования Уфимск. гос. авиац. техн. ун-т. – Уфа 2003. – 17 с.
Анурьев В.И. Справочник конструктора-машиностроителя: в 3-х томах. Т.1-3 – 5-е изд. перераб. и доп. – М.: Машиностроение 1978.
Анухин В.И. Допуски и посадки: учебное пособие. – 2-е изд. перераб. и доп. – СПб.: Издательство СПбГТУ 2001. – 219 с.
Иванов М.Н. Детали машин: Учеб. для студентов вузов. – 6-е изд. перераб. – М.: Высш. шк. 2000 – 383 с. ил.
Дунаев П.Ф. Леликов О.П. Детали машин. Курсовое проектирование: Учеб. пособие.– 2-е изд. перераб. и доп. – М.: Высшая школа 1990 – 399 с. ил.
Содержание - 1 лист.docx
Проектирование привода лебедки
Определение диаметра грузового каната
Определение диаметра барабана
Определение частоты вращения барабана
Выбор электродвигателя
Определение момента на барабане лебедки
Момент на зубчатом колесе тихоходной передачи
Допускаемые контактные напряжения
Коэффициенты относительной ширины колес
Эквивалентное время работы
Выбор оптимального варианта компоновки редуктора
Статический расчет редуктора
Расчет частот вращения валов
Расчет моментов на валах
Определение усилий в зацеплении зубчатых передач
Разработка эскизного проекта редуктора
Определение диаметров валов
Геометрические расчеты зубчатых колес
Определение расстояний между деталями передач
Конструирование зубчатых колес
Проверочный расчет редуктора
Подбор материала твердости и термообработки зубчатых колес проверочный расчет
Проверочный расчет промежуточного вала
Проверочный расчет подшипников
Подбор и расчет шпоночных соединений
Конструирование корпусных деталей и крышек
Расчет отклонений размеров и допусков формы зубчатого колеса быстроходной ступени и промежуточного вала
Расчет отклонений размеров допусков формы зубчатого колеса быстроходной ступени
Расчет отклонений размеров допусков формы промежуточного вала
Пояснительная запискаFinal (Автосохраненный).docx
1 Расчет рабочего органа машины
Конструкции канатов должны соответствовать ГОСТам 3067-74 2688-69 или 3081-69.
В упрощенных расчетах для легкого и средних режимов диаметр каната dк можно определить по формуле
где Fk – усилие в канате определенное в задании.
Диаметр грузового барабана лебедки предварительно назначаем из условия:
Полученное значение округляем в большую сторону до размера Dбар кратного десяти:
Длину грузового барабана лебедки определяем по формуле:
lб = 15*260= 390 мм.
Частота вращения барабана вычисляется по формуле:
где V – скорость лебедки (ммин).
Крутящий момент барабана:
где F – нагрузка на барабан (кН).
Мощность привода определяем по формуле
Значение потерь мощности учитывает КПД рассчитываемым по универсальной формуле:
где - КПД барабана учитывающий потери за счет внутреннего трения в канате и трения каната в контакте с барабаном. Обычно =085 095;
- КПД открытой передачи принимаемый равным 094 096;
- потери в муфтах соединяющих валы электродвигателя и редуктора. =098;
- КПД тихоходной и быстроходной передачи принимаем х равных 097.
Определяем мощность привода:
2 Выбор электродвигателя.
Определим диапазон частот вращения вала электродвигателя:
где- передаточное отношение цилиндрического редуктора = 8 25;
- Передаточное отношение открытой зубчатой передачи = 2.5 5;
Таким образом выбираем электродвигатель серии АИР типа 100S2 с мощностью P=48 кВт и частотой вращения = 2850 обмин
3 Определение передаточного отношения
Определение общего передаточного отношения:
Определим передаточное отношение редуктора:
где - передаточное отношение открытой зубчатой передачи
4 Разработка исходных данных для ввода в ЭВМ
Крутящий момент на выходном валу
Назначение термообработки материала и допускаемых контактных напряжений:
Если 1000 (термоулучшение нормолизация); 1000 > 1500 (закалка с низким отпуском); > 1500(цементация или азотирование). Из этих условий назначаем термообработку – термоулучшение.
Определим допускаемые контактные напряжения для тихоходной ступени:
Для передачи быстроходной ступени:
Полученные значения округляем до чисел кратных десяти:
Относительная ширина зубчатых венцов в передачах быстроходной и тихоходной ступеней редуктора подсчитываем по формулам:
-тихоходной передачи
-быстроходной передачи
Эквивалентное время работы Lhe назначают с учетом категории режима работы по ГОСТ 21354-87 по следующим правилам:
- по таблице 8.10 [ ] определяем коэффициент - режим нагружения. В нашем случае он равен среднему равновероятному второму классу где = 025.
- находим Lhe по формуле:
где Lhe- заданный срок службы час.
5 Анализ полученных результатов и выбор наиболее оптимального варианта
Определяем диаметр выходного вала:
где = 15 30 МПа. Принимаем = 20 МПа.
Условие для выбора наилучшего варианта разбивки передаточного отношения редуктора:
Рис. 1. Основные размеры трехступенчатой передачи
Значения для выбора наиболее рационального варианта разбивки редуктора представлены в распечатке (Приложение I).
Проверим выполнение условий для каждого варианта разбивки передаточного отношения редуктора.
Выбираем оптимальный вариант V.
Геометрический расчет передач редуктора.
Определению подлежат: делительные диаметры d1 и начальные диаметры dw1 и коэффициенты смещения диаметры окружностей вершин da1 и угол зацепления ; коэффициент осевого перекрытия для косозубых колес. Все колеса нарезаются реечным инструментом или долбяком с исходным контуром по ГОСТ 13755-81 с параметрами: угол профиля = 200; коэффициентом головки зуба ; коэффициент радиального зазора с*=025.
1 Прямозубая передача
- делительные диаметры:
- коэффициент торцевого перекрытия для косозубой передачи:
- коэффициент осевого перекрытия:
- суммарный коэффициент перекрытия:
2 Косозубая передача
-начальные диаметры:
- коэффициент перекрытия
Статический расчет редуктора
1 Расчет частот вращения валов
Частоту вращения быстроходного вала принимаем из предварительного расчета:
n1= n1б= 2850 мин-1.
Частота вращения промежуточного вала:
Частота вращения тихоходного вала:
Окружная скорость в зацеплении быстроходной передачи:
Окружная скорость в зацеплении тихоходной передачи:
2 Расчет вращающих моментов на валах
Рассчитаем моменты на валах и колесах редуктора. Момент на хвостовике быстроходного вала:
Момент на шестерне полушеврона быстроходной передачи:
Момент на колесе полушеврона быстроходной передачи:
Момент на шестерне тихоходной передачи редуктора:
3 Расчет усилий в зацеплениях быстроходной и тихоходной передач передачи
Окружная сила на шестерне быстроходной передачи:
Радиальная сила на шестерне быстроходной передачи:
Осевая сила на шестерне быстроходной передачи:
Усилия действующие на колесо быстроходной передачи:
Силы на шестерне тихоходной передачи:
Усилия действующие на колесо тихоходной передачи:
Расчет на прочность зубчатых передач редуктора
1 Определение материалов и термообработки
Зубчатые колеса редукторов изготавливают из сталей с твердостью Н350 НВ или Н>350НВ. В первом случае заготовки для колес подвергают нормализации или улучшению во втором – после нарезания зубьев подвергают различным видам термической и химико-термической обработки: объемной закалки поверхностной закалке ТВЧ цементации азотированию нитроцементации и т.д. обеспечивающим высокую твердость поверхности зуба.
Относительно низкая твердость при Н350 допускает возможность зубонарезания с достаточной точностью без отделочных операций что используется как средство для снижения затрат Применение других видов термообработки вызывает заметное искажение размеров и формы зубьев. При высоких требованиях к точности такие колеса подвергают отделочным операциям – зубошлифованию притирке на специальных станках обкатке и т.п. что повышает стоимость колес в десятки раз.
Зубчатые колеса с низкой твердостью хорошо прирабатываются особенно если зубья шестерни имеют твердость больше чем у колес на (80 200)НВ. У косозубых колес перепад твердости выше. Хорошие результаты обеспечивает закалка ТВЧ зубьев шестерни с HRC 45 55 и термоулучшение колес до 280 350 НВ.
Подбираем материал исходя из условия:
Так как материал подвергается только нормализации и улучшению
Определим твердость НВ с помощью которой подбираем материал:
Для подборки материала воспользуемся таблицей 8.7 [ ]. Выбираем сталь 40ХН для тихоходной и быстроходной передачи с параметрами стали:
Выбираем твердость для колес и шестерен быстроходной и тихоходной передачи:
Для быстроходной передачи: -колеса НВ2=235:
Для тихоходной передачи:-колеса НВ2=257;
2 Допускаемые контактные напряжения
Допускаемые контактные напряжения для передачи определяются по формуле:
где - меньшее из двух:
Определим допускаемое контактное напряжение для быстроходной передачи:
где- коэффициент безопасности выбираемый согласно таблицы 87[ ] равный =1.1;
- коэффициент учитывающий срок службы и режим работы определяемый из условия: для шестерни и колеса
где- базовое число циклов перемены напряжений;
- эквивалентное число циклов.
где- число зацеплений в которое входит шестерня или колесо за один оборот в нашем случае =1;
n – соответствующая частота вращения;
Lh – ресурс привода;
- коэффициент режима нагружения.
Так как NНЕ>NHO для колеса и шестерни а ZN должен лежать в пределах (1ZN18) то принимаем ZN = 1.
Допускаемые контактное напряжение для колеса:
Допускаемое контактное напряжение для шестерни:
Допускаемое контактное напряжение для быстроходной передачи:
Определим допускаемое контактное напряжение для тихоходной передачи:
Так как NНЕ>NHO следовательно ZN = 1.
Допускаемое контактное напряжение для колеса:
Допускаемое контактное напряжение для тихоходной передачи выбирается наименьшим из и .
3 Допускаемые напряжения изгиба
Допускаемые напряжения изгиба определяются для шестерни и колеса отдельно по формуле:
где - предел изгибной выносливости определяемый по таблице 8.8 [ ]:
- коэффициент безопасности приведенный в таблице 8.8 [ ];
- коэффициент учитывающий влияния двухстороннего приложения нагрузки. В нашем случае =1;
-коэффициент учитывающий шероховатость переходной кривой. =1 при шероховатости Rz 40 мкм.;
-коэффициент учитывающий срок службы передачи и переменность режима нагружения рассчитываемый по формуле:
где - базовое число циклов. Для всех сталей =;
- эквивалентное время работы:
Для колеса быстроходной ступени:
Так как YN должен лежать в промежутке от 1 до 25 то берем YN.
Для шестерни быстроходной ступени:
YN 1 следовательно принимаем YN = 1;
Для колеса тихоходной ступени:
Допускаемое напряжение изгиба:
Для шестерни тихоходной ступени:
4 Контактные напряжения в зацеплении передачи
Контактное напряжение в зацеплении определяется по формуле используемой для прямозубой и косозубой передачи:
Для прямозубой передачи принимают = 1 подставляя следующие значения параметров:
Епр – приведенный модуль упругости. Для стальных шестерен и колес ;
Т1 – момент на шестерне передачи Нм;
dw1 – начальный диаметр шестерни мм;
bw – ширина зубчатого венца колеса мм;
аw – угол зацепления;
u – передаточное число передачи.
Определим степень точности (nст) редуктора коэффициент распределения нагрузки между зубьями () коэффициент концентрации нагрузки () и коэффициент динамической нагрузки ().
Степень точности выбирают в зависимости от назначения и условий работы передачи. В нашем случае редуктор будет работать при передачах не требующих особлй точности следствии чего выбираем степень точности nст = 9;
Для нахождения коэффициента распределения нагрузки между зубьями воспользуемся формулой:
где - коэффициент значение которого находят по таблице 2.8 [ ] для колеса с меньшей твердостью. =027.
- начальное значение коэффициента распределения нагрузки между зубьями в связи с погрешностями изготовления определяют в зависимости от степени точности по нормам плавности: - для прямозубых передач: = 1;
- для косозубых передач:
Для зубчатых колес с твердостью меньше чем 350НВ значение А=006.
Определим коэффициент для косозубой передачи:
Определим коэффициент для прямозубой передачи:
Значение коэффициента () принимают по таблице 2.7 [ ] в зависимости от коэффициента схемы передачи и твердости зубьев.
Следовательно: -быстроходная ступень = 115;
-тихоходная ступень = 105.
Значение принимают по таблице 2.6 [ ] в зависимости от степени точности передачи по нормам плавности окружной скорости и твердости рабочей поверхности. Принимаем: - быстроходная ступень = 106;
- тихоходная ступень = 102.
Определим для шестерни быстроходной передачи:
Коэффициент нагрузки КН :
Определим контактное напряжение для шестерни быстроходной передачи:
Так как контактное напряжение =463 МПа удовлетворяет условию примем ширину венца для шестерни быстроходной передачи bw = 545 мм.
Определим фактическое контактное напряжение для шестерни тихоходной ступени:
Коэффициент нагрузки: .
5 Напряжение изгиба в зубьях шестерни и колеса
Напряжение изгиба в основании зубьев в шестерне тихоходной передачи определяем по формуле:
Фактическое напряжение изгиба в колесе тихоходной передачи:
где и - коэффициенты учитывающие форму зубьев соответственно шестерни и колеса находится по графикам на рис. 20 [ ]:
Ft – окружная сила в зацеплении.
Фактическое напряжение изгиба в шестерне тихоходной передачи:
Фактическое напряжение в основании зубьев быстроходной передачи определяется по формуле:
где - коэффициент учитывающий распределение нагрузки между зубьями;
- коэффициент вычисляемый по формуле:
YB – коэффициент учитывающий работу зуба как пластины и определяется равенством
Фактическое напряжение на шестерне быстроходной передачи:
6 Заключение о работоспособности передачи
Передача считается работоспособной если выполняются условия:
)Контактная выносливость поверхности зубьев быстроходной ступени:
Контактная выносливость поверхности зубьев тихоходной ступени:
)Изгибная выносливость зубьев шестерни быстроходной ступени:
Изгибная выносливость зубьев колеса быстроходной ступени:
)Изгибная выносливость зубьев шестерни тихоходной ступени:
Изгибная выносливость зубьев колеса тихоходной ступени:
Так как все условия выполняются наша передача является работоспособной.
Разработка эскизного проекта редуктора
Рис. 2. Конструкция быстроходного промежуточного и тихоходного валов
1 Конструирование валов редуктора привода
Определим диаметры участков валов с помощью формул:
- диаметры быстроходного вала:
Диаметр вала электродвигателя (АИР100L4) dэл = 22 мм. Согласовав диаметры принимаем диаметр быстроходного вала dБ = 22 мм.
Диаметр цапфы вала под подшипником:
где tкон – высота заплечика равная 18 [ Л 46]
Согласуем значение до кратного пяти и примем dП(Б) = 25 мм.
Диаметр буртика для упора кольца подшипника:
где r – координата фаски внутреннего кольца подшипника равная 15 [ 45]
Принимаем dБП(Б) = 30 мм.
- диаметры промежуточного вала:
В целях унификации для промежуточного вала диаметр цапфы вала под подшипником примем равному диаметру цапфы быстроходного вала:
Диаметр шейки вала в месте установки зубчатых колес:
Диаметр буртика колеса:
где f – высота заплечика равная 16 [ 45]
Принимаем dБК = 28 мм.
- диаметры тихоходного вала:
Принимаем dТ = 26 мм.
Диаметр цапфы под подшипник тихоходного вала:
Примем dБП = dКТ = 42 мм.
- длины участков валов:
Длина посадочного участка быстроходного и тихоходного валов:
Длина промежуточного участка быстроходного вала:
Длина промежуточного участка тихоходного вала:
Наружная резьба хвостовика быстроходного вала:
Согласно ГОСТу 12081-72 принимаем наружную резьбу хвостовика быстроходного вала dр = 16 мм: М16х15 [ Л стр. 475 табл. 2427].
Длина резьбового участка для быстроходного вала:
Принимаем по ГОСТ 12081-72: LР = 18 мм.
Диаметр внутренней резьбы для тихоходного вала принимаем согласно стандарта на концевые шайбы (ГОСТ 14734-69) [ стр. 477 табл. 2430]:
Отверстие под резьбу: М16.
Длина отверстия под резьбу тихоходного вала:
Остальные длины участков валов определяем графически по эскизной компоновке.
2 Определение расстояния между деталями.
Расстояние a между стенками корпуса и зубчатыми колесами определяем исходя из рекомендаций [1 стр. 24]. Определяем это расстояние согласно формуле:
где L – длина зубчатой передачи определяемая по формуле:
Подшипники качения в значительной степени определяют ресурс редуктора поскольку ресурс подшипников ограничен тогда как ресурс зубчатых передач может быть неограниченно большим.
Из экономических соображений и из особенностей технологии сборки предпочтительнее применение шариковых однорядных подшипников легкой серии ГОСТ 8338-75. В случае если в дальнейших этапах проектирования выяснится их недостаточная грузоподъемность следует применить подшипники других типов.
Подбор подшипников осуществляется по диаметру внутреннего кольца соответствующая принятому ранее диаметру dП. Необходимо по таблицам каталога определить характеристики подшипников – динамическую грузоподъемность С статическую грузоподъемность С0 размеры подшипника – d D и bП также другие параметры.
Для подшипников должно выполнятся условие:
где [C] – требуемая динамическая грузоподъемность содержащаяся в распечатке (приложение I).
- для быстроходного вала выбираем шариковый однорядный радиальный подшипник легкой серии №205: [ Л стр. 459 табл. 24.10]
d = 25 мм; D = 52 мм; B = 15 мм; C = 11 кН; С0 = 709 кН.
- для промежуточного вала выбираем шариковый однорядный радиальный подшипник легкой серии №305:
d = 25 мм; D = 62 мм; B = 17 мм; C = 176 кН; С0 = 116 кН.
- для тихоходного вала выбираем шариковый однорядный радиальный подшипник средней серии №307:
d = 35 мм; D = 80 мм; B = 21 мм; C =262 кН; С0 = 179 кН.
Расчет промежуточного вала на прочность
Рис.3. Расчетная схема промежуточного вала.
1 Определение моментов действующих на промежуточный вал.
Определим координаты средних плоскостей подшипников и зубчатых колес:
Соответственно: L1 = L4 = e = 31мм; L2 = L3 = c = 51мм.
Определим реакции в опорах:
RА2 = RB2 =183145 Н.
Определим моменты в вертикальной плоскости и построим эпюру моментов:
Рис 4. Эпюра моментов вертикальной плоскости.
Определим моменты в горизонтальной плоскости и построим эпюру моментов:
Рис 5. Эпюра моментов горизонтальной плоскости.
Определим суммарный изгибающий момент в опасных сечениях:
Можно выделить три опасных сечения C D E т.к. в них изгибающие моменты имеют наибольшее значение.
Рис. 6. Суммарный изгибающий момент.
2 Определение фактического запаса прочности промежуточного вала
где и - коэффициенты запаса по нормальным и касательным напряжениям.
где и - амплитуды запаса напряжений;
и - средние напряжения циклов;
и - переделы выносливости гладких образцов при симметричном цикле изгиба и кручения;
и - эффективные коэффициенты концентрации напряжений;
Кd – коэффициент влияния шероховатости;
и - коэффициенты чувствительности материала.
Материал: Сталь 40ХН
Выбираем значения коэффициентов: [ стр. 146 табл. 106]
В опасных сечениях С и Е S=118 что больше минимально допустимого [S]=15 следовательно работоспособность обеспечена.
Проверочный расчет подшипников промежуточного вала.
Нагрузки на подшипник определяются геометрическим суммированием опорных реакций по формулам:
Определяем эквивалентную динамическую нагрузку:
гдеи - радиальная и осевая силы;
V – коэффициент вращения V=1;
КБ – коэффициент безопасности учитывающий характер нагрузки КБ = 14;
КТ – температурный коэффициент КТ= 1.
На валу установлен подшипник №205 его работоспособность считается обеспеченной если выполняется условие:
гдеа1 – коэффициент долговечности а1=1;
а2 – обобщенный коэффициент совместного влияния качества металла особенностей технологии производства конструкции и условий эксплуатации а2=1;
L – номинальная долговечность:
кН > 551 кН следовательно работоспособность выбранных подшипников обеспечена.
Расчет шпоночного соединения.
Быстроходный вал является валом-шестерней так как диаметр шестерни и вала принимаем одинаковыми.
Определяем шпонку под колесом быстроходной ступени: шпонка призматическая по ГОСТ 23360-78 с параметрами: d = 25 мм; b = 8 мм; h = 7 мм.
Из условия прочности определим рабочую длину шпонки (мм) по формуле:
Полная длина шпонки первого исполнения (со скругленными торцами):
Согласуем полученное значение со стандартом [ стр. 476 табл. 2429 ] и примем длину шпонки из ряда длин при последующем проектировании. Диапазон размеров: L = 18 90 мм.
Выбираем шпонку под колесо тихоходной ступени: шпонка призматическая по ГОСТ 23360-78 с параметрами: d = 42 мм; b = 12 мм; h = 8 мм.
Согласуем полученное значение со стандартом [ стр. 476 табл. 2429 ] и примем длину шпонки из ряда длин при последующем проектировании. Диапазон размеров: L = 28 140 мм
Выбираем шпонку на хвостовике быстроходного вала: шпонка призматическая по ГОСТ 12081-72 на конические концы валов с параметрами: dср = 195 мм [ стр. 475 табл. 2427]; b =6 мм; h = 6 мм.
Выберем шпонку на хвостовике тихоходного вала: шпонка призматическая по ГОСТ 23360-78 с параметрами: d = 26 мм; b = 8 мм; h = 7 мм.
Рабочая длина шпонки:
Конструирование корпусных деталей и крышек
Корпусная деталь состоит из стенок ребер бобышек фланцев и других элементов соединяемых в одно целое. Для редукторов толщину стенки отвечающим требованиям технологии литья необходимой прочности и жесткости корпуса вычисляют по формуле:
где Т – вращающий момент на выходном валу Нм.
Примем толщину стенок корпуса редуктора равной восьми миллиметрам.
Толщина стенки крышки корпуса:
Примем толщину стенок крышки корпуса равной восьми миллиметрам.
Расстояние между дном корпуса и поверхностью колеса:
Для соединения корпуса и крышки по всему контуру плоскости разъема редуктора выполняют специальные фланцы как показаны на рисунке 5.
Рис.5 Фланец корпуса и крышки.
Размеры конструктивных элементов фланца:
Дно корпуса выполняют с уклоном 1-2 0 в сторону сливного отверстия.
Определим высоту масляного слоя:
Выразим величину hmin из объема смазочного материала
гдес = 07 14 лкВт - расход масла на киловатт мощности электродвигателя;
а b – геометрические параметры днища корпуса;
Nэ = 48 кВт – мощность электродвигателя.
Получим что при hmin = 40 мм нарушается условие bо = 40мм от днища до колеса тихоходной ступени. Окружная скорость колеса тихоходной ступени v 1 мс то высоту масленого слоя выбираем от среднего делительного диаметра колеса быстроходной ступени. Примем hmin = 65 мм.
Конструктивное оформление опорной части корпуса
Диаметр винта крепления редуктора к плите (раме):
где dв – диаметр винта крепления крышки и корпуса редуктора.
Принимаем dф = 16 мм.
Места крепления корпуса к плите или раме располагают на возможно большем расстоянии друг от друга и оформляют в виде ниш расположенным по углам корпуса (Рис8):
Рисунок . Конструирование фланца.
Высоту ниши принимают при креплении болтами:
Число винтов примем в зависимости от межосевого расстояния w (мм) тихоходной ступени: z=4 при w 140мм.
Конструктивное оформление приливов для подшипниковых гнезд.
Приливы в которых располагают подшипник конструктивно оформляют по рис. .
Рис. . Прилив для подшипника
Диаметр прилива принимают (мм):
Для промежуточного вала:
Для быстроходного вала:
Длина l1 подшипниковых гнезд определяется конструктивно шириной подшипников в опорах высотой крышки и расстоянием от подшипника до внутреннего края прилива равного 1 мм. В нашем случае l1 постоянна для всех гнезд и равна 40 мм.
Для соединения крышки с корпусом используем винты с цилиндрической головкой с шестигранным углублением под ключ. Диаметр dв винтов крепления крышки принимают в зависимости от вращающего момента Т (Нм) на выходном валу редуктора:
Используем винты М12 с цилиндрической головкой длиной 70 мм. (длина определяется конструктивно с учетом материала из которого выполнен корпус в нашем случае это чугун и винты должны быть закручен на расстояние не меньшее чем 15 диаметра).
Высоту h1 прилива в крышке под стягивающий винт определяем графически исходя из условия размещения головки болта на плоской опорной поверхности. В нашем случае крышка редуктора крепится винтами М12 поэтому принимаем h1 равной 70 мм.
Ширина фланца l3 равна длине подшипниковых гнезд за вычетом припуска на обработку равного 05 т.е. 3 мм. L3 постоянна для всех гнезд и равна 37 мм.
Фиксирование крышки относительно корпуса.
При сборке редуктора нужно точно фиксировать положение крышки относительно корпуса. Необходимую точность фиксации обеспечиваем штифтами. Диаметр штифтов:
где d – диаметр крепежного винта.
Примем два конических штифта с внутренней резьбой которые установим по срезу угла крышки с одной стороны и в нише с другой.
3 Выбор крышек подшипников
Для данного редуктора целесообразно применение привертных крышек подшипников изготовленных из серого чугуна марки СЧ21 [ стр. 166]. На рис. 7 показаны основная конструкция привертных крышек. Они в свою очередь разделяются на глухие и с отверстием для выходного вала.
Рисунок 7 – крышка подшипника.
Диаметр D крышки равен диаметру внешнего кольца подшипника. Диаметр DМ равен внешнему диаметру манжетного уплотнения. Быстроходный вал D = 52 мм. DМ = 38 мм.
Промежуточный вал D = 62 мм. Тихоходный вал D = 80 мм. DМ = 55 мм.
Размеры К К1 диаметры и количество винтов крепления крышки принимаем исходя из рекомендаций [ стр. 166]. Для быстроходного вала: К = 5 мм К1 = 6 мм. крышка крепится четырьмя винтами М6. Для промежуточного вала: К = 5 мм К1 = 6 мм. крышка крепится четырьмя винтами М6. Для тихоходного вала: К = 6 мм К1 = 72 мм. крышка крепится четырьмя винтами М8.
4. Выбор уплотнений.
Для предохранения вытекания смазочного материала из подшипниковых узлов а также для защиты их от попадания извне пыли и влаги используем армированные манжетные уплотнения из бензомаслостойкой резины. В нашем случае достаточно установить манжеты без пыльника и в один ряд так как уровень масла не доходит до уровня манжеты и редуктор не предназначен для работы в запыленной внешней среде.
На быстроходном валу устанавливаем манжету 25х38 на тихоходном 35х55. Установленные манжеты соответствуют ГОСТ 8752-79.
Расчет открытой цилиндрической зубчатой передачи.
Определим модуль зацепления по формуле:
где z –Число зубьев шестерни открытой передачи.
-коэффициент ширины зубчатого венца колеса относительно модуля.
T-момент на шестерне
-допустимое напряжение изгиба зубьев шестерни.
Диаметр вершин зубьев
Диаметр впадин зубьев
Смазка редуктора.docx
Для уменьшения потерь мощности на трение и снижения интенсивности износа трущихся поверхностей а также для предохранения их от заедания задиров коррозии и лучшего отвода теплоты трущиеся поверхности должны иметь надежную смазку.
Для проектируемого редуктора применим картерную систему смазки наиболее распространенную в машиностроении. Такую систему смазки применяют при окружной скорости зубчатых колес от 03 до 125 мс. В нашем случае окружные скорости быстроходной и тихоходной ступеней находятся в этих пределах поэтому применение картерной системы вполне оправдано.
Выбор смазочного материала определяется в зависимости от контактного напряжения и окружной скорости колес. Предварительно определим необходимую кинематическую вязкость масла по табл. 11.1 [2 стр. 198]. Для зубчатых колес контактные напряжения которых не превышают 600 МПа а окружные скорости свыше 5 мс рекомендуемая кинематическая вязкость равна 22·10-6 м2с. Редуктор предназначен для работы при температурах ≤ 50ºС. Всем перечисленным выше условиям соответствует масло индустриальное И-Л-А-22. Его употребляют в качестве рабочей жидкости в гидравлических системах станочного оборудования автоматических линий прессов для смазывания легко- и средненагруженных зубчатых передач направляющих качения и скольжения станков где не требуются специальные масла и других механизмов.
В двухступенчатой передаче при окружной скорости ≥ 1 мс (как в нашем случае) в масло достаточно погрузить только колесо тихоходной ступени а максимальный уровень принимается равным трети радиуса колеса тихоходной ступени [2 стр. 199]. Таким образом минимальный уровень масла будет равен 70 мм. а максимальный 95 мм. от днища редуктора.
Необходимое количество масла – 6 литров.
Расчет отклонений.doc
Расчет отклонений размеров допусков формы зубчатого колеса быстроходной ступени.
Расчет отклонений размеров зубчатого колеса.
Осевой размер определяющий ширину зубчатого венца принимаем по сборочному чертежу редуктора. Предельные отклонения ширины зубчатого венца назначаем в зависимости от степени точности передачи по табл. 7.1.
Диаметр вершин с зубьями
В нашем случае для 8 степени кинематической точности устанавливаем допуски: для диаметра вершин 1688H(+004) а для ширины зубчатого венца 275h11(-013)
Свободные размеры определяющие конфигурацию и размеры ступицы и диска определяем по рекомендациям [2 стр. 41-46].
Номинальное значение посадочного диаметра определяем по сборочному чертежу его предельные отклонения в нашем случае 25H7(+0015).
Размеры поперечного сечения шпоночного паза и их предельные отклонения определяют в соответствии с [8 п.2 табл. 2.3.] В соответствии с табл. 21 [5 стр. 24] проставлена ширина шпоночного паза b=8 мм и глубина паза во втулке A=d+t2=25+33=283 мм. На основании рекомендаций [8 п.2 табл. 2.3.] на чертеже проставляем: 8JS9(±0018) и 283+02.
Расчет допусков формы зубчатого колеса.
Допуск цилиндричности базового отверстия.
где ta - допуск диаметра отверстия равный 0025 мм. [2 стр. 335]
Т = 03×0033= 001 мм.
После округления по [8 табл. 3.1] принимаем Т = 001 мм.
Допуск перпендикулярности торца ступицы.
Так как отношение длины ступицы к её диаметру ldст³08 допуск перпендикулярности на диаметре dст можем определить по таблице 22.7. [2 стр. 333] приняв степень точности для подшипников I группы равным 8 [2 стр. 334] Таким образом Т^dст= 002 мм.
Допуск параллельности и симметричности расположения шпоночного паза.
Допуск параллельности Т и симметричности Т назначают для обеспечения более равномерного контакта рабочих поверхностей шпоночного паза ступицы и шпонки. Принимают Т=06tш и Т=4tш tш – допуск ширины шпоночного паза. [3 стр. 13] tш в нашем случае 003 мм [2 стр. 336]. Таким образом T=06×003=0018 мм. Т=4×0035=014 мм. После округления получим T=0018 мм. Т=014 мм. На глубину шпоночного паза задают предельные отклонения при сечении шпонки 6×6 32×18 - +02 мм.
Расчет длины общей нормали зубчатого колеса быстроходной ступени.
Длину общей нормали для цилиндрических колес с внешними косыми зубьями рассчитывают по формуле
где mn – нормальный модуль мм;
– угол профиля исходного контура по стандарту ГОСТ 13755-81 =200;
zw – число зубьев в длине общей нормали;
z – число зубьев контролируемого колеса;
inv t – эвольвентный угол соответствующий углу профиля который находится по формуле
– торцовый угол профиля исходного контура.
Число зубьев в длине общей нормали zw для цилиндрических колес с косыми зубьями при небольших коэффициентах смещения (x 1):
Округлив полученное значение до ближайшего целого числа получим штук.
Допуск на длину общей нормали принимаем по [3 стр. 8-12]:
Расчет отклонений размеров допусков формы промежуточного вала.
Расчет отклонений размеров промежуточного вала.
Осевые размеры вала определяются размерами сборочной размерной цепи редуктора: габаритный размер 180 мм осевые размеры 30 40 и 35 мм соответственно определяющие длину посадочных поверхностей; размер 5 мм координирующий осевое положение шпоночного паза а также размеры фасок и проточки. Предельные отклонения этих размеров назначают как что соответствует ±t2 среднего класса точности. Значения t определяют по табл.2.2 [8].
Длину шпоночных пазов определяют из расчёта шпоночного соединения на прочность (см. п. 8)
Для размера »12 предельные отклонения не указаны так как он определяет зоны различной шероховатости одной и той же поверхности 25 мм.
Свободные диаметральные размеры вала определяют по сборочному чертежу редуктора. Предельные отклонения этих размеров назначены соответствующей записью в технических требованиях.
Номинальные значения сопряженных размеров определяют по сборочному чертежу а предельные отклонения принимают в соответствии с посадкой: 25.
Размеры поперечного сечения шпоночного паза и их предельные отклонения определяют в соответствии с [8 п.2 табл. 2.3.] В соответствии с табл. 21 [5 стр. 24] проставлена ширина шпоночного паза b=6 мм и глубина паза 4+02 мм. На основании рекомендаций [8 п.2 табл. 2.3.] на чертеже проставляем: 8Р9 и 4+02.
Осевой размер определяющий ширину зубчатого венца принимаем по сборочному чертежу редуктора. Предельные отклонения ширины зубчатого венца назначаем в зависимости от степени точности передачи по табл. 7.1. В нашем случае для 8 степени кинематической точности устанавливаем допуски: для диаметра вершин 70h11(-019) а для ширины зубчатого венца – 50h13(-046).
Расчет допусков формы промежуточного вала.
Соосность посадочных поверхностей являющихся цапфами подшипников.
Допуск соосности Т ограничивает перекос колец подшипников. Он назначается по табл.7.2 в зависимости от типа подшипника устанавливаемого на вал. Для шариковых радиальных подшипников качения установлена 7-я степень точности допусков соосности.
Интервалы размеров мм
Степени точности допусков соосности
допуски соосности мкм
В нашем случае цапфы 25K6 предназначены для установки на них шариковых подшипников. По табл. 7.2 для 8-й степени точности допуск соосности равен 0030 мм.
Цилиндричность посадочных поверхностей для подшипников качения.
Допуск цилиндричности Т этих поверхностей задают для ограничения величины искажения геометрической формы дорожек качения колец подшипников. Рекомендуется принимать Т »03td где td – допуск размера посадочной поверхности вала. Допуск цилиндричности в нашем случае равен Т =03td=03(002-0002)=0007 мм. Округляя получим Т = 0007 мм.
Перпендикулярность базовых торцов валов для подшипников качения.
Допуск перпендикулярности Т назначают для уменьшения перекоса колец подшипников и связанной с ним ориентации дорожек качения. Его значение принимают по табл.7.3 для посадочного диаметра подшипника dn в зависимости от типа подшипника качения и соответствующей ему степени точности допуска перпендикулярности: 8-я – для шариковых радиальных подшипников.
Интервалы размеров мм.
Степени точности допусков параллельности перпендикулярности
допуски параллельности перпендикулярности мм
На обоих концах вала 25k6 (рис.П.1) устанавливаются зубчатые колеса. Т.к. зубчатое колесо упирается в торец поверхности 28. По табл.7.3 допуск перпендикулярности Т на диаметре d=28 мм для 8-й степени точности допусков перпендикулярности равен 20 мкм.
Соосность посадочных поверхностей для зубчатых колёс относительно общей оси вращения вала.
Допуски соосности Т регламентируют нормы кинематической точности и нормы контакта колёс. Они назначаются по табл.7.4 в зависимости от степени кинематической точности передачи.
Степень кинематической
Диаметр делительной окружности мм
степень точности допуска соосности
Т.к. поверхность 25d11 является базой для цилиндрического
колеса 8-й степени кинематической точности с делительным диаметром d = 168 мм. В соответствии с табл.7.4 степень точности допуска соосности равна 8. По табл.7.2 величина допуска соосности равна 0080 мм.
Параллельность и симметричность расположения шпоночного паза вала.
Допуск параллельности Т и симметричности Т назначают для обеспечения более равномерного контакта рабочих поверхностей шпоночного паза и шпонки. Эти значения рекомендуется принимать в зависимости от допуска tш на ширину паза по формулам: Т»06 tш и Т»4 tш.
Значение допуска Т»06 tш=06[-0018-(0061)]=0040 мм. В соответствии с базовым рядом числовых значений допусков полученное значение округляем до 0040 мм.
Значение допуска Т»4 tш=4[-0018-(-0061)]=0080 мм. В соответствии с базовым рядом числовых значений допусков полученное значение округляем до 0080 мм. Символ Т на чертеже означает что указывается полная ширина соответствующего поля допуска.
Измерительные размеры шестерни тихоходной ступени.
По формулам (7.1) (7.2) (7.4) и (7.4) рассчитаем длину общей нормали для шестерни тихоходной ступени:
Округлив полученное значение до ближайшего целого числа получим .
введение.doc
Все эти элементы крепятся на одной конструкции - сварной раме. Она воспринимает и передает на фундамент действующие на машину нагрузки и обеспечивает правильность расположения узлов в процессе эксплуатации. Рама представляет собой сварную конструкцию из швеллеров. Швеллера выбираются в соответствие с диаметрами фундаментных болтов. По сравнению с плитой эта конструкция дешевле легче примерно в 2 раза имеет достаточную жесткость поэтому надобность в специальных ребрах жесткости отпадает. При выполнении рамы из швеллеров их располагают для удобства постановки болтов полками наружу. На внутреннюю поверхность полки накладывают косые шайбы. Опорные поверхности-платики на которые устанавливают редуктор и электродвигатель создаются привариванием тонких полосок стали высотой 5-6 мм.
Редуктор состоит из литого корпуса «чемоданного» типа достоинствами которого является: большая жесткость вибро-аккустические свойства уменьшение коробления при старении возможность размещения большего объема масла простота очистки удовлетворение современным требованиям технической эстетики. В корпусе редуктора помещают элементы передачи: зубчатые колеса валы подшипники. Валы редуктора расположены горизонтально относительно опоры. Редуктор двухступенчатый. Первая ступень - конический вал вторая ступень - вал цилиндрический. Корпус выполнен разъемным по осям валов состоящий из основания и крышки. Основание и крышку фиксируют относительно друг друга двумя центрирующими коническими штифтами установленными по срезам углов. Основание и крышка соединяются винтами М12.
Для герметизации осевой фиксации и восприятия осевых нагрузок подшипники качения закрывают глухими и сквозными привертными крышками. В сквозных крышках в качестве уплотнений принимают манжеты.
Для повышения плавности работы и долговечности в картер редуктора заливается 7 л индустриального масла И-30А. Для заливки масла контроля правильности зацепления и для внешнего осмотра деталей в верхней части редуктора размещают люк. Для предотвращения протекания масла поверхности сопряжения корпуса и крышки смазывают герметиком УТ-34.
В процессе эксплуатации трущиеся детали редуктора изнашиваются а продукты износа загрязняют смазывающую жидкость. Поэтому на дне корпуса предусмотрено сливное отверстие которое закрыто пробкой цилиндрической резьбой. Для удобства слива масла днище картера выполняют под углом 1-20 в сторону сливного отверстия. Для проверки и контроля уровня масла применяются жезловые маслоуказатели.
При работе редуктора внутри него повышается температура а следовательно и давление поэтому во избежание выдавливания масла через манжеты в крышке редуктора установлена отдушина.
Для транспортирования редуктора в его верхней части предусмотрены проушены.
Спецификация приводная станция.spw

Болт М20 х 65 ГОСТ 7805-70
Болт М12 х 45 ГОСТ 7805-70
Винт установочный М8 х 12
Гайка М20 ГОСТ 5915-70
Гайка М12 ГОСТ 5915-70
Муфта МУВП-28 ГОСТ 21424-93
Шайба косая 20 ГОСТ 10906-78
Шайба косая 12 ГОСТ 10906-78
Шайба пружинная 20 65Г
Шайба пружинная 12 65Г
Электродвигатель АИР132М6
Приводная станция.cdw

Электродвигатель АИР100S2
Передаточное отношение привода 21
Вращающий момент на выходном валу
Частота вращения тихоходного вала
Технические требования
Допускаемые смещения валов электродвигателя
Разрез А-А.cdw

эуб. колесо.cdw

Штамповочные уклоны 5
штамповочные радиусы R4
Неуказанные предельные отклонения размеров отверстия - h14
Сталь40X ГОСТ4543-71
Направление линии зуба
Разрез А-А(2).cdw

Спецификация редуктор.spw

Крышка подшипника глухая
Крышка подшипника сквозная
Болт М6 х 20 ГОСТ 15589-70
Винт М12 х 60 ГОСТ 11738-84
Винт М6 х 14 ГОСТ 17473-80
Гайка М16 ГОСТ 15522-70
Кольцо 25 ГОСТ 13942-80
Мaнжета 1-35 х 55-1 ГОСТ 8752-79
Мaнжета 1-25 х 38-1 ГОСТ 8752-79
Подшипник 205 ГОСТ 8338-75
Подшипник 305 ГОСТ 8338-75
Подшипник 307 ГОСТ 8328-75
Уплотняющая прокладка
Шайба 12 Н ГОСТ 6402-70
Шайба 6 Л ГОСТ 6402-70
Шайба 16 Н ГОСТ 13464-77
Шпонка 6 х 6 х 28 ГОСТ 23360-78
Шпонка 8 х7 х 25 ГОСТ 23360-78
Шпонка 8 х 7 х 36 ГОСТ 23360-78
Шпонка 12 х 8 х 45 ГОСТ 23360-78
Штифт 10 х 30 ГОСТ 9464-79
Штифт 4 х 12 ГОСТ 3128-70
Герметик УТ-34 ГОСТ 24285-80
Масло И-Г-А-32 ГОСТ 20799-88
Эмаль серая (ХВ 16)
Рекомендуемые чертежи
- 29.07.2014
- 24.01.2023